DOI:
10.1039/D1RA03618A
(Paper)
RSC Adv., 2021,
11, 30569-30573
Moisture affinity of HDPE/phase-change material composites for thermal energy storage applications†
Received
8th May 2021
, Accepted 6th September 2021
First published on 8th November 2021
Abstract
Moisture adsoprtion can degrade the structural integrity of thermal energy storage devices and can negatively impact the capacity and charging/discharging behaviour. Steady-state and transient experiments are conducted at various operating temperatures to evaluate the moisture affinity of organic phase-change material (PCM) shape stabilized with high-density polyethylene (HDPE).
Introduction
Due to increasing demand to shift the grid load and to provide sustainable performance, there has been an increasing interest in various energy storage materials.1 Conventionally, phase-change-material (PCM) based thermal batteries have shown promising results for wide-scale implementation over a range of temperatures.2–4 Both organic (e.g., paraffin wax) and inorganic (e.g., salt hydrates) PCMs are widely used in various applications. When selecting a PCM, several factors need to be considered, including the latent heat of fusion, density, thermal resistance, and reliability of repeated thermal cycling.
Recent interest in the use of polymers and polymer-PCM composites to build heat exchangers5 and thermal energy storage systems6 has motivated the present study. To make a polymer–PCM composite, organic PCM is mixed with a compatible polymer, such as HDPE, and shape stabilized.7 The PCM is essentially encapsulated directly into the HDPE, where the HDPE has a much higher melting temperature than the PCM to allow the PCM, which melts and freezes continuously, to remain contained within the HDPE structure.
In addition to the selection criteria previously mentioned, when PCM is contained within a polymer as its supporting structure, moisture affinity is also an important consideration since it dictates the long-term performance of these composite materials. Prior investigators have studied moisture transfer of composite porous textiles containing encapsulated PCM.8 The moisture affinity of HDPE and wood-flour composites,9 HDPE and rice-hull composites,10 and HDPE and bio-fiber composites11 have been studied extensively. However, to the best knowledge of the authors, the moisture adsorption and desorption characteristics of an organic PCM shape stabilized with HDPE has not been conducted.
In this investigation, steady-state and transient experiments are conducted at several different operating temperatures to evaluate the moisture affinity of an organic PCM (PureTemp 42) shape stabilized with HDPE. Prior studies by the authors report the latent heats of fusion, phase-change temperature ranges, and thermal conductivity of these composite materials.6,12,13
Sample preparation
PureTemp 42 (PureTemp, Minneapolis, MN), an organic PCM which changes phase at 42 °C and has a latent heat of fusion of 218 kJ kg−1, was heated and mixed with HDPE (PPR-HDPE01, Premier Plastics Resins, Lake Orion, MI). A mixture of 50% PureTemp 42 and 50% HDPE by mass (50/50) was prepared. The mixture was then formed into pellets utilizing a shredder (SHR3D IT, 3devo, Utrecht, Netherlands). The pellets were then fed into the hopper of a filament extruder (next 1.0, 3devo, Utrecht, Netherlands) to fabricate 1.75 mm diameter filament.
Microscopy
Filament samples were frozen using liquid nitrogen and then subsequently shattered to examine the interior of the filament. The samples were gold coated (Sputter Coater 108, Cressington Scientific Instruments, Watford, UK) for visualizing with a scanning electron microscope (SEM, Quanta 650, ThermoFisher Scientific, Hillsboro, OR).
Fig. 1 shows SEM images of the extruded filament containing HDPE and PureTemp 42. Prior work examined the microstructures of both pure HDPE and pure PureTemp 42.12,13 The platelet-like structure of the HDPE is clearly seen with the lattice-like structure of the PCM embedded in between the platelets. Upon visual inspection of Fig. 1 and other similar SEM images, the dispersion of PCM appears to be homogeneous.
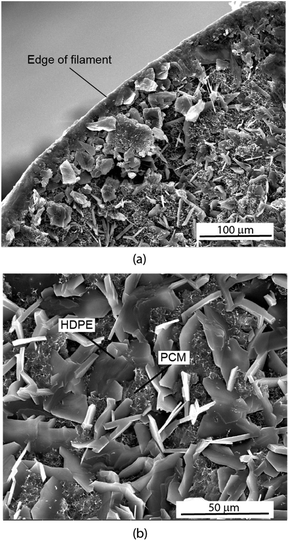 |
| Fig. 1 Microstructure visualization of HDPE with PureTemp 42 (50% PCM by mass) at 25 °C (a) image showing edge of filament, and (b) view showing HDPE (platelet-like structures) and PCM (lattice-like structures). | |
Dynamic vapor sorption
Both equilibrium (steady-state) and transient adsorption and desorption behaviour of the materials are important to characterize the affinity of water. While the steady-state isotherms establish the total moisture adsorption capacity, the diffusion coefficient determines the response of the material (i.e., how quickly water can be adsorbed or desorbed). A dynamic vapor sorption apparatus (DVS Advantage, Surface Measurement System, UK) has been used to conduct the steady-state and transient experiments.14,15
Fig. 2 shows the DVS experimental setup. The relative humidity is controlled by mixing wet and dry nitrogen gas (N2). A vapor sensor is used to measure the relative humidity. Water vapor, with a known concentration, flows over a sample that is suspended from an ultra-fine microbalance, which is used to measure the change in weight of the sample due to adsorption or desorption of the vapor molecules. The sample mass for various experiments varied between 1–3 mg. It is worth noting that regardless of the variation of dry sample mass, the percentage in mass is an indication of potential for moisture for various samples and provides the relative comparison independent of the sample mass.
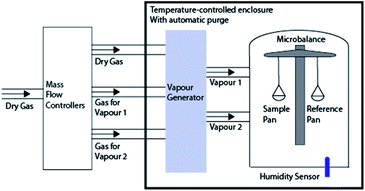 |
| Fig. 2 Components of the experimental setup. | |
Temperature is an important factor for moisture adsorption and desorption potential. Prior studies have shown that, in general, the moisture adsorption capacity of the material increases with temperature while the response time decreases, indicating higher diffusion coefficients.14,15
In the current study, the samples were suddenly exposed to a dry or humid environment and the weight change due to moisture adsorption and desorption was measured as a function of time. The data was then used to calculate the steady-state capacity and diffusion coefficients.
Steady-state adsorption/desorption capacity
Steady-state experiments have been conducted to investigate the moisture adsorption capacity of the materials. The experimental procedure is presented in Fig. 3. A sample, with a known initial mass, is exposed to a series of moisture levels, and the change-in-mass response is recorded. The experiments are conducted for both adsorption and desorption modes for a set temperature. The entire process is repeated for various temperatures, and the steady-state mass gain at respective humidity conditions is recorded to establish the moisture adsorption/desorption isotherms at specified temperatures. The relative error in measurement is less than 1 μg. The average variation in relative humidity and temperature is noted as ±1% and ±0.25 °C, respectively. Prior to the beginning of the test, each sample was exposed to a completely dry-air condition (0% RH) for sufficent time to ensure that the sample had no initial moisture content at the beginning of the test. The same drying test has been repeated for different temperatures.
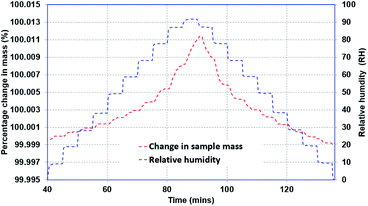 |
| Fig. 3 Experimental procedure to establish adsorption/desorption isotherms. | |
Transient adsorption/desorption analysis
The transient response of the sample is established by evaluating the time response of the sample when the ambient moisture content is changed as a step function, and the mass of the sample continues to change until it reaches the steady-state condition. Two types of experiments were performed: (i) small incremental change in moisture content (10%), and (ii) large incremental change in moisture content (70% and 90%). Fig. 4 presents representative data for the second type of test. As can be noted, the relative humidity in the chamber was increased from 0% to 90% and then decreased back to 0%. Once the sample was completely dry, another cycle with 70% RH was initiated.
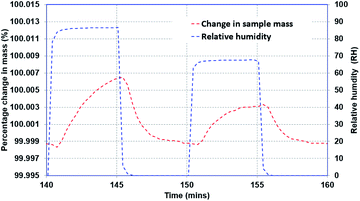 |
| Fig. 4 Transient experimental procedure to establish the diffusion coefficients. | |
The one-dimensional transient diffusion equation can be solved to extract the bulk diffusion coefficients (eqn (1)) for the samples under consideration using appropriate initial and boundary conditions (eqn (2)). The diffusion coefficient is obtained by curve fitting the solution while minimizing the error in predicted and measured values.14,15
|
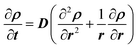 | (1) |
Initial and boundary conditions
|
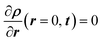 | (2c) |
Results and discussion
Samples of HDPE, PureTemp 42, and a 50/50 (by mass) composition were prepared and subjected to the experimental procedures outlined in the preceding sections. The steady-state isothermal experiments were performed for multiple temperature settings (25, 35, and 45 °C). For pure PCM and the composite sample, the 45 °C experiments were excluded since the melting temperature for PCM is 42 °C. Fig. 5–7 show the adsorption and desorption isotherms for pure PCM, HDPE, and the composite sample, respectively. It also can be noted that the relative hysteresis is negligible except at relatively higher humidity values, and the capacity is increased slightly with increase in temperature for both types of materials.
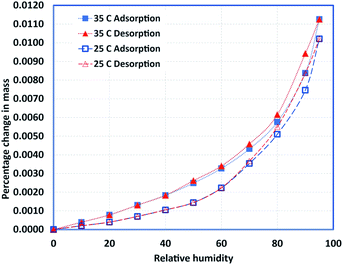 |
| Fig. 5 Adsorption/desorption isotherms for pure PCM at 25 and 35 °C. | |
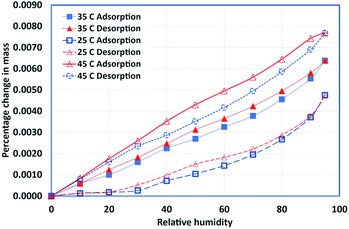 |
| Fig. 6 Adsorption/desorption isotherms for pure HDPE at 25, 35, and 45 °C. | |
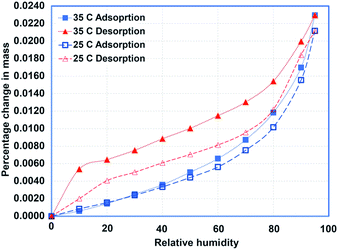 |
| Fig. 7 Adsorption/desorption isotherms for 50/50 composite at 25 and 35 °C. | |
The most important observation is the total capacity. Pure PCM can adsorb about 30% more moisture at higher humidity values. Similarly, the composite samples adsorb almost twice the amount of moisture adsorbed by the pure materials, which can be explained in terms of potential voids created during the mixing process. Regardless, the overall change in the sample mass is negligible due to a very small amount of moisture adsoprtion. It is concluded that the material has very little affinity for moisture.
The transient performance of the samples has been established in terms of bulk diffusion coefficients, as shown in Table 1. The diffusivity is determined for both the adsorption and desorption processes to observe any noticeable differences in the mechanism. Also, the temperature of the operation has been varied to establish the impact of temperature. As with the steady-state experiments, the 45 °C temperature was not reported for pure PCM and the composite sample since the PCM starts melting at 42 °C. Based on the established values (±5% uncertainty), it can be concluded that relative moisture diffusivity for pure PCM and the composite (50/50 by mass) is around 10 and 3 times higher, respectively, compared to the pure HDPE. Furthermore, the mass diffusivity for moisture is independent of adsorption or desorption processes as well as the temperature. The relatively small variation in predictions can be justified in terms of errors in measurements.
Table 1 Adsorption/desorption diffusion coefficients
Material composition |
Temperature (°C) |
Adsorption diffusivity m2 s−1 (×10−7) |
Desorption diffusivity m2 s−1 (×10−7) |
Pure PCM |
25 |
10.12 |
10.34 |
35 |
11.95 |
11.19 |
Pure HDPE |
25 |
1.25 |
1.29 |
35 |
1.33 |
1.34 |
45 |
1.45 |
1.41 |
50–50% HDPE + PCM |
25 |
4.23 |
4.12 |
35 |
3.95 |
3.98 |
Conclusions
The goal of the present study was to show that an organic-based PCM shape stabilized with HDPE has very little affinity for moisture (i.e., they are extremely nonhygroscopic materials). Different compositions of the samples have been prepared to determine if the composition can impact the steady-state and transient moisture adsorption and desorption behaviour. While some distinction between the various compositions and operating temperatures was observed, the moisture adsorption and desorption diffusivities indicate that the materials will not be impacted by the presence of moisture. This is a highly promising outcome since it helps justify the use of these materials in various thermal energy storage applications where the presence of moisture is anticipated.
Author contributions
Kashif Nawaz: conceptualization, methodology, investigation, formal analysis, writing-original draft preparation, writing-review and editing, funding acquisition. Thomas B. Freeman: investigation, writing-review and editing. Rafael M. Rodriguez: supervision, writing-review and editing. Sandra K. S. Boetcher: conceptualization, supervision, writing-original draft preparation, writing-review and editing.
Conflicts of interest
There are no conflicts to declare.
Acknowledgements
This work was supported by the US Department of Energy's Building Technologies Office (DOE/BTO) under Contract No. DE-AC05-00OR22725 with UT-Battelle, LLC. This research used resources at the Building Technologies Research and Integration Center, a DOE Office of Science User Facility operated by the Oak Ridge National Laboratory. The authors would like to acknowledge Mr Antonio Bouza, Technology Manager of DOE BTO. Support from the National Science Foundation is also acknowledged under grant no. MRI-1337742 for the purchase of the SEM.
Notes and references
- B. Lindsay, J. Andrepont, C. Dorgan, M. Maccracken, L. Markel, D. Reindl, P. Turnbull, V. Williams and G. Bares, ASHRAE J., 2020, 61, 42–59 Search PubMed
. - E. Borri, J. Y. Sze, A. Tafone, A. Romagnoli, Y. Li and G. Comodi, Appl. Energy, 2020, 275, 115131 CrossRef CAS
. - P. Tan, P. Lindberg, K. Eichler, P. Loveryd, P. Johansson and A. S. Kalagasidis, Appl. Energy, 2020, 276, 115433 CrossRef CAS
. - H. Tian, W. Wang, J. Ding and X. Wei, Energy, 2021, 227, 120412 CrossRef CAS
. - M. Arie, D. Hymas, F. Singer, A. Shooshtari and M. Ohadi, Int. J. Heat Mass Transfer, 2020, 147, 118889 CrossRef CAS
. - T. Freeman, M. Messenger, C. Troxler, K. Nawaz, R. Rodriguez and S. Boetcher, Addit. Manuf., 2021, 39, 101839 CAS
. - H. Inaba and P. Tu, Heat Mass Transfer, 1997, 32, 307–312 CrossRef CAS
. - Y. Li and Q. Zhu, Text. Res. J., 2004, 74, 447–457 CrossRef CAS
. - B. Dawson-Andoh, L. Matuana and J. Harrison, J. Inst. Wood Sci., 2005, 17, 114–119 CrossRef
. - W. Wang, M. Sain and P. Cooper, Polym. Degrad. Stab., 2005, 90, 540–545 CrossRef CAS
. - P. Aggarwal, N. Raghu, A. Kale, C. Vani and S. Chauhan, J. Indian Acad. Wood Sci., 2015, 12, 104–109 CrossRef
. - T. Freeman, D. Spitzer, P. Currier, V. Rollin and S. Boetcher, J. Therm. Sci. Eng. Appl., 2019, 11, 054502 CrossRef CAS
. - T. Freeman, K. Nabutola, D. Spitzer, P. Currier and S. Boetcher, Proceedings of the ASME IMECE, 2018 Search PubMed
. - K. Nawaz, S. Schmidt and A. Jacobi, Int. J. Heat Mass Transfer, 2014, 74, 25–34 CrossRef CAS
. - K. Nawaz, S. Schmidt and A. Jacobi, Int. J. Heat Mass Transfer, 2014, 73, 634–644 CrossRef CAS
.
Footnote |
† This manuscript has been authored by UT-Battelle, LLC, under contract DE-AC05-00OR22725 with the US Department of Energy (DOE). The US government retains and the publisher, by accepting the article for publication, acknowledges that the US government retains a nonexclusive, paid-up, irrevocable, worldwide license to publish or reproduce the published form of this manuscript, or allow others to do so, for US government purposes. DOE will provide public access to these results of federally sponsored research in accordance with the DOE Public Access Plan (http://energy.gov/downloads/doe-public-access-plan). |
|
This journal is © The Royal Society of Chemistry 2021 |
Click here to see how this site uses Cookies. View our privacy policy here.