DOI:
10.1039/D2RA00064D
(Paper)
RSC Adv., 2022,
12, 11207-11215
Facile fabrication of a phosphonium-based ionic liquid impregnated chitosan adsorbent for the recovery of hexavalent chromium†
Received
5th January 2022
, Accepted 4th April 2022
First published on 11th April 2022
Abstract
Chitosan adsorbents impregnated with a phosphonium-based ionic liquid (Chi_IL), trioctyldodecyl phosphonium chloride, were prepared for the adsorption of hexavalent chromium and compared to the performance of native chitosan. The physical and chemical properties of the adsorbents were characterized by Fourier-transform infrared spectroscopy, X-ray diffraction, scanning electron microscopy, and energy-dispersive X-ray spectroscopy. Effects of various parameters, such as pH, adsorbent dosage, contact time, temperature, and multi-component systems, were systematically examined. Chi_IL showed a high adsorption capacity (282.6 mg g−1) compared to native chitosan (238.1 mg g−1). The adsorption kinetics of the metals followed a pseudo-second-order kinetic model, and the experimental data were a good fit for the Freundlich isotherm model. Following the isotherm and activation energy parameter, adsorption of Cr(VI) onto Chi_IL follows a chemisorption process, possibly through an anionic exchange with the anion of the IL. The thermodynamic parameters suggested that the adsorption of Cr(VI) is a spontaneous and exothermic reaction. In the column adsorption, Chi_IL exhibited a longer column exhaustion time than that of native chitosan owing to the enhanced adsorption capacity caused by the introduction of IL. Moreover, the column with the parameters of 6 cm bed depth, 5 mL min−1 flow rate, and 50 mg L−1 was able to achieve the best performance in Cr(VI) adsorption.
Introduction
Heavy metals in wastewater have been an environmental concern for many years because of their harmful effect on human health and impact on other organisms; they are also considered non-biodegradable.1 Industrial discharge, such as that from smelting, cosmetics, and stabilizers, and also effluence from domestic households introduce these metals into the environment through wastewater.2 The main heavy metal pollutants in wastewater are known to be arsenic (As), cobalt (Co), chromium (Cr), cadmium (Cd), and lead (Pb), with Cr(VI) being widely used in many industrial applications. According to Indonesia's regulations, the permissible limits of Cr(VI) in industrial and domestic wastewater are 0.4 and 1 mg L−1, respectively.3 Cr(VI) accumulates in soils and living organisms and can cause various health issues, ranging from simple skin irritation to lung carcinoma.4 In addition, Cr(VI) is known to be highly mobile in soils and in aquatic systems.
Adsorption methods have been widely used as an effective method for removing and separating metals.5 Operation costs and user friendliness are some of the advantages of the adsorption process, and the current trend is toward cheap and abundant nonconventional bio-sorbents with a high removal efficiency.6 However, the lack of adequate regeneration methods and the difficulty of handling spent adsorbents are among the limitations of adsorption processes. In recent years, there has been increased interest in the use of biopolymers, such as cellulose and chitosan, as alternative adsorbents because of their low cost and abundance and advantageous properties, such as their antibacterial activity, nontoxicity, biocompatibility, biodegradability, hydrophilicity, and high adsorption capacity.7 Chitosan has been used in a number of metal adsorption studies.8 Its chemical structure is modifiable, and a large number of applications are improved by modifying its properties. Modification of the chitosan molecule has been explored through grafting or crosslinking, which enhance its properties. Chitosan has been successfully impregnated with hydrogel, surfactant, and ionic liquid (IL) for various applications, such as catalysis, support materials, and adsorption.8–10 Furthermore, the impregnation of chitosan with IL can alleviate most of the IL's disadvantages. IL has various attractive properties, such as being nonvolatile, thermally stable, and miscible in organic and aqueous solutions; however, it has a low mass transfer rate and may be lost into the aqueous system during adsorption operations.
In recent years, there has been increasing interest in IL-impregnated chitosan (chitosan-IL) because of its adsorption applications. Kumar et al. reported the immobilization of tetraoctylammonium bromide on chitosan for Cr(VI) adsorption.11 This adsorbent demonstrates excellent performance due to the cooperative effect of both IL and chitosan, and it was easily regenerated with ammonium hydroxide. Moreover, Shekawat et al. reported the enhanced adsorption capacity of chitosan-IL by crosslinking it with sulfate.12 Chitosan-IL has also been applied to the adsorption of Cr(VI), Hg(II), Ce(II), Sr(II), and Mo(II).13,14 Aside from metal adsorption, chitosan-IL has also been used in the removal of dyes and herbicides.15,16 Lin et al. reported an interesting application for the immobilization of IL using a chitosan-based capsule.17 IL capsules require nontoxic and harmless natural macromolecule materials (chitosan, sodium alginate, etc.), which reduce their environmental impact. The volume of these capsules is generally large, which makes separation easier; however, it seems that the issue of adsorption regeneration has not yet been resolved for this capsule.
A number of studies have explored ammonium- and imidazolium-based IL in relation to the chitosan-IL adsorbent because of their inherent ability to interact with the chitosan structure. However, phosphonium-based IL has not been explored in this context. Phosphonium-based IL is typically stable compared with ammonium- or imidazolium-based IL, and it is also more stable under acidic and basic conditions owing to the absence of acidic protons.18 Lin et al. reported the use of trihexyldodecylphosphonium chloride in the chitosan-capsule adsorbent.17 In the present study, chitosan adsorbent impregnated with a phosphonium-based IL (Chi_IL), trioctyldodecyl phosphonium chloride, was synthesized and used as the separation tool for Cr(VI) in batch and column adsorption process. The effects of different parameters on adsorption performance, including adsorbent dosage, pH, and temperature, were investigated. In addition, adsorption kinetics, isotherms, and thermodynamics were studied comprehensively.
Experimental
Materials
Trioctylphosphine (97%) and 1-chlorododecane (97%), used as precursors for trioctyldodecyl phosphonium chloride (P8,8,8,12Cl), were obtained from Sigma Aldrich (Tokyo, Japan) and Tokyo Chemical Industry Co., Ltd (Tokyo, Japan), respectively. HCl (5 mol L−1), 1,5-diphenylcarbazide (DPC, 98%), and chromium(VI) standard solutions (1000 mg L−1) were purchased from Merck. Locally source chitosan (Crab from Cirebon, Indonesia) was provided by Chimultiguna (Indonesia, deacetylation degree of 86.94%), and acetone was purchased from Himedia (India).
Preparation of P8,8,8,12Cl-impregnated chitosan (Chi_IL)
An IL, trioctyldodecyl phosphonium chloride (P8,8,8,12Cl), was prepared as reported previously.19 The preparation of chitosan impregnated with ILs was performed as planned in the previous report.20 Initially, chitosan was crosslinked with sulfate by mixing 5 g of chitosan and 100 mL of 1 mol L−1 H2SO4 and then stirring the mixture for 1 h. The residue was washed and air-dried at 333 K in an oven. The impregnation of chitosan by IL was conducted by mixing crosslinked chitosan (2.5 g) with 30 mL of P8,8,8,12Cl in acetone (0.05 mol). The mixture was then refluxed for 1 h at 323 K. The residue was washed and air-dried at 333 K in an oven and used for further adsorption studies.
The chitosan impregnated with IL (Chi_IL) was characterized using Fourier-transform infrared spectroscopy (FTIR), X-ray diffraction (XRD), scanning electron microscopy (SEM), and energy-dispersive X-ray spectroscopy (EDX). The FT-IR measurement was recorded using the Shimadzu FT-IR Affinity-1 spectrometer in the range of 500–4000 cm−1 with a resolution of 1 cm−1. The crystalline structure of the catalysts was studied using XRD and recorded on a Bruker D2 Phaser X-ray diffractometer using Cu Kα radiation with an increment of 1° per second. The Chi_IL morphology and elemental composition were characterized through an SEM/EDX analysis on the Phenom Desktop ProXL.
Metal concentration measurements
The determination of metal concentrations was carried out using the spectrophotometric method. Diphenylcarbazide (DPC) was used as a complexing agent for Cr(VI); the DPC–Cr(VI) complex becomes bright purple when the absorbance peak reaches 540 nm.21 All the experiments and spectrophotometric measurements were conducted in triplicate to minimize errors, which did not exceed 4%. Spectrophotometric analysis was performed with a Hinotek N4S UV-Vis Spectrophotometer (Ningbo Hinotek Technology Co., Ltd, China). The absorbance of the solutions was measured using a 1 cm-thick quartz cell against double-distilled water as a blank, unless stated otherwise. The metal-containing solution with concentrations in the range of 50–150 mg L−1 was mixed with the appropriate color-developing reagents. The absorbance of the Cr(VI)-containing solution was then measured at 540 nm.
Adsorption procedure
Batch adsorption. The adsorption experiment was carried out by mixing 0.2 g of adsorbent with a 50 mL metal-containing solution (100 mg L−1) at 298 K for a 90 min. The metal concentration in the solution was determined using a UV spectrophotometer. The adsorption efficiency and equilibrium adsorption capacity (qeq) were calculated as follows: |
E (%) = ((Ci − Ceq)/Ci) × 100
| (1) |
|
qeq = ((Ci − Ceq)/W) × V
| (2) |
where Ci and Ceq refer to the metal concentration (mg L−1) in the initial and equilibrium states, respectively, and V and W are the volume of the metal-containing solution and the weight of the adsorbent, respectively. All experiments were conducted in triplicate to obtain reliable data.
Column adsorption. Column adsorption experiment was performed in a glass column with a length 30 and 2.0 cm internal diameter at the temperature of 298 K. The column was packed according to Fig. 1. Glass wool which could aid as a filter aid provided at the top and bottom of the column. The adsorbent was placed from top to bottom and then covered glass beads (5 mm) to ensure the influent was distributed properly. Peristaltic pump was used to pump the influent solution at a controlled flow rate. Parameters, such as bed depth (4, 5, and 5 cm), flow rate (5, 10, 15 mL min−1) and influent concentration (50, 100, 200 mg L−1) were investigated. The effluent was sampled at regular intervals of ten minutes.
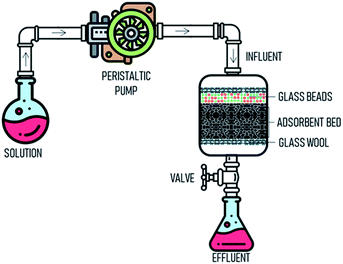 |
| Fig. 1 The schematic drawing of the fixed-bed adsorption column for experimental study. | |
The value of effluent volume (Veff, mL), total mass of metal adsorbed (qtot, mg), maximum uptake (qeq, mg g−1), total amount of metal entering column (mtot, mg) and Cr(VI) removal efficiency (E, %) can be calculated from the eqn (3)–(7), respectively.
|
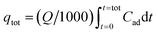 | (4) |
|
mtot = (CiQttot)/1000
| (6) |
|
E (%) = (qtot/mtot) × 100
| (7) |
where
Q is the volumetric flow rate (mL min
−1),
ttot is the total flow time (min) and
Cad is the concentration of metal removal (mg L
−1).
Results and discussions
Physicochemical characterization of the adsorbent
The structural and morphological analysis of chitosan and Chi_IL were carried out using an XRD and SEM analyses, respectively. As shown in Fig. 2A, the amorphous nature of chitosan was reflected in the XRD patterns, and chitosan characteristic peaks were also observed at 2θ = 12.12°, 19.55°, and 23.45° in both chitosan and Chi_IL diffraction.22 In the Chi_IL diffraction pattern, the characteristic peaks of chitosan shifted slightly to 19.37°. Chi_IL also showed a lower intensity in the chitosan characteristic peaks than that of chitosan, which indicates a decrease in crystallinity due to the interaction between P8,8,8,12Cl and chitosan.
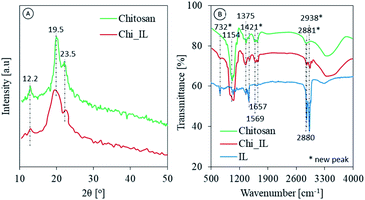 |
| Fig. 2 (A) Diffraction pattern and (B) FTIR spectrum of chitosan and Chi_IL. | |
The chemical interactions and footprints of the adsorbents were examined with a FTIR spectrophotometer (Fig. 2B). In the chitosan spectra, the presence of maxima at 3400 cm−1 was assigned to O–H and N–H stretching vibrations. Moreover, N–H bending and C–H, C–O, and C
O stretching vibrations were observed at 1569, 2880, 1154, and 1657 cm−1, respectively.14,23 Changes were observed after the impregnation process, such as the shifting and broadening of the hydroxyl peak from 3400 to 3451 cm−1. Moreover, shifting also occurred in the C–N bending vibrations from 1375 to 1359 cm−1, and the occurrence of two additional peaks at 2938 and 2881 cm−1 was assigned to the IL C–H2.24 New peaks were observed in the Chi_IL FT-IR spectra, which could be ascribed to the P–C vibrations originating in the cationic moieties of P8,8,8,12Cl. Peaks at 1421 and 732 cm−1 were ascribed to P–C deformation and stretching vibrations, respectively.24 Upon the adsorption of metal ions, shifts in the P–C characteristic peak were observed from 1421 to 1398 cm−1 and 732 to 710 cm−1 (Fig. S2†). This result could be interpreted as the adsorption of metal ions through their coordination with P8,8,8,12Cl cationic moieties due to an electrical interaction.
Fig. 3 shown the morphology of chitosan and Chi_IL post adsorption. Chitosan morphology exhibits a dense and uneven surface, and there are no observable visual changes in the chitosan morphology upon IL impregnation or metal adsorption. Post-impregnation and post-adsorption Chi_IL showed the presence of phosphorus atoms that originate from the cationic center of P8,8,8,12Cl and Cr(VI) (Fig. S1†).
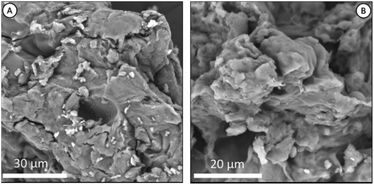 |
| Fig. 3 (A) SEM image of native chitosan, and (B) SEM image of Chi_IL post-adsorption. | |
Adsorption behavior
Speciation of adsorbate and surface charge of adsorbent depends upon pH of the solution. Hence, it is customary to study pH effect on adsorption efficiency. In the present study, 50 mL of 100 mg L−1 of Cr(VI) solutions were equilibrated with 300 mg of Chi_IL. The pH of the solutions was varied from 2.0 to 10.0. As shown in Fig. 4A, the highest adsorption efficiency of Cr(VI) was achieved at pH of 4.0. Cr(VI) complexes in aqueous solution mainly exists in the form of HCrO4−, Cr2O72−, and CrO42−. The equilibrium between these complexes was presented as follows: |
H2CrO4 H+ + HCrO−4
| (8) |
|
2HCrO−4 Cr2O2−7 + H2O
| (9) |
|
HCrO−4 H+ + CrO2−4
| (10) |
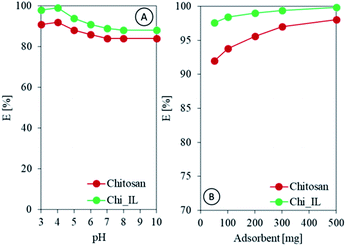 |
| Fig. 4 (A) Effect of pH on the adsorption efficiency of Cr(VI), and (B) effect of the adsorbent dose on the adsorption efficiency of Cr(VI). | |
Following the UV-vis spectra, Cr(VI) containing solution in acidic condition shows two peak at 255 and 345 nm. While, the solution in basic and neutral condition shows two peak at 270 and 370 nm, indicating the presence of difference Cr(VI) complexes in both condition (Fig. S3A†).25,26 CrO42− mainly exists in basic and neutral condition. While, HCrO4- and Cr2O72− mainly exists in acidic condition.27 The solution in different pH also showed a different color (Fig. S3B†). The acidic Cr(VI) solution showed a yellow color, while basic Cr(VI) solution showed an amber color. The adsorption of Cr(VI) by Chi_IL could be done through electrostatic interaction between the anionic complex and the amine through the exchange with the sulfate group or with the IL through the anionic exchange.28 A notable decrease was observed after the pH was increased to 6. This could be due to the change in the surface charge of the adsorbent since the pHpzc of Chi_IL was found to be 4. The pHpzc was determined by using pH drift method as reported by Jiao et al.29 The pHpzc reflect the surface charge of the materials at certain pH. Material will have positively charged surface in pH below the pHpzc and negatively charged above it.
Assessing the effective adsorbent dose is paramount when measuring adsorbent potential within a certain concentration range. Thus, chitosan and Chi_IL doses were varied from 50 to 500 mg to investigate the effect of different doses on adsorption efficiency. As shown in Fig. 4C, the adsorption of Cr(VI) increased linearly with the increased adsorbent dose. Chi_IL was able to reach equilibrium at lower dose than that of chitosan, which is 300 mg. Chitosan achieved above 95% adsorption efficiency also at 300 mg. Beyond 300 mg, there was a little to no observable changes in the removal of Cr(VI) owing to the saturation of the active adsorption sites. Therefore, 300 mg of adsorbent dose was used for the rest of the adsorption studies.
The desorption of Cr(VI) from both adsorbent was done by using 0.005 mol L−1 HCl. The desorption efficiency of both chitosan and Chi_IL reached 90%. After the desorption, the adsorbent was thoroughly washed with deionized water and regenerated with 0.01 mol L−1 NaCl solution. The regenerated adsorbent was used in the further adsorption–desorption cycle investigate its regenerability. The test was done in 3 cycle. Considering the accumulated Cr(VI) in the adsorbent, the Chi_IL showed a 10% decrease in the efficiency after three cycles (Fig. S4†). While, chitosan showed a notable decrease in the 2nd cycle.
Adsorption kinetics
The contact time of the experiment was varied from 10 to 90 min to analyze the adsorption kinetics of Cr(VI). Chi_IL was able to reached equilibrium in Cr(VI) adsorption in 60 minutes, while chitosan achieved the equilibrium in 90 minutes. Thus, 90 minutes was then used in further experiments. Moreover, pseudo-first-order and pseudo-second-order kinetic models were applied to determine the number of metal ions adsorbed at various contact times and their kinetic parameters, as shown in eqn (11) and (12):30,31 |
qt = K2q2eqt/(1 + K2qeqt)
| (12) |
Both equations were transformed to their linear form according to the following equations:
|
log(qeq − qt) = log qeq − (K1t/2.303)
| (13) |
|
(t/qt) = 1/K2q2eq + t/qeq
| (14) |
where
qeq and
qt are the amount of Cr(
VI) adsorbed at the equilibrium and at the specified time
t, respectively, and
K1 and
K2 are the rate constant of the pseudo-first-order and pseudo-second-order rate, respectively. The linear correlation between log(
qeq −
qt) and
t provides the pseudo-first-order rate constant, and the linear correlation between
t/
qt and
t provides the pseudo-second-order rate constant.
Table 1 shows the adsorption kinetic parameters of Cr(VI) by chitosan and Chi_IL. The pseudo-second-order parameters fit well with the adsorption kinetics of Cr(VI) by both adsorbents, as they showed the closest calculated qe values to Cr(VI) and the highest correlation coefficient (R2). The faster adsorption of Cr(VI) by Chi_IL was also reflected in the kinetic constant, which shows that the kinetic constant of Chi_IL was higher than that of chitosan. The higher kinetic of Chi_IL could be contributed by the presence of IL that could enhanced adsorption through electrostatic interaction with the metal ions.12 Moreover, the activation energy (Ea) can be obtained with the linearized Arrhenius equation, which is shown in eqn (15).
|
ln Kt = ln A − (Ea/RT).
| (15) |
Table 1 Kinetic parameters for the adsorption of Cr(VI) onto adsorbents
Kinetic model |
Parameters |
Adsorbent |
Chitosan |
Chi_IL |
Pseudo-first order |
K1 |
0.041 |
0.054 |
qe,exp |
12.31 |
12.45 |
qe,cal |
8.99 |
7.68 |
R2 |
0.9480 |
0.9967 |
Pseudo-second order |
K2 |
0.072 |
0.092 |
qe,exp |
12.31 |
12.45 |
qe,cal |
12.26 |
12.43 |
R2 |
0.9995 |
0.9999 |
Intraparticle diffusion |
Kint |
0.174 |
0.278 |
R2 |
0.8858 |
0.8872 |
With the suitability of pseudo-second order kinetic model, the calculation of Ea was done by using the coefficient of K2. The Ea of Cr(VI) adsorption for chitosan and Chi_IL that was calculated from the linear plot between ln
K vs. 1/T (Fig. S5†), were 71.7 and 59.8 kJ mol−1, respectively. Since the Ea values was higher than that of 40 kJ mol−1, the Cr(VI) ions was chemically adsorbent onto the adsorbents.32 The Ea of Chi_IL was lower than that of chitosan due to the presence of P8,8,8,12Cl which provide additional adsorption sites for the Cr(VI). The Ea also a crucial aspect in the determination of the reaction rate. The reaction was consider as quick with Ea less than 40 kJ mol−1 and slow with Ea more than 120 kJ mol−1.33 Thus, the adsorption of Cr(VI) by both adsorbent was not particularly fast reaction due to the chemical adsorption process.
In addition, the diffusion model involved in the adsorption of Cr(VI) was explored with the intraparticle diffusion model. The Weber–Morris equation was used to explain this model:34
where
qt (mg g
−1) and
Kint (mg g
−1 min
−1/2) represent the amount of metal adsorbed at a certain time and the intraparticle diffusion rate constant, respectively. The value
kint was obtained from the slope of
qt versus the
t1/2 plot. The calculated
Kint for Cr(
VI) was presented in
Table 1. Cr(
VI) show a nonzero intercept, demonstrating that there are further factors contributing to the rate-limiting step aside from the diffusion process.
Adsorption isotherms
Chitosan and Chi_IL were subjected to adsorption of Cr(VI) at a different initial concentration in the range of 50–700 mg L−1 with 50 mg L−1 interval. Chi_IL showed a slight decrease in the adsorption efficiency, which was 98.8 to 96.7%, after the concentration of 200 mg L−1, while chitosan showed a higher decrease in adsorption efficiency, which was 96.8 to 91.1%, after the concentration of 100 mgL−1. The lesser decrease in Chi_IL than that of chitosan could be attributed to the presence of IL which provided additional adsorption sites. The experimental data were then fitted to several adsorption isotherm models, such as the Langmuir, Freundlich, Temkin, and Frenkel–Helsey–Hill (FHH) models, and the correlation coefficient (R2) was used to determine the most suitable isotherm model for adsorption.
Typically, monolayer adsorption is explained by the Langmuir isotherm model.35,36 A linearized Langmuir equation (eqn (17)) presents the maximum adsorption capacity (q0, mg g−1) and the Langmuir constant (b, L mg−1), which was obtainable from the plot of Ceq/qeq versus Ceq:
|
(Ceq/qeq) = (1/q0b) + (Ceq/q0)
| (17) |
Moreover, the Langmuir constant is related to the separation factor (RL), which reflects the effectiveness of adsorption and is given by the following equation:
where
RL indicates the favorability of the adsorption process (
RL = 0: irreversible adsorption, 0 <
RL > 1: favorable adsorption,
RL = 1: linear adsorption, and
RL > 1: unfavorable adsorption).
37
Multilayer adsorption was modeled with the Freundlich and FHH isotherm models.38 The linearized equations for both models are presented in eqn (19) and (20):
|
log qeq = log kF + (1/n)log Ceq
| (19) |
|
lnqeq = (1/n)ln K + (1/n)ln Ceq
| (20) |
The Freundlich adsorption parameters, such as adsorption capacity (KF, mg1−1/n g−1 L−1) and adsorption heterogeneity (n), were obtained from the plot of log
qeq against log
Ceq (eqn (10)). The FHH adsorption parameters, such as the FHH constant (K) and adsorption intensity (1/n), were obtained from the plot of ln
qeq against ln
Ceq (eqn (11)). In both isotherm models, the values n and 1/n indicate the interaction between the adsorbent and the adsorbate.36,38
The Temkin isotherm explores the adsorbent–adsorbate interaction, which decreases the adsorption heat in multilayer adsorption. Ignoring the low and high thresholds of the concentrations, the Temkin model assumes a linear decrease in the heat of adsorption with an increase in the layers of adsorbate.31 The linearized Temkin equation is expressed as follows:
|
qeq = βln AT + βln Ceq
| (21) |
The Temkin adsorption parameters, such as the equilibrium binding constant (AT, L g−1) and heat of adsorption (β, kJ mol L−1), were obtained from the slope and intercept of the plot of qeq against ln
Ceq. The Temkin constant (bT), which clarifies the adsorption process (bT > 40 kJ mol−1 = chemisorption process, bT < 40 kJ mol−1 = physisorption process),39 was obtained from the following equation
According to the comparison of the regression coefficient, multilayer adsorption was a suitable fit for the sorption of Cr(VI) by both chitosan and Chi_IL. In agreement with the adsorption results, Chi_IL showed higher adsorption capacity than that of chitosan, which could be attributed to the native adsorption sites and the presence of P8,8,8,12Cl.
Following the Langmuir model, chitosan and Chi_IL showed separation factor less than unity (Table 2), which indicates the effective interaction between the Cr(VI) ions and both chitosan and Chi_IL. According to both the Freundlich and FHH isotherm models, the n-factor values were between 1 and 10, which indicates beneficial adsorption for Cr(VI), and the small value of 1/n (0.50 for chitosan and 0.49 for Chi_IL) signifies an active interaction between both components. The Temkin constant (bT) from the adsorption of Cr(VI) by chitosan and Chi_IL was higher than 40 kJ mol−1, which means that the adsorption of Cr(VI) followed the chemisorption pathway. Fig. 5 shows the isotherm fit between the experimental data with Langmuir and Freundlich models. In agreement with the regression coefficient, the experimental data fitted better to the Freundlich isotherm models. Thus, the adsorption of Cr(VI) by both adsorbent followed a multilayer chemisorption pathway with a beneficial interaction between components.
Table 2 Isotherm parameters for the adsorption of Cr(VI) onto Chi_IL
Isotherms models |
Parameters |
Chi_IL |
Chitosan |
Langmuir |
q0 |
282.6 |
238.1 |
B |
0.076 |
0.050 |
R2 |
0.9641 |
0.9025 |
RL |
0.2075–0.0183 |
0.2852–0.0277 |
Freundlich |
KF |
34.92 |
16.75 |
N |
2.00 |
1.97 |
R2 |
0.9905 |
0.9900 |
Temkin |
AT |
1.46 |
2.24 |
bT |
45.23 |
52.33 |
β |
54.77 |
47.33 |
R2 |
0.9419 |
0.8686 |
Frenkel-Helsey Hill |
K |
0.0008 |
0.0038 |
n |
2.00 |
1.97 |
R2 |
0.9905 |
0.9800 |
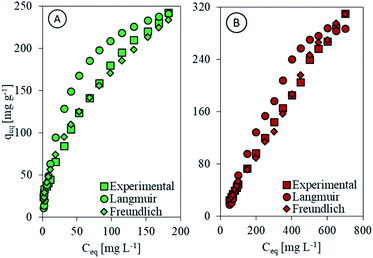 |
| Fig. 5 Comparison of experimental data with Langmuir and Freundlich model for (A) chitosan and (B) Chi_IL. | |
Adsorption thermodynamics
Temperature is a critical parameter that has a perceivable influence over the adsorption performance of an adsorbent.40 The adsorption of Cr(VI) was studied under the isothermal condition at a temperature range of 298–328 K and pH of 4. The thermodynamic parameters, such as the Arrhenius activation energy (Ea, kJ mol−1), Gibbs free energy (ΔG, kJ mol−1), enthalpy change (ΔH, kJ mol−1), and entropy change (ΔS, J mol−1 K−1), were determined from the experimental data. These parameters were calculated (given in Table 3) using following Van't Hoff equation:41,42 |
ΔG = −RTln KD.
| (23) |
Table 3 Thermodynamic parameters of Cr(VI) adsorption onto adsorbents
T (K) |
298 |
303 |
308 |
318 |
328 |
Chitosan |
ΔG [kJ mol−1] |
−29.8 |
−29.8 |
−29.8 |
−29.7 |
−29.7 |
ΔH [kJ mol−1] |
−32.4 |
ΔS [J mol−1 K−1] |
−8.4 |
Chi_IL |
ΔG [kJ mol−1] |
−57.1 |
−57.9 |
−56.7 |
−56.6 |
−56.5 |
ΔH [kJ mol−1] |
−63.8 |
ΔS [J mol−1 K−1] |
−22.6 |
A combination of eqn (21) and (22) gives a linearized form for the Van't Hoff plot (eqn (23)), which then provides ΔH and ΔS from the slope and the intercept of the plots41,42
|
ln KD = (ΔS/R) − (ΔH/RT),
| (25) |
where
R (8.314 J mol
−1 K
−1) and
T (K) are the gas constant and temperature, respectively. The thermodynamic equilibrium constant (
KD) was obtained from the plots of ln(
qeq/
Ceq)
versus Ceq at various temperatures.
43,44 The adsorption of Cr(
VI) demonstrated negative Δ
H, negative Δ
S, and negative Δ
G, which indicates that the adsorption was exothermic and spontaneous with a high affinity for Cr(
VI).
43
Fixed-bed column adsorption
Table 4 shows the column adsorption parameters for the adsorption of Cr(VI) by chitosan and Chi_IL. The breakthrough time (tb) and total flow time (ttot) were defined as the time needed to achieve 5 and 95% of total influent concentration, respectively. Moreover, various parameters, such as the bed depth, the influent flow rate, and the initial Cr(VI) concentration were also assessed to determine the best parameter for the column adsorption. An increase in the bed depth provided a longer contact time between the adsorbate and the adsorbent which leads to a significant increase in tb and ttot (Table 4 and Fig. S6†). An increase in the bed depth also resulted in an increase in the amount of adsorbent. This leads to an increase in the total metal adsorbed (qtot) and a decrease in the maximum uptake (qeq) due to an increase in the adsorbent amount. On the other hand, the shorter residence time due to the increase in the flow rate negatively affected the ttot and tb, which cause almost 50% decrease in both value.45 An increase in the flow rate also enhanced the total amount of metals in the column (mtot), and qeq. However, the highest adsorption efficiency was achieved at flow rate of 5 mL min−1 due to the column ability to retain equilibrium and sufficient contact time. Increase in the Cr(VI) initial concentration also negatively affected the tb and ttot due to higher concentration gradient driven up the adsorption kinetic. Moreover, the increase in the influent concentration also enhanced the mtot, qtot, and qeq but not to a greater extent. However, Chi_IL showed significantly higher column capacity and uptake than that of chitosan regardless of the experimental conditions. This could be associated with the enhanced adsorption capacity of chitosan by the introduction of P8,8,8,12Cl. The high hydrophobicity of P8,8,8,12Cl which could prevent the leakage of the IL into the aqueous phase, could also influenced the column exhaustion time.
Table 4 Column adsorption parameter for chitosan and Chi_IL
Cia |
Qb |
Zc |
Chitosan |
Chi_IL |
ttot |
mtot |
qtot |
qeq |
E |
ttot |
mtot |
qtot |
qeq |
E |
mg L−1. mL min−1. cm. |
50 |
5 |
4 |
980 |
245 |
171 |
114 |
70 |
1320 |
330 |
309 |
206 |
94 |
50 |
5 |
5 |
1050 |
263 |
201 |
67 |
76 |
1470 |
368 |
341 |
114 |
93 |
50 |
5 |
6 |
1120 |
280 |
225 |
45 |
80 |
1560 |
390 |
371 |
74 |
95 |
50 |
5 |
6 |
1120 |
280 |
225 |
45 |
80 |
1560 |
390 |
371 |
74 |
95 |
50 |
10 |
6 |
840 |
420 |
254 |
51 |
60 |
1230 |
615 |
518 |
104 |
84 |
50 |
15 |
6 |
660 |
495 |
268 |
54 |
54 |
930 |
698 |
547 |
109 |
78 |
50 |
5 |
6 |
1120 |
280 |
225 |
45 |
80 |
1560 |
390 |
371 |
74 |
95 |
100 |
5 |
6 |
910 |
455 |
229 |
46 |
50 |
990 |
495 |
377 |
75 |
76 |
200 |
5 |
6 |
580 |
580 |
233 |
47 |
40 |
620 |
620 |
428 |
86 |
69 |
In this study, Adams–Bohart, Thomas, and Yoon–Nelson models were developed to identify the best model for predicting the dynamic behavior of the column.46 The equation for these models were presented in eqn (26)–(28).
|
 | (26) |
|
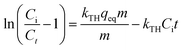 | (27) |
|
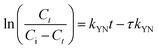 | (28) |
where
kAB (L mg
−1 min
−1) is the Adam–Bohart kinetic constant,
N0 (mg L
−1) is the saturation concentration,
U0 (cm min
−1) is the superficial velocity,
kTH (L mg
−1 min
−1) is the Thomas kinetic constant,
qeq (mg g
−1) is the adsorption capacity,
kYN (L mg
−1 min
−1) is the Yoon–Nelson kinetic constant, and
τ (min) is the time for 50% breakthrough.
The breakthrough curve of both chitosan and Chi_IL showed a close fit with Thomas and Yoon–Nelson model (Fig. S6†). The R2 values of the Thomas model (0.995–0.998) and Yoon–Nelson model (0.997–0.996) were larger than those of the Adam–Bohart model (0.789–0.822). In addition, both models also showed a close fit between calculated qeq and τ value and experimental value (Table S1†). The τ value showed a good correlation between the availability of adsorbent and concentration gradient, which could indicated the influence of mass transfer over the adsorption process. The highest Cr(VI) adsorption efficiency by chitosan and Chi_IL was achieved at flow rate of 5 mL min−1, bed depth of 6 cm and 50 mg L−1 of Cr(VI) solution. Following the results, it can be concluded that both Thomas and Yoon–Nelson model can predict the dynamic behavior of Cr(VI) adsorption by Chi_IL and chitosan.
Comparison with other chitosan-based adsorbents
The performance of chitosan and Chi_IL compared with previously reported materials was shown in Table 5. While, chitosan showed a similar capacity to other reports. Chi_IL has shown to possess a better adsorption capacity compared with other materials.
Table 5 Comparison of Chi_IL with other reported materials
Adsorbent |
Analyte |
Adsorption capacity [mg g−1] |
Ref. |
Chitosan |
Cr(VI) |
225.9 |
47 |
Chitosan |
Cr(VI) |
238.1 |
20 |
A336/chitosan |
Pd(II) |
187.6 |
48 |
Cyphos101/chitosan beads |
Cr(VI) |
104.4 |
17 |
Glutamic-IL/chitosan |
Pb(II) |
185.0 |
49 |
EPmim/chitosan |
Re(VII) |
149.2 |
50 |
Chitosan |
Cr(VI) |
238.1 |
This study |
Chi_IL |
Cr(VI) |
282.6 |
Conclusions
Chitosan and Chi_IL were prepared as adsorbent for Cr(VI). Chi_IL has shown an superior adsorption capacity for Cr(VI) with fast sorption kinetics than that of native chitosan. The adsorbent dosage, pH, initial concentration, contact time, and temperature were influential factors in the adsorption of Cr(VI). The adsorption of Cr(VI) onto the chitosan and Chi_IL probably proceeds by electrostatic static interaction with chitosan and anionic exchange with the P8,8,8,12Cl. The adsorption process is thermodynamically favorable for the removal of Cr(VI) from synthetic effluents. Moreover, an exothermic multilayer chemisorption process was a good fit for the adsorption of Cr(VI) by both adsorbent. The pseudo-second-order kinetic model was also a good fit to this mechanism. Chi_IL showed a high adsorption capacity (282.6 mg g−1), which could be contributed due to the presence of P8,8,8,12Cl in the Chi_IL. While, native chitosan showed an adsorption capacity of 238.1 mg g−1. Moreover, chitosan and Chi_IL also performed well in column adsorption experiment. Chi_IL was able to achieve longer column exhaustion time than that of native chitosan due to the enhanced adsorption capacity as well as high hydrophobicity of P8,8,8,12Cl that prevent leakage of IL onto the mobile phase. The best performance on column adsorption of Cr(VI) was obtained with parameter of 6 cm of bed depth, 5 mL min−1 of flow rate and 50 mg L−1 initial Cr(VI) concentration.
Author contributions
Mochamad L. Firmansyah: conceptualization, methodology, investigation, writing – original draft, visualization, funding acquisition; Thalabul Ilmi: investigation; Rino R. Mukti: writing – review & editing, supervision, resources; Patmawati: writing – review & editing, supervision; Masahiro Goto: writing – review & editing, resources.
Conflicts of interest
The authors declare that they have no known competing financial or non-financial interests or personal relationships that could have appeared to influence the work reported in this paper.
Acknowledgements
This work was supported by Universitas Airlangga under grant Hibah Riset Mandat 2020 [395/UN3.14/PT/2020]. The author grateful towards Central Laboratory of Universitas Islam Indonesia, Yogyakarta for the assistance in the adsorbent characterization, and to CV. Chimultiguna for providing the chitosan for the present study.
References
- A. S. Ayangbenro and O. O. Babalola, Int. J. Environ. Res. Public Health, 2017, 14 Search PubMed.
- P. K. Samantaray, S. Indrakumar, K. Chatterjee, V. Agarwal and S. Bose, Nanoscale Adv., 2020, 2, 2824–2834 RSC.
- Ministry of Environment and Forestry of The Republic of Indonesia, Peraturan Menteri Lingkungan Hidup RI No. 5 Tahun 2014 Tentang Baku Mutu Air Limbah, 2014 Search PubMed.
- P. Sharma, S. P. Singh, S. K. Parakh and Y. W. Tong, Bioengineered, 2022, 13, 4923–4938 CrossRef CAS PubMed.
- K. C. K. T. Matsuura and E. D. A. Ethylenediamine, Appl. Water Sci., 2018, 8, 1–30 CrossRef.
- G. Crini, E. Lichtfouse, L. Wilson, N. Morin-crini, G. Crini, E. Lichtfouse, L. Wilson and N. M. Conventional, Environ. Chem. Lett., 2019, 17, 195–213 CrossRef CAS.
- H. El Knidri, R. Belaabed, A. Addaou, A. Laajeb and A. Lahsini, Int. J. Biol. Macromol., 2018, 120, 1181–1189 CrossRef CAS PubMed.
- M. Vakili, S. Deng, G. Cagnetta, W. Wang, P. Meng, D. Liu and G. Yu, Sep. Purif. Technol., 2019, 224, 373–387 CrossRef CAS.
- G. Ohemeng-Boahen, D. D. Sewu, H. N. Tran and S. H. Woo, Colloids Surf., A, 2021, 625, 126911 CrossRef CAS.
- H. Karimi-Maleh, S. Ranjbari, B. Tanhaei, A. Ayati, Y. Orooji, M. Alizadeh, F. Karimi, S. Salmanpour, J. Rouhi, M. Sillanpää and F. Sen, Environ. Res., 2021, 195, 110809 CrossRef CAS PubMed.
- A. Santhana Krishna Kumar, T. Gupta, S. S. Kakan, S. Kalidhasan, Manasi, V. Rajesh and N. Rajesh, J. Hazard. Mater., 2012, 239–240, 213–224 CrossRef CAS PubMed.
- A. Shekhawat, S. Kahu, D. Saravanan and R. Jugade, Int. J. Biol. Macromol., 2015, 80, 615–626 CrossRef CAS PubMed.
- A. Shekhawat, S. Kahu, D. Saravanan and R. Jugade, Int. J. Biol. Macromol., 2017, 104, 1556–1568 CrossRef CAS PubMed.
- T. Monir, A. Shahr El-Din, Y. El-Nadi and A. Ali, Radiochim. Acta, 2020, 108, 649–659 CrossRef CAS.
- X. Huang, S. Feng, G. Zhu, W. Zheng, C. Shao, N. Zhou and Q. Meng, Int. J. Biol. Macromol., 2020, 149, 882–892 CrossRef CAS PubMed.
- S. Ranjbari, B. Tanhaei, A. Ayati and M. Sillanpää, Int. J. Biol. Macromol., 2019, 125, 989–998 CrossRef CAS PubMed.
- X. Lin, J. Liu, S. Wan, X. He, L. Cui and G. Wu, Int. J. Biol. Macromol., 2019, 136, 35–47 CrossRef CAS PubMed.
- F. Atefi, M. T. Garcia, R. D. Singer and P. J. Scammells, Green Chem., 2009, 11, 1595 RSC.
- M. L. Firmansyah, A. T. N. Fajar, W. Yoshida, T. Hanada and M. Goto, J. Chem. Eng. Jpn., 2020, 53, 1–8 CrossRef.
- S. Kahu, D. Saravanan and R. Jugade, Water Sci. Technol., 2014, 70, 2047–2055 CrossRef CAS PubMed.
- K. K. Onchoke and S. A. Sasu, Adv. Environ. Chem., 2016, 2016, 1–10 CrossRef.
- J. Song, S. A. Messele, L. Meng, Z. Huang and M. Gamal El-Din, Water Res., 2021, 194, 116930 CrossRef CAS PubMed.
- D. Wanule, J. V. Balkhande, P. U. Ratnakar, a. N. Kulkarni and C. S. Bhowate, Int. J. Eng. Sci. Innov. Technol., 2014, 3, 299–304 Search PubMed.
- D. Cholico-gonzalez, M. Avila-rodriguez, G. Cote and A. Chagnes, J. Mol. Liq., 2013, 187, 165–170 CrossRef CAS.
- M. C. Fournier-Salaün and P. Salaün, Cent. Eur. J. Chem., 2007, 5, 1084–1093 Search PubMed.
- A. Sanchez-Hachair and A. Hofmann, C. R. Chim., 2018, 21, 890–896 CrossRef CAS.
- C. lu Jiang, R. Wang, X. Chen, L. gen Zheng and H. Cheng, J. Cent. South Univ., 2021, 28, 1652–1664 CrossRef.
- B. S. Cunha, R. A. Bataglioli, T. B. Taketa, L. M. Lopes and M. M. Beppu, J. Environ. Chem. Eng., 2019, 7, 103181 CrossRef CAS.
- Y. Jiao, D. Han, Y. Lu, Y. Rong, L. Fang, Y. Liu and R. Han, Desalin. Water Treat., 2017, 77, 247–255 CrossRef CAS.
- S. Lagergreen, Z. Chem. Ind. Kolloide, 1907, 2, 174–175 Search PubMed.
- Y. Ho and G. McKay, Process Biochem., 1999, 34, 451–465 CrossRef CAS.
- Y. Chen, J. Tang, S. Wang, L. Zhang and W. Sun, Chem. Eng. J., 2021, 425, 131474 CrossRef CAS.
- D. Özmen, J. Turk. Chem. Soc., Sect. B, 2021, 4, 47–56 Search PubMed.
- H. Qiu, L. Lv, B. C. Pan, Q. J. Zhang, W. M. Zhang and Q. X. Zhang, J. Zhejiang Univ., Sci., A, 2009, 10, 716–724 CrossRef CAS.
- A. Kong, Y. Ji, H. Ma, Y. Song, B. He and J. Li, J. Cleaner Prod., 2018, 192, 801–808 CrossRef CAS.
- A. Dada, A. Olalekan, A. Olatunya and O. Dada, IOSR J. Appl. Chem., 2012, 3, 38–45 CrossRef.
- P. Thilagavathy and T. Santhi, BioResources, 2014, 9, 3805–3824 Search PubMed.
- A. A. Inyinbor, F. A. Adekola and G. A. Olatunji, Water Resour. Ind., 2016, 15, 14–27 CrossRef.
- M. G. El-Desouky, M. A. El-Bindary and A. A. El-Bindary, Vietnam J. Chem., 2021, 59, 341–361 CAS.
- S. Iftekhar, D. L. Ramasamy, V. Srivastava, M. B. Asif and M. Sillanpää, Chemosphere, 2018, 204, 413–430 CrossRef CAS PubMed.
- A. L. Taka, E. Fosso-Kankeu, K. Pillay and X. Y. Mbianda, Environ. Sci. Pollut. Res., 2018, 25, 21752–21767 CrossRef CAS PubMed.
- E. Fosso-Kankeu, H. Mittal, F. Waanders and S. S. Ray, J. Ind. Eng. Chem., 2017, 48, 151–161 CrossRef CAS.
- R. Niwas, U. Gupta, A. A. Khan and K. G. Varshney, Colloids Surfaces A Physicochem. Eng. Asp., 2000, 164, 115–119 CrossRef CAS.
- F. E. Soetaredjo, Y. H. Ju, S. Ismadji and A. Ayucitra, Desalin. Water Treat., 2017, 82, 188–200 CrossRef CAS.
- M. Li, S. Tang, Z. Zhao, X. Meng, F. Gao, S. Jiang, Y. Chen, J. Feng and C. Feng, Chem. Eng. J., 2020, 386, 123947 CrossRef CAS.
- H. Patel, Appl. Water Sci., 2019, 9(45) DOI:10.1007/s13201-019-0927-7.
- S. Kahu, A. Shekhawat, D. Saravanan and R. Jugade, Int. J. Environ. Sci. Technol., 2016, 13, 2269–2282 CrossRef CAS.
- A. S. K. Kumar, S. Sharma, R. S. Reddy, M. Barathi and N. Rajesh, Int. J. Biol. Macromol., 2015, 72, 633–639 CrossRef CAS PubMed.
- H. Ren, B. Li, M. Neckenig, D. Wu, Y. Li, Y. Ma, X. Li and N. Zhang, Carbohydr. Polym., 2019, 207, 737–746 CrossRef CAS PubMed.
- Z. Lou, S. Xing, X. Xiao, W. Shan, Y. Xiong and Y. Fan, Hydrometallurgy, 2018, 179, 141–148 CrossRef CAS.
|
This journal is © The Royal Society of Chemistry 2022 |
Click here to see how this site uses Cookies. View our privacy policy here.