DOI:
10.1039/D1CE01184G
(Paper)
CrystEngComm, 2022,
24, 107-118
Morphology evolution of primary Mg2Si in Ca-modified Al–Mg2Si alloy with various contents of Mg/Si
Received
2nd September 2021
, Accepted 20th October 2021
First published on 9th November 2021
Abstract
The combined influence of Mg/Si and Ca contents on the crystallization of primary Mg2Si in Al–Mg2Si alloy is investigated. Embryo formation of primary Mg2Si can be restricted by the addition of Ca while the restricted effect is weakened by increasing the content of Mg/Si, and content of Ca for over-modification is increased with the increased Mg/Si content. Growth of primary Mg2Si is encouraged with the increasing content of Mg/Si, while the addition of Ca can restrict the growth rate directionally in Ca-modified Al–Mg2Si alloy, which leads to the morphology evolution of primary Mg2Si. The serious inhibition effect on the whole crystallization process of primary Mg2Si caused by increasing the content of Ca is the main reason for the occurrence of over-modification. Dice-like primary Mg2Si is prepared successfully in the over-modified alloy for the first time. The tip-growth process of the dice-like primary Mg2Si is revealed, which is completed by 2-D nucleation growth. The study provides a novel method to control the morphology and particle size of primary Mg2Si, which can further help understand the crystallization process of the crystal.
1. Introduction
Controlling crystal morphology is a critical technique for improving the chemical and physical properties of materials.1–3 Therefore, the preparation of materials with controllable morphology and structure is gaining extensive research in the fields of mechanics, catalysis, electronics, and biotechnology.4,5 It is well known that the final morphology of a crystal is mainly determined by environmental factors. Crystal structure and morphology can be controlled by changing many conditions such as growth temperature, supersaturation, and additives.6–8
Nowadays, light-weight materials such as Al alloy dominate the field of industrial production.9 As the only reinforcement of Al–Mg2Si alloy, intermetallic compound Mg2Si exhibits low density (1.99 × 103 kg m−3), high melting temperature (1085 °C), high hardness (4.5 × 109 N m−2), and high elastic modulus (120 GPa).10–12 Thus, Al–Mg2Si alloy is widely used for automobile, aerospace, and corrosion-resistant materials.13–15 However, coarse dendritic primary Mg2Si usually exists in the Al–Mg2Si alloy during the equilibrium solidification process, which damages the mechanical property of the alloy.16,17 Controlling the morphology and particle size of primary Mg2Si is beneficial for preparing novel Al–Mg2Si alloy, which broadens the application scope of the alloy.18–22
According to the crystallography theory, primary Mg2Si morphology is determined by the ratio of growth rates along <100> and <111> directions, i.e., R = V<100>/V<111>: if
, a dendrite is formed; if
, an octahedron can be achieved; whereas if
, a truncated octahedron can be achieved; if
, a truncated cube is prepared and if
, a cube is formed.26,27 Normally, the morphology evolution of primary Mg2Si is completed by only regulating the content of modifiers (e.g., Sr, Sb, P, and Ca–Sb) in Al–Mg2Si alloy.23–28 With the addition of the modifier, the modifier atoms preferentially adsorb on the {100} facets of primary Mg2Si, growth rates along <100> directions are retarded, the value of R is also changed.23,24 Octahedral, truncated octahedral, truncated cubic, and cubic primary Mg2Si have been prepared successfully.29,30 Among them, primary Mg2Si with truncated octahedral morphology can further transform to spherical by T6 heat-treatment, and the mechanical property of the alloy can be improved significantly.29 Based on the Al–Mg2Si pseudo binary phase diagram, the microstructure of Al–Mg2Si alloy is affected by controlling the content of Mg/Si, and morphology and particle size of primary Mg2Si are also changed.17 However, the combined influence of Mg/Si composition and the modifier content on the crystallization process of primary Mg2Si in Al–Mg2Si alloy is still unknown. In addition, with some modifiers such as La and Y, dendritic primary Mg2Si can be formed again by increasing the content of the modifier, which is called over-modification.16–31 Nowadays, the commonly accepted over-modification mechanism is explored only from the perspective of primary Mg2Si growth: the modifier can participate in the formation of some compounds before the crystallization of primary Mg2Si in Al–Mg–Si alloy, and the reduced amount of effective modifier atoms adsorb on the {100} facets of primary Mg2Si in the growth process and a weakened modification effect happens.32 It is well known that nucleation and growth processes of primary Mg2Si can be influenced by the addition of the modifier.33–35 Therefore, the over-modification phenomenon is attributed to the combined effect of the modifier on nucleation and growth processes of primary Mg2Si. However, research on investigating the over-modification mechanism from the aspects of nucleation and growth has been rather limited.
In our previous study, the over-modification phenomenon can be observed in Ca-modified Al–Mg2Si alloy.31,32 Therefore, by simultaneously regulating the contents of Mg/Si and Ca in Al–Mg2Si alloy, the combined influence of Mg/Si and Ca compositions on the crystallization process of primary Mg2Si in Al–Mg2Si alloy is investigated. The over-modification mechanism of Ca-modified primary Mg2Si from the aspects of nucleation and growth is revealed. Dice-like dendritic primary Mg2Si is prepared in the over-modified alloy, and the corresponding growth process is investigated, which is called the tip-growth process. This research will be a big step forward in realizing the artificial manipulation of crystal morphology and particle size of primary Mg2Si, which is essential to enrich the methods for controlling the morphology of primary Mg2Si.
2. Experimental section
2.1 Preparation of Ca-modified Al–Mg2Si alloy with various contents of Mg/Si
Pure Al ingot (99.98 wt% purity), pure Mg ingot (99.85 wt% purity), and Al–24.4Si master alloy were used as raw materials to prepare the Al–Mg2Si alloy. The total masses of the added Mg/Si are 15, 17, and 19 wt%, with the added Mg/Si molar ratios of 2/1 (Al–xMg2Si (x = 15, 17, 19) alloy). Mg–30Ca master alloy was the modifier of the alloy. Al ingot and Al–24.4Si master alloy were melted at 770 °C in a graphite crucible in an electric resistance furnace at 7 kW; then, pure Mg ingot and Mg–30Ca master alloy preheated at 150 °C in a vacuum oven were added to the molten alloy. The contents of added Ca were 0, 0.1, 0.2, and 0.3 wt% in Al–15Mg2Si alloy, the contents of Ca in Al–17Mg2Si alloy were 0, 0.1, 0.2, 0.3, and 0.4 wt%, and the contents of Ca in Al–19Mg2Si alloy were 0, 0.1, 0.2, 0.3, 0.4, 0.5, and 0.6 wt%. After manual agitation for about 2 min and holding the temperature at 770 °C for 20 min, the Al–Mg–Si melts were poured into a steel mold at room temperature to produce Ca-modified Al–Mg2Si alloy with various contents of Mg/Si.
2.2 Characterization
Metallographic samples with a size of 10 mm × 10 mm were cut at the bottom of the sample. The metallographic samples were prepared by the standard procedure of ASTM E3-2007, and then etched with 0.5% HF (in vol.) for about 15 s at room temperature. To observe the morphology of primary Mg2Si, samples with a size of 1.2 mm × 12 mm were dissolved in a 30 vol% HNO3 distilled water solution to remove the Al coating on the surface of the primary Mg2Si crystal. The phase compositions of the samples were conducted by X-ray diffraction (XRD) (X'Pert3 Powder, PANalytical, Holland) using CuKα radiation (λ = 1.5406) in step mode from 20° to 80° with a scanning speed of 4° min−1 and an acquisition step of 0.02° (2θ). The microstructure of Ca-modified Al–xMg2Si (x = 15, 17, 19) alloy was observed by optical microscopy (OM) (Axiovert 200 MAT, Carl Zeiss, Germany). The morphology of the extracted primary Mg2Si and element line scanning spectra were observed using a scanning electron microscope (SEM) (S-3400 N, HITACHI, Japan) equipped with an energy dispersive spectrometer analyzer (EDS). Differential scanning calorimetry (DSC25, TA Instruments Inc., USA) was conducted under argon flow (100 ml min−1) in the temperature range of 200–800 °C with a rate of 10 °C min−1 during the cooling process. The particle size distribution was calculated by Nano Measurer. The diagonal length of primary Mg2Si was measured in five optical microscope images to compute the average particle size of primary Mg2Si, and the magnification of the optical microscope image used for particle size distribution statistics was ×200. Brinell hardness of the prepared materials is measured using HB-3000C, China. The applied load is 4903 N, diameter of the pressure ball is 10 mm, pressure application time is 8 s, and the pressure holding time is 30 s. The Brinell hardness test is generally repeated five times to ensure the reproducibility of the test.
3. Results and discussions
3.1 Morphology evolution of primary Mg2Si in Al–xMg2Si (x = 15, 17, 19) alloys
XRD patterns of Al–xMg2Si (x = 15, 17, 19) alloys are shown in Fig. 1(a)–(c). The alloy only consists of Al and Mg2Si phases regardless of the contents of Ca and Mg/Si. Typical 2-D morphology of primary Mg2Si in Ca-modified Al–15Mg2Si alloy is shown in Fig. 2. Corresponding particle size statistics of primary Mg2Si are also given in Fig. 3. In Al–15Mg2Si alloy, the 2-D morphology of primary Mg2Si is polyhedral (Fig. 2(a)–(c)) with the content of Ca increasing from 0 to 0.2 wt%. However, dendritic primary Mg2Si is observed in 0.3 wt% Ca-modified Al–15Mg2Si alloy (Fig. 2(d)), which means that the over-modification phenomenon appears. The particle size of primary Mg2Si increases from 10.2 to 31.0 and to 35.1 and finally to 46.5 μm with the Ca content increasing from 0 to 0.1 and to 0.2 and finally to 0.3 wt% (Fig. 3(a)–(e)), respectively. In Al–17Mg2Si alloy, the 2-D morphology of primary Mg2Si is still polyhedral (Fig. 4(a)–(d)) with the content of Ca increasing from 0 to 0.3 wt%. The corresponding particle size increases indistinctly as compared to Al–15Mg2Si alloy, which is changed from 17.8 to 22.9 and to 24.8 and finally to 29.6 μm (Fig. 5(a)–(f)). Interestingly, the Ca content for over-modification is increased to 0.4 wt% with the Mg/Si content increasing to 17 wt%, and dendritic primary Mg2Si with the particle size of 48.7 μm is formed in the over-modified alloy (Fig. 4(e) and 5(e) and (f)). In Al–19Mg2Si alloy, dendritic primary Mg2Si with a size of 121.4 μm exists in Ca-free alloy (Fig. 6(a) and 7(a)); polyhedral primary Mg2Si is formed, and particle size decreases to 32.7 μm in 0.1 wt% Ca-modified Al–19Mg2Si alloy (Fig. 6(b) and 7(b)). The 2-D morphology of primary Mg2Si is polyhedral, and the particle size further decreases to ∼27 μm and keeps unchanged with the Ca content increasing from 0.2 to 0.5 wt% (Fig. 6(c)–(f) and 7(c)–(f)). It is worth noting that the content of Ca for over-modification is further increased to 0.6 wt% with the content of Mg/Si increasing to 19 wt%, and dendritic primary Mg2Si with the particle size of 63.8 μm is formed (Fig. 6(g) and 7(g) and (h)).
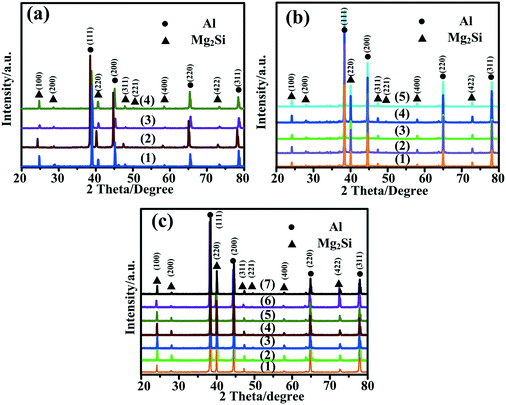 |
| Fig. 1 (a) XRD of Al–15Mg2Si alloys modified with (1) 0.0, (2) 0.1, (3) 0.2, and (4) 0.3 wt% Ca; (b) XRD of Al–17Mg2Si alloys modified with (1) 0.0, (2) 0.1, (3) 0.2, (4) 0.3, and (5) 0.4 wt% Ca; (c) XRD of Al–19Mg2Si alloys modified with (1) 0.0, (2) 0.1, (3) 0.2, (4) 0.3, (5) 0.4, (6) 0.5, and (7) 0.6 wt% Ca. | |
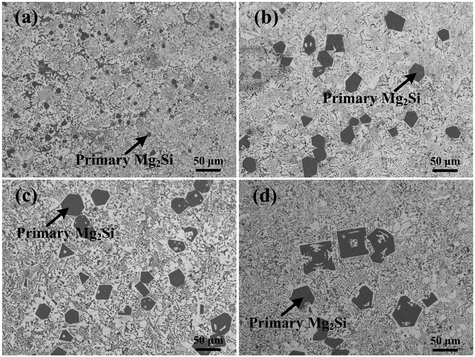 |
| Fig. 2 OM images (×200) of primary Mg2Si in Al–15Mg2Si alloys modified with (a) 0, (b) 0.1, (c) 0.2, and (d) 0.3 wt% Ca. | |
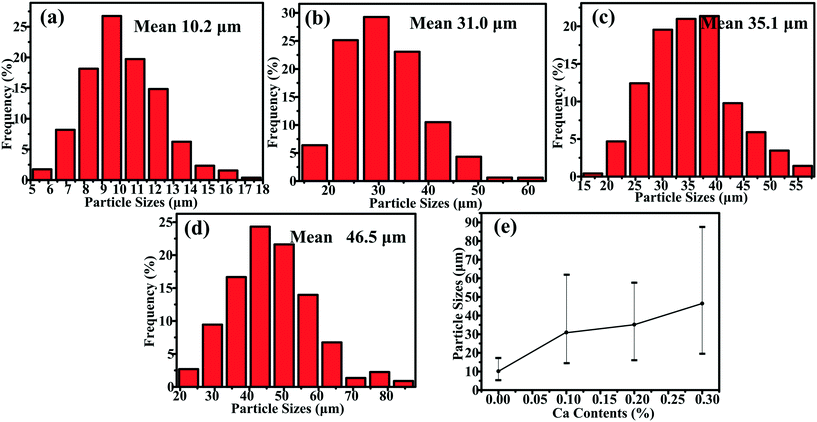 |
| Fig. 3 Particle size statistics of primary Mg2Si in Al–15Mg2Si alloys modified with (a) 0.0, (b) 0.1, (c) 0.2, (d) 0.3 wt% Ca and (e) particle size summary of Ca-modified Al–15Mg2Si alloys. | |
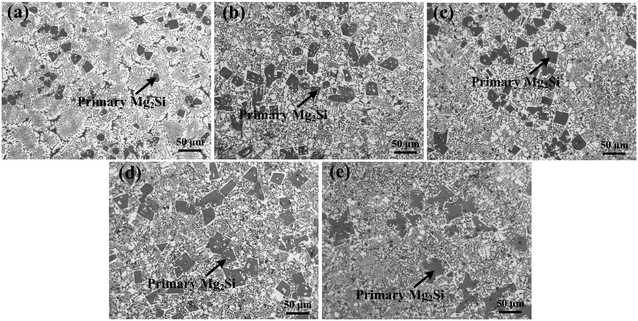 |
| Fig. 4 OM images (×200) of primary Mg2Si in Al–17Mg2Si alloys modified with (a) 0, (b) 0.1, (c) 0.2, (d) 0.3, and (e) 0.4 wt% Ca. | |
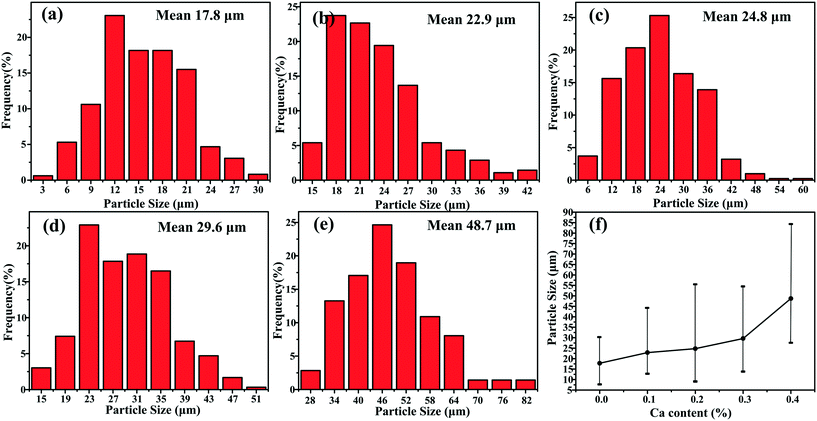 |
| Fig. 5 Particle size statistics of primary Mg2Si in Al–17Mg2Si alloys modified with (a) 0.0, (b) 0.1, (c) 0.2, (d) 0.3, (e) 0.4 wt% Ca and (f) particle size summary of Ca-modified Al–17Mg2Si alloys. | |
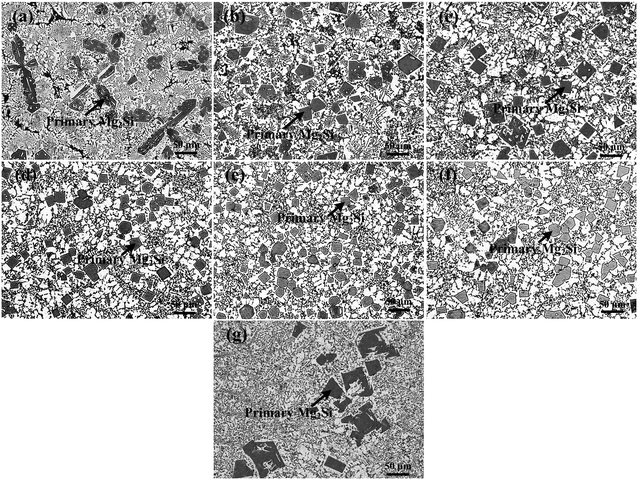 |
| Fig. 6 OM images (×200) of primary Mg2Si in Al–19Mg2Si alloys modified with (a) 0, (b) 0.1, (c) 0.2, (d) 0.3, (e) 0.4, (f) 0.5, and (g) 0.6 wt% Ca. | |
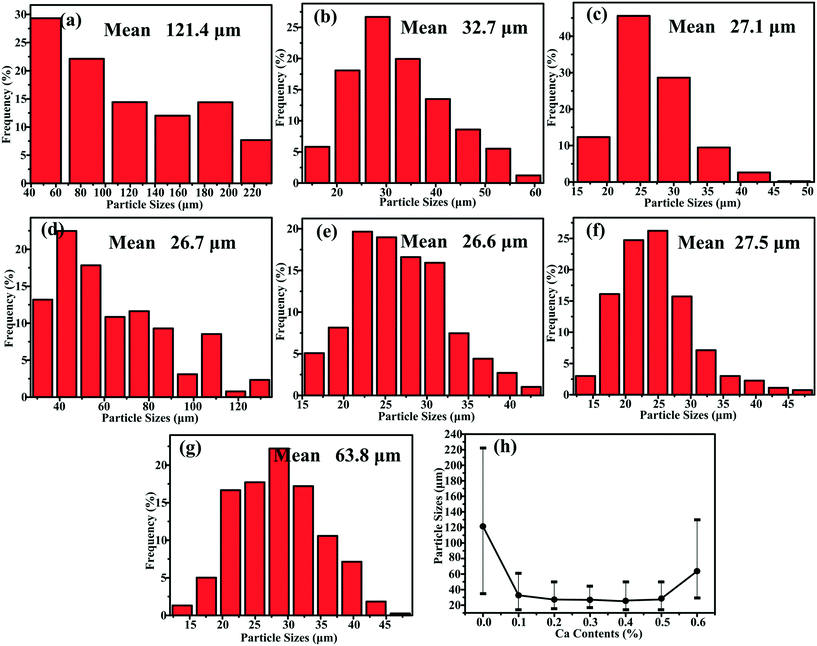 |
| Fig. 7 Particle size statistics of primary Mg2Si in Al–19Mg2Si alloys modified with (a) 0.0, (b) 0.1, (c) 0.2, (d) 0.3, (e) 0.4, (f) 0.5, (g) 0.6 wt% Ca and (h) particle size summary of Ca-modified Al–19Mg2Si alloys. | |
Typical 3-D morphology of primary Mg2Si in Ca-modified Al–15Mg2Si alloy is shown in Fig. 8. Truncated octahedral primary Mg2Si is formed in Ca-free Al–15Mg2Si alloy (Fig. 8(a)). In 0.1 wt% Ca-modified Al–15Mg2Si alloy, the morphology of primary Mg2Si is still retained as truncated octahedral while the exposed area of the (001) surface is increased significantly (Fig. 8(b)). Morphology of primary Mg2Si transforms to a truncated cube (Fig. 8(c)) with the Ca content increasing to 0.2 wt%. Interestingly, dice-like primary Mg2Si exist in the 0.3 wt% Ca-modified Al–15Mg2Si alloy (Fig. 8(d)). In Ca-free Al–17Mg2Si alloy, octahedral primary Mg2Si is formed (Fig. 9(a)). With the content of Ca increasing to 0.1 wt%, the morphology of primary Mg2Si transforms to a truncated octahedron (Fig. 9(b)). Cubic primary Mg2Si exists in 0.2 and 0.3 wt% Ca-modified Al–Mg2Si alloys (Fig. 9(c) and (d)). Finally, dice-like primary Mg2Si is formed with the content of Ca further increasing to 0.4 wt% in Al–17Mg2Si alloy (Fig. 9(e)). Different from the Al–15Mg2Si and Al–17Mg2Si alloys, dendritic primary Mg2Si exists in Ca-free Al–19Mg2Si alloy (Fig. 10(a)). Morphology of primary Mg2Si transforms to octahedron with the addition of 0.1 wt% Ca in Al–19Mg2Si alloy (Fig. 10(b)). Morphology of primary Mg2Si further transforms to a cube when the content of Ca increases from 0.2 to 0.5 wt% (Fig. 10(c)–(f)). Finally, dice-like primary Mg2Si is formed in 0.6 wt% Ca-modified Al–19Mg2Si alloy (Fig. 10(g)).
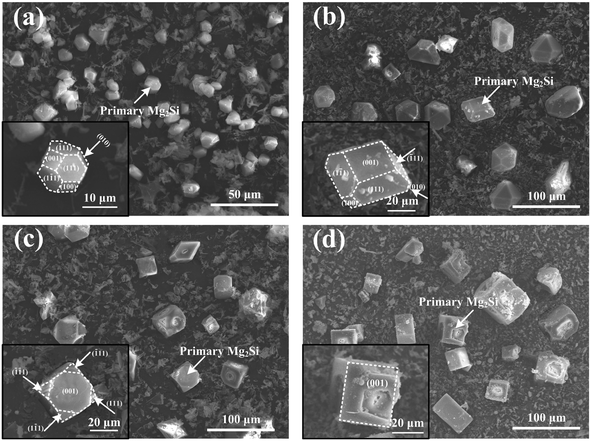 |
| Fig. 8 3-D morphologies of primary Mg2Si in Al–15Mg2Si alloys modified with (a) 0, (b) 0.1, (c) 0.2 and (d) 0.3 wt% Ca; insets are the enlarged morphology images of single primary Mg2Si. | |
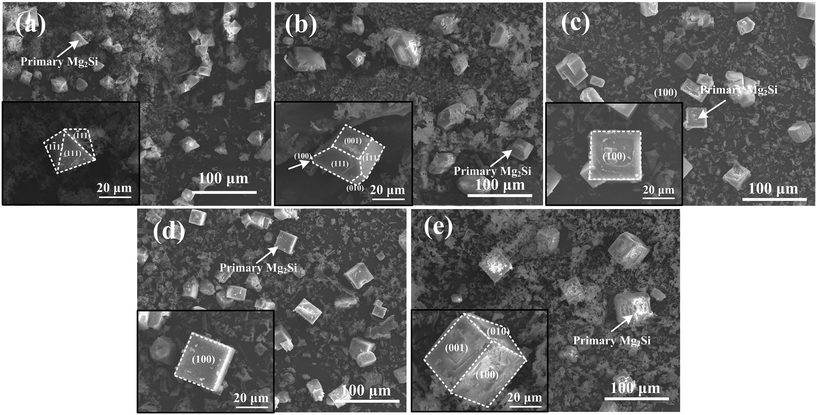 |
| Fig. 9 3-D morphologies of primary Mg2Si in Al–17Mg2Si alloys modified with (a) 0, (b) 0.1, (c) 0.2, (d) 0.3, and (e) 0.4 wt% Ca; insets are the enlarged morphology images of single primary Mg2Si. | |
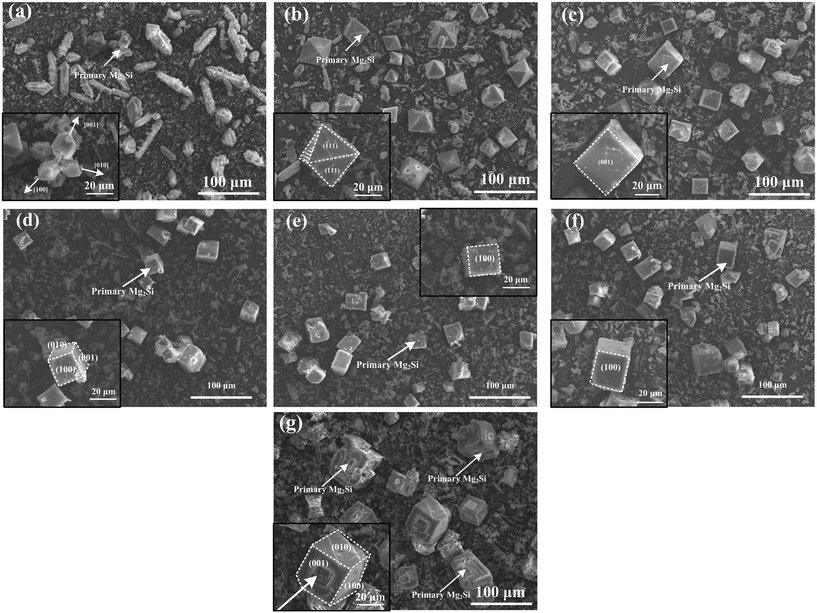 |
| Fig. 10 3-D morphologies of primary Mg2Si in Al–19Mg2Si alloys modified with (a) 0, (b) 0.1, (c) 0.2, (d) 0.3, (e) 0.4, (f) 0.5, and (g) 0.6 wt% Ca; insets are the enlarged morphology images of single primary Mg2Si. | |
3.2 Over-modification mechanism of primary Mg2Si in Ca-modified Al–xMg2Si alloy
“Environmental factors have a great influence on the crystallization of a crystal under nonequilibrium solidification condition”.36,37 In the present study, the crystallization process of primary Mg2Si is influenced by simultaneously changing the contents of Ca and Mg/Si (environmental factors). Normally, the crystallization of a crystal begins at the nucleation stage, the exothermic phenomenon starts at the same time, and DSC can capture the heat flow precisely in the crystal nucleation process. The influence of the contents of Ca and Mg/Si on the nucleation process of primary Mg2Si can be investigated by observing the relative movement of the exothermic peak onset temperature in the DSC pattern.38–40 Differential scanning calorimetry (DSC) patterns of Ca-modified Al–xMg2Si (x = 15, 17, 19) alloys are shown in Fig. 11(a)–(c). In order to enhance the credibility of experimental results, DSC characterizations are repeated twice in each sample, and the value of the primary Mg2Si exothermic peak onset temperature (TN) is obtained by calculating the average of these two results. According to Fig. 11(a)–(c), a significant movement of the primary Mg2Si exothermic peak towards low temperature is observed with the addition of Ca. With the increasing content of Ca, TN is decreased obviously in Al–xMg2Si alloy with the fixed content of Mg/Si (Fig. 11(d)–(f)), and a large undercooling is needed for the embryo formation of primary Mg2Si. It means that the embryo formation of primary Mg2Si can be inhibited by the addition of Ca, and the inhibition effect on the embryo formation is enhanced by increasing the Ca content. Moreover, with the Mg/Si content increasing from 15 to 19 wt%, the supersaturation of Mg/Si in Al–Mg–Si melt increases, and embryo formation of primary Mg2Si is encouraged significantly. The restriction of embryo formation caused by the addition of Ca is weakened with the increasing Mg/Si content.
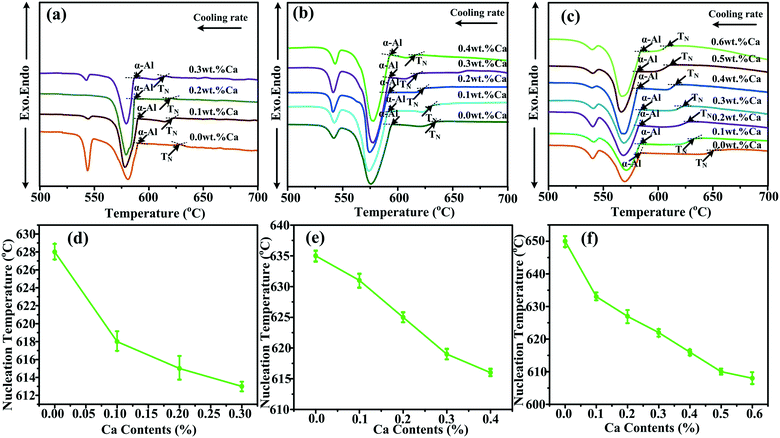 |
| Fig. 11 DSC patterns and TN of primary Mg2Si: DSC patterns of (a) Ca-modified Al–15Mg2Si alloys, (b) Ca-modified Al–17Mg2Si alloys and (c) Ca-modified Al–19Mg2Si alloys; TN of (d) Ca-modified Al–15Mg2Si alloys, (e) Ca-modified Al–17Mg2Si alloys and (f) Ca-modified Al–19Mg2Si alloys. | |
The adsorption energy of Ca atoms on {100} and {111} facets of primary Mg2Si has been calculated by Wang et al., and the result shows that Ca atoms can preferentially adsorb on the {100} facets of primary Mg2Si and the growth rates along <100> directions are inhibited by the adsorption of Ca atoms in the growth process, the morphology of primary Mg2Si is changed, and the particle size of primary Mg2Si is decreased.29–31 SEM micrograph with an elemental line scan through an over-modified primary Mg2Si particle in 0.6 wt% Ca-modified Al–19Mg2Si alloy is shown in Fig. 12. Abundant Ca atoms are detected at the interface between the primary Mg2Si and the matrix. In non-equilibrium solidification process, it is difficult for Ca atoms to be fully diffused due to the existence of preferential absorption of Ca atoms in the over-modified alloy, which results in the Ca atoms enriching the growth of primary Mg2Si {100} facets. In addition, with the content of Mg/Si increasing from 15 to 17 and to 19 wt%, the growth process of primary Mg2Si can be apparently promoted by increasing the supersaturation of Mg/Si, and the value of R is also increased. The morphology of primary Mg2Si transforms from truncated octahedron (
) to octahedron (
) and to dendrite (
), and the corresponding particle size is also increased.
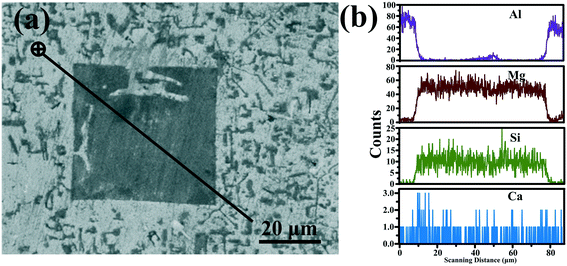 |
| Fig. 12 (a) SEM micrograph and (b) element line scanning spectra for Al–19Mg2Si alloy modified with 0.6 wt% Ca. | |
In Ca-modified Al–15Mg2Si alloy (Fig. 13(a)), with the addition of 0.1 wt% Ca, embryo formation of primary Mg2Si is restricted by Ca addition, and low Mg/Si content is adverse to the embryo formation in the nucleation process. Limited embryos are formed in the melt, and the particle size of primary Mg2Si is increased effectively as compared to Ca-free Al–15Mg2Si alloy. Although the growth rate along the <100> directions is restricted by the addition of Ca, the value of R is still in the range of
. Truncated octahedral primary Mg2Si is formed, and the exposed area of {100} facet is increased by the addition of Ca. With the content of Ca increasing to 0.2 wt%, restriction of embryo formation caused by Ca addition is enhanced, and low Mg/Si content is still adverse to embryo formation, and the particle size of primary Mg2Si keeps increasing. It is worth noting that restriction of the growth rate is also enhanced by the increasing content of Ca, which leads to
. The morphology of primary Mg2Si transforms from truncated octahedron to truncated cube. With the content of Ca further increasing to 0.3 wt%, primary Mg2Si embryo formation is further inhibited, and the restriction of the growth rate along the <100> direction is further enhanced, which results in
. Although cubic primary Mg2Si is formed by the serious suppression of the growth rate along <100> direction, sufficient Mg and Si atoms still exist in the melt, and continued growth of some cubic primary Mg2Si occurs. In the growth process, Al atoms diffuse into a large body of the melt, and Mg and Si atoms are enriched in the growth interface front of the corners and edges, which results in the occurrence of over-modification and the formation of dice-like primary Mg2Si with increased particle size.41–43
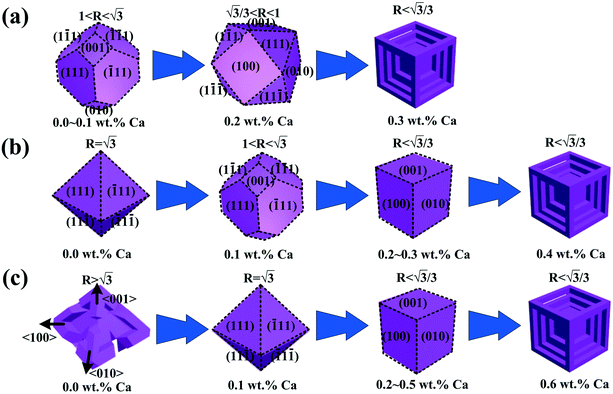 |
| Fig. 13 Morphology evolution illustrations of primary Mg2Si in Ca-modified Al–xMg2Si alloy with various Mg/Si: (a) 15 wt% Mg/Si, (b) 17 wt% Mg/Si, (c) 19 wt% Mg/Si. | |
In Ca-modified Al–17Mg2Si alloy (Fig. 13(b)), with the addition of 0.1 wt% Ca, embryo formation of primary Mg2Si is still restricted by the addition of Ca. However, the restriction effect on embryo formation is weakened by increasing the content of Mg/Si, and increasing particle size becomes indistinct as compared to 0.1 wt% Ca-modified Al–15Mg2Si alloy. Although the growth of primary Mg2Si can be promoted by increasing the content of Mg/Si, growth rates along <100> directions are still restricted by the addition of Ca, which leads to
, and the morphology of primary Mg2Si transforms to truncated octahedron (Fig. 13(b)). With the content of Ca increasing to 0.2 wt%, restriction of the embryo formation is enhanced, and particle size of primary Mg2Si keeps increasing. Moreover, restriction of growth rates along <100> directions is enhanced, which leads to the formation of cubic primary Mg2Si (
). In 0.3 wt% Ca-modified Al–17Mg2Si alloy, restriction of the embryo formation is further enhanced, and the particle size of primary Mg2Si keeps increasing. However, enhanced restriction of the growth rates along the <100> directions still results in
, and morphology of primary Mg2Si is retained as cubic. It is worth noting that over-modification of primary Mg2Si is attributed to the serious inhibition of nucleation and growth processes caused by the addition of Ca. With the Mg/Si content increasing to 17 wt%, embryo formation of primary Mg2Si is promoted, with more Ca content (0.4 wt%) needed to fully inhibit the embryo formation for over-modification. In addition, growth rates along <100> directions of primary Mg2Si are also restricted seriously in 0.4 wt% Ca-modified Al–17Mg2Si alloy. Dice-like primary Mg2Si is formed, and the particle size is increased.
In 0.1 wt% Ca-modified Al–19Mg2Si alloy (Fig. 13(c)), restriction on embryo formation caused by the addition of Ca is further weakened by increasing the content of Mg/Si, which leads to the continuous formation of ample embryos in the melt. Moreover, the addition of Ca restricts the growth rate of <100> direction and results in
. The morphology of primary Mg2Si is octahedral, and particle size is also decreased by the restricted growth rates. With the Ca content increasing from 0.2 to 0.5 wt%, although the restriction of the embryo formation is enhanced, sufficient embryos still can be formed in the melt. It is worth noting that restriction of growth rates along <100> directions is also enhanced, which leads to the formation of cubic primary Mg2Si (
). As for the particle size, on the one hand, the particle size of primary Mg2Si can be increased by the inhibited nucleation process; on the other hand, a restricted growth rate can simultaneously decrease the particle size. Thus, the particle size of primary Mg2Si is influenced by the interaction of inhibited nucleation process and restricted growth rate, which remains unchanged in Al–19Mg2Si alloy with the Ca content increasing from 0.2 to 0.5 wt%. Finally, the content of Ca for over-modification is increased to 0.6 wt% due to further weakened restriction effect on embryo formation in Al–19Mg2Si alloy. The whole crystallization process of primary Mg2Si is restricted seriously, and a large amount of Mg/Si atoms exist in the melt. The continuous growth of the cubic primary Mg2Si is conducted by these Mg/Si atoms. Dice-like primary Mg2Si is formed, and the particle size is increased.
Brinell hardness of the prepared material is shown in Fig. 14. The values of Brinell hardness in Al–xMg2Si alloy are mainly determined by the stress concentration of the particle–matrix interface. Stress concentration of the matrix–particle interface can be controlled by changing the particle morphology. According to the Hall–Petch theory:29
where
kn is the stress concentration factor,
a and
b are the long diameter and the short diameter of the particle, respectively. Usually, a high stress concentration factor results in a serious stress concentration for the alloy, which is harmful to mechanical properties. In Al–15Mg
2Si alloy, the morphology of primary Mg
2Si is a truncated octahedron, and the value of
kn is lower than that of other morphologies of primary Mg
2Si (
e.g., octahedron, cube, dice-like shape, and dendrite). Thus, the hardness of Al–15Mg
2Si alloy (∼90 HB) is much higher than other alloys.
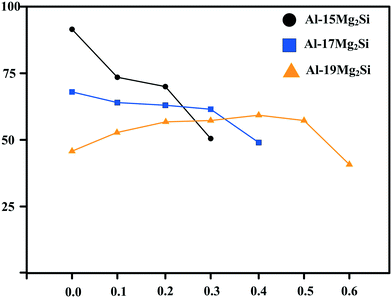 |
| Fig. 14 Brinell hardness of the prepared materials. | |
3.3 Growth process of dice-like primary Mg2Si
Primary Mg2Si with different growth stages can be found in the same sample because of the existence of composition segregation and temperature gradient in Al–xMg2Si alloy.44–47 The growth process of dice-like primary Mg2Si is observed in Al–15Mg2Si alloy modified with 0.3 wt% Ca (Fig. 15(a)–(d)). A cubic primary Mg2Si with the bulges existing on the corners of the cube is the beginning of the growth process (Fig. 15(a)). With the growth of the bulges, the edges of the cube begin to raise, the bulges are close to each other gradually, and a dice-like outline with some gaps is formed (Fig. 15(b) and (c)). Finally, with the gaps disappearing, a dice-like primary Mg2Si is formed (Fig. 15(d)). A schematic illustration of the corresponding growth process of a dice-like primary Mg2Si is also given (Fig. 15(e)). Although the cubic primary Mg2Si has been formed by the skeleton-type growth process in the melt, the adsorption of Ca atoms can restrict the nucleation and suppress the growth rates along <100> directions of primary Mg2Si. Many Mg and Si atoms are collected at the corners of the cube, which leads to the continuous growth of cubic primary Mg2Si along <111> directions, and the bulges are preferentially formed on the corners (Fig. 15(e)). With the growth proceeding, the adjacent bulges begin to join each other, and the cube edges are covered by the growing bulges, a dice-like outline with some gaps is formed; finally, the growth of dice-like primary Mg2Si is finished with the gaps vanishing, which is called the tip-growth process. Moreover, the growth steps can be observed in the growth process (white arrows), which means that the tip-growth process is still completed by the 2-D nucleation growth.
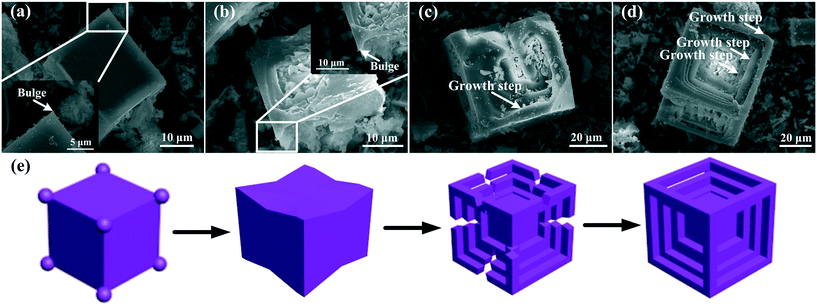 |
| Fig. 15 (a)–(d) Tip growth process of primary Mg2Si at different growth stages in Al–15Mg2Si alloy modified with 0.3 wt% Ca, (e) schematic illustrations of the tip-growth process. | |
4. Conclusions
In summary, embryo formation of primary Mg2Si is restricted by the addition of Ca while the restricted effect is weakened by increasing the Mg/Si content. Although the growth of primary Mg2Si is encouraged with the increasing content of Mg/Si, the growth rates along <100> directions are still restricted by the addition of Ca in Al–xMg2Si alloy. Morphology of primary Mg2Si can be changed by controlling the contents of Mg/Si and Ca simultaneously. Octahedral, truncated octahedral, truncated cubic, cubic, and dice-like primary Mg2Si are prepared successfully. Over-modification is attributed to the serious inhibition effect on the whole crystallization of primary Mg2Si caused by increasing the Ca content. The content of Ca for over-modification is increased with the increasing Mg/Si content. A new growth mechanism of the dice-like primary Mg2Si named tip-growth process is also investigated. The present study is beneficial for understanding the nucleation and growth processes of primary Mg2Si, which enriches the modification theory of primary Mg2Si in Al–Mg–Si alloys.
Conflicts of interest
There are no conflicts to declare.
Acknowledgements
Financial support from the Science and Technology Program of Education Department of Jilin Province (JJKH20200614KJ) is acknowledged. The Doctor Initiated Fund Project of Changchun Institute of Technology (01130292019016), the Science and Technology Fund Project of Changchun Institute of Technology (01120120200008), and Innovation and Entrepreneurship Project Plan for College Students of Changchun Institute of Technology (S202111437090, S202111437091) are greatly acknowledged.
References
- C. Acquah and M. Cagnetta, Ind. Eng. Chem. Res., 2015, 54, 12108–12113 CrossRef CAS.
- Y. F. Shen, J. Mater. Chem. A, 2015, 3, 13114 RSC.
- C. Li, X. F. Liu and Y. Y. Wu, Refinement and modification performance of Al-P master alloy on primary Mg2Si in Al-Mg-Si alloys, J. Alloys Compd., 2008, 465, 145–150 CrossRef CAS.
- U. K. Krieger, C. Marcollia and J. P. Reid, Chem. Soc. Rev., 2012, 41, 6631–6662 RSC.
- R. J. Ma, Y. F. Liu, Y. X. Yang, K. C. Pu, M. X. Gao and H. G. Pan, Acta Mater., 2015, 98, 128–134 CrossRef CAS.
- H. Balout, P. Boulet and M. C. Record, J. Phys. Chem. C, 2014, 118, 19635–19645 CrossRef CAS.
- J. Mao, H. S. Kim, J. Shuai, Z. H. Liu, R. He, U. Saparamadu, F. Tian, W. S. Liu and Z. F. Ren, Acta Mater., 2016, 103, 633–642 CrossRef CAS.
- H. Y. Wang, L. Chen, B. Liu, X. R. Li, J. G. Wang and Q. C. Jiang, Mater. Chem. Phys., 2012, 135, 358–364 CrossRef CAS.
- J. G. Jung, T. Y. Ahn, Y. H. Cho, S. H. Kim and J. M. Lee, Acta Mater., 2018, 144, 31–40 CrossRef CAS.
- X. Tong, D. C. Zhang, K. Wang, J. G. Lin, Y. Y. Liu, Z. M. Shi, Y. C. Li, J. X. Lin and C. E. Wen, Mater. Sci. Eng., A, 2018, 733, 9–15 CrossRef CAS.
- A. L. Chaudhary, D. A. Sheppard, M. Paskevicius, C. J. Webb, E. M. Gray and C. E. Buckley, J. Phys. Chem. C, 2014, 118, 1240–1247 CrossRef CAS.
- S. B. Jin, P. Shen, Y. J. Li, D. S. Zhou and Q. C. Jiang, CrystEngComm, 2012, 14, 1925–1928 RSC.
- W. Chrominski and M. Lewandowska, Acta Mater., 2016, 103, 547–557 CrossRef CAS.
- L. Ye, J. Hu, C. Tang, X. Zhang, Y. Deng, Z. Liu and Z. Zhou, Mater. Charact., 2013, 79, 1–6 CrossRef CAS.
- K. Chen and Z. Q. Li, J. Alloys Compd., 2014, 592, 196–201 CrossRef CAS.
- Q. C. Jiang, H. Y. Wang, Y. Wang, B. X. Ma and J. G. Wang, Mater. Sci. Eng., A, 2005, 392, 130–135 CrossRef.
- J. Zhang, Z. Fan, Y. Q. Wang and B. L. Zhou, Mater. Sci. Technol., 2001, 17, 494–496 CrossRef CAS.
- P. T. Li, C. Li, J. F. Nie, J. Ouyang and X. F. Liu, CrystEngComm, 2013, 15, 411–420 RSC.
- S. B. Jin, P. Shen, Y. J. Li, D. S. Zhou and Q. C. Jiang, CrystEngComm, 2012, 14, 1925–1928 RSC.
- J. F. Nie, Y. Y. Wu, P. T. Li, H. Li and X. F. Liu, CrystEngComm, 2012, 14, 2213–2221 RSC.
- D. S. Zhou, S. B. Jin, Y. J. Li, F. Qiu, F. Deng, J. G. Wang and Q. C. Jiang, CrystEngComm, 2013, 15, 643–649 RSC.
- S. B. Jin, P. Shen, D. S. Zhou and Q. C. Jiang, Cryst. Growth Des., 2012, 12, 2814–2824 CrossRef CAS.
- L. Chen, H. Y. Wang, D. Luo, H. Y. Zhang, B. Liu and Q. C. Jiang, CrystEngComm, 2013, 15, 1787–1793 RSC.
- L. Chen, H. Y. Wang, Y. J. Li, M. Zha and Q. C. Jiang, CrystEngComm, 2014, 16, 448–454 RSC.
- H. C. Yu, H. Y. Wang, L. Chen, F. Liu, C. Wang and Q. C. Jiang, CrystEngComm, 2015, 17, 7048–7055 RSC.
- S. Z. Lu and A. Hellawell, Metall. Trans. A, 1987, 18, 1721–1733 CrossRef.
- G. H. Li, H. S. Gill and R. A. Varin, Metall. Trans. A, 1993, 24, 2383–2391 CrossRef.
- J. J. Kim, D. H. Kim, K. S. Shin and N. J. Kim, Scr. Mater., 1999, 41, 333–340 CrossRef CAS.
- H. C. Yu, H. Y. Wang, L. Chen, M. Zha, C. Wang, C. Li and Q. C. Jiang, Mater. Sci. Eng., A, 2017, 685, 31–38 CrossRef CAS.
- H. Y. Wang, F. Liu, L. Chen, M. Zha, G. J. Liu and Q. C. Jiang, Mater. Sci. Eng., A, 2016, 657, 331–338 CrossRef CAS.
- L. Chen, H. Y. Wang, K. Liu, C. Wang, D. Luo and Q. C. Jiang, CrystEngComm, 2017, 19, 3058–3062 RSC.
- H. Y. Wang, H. C. Yu, C. Li, M. Zha, C. Wang and Q. C. Jiang, CrystEngComm, 2017, 9, 1680–1688 RSC.
- H. C. Yu, J. Alloys Compd., 2019, 787, 872–881 CrossRef CAS.
- Y. F. Yang, S. B. Jin and Q. C. Jiang, CrystEngComm, 2013, 15, 852–855 RSC.
- H. Y. Wang, X. N. Xue, X. Y. Xu, C. Wang, L. Chen and Q. C. Jiang, CrystEngComm, 2016, 44, 8599–8607 RSC.
- T. Gao, X. L. Cui, X. Y. Li, H. Li and X. F. Liu, CrystEngComm, 2014, 16, 3548–3557 RSC.
- C. L. Xu and Q. C. Jiang, Mater. Sci. Eng., A, 2006, 437, 451–455 CrossRef.
- C. Li, J. Y. Sun, Z. D. Li, Z. M. Gao, Y. C. Liu, L. M. Yu and H. J. Li, Mater. Charact., 2016, 122, 142–147 CrossRef CAS.
- M. Tebib, A. M. Samuel, F. Ajersch and X. G. Chen, Mater. Charact., 2014, 89, 112–123 CrossRef CAS.
- N. A. Nordin, S. Farahany, A. Ourdjini, T. A. A. Bakar and E. Hamzah, Mater. Charact., 2013, 86, 97–107 CrossRef CAS.
- Y. He, H. L. Zhang, T. Li and X. T. Wang, J. Alloys Compd., 2013, 581, 494–497 CrossRef CAS.
- M. E. Moussa, M. A. Waly and A. M. El-Sheikh, J. Alloys Compd., 2014, 615, 576–581 CrossRef CAS.
- M. E. Moussa, M. A. Waly and A. M. El-Sheikh, J. Magnesium Alloys, 2014, 2, 230–238 CrossRef CAS.
- C. Li, Y. Y. Wu, H. Li and X. F. Liu, Acta Mater., 2011, 59, 1058–1067 CrossRef CAS.
- G. Han and X. F. Liu, Acta Mater., 2016, 114, 54–66 CrossRef CAS.
- H. Ghandvar, M. H. Idris and N. Ahmad, J. Alloys Compd., 2018, 751, 370–390 CrossRef CAS.
- R. Du, D. Yuan, F. Li, D. C. Zhang, S. S. Wu and S. L. Lü, J. Alloys Compd., 2019, 776, 536–542 CrossRef CAS.
|
This journal is © The Royal Society of Chemistry 2022 |
Click here to see how this site uses Cookies. View our privacy policy here.