DOI:
10.1039/D2RA02318K
(Paper)
RSC Adv., 2022,
12, 16386-16395
Kinetic mechanism on elemental mercury adsorption by brominated petroleum coke in simulated flue gas
Received
10th April 2022
, Accepted 26th May 2022
First published on 1st June 2022
Abstract
A waste byproduct of petroleum coke was obtained as a precursor modified with bromine for elemental mercury capture from simulated flue gas on a bench scale fixed-bed reactor. The reaction temperature, the initial inlet elemental mercury concentration and the individual flue gas components of O2, NO, SO2 and HCl were determined to explore their influence on elemental mercury capture by the brominated petroleum coke. Results indicate that high initial inlet mercury concentration can enhance initial mercury accumulation and the optimal temperature for elemental mercury capture by brominated petroleum coke is about 150 °C. Kinetic models reveal that the pseudo-second order and Elovich models are best fitted to the mercury adsorption process, indicating that chemisorption is the control step with the intra-particle diffusion and external mass transfer taking place simultaneously. The kinetic parameters demonstrate that the initial mercury adsorption rate (h or a) and the equilibrium adsorption quantity (Qe) increase remarkably, when higher concentrations of O2 or NO exist in N2 atmosphere. On the contrary, Qe decreases with the presence of high SO2 or HCl, which indicates a two-sided effect on the performance of mercury adsorption owing to their concentrations.
1. Introduction
Elemental mercury emitted from coal combustion has increasingly become a global threat and injecting a carbon based adsorbent upstream of coal-fired flue gas to control elemental mercury has been proved a relatively effective technology.1 However, the cost of injecting activated carbon is high, and replaceable low-cost adsorbents, especially bromine and sulfur modified carbon based materials, have received more and more attention.2–6 Petroleum coke, produced from the exploitation of oil or the extraction of traditional oil all over the world, is considered as an industrial waste due to the high content of organic sulfur.
In our previous studies, petroleum coke was modified by a chemical–mechanical bromination procedure7 to remove elemental mercury from coal-fired flue gas, in order to replace the expensive activated carbon adsorbent, which showed better performance than commercial activated carbon in ideal argon gas. The adsorption mechanism confirmed that more active mercury binding sites were created on the surface of brominated petroleum coke after the special bromination process, the inherent thiophene S and the loading Br in petroleum coke played a dominant role on mercury removal.8,9 Further Density Functional Theory confirmed that the mercury adsorption capacity directly correlated with the inherent organic S and the binding Br from chemical–mechanical bromination procedure, HgBr and Hg(Br)Br were the main forms chemisorbed on the surface of brominated petroleum coke and appeared approaching to bind on the carbon site next to the sulfur atom.10 The synergetic effect of the inherent thiophene sulfur and loading bromine enhanced the elemental mercury removal efficiency of the adsorbent in ideal argon gas. However, the environment in real flue gas of coal-fired power plant is complex, and the intrinsic reaction rate, the adsorption strength and quantity of solid surface active sites of the sorbent are affected by flue gas components including O2, NO, SO2, HCl, et al.,11–16 it is necessary to find out the influences of the components on mercury removal by the brominated petroleum coke for its further application in the plant.
Some researchers discussed the effect of flue gas component on mercury oxidation/adsorption and the atomic interaction between elemental mercury and the flue gas component using the first-principles calculation.17,18 However, kinetic studies are also widely used on understanding the adsorption process of carbon based adsorbents.19–27 Zhou24 revealed that the mercury adsorption process for activated carbon could be divided into two stages: external diffusion and intraparticle diffusion adsorption. Johari25 confirmed that pseudo-second order kinetic model could accurately describe the adsorption mechanism of mercury on the surface of modified coconut shell adsorbent. Khunphonoi26 found that pseudo-second order kinetic equation accurately described the mechanism on the surface of silver loaded activated carbon. Zhang27 found that the pseudo-first order and pseudo-second order kinetic models could better describe the adsorption process of mercury on the surface through the study of the kinetic models before and after the modification of activated carbon, indicating that the external mass transfer and chemical adsorption were dominant.
Since the influence of flue gas components on mercury removal by brominated petroleum coke have not been discussed in bench scale fixed-bed experimental system before, the apparent reaction rate of brominated petroleum coke will be affected by the internal and external diffusion process, and the relevant parameters involved are difficult to be obtained directly through experiments. It is necessary to use mathematical models to describe the kinetic adsorption mechanism, so as to further understand the mercury removal by the adsorbent in the simulated coal-fired flue gases. Thus in this study, the bench scale fixed-bed reactor is used as an experimental system to better understand the novel brominated petroleum coke on elemental mercury removal in flue gas. The fixed-bed reaction temperature, the initial elemental mercury concentration and the possible flue gas components of O2, NO, SO2 and HCl are investigated. Mathematic kinetic adsorption models are chosen to find out the adsorption mechanism on elemental mercury by brominated petroleum coke in simulated flue gas.
2. Experimental
2.1 Material preparation
The raw petroleum coke obtained from the upgrading of oil sands deposits in Alberta, Canada was grounded with ball mill and sieved through 100-mesh. After dried at 110 °C for 24 h, 2 g of which was put in a ball with certain amount of small glass beads and 20 mg liquid bromine to shake for 30 min. Then, the ball was put in a fume hood for 1 h and set in a vacuum drying oven at 200 °C for 30 min to let the non-binding bromine evaporate completely. The received sample was cooled naturally and then kept in a sealed container for further experiments. The novel chemical–mechanical bromination procedure and the tested brominated petroleum coke were described in detail and well characterized in our previous studies.7,8
2.2 Bench scale fixed-bed experimental system
The schematic diagram of bench scale fixed-bed experimental system for elemental mercury adsorption by brominated petroleum coke is shown in Fig. 1. The setup includes five parts as flue gas distribution part, elemental mercury permeation device, fixed-bed adsorption reactor, gas washing device and on-line mercury analyzer. Elemental mercury is volatilized by adjusting the temperature of the circulating water bath. The high-purity N2 with the rate of 30 mL min−1 as carrier gas passes through elemental mercury permeation device and enters the gas premix tank. The rate of carrier flow and balancer flow is controlled by D07-19B mass flow-meter, so as to keep the inlet mercury content constant in the simulated flue gases. The flow rate of flue gas component (O2, NO, SO2, HCl) is controlled by the rote-meter to keep 2 L min−1 in the pipeline. After fully mixed in the gas premix tank, the mixed gas is divided into two paths, part of which discharges through the tail gas and the rest enters the temperature controlled fixed-bed reactor, where a quartz glass tube is set inside.
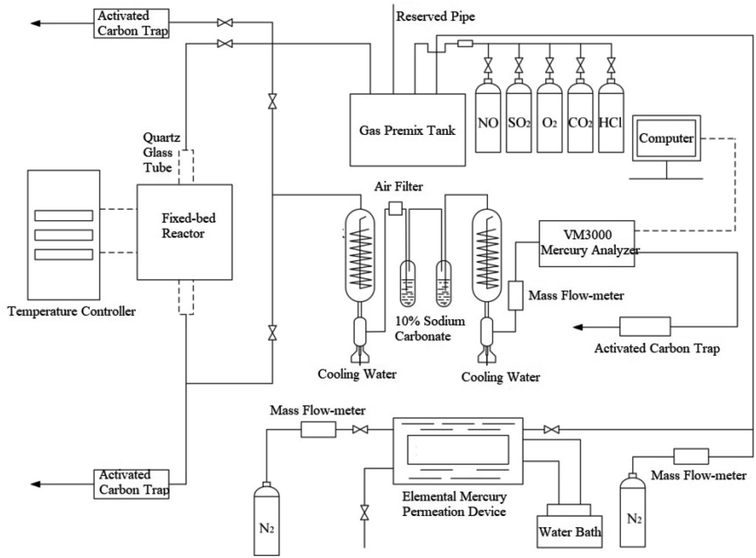 |
| Fig. 1 Schematic diagram of bench scale fixed-bed experimental system. | |
During the experiment, 50 mg brominated petroleum coke was evenly laid on the glass wool in the quartz tube reactor. The mixed gas containing a certain amount of elemental mercury passed through the adsorbent, which first came into the gas washing device to remove the possible acid gas in the gas path, and then entered the VM3000 mercury analyzer (Mercury Instruments, German) for online monitoring, of which the accuracy of which was 0.1 μg m−3. The mixed gas was divided into two air flows, the main flow was set passing the brominated petroleum coke and the VM3000 mercury analyzer, the bypass flow was set not passing the adsorbent but the VM3000 mercury analyzer. Before each test, the main flow was closed and the initial elemental mercury passed through the bypass flow and kept for 30 min for inlet mercury stable. After that, the setup was changed to the main flow and the outlet mercury concentration was recorded continuously. The initial inlet mercury concentration and the outlet mercury concentration were expressed as Hgin0 and Hgout0 separately. At the end of each pipeline, an adsorption box equipped with activated carbon filter was used to treat the tail gas before discharging it into the atmosphere.
The unit cumulative mercury quantity at a certain time was used to evaluate the adsorption performance of mercury, which could be expressed by (1):
|
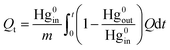 | (1) |
where
Qt: the unit cumulative mercury adsorption quantity, μg g
−1;
Q: the unit flow rate, m
3 min
−1;
t: the cumulated time, min;
m: the total amount of brominated petroleum coke, g.
2.3 Kinetic models
The changes of mercury mass, based on the principle of mass balance in axial microelements inside the fixed-bed reactor during the adsorption process by brominated petroleum coke was shown in Fig. 2 and the reaction formula was obtained as (2): |
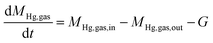 | (2) |
where MHg,adsorb expresses mercury mass adsorbed in microelement of brominated petroleum coke in unit time; MHg,gas,in expresses the inlet mercury mass to microelement in unit time; MHg,desorb expresses mercury mass desorbed from microelement of brominated petroleum coke in unit time; MHg,gas,out expresses the outlet mercury mass from microelement in unit time; MHg,gas expresses accumulative mercury gas mass in microelement of brominated petroleum coke in unit time; G expresses mercury adsorption efficiency of brominated petroleum coke in unit time.
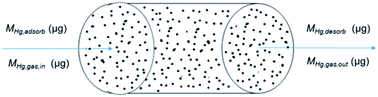 |
| Fig. 2 Changes of mercury mass in microelement during adsorption process. | |
Because of the complex situation of the mercury adsorption in coal fired flue gas, the reaction rate is affected by various environmental factors and is difficult to obtain from the experiments, appropriate kinetic models were needed to fit the mercury adsorption data, the relevant parameters are obtained to predict the control steps and the adsorption mechanism.28 Based on the mass balance principle, Langmuir adsorption isotherm and Temkin adsorption isotherm,29–31 four simplified kinetic models9 were obtained to evaluate the elemental mercury adsorption from flue gas by brominated petroleum coke. The fixed-bed temperature, initial inlet mercury concentration and individual flue gas components of O2, NO, SO2 and HCl were conducted on the fixed-bed reactor. Intra-particle diffusion model is to describe the process of elemental mercury diffusing to brominated petroleum coke through the action of concentration gradient and the role of van der Waals force, and the mathematical expression is shown as: Qt = kpt1/2 + C; Pseudo-first order kinetic model is originated from Lagergren equation, which is to describe the process of external mass transfer, and the mathematical expression is shown as: dQt/dt = k1(Qe − Qt); Pseudo-second order kinetic model is based on Langmuir adsorption isotherm, which is to describe the process of chemical adsorption, and the mathematical expression is shown as: dQt/dt = k2 (Qe − Qt)2; Elovich kinetic model is based on Temkin adsorption isotherm, which is the other equation to describe the process of chemical adsorption in more complex situation, and the mathematical expression is shown as:
where
Qt: the unit cumulative mercury adsorption quantity, μg g
−1;
Kp: the intra-particle diffusion rate constant, μg (g
−1 min
−1/2);
C: the constant related to the boundary layer, mg g
−1;
Qe: the mercury equilibrium adsorption quantity, μg g
−1;
k1: the pseudo-first order adsorption rate constant (min
−1);
k2: the pseudo-second order adsorption rate constant, g (μg
−1 min
−1);
a: the Elovich initial adsorption rate, μg (g
−1 min
−1);
b: the Elovich desorption constant, g μg
−1.
3. Results and discussion
3.1 Effect of reaction temperature and Hgin0 concentration
3.1.1 Temperature and Hgin0 concentration. The temperature of fixed-bed reactor which is one of the key factors can affect the elemental mercury removal performance of brominated petroleum coke. As shown in Fig. 3a, the elemental mercury cumulative quantity was greatly different when the reaction temperature from 50 to 200 °C, and 150 °C was found as the best reaction temperature. The main reason was that high temperature provided sufficient activation energy for the occurrence of chemisorption,32 with the increase of reaction temperature, molecules accelerated moving, resulting in the increase of effective collision of mercury molecules on the surface of brominated petroleum coke, which improved the reaction rate of substances, while the amount of mercury adsorbed by adsorbent also increased. However, when the temperature reached 200 °C, the mercury cumulative quantity decreased because of the loss of effective bromine breaking away from the sorbent.8 Another, the amount of mercury adsorbed at 50 °C was higher than that at 100 °C, because the activation energy provided by temperature was limited at low temperatures, with the physisorption played a leading role with small amount mercury could be chemically adsorbed.33 The flue gas temperature of upstream of the electrostatic precipitator in coal-fired power plant was about 140 °C,33 indicating that the optimal temperature for mercury removal by brominated petroleum coke was consistent with the flue gas temperature in actual coal-fired power plant.
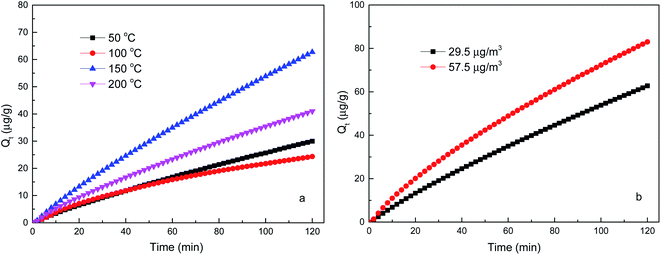 |
| Fig. 3 Effect of temperature and inlet Hg0 concentration on mercury adsorption. | |
The initial elemental mercury concentration is the other important factor affecting elemental mercury accumulation on the brominated petroleum coke. The inlet mercury concentration of (29.5 ± 0.5) μg m−3 and (57.5 ± 0.5) μg m−3 were set to compare the different cumulative mercury adsorption quantity at 150 °C with the data acquisition time of 120 min as shown in Fig. 3b. The amount of mercury adsorbed by brominated petroleum coke increased when the initial inlet mercury concentration increased, it is mainly because the increase of inlet Hg0 concentration can increase the driving force towards the surface of activated carbon and improve the efficiency external mass transfer rate and internal diffusion rate.24
3.1.2 Kinetic analysis. Four kinetic models of intra-particle diffusion, pseudo-first order, pseudo-second order and Elovich were used in order to find out the elemental mercury adsorption mechanism of brominated petroleum coke with the inlet elemental mercury concentration of (29.5 ± 0.5) μg m−3 at 150 °C in 120 min as shown in Table 1. Elovich kinetic model demonstrated the highest related coefficient R2 of 0.9999, which indicated that chemical adsorption was the dominant step on elemental mercury removal for brominated petroleum coke in pure N2 atmosphere. Meanwhile, R2 of intra-particle diffusion and pseudo-first order were 0.9957 and 0.9997 separately, which showed that intra-particle diffusion and external mass transfer carried out simultaneously as well in the complex process. The intra-particle diffusion rate kp was higher than that the initial mercury adsorption rate a from Elovich kinetic model, which indicated that the adsorption process could be divided into two stages: chemical adsorption and internal diffusion adsorption. The chemical adsorption was dominant in the initial adsorption stage, because a large number of adsorption active sites with loading bromine8 existed on the surface of the adsorbent promoting the adsorption rate. The surface adsorption rate decreased and the internal diffusion rate increased when the active sites were occupied gradually. Although the external mass transfer and internal diffusion limited the whole adsorption process, the chemisorption at the active sites on the surface of brominated petroleum coke was the rate control step because of the initial lower chemisorption rate.
Table 1 Data obtained from kinetic modelsa
Kinetic models |
Kinetic parameters |
R2: fitting correlation coefficient; Kp: intra-particle diffusion rate constant, μg (g−1 min−1/2); C: the constant related to the boundary layer, mg g−1; Qe: mercury equilibrium adsorption quantity, μg g−1; k1: pseudo-first order adsorption rate constant (min−1); k2: pseudo-second order adsorption rate constant, g (μg−1 min−1); a: Elovich initial adsorption rate, μg (g−1 min−1); b: Elovich desorption constant, g μg−1. |
Intra-particle diffusion model |
Kp (μg (g−1 min−1/2)) |
C (μg g−1) |
R2 |
1.0269 |
2.9605 |
0.9959 |
Pseudo-first order kinetic model |
Qe (μg g−1) |
k1 (min−1) |
R2 |
152.85 |
0.0044 |
0.9997 |
Pseudo-second order kinetic model |
Qe (μg g−1) |
k2 (g (μg−1 min−1)) |
R2 |
273.49 |
8.9718 × 10−6 |
0.9998 |
Elovich kinetic model |
a (μg (g−1 min−1)) |
b (g μg−1) |
R2 |
0.6668 |
0.0078 |
0.9999 |
The adsorption equilibrium state of the fixed bed system was considered as that the mercury concentration at the outlet was equal to the inlet concentration. Thus, the saturated adsorption capacity of the adsorbent was defined as the equilibrium adsorption quantity, which could be calculated by the kinetic models and accurately predicted from the adsorption parameters.23,24 As pseudo-second order kinetic model was better fitted the adsorption process than pseudo-first order kinetic model, the obtained equilibrium adsorption quantity was 273.49 μg g−1 of the system with the inlet elemental mercury concentration of (29.5 ± 0.5) μg m−3 at 150 °C.
3.2 Effect of individual flue gas components
The volume percentages for main components in the flue gas of coal-fired power plants are about 12% CO2, 6% O2, 75% N2, 5% H2O and the other possible components include SO2, HCl and NOx.33 Among them, SO2, HCl, NO and O2 can oxidize elemental mercury so then affect the mercury adsorption process by the adsorbent. Thus, the effects of individual flue gas component of SO2, HCl, NO and O2 on mercury removal by brominated petroleum coke was investigated, in order to understand their promotion or inhibition mechanism.
3.2.1 Effect of O2. The effect of O2 on elemental mercury adsorption by brominated petroleum coke was explored under 5% and 10% O2 in N2 atmosphere on the fixed-bed reactor. As shown in Fig. 4, a certain amount of O2 could promote the unit mercury accumulation on the brominated petroleum coke obviously. The unit accumulation enhanced via increasing O2 composition, indicating that oxygen promoted mercury adsorption by brominated petroleum coke in simulated flue gas compared with that under pure N2 atmosphere.
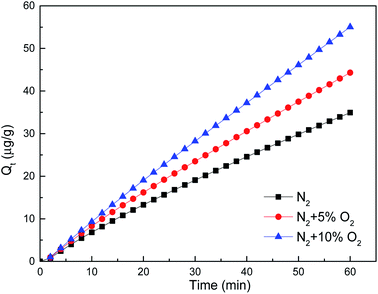 |
| Fig. 4 Effect of O2 on mercury adsorption by brominated petroleum coke. | |
The mechanism was explored mainly as the following possibilities: (1) oxygen were adsorbed by brominated petroleum coke to form new oxygen-containing functional groups, such as carbonyl and lactone groups, which were proved to promote mercury adsorption34,35 when oxygen was in contact with the surface of the brominated petroleum coke. (2) Oxygen were adsorbed on the active sites of the brominated petroleum coke, which could form carbon oxygen compounds, and then reacted with elemental mercury to form new substances.36 (3) Oxygen reacted with mercury in simulated flue gas in the form of mercuric oxide, and then adsorbed on the surface of the brominated petroleum coke.37
3.2.2 Effect of HCl. HCl was one of the important factors on mercury removal by brominated petroleum coke. It was reported that HCl in flue gas reacted with the active sites on the surface of the adsorbent to form active Cl reaction group and then undergo heterogeneous oxidation in the form of electron exchange to form HgClx,32 which was competitive with HgBrx (ref. 8) on active sites of the brominated petroleum coke. The adsorption mechanism might be that they promoted simultaneously or competed for active sites on the surface of the sorbents. As shown in Fig. 5, the unit cumulative adsorption mercury quantity on brominated petroleum coke sample increased compared with that in pure N2 atmosphere, when adding HCl to the simulated flue gas, and the results had not changed a lot with the concentration between 50 and 100 ppm HCl in the flue gas. Therefore, continuing increasing the concentration of HCl would not improve mercury adsorption quantity on the surface of brominated petroleum coke. The result was consistent with other researchers reported.38
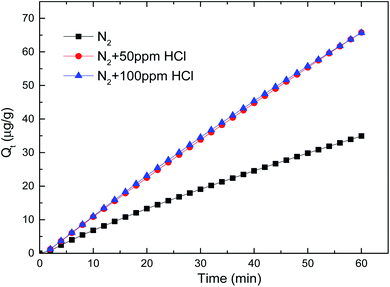 |
| Fig. 5 Effect of HCl on mercury adsorption by brominated petroleum coke. | |
Krishnakumar39 explored that Cl atom was reacted much faster than Cl2, and HCl got the highest reaction barrier as to cause the lowest reaction process. That was confirmed in our previous inlet mercury stable test, when a certain amount of HCl flowing through the bypass pipeline, the concentration of outlet elemental mercury got a sudden decrease of 3 μg m−3, indicating a partial homogeneous oxidation occurred possibly.40 In conclusion, a proper certain amount of HCl was benefit for elemental mercury removal by brominated petroleum coke, but it would cause mercury adsorption decrease in the high HCl concentration.
3.2.3 Effect of NO. In order to explore the effect of NO on elemental mercury removal by brominated petroleum coke, the test was conducted under N2 atmosphere with 250 and 800 ppm NO for comparison on fixed-bed reactor. As shown in Fig. 6, the unit mercury cumulative quantity increased compared with that in pure N2 atmosphere and the higher the NO concentration in N2 atmosphere, the higher the mercury cumulative quantity, which indicated NO in simulated flue gas promoted mercury removal by brominated petroleum coke obviously. The results confirmed that NO in flue gas played an important role in promoting the unit mercury cumulative adsorption quantity.
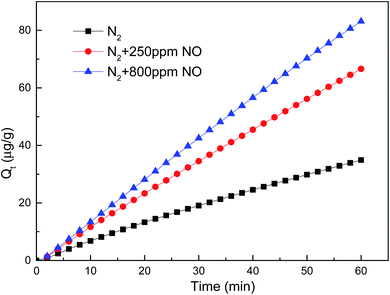 |
| Fig. 6 Effect of NO on mercury adsorption by brominated petroleum coke. | |
The chemical adsorption mechanism was mainly that NO was easily adsorbed by the active sites on the surface of carbon based adsorbent to form NO–Cn reaction groups.41 When NO–Cn groups increased, more stable (NO)2–Cn reaction group could be easily formed with two NO–Cn groups on the adjacent adsorption sites. The reaction formula was shown as follows:
NO–Cn + Hg0 + 2NO → HgNO3–Cn + N2 |
(NO)2–Cn + Hg0 + NO → HgNO3–Cn + N2 |
HgNO3–Cn + 3NO → Hg(NO3)2–Cn + N2 |
3.2.4 Effect of SO2. The effect of SO2 was conducted in N2 atmosphere with 450 and 1500 ppm separately for comparison. As shown in Fig. 7, a certain amount of SO2 adding in the pipeline accelerated mercury adsorption rate by brominated petroleum coke. When the amount increased to 1500 ppm, the mercury adsorption rate decreased. The results were consistent with the research results reported by other researchers, An et al. reported that the promotion of 800 ppm SO2 was reduced on elemental mercury adsorption by active coke,42 Chiu reported that mercury removal changed from promotion to inhibition with SO2 concentration of 500 ppm by MnOx/SCR catalyst.43
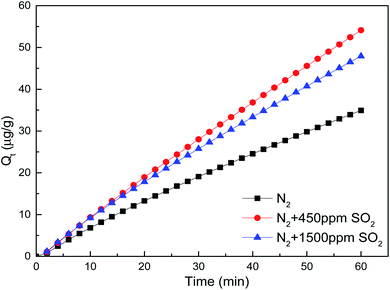 |
| Fig. 7 Effect of SO2 on mercury adsorption by brominated petroleum coke. | |
SO2 mainly played a role in promoting the mercury removal process by brominated petroleum coke, and the promotion level was greatly affected by the concentration of SO2 in flue gas, which had a two-sided effect on the performance of mercury removal by adsorbents, oxidation and activated adjacent sites were considered to be the main reasons for the promotion effect. It was confirmed that more complex structure with sulfur functional groups was formed on the surface of brominated petroleum coke for elemental mercury adsorption, because the free orbit of the outer layer of the sulfur atom could accept two electrons in the outer layer of the elemental mercury to form oxidized mercury. On the other side, SO2 was easy to combine with oxygen-containing functional groups on the surface of the adsorbent, which was compete with elemental mercury adsorption, so then lead to the reduction of adsorption capacity of brominated petroleum coke in high SO2 concentration.44–49
3.2.5 Comparison among flue gas components. It was secured from Fig. 8 that the final mercury cumulative quantity was 35 μg g−1 in pure N2 environment within 60 min, and all other flue gas components improved the unit mercury accumulative quantity on the surface of brominated petroleum coke. With the existence of 800 ppm NO in N2 atmosphere, the mercury accumulative quantity reached 85 μg g−1, which was increased significantly compared to that under other flue gas components. The presence of 250 ppm NO, 100 and 500 ppm HCl increased the mercury accumulative quantity by about twofold quantity compared to that under N2 atmosphere. But to SO2, the situation was different, the quantity increased with the concentration 450 ppm, but decreased with 1500 ppm, which inhibited the final mercury cumulative quantity, so as to lower the mercury accumulative quantity of brominated petroleum coke in 60 min.
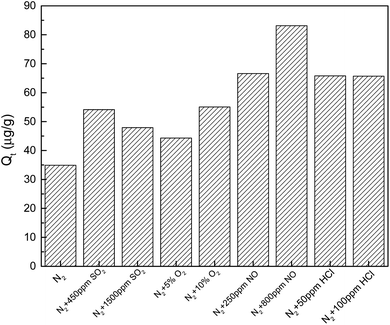 |
| Fig. 8 Comparison of flue gases on unit accumulative mercury adsorption in 60 min. | |
3.2.6 Kinetic mechanism. In elemental mercury adsorption by brominated petroleum coke, it was confirmed that chemical adsorption played the dominant place in pure N2 atmosphere, which revealed from kinetic analysis at various fixed-bed temperature and initial mercury concentration. To further investigate the effect of flue gas components on mercury adsorption by brominated petroleum coke, kinetics analysis was also used to conduct the influence of O2, HCl, NO and SO2 with pseudo-second order kinetic model and Elovich kinetic model describing chemical adsorption. The experimental data was obtained with the inlet mercury concentration (29.5 ± 0.5) μg m−3 and the fixed-bed reaction temperature 150 °C in 60 min. The relevant kinetic parameters like the fitting correlation coefficient R2, pseudo-second order adsorption rate h(k2Qe2), the initial mercury adsorption rate a and the equilibrium adsorption quantity Qe were obtained and compared as shown in Table 2.
Table 2 Kinetic data obtained from kinetic modelsa
Flue gas |
Simulated condition |
Pseudo-second order kinetic model |
Elovich kinetic model |
Qe (μg g−1) |
k2 (g (μg−1 min−1)) |
h (μg (g−1 min−1)) |
R2 |
a (μg (g−1 min−1)) |
b (g μg−1) |
R2 |
R2: fitting correlation coefficient; Qe: mercury equilibrium adsorption quantity, μg g−1; k2: pseudo-second order adsorption rate constant, g (μg−1 min−1); h: pseudo-second order adsorption rate, μg (g−1 min−1) a: Elovich initial adsorption rate, μg (g−1 min−1); b: Elovich desorption constant, g μg−1. |
|
N2 |
196.99 |
1.8149 × 10−5 |
0.7043 |
0.9998 |
0.7267 |
0.0122 |
0.9998 |
O2 |
N2 + 5% O2 |
351.20 |
6.8143 × 10−6 |
0.8405 |
0.9998 |
0.8597 |
0.0067 |
0.9998 |
N2 + 10% O2 |
1228.14 |
6.3637 × 10−7 |
0.9599 |
0.9998 |
0.9959 |
0.0027 |
0.9999 |
HCl |
N2 + 50 ppm HCl |
1986.37 |
2.8865 × 10−7 |
1.1389 |
0.9997 |
1.1997 |
0.0023 |
0.9999 |
N2 + 100 ppm HCl |
919.90 |
1.4022 × 10−6 |
1.1866 |
0.9995 |
1.2652 |
0.0007 |
0.9999 |
NO |
N2 + 250 ppm NO |
1002.70 |
1.1835 × 10−6 |
1.1899 |
0.9998 |
1.2315 |
0.0028 |
0.9999 |
N2 + 800 ppm NO |
4074.85 |
8.5883 × 10−8 |
1.4260 |
0.9995 |
1.5082 |
0.0015 |
0.9999 |
SO2 |
N2 + 450 ppm SO2 |
889.85 |
1.2137 × 10−6 |
0.9610 |
0.9998 |
0.9948 |
0.0033 |
0.9999 |
N2 + 1500 ppm SO2 |
317.98 |
9.2539 × 10−6 |
0.9357 |
0.9998 |
0.9529 |
0.0072 |
0.9999 |
It could be seen from the table that the correlation coefficient R2 in pseudo-second order kinetic equation and the Elovich equation were basically reached to above 0.999, indicating that both equations could be used to describe the adsorption process of mercury removal by brominated petroleum coke and chemisorption was still dominant under the condition of participation of flue gas components. The difference of initial mercury adsorption rates h and a from both models were not statistically significant, which illustrated that h and a both could be used to describe the reaction process.
The initial mercury adsorption rate (h/a) in each flue gas component improved compared with that in pure nitrogen, indicating that the participation of oxidizing gas could accelerate the chemical adsorption process of mercury removal by brominated petroleum coke. 800 ppm NO existence in flue gas demonstrated the highest acceleration, more than double rate than in pure N2 atmosphere, with the initial mercury adsorption rate of 1.5082 μg (g−1 min−1) obtained from the Elovich kinetic model. Almost the same initial mercury adsorption rate was obtained for the other components' concentration of 50 ppm HCl, 100 ppm HCl and 250 ppm NO, which enhanced positively as well. However, when the concentration of SO2 reached to 1500 ppm, the initial mercury adsorption rate decreased more than that for 450 ppm, indicating that there was a maximum limit for the concentration of SO2 in flue gas. After reaching to a high concentration, the promotion effect was weakened. This result was consistent with the conclusion that high content of sulfur oxides could reduce the mercury capture ability of activated carbon as reported by other researchers.45,46
Regarding the equilibrium adsorption quantity Qe, found from pseudo-second order, applying oxidized gas could increase the mercury adsorption quantity, the mercury adsorption amount came to 4074.85 μg g−1 with the existence of 800 ppm NO in the flue gas. As to O2, the equilibrium adsorption quantity increased almost fourfold when double concentration applied in N2 atmosphere. As to HCl and SO2, the equilibrium adsorption quantity decreased sharply in higher concentration, that meant high HCl and SO2 in flue gas was negative for elemental adsorption on brominated petroleum coke.
It was interesting to find that, 800 ppm NO in flue gas showed the highest rate, more than twofold the rate in pure atmosphere; increasing HCl concentration from 50 to 100 ppm, the equilibrium adsorption quantity decreased evidently but the initial mercury adsorption rate increased; increasing SO2 concentration from 450 to 1500 ppm, the equilibrium adsorption quantity decreased obviously but the initial mercury adsorption rate remained almost the same; increasing O2 concentration from 5 to 10%, and NO concentration from 250 to 800 ppm, the equilibrium adsorption quantity increased remarkably while the initial mercury adsorption rate increased concurrently, it might be the new oxygen-containing functional groups formed and more active sites created on the surface of the brominated petroleum coke. Since the mercury removal behavior of the different brominated carbon-based sorbents such as brominated biomass based, brominated coal based and commercial brominated activated carbon in coal-fired flue gas50 are quite different from those in the simulated flue gas, mainly as a result of large proportion of Hg2+ and Hgp, the effect of components on mercury removal of brominated petroleum coke might be different, further comparison should be conducted in the coal-fired flue gas.
4. Conclusions
The effect of temperature, initial elemental mercury concentration and flue gas components of O2, HCl, NO and SO2 were compared on mercury capture by brominated petroleum coke, and then the kinetic mechanism was investigated with the data of unit accumulative mercury quantity on a bench scale fixed-bed reactor. The initial inlet mercury concentration could enhance the adsorption by brominated petroleum coke and the optimal temperature for elemental mercury removal was about 150 °C. Another, all the flue gas components including O2, HCl, NO and SO2 showed a certain promoting effect on the mercury adsorption, but demonstrated promotion or competition on mercury removal by brominated petroleum coke according to the concentration of each flue gas component.
The fitting correlation coefficients R2 of pseudo-second order kinetic model and Elovich kinetic model were slightly higher than those of the intra particle diffusion model and pseudo-first order kinetic model, indicating that the chemical adsorption was accelerated and taken the role, while intra-particle diffusion and external mass transfer taking place simultaneously in the complex adsorption process as well. Kinetic parameters indicated that the initial mercury adsorption rate h and the equilibrium adsorption quantity Qe increased, when supplying higher concentration of O2 or NO in N2 atmosphere as new oxygen-containing functional groups formed and more active sites created on the surface of the brominated petroleum coke. On the contrary, the concentration of SO2 or HCl was too high, the mercury equilibrium adsorption quantity decreased as heterogeneous reaction occurred simultaneously. The adsorption kinetic mechanism can be concluded that chemical adsorption process is dominant and accelerated while intra-particle diffusion and external mass transfer taking place concurrently in simulated flue gas. Further effects of these gas mixtures and inter-reaction should be conducted between flue gas components and S/Br on the surface of brominated petroleum coke in simulated flue gas; the reusable possibility and adsorption performance of the adsorbent for elemental mercury after regenerating the brominated petroleum coke at elevated temperatures were expected to study in the future.
Conflicts of interest
There are no conflicts to declare.
Acknowledgements
Thanks to the National Fundamental Research Funds for the Central Universities (CUSF-DH-D-2017097), Shanghai New Teacher Training Program (ZZNL20012), Scientific and Technological Leading Talent Project (A2-0265-22-40) and Scientific Research Project (KY2-0000-20-04) of Shanghai Vocational College of Agriculture and Forestry. Highly appreciate Professor Zhenghe Xu in University of Alberta (Alberta, Canada) for supporting the experimental materials preparation and Professor Yongfa Diao in Donghua University for supporting mercury removal experiments.
References
- H. Yang, Z. Xu and M. Fan, et al. Adsorbents for capturing mercury in coal-fired boiler flue gas, J. Hazard. Mater., 2007, 146(1), 1–11 CrossRef CAS PubMed.
- A. D. Karatza, D. Lansia and C. Musmarra, et al. Study of mercury absorption and desorption on sulfur impregnated carbon, Exp. Therm. Fluid Sci., 2000, 21, 150–155 CrossRef.
- K. Suresh Kumar Reddy, A. Al Shoaibi and C. Srinivasakannan, Elemental mercury adsorption on sulfur-impregnated porous carbon – A review, Environ. Technol., 2013, 35, 18–26 CrossRef PubMed.
- T. M. Bisson, L. C. Mac Lean and Y. Hu, et al. Characterization of mercury binding onto a novel brominated biomass ash sorbent by X-ray absorption spectroscopy, Environ. Sci. Technol., 2012, 46, 86–93 CrossRef PubMed.
- A. Saha, Investigation of changes in surface chemistries on virgin and brominated activated carbon sorbents during mercury capture: before and after regeneration, Energy Fuels, 2014, 28, 4021–4027 CrossRef CAS.
- D. Karatza, A. Lansia, D. Musmarra and C. Zucchili, Study of mercury absorption and desorption on sulfur impregnated carbon, Exp. Therm. Fluid Sci., 2000, 21, 150–155 CrossRef CAS.
- Y. Xiao, D. Pudasaineeb and R. P. Gupta, et al. Bromination of petroleum coke for elemental mercury capture, J. Hazard. Mater., 2017, 336, 232–239 CrossRef CAS PubMed.
- Y. Xiao, D. Pudasaineeb and R. P. Gupta, et al. Elemental mercury reaction chemistry on brominated petroleum cokes, Carbon, 2017, 124, 89–96 CrossRef CAS.
- Y. Xiao, Y. Diao and L. Tian, et al. Kinetic mechanism of novel brominated petroleum coke on trace Hg0 removal from flue gas, China Environ. Sci., 2018, 38(2), 508–515 CAS.
- Y. Xiao, X. Liu and Y. Diao, Understanding the effect of thiophene sulfur on brominated petroleum coke for elemental mercury capture from flue gases, RSC Adv., 2021, 11, 4515–4522 RSC.
- Q. Lv, M. Cai and C. Wang, et al. Investigation on elemental mercury removal by cerium modified semi-coke, J. Energy Inst., 2020, 93(2), 666–678 CrossRef CAS.
- Y. Chen, X. Guo and F. Wu, Development and evaluation of magnetic iron carbon sorbents for mercury removal in coal combustion flue gas, J. Energy Inst., 2020, 93(4), 1615–1623 CrossRef CAS.
- A. Dal Pozzo, L. Lazazzara and G. Antonioni, et al. Techno-economic performance of HCl and SO2 removal in waste-to-energy plants by furnace direct sorbent injection, J. Hazard. Mater., 2020, 394, 122518 CrossRef CAS PubMed.
- X. Geng, J. Hu and Y. Duan, et al. The effect of mechanical-chemical-brominated modification on physicochemical properties and mercury removal performance of coal-fired by-product, Fuel, 2020, 266, 117041 CrossRef CAS.
- J. Liu, W. Qu and S. W. Joo, et al. Effect of SO2 on mercury binding on carbonaceous surfaces, Chem. Eng. J., 2012, 184, 163–167 CrossRef CAS.
- H. Qin, P. He and J. Wu, et al. Theoretical study of hydrocarbon functional groups on elemental mercury adsorption on carbonaceous surface, Chem. Eng. J., 2020, 380, 122505 CrossRef CAS.
- P. He, Y. Zhang and X. Zhao, et al. Effect of flue gas on elemental mercury removal capacity of defective carbonaceous surface: A first-principles study, J. Hazard. Mater., 2021, 404, 124013 CrossRef CAS PubMed.
- Q. Zhou, Y. Duan and M. Chen, et al. Effect of flue gas component and ash composition on elemental mercury oxidation/adsorption by NH4Br modified fly ash, Chem. Eng. J., 2018, 345, 578–585 CrossRef CAS.
- C. L. M. Camargo, N. S. D. Resende and A. G. D. Oliveira, et al. Investigation of adsorption enhanced reaction process of mercury removal from simulated natural gas by mathematical modeling, Fuel, 2014, 129(4), 129–137 CrossRef CAS.
- C. Reid and K. Thomas, Adsorption of gases on a carbon molecular sieve used for air separation: Linear adsorptive as probes for kinetic selectivity, Langmuir, 1999, 15(9), 3206–3218 CrossRef CAS.
- H. C. His and C. H. Chen, Influences of acidic/oxidizing
gases on elemental mercury adsorption equilibrium and kinetics of sulfur-impregnated activated carbon, Fuel, 2012, 98, 229–235 CrossRef.
- J. Cai, B. Shen and Z. Li, et al. Removal of elemental mercury by clays impregnated with KI and KBr, Chem. Eng. J., 2014, 241, 19–27 CrossRef CAS.
- G. Skodras, I. R. Diamantopoulou and G. Pantoleontos, et al. Kinetic studies of elemental mercury adsorption in activated carbon fixed bed reactor, J. Hazard. Mater., 2008, 158, 1–13 CrossRef CAS PubMed.
- Q. Zhou, Y. F. Duan and Y. G. Hong, et al. Experimental and kinetic studies of gas-phase mercury adsorption by raw and bromine modified activated carbon, Fuel Process. Technol., 2015, 134, 325–332 CrossRef CAS.
- K. Johari, N. Saman and S. T. Song, et al. Adsorption equilibrium and kinetics of elemental mercury onto coconut pith, J. Environ. Sci. Technol., 2015, 8, 74–82 CrossRef CAS.
- R. Khunphonoi, P. Khamdahsag and S. Chiarakorn, et al. Enhancement of elemental mercury adsorption by silver supported material, J. Environ. Sci., 2015, 32, 207–216 CrossRef CAS PubMed.
- J. Zhang, Y. F. Duan and Q. Zhou, et al. Adsorptive removal of gas-phase mercury by oxygen non-thermal plasma modified activated carbon, Chem. Eng. J., 2016, 294, 281–289 CrossRef CAS.
- L. Wang, C. Chen and H. Kruse, Modeling mercury adsorption on carbon particles in simulated flue gas, J. Southeast Univ., Engl. Ed., 2006, 22(2), 256–259 CAS.
- C. Reid and K. Thomas, Adsorption of gases on a carbon molecular sieve used for air separation: Linear adsorptive as probes for kinetic selectivity, Langmuir, 1999, 15(9), 3206–3218 CrossRef CAS.
- S. Goswami and U. C. Ghosh, Studies on adsorption behaviour of Cr (VI) onto synthetic hydrous stannic oxide, Water S.A., 2006, 31(4), 597–602 Search PubMed.
- C. L. M. Camargo, N. S. D. Resende and A. G. D. Oliveira, et al. Investigation of adsorption enhanced reaction process of mercury removal from simulated natural gas by mathematical modeling, Fuel, 2014, 129(4), 129–137 CrossRef CAS.
- H. C. Zeng, F. Jin and J. Guo, Removal of elemental mercury from coal combustion flue gas by chloride-impregnated activated carbon, Fuel, 2004, 83(1), 143–146 CrossRef CAS.
- S. R. Shewchuk and R. Azargohar, Elemental Mercury Capture Using Activated Carbon: A Review[J], J. Environ. Anal. Toxicol., 2016, 6(4), 379 Search PubMed.
- G. G. Stavropoulos, P. Samaras and G. P. Sakellaropoulos, Effect of activated carbons modification on porosity, surface structure and phenol adsorption, J. Hazard. Mater., 2008, 151(2–3), 414 CrossRef CAS PubMed.
- J. Liu, M. A. Cheney and F. Wu, et al. Effects of chemical functional groups on elemental mercury adsorption on carbonaceous surfaces, J. Hazard. Mater., 2011, 186(1), 108–113 CrossRef CAS PubMed.
- Y. H. Li, C. W. Lee and B. K. Gullett, The effect of activated carbon surface moisture on low temperature mercury adsorption, Carbon, 2002, 40(1), 65–72 CrossRef CAS.
- Y. Liu, Comment on “Impact of sulfur oxides on mercury capture by activated carbon”, J. Environ. Sci. Technol., 2008, 42(3), 970–971 CrossRef CAS PubMed.
- R. Ochiai, M. A. Uddin and E. Sasaoka, et al. Effects of HCl and SO2 Concentration on Mercury Removal by Activated Carbon Sorbents in Coal-Derived Flue Gas, Energy Fuels, 2009, 23(10), 52–55 CrossRef.
- B. Krishnakumar and J. J. Helble, Determination of transition state theory rate constants to describe mercury oxidation in combustion systems mediated by Cl, Cl2, HCl and HOCl, Fuel Process. Technol., 2012, 94(1), 1–9 CrossRef CAS.
- B. Hall, P. Schager and O. Lindqvist, Chemical reactions of mercury in combustion flue gas, Water, Air, Soil Pollut., 1991, 56(1), 3–14 CrossRef CAS.
- J. H. Pavlish, E. A. Sondreal and M. D. Mann, et al. Status review of mercury control options for coal-fired power plants, Fuel Process. Technol., 2003, 82(2), 89–165 CrossRef CAS.
- D. An, X. Sun and X. Cheng, et al. Investigation on mercury removal and recovery based on enhanced adsorption by activated coke, J. Hazard. Mater., 2020, 384, 121354 CrossRef CAS PubMed.
- C. H. Chiu, H. C. Hsi and H. P. Lin, et al., Effects of properties of manganese oxide-impregnated catalysts and flue gas condition on multipollutant control of Hg0 and NO, J. Hazard. Mater., 2015, 291, 1–8 CrossRef CAS PubMed.
- W. Liu, R. D. Vidic and T. D. Brown, Impact of Flue Gas Conditions on Mercury Uptake by Sulfur-Impregnated Activated Carbon, J. Environ. Sci. Technol., 2000, 34(34), 154–159 CrossRef CAS.
- J. D. Laumb, S. A. Benson and E. A. Olson, X-ray photoelectron spectroscopy analysis of mercury sorbent surface chemistry, Fuel Process. Technol., 2004, 85, 577–585 CrossRef CAS.
- S. J. Miller, G. E. Dunham and E. S. Olson, et al. Flue gas effects on a carbon-based mercury sorbent, Fuel Process. Technol., 2000, 65(66), 343–363 CrossRef.
- A. A. Presto, E. J. Granite and A. Karash, Further Investigation of the Impact of Sulfur Oxides on Mercury Capture by Activated Carbon, Ind. Eng. Chem. Res., 2007, 46(24), 8273–8276 CrossRef CAS.
- A. A. Presto and E. J. Granite, Impact of sulfur oxides on mercury capture by activated carbon, Environ. Sci. Technol., 2007, 41, 6579–6584 CrossRef CAS PubMed.
- H. Zhang, T. Wang and Y. Zhang, et al. A review on adsorbent/catalyst application for mercury removal in flue gas: Effect of sulphur oxides (SO2, SO3), J. Cleaner Prod., 2020, 276, 124220 CrossRef CAS.
- W. Zhao, X. Geng and J. Lu, et al. Mercury removal performance of brominated biomass activated carbon injection in simulated and coal-fired flue gas, Fuel, 2021, 285, 119131 CrossRef CAS.
|
This journal is © The Royal Society of Chemistry 2022 |
Click here to see how this site uses Cookies. View our privacy policy here.