DOI:
10.1039/D1MA01021B
(Paper)
Mater. Adv., 2022,
3, 3165-3173
Porous organic polymer (POP) nanosheets: an efficient photo-catalyst for visible-light assisted CO2 reduction†
Received
2nd November 2021
, Accepted 14th February 2022
First published on 15th February 2022
Abstract
We have designed a nano-sheet-like porous organic polymer (POP) constructed via a schematic hydrothermal process and characterized it using PXRD, N2 adsorption–desorption studies, UV-vis, XPS and microscopic analyses (TEM and FESEM). The synthesized POP can perform as a dynamic photo-catalyst for the production of formic acid and formaldehyde. This pure polymeric porous photo-catalytic system demonstrates exceptionally good catalytic performances for the generation of formic acid (major product) and formaldehyde (minor product) with TON values of 355 and 47, respectively, under visible light irradiation. The as-synthesized catalyst also exhibited excellent yield for the synthesis of both products HCOOH (TON: 338) and HCHO (TON: 10) even under sunlight irradiation. The recyclability of the photo-catalyst is also confirmed for five reaction cycles and the POP material showed excellent recycling capability without any visible catalyst degradation.
Introduction
Fossil fuels have been the backbone of modern industrial development since the industrial revolution. For advanced technology in industry, the combustion of fossil fuels generates carbon dioxide (CO2), which is one of the most important greenhouse gases contributing to a sharp increase in global temperature. According to the National Oceanic and Atmospheric Administration (NOAA), the mean concentration of CO2 in the atmosphere increased to 419.05 ppm in April 2021.1 The advancement of CO2 emissions control and carbon capture processes will mitigate the unusual changes seen in global climate. Because CO2 is the chief greenhouse gas, its capture and catalytic transformation is believed to be a serious matter to solve at present. Given the thermally stable and inert nature of CO2, it is extremely beneficial to construct advanced catalysts to facilitate the conversion of CO2 to other higher value-added chemicals under mild conditions. Due to the most highly oxidized form of carbon, CO2 is thermodynamically stable and/or kinetically inert.2 Therefore, utilization of CO2 is still a challenging issue and a major thriving area of research to solve the environmental problem. However, CO2 is a non-toxic, renewable, inexpensive and abundant raw C1 feedstock and it is a C1 building block for the synthesis of various valuable chemicals with added economic value such as carbonate, carbamate, urea, etc.3–8 Furthermore, through CO2 reduction some C1 chemicals such as HCHO, HCOOH, CH4, CO, and CH3OH can easily be formed through thermo-catalysis, electrocatalysis and photocatalysis methods.9 Recently, to maintain the ecological balance of the earth, photocatalytic reduction10 of CO2 has become a more efficient and greener approach to convert atmospheric CO2 into eco-friendly fuels and organic materials in a sustainable and cost-effective manner which provides a way to obtain carbon resources.11 To avert the adverse effects of global warming, a large-scale study has been dedicated to the development of CO2-philic adsorbent materials that are robust, have significantly high chemical/mechanical stability, and are regeneration efficient and economically inexpensive.12
Due to their great performance and wide application, a novel kind of emerging nanoporous material has drawn tremendous interest in the fields of gas storage, gas separation, energy conversion, medicine loading and delivery, energy storage, catalysis, and so on.13–16 As a class of emerging photocatalysts, organic conjugated polymers offer high flexibility in tuning the framework of the backbone and porosity to fulfill the requirements for photocatalytic applications.17 In this consideration, highly crosslinked porous organic polymers (POPs),18–21 with greater thermal and chemical stabilities,22 inherent nanoscale porosity,23 large surface areas24 and diverse building blocks are consummate platforms for the creation of heterogeneous catalysts for CO2 conversion. Here, we mainly focus on photocatalytic applications of POPs particularly for CO2 reduction.
In the past few years, the work on the reduction of CO2 into formic acid (HCOOH) and/or formaldehyde (HCHO) using covalent organic framework (COF) and metal oxide has been established photo-catalytically. Our recent work consisted of metal free PCA-TOL (4,4′-biphenyldicarbaldehyde-ortho-tolidine) POP with strong crystallinity and robust stability for heterogeneous photocatalytic reduction of CO2 into both formic acid (HCOOH) and formaldehyde (HCHO) under visible light in the presence of acetonitrile (CH3CN) solvent. The reduced products of HCHO and HCOOH are widely abundant feedstocks in the chemical industry and find various valuable applications. HCHO is used in hydrogen fuel cells for hydrogen gas production. It serves as a liquid organic hydrogen carrier molecule (LOHC)25 and useful life product whereas HCOOH (the two-electron reduced products of CO2)26 is used as an interesting fuel in fuel cells, a hydrogen storage material and a reducing agent for many organic reactions.27
Experimental
Preparation of the catalyst
The synthesis of the PCA-TOL porous organic polymer (POP) material is delineated in Scheme 1.
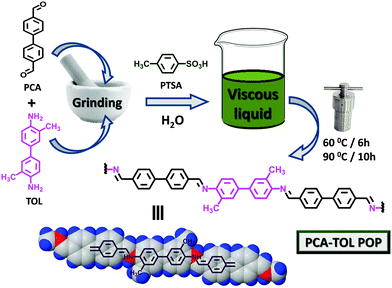 |
| Scheme 1 Synthetic route of the PCA-TOL POP nano-sheet. | |
Synthetic procedure of the PCA-TOL porous organic polymer (POP) material
PCA-TOL POP was fabricated by the reaction of 4,4′-biphenyldicarbaldehyde (PCA) and ortho-tolidine (TOL) using para-toluene sulfonic acid (PTSA) in a hydro-thermal process as shown in Scheme 1. A mixture of 7.5 mmol PTSA and 1.35 mmol TOL was taken in a mortar-pestle and homogeneously mixed for 10 minutes to obtain a grey color glue-like material. 0.9 mmol PCA was added to it subsequently with appropriate grinding for the subsequent 10–15 minutes. A small amount of distilled water (100–200 μL) was added drop-wise to form a viscous paste, and it was put into a Teflon-lined steel autoclave and heated at 60 °C for the first 6 h and then at 90 °C for the next 10 h under stable conditions. Afterward, N,N-dimethyl acetamide (DMAc) and excess acetone were used to wash the PCA-TOL POP product until it was available in pure form. The POP material was dried under vacuum at room temperature to obtain the green colored PCA-TOL POP (80% isolated yield).
General procedure for the synthesis of formic acid and formaldehyde using PCA-TOL POP
The procedure of formic acid and formaldehyde synthesis from atmospheric CO2 was performed at room temperature for 6 hours using 5 mg of PCA-TOL POP as a heterogeneous catalyst, 5 mg of nickel chloride (NiCl2) as a co-catalyst and 1 mmol triethanolamine (TEOA) as a sacrificial electron donor in the presence of 5 mL of acetonitrile (CH3CN) solvent in a round bottom flask using 445 nm blue LED light irradiation. After cooling the reaction mixture at the end, the catalyst was isolated using a filtration method and the product was confirmed using a UV-Visible spectrophotometer and also analyzed via1H and 13C NMR spectroscopy (ESI†).
Results and discussion
Characterization
The PCA-TOL POP formation was confirmed using powder diffraction analysis (Fig. 1). The presence of sharp peaks for the porous polymeric material implies the crystalline character of PCA-TOL POP. The crystallite size of PCA-TOL POP was calculated by Scherrer's equation as shown below:
D = κλ/β cos θ, |
where κ (the shape factor) = 0.9 (spherical particle), λ (X-ray wavelength) = 0.15406 nm, β = FWHM and θ (the Bragg angle) = 21.25/2 = 10.625.
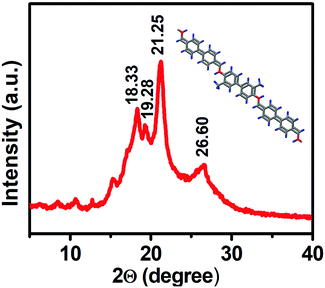 |
| Fig. 1 Powder XRD patterns of PCA-TOL POP. | |
The particle size was found to be 7.97 nm.
The FT-IR analysis spectra of the PCA-TOL POP catalyst are depicted in Fig. 2. The absorption band at 2920 cm−1 signifies the presence of the sp3 bond of carbon–hydrogen in the porous polymeric material PCA-TOL POP. The presence of the C
C bonds in the aromatic rings was confirmed by the appearance of a sharp peak at 1600 cm−1 (stretching frequency). A peak appeared at 1040 cm−1 that corresponds to the C–N stretching vibration. The broad peak at 3441 cm−1 appeared from the O–H stretching vibration of the adsorbed water.
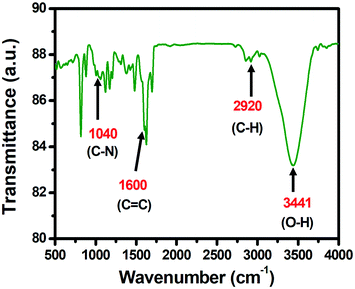 |
| Fig. 2 FTIR spectra of PCA-TOL POP. | |
The thermal stability of the photocatalyst was studied via thermal gravimetric analysis of PCA-TOL POP executed at a rate of 10 °C temperature ramp/minute in air. Fig. 3 depicts the TG/DTA profile of the PCA-TOL POP catalyst. Due to burning of the residual portion and degradation of the POP framework, the reduction in mass begins at around 550 °C (Fig. 10). The exothermic peaks at 576 °C and 644 °C suggest the oxidative destruction of the organic matrix.
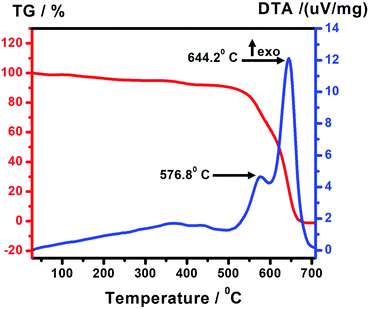 |
| Fig. 3 TGA-DTA profile plot of PCA-TOL POP. | |
The N2 adsorption–desorption study of the POP photocatalyst is depicted in Fig. 4. It shows a type III isotherm with a H3 loop which indicates the presence of slit-like pores with non-uniform size and/or shape. The subsequent pore size distribution (PSD) resulting from the respective adsorption data is given in the inset of the isotherm plot, which confirms the presence of pores with irregular shape and size in the sample. The POP catalyst contains pores with a diameter range of about 2.5 nm to 10 nm, which falls in the mesoporous region (2–50 nm). The mesoporous slit-like pores were generated from the interparticle pores among aggregated sheet-like particles. The estimated BET surface area and total pore volume of the POP catalyst are found to be 80.64 m2 g−1 and 0.43 cm3 g−1, respectively.
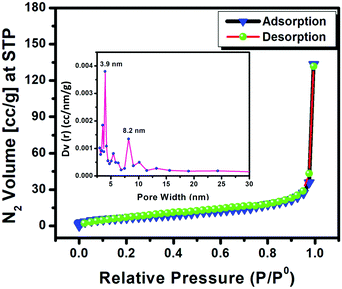 |
| Fig. 4 N2 adsorption–desorption isotherm of the POP material. The pore size distribution is shown in the inset. | |
The nano-sheet-like structure of the PCA-TOL POP material is observed in the FESEM images (Fig. 5) which is further established by the HR-TEM images (Fig. 6). The crystalline organic nanosheets formed via strong interactions can be obtained using a reaction induced self-assembly approach.28 The porosity in the catalyst can be also observed in the HR-TEM images shown in Fig. 6b, c and e. Fig. 6f indicates the EDS analysis revealing the atomic percentages of carbon, nitrogen and oxygen as 85.9%, 2.3% and 11.8%, respectively, in the sample. The sheet-like structure can be further observed from the atomic force microscopy (AFM) image (Fig. 6g and h). The corresponding height profiles reflected that the average thickness of the nanosheets is ∼70.0 nm (Fig. 6i).
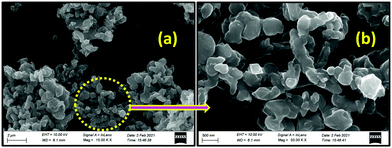 |
| Fig. 5 FESEM images of the POP material at two different scales (a) 2 μm and (b) 500 nm. | |
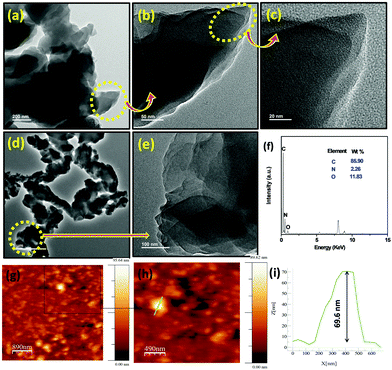 |
| Fig. 6 HR-TEM images of PCA-TOL POP (a–e) at three different scales, (f) EDAX spectra and (g–i) AFM images of PCA-TOL POP. | |
The UV-Visible absorbance spectra (solid state) of the synthesized POP catalyst were recorded using barium sulphate as a reflecting substance. The presence of the broad absorption spectra confirmed multiple transitions in the extremely well-ordered conjugation arrangement in the material. As shown in Fig. 7a, the peak of POP in the UV-vis region suggests transitions of σ to σ* and π to π* attributed to the aromatic cycles. The fabricated POP shows an absorption edge at about 515 nm signifying the absorption of light in both the ultra-violet and visible regions. The band gap energy (Eg) is calculated using the following Tauc equation:
where
α,
hν, and
A are the absorption coefficient, energy of the photons and proportionality constant, respectively, according to the possibility of transition. The value constant,
n = 2, 1/2, 3 and 3/2 corresponds to transition patterns of indirect allowed, direct allowed, indirect forbidden and direct forbidden, respectively. In this context
n = 1/2 signifies direct allowed band gap. Here, the (
αhν)
2vs. hν curve for the POP material is depicted in
Fig. 7b. The value of band gap energy (
Eg) is observed to be 2.48 eV which is calculated from the tangent extrapolated to the
X-axis, signifying that the migration of electrons takes place between the valence band and the conduction band due to irradiation under visible light. Hence, the as-prepared POP could serve as a new potential applicant for a metal free photocatalytic reaction under visible-light irradiation.
Fig. 7c shows the XPS valence band spectra of the POP catalyst from which the valence band energy (VB) is calculated to be 2.23 eV. The schematic diagram of the band structure of the synthesized POP photocatalyst is shown in
Fig. 7d which was obtained from the experimental results. The conduction band energy (CB) was found to be −0.25 eV.
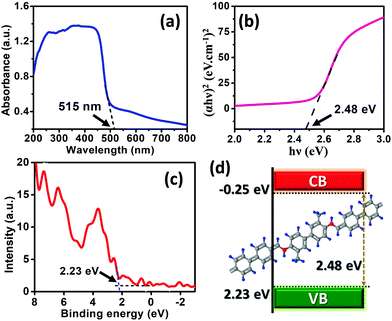 |
| Fig. 7 (a) UV-Visible absorbance spectra and (b) Tauc plot for the absorption spectra. (c) XPS valence band spectra and (d) schematic diagram of the band structure of the POP sample. | |
The XPS survey (Fig. 8a) scan confirms that the carbon (C) and nitrogen (N) exists within the synthesized catalyst. The XPS spectrum (high-resolution) of the C 1s region (Fig. 8b) on deconvolution illustrates peaks at binding energies of 284.8 and 285.5 eV, respectively indicating the presence of C–C/C
C/C–H and C–N/C
N bonds in the catalyst.29 The N 1s band (Fig. 8c) present at 398.8 eV might be associated with the presence of the nitrogen atoms of the amino groups of the POP. The O 1s band at 531.5 eV (Fig. 8a) validates the presence of the surface adsorbed oxygen atoms within the synthesized catalyst.30
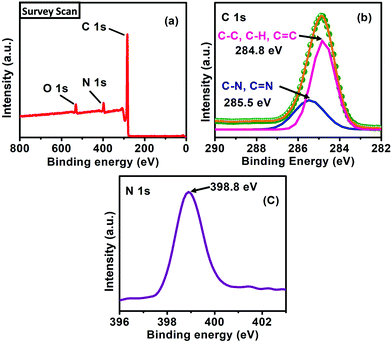 |
| Fig. 8 (a) XPS survey scan, XPS curve of (b) C 1s and (c) N1s for PCA-TOL POP. | |
Catalytic activity
The photochemical reaction of CO2 reduction into formic acid (HCOOH) and formaldehyde (HCHO) under atmospheric pressure was carried out in the presence of heterogeneous PCA-TOL POP (5 mg), nickel chloride (NiCl2, 5 mg) co-catalyst and triethanolamine (TEOA, 1 mmol) as a sacrificial electron donor in acetonitrile (CH3CN, 5 mL) solvent at room temperature for 6 h. The proposed reaction is shown in Fig. S1 (ESI†). The reaction mixture was irradiated using 445 nm blue LED light under incessant stirring. At the end of this reaction, the respective yield of both the products was measured from the calibration plots (Fig. S2 and S3, ESI†) using a UV-Visible spectrophotometer and PCA-TOL POP was filtered and the filtrate portion was analyzed using 1H NMR and 13C NMR spectroscopy (Fig. S4 and S5, ESI†), which validates the generation of formic acid (HCOOH) and formaldehyde (HCHO). A range of conditions for our recent photochemical work were verified and the outcomes are discussed briefly in Tables 1 and 2.
Table 1 Optimization table for the reduction of CO2via photochemical reaction into formic acid (HCOOH)
S. no. |
PCA-TOL (mg) |
Co-Cat (mg) |
Light source |
Temp. (°C) |
Yield of HCOOHa (mol) |
TON of HCOOHa |
Reaction conditions unless otherwise noted: catalyst (5 mg), NiCl2 (5 mg), acetonitrile (5 mL), TEOA (1 mmol), room temperature, pressure (1 atm), time (6 h), and CO2 balloon. Determined from the calibration curve (the concentration of HCOOH is known) obtained using a UV-Visible spectrometer. Irradiation under an open atmosphere for 6 hours. The reaction was completed in 10 hours. The reaction proceeded without any sacrificial electron donor. |
1 |
5 |
— |
– |
60 |
0 |
0 |
2 |
— |
5 |
— |
60 |
0 |
0 |
3 |
5 |
5 |
— |
60 |
0 |
0 |
4 |
5 |
5 |
— |
40 |
0 |
0 |
5 |
5 |
5 |
— |
50 |
0 |
0 |
6 |
5 |
5 |
445 nm |
RT |
0.0137 |
355 |
7 |
5 |
5 |
White LED |
RT |
0.0124 |
321 |
8 |
5 |
5 |
Sunlight |
RT |
0.013 |
338 |
9b |
5 |
5 |
445 nm |
RT |
0 |
0 |
10c |
5 |
— |
445 nm |
RT |
0 |
0 |
11 |
— |
5 |
445 nm |
RT |
0 |
0 |
12 |
5 |
5 |
— |
RT |
0 |
0 |
13d |
5 |
5 |
445 nm |
RT |
0 |
0 |
Table 2 Optimization table for the reduction of CO2via photochemical reaction into formaldehyde (HCHO)
S. no. |
PCA-TOL (mg) |
Co-Cat (mg) |
Light source |
Temp. (°C) |
Yield of HCHOa (mol) |
TON of HCHOa |
Reaction conditions unless otherwise noted: catalyst (5 mg), NiCl2 (5 mg), acetonitrile (5 mL), TEOA (1 mmol), room temperature, pressure (1 atm), time (6 h), and CO2 balloon. Determined from the calibration curve (the concentration of HCOOH is known) obtained using a UV-Visible spectrometer. Irradiation under an open atmosphere for 6 hours. Reaction was completed in 10 hours. Reaction proceeded without any sacrificial electron donor. |
1 |
5 |
— |
— |
60 |
0 |
0 |
2 |
— |
5 |
— |
60 |
0 |
0 |
3 |
5 |
5 |
— |
60 |
0 |
0 |
4 |
5 |
5 |
— |
40 |
0 |
0 |
5 |
5 |
5 |
— |
50 |
0 |
0 |
6 |
5 |
5 |
445 nm |
RT |
0.0018 |
47 |
7 |
5 |
5 |
White LED |
RT |
0.0005 |
13 |
8 |
5 |
5 |
Sunlight |
RT |
0.0004 |
10 |
9b |
5 |
5 |
445 nm |
RT |
0 |
0 |
10c |
5 |
— |
445 nm |
RT |
0 |
0 |
11 |
— |
5 |
445 nm |
RT |
0 |
0 |
12 |
5 |
5 |
— |
RT |
0 |
0 |
13d |
5 |
5 |
445 nm |
RT |
0 |
0 |
Irradiation of the solution containing PCA-TOL POP (5 mg) as a photocatalyst, nickel chloride (NiCl2, 5 mg), TEOA (1 mmol) and acetonitrile as the solvent with 445 nm (12 W cm−2) under 1 atm CO2 pressure for 6 h at room temperature produced formic acid with 355 TON as a major product (Table 1, entry 6) along with 47 TON formaldehyde as the minor product (Table 2, entry 6). The analysis of UV-DRS suggests that the POP catalyst exhibited outstanding absorbance for the complete region of visible light, and for this reason this POP catalyst is selectively excited in the presence of visible light which acts as an energy source. It is worth noting that the reaction proceeds even under sunlight and performs well for the generation of formic acid with 338 TON (Table 1, entry 8) and formaldehyde with 10 TON (Table 2, entry 8). The production of formic acid with 321 TON (Table 1, entry 7) and formaldehyde with 13 TON (Table 2, entry 7) was also observed when this reaction was carried out under irradiation of white LED light. In the nonexistence of light at room temperature (Table 1, entry 12 and Table 2, entry 12) even at high temperatures (Table 1, entry 3 and Table 2, entry 3) no reaction could be started, which ensures light dependence on CO2 reduction by the POP component. In a dark environment, at high temperatures up to 60 °C (entry 1–5 in Tables 1 and 2), the reaction did not proceed which indicates that these are not thermal transformations. It is significant to note that without the POP photocatalyst, irradiation of the NiCl2 co-catalyst with a sacrificial electron source and CO2 in the CH3CN solvent could not develop any product (entry 2 in Table 1 and entry 2 in Table 2). Correspondingly, with the excitation of the POP material in the range of visible light along with a co-catalyst in the absence of TEOA (sacrificial electron source), the reaction could not proceed (entry 13 in Table 1 and entry 13 in Table 2). The reaction mainly occurred following the three steps: (i) photoexcitation of POP, (ii) transfer of electron to the co-catalyst NiCl2 and (iii) regeneration of POP by a sacrificial electron source, TEOA.
The intensity of light was varied from 3 W to 17 W using the optimized photocatalytic system for the CO2 reduction to HCOOH and HCHO (Fig. 9). From Fig. 9, it is evident that with increasing light intensity the obtained yields of the products with CO2 reduction increase. At the beginning with increasing light intensity the HCOOH product formation increases rapidly but after a certain amount of light intensity the increment rate slowed down, which could be due the fact that with increasing photon flux the 4e− transfer reaction was facilitated rather than the 2e− transfer, therefore consequently HCOOH converted to HCHO through a further reduction process. This demonstrates that the formation of products depends on the quantity of photon-flux on the reaction mixture.
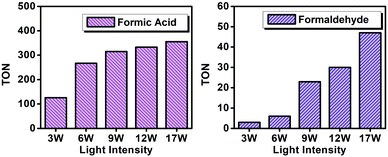 |
| Fig. 9 Effect of light intensity on the yield of photocatalytic CO2 reduction products catalyzed by PCA-TOL POP. | |
Fig. 10 suggests that the increment of the HCOOH and HCHO production was observed with increasing irradiation time until 6 h. Furthermore, the reaction mixture was irradiated up to 48 h without any enhancement of yield. Hence, it is concluded that the completion of reaction time was noticed after irradiating the reaction mixture for 6 h. It is interesting to note that after 6 h of irradiation, the formation of both the products slowed down and the amount of yield decreases.
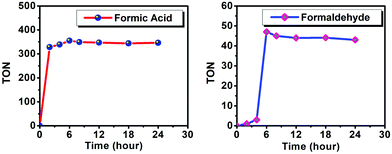 |
| Fig. 10 Formation of formic acid and formaldehyde with time upon irradiation. | |
The formation of HCOOH and HCHO with CO2 reduction using the POP catalyst is solely linked to the light as verified by investigating the production of products while controlling the light and dark environments at 30 min breaks (Fig. 11). The product formation increases during irradiation of light; however, in the progression of a 3 h experiment it remains nearly constant in the absence of light.
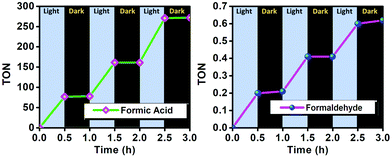 |
| Fig. 11 TON of formic acid formed with respect to time while modulating between light and dark under optimum reaction conditions. | |
Plausible mechanism
The probable formation mechanism of HCOOH and HCHO is depicted in Fig. 12. Here, PCA-TOL POP performs as a potentially dynamic photocatalyst for avisible-light driven reaction. Besides the textural properties, the morphology (sheet-like) of the synthesized POP material offers additional geometrical sites which provide many surface-active sites and assist heterogeneous catalysis. Upon irradiation with visible light, PCA-TOL POP becomes a photo-excited state (PCA-TOL POP*) and reduces H+ into H·. After that, the catalytic cycle proceeds through an oxidative quenching process31 followed by formation of a cationic radical which remains in the ground state by acquiring a single electron from a sacrificial electron donor (TEOA), while PCA-TOL POP regenerates itself and is available for the next cycle. Meanwhile, the metal cocatalyst (NiCl2) with a lower Fermi level can readily trap electrons and it possesses effective reduction sites within the pores that significantly aid reduction reactions. The photocatalytic activity of the POP catalyst is boosted by the partial captivity of the metal active sites within the pores of the photocatalyst, which create strong interfacial electronic interactions between the POP photocatalyst and NiCl2 cocatalyst, enhancing the interfacial electron transfer from POP to NiCl2. When Ni(I) oxidizes itself into Ni(II), CO2 gets reduced to HCOOH by two electron charge transfer and HCHO by four electron charge transfer using TEOA as the proton source.
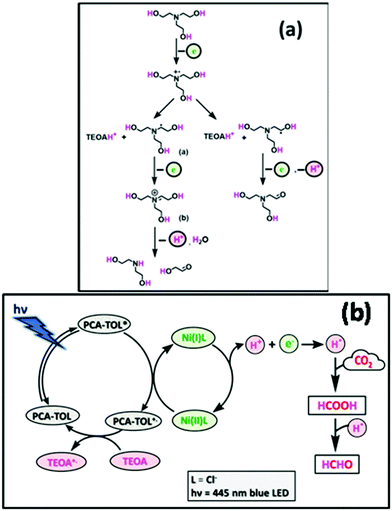 |
| Fig. 12 Proposed (a) degradation pathway of TEOA and (b) plausible mechanism for the photo-induced CO2 reduction reaction into HCOOH and HCHO by the PCA-TOL POP catalyst. | |
Comparison for photocatalytic potentiality of our POP catalyst in CO2 reduction reactions with other published catalyst schemes
The comparison of our recent work using a PCA-TOL POP compound with other reported catalytic processes for the production of HCOOH and HCHO is summarized in Table 3. Our catalyst demonstrated the excellent yields of the outcome with economically efficacious green reaction conditions compared to the other reported catalysts. According to some previously reported studies,32,33 sheet-like POPs are advantageous for heterogeneous catalysis rather than bulk POPs. Bulk POP formed by stacked layers creates an obstacle for ion diffusion and for reaching the active sites, and the defects of POPs and boundaries between particles confine the transportation of electrons and ions which lead to an increased mass transport resistance and inherent low conductivity of bulk POPs, consequently limiting their applications. On the other hand, the sheet-like POPs with a thickness of single- or few-atom layers having unique chemical, physical, electronic, and optical properties can minimize the transport length for the ions to reach the active sites, and provide sufficient electron conduction pathways.
Table 3 Comparison table for CO2 reduction reactions using PCA-TOL POP with other reported catalysts
Catalyst |
Reaction conditions |
Yield of HCOOH (mol) |
Yield of HCHO (mol) |
Ref. |
Giant polyoxome-alate{Mo368} |
Catalyst (0.0003 mmol), 373 nm UV-light |
0.0083 |
3.7 × 10−5 |
34
|
TFPG-DAAQ COF |
Photocatalyst (10 mg), Co-catalyst (Co(dmg)2), 445 nm blue LED light, CO2 (1 atm), room temperature |
0.0108 |
— |
31
|
SnO2 nanoparticles |
Catalyst (10 mg), white LED light, CO2 (1 atm), room temperature |
0.0076 |
— |
26
|
PCA-TOL POP |
Photocatalyst (5 mg), Co-catalyst (NiCl2),445 nm blue LED light, CO2 (1 atm), room temperature |
0.0137 |
0.0018 |
This study |
Recyclability of the catalyst
To verify the recyclability of the PCA-TOL POP catalyst, the catalyst was collected after the completion of each reaction cycle using a centrifugation method followed by several washing steps with ethanol followed by drying in an oven for the subsequent run. Fig. 13 shows that negligible changes were noticed in the yields of both products (formic acid and formaldehyde) after reprocessing the POP up to 5 reaction cycles. The TON values of the products for different cycles are shown in Table 4. As shown in the FTIR spectra of the recycled catalyst in Fig. S6, the recycled catalyst retains all the peaks of the original PCA-TOL POP after recycling, i.e. the structure of the catalyst remains unchanged. Furthermore, the morphology of the recycled catalyst also retained itself which was confirmed by the FESEM analysis of the recycled catalyst as shown in Fig. S7. These observations help us to predict that the prepared PCA-TOL POP material is heterogeneous in nature as well as stable, recyclable and effective for photocatalytic CO2 reduction reaction under environmentally green reaction conditions. This investigation suggests the economic significance and scalability of the POP as an efficient photocatalyst for the reaction of CO2 reduction.
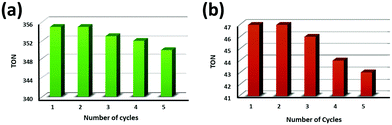 |
| Fig. 13 Recyclable potentiality of the PCA-TOL POP photocatalyst for (a) formic acid and (b) formaldehyde production. | |
Table 4 Chart of catalytic activity for the recycled PCA-TOL POP photocatalyst
Entry |
No. of cycles |
TONa of formic acid |
TONa of formaldehyde |
Reaction conditions unless otherwise noted: catalyst (5 mg), NiCl2 (5 mg), acetonitrile (5 mL), TEOA (1 mmol), room temperature, pressure (1 atm), time (6 h), and CO2 balloon. The yield of each product was ascertained from a calibration plot obtained using a UV-vis spectrometer. |
1 |
1st |
355 |
47 |
2 |
2nd |
355 |
47 |
3 |
3rd |
353 |
45 |
4 |
4th |
352 |
44 |
5 |
5th |
350 |
42 |
Conclusion
A sheet-like PCA-TOL POP photocatalyst is fabricated through a facile solvothermal process. The formed POP material serves as a potential photocatalyst along with NiCl2 as the co-catalyst to reduce CO2 under visible light (blue LED) irradiation and atmospheric pressure in a green route to generate formic acid and formaldehyde with an excellent TON value. The catalytic reduction does not proceed without a catalyst, co-catalyst or even light and heat which is confirmed by control reactions and therefore the yield of the reduced products can effortlessly be monitored by tuning the light intensity. Furthermore, the POP photocatalyst additionally provides facile recovery and reusability for several reaction cycles without considerable catalyst deactivation.
Conflicts of interest
There are no conflicts to declare.
Acknowledgements
SMI thankfully acknowledges the Department of Science and Technology DST-SERB (project reference no. CRG/2020/000244), New Delhi, Govt. of India and Council of Scientific and Industrial and Research, CSIR (project reference no 02(0453)21/EMR-II), New Delhi, Govt. of India for providing financial support. I. H. Chowdhury is thankful to CSIR, India (File no. 09/106(0181)/2019-EMR-I) for her fellowship. S. Das is thankful to SVMCM Fellowship, Govt. of West Bengal, India. SMI is thankful to University of Kalyani for providing support under the PURSE and PRG program. We acknowledge the DST for providing a grant to the Department of Chemistry by FIST, PURSE grant.
Notes and references
-
https://gml.noaa.gov/ccgg/trends/mlo.html
.
-
(a) Q. Liu, L. Wu, R. Jackstell and M. Beller, Nat. Commun., 2015, 6, 1–5 Search PubMed;
(b) M. R. Kember, A. Buchard and C. K. Williams, Chem. Commun., 2011, 47, 141–163 RSC.
-
(a) A. J. Kamphuis, F. Picchioni and P. P. Pescarmona, Green Chem., 2019, 21, 406–448 RSC;
(b) I. H. Chowdhury, A. H. Chowdhury, P. Sarkar and S. M. Islam, ChemNanoMat, 2021, 7, 580–591 CrossRef;
(c) A. H. Chowdhury, I. H. Chowdhury, S. Biswas and S. M. Islam, Mol. Catal., 2020, 493, 111050 CrossRef;
(d) A. H. Chowdhury, I. H. Chowdhury and S. M. Islam, Ind. Eng. Chem. Res., 2019, 58, 11779–11786 CrossRef CAS;
(e) S. Ghosh, R. A. Molla, U. Kayal, A. Bhaumik and S. M. Islam, Dalton Trans., 2019, 48, 4657–4666 RSC;
(f) S. M. Islam, D. Mal, B. K. Palit and C. R. Saha, J. Mol. Catal. A: Chem., 1999, 142, 169–181 CrossRef CAS;
(g) N. Haque, S. Biswas, P. Basu, I. H. Biswas, R. Khatun, A. Khan and S. M. Islam, New J. Chem., 2020, 44, 15446–15458 RSC;
(h) A. Sahoo, A. H. Chowdhury, P. Singha, A. Banerjee, S. M. Islam and T. Bala, Mol. Catal., 2020, 493, 111070 CrossRef CAS.
-
(a) B. Yu and L. N. He, ChemSusChem, 2015, 8, 52–62 CrossRef CAS PubMed;
(b) H. R. Li and L. N. He, Organometallics, 2019, 39, 1461–1475 CrossRef;
(c) M. Y. Wang, Y. Cao, X. Liu, N. Wang, L. N. He and S. H. Li, Green Chem., 2017, 19, 1240–1244 RSC;
(d) L. Sun, J. H. Ye, W. J. Zhou, X. Zeng and D. G. Yu, Org. Lett., 2018, 20, 3049–3052 CrossRef CAS PubMed;
(e) S. S. Islam, P. Bhanja, K. Ghosh, R. A. Molla, N. Yasmin, D. Das and S. M. Islam, ChemistrySelect, 2017, 2, 10595–10602 CrossRef CAS;
(f) N. Haque, S. Biswas, S. Ghosh, A. H. Chowdhury, A. Khan and S. M. Islam, ACS Appl. Nano Mater., 2021, 4, 7663–7674 CrossRef CAS.
-
(a) Y. Chen and T. Mu, Green Chem., 2019, 21, 2544–2574 RSC;
(b) P. Sarkar, A. H. Chowdhury, S. Riyajuddin, S. Biswas, K. Ghosh and S. M. Islam, New J. Chem., 2020, 44, 744–752 RSC;
(c) P. Chakrabortty, A. Das, A. H. Chowdhury, S. Ghosh, A. Khan and S. M. Islam, New J. Chem., 2021, 45, 4738–4745 RSC;
(d) P. Sarkar, A. H. Chowdhury, S. Biswas, A. Khan and S. M. Islam, Mater. Today Chem., 2021, 21, 100509 CrossRef CAS;
(e) S. Biswas, R. Khatun, M. Sengupta and S. M. Islam, Mol. Catal., 2018, 452, 129–137 CrossRef CAS;
(f) S. Roy, B. Banerjee, A. Bhaumik and S. M. Islam, RSC Adv., 2016, 6, 31153–31160 RSC;
(g) S. Ghosh, P. Bhanja, R. A. Molla, R. Khatun and S. M. Islam, ChemistrySelect, 2017, 2, 2159–2165 CrossRef CAS.
-
(a) S. Wang and C. Xi, Chem. Soc. Rev., 2019, 48, 382–404 RSC;
(b) R. A. Molla, M. A. Iqubal, K. Ghosh and S. M. Islam, Green Chem., 2016, 18, 4649–4656 RSC;
(c) R. Khatun, S. Biswas, I. H. Biswas, S. Riyajuddin, N. Haque and K. Ghosh, J. CO2 Utiliz., 2020, 40, 101180 CrossRef CAS;
(d) R. Khatun, P. Bhanja, R. A. Molla, S. Ghosh, A. Bhaumik and S. M. Islam, Mol. Catal., 2017, 434, 25–31 CrossRef CAS;
(e) S. Biswas, R. Khatun, M. Dolai, I. H. Biswas, N. Haque, M. Sengupta and S. M. Islam, New J. Chem., 2020, 44, 141–151 RSC;
(f) I. H. Biswas, S. Biswas, M. S. Islam, S. Riyajuddin, P. Sarkar and K. Ghosh, New J. Chem., 2019, 43, 14643–14652 RSC;
(g) S. Ghosh, A. Ghosh, S. Riyajuddin, S. Sarkar, A. H. Chowdhury and K. Ghosh, Chem. Cat. Chem., 2020, 12, 1055–1067 CAS;
(h) S. Sarkar, S. Ghosh, J. Mondal and S. M. Islam, Chem. Commun., 2020, 56, 12202–12205 RSC;
(i) T. K. Dey, P. Bhanja, P. Basu, A. Ghosh and S. M. Islam, ChemistrySelect, 2019, 4, 14315–14328 CrossRef CAS;
(j) S. Ghosh, A. Ghosh, S. Biswas, M. Sengupta, D. Roy and S. M. Islam, ChemistrySelect, 2019, 4, 3961–3972 CrossRef CAS;
(k) S. S. Islam, S. Biswas, R. Ali Molla, N. Yasmin and S. M. Islam, ChemNanoMat, 2020, 6, 1386–1397 CrossRef CAS;
(l) P. Basu, T. K. Dey, S. Riyajuddin, S. Biswas, K. Ghosh and S. M. Islam, New J. Chem., 2020, 44, 12680–12691 RSC.
-
(a) B. Grignard, S. Gennen, C. Jérôme, A. W. Kleij and C. Detrembleur, Chem. Soc. Rev., 2019, 48, 4466–4514 RSC;
(b) R. Khatun, S. Biswas, S. Islam, I. H. Biswas, S. Riyajuddin, K. Ghosh and S. M. Islam, ChemCatChem, 2019, 11, 1303–1312 CrossRef CAS;
(c) M. Sengupta, A. Bag, S. Ghosh, P. Mondal, A. Bordoloi and S. M. Islam, J. CO2 Utiliz., 2019, 34, 533–542 CrossRef CAS;
(d) A. H. Chowdhury, S. Ghosh and S. M. Islam, New J. Chem., 2018, 42, 14194–14202 RSC;
(e) R. Khatun, P. Bhanja, P. Mondal, A. Bhaumik, D. Das and S. M. Islam, New J. Chem., 2017, 41, 12937–12946 RSC;
(f) A. H. Chowdhury, U. Kayal, I. H. Chowdhury, S. Ghosh and S. M. Islam, ChemistrySelect, 2019, 4, 1069–1077 CrossRef CAS;
(g) S. Ghosh, P. Bhanja, N. Salam, R. Khatun, A. Bhaumik and S. M. Islam, Catal. Today, 2018, 309, 253–262 CrossRef CAS.
-
(a) M. Cokoja, C. Bruckmeier, B. Rieger, W. A. Herrmann and F. E. Kühn, Angew. Chem., Int. Ed., 2011, 50, 8510–8537 CrossRef CAS PubMed;
(b) I. Omae, Coord. Chem. Rev., 2012, 256, 1384–1405 CrossRef CAS;
(c) S. Ghosh, S. Riyajuddin, S. Sarkar, K. Ghosh and S. M. Islam, ChemNanoMat, 2020, 6, 160–172 CrossRef CAS;
(d) S. Ghosh, P. Mondal, D. Das, K. Tuhina and S. M. Islam, J. Organomet. Chem., 2018, 866, 1–12 CrossRef CAS;
(e) N. Salam, P. Paul, S. Ghosh, U. Mandi, A. Khan, S. M. Alam, D. Das and S. M. Islam, New J. Chem., 2020, 44, 5448–5456 RSC;
(f) S. S. Islam, N. Salam, R. A. Molla, S. Riyajuddin, N. Yasmin, D. Das and K. Ghosh, Mol. Catal., 2019, 477, 110541 CrossRef;
(g) R. K. Mondal, S. Riyajuddin, A. Ghosh, S. Ghosh, K. Ghosh and S. M. Islam, J. Organomet. Chem., 2019, 880, 322–332 CrossRef CAS;
(h) S. Biswas, D. Roy, S. Ghosh and S. M. Islam, J. Organomet. Chem., 2019, 898, 120877 CrossRef;
(i) A. Das, R. K. Mondal, P. Chakrabortty, S. Riyajuddin and A. H. Chowdhury, Mol. Catal., 2021, 499, 111253 CrossRef CAS.
-
(a) X. He, L. Q. Qiu, W. J. Wang, K. H. Chen and L. N. He, Green Chem., 2020, 22, 7301–7320 RSC;
(b) Z. J. Wang, H. Song, H. Liu and J. Ye, Angew. Chem., Int. Ed., 2020, 59, 8016–8035 CrossRef CAS PubMed.
- I. H. Chowdhury, A. H. Chowdhury, A. Das, A. Khan and S. M. Islam, New J. Chem., 2020, 44, 11720–11726 RSC.
- Z. Li, J. Chu, D. Meng, Y. Wen, X. Xing, H. Miao, M. Hu, C. Yu, Z. Wei, Y. Yang and Y. Li, ACS Catal., 2019, 9, 8659–8668 CrossRef CAS.
- P. Bhanja, A. Modak and A. Bhaumik, ChemCatChem, 2019, 11, 244–257 CrossRef CAS.
- S. Das, P. Heasman, T. Ben and S. Qiu, Chem. Rev., 2017, 117, 1515–1563 CrossRef CAS PubMed.
- T. X. Wang, H. P. Liang, D. A. Anito, X. Ding and B. H. Han, J. Mater. Chem. A, 2020, 8, 7003–7034 RSC.
- M. Du, A. M. Agrawal, S. Chakraborty, S. J. Garibay, R. Limvorapitux, B. Choi, S. T. Madrahimov and S. T. Nguyen, ACS Sustainable Chem. Eng., 2019, 7, 8126–8135 CrossRef CAS.
- W. Liu, C. Wang, L. Zhang, H. Pan, W. Liu, J. Chen, D. Yang, Y. Xiang, K. Wang, J. Jiang and X. Yao, J. Mater. Chem. A, 2019, 7, 3112–3119 RSC.
- C. Zhao, Z. Chen, R. Shi, X. Yang and T. Zhang, Adv. Mater., 2020, 32, 1907296 CrossRef CAS PubMed.
- Z. Li and Y. W. Yang, J. Mater. Chem. B, 2017, 5, 9278–9290 RSC.
- P. Kaur, J. T. Hupp and S. T. Nguyen, ACS Catal., 2011, 1, 819–835 CrossRef CAS.
-
(a) W. Zhang, B. Aguila and S. Ma, J. Mater. Chem. A, 2017, 5, 8795–8824 RSC;
(b) X. Zou, H. Ren and G. Zhu, Chem. Commun., 2013, 49, 3925–3936 RSC.
- Q. Sun, Z. Dai, X. Meng, L. Wang and F. S. Xiao, ACS Catal., 2015, 5, 4556–4567 CrossRef CAS.
- T. Zhang, G. Xing, W. Chen and L. Chen, Mater. Chem. Front., 2020, 4, 332–353 RSC.
- B. Aguila, Q. Sun, J. A. Perman, L. D. Earl, C. W. Abney, R. Elzein, R. Schlaf and S. Ma, Adv. Mater., 2017, 29, 1700665 CrossRef PubMed.
- Q. Sun, Z. Dai, X. Meng, L. Wang and F. S. Xiao, ACS Catal., 2015, 5, 4556–4567 CrossRef CAS.
- L. E. Heim, H. Konnerth and M. H. Prechtl, Green Chem., 2017, 19, 2347–2355 RSC.
- A. H. Chowdhury, A. Das, S. Riyajuddin, K. Ghosh and S. M. Islam, Catal. Sci. Tech., 2019, 9, 6566–6569 RSC.
- H. Wu, J. Song, C. Xie, Y. Hu and B. Han, Green Chem., 2018, 20, 1765–1769 RSC.
- L. Wang, J. Liu, H. Wang, H. Cheng, X. Wu, Q. Zhang and H. Xu, Sci. Bull., 2021, 66, 265–274 CrossRef CAS.
- J. F. Moulder, Phys. Electron., 1995, 230–232 Search PubMed.
- Z. Xin, Y. Qiuhua and C. U. I. Jinjin, J. Rare Earths, 2008, 26, 511–514 CrossRef.
- P. Sarkar, S. Riyajuddin, A. Das, A. H. Chowdhury, K. Ghosh and S. M. Islam, Mol. Catal., 2020, 484, 110730 CrossRef CAS.
- J. Li, X. Jing, Q. Li, S. Li, X. Gao, X. Feng and B. Wang, Chem. Soc. Rev., 2020, 49, 3565–3604 RSC.
- H. Wang, Z. Zeng, P. Xu, L. Li, G. Zeng, R. Xiao, Z. Tang, D. Huang, L. Tang, C. Laiand and D. Jiang, Chem. Soc. Rev., 2019, 48, 488–516 RSC.
- S. Das, T. Balaraju, S. Barman, S. S. Sreejith, R. Pochamoni and S. Roy, Front. Chem., 2018, 6, 514 CrossRef CAS PubMed.
Footnote |
† Electronic supplementary information (ESI) available. See DOI: 10.1039/d1ma01021b |
|
This journal is © The Royal Society of Chemistry 2022 |
Click here to see how this site uses Cookies. View our privacy policy here.