DOI:
10.1039/D2RA06390E
(Paper)
RSC Adv., 2022,
12, 36018-36027
Fatty acid wax from epoxidation and hydrolysis treatments of waste cooking oil: synthesis and properties†
Received
11th October 2022
, Accepted 9th December 2022
First published on 15th December 2022
Abstract
To provide low-cost wax and a new methodology for utilizing waste cooking oil (WCO), fatty acid wax based on WCO was synthesized by using epoxidation and hydrolysis treatments, whose properties included melting point, color, hardness, combustion properties, aldehyde content, and microscopic morphology were tested and analyzed. The obtained WCO-based wax contained mixed fatty acids, including palmitic acid and 9,10-dihydroxystearic acid as main constituents, which could form a 3D stable crossing network constructed by large long-rod crystals. The WCO-based wax with high fatty acid content (96.41 wt%) has a high melting point (44–53 °C), light color (Lovibond color code Y = 11.9, R = 2.3), good hardness (needle penetration index = 2.66 mm), long candle burning time (293 min), and low aldehyde content (7.98 × 10−2 μg g−1), which could be a lower-cost alternative of commercial soybean wax (SW) for producing various wax products including candles, crayons, waxworks, etc.
1. Introduction
Waste cooking oil (WCO) is an inedible waste resource that can pollute the environment, cause serious harm to human health, and affect the quality of our lives. Therefore, the reclaim and reuse of WCO can effectively address the scarcity of petroleum resources, reduce environmental pollution, and safeguard public health.1–3 Although there are numerous ways to repurpose WCO and it can produce a variety of products like biofuels (biodiesel,4–7 bioethanol8–10 and biogas11,12), biolubricants,13–15 biosurfactants,16–18 asphalt modifier,19–22 washing product,23,24 etc., traditional products based on WCO often exhibit quite a low-profit margin (often <20%) and necessitate large-scale production lines and significant investments. For instance, to produce biodiesel from WCO, first a stable and optimal supply chain of raw materials must be established, requiring strong policy and financial support.25,26 Second, as not all WCOs are suitable for biodiesel production, complex pre-treatment steps for WCOs are required, thus increasing the cost.27 Third, cost-prohibitive catalysts are also requisite for large-scale biodiesel production.28–32 Therefore, the traditional utilisation strategy for WCO (such as the production of biodiesel) is only suitable for economically developed areas.33,34 In the regions where the oil source and economy are scarce, a simple, convenient, and inexpensive method that could produce WCO-based material with high technology and added value may be a better choice.
On the other hand, plant wax materials, such as soybean wax (SW), can be used to create essential oil candles, crayons, wax figures, lubricating wax, or protective wax, which are thought of as renewable and biodegradable substitutes for paraffin wax with a wide range of market potential.35–38 Plant wax material has a smaller market share than biodiesel, but it also has a better profit margin (typically >50%), fewer equipment requirements, and more flexible production management. Consequently, the conversion of WCO to wax may be one of the most beneficial approaches to recycling WCO. The majority of plant waxes used in commerce today are hydrogenation products of plant oil, whose hydrogenation process usually requires relatively high temperatures (>300 °C), high H2 pressure (>1 MPa), expensive catalysts, and safety facilities.39–43 Thus, the hydrogenation technique may increase production and investment costs and is inappropriate for WCO-based wax manufacturing with a modest market size.
The epoxidation reaction can also be used for WCO modification. By comparison with hydrogenation, epoxidation can be carried out under more gentle reaction conditions with lower synthetic costs.44–46 For example, Paul et al. reported the epoxidation of WCO using an epoxidation reagent composed of hydrogen peroxide (H2O2), glacial acetic acid, and sulfuric acid, with a reaction temperature of 60 °C and a reaction time of 6 h, which could afford epoxy waste cooking oil (E-WCO) as a lubricant. Thus, it could be expected that the epoxidation reaction is more suitable for the WCO-to-wax conversion technique.46 We recently reported the first low-cost WCO-based wax using an “epoxidation & combination” strategy.44 In this method, WCO was first epoxidized to create E-WCO, and then mixed with stearic acid (SA) to create a wax material that is both cost-effective and capable of replacing commercial SW. The epoxidation reaction might result in E-WCO, which would be harder, lighter in color, and have a higher melting point than the original WCO. The E-WCO, however, had a lower melting point and a weaker hardness than commercial SW due to the very small grains in its solid, and its candle was soft and had a brief combustion duration throughout the combustion process. To solve this problem, SA, a kind of rod-like molecule, could form large long-rod crystals and hence could be introduced to further modify the WCO-based wax. The large long-rod crystals of SA could form a stable 3D crossing network, which effectively solves the constraints associated with E-WCO grain size. This inhances the melting point and hardness of the WCO-based wax and increases the combustion time of the candle during the combustion process. However, this type of WCO-based wax should include more than 50% SA to achieve practical performance, which is bad for further cost-cutting.
From our previous work, it was observed that, compared with the branching triglyceride of WCO, the rod-shaped fatty acid molecule was more suitable to construct high-performance plant wax. Therefore, the conversion of E-WCO molecules to fatty acids is probably a feasible strategy to produce a less expensive WCO-based wax without utilising SA. It is well known that, by hydrolyzing with a strong base47–50 or enzyme,51,52 WCO can be easily saponified to produce mixed fatty acids (or their salts) and glycerol. Based on the above analysis, we used a novel “epoxidation & hydrolysis” technique to design and synthesise a type of fatty acid wax based on WCO for the first time. In this method, WCO is first epoxidized to create E-WCO before being hydrolyzed with sodium hydroxide (NaOH) to create mixed fatty acids, which may be used as an inexpensive wax material to take the place of commercial SW (see Fig. 1). The produced WCO-based wax's melting point, color, hardness, combustion performance, aldehyde content, and microscopic morphology were also investigated and reported in this paper.
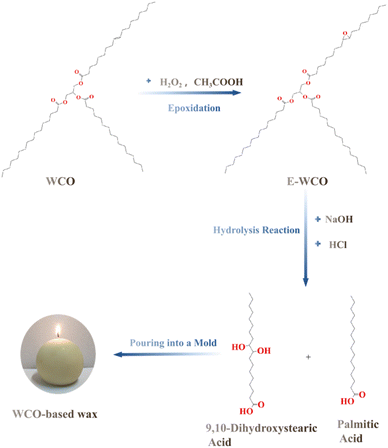 |
| Fig. 1 Schematic diagram of the synthesis of fatty acid wax based on WCO. | |
2. Experimental
2.1 Materials
The WCO (iodine value: 33.04) was collected from Obligi Chicken fast food restaurant in Guilin, China. The sodium hydroxide (NaOH), hydrogen peroxide (analytical grade, 30 wt% in H2O), and sulfuric acid (analytical grade) were purchased from Xiya Chemical Technology Co., Ltd. (Shandong, China). The SA (98% purity), glacial acetic acid (99.5% purity), urea (99% purity), and sodium bicarbonate (99.5% purity) was purchased from the McLean Company (Shanghai, China). The commercial SW was purchased from Xu's Wax Co., Ltd. (Hebei, China).
2.2 Synthesis of wax based on WCO
According to our previous research, the WCO was first epoxidized to produce E-WCO.44 In a typical synthesis, 620 g of 30% H2O2, 160 g of glacial acetic acid, 4 g of concentrated sulfuric acid, and 4 g of urea were mixed in a lightproof container and placed in an oven at 40 °C for 12 h to prepare peracetic acid as the epoxidation reagent. Then, 1000 g of WCO was placed in a glass-stirred reactor and heated at 40 °C, and the initially prepared epoxidation reagent was slowly added to the reactor within 2 h. The reaction mixture was then heated to 70 °C and stirred continuously for a further 3 h, to ensure the C
C double bonds in the triglycerides of WCO were fully transformed into epoxy groups. Furthermore, because peracetic acid is a strong oxidant, it could cause peroxidative degradation of various colored and odorous organic impurities in WCO, removing the rancid odor and improving its color. After the reaction was completed, the reaction mixture was allowed to stand for 12 h for stratification. The upper oil layer was collected, washed once with 5% NaHCO3 solution and twice with deionized water at 60 °C, and then evaporated under vacuum for 2 h at 70 °C. After cooling, E-WCO was obtained as a kind of odorless light yellow solid with an epoxy value of 1.04 and a saponification degree of 0.1336 g NaOH g−1.
The resulting E-WCO was then hydrolysised in the presence of NaOH. In this process, an appropriate amount of NaOH was dissolved in 30 ml of distilled water to obtain a NaOH solution. Under magnetic stirring, the resulting NaOH solution was added to the E-WCO drop by drop. After the dropwise of NaOH solution, 62 g of 30% H2O2 was added to the mixture, for the addition of H2O2 to E-WCO could further lighten the color of the WCO-based wax in the hydrolysis process. The effects of the NaOH dosage, reaction temperature, and reaction time on the free fatty acid content of the WCO-based wax were given in Tables 1 and S1 in ESI.† In the optimised hydrolysis condition, the reaction mixture was heated and hydrolyzed using two times the theoretical amount of NaOH at 70 °C for 4 h with magnetic stirring, which could afford a high free fatty acid content of 96.41 wt% (A6 sample). To further explore the effects of the NaOH dosage and fatty acid content on the properties of the wax, a series of WCO-based wax samples with different free fatty acid contents were synthesised (see Table 1) and the NaOH dosage was set as follows:
|
mNaOH = A × Sv × mE-WCO
| (1) |
Herein,
mNaOH: NaOH dosage (g),
Sv: saponification value of E-WCO (0.1336 g NaOH g
−1),
mE-WCO: E-WCO dosage (100 g for each sample),
A: multiple theoretical NaOH dosage, which was set as 0.75, 1 (theoretical amount of NaOH), 1.25, 1.5, 1.75, and 2 for A1 to A6 samples, respectively.
Table 1 Synthesis recipe of fatty acid wax based on WCO. The dosage of E-WCO was 100 g for each sample. The hydrolysis temperature and time were 70 °C and 4 h respectively
Sample |
Dosage of NaOH (g) |
Multiple theoretical amounts of NaOH |
Free fatty acid content (wt%) |
A1 |
10.02 |
0.75 |
35.37 |
A2 |
13.36 |
1 |
50.65 |
A3 |
16.70 |
1.25 |
62.37 |
A4 |
20.04 |
1.5 |
78.08 |
A5 |
23.38 |
1.75 |
85.29 |
A6 |
26.72 |
2 |
96.41 |
Finally, 10% hydrochloric acid (HCl) was added to neutralise residual alkali which adjusted the pH of the mixture to 6. After stirring for 5 min, the processed mixture was allowed to separate into layers at 70 °C. The upper organic phase was separated and vacuum evaporated at 70 °C to remove residual water. The resulting light yellow melted wax could then be poured directly into a mould to take shape. Products made from WCO-based wax, such as waxworks (see Fig. 2a), candles (see Fig. 2b), or crayons (see Fig. 2c), were obtained after cooling and demolding.
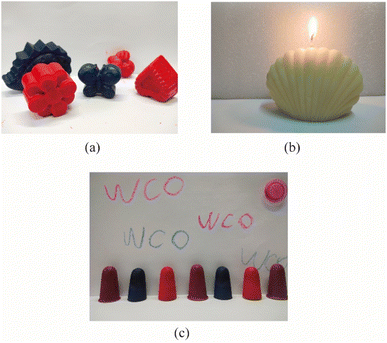 |
| Fig. 2 Photos of waxworks (a), shell candles (b), and crayons (c) produced by WCO-based wax (A6 sample). The various colors (red, blue, or brownish red) of the waxworks (a) and crayons (c) were caused by additional organic dyes with a dosage of 0.5 wt% in the wax. | |
2.3 Characterization
The determination of the iodine value of WCO was carried out by the China Standard GB/T 5532-2008. The epoxy value and saponification value of E-WCO were tested following the China Standard GB/T 1677-2008 and GB/T 5534-2008, respectively. The aldehyde content of the samples was determined according to GB/T 14571.3-2008. The contents of various fatty acids in the WCO-based wax were measured following the China Standards GB/T 5009.168-2016 (to prepare the methyl esters), using an Agilent 7890-5979 gas chromatography-mass (GC-MS) spectrometer (Agilent, Santa Clara, USA). A brief introduction of China standards concerned in this paper was given in Table S2 in ESI.†
The 1H NMR spectra were recorded on a Bruker Avance DRX-400 spectrometer (Bruker, Karlsruhe, Germany). The IR spectra were captured using KBr pellets and a Nicolet 5700 FT-IR spectrometer (Thermofisher, Waltham, USA) with a spectral resolution of 4.00 cm−1 over the range of 400–4000 cm−1. The melting point of the wax was tested by an X-5 microscope melting point detector (Yuhua Instrument, Gongyi, China). The Lovibond color of the waxes was tested by a LABO-HUB WSL-2 Lovibond tintometer (Xinrui Instrument, Shanghai, China). The needle penetration index of the wax product was recorded by an FY-2801 C penetrometer (Fengjian Instrument, Cangzhou, China) at 25 °C. The micro-morphology image of the wax was recorded on a Scope A1 microscope (Zeiss, Oberkochen, Germany) with transmission mode. The powder X-ray diffraction (PXRD) pattern of the wax was obtained with an X'Pert PRD diffractometer with Cu Kα radiation (λ = 1.54056 Å) at 40 kV and 40 mA at a scan speed of 4° min−1 (2 Theta).
The combustion performance of the wax was carried out using a cube candle (size: 5 cm × 5 cm × 5 cm). For numerous parallel tests, such candles were repeatedly made. Without lateral support, the candle was lit in a breezeless, open environment. The candle's burning period was measured from ignition to burnout, which was at 5 cm. Every combustion time listed in this study is the average of four samples with identical compositions.
3. Results and discussion
3.1 Structure characterization
The 1H NMR spectra of the WCO, E-WCO and WCO-based wax (A6 sample) are given in Fig. 3a and S1–S3 in ESI.† 1H NMR signals of WCO displayed unsaturated double bonds of triglyceride with chemical shifts of δ 5.2–5.3 ppm. These signal peaks weakened significantly in E-WCO after the epoxidation reaction. In contrast, the signals of the epoxy group could be observed (at δ 2.8–3.2 ppm), demonstrating the successful epoxidation of the triglycerides of WCO. After hydrolysis, the epoxy group signals in E-WCO at δ 2.8–3.2 ppm nearly completely vanished, while doublet signals at around 3.4 ppm and 3.6 ppm were observed, which could be due to the methine (C–H) protons in the dihydroxy group with erythro and threo model, respectively.53–55 It was suggested that the epoxy group in E-WCO was almost consumed during the hydrolysis and formed a dihydroxy group.
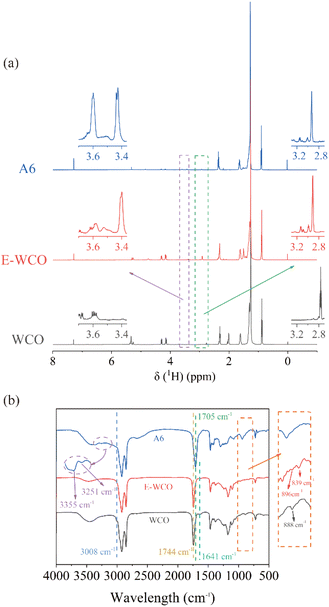 |
| Fig. 3 The 1H NMR spectra (a) and IR spectra (b) of the WCO, E-WCO, and A6 samples. | |
The epoxidation & hydrolysis processes were also proven by IR spectra (Fig. 3b). After epoxidation, the characteristic peaks related to C
C double bonds almost disappeared, including the stretching vibration of the C–H bond in the C
CH unit (located at 3008 cm−1), the stretching vibration of the C
C double bond (located at 1641 cm−1), as well as the bending vibrations of C–H bond in –CH= unit (located at 888 cm−1). Meanwhile, the epoxy absorption peaks located at 896 cm−1 and 839 cm−1 were observed, which indicated the formation of E-WCO. The stretching vibration of the C
O bond in the ester group of E-WCO at 1744 cm−1 disappeared after hydrolysis, while the C
O stretching vibration of carboxylic acid appeared at 1705 cm−1, indicating that the E-WCO molecule was successfully hydrolyzed to fatty acids. In the meantime, the absorption peak of the epoxy group in E-WCO disappeared, while the characteristic peaks of the hydroxyl group appeared at 3355 cm−1 and 3251 cm−1, indicating that the epoxy group in E-WCO was consumed to generate the dihydroxy group.55,56
Additionally, the contents of various fatty acids in the WCO-based wax (A6 sample) were measured by GC-MS and given in Table 2. It was observed that palmitic acid showed the highest amount in the wax, with a mass fraction of 47.71 wt%, followed by 9,10-dihydroxystearic acid (38.42 wt%). Thus, the obtained WCO-based wax contained mixed fatty acids, mainly including palmitic acid and 9,10-dihydroxystearic acid, which originate from the palmitate and oleate moieties in the triglycerides of WCO, respectively.
Table 2 The contents of various fatty acids of the WCO-based wax (A6 sample)
Fatty acid composition |
Molecular formula |
Content (wt%) |
Palmitic acid |
C16H32O2 |
47.71 |
9,10-Dihydroxystearic acid |
C18H36O4 |
38.42 |
Stearic acid |
C18H36O2 |
5.38 |
9,10,12,13-Tetrahydroxystearic acid |
C18H36O6 |
2.53 |
Myristic acid |
C14H28O2 |
1.19 |
Arachidic acid |
C20H40O2 |
0.41 |
Lauric acid |
C12H24O2 |
0.38 |
Decanoic acid |
C10H20O2 |
0.31 |
3.2 Melting point
As shown in Fig. 4 and Table S3 in ESI,† the WCO used as raw material displayed a low melting point ranging from 33–36 °C, which makes it difficult to maintain its shape at room temperature and could be used to produce wax products directly. Compared to WCO, the E-WCO exhibited a higher melting point range (36–40 °C). Its shape is stable and can be maintained at room temperature, which makes it ideal to produce wax products. The E-WCO, however, had a lower melting point than commercial SW. The E-WCO was transformed into mixed fatty acids after hydrolysis, which significantly raised the sample's melting point. With the increase in NaOH dosage, the fatty acid content of the samples increased, and the melting point of the wax sample also presented an upward trend. The WCO-based wax (A6 sample), which had a high fatty acid content of 96.41%, had a melting point ranging from 44–53 °C, which was higher than that of SA-modified WCO-base wax previously reported (the composite of E-WCO and SA with equal mass ratio, 46–49 °C),44 but slightly lower than that of commercial SW (51–54 °C).
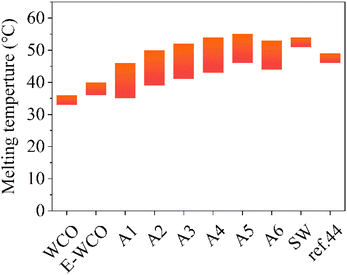 |
| Fig. 4 The melting points of WCO-based waxes and other control samples. The symbol of ref. 44 represents a kind of SA-modified WCO-base wax in our previous work44 which was the composite of E-WCO and SA with an equal mass ratio. | |
3.3 Color
To prepare highly artistic essential oil candles or wax figures, a commercializable plant wax requires light color to facilitate subsequent coloring and other processing. According to China Standard GB/T 30392-2013, the Lovibond color codes of plant wax materials are mainly reflected in the yellow color code (Y) and the red color code (R), with a requirement of Y ≤ 35 and R ≤ 4, which display color of light yellow to white visually. The Lovibond color codes of WCO-based waxes and other control samples are shown in Fig. 5 and Table S4 in ESI.† The results showed that the dark brown soft solid WCO exhibited a very high Lovibond color value (Y = 52.3, R = 24.8). After epoxidation, the color of E-WCO became lighter and turned yellow, with a lower Lovibond color value of Y = 34.5 and R = 10.7. With the addition of H2O2, the hydrolysis process could also further reduce the color of the WCO-based wax. The Y and R color codes decreased with the increase in the dosage of NaOH. When using more than 1.5 times the theoretical amount of NaOH, the color codes of the obtained wax samples could meet the requirements of Chinese standards. The WCO-based wax which had the highest fatty acid content of the six wax samples (A6 sample), had the lightest hue (Y = 11.9, R = 2.3), while it was slightly darker than commercial SW (Y = 12.1, R = 0.7) but lighter than that of SA-modified WCO-base wax previously reported (Y = 16.1, R = 2.3).44
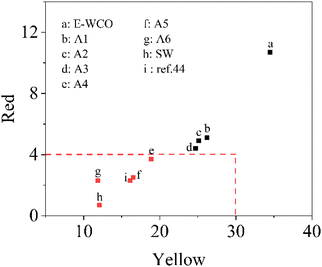 |
| Fig. 5 The Lovibond color codes of WCO-based waxes and other control samples. The symbol of ref. 44 represents a kind of WCO-based wax in our previous work44 which was the composite of E-WCO and SA with an equal mass ratio. | |
3.4 Hardness
The hardness of wax products based on WCO was characterized using the needle penetration index: the lower the needle penetration index, the harder the wax. As shown in Fig. 6 and Table S5 in ESI,† the WCO was too soft and its needle penetration index could not be detected, while the E-WCO showed an improved hardness with a needle penetration index of 23.15 mm, which was still much softer than that of commercial SW (5.67 mm). After hydrolysis, the E-WCO was converted into mixed fatty acids, considerably enhancing the wax samples' hardness. The wax contained about 50 wt% fatty acids (A2 sample) and could show better hardness than that of commercial SW, with a needle penetration index of 5.16 mm. With the increase of NaOH dosage as well as fatty acid content, the hardness of the wax samples enhanced continuously. The wax which had a fatty acid content of 96.41 wt% (A6 sample), displayed an even lower needle penetration index (2.66 mm) than that of SA-modified WCO-base wax previously reported (2.95 mm).44
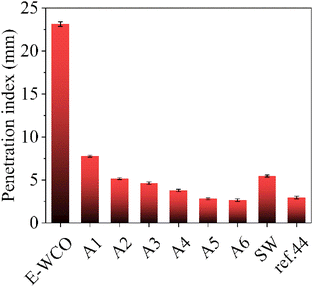 |
| Fig. 6 The penetration indexes of WCO-based waxes and other control samples. The symbol of ref. 44 represents a kind of WCO-based wax in our previous work44 which was the composite of E-WCO and SA with an equal mass ratio. | |
3.5 Combustion performance
Combustion performances of the synthesized waxes were investigated and the corresponding combustion times of the candles made of the WCO-based wax are presented (see Fig. 7 and Table S6 in ESI†). The WCO itself was too soft to maintain its shape at room temperature and could not produce a candle. E-WCO could be utilized to create a free-standing candle that can provide a consistent, brilliant flame without black smoke because of its greater melting point and relative hardness. However, its melting speed was quite fast and it exhibited a short combustion time (37 min). By contrast, the fatty acid wax based on WCO could produce practical candles with a relatively long combustion time. Furthermore, the combustion time of WCO-based candles could be continuously increased by increasing the NaOH dosage as well as the fatty acid content. The WCO-based wax contains the highest fatty acid content (A6 sample) and could produce a candle with a relatively long combustion time (293 min), which is better than that of commercial SW (276 min) as well as SA-modified WCO-base wax previously reported (227 min).44
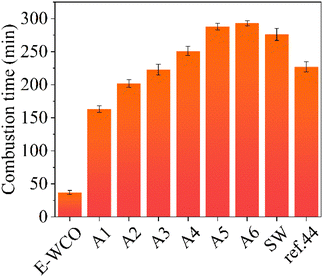 |
| Fig. 7 The combustion times of cube candles of WCO-based waxes and other control samples. The symbol of ref. 44 represents a kind of WCO-based wax in our previous work44 which was the composite of E-WCO and SA with an equal mass ratio. | |
3.6 Aldehyde content
Due to repeated heating and frying, the WCO contains a series of hazardous organics. Among them, aldehydes are the primary volatile organic chemicals in WCO, which may stimulate the mucosa, corrode the skin or even cause carcinogenesis.57–59 As shown in Fig. 8 and Table S7 in ESI,† the WCO displayed a very high aldehyde content of 3.84 μg g−1, which could emit an obvious rancidity odor. The epoxidation process could eliminate the odorous aldehydes in WCO effectively, for the aldehyde content of E-WCO (0.844 μg g−1) was only 1/5 of that of WCO. The hydrolysis process could also further reduce the aldehyde content of the WCO-based wax. The A6 sample showed a very low aldehyde content (7.98 × 10−2 μg g−1) which is similar to that of commercial SW (3.84 × 10−2 μg g−1), which could ensure the health of consumers effectively.
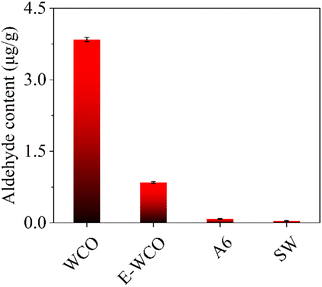 |
| Fig. 8 The aldehyde contents of WCO-based wax and other control samples. | |
3.7 Micro-morphology
According to the results of micro-morphology images and PXRD diffraction patterns (see Fig. 9 and S4–S13 in ESI†), the WCO solid showed irregular fine particles with poor crystallization performance with a considerable number of circular oil droplets. The E-WCO solid, in comparison, was made up of homogenous, fine grains without oil droplets, whose grain size was much smaller than that of commercial SW.
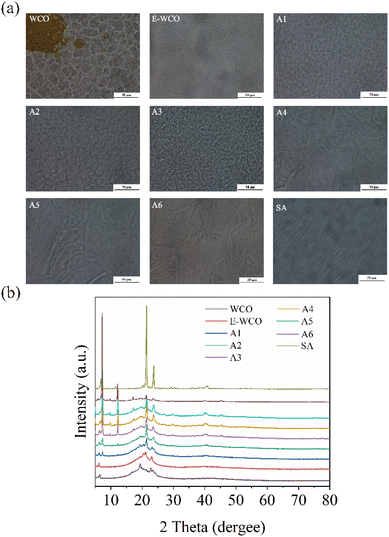 |
| Fig. 9 The 500× microphotographs (a) and PXRD patterns (b) of WCO-based waxes and other control samples. | |
The hydrolysis process by NaOH could significantly change the micro-morphologies of WCO-based waxes. With the increase of NaOH dosage as well as the fatty acid content, the crystallinity and the grain sizes of WCO-based wax enhanced significantly, and long-rod crystals of mixed fatty acids increased and progressively formed 3D crossing networks. When the fatty acid content of the wax was more than 78% (A4–A6 samples), the WCO-based wax showed a similar micro-morphology to pure SA, which displayed regularly arranged, large long-rod crystalline crystals.
As previously mentioned, the WCO consisted of mainly mixed triglycerides with a certain amount of double bonds and many kinds of colored or odorous organic impurities. The unsaturated double bonds would lead to a loose molecular arrangement. Thus, in the microscale, the WCO was composed of irregular fine particles and even liquid oil drops, which may cause its low melting point and very weak hardness. Together with its dark color and rancid odor, the WCO could not be a good raw material for wax production. Compared with those in WCO, the epoxy triglycerides in E-WCO could form more regular grains without oil droplets. Thus, E-WCO displayed a higher melting point and hardness than that WCO, which could maintain its shape at room temperature or in the initial combustion stage. However, due to too small grains in its solid, the E-WCO displayed a lower melting point and weaker hardness than that of commercial SW, and its candle was soft and displayed a short combustion time during the combustion process.
Our prior study attempted to address this issue by introducing SA that could further change WCO-based waxes. As a kind of rod-shaped molecule, SA could form a 3D stable crossing network, which could effectively constrain the small grain of E-WCO, thus enhancing the melting point and hardness of the WCO-based wax and increasing the combustion time of its candle during the combustion process.44 However, we applied a new technique in this work to change the branching triglyceride molecules into rod-shaped fatty acid molecules. The long rod-like crystals of mixed fatty acids (like palmitic acid and 9,10-dihydroxystearic acid) can form a 3D stable cross network similar to that of SA, and effectively improve the grain size of the wax. This could also improve the melting point and hardness of WCO-based wax, as well as increased its burning time during the combustion process. In addition, the synergistic effect of NaOH and H2O2 can further reduce the color code and aldehyde content of WCO-based wax.
In general, the WCO-based wax containing a high content of fatty acids (like samples A6) showed similar performance to commercial SW and the SA-modified WCO-base wax in our previous work.44 It also fulfilled the national standard's requirements and could be used to create actual wax products like candles, crayons, or wax figures. Due to its application of WCO as a raw material, this fatty acid wax from WCO is cost-effective and competitive in the market. The estimated total synthesis costs of the WCO-based wax (A6 sample) is only $0.20 per kg, which is about 1/10 of the commercial SW ($2.35 per kg), and 1/3 of that of SA-modified WCO-based wax previously reported ($0.64 per kg, the composite of E-WCO and SA with an equal mass ratio).44 Thus, the expected profit margin of this WCO-based wax could be more than 500%.
4. Conclusions
In this paper, we report on the synthesis and properties of a kind of fatty acid wax based on WCO and discuss the effects of epoxidation & hydrolysis strategy on the wax. The findings demonstrated that the epoxidation &hydrolysis treatment of WCO is a feasible way to obtain WCO-based wax with low costs and high quality. Among them, the epoxidation of WCO can produce E-WCO, and then the hydrolysis of E-WCO can convert the branched triglyceride molecules to rod-shaped fatty acid molecules, such as palmitic acid and 9,10-dihydroxystearic acid. The obtained WCO-based fatty acid wax has many advantages, such as light color, good hardness, suitable melting point, relatively long candle burning time, and low aldehyde content, which can be a low-cost substitute for commercial SW. Moreover, compared to other WCO recycling methods, the synthesis of this kind of WCO-based wax requires only easy pre-treatment procedures, simple equipment, and very low synthesis costs to obtain products with good quality and a high-profit margin, making it a more advantageous option for the use of WCO in economically disadvantaged regions.
Abbreviations
WCO | Waste cooking oil |
E-WCO | Epoxy waste cooking oil |
SA | Stearic acid |
SW | Soybean wax |
A1–A6 | WCO-based wax samples with different dosages of NaOH |
Author contributions
Conceptualization, methodology & writing (original draft preparation): Yan Liu; software: Xin-Gang Fan; investigation: Lie Wang, Han-Rui Xu, Yu-Xin Chen; resources & data curation: Meng-Yu Liu; formal analysis: Peng-Yu Wang; writing (review and editing), project administration, funding acquisition & supervision: Shuo-ping Chen. All authors have read and agreed to the published version of the manuscript.
Conflicts of interest
There are no conflicts to declare.
Acknowledgements
This work was supported by grants from the National Nature Science Foundation of China (No. 51763007), the Guangxi Natural Science Foundation Program (No. 2015GXNSFBA139033), and the Sharing Foundation of Guangxi Key Laboratory of Optical and Electronic Materials and Devices (No. 20 AA-9).
Notes and references
- H. Hosseinzadeh-Bandbafha, C. Li, X. Chen, W. Peng, M. Aghbashlo, S. S. Lam and M. Tabatabaei, Managing the hazardous waste cooking oil by conversion into bioenergy through the application of waste-derived green catalysts: a review, J. Hazard. Mater., 2022, 424, 127636 CrossRef CAS PubMed.
- M. Lopes, S. M. Miranda and I. Belo, Microbial valorization of waste cooking oils for valuable compounds production – a review, Crit. Rev. Environ. Sci. Technol., 2019, 50(24), 2583–2616 CrossRef.
- A. Mannu, S. Garroni, J. Ibanez Porras and A. Mele, Available Technologies and Materials for Waste Cooking Oil Recycling, Processes, 2020, 8(3), 366 CrossRef CAS.
- B. Changmai, C. Vanlalveni, A. P. Ingle, R. Bhagat and S. L. Rokhum, Widely used catalysts in biodiesel production: a review, RSC Adv., 2020, 10(68), 41625–41679 RSC.
- B. H. H. Goh, C. T. Chong, Y. Ge, H. C. Ong, J.-H. Ng, B. Tian, V. Ashokkumar, S. Lim, T. Seljak and V. Józsa, Progress in utilisation of waste cooking oil for sustainable biodiesel and biojet fuel production, Energy Convers. Manage., 2020, 223, 113296 CrossRef CAS.
- M. Jindal, P. Rosha, S. K. Mahla and A. Dhir, Experimental investigation of performance and emissions characteristics of waste cooking oil biodiesel and n-butanol blends in a compression ignition engine, RSC Adv., 2015, 5(43), 33863–33868 RSC.
- J. M. Londoño Feria, G. A. Nausa Galeano and D. H. Malagón-Romero, Production of Bio-Oil from Waste Cooking Oil by Pyrolysis, Chem. Eng. Technol., 2021, 44(12), 2341–2346 CrossRef.
- M. M. El-Sheekh, M. Y. Bedaiwy, A. A. El-Nagar, M. Elkelawy and H. Alm-Eldin Bastawissi, Ethanol biofuel production and characteristics optimization from wheat straw hydrolysate: performance and emission study of DI-diesel engine fueled with diesel/biodiesel/ethanol blends, Renewable Energy, 2022, 191, 591–607 CrossRef CAS.
- M. Gohain, M. Hasin, K. S. H. Eldiehy, P. Bardhan, K. Laskar, H. Phukon, M. Mandal, D. Kalita and D. Deka, Bio-ethanol production: a route to sustainability of fuels using bio-based heterogeneous catalyst derived from waste, Process Saf. Environ. Prot., 2021, 146, 190–200 CrossRef CAS.
- K. Sangkharak, K. Chookhun, J. Numreung and P. Prasertsan, Utilization of coconut meal, a waste product of milk processing, as a novel substrate for biodiesel and bioethanol production, Biomass Convers. Biorefin., 2019, 10, 651–662 CrossRef.
- W. H. Foo, W. Y. Chia, D. Y. Y. Tang, S. S. N. Koay, S. S. Lim and K. W. Chew, The conundrum of waste cooking oil: transforming hazard into energy, J. Hazard. Mater., 2021, 417, 126129 CrossRef CAS PubMed.
- R. Marchetti, C. Vasmara, L. Bertin and F. Fiume, Conversion of waste cooking oil into biogas: perspectives and limits, Appl. Microbiol. Biotechnol., 2020, 104, 2833–2856 CrossRef CAS PubMed.
- J. R. Guimaraes, L. P. Miranda, R. Fernandez-Lafuente and P. W. Tardioli, Immobilization of Eversa((R)) Transform via CLEA Technology Converts It in a Suitable Biocatalyst for Biolubricant Production Using Waste Cooking Oil, Molecules, 2021, 26(1), 193 CrossRef CAS PubMed.
- R. Z. K. Hussein, N. K. Attia, M. K. Fouad and S. T. Elsheltawy, Experimental investigation and process simulation of biolubricant production from waste cooking oil, Biomass Bioenergy, 2021, 144, 105850 CrossRef CAS.
- N. Singh, P. Agarwal and S. K. Porwal, Natural Antioxidant Extracted Waste Cooking Oil as Sustainable Biolubricant Formulation in Tribological and Rheological Applications, Waste Biomass Valorization, 2022, 13(7), 3127–3137 CrossRef CAS PubMed.
- W. H. Foo, S. S. N. Koay, S. R. Chia, W. Y. Chia, D. Y. Y. Tang, S. Nomanbhay and K. W. Chew, Recent advances in the conversion of waste cooking oil into value-added products: a review, Fuel, 2022, 324, 124539 CrossRef CAS.
- J. H. Kim, Y. R. Oh, J. Hwang, J. Kang, H. Kim, Y. A. Jang, S. S. Lee, S. Y. Hwang, J. Park and G. T. Eom, Valorization of waste-cooking oil into sophorolipids and application of their methyl hydroxyl branched fatty acid derivatives to produce engineering bioplastics, Waste Manage., 2021, 124, 195–202 CrossRef CAS PubMed.
- S. Sharma, R. Verma, S. Dhull, S. K. Maiti and L. M. Pandey, Biodegradation of waste cooking oil and simultaneous production of rhamnolipid biosurfactant by Pseudomonas aeruginosa P7815 in batch and fed-batch bioreactor, Bioprocess Biosyst. Eng., 2022, 45(2), 309–319 CrossRef CAS PubMed.
- Z. Elahi, F. Mohd Jakarni, R. Muniandy, S. Hassim, M. S. Ab Razak, A. H. Ansari and M. M. Ben Zair, Waste Cooking Oil as a Sustainable Bio Modifier for Asphalt Modification: A Review, Sustainability, 2021, 13(20), 11506 CrossRef CAS.
- C. Li, X. Han, J. Gong, W. Su, Z. Xi, J. Zhang, Q. Wang and H. Xie, Impact of waste cooking oil on the viscosity, microstructure and mechanical performance of warm-mix epoxy asphalt binder, Constr. Build. Mater., 2020, 251, 118994 CrossRef CAS.
- J. Norambuena-Contreras, J. Concha, L. Arteaga-Pérez and I. Gonzalez-Torre, Synthesis and Characterisation of Alginate-Based Capsules Containing Waste Cooking Oil for Asphalt Self-Healing, Appl. Sci., 2022, 12(5), 2739 CrossRef CAS.
- D. Ruikun, Y. Huifang, Z. Mengzhen and H. Wang, Preparation of Asphalt Modifier Made of Waste Tire Crumb Rubber and Waste Cooking Oil, J. Mater. Civ. Eng., 2022, 34(8), 04022175 CrossRef CAS.
- A. Pospisilova, I. Novackova and R. Prikryl, Isolation of poly(3-hydroxybutyrate) from bacterial biomass using soap made of waste cooking oil, Bioresour. Technol., 2021, 326, 124683 CrossRef CAS PubMed.
- K. Sharma, S. S. Toor, J. Brandão, T. H. Pedersen and L. A. Rosendahl, Optimized conversion of waste cooking oil into ecofriendly bio-based polymeric surfactant- a solution for enhanced oil recovery and green fuel compatibility, J. Cleaner Prod., 2021, 294, 126214 CrossRef CAS.
- J. Yang and H. Shan, The willingness of submitting waste cooking oil (WCO) to biofuel companies in China: an evolutionary analysis in catering networks, J. Cleaner Prod., 2021, 282, 125331 CrossRef.
- Y. Zhao, C. Wang, L. Zhang, Y. Chang and Y. Hao, Converting waste cooking oil to biodiesel in China: environmental impacts and economic feasibility, Renewable Sustainable Energy Rev., 2021, 140, 110661 CrossRef CAS.
- A. R. Mohammed and C. Bandari, Lab-scale catalytic production of biodiesel from waste cooking oil – a review, Biofuels, 2017, 11(4), 409–419 CrossRef.
- V. Cordero-Ravelo and J. Schallenberg-Rodriguez, Biodiesel production as a solution to waste cooking oil (WCO) disposal. Will any type of WCO do for a transesterification process? A quality assessment, J. Environ. Manage., 2018, 228, 117–129 CrossRef CAS PubMed.
- A. Gouran, B. Aghel and F. Nasirmanesh, Biodiesel production from waste cooking oil using wheat bran ash as a sustainable biomass, Fuel, 2021, 295, 120542 CrossRef CAS.
- H. Kumar, A. A. Renita and S. A. Jabasingh, Biodiesel production from preutilized cooking oil using a renewable heterogeneous eggshell-coconut pith catalyst: Process optimization and characterization, Environ. Prog. Sustainable Energy, 2021, 40(5), e13632 CAS.
- J. H. C. Wancura, A. L. Fantinel, G. A. Ugalde, F. F. Donato, J. Vladimir De Oliveira, M. V. Tres and S. L. Jahn, Semi-continuous production of biodiesel on pilot scale via enzymatic hydroesterification of waste material: process and economics considerations, J. Cleaner Prod., 2021, 285, 124838 CrossRef CAS.
- F. Zaman, M. W. Ishaq, N. Ul-Haq, W. U. Rahman, M. M. Ali, F. Ahmed and A. u. Haq, Effect of Different Parameters on Catalytic Production of Biodiesel from Different
Oils, ChemBioEng Rev., 2021, 9(1), 6–20 CrossRef.
- O. Awogbemi, D. V. V. Kallon, V. S. Aigbodion and S. Panda, Advances in biotechnological applications of waste cooking oil, Case Stud. Chem. Environ. Eng., 2021, 4, 100158 CrossRef CAS.
- J. Ibanez, M. S. Martel, S. Baldino, C. Prandi and A. Mannu, European Union Legislation Overview about Used Vegetable Oils Recycling: The Spanish and Italian Case Studies, Processes, 2020, 8, 798 CrossRef CAS.
- B. Boekaerts, M. Vandeputte, K. Navaré, J. Van Aelst, K. Van Acker, J. Cocquyt, C. Van Caneyt, P. Van Puyvelde and B. F. Sels, Assessment of the environmental sustainability of solvent-less fatty acid ketonization to bio-based ketones for wax emulsion applications, Green Chem., 2021, 23(18), 7137–7161 RSC.
- T. Fei, K. Ren and T. Wang, The Friction and Wear Behaviors of Vegetable Oil-Based Waxes, Natural Beeswax, and Petroleum Paraffin Wax, J. Am. Oil Chem. Soc., 2020, 97(10), 1141–1150 CrossRef CAS.
- K. Rezaei, T. Wang and L. A. Johnson, Hydrogenated Vegetable Oils as Candle Wax, J. Am. Oil Chem. Soc., 2002, 79(12), 1241–1247 CrossRef CAS.
- A. N. Surendran, K. P. K. Ajjarapu, A. A. Arumugham, K. Kate and J. Satyavolu, Characterization of industry grade soybean wax for potential applications in natural fiber reinforced composite (NFRC) filaments, Ind. Crops Prod., 2022, 186, 115163 CrossRef CAS.
- T. Burimsitthigul, B. Yoosuk, C. Ngamcharussrivichai and P. Prasassarakich, Hydrocarbon biofuel from hydrotreating of palm oil over unsupported Ni–Mo sulfide catalysts, Renewable Energy, 2021, 163, 1648–1659 CrossRef CAS.
- H. Iida, K. Takahashi, A. Yanagisawa, H. Hashimoto and A. Igarashi, Reduction of trans fatty acids in hydrogenated soybean oil using Ni/TiO2 catalysts, Food Chem., 2021, 340, 127927 CrossRef CAS PubMed.
- P. Ji, Z. Fan, M. Niu, L. Pan, G. Jing, R. Tian and W. Li, Study on the co-hydrogenation of coal tar and kitchen waste oil over Co–Mo/γ–Al2O3, React. Kinet., Mech. Catal., 2021, 132(2), 751–769 CrossRef CAS.
- A. Philippaerts, P. A. Jacobs and B. F. Sels, Is there still a future for hydrogenated vegetable oils?, Angew. Chem., Int. Ed., 2013, 52(20), 5220–5226 CrossRef CAS PubMed.
- Z. Shah, R. C. Veses, J. C. P. Vaghetti, V. D. A. Amorim and R. d. Silva, Preparation of jet engine range fuel from biomass pyrolysis oil through hydrogenation and its comparison with aviation kerosene, Int. J. Green Energy, 2019, 16(4), 350–360 CrossRef CAS.
- Y. Liu, M. Y. Liu, Y. X. Qi, X. Y. Jin, H. R. Xu, Y. X. Chen, S. P. Chen and H. P. Su, Synthesis and properties of wax based on waste cooking oil, RSC Adv., 2022, 12, 3365–3371 RSC.
- U. Azzena, A. Montenero, M. Carraro, R. Crisafulli, L. De Luca, S. Gaspa, A. Muzzu, L. Nuvoli, R. Polese, L. Pisano, E. Pintus, S. Pintus, A. Girella and C. Milanese, Recovery, Purification, Analysis and Chemical Modification of a Waste Cooking Oil, Waste Biomass Valorization, 2022, DOI: DOI:10.1007/s12649-022-01845-3.
- A. K. Paul, V. B. Borugadda and V. V. Goud, In Situ Epoxidation of Waste Cooking Oil and Its Methyl Esters for Lubricant Applications: Characterization and Rheology, Lubricants, 2021, 9, 27 CrossRef CAS.
- H. He, S. Niu, J. Wang, K. Wang and G. Rao, Research progress of decolorization and saponification technology of drainage oil, Chem. Propellants Polym. Mater., 2015, 13(3), 39–44 CAS.
- X. Meng, W. Ma, Y. Ma and J. Wan, Study on Cleaning Agent for Industrial Production of Gutter Oil, Jiangxi Chem. Ind., 2018,(5), 157–160 Search PubMed.
- K. Xu, Y. Sun, J. Guo, Y. Lu and Y. Yang, New technology of gutter oil saponification soap, Yunnan Chem. Technol., 2016, 43(5), 72–74 Search PubMed.
- Y. Xiong, W. F. Miao, N. N. Wang, H. M. Chen, X. R. Wang, J. Y. Wang, Q. L. Tan and S. P. Chen, Solid alcohol based on waste cooking oil: synthesis, properties, micromorphology and simultaneous synthesis of biodiesel, Waste Manage., 2019, 85, 295–303 CrossRef CAS PubMed.
- A. Baena, A. Orjuela, S. K. Rakshit and J. H. Clark, Enzymatic hydrolysis of waste fats, oils and greases (FOGs): status, prospective, and process intensification alternatives, Chem. Eng. Process., 2022, 175, 108930 CrossRef CAS.
- M. R. Khodadadi, I. Malpartida, C. W. Tsang, C. S. K. Lin and C. Len, Recent advances on the catalytic conversion of waste cooking oil, Mol. Catal., 2020, 494, 111128 CrossRef CAS.
- V. Benessere, M. E. Cucciolito, A. De Santis, M. Di Serio, R. Esposito, F. Ruffo and R. Turco, Sustainable Process for Production of Azelaic Acid Through Oxidative Cleavage of Oleic Acid, J. Am. Oil Chem. Soc., 2015, 92(11–12), 1701–1707 CrossRef CAS.
- S. Santos, V. Cabral and J. Graca, Cork suberin molecular structure: stereochemistry of the C18 epoxy and vic-diol omega-hydroxyacids and alpha, omega-diacids analyzed by NMR, J. Agric. Food Chem., 2013, 61(29), 7038–7047 CrossRef CAS PubMed.
- L. Zhang, Y. Sun, M. Di Serio, J. Zhou, L. Ding, Y. Zhang, H. Liang, H. Wu and J. Sun, Synthesis and Properties of 9,10-Dihydroxystearic Acid Ethoxylate, Tenside, Surfactants, Deterg., 2019, 56(3), 237–243 CAS.
- C. Y. Xue, Y. H. Zhang, Y. Liu, R. X. Zhang, H. J. Jing and E. Chen, Synthesis, purification and identification of 9,10-dihydroxystearic acid by mass spectrometry, infrared spectrum and nuclear magnetic resonance, Chin. J. Tissue Eng. Res., 2007, 11(35), 7028–7031 CAS.
- K. Ganesan and B. Xu, Deep frying cooking oils promote the high risk of metastases in the breast-A critical review, Food Chem. Toxicol., 2020, 144, 111648 CrossRef CAS PubMed.
- Z. Wei, X. Li, D. Thushara and Y. Liu, Determination and removal of malondialdehyde and other 2-thiobarbituric acid reactive substances in waste cooking oil, J. Food Eng., 2011, 107(3–4), 379–384 CrossRef CAS.
- L. Huang, H. Cheng, S. Ma, R. He, J. Gong, G. Li and T. An, The exposures and health effects of benzene, toluene and naphthalene for Chinese chefs in multiple cooking styles of kitchens, Environ. Int., 2021, 156, 106721 CrossRef CAS PubMed.
Footnote |
† Electronic supplementary information (ESI) available: The optimization of the experimental conditions of hydrolysis process; brief introduction of China standards concerned in this paper; 1H NMR spectra, microphotographs and PXRD patterns; the data table of melting temperatures, Lovibond color codes, combustion times, penetration indexes and aldehydes contents of WCO-based waxes and other control samples. See DOI: https://doi.org/10.1039/d2ra06390e |
|
This journal is © The Royal Society of Chemistry 2022 |
Click here to see how this site uses Cookies. View our privacy policy here.