DOI:
10.1039/D1RA07393A
(Paper)
RSC Adv., 2021,
11, 37514-37527
Synthesis of calixresorcarenes using magnetic poly triazine-benzene sulfonamide-SO3H†
Received
5th October 2021
, Accepted 15th November 2021
First published on 22nd November 2021
Abstract
The purpose of this work is to develop a magnetically recyclable immobilized base catalyst for the green synthesis of calixresorcarenes. To achieve this, poly triazine-benzene sulfonamide (PTBSA) has been coated on magnetic Fe3O4 nanoparticles and subsequently chlorosulfonic acid has been supported to obtain Fe3O4@PTBSA-SO3H. The structure of nano-Fe3O4@PTBSA-SO3H was characterized by TEM, XRD, FT-IR, VSM, WDX, EDX, TGA/DSC and FE-SEM. The catalytic efficiency of this catalyst was also investigated in the synthesis of novel calixresorcarene derivatives. The advantages of heterogeneous nature, catalytic activity and the recyclability of the polymer support were also strengthened by advanced surface treatment. These key factors (basic sites, acidic sites and heterogeneity) play essential roles in the catalyst performance. This procedure has some advantages such as short reaction time, clean and fast work-up and easy separation of the catalyst by an external magnet.
1 Introduction
A calixarene/calixresorcinarene is one of the most important macrocyclic molecules in materials chemistry.1 This compound is the key structural fragment of fluorescent and chromogenic sensors.2 Calixarene and its derivatives demonstrate numerous biological activities such as, anti-infective, antibacterial, antitumour and antifungal.3 Moreover, many researchers have concentrated on the phase transfer catalyst activity,4 encapsulation,5 and supramolecular chemistry of calix[4] arene and its derivatives.6 The functionalization of calix[4]arene has attracted considerable interest,7 from characterization such as the ease of functionalization or modification, the flexibility and rigidity of the four different three dimensional conformations.3 For the synthesis of various calixarenes/calixresorcinarenes, the reaction of resorcinol with benzaldehyde derivatives is a particularly important method.8 Despite the existence of this synthetic method, the synthesis of these structures by the above-mentioned routes has some drawbacks such as multi-step synthetic operation, low product yield, inaccessible starting materials, limited scope and using a homogeneous catalyst.
Homogeneous catalysts function in the same phase as reactants but heterogeneous or heterogenized ones react in a different phase. With respect to the reaction medium, the advantage of heterogeneous catalysts compared to homogeneous ones is that the former function in a different phase leading to cheap and easy separation.9 Magnetic nanoparticles (MNPs) have recently been developed as a very useful type of supported catalyst because of their easy synthesis and functionalization, good stability, high surface area, low toxicity and low price as well as facile separation using magnetic forces.10 Also, to bridge the gap between heterogeneous and homogeneous catalysis, surface functionalization of magnetic particles can be considered to be a good method.11
Surface modification of heterogeneous support with polymer have attracted much attention of researchers due to its remark-able catalytic efficiency in organic synthesis which addresses the sustainability concerns including ease of recyclability, high capacity chelating, excellent chemical and thermal stability.12 Thus, the application of magnetic nanoparticles and polymers as attractive candidates is currently a subject of interest in chemical processes and organic reaction.13
Many of the organic reactions can be performed in the presence of acidic catalysts. These catalysts generally are classified into two groups: homogeneous and heterogeneous acidic catalysts. Homogeneous acids are hazardous in handling, damaging the plant and environment through their corrosiveness, add process difficulties using quenching and separation stages, which led to the large volume of toxic and corrosive wastes. Consequently, in recent years there has been developed a great interest in using heterogeneous acid catalysts instead of those homogeneous acid catalysts, because of the possibility for recovering and recycling solids, and therefore significantly reducing the environmental impact.14
There are numerous organic and inorganic materials which can be used as supporting reagents to produce heterogeneous catalysts such as polymers,15 carbons,16,17 zeolites,18,19 silica,20 hydroxyapatite,21,22 zirconia,23 magnetite nanoparticle,24 alumina25 and etc. Consequently, progress in heterogeneous solid acid catalysts as a fundamental principle in green chemistry is expected to have a major impact on industrial applications as well as on scientific aspects.
In view of the green chemistry, we tried in this work to substitute harmful mineral acids by magnetic polysulfonamide nanocomposite which contains high surface density functional group (SO3H groups). In continuation of our previous effort on the synthesis of heterogeneous polysulfonamide-based catalyst,26 we have been encouraged to develop a unique nanocatalyst Fe3O4@PTBSA-SO3H by immobilization of chlorosulfonic acid over the PTBSA grafted magnetic Fe3O4 NP (Scheme 1) and employed it in the green synthesis of calixresorcarenes (Scheme 2). The presence of chlorosulfonic acid as a strongly basic material efficiently promotes the reaction.27 In order to take advantage of the high surface area, high coordination group and easy magnetic reusability, Fe3O4 MNP grafted PBTSA was used as the base matrix. To the best of our knowledge, there is no report hitherto on the catalytic green synthesis of calixresorcinarene using magnetic-polysulfonamide based nanocomposite.
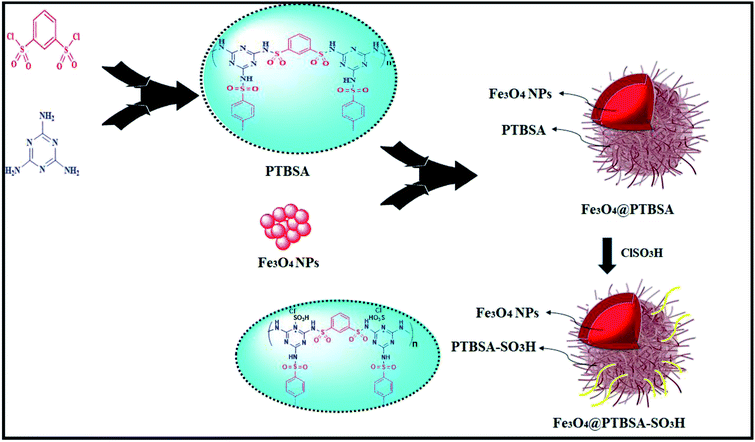 |
| Scheme 1 The general route for the synthesis of Fe3O4@PTBSA-SO3H. | |
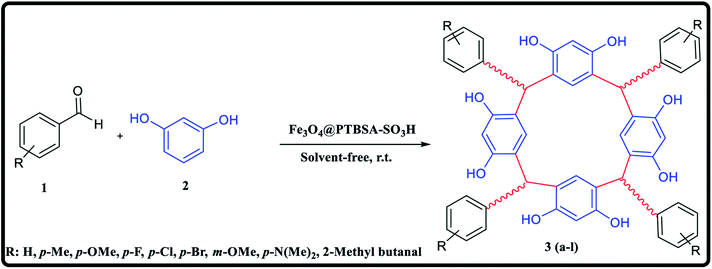 |
| Scheme 2 Synthesis of calixresorcarene derivatives using Fe3O4@PTBSA-SO3H. | |
2 Experimental section
2.1. Material and methods
All reagents and materials used in this work were of analytical reagent grade. Iron(III) chloride hexahydrate [FeCl3·6H2O, ≥98%], iron(II) chloride tetrahydrate [FeCl2·4H2O, ≥98%], melamine [1,3,5-triazine-2,4,6-triamine, ≥98%], [ammonia solution, ≥25%], [chlorosulfonic acid, ≥99%], [resorcinol ≥99%], were purchased from Sigma-Aldrich (Germany). Melting points were measured with open capillary tubes in the device BUCHI 510. Infrared (IR) spectroscopy was conducted on a PerkinElmer GX FT-IR spectrometer. Nuclear magnetic resonance spectra have been reported in DMSO-d6 with ppm chemical displacement. Mass spectrometer was recorded in a spectrometer Shimadzu QP 1100 BX. The thermal properties of the samples were conducted using a thermogravimetric analyzer (TGADSC/Mettler Toledo) ranging from room temperature to 600 °C at a rate of 10 °C min−1 under N2 atmosphere.
2.2. Preparation of Fe3O4 MNPs
First, FeCl3·6H2O (5.83 g) and FeCl2·4H2O (2.147 g) were dissolved in 100 mL of deionized water and subjected to magnetic stirring at 80 °C for 10 min. Then 10 mL of ammonia solution (25% aqueous) was added to the reaction mixture for 30 min. To prepare Fe3O4 nanoparticles, the reaction was refluxed for 10 h. Then, the suspended Fe3O4 nanoparticles were separated by an external magnet and washed with distilled water and ethanol, and dried in an oven at 80 °C for 12 h.13a
2.3. Synthesis of poly(triazine-benzene sulfonamide) (PTBSA)
A mixture of melamine (0.7 mmol) and benzene-1,3-disulfonyl chloride (1 mmol) monomers was refluxed in dry acetonitrile (40 mL) for 12 h. The resulting PTBSA precipitate was washed with acetonitrile and subsequently dried in a vacuum oven at 60 °C (Scheme 1).
2.4. Synthesis of Fe3O4@PTBSA nanocomposite
To 100 mL acetonitrile, a mixture of Fe3O4 NPs (1 g) and poly(triazine-benzene sulfonamide) (1 g) was added and refluxed for 24 h. Fe3O4@PTBSA were separated by an external magnet, washed with acetonitrile and subsequently dried in a vacuum oven at 60 °C (Scheme 1).
2.5. Synthesis of Fe3O4@PTBSA-SO3H
In order to sulfonation of Fe3O4@PTBSA, 1.0 g of prepared nanocomposite was dispersed in 20 mL of dichloromethane and chlorosulfonic acid (10 mmol) was slowly added. The pre-synthesized Fe3O4@PTBSA-SO3H were then stirred for 24 h. The resulting catalyst (Fe3O4@PTBSA-SO3H) were separated by an external magnet, washed thoroughly with dichloromethane (20 mL) and dried.
2.6. Preparation of calixresorcarene derivatives using Fe3O4@PTBSA-SO3H
A mixture of resorcinol (5 mmol), benzaldehyde derivatives (5 mmol), and Fe3O4@PTBSA-SO3H catalyst (0.2 g) was added in a mortar and pestle and ground vigorously at room temperature. After reaction completion (monitored by TLC, n-hexane/ethyl acetate, 10
:
4), the catalyst was separated from the reaction mixture by an external magnet and washed with hot ethanol. After solvent evaporation, the crude product was crystallized in ethanol, and the product was obtained with good efficiency.
2.7. Analytical data of the products
2.7.1 2,8,14,20-Tetraphenyl-4,6,10,12,16,18,22,24-octahydroxycalix[4]-resorcarene (3a). Colorless solid, mp > 300 °C (dec); FT-IR (KBr) v: 3406, 3030, 2929 cm−1; 1H NMR (500 MHz, DMSO-d6) δ ppm: 5.55 (s, 1H, CH, H4), 6.13 (s, 1H, Ar–H, H1), 6.20 (s, 1H, Ar–H, H3), 6.75–6.96 (m, 5H, Ar–H, H5, H6, H7), 8.53–8.94 (OH, broad peak, H2, 3H), ppm. 13C NMR (125 MHz, DMSO-d6) δ ppm: 50.03, 106.94, 121.44, 127.44, 127.47, 129.03, 130.16, 144.54, 159.12.28 MS: m/z = 800 [M+].
2.7.2 2,8,14,20-Tetra-p-tolyl-4,6,10,12,16,18,22,24-octahydroxycalix[4]-resorcarene (3b). Reddish orange solid, mp > 300 °C (dec); FT-IR (KBr) v: 3353, 3137, 2919 cm−1; 1H NMR (500 MHz, DMSO-d6) δ ppm: 2.21 (s, 3H, H7), 5.57 (s, 1H, CH, H4), 6.09 (s, 1H, Ar–H, H2), 6.16 (s, 1H, Ar–H, H3), 6.37–6.97 (m, 4H, Ar–H, H5, H6, 4H), 7.96–9.12 (OH, broad peak, H1, 2H), ppm. 13C NMR (125 MHz, DMSO-d6) δ ppm: 20.04, 55.75, 106.54, 121.05, 127.75, 128.86, 133.20, 143.91, 153.29.29 MS: m/z = 856 [M+].
2.7.3 2,8,14,20-Tetra-p-methoxyphenyl-4,6,10,12,16,18,22,24-octahydroxycalix[4]-resorcarene (3c). Reddish orange solid, mp > 300 °C (dec); FT-IR (KBr) v: 3553, 3397, 2971 cm−1; 1H NMR (300 MHz, DMSO-d6) δ ppm: 3.71 (s, 3H, CH3 H7), 5.56 (s, 1H, CH, H4), 6.16 (s, 1H, Ar–H, H2), 6.18 (s, 1H, Ar–H, H3), 6.47–6.63 (m, 4H, Ar–H, H5, H6, 4H), 7.58–8.51 (OH, broad peak, H1, 3H), ppm. 13C NMR (75 MHz, DMSO-d6) δ ppm: 55.26, 59.35, 102.38, 106.69, 113.19, 121.22, 129.91, 138.19, 152.84, 156.96.30 MS: m/z = 920 [M+].
2.7.4 2,8,14,20-Tetra-p-N,N-dimethylphenyl-4,6,10,12,16,18,22,24-octahydroxycalix[4]-resorcarene (3d). Yellow solid, mp: 228–230 °C; FT-IR (KBr) v: 3268, 3161, 3004 cm−1; 1H NMR (300 MHz, DMSO-d6) δ ppm: 3.02 (s, 7H, N(CH3)2, H7), 5.76 (s, 1H, CH, H4), 6.12 (s, 1H, Ar–H, H2), 6.21 (s, 1H, Ar–H, H3), 6.28–7.16 (m, 4H, Ar–H, H5, H6, 4H), 9.89 (OH, broad peak, H1, 4H), ppm. 13C NMR (75 MHz, DMSO-d6) δ ppm: 43.66, 56.77, 102.65, 105.89, 111.36, 117.31, 121.84, 130.47, 155.80, 156.98.31
2.7.5 2,8,14,20-Tetra-m-methoxyphenyl-4,6,10,12,16,18,22,24-octahydroxycalix[4]-resorcarene (3e). Red solid, mp: 298–300 °C; FT-IR (KBr) v: 3403, 3059, 2926 cm−1; 1H NMR (500 MHz, DMSO-d6) δ ppm: 3.58 (s, 3H, OCH3, H9), 5.50 (s, 1H, CH, H4), 6.16 (s, 1H, Ar–H, H2), 6.18 (s, 1H, Ar–H, H3), 6.50–7.70 (m, 3H, Ar–H, H5, H6, H7, H8, 4H), 8.58–9.5 (OH, broad peak, H1, 3H), ppm. 13C NMR (125 MHz, DMSO-d6) δ ppm: 54.95, 58.90, 102.39, 106.98, 110.77, 113.92, 121.66, 128.63, 147.67, 152.79, 158.90.
2.7.6 2,8,14,20-Tetra-p-flourophenyl-4,6,10,12,16,18,22,24-octahydroxycalix[4]-resorcarene (3e). Yellow solid, mp: 223–225 °C; FT-IR (KBr) v: 3268, 3061, 3004 cm−1; 1H NMR (500 MHz, DMSO-d6) δ ppm: 5.63 (s, 1H, CH, H3), 6.17 (s, 1H, Ar–H, H5), 6.18 (s, 1H, Ar–H, H4), 6.63–6.80 (m, 4H, Ar–H, H1, H2, 4H), 8.65–9.05 (OH, broad peak, H6, 4H), ppm. 13C NMR (125 MHz, DMSO-d6) δ ppm: 62.98, 102.78, 106.80, 114.36, 121.85, 130.20, 142.25, 158.96.32 MS: m/z = 864 [M+].
2.7.7 2,8,14,20-Tetra-p-bromophenyl-4,6,10,12,16,18,22,24-octahydroxycalix[4]-resorcarene (3f). Reddish orange solid, mp: 286–288 °C; FT-IR (KBr) v: 3351, 3058, 2919 cm−1; 1H NMR (300 MHz, DMSO-d6) δ ppm: 5.50 (s, 1H, CH, H3), 6.14 (s, 1H, Ar–H, H4), 6.31 (s, 1H, Ar–H, H5), 6.57–6.80 (m, 4H, Ar–H, H1, H2), 7.52–8.46 (OH, broad peak, H6, 2H), ppm. 13C NMR (75 MHz, DMSO-d6) δ ppm: 65.20, 103.09, 124.29, 128.86, 130.43, 134.76, 138.08, 158.95.33
2.7.8 2,8,14,20-Tetra-p-chlorophenyl-4,6,10,12,16,18,22,24-octahydroxycalix[4]-resorcarene (3g). Reddish orange solid, mp: 286–288 °C; FT-IR (KBr) v: 3389, 1520, 1148 cm−1; 1H NMR (300 MHz, DMSO-d6) δ ppm: 5.60 (s, 1H, CH, H3), 6.20 (s, 1H, Ar–H, H4), 6.33 (s, 1H, Ar–H, H5), 6.60 (broad peak, 2H, Ar–H, H1), 6.69 (broad peak, 2H, Ar–H, H2),7.73–8.83 (OH, broad peak, H6, 3H), ppm. 13C NMR (75 MHz, DMSO-d6) δ ppm: 62.96, 111.87, 120.13, 127.05, 127.54, 130.66, 134.00, 145.31, 153.28.34
2.7.9 2,8,14,20-Isobutyl-4,6,10,12,16,18,22,24-octahydroxycalix[4]-resorcarene (3h). Orange solid, mp: 286–288 °C; FT-IR (KBr) v: 3258, 2955, 2906 cm−1; 1H NMR (500 MHz, DMSO-d6) δ ppm: 0.83 (s, 3H, CH3, H5), 0.84 (s, 3H, CH3, H8), 1.37 (m, 1H, H6), 1.67 (m, 2H, H7), 6.14 (s, 1H, Ar–H, H4, 10 Hz), 6.19–6.21 (m, 2H, Ar–H, H1,H3), 8.91 (OH, broad peak, H1, 3H), ppm. 13C NMR (125 MHz, DMSO-d6) δ ppm: 15.48, 23.28, 26.19, 32.90, 44.47, 103.09, 122.94, 130.18, 159.19. MS: m/z = 712 [M+].
3 Results and discussion
3.1. Analysis of catalyst characterization data
Fig. 1 represents the FTIR spectra of the samples. According to the results of the spectrum pattern, Fe–O vibrations have been observed in the wavelength of 427–627 cm−1. The signals at around 3239 cm−1 are related to vibrations of O–H functional groups (Fig. 1a). After modification of Fe3O4 NPs with PTBSA, the presence of new bands appeared at around 1115 and 1181 cm−1 are attributed to the stretching vibrations of C–S and C–N in the polymer, respectively. Also, the absorption vibrational bands at 1650 and 1693 cm−1 related to the N–H and C
N bands of the polymer. In addition, the vibration of N–S, S
O bands was found at 1528 cm−1 and the broad absorption band between 3339–33
590 cm−1 is mainly due to the N–H and O–H bonds (Fig. 1b). These approved the successful modification of Fe3O4 MNPs with PTBSA. In the case of Fe3O4@PTBSA-SO3H, new adsorption bands related to chlorine and SO3H as well as all the above characteristic absorption bands were observed in the nanocomposite structure (Fig. 1c).
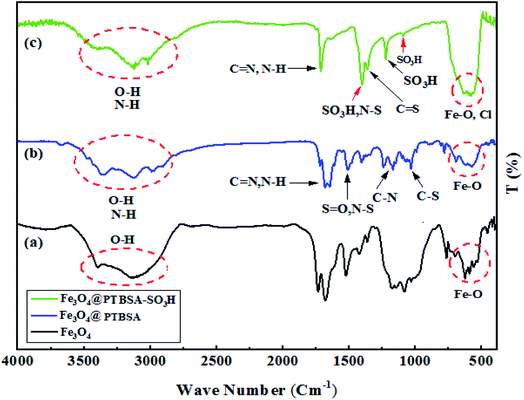 |
| Fig. 1 FT-IR spectra of Fe3O4 MNPs (a), Fe3O4@PTBSA (b), and Fe3O4@PTBSA-SO3H (c). | |
The XRD pattern of Fe3O4@PTBSA-SO3H is shown in Fig. 2. The XRD spectrum of Fe3O4@PTBSA-SO3H sample contains all characteristic peaks of both Fe3O4 NPs, polymer and chlorosulfonic acid, which is indicative of the successful combination and simultaneous presence of both organic and inorganic phases in the nanocomposite texture. Three distinct peak values observed at 2θ angle are 38.9°, 44.4°, and 60°, which are also related to the Fe3O4 MNPs.13b The diffraction peaks at 2θ angles of 25°, 26.7° and 28.4° confirmed the presence of SO3H groups.35 Additionally, the peak observed at 42.65°, 18.5°, 9.45° and 21.65° is attributed to the PTBSA.36 Through the Scherrer formula, the average particle size is found to be 6.81 nm (Fig. 2).
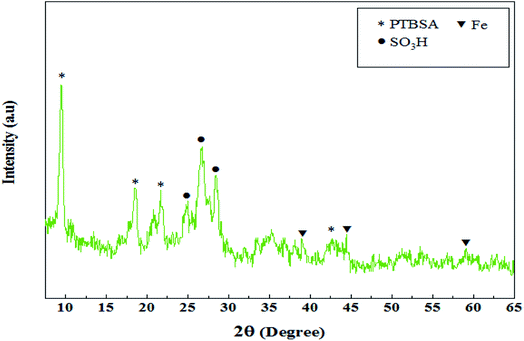 |
| Fig. 2 XRD pattern of Fe3O4@PTBSA-SO3H. | |
The surface morphologies of the samples were observed by the FESEM technique and are shown in Fig. 3. The bulk polymer structure of the pure PTBSA is given in Fig. 3a; the soft, polymeric surface of the TBSA is well visible. Surface morphologies of the Fe3O4@PTBSA and Fe3O4@PTBSA-SO3H are shown in Fig. 3b and c. The formation of sub-micrometer-sized poly TBSA and the presence of Fe3O4 NPs on the surface of the Fe3O4@PTBSA and Fe3O4@PTBSA-SO3H can be observed, indicating the growth and formation of PTBSA after surface modification of Fe3O4 MNPs. The simultaneous presence of both Fe3O4 MNPs and polymer matrix can be observed in the FESEM images of Fe3O4@PTBSA and Fe3O4@PTBSA-SO3H nanocomposite (Fig. 3b and c), indicating the successful combination of Fe3O4 core and PTBSA polymeric matrix for preparation of nanocomposite structure. According to the Fe3O4@PTBSA-SO3H particle size distribution, most particles are 40 nm (Fig. 3d). Also, the images obtained from TEM image are shown, that the nanocatalyst Fe3O4@PTBSA-SO3H has a core–shell structure and a uniform spherical morphology of 30 nm (Fig. 4).
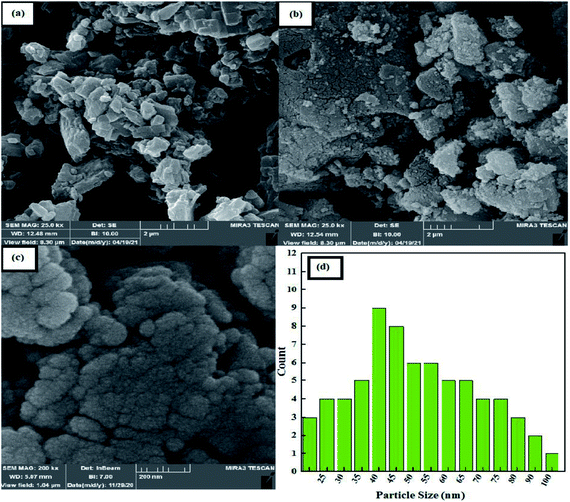 |
| Fig. 3 FE-SEM photographs of (a) PTBSA, (b) Fe3O4@PTBSA, (c) Fe3O4@PTBSA-SO3H and (d) particle size distribution of Fe3O4@PTBSA-SO3H. | |
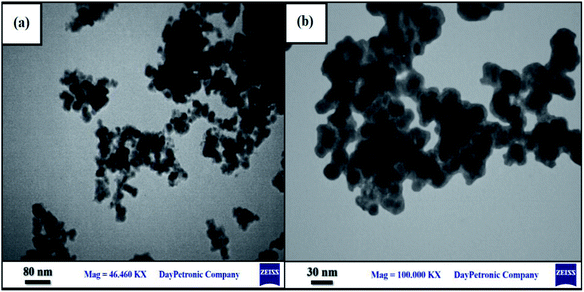 |
| Fig. 4 TEM photographs of Fe3O4@PTBSA-SO3H with the scale bar of (a) 80 nm and (b) 30 nm. | |
Fe3O4@PTBSA-SO3H was analysed using EDX as shown in Fig. 5. The presence of Fe, O, N, S and Fe signals in Fig. 5 indicates that the iron oxide particles are coated with PTBSA. The characteristic peak of Cl in Fig. 5 indicate that the Fe3O4@PTBSA have been immobilized with chlorosulfonic acid.
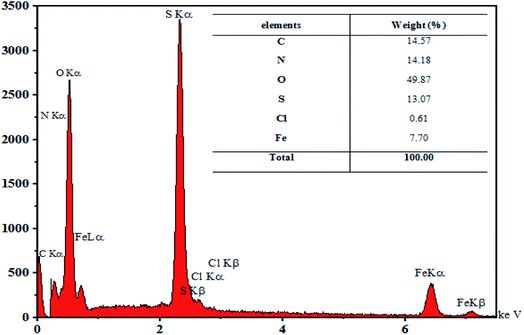 |
| Fig. 5 EDX spectrum of Fe3O4@PTBSA-SO3H. | |
According to this analysis, we conclude that Fe3O4@PTBSA-SO3H has been successfully synthesized. Elemental mapping images of nano-Fe3O4@PTBSA-SO3H, shows the elements of Cl, C, N, Fe, S and O in the framework of catalyst with a uniform distribution (Fig. 6).
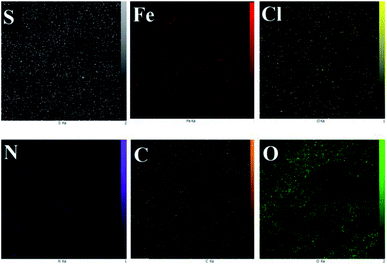 |
| Fig. 6 Elemental mapping of Fe3O4@PTBSA-SO3H shows the presence of Fe, C, N, S, Cl and O atoms in the nanocomposite. | |
Fig. 7 shows the magnetic properties of the catalyst as determined using VSM. According to the figure, the amount of saturated magnetization (Ms), coercivity field (Hc), remanent magnetization (Mr) for Fe3O4@PTBSA-SO3H are 3.26 emu g−1, 30 Oe and 0.26 emu g−1, respectively. Also, due to the s-shape of the curve and the Hc values, the synthesized materials are super-magnetic. The value is quite reduced from the bare unmodified ferrite NPs due to the surface functionalization by SO3H groups and the polysulfonamide around it.13b
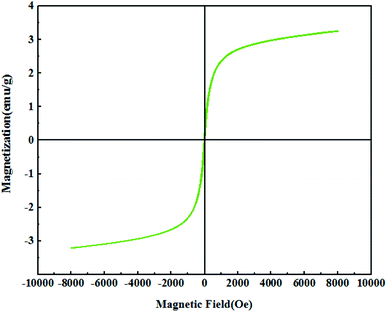 |
| Fig. 7 VSM analysis of Fe3O4@PTBSA-SO3H. | |
Thermal properties of the nanocomposite were investigated by thermal gravimetric analysis (TGA) and differential scanning calorimetry (DSC). The TGA curve of Fe3O4@PTBSA-SO3H shows the mass loss of the organic materials as they decompose upon heating (Fig. 8). TGA curve of Fe3O4@PTBSA-SO3H can be divided into several regions corresponding to different mass loss ranges. The first region, situated below 200 °C, displays a mass loss that is attributed to loss of trapped water or adsorbed solvent from the catalyst. The weight loss at higher temperature can be mainly ascribed to the evaporation and subsequent decomposition organic groups. Thus, the catalyst is stable up to 600 °C, establishing that it could be safely used in organic reactions at temperatures in the region of 200 °C. According to Fig. 8, as mentioned, the material is decomposed in 4 steps. In the first stage at 60.87 °C, the second stage at 124.37 °C, the third stage at 390.21 °C and finally at 473.11 °C, it loses 76.29% of its weight. The glass transition occurs at 173 °C. According to TG/DSC analysis, Fe3O4@PTBSA-SO3H nanocomposite is decomposed in 4 steps. In the first stage at 131.4 °C, the second stage at 251 °C, the third stage at 373.2 °C and finally at 438.9 °C, it loses 40.3% of its weight (Fig. 9).
 |
| Fig. 8 TGA curve of Fe3O4@PTBSA-SO3H. | |
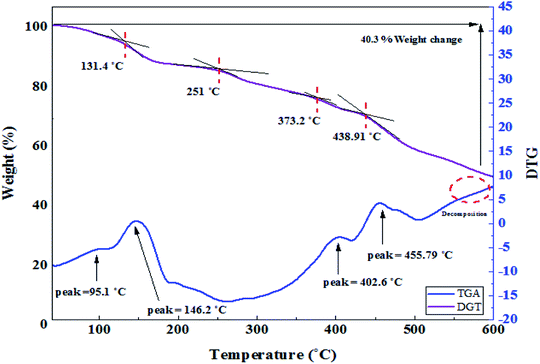 |
| Fig. 9 DSC analysis of Fe3O4@PTBSA-SO3H. | |
3.2. Titration for the determination of SO3H group density
In order to compare the synthesized catalyst with the literature reported magnetic catalysts with SO3H group, surface density of the SO3H groups was determined using back titration method.
According to back titration method, surface high density functional group is 12 mmol per H+ per g.
3.3. Catalytic studies
After the full characterization of prepared Fe3O4@PTBSA-SO3H nanocomposite, we evaluated its catalytic efficiency for the synthesis of 2,8,14,20-tetraphenyl-4,6,10,12,16,18,22,24-octahydroxycalix[4]-resorcarene (3a). The venture was started with the optimization of the reaction conditions and thereby the influence of an array of parameters like solvents, catalysts with their loads and temperature for the model reaction. Table 1 displays the corresponding results. The reaction was not successful without the catalyst (entry 1), thus signifying its importance. To investigate the effect of the catalyst concentration, systematic studies were carried out in the presence of various amounts of the nanocatalyst (entries 2–6). Thus, the best yield is found in the presence of just 0.2 g of Fe3O4@PTBSA-SO3H (entry 5), and the use of higher amounts of catalyst up to 0.25 g does not improve the result (entry 6). Thereafter, we optimized the ideal solvent in the reaction by screening the probe in different solvents like EtOH, DMF, toluene and CH3CN (entries 7–10). The results indicated that solvent-free condition play an important role in the reaction efficiency. Considering the model reaction at different temperature (entry 11), the room temperature is the best temperature that affects the progress of the model reaction process (entry 5).
Table 1 Optimization of reaction conditions
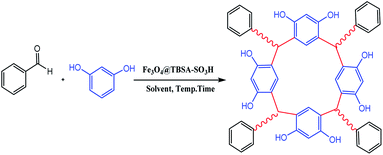
|
Entry |
Cat. (g) |
Solvent |
Temperature (°C) |
Time (min) |
Yielda (%) |
Isolated yield. |
1 |
— |
Solvent-free |
R.T. |
5 |
N.R |
2 |
0.05 |
Solvent-free |
R.T. |
5 |
Trace |
3 |
0.1 |
Solvent-free |
R.T. |
5 |
48 |
4 |
0.15 |
Solvent-free |
R.T. |
5 |
70 |
5 |
0.2 |
Solvent-free |
R.T. |
5 |
92 |
6 |
0.25 |
Solvent-free |
R.T. |
5 |
92 |
7 |
0.2 |
EtOH |
R.T. |
5 |
Trace |
8 |
0.2 |
DMF |
R.T. |
5 |
Trace |
9 |
0.2 |
Toluene |
R.T. |
5 |
Trace |
10 |
0.2 |
CH3CN |
R.T. |
5 |
Trace |
11 |
0.2 |
Solvent-free |
50 °C |
5 |
88 |
In order to study the effect of surface modification on the reaction progress, Fe3O4 MNPs, Fe3O4@PTBSA, PTBSA-SO3H and PTBSA was used to carry out the same model reaction and none of them produced satisfactory results (Table 2). Therefore, Fe3O4@PTBSA-SO3H has a larger surface area for catalytic reactions and higher efficiency.
Table 2 Comparison study on the catalytic efficiency of variety of catalysts with different surface modifications
Catalyst |
Yield (%) |
Time (min) |
PTBSA-SO3H |
75 |
5 |
PTBSA |
68 |
5 |
Fe3O4 NPs |
16 |
5 |
Fe3O4@PTBSA |
83 |
5 |
Fe3O4@PTBSA-SO3H |
92 |
5 |
With the optimized condition in hand, we then investigated the reactions scope, not only with unsubstituted substrates but also with a wide range of substrates bearing electron withdrawing and electron-donating functional groups. The reactions proceeded smoothly, affording calixerane derivatives in moderate to good yields (Table 3).
Table 3 Synthesis of calixresorcarenes using Fe3O4@PTBSA-SO3H.a
Entry |
Substrate |
Producta |
Time (min) |
Yieldb (%) |
Reaction condition: benzaldehyde derivatives (5 mmol), resorcinol (5 mmol), and Fe3O4@PTBSA-SO3H (0.2 g) at room temperature. Isolated yield. |
1 |
Benzaldehyde |
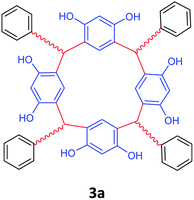 |
5 |
92 |
2 |
p-Methylbenzaldehyde |
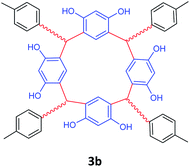 |
5 |
95 |
3 |
p-Methoxybenzaldehyde |
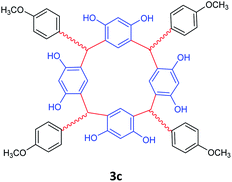 |
5 |
98 |
4 |
4-(Dimethylamino)benzaldehyde |
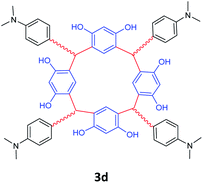 |
5 |
90 |
5 |
m-Methoxybenzaldehyde |
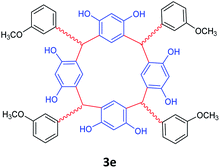 |
5 |
88 |
6 |
p-Flourobenzaldehyde |
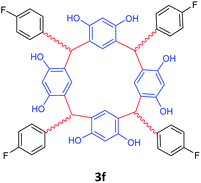 |
5 |
83 |
7 |
p-Boromobenzaldehyde |
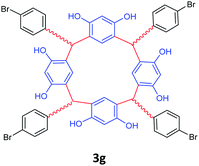 |
5 |
80 |
8 |
p-Chlorobenzaldehyde |
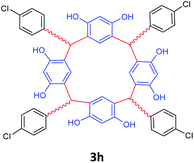 |
5 |
85 |
9 |
2-Methylbutanal |
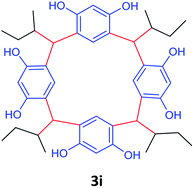 |
5 |
76 |
A probable mechanistic sequence for the formation of calixresorcarenes catalyzed by Fe3O4@PTBSA-SO3H is presented in Scheme 3. It is assumed that during the course of reaction, the nucleophilic addition of resorcinol to activated benzaldehyde by Fe3O4@PTBSA-SO3H leads to the formation of intermediate (A). By leaving the water, the intermediate A is converted to the intermediate (B), and then intermediate (C) is obtained. By performing the steps described above, the desired final product is synthesized (Scheme 3).
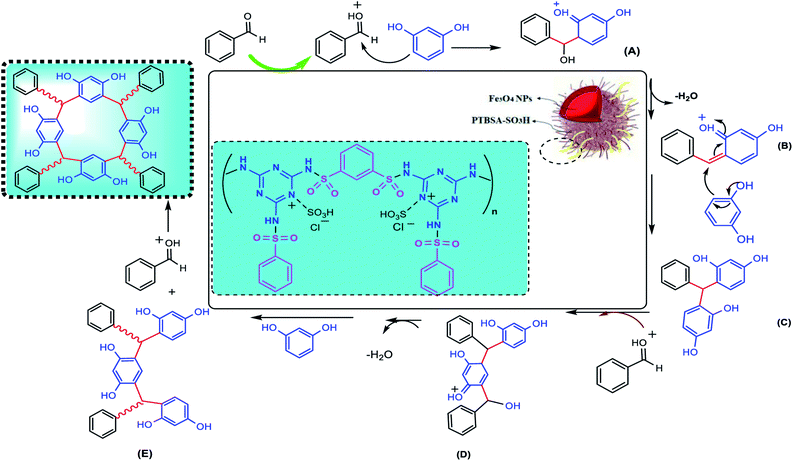 |
| Scheme 3 The plausible mechanism for the synthesis of calixresorcarenes using Fe3O4@PTBSA-SO3H. | |
To explore the stability and recyclability of Fe3O4@PTBSA-SO3H, the synthesized nanocatalyst was examined for six runs in the synthesis of C-phenilcalix[4]resorcinarene (3a) under the optimized reaction conditions. The observed slight decrease in the activity during the sixth runs of the recycling experiments was due to the absorption/adsorption of the reactants/products in the channels or on the surface of the Fe3O4@PTBSA-SO3H (Fig. 10) (92, 92, 90, 89, 87, 85%).
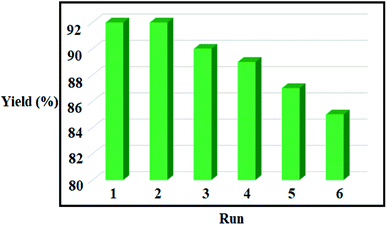 |
| Fig. 10 Recycling of the Fe3O4@PTBSA-SO3H for the reaction of benzaldehyde and resorcinol. | |
Surface charge of the prepared magnetic Fe3O4@PTBSA and Fe3O4@PTBSA-SO3H were estimated using zeta potential measurements. The zeta potentials of Fe3O4 MNPs is −10.63 mV.37 As shown in Fig. 10 and 11, the zeta potentials of Fe3O4@PTBSA and Fe3O4@PTBSA-SO3H are −23.0 and −13.3 mV, respectively. Zeta potential measurements indicate the successful coating of magnetite nanoparticles. The increase in the negative charge density of the Fe3O4@PTBSA is attributed to the presence of the triazine groups (Fig. 11) and the decrease in the negative charge density on the surface of Fe3O4@PTBSA is attributed to the presence of the chlorosulfonic acid groups (Fig. 12).
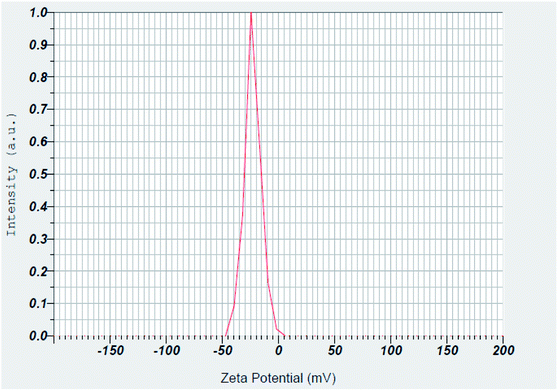 |
| Fig. 11 Zeta potential of Fe3O4@PTBSA MNPs. | |
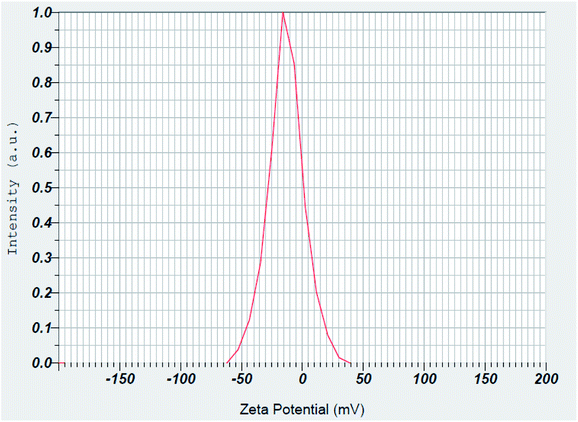 |
| Fig. 12 Zeta potential of Fe3O4@PTBSA-SO3H MNPs. | |
The efficiency of Fe3O4@PTBSA-SO3H as a catalyst for the synthesis of the model compound 3a was compared with that of other catalysts reported in the literature (Table 4). It is clear from this table that Fe3O4@PTBSA-SO3H is a more efficient catalyst for the synthesis of calixresorcarenes. Many SO3H groups of the catalyst provide efficient acidic sites and good catalytic activity of Fe3O4@PTBSA-SO3H. Compared to the other catalysts, Fe3O4@PTBSA-SO3H provides short reaction times, simple isolation of products, high to excellent yields, stability of the catalyst and its easy magnetic separation and re-use with no significant loss of activity.
Table 4 Comparison of the present methodology with other reported catalyst for the synthesis of 2,8,14,20-tetraphenyl-4,6,10,12,16,18,22,24-octahydroxycalix[4]-resorcarene (3a)
Entry |
Conditions |
Yield (%) [Ref] |
1 |
Stage 1: recorcinol with hydrogenchloride in ethanol; water at 70 °C; for 1 h |
94 (ref. 38) |
Stage 2: benzaldehyde in ethanol; water for 8 h; Reflux |
2 |
Yttrium(III) nitrate hexahydrate in neat (no solvent) at 120 °C; for 0.25 h |
92 (ref. 34) |
3 |
Toluene-4-sulfonic acid in ethanol at 20 °C; for 1 h |
85 (ref. 28) |
4 |
Fe3O4@PTBSA-SO3H (0.2 g), grinding condition in solvent-free, R.T., 5 min |
92 [this work] |
4 Conclusions
The main goal of the current study was to design and synthesis of a novel magnetic polysulfonamide based nanocatalyst (Fe3O4@PTBSA-SO3H). The synthesized sample was characterized with different instrumental techniques including FE-SEM, TEM, XRD, FT-IR, and VSM to gain an in-depth insight into the physicochemical features of the synthesized catalyst. To evaluate the effectiveness of this material in practical use the catalytic performance of the Fe3O4@PTBSA-SO3H nanocomposite toward synthesis of novel calixresorcarenes was monitored. The results of this study revealed that Fe3O4@PTBSA-SO3H nanocomposite can be utilized as a highly efficient catalyst for green synthesis of calixresorcarenes.
Conflicts of interest
The authors declare that they have no competing interests.
Acknowledgements
We sincerely thank Bu-Ali Sina University, Center of Excellence in Development of Environmentally Friendly Methods for Chemical Synthesis (CEDEFMCS) for financial support.
References
-
(a) M. Raynal, P. Ballester, A. Vidal-Ferran and P. W. N. M. van Leeuwen, Chem. Soc. Rev., 2014, 43, 1734–1787 RSC;
(b) L. Cera and C. A. Schalley, Chem. Soc. Rev., 2014, 43, 1800–1812 RSC;
(c) R. Custelcean, Chem. Soc. Rev., 2014, 43, 1813–1824 RSC;
(d) M. E. Carnes, M. S. Collins and D. W. Johnson, Chem. Soc. Rev., 2014, 43, 1825–1834 RSC;
(e) K. J. Skilling, F. Citossi, T. D. Bradshaw, M. Ashford, B. Kellam and M. Marlow, Soft Matter, 2014, 10, 237–256 RSC;
(f) G. Zhang, G. Kim and W. Choi, Energy Environ. Sci., 2014, 7, 954–966 RSC;
(g) H.-J. Schneider, P. Agrawal and A. K. Yatsimirsky, Chem. Soc. Rev., 2013, 42, 6777–6800 RSC;
(h) S. S. Zhu, H. Staats, K. Brandhorst, J. Grunenberg, F. Gruppi, E. Dalcanale, A. Lutzen, K. Rissanen and C. A. Schalley, Angew. Chem., Int. Ed., 2008, 47, 788–792 CrossRef CAS PubMed.
-
(a) L. Pirondini and E. Dalcanale, Chem. Soc. Rev., 2007, 36, 695–706 RSC;
(b) M. H. Düker, H. Schäfer, M. Zeller and V. A. Azov, J. Org. Chem., 2013, 78, 4905–4912 CrossRef PubMed.
- F. Nasuhi Pur, Mol. Diversity, 2016, 20, 781–787 CrossRef CAS PubMed.
- R. J. Hooley, S. M. Biros and J. Rebek Jr, Angew. Chem., Int. Ed., 2006, 45, 3517–3519 CrossRef CAS PubMed.
- J. Rebek Jr, Angew. Chem., Int. Ed., 2005, 44, 2068–2078 CrossRef PubMed.
-
(a) H. Mansikkamaki, M. Nissinen and K. Rissanen, Angew. Chem., Int. Ed., 2004, 43, 1243–1246 CrossRef PubMed;
(b) P. Timmerman, W. Verboom and D. N. Reinhoudt, Tetrahedron, 1996, 52, 2663–2704 CrossRef CAS;
(c) A. Jasat and J. C. Sherman, Chem. Rev., 1999, 99, 931–967 CrossRef CAS PubMed.
-
(a) Y. Ding, J. Jiao, B. Sun, Z. Yang, C. Lin and L. Wang, The facile preparation of p-(methoxy)calix[n]arenes (n = 6, 7, or 8) and their permethylated derivatives, Chin. Chem. Lett., 2021 DOI:10.1016/j.cclet.2021.05.045;
(b) B. Gassoumi, M. Echabaane, F. E. Ben Mohamed, L. Nouar, F. Madi, A. Karayel, H. Ghalla, M. E. Castro, F. J. Melendez, S. Özkınalı, A. Rouis and R. B. Chaaban, Spectrochim. Acta, Part A, 2022, 264, 120242 CrossRef CAS PubMed;
(c) C. L. Boldrini, N. Manfredi, T. Montini, L. Baldini, A. Abbotto and P. Fornasiero, Current Opinion in Green and Sustainable Chemistry., 2021, 32, 100534 CrossRef;
(d) K. Jlassi, K. Eidb, M. H. Sliema, A. M. Abdullaha and M. M. Chehimi, Data in Brief, 2021, 35, 106799 CrossRef PubMed;
(e) E. Ozyilmaz, S. Ascioglu and M. Yilmaz, Int. J. Biol. Macromol., 2021, 175, 79–86 CrossRef CAS PubMed;
(f) Y. Jin, K. Akagawa, T. Mutai, I. Yoshikawa and K. Kudo, Tetrahedron, 2021, 88, 132146 CrossRef CAS.
-
(a) A. Arami, B. Karamia and S. Khodabakhshi, J. Chin. Chem. Soc., 2014, 62, 13–16 CrossRef;
(b) B. A. Roberts, G. W. Cave, V. C. L. Raston and J. L. Scott, Green Chem., 2001, 3, 280–284 RSC;
(c) S. A. Senthan and V. Alexander, Dalton Trans., 2015, 44, 14813–14822 RSC.
- E. Farnetti, R. Di Monte and J. Kašpar, Inorganic and Bio-organic Chemistry: Vol. II. Homogeneous and Heterogeneous Catalysis, University of Trieste, Trieste, Italy, 2009 Search PubMed.
- X. Zheng, S. Luo, L. Zhang and J. P. Cheng, Green Chem., 2009, 11, 455 RSC.
- J. Safari and Z. Zarnegar, J. Mol. Catal. A: Chem., 2013, 379, 269 CrossRef CAS.
-
(a) R. J. Kalbasi, M. Kolahdoozan and M. Rezaei, Mater. Chem. Phys., 2011, 125, 784–790 CrossRef CAS;
(b) S. Zafari, R. Ghorbani-Vaghei and S. Alavinia, Mater. Chem. Phys., 2021, 270, 124840 CrossRef CAS;
(c) N. Shekarlab, R. Ghorbani-Vaghei and S. Alavinia, Appl. Organomet. Chem., 2020, 34, e5918 CrossRef CAS;
(d) J. Babamoradi, R. Ghorbani-Vaghei and S. Alavinia, RSC Adv., 2021, 11, 19147–19157 RSC;
(e) Z. Hamidi and M. A. K. Zarchi, Res. Chem. Intermed., 2018, 44, 6995–7011 CrossRef CAS.
-
(a) R. Ghorbani-Vaghei, S. Alavinia, Z. Merati and V. Izadkhah, Appl. Organomet. Chem., 2018, 32, e4127 CrossRef;
(b) R. Ghorbani-Vaghei, S. Alavinia and N. Sarmast, Appl. Organomet. Chem., 2018, 32, e4127 CrossRef;
(c) K. V. Karthik, A. V. Raghu, K. R. Reddy, R. Ravishankar, M. Sangeeta, N. P. Shetti and Ch V. Reddy, Chemosphere, 2022, 287, 132081 CrossRef CAS PubMed;
(d) Y. V. Divyasri, Y. N. Teja, V. N. Koteswara Rao, N. C. G. Reddy, S. Mohan, M. M. Kumari and M. V. Shankar, Nanostructured Materials for Environmental Applications, 2021, 485–519 Search PubMed;
(e) A. V. Raghu, G. S. Gadaginamath, H. M. Jeong, N. T. Mathew, S. B. Halligudi and T. M. Aminabhavi, J. Appl. Polym. Sci., 2009, 113, 2747–2754 CrossRef CAS;
(f) A. V. Raghu, G. S. Gadaginamath, M. Priya, P. Seema, H. M. Jeong and T. M. Aminabhavi, J. Appl. Polym. Sci., 2008, 110, 2315–2320 CrossRef CAS;
(g) A. V. Raghu, G. S. Gadaginamath, N. Mathew, S. B. Halligudi and T. M. Aminabhavi, J. Appl. Polym. Sci., 2007, 106, 299–308 CrossRef CAS;
(h) G. T. Vidyavathi, B. V. Kumar, A. V. Raghu, T. Aravinda, U. Hani, H. C. AnandaMurthy and A. H. Shridhar, J. Mol. Struct., 2021, 1249, 131656 CrossRef;
(i) L. H. Janardhan, J. M. Dong, K. Raghava Reddy, C. V. Reddy, T. Naveen Kumar, M. I. Ahamed and A. V. Raghu, Int. J. Hydrogen Energy, 2021, 46, 3289–3301 CrossRef;
(j) K. Kannan, D. Radhika, K. R. Reddy, A. V. Raghu, K. K. Sadasivuni, G. Palani and K. Gurushankar, Nano Express, 2021, 2, 010014 Search PubMed.
-
(a) E. Doustkhah, J. Lin, S. Rostamnia, C. Len, R. Luque, X. Luo, Y. Bando, K. C. W. Wu, J. Kim, Y. Yamauchi and Y. Ide, Chem.–Eur. J., 2019, 25, 1614–1635 CrossRef CAS PubMed;
(b) M. Fallah-Mehrjardi, A. R. Kiasat and K. Niknam, J. Iran. Chem. Soc., 2018, 15, 2033–2081 CrossRef CAS;
(c) M. A. Zolfigol, R. Ayazi-Nasrabadi, S. Baghery, V. Khakyzadeh and S. Azizian, J. Mol. Catal. A: Chem., 2016, 418, 54–67 CrossRef.
- C. Ying and B. Chulsung, Curr. Org. Synth., 2011, 8, 208–236 CrossRef.
- K. Nakajima and M. Hara, ACS Catal., 2012, 2, 1296–1304 CrossRef CAS.
- H. Sharghi, P. Shiri and M. Aberi, Beilstein J. Org. Chem., 2018, 14, 2745–2770 CrossRef CAS PubMed.
- P. Gogoi, A. K. Dutta, S. Saikia and R. Borah, Appl. Catal., A, 2016, 523, 321–331 CrossRef CAS.
- A. Brito, M. E. Borges and N. Otero, Energy Fuels, 2007, 21, 3280–3283 CrossRef CAS.
- W. Long and C. W. Jones, ACS Catal., 2011, 1, 674–681 CrossRef CAS.
- J. Deng, L.-P. Mo, F.-Y. Zhao, L.-L. Hou, L. Yang and Z.-H. Zhang, Green Chem., 2011, 13, 2576–2584 RSC.
- L. Ma’mani, M. Sheykhan, A. Heydari, M. Faraji and Y. Yamini, Appl. Catal., A, 2010, 377, 64–69 CrossRef.
- Y. Zhou, R. Huang, F. Ding, A. D. Brittain, J. Liu, M. Zhang, M. Xiao, Y. Meng and L. Sun, ACS Appl. Mater. Interfaces, 2014, 6, 7417–7425 CrossRef CAS PubMed.
- N. Koukabi, E. Kolvari, M. A. Zolfigol, A. Khazaei, B. S. Shaghasemi and B. Fasahati, Adv. Synth. Catal., 2012, 354, 2001–2008 CrossRef CAS.
- M. Khoshnevis, A. Davoodnia, A. Zare-Bidaki and N. Tavakoli-Hoseini, Synth. React. Inorg., Met.-Org., Nano-Met. Chem., 2013, 43, 1154–1161 CrossRef CAS.
-
(a) S. Alavinia and R. Ghorbani-Vaghei, J. Phys. Chem. Solids, 2020, 146, 109573–109584 CrossRef CAS;
(b) F. Hamidi Dastjerdi, R. Ghorbani-Vaghei and S. Alavinia, Catal. Lett., 2020, 150, 3514–3522 CrossRef CAS;
(c) S. Alavinia, R. Ghorbani-Vaghei, J. Rakhtshah, J. Yousefi Seyf and I. Ali Arabian, Appl. Organomet. Chem., 2020, 34, e5449 CrossRef CAS;
(d) S. Alavinia and R. Ghorbani-Vaghei, New J. Chem., 2020, 44, 13062–13073 RSC;
(e) S. Solgi, R. Ghorbani-Vaghei and S. Alavinia, J. Porous Mater., 2021, 28, 289–298 CrossRef CAS;
(f) N. Shekarlab, R. Ghorbani-Vaghei and S. Alavinia, J. Organomet. Chem., 2021, 949, 121971 CrossRef CAS;
(g) A. Rahimi, R. Ghorbani-Vaghei and S. Alavinia, J. Porous Mater., 2021, 28, 1643–1653 CrossRef;
(h) S. Alavinia and R. Ghorbani-Vaghei, RSC Adv., 2021, 11, 29728–29740 RSC;
(i) S. Alavinia and R. Ghorbani-Vaghei, Monatsh. Chem., 2021, 152, 1269–1276 CrossRef CAS.
- S. Solgi, R. Ghorbani-Vaghei, S. Alavinia and V. Izadkhah, Preparation and Application of Highly Efficient and Reusable Nanomagnetic Catalyst Supported with Sulfonated-Hexamethylenetetramine for Synthesis of 2,3-Dihydroquinazolin-4(1H)-Ones, Polycyclic Aromat. Compd., 2020 DOI:10.1080/10406638.2020.1833054.
- A. M. Shebitha, S. S. Sreejith, P. B Sherly mole, N. Mohan, G. Avudaiappan, K. Hiba, K. S. Priya and K. Sreekumar, J. Mol. Struct., 2020, 1214, 128215 CrossRef CAS.
- B. Karami, S. Khodabakhshi, N. Safikhani and A. Arami, Bull. Korean Chem. Soc., 2012, 33, 123–127 CrossRef CAS.
- A. A. Castillo-Aguirre, A. Pérez-Redondo and M. Maldonado, J. Mol. Struct., 2020, 1202, 127402 CrossRef CAS.
- A. Mobinikhaledi, M. Kalhor, A. R. Ghorbani and H. Fathinejad, Asian J. Chem., 2010, 22, 1103–1106 CAS.
- Z. Ling-ling, W. Yu, H. Shu-ying, L. Gui-xiang, C. Liang-feng, Y. Shu-ning, Z. Wen-li and W. Hui, Lett. Org. Chem., 2013, 10, 298–301 CrossRef.
- L. M. Tunstad, J. A. Tucker, E. Dalcanale, J. Weiser, J. A. Bryant, J. C. Sherman, R. C. Helgeson, C. B. Knobler and D. J. Cram, J. Org. Chem., 1989, 54, 1305–1312 CrossRef CAS.
- A. Arami, B. Karami and S. Khodabakhshi, J. Chin. Chem. Soc., 2015, 62, 13–16 CrossRef CAS.
- J. Safaei-Ghomi and H. Shahbazi-Alavi, Sci. Iran., 2017, 24, 1209–1219 Search PubMed.
-
(a) F. Fina, S. K. Callear, G. M. Carins and J. T. Irvine, Chemistry of Materials, 2015, 27, 2612–2618 CrossRef CAS;
(b) L. Jia, D. Wang, L. Liu, S. Zhang and T. Xu, Des. Monomers Polym., 2014, 17, 425–429 CrossRef CAS.
- M. A. Akl, A. M Atta, A. E.-F. M Yousef and M. I. Alaa, Polym. Int., 2013, 62, 1667–1677 CrossRef CAS.
- S. A. Senthan and V. Alexander, Dalton Trans., 2015, 44, 14813–14822 RSC.
Footnote |
† Electronic supplementary information (ESI) available: Detailed experimental procedure and FT-IR and MS of all compounds. See DOI: 10.1039/d1ra07393a |
|
This journal is © The Royal Society of Chemistry 2021 |
Click here to see how this site uses Cookies. View our privacy policy here.