DOI:
10.1039/D1RA06190A
(Paper)
RSC Adv., 2021,
11, 34235-34244
Comparative study on interfacial and foaming properties of glycolipids in relation to the gas applied for foam generation†
Received
16th August 2021
, Accepted 14th October 2021
First published on 21st October 2021
Abstract
Glycolipids are biosurfactants with a wide range of structural diversity. They are biodegradable, based on renewables, ecocompatible and exhibit high surface activity. Still, studies comparing glycolipids and conventional surfactants in terms of interfacial properties and foaming performance are lacking. Here, we compared interfacial and foaming properties of microbial and enzymatically synthesized glycolipids to those of the widely-used, conventional surfactant sodium dodecyl sulfate (SDS). The enzymatically produced sorbose monodecanoate, as well as microbially produced di-rhamno-di-lipids exhibited high foam stabilizing properties, similar to those of SDS. However, sophorolipid and mono-rhamno-di-lipids did not produce metastable foams. An appropriate selection of head and tail groups depending on the application of interest is therefore necessary. Then, glycolipids can serve as an ecofriendly and efficient alternative to petroleum-based surfactants, even at substantially lower concentrations than e.g. SDS. Moreover, the influence of three foaming gases on the foaming properties of the glycolipids was evaluated. Slightly higher foam stability and lower coarsening rates were determined for sorbose monodecanoate when using nitrogen as the foaming gas instead of air. Foams generated with carbon dioxide were not metastable, no matter which surfactant was used.
Introduction
Surfactants are amphiphilic molecules with a wide range of applications in industry and in everyday-life, e.g. in petrochemistry, in cosmetics, in agriculture, in paints, coatings and detergents, as well as in the food industry.1–3 Biosurfactants are gaining interest due to growing environmental awareness and the depletion of fossil resources. Glycolipids are a class of biosurfactants containing a sugar moiety and a fatty acid or fatty alcohol moiety. They can be produced based on renewables either by fermentation or by enzymatic synthesis, moreover they are biodegradable and non-toxic.4–10 However, not only the production and environmental burden must be considered when selecting alternative surfactants, but also their properties compared to conventional ones. In recent studies glycolipids exhibited high potential as emulsion and foam stabilizing agents but comparisons of their properties with conventional surfactants are still lacking.11,12 Critical micelle concentration (CMC), dynamic interfacial tension, dilatational interfacial elasticity and dilatational interfacial viscosity are parameters of interest for characterizing interfacial properties as they are correlated with stabilizing effects on disperse systems.13–18
Foams are thermodynamically unstable systems with applications in various fields e.g. in detergents, cosmetics, foods, pharmaceuticals, agriculture, fire-fighting, oil recovery or wastewater treatment.19–24 The demands on foamed products are just as diverse as their fields of application, but foam stability is one of the key parameters. While low foaming is desirable in detergents for washing machines, foaming is an important criterion for hand laundry detergents and shampoos due to consumer acceptance. For cosmetics, pharmaceuticals and foods high foam stability with narrow bubble size distribution is desired to achieve a homogeneous product with the expected perception properties and high storage stability.19,20,22
Surfactants are applied for stabilizing the dispersion of bubbles in a solution by lowering interfacial tension and by reducing aggregation and coarsening.13–15,23–25 However, foam stabilization mechanisms are strongly related to the surfactant used.13,15,24 Reported results of different laboratories may not be comparable as foaming properties are highly dependent on the experimental set-up, as well as the employed measurement protocols, and as disparities are observed between the different methods used.26,27
In this study we compared two microbial glycolipids and an enzymatically synthetized glycolipid with the conventional surfactant sodium dodecylsulfate (SDS) in regard to interfacial and foaming properties. The structural formulae of the investigated molecules are depicted in Fig. 1. SDS was chosen as reference surfactant because it exhibits high foaming power and produces metastable foams.28 As microbial surfactants, sophorolipid and a commercial rhamnolipid product, Rhapynal V3 800 were selected. Rhapynal V3 800 contains two different rhamnolipids that were further separated by flash chromatography in two fractions (mono-rhamno-di-lipids, R1, and di-rhamno-di-lipids, R3). Sorbose monodecanoate was chosen as a model of enzymatically derived glycolipid because it showed promising results in a previous study dealing with high foaming properties at low surfactant concentrations.11 Foaming properties were evaluated using three different gases for foam generation, air, nitrogen and carbon dioxide, in order to analyze their influence. Nitrogen was chosen as it exhibits low solubility in water which is beneficial for foam stability and low coarsening rates.29 Air was selected as second foaming gas due to ubiquitous availability and low price. Carbon dioxide was chosen because of its industrial relevance.
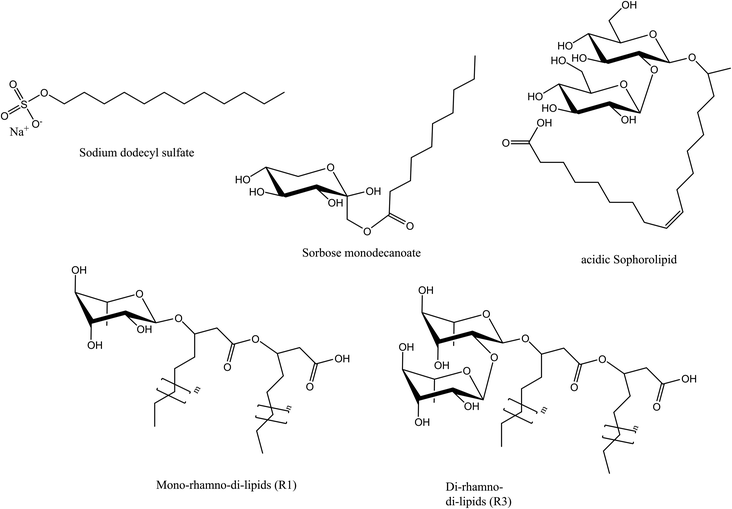 |
| Fig. 1 Structures of the investigated glycolipids. Rhamnolipids were purified from the commercial Rhapynal V3 800, chain length of the β-hydroxyfatty acids is 8 to 14 carbon with 1 ≤ m,n ≤ 7. Sorbose monodecanoate was synthesized enzymatically. | |
The aim of the study was to evaluate interfacial and foaming properties of glycolipids compared to SDS in order to assess whether they represent suitable, green alternatives to conventional surfactants in terms of foam formation and application.
Experimental
Materials
Lipase B from Candida antarctica, immobilized on acrylic resin (iCalB) was acquired from Strem Chemicals (Strem chemicals Europe, Germany). Vinyl decanoic acid was purchased from Tokyo Chemical Industry Co., Ltd. (TCI Europe, Belgium). Celite 545 sodium dodecyl sulfate and solvents (HPLC grade) were acquired from Carl-Roth GmbH & Co. KG (Germany). Sorbose was graciously gifted from Givaudan (France). 6-Decanoyl-D-glucose was purchased from Sohena GmbH (Germany). Rhapynal V3 800 was kindly provided by Biotensidon GmbH (Germany). Acidic, non-acetylated Sophorolipid were acquired from Biosynth s.r.o. (Slovakia).
Synthesis of sorbose monodecanoate
Sorbose monodecanoate was synthesized according to Hollenbach et al.11 Briefly, 0.5 M sorbose, 0.5 M vinyldecanoate and 10 mg mL−1 iCalB were mixed in a 250 mL round bottom flask in 100 mL acetone at 50 °C and 600 rpm in a Laborota 4000 rotatory evaporator (Heidolph, Germany) at atmospheric pressure for 48 h.
Then, the obtained reaction mixture was filtrated with a Büchner funnel and the filtrate was washed three times with ethyl acetate. The glycolipid containing solvent was mixed with Celite 545 in a ratio of 1
:
3 (w/w) and the solvent was subsequently evaporated with a rotatory evaporator at 40 °C and 240 mbar. Solids were purified by flash chromatography using a Reveleris Prep® system from Büchi Labortechnik GmBH (Essen, Germany) and a Flash Pure Silica® column (40 g, 53–80 Å) using solid loading. Mobile phase consisted of chloroform (C) and methanol (M). A gradient was used to separate sorbose monodecanoate and residual substrates: starting from 100% C a linear gradient was applied to 96% C and 4% M within 2 min. This ratio was maintained for 9 min, followed by another linear gradient to 90% C and 10% M within 2 min. After maintaining this ratio for 6 min, a linear gradient to 75% C and 25% M within 2 min was applied and this ratio was hold for 4 min followed by a linear gradient to 100% M in 2 min and the latter was hold for 6 min. Peaks were collected and fractions controlled by TLC. Glycolipid containing fractions were collected and solvents were again evaporated with a S-Concentrator BaVC-300H from Helmut Saur Laborbedarf (Germany). The purity of sorbose monodecanoate was determined by HPLC-ELSD.
Flash chromatography of Rhapynal V3 800
Rhapynal V3 800 was dissolved in chloroform
:
methanol (2
:
1, v/v) and subsequently absorbed on a diatomaceous matrix (Rhapynal
:
Celite 545, 1
:
3) for further solid loading onto the flash chromatography. The obtained solid was purified using flash chromatography. For the purification of Rhapynal V3 800 a mobile phase of chloroform (C) and methanol (M) was used. The program started with an isocratic phase of 100% C for 3 min. Afterwards a linear gradient to 92% C was applied over 3 min, followed by a linear gradient to 90% C in 4.5 min, then up to 82% C in 3.6 min and further to 74% C in 4.5 min. Finally, a step gradient to 100% M was applied which was held for 3.5 min. Mono-rhamno-di-lipids (R1) eluated between 9-12 min and di-rhamno-di-lipids (R3) between 20–24 min. Peaks were collected and checked for rhamnolipids by TLC-analysis.
Thin layer chromatography (TLC)
For TLC analysis 5 μl of samples were spotted on Alugram® Xtra SIL G plates from Machery-Nagel (Düren, Germany). A mobile phase consisting of chloroform
:
methanol
:
acetic acid (65
:
15
:
2, v/v/v) was applied for elution. Compounds were visualized by anisaldehyde dying (anisaldehyde
:
sulfuric acid
:
acetic acid 0.5
:
1
:
100, by vol). A Jeneil JBR 425 standard (Saukville, Wisconsin, USA) was applied as a reference substance for the identification of the samples.
HPLC-ELSD
Glycolipids were quantified by reversed-phase chromatography using a Kinetex EVO C18 (2.6 μm, 250 × 4.6 mm) column from Phenomenex (Aschaffenburg, Germany) with an accompanying guard column (4 × 3.0 mm ID) of the same phase and an Agilent (Germany) 1260 series liquid chromatograph equipped with a quaternary pump, an autosampler and a column oven. HPLC analysis was performed according to Hollenbach et al. (2020)(11). Briefly, an evaporative light scattering detector from BÜCHI Labortechnik (Essen, Germany) was used for detection. Mobile phase was a gradient of acetonitrile and water with a total flow rate of 1 mL min−1.
Determination of interfacial tension and critical micelle concentration
Interfacial tension was determined by Du Noüy-ring method using a Lauda Tensiometer TD1 (Germany). The tensiometer was prepared by calibration with a 500 mg calibration weight. A test vessel was filled with at least 2 mL glycolipid solution and placed on the stage of the tensiometer and a Du Noüy ring (19.1 mm diameter) was submerged at least 2–3 mm below the solution surface and equilibration time of 15 min was applied. Then, the measurement was started by lowering the stage manually. The maximum normal force before the lamella formed between ring and solution breaks is the uncorrected interfacial tension σunc. The absolute interfacial tension σabs is obtained by multiplying σunc with a correction factor f. The correction factor f for the used ring was calculated as follows:30,31 |
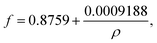 | (1) |
where ρ is the density of the test liquid.
Dynamic interfacial tension and interfacial rheology measurements
The dynamic interfacial tension and interfacial viscoelasticity of all solutions were determined using a pendant drop tensiometer (PAT1, Sintaface, Berlin, Germany). The interfacial tension was calculated from the drop shape over a period of 10
000 seconds maintaining a constant surface area of 20 mm2. Drops were produced from a cannula with 1 mm diameter.
The interfacial tension, interfacial viscosity, and interfacial elasticity were determined as described in Loglio et al. (2011) from oscillatory dilation experiments with frequencies of 0.05, 0.1, 0.33, 0.5 and 0.67 Hz.32 The surface area of the drop was then sinusoidally dilated with an amplitude of 2 mm2 for at least 10 oscillations, followed by an oscillation pause at a constant surface area of 15 min.
Foam generation
For foam generation 16 mL of surfactant solution (concentration = 2 × CMC) were filled into a 50 mL VitaPor suction filter funnel (Por.4, 10–16 μm) from ROBU Glasgeräte GmbH (Hattert, Germany). Foam formation was initiated by a gas flow of 60 mL min−1 through the funnel outlet. Either nitrogen, air or carbon dioxide were applied as gases. Gas flow was stopped at a foam height of 5.3 cm and the measurements were started.
Foam height measurements
Foam height was measured over a period of 60 min. From these measurements, the foam stability was calculated using the parameters r5 and r60: |
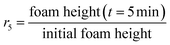 | (2) |
|
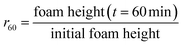 | (3) |
Bubble size distribution measurements
Bubble sizes were analyzed according to Völp et al. (2020)33 using a VHX-950F microscope equipped with a VH-B55 endoscope both supplied by Keyence Deutschland GmbH (Germany). A KL 1500 LCD goose neck lamp from Schott AG (Germany) was used for illumination. The endoscope was equipped with a 90° angle mirror tube and inserted into a customized optical glass cuvette. Pictures were taken every 15 s over a period of 10 min at a height of 22 mm above the filter. The endoscopic pictures were evaluated using a software tool written in Matlab® (MathWorks®, Natick, MA, USA) based on a template matching method as described by Völp et al. (2020).33
Coarsening rate Ω was determined according to Briceño-Ahumada et al. (2017) from the slope of square Sauter diameter versus time plots
.13
Determination of gas volume fractions
The gas volume fraction φ was determined based on conductivity measurement performed using a SevenCompact conductivity meter equipped with an Inlab® 738 ISM four-electrode conductivity sensor from Mettler-Toledo (Switzerland). The sensor was placed 22 mm above the filter membrane. The conductivity of the surfactant solution (before foaming) and foam conductivity (every 15 s over a period of 10 min) was measured. The relative conductivity κrel was calculated by: |
 | (4) |
where κfoam is the conductivity of the foam and κsolution is the conductivity of the surfactant solution.
The gas volume fraction φ was calculated as described by Feitosa et al. (2005):34
|
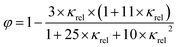 | (5) |
Statistical analysis
Results are given as mean ± standard deviation. Statistical data analysis was performed by ANOVA and Tukey test using the OriginPro 9.6 (version 2019, OriginLab, Nothampton, MA, USA) software. Results were considered significant if p-value was <0.05.
Results
In this study two microbial glycolipids, rhamnolipids and sophorolipid, and an enzymatically synthesized glycolipid, sorbose monodecanoate, were compared with the anionic surfactant SDS. In the case of rhamnolipids, the commercially available rhamnolipid mixture Rhapynal V3 800 and two purified fractions of it were tested. TLC analysis of Rhapynal V3 800 revealed that it consists of two rhamnolipids: R1 and R3 (Table 1), therefore it was separated by flash chromatography in the R1 containing fraction A and the R3 containing fraction B. R1 and R3 were obtained in a ratio of 1/5 (w/w) after purification. Interfacial and foaming properties of all surfactants were investigated.
Table 1 Thin layer chromatography of rhamnolipid samples
Rhamnolipid sample |
Rf |
Rhamnolipid typea |
According to Arino et al. (1996), Syldatk et al. (1985); Amani et al. (2015)35–37 Rf retention factor. |
Jeneil standard |
0.83 |
Mono-rhamno-di-lipids (R1) |
0.66 |
Mono-rhamno-mono-lipids (R2) |
0.46 |
Di-rhamno-di-lipids (R3) |
0.22 |
Di-rhamno-mono-lipids (R4) |
Rhapynal V3 800 |
0.83 |
Mono-rhamno-di-lipids (R1) |
0.46 |
Di-rhamno-di-lipids (R3) |
Rhapynal fraction A |
0.83 |
Mono-rhamno-di-lipids (R1) |
Rhapynal fraction B |
0.46 |
Di-rhamno-di-lipids (R3) |
Interfacial properties
Critical micelle concentration, dynamic interfacial tension, dilatational interfacial elasticity and dilatational interfacial viscosity were determined to characterize interfacial properties. Critical micelle concentration was determined in order to identify a suitable concentration for foaming experiments. Dynamic interfacial tension was earlier identified as crucial parameter for foam stabilization by glycolipids and non-ionic surfactants.11,18
Results of interfacial tension measurements are summarized in Table 2. CMC of all investigated glycolipids were considerably lower than for SDS. Interfacial tension of the investigated surfactants varied between 26–34 mN m−1. All investigated surfactants lowered the interfacial tension to at least 35 mN m−1 within 5 s or less (ESI Fig. S1†).
Table 2 Interfacial properties of investigated surfactants
Surfactant |
CMC |
Interfacial tensiona |
Concentration (surfactant) = 2CMC |
SDS |
2.35 g L−1 |
32.7 ± 0.1 mN m−1 |
Sorbose monodecanoate |
0.325 g L−1 |
25.7 ± 0.2 mN m−1 |
Rhapynal (not fractionated) |
0.35g L−1 |
29.0 ± 0.7 mN m−1 |
R1 |
0.05g L−1 |
26.5 ± 0.1 mN m−1 |
R3 |
0.125g L−1 |
34.2 ± 0.7 mN m−1 |
Sophorolipid |
0.23 g L−1 |
34.0 ± 0.1 mN m−1 |
Interfacial rheology of surfactants was investigated as foam stability and destabilization mechanisms are correlated with interfacial elasticity and interfacial viscosity. Higher interfacial elasticity and interfacial viscosity are reported to result in higher resistance of foams against foam rupture and coarsening and therefore slowdown foam decay.13–17
Sophorolipid and SDS exhibited the lowest dilatational interfacial elasticities of the investigated surfactants (Fig. 2). Concerning the rhamnolipids, interfacial elasticity of commercial Rhapynal V3 800 (9.4 ± 0.9 mN m−1; 0.67 Hz) is lower than that of both separated rhamnolipid fractions with R1 (56.9 ± 0.4 mN m−1; 0.67 Hz) exhibiting highest interfacial elasticity. Evaluation of dilatational interfacial viscosities revealed similar findings. R1 showed highest dilatational interfacial viscosity of 6.2 ± 0.1 mN s m−1 (0.67 Hz) while the dilatational interfacial viscosities of SDS, sorbose monodecanoate, sophorolipid and Rhapynal V3 800 exhibited no significant differences for high frequencies (0.6–1.2 mN s m−1; 0.67 Hz).
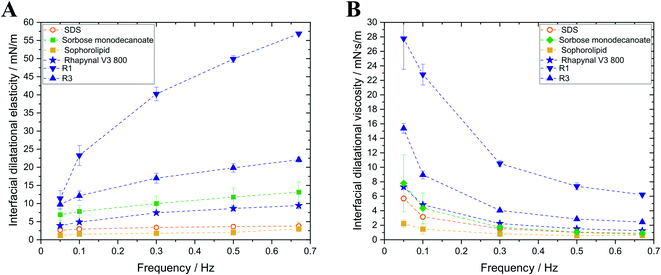 |
| Fig. 2 Interfacial rheological properties of investigated surfactants. (A) shows interfacial dilatational elasticity, (B) shows interfacial dilatational viscosity. R1 exhibits highest dilatational interfacial elasticity and viscosity while dilatational interfacial viscosity of the other investigated surfactants was similar. | |
Foam stability
Foam stability is an important parameter in designing foamed commercial products. The requirements for foam stability can vary considerably depending on the field of application.19,20
Foams made of sorbose monodecanoate solution and SDS solution showed highest transient foam heights while foam height of sophorolipid solutions decreased sharply with time (Fig. 3). For R3, more stable foams were observed than for the commercial Rhapynal V3 800. In contrast, foams stabilized by R1 were highly unstable and exhibited also lower foaminess as the initial foam height of 5.3 cm could not be reached despite its high interfacial elasticity.
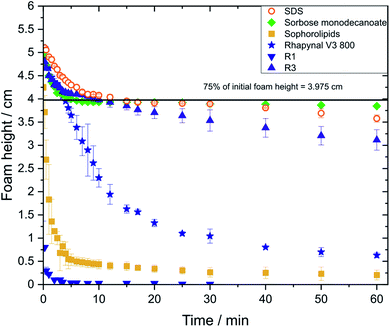 |
| Fig. 3 Transient foam height of investigated surfactant solutions over time (foams prepared with nitrogen). Initial foam height was 5.3 cm. Foams stabilized by SDS, sorbose monodecanoate and R3 showed most stable foams while R1 and sophorolipid were weak in stabilizing foams. | |
Comparing the foaming properties depending on the gas used for foam formation, only for sorbose monodecanoate solutions foam stability r60 was higher using nitrogen in comparison to using air while for the other investigated glycolipids both gases are merely the same (Table 3). With carbon dioxide, significantly lower foam stabilities were achieved for all 6 tested surfactants in comparison with the other two gases (ESI Fig. S2†). The r5 value with carbon dioxide was below 0.5 for all surfactants investigated. When using carbon dioxide, no foam could be generated with R1, sophorolipid exhibited lower foaminess and the obtained foams collapsed within less than 5 min.
Table 3 Foam stability parameters r5 and r60, as well as time where drainage-controlled foam decay ends tDEV
Surfactant |
Gas |
r5 |
r60 |
tDEV |
r60 of sorbose monodecanoate shows significant difference between nitrogen and air. |
SDS |
N2 |
0.81 ± 0.00 |
0.68 ± 0.01 |
20 min |
Air |
0.81 ± 0.00 |
0.65 ± 0.02 |
20 min |
CO2 |
0.41 ± 0.02 |
0.10 ± 0.03 |
|
Sorbose monodecanoate |
N2 |
0.75 ± 0.00 |
0.73 ± 0.00a |
>60 min |
Air |
0.75 ± 0.02 |
0.69 ± 0.01 |
40 min |
CO2 |
0.19 ± 0.01 |
0.14 ± 0.01 |
|
Rhapynal |
N2 |
0.69 ± 0.03 |
0.12 ± 0.01 |
2 min |
Air |
0.73 ± 0.01 |
0.13 ± 0.03 |
2 min |
CO2 |
0.18 ± 0.03 |
0.08 ± 0.00 |
|
R3 |
N2 |
0.78 ± 0.00 |
0.59 ± 0.04 |
12 min |
Air |
0.77 ± 0.00 |
0.59 ± 0.02 |
12 min |
CO2 |
0.24 ± 0.02 |
0.17 ± 0.03 |
|
R1 |
N2 |
0.01 ± 0.00 |
|
|
Air |
0.002 ± 0.00 |
|
|
CO2 |
— |
— |
|
Sophorolipid |
N2 |
0.10 ± 0.02 |
0.04 ± 0.02 |
|
Air |
0.11 ± 0.04 |
0.04 ± 0.01 |
|
CO2 |
— |
— |
|
Regarding the phases of foam decay, the initial drainage-controlled foam decay, as characterized by a ratio of 1 for change in foam height to change in solution height,23 is substantially longer for sorbose monodecanoate than for the other investigated glycolipids. The drainage-driven foam decay was longer for R3 (12 min) than for of Rhapynal (2 min). No drainage-controlled phase could be observed for foams made of R1 and sophorolipid solutions which collapsed almost completely within 5 min.
Concerning the investigated gases, a longer drainage-driven phase with nitrogen than with air was only observed for sorbose monodecanoate. For carbon dioxide, no drainage-controlled foam decay was observed with any of the surfactants investigated.
Bubble size distribution
Bubble size distribution is known to effect quality of foamed products by influencing perception properties, foam texture and flow, as well as storage stability.21,22
Determination of bubble size distribution was only possible for SDS, Rhapynal, R3 and sorbose monodecanoate due to the low foam stability of foams produced with sophorolipid and R1.
Foam stabilized by SDS, sorbose monodecanoate (using nitrogen) and R3 (using nitrogen) showed similar coarsening rates (Ω = 0.007–0.009 μm2 s−1), while coarsening rates using air for sorbose monodecanoate and R3 were higher and like the coarsening rates of foams from Rhapynal solutions (Ω = 0.014–0.017 μm2 min−1) (Table 4). Coarsening rates of foams made of SDS and Rhapynal solutions exhibited no differences between the two foaming gases, air and nitrogen (ESI Fig, S3†).
Table 4 Parameters of bubble size distribution in relation to the gas used for foam generation
Surfactant |
Gas |
Coarsening rate Ω |
Q3Span (0.25 min) |
Q3Span (10 min) |
Q3Span of SDS at 0.25 min is significantly smaller than all the other Q3Span measured. |
SDS |
N2 |
0.007 |
0.41 ± 0.06a |
0.86 ± 0.07 |
Air |
0.007 |
0.38 ± 0.05a |
1.10 ± 0.26 |
Sorbose monodecanoate |
N2 |
0.008 |
0.89 ± 0.08 |
0.81 ± 0.12 |
Air |
0.017 |
1.30 ± 0.17 |
1.10 ± 0.13 |
Rhapynal |
N2 |
0.014 |
1.12 ± 0.09 |
1.07 ± 0.13 |
Air |
0.014 |
1.35 ± 0.27 |
1.16 ± 0.22 |
R3 |
N2 |
0.008 |
0.91 ± 0.10 |
1.08 ± 0.09 |
Air |
0.015 |
1.01 ± 0.18 |
1.15 ± 0.20 |
Initial bubble size was significantly higher for foams generated with carbon dioxide compared to those generated with nitrogen or air regardless of the surfactant used (ESI Fig. S4†).
The width of the cumulative volumetric bubble size distribution Q3 is described by the span
. Initial Q3Span determined at 0.25 min is significantly lower for foams made from SDS solutions than for the other investigated surfactants. There is a significant difference in the Q3Span between 0.25 min and 10 min for SDS. However, no changes in Q3Span over time were observed for the other surfactants. Furthermore, for all the investigated surfactants Q3Span was the same no matter whether the foams were generated with air or nitrogen. With carbon dioxide no metastable foams were obtained and therefore Q3 could not be determined.
Gas volume fraction
The gas volume fraction has a strong impact on the flow behaviour and perception properties of foamed products.21,22 Conductivity measurements were only possible for the metastable foams and revealed no differences in gas volume fraction between foams generated with air and nitrogen. As with carbon dioxide no metastable foams were achieved, gas volume fractions could not be determined. The initial gas volume fraction of SDS (0.73 ± 0.01 with nitrogen; 0.74 ± 0.01 with air) was lower than that of the biosurfactant foams, while the sorbose monodecanoate foam (0.87 ± 0.01 with nitrogen; 0.90 ± 0.00 with air) had the highest initial gas volume fraction (Fig. 4). However, for all biosurfactant foams the gas volume fraction reaches values of 0.92–0.94 within 4 min, while it took about 8 min for the SDS foams to reach that level.
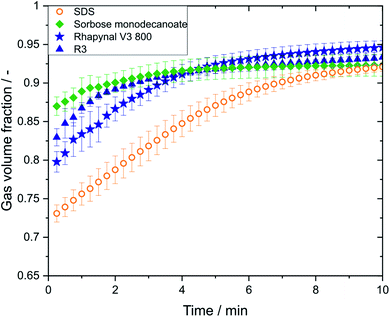 |
| Fig. 4 Gas volume fraction over time of foams generated with nitrogen. SDS foams showed the lowest initial gas volume fraction while sorbose monodecanoate foams exhibited the highest initial gas volume fraction. No stable foams could be produced with sophorolipid and R1. The gas volume fractions of the different foams approached each other with time. | |
Discussion
Foams are classified into metastable foams and foams of low stability by the parameter r5,38 which indicates the foam height after 5 min compared to the initial foam height. Foams made of sophorolipid and Rhapynal fraction R1 exhibit r5 values of less than 0.5 and are therefore of low stability. SDS, sorbose monodecanoate, Rhapynal and Rhapynal fraction R3 foams are classified as metastable instead. All foams generated with carbon dioxide are classified as nonstable as r5 <0.5.
r5 values of 0.8 were reported in literature for SDS28,38 which is in good accordance with our measured value of 0.81.
Sophorolipid is classified as weak foaming agent, foams even when made from solutions concentrations up to 100times their CMC.4 The determined r5 of sophorolipid is 0.1 and the r60 is 0.04 which confirms their poor foaming properties. Still, R1 exhibited even lower foam stability and foaminess than sophorolipid. In contrast, R3 stabilizes foams more effectively than R1 and exhibits r5 and r60 values close to those found for SDS foams. In literature, foam half-life times, i.e. the time when foam height drops to half of its initial value, of 17–35 min are reported for 0.5–1.5% solutions of rhamnolipid mixtures.39 Half-life time of foams made of R3 solutions were longer than 60 min and for foams of Rhapynal a half-life time of 10 min was determined. The differences in our measured foam half-life times and those reported in literature are due to different compositions of rhamnolipid samples and different concentrations. A higher CMC value was determined for Rhapynal than for the two purified rhamnolipids R1 and R3. This is related to the presence of other components in the commercial formulation. CMC of rhamnolipids is reported to decrease with increasing purity of the samples.40
Rhamnolipids cover a wide range of hydrophilic–lipophilic balance (HLB) with R3 being highly hydrophilic and R1 being the least hydrophilic rhamnolipids. HLB is reported to have a significant effect on surfactant properties, e.g. CMC values or emulsification, detergent properties and foaming behaviour.40,41 R1 with its lower HLB exhibits weak foamability and lower foam stability than the more hydrophilic R3 and sorbose monodecanoate. High HLB values were also previously reported to correlate with higher foamability and foam stability.42,43 However, the weakly foaming sophorolipid has a similar HLB to sorbose monodecanoate. A characteristic of the sophorolipid, though, is the double bond in the fatty acid chain. Unsaturation was previously shown to reduce the foam stabilizing properties of glycolipids.11 The double bond causes a change in the molecular geometry of the fatty acid chain and thus van der Waals interactions between the tails are weaker than for the saturated glycolipids Therefore, the alkene in the lipophilic group of the sophorolipid is an explanation for the reduced foamability compared to sorbose monodecanoate solutions despite similar HLB.
In the first couple of minutes of foam decay, foams made of SDS, sorbose monodecanoate, Rhapynal V3 800 and R3 show a similar behaviour. This phase is characterized by rapid foam drainage. No differences between these four surfactants were observed in this regime as herein drainage is not controlled by stabilizing effects of different surfactants due to the high thickness of the foam lamella.38 Afterwards, stabilizing effects of surfactants start to play a role and the pattern of foam decay differs significantly between the different surfactants. However, the typical pattern of rapid foam drainage could not be observed for foams from sophorolipid and R1 solutions, most likely because these foams are so unstable that rupture of lamellae already starts during foam formation. Foam decay is characterised by three phases: the drainage driven phase 1, phase 2, where drainage and rupture coexist, and phase 3, where foam film rupture is the controlling mechanism.23 In the case of R1 and sophorolipid, where phase 1 did not exist, phase 3 started already at early foam ages as the drained solution height remained constant.
Interfacial rheological properties, i.e. interfacial elasticity and interfacial viscosity, affect rupture of foam lamellae and therefore foam stability.13,14,16,17 However, no correlation between interfacial rheological properties and foam stability, coarsening rates or the time of drainage-controlled foam decay could be observed in this study. Indeed, sophorolipid showed the lowest values for interfacial elasticity and interfacial viscosity and had low foam stabilizing properties. However, sorbose monodecanoate, showing 5times higher interfacial elasticity than sophorolipid, exhibited high foam stability and the longest time of drainage-controlled foam decay albeit low interfacial viscosity. Moreover, R1 showed low foam stabilizing effects even though it has the highest interfacial elasticity and the highest interfacial viscosity of the investigated surfactants. In another investigation, it was already reported that foaming properties of enzymatically produced glycolipids cannot be directly correlated to interfacial rheological parameters.11 In this study, we observed slightly lower interfacial elasticity (13.2 ± 2.9 mN m−1 at 0.67 Hz) for sorbose monodecanoate than previously reported in literature (16.4 ± 0.05 mN m−1) which is most likely due to higher purity (98.5% vs. 96.4% in the previous study). Also interfacial viscosity was slightly lower for low frequencies but with increasing frequency interfacial viscosity gets similar to the ones previously reported.
Different gases are known to influence foams. Diffusivity and solubility of gases differ and have an impact on coarsening and foam stability.29,44–47 In this study, we investigated the effect of pure nitrogen, carbon dioxide and the gas mixture air on foam stability, coarsening rates, and bubble size distribution of different glycolipids and SDS. Foams generated with carbon dioxide showed much lower stability and bigger bubble sizes. This is due to the higher diffusivity and solubility of carbon dioxide in water and in good accordance to literature.29,46,47 Moreover, carbon dioxide is reported to cause hydrolysis of SDS at the surface.45,48 Similar effects of carbon dioxide may occur with glycolipids. Therefore, carbon dioxide is no suitable foaming gas for glycolipids and SDS in order to obtain metastable foams.
For sorbose monodecanoate and R3 coarsening rates of foams generated with nitrogen were smaller than the ones generated with air. However, no differences in the coarsening rates for foams made of Rhapynal and SDS were observed. Foam stability and drainage-controlled foam decay also showed different influences of the foaming gases depending on the surfactants applied. For these parameters, a difference between the foaming gases air and nitrogen was only found for sorbose monodecanoate. These results indicate that the surfactant type influences the role of the foaming gas. Surfactants producing an ordered interfacial surfactant layer are reported to show less pronounced differences between foaming gases than surfactants which produce a more disordered arrangement at the interface.47 Sun et al. (2016) reported that the reduced foam stability and faster rupture of foam lamellae due to the oxygen present in air could be reduced by increasing the concentration of SDS.47 This explains the similar behaviour of SDS foams generated with nitrogen and air as we applied SDS concentrations of twice the CMC in our study.
The results of this investigation indicate that certain glycolipids exhibit similar foamability and foam stabilizing properties as conventional surfactants. Foams made from sorbose monodecanoate solutions showed similar foam stability and coarsening rates as foams made from the conventional surfactant SDS which is known for its good foaming power and for producing metastable foams.28 R3 solutions also produced metastable foams at similar coarsening rates as observed for SDS and sorbose monodecanoate, whereas the other two microbial glycolipids, R1 and sophorolipid, did not yield stable foams.
Conclusions
The aim of this study was to investigate the interfacial and foaming properties of glycolipids in comparison to the conventional surfactant SDS.
Sorbose monodecanoate, an enzymatically synthesized glycolipid, and the microbially produced R3, produced highly stable foams while sophorolipid and R1 showed poor foam stabilization. Sorbose monodecanoate exhibited similar foaming properties as the widely used conventional SDS indicating that glycolipids are competitive in foam stabilizing to conventional surfactants. Moreover, sorbose monodecanoate was more efficient in foam stabilization than SDS as substantially lower molar concentrations were applied.
Consequently, glycolipids present an ecofriendly and efficient alternative to petroleum-based surfactants for foam stabilization if the head and tail groups are chosen appropriately.
Funding
This work by R. H. was supported by the European Regional Development Fund and the Ministry of Science, Research and the Arts of the State of Baden-Württemberg within the research center ZAFH InSeL (Grant#32-7545.24-20/6/3). A. V. was supported by Deutsche Forschungsgemeinschaft (grant WI 3138/29-1). We gratefully thank the Open Access Publishing Fund of Karlsruhe Institute of Technology.
Author contributions
Conceptualization, R. H.; methodology, R. H. and A. V.; formal analysis, R. H.; investigation, R. H., S. O., A. D.; writing—original draft preparation, R. H.; writing—review and editing, R. H., A. D., A. V., J. R., K. O., N. W. and C. S.; supervision, N. W. and C. S.; funding acquisition, N. W. and C. S. All authors have read and agreed to the published version of the manuscript.
Conflicts of interest
There are no conflicts to declare.
Acknowledgements
The authors gratefully acknowledge Biotensidon (Germany, Karlsruhe) for the kind gift of Raphynal V3 800 and Givaudan (France) for providing sorbose. Furthermore, the authors kindly acknowledge the group of Prof. H. Karbstein (Institute of Process Engineering in Life Sciences I: Food Process Engineering, Karlsruhe Institute of Technology, Germany) for support with the pendant drop tensiometer for the interfacial dilatational experiments.
Notes and references
- A. M. Shete, G. Wadhawa, I. M. Banat and B. A. Chopade, Mapping of patents on bioemulsifier and biosurfactant: A review, J. Sci. Ind. Res., 2006, 65(2), 91–115 Search PubMed.
- D. R. Perinelli, S. Lucarini, L. Fagioli, R. Campana, D. Vllasaliu and A. Duranti, et al., Lactose oleate as new biocompatible surfactant for pharmaceutical applications, Eur. J. Pharm. Biopharm., 2018, 124(124), 55–62 CrossRef CAS PubMed.
- M. Younes, P. Aggett, F. Aguilar, R. Crebelli, B. Dusemund and M. Filipič, et al., Refined exposure assessment of sucrose esters of fatty acids (E 473) from its use as a food additive, EFSA J., 2018, 16(1), 1–22 Search PubMed.
- Y. Hirata, M. Ryu, Y. Oda, K. Igarashi, A. Nagatsuka and T. Furuta, et al., Novel characteristics of sophorolipids, yeast glycolipid biosurfactants, as biodegradable low-foaming surfactants, J. Biosci. Bioeng. [Internet], 2009, 108(2), 142–146, DOI:10.1016/j.jbiosc.2009.03.012.
- T. M. S. Lima, L. C. Procópio, F. D. Brandão, A. M. X. Carvalho, M. R. Tótola and A. C. Borges, Biodegradability of bacterial surfactants, Biodegradation, 2011, 22(3), 585–592 CrossRef CAS PubMed.
- J. Grüninger, A. Delavault and K. Ochsenreither, Enzymatic glycolipid surfactant synthesis from renewables, Process Biochem., 2019, 87, 45–54 CrossRef.
- J. Dörjes, Experimentelle Untersuchungen zur Wirkung von Rohöl und Rohöl/Tensid-Gemischen im Ökosystem Wattenmeer. XVI. Zusammenfassung und Schlußfolgerungen. Senckenbergiana maritima, Int. J. Mar. Sci., 1984, 16, 267–271 Search PubMed.
- K. Poremba, W. Gunkel, S. Lang and F. Wagner, Toxicity testing of synthetic and biogenic surfactants on marine microorganisms, Environ. Toxicol. Water Qual., 1991, 6(2), 157–163 CrossRef CAS.
- S. Johann, T. B. Seiler, T. Tiso, K. Bluhm, L. M. Blank and H. Hollert, Mechanism-specific and whole-organism ecotoxicity of mono-rhamnolipids, Sci. Total Environ., 2016, 548–549, DOI:10.1016/j.scitotenv.2016.01.066.
- I. J. A. Baker, B. Matthews, H. Suares, I. Krodkiewska, D. N. Furlong and F. Grieser, et al., Sugar fatty acid ester surfactants: Structure and ultimate aerobic biodegradability, J. Surfactants Deterg., 2000, 3(1), 1–11 CrossRef CAS.
- R. Hollenbach, A. R. Völp, L. Höfert, J. Rudat, K. Ochsenreither and N. Willenbacher, et al., Interfacial and Foaming Properties of Tailor-Made Glycolipids—Influence of the Hydrophilic Head Group and Functional Groups in the Hydrophobic Tail, Molecules, 2020, 25(17), 3797 CrossRef CAS PubMed.
- S. Ji, C. Jia, D. Cao, S. Li and X. Zhang, Direct and selective enzymatic synthesis of trehalose unsaturated fatty acid diesters and evaluation of foaming and emulsifying properties, Enzyme Microb Technol, 2020, p. 136, November 2019: 109516, available from: DOI : DOI:10.1016/j.enzmictec.2020.109516.
- Z. Briceño-Ahumada and D. Langevin, On the influence of surfactant on the coarsening of aqueous foams, Adv. Colloid Interface Sci., 2017, 244, 124–131 CrossRef PubMed.
- H. Fruhner, K. D. Wantke and K. Lunkenheimer, Relationship between surface dilational properties and foam stability, Colloids Surf., A, 2000, 162(1–3), 193–202 CrossRef CAS.
- D. Beneventi, B. Carre and A. Gandini, Properties, 2001, 189, 65–73 CrossRef CAS.
- J. L. Joye, G. J. Hirasaki and C. A. Miller, Asymmetric Drainage in Foam Films, Langmuir, 1994, 10(9), 3174–3179 CrossRef CAS.
- J.-L. Joye, G. J. Hirasaki and C. A. Miller, Numerical simulation of instability causing asymmetric drainage in foam films, J. Colloid, 1996, 552(177), 542–552 CrossRef.
- B. Petkova, S. Tcholakova, M. Chenkova, K. Golemanov, N. Denkov and D. Thorley, et al., Foamability of aqueous solutions: Role of surfactant type and concentration, Adv. Colloid Interface Sci., 2020, 276, DOI:10.1016/j.cis.2019.102084.
- A. Bureiko, A. Trybala, N. Kovalchuk and V. Starov, Current applications of foams formed from mixed surfactant-polymer solutions, Adv Colloid Interface Sci [Internet], 2015, 222, 670–677, DOI:10.1016/j.cis.2014.10.001.
- A. P. J. Middelberg and M. Dimitrijev-Dwyer, A designed biosurfactant protein for switchable foam control, ChemPhysChem, 2011, 12(8), 1426–1429 CrossRef CAS PubMed.
- A. Barella and A. M. Manich, Bubble Size Distribution During Application of Foam to Fabrics and Its Effects on Product Quality, Text Res. J., 1996, 66(1), 59–60 CrossRef CAS.
- N. Müller-Fischer and E. J. Windhab, Influence of process parameters on microstructure of food foam whipped in a rotor-stator device within a wide static pressure range, Colloids Surf., A, 2005, 263, 353–362 CrossRef.
- K. Lunkenheimer, K. Malysa, K. Winsel, K. Geggel and S. Siegel, Novel method and parameters for testing and characterization of foam stability, Langmuir, 2010, 26(6), 3883–3888 CrossRef CAS PubMed.
- P. Kanokkarn, T. Shiina, M. Santikunaporn and S. Chavadej, Equilibrium and dynamic surface tension in relation to diffusivity and foaming properties: Effects of surfactant type and structure, Colloids Surf., A, 2017, 524, 135–142 CrossRef CAS.
- D. Georgieva, A. Cagna and D. Langevin, Link between surface elasticity and foam stability, Soft Matter, 2009, 5(10), 2063–2071 RSC.
- L. Grossmann, P. Moll, C. Reichert and J. Weiss, Influence of Energy Density on Foamability: Comparison of Three Foaming Methods, Food Res. Int., 2020, 129, 108794, DOI:10.1016/j.foodres.2019.108794.
- S. Kumar and A. Mandal, Investigation on stabilization of CO2 foam by ionic and nonionic surfactants in presence of different additives for application in enhanced oil recovery, Appl. Surf. Sci., 2017, 420, 9–20, DOI:10.1016/j.apsusc.2017.05.126.
- H. Azira, A. Tazerouti and J. P. Canselier, Study of foaming properties and effect of the iomeric distribution of some anionic surfactants, J. Surfactants Deterg., 2008, 11(4), 279–286 CrossRef CAS.
- M. Ramanathan, H.-J. Müller, H. Möhwald and R. Krastev, Foam Films as Thin Liquid Gas Separation Membranes, ACS Appl. Mater. Interfaces, 2011, 3(3), 633–637, DOI:10.1021/am101126n.
- H. W. Fox and C. H. Chrisman, The ring method of measuring surface tension for liquids of high density and low surface tension, J Phys Chem, 1952, 56(2), 284–287 CrossRef CAS.
- H. H. Zuidema and G. W. Waters, Ring Method for the Determination of Interfacial Tension, Ind. Eng. Chem., Anal. Ed., 1941, 13(5), 312–313 CrossRef CAS.
- G. Loglio, P. Pandolfini, L. Liggieri, A. Makievski and F. Ravera, Determination of interfacial properties by the pendant drop tensiometry: Optimisation of experimental and calculation procedures, Bubble Drop Interfaces, 2011, 2 Search PubMed.
- A. R. Völp, F. Fessler, J. Reiner and N. Willenbacher, High throughput object recognition and sizing in disperse systems using an image processing tool based on template matching, Chem. Eng. Technol., 2020,(9), 1–7 Search PubMed.
- K. Feitosa, S. Marze, A. Saint-Jalmes and D. J. Durian, Electrical conductivity of dispersions: From dry foams to dilute suspensions, J. Phys. Condens. Matter., 2005, 17(41), 6301–6305 CrossRef CAS.
- H. Amani, Study of enhanced oil recovery by rhamnolipids in a homogeneous 2D micromodel, J. Pet. Sci. Eng., 2015, 128, 212–219, DOI:10.1016/j.petrol.2015.02.030.
- S. Arino, R. Marchal and J. P. Vandecasteele, Identification and production of a rhamnolipidic biosurfactant by a Pseudomonas species, Appl. Microbiol. Biotechnol., 1996, 45(1–2), 162–168 CrossRef CAS.
- C. Syldatk, S. Lang and F. Wagner, Chemical and physical characterization of four interfacial-active rhamnolipids from Pseudomonas sp, Zeitschrift für Naturforschung, J. Biosci., 1985, 40(1–2), 51–60 CrossRef CAS PubMed.
- K. Lunkenheimer and K. Malysa, Simple and generally applicable method of determination and evaluation of foam properties, J. Surfactants Deterg., 2003, 6(1), 69–74 CrossRef CAS.
- S. Wang and C. N. Mulligan, Rhamnolipid foam enhanced remediation of cadmium and nickel contaminated soil, Water Air Soil Pollut., 2004, 157(1–4), 315–330 CrossRef CAS.
- I. E. Kłosowska-Chomiczewska, K. Mędrzycka, E. Hallmann, E. Karpenko, T. Pokynbroda and A. Macierzanka, et al., Rhamnolipid CMC prediction, J. Colloid Interface Sci., 2017, 488, 10–19 CrossRef PubMed.
- W. C. Griffin, Classification of surface-active agents by “HLB”, J. Soc. Cosmet. Chem., 1949, 1(5), 311–326 Search PubMed . Available from: http://journal.scconline.org//pdf/cc1949/cc001n05/p00311-p00326.pdf.
- K. Theander and R. J. Pugh, Synergism and foaming properties in mixed nonionic/fatty acid soap surfactant systems, J. Colloid Interface Sci., 2003, 267(1), 9–17 CrossRef CAS PubMed.
- L. Fekarcha and A. Tazerouti, Surface activities, foam properties, HLB, and krafft point of some n-alkanesulfonates (C14-C18) with different isomeric distributions, J. Surfactants Deterg., 2012, 15(4), 419–431 CrossRef CAS.
- R. Farajzadeh, R. Krastev and P. L. J. Zitha, Foam film permeability: Theory and experiment, Adv. Colloid Interface Sci., 2008, 137(1), 27–44 CrossRef CAS PubMed.
- R. Farajzadeh, A. Andrianov, H. Bruining and P. L. J. Zitha, Pressure – Temperatures, 2009, 4542–4552 CAS.
- S. Hilgenfeldt, S. A. Koehler and H. A. Stone, Dynamics of coarsening foams: Accelerated and self-limiting drainage, Phys. Rev. Lett., 2001, 86(20), 4704–4707 CrossRef CAS PubMed.
- Y. Sun, X. Qi, H. Sun, H. Zhao and Y. Li, Understanding about How Different Foaming Gases Effect the Interfacial Array Behaviors of Surfactants and the Foam Properties, Langmuir, 2016, 32(30), 7503–7511 CrossRef CAS PubMed.
- T. Gildnyi, C. Stergiopoulos and E. Wolfram, Equilibrium surface tension of aqueous surfactant solutions, Colloid Polym. Sci., 1976, 254(11), 1018–1023 CrossRef.
Footnote |
† Electronic supplementary information (ESI) available. See DOI: 10.1039/d1ra06190a |
|
This journal is © The Royal Society of Chemistry 2021 |
Click here to see how this site uses Cookies. View our privacy policy here.