DOI:
10.1039/D1TA02736K
(Paper)
J. Mater. Chem. A, 2021,
9, 19847-19853
Electrostatically confined Bi/Ti3C2Tx on a sponge as an easily recyclable and durable catalyst for the reductive transformation of nitroarenes†
Received
1st April 2021
, Accepted 6th May 2021
First published on 6th May 2021
Abstract
Developing novel catalysts with both easily accessible recyclability and long-term durability toward chemical synthesis is highly desirable yet remains to be explored. In this work, a porous and bulk sponge-confined bismuth (Bi)/Ti3C2Tx (MXene) composite as a monolithic catalyst is synthesized via the photodeposition of Bi nanoparticles with a mean size of 4.4 nm on Ti3C2Tx followed by electrostatic self-assembly between the negatively charged Bi/Ti3C2Tx and positively charged sponge. It is noteworthy that compared to the analogue of widely investigated reduced graphene oxide, Ti3C2Tx with favorable hydrophilic surface groups as the scaffold for the high dispersion of Bi nanoparticles benefits not only efficient aqueous phase catalytic reactions, but also strong electrostatic interaction with the sponge substrate for ensuring the recyclability towards practical applications. As a result, the bulk sponge-confined Bi/Ti3C2Tx as an easily recyclable catalyst possesses both improved catalytic performance and long-term durability for the hydrogenation of nitroarenes in the aqueous phase. This study presents a facile and valuable protocol for functionalizing inexpensively available porous bulk materials to confine catalysts towards integrated materials featuring easy-separation and long-term stability for practical catalytic processes.
1 Introduction
Catalytic hydrogenation using sodium borohydride (NaBH4) as a reductant represents an advanced and promising process for simultaneously detoxicating and reducing nitroarenes into amines.1–5 Catalysts are indispensable for capably catalyzing NaBH4 to afford this process.6,7 Among the reported catalysts, Au,8 Ag,6 Cu,9 Pd,5 Pt,10 and metal alloys11–16 have been proved to be thermodynamically favorable, considerably efficient, and catalytically durable for NaBH4-participating nitroarene hydrogenation reactions.1,17–19 Especially, nanometal bismuth (Bi) has practical potential for catalyzing nitroarene hydrogenation with the consideration of both the merits mentioned above and the low cost.20,21 However, the agglomeration of nanometals into bulk ones resulting from high surface free energy leads to poor catalytic efficiency.22,23 It has been demonstrated that the introduction of supporting materials can not only act as a crystal-growth mediator by providing nucleation and growth sites, but also alleviate the agglomeration of nanometals to unveil abundant active sites for enhancing catalytic reactivity.15,24–26 Furthermore, supporting materials can also stabilize nanomaterials through interfacial interaction.27
Graphene oxide (GO) is a widely used surface functional group-terminated two-dimensional (2D) material with a large surface area and is proved to be promising for assembling nanomaterials.28,29 However, GO is inevitably converted into reduced graphene oxide (rGO) during the anchoring of metal nanoparticles, which therefore ruins surface properties.30,31 MXenes represent 2D metal carbides, nitrides, and carbonitrides with the formula of Mn+1XnTx, where n = 1, 2, 3, and 4, M represents transition metals, X corresponds to carbon and/or nitrogen, and Tx stands for terminal groups.32–35 The large surface area, rich surface groups, and opportune stability towards redox surroundings make 2D MXenes competent for assembling nanometals to achieve reinforced aqueous catalytic activity.36–39 Hitherto, the anchoring of Bi nanoparticles on MXenes for catalyzing NaBH4 to hydrogenate nitroarenes remains to be explored. Thus, it is of significance to devote efforts towards examining the catalytic hydrogenation activity of Bi/MXene composites towards the reduction of nitroarenes.
The use of integrated catalysts avoids the time-consuming and complicated separation of powder catalysts from catalytic systems, which simplifies the catalytic process, saves energy, and elevates efficiency.40,41 Additionally, the loss of powder catalysts during the recycling process accounts for the poor cyclability of nanometals to a large extent. In this context, an integrated catalyst is of great value in practical catalytic chemical synthesis. Enlighted by the superior cyclability of catalysts assembled on porous materials,42–44 and the electrostatically strong interaction between Ti3C2Tx and catalysts, which imparts Ti3C2Tx/semiconductor hybrids with unique durability,32 in this work, we evenly assemble Bi nanoparticles on a Ti3C2Tx platform with small size, abundant catalytically active sites, and strong interfacial chemical interaction via a facile photodeposition process. The as-synthesized Bi/Ti3C2Tx catalyst shows enhanced activity and durability for hydrogenating a class of nitroarenes. Electrostatically confined Bi/Ti3C2Tx onto a bulk sponge enables easy recyclability without compromising durability.
2 Experimental section
2.1. Synthesis of Ti3C2Tx MXene nanoflakes
Ti3C2Tx nanoflakes are obtained via selectively etching the Ti3AlC2 precursor with a mixture of hydrochloric acid and lithium fluoride. Firstly, 20.0 mL hydrochloric acid (9 M) and 1.6 g lithium fluoride are mixed and magnetically stirred for 10 min. Then, 1.0 g Ti3AlC2 is introduced into the mixture and held at 40 °C for 24 h. Deionized water is used to wash the final product to ensure that the pH of supernatant is around 6.0. Subsequently, the final precipitate is diluted with 100.0 mL deionized water, sonicated under a nitrogen atmosphere for 1.5 h at 25 °C, and centrifuged at a speed of 3500 rpm for 1.5 h to acquire the Ti3C2Tx colloid. Finally, the concentration of Ti3C2Tx nanoflakes is determined by filtering and drying 4.0 mL of the colloid in a vacuum. The Ti3C2Tx colloid with desired concentration (2.0 mg mL−1) is obtained by diluting the known-concentration Ti3C2Tx colloid with deionized water.
2.2. Synthesis of Bi/Ti3C2Tx
Bi/Ti3C2Tx is fabricated through a facile photodeposition method (Fig. 1a). In detail, 30.0 mL deionized water is mixed with 10.0 mL lactic acid, 1.0 g polyethylene glycol, and 0.3 g bismuth ammonium citrate to form translucent solution. Then, different volumes (250 μL, 500 μL, and 750 μL) of Ti3C2Tx colloid (2.0 mg mL−1) are added, stirred for 30 min, sealed in a photoreactor, bubbled with nitrogen to remove air, and illuminated with a 200 W Xe lamp (PLS-SXE300D, Beijing Perfectlight) for 4 h. Temperature-controlled cycling water is used to make sure that the temperature of reaction system is 25 °C, and nitrogen is continuously bubbled during the whole experiment. The final product is rinsed sequentially with ethanol and deionized water, freezingly dried, and labelled Bi–0.5% Ti3C2Tx, Bi–1.0% Ti3C2Tx, and Bi–1.5% Ti3C2Tx. GO is also used to synthesize a Bi–rGO composite in the same way as Ti3C2Tx. For comparison, pure Bi is also synthesized in the same way except for the absence of Ti3C2Tx.
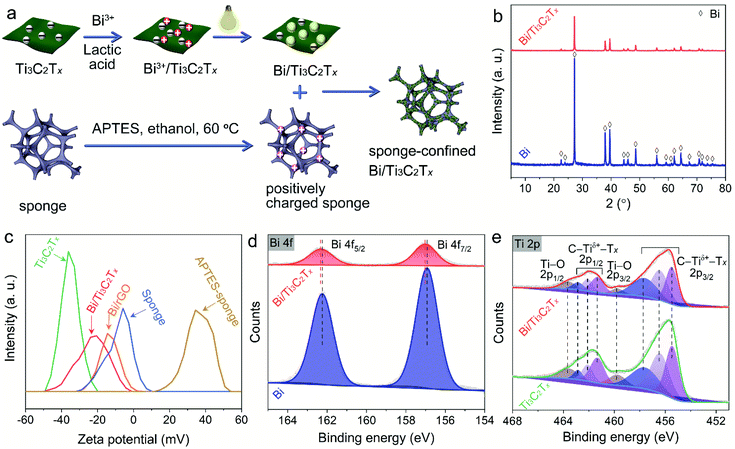 |
| Fig. 1 (a) Schematics of the synthesis of Bi/Ti3C2Tx and sponge-confined Bi/Ti3C2Tx. (b) XRD patterns of Bi and Bi/Ti3C2Tx. (c) Zeta potentials of Ti3C2Tx, Bi/Ti3C2Tx, Bi/rGO, sponge, and APTES-modified sponge. (d) High-resolution Bi 4f XPS spectra of Bi and Bi/Ti3C2Tx. (e) High-resolution Ti 2p XPS spectra of Ti3C2Tx and Bi/Ti3C2Tx. | |
2.3. Synthesis of the APTES-modified sponge
The porous bulk sponge (2.0 cm in width, 2.0 cm in height, and 0.3 cm in thickness) is immersed in a solution containing 0.4 mL APTES and 50.0 mL anhydrous ethanol. The system is then maintained at 60 °C for 4 h. The modified porous bulk sponge is washed with ethanol and deionized water to dislodge surplus APTES.
2.4. Synthesis of sponge-confined Bi/Ti3C2Tx
An electrostatic self-assembly process is carried out to synthesize the sponge-confined Bi/Ti3C2Tx or Bi/rGO (Fig. 1a). Typically, the APTES-modified porous bulk sponge is immersed in a suspension composed of 60.0 mL deionized water and 2.0 mg Bi/Ti3C2Tx or Bi/rGO composites, followed by magnetic stirring. Afterwards, the sponge with Bi/Ti3C2Tx or Bi/rGO composites electrostatically confined onto its skeleton is dried at 60 °C for 4 h in a vacuum.
2.5. Characterization
The phase composition is verified by X-ray diffraction (XRD) with a miniFlex diffractometer (Rigaku, Japan). Raman spectra are obtained by using an inVia-reflex spectrometer (Renishaw, UK). Surface charge properties are detected with a Zetasizer Nano ZSP instrument (Malvern, UK). X-ray photoelectron spectra (XPS) signals are gathered by using a K-ALPHA apparatus (Thermo Fisher Scientific, USA). The morphology is analyzed with a S-4800 scanning electron microscope (SEM, Hitachi, Japan). The microstructure is analyzed via a Titan G2 60-300 transmission electron microscope (TEM, FEI, USA). The contacting angle is tested by using a DSA100 machine (Kruss, Germany). Ultraviolet-visible (UV-vis) adsorption spectra are record using an UV-1780 spectrophotometer (Shimadzu, Japan). An ASAP 2020 instrument (Micromeritics, USA) is employed to investigate surface properties.
2.6. Catalytic activity
The hydrogenation of nitroarenes with NaBH4 as the reductant is performed to test the catalytic activity of the as-synthesized Bi/Ti3C2Tx and sponge-confined Bi/Ti3C2Tx. In detail, 10.0 mL Bi/Ti3C2Tx suspension with a concentration of 0.1 mg mL−1 is mixed with 40.0 mL of 10.0 mg L−1 4-NA under magnetic stirring for 30 min. Afterwards, 10.0 mL of 0.1 M NaBH4 is introduced to initiate catalytic reduction reactions. A suspension with a volume of 2.0 mL is collected at a given time interval by using a syringe and filtered by passing through a 0.22 μm polyethersulfone film to obtain the solution for measuring optical absorbance at the maximum absorption wavelength using a UV-vis spectrophotometer. For sponge-confined Bi/Ti3C2Tx, it is immersed in 60.0 mL 4-NA solution, and the dosage of NaBH4 is 15.0 mL (Fig. S1†). The reused sponge-confined Bi/Ti3C2Tx is immersed in ethanol and deionized water to achieve recovery.
3 Results and discussion
As can be seen from Fig. S2,† the diffraction peaks at 9.45°, 18.89°, 33.60°, 36.5°, 38.48°, 41.22°, 47.91°, 51.90°, 55.81°, 59.62°, 64.81°, 69.59°, 73.20°, and 74.63° correspond to the (002), (004), (101), (103), (104), (105), (107), (108), (109), (110), (1,0,11), (1,0,12), (118), and (204) planes of hexagonal Ti3AlC2 (JCPDS 52-0875), respectively. The peak of Ti3AlC2 (002) shifts from 9.45° to 7.22° with selective etching of Al, revealing the formation of a Ti3C2Tx MXene.45 For bare Bi, the peaks that appeared at 22.46°, 23.74°, 27.15°, 37.40°, 39.61°, 44.55°, 45.91°, 48.71°, 56.05°, 59.33°, 61.12°, 62.17°, 64.51°, 67.46°, 70.80°, 71.88°, 72.91°, and 74.58° correspond to the (003), (101), (012), (104), (110), (015), (006), (202), (024), (107), (205), (116), (122), (018), (214), (300), (027), and (125) planes of rhombohedral Bi metal (JCPDS 05-0519) (Fig. 1b). The diffraction peaks of Bi metal are clearly detected with the introduction of Ti3C2Tx, proving the coexistence of Bi and Ti3C2Tx. No additional diffraction peaks appear in the patterns of the samples. The Raman spectrum of Bi/Ti3C2Tx is identical to that of Ti3C2Tx, which indicates that Ti3C2Tx is stable during the photodeposition of Bi nanoparticles (Fig. S3†).
According to Fig. 1c, the zeta potential of pristine Ti3C2Tx is −36.1 mV, which enables the electrostatic absorption of Bi3+ onto Ti3C2Tx to afford in situ growth of Bi nanoparticles. The zeta potential of Bi/Ti3C2Tx is −20.7 mV, which is less negative than that of pristine Ti3C2Tx. This can be ascribed to the partial shielding of Bi towards the functional groups of Ti3C2Tx. The sponge is successfully modified with APTES with its zeta potential changing from −5.9 mV to +34.6 mV to enable the electrostatic self-assembly process. As a result, Bi/Ti3C2Tx can be electrostatically confined onto the porous bulk sponge.
High-resolution Bi 4f XPS shows two peaks at 162.24 eV (Bi 4f5/2) and 156.91 eV (Bi 4f7/2) (Fig. 1d), confirming the successful anchoring of Bi on Ti3C2Tx through a facile photodeposition process.46 The Bi 4f XPS spectra of Bi/Ti3C2Tx shift to higher binding energies, which implies that Bi has chemically bonded with Ti3C2Tx. High-resolution Ti 2p XPS spectra can be fitted into eight peaks according to the valence state of Ti ions in Ti3C2Tx (Fig. 1e). The Ti 2p1/2 (462.88 eV, 462.10 eV, and 461.33 eV) and Ti 2p3/2 (457.72 eV, 456.47 eV, and 452.51 eV) XPS spectra are assigned to C–Tiδ+–Tx (δ = 1, 2, and 3).47 Two other peaks of 463.66 eV (2p1/2) and 459.82 eV (2p3/2) are mainly caused by the Ti–O group.48 Correspondingly, the contents of Ti–O bonds for Ti3C2Tx and Bi/Ti3C2Tx obtained from XPS analysis are 11.85% and 12.22%, respectively. The almost unchanged content of Ti–O bonds in Bi/Ti3C2Tx further confirms the stability of Ti3C2Tx during the photodeposition of Bi. The C 1s XPS spectra of Ti3C2Tx have four peaks at 288.40 eV, 286.30 eV, 284.71 eV, and 281.45 eV (Fig. S4†), reflecting the existence of C–F, C–O, C–C, and C–Ti bonds in Ti3C2Tx.49
Ti3C2Tx nanoflakes are confirmed by both SEM and TEM with a size of 50–200 μm (Fig. S5a and b†). Pure Bi particles with a size of 200–800 nm are well crystalized as their crystal faces are clearly exposed (Fig. 2a). It is difficult to observe metallic Bi on Ti3C2Tx (Fig. 2b) due to small particle sizes that are beyond the resolution of SEM. Energy dispersive X-ray (EDX) spectra authenticate the presence of Ti, C, O, Bi, F, and Cl elements in Bi/Ti3C2Tx (Fig. 2b, inset). The porous bulk sponge with a smooth surface is observed (Fig. S5c†), which contributes to absorbing and supporting catalysts. From Fig. 2c, it can be seen that Bi/Ti3C2Tx is fully assembled on the sponge skeleton, verifying the successful synthesis of sponge-confined Bi/Ti3C2Txvia the electrostatic self-assembly process. The shape of sponge-confined Bi/Ti3C2Tx is well preserved (Fig. 2d), which is conductive to practical applications. TEM is further utilized to explore the morphology and microstructure of the samples. As evidently shown in Fig. 2e, Bi nanoparticles are fully anchored on Ti3C2Tx with a mean particle size of 4.4 nm (Fig. 2f), which means that Bi nanoparticles possess high surface energy and can interact with Ti3C2Tx by virtue of their large surface area. The distance of 0.32 nm between two lattice fringes (Fig. 2e and S5d,† insets) matches well with the d value of the Bi (012) plane, which is consistent with phase composition analysis on the basis of XRD.
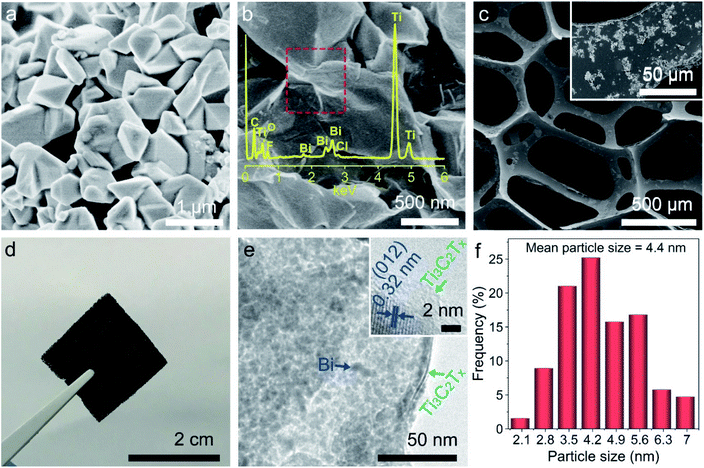 |
| Fig. 2 SEM images of (a) Bi and (b) Bi/Ti3C2Tx (inset is EDX spectra). (c) SEM and (d) photograph of sponge-confined Bi/Ti3C2Tx. (e) TEM images of Bi/Ti3C2Tx (inset shows the high-resolution image). (f) Particle size distribution of Bi nanoparticles anchored on Ti3C2Tx. | |
The catalytic ability of the as-fabricated Bi/Ti3C2Tx powder catalysts is assessed by catalyzing NaBH4 to transform 4-nitroaniline (4-NA) into p-phenylenediamine (PPD) (Fig. S6†). Fig. 3a shows the catalytic activities of 4-NA under various systems. The adsorption capacities of Ti3C2Tx, Bi, and Bi/Ti3C2Tx for 4-NA are 7.21%, 8.06%, and 11.38%, respectively. NaBH4 alone does not hydrogenate 4-NA, revealing the essential role of the catalyst. This is because the reduction of nitroarenes with NaBH4 is kinetically impeded by the high activation barrier.50 Apparently, 4-NA is completely reduced to PPD by NaBH4 within 6 min over Bi–1.0% Ti3C2Tx, while the conversion rate reaches only 58.21% for pristine metallic Bi. Thus, the role of Ti3C2Tx in strengthening the conversion of Bi towards reducing 4-NA is confirmed, which generally comes from the high surface-to-volume ratio of Ti3C2Tx supported Bi nanoparticles.
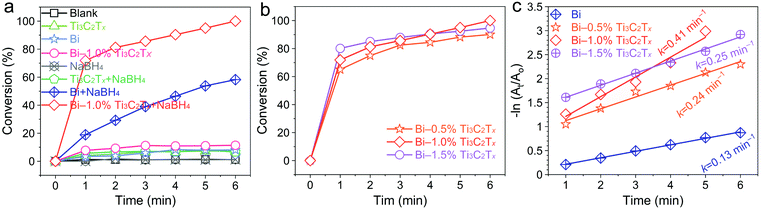 |
| Fig. 3 (a) Catalytic hydrogenation of 4-NA in various systems. The effect of Ti3C2Tx content in Bi/Ti3C2Tx on the catalytic activity (b) and corresponding pseudo-first-order kinetic plots (c). | |
The effect of the contents of Ti3C2Tx in Bi/Ti3C2Tx on catalytic activity is also investigated (Fig. 3b). The optimum weight ratio of Ti3C2Tx to Bi is 1.0% and both decreasing and increasing the weight ratio of Ti3C2Tx lead to the deterioration of catalytic activity. The reason may be that a lower Ti3C2Tx loading (0.5%) is unable to disperse metallic Bi well to efficiently expose active sites, while a high Ti3C2Tx loading amount (1.5%) hinders metallic Bi nanoparticles from catalyzing NaBH4. According to the fitted pseudo-first-order kinetic plots for Bi/Ti3C2Tx with vary loading amounts of Ti3C2Tx (Fig. 3c), Bi–1.0% Ti3C2Tx possesses the largest apparent reaction rate constant of 0.41 min−1, which is three times larger than that of pristine Bi and is comparable to that of noble metal-based catalysts (Table S1†). Additionally, Bi–1.0% Ti3C2Tx also shows enhanced catalytic activity for the hydrogenation of 3-nitroaniline (3-NA), 2-nitroaniline (2-NA), 4-nitroanisole, and 4-nitrotoluene (Fig. S7†).
For comparison, Bi/rGO counterparts have been prepared in a similar process. XPS (Fig. S8†) and SEM (Fig. S9†) confirm the successful growth of metallic Bi onto GO and the electrostatic self-assembly between Bi–1.0% rGO and the APTES-modified sponge, respectively. The conversion (%) of 4-NA within 6 min over Bi–1.0% rGO powder is 80.6%, which is smaller than that of Bi–1.0% Ti3C2Tx (99.5%) (Fig. 4a). Additionally, as shown in Fig. S10,† the adsorption ability of Bi–1.0% Ti3C2Tx for 4-NA (11.3%) is higher than that of Bi–1.0% rGO (5.9%). We further employ characterization technologies to gain insight into the factors that differentiate catalytic activity between the two catalysts. Based on nitrogen adsorption–desorption analysis (Fig. S11†), the specific surface area and total pore volume of Bi–1.0% rGO (100.5 m2 g−1 and 0.05 cm3 g−1) are larger than those of Bi–1.0% Ti3C2Tx (64.2 m2 g−1 and 0.04 cm3 g−1) and Bi (5.5 m2 g−1 and 0.03 cm3 g−1) (Table S2†). Besides, the mean particle size of Bi nanoparticles in Bi–1.0% rGO is 1.46 nm (Fig. S12†), which is smaller than that of Bi–1.0% Ti3C2Tx (4.4 nm). Theoretically, the fully dispersed Bi nanoparticles on rGO with abundant active sites ought to be more catalytically active. The conversion rates and turnover efficiency (TOF) on the basis of the loading of Bi nanoparticles for Bi–1.0% rGO and Bi–1.0% Ti3C2Tx are 0.552 mmol gBi−1 min−1 (6.92 NP−1 h−1) and 0.642 mmol gBi−1 min−1 (8.05 NP−1 h−1), respectively (Fig. 4b, Table S3†), which contradicts specific surface area and pore size analyses. It is reasonable to conclude that the enhanced catalytic ability of Bi–1.0% Ti3C2Tx compared to Bi–1.0% rGO originates from the better hydrophilicity as confirmed by the contact angle measurements (Fig. 4c). This is because rGO possesses low-content hydrophilic surface functional groups (Fig. S13†).
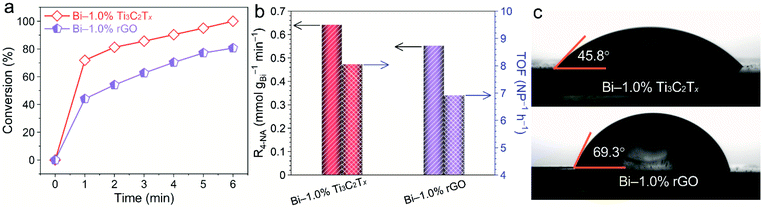 |
| Fig. 4 (a) The time on-line conversion curves of 4-NA and (b) 4-NA conversion rates and TOF over Bi–1.0% Ti3C2Tx and Bi–1.0% rGO powders. (c) Contact angles of Bi–1.0% Ti3C2Tx and Bi–1.0% rGO with water. | |
The catalytic activities of the bulk sponge-confined Bi–1.0% Ti3C2Tx and Bi–1.0% rGO are assessed by reducing 4-NA, 3-NA, and 2-NA. Evidently, the catalytic activity of sponge-confined Bi–1.0% Ti3C2Tx is superior to that of sponge-confined Bi–1.0% rGO (Fig. S14†), which is due to the favourable wettability of Bi/Ti3C2Tx. Fig. 5 shows the durability test of the sponge-confined catalysts. The catalytic activities of sponge-confined Bi–1.0% Ti3C2Tx are well sustained after being successively used ten times, while the sponge-confined Bi–1.0% rGO shows considerably diminished catalytic activities. The durability of pristine Bi, Bi–1.0% Ti3C2Tx and Bi–1.0% rGO is also examined. The conversion (%) of 4-NA over Bi–1.0% Ti3C2Tx and Bi–1.0% rGO is nearly unchanged after five successive cycles of catalytic reactions (Fig. S15†), while it diminishes after each cycle for Bi, which suggests that Ti3C2Tx and rGO can stabilize Bi. This is a result of the strongly interfacial chemical interaction between Bi and Ti3C2Tx (rGO). With the combination of durability tests among Bi–1.0% Ti3C2Tx, Bi–1.0% rGO, sponge-confined Bi–1.0% Ti3C2Tx, and sponge-confined Bi–1.0% rGO, it can be concluded that the decrease in catalytic activities for sponge-confined Bi–1.0% rGO can be ascribed to the loss of Bi–1.0% rGO (Fig. S16†). The zeta potential of Bi–1.0% rGO (−14.31 mV) is less negative than that of Bi–1.0% Ti3C2Tx (−20.71 mV) (Fig. 1c), which cannot afford strong electrostatic force to powerfully confine Bi–1.0% rGO on the APTES-modified sponge.
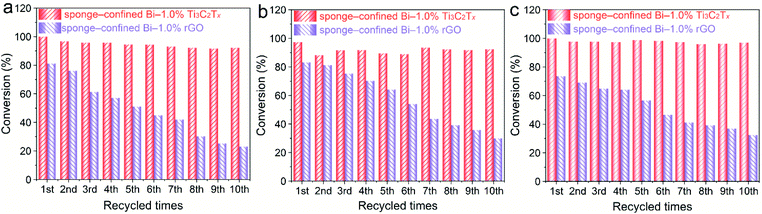 |
| Fig. 5 Cycling tests for the conversion of (a) 4-NA, (b) 3-NA, and (c) 2-NA over sponge-confined Bi–1.0% Ti3C2Tx and Bi–1.0% rGO. | |
With the overall consideration of the analyses mentioned above, a credible mechanism for the hydrogenation of nitroarenes over the sponge-confined Bi/Ti3C2Tx is proposed1,51 and schematically elucidated in Fig. 6. Firstly, BH4− reacts with water to generate BO2− and highly active H−, followed by the swift adherence of the latter to Bi/Ti3C2Tx to form Bi–H species. Secondly, nitroarenes are absorbed onto Bi/Ti3C2Tx with their –NO2 selectively getting close to the Bi–H species. Thirdly, the –NO2 of nitroarenes reacts with Bi–H species via electron and mass transfer processes to form –NH2. Finally, the reduced products are released from Bi/Ti3C2Tx to liberate active sites for the next catalytic cycle. It should be noted that the interfacial chemical interaction-derived stabilization of Bi with Ti3C2Tx, the effective electrostatic confinement of the APTES-modified sponge towards Bi/Ti3C2Tx, and the high wettability of Ti3C2Tx account for the improved durability, viable recyclability, and superior catalytic activity, respectively.
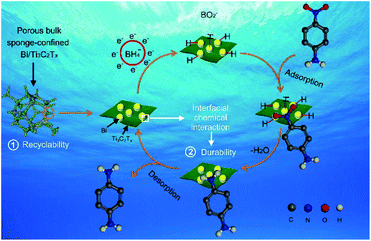 |
| Fig. 6 The catalytic mechanism for the reduction of 4-NA over sponge-confined Bi/Ti3C2Tx. | |
4 Conclusions
In summary, a sponge-confined Bi/Ti3C2Tx catalyst is synthesized via the photodeposition of metallic Bi nanoparticles on Ti3C2Tx and the strong electrostatic self-assembly between the negatively charged Bi/Ti3C2Tx and APTES-modified sponge. The anchoring of metallic Bi nanoparticles on Ti3C2Tx enables both the efficient utilization of active sites for strengthening catalytic activity and chemically stabilized catalytic durability. In comparison with rGO, Ti3C2Tx with abundant hydrophilic surface groups as the support for attaching Bi nanoparticles favors both efficient aqueous catalytic reactions and electrostatic interaction-derived recyclability. This study is expected to offer new strategy for designing cost-effective, stable, and easily recyclable integrated catalysts on the basis of economically porous bulk and 2D materials for catalytic reactions.
Author contributions
Changqiang Yu: methodology, conceptualization, investigation, formal analysis, and writing – original draft. Linfen Peng: resources, investigation, and visualization. Yisong Zhu: resources. Guanshun Xie: resources. Zhenjun Wu: resources. Xiuqiang Xie: project administration, supervision, and writing – review & editing. Nan Zhang: project administration, supervision, and writing – review & editing.
Conflicts of interest
There are no conflicts to declare.
Acknowledgements
The work was supported by the National Natural Science Foundation of China (52071137, 51977071, 51802040, and 21802020) and Natural Science Foundation of Hunan (2020JJ3004 and 2020JJ4192). N. Z. also acknowledges the financial support of the Fundamental Research Funds for the Central Universities. C. Yu thanks Fei Song for his assistance with the schematics design.
Notes and references
- Y. T. Yang, K. D. Jiang, J. Guo, J. Li, X. L. Peng, B. Hong, X. Q. Wang and H. L. Ge, Chem. Eng. J., 2020, 381, 122596 Search PubMed.
- P. Veerakumar, N. Dhenadhayalan, K. C. Lin and S. B. Liu, J. Mater. Chem. A, 2015, 3, 23448–23457 Search PubMed.
- Q. Yan, X.-Y. Wang, J.-J. Feng, L.-P. Mei and A.-J. Wang, J. Colloid Interface Sci., 2021, 582, 701–710 Search PubMed.
- X. Q. Qiu, Q. W. Liu, M. X. Song and C. J. Huang, J. Colloid Interface Sci., 2016, 477, 131–137 Search PubMed.
- N. Zhang and Y. J. Xu, Chem. Mater., 2013, 25, 1979–1988 Search PubMed.
- R. Das, V. S. Sypu, H. K. Paumo, M. Bhaumik, V. Maharaj and A. Maity, Appl. Catal., B, 2019, 244, 546–558 Search PubMed.
- Z. Hasan, D. W. Cho, C. M. Chon, K. Yoon and H. Song, Chem. Eng. J., 2016, 298, 183–190 Search PubMed.
- M. K. Dixit, D. Chery, C. Mahendar, C. Bucher and M. Dubey, Inorg. Chem. Front., 2020, 7, 991–1002 Search PubMed.
- J. Park, G. D. Saratale, S. K. Cho and S. Bae, Sci. Total Environ., 2020, 705, 134544 Search PubMed.
- J. Y. Yeh, B. M. Matsagar, S. S. Chen, H. L. Sung, D. C. W. Tsang, Y. P. Li and K. C. W. Wu, J. Catal., 2020, 390, 46–56 Search PubMed.
- K. Hareesh, R. P. Joshi, D. V. Sunitha, V. N. Bhoraskar and S. D. Dhole, Appl. Surf. Sci., 2016, 389, 1050–1055 Search PubMed.
- Y. Cui, K. B. Ma, Z. Chen, J. L. Yang, Z. G. Geng and J. Zeng, J. Catal., 2020, 381, 427–433 Search PubMed.
- N. Maity, A. Sahoo, R. Boddhula, S. Chatterjee, S. Patra and B. B. Panda, Dalton Trans., 2020, 49, 11019–11026 Search PubMed.
- H. Saikia, B. J. Borah, Y. Yamada and P. Bharali, J. Colloid Interface Sci., 2017, 486, 46–57 Search PubMed.
- T. A. Revathy, S. Dhanavel, T. Sivaranjani, V. Narayanan, T. Maiyalagan and A. Stephen, Appl. Surf. Sci., 2018, 449, 764–771 Search PubMed.
- E. Herrera, M. S. Aprea, J. S. Riva, O. F. Silva, P. G. Bercoff and A. Granados, Appl. Surf. Sci., 2020, 529, 147029 Search PubMed.
- B. Bhaduri and T. Polubesova, Mater. Lett., 2020, 267, 127546 Search PubMed.
- Y. Junejo, M. Safdar, M. A. Akhtar, M. Saravanan, H. Anwar, M. Babar, R. Bibi, M. T. Pervez, T. Hussain and M. E. Babar, J. Inorg. Organomet. Polym. Mater., 2019, 29, 111–120 Search PubMed.
- H. Chen, C. Liu, M. Wang, C. Zhang, N. Luo, Y. Wang, H. Abroshan, G. Li and F. Wang, ACS Catal., 2017, 7, 3632–3638 Search PubMed.
- W. Yue, M. F. Hao, B. Yu, R. Z. Ouyang and Y. Q. Miao, Nanotechnology, 2020, 31, 145717 Search PubMed.
- J. K. Zhou, J. P. Gao, X. Y. Xu, W. Hong, Y. H. Song, R. N. Xue, H. L. Zhao, Y. Liu and H. X. Qiu, J. Alloys Compd., 2017, 709, 206–212 Search PubMed.
- C. Yu, Z. Tong, S. Li and Y. Yin, Mater. Lett., 2019, 240, 161–164 Search PubMed.
- C. Yu, M. Wen, Z. Tong, S. Li, Y. Yin, X. Liu, Y. Li, T. Liang, Z. Wu and D. D. Dionysiou, Beilstein J. Nanotechnol., 2020, 11, 407–416 Search PubMed.
- D. B. Jiang, X. Y. Liu, Y. S. Yuan, L. Feng, J. Y. Ji, J. S. Wang, D. Losic, H. C. Yao and Y. X. Zhang, Chem. Eng. J., 2020, 383, 123156 Search PubMed.
- J. Y. Liu, H. Xu, H. P. Li, Y. H. Song, J. J. Wu, Y. J. Gong, L. Xu, S. Q. Yuan, H. M. Li and P. M. Ajayan, Appl. Catal., B, 2019, 243, 151–160 Search PubMed.
- X. D. Wang, J. He, J. Y. Li, G. Lu, F. Dong, T. Majima and M. S. Zhu, Appl. Catal., B, 2020, 277, 119230 Search PubMed.
- Y. Zhang and S. J. Park, Chem. Eng. J., 2019, 369, 353–362 Search PubMed.
- B. Han, Y. L. Zhang, L. Zhu, Y. Li, Z. C. Ma, Y. Q. Liu, X. L. Zhang, X. W. Cao, Q. D. Chen, C. W. Qiu and H. B. Sun, Adv. Mater., 2019, 31, 1806386 Search PubMed.
- Y. Fu, T. Mei, G. Wang, A. K. Guo, G. C. Dai, S. Wang, J. Y. Wang, J. H. Li and X. B. Wang, Appl. Therm. Eng., 2017, 114, 961–968 Search PubMed.
- Y. X. Duan, K. H. Liu, Q. Zhang, J. M. Yan and Q. Jiang, Small Methods, 2020, 4, 1900846 Search PubMed.
- B. K. Barman, B. Sarkar, R. Nandan and K. K. Nanda, New J. Chem., 2021, 45, 1556–1564 Search PubMed.
- X. Q. Xie, N. Zhang, Z. R. Tang, M. Anpo and Y. J. Xu, Appl. Catal., B, 2018, 237, 43–49 Search PubMed.
- M. Naguib, M. Kurtoglu, V. Presser, J. Lu, J. J. Niu, M. Heon, L. Hultman, Y. Gogotsi and M. W. Barsoum, Adv. Mater., 2011, 23, 4248–4253 Search PubMed.
- V. Kamysbayev, A. S. Filatov, H. C. Hu, X. Rui, F. Lagunas, D. Wang, R. F. Klie and D. V. Talapin, Science, 2020, 369, 979–983 Search PubMed.
- X. Q. Xie and N. Zhang, Adv. Funct. Mater., 2020, 30, 2002528 Search PubMed.
- Y. Liu, Y.-H. Li, X. Li, Q. Zhang, H. Yu, X. Peng and F. Peng, ACS Nano, 2020, 14, 14181–14189 Search PubMed.
- S. Min, Y. Xue, F. Wang, Z. Zhang and H. Zhu, Chem. Commun., 2019, 55, 10631–10634 Search PubMed.
- L. Liu, Q. Zhao, R. Liu and L. Zhu, Appl. Catal., B, 2019, 252, 198–204 Search PubMed.
- F. Song, G. H. Li, Y. S. Zhu, Z. J. Wu, X. Q. Xie and N. Zhang, J. Mater. Chem. A, 2020, 8, 18538–18559 Search PubMed.
- J. X. Low, B. Z. Dai, T. Tong, C. J. Jiang and J. G. Yu, Adv. Mater., 2019, 31, 1802981 Search PubMed.
- E. Jeong, J. Byun, B. Bayarkhuu and S. W. Hong, Appl. Catal., B, 2021, 282, 119587 Search PubMed.
- C. L. Li, M. C. Wu and R. Liu, Appl. Catal., B, 2019, 244, 150–158 Search PubMed.
- J. Yang, X. Wang, B. Li, L. Ma, L. Shi, Y. Xiong and H. Xu, Adv. Funct. Mater., 2017, 27, 1606497 Search PubMed.
- X. Q. Xie, Z. J. Wu and N. Zhang, Chin. Chem. Lett., 2020, 31, 1014–1017 Search PubMed.
- J. Li, X. T. Yuan, C. Lin, Y. Q. Yang, L. Xu, X. Du, J. L. Xie, J. H. Lin and J. L. Sun, Adv. Energy Mater., 2017, 7, 1602725 Search PubMed.
- Q. Hao, R. T. Wang, H. J. Lu, C. A. Xie, W. H. Ao, D. M. Chen, C. Ma, W. Q. Yao and Y. F. Zhu, Appl. Catal., B, 2017, 219, 63–72 Search PubMed.
- X. Q. Xie, C. Chen, N. Zhang, Z. R. Tang, J. J. Jiang and Y. J. Xu, Nat. Sustain., 2019, 2, 856–862 Search PubMed.
- T. T. Hou, Q. Q. Luo, Q. Li, H. L. Zu, P. X. Cui, S. W. Chen, Y. Lin, J. J. Chen, X. S. Zheng, W. K. Zhu, S. Q. Liang, J. L. Yang and L. B. Wang, Nat. Commun., 2020, 11, 4251 Search PubMed.
- T. Cai, L. L. Wang, Y. T. Liu, S. Q. Zhang, W. Y. Dong, H. Chen, X. Y. Yi, J. L. Yuan, X. N. Xia, C. B. Liu and S. L. Luo, Appl. Catal., B, 2018, 239, 545–554 Search PubMed.
- K. Peng, L. J. Fu, H. M. Yang, J. Ouyang and A. D. Tang, Nano Res., 2017, 10, 570–583 Search PubMed.
- X. Y. Yang, Y. Li, P. Zhang, R. M. Zhou, H. L. Peng, D. Liu and J. Z. Gui, ACS Appl. Mater. Interfaces, 2018, 10, 23154–23162 Search PubMed.
Footnote |
† Electronic supplementary information (ESI) available. See DOI: 10.1039/d1ta02736k |
|
This journal is © The Royal Society of Chemistry 2021 |
Click here to see how this site uses Cookies. View our privacy policy here.