DOI:
10.1039/D2MH01073A
(Communication)
Mater. Horiz., 2023,
10, 235-247
High-strength, low infrared-emission nonmetallic films for highly efficient Joule/solar heating, electromagnetic interference shielding and thermal camouflage†
Received
29th August 2022
, Accepted 28th October 2022
First published on 28th October 2022
Abstract
High-strength nonmetallic materials with low infrared (IR) emission are rare in nature, yet highly anticipated especially in military and aerospace fields for thermal camouflage, IR stealth, energy-saving heating. Here, we reported a high-strength (422 MPa) nonmetallic film with very low IR emissivity (12%), realized by constructing alternating multilayered structures consisting of successive MXene functionalized outer layers and continuous GO reinforced inner layers. This nonmetallic film is capable of competing with typical stainless steel (415 MPa, 15.5%), and exhibits remarkable thermal camouflage performance (ΔT = 335 °C), ultrahigh Joule heating capability (350 °C at 2 V), excellent solar-to-thermal conversion efficiency (70.2%), and ultrahigh specific electromagnetic interference shielding effectiveness (83
429 dB cm−1). Impressively, these functionalities can be maintained well after prolonged outdoor aging, and even after undergoing harsh application conditions including strong acid/alkali and boiling water immersion, and cryogenic (−196 °C) temperature.
New concepts
Metals are typical low infrared (IR) emitters for application in thermal camouflage, IR stealth, and energy-saving heating, but the drawbacks of easy corrosion, high-density, and hard-processability seriously hinder their usefulness. Nonmetallic low IR emitters with comparable strength to metals are rare in nature yet are highly desired. This has been a formidable challenge for decades. Here, we propose a new concept of the construction of alternating multilayered structures consisting of continuous MXene layers and GO layers to successfully fabricate a high-strength yet low IR-emission nonmetallic film. The obtained nonmetallic film has a low density (2.3 g cm−3), high strength (422 MPa), and very low IR emissivity (12%) which are superior to those of the rival typical stainless steel (6.8 g cm−3, 415 MPa, 15.5%, respectively). This nonmetallic film shows remarkable thermal camouflaging capability by reducing the radiation temperature of an object from 511 °C to 176 °C (ΔT = 335 °C), ultrahigh electric heating capability (350 °C at a low voltage of 2 V), high solar-to-thermal conversion efficiency (70.2%), and ultrahigh specific electromagnetic interference shielding effectiveness (83 429 dB cm−1). Furthermore, the functionalities of the nonmetallic film can be maintained well after undergoing various harsh conditions, making it an ideal alternative to traditional metal-based low IR emitters in many significant applications.
|
1. Introduction
Materials with low infrared (IR) emissivity are of great importance in many fields, such as thermal camouflage/IR stealth,1,2 radiative heating,3–5 smart textiles,6,7etc. Metals are typically low IR emitters,5,8 but the drawbacks of easy corrosion, high-density, and hard-processability seriously hinder their applications. Moreover, the intrinsic IR emissivity of many metals is not low enough so that special processes, such as electrodeposition, are required to obtain low IR emissivity.9 Nonmetallic materials with intrinsic low IR emissivity are rare in nature yet highly desired, which have been a long-standing challenge for decades. Some metamaterials such as photonic crystals,10,11 plasmon resonances,12–14 and nanostructure-based surfaces,15–18 have been developed with low IR emissivity, but the complex micro-/nanostructure, high technical requirement, and high cost of these materials greatly restrict their usefulness. Furthermore, the inferior mechanical performances of these metamaterials to their metal counterparts also obstruct their applications in many fields, especially in military and aerospace scenarios where a high strength/modulus is usually required.
Recently, Ti3C2Tx MXene has been reported with intrinsically low IR emissivity (19%) comparable to that of metals, which has shown great potential in thermal camouflage,19 radiative heating,20 and photothermal conversion.21 MXenes are water/organic solvent soluble with tunable surface chemistry,22 and can be processed through simple and low-cost approaches, such as spraying,23 spinning,24 solution blending,25 and in situ polymerization,26 rather than the complex process of metals such as high temperature sputtering. Low IR emitters from MXenes are ideal alternatives to traditional metals. However, the mechanical performance of pure macro-assembled MXene materials, such as thin films, are generally poor with a tensile strength of dozens of MPa and are far inferior to that of metals, hindering their practical utilization. Reinforcing additives with oxygen-containing groups, including polymers such as poly(vinyl alcohol) (PVA),27 small molecules such as dopamine,28 nanomaterials such as cellulose nanofiber (CNF)29 and graphene oxide (GO),30 has been done to enhance the mechanical performance of MXene-based nanocomposite film through formation of hydrogen, ionic, and covalent bonding interactions.31,32 Despite the promising reinforcing effects, these introduced materials are usually high IR emitters, which undoubtedly increase the IR emissivity of MXene films. Integrating the “trade-off” high strength and low IR emissivity in MXene films remains an urgent challenge to be addressed.
Here, we report high-strength (422 ± 25 MPa) and low IR-emissivity (12%) Ti3C2Tx MXene films that are capable of competing with typical stainless steel (415 MPa, 15.5%), realized through constructing continuous GO reinforced inner layers and successive MXene functionalized outer layers via a facile vacuum-assisted alternating filtration approach. This unique alternating multilayered structure endows a higher alignment of nanosheets, stronger hydrogen bonding interactions, and more compact layered structure than their counterparts of a conventional MXene/GO blending composite film. In addition to the low IR emissivity, these high-strength MXene/GO multilayered (MGM) films also possess high solar absorptivity (77.5%) and high electrical conductivity (3871 S cm−1). These merits endow the MGM film with remarkable thermal camouflage performance by reducing the radiation temperature of a high-temperature object from 511 °C to 176 °C, ultrahigh Joule heating temperature of 350 °C at a low driving voltage of 2 V within 1 s, high solar-to-thermal conversion efficiency (70.2%) under practical solar irradiation, and ultrahigh specific electromagnetic interference (EMI) shielding effectiveness (SE) (83
429 dB cm−1). Additionally, the thermal camouflage, electric-/solar heating, and EMI shielding performance can be maintained stable after prolonged outdoor aging, as well as after resisting many harsh application scenarios including strong acids/alkalis and boiling water immersion, and extreme cryogenic temperature (−196 °C) or even high temperature (350 °C).
2. Results and discussion
2.1 Fabrication and structure of MGM films
Fig. 1a shows the fabrication process of MXene/GO multilayered films by vacuum-assisted alternating filtration of Ti3C2Tx MXene and GO. It is noted that the outer surfaces on two sides of the multilayered film are MXene layers, and the total mass fraction ratio of MXene to GO in the multilayered film is controlled to be 1
:
1. The as-obtained MXene/GO multilayered films were named MGM-(2n + 1), where n + 1 and n represent the number of MXene layers and GO layers, respectively. The MXene nanosheets, displaying a typical sheet-like morphology, were synthesized by etching Ti3AlC2 powder using the minimally intensive delamination (MILD) method.33 As shown in transmission electron microscopy (TEM) images (Fig. 1b), the lateral size of MXene nanosheets is around 3 μm with their homogeneous dispersion liquid exhibiting a typical Tyndall effect (inset in Fig. 1b). GO nanosheets, prepared through an improved Hummers’ method,34 exhibit a lateral size larger than 20 μm (Fig. 1c) with their homogeneous dispersion liquid exhibiting a typical Tyndall effect (inset in Fig. 1c). The as-obtained free-standing MGM-7 film (7 μm) is mechanically flexible (Fig. 1d) and shows successive compact layered structures with alternating MXene and GO with tiny voids (Fig. 1e), which is completely different from the undulating nacre-like structure in the MXene/GO composite (MGC) film with a large number of voids (Fig. S1 and S2, ESI†). Compared with the pure MXene film (Fig. S3, ESI†), MXene nanosheets as well as GO nanosheets in the continuous alternating layers in MGM film stack much denser, resulting in unobvious defects or gaps at the layer interface. The distribution map of titanium (Ti) element displayed by the energy dispersive spectrometer (EDS) mapping of MGM films (Fig. 1e) verifies the alternating layered distribution of MXene and GO. The formation of a compact layered structure in MGM films is perhaps attributed to the unique alternating filtration method. During a conventional filtration process, nanosheets are subjected to a vertical downward suction force, which easily causes a large stacking of 2D nanosheets in the horizontal direction. However, this stacking is often not tight enough, and more porosity is usually created inside the film (like in the MGC film). As shown in Fig. S4 in the ESI,† layer-by-layer alternating filtration methods used in the MGM film, on the other hand, causes the upper component to continuously exert an additional pressure to the lower component during the filtration process. As a result, the nanosheets are arranged more regularly and more tightly in the MGM-7 film.
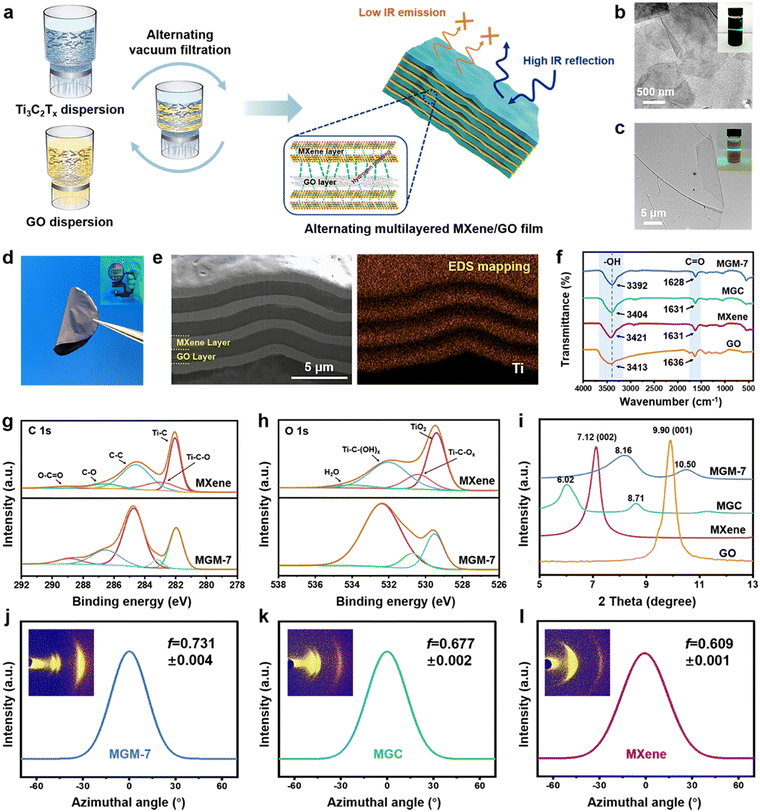 |
| Fig. 1 Fabrication process and structure of the MGM film. (a) Schematic of the process for fabricating the MGM film. TEM image of delaminated (b) MXene and (c) GO nanosheets. Insets are the photographs of MXene dispersion liquid and GO dispersion liquid, and their Tyndall effects, respectively. (d) Digital image of the MGM-7 film with the inset demonstrating its thickness. (e) Scanning electron microscope (SEM) images and EDS mapping of the MGM-7 film cut by a focused ion beam (FIB). (f) FTIR spectra of GO, MXene, MGC, and MGM-7 films. High-resolution XPS spectra of (g) C 1s and (h) O 1s for MXene and MGM-7 films. (i) XRD patterns of GO, MXene, MGC, and MGM-7 films. WAXS patterns for corresponding azimuthal scan profiles for the 002 peak for (j) MGM-7, (k) MGC, and (l) MXene films. | |
Fourier transform infrared (FTIR) spectroscopy of GO, MXene, MGC, and MGM-7 films are shown in Fig. 1f. The stretching vibration peaks of –OH are clearly seen at 3421 cm−1 and 3413 cm−1 for MXene and GO films, respectively. The weak absorption bands at 1631 cm−1 and 1636 cm−1 are associated with the C
O stretching vibrations of MXene and GO films, respectively. This indicates that MXene and GO nanosheets contain a significant number of oxygen-containing groups, which serve as the foundation for the formation of hydrogen bonds. In the FTIR spectrum of MGC films, the stretching vibration of –OH red-shifted from 3421 cm−1 to 3404 cm−1, indicating the existence of hydrogen bonding interactions in MGC films.35 Notably, the –OH peak of the MGM-7 film further red-shifted to a lower position of 3392 cm−1 compared to MGC films, while the C
O peak also red-shifted to 1628 cm−1, indicating the formation of stronger hydrogen bonding interactions in the MGM-7 film.36 In addition, X-ray photoelectron spectroscopy (XPS) analysis was used to verify the strong hydrogen bonding and electrostatic interaction generated between the MXene component and the GO component. Fig. 1g, h and Fig. S5 in the ESI† show the wide-scan spectra, C 1s and O 1s high-resolution spectra obtained by XPS. All the spectra are referenced to the C 1s peak with a binding energy of 284.6 eV. All peaks belonging to MXene could be detected in both MGM-7 and MGC films (Fig. S5, ESI†), indicating that the structure of MXene nanosheets was not disrupted during blending or alternating filtration processes. Furthermore, the C 1s spectrum of XPS (Fig. 1g and Fig. S5, ESI†) shows that the peak of Ti–C changed from 282.0 eV for the MXene film to 281.5 eV for the MGC film and 281.8 eV for the MGM-7 film, respectively, indicating chemical interaction between the MXene component and the GO component in MGC and MGM-7 films.37 It is noteworthy that the peaks of C–O at 286.4 eV and C
O at 288.7 eV in the MXene film shifted to higher binding energies in the MGM-7 film (i.e., 286.8 and 289.1 eV), while no pronounced changes appeared in the MGC film. Moreover, both peaks were stronger in the MGM-7 film than those in the MXene film, which was attributed to the formation of stronger hydrogen bonds in the MGM-7 film. In the O 1s spectrum of XPS (Fig. 1h and Fig. S5, ESI†), the characteristic peaks Ti–C–(OH)x in the MGM-7 film and the MGC film moved from 532.0 eV in the MXene film to higher binding energies of 532.6 eV and 532.4 eV, respectively.38 The results indicate that stronger hydrogen bonding interactions are generated in the MGM-7 film, which is consistent with the results of FTIR spectroscopy. In addition, Fig. S6 in the ESI† shows the Raman spectra of MXene, GO, MGC, and MGM-7 films in the range of 600–4000 cm−1. The characteristic fingerprints of MXene films are in the range of 100–800 cm−1, where the peaks at 199 cm−1 and 719 cm−1 are typical A1g out-of-plane vibrations of Ti and C atoms, and the 270–590 cm−1 region are Eg in-plane vibrations of Ti, C, and surface functional group atoms. These vibrations are expected in the exfoliated MXene nanosheets. Notably, these characteristic fingerprints of MXene could be found in the Raman spectrum of the MGM-7 film obviously while they were absent in the MGC film. This indicates that MXene nanosheets cannot completely cover the surface of MGC films, which is very unfavorable for MXene to exploit their intrinsically low IR-emissivity properties in MGC films. The Raman spectrum of the GO film shows two prominent peaks of the D band at 1340 cm−1 and G band at 1581 cm−1. Notably, the ID/IG ratio of the MGM-7 film increased from 0.88 (GO films) to 1.02, while that of MGC films was 0.98, indicating the presence of strong interactions in the MGM-7 film.39,40 In addition, the result of low-field nuclear magnetic resonance (LF-NMR)41 and temperature-dependent FTIR42 spectroscopy further verify the formation of stronger hydrogen bonding interactions in the MGM film (Fig. S7 and S8, ESI†). The large number of strong hydrogen bonding interactions in the MGM film can induce densification and strengthen the interlayer interactions, thus enhancing the mechanical properties of the film greatly.32
X-Ray diffraction (XRD, Fig. 1i) shows that the (001) characteristic peak of GO and the (002) characteristic peak of MXene downshifted from 9.90° in the pure GO film and 7.12° in the pure MXene film to 8.71° and 6.02° in the MGC film, respectively, demonstrating the enhanced interplanar spacing of both MXene nanosheets and GO nanosheets due to their mutual intercalation in the MGC film. In contrast, the (001) characteristic peak and the (002) characteristic peak in the MGM-7 film upshifted to 10.5° and 8.16°, respectively, indicating the reduced interplanar spacing of both MXene nanosheets and GO nanosheets because of their much more regular and compact structure (Fig. S9, ESI†).29,43 In addition, the orientation degree of MXene nanosheets and GO nanosheets was characterized by wide-angle X-ray scattering (WAXS) (Fig. 1j–l and Fig. S10, ESI†). The Herman's orientation factor (f) of MXene nanosheets and GO nanosheets in the MGM-7 film is clearly larger than that of MXene and GO films, as well as the MGC film, indicating that the alternating multilayered structure can enhance the alignment degree of MXene nanosheets and GO nanosheets in the MGM-7 film greatly.44,45 Notably, higher orientation of nanosheets in the MGM-7 film could also induce more hydrogen bonding interactions. Moreover, the higher orientation degree of nanosheets and more compact layered structure in the MGM film is beneficial to the formation of enhanced van der Waals forces of attraction, which further make a positive contribution to enhancing the mechanical strength of the MGM film.
2.2 Mechanical performance
Fig. 2a–e shows the mechanical properties of pure MXene, GO, MGC, and MGM films. The MGM film can not only withstand a weight of 1 kg without breaking but also be folded to paper airplanes easily (Fig. 2a), visually indicating its strong mechanical properties and excellent flexibility. As shown in Fig. 2b, c and Fig. S11a–c in the ESI,† pure MXene films have a tensile strength of 44.8 ± 1.4 MPa, a toughness of 0.81 ± 0.08 MJ m−3, and a Young's modulus of 1.43 ± 0.21 GPa. MGC films show a tensile strength of 278 ± 6.8 MPa, a toughness of 7.04 ± 0.16 MJ m−3, and a Young's modulus of 11.47 ± 0.59 GPa. For MGM films, MGM-7 films have the highest tensile strength of 422 ± 25 MPa, a toughness of 11.85 ± 1.13 MJ m−3, and a Young's modulus of 15.03 ± 1.47 GPa, which are 1.5, 1.7, and 1.3 times higher than those of MGC films, and 9.4, 14.6, and 10.5 times higher than those of pure MXene films, respectively. Additionally, the MGM-11 films show the highest Young's modulus of 24.3 ± 1.0 GPa, which is superior to that of most reported MXene-based films. In combination with relatively low density (2.3 g cm−3), the MGM-7 films possess a remarkable specific strength (184 kN m kg−1), which is higher than that of typical stainless steel (Fig. S11d and Table S1, ESI†).
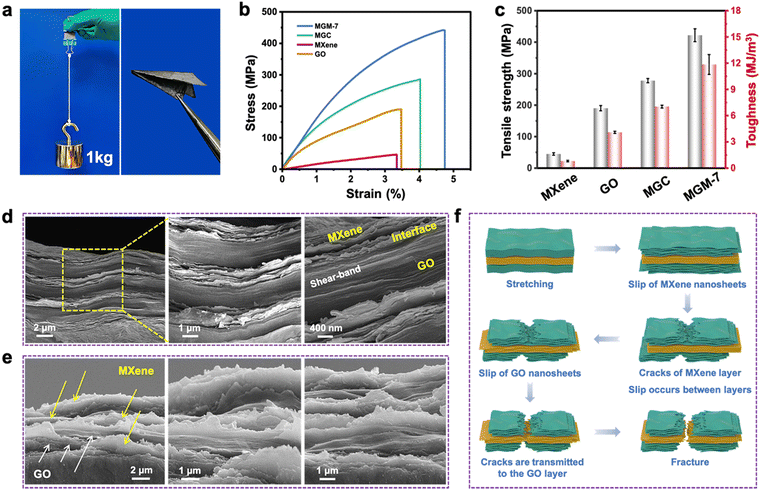 |
| Fig. 2 Mechanical properties of MGM films. (a) Digital images of the MGM-7 film withstanding a weight of 1 kg and being folded into paper airplanes. (b) Tensile stress–strain curves, (c) tensile strength and fracture toughness of pure MXene, GO, MGC, and MGM-7 films. (d) SEM images of fracture surface of the MGM-7 film at different magnifications observed from the direction perpendicular to the fracture surface. (e) Inclined-view SEM images of fracture surface of MGM-7 film at different magnifications. (f) Schematic illustration of the fracture mechanism in the MGM film. | |
The reinforcing and toughening mechanism in MGM films was further understood by investigating the morphology of tensile fracture surfaces. As shown in Fig. 2d and Fig. S12 in the ESI,† after the tensile test, the fracture surface of MGM-7 films still maintained a highly dense and oriented layered structure. Notably, a large number of nanometer-sized jagged cracks were observed not only in the MXene layer and the GO layer but also at the interface layer on the fracture surface of the compact MGM-7 film.46 These layered jagged cracks could absorb a large amount of fracture energy during crack extension, resulting in a large increase in both tensile strength and toughness. In other words, the robustness of GO layer as a mechanical framework in the alternating multilayered structure prevents nano jagged cracks in the MXene layer from propagating to the whole film, and the layer-to-layer interaction ensures the transfer of stress from the MXene layer to the GO layer. Meanwhile, MXene nanosheets with abundant curved or jagged edges were pulled out and fractured on the fracture surface of MGM-7 film, which were mainly because of the interfacial shear fracture caused by the slippage of MXene nanosheets during the stretching process. Additionally, GO nanosheets in the compact GO layer showed brittle and jagged edges with a shear-band characteristic among the dense stacked GO nanosheets, which contributed to the high fracture strength of the whole MGM-7 film. Moreover, from the inclined-view SEM images (Fig. 2e), one can observe clearly that the MGM-7 film showed a zigzag characteristic with curled fractured edges in both MXene layer, GO layer and the layer interface, verifying the improved interlayer interaction that results in greatly enhanced mechanical performance in the MGM-7 film.47 For MGC films as shown in Fig. S13 in the ESI,† however, cracks will be generated first at the stress concentration points (defects, holes, etc.) during the stretching process. The relatively poor density and greater void structure of MGC films limit the mechanical strength. Stress spreads rapidly from defects in MGC films, and relatively weak interfacial interactions could not retard the fracture of the films, resulting in a pronounced brittle fracture.
In order to illustrate the synergistic toughening effect of the MXene layer and GO layer in MGM films more clearly, a possible fracture mechanism model is proposed. As shown in Fig. 2f, during the early stage of stretching, MXene nanosheets slide past each other, which results in continual breaking and reforming of hydrogen bonds between MXene nanosheets, contributing to the dissipation of some fracture energy and then inducing the formation of cracks. The strong GO layer can function as a load-bearing frame to prevent the entire film from breaking when the crack in the MXene layer spreads to the interface and begins to deflect in a direction parallel to the layer, consuming a significant amount of energy. When the slippage of GO nanosheet reaches the limit, cracks expand along the nanoscale jagged path toward the GO layer.48 At this time, large number of jagged cracks are formed between the MXene layer and the GO layer. Additionally, shear-band theory also claims that when cracks move from the MXene layer to the GO layer, the tensile stress borne by the GO layer will form a balanced relationship with the shear stress at the interface. This makes the cracks tend to move along the interface, delaying their rapid expansion and preventing the rapid onset of a brittle fracture. Finally, GO nanosheets fracture with jagged edges and a shear-band characteristic among the dense stacked GO layers, contributing to the high fracture strength of the whole MGM film.
Except for the tensile strength and toughness, surface hardness and abrasion resistance of the MGM film was further investigated via a nanoindentation test and a tribological abrasion test (Fig. S14 and S15, ESI†). The results show that MGM films exhibit both soft and tough characteristics due to their unique layer structures and have relatively excellent macroscopic frictional resistance. However, it is noted that the surface hardness of the MGM film is still far inferior to that of stainless steel film.
2.3 IR emission and thermal camouflage performance
As shown in Fig. 3a, the GO film exhibits a high IR emissivity of 67% in 7–14 μm (the IR emissivity here is an averaged value20), resulting in a high IR emissivity (46%) of the MGC film, even though the IR emissivity of the pure MXene film is as low as 9%. Interestingly, the MGM-7 film has a very low IR emissivity of 12%, which is comparable to that of the pure MXene film, and is far below those of the MGC film and the GO film. This is mainly because the layered structure in the MGM film ensures the continuous dispersion of MXene nanosheets on the outermost surface of the film. We measured and compared the IR emissivity and tensile strength of different types of materials including metals, carbon nanomaterials, polymers, etc. (Fig. 3b). The IR emissivity and strength of the MGM-7 film (12%, 422 MPa) are capable of competing with those of typical metals such as stainless steel (15.5%, 415 MPa). Furthermore, the IR emission of the MGM-7 film will become much more prominent when considering the strength and density of materials at the same time (Fig. 3c).
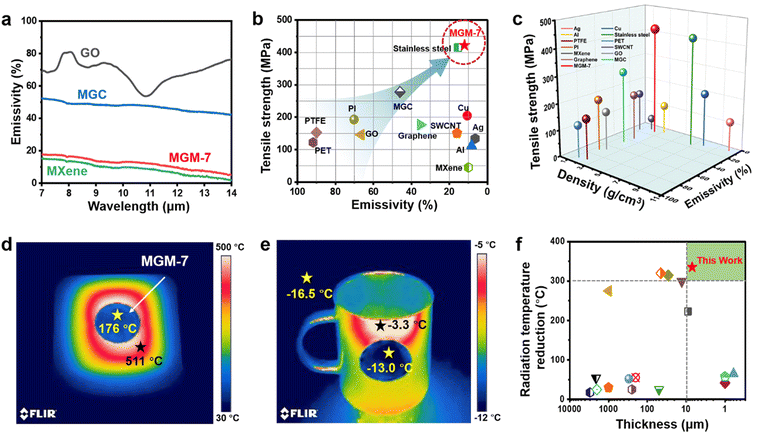 |
| Fig. 3 IR-emission properties of MGM films. (a) Middle IR emissivity of MXene, GO, MGC, and MGM-7 films. (b) Comparison of IR emissivity and strength of different types of materials. (c) Comparison of IR emissivity, strength, and density of different types of materials. (d) IR images of the MGM-7 film covering on an object with a thermal radiation temperature of 511 °C. (e) IR images of the MGM-7 film covering on a cold ceramic cup with a thermal radiation temperature of −3.3 °C. (f) Comparison of the radiation temperature reduction of various film-based thermal camouflage materials/systems taking thickness into consideration. | |
The low IR emission of MGM films endows them with excellent thermal camouflage performance. For a high-temperature object (>500 °C), its thermal radiation temperature (511 °C) could be reduced to 176 °C by covering with a MGM-7 film with a hue approximate to the color of the surroundings (Fig. 3d), thus verifying the remarkable thermal camouflage performance of the MGM film with a large radiation temperature reduction (ΔT = 335 °C). For comparison, the MGC film could only reduce the thermal radiation temperature (511 °C) to 345 °C (ΔT = 166 °C) with a hue darker than that of the object but much brighter than that of the surroundings (Fig. S16a, ESI†). Moreover, the MGM-7 film can show remarkable thermal camouflage performance for objects with varying temperatures from room temperature to 511 °C (Fig. S17, ESI†), making it of great potential in various scenarios in a wide temperature range even outdoors in cold winter. As shown in Fig. 3e, the thermal radiation temperature of a cold ceramic cup (−3.3 °C) was reduced to −13 °C after covering with an MGM-7 film, which was close to that the surroundings (−16.5 °C). By comparison, after covering with the MGC film, the radiation temperature of the cold ceramic cup was reduced to −10.4 °C (Fig. S16b, ESI†). The thermal camouflage capability of the MGM film is superior to that of most known film-based camouflage materials/systems taking thickness into consideration (Fig. 3f and Table S2, ESI†).2,8,9,19,49–59
2.4 Joule/solar heating performance
The electrical conductivity of MGC films is 731 S cm−1, while that of MGM films increases effectively, and reaches a maximum value of 3871 S cm−1 in the MGM-7 film (Fig. S18, ESI†), indicating its excellent Joule heating performance. Fig. 4a are IR images of MGM-7 film (2 × 1 cm2) after applying a voltage of 0.5, 1, 1.5, and 2 V, the temperature of which increased rapidly on applying the voltage (Fig. 4b), and reached a saturated temperature of 27.1, 39.2, 56.1, and 100.7 °C very rapidly within 1 s, respectively. It is worth noting that these are illusional temperatures resulting from the low IR emission of MGM-7 films. We further measured the actual temperature of the MGM-7 film by adjusting the emissivity of the IR camera to be identical to that of MGM-7 film. As shown in Fig. 4c, the actual saturated temperatures of MGM-7 films at a voltage of 0.5, 1, 1.5, and 2 V were 56.2, 114.5, 203.4, and 350 °C, respectively, which were much higher than the temperatures obtained using an IR camera (Fig. 4b). The above results demonstrate the remarkable disguised Joule heating performance of MGM film. Moreover, the nearly linear I–V curve (Fig. 4d) demonstrates the low resistance and great stability of MGM film, ensuring energy-saving and safe operation in practical applications. As a comparison, the thermal camouflage temperature and actual temperature of MGC film at different driving voltages are shown in Fig. S19 in the ESI.† At a driving voltage of 2 V, the thermal camouflage temperature and actual temperature of the MGC film were only 43 °C and 81.7 °C, respectively, which were much inferior to those of the MGM-7 film. This is mainly because the blending structure in the MGC film makes it difficult for MXene nanosheets to form a continuous conductive path in the film. Current changes in the MGM-7 film and MGC film at identical driving voltages confirm this point of view (Fig. S20, ESI†). Moreover, owing to the very low IR emissivity of the MGM-7 film, a tiny IR thermal radiation loss was generated during the Joule heating process, which greatly contributes to the excellent Joule heating performance in the MGM-7 film. In addition, we further used a high IR-emission (98%) insulating tape attached onto the film to measure its surface actual temperature at different driving voltages, which also verifies the excellent Joule heating performance of the MGM film (Fig. S21, ESI†).
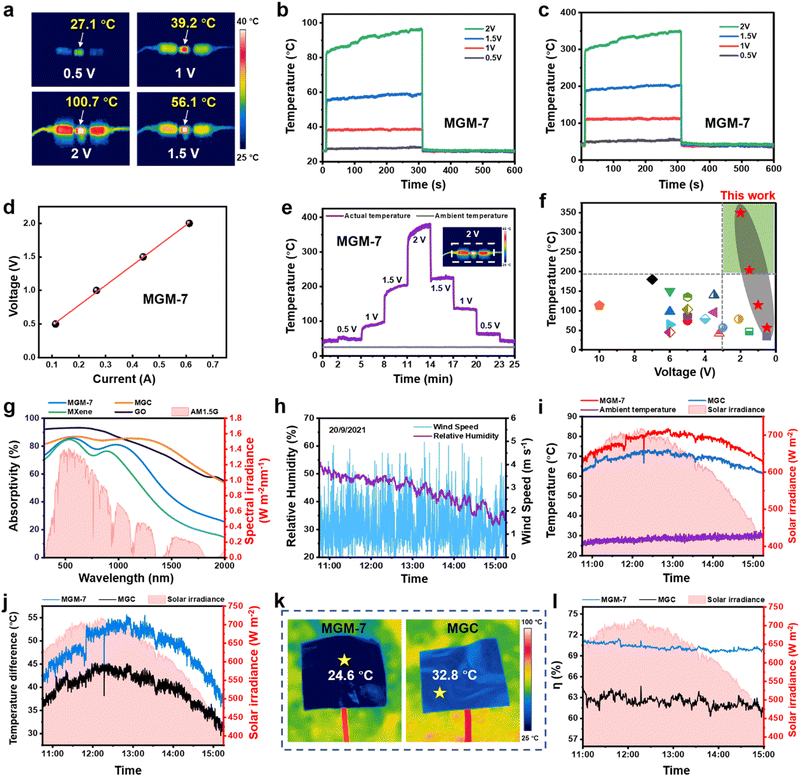 |
| Fig. 4 Energy-saving heating performance of MGM films. (a) IR images, (b) IR thermal camouflage temperature and (c) actual temperature of the MGM-7 film at different driving voltages. (d) I–V curves of the MGM-7 film at different voltages. (e) Apparent and actual temperature of the MGM-7 film by adjusting the driving voltage from 0.5 to 2 V and from 2 to 0.5 V. (f) Comparison of the Joule heating performance of different electric heaters. (g) Measured absorptivity of MXene, GO, MGC, and MGM-7 films from ultraviolet to near-infrared wavelength. (h) The wind speed and relative humidity from 11:00 to 15:00 on a sunny day (September 20, 2021, east longitude: 113°32′; northern latitude: 34°48′). (i) Real-time temperature of MGM-7 film and MGC film on the sunny day. (j) The actual temperature difference between the MGM-7 film, the MGC film, and the ambient film on a sunny day. (k) IR images of different films at 12:00 on a sunny day. (l) Solar-to-thermal conversion efficiency (η) of the MGM-7 film and the MGC film. | |
Moreover, the saturated heating temperature of the MGM-7 film can be controlled easily and rapidly from a low temperature at 0.5 V to a very high temperature at 2 V, and further from 2 V to 0.5 V (Fig. 4e), which is much better than that of the MGC film (Fig. S19e, ESI†). The Joule heating performance of the MGM-7 film is far superior to that of other reported electric heaters (Fig. 4f and Table S3, ESI†),29,30,60–76 and is an ultrahigh value (350 °C) at such a low driving voltage (2 V).
The solar absorptivity spectra of MXene, GO, MGC, and MGM films were measured using a UV-vis-NIR spectrometer (Fig. 4g), which exhibits an averaged absorptivity of 71.5%, 88.7%, 84.5%, and 77.5%, respectively. The solar heating performance of a material is determined not only by the energy absorbed from solar irradiation but also by the thermal radiation loss to the surroundings. Therefore, materials with high solar absorptivity yet low IR emissivity are anticipated for achieving efficient solar-to-thermal conversion. Interestingly, the MGM film exhibits high solar absorptivity and low IR emissivity synchronously, and is an ideal material for solar heating. We tested the practical solar heating performance of the MGM-7 film and the MGC film on one roof at Zhengzhou University (east longitude: 113°32′; northern latitude: 34°48′) on a sunny day (September 20, 2021, Fig. S22, ESI†) with real-time monitoring of the weather parameters (Fig. 4h). Fig. 4i depicts the actual temperatures (obtained using a K-type thermocouple attached onto the shade surface of films) of the MGM-7 film and the MGC film from 11:00 to 15:00, which reached a maximum value of 83.9 °C and 73.5 °C at around 13:00 with a solar irradiation of 645.2 W m−2, respectively. The average temperature of the MGM-7 film under sunlight was 49.3 °C and 8.7 °C higher than that of the ambient and MGC film, respectively (Fig. 4j). It is noted that the solar absorptivity of MGC film (84.5%) is higher than that of MGM-7 film (77.5%), but the solar heating performance is inferior to that of the MGM-7 film. This is mainly because the lower IR emissivity in the MGM-7 film (12%) generates a lower thermal radiation loss than the MGC film with high IR emissivity (46%) to the surroundings (Fig. 4k). We calculated the solar-to-thermal conversion efficiency of the MGM-7 film and the MGC film (Fig. 4l). The average solar-to-thermal conversion efficiency of the MGM-7 film was as high as 70.2% and was higher than that of the MGC film (62.4%). The high-strength MGM films will have great potential in solar energy utilization.
2.5 EMI shielding performance
The high electrical conductivity of the MXene film always indicates excellent EMI shielding performance. As shown in Fig. 5a, the EMI SE of the MGC film was 30.7 dB in the whole X-band, while that of MGM films increased greatly. For instance, the MGM-7 film had the highest EMI SE value of 58.4 dB. We calculated the specific SE (SEt) by dividing the film thickness (Fig. 5b). For instance, the SEt of the MGM-7 film was as high as 83
429 dB cm−1, which is superior to the values of well-studied metal-based, carbon-based, and MXene-based composites,28–30,35,36,48,77–93 and is among the best values when taking the tensile strength of materials into consideration at the same time (Fig. 5d and Table S4, ESI†). In addition, the SSEt taking material density and thickness into consideration synchronously was further calculated (Fig. 5c). The SSEt of the MGM-7 film was also at a high value of 36
273 dB cm2 g−1. To highlight the outstanding EMI shielding performance of MGM films, the EMI SE, SEt, SSEt, content, strength, and thickness of the MGM film were compared with those of other MXene-based films reported in the literature (Fig. 5e and Table S5, ESI†).29,35,36,48,77,78,90,93 Obviously, the EMI shielding performance of MGM films outperforms that of most of the previously reported MXene-based EMI shielding materials, which is mainly attributed to the hierarchical reflection loss in the MGM film, including the reflection at the interface between the MXene layer and the GO layer owing to their high impedance mismatch, and reflection between the MXene nanosheets in the MXene layer (Fig. S23, ESI†). Therefore, the alternating multilayered structure contributes to a significant increase in the EMI shielding performance of MGM films compared to that of MGC films.
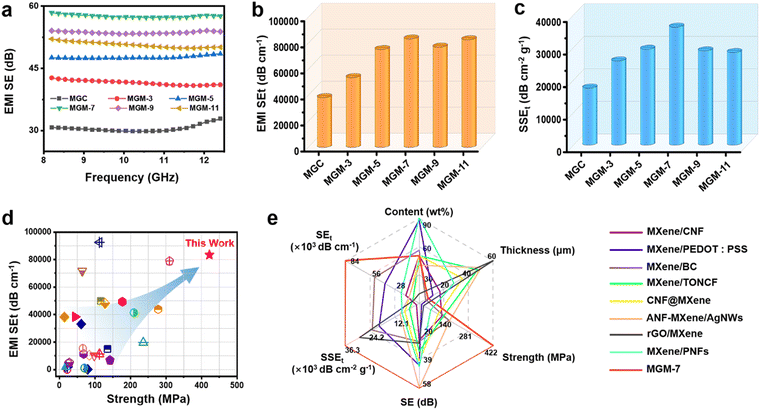 |
| Fig. 5 (a) EMI SE, (b) SEt, and (c) SSEt of MGC film and MGM films. (d) EMI SEtversus tensile strength of different materials. (e) Comparison of the EMI shielding performance of various MXene-based films taking EMI SE, SEt, SSEt, thickness, content, and strength into consideration at the same time. | |
2.6 Stability for practical applications
It is well known that MXene nanosheets are susceptible to oxidation due to moisture and oxygen in the environment, leading to degradation of their performance. Therefore, the long-time stability of the MXene-based film is important for its practical application under some special conditions. Here, the stability of MGM-7 films as well as MGC films for practical application was explored in various scenarios including prolonged outdoor aging for three weeks (Fig. S24, ESI†), strong acids (Fig. S25, ESI†), strong alkali (Fig. S26, ESI†), boiling water (Fig. S27, ESI†), extreme cryogenic temperature (Fig. S28, ESI†) and high temperature environments (Fig. S29, ESI†). After resisting various scenarios, the IR emissivity of MGM-7 films changes slightly, while those of MGC films increase particularly after strong alkali treatment (Fig. S30, ESI†). In addition, the electrical conductivity of MGM-7 films changes slightly except for that after high-temperature treatment as well as being immersed in boiling water, which was reduced to around 1500 S cm−1 but was still maintained at a high value (Fig. S31, ESI†). As for solar absorptivity, the MGM-7 film could be maintained at almost a consistent value of 75% after resisting various conditions (Fig. S32 and S33, ESI†).
We further explored the thermal camouflage, electric/solar heating, and EMI shielding performance of MGM-7 films and MGC films after resisting various conditions (Fig. 6). Firstly, prolonged daily stability is the most important factor for long-time application of the MGM film. After being placed outdoors for three weeks, the MGM-7 film also exhibited remarkable thermal camouflage performance with a highest radiation temperature reduction of 331 °C (Fig. 6a), a saturated Joule heating temperature of 311 °C at 2 V (Fig. 6b), a maximum solar heating temperature of 52.3 °C (Fig. 6c) with a solar-to-thermal conversion efficiency of 68.5% under practical solar irradiation (447 W m−2) (Fig. S34 and S35, ESI†), and an EMI SE of 57.6 dB (Fig. 6d). The functional performance of the MGM-7 film after prolonged outdoor aging is comparable to those of the pristine MGM-7 film. For comparison, the MGC film after prolonged outdoor aging has a thermal camouflage performance with a highest radiation temperature reduction of 120 °C (Fig. S36, ESI†), a saturated Joule heating temperature of 56.3 °C at 2 V (Fig. S37, ESI†), a maximum solar heating temperature of 39.5 °C (Fig. 6c) with a solar-to-thermal conversion efficiency of 59.4% under practical solar irradiation (447 W m−2) (Fig. S34 and S35, ESI†), and an EMI SE of 27.7 dB (Fig. 6d). Unfortunately, the originally moderate functional performances of MGC films became worse after prolonged outdoor aging.
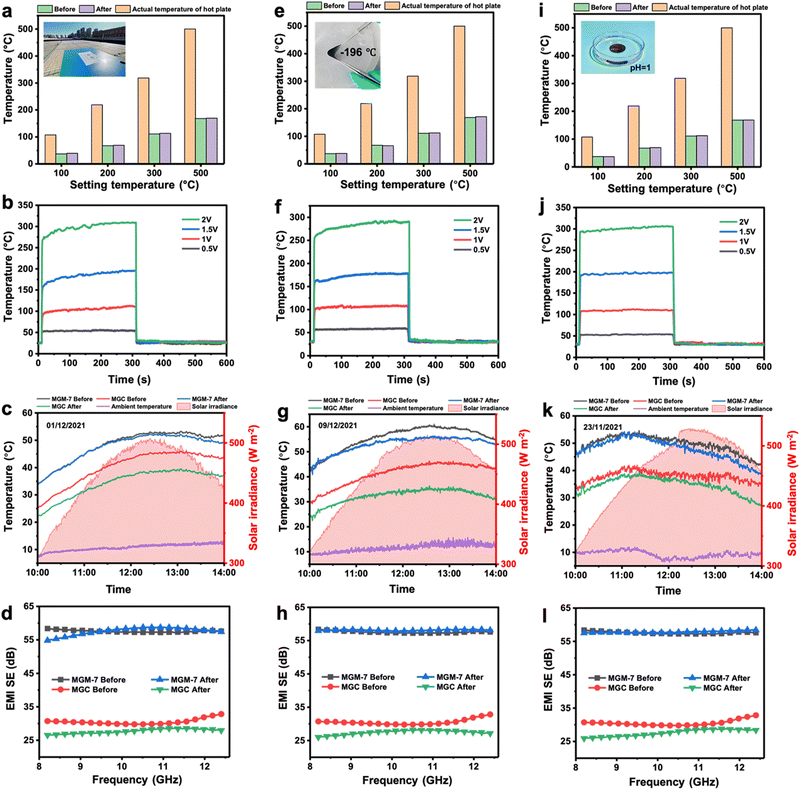 |
| Fig. 6 Stability for functional performances of MGM films after resisting various scenarios. (a) IR thermal camouflage temperature changes, (b) actual temperature at different driving voltages, (c) real-time temperature on a sunny day from 10:00 to 14:00 (December 01, 2021, east longitude: 113°32′; northern latitude: 34°48′), (d) EMI SE of the MGM-7 film after subjected to prolonged outdoor aging. (e) IR thermal camouflage temperature changes, (f) actual temperature at different driving voltages, (g) real-time temperature on a sunny day from 10:00 to 14:00 (December 09, 2021), (h) EMI SE of the MGM-7 film after resisting cryogenic temperature (−196 °C). (i) IR thermal camouflage temperature changes, (j) actual temperature at different driving voltages, (k) real-time temperature on a sunny day from 10:00 to 14:00 (November 23, 2021), (l) EMI SE of the MGM-7 film after being immersed in strong acid. | |
In addition, for MGM films with excellent energy-saving heating performance, the future application scenarios are often severe cold and high-altitude areas. Therefore, the performance stability of MGM films after experiencing extreme cryogenic temperatures is particularly important. After being frozen in liquid nitrogen (−196 °C) for 10 minutes, the MGM-7 film showed good flexibility at cryogenic temperature, and exhibited stable functional performances: remarkable thermal camouflage performance with a highest radiation temperature reduction of 329 °C (Fig. 6e), a saturated Joule heating temperature of 293 °C at 2 V (Fig. 6f), a maximum solar heating temperature of 56.3 °C (Fig. 6g) with a solar-to-thermal conversion efficiency of 65.7% under practical solar irradiation (459 W m−2) (Fig. S34 and S35, ESI†), and an EMI SE of 58.1 dB (Fig. 6h). In order to simulate the strong acid attack that may be encountered during practical application, the MGM-7 film was immersed in a strong acid solution for 2 hours to explore its performance stability. After being immersed in strong acid for 2 hours, the MGM-7 film also showed stable functional performances: remarkable thermal camouflage performance with a highest radiation temperature reduction of 332 °C (Fig. 6i), a saturated Joule heating temperature of 307 °C at 2 V (Fig. 6j), a maximum solar heating temperature of 54.2 °C (Fig. 6k) with a solar-to-thermal conversion efficiency of 68.2% under practical solar irradiation (464 W m−2) (Fig. S34 and S35, ESI†), and an EMI SE of 57.8 dB (Fig. 6l). Similarly, the functional performances of MGM-7 film can be maintained well after being immersed in strong alkali (Fig. S38, ESI†), boiling water (Fig. S39, ESI†). Moreover, the MGM-7 film maintains stable mechanical properties after prolonged outdoor aging, extreme low temperatures, strong acids/alkalis, and boiling water (Fig. S40, ESI†).
Additionally, the functional performances of the MGM-7 film can be maintained well after aging at high temperature of 350 °C (Fig. S41, ESI†), whereas the mechanical properties of MGM-7 film deteriorated seriously after high-temperature treatment (Fig. S42, ESI†). The chemical nature and the internal structure of MGM films after high temperature aging were explored (Fig. S43 and S44, ESI†). The delaminated internal structure and the severe oxidation of the mechanically reinforced GO layer are the main reasons for the drastic degradation of the mechanical properties of the MGM film. Although MXene nanosheets also underwent oxidation at high temperature, it did not cause serious damage to the functionality of the MXene layer. This is the reason why the MGM film can maintain relatively stable electrical properties, IR thermal camouflage, Joule/solar heating, and electromagnetic shielding. Overall, MGM films maintain good performance stability in various scenarios, which is very important for their practical applications.
3. Conclusions
In summary, multilayered MXene films with alternating GO layers and MXene layers have been designed and fabricated through a facile vacuum-assisted filtration approach. The continuous inner GO layer plays the reinforcing role while the successive outer MXene layer ensures a very low IR emission on the film surface. This unique structural design imparts strong hydrogen bonding interactions, high alignment of MXene/GO nanosheets, and compact layered structure in the MGM film, endowing it with high strength and very low IR emissivity that are capable of competing with typical stainless steel. This is of great significance for the long-time absence of high-strength nonmetallic materials with intrinsically low IR emissivity in nature. Meanwhile, these high-strength MGM films also show high solar absorptivity and high electrical conductivity, making it exhibit remarkable thermal camouflage performance and realize an ultrahigh Joule heating capability as well as a high solar-to-thermal conversion efficiency. The multiscale multilayered structure ensures hierarchical reflection of electromagnetic waves, contributing to ultrahigh specific EMI shielding effectiveness in MGM films. Furthermore, the excellent stability of MGM films after resisting various scenarios makes them ideal alternatives to traditional metal-based low IR emitters in many significant applications, such as IR stealth, electromagnetic pollution protection, electric/solar energy utilization, communication security, and military safety.
4. Experimental section
The detailed Experimental section can be found in the ESI.†
Author contributions
Y. Zhang: conceptualization, methodology, investigation, data curation, writing – original draft, and writing – review and editing. L. Li: methodology, investigation, data curation, and writing – original draft. Y. Cao, Y. Yang: supervision, and writing – review and editing. W. Wang: conceptualization, supervision, methodology, writing – review and editing. J. Wang: conceptualization, supervision, methodology, formal analysis, writing – review and editing, project administration, and funding acquisition.
Conflicts of interest
The authors declare no competing financial interest.
Acknowledgements
Financial support of the National Natural Science Foundation of China (52003248), the China Postdoctoral Science Foundation (2018M642780 and 2021T140613), the Opening Project of State Key Laboratory of Polymer Materials Engineering (Sichuan University) (sklpme2019-4-31), and the Key Research and Development and Promotion projects of Henan Province in China (202102210032) are gratefully acknowledged.
References
- S. Zeng, K. Shen, Y. Liu, A. P. Chooi, A. T. Smith, S. Zhai, Z. Chen and L. Sun, Mater. Today, 2021, 45, 44–53 CrossRef CAS.
- K. Tang, X. Wang, K. Dong, Y. Li, J. Li, B. Sun, X. Zhang, C. Dames, C. Qiu, J. Yao and J. Wu, Adv. Mater., 2020, 32, 1907071 CrossRef CAS.
- P. Hsu, C. Liu, A. Y. Song, Z. Zhang, Y. Peng, J. Xie, K. Liu, C. Wu, P. B. Catrysse, L. Cai, S. Zhai, A. Majumdar, S. Fan and Y. Cui, Sci. Adv., 2017, 3, e1700895 CrossRef PubMed.
- H. Fang, W. Xie, X. Li, K. Fan, Y. Lai, B. Sun, S. Bai, W. J. Padilla and P. Hsu, Nano Lett., 2021, 21, 4106–4114 CrossRef CAS.
- L. Cai, A. Y. Song, P. Wu, P. Hsu, Y. Peng, J. Chen, C. Liu, P. B. Catrysse, Y. Liu, A. Yang, C. Zhou, C. Zhou, S. Fan and Y. Cui, Nat. Commun., 2017, 8, 496 CrossRef.
- X. A. Zhang, S. Yu, B. Xu, M. Li, Z. Peng, Y. Wang, S. Deng, X. Wu, Z. Wu, M. Ouyang and Y. Wang, Science, 2019, 363, 619–623 CrossRef CAS.
- Y. Peng and Y. Cui, Joule, 2020, 4, 724–742 CrossRef CAS.
- T. Kim, J. Y. Bae, N. Lee and H. H. Cho, Adv. Funct. Mater., 2019, 29, 1807319 CrossRef.
- M. Li, D. Liu, H. Cheng, L. Peng and M. Zu, Sci. Adv., 2020, 6, eaba3494 CrossRef CAS.
- V. Rinnerbauer, A. Lenert, D. M. Bierman, Y. X. Yeng, W. R. Chan, R. D. Geil, J. J. Senkevich, J. D. Joannopoulos, E. N. Wang, M. Soljačić and I. Celanovic, Adv. Energy Mater., 2014, 4, 1400334 CrossRef.
- P. Li, B. Liu, Y. Ni, K. K. Liew, J. Sze, S. Chen and S. Shen, Adv. Mater., 2015, 27, 4585–4591 CrossRef CAS.
- K.-T. Lin, H. Lin, T. Yang and B. Jia, Nat. Commun., 2020, 11, 1389 CrossRef CAS.
- Y. Li, C. Lin, Z. Wu, Z. Chen, C. Chi, F. Cao, D. Mei, H. Yan, C. Y. Tso, C. Y. H. Chao and B. Huang, Adv. Mater., 2021, 33, 2005074 CrossRef CAS.
- J. Mandal, D. Wang, A. C. Overvig, N. N. Shi, D. Paley, A. Zangiabadi, Q. Cheng, K. Barmak, N. Yu and Y. Yang, Adv. Mater., 2017, 29, 1702156 CrossRef.
- M. J. Moghimi, G. Lin and H. Jiang, Adv. Eng. Mater., 2018, 20, 1800038 CrossRef.
- H. X. Guo, C. Y. He, X. L. Qiu, Y. Q. Shen, G. Liu and X. H. Gao, Sol. Energy Mater. Sol. Cells, 2020, 209, 110444 CrossRef CAS.
- Y. Li, C. Lin, D. Zhou, Y. An, D. Li, C. Chi, H. Huang, S. Yang, C. Y. Tso, C. Y. H. Chao and B. Huang, Nano Energy, 2019, 64, 103947 CrossRef CAS.
- Z. X. Wu, Y. J. Liu, D. Wei, L. Yin, F. X. Bai, X. J. Liu, Q. Zhang and F. Cao, Mater. Today Phys., 2019, 9, 100089 CrossRef.
- L. Li, M. Shi, X. Liu, X. Jin, Y. Cao, Y. Yang, W. Wang and J. Wang, Adv. Funct. Mater., 2021, 31, 2101381 CrossRef CAS.
- M. Shi, M. Shen, X. Guo, X. Jin, Y. Cao, Y. Yang, W. Wang and J. Wang, ACS Nano, 2021, 15, 11396–11405 CrossRef CAS.
- Y. Li, C. Xiong, H. Huang, X. Peng, D. Mei, M. Li, G. Liu, M. Wu, T. Zhao and B. Huang, Adv. Mater., 2021, 33, 2103054 CrossRef CAS.
- V. Kamysbayev, A. S. Filatov, H. Hu, X. Rui, F. Lagunas, D. Wang, R. F. Klie and D. V. Talapin, Science, 2020, 369, 979–983 CrossRef CAS.
- M. Han, Y. Liu, R. Rakhmanov, C. Israel, M. A. S. Tajin, G. Friedman, V. Volman, A. Hoorfar, K. R. Dandekar and Y. Gogotsi, Adv. Mater., 2021, 33, 2003225 CrossRef CAS.
- C. Zhang, B. Anasori, A. Seral-Ascaso, S. Park, N. McEvoy, A. Shmeliov, G. S. Duesberg, J. N. Coleman, Y. Gogotsi and V. Nicolosi, Adv. Mater., 2017, 29, 1702678 CrossRef.
- W. Tian, A. VahidMohammadi, M. S. Reid, Z. Wang, L. Ouyang, J. Erlandsson, T. Pettersson, L. Wågberg, M. Beidaghi and M. M. Hamedi, Adv. Mater., 2019, 31, 1902977 CrossRef PubMed.
- R. M. McDaniel, M. S. Carey, O. R. Wilson, M. W. Barsoum and A. J. D. Magenau, Chem. Mater., 2021, 33, 1648–1656 CrossRef CAS.
- Z. Ling, C. Ren, M. Zhao, J. Yang, J. Giammarco, J. Qiu, M. Barsoum and Y. Gogotsi, Proc. Natl. Acad. Sci. U. S. A., 2014, 111, 16676–16681 CrossRef CAS PubMed.
- G. S. Lee, T. Yun, H. Kim, I. H. Kim, J. Choi, S. H. Lee, H. J. Lee, H. S. Hwang, J. G. Kim, D. Kim, H. M. Lee, C. M. Koo and S. O. Kim, ACS Nano, 2020, 14, 11722–11732 CrossRef CAS.
- W. T. Cao, F. F. Chen, Y. J. Zhu, Y. G. Zhang, Y. Y. Jiang, M. G. Ma and F. Chen, ACS Nano, 2018, 12, 4583–4593 CrossRef CAS.
- J. Liu, Z. Liu, H. B. Zhang, W. Chen, Z. Zhao, Q. W. Wang and Z. Z. Yu, Adv. Electron. Mater., 2020, 6, 1901094 CrossRef CAS.
- S. Wan, X. Li, Y. Wang, Y. Chen, X. Xie, R. Yang, A. P. Tomsia, L. Jiang and Q. Cheng, Proc. Natl. Acad. Sci. U. S. A., 2020, 117, 27154–27161 CrossRef CAS.
- S. Wan, X. Li, Y. Chen, N. Liu, Y. Du, S. Dou, L. Jiang and Q. Cheng, Science, 2021, 374, 96–99 CrossRef CAS.
- L. Li, Y. Cao, X. Liu, J. Wang, Y. Yang and W. Wang, ACS Appl. Mater. Interfaces, 2020, 12, 27350–27360 CrossRef CAS.
- D. C. Marcano, D. V. Kosynkin, J. M. Berlin, A. Sinitskii, Z. Sun, A. S. Slesarev, L. B. Alemany, W. Lu and J. M. Tour, ACS Nano, 2018, 12, 2078 CrossRef CAS PubMed.
- Y. Wan, P. Xiong, J. Liu, F. Feng, X. Xun, F. M. Gama, Q. Zhang, F. Yao, Z. Yang, H. Luo and Y. Xu, ACS Nano, 2021, 15, 8439–8449 CrossRef CAS PubMed.
- Z. Ma, S. Kang, J. Ma, L. Shao, Y. Zhang, C. Liu, A. Wei, X. Xiang, L. Wei and J. Gu, ACS Nano, 2020, 14, 8368–8382 CrossRef CAS PubMed.
- Z. Ma, X. Xiang, L. Shao, Y. Zhang and J. Gu, Angew. Chem., Int. Ed., 2022, 61, e202200705 CAS.
- Z. Hao, S. Zhang, S. Yang, X. Li, Y. Gao, J. Peng, L. Li, L. Bao and X. Li, ACS Appl. Energy Mater., 2022, 5, 2898–2908 CrossRef CAS.
- X. Tan, T. Liu, W. Zhou, Q. Yuan, J. Ying, Q. Yan, L. Lv, L. Chen, X. Wang, S. Du, Y. Wan, R. Sun, K. Nishimura, J. Yu, N. Jiang, W. Dai and C. Lin, ACS Nano, 2022, 16, 9254–9266 CrossRef CAS PubMed.
- I. K. Moon, J. Lee, R. S. Ruoff and H. Lee, Nat. Commun., 2010, 1, 73 CrossRef.
- J. Wu, W. Lin, Z. Wang, S. Chen and Y. Chang, Langmuir, 2012, 28, 7436–7441 CrossRef CAS.
- J. Cao, Z. Zhou, Q. Song, K. Chen, G. Su, T. Zhou, Z. Zheng, C. Lu and X. Zhang, ACS Nano, 2020, 14, 7055–7065 CrossRef CAS PubMed.
- X. Huang, J. Huang, G. Zhou, Y. Wei, P. Wu, A. Dong and D. Yang, Small, 2022, 18, 2200829 CrossRef CAS.
- T. Zhou, C. Wu, Y. Wang, A. P. Tomsia, M. Li, E. Saiz, S. Fang, R. H. Baughman, L. Jiang and Q. Cheng, Nat. Commun., 2020, 11, 2077 CrossRef CAS PubMed.
- T. Zhou, H. Ni, Y. Wang, C. Wu, H. Zhang, J. Zhang, A. P. Tomsia, L. Jiang and Q. Cheng, Proc. Natl. Acad. Sci. U. S. A., 2020, 117, 8727–8735 CrossRef CAS PubMed.
- Y. Cheng, J. Peng, H. Xu and Q. Cheng, Adv. Funct. Mater., 2018, 28, 1800924 CrossRef.
- S. Wan, X. Li, Y. Wang, Y. Chen, X. Xie, R. Yang, A. P. Tomsia, L. Jiang and Q. Cheng, Proc. Natl. Acad. Sci. U. S. A., 2020, 117, 27154–27161 CrossRef CAS.
- B. Zhou, Z. Zhang, Y. Li, G. Han, Y. Feng, B. Wang, D. Zhang, J. Ma and C. Liu, ACS Appl. Mater. Interfaces, 2020, 12, 4895–4905 CrossRef CAS.
- H. Zhu, Q. Li, C. Zheng, Y. Hong, Z. Xu, H. Wang, W. Shen, S. Kaur, P. Ghosh and M. Qiu, Light: Sci. Appl., 2020, 9, 60 CrossRef CAS.
- M. Pan, Y. Huang, Q. Li, H. Luo, H. Zhu, S. Kaur and M. Qiu, Nano Energy, 2020, 69, 104449 CrossRef CAS.
- Q. Liao, P. Zhang, H. Yao, H. Cheng, C. Li and L. Qu, Adv. Sci., 2020, 7, 1903125 CrossRef CAS.
- L. Peng, D. Liu, H. Cheng, S. Zhou and M. Zu, Adv. Opt. Mater., 2018, 6, 1801006 CrossRef.
- J. Lyu, Z. Liu, X. Wu, G. Li, D. Fang and X. Zhang, ACS Nano, 2019, 13, 2236–2245 CrossRef.
- O. Salihoglu, H. B. Uzlu, O. Yakar, S. Aas, O. Balci, N. Kakenov, S. Balci, S. Olcum, S. Suzer and C. Kocabas, Nano Lett., 2018, 18, 4541–4548 CrossRef CAS.
- H. Ji, D. Liu, H. Cheng, C. Zhang and L. Yang, Sol. Energy Mater. Sol. Cells, 2018, 175, 96–101 CrossRef CAS.
- X. Wang, Y. Tang, Y. Wang, L. Ke, X. Ye, X. Huang and B. Shi, Chem. Eng. Sci., 2019, 196, 64–71 CrossRef CAS.
- W. Gu, J. Tan, J. Chen, Z. Zhang, Y. Zhao, J. Yu and G. Ji, ACS Appl. Mater. Interfaces, 2020, 12, 28727–28737 CrossRef CAS.
- A. Choe, J. Yeom, Y. Kwon, Y. Lee, Y.-E. Shin, J. Kim and H. Ko, Mater. Horiz., 2020, 7, 3258–3265 RSC.
- X. Zhang, N. Li, Z. Hu, J. Yu, Y. Wang and J. Zhu, Chem. Eng. J., 2020, 388, 124310 CrossRef.
- W. Lan, Y. Chen, Z. Yang, W. Han, J. Zhou, Y. Zhang, J. Wang, G. Tang, Y. Wei, W. Dou, Q. Su and E. Xie, ACS Appl. Mater. Interfaces, 2017, 9, 6644–6651 CrossRef CAS.
- H. J. Kim, Y. Kim, J. H. Jeong, J. H. Choi, J. Lee and D. G. Choi, J. Mater. Chem. A, 2015, 3, 16621–16626 RSC.
- Y. Guo, C. Dun, J. Xu, J. Mu, P. Li, L. Gu, C. Hou, C. A. Hewitt, Q. Zhang, Y. Li, D. L. Carroll and H. Wang, Small, 2017, 13, 1702645 CrossRef PubMed.
- Y. Wang, Z. Yu, G. Mao, Y. Liu, G. Liu, J. Shang, S. Qu, Q. Chen and R. W. Li, Adv. Mater. Technol., 2019, 4, 1800435 CrossRef.
- W. J. Sun, L. Xu, L. C. Jia, C. G. Zhou, Y. Xiang, R. H. Yin, D. X. Yan, J. H. Tang and Z. M. Li, Compos. Sci. Technol., 2019, 181, 107695 CrossRef CAS.
- H. Kim, M. Seo, J.-W. Kim, D.-K. Kwon, S.-E. Choi, J. W. Kim and J.-M. Myoung, Adv. Funct. Mater., 2019, 29, 1901061 CrossRef.
- Z. Ma, S. Kang, J. Ma, L. Shao, A. Wei, C. Liang, J. Gu, B. Yang, D. Dong, L. Wei and Z. Ji, ACS Nano, 2019, 13, 7578–7590 CrossRef CAS.
- P. Hu, J. Lyu, C. Fu, W. Gong, J. Liao, W. Lu, Y. Chen and X. Zhang, ACS Nano, 2020, 14, 688–697 CrossRef CAS PubMed.
- H. S. Jang, K. J. Sang and S. H. Nahm, Carbon, 2011, 49, 111–116 CrossRef CAS.
- Y. Cheng, H. Zhang, R. Wang, X. Wang, H. Zhai, T. Wang, Q. Jin and J. Sun, ACS Appl. Mater. Interfaces, 2016, 8, 32925–32933 CrossRef CAS.
- P. Liu, Y. Li, Y. Xu, L. Bao, L. Wang, J. Pan, Z. Zhang, X. Sun and H. Peng, Small, 2018, 14, 1702926 CrossRef.
- L. Zhang, M. Baima and T. L. Andrew, ACS Appl. Mater. Interfaces, 2017, 9, 32299–32307 CrossRef CAS.
- Q. W. Wang, H. B. Zhang, J. Liu, S. Zhao, X. Xie, L. Liu, R. Yang, N. Koratkar and Z. Z. Yu, Adv. Funct. Mater., 2019, 29, 1806819 CrossRef.
- G. S. Lee, T. Yun, H. Kim, I. H. Kim, J. Choi, S. H. Lee, H. J. Lee, H. S. Hwang, J. G. Kim, D. Kim, H. M. Lee, C. M. Koo and S. O. Kim, ACS Nano, 2020, 14, 11722–11732 CrossRef CAS.
- X. Luo, W. Weng, Y. Liang, Z. Hu, Y. Zhang, J. Yang, L. Yang, S. Yang, M. Zhu and H. M. Cheng, J. Mater. Chem. A, 2019, 7, 8790–8797 RSC.
- Q. Liu, J. Huang, J. Zhang, Y. Hong, Y. Wan, Q. Wang, M. Gong, Z. Wu and C. F. Guo, ACS Appl. Mater. Interfaces, 2018, 10, 2026–2032 CrossRef CAS PubMed.
- A. Hazarika, B. K. Deka, C. Jeong, Y. B. Park and H. W. Park, Adv. Funct. Mater., 2019, 29, 1903144 CrossRef.
- R. Liu, M. Miao, Y. Li, J. Zhang, S. Cao and X. Feng, ACS Appl. Mater. Interfaces, 2018, 10, 44787–44795 CrossRef CAS.
- Z. Zhan, Q. Song, Z. Zhou and C. Lu, J. Mater. Chem. C, 2019, 7, 9820–9829 RSC.
- F. Xie, F. Jia, L. Zhuo, Z. Lu, L. Si, J. Huang, M. Zhang and Q. Ma, Nanoscale, 2019, 11, 23382–23391 RSC.
- W. Yang, Z. Zhao, K. Wu, R. Huang, T. Liu, H. Jiang, F. Chen and Q. Fu, J. Mater. Chem. C, 2017, 5, 3748–3756 RSC.
- W. Cao, C. Ma, S. Tan, M. Ma, P. Wan and F. Chen, Nano-Micro Lett., 2019, 11, 72 CrossRef CAS.
- Y. Chen, H.-B. Zhang, Y. Yang, M. Wang, A. Cao and Z.-Z. Yu, Adv. Funct. Mater., 2016, 26, 447–455 CrossRef CAS.
- K. Yao, J. Gong, N. Tian, Y. Lin, X. Wen, Z. Jiang, H. Na and T. Tang, RSC Adv., 2015, 5, 31910–31919 RSC.
- Y. Sun, R. Ding, S. Y. Hong, J. Lee, Y. Seo, J. Nam and J. Suhr, Chem. Eng. J., 2021, 410, 128348 CrossRef CAS.
- F. Fang, Y.-Q. Li, H.-M. Xiao, N. Hu and S.-Y. Fu, J. Mater. Chem. C, 2016, 4, 4193–4203 RSC.
- L.-C. Jia, M.-Z. Li, D.-X. Yan, C.-H. Cui, H.-Y. Wu and Z.-M. Li, J. Mater. Chem. C, 2017, 5, 8944–8951 RSC.
- W. Yang, Y. Zhang, T. Liu, R. Huang, S. Chai, F. Chen and Q. Fu, ACS Sustainable Chem. Eng., 2017, 5, 9102–9113 CrossRef CAS.
- X. Li, S. Zeng, S. E, L. Liang, Z. Bai, Y. Zhou, B. Zhao and R. Zhang, ACS Appl. Mater. Interfaces, 2018, 10, 40789–40799 CrossRef CAS PubMed.
- Q. Wei, S. Pei, X. Qian, H. Liu, Z. Liu, W. Zhang, T. Zhou, Z. Zhang, X. Zhang, H. Cheng and W. Ren, Adv. Mater., 2020, 32, 1907411 CrossRef CAS.
- Y. Zhang, M.-K. Wang, Z. Wang, T. Zhao, L.-X. Liu, H.-B. Zhang and Z.-Z. Yu, Nano Res., 2022, 15, 4916–4924 CrossRef CAS.
- J.-Q. Luo, S. Zhao, H.-B. Zhang, Z. Deng, L. Li and Z.-Z. Yu, Compos. Sci. Technol., 2019, 182, 107754 CrossRef CAS.
- Y. L. Zhang, K. P. Ruan and J. W. Gu, Small, 2021, 17, 2101951 CrossRef CAS PubMed.
- L. Wang, Z. Ma, Y. Zhang, H. Qiu, K. Ruan and J. Gu, Carbon Energy, 2022, 4, 200–210 CrossRef CAS.
|
This journal is © The Royal Society of Chemistry 2023 |
Click here to see how this site uses Cookies. View our privacy policy here.