DOI:
10.1039/D1MA00891A
(Paper)
Mater. Adv., 2022,
3, 665-671
Facile access to template-shape-replicated nitrogen-rich mesoporous carbon nanospheres for highly efficient CO2 capture and contaminant removal†
Received
28th September 2021
, Accepted 15th November 2021
First published on 16th November 2021
Abstract
Rising atmospheric CO2 levels and water pollution have necessitated new research towards the development of novel CO2 capture materials and innovative methods for wastewater treatment. Herein, we demonstrate a facile fabrication strategy to prepare novel template-shape-replicated nitrogen-rich mesoporous carbon nanospheres (NMCN) with high surface area, pore volume and ordered pore geometry via a combination of in situ co-condensation, surface-confined atom transfer radical polymerization (SC-ATRP) and post-polymerization modification. NMCN exhibited efficient CO2 capture performance and contaminant removal capability from wastewater. This work may open a new direction for the design of novel porous nanomaterials for CO2 capture and other emerging applications.
Introduction
The extensive combustion of fossil fuels in the post-industrial era to meet energy demands has resulted in a dramatic increase of the atmospheric concentration of CO2. Atmospheric CO2 concentration at present is ∼400 ppm, which is expected to rise to 570 ppm by the year 2100. Due to this high level of atmospheric CO2, various environmental issues have arisen, including global warming, imbalance in ocean acidification, unpredictable weather pattern and a slew of medical problems, including respiratory diseases.1,2 The use of various renewable energy technologies on a large scale, such as solar, nuclear, and wind, has the potential to cut CO2 emissions.3 However, the replacement of fossil fuel sources with renewable energy in all applications is insufficient to mitigate CO2's impact on climate change. As a result, there is an unmet demand to cut carbon emissions.4 Post-combustion CO2 capture from the source of the emission, such as power plants,5 and geologic CO2 storage,6 which were once considered viable strategies, have gradually lost favor due to the high costs involved. To address this drawback, alternative CO2 capture methods are urgently needed to combat climate change.7–9 Various porous materials have been investigated to develop new CO2 capture materials, such as zeolites,10–13 carbon-based materials,14–21 covalent organic frameworks,22 metal organic frameworks,23,24 polymers25 and silica/polymer hybrids.26–30 Porous carbon nanomaterials possessing controlled pore geometry and morphology are used in applications such as energy storage, catalysis, and air purification. Porous carbon is also employed as a CO2 capture material.17 However, the absence of ordered pore geometry in these materials has led to their poor CO2 adsorption performance. Furthermore, the synthesis protocols of such materials involve stringent reaction conditions and multistep purification processes.
Mesoporous materials, with pore diameter between 2–50 nm and high surface area, organized pore geometry, and high pore volume, have received some interest due to their widespread use in adsorption, separation, catalysis, and sensing applications.31 We hypothesized that nitrogen-rich functional mesoporous carbon nanospheres (NMCN) with high surface area and ordered pore geometry may be exploited to make efficient CO2 capture materials. NMCN is synthesized via the surface-confined atom transfer radical polymerization (SC-ATRP)32 of acrylonitrile (AN) and 4-vinylbenzyl chloride (VBC) from a bromo-functionalized mesoporous silica nanomaterial (MSN-Br), followed by carbonization and etching of the silica template.
Experimental section
Materials
Cetyltrimethylammonium bromide (CTAB, ≥96%, Aldrich), (3-aminopropyl)trimethoxysilane (APTMS, 97%, Aldrich), tetraethyl orthosilicate (TEOS, 98%, Aldrich), 2-bromo-2-methylpropionyl bromide (BIBB, 98%, Aldrich), N,N,N′,N′′,N′′-pentamethyldiethylenetriamine (PMDETA, 99%, Aldrich), copper(I) chloride (CuCl, 97%, Aldrich), copper(II) chloride (CuCl2, 97%, Aldrich), triethylamine (Et3N, ≥99%, Aldrich), N-methyl-2-pyrrolidone (NMP, ≥99%, Aldrich), hydrogen fluoride (HF, 40%, Aldrich) and potassium hydroxide (KOH, Aldrich) were used as received. Acrylonitrile (AN, ≥99%, Aldrich) and 4-vinylbenzyl chloride (VBC, 90%, Aldrich) were purified by passing through a basic aluminium oxide (Aldrich) column to remove the inhibitor before use in polymerization. Xylene (Merck, India) was dried by refluxing over sodium/benzophenone just before use.
Preparation of amine-functionalized mesoporous silica nanoparticles
MSN-NH2 was synthesized following an earlier reported procedure.33 Typically, in a round-bottom flask, CTAB (1.0 g, 2.745 mmol), 2.0 M of aqueous NaOH (3.5 mL of 2.0 M, 7.0 mmol) and water (240 g, 13.335 mol) were mixed and heated for 30 min at 80 °C under stirring to obtain a clear solution. The pH of this solution was measured to be 12. Then, TEOS (4.67 g, 22.4 mmol) and APTMS (0.515 g, 2.875 mmol) were introduced rapidly to the solution under continuous magnetic stirring. A white precipitate appeared 5 min after the addition of TEOS and APTMS. The mixture was heated at 80 °C for another 2 h, then the product was isolated by hot filtration, washed with water/methanol, and dried under vacuum at 80 °C. CTAB template was eliminated by refluxing the crude product with a solution of 100 mL methanol and 1.0 mL of conc. HCl at 60 °C for 6 h. Then, the product was collected by filtration, washed with water/methanol, and dried under vacuum to obtain pure MSN-NH2.
Preparation of bromo-initiator-functionalized mesoporous silica nanoparticles
MSN-Br was synthesized by the coupling reaction of MSN-NH2 with 2-bromo-2-methylpropionyl bromide (BIBB). For a typical reaction, MSN-NH2 was added to a flask, and TEA and dry CH2Cl2 were added to the flask under N2 atmosphere. The flask was cooled to 0 °C, and BIBB was added to it dropwise at 0 °C under continuous magnetic stirring. After the addition, the temperature was raised to room temperature, and the reaction was allowed to continue at ambient temperature for another 12 h. After the reaction, the product was collected by filtration, washed successively with CH2Cl2 and acetone, and dried to obtain pure MSN-Br.
Calculation of initiator grafting density
Initiator grafting density (GI) was calculated using TGA and eqn (1): |  | (1) |
where W%initiator+silica, W%silica, NA, Minitiator and Ssp stand for weight loss (between 120 °C to 800 °C) of the bromo-initiator-functionalized MSN-Br (= 16.4%), neat MSN (= 8.4%), Avogadro's number, molar mass of the initiator fragment after subtracting the molar mass of one Br atom (= 150 g mol−1) and specific surface area of MSN-Br (= 1210 m2 g−1).
Preparation of –CH2Cl functionalized mesoporous silica/polymer hybrid nanoparticles (MSPN)
MSPN was synthesized via SC-ATRP of AN/VBC from bromo-initiator-functionalized MSN-Br using the following molar ratio: [AN + VBC]0/[MSN-Br]0/[CuCl]0/[CuCl2]0/[PMDETA]0 = 200
:
1
:
1
:
0.1
:
1.1 at 70 °C for 24 h. In a typical polymerization, MSN-Br was added to a flask, which was evacuated at 60 °C for 2 h to eliminate any trapped gaseous entity or moisture. Then, a magnetic stir bar, degassed xylene, CuCl, CuCl2 and PMDETA were introduced to the flask under N2 atmosphere. Finally, degassed AN and VBC were added under N2 flow, and the flask was heated at 790 °C. After polymerization, the crude product was isolated by centrifugation and washed successively with THF/methanol and finally dried to obtain the MSPN hybrid. For kinetics investigation of the polymerization, a series of polymerization reactions were performed, and these reactions were quenched at different polymerization times to monitor (i) %polymer grafting by TGA and (ii) the evolution of molecular weights and dispersities (by SEC) with time.
Preparation of nitrogen-rich mesoporous carbon nanospheres
Nitrogen-rich mesoporous carbon nanospheres (NMCN) were obtained via pyrolysis of the nitrogen-rich polymer (MSPN). Typically, the purified MSPN silica/polymer hybrid was first stabilized at 280 °C for 2 h under air flow at a heating rate of 1 °C min−1, then purged with N2 gas for 1 h and heated to reach 800 °C with a heating rate of 10 °C min−1, then pyrolyzed at 800 °C for 6 h and finally cooled to ambient temperature. After carbonization, the silica template was selectively removed by HF, and the product was isolated by centrifugation and subsequently washed with water/ethanol, respectively, and then dried to obtain NMCN.
Characterization studies
X-Ray diffraction (XRD).
XRD analysis of the prepared porous samples were carried out on a Bruker D8 Advance X-ray diffractometer equipped with a Cu X-ray tube (40 kV & 40 mA).
Attenuated total reflection infrared (ATR-IR) spectroscopy.
IR spectra of the prepared porous samples were recorded using an IR spectrophotometer (PerkinElmer, Model: Spectrum 100) in the attenuated total reflectance (ATR) mode with a diamond crystal, using the spectral range of 4000–400 cm−1 and a resolution of 4 cm−1.
Size exclusion chromatography (SEC).
The silica-free cleaved polymer samples were analysed with an Agilent triple detection size exclusion chromatography (SEC) system equipped with two PL1113-6300 ResiPore 300 × 7.5 mm columns and using DMF as the eluent (at 35 °C, flow rate of 1 mL min−1). The SEC instrument was calibrated using narrow linear poly(methyl methacrylate) standard samples.
Thermogravimetric analysis (TGA).
TGA of the synthesized materials were performed using a Netzsch TG 209 F3 instrument (under air) from room temperature to 800 °C at a heating rate of 10 °C min−1.
N2 physisorption measurement.
N2 adsorption/desorption experiments of the porous materials were carried out using an Anton Paar (Model: Autosorb iQ-XR-XR-AG) gas sorption system at 77 K.
CO2 capture characterization.
CO2 capture experiments of the synthesized porous carbon nanomaterials were carried out using an Anton Paar (Model: Autosorb iQ-C-AG) gas sorption analyzer system at 25 °C.
Field emission scanning electron microscopy (FESEM).
The morphologies of the porous samples were analysed using a Zeiss Gemini SEM500 electron microscope at an accelerating voltage of 5 kV.
Dynamic light scattering (DLS).
Hydrodynamic diameters (Dh) of the ethanol dispersions of porous samples were analysed using a Malvern particle size analyzer (Zetasizer NANO ZS90).
UV-vis absorption spectra. UV-vis absorption spectra of the solution of Coumarin 102 (C102) and suspension of C102-encapsulated NMCN were acquired in a Shimadzu UV-2600 spectrophotometer. %Encapsulation was calculated using the following eqn (2):
|  | (2) |
Photoluminescence spectra.
Photoluminescence (PL) spectra of the samples were recorded in a Fluorolog FL3-211 (HORIBA Scientific) with a 450 Watt Xenon arc lamp.
Fluorescence microscopy.
A drop of the dye-encapsulated nanomaterial sample suspension was placed on a glass slide, and images were recorded using a light microscope (DM2700M, Leica).
Results and discussion
Synthesis and structural characterization of the nitrogen-rich mesoporous carbon nanoparticles (NMCN)
Tertiary alkyl bromide-functionalized MSN-Br, suitable for use as ATRP initiator,34,35 was synthesized via the process described in Scheme 1. First, -NH2-functionalized MSN (MSN-NH2) was synthesized via in situ co-condensation of TEOS and APTMS using CTAB as the template and with subsequent elimination of the CTAB template.33,36 MSN-NH2 was then coupled with 2-bromoisobutyryl bromide (BIBB) to introduce tertiary alkyl bromide-containing ATRP initiation sites (MSN-Br).37 The ATR-IR spectrum of MSN-Br (Fig. 1a and Fig. S1, ESI†) exhibited characteristic bands at 2927 cm−1 (C–H asymm stretch.), 1060 cm−1 (Si–O–Si linkage)32 and 614 cm−1 (C–Br stretch.).38 This indicates that integration of the bromo-initiator functionality into the pore walls of the silica framework was successful. The significant weight loss (16.4%) of MSN-Br between 120 and 800 °C was attributed to the organic (aminopropyl + 2-bromoisobutyryl) functionalities, while the modest weight loss (8.4%) of neat MSN (Fig. 1b) is due to removal of water or other adsorbed gases. The initiator grafting density (GI) of MSN-Br, estimated using eqn (1),39 was found to be 0.33 molecule nm−2. A high-intensity (100) reflection peak at 2θ = 2.55° was observed in the XRD pattern of MSN-Br (Fig. 1c), suggesting the presence of cylindrical mesopores.33
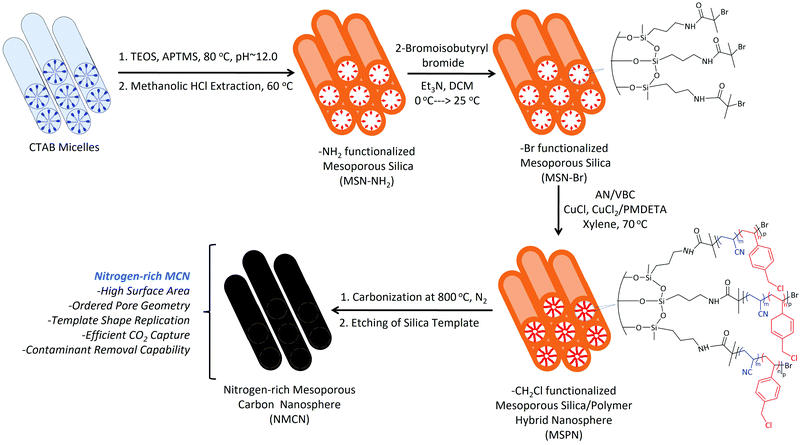 |
| Scheme 1 Synthesis of nitrogen-rich mesoporous carbon nanoparticles. | |
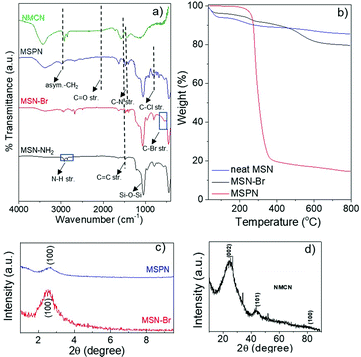 |
| Fig. 1 Characterization of the obtained porous MSN-Br, MSPN and NMCN nanomaterials: (a) ATR-IR spectra, (b) TGA thermograms and (c and d) powder XRD patterns. | |
N2 sorption analyses of MSN-Br (Fig. 2a) revealed a high specific surface area (SBET) of 1210 m2 g−1 and narrow pore size distribution (PSD) with an average diameter of around 1.98 nm and pore volume of 0.728 cc g−1, suggesting a cylindrical mesoporous structure.33 MSN-Br exhibited spherical morphology diameters ranging from 200–280 nm, as revealed by the FESEM image (Fig. 3). Somewhat higher value (344 nm) of the MSN-Br diameter was obtained from dynamic light scattering (DLS) compared to that from FESEM, which is most likely due to MSN-Br's hydrodynamic nature.40
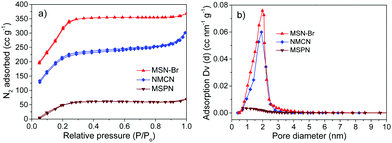 |
| Fig. 2 (a) N2 adsorption–desorption isotherm and (b) pore size distribution of porous MSN-Br, MSPN and NMCN nanomaterials. | |
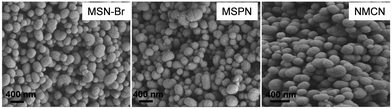 |
| Fig. 3 FESEM images of porous MSN-Br, MSPN and NMCN nanomaterials. | |
Subsequent SC-ATRP of acrylonitrile (AN) in the presence of a functional monomer, 4-vinylbenzyl chloride (VBC, 5, 10 and 15 mol%), from MSN-Br using CuCl/CuCl2/PMDETA led to the synthesis of MSPN silica/polymer hybrids. FTIR spectrum of a representative MSPN hybrid (Fig. 1a) showed bands at 1060 (Si–O–Si linkage), 1589 (–N–C
O band of PAN),41 and 1415 (–C
N band of PAN),41 along with additional bands at 1474, 1512 and 1626 (stretching vibration of the phenyl ring),42 827 (CH2 of chloromethyl functionality),43 and 725 cm−1 (C–Cl stretching vibration). A representative MSPN hybrid (with 15% –CH2Cl functionalization) revealed 66% polymer grafting into the MSN, as revealed by TGA analysis (Fig. 1b).
XRD analysis of a representative MSPN-15% hybrid (Fig. 1c) exhibited a diffraction peak at 2θ = 2.58°, although with lower intensity compared to that of MSN-Br. This suggests polymer grafting of the mesopores of MSN-Br. The SBET of MSPN reduced to 94 m2 g−1 from that of the starting material, MSN-Br (SBET = 1210 m2 g−1), during which the total pore volume also shrunk to 0.041 from 0.728 cc g−1 (Fig. 2 and Table 1). Spherical morphology of the MSN-Br template remained intact in MSPN-15% even after polymer grafting, as revealed by FESEM analysis.
Table 1 Molecular characterization data of different mesoporous nanoparticles
Entry |
Material |
D
SEM
(nm) |
D
h
(nm) |
S
BET
(nm) |
Total pore volumec |
Pore diameterc |
Diameter measured from FESEM.
Hydrodynamic diameter measured from DLS.
Analysed by N2 adsorption/desorption study.
Pores were inaccessible to N2 adsorbate.
|
E1 |
MSN-Br |
200–280 |
344 |
1210 |
0.728 |
1.98 |
E2 |
MSPN |
196–240 |
292 |
94 |
0.041 |
—d |
E3 |
NMCN |
190–260 |
310 |
860 |
0.462 |
1.92 |
To have a better idea of the surface grafting of the polymer, a detailed kinetic investigation was carried out (see Experimental section for more details, Table S1, ESI†), and the evolution of %polymer grafting (from the TGA analysis) and molar masses/dispersities with time (by SEC analysis) was monitored. The %polymer grafting into the mesoporous channel of MSN-Br increased steadily with time, reaching 66% after 24 h of polymerization. The molar mass of the cleaved polymer (after dissolution of the silica template) increased linearly with conversion (Fig. 4b and Table S1, ESI†), sustaining low Đ values (1.17–1.25) during polymerization (Fig. 4b), indicating a controlled copolymerization.35,44–46
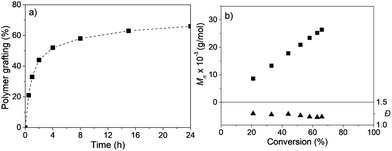 |
| Fig. 4 (a) Evolution of %polymer grafting into the mesopores of MSN-Br vs. time and (b) plot of Mn and Đ of the cleaved polymer vs. %polymer grafting for SC-ATRP of AN + 15% VBC in xylene at 90 °C. | |
Mesoporous carbon nanospheres (MCN) were obtained by a two-step thermal treatment47,48 involving thermal stabilization (under air) and carbonization (under N2) of the MSPN silica/polymer hybrids, followed by removal of silica template. The FTIR spectrum of NMCN (Fig. 1a) exhibits characteristic bands at ∼1626 (C
C stretching), ∼2920 (CH2 asymm stretch.) and 2847 cm−1 (CH2 symm stretch.), which originate from the adsorbed gaseous AN monomer fragments produced during pyrolysis.49 Notably, the absence of the Si–O–Si absorption band in the IR spectrum of NMCN suggests complete dissolution of the silica framework. The XRD pattern (Fig. 1d) of NMCN showed broad peaks at 2θ of 25°, 44°, and 80° ascribed to the (002), (101), and (100) reflections of a typical graphitic carbon-type structure.32
The SBET of NMCN was estimated to be 860 m2 g−1, and the average pore diameter of 1.92 nm and total pore volume of 0.462 cc g−1 (Table 1) were estimated from the N2 sorption analysis. Notably, this high pore diameter and pore volume of NMCN are key features for its potential application as adsorbent. The FESEM image of NMCN (Fig. 3) reveals it has retained the spherical morphology of MSN-Br (Table 1). The formation of spherical mesoporous NMCN, retaining the morphology of the MSN, was mainly enabled by the presence of the interconnected mesoporous network in the material and high polymer grafting into the mesopores of MSN-Br via SC-ATRP.50 The diameters of NMCN obtained from DLS are somewhat higher than DFESEM. This is probably due to their hydrodynamic nature and aggregation in ethanol.
CO2 is an anthropogenic greenhouse gas and is majorly accountable for global warming.20,51,52 The synthesized mesoporous NMCN nanoparticles were employed as potential candidates for CO2 capture. CO2 adsorption performance at 25 °C (Fig. 5) of the three porous NMCN nanoparticle samples bearing 5, 10 and 15% functionalization exhibited acceptable CO2 adsorption capacities of 2.84, 3.76 and 4.93 mmol g−1, respectively. These results are comparable to the reported porous N-rich carbon nanospheres, including copolymer-templated nitrogen-enriched porous nanocarbon,20 N-doped acicular hollow porous carbon,53 porous carbon derived from sugarcane54 and porous carbon derived from sustainable biomass.55 Among the three samples, NMCN (15%) displays the highest CO2 adsorption, possibly due to higher pore volume.
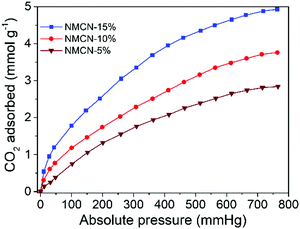 |
| Fig. 5 CO2 adsorption isotherms for NMCN samples at 25 °C. | |
The efficiency of NMCN for the removal of a representative hydrophobic dye (Coumarin 102, C102) from water was tested, and the encapsulation capacity was observed by UV-Vis spectroscopy. The absorbance of C102 at 387 nm decreased gradually with time (Fig. 6a), leading to ∼82% dye exchange after incubation for 24 h (Fig. 6b). The fluorescence emission spectrum of NMCN (Fig. 6c) with encapsulated C102 was of lower intensity than that of neat C102; however, the peak position remains same, suggesting successful dye encapsulation. Furthermore, the fluorescence light microscopic image (Fig. 6d) depicts green light-emitting beads of NMCN with encapsulated C102, confirming successful encapsulation of the dye inside the mesopores of NMCN.
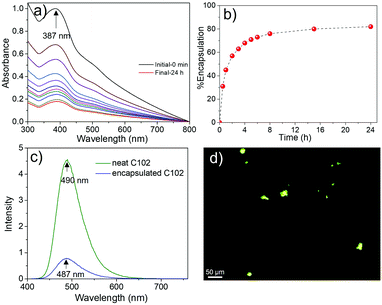 |
| Fig. 6 (a) Time-dependent (initial – 0 min, final – 24 h) UV-Vis spectra of C102 after incubating with NMCN; (b) evaluation of %encapsulation of C102 with time; (c) fluorescence emission spectra of aqueous solution of C102 and aqueous suspension of C102 encapsulated-NMCN (Excitation wavelength: 390 nm); (d) fluorescent microscopy images of C102 encapsulated-NMCN. | |
Conclusions
In summary, this work demonstrates, for the very first time, the development of a facile fabrication method for nitrogen-rich mesoporous carbon nanomaterials (NMCN) with high surface area and ordered pore geometry for efficient ambient-temperature CO2 capture and contaminant removal. Overall, the CO2 uptake performance of NMCN is comparable to or better than the contemporary benchmark porous materials, including carbons, zeolites, and metal organic frameworks. This approach, with (i) greater sustainability, including but not limited to carbon neutrality, and (ii) simpler and cost-effective preparation routes, leading to the preparation of nitrogen-rich mesoporous carbon nanomaterials with improved properties for specific applications in CO2 capture and contaminant removal, introduces a new avenue for the fabrication of unique advanced porous materials for a wide range of potential applications in adsorption, energy, catalysis, and medicine.
Conflicts of interest
There are no conflicts to declare.
Acknowledgements
We acknowledge grants from SERB, Govt. of India, under Ramanujan Fellowship Award (SB/S2/RJN-113/2016) and IIT Bhilai under Research Initiation Grant. We thank Arindam Mondal for his help on the PL measurement. SS and DK thank DBT, Govt. of India and CSIR, Govt. of India for their fellowship.
Notes and references
- S. Chu, Science, 2009, 325, 1599 CrossRef CAS PubMed.
- A. Harjanne and J. M. Korhonen, Energy Policy, 2019, 127, 330–340 CrossRef.
- C. W. Forsberg, Prog. Nucl. Energy, 2009, 51, 192–200 CrossRef.
- M. Bui, C. S. Adjiman, A. Bardow, E. J. Anthony, A. Boston, S. Brown, P. S. Fennell, S. Fuss, A. Galindo, L. A. Hackett, J. P. Hallett, H. J. Herzog, G. Jackson, J. Kemper, S. Krevor, G. C. Maitland, M. Matuszewski, I. S. Metcalfe, C. Petit, G. Puxty, J. Reimer, D. M. Reiner, E. S. Rubin, S. A. Scott, N. Shah, B. Smit, J. P. M. Trusler, P. Webley, J. Wilcox and N. Mac Dowell, Energy Environ. Sci., 2018, 11, 1062–1176 RSC.
- A. Samanta, A. Zhao, G. K. H. Shimizu, P. Sarkar and R. Gupta, Ind. Eng. Chem. Res., 2012, 51, 1438–1463 CrossRef CAS.
- M. D. Zoback and S. M. Gorelick, Proc. Natl. Acad. Sci. U. S. A., 2012, 109, 10164–10168 CrossRef CAS PubMed.
- K. S. Lackner, S. Brennan, J. M. Matter, A.-H. A. Park, A. Wright and B. van der Zwaan, Proc. Natl. Acad. Sci. U. S. A., 2012, 109, 13156–13162 CrossRef CAS PubMed.
- E. S. Sanz-Pérez, C. R. Murdock, S. A. Didas and C. W. Jones, Chem. Rev., 2016, 116, 11840–11876 CrossRef PubMed.
- K. Z. House, A. C. Baclig, M. Ranjan, E. A. van Nierop, J. Wilcox and H. J. Herzog, Proc. Natl. Acad. Sci. U. S. A., 2011, 108, 20428–20433 CrossRef CAS PubMed.
- P. Subha, B. N. Nair, V. Visakh, C. Sreerenjini, A. P. Mohamed, K. Warrier, T. Yamaguchi and U. Hareesh, J. Mater. Chem. A, 2018, 6, 7913–7921 RSC.
- A. Maity, R. Belgamwar and V. Polshettiwar, Nat. Protoc., 2019, 14, 2177–2204 CrossRef CAS PubMed.
- M. Niu, H. Yang, X. Zhang, Y. Wang and A. Tang, ACS Appl. Mater. Interfaces, 2016, 8, 17312–17320 CrossRef CAS PubMed.
- N. Minju, B. N. Nair, A. Peer Mohamed and S. Ananthakumar, Sep. Purif. Technol., 2017, 181, 192–200 CrossRef CAS.
- Z. Zhang, Z. P. Cano, D. Luo, H. Dou, A. Yu and Z. Chen, J. Mater. Chem. A, 2019, 7, 20985–21003 RSC.
- H. He, W. Li, M. Zhong, D. Konkolewicz, D. Wu, K. Yaccato, T. Rappold, G. Sugar, N. E. David and K. Matyjaszewski, Energy Environ. Sci., 2013, 6, 488–493 RSC.
- Z. Li, D. Wu, X. Huang, J. Ma, H. Liu, Y. Liang, R. Fu and K. Matyjaszewski, Energy Environ. Sci., 2014, 7, 3006–3012 RSC.
- J. Zhang, R. Yuan, S. Natesakhawat, Z. Wang, Y. Zhao, J. Yan, S. Liu, J. Lee, D. Luo, E. Gottlieb, T. Kowalewski, M. R. Bockstaller and K. Matyjaszewski, ACS Appl. Mater. Interfaces, 2017, 9, 37804–37812 CrossRef CAS PubMed.
- W. Shen, S. Zhang, Y. He, J. Li and W. Fan, J. Mater. Chem., 2011, 21, 14036–14040 RSC.
- M. Nandi, K. Okada, A. Dutta, A. Bhaumik, J. Maruyama, D. Derks and H. Uyama, Chem. Commun., 2012, 48, 10283–10285 RSC.
- M. Zhong, S. Natesakhawat, J. P. Baltrus, D. Luebke, H. Nulwala, K. Matyjaszewski and T. Kowalewski, Chem. Commun., 2012, 48, 11516–11518 RSC.
- Y. K. Kim, G. M. Kim and J. W. Lee, J. Mater. Chem. A, 2015, 3, 10919–10927 RSC.
- Y. Zeng, R. Zou and Y. Zhao, Adv. Mater., 2016, 28, 2855–2873 CrossRef CAS PubMed.
- Y. Chen, Z. Qiao, J. Huang, H. Wu, J. Xiao, Q. Xia, H. Xi, J. Hu, J. Zhou and Z. Li, ACS Appl. Mater. Interfaces, 2018, 10, 38638–38647 CrossRef CAS PubMed.
- M. Ding, R. W. Flaig, H.-L. Jiang and O. M. Yaghi, Chem. Soc. Rev., 2019, 48, 2783–2828 RSC.
- F.-Q. Liu, L.-L. Wang, G.-H. Li, W. Li and C.-Q. Li, ACS Appl. Mater. Interfaces, 2017, 9, 33997–34004 CrossRef CAS PubMed.
- A. Holewinski, M. A. Sakwa-Novak and C. W. Jones, J. Am. Chem. Soc., 2015, 137, 11749–11759 CrossRef CAS PubMed.
- R. Zhang, X. Wang, S. Liu, L. He, C. Song, X. Jiang and T. P. Blach, ACS Appl. Mater. Interfaces, 2019, 11, 36515–36524 CrossRef CAS PubMed.
- A. R. Sujan, S. H. Pang, G. Zhu, C. W. Jones and R. P. Lively, ACS Sustainable Chem. Eng., 2019, 7, 5264–5273 CrossRef CAS.
- F. Lou, A. Zhang, G. Zhang, L. Ren, X. Guo and C. Song, Appl. Energy, 2020, 264, 114637 CrossRef CAS.
- M. L. Sarazen, M. A. Sakwa-Novak, E. W. Ping and C. W. Jones, ACS Sustainable Chem. Eng., 2019, 7, 7338–7345 CrossRef CAS.
- J. Wang, Q. Ma, Y. Wang, Z. Li, Z. Li and Q. Yuan, Chem. Soc. Rev., 2018, 47, 8766–8803 RSC.
- S. Banerjee, T. K. Paira, A. Kotal and T. K. Mandal, Adv. Funct. Mater., 2012, 22, 4751–4762 CrossRef CAS.
- S. Huh, J. W. Wiench, J.-C. Yoo, M. Pruski and V. S.-Y. Lin, Chem. Mater., 2003, 15, 4247–4256 CrossRef CAS.
- K. Matyjaszewski, Macromolecules, 2012, 45, 4015–4039 CrossRef CAS.
- K. Matyjaszewski and J. Xia, Chem. Rev., 2001, 101, 2921–2990 CrossRef CAS PubMed.
- P. Mondal, S. Banerjee, A. S. Roy, T. K. Mandal and S. M. Islam, J. Mater. Chem., 2012, 22, 20434–20442 RSC.
- J. Pyun, S. Jia, T. Kowalewski, G. D. Patterson and K. Matyjaszewski, Macromolecules, 2003, 36, 5094–5104 CrossRef CAS.
- G. Mukherjee and K. Biradha, CrystEngComm, 2014, 16, 4701–4705 RSC.
- M. Save, G. Granvorka, J. Bernard, B. Charleux, C. Boissière, D. Grosso and C. Sanchez, Macromol. Rapid Commun., 2006, 27, 393–398 CrossRef CAS.
- Q. Zeng, D. Wu, C. Zou, F. Xu, R. Fu, Z. Li, Y. Liang and D. Su, Chem. Commun., 2010, 46, 5927–5929 RSC.
- X. Zhang, H. Qin, X. Zheng and W. Wu, Mater. Res. Bull., 2013, 48, 3981–3986 CrossRef CAS.
- C. Valencia, C. H. Valencia and F. Zuluaga, Molecules, 2018, 23, 2651 CrossRef PubMed.
- N. D. Koromilas, G. C. Lainioti, E. K. Oikonomou, G. Bokias and J. K. Kallitsis, Eur. Polym. J., 2014, 54, 39–51 CrossRef CAS.
- A. Saha, T. K. Paira, M. Biswas, S. Jana, S. Banerjee and T. K. Mandal, J. Polym. Sci., Part A: Polym. Chem., 2015, 53, 2313–2319 CrossRef CAS.
- S. Banerjee, V. Ladmiral, A. Debuigne, C. Detrembleur, S. M. W. Rahaman, R. Poli and B. Ameduri, Macromol. Rapid Commun., 2017, 38, 1700203 CrossRef PubMed.
- S. Banerjee, Y. Patil, O. Gimello and B. Ameduri, Chem. Commun., 2017, 53, 10910–10913 RSC.
- C. Tang, L. Bombalski, M. Kruk, M. Jaroniec, K. Matyjaszewski and T. Kowalewski, Adv. Mater., 2008, 20, 1516–1522 CrossRef CAS.
- M. Zhong, E. K. Kim, J. P. McGann, S.-E. Chun, J. F. Whitacre, M. Jaroniec, K. Matyjaszewski and T. Kowalewski, J. Am. Chem. Soc., 2012, 134, 14846–14857 CrossRef CAS PubMed.
- D. S. Achilias, Eur. Polym. J., 2007, 43, 2564–2575 CrossRef CAS.
- D.-W. Wang, F. Li, M. Liu, G. Q. Lu and H.-M. Cheng, Angew. Chem., Int. Ed., 2008, 47, 373–376 CrossRef CAS PubMed.
- G.-P. Hao, W.-C. Li, D. Qian and A.-H. Lu, Adv. Mater., 2010, 22, 853–857 CrossRef CAS PubMed.
- N. P. Wickramaratne and M. Jaroniec, J. Mater. Chem. A, 2013, 1, 112–116 RSC.
- X. He, J. Liu, Y. Jiang, M. Yaseen, H. Guan, J. Sun, X. Cui, D. Liao and Z. Tong, Chem. Eng. J., 2019, 361, 278–285 CrossRef CAS.
- S. O. Adio, S. A. Ganiyu, M. Usman, I. Abdulazeez and K. Alhooshani, Chem. Eng. J., 2020, 382, 122964 CrossRef CAS.
- P. Yang, L. Rao, W. Zhu, L. Wang, R. Ma, F. Chen, G. Lin and X. Hu, Ind. Eng. Chem. Res., 2020, 59, 6194–6201 CrossRef CAS.
Footnote |
† Electronic supplementary information (ESI) available: Tables of results of the kinetic study. See DOI: 10.1039/d1ma00891a |
|
This journal is © The Royal Society of Chemistry 2022 |
Click here to see how this site uses Cookies. View our privacy policy here.