DOI:
10.1039/D3EY00005B
(Communication)
EES Catal., 2023,
1, 250-254
Direct electrocatalytic conversion of crude syngas to ethylene via a multi-process coupled device†
Received
12th January 2023
, Accepted 14th February 2023
First published on 16th February 2023
Abstract
Direct electrocatalytic conversion of crude syngas is an economical and ideal strategy for producing value-added ethylene without CO2 emission, which can directly use H2O instead of H2 as the clean hydrogen source at atmospheric pressure and room temperature. However, H2S impurities in the syngas inevitably poison the catalysts and the sluggish anodic oxygen evolution reaction induces substantial electricity losses, which largely hinder the overall efficiency of the electrolysis process. Herein, we developed an energy-saving carbon reduction multi-process coupled electrolysis device for the conversion of H2S-containing syngas, which not only realized a high faradaic efficiency (FE) of ethylene with the removal of H2S impurities but also increased the ratio of H2/CO in the residual syngas and reduced the total energy consumption of electrolysis. This “Four in One” device can typically remove 10% H2S from syngas and obtain an ethylene FE of up to 49.7%, which saves 46.5% energy as compared to the uncoupled device.
Broader context
Ethylene (C2H4) constitutes the most predominant olefin in the global market and is primarily produced through steam cracking of naphtha and gas oil. With conventional oil reserves dwindling, Fischer–Tropsch synthesis (FTS) process provides an alternative approach for C2H4 production from the coal derived syngas (CO + H2). While the selectivity of C2H4 from the FTS process is often less than 30% accompanied by high temperatures (200–450 °C) and high pressures (5–50 bar). Electrocatalytic conversion of syngas presents a promising way for C2H4 production under mild reaction conditions at room temperature (25 °C) and atmospheric pressure (1 bar). However, H2S impurities in the crude syngas inevitably poison the catalysts and the sluggish anodic oxygen evolution reaction induces substantial electricity losses. Herein, we develop a multi-process coupled device for the direct electrolysis of H2S-containing syngas to produce ethylene, which not only realized 75.0% C2H4 selectivity by removing H2S impurities but also increased the ratio of H2/CO in the residual syngas and saved 46.5% energy for C2H4 production. This multi-process coupled device provides a new route for converting crude syngas to prepare valuable chemicals.
|
Introduction
Conversion of syngas (CO + H2) to ethylene via Fischer–Tropsch synthesis (FTS) provides an important pathway for producing high-valued chemicals from coal or natural gas, which typically requires high temperatures (200–450 °C) and high pressures (5–50 bar).1–3 Apart from these harsh reaction conditions, the selectivity of ethylene from the FTS process is often less than 30% according to the Anderson–Schulz–Flory distribution, leading to further complex processes for product separation.4–6 Different from the FTS, the electrocatalytic conversion of syngas to produce ethylene proceeds under mild conditions at atmospheric pressure and room temperature, which can directly use H2O instead of H2 as the clean hydrogen source.7,8 Moreover, the electroreduction process can deliver much higher ethylene selectivity and produce no CO2 emissions directly compared with the FTS.9,10 As a more economical and ecofriendly way, preparing ethylene by the electrolysis of syngas has attracted wide attention.
Many efforts have been devoted to improving the electrolytic efficiency of ethylene production, including searching for better electrocatalysts to increase the ethylene yield11–13 and designing electrolyzers with lower resistance and higher reactant concentration.7,9 While pure CO was always employed as the reaction gas,7 the direct electrolysis of crude syngas has not been reported until now due to its complex components. Hydrogen sulfide (H2S), as the main impurity (even exceeding 10%) contained in the crude syngas, significantly decreases the catalytic activity for ethylene production due to its poisoning of the catalysts.14–17 Besides, the sluggish half-reaction of oxygen evolution reaction (OER) always proceeds over 1.23 V at the anode, causing high energy consumption of the total electrolysis process.18,19 Therefore, it is of great significance to produce ethylene via direct electrolysis of crude syngas with lower energy consumption, which requires innovative catalytic processes.
Herein, we design a multi-process coupled device for the direct electrolysis of H2S-containing syngas to produce ethylene. It integrates the process of H2S elimination and ethylene production into one electrolytic device by carrying out the sulfide oxidation reaction (SOR) at the anode and CO reduction reaction (CORR) at the cathode (Fig. 1a). Specifically, the H2S-containing syngas is firstly bubbled through the anodic electrolyte, and the graphene encapsulating CoNi alloy nanoparticles supported on the Ni foam can catalyze the electro-oxidation of H2S into sulfur. The SOR process can completely eliminate H2S impurities from the crude syngas. Next, the purified syngas is fed into the cathodic electrolyte, which can be electro-reduced to ethylene efficiently by copper particles supported on the carbon paper. Significantly, the ratio of H2/CO in the residual syngas increases rather than decreases and is caused by the competitive hydrogen evolution reaction (HER) process and water as the hydrogen source for ethylene production. Furthermore, the substitution of SOR with OER substantially reduces the anodic potential, thereby decreasing the total energy consumption of syngas electrolysis. In brief, this multi-process coupled device integrates four functions in one device, including i) the removal of H2S, ii) the high efficiency of ethylene production, iii) the increase of H2 content in the residual syngas, and iv) the reduction of energy consumption for ethylene production. Typically, by electrolyzing the 10% H2S-containing syngas, it can remove H2S impurities completely and obtain an ethylene faradaic efficiency (FE) of up to 49.7%, saving 46.5% energy as compared to the uncoupled device (Fig. 1b).
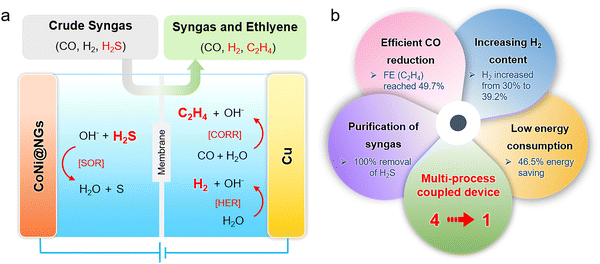 |
| Fig. 1 The multi-process coupled device of crude syngas electrolysis. (a) A schematic of the multi-process coupled device. CoNi@NGs and Cu catalysts are used as anodic and cathodic catalysts, respectively. The crude syngas is first bubbled to the anodic chamber, where the SOR occurs to remove H2S. Then, the outflow is bubbled to the cathodic chamber, where the CORR occurs to generate C2H4 and HER to produce H2. (b) Four functions integrated into a multi-process coupled device for the direct electrolysis of crude syngas. Data in (b) from the electrolysis results of 10% H2S-containing syngas. | |
Results and discussion
A schematic of the multi-process coupled device, shown in Fig. 1a, presents that the double-cell electrolyzer is separated by a Nafion 117 proton exchange membrane to form cathode and anode chambers with 1 M NaOH as the electrolyte. Compared to the commercial 40% Pt/C, graphene, carbon nanotubes (CNTs), and cobalt and nickel oxide nanoparticles supported on carbon nanotubes (CoNiOx-CNTs) as anodic catalysts, robust single-layer graphene shell encapsulating CoNi alloy nanoparticles (CoNi@NGs) deliver a much higher activity for electrocatalytic oxidation of H2S with excellent stability (Fig. S1–S8, ESI†). The CoNi alloy nanoparticles with an average size of 5 nm were physically isolated from the reaction medium by the graphene shell (Fig. S2 and S3, ESI†), for which the electrocatalytic oxidation of H2S occurs on the graphene shell and catalytic activity arises from the electron transfer from CoNi nanoparticles to the graphene shell.16,20 Copper particles with around 10 μm size supported on carbon paper act as the cathode (Fig. S9 and S10, ESI†). In the electrolysis process, the crude syngas containing CO, H2, and H2S is firstly bubbled through the anodic electrolyte and then to the cathodic electrolyte. In the anodic chamber, H2S impurities are absorbed by the alkaline electrolyte to form S2− and then rapidly electro-oxidized to produce sulfur by the SOR reaction [eqn (1)]. Subsequently, the purified syngas is fed into the cathodic electrolyte. The combined occurrence of the CORR and HER are catalyzed by the Cu catalyst [eqn (2) and (3)]. As a result, the H2S-containing syngas is converted to ethylene, and the residual syngas possesses a higher ratio of H2/CO without H2S, which is a high-quality feedstock gas for preparing highly value-added chemicals. | [SOR] H2S + 2OH− → S + 2H2O + 2e− | (1) |
| [CORR] 2CO + 6H2O + 8e− → C2H4 + 8OH− | (2) |
| [HER] 2H2O + 2e− → H2 + 2OH− | (3) |
For the ease of evaluation of the catalytic performance of the multi-process coupled device, experiments are carried out under simulated conditions with the mixture of 1 M NaOH and 1 M Na2S as the anodic electrolyte and 1 M NaOH as the cathodic electrolyte in a two-electrode system. The reactions of SOR and CORR occur at the anode and cathode, respectively. In contrast, the uncoupled device uses 1 M NaOH as the electrolyte for the anode and cathode for the OER and CORR, respectively. As shown in Fig. 2a and Fig. S11 (ESI†), the driving potentials of SOR-CORR in the coupled device are at least 1.2 V lower than the potentials of OER-CORR in the uncoupled device between 5 and 100 mA cm−2. Moreover, the driving potentials remain steady during the 24 h galvanostatic tests (Fig. 2b and Fig. S12, ESI†). Furthermore, qualitative and quantitative analyses present that the highest FE of C2H4 can reach 45.7% at the current density of 10 mA cm−2, which is comparable to the uncoupled device with a C2H4 FE of 47.4% (Fig. 2c and Fig. S13 and S14, ESI†). Consequently, the energy consumption of producing C2H4 is only 21.0 kW h m−3 in the SOR-CORR process at the current density of 10 mA cm−2 but 43.3 kW h m−3 in the OER-CORR process, indicating that the multi-process coupled device consumes lower energy than the uncoupled device for C2H4 production (Fig. 2d). The optimal selectivity of ethylene based on CO conversion can reach over 74.5% at the current density of 20 mA cm−2, breaking the 30% selectivity limitation from CO to C2 hydrocarbons in the traditional FTS process (Fig. S15, ESI†). These results demonstrated that the multi-process coupled device achieves the low-cost and high-efficient production of C2H4via direct electrolysis of crude syngas.
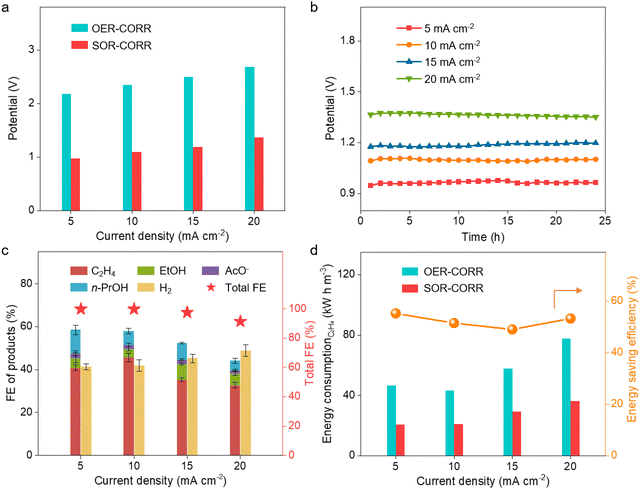 |
| Fig. 2 Performance of the multi-process coupled device. (a) Comparison of the driving potentials for SOR-CORR and OER-CORR at current densities from 5 to 20 mA cm−2. (b) Galvanostatic tests for the multi-process coupled device in the SOR-CORR process. (c) The FE of CORR products at the cathode. (d) The energy consumption of C2H4 production and energy saving efficiency in the SOR-CORR process in contrast to the OER-CORR process. All the experiments are carried out at 25 °C. | |
To further verify the feasibility of the multi-process coupled device, we evaluate the performance of direct electrolysis of H2S-containing syngas to produce ethylene with different H2S and CO contents. As shown in Fig. 3a, there is no response current for CO and H2 electro-oxidation below 1.3 V, indicating that CO and H2 in the syngas cannot be consumed at the anode. In contrast, the high response currents for the 2% and 10% H2S-containing syngas are observed below 1 V, which corresponds to the efficient electro-oxidation of H2S to sulfur. When dealing with H2S-containing syngas, the optimal FE and selectivity of ethylene can reach 49.7% and 75.0% at 10 mA cm−2 in the multi-process coupled device, respectively. It is noteworthy that the coupled device still delivers comparable ethylene FE but much lower driving potentials than the uncoupled device in a wide range of current density from 5 to 20 mA cm−2 when the content of H2S increases from 0% to 10% (Fig. 3b and c and Fig. S16 and Tables S1–S3, ESI†). Moreover, with the increase of H2 to CO ratio from 1
:
2 to 1
:
1, no obvious difference in the driving potentials and FE of ethylene could be observed at a current density of 10 mA cm−2 for the coupled device (Fig. S17, ESI†). These results demonstrate that the multi-process coupled device can handle a wide range of H2S-containing syngas and maintain high efficiency for ethylene production. Further analysis of the energy consumption of ethylene production indicates that 40.5 kW h is needed to produce one stere ethylene for the OER-CORR process at the current density of 10 mA cm−2, while 21.7 kW h is needed for the SOR-CORR process when dealing with 10% H2S-containing syngas (Fig. 3d). These results indicate that 46.5% of electrical energy can be effectively saved when dealing with 10% H2S-containing syngas. Moreover, the content of H2 can even be increased from 30% to 39.2% at the current density of 20 mA cm−2, which is favorable for converting syngas into highly value-added chemicals (Fig. 3e). The composition of effluent gas from the cathodic chamber is further analyzed by real-time mass spectrometry. No signal of H2S in the tail gas is observed, indicating that H2S impurities can be fully removed via the multi-process coupled device (Fig. 3f).
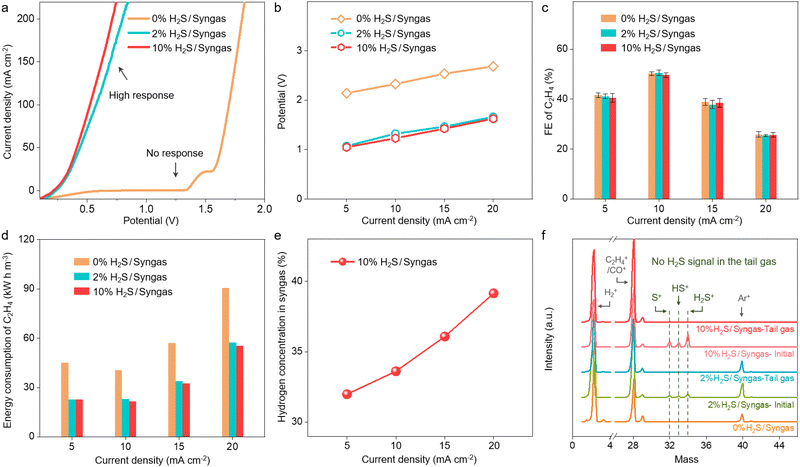 |
| Fig. 3 The performance of the multi-process coupled device when dealing with syngas with different H2S contents. (a) The linear sweep voltammetry curves with different contents of H2S-containing syngas as the reaction gas. (b) The potentials of the multi-process coupled device at current densities from 5 to 20 mA cm−2. (c) The FE and energy consumption (d) for C2H4 production by electrolysis of different contents of H2S-containing syngas. (e) H2 concentration in the residual syngas after electrolyzing 10% H2S-containing syngas in the multi-process coupled device. (f) Analysis of the composition of the residual syngas from cathodic chamber by real-time mass spectrometry. All the experiments are carried out in 1 M NaOH electrolyte at 25 °C. | |
Conclusions
In summary, we have designed a “Four in One” multi-process coupled device to directly electrolyze H2S-containing syngas for ethylene production, which integrates the process of H2S elimination and ethylene production into one electrolytic device by proceeding with the SOR at the anode and CORR at the cathode. The FE of ethylene can reach up to 49.7%, and the content of H2 can increase from 30% to 39.2% when dealing with 10% H2S-containing syngas via the multi-process coupled electrolysis device. Moreover, 46.5% of the electrical energy can be effectively saved when producing one stere ethylene in contrast to the traditional OER-CORR process. This efficient multi-process coupled electrolysis device provides a promising route for the direct conversion of crude syngas to produce valuable chemicals.
Author contributions
D. D. and X. C. conceived the project and designed the experiments. M. Z., R. C., S. W. and Y. T. performed the materials synthesis, characterization, and electrochemical measurements. M. Z., X. C. and D. D. co-wrote the manuscript.
Conflicts of interest
There are no conflicts to declare.
Acknowledgements
We gratefully acknowledge the financial support from the National Key R&D Program of China (No. 2022YFA1504500), the National Natural Science Foundation of China (No. 21890753, 21988101, 22225204, 22102184, and 22209170), the Strategic Priority Research Program of the Chinese Academy of Sciences (No. XDB36030200), the CAS Project for Young Scientists in Basic Research (No. YSBR-028), and China Postdoctoral Science Foundation (No. 2021M703146).
References
- H. M. Torres Galvis and K. P. de Jong, ACS Catal., 2013, 3, 2130–2149 CrossRef CAS.
- V. Dieterich, A. Buttler, A. Hanel, H. Spliethoff and S. Fendt, Energy Environ. Sci., 2020, 13, 3207–3252 RSC.
- Y. Liu, D. Deng and X. Bao, Chemistry, 2020, 6, 2497–2514 CrossRef CAS.
- F. Jiao, J. Li, X. Pan, J. Xiao, H. Li, H. Ma, M. Wei, Y. Pan, Z. Zhou, M. Li, S. Miao, J. Li, Y. Zhu, D. Xiao, T. He, J. Yang, F. Qi, Q. Fu and X. Bao, Science, 2016, 351, 1065–1068 CrossRef CAS PubMed.
- G. Henrici-Olivé and S. Olivé, Angew. Chem., Int. Ed. Engl., 1976, 15, 136–141 CrossRef.
- Y. Yao, D. J. Graziano, M. Riddle, J. Cresko and E. Masanet, Ind. Eng. Chem. Res., 2015, 55, 3493–3505 CrossRef.
- M. Jouny, G. S. Hutchings and F. Jiao, Nat. Catal., 2019, 2, 1062–1070 CrossRef CAS.
- S. Sarkar, J. Raj, D. Bagchi, A. Cherevotan, C. P. Vinod and S. C. Peter, EES Catalysis, 2023 10.1039/d2ey00081d.
- M. Jouny, W. Luc and F. Jiao, Nat. Catal., 2018, 1, 748–755 CrossRef CAS.
- J. Li, Z. Wang, C. McCallum, Y. Xu, F. Li, Y. Wang, C. M. Gabardo, C.-T. Dinh, T.-T. Zhuang, L. Wang, J. Y. Howe, Y. Ren, E. H. Sargent and D. Sinton, Nat. Catal., 2019, 2, 1124–1131 CrossRef CAS.
- R. Chen, H. Y. Su, D. Liu, R. Huang, X. Meng, X. Cui, Z. Q. Tian, D. H. Zhang and D. Deng, Angew. Chem., Int. Ed., 2020, 59, 154–160 CrossRef CAS PubMed.
- X. Lyu, J. Li, T. Zhang, Z. Li, I.-h Hwang, C. Sun, C. J. Jafta, J. Yang, T. J. Toops, D. A. Cullen, A. Serov and J. Wu, EES Catalysis, 2023 10.1039/d2ey00071g.
- J. Jia, H. Zhang, Z. Wang, J. Zhao and Z. Zhou, J. Mater. Chem. A, 2020, 8, 9607–9615 RSC.
- K. Petrov and S. Srinivasan, Int. J. Hydrogen Energy, 1996, 21, 163–169 CrossRef CAS.
- X. Zong, J. Han, B. Seger, H. Chen, G. M. Lu, C. Li and L. Wang, Angew. Chem., Int. Ed., 2014, 53, 4399–4403 CrossRef CAS PubMed.
- M. Zhang, J. Guan, Y. Tu, S. Chen, Y. Wang, S. Wang, L. Yu, C. Ma, D. Deng and X. Bao, Energy Environ. Sci., 2020, 13, 119–126 RSC.
- A. Qayyum, U. Ali and N. Ramzan, Energy Sources, Part A, 2020, 1–24 Search PubMed.
- F. Gao, J. He, H. Wang, J. Lin, R. Chen, K. Yi, F. Huang, Z. Lin and M. Wang, Nano Res. Energy, 2022, 1, e9120029 CrossRef.
- Q. Xu, J. Zhang, H. Zhang, L. Zhang, L. Chen, Y. Hu, H. Jiang and C. Li, Energy Environ. Sci., 2021, 14, 5228–5259 RSC.
- D. Deng, L. Yu, X. Chen, G. Wang, L. Jin, X. Pan, J. Deng, G. Sun and X. Bao, Angew. Chem., Int. Ed., 2013, 52, 371–375 CrossRef CAS PubMed.
|
This journal is © The Royal Society of Chemistry 2023 |
Click here to see how this site uses Cookies. View our privacy policy here.