DOI:
10.1039/D3CC00456B
(Highlight)
Chem. Commun., 2023,
59, 3948-3956
Exsolution on perovskite oxides: morphology and anchorage of nanoparticles
Received
31st January 2023
, Accepted 7th March 2023
First published on 14th March 2023
Abstract
Perovskites are very promising materials for a wide range of applications (such as catalysis, solid oxide fuel cells…) due to beneficial general properties (e.g. stability at high temperatures) and tunability – doping both A- and B-site cations opens the path to a materials design approach that allows specific properties to be finely tuned towards applications. A major asset of perovskites is the ability to form nanoparticles on the surface under certain conditions in a process called “exsolution”. Exsolution leads to the decoration of the material's surface with finely dispersed nanoparticles (which can be metallic or oxidic – depending on the experimental conditions) made from B-site cations of the perovskite lattice (here, doping comes into play, as B-site doping allows control over the constitution of the nanoparticles). In fact, the ability to undergo exsolution is one of the main reasons that perovskites are currently a hot topic of intensive research in catalysis and related fields. Exsolution on perovskites has been heavily researched in the last couple of years: various potential catalysts have been tested with different reactions, the oxide backbone materials and the exsolved nanoparticles have been investigated with a multitude of different methods, and the effect of different exsolution parameters on the resulting nanoparticles has been studied. Despite all this, to our knowledge no comprehensive effort was made so far to evaluate these studies with respect to the effect that the exsolution conditions have on anchorage and morphology of the nanoparticles. Therefore, this highlight aims to provide an overview of nanoparticles exsolved from oxide-based perovskites with a focus on the conditions leading to nanoparticle exsolution.
1. Introduction
(a) Perovskites
Perovskites are materials of the general formula ABX3, where A and B are different (mostly) metallic cations of differing sizes (A-site cations are larger), whereas X are counter anions. The basic (undistorted) structure is cubic with A cations at the corners. The B cation occupies the centre of the unit cell (cf.Fig. 1, middle) and is octahedrally coordinated with X anions – these octahedra form a network with shared corners.
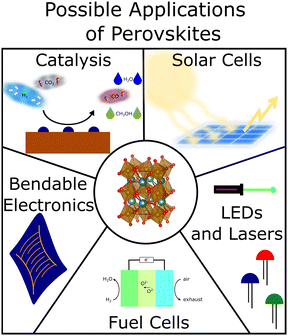 |
| Fig. 1 Example applications of perovskites include catalysis,1–3 solar cells,7,8 LEDs and lasers,9,10 fuel cells4,5 and bendable electronics.6 In the centre, a representation of the unit cell of one of our perovskite oxides is shown. | |
Despite appearing to be deceptively simple materials, perovskites are remarkably compositionally versatile – different A- and B-site elements across the periodic table are possible – and exhibit a vast range of properties that lead to their applicability across many technological fields. To give just a few examples: perovskite oxides have been extensively investigated for applications in catalysis1–3 and as electrode materials in solid oxide fuel cells.4,5 Perovskite halides are widespread in photovoltaics and solar cells6–8 as well as in lasers and light emitting diodes9,10 (cf.Fig. 1). Perovskite nitrides – albeit not as common – have been predicted to be stable and are expected to be ferroelectric11 and more exotic nitrogen-based perovskites have been found to be superconducting.12
In our own work, we utilise iron-based perovskite oxides as catalysts for multiple reactions (e.g. reverse water–gas shift13 or methane dry reforming14) because of their highly beneficial properties: this type of perovskite oxides can be used at high temperatures, as they are thermally stable. Due to their compositional flexibility and their tunability (both A- and B-sites can be relatively easily doped with catalytically active elements), perovskite oxides lend themselves to a rational catalyst design approach. Moreover, increased resistance against coking14,15 makes these materials interesting for CO2 utilization reactions. Another property of these materials – that makes them highly relevant for applications in catalysis and related fields – is their ability to undergo a process called “exsolution” under certain conditions.
(b) Exsolution
Exsolution as a process has been studied extensively.13–19 Depending on the conditions, it reversibly20 leads to the decoration of a material's surface with finely dispersed nanoparticles.16 The formation of such nanoparticles can be achieved before reactions (in reducing gas atmospheres or electrically by applying a bias to the sample21,22) or in situ, provided the reaction conditions are sufficiently reducing:14,23
The perovskite material is partially reduced causing reducible B-site cations to migrate to the surface, where they exsolve and form metallic or oxidic nanoparticles (depending on the conditions) – as can be seen in Fig. 2.
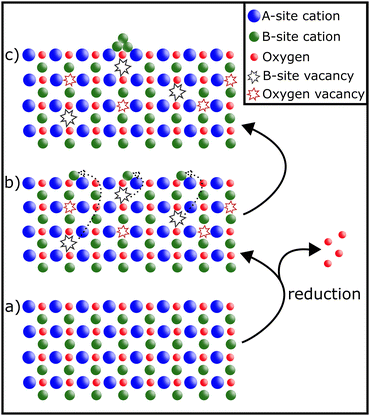 |
| Fig. 2 Schematic representation of exsolution: under reducing conditions (a), B-site cations migrate to the surface leaving behind vacancies (b). On the surface they form finely dispersed nanoparticles that are stable against sintering due to them being anchored in the material (c). | |
Among the many advantages of nanoparticles exsolved via exsolution are the fine dispersion of the resulting particles,16 their high stability and sinter resistance due to “anchoring” in the surface,15,16,19 and their tunability: either by varying the composition of the perovskite16,17,24 or adapting the conditions during the exsolution process.18,21,23 Another feature of exsolution catalysts (provided they exhibit reversible exsolution) is the possible regeneration of the active nanoparticles via re-oxidation, thus improving catalyst lifetime.1,25
(c) Scope of this work
Exsolution in perovskite oxides as well as its applications in catalysis and related fields have been the topic of extensive studies, since catalysts with nanoparticles formed via exsolution offer a great number of advantages and chances for new and improved catalysts.13–19 However, to our knowledge more detailed investigations of the connection between exsolution conditions and morphology (size, population density, shape) and anchorage of the resulting nanoparticles are still rare. Especially so in the context of comparisons across different materials.
With this article, we want to provide a summary of works published on this topic in recent years to serve as starting point for such in-depth comparisons. We strongly believe that it is of vital importance to further deepen the understanding of the relation of exsolution conditions and the properties of the resulting nanoparticles in order to use perovskite oxides (and exsolution) to their fullest potential for the design of new efficient catalysts.
2. Overview of published work
For this article, we considered all publications of the Clarivate database “Web of Science”‡ as well as “Google Scholar”§ between January 2016 and mid 2022 that contained the keywords “nanoparticle exsolution” and “perovskite”.
As this overview is focussed on morphology and anchorage of nanoparticle, we further constricted the search to publications containing Scanning Electron Microscopy (SEM) or Transmission Electron Microscopy (TEM) images (ideally both). Both methods are ideally suited to provide information relevant to the question at hand: SEM images not only reveal the surface decoration of the investigated materials – and the fact that exsolution took place, but also allow assessments of size, population density, and shape of the exsolved nanoparticles. TEM images give complementary information about the anchorage of a nanoparticle (in some instances, even the orientation of the visible nanoparticle facet is available). Both microscopy methods additionally offer the possibility to perform elemental analysis to gain information about the make-up of the particles (via Energy Dispersive X-ray Spectroscopy – EDX or EDS).26 As an example, Fig. 317 shows a series of TEM images that combine anchorage information (the nanoparticles are about 33% embedded in the perovskite surface) with an elemental map revealing the composition of the nanoparticles (shown are Co and Ni nanoparticles, respectively).
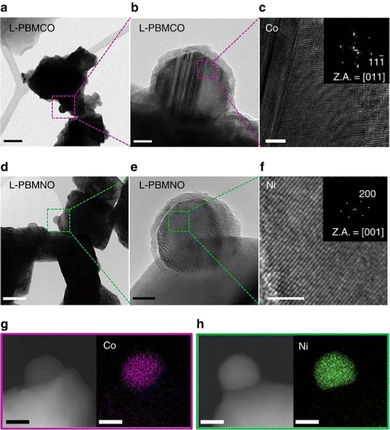 |
| Fig. 3 “(a) A bright-field (BF) TEM image; scale bar, 100 nm and (b) high-resolution (HR) TEM image of PrBaMn1.7Co0.3O5+δ (L-PBMCO) sample; scale bar 10 nm. (c) Magnified HR TEM image of exsolved Co nanoparticle; scale bar 2 nm, (d) BF TEM image; scale bar 100 nm and (e) HR TEM image of PrBaMn1.7Ni0.3O5+δ (L-PBMNO) sample; scale bar 10 nm. (f) Magnified HR TEM image of Ni nanoparticle; scale bar 2 nm. (g) High-angle annular dark-field (HAADF) image of the L-PBMCO with the EDS elemental map of Co; scale bar 25 nm. (h) HAADF image of the L-PBMNO with the EDS elemental map of Ni; scale bar 25 nm.” Reproduced from Kwon et al.17 under CC BY 4.0. | |
By imposing these restrictions, more than 2.500 publications of studies done about nanoparticle exsolution on perovskites could be reduced to about 950 works that also contained at least one SEM/TEM image. To bring this number down even further, publications that did not contain information about the nanoparticle morphology (at least an estimate for the average size or information about the anchorage of the nanoparticles) or that used SEM imaging “merely” as proof for the presence of exsolution were excluded. Furthermore, we eliminated publications with insufficient image quality and/or conclusions we could not reproduce from the presented data.
Ultimately, 83 remaining articles were analysed with respect to the used material (composition of the host material, make-up of the exsolved nanoparticles…), the conditions of the exsolution (pre-treatment/in situ, gas atmospheres, temperatures…), and morphology (size, population density, shape) of the exsolved nanoparticles as well as the degree of their anchorage.
(a) Materials and exsolved nanoparticles
As the publications collected in this work use roughly 125 different perovskite oxide materials, they were grouped by elemental composition of the exsolved nanoparticles (Table 1):
Table 1 Elements reported more than once in exsolved nanoparticles
Element |
Number of publications |
Reported composition of nanoparticles |
Ni |
42 |
Ni,13,17,23,27–47 Fe–Ni,35,48–64 Co–Ni,65 Cu–Ni,66 Fe–Ni–Re,49 Fe–Ni–Mo58 |
Fe |
41 |
Fe,13,24,67–74 Fe–Ni,35,48–64 Co–Fe,22,53,75–84 Fe–Re,49 Ru–Fe,85 Fe–Ni–Re,49 Fe–Ni–Mo58 |
Co |
23 |
Co,13,17,23,24,40,68,80,86–89 Co–Fe,22,53,75–84 Co–Ni65 |
Ru |
6 |
Ru,90–94 Fe–Ru85 |
Ag |
4 |
Ag95–98 |
Cu |
3 |
Cu,40,99 Cu–Ni66 |
Re |
2 |
Fe–Re,49 Fe–Ni–Re49 |
As Table 1 shows, Ni and Fe are each reported as (part of) exsolved nanoparticles in about 50% of the collected papers, with Co (in slightly more than 25%) a distant third. Ru (6 occurrences), Ag (4), Cu (3), and Re (2) only appear in few publications. Nanoparticles comprised of the following are mentioned once each: Au,100 Bi,70 Ir,101 Mo,58 Rh,102 (PrBa)Ox,103 and SrO.104
In terms of mono-metallic nanoparticle composition, Ni particles are reported in 25 publications, whereas Co and Fe are notably less common with 11 and 10 reports, respectively. Fe is the most common element in metal–alloy nanoparticles (34) with Ni (22) and Co (13) far behind. Interestingly, Bi, Mo, and Re are only found in metal–alloy nanoparticles.
Except for two publications, all collected publications report on mono-metallic or metal–alloy nanoparticles, even though (partial) oxidation of the nanoparticles depending on the gas atmosphere during application is conceivable in many cases. Zhu et al.103 and Ye et al.104 explicitly study oxidic nanoparticles – (PrBa)Ox and SrO, respectively.
(b) Driving force of exsolution
In all of the collected studies – with the exceptions of Fan et al.,22 where a potential is applied, and Kim et al.,97 where water mediated exsolution in a H2O/O2 gas mixture is investigated – reducing gas atmospheres are used to drive exsolution. The most commonly used way to do this, is to use H2 in an inert carrier gas (Ar and N2 are usually used – refer to Table 2 for the references, however, Kousi et al.36 use He as inert gas). Alternatives are the usage of wet H2 (or “humidified H2” with 3% water added) or dry (pure) H2. In a few studies, mixtures of reactive gases (H2O/H2 and H2/CO2, respectively) in Ar are used to investigate exsolved particles during chemical reactions (e.g. during methane dry reforming49,56 with addition of CH4).
Table 2 Gas atmospheres used during exsolution (only the constituent gases are given, and no further distinctions were made regarding other parameters)
Atmosphere |
Number of publications |
Ref. |
H2 in Ar |
36 |
28–30, 33, 39, 41, 42, 47–49, 51, 53, 55, 56, 60, 66, 67, 70, 73–75, 78, 80–85, 89, 91–93, 95, 96, 100 and 104
|
H2 in N2 |
20 |
31, 34, 44, 46, 57, 62–65, 72, 76, 86–88, 94, 95, 98, 99, 101 and 102
|
wet H2 |
13 |
17, 24, 27, 30, 35, 38, 52, 54, 61, 68, 69, 77 and 79
|
dry H2 |
10 |
37, 40, 43, 45, 58, 59, 81, 87, 103 and 104
|
H2O/H2 in Ar |
5 |
28, 32, 50, 71 and 90
|
H2/CO2 in Ar |
2 |
13 and 23
|
Another way of classifying the publications review for this article is to distinguish between exsolution triggered during a pre-treatment before further tests or applications (for instance electrochemical measurements65 or NH3 sensing95) and in situ exsolution, i.e. nanoparticles are exsolve during tests, applications, or chemical reactions (like the aforementioned methane dry reforming or reverse water–gas shift reaction13). Such in situ studies are reported in ref. 13, 23, 24, 29, 32, 37, 39, 42, 49, 52, 56, 57, 68, 71, 72, 75, 85, 89, 92, 104.
3. Morphology
In this highlight, we focus on three different descriptors of exsolved nanoparticles: (i) the size and/or the size distribution, (ii) the population density and (iii) the shape of the particles. The first two of these can be determined relatively easily during nanoparticle characterisation (e.g. by SEM): nanoparticles sizes (of at least one specific type) are given in almost all publications collected for this article (with the exception of 5), whereas the population density is reported in only 22 out of 83 studies. The particle shape, on the other hand, is rarely reported expressly and hardly ever the main topic of investigation (with the notable exception of a study of Kim et al.45 – see Section 3c). However, it can usually be derived from electron microscope images, given proper image quality.
(a) Size of nanoparticles
Despite the fact that nanoparticle sizes are reported in almost all publications, comparing the results let alone formulating trends across publications is usually not useful. This is due to the large number of parameters that can be varied during exsolution (temperature, type of atmosphere, pressure, duration, specific composition of the host material…). For instance, the sizes described for Fe nanoparticles (across 7 publications24,67–69,71,73,74) span a range from 14 nm up to 600 nm. That is, of course, not surprising given the fact that in those cases 6 different reducing gas atmospheres were used, temperatures between 625 °C and 850 °C were applied and the duration of the reducing treatment varied from 30 minutes to 60 hours.
More meaningful comparisons can be drawn from comparative studies: Spring et al.,39 for instance, find that Ni nanoparticles grow larger at higher temperatures or if treated for a longer time (see Fig. 4). Islam et al.,65 Wu et al.,54 Deka et al.57 and Cali et al.101 report the same temperature behaviour of Co–Ni, Fe–Ni, Fe–Ni (albeit on a very small scale), and Ir particles, respectively. Carrillo et al.56 confirm the same trend for Fe–Ni particles and additionally report broadening of the size distribution. Zhang et al.52 found similar behaviour when they performed long-term tests of the stability of Ni–Fe alloy particles in an atmosphere of wet H2 (see Fig. 5): the particles start small with a narrow size distribution (with an average of 28.9 nm), but after 25 h the average increased to 35.5 nm (and a broader distribution). Subsequent measurements (up to 200 h later) confirmed that nanoparticle size stabilises at this value. Ansari et al.62 report similar findings for prolonged heat treatment of Ni–Fe alloy nanoparticles (at two different temperatures), where they find a similar initial increase, however, cannot confirm the stabilisation (due to too short measurements).
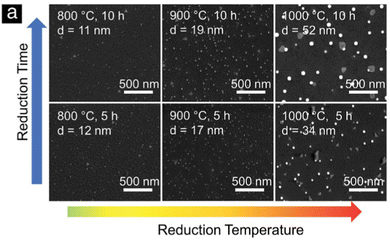 |
| Fig. 4 “(2) SEM micrographs of La0.2Sr0.7Ti0.9Ni0.1O3−δ thin films after reduction at different conditions.” Reprinted (in part) with permission from J. Spring, E. Sediva, Z. D. Hood, J. C. Gonzalez-Rosillo, W. O’Leary, K. J. Kim, A. J. Carrillo and J. L. M. Rupp, Small, 2020, 16, 2003224. Copyright (2020) Wiley-VCH GmbH. | |
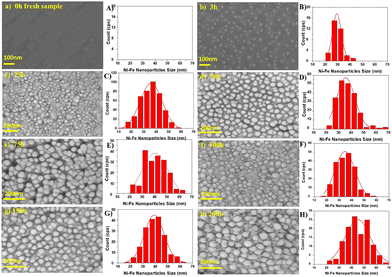 |
| Fig. 5 “(a)–(h) SEM images of the surface of in situ exsolved Ni–Fe nanoparticle structured SFMNi bar treated at different aging times of (a) 0 h, (b) 3 h, (c) 25 h, (d) 50 h, (e) 75 h, (f) 100 h, (g) 150 h, and (h) 200 h in a condition of 97% H2–3% H2O atmosphere and 800 °C and (A–H) the particle size distribution and population density of the corresponding in situ exsolved Ni–Fe nanoparticles shown in parts a–h calculated by using ImageJ software.” Reprinted with permission from T. H. Zhang, Y. Q. Zhao, X. Y. Zhang, H. Zhang, N. Yu, T. Liu and Y. Wang, ACS Sustainable Chemistry & Engineering, 2019, 7, 17834–17844. Copyright (2019) American Chemical Society. | |
Horlick et al.58 investigated the effect of varying substitution (substituting Fe for Ni and Mo on the B-site of SrFeO3−δ) and found decreasing size for the alloyed nanoparticles. Wang et al.40 studied different B-site dopants (Co, Ni, and Cu, respectively) and found different average particle sizes. Sun et al.46 compared exsolution results of the “conventional” heat treatment of the host material (900 °C for 20 h) with a newly proposed thermal shock method (1400 °C for a few seconds) and report significantly smaller particles.
(b) Population density of nanoparticles
We will again focus on trends and comparisons found within a given publication (as comparisons across studies are not really meaningful for abovementioned reasons) regarding the population density.
In our own work (Lindenthal et al.23) while performing temperature ramps, we found that the population density of Co nanoparticles tends to decrease with temperature (while the size in this particular case remained rather constant). Deka et al.57 (see Fig. 6(d)) and Ansari et al.62 report similar findings for Fe–Ni alloy particles. However, the temperature dependence of the population density seems not as straightforward as was the case for the particle size: Cali et al.101 and Wu et al.54 find the opposite behaviour for Ir and Fe–Ni, respectively; with the population density increasing with temperature. Carrillo et al.,56 on the other hand, find an initial drop of population density for Fe–Ni followed by an increase when increasing the temperature further. Zhang et al.52 report a similar but inverted trend during sample heat treatment in wet H2: they observe a larger number of particles emerging per unit area during the first 150 hours but find a decrease after 200 hours (still at a value above the start).
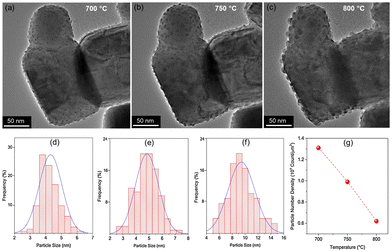 |
| Fig. 6 “in situ TEM of LSNF under 5% H2/N2 collected at (a) 700 °C, (b) 750 °C and (c) 800 °C showing formation of nanoparticles, (d)–(f) show distribution of particle sizes at these three temperatures, (g) nanoparticle number density at these three temperatures.” Reprinted from, D. J. Deka, J. Kim, S. Gunduz, M. Aouine, J.-M. M. Millet, A. C. Co, U. S. Ozkan, Investigation of hetero-phases grown via in situ exsolution on a Ni-doped (La,Sr)FeO3 cathode and the resultant activity enhancement in CO2 reduction, Appl. Catal., B, 286, 119917, Copyright (2021), with permission from Elsevier. | |
Another possible factor influencing population density is composition: Horlick et al.58 observed that during the B-site substitution of SrFeO3−δ with equal amounts of Ni and Mo the population density of the alloy particles starts to slowly increase with a notable jump at the highest substitution tested. Wang et al.40 found different population densities for different B-site dopants (Co, Ni, and Cu, respectively) under otherwise similar conditions. Other factors include applied voltage during electrochemically driven exsolution (Fan et al.,22 larger voltage leads to increased population density), oxygen partial pressure during water driven exsolution (Kim et al.,97 higher pressures increase the density), preparation method (Sun et al.,45 the thermal shock method leads to a significantly larger density), or number of atomic layer deposition cycles (Joo et al.35 deposit Fe2O3 on the investigated samples to form Fe–Ni alloy nanoparticles after an additional reduction step and find that more deposition cycles lead to higher particle numbers per unit area, with the particle size, however, remaining rather similar).
(c) Shape of nanoparticles
Control over the shape of exsolved nanoparticles offers another adjustment screw to optimise the performance of materials or tailor them towards the specific application. For instance, the shape of the catalytically active nanoparticles is crucial in heterogeneous catalysis, where depending on the reaction at hand, the presence of kinks or edges on a non-spherical particle might greatly influence the activity of a given catalyst.45
That being said, the work by Kim et al.45 is the only one of 83 collected works that investigates this possibility in-depth with the goal of designing high performance catalysts. They used a (La,Ca)(Ni,Ti)O3 host and investigated exsolved Ni particles, for the exsolution of which variations of reduction temperatures and durations were used. TEM images reveal that depending on the exact conditions different nanoparticles shapes can be found (Fig. 7).
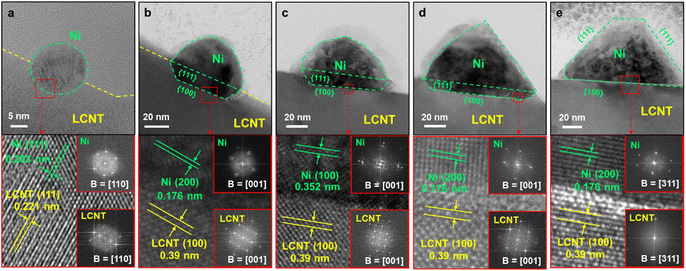 |
| Fig. 7 “HVEM images with fast Fourier transform (FFT) of exsolved Ni particles with different size. (a) The spherical nickel nanoparticle on LCNT powder reduced at 800 °C for 24 h, and the polyhedral nickel nanoparticles with different size and shape, on lamella sample from LCNT pellets reduced at 900 °C for (b), (c) 3 and (d), (e) 24 h.” Reprinted from, Y. H. Kim, Y. Kang, H. Jeong, D. Neagu, J.-H. Myung, Shape-shifting nanoparticles on a perovskite oxide for highly stable and active heterogeneous catalysis, Chem. Eng. J., 441, 136025, Copyright (2022), with permission from Elsevier. | |
Even though the shape (as well as the size) of a particle can affect the activity and/or the selectivity of a catalyst,45 nanoparticle shape appears to mostly be a rather inconsequential descriptor of the exsolved nanoparticles. By far the most commonly observed are spherically shaped particles (42 publications), with ellipsoidal particles reported with only half the frequency of spherical ones (23). Other shapes that occurred during our search are “polyhedral” (2), “pyramid”, “triangular plate”, and “trapezoidal” (1 mention each) – notably, pyramidal, and triangular plate shaped particles only appear in the study by Kim et al.45 A summary of the reported particle shapes (sorted by shape and grouped by particle composition) is presented in Table 3.
Table 3 Overview of reported nanoparticles shapes
Shape |
Number of publications |
Element/aloy with references |
Spherical |
42 |
Ni,28,31–33,38,39,41,45,47 Co,80 Fe,67,74 Ru,90,93 Ag,95–97 Au,100 Fe–Ni,35,49–51,53–59,62,64 Co–Ni,83 Co–Fe,75,77,79–84 Fe–Re,49 (Pr,Ba)Ox103 |
Ellipsoidal |
23 |
Ni,29,30,32,40,46 Co,87,88 Fe,69,72,73 Ru,94 Ag,95 Fe–Ni,58,60,62–64 Co–Fe,53,79,81 Cu,40 Fe–Ni–Re,49 (Fe)–Ni–Mo58 |
Polyhydral |
2 |
Ni45,77 |
Pyramid |
1 |
Ni45 |
Triangular |
1 |
Ni45 |
Trapezoidal |
1 |
Ni78 |
4. Anchorage
The fact that exsolved nanoparticles are (partially) embedded in the host material is one of their main benefits, as this “anchoring” leads to nanoparticles with higher resistance against sintering compared to other methods.15,16,19 This property makes, for instance, catalysts based on perovskite oxides potentially interesting for high-temperature applications, since the catalytically active nanoparticles are anchored and should not be deactivated (as easily).
However, assessing the degree of embedment is often difficult, as one needs good quality TEM images of small areas (like for instance in Fig. 3; whether it is possible to gain information about the degree of anchorage from images of larger areas like in Fig. 6 is open for debate) – i.e. it is necessary to find a particle of interest to focus on first. Moreover, this anchorage is often not explicitly reported, but has to be inferred from the images. We summarised the publications that allow the assessment of the degree of anchorage in Table 4.
Studies that allow meaningful comparisons or the formulation of general trends are still rare: for instance, Zhai et al.64 find similar anchorage (50%) of Fe–Ni nanoparticles independent of reducing atmosphere. Wang et al.40 report slightly more strongly embedded metal particles when increasing the atomic number of the used B-site dopants (Co, Ni, and Cu, respectively). In Islam et al.,65 the nanoparticles exsolved at low temperatures sit on top of the surface, while high temperature nanoparticles exhibit anchorage of about 33%. However, whether those findings point to trends or are just anecdotal cannot be assessed at this point, since the number of data points is still far too low.
5. Summary and outlook
Nanoparticle exsolution on perovskite oxides has been a “hot topic” and focus of extensive research for more than a decade. Potential materials and applications across many fields – most notably catalysis and electrochemistry (both electrolysis and fuel cells) – are heavily researched to make use of the beneficial properties of materials with nanoparticle surface decoration, where the nanoparticles are produced – either via a pre-treatment or in situ – by utilising the exsolution capabilities of perovskite oxides.
Table 4 Overview of degrees of anchorage
Anchorage |
Number of publications |
Element/aloy with references |
On top (0%) |
23 |
Fe–Ni,28,37,53,66,71,93 Ni,33,45,63,64,97 Co–Fe,51,59,83,100 Co,45,60 Fe,67,86 Bi–Fe,52 Co–Ni,82 Fe–Ru,74 Ir99 |
25% |
8 |
Ni,22,45 Co,22 Co–Fe,73 Fe,36 Fe–Ni,65 Fe–Ru,74 Ir99 |
33% |
16 |
Co–Fe,51,60,62,69,70 Fe–Ni,32,46,72,85,94 Ni,47,83 Co,55 Co–Ni,83 SrO78 |
50% |
33 |
Fe–Ni,37,43,46,50,53,66,89,90,100 Ni,24,31,34,41,45,49 Ag,38,44,45,84 Co–Fe,42,62,69,87 Ru,75,83,88 Fe,61,91 Au,95 Cu,22 Cu–Ni,13 Fe–Ni–Re,46 (Pr,Ba)Ox68 |
These beneficial properties (such as for instance high thermal stability of iron-based perovskites, sintering resistance of the nanoparticles, and coking resistance of the surface…) have been proven in a vast number of studies: database searches of “nanoparticle exsolution” and “perovskite” yield thousands of results.
It is quite common to characterise the sample(s) with respect to nanoparticle size or degree of anchoring. That being said, population densities of nanoparticle are not as often investigated: almost all studies collected in this work report particle sizes for at least one material, and roughly 80% of papers provide information about anchorage (if not explicitly stated, it is possible to infer from TEM images). Population density, on the other hand, is only addressed in about a quarter of all publications. Moreover, comparisons across different studies are rarely useful, even if data is available, as a large number of adjustable parameters would need to be controlled, which is usually not the case when comparing multiple studies.
However, comparative investigations of the effects of exsolution parameters (temperature, duration, gas atmosphere…) on the nanoparticles (size, population density, anchorage…) are still scarce. Recently, studies have emerged that look into this connection: for instance, Spring et al.39 showed the influence of reduction temperature and time on the nanoparticle size, Zhang et al.52 observed nanoparticle size and population density changes over time while exposing their sample to humidified H2, Deka et al.57 compared the effect of different exsolution temperatures on the particles size as well as the population density, and Kim et al.45 explored how exsolution temperature and duration affect the shape of the resulting nanoparticles.
As we focussed on a general broad overview over recent studies about exsolved nanoparticles, we omitted more in-depth discussions about mechanisms to exsolution itself, particle growth or shape control. Further analyses with respect to these topics can be found, for instance, in ref. 105 and 106.
As stated before, we strongly believe that more comparative studies such as the aforementioned examples are necessary to understand the interplay between perovskite oxide composition as well as exsolution parameter and the formation of nanoparticles. Achieving such understanding is paramount to be able to even better tailor perovskite oxide-based materials toward their desired applications.
Apart from comparative studies, more complete data sets (ideally even under “standardised” testing conditions) would be highly desirable – aside from particle sizes, population densities and shapes, catalytic tests under reaction/application conditions (in case of potential catalyst materials) as well as long-term stability data would be very useful going forward. Moreover, addressing the issue of reversibility of exsolution could be another highly relevant topic of further studies.
We recognize that providing such comprehensive data for every material under investigation can be tedious (especially as materials, exsolution conditions, and applications vary greatly). However, we believe in the vast potential such a collection of data about exsolution materials (a “library of exsolution materials” as it were) could have. Therefore, we sincerely hope that this article may serve as starting point for further and even more in-depth investigations of this matter.
Author contributions
Conceptualization, C. R.; data curation, T. R. and D. B.; supervision, C. R.; visualization, T. R., D. B. and F. S.; writing – original draft, T. R. and D. B.; writing – review and editing, T. R., F. S. and C. R. All authors have read and agreed to the published version of this manuscript.
Conflicts of interest
There are no conflicts to declare.
Acknowledgements
The authors gratefully acknowledge funding from the European Research Council (ERC) under the European Union's Horizon 2020 research and innovation programme (grant agreement no. 755744/ERC – Starting Grant TUCAS).
Notes and references
- Y. Nishihata, J. Mizuki, T. Akao, H. Tanaka, M. Uenishi, M. Kimura, T. Okamoto and N. Hamada, Nature, 2002, 418, 164–167 CrossRef CAS PubMed.
- J. Hwang, R. R. Rao, L. Giordano, Y. Katayama, Y. Yu and Y. Shao-Horn, Science, 2017, 358, 751–756 CrossRef CAS PubMed.
- R. Thalinger, A. K. Opitz, S. Kogler, M. Heggen, D. Stroppa, D. Schmidmair, R. Tappert, J. Fleig, B. Klotzer and S. Penner, J. Phys. Chem. C, 2015, 119, 11739–11753 CrossRef CAS PubMed.
-
T. Ishihara, Perovskite oxide for solid oxide fuel cells, Springer Science & Business Media, 2009 Search PubMed.
- T. H. Shin, J. H. Myung, M. Verbraeken, G. Kim and J. T. S. Irvine, Faraday Discuss., 2015, 182, 227–239 RSC.
- B. J. Kim, D. H. Kim, Y. Y. Lee, H. W. Shin, G. S. Han, J. S. Hong, K. Mahmood, T. K. Ahn, Y. C. Joo, K. S. Hong, N. G. Park, S. Lee and H. S. Jung, Energy Environ. Sci., 2015, 8, 916–921 RSC.
- T. A. Berhe, W. N. Su, C. H. Chen, C. J. Pan, J. H. Cheng, H. M. Chen, M. C. Tsai, L. Y. Chen, A. A. Dubale and B. J. Hwang, Energy Environ. Sci., 2016, 9, 323–356 RSC.
- A. K. Jena, A. Kulkarni and T. Miyasaka, Chem. Rev., 2019, 119, 3036–3103 CrossRef CAS PubMed.
- B. R. Sutherland and E. H. Sargent, Nat. Photonics, 2016, 10, 295–302 CrossRef CAS.
- S. A. Veldhuis, P. P. Boix, N. Yantara, M. J. Li, T. C. Sum, N. Mathews and S. G. Mhaisalkar, Adv. Mater., 2016, 28, 6804–6834 CrossRef CAS PubMed.
- R. Sarmiento-Perez, T. F. T. Cerqueira, S. Korbel, S. Botti and M. A. L. Marques, Chem. Mater., 2015, 27, 5957–5963 CrossRef CAS.
- T. He, Q. Huang, A. P. Ramirez, Y. Wang, K. A. Regan, N. Rogado, M. A. Hayward, M. K. Haas, J. S. Slusky, K. Inumara, H. W. Zandbergen, N. P. Ong and R. J. Cava, Nature, 2001, 411, 54–56 CrossRef CAS PubMed.
- L. Lindenthal, J. Popovic, R. Rameshan, J. Huber, F. Schrenk, T. Ruh, A. Nenning, S. Löffler, A. K. Opitz and C. Rameshan, Appl. Catal., B, 2021, 292, 120183 CrossRef CAS.
- F. Schrenk, L. Lindenthal, H. Drexler, R. Rameshan, H. Summerer, T. Berger, T. Ruh, A. K. Opitz and C. Rameshan, Appl. Catal., B, 2022, 318, 121886 CrossRef CAS.
- D. Neagu, T. S. Oh, D. N. Miller, H. Menard, S. M. Bukhari, S. R. Gamble, R. J. Gorte, J. M. Vohs and J. T. S. Irvine, Nat. Commun., 2015, 6, 8120 CrossRef PubMed.
- D. Neagu, G. Tsekouras, D. N. Miller, H. Menard and J. T. S. Irvine, Nat. Chem., 2013, 5, 916–923 CrossRef CAS PubMed.
- O. Kwon, S. Sengodan, K. Kim, G. Kim, H. Y. Jeong, J. Shin, Y. W. Ju and J. W. Han, Nat. Commun., 2017, 8, 15967 CrossRef CAS PubMed.
- J. M. Haag, S. A. Barnett, J. W. Richardson and K. R. Poeppelmeier, Chem. Mater., 2010, 22, 3283–3289 CrossRef CAS.
- T. S. Oh, E. K. Rahani, D. Neagu, J. T. S. Irvine, V. B. Shenoy, R. J. Gorte and J. M. Vohs, J. Phys. Chem. Lett., 2015, 6, 5106–5110 CrossRef CAS PubMed.
- M. B. Katz, S. Y. Zhang, Y. W. Duan, H. J. Wang, M. H. Fang, K. Zhang, B. H. Li, G. W. Graham and X. Q. Pan, J. Catal., 2012, 293, 145–148 CrossRef CAS.
- R. Rameshan, A. Nenning, J. Raschhofer, L. Lindenthal, T. Ruh, H. Summerer, A. K. Opitz, T. M. Huber and C. Rameshan, Crystals, 2020, 10, 947 CrossRef CAS.
- W. W. Fan, Z. Sun and Y. Bai, Small, 2022, 18, 2107131 CrossRef CAS PubMed.
- L. Lindenthal, J. Huber, H. Drexler, T. Ruh, R. Rameshan, F. Schrenk, S. Loeffler and C. Rameshan, Catalysts, 2021, 11, 1484 CrossRef CAS.
- L. Lindenthal, T. Ruh, R. Rameshan, H. Summerer, A. Nenning, C. Herzig, S. Loffler, A. Limbeck, A. K. Opitz, P. Blaha and C. Rameshan, Acta Crystallogr., Sect. B: Struct. Sci., Cryst. Eng. Mater., 2020, 76, 1055–1070 CrossRef CAS PubMed.
- H. Tanaka, M. Taniguchi, M. Uenishi, N. Kajita, I. Tan, Y. Nishihata, J. Mizuki, K. Narita, M. Kimura and K. Kaneko, Angew. Chem., Int. Ed., 2006, 45, 5998–6002 CrossRef CAS PubMed.
-
P. J. Goodhew and J. Humphreys, Electron microscopy and analysis, CRC press, 2000 Search PubMed.
- Y. Gao, D. J. Chen, M. Saccoccio, Z. H. Lu and F. Ciucci, Nano Energy, 2016, 27, 499–508 CrossRef CAS.
- G. M. Yang, W. Zhou, M. L. Liu and Z. P. Shao, ACS Appl. Mater. Interfaces, 2016, 8, 35308–35314 CrossRef CAS PubMed.
- L. T. Ye, M. Y. Zhang, P. Huang, G. C. Guo, M. C. Hong, C. S. Li, J. T. S. Irvine and K. Xie, Nat. Commun., 2017, 8, 14785 CrossRef CAS PubMed.
- Y. Gao, Z. H. Lu, T. L. You, J. Wang, L. Xie, J. Q. He and F. Ciucci, J. Phys. Chem. Lett., 2018, 9, 3772–3778 CrossRef CAS PubMed.
- V. Kyriakou, D. Neagu, E. I. Papaioannou, I. S. Metcalfe, M. C. M. van de Sanden and M. N. Tsampas, Appl. Catal., B, 2019, 258, 117950 CrossRef CAS.
- D. Neagu, V. Kyriakou, I. L. Roiban, M. Aouine, C. Y. Tang, A. Caravaca, K. Kousi, I. Schreur-Piet, I. S. Metcalfe, P. Vernoux, M. C. M. van de Sanden and M. N. Tsampas, ACS Nano, 2019, 13, 12996–13005 CrossRef CAS PubMed.
- Y. H. Wan, Y.
L. Xing, Y. Xie, N. Shi, J. Xu and C. R. Xia, ACS Appl. Mater. Interfaces, 2019, 11, 42271–42279 CrossRef CAS PubMed.
- Z. Chen, B. Hua, X. Zhang, L. F. Chen, Y. Q. Zhang, G. M. Yang, G. Wan, H. Zhou, Y. L. Yang, J. Chen, H. Q. Fan, Q. Li, M. Li, J. H. Li, W. Zhou, Z. P. Shao, J. L. Luo and Y. F. Sun, Cell Rep. Phys. Sci., 2020, 1, 100243 CrossRef.
- S. Joo, A. Seong, O. Kwon, K. Kim, J. H. Lee, R. J. Gorte, J. M. Vohs, J. W. Han and G. Kim, Sci. Adv., 2020, 6, eabb1573 CrossRef CAS PubMed.
- K. Kousi, D. Neagu and I. S. Metcalfe, Catalysts, 2020, 10, 468 CrossRef CAS.
- Z. J. Liu, M. Y. Zhou, M. L. Chen, D. Cao, J. Shao, M. L. Liu and J. Liu, Ceram. Int., 2020, 46, 19952–19959 CrossRef CAS.
- N. Shi, S. S. Xue, Y. Xie, Y. Yang, D. M. Huan, Y. Pan, R. R. Peng, C. R. Xia, Z. L. Zhan and Y. L. Lu, Appl. Catal., B, 2020, 272, 118973 CrossRef CAS.
- J. Spring, E. Sediva, Z. D. Hood, J. C. Gonzalez-Rosillo, W. O’Leary, K. J. Kim, A. J. Carrillo and J. L. M. Rupp, Small, 2020, 16, 2003224 CrossRef CAS PubMed.
- J. K. Wang, J. Zhou, J. M. Yang, Z. Zong, L. Fu, Z. J. Lian, X. C. Zhang, X. Wang, C. X. Chen, W. L. Ma and K. Wu, Renewable Energy, 2020, 157, 840–850 CrossRef CAS.
- S. Yu, D. Yoon, Y. Lee, H. Yoon, H. Han, N. Kim, C. J. Kim, K. Ihm, T. S. Oh and J. Son, Nano Lett., 2020, 20, 3538–3544 CrossRef CAS PubMed.
- D. M. Amaya-Duenas, G. X. Chen, A. Weidenkaff, N. Sata, F. Han, I. Biswas, R. Costa and K. A. Friedrich, J. Mater. Chem. A, 2021, 9, 5685–5701 RSC.
- M. R. Bin Mamtaz, Z. Wang, A. Belotti, E. Quattrocchi, J. Yu, J. P. Liu and F. Ciucci, Energy Fuels, 2021, 35, 15084–15093 CrossRef CAS.
- V. Kyriakou, R. K. Sharma, D. Neagu, F. Peeters, O. De Luca, P. Rudolf, A. Pandiyan, W. Yu, S. W. Cha, S. Welzel, M. C. M. van de Sanden and M. N. Tsampas, Small Methods, 2021, 5, 2100868 CrossRef CAS PubMed.
- Y. H. Kim, Y. Kang, S. Jo, H. Jeong, D. Neagu and J. H. Myung, Chem. Eng. J., 2022, 441, 136025 CrossRef CAS.
- Z. Sun, W. W. Fan and Y. Bai, Adv. Sci., 2022, 9, 2200250 CrossRef CAS PubMed.
- J. R. Wang, M. M. Wang, J. C. Xiao, J. M. Dong, Y. X. Li, L. M. Zhang, J. T. Si, B. C. Pan, C. S. Chen and C. H. Chen, Nano Energy, 2022, 94, 106972 CrossRef CAS.
- N. Wu, W. Wang, Y. J. Zhong, G. M. Yang, J. F. Qu and Z. P. Shao, ChemElectroChem, 2017, 4, 2378–2384 CrossRef CAS.
- D. Zubenko, S. Singh and B. A. Rosen, Appl. Catal., B, 2017, 209, 711–719 CrossRef CAS.
- T. L. Zhu, H. E. Troiani, L. V. Mogni, M. F. Han and S. A. Barnett, Joule, 2018, 2, 478–496 CrossRef CAS.
- D. Papargyriou, D. N. Miller and J. T. S. Irvine, J. Mater. Chem. A, 2019, 7, 15812–15822 RSC.
- T. H. Zhang, Y. Q. Zhao, X. Y. Zhang, H. Zhang, N. Yu, T. Liu and Y. Wang, ACS Sustainable Chem. Eng., 2019, 7, 17834–17844 CrossRef CAS.
- H. D. Li, Y. F. Song, M. G. Xu, W. Wang, R. Ran, W. Zhou and Z. P. Shao, Energy Fuels, 2020, 34, 11449–11457 CrossRef CAS.
- X. Wu, Y. Yu, Y. Chen, L. S. Li, Z. F. Ma and Y. M. Yin, ACS Appl. Mater. Interfaces, 2020, 12, 34890–34900 CrossRef CAS PubMed.
- L. Z. Bian, C. C. Duan, L. J. Wang, Z. Y. Chen, Y. T. Hou, J. Peng, X. W. Song, S. L. An and R. O’Hayre, J. Power Sources, 2021, 482, 228887 CrossRef CAS.
- A. J. Carrillo and J. M. Serra, Catalysts, 2021, 11, 741 CrossRef CAS.
- D. J. Deka, J. Kim, S. Gunduz, M. Aouine, J. M. M. Millet, A. C. Co and U. S. Ozkan, Appl. Catal., B, 2021, 286, 119917 CrossRef CAS.
- S. A. Horlick, Y. L. Huang, I. A. Robinson and E. D. Wachsman, Nano Energy, 2021, 87, 106193 CrossRef CAS.
- R. Huang, C. Lim, M. G. Jang, J. Y. Hwang and J. W. Han, J. Catal., 2021, 400, 148–159 CrossRef CAS.
- J. S. Xu, M. Wu, Z. Y. Song, Y. Chen, L. L. Zhang, L. Wang, H. D. Cai, X. G. Su, X. Han, S. B. Wang and W. Long, J. Eur. Ceram. Soc., 2021, 41, 4537–4551 CrossRef CAS.
- L. J. Zhang, Y. H. Li, B. Z. Zhang, Y. H. Wan, Z. Q. Xu, S. W. Zhang, T. L. Zhu and C. R. Xia, Int. J. Energy Res., 2021, 45, 21264–21273 CrossRef CAS.
- H. M. Ansari, A. S. Bass, N. Ahmad and V. I. Birss, J. Mater. Chem. A, 2022, 10, 2280–2294 RSC.
- Y. H. Li, Y. P. Li, S. W. Zhang, C. Ren, Y. F. Jing, F. P. Cheng, Q. X. Wu, P. Lund and L. D. Fan, ACS Appl. Mater. Interfaces, 2022, 14, 9138–9150 CrossRef CAS PubMed.
- S. Zhai, H. P. Xie, B. Chen and M. Ni, Chem. Eng. J., 2022, 430, 132615 CrossRef CAS.
- Q. A. Islam, R. Majee and S. Bhattacharyya, J. Mater. Chem. A, 2019, 7, 19453–19464 RSC.
- X. R. Zhang, L. T. Ye and K. Xie, Energy Fuels, 2022, 36, 11576–11583 CrossRef CAS.
- L. H. Chen, J. Xu, X. Wang and K. Xie, Int. J. Hydrogen Energy, 2020, 45, 11901–11907 CrossRef CAS.
- L. Lindenthal, R. Rameshan, H. Summerer, T. Ruh, J. Popovic, A. Nenning, S. Loffler, A. K. Opitz, P. Blaha and C. Rameshan, Catalysts, 2020, 10, 268 CrossRef CAS.
- H. Kim, C. Lim, O. Kwon, J. Oh, M. T. Curnan, H. Y. Jeong, S. Choi, J. W. Han and G. Kim, Nat. Commun., 2021, 12, 6814 CrossRef CAS PubMed.
- N. Sun, F. J. Jin, X. L. Liu, X. W. Liu, J. X. Li, Y. Shen, F. Wang, X. Y. Chu, Z. Wu, J. H. Li and X. L. Lv, ACS Appl. Energy Mater., 2021, 4, 7992–8002 CrossRef CAS.
- A. K. Opitz, A. Nenning, V. Vonk, S. Volkov, F. Bertram, H. Summerer, S. Schwarz, A. Steiger-Thirsfeld, J. Bernardi, A. Stierle and J. Fleig, Nat. Commun., 2020, 11, 4801 CrossRef CAS PubMed.
- J. Y. Wang, J. Yang, A. K. Opitz, W. Bowman, R. Bliem, G. Dimitrakopoulos, A. Nenning, I. Waluyo, A. Hunt, J. J. Gallet and B. Yildiz, Chem. Mater., 2021, 33, 5021–5034 CrossRef CAS.
- Z. S. Wang, Z. Y. Hao, F. Shi, K. Y. Zhu, X. F. Zhu and W. S. Yang, J. Energy Chem., 2022, 69, 434–441 CrossRef CAS.
- Y. K. Zhang, Y. H. Xu and L. Z. Gan, J. Solid State Electrochem., 2022, 26, 409–417 CrossRef CAS.
- N. J. Hou, T. T. Yao, P. Li, X. L. Yao, T. Gan, L. J. Fan, J. Wang, X. J. Zhi, Y. C. Zhao and Y. D. Li, ACS Appl. Mater. Interfaces, 2019, 11, 6995–7005 CrossRef CAS PubMed.
- K. Shao, F. J. Li, G. H. Zhang, Q. L. Zhang, K. Maliutina and L. D. Fan, ACS Appl. Mater. Interfaces, 2019, 11, 27924–27933 CrossRef CAS PubMed.
- T. L. Zhu, X. Y. Chen, W. J. Ni, Q. Zhong and M. F. Han, Int. J. Hydrogen Energy, 2019, 44, 31386–31393 CrossRef CAS.
- Y. L. Jiang, Z. B. Geng, Y. Sun, X. Y. Wang, K. K. Huang, Y. G. Cong, F. B. Shi, Y. Wang, W. Zhang and S. H. Feng, ACS Sustainable Chem. Eng., 2020, 8, 302–310 CrossRef CAS.
- J. N. Song, T. L. Zhu, X. Y. Chen, W. J. Ni and Q. Zhong, J. Materiomics, 2020, 6, 377–384 CrossRef.
- W. W. Zhang, H. C. Wang, K. Guan, J. L. Meng, Z. Y. Wei, X. J. Liu and J. Meng, ACS Appl. Mater. Interfaces, 2020, 12, 461–473 CrossRef CAS PubMed.
- Z. H. Du, Y. Gong, H. L. Zhao, Y. Zhang, S. Yi and L. Gu, ACS Appl. Mater. Interfaces, 2021, 13, 3287–3294 CrossRef CAS PubMed.
- J. D. Jiang, Y. Zhang, X. Yang, Y. Shen and T. M. He, ACS Appl. Energy Mater., 2021, 4, 134–145 CrossRef CAS.
- Z. Sun, W. W. Fan, Y. Bai, K. Wu and Y. H. Cheng, ACS Appl. Mater. Interfaces, 2021, 13, 29755–29763 CrossRef CAS PubMed.
- H. B. Hu, M. Z. Li, H. H. Min, X. H. Zhou, J. Li, X. Y. Wang, Y. Lu and X. F. Ding, ACS Catal., 2022, 12, 828–836 CrossRef CAS.
- H. F. Lv, L. Lin, X. M. Zhang, R. T. Li, Y. F. Song, H. Matsumoto, N. Ta, C. B. Zeng, Q. Fu, G. X. Wang and X. H. Bao, Nat. Commun., 2021, 12, 5665 CrossRef CAS PubMed.
- S. B. Liu, Q. X. Liu, X. Z. Fu and J. L. Luo, Appl. Catal., B, 2018, 220, 283–289 CrossRef CAS.
- Y. R. Yang, Y. R. Wang, Z. B. Yang, Z. Lei, C. Jin, Y. D. Liu, Y. H. Wang and S. P. Peng, J. Power Sources, 2019, 438, 226989 CrossRef CAS.
- Y. R. Yang, Y. H. Wang, Z. B. Yang, Y. Chen and S. P. Peng, J. Power Sources, 2020, 478, 229082 CrossRef CAS.
- C. M. Xu, W. Sun, R. Z. Ren, X. X. Yang, M. J. Ma, J. S. Qiao, Z. H. Wang, S. Y. Zhen and K. N. Sun, Appl. Catal., B, 2021, 282, 119553 CrossRef CAS.
- R. Glaser, T. Zhu, H. Troiani, A. Caneiro, L. Mogni and S. Barnett, J. Mater. Chem. A, 2018, 6, 5193–5201 RSC.
- W. W. Fan, Z. Sun, Y. Bai, K. Wu and Y. H. Cheng, ACS Appl. Mater. Interfaces, 2019, 11, 23168–23179 CrossRef CAS PubMed.
- W. W. Fan, Z. Sun, Y. Bai, K. Wu, J. Zhou and Y. H. Cheng, J. Power Sources, 2020, 456, 228000 CrossRef CAS.
- A. J. Carrillo, L. Navarrete, M. Laqdiem, M. Balaguer and J. M. Serra, Mater. Adv., 2021, 2, 2924–2934 RSC.
- L. Fu, J. Zhou, L. K. Zhou, J. M. Yang, Z. R. Liu, K. Wu, H. F. Zhao, J. K. Wang and K. Wu, Chem. Eng. J., 2021, 418, 129422 CrossRef CAS.
- X. Li, L. Dai, Z. X. He, W. Meng, Y. H. Li and L. Wang, Sens. Actuators, B, 2019, 298, 126854 CrossRef CAS.
- M. G. Xu, W. Wang, Y. J. Zhong, X. M. Xu, J. Wang, W. Zhou and Z. P. Shao, J. Mater. Chem. A, 2019, 7, 17489–17497 RSC.
- J. H. Kim, J. Hong, D. K. Lim, S. Ahn, J. Kim, J. K. Kim, D. Oh, S. Jeon, S. J. Song and W. Jung, Energy Environ. Sci., 2022, 15, 1097–1105 RSC.
- L. Zhang, Y. L. Yang, J. S. Tian, J. H. Li, G. Chen, L. J. Zhou, Y. F. Sun and Y. F. Qiu, ChemSusChem, 2022, 15, e202102729 CAS.
- L. Fu, J. Zhou, J. M. Yang, Z. J. Lian, J. K. Wang, Y. H. Cheng and K. Wu, Appl. Surf. Sci., 2020, 511, 145525 CrossRef CAS.
- Y. Gao, C. Xing, S. Q. Hu and S. G. Zhang, J. Mater. Chem. A, 2021, 9, 10374–10384 RSC.
- E. Cali, G. Kerherve, F. Naufal, K. Kousi, D. Neagu, E. I. Papaioannou, M. P. Thomas, B. S. Guiton, I. S. Metcalfe, J. T. S. Irvine and D. J. Payne, ACS Appl. Mater. Interfaces, 2020, 12, 37444–37453 CrossRef CAS PubMed.
- V. Kyriakou, D. Neagu, G. Zafeiropoulos, R. K. Sharma, C. Y. Tang, K. Kousi, I. S. Metcalfe, M. C. M. van de Sanden and M. N. Tsampas, ACS Catal., 2020, 10, 1278–1288 CrossRef CAS.
- Y. J. Zhu, T. Liu, Y. Wang, X. Y. Zhang, C. Ren, W. L. Li and S. M. Wang, Sustainable Energy Fuels, 2022, 6, 1373–1381 RSC.
- L. T. Ye, C. C. Pan, M. Y. Zhang, C. S. Li, F. L. Chen, L. Z. Gan and K. Xie, ACS Appl. Mater. Interfaces, 2017, 9, 25350–25357 CrossRef CAS PubMed.
- J. H. Kim, J. K. Kim, J. Liu, A. Curcio, J.-S. Jang, I.-D. Kim, F. Giucci and W. Jung, ACS Nano, 2015, 15, 81–110 CrossRef PubMed.
- D. Neagu, T.-S. Oh, D. N. Miller, H. Ménard, S. M. Bukhari, S. R. Gamble, R. J. Gorte, J. M. Vohs and J. T. S. Irvine, Nat. Commun., 2015, 6, 8120 CrossRef PubMed.
Footnotes |
† These authors contributed equally. Shared first authors. |
‡ https://www.webofscience.com by Clarivate Analytics. |
§ https://scholar.google.com. |
|
This journal is © The Royal Society of Chemistry 2023 |
Click here to see how this site uses Cookies. View our privacy policy here.