DOI:
10.1039/D2RA03609F
(Paper)
RSC Adv., 2022,
12, 23366-23378
Continuous hydrothermal furfural production from xylose in a microreactor with dual-acid catalysts
Received
11th June 2022
, Accepted 11th August 2022
First published on 17th August 2022
Abstract
An effective continuous furfural production from xylose in a microreactor over dual-acid catalysts was proposed. In this work, furfural was synthesized in an organic solvent-free system using formic acid and aluminum chloride as catalyst. The role of these catalysts in the consecutive reactions was examined and verified. The influence of operating conditions including xylose concentration, reaction temperature, residence time, total catalyst concentration, and catalyst ratio on the yield of furfural was investigated and optimized. The furfural yield of 92.2% was achieved at the reaction temperature of 180 °C, residence time of 15 min, catalyst molar ratio of 1
:
1, xylose concentration of 1 g L−1, and total catalyst concentration of 16 mM. The superior production performance of our process was highlighted in terms of the low catalyst concentration and short residence time compared to those of other systems based on the literature. In addition, a continuous in situ catalyst removal (purification) was demonstrated, providing further insights into the practical development of continuous furfural production.
1. Introduction
Furfural has been regarded as a promising platform chemical for numerous attractive bio-based chemicals and biofuels. 2-Furanmethanol, furan-2-carboxylic acid, and maleic anhydride are some of the furfural-based chemicals for biorefinery and pharmaceutical applications.1 Unfortunately, these chemicals can be partially substituted by petroleum-based counterparts. This is due to the relatively high price of furfural as raw material. For example, the commercial price of maleic anhydride derived from benzene was around 0.8–1.6 $ per kg
2 which was in a similar range to furfural price.3 Further development of the furfural production is required to improve efficiency, profitability, and competitiveness against those of petroleum-based competitors. One of the main causes for this issue is the inefficient furfural production (low yield), addressed as a significant barrier for sustainable development.4 The novel technologies are required to enhance the competitiveness of furfural production.
Conventionally carried out in a one-pot batch process, furfural production has been associated with high production costs with relatively low yield (<50%)5 (see Fig. 1: one-pot process). In this process, lignocellulosic material (pentosans) was converted to furfural through simultaneous hydrolysis and dehydration reactions using highly concentrated mineral acid as a catalyst. Side reactions such as condensation, isomerization, and resinification were responsible for the low furfural yield.6 Over the past decade, the yield was successfully enhanced to 50–80% via a two-step process (see Fig. 1: 2-step process). The hydrolysis was carried out in the first step to convert pentosans into xylose, which was subsequently converted to furfural via direct dehydration in the second step. The side reactions were suppressed to some extent in the 2-step process. However, the issues of side reactions and the large amount of catalyst require further development to achieve a higher yield (>80%). The limiting step for this process is the conversion of xylose into furfural. Hence, as the most abundant component in hemicellulose, xylose has been used as a starting material/model compound for the development of a 2-step furfural process.6
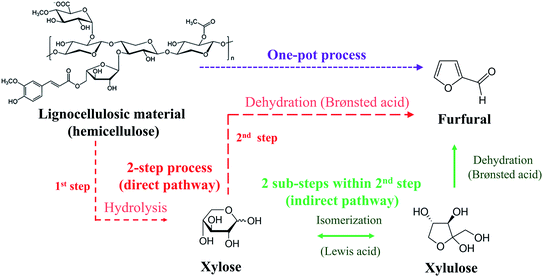 |
| Fig. 1 Furfural production pathways. | |
The indirect route of xylose conversion into furfural has recently been introduced (see Fig. 1: 2 sub-steps within 2nd step) to overcome the drawback of the 2-step furfural process. For this method, xylose was converted into xylulose through isomerization, followed by the dehydration of xylulose into furfural, offering a relatively small degree of side reactions.7 This reaction route allows milder operating conditions compared to that of the direct dehydration of xylose into furfural and higher furfural yield is generally observed.8 However, a drawback of the indirect route of xylose conversion into furfural is the requirement of two different catalysts. The isomerization requires Lewis acid and the dehydration is catalyzed by Brønsted acid (Fig. 1). An interesting approach is to apply the effective bi-functional or dual catalysts for the conversion of xylose into furfural, where Brønsted acid and Lewis acid catalysts can be used simultaneously. For example, in the work of Lopes et al. (2017),9 who applied both formic acid (55 wt%) and aluminum chloride (0.4 M) as catalyst for the furfural synthesis from xylose in a batch process. Although the furfural yield of 70% was achieved within 30 min of reaction time, the high concentration of acid catalysts was the main weakness of this technique. In addition, equipment corrosion can be another challenge for this process. These problems have been observed in various research works when dealing with highly corrosive acid catalysts.8,10 Besides, the relatively long reaction time required to achieve high furfural yield was also one of the major issues for improvement.11 Inefficient heat and mass transfers have been the main causes of these issues which could be overcome by the use of microreactor technology. Note that the development from batch to continuous process is mostly based on superior productivity.
An alternative to conventional reactors, microreactors have been regarded as efficient devices for process intensification in various bio-based applications due to the excellent properties of heat and mass transfer. For example, for the production of 5-hydroxymethylfurfural (5-HMF), high conversion of monosaccharide into 5-HMF was achieved within a few minutes of residence time instead of hours as generally required for the conventional batch production, demonstrating the remarkable performance of the microreactor.12–14 In our previous work,15 80% of 5-HMF yield from glucose conversion using 0.15 M of HCl was obtained with the residence time of 3 min. Evidently, the organic solvent is required to suppress the side reactions (biphasic system), increasing the complexity of separation and purification of the desired product. Moreover, the high price of solvent and high catalyst concentration are the disadvantages of this technique. Similar issues have been reported in the recent studies of furfural production in a microreactor.16,17 For example, in the work of Guo et al. (2022),16 the furfural synthesis from xylose was studied in the water-MIBK system. The high HCl concentration of 0.2 M was required to achieve the yield of 93% with the residence time of 4 min. In chemical processing, the total production cost is heavily influenced by the separation/purification processes.18 Hence, in this work, the development of continuous solvent-free furfural production from xylose in a microreactor using dual catalysts was proposed and investigated.
This work represents the intensification of continuous furfural production by applying microreactor technology, particularly for the conversion of xylose into furfural under organic solvent-free conditions. The aluminum chloride and formic acid were used as the dual-acid catalysts. The role of individual and combined catalysts in furfural production via consecutive reactions was examined and verified. The effects of operating conditions including xylose concentration, reaction temperature, residence time, total catalyst concentration, and catalyst ratio on the furfural yield were investigated and optimized using response surface methodology. The production performance of this proposed process was compared with the literature. Moreover, the in situ continuous acid catalyst removal was demonstrated using the fixed-bed adsorption technique.
2. Materials and methods
2.1 Materials
D-Xylose (>98%) from Alfa Aesar was used as a raw material for furfural production. D-Xylose (>99%), D-xylulose (>98%), D-lyxose (99%) and furfural (>98.5%) obtained from Sigma-Aldrich were used for product analysis. Aluminum chloride (>95%) and formic acid (88%) were purchased from Alfa Aesar. Acetonitrile (99.9%) used as a mobile phase for the analysis of product was obtained from RCI Labscan. Amberlyst 21 was purchased from Alfa Aesar for the acid catalyst removal process.
2.2 Furfural production
The schematic diagram of our continuous furfural production from xylose is shown in Fig. 2. A stream of xylose solution mixed with dual-acid catalysts (formic acid and aluminum chloride) was fed into a microreactor (VR: 4 mL; ID: 0.87 mm) at a constant flow rate using HPLC pump (LKB Bromma 2150). The volumetric flow rate (0.05 to 0.8 mL min−1), concentration of sugar (1 to 20 g L−1), and the total catalysts amount (5 to 25 mM) were adjusted depending on the conditions studied. The microreactor was placed inside a convection oven to control the reaction temperature. The reacting mixture exiting the reactor was quenched as it passed through a cooling bath. A back-pressure regulator (Idex, 100 psi) was installed at the end of the cooling system to prevent the vaporization of reactants and products. The cooled effluent was collected for product analysis by HPLC technique. Furfural yield, xylose conversion, and furfural selectivity were calculated from eqn (1)–(3). |
 | (1) |
|
 | (2) |
|
 | (3) |
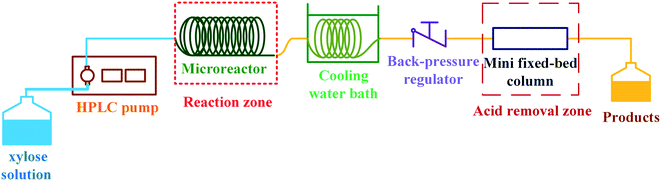 |
| Fig. 2 Proposed continuous furfural production with acid catalyst removal. | |
2.3 Acid catalyst removal process
After the furfural production as previously described, the product obtained was in a mixture and the purification of furfural was necessary. For the demonstration of in situ acid removal (see Fig. 2), the product stream from the condenser passed through a mini fixed-bed (VR: 1.4 mL; ID: 4.6 mm) of anion-exchange resin (Amberlyst A21, 0.8 g). The properties of Amberlyst 21 according to the manufacturer were as follows: the BET surface area of 35 m2 g−1, pore diameter of 11 nm, total pore volume of 0.1 cm3 g−1, and particle size of 590 μm. The system was operated at ambient temperature (∼26 °C) and pressure (∼1 bar). The effluent was collected for the product analysis by HPLC technique. This process was slightly modified based on our previous work.15
2.4 Raw material and product analysis
The pentose sugar components (xylose, lyxose, and xylulose) were analyzed by the HPLC-RI technique (RI 2300, Knauer). ACE excel 5 NH2 (250 mm × 4.6 mm × 5 μm) was used to separate and to quantify these sugars at a temperature of 40 °C. 85
:
15 (v/v) using acetonitrile and DI water as mobile phase at a volumetric flow rate of 0.7 mL min−1. The injection volume for each analysis was 10 μL. Analytical standards were applied as reference peaks for sample identification. The concentration of sugar sample (g L−1) was calculated based on the calibration curve of each analytical standard which was prepared for the range of 0.5 to 30 g L−1.
The furfural content was analyzed by the HPLC-UV technique (UV 2500, Knauer). The quantitative analysis was carried out on ACE excel C18 (250 mm × 4.6 mm × 5 μm). The mobile phase of acetonitrile and water (10
:
90 v/v) at a flow rate of 0.7 mL min−1 was used under the separation temperature of 40 °C and the wavelength of 320 nm. The injection volume for each analysis was 10 μL. The analytical standard of furfural was used to identify and quantify this compound. The calibration curve of furfural standard was in the range of 0.6 to 19.2 g L−1.
3. Results and discussion
3.1 Role and effect of formic acid on furfural production
In this work, the development of continuous furfural production from xylose was proposed through indirect xylose conversion into furfural. Two consecutive reaction steps of isomerization of xylose into xylulose followed by dehydration of xylulose into furfural were performed in a microreactor (see Fig. 3). Formic acid and aluminum chloride were used as the Brønsted and Lewis acid catalysts to separately accelerate isomerization and dehydration reactions, respectively. Before simultaneously applying these two catalysts for furfural production through the two-step reaction pathway, the use of individual catalysts for furfural production was investigated for better understanding of the role and effect of each catalyst.
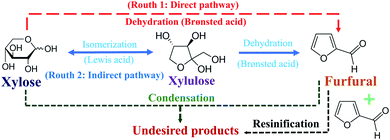 |
| Fig. 3 Direct and indirect pathways of furfural production from xylose. | |
A preliminary study on the role of formic acid in furfural production was carried out with the catalyst concentration of 20 mM, initial xylose concentration of 10 g L−1, and residence time of 20 min, while reaction temperature in a range of 130 to 180 °C was investigated. Note that, the side reactions easily competed with the main reaction (dehydration) at high reaction temperatures exceeding 180 °C even without the catalyst.19 The furfural yield of less than 10% was obtained when the reaction temperature was in the range of 130 to 150 °C (data not shown). This indicated that the reaction temperature of greater than 150 °C was necessary to directly dehydrate xylose into furfural using only Brønsted acid (formic acid) catalyst. The protonated form of HCOOH (hydronium ions, H3O+) was responsible for this direct dehydration of xylose into furfural (see eqn (4)). This result was in agreement with the research work of Binder et al. (2010),20 who used hydrochloric acid as catalyst to directly convert xylose into furfural. In their work, the furfural yield of 54.2% and xylose conversion of 93.1% were obtained at the reaction temperature of 180 °C. However, the furfural yield exceeding 60% (see Fig. 4(b)) could not be reached by further increasing the reaction temperature due to the accelerated side reactions and the relatively long residence time. Similar results for this production pathway were observed in other research works.21
|
HCOOH (aq) + H2O ↔ HCOO− (aq) + H3O+ (aq)
| (4) |
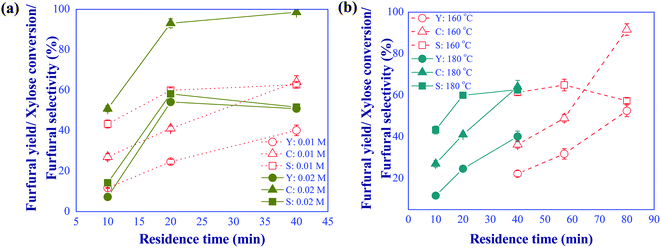 |
| Fig. 4 (a) Effects of formic acid concentration (conditions; xylose: 10 g L−1 and temp: 180 °C) and (b) reaction temperature (conditions; FA: 10 mM and xylose: 10 g L−1) on the furfural yield (Y)/selectivity (S) and xylose conversion (C) under various residence times. | |
The effect of operating conditions on the yield of furfural produced using formic acid as catalyst was subsequently investigated by varying the catalyst concentration (10 and 20 mM), the reaction temperature (160 and 180 °C), and the residence time (10 to 80 min). The xylose concentration of 10 g L−1 in the feed was kept constant for this study. Fig. 4(a) shows the effect of catalyst concentration on the furfural yield and selectivity and xylose conversion at the reaction temperature of 180 °C for different residence times. It was found that increasing the catalyst concentration from 10 to 20 mM promoted the furfural yield and xylose conversion; however, furfural selectivity decreased with prolonged residence time due to the formation of by-products. The solid powder (humin) was observed in the reaction product. The optimal furfural yield of 54.2% was obtained for the catalyst concentration of 20 mM and residence time of 20 min (58.2% of selectivity). Similar results were reported in the work of Delbecq et al. (2016)22 despite the application of biphasic system.
The effect of reaction temperature was further examined as shown in Fig. 4(b). In this experiment, the catalyst concentration and xylose feed concentration were kept constant at 10 mM and 10 g L−1, respectively. The findings indicated that reaction temperature was one of the main factors affecting the formation of side products. At 160 °C, the rates of xylose dehydration and side reactions were small and a prolonged residence time was required to enhance the conversion of xylose. Note that the conversion of xylose rapidly increased from 46% to 92% in response to the change of residence time from 58 to 80 min. However, a decline in the furfural selectivity was observed due to the promoted side reactions. The residence time required for the dehydration of xylose was significantly shortened when the reaction temperature was increased to 180 °C. Similar furfural selectivity was obtained at 160 °C with 60 min of residence time and 180 °C with 20 min of residence time. The latter was conceivably more productive, possibly resulting in lower production costs. To overcome the problem of direct conversion of xylose into furfural by using sole formic acid as Brønsted catalyst, the furfural production could be performed through the indirect xylose conversion route (two consecutive reaction steps) by using dual catalysts to possibly lower reaction temperature, shorten reaction time, and lower the catalyst concentration. Hence, another catalyst, aluminum chloride, as a Lewis acid was further studied in our system.
3.2 Role and effect of aluminum chloride on furfural yield
In this section, the conversion of xylose to furfural via the consecutive isomerization and dehydration using aluminum chloride as Lewis acid catalyst was investigated. The feed concentration of xylose was 10 g L−1 and the catalyst concentration was 5 mM. The effects of reaction temperature in a range of 120 to 180 °C and residence time in a range of 10 to 80 min were examined to study the role and effect of this catalyst on the furfural production. Results are shown in Fig. 5. Apparently, side reactions occurred especially at high reaction temperatures as indicated by the large difference between xylose conversion and the yield of furfural (see Fig. 5(a)). For example, a high xylose conversion of 94.5% was achieved at the reaction temperature of 180 °C and the residence time of 10 min, while only 39.8% of furfural yield was obtained at this reaction condition. Therefore, xylose and furfural could be converted into undesired products such as formaldehyde, oligosaccharides, intermediate compounds, and humins.23 Lowering the reaction temperature (<180 °C) caused the sharp decline in xylose conversion while preventing the side reactions. This result was in line with the research work of Yang et al. (2012).24 Compared to the direct dehydration of xylose to furfural using formic acid (with the concentration of 10 and 20 mM) as catalyst (see Fig. 4), a higher xylose conversion was observed for the lower concentration of aluminum chloride (5 mM), indicating that the xylose could be effectively converted into xylulose via isomerization. The isomerization of xylose was facilitated by the presence of aluminum complex ions (such as [Al(H2O)5OH]2+ and [Al(H2O)4(OH)2]+) from the dissolution of aluminum chloride in water (see eqn (5)–(12)).25 The main contribution of this reaction was associated with [Al(H2O)4(OH)2]+ ion.26 Note that, the positive aluminum ions occurred under the acidic solution (eqn (5)–(7)). Some furfural products could be obtained from the reaction system using this catalyst due to the occurrence of hydronium ions (see eqn (6) and (7)), which was able to convert xylulose into furfural. However, the small amount of hydronium ions (Brønsted acid) resulted in the small yield of furfural. |
AlCl3 (s) + 6H2O (l) → [Al(H2O)6]3+ (aq) + 3Cl− (aq)
| (5) |
|
[Al(H2O)6]3+ (aq) + H2O (l) ↔ [Al(H2O)5OH]2+ (aq) + H3O+ (aq)
| (6) |
|
[Al(H2O)5OH]2+ (aq) + H2O (l) ↔ [Al(H2O)4(OH)2]+ (aq) + H3O+ (aq)
| (7) |
|
[Al(H2O)4(OH)2]+ (aq) + H2O (l) ↔ [Al(H2O)3(OH)3] (s) + H3O+ (aq)
| (8) |
|
[Al(H2O)3(OH)3] (s) + H2O (l) ↔ [Al(H2O)2(OH)4]− (aq) + H3O+ (aq)
| (9) |
|
[Al(H2O)2(OH)4]− (aq) + H2O (l) ↔ [Al(H2O)(OH)5]2− (aq) + H3O+ (aq)
| (10) |
|
[Al(H2O)(OH)5]2− (aq) + H2O (l) ↔ [Al(OH)6]3− (aq) + H3O+ (aq)
| (11) |
|
[Al(OH)6]3− (aq) → AlO2− (aq) + 2OH (aq) + 2H2O (l)
| (12) |
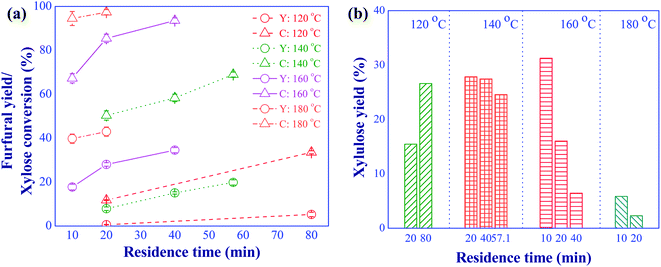 |
| Fig. 5 Effects of reaction temperature and residence time on the furfural yield (Y) and xylose conversion (a), xylulose yield (b); (conditions; AlCl3: 5 mM and xylose: 10 g L−1). | |
The yield of xylulose produced at various residence times and temperatures was analyzed as shown in Fig. 5(b). The presence of xylulose in the product confirmed that the role of aluminum chloride was to accelerate the isomerization of xylose (see Fig. 3). Note that, lyxose, another isomerization product of xylose, was not considered in this work due to the less kinetically favorable pathway compared to that of xylulose.27 The reaction temperature in the range of 140 to 160 °C provided a high xylulose yield with a short residence time (<40 min), indicating a suitable condition for the indirect pathway. The reaction temperature exceeding 160 °C resulted in a low xylulose yield due to further conversion of xylulose into furfural and humins. Although higher furfural yield was obtained at the reaction temperature of 180 °C (see Fig. 5(a)), large amount of humins was evidently observed compared to those obtained at lower reaction temperatures. A similar observation was reported in the research work of Padilla-Rascón et al. (2020),28 who used FeCl3 as catalyst for the conversion of xylose into furfural. In their work, only 57% furfural yield was obtained due to the formation of undesired products under the extreme reaction temperature of 210 °C, suggesting that the use of Lewis acid alone was not effective for the conversion of xylulose into furfural.27 Hence, the simultaneous use of Lewis and Brønsted acid catalysts was required to enhance the production of furfural from xylose via the indirect reaction pathway.
The effect of aluminum chloride concentration (5 to 20 mM) on the furfural yield was investigated under three different conditions including (1) high temperature with short residence time (180 °C and 10 min), (2) moderate temperature with moderate residence time (160 °C and 40 min) and (3) low temperature with long residence time (140 °C and 57.1 min), as shown in Fig. 6. We observed the positive effect of increasing the catalyst concentration on the yield of furfural at the reaction temperature of 140 °C. On the contrary, for the reaction temperature of 160 °C, significantly promoted the side reactions. Note that the effect of catalyst concentration was subdued when a short residence time was used at high reaction temperature. However, the furfural yield of greater than 40% could not be achieved in this system with only Lewis acid catalyst, confirming that the addition of Brønsted acid, as the second catalyst, was required to improve the conversion of xylulose into the furfural.
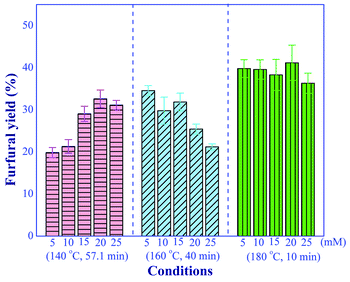 |
| Fig. 6 Effect of aluminum chloride concentrations on the furfural yield under the various operating conditions (conditions; xylose: 10 g L−1). | |
3.3 Furfural synthesis with dual catalysts
To demonstrate the furfural synthesis via the indirect pathway, a set of experiments were performed using dual-acid catalysts. The reaction temperature in a range of 140 to 180 °C, aluminum chloride-to-formic acid molar ratio of 1
:
1 (total of 10 mM), and residence time in a range of 10 to 80 min were applied. The results, as shown in Fig. 7(a), illustrate that the use of dual-acid catalysts offered a higher furfural yield than that of the individual catalyst at a reaction temperature of above 140 °C. For example, at the reaction temperature of 160 °C, residence time of 40 min, and 10 mM, a furfural yield of 47.1% was obtained using dual-acid catalysts, while the furfural yields of 26.9% and 22.3% were found for the individual uses of aluminum chloride and formic acid, respectively. Another example is shown in Fig. 7(b), when high temperature and short residence time (180 °C and 10 min) were applied for the synthesis of furfural, the use of dual-acid catalysts significantly improved furfural yield compared to those of sole catalysts, verifying the effective implementation of this synthesis route. Hence, the dual catalyst-based synthesis was used for further development in this work.
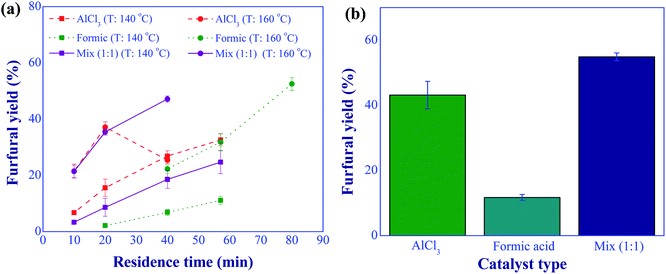 |
| Fig. 7 Furfural yield comparison between the uses of individual catalyst and dual catalysts; (a) at 140 and 160 °C with various residence times, (b) at 180 °C and 10 min (conditions; catalyst: 10 mM and xylose: 10 g L−1). | |
3.4 Effect of operating conditions on furfural yield
The effects of reaction temperature and residence time on the furfural yield and xylose conversion were preliminarily investigated when the dual-acid catalysts were applied at the molar ratio of 1
:
1 (total catalyst concentration of 10 mM). The results are shown in Fig. 8. It was found that increasing both reaction temperature and residence time considerably promoted the furfural yield and xylose conversion, indicating a significant effect of these operating parameters on the furfural production performance. According to the results shown in Fig. 8 and 9, the appropriate ranges of reaction temperature and residence time that can potentially provide high furfural yield and xylose conversion were 140 to 180 °C and 10 to 57.1 min, respectively. Moreover, the improvement of furfural yield and xylose conversion could be implemented by adjusting the operating conditions such as the total catalyst concentration, the xylose feed concentration, and the proportion of the two catalysts. Compared to the heterogeneous-based process,29,30 our process provided a significant improvement in terms of reaction time and temperature. For instance, in the work of Wang et al. (2021),30 the conversion of xylose performed at 200 °C and 45 min provided the furfural yield of 76.6%. Another concern with the use of these solid catalysts was catalyst stability.31 This leads to the difficulty for developing a practical large-scale production.
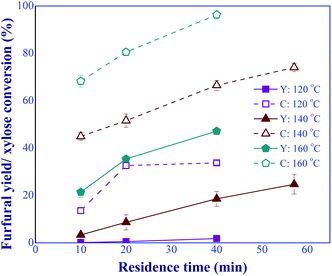 |
| Fig. 8 Effects of residence times and temperatures on the furfural yield (Y) and xylose conversion (C), synthesized under the dual-acid catalysts (condition: AlCl3-to-FA: 1 : 1, total catalyst: 10 mM). | |
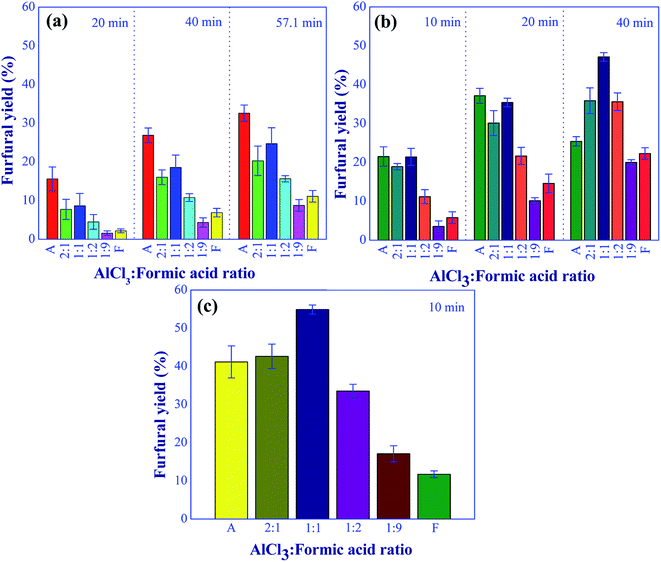 |
| Fig. 9 Effect of aluminum chloride to formic acid molar ratios on the furfural yield under the various residence times and temperatures; (a) at 140 °C, (b) 160 °C, and (c) 180 °C (condition: total catalyst: 10 mM). | |
Three operating parameters including the aluminum chloride to formic acid molar ratio, total catalyst concentration, and xylose concentration were further examined to determine the optimal operating conditions of furfural synthesis. The experiments were carried out with the residence time in a range of 10 to 57.1 min and reaction temperature in a range of 140 to 180 °C. The effect of aluminum chloride-to-formic acid molar ratio on furfural yield is shown in Fig. 9. The xylose concentration of 10 wt% in the feed stream and the total catalyst concentration of 0.01 M were kept constant for this study. At low reaction temperature (140 °C), the xylose conversion into furfural using aluminum chloride catalyst was more effective compared to the cases of formic acid and mixed catalysts as shown in Fig. 9(a). However, prolonged residence time (>40 min) was required to achieve a furfural yield of higher than 30%, which was lower than the yield obtained at reaction temperatures of 160 and 180 °C with shorter residence time. When the reaction temperature was increased to 160 °C and 180 °C as shown in Fig. 9(b) and (c), respectively, the dual catalysts with aluminum chloride-to-formic acid molar ratio of 2
:
1 and 1
:
1 significantly improved the furfural yield and also shortened residence time. This was due to the increase in the hydronium ions (Brønsted acid) as the aluminum chloride-to-formic acid molar ratio decreased, accelerating the conversion of xylulose into furfural. The negative effect of an increase in formic acid proportion on furfural yield was found at the catalyst molar ratio beyond 1
:
1 as the excess of Brønsted acid could lead to the formation of undesired products. In addition, the active components of aluminum ions ([Al(H2O)5OH]2+ and [Al(H2O)4(OH)2+) were decreased due to the equilibrium shifting to the left side (Al(H2O)5OH]3+), resulting in the slower rate of isomerization. Based on these results, the molar ratio of 1
:
1 provided the promising yield of furfural. Therefore, this molar ratio was used for further study in this work. In addition, the highest furfural yield of 54.8% was achieved in a very short reaction time of 10 min when the reaction was carried out at 180 °C with the aluminum chloride to the formic acid molar ratio of 1
:
1.
One of the primary goals of this work was to develop the efficient process for converting xylose to furfural using a relatively small amount of catalyst. Hence, the next operating variable studied was the total catalyst concentration. In this experiment, the total catalyst concentration in a range of 5 to 25 mM was studied, while the aluminum chloride-to-formic acid molar ratio of 1
:
1 and xylose concentration of 10 g L−1 were kept constant. The optimal residence time for each reaction temperature as previously reported for the effect of aluminum chloride-to-formic acid molar ratio was used in this study. Fig. 10 shows the effect of total catalyst concentration on the furfural yield. It was found that the maximum furfural yield was obtained with the catalyst concentration in the range of 15 and 25 mM, depending on the reaction temperature and residence time. At low reaction temperature, a relatively high concentration of catalyst was required to accelerate the reactions. The highest furfural yield of 57.8% was found when the total catalyst concentration of 15 mM was used at the reaction temperature of 180 °C and the residence time of 10 min. This result illustrated that using dilute acid catalyst was sufficient to achieve the high furfural yield when compared to other research works. For example, in the work of Lopes et al. (2017)9 who applied the combination of metal trichloride and formic acid for the batch synthesis of furfural (400 mM of AlCl3 and 55 wt% of formic acid), the mixed catalysts were required for their system to achieve the furfural yield around 62%. Although the reaction was performed at 130 °C, the high operating cost associated with the corrosion and degradation of equipment and waste treatment was a significant disadvantage. Marcotullio and Jong (2010)32 reported that 62% furfural yield was obtained with the use of 113 mM of FeCl3 and 50 mM of HCl catalysts at the reaction temperature of 200 °C. Therefore, our reduced catalyst concentration could be used to mitigate the problems of homogeneous-based industrial furfural production (corrosion and environmental issues), while still maintaining the high furfural product yield. This allows the development of economic and effective furfural production. Hence, the total catalyst concentration of 20 mM was selected for further investigation in our study.
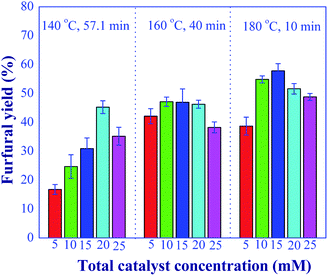 |
| Fig. 10 Effect of total catalyst amounts on the furfural yield under the various conditions; 140 °C and 57.1 min; 160 °C and 40 min; 180 °C and 10 min (condition AlCl3-to-FA: 1 : 1). | |
The effect of xylose feed concentration on the furfural yield was examined in a range of 1 to 20 g L−1. The reaction temperature of 180 °C, aluminum chloride-to-formic acid molar ratio of 1
:
1, and total catalyst concentration of 20 mM were kept constant for this study. Fig. 11 shows that the furfural yield continuously declined as the initial xylose concentration increased. This might be due to the polymerization and retro-aldol condensation reactions of xylose into humins and aldehyde-based compounds, respectively,33,34 resulting from the high concentration of xylose in the system. As shown by the embedded picture in Fig. 11, the solid humins and yellowish soluble by-products were observed in the product when the feed concentration of xylose exceeded 5 wt%. These side reaction(s) was also confirmed by the nearly complete conversion of xylose for the entire range of xylose inlet concentration studied. Note that, the prolonged residence time for furfural production under the high feed concentration (>5 wt%) may cause clogging inside the system. Hence, the initial feed concentration for the continuous-flow furfural production in a microreactor was limited by the formation of humins. The attractive furfural yield of 82.8% was achieved when the feed concentration of xylose was 1 g L−1, which was in agreement with the literature.8,35,36 For example, the furfural yield of around 76.3% was reported in the work of Choudhary et al. (2012),8 who used the initial xylose concentration of ∼1 wt% for the biphasic furfural production (water-toluene) with CrCl3 (6 mM) and HCl (100 mM). Another work was published by Agirrezabal-Telleria et al. (2011)35 who applied Amberlyst 70 as catalyst for the biphasic furfural production (water-toluene) from xylose. The initial concentration was studied in the range of 1 to 7 wt% and the maximum yield of 65% was achieved at the initial concentration of 1 wt% with the reaction time of 6 h at 175 °C. In addition, the conversion of lignocellulosic biomass by the flow-through hydrothermal pretreatment (HTP) technology provided the suitable xylose concentration of 0.4–1.4 g L−1 (ref. 37 and 38) as a desired product which could be further converted into furfural via our in situ continuous furfural production process. Therefore, the semi continuous-flow system for furfural production from lignocellulosic biomass could possibly be competitive with the conventional processes.
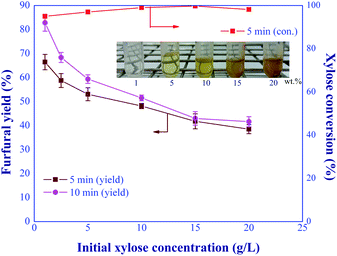 |
| Fig. 11 Effect of initial xylose concentrations on the furfural yield under the various residence times (condition: AlCl3-to-FA: 1 : 1, total catalyst: 20 mM, temp: 180 °C). | |
3.5 Optimization and validation
Based on the studies on five operating parameters discussed in Sections 3.3 and 3.4, the feed concentration of xylose of 1 g L−1 and the aluminum chloride-to-formic acid molar ratio of 1
:
1 were kept constant, while the three remaining operating parameters including, total catalyst concentration, residence time, and reaction temperature were the factors for the optimization to achieve high furfural yield. In this work, 3-factor and 3-level response surface methodology based (RSM) on Box–Behnken design was employed to maximize the furfural yield and the experimental boundaries are shown in Table 1. The relationship between process variables and furfural yield is represented by eqn (13). The P-value of 0.334 for the lack of fit indicated that the actual response was well-represented by the model. The coefficient of determination (R2) of 99.6% also confirmed the model accuracy. The model suggested that 93.1% furfural yield can be accomplished when synthesized at the reaction temperature of 180 °C, the residence time of 15 min, and the total catalyst concentration of 16 mM. This was experimentally validated and the furfural yield of 92.2% was obtained (error of 0.97%). To the best of our knowledge, this is the highest furfural yield achieved in the monophasic system (hydrothermal process) without any additives (such as salt39). The use of a very dilute acid catalyst and short residence time allowed the system to be further developed as the high-throughput production process. |
Furfural yield = −1020 + 6X1 + 15600X2 + 9X3 − 1.967 × 105X32 − 65X1X3 − 46X2X3
| (13) |
Table 1 Operating variables and boundaries for optimization study
Variables |
Symbol |
Levels |
Constrains |
−1 |
0 |
1 |
Independent variables |
Residence time (min) |
X1 |
5 |
10 |
15 |
In the range |
Total catalyst concentration (mM) |
X2 |
10 |
15 |
20 |
In the range |
Reaction temperature (°C) |
X3 |
160 |
170 |
180 |
In the range |
![[thin space (1/6-em)]](https://www.rsc.org/images/entities/char_2009.gif) |
Dependent variable |
Furfural yield (%) |
Y |
|
|
|
Maximize |
3.6 In situ acid catalyst removal process
The in situ acid catalyst removal of this proposed process was performed through the adsorption in a mini-fixed bed column where the commercial basic ion-exchange resin (Amberlyst 21) was packed. Note that, the weakly basic ion-exchange resin is a promising adsorbent for acid removal.40,41 The results found that no significant amount of acid components and unknown compound was detected at the product outlet as shown in Fig. 12, indicating the effective acid removal of this method. However, the trace of 5-HMF was still detected due to the low affinity of adsorption on the resin. The loss of furfural yield due to the acid removal process was not observed. These results indicate that our technique of catalyst removal was effective, while the operating conditions at ambient temperature (∼26 °C) and pressure (∼1 bar) suggested the low energy consumption. The output of this step could be purified using a simple distillation to achieve the high purity of furfural product (>99%) (see Section 3.7). Therefore, the in situ continuous furfural production from xylose and acid removal processes could be achieved through our technique. Note that, the economic feasibility of this process should be further studied for its practical application.
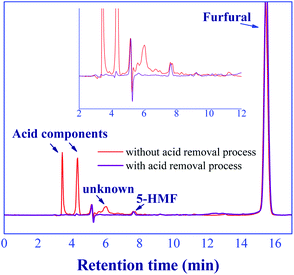 |
| Fig. 12 Chromatograms of product outlet between with/without acid catalyst removal process. | |
3.7 Furfural purification process
The conceptual design and simulation of furfural purification process with a production capacity of 10
000 kg h−1 were performed using Aspen plus V12 with Soave–Redlich–Kwong (SRK) thermodynamic model. The design of this process was based on the furfural composition obtained after the acid removal, containing 99.4 wt% of water and 0.6 wt% furfural. The process design and simulation data are presented in Fig. 13 and Table 2. In our design, one distillation tower (C-101) and one flash drum (V-101) were required for the purification to achieve the furfural purity up to 99%. The distillation tower was operated near azeotropic conditions (reboiler temperature of 101.2 °C, condenser temperature of 99.1 °C, 1 atm) to remove the large amount of water without the loss of furfural (stream 4.1). This stream was recycled without any pretreatment as a make-up water source for the production process. Note that, the azeotropic temperature of furfural-water mixture at 1 atm is 97.9 °C. The number of trays of this tower was 7, which was lower than the typical applications (20–30 stages).42 The remaining water in the distillate or furfural rich-phase (stream 3) was separated by the simple flash drum (V-101) at 144 °C and 1 atm. The water-rich stream (stream 5.1) was returned to the C-101, while the bottom stream (stream 6) containing 99% of furfural was sent to the storage tank. However, the optimization of the distillation process design and heat integration require further study to minimize the capital cost and energy consumption. For the conventional production of furfural, on the other hand, the complex downstream processing such as the combination of distillation and solvent extraction is essential.42,43 The energy performance of our purification process in terms of energy consumption per mass of furfural produced (kW kgfurfural−1) was 50.2 kW kgfurfural−1. This was similar to the work of Millán et al., (2021)44 (49.3 kW kgfurfural−1) who applied the combination of solvent extraction and distillation to obtain the furfural purity of 97.8%.
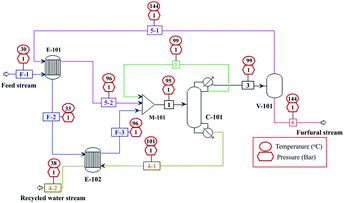 |
| Fig. 13 Conceptual design of furfural purification process (heat exchangers (E101–E102), flash drum (V-101), distillation tower (C-101), and mixer (M-101)). | |
Table 2 Purification process data
Information |
C-101 |
V-101 |
Number of stages |
7 |
— |
Feed stage number (above-stage) |
2 |
— |
Reflux ratio |
11 |
— |
Bottom to feed ratio (mass) |
0.965 |
— |
Total heating duty (kW) |
1519.1 |
37.88 |
Total cooling duty (kW) |
1455.1 |
— |
Mass flowrate of top product (kg h−1) |
237.6 |
177.0 |
- Furfural (wt%) |
90.1 |
87.0 |
- Water (wt%) |
9.9 |
12.9 |
Mass flowrate of bottom product (kg h−1) |
9939.5 |
60.5 |
- Furfural (wt%) |
0 |
99 |
- Water (wt%) |
100 |
1 |
3.8 Production performance
Our production process was compared to the other related processes as reported in Table 3. Various operating conditions, productivity term (P0), process and system type, and furfural yield were used to demonstrate our production performance. Apparently, the continuous microreactor process offers a superior furfural yield with the short residence time compared to that of the stirred batch and microwave-assisted batch processes. This was due to the main features of microreactors such as high surface-to-volume ratio and short diffusion length, which improve the mass and heat transfers of the reacting liquids. Note that, both mass and heat transfers are significant parameters affecting the overall reaction rate. Compared to the biphasic microreactor system, the phase separation/purification and solvent recycling are not required in our monophasic system, reducing the post-treatment cost. Another highlight of our process was the low concentration of catalyst compared to that of other homogeneous catalyst-based systems. This could contribute to a significant reduction in the cost of chemicals and separation process. The higher productivity of our process (52 gfurfural gcat−1 min−1) over batch processes was achieved due to the low requirement of both catalyst concentration and residence time. Hence, with the moderate operating conditions (180 °C and 15 min) and the high yield of furfural of 92.2%, the highly effective furfural production could be further developed based on our continuous monophasic synthesis in a microreactor. The yield and productivity of our process might be further improved via the little addition of the promoter.45
Table 3 Comparison of furfural process from xylose with literature
Process |
System |
Reactor |
Solvent |
Catalyst and promoter amount (mM) |
Temp (°C) |
Time (min) |
Yield/select. (%) |
P0a × 10−3 (gfurfural gcat−1 min−1) |
Reference |
Productivity = gfurfural gcatalyst−1 reaction time. |
Batch |
Monophasic |
Microwave-assisted batch |
Water |
Maleic acid (250 mM) |
200 |
28 |
67 |
0.8 |
46 |
Batch |
Monophasic |
Microwave-assisted batch |
Water |
HCl (50 mM) + NaCl (500 mM) |
200 |
40 |
62.5 |
0.04 |
47 |
Batch |
Monophasic |
Stirred batch |
Water |
Formic acid (2700 mM) + betaine (0.07 g) |
170 |
60 |
80 |
0.2 |
22 |
Batch |
Biphasic |
Stirred batch |
Water/THF |
AlCl3 (100 mM) + NaCl (6 mM) |
140 |
45 |
75 |
0.9 |
24 |
Batch |
Biphasic |
Stirred batch |
DMSO/H2O |
PWSn0.625Cs0.5PW (0.08 g) |
200 |
180 |
63 |
4.3 |
48 |
Batch |
Monophasic |
Stirred batch |
Water |
MC–SnOx (0.1 g) + NaCl (200 mM) |
180 |
20 |
53.9 |
0.02 |
49 |
Continuous |
Biphasic |
Millireactor |
Water/toluene |
H2SO4 (100 mM) |
190 |
6.6 |
62 |
NA |
17 |
Continuous |
Biphasic |
Microreactor |
Water/MIBK |
HCl (200 mM) + NaCl (10 wt%) |
180 |
4 |
93 |
NA |
16 |
Continuous |
Monophasic |
Microreactor |
Water |
Formic acid (8 mM) + AlCl3 (8 mM) |
180 |
15 |
92.2 |
52 |
This work |
4. Conclusion
High-performance continuous production of furfural from xylose was proposed with the use of a microreactor and dual-acid catalysts (formic acid and aluminum chloride). Indirect xylose conversion into furfural via xylulose was the main route of this proposed process, avoiding the side reactions that were significant for the conventional direct pathway. Formic acid was used as a Brønsted acid catalyst, while aluminum chloride was considered as Lewis acid catalyst. According to the optimization results, the furfural yield of 92.2% was achieved at the reaction temperature of 180 °C, residence time of 15 min, xylose feed concentration of 1 g L−1, and the total catalyst concentration (1
:
1 mol of formic/mol of aluminum chloride) of 16 mM, indicating superior reaction performance compared to the literature. The low catalyst requirement and short residence time of our monophasic system support the development of a high-throughput furfural production. The in situ catalyst removal process without the loss of furfural product could be completed via the continuous adsorption in a mini fixed-bed adsorber, offering the opportunity to reduce the separation cost and energy consumption. The furfural productivity of 52 gfurfural gcat−1 min−1 was obtained. The purity of furfural of 99% could be achieved via the simple purification process, comprising distillation and flash drum units.
Author contributions
Nattee Akkarawatkhoosith: conceptualization, methodology, investigation, formal analysis, validation, funding acquisition, writing – original draft, writing – review & editing. Tiprawee Tongtummachat: investigation, methodology, resources, formal analysis, writing – original draft. Attasak Jaree: resources, supervision, writing – review & editing.
Conflicts of interest
The authors have no competing interests to declare that are relevant to the content of this article.
Acknowledgements
This research project is supported by Mahidol University (Basic Research fund: fiscal year 2021).
References
- R. Mariscal López, P. Maireles-Torres, M. Ojeda, I. Sadaba and M. López Granados, Furfural: a renewable and versatile platform molecule for the synthesis of chemicals and fuels, Energy Environ. Sci., 2016, 9, 1144–1189 RSC.
- A. Chatzidimitriou and J. Q. Bond, Oxidation of levulinic acid for the production of maleic anhydride: breathing new life into biochemicals, Green Chem., 2015, 17, 4367–4376 RSC.
- S. H. Krishna, K. Huang, K. J. Barnett, J. He, C. T. Maravelias, J. A. Dumesic and G. W. Huber, Oxygenated Commodity Chemicals from Chemo-Catalytic Conversion of Biomass Derived Heterocycles, AIChE J., 2018, 64, 1910–1922 CrossRef CAS.
- J. S. Luterbacher, D. M. Alonso and J. A. Dumesic, Targeted chemical upgrading of lignocellulosic biomass to platform molecules, Green Chem., 2014, 16, 4816–4838 RSC.
- J. B. Binder, J. J. Blank, A. V. Cefali and R. T. Raines, Synthesis of Furfural from Xylose and Xylan, ChemSusChem, 2010, 3, 1268–1272 CrossRef CAS PubMed.
- R. K. Mishra, V. B. Kumar, A. Victor, I. N. Pulidindi and A. Gedanken, Selective production of furfural from the dehydration of xylose using Zn doped CuO catalyst, Ultrason. Sonochem., 2019, 56, 55–62 CrossRef CAS PubMed.
- R. S. D. Carvalho, F. D. A. Rodrigues, R. S. Monteiro and W. L. D. S. Faria, Optimization of Furfural Synthesis from Xylose Using Niobic Acid and Niobium Phosphate as Catalysts, Waste Biomass Valorization, 2019, 10, 2673–2680 CrossRef.
- V. Choudhary, S. L. Sandler and D. G. Vlachos, Conversion of Xylose to Furfural Using Lewis and Brønsted Acid Catalysts in Aqueous Media, ACS Catal., 2012, 2, 2022–2028 CrossRef CAS.
- M. Lopes, K. Dussan and J. J. Leahy, Enhancing the conversion of D-xylose into furfural at low temperatures using chloride salts as co-catalysts: Catalytic combination of AlCl3 and formic acid, Chem. Eng. J., 2017, 323, 278–286 CrossRef CAS.
- C. Rong, X. Ding, Y. Zhu, Y. Li, L. Wang, Y. Qu, X. Ma and Z. Wang, Production of furfural from xylose at atmospheric pressure by dilute sulfuric acid and inorganic salts, Carbohydr. Res., 2012, 350, 77–80 CrossRef CAS PubMed.
- Q. Zhang, C. Wang, J. Mao, S. Ramaswamy, X. Zhang and F. Xu, Insights on the efficiency of bifunctional solid organocatalysts in converting xylose and biomass into furfural in a GVL-water solvent, Ind. Crops Prod., 2019, 138, 111454 CrossRef CAS.
- J. Slak, B. Pomeroy, A. Kostyniuk, M. Grilc and B. Likozar, A review of bio-refining process intensification in catalytic conversion reactions, separations and purifications of hydroxymethylfurfural (HMF) and furfural, Chem. Eng. J., 2022, 429, 132325 CrossRef CAS.
- T. M. Kohl, B. Bizet, P. Kevan, C. Sellwood, J. Tsanaktsidis and C. H. Hornung, Efficient synthesis of 5-(chloromethyl)furfural (CMF) from high fructose corn syrup (HFCS) using continuous flow processing, React. Chem. Eng., 2017, 2, 541–549 RSC.
- T. Shimanouchi, Y. Kataoka, T. Tanifuji, Y. Kimura, S. Fujioka and K. Terasaka, Chemical conversion and liquid-liquid extraction of 5-hydroxymethylfurfural from fructose by slug flow microreactor, AIChE J., 2016, 62, 2135–2143 CrossRef CAS.
- T. Tongtummachat, N. Akkarawatkhoosith, A. Kaewchada and A. Jaree, Conversion of glucose to 5-hydroxymethylfurfural in a microreactor, Front. Chem., 2020, 7, 951 CrossRef PubMed.
- W. Guo, H. C. Bruining, H. J. Heeres and J. Yue, Efficient synthesis of furfural from xylose over HCl catalyst in slug flow microreactors promoted by NaCl addition, AIChE J., 2022, 68, 17606 Search PubMed.
- M. Papaioannou, R. J. T. Kleijwegt, J. van der Schaaf and M. F. Neira d'Angelo, Furfural Production by Continuous Reactive Extraction in a Millireactor under the Taylor Flow Regime, Ind. Eng. Chem. Res., 2019, 58(35), 16106–16115 CrossRef CAS.
- L. C. Nhien, N. V. D. Long, S. Kim and M. Lee, Techno-economic assessment of hybrid extraction and distillation processes for furfural production from lignocellulosic biomass, Biotechnol. Biofuels, 2017, 10, 81 CrossRef PubMed.
- O. Ershova, J. Kanervo, S. Hellsten and H. Sixta, The role of xylulose as an intermediate in xylose conversion to furfural: insights via experiments and kinetic modelling, RSC Adv., 2015, 5, 66727–66737 RSC.
- J. B. Binder, J. J. Blank, A. V. Cefali and R. T. Raines, Synthesis of Furfural from Xylose and Xylan, ChemSusChem, 2010, 3, 1268–1272 CrossRef CAS PubMed.
- J. Köchermann, J. Schreiber and M. Klemm, Conversion of D-Xylose and Hemicellulose in Water/Ethanol Mixtures, ACS Sustainable Chem. Eng., 2019, 7, 12323–12330 Search PubMed.
- F. Delbecq, Y. Wang and C. Len, Conversion of xylose, xylan and rice husk into furfural via betaine and formic acid mixture as novel homogeneous catalyst in biphasic system by microwave-assisted dehydration, J. Mol. Catal. A: Chem., 2016, 423, 520–525 CrossRef CAS.
- C. Rong, X. Ding, Y. Zhu, Y. Li, L. Wang, Y. Qu, X. Ma and Z. Wang, Production of furfural from xylose at atmospheric pressure by dilute sulfuric acid and inorganic salts, Carbohydr. Res., 2012, 350, 77–80 CrossRef CAS PubMed.
- Y. Yang, C. W. Hu and M. M. Abu-Omar, Synthesis of furfural from xylose, xylan, and biomass using AlCl3-6H2O in biphasic media via xylose isomerization to xylulose, ChemSusChem, 2012, 5, 405–410 CrossRef CAS PubMed.
- W. Wang, J. Ren, H. Li, A. Deng and R. Sun, Direct transformation of xylan-type hemicelluloses to furfural via SnCl4 catalysts in aqueous and biphasic systems, Bioresour. Technol., 2015, 183, 188–194 CrossRef CAS PubMed.
- J. Tang, L. Zhu, X. Fu, J. Dai, X. Guo and C. Hu, Insights into the Kinetics and Reaction Network of Aluminum Chloride-Catalyzed Conversion of Glucose in NaCl-H2O/THF Biphasic System, ACS Catal., 2017, 7, 256–266 CrossRef CAS.
- V. Choudhary, S. Caratzoulas and D. G. Vlachos, Insights into the isomerization of xylose to xylulose and lyxose by a Lewis acid catalyst, Carbohydr. Res., 2013, 368, 89–95 CrossRef CAS PubMed.
- C. Padilla-Rascón, J. M. Romero-García, E. Ruiz and E. Castro, Optimization with Response Surface Methodology of Microwave-Assisted Conversion of Xylose to Furfural, Molecules, 2020, 25, 3574 CrossRef PubMed.
- L. Ye, Y. Han, X. Wang, X. Lu, X. Qi and H. Yu, Recent progress in furfural production from hemicellulose and its derivatives: Conversion mechanism, catalytic system, solvent selection, Mol. Catal., 2021, 515, 111899 CrossRef CAS.
- X. Wang, M. Qiu, Y. Tang, J. Yang, F. Shen, X. Qi and Y. Yu, Synthesis of sulfonated lignin-derived ordered mesoporous carbon for catalytic production of furfural from xylose, Int. J. Biol. Macromol., 2021, 187, 232–239 CrossRef CAS PubMed.
- V. Krzelj, D. P. Ferrandez and M. F. N. D'Angelo, Sulfonated foam catalysts for the continuous dehydration of xylose to furfural in biphasic media, Catal. Today, 2021, 365, 274–281 CrossRef CAS.
- G. Marcotullio and W. D. Jong, Chloride ions enhance furfural formation from d-xylose in dilute aqueous acidic solutions, Green Chem., 2010, 12, 1739–1746 RSC.
- G. G. Millán, Z. E. Assal, K. Nieminen, S. Hellsten, J. Llorca and H. Sixta, Fast furfural formation from xylose using solid acid catalysts assisted by a microwave reactor, Fuel Process. Technol., 2018, 182, 56–67 CrossRef.
- T. M. Aida, N. Shiraishi, M. Kubo, M. Watanabe and R. L. Smith, Reaction kinetics of d-xylose in sub- and supercritical water, J. Supercrit. Fluids, 2010, 55, 208–216 CrossRef CAS.
- I. Agirrezabal-Telleria, A. Larreategui, J. Requies, M. B. Güemez and P. L. Arias, Furfural production from xylose using sulfonic ion-exchange resins (Amberlyst) and simultaneous stripping with nitrogen, Bioresour. Technol., 2011, 102, 7478–7485 CrossRef CAS PubMed.
- E. I. Gürbüz, S. G. Wettstein and J. A. Dumesic, Conversion of hemicellulose to furfural and levulinic acid using biphasic reactors with alkylphenol solvents, ChemSusChem, 2012, 5, 383–387 CrossRef PubMed.
- G. Gallina, E. R. Alfageme, P. Biasi and J. García-Serna, Hydrothermal extraction of hemicellulose from lab to pilot scale, Bioresour. Technol., 2018, 247, 980–991 CrossRef CAS PubMed.
- X. Meng, C. G. Yoo, Y. Pu and A. J. Ragauskas, Opportunities and challenges for flow-through hydrothermal pretreatment in advanced biorefineries, Bioresour. Technol., 2022, 343, 126061 CrossRef CAS PubMed.
- A. Rusanen, R. Kupila, K. Lappalainen, J. Kärkkäinen, T. Hu and U. Lassi, Conversion of xylose to furfural over lignin-based activated carbon-supported iron catalysts, Catalysts, 2020, 10(8), 821 CrossRef CAS.
- H. Uslu, Adsorption equilibria of formic acid by weakly basic adsorbent Amberlite IRA-67: Equilibrium, kinetics, thermodynamic, Chem. Eng. J., 2009, 155, 320–325 CrossRef CAS.
- V. M. Bhandari, T. Yonemoto and V. A. Juvekar, Investigating the differences in acid separation behaviour on weak base ion exchange resins, Chem. Eng. Sci., 2000, 55, 6197–6208 CrossRef CAS.
- L. C. Nhien, N. V. D. Long and M. Lee, Novel Hybrid Reactive Distillation with Extraction and Distillation Processes for Furfural Production from an Actual Xylose Solution, Energies, 2021, 14, 1152 CrossRef CAS.
- G. Contreras-Zarazúa, M. Martin-Martin, E. Sánchez-Ramirez and J. G. Segovia-Hernández, Furfural Production from Agricultural Residues Using Different Intensified Separation and Pretreatment Alternatives. Economic and Environmental Assessment, Chem. Eng. Process., 2021, 171, 108569 CrossRef.
- G. Gómez Millán, R. P. Bangalore Ashok and P. Oinas, et al., Furfural production from xylose and birch hydrolysate liquor in a biphasic system and techno-economic analysis, Biomass Convers. Biorefin., 2021, 11, 2095–2106 CrossRef.
- Z. Li, Y. Luo, Z. Jiang, Q. Fang and C. Hu, The promotion effect of NaCl on the conversion of xylose to furfural, Chin. J. Chem., 2019, 38, 178–184 CrossRef.
- E. S. Kim, S. Liu, M. M. Abu-Omar and N. S. Mosier, Selective Conversion of Biomass Hemicellulose to Furfural Using Maleic Acid with Microwave Heating, Energy Fuels, 2012, 26, 1298–1304 CrossRef CAS.
- C. Xiouras, N. Radacsi, G. Sturm and G. D. Stefanidis, Furfural Synthesis from d-Xylose in the Presence of Sodium Chloride: Microwave versus Conventional Heating, ChemSusChem, 2016, 9, 2159–2166 CrossRef CAS PubMed.
- X. Guo, F. Guo, Y. Li, Z. Zheng, Z. Xing, Z. Zhu, T. Liu, X. Zhang and Y. Jin, Dehydration of D-xylose into furfural over bimetallic salts of heteropolyacid in DMSO/H2O mixture, Appl. Catal., A, 2018, 558, 18–25 CrossRef CAS.
- N. Zhou, C. Zhang, Y. Cao, J. Zhan, J. Fan, J. H. Clark and S. Zhang, Conversion of xylose into furfural over MC-SnOx and NaCl catalysts in a biphasic system, J. Cleaner Prod., 2021, 311, 127780 CrossRef CAS.
|
This journal is © The Royal Society of Chemistry 2022 |
Click here to see how this site uses Cookies. View our privacy policy here.