DOI:
10.1039/D3NA00326D
(Paper)
Nanoscale Adv., 2023,
5, 4911-4924
Fast synthesis of [1,2,3]-triazole derivatives on a Fe/Cu-embedded nano-catalytic substrate†
Received
14th May 2023
, Accepted 6th August 2023
First published on 29th August 2023
Abstract
Triazoles are biologically important compounds that play a crucial role in biomedical applications. In this study, we present an innovative and eco-friendly nanocatalyst system for synthesizing compounds via the click reaction. The system is composed of Arabic gum (AG), iron oxide magnetic nanoparticles (Fe3O4 MNPs), (3-chloropropyl) trimethoxysilane (CPTMS), 2-aminopyridine (AP), and Cu(I) ions. Using AP as an anchor for Cu(I) ions and Fe3O4 MNPs allows facile separation using an external magnet. The hydrophilic nature of the Fe3O4@AG/AP-Cu(I) nanocomposite makes it highly efficient in water as a green solvent. The highest reaction efficiency (95.0%) was achieved in H2O solvent with 50.0 mg of nanocatalyst for 60 min at room temperature. The reaction yield remained consistent for six runs, demonstrating the stability and effectiveness of the catalyst.
1. Introduction
Heterocycles are a large group of organic compounds with high biological properties, including anticancer, antimicrobial, anti-Alzheimer, anti-obesity, anti-diabetic, antihistaminic, anticonvulsant, antiviral, and antiparasitic properties, and are widely used in medicinal compounds.1 In recent decades, research based on triazole derivatives as medicinal compounds has received much attention, and impressive results have been obtained.2,3 Triazole compounds contain a five-membered aromatic azole ring with three nitrogen atoms, which can connect to various enzymes and receptors in the biological system through non-covalent bonds and show excellent biological activities.4 One of the methods for developing triazole products is azide-alkyne Huisgen cycloaddition which occurs between an azide and a terminal or internal alkyne to give a 1,2,3-triazole and named the click reaction.5 The Azide-alkyne Huisgen cycloaddition reaction, which produces covalently linked molecules via a 1,2,3-triazole, is among the superior transformations in synthetic organic chemistry.6,7
Click reactions are gaining tremendous attention because they allow chemists to connect two building blocks easily.8 The distinctive features of thermodynamically controlled copper-catalyzed azide-alkyne cycloaddition, such as facile and moderate reaction conditions, compatibility with a wide range of different functional groups and various solvents, and wide pH range tolerance, introduce this reaction as a powerful method for biologically pertinent molecule synthesis and modification of organic scaffolds.9 Nevertheless, high reaction temperature and lack of regioselectivity are the main disadvantages of this reaction.10 Using metal ions as catalysts is a powerful method to accelerate many organic reactions.11 Studies show that copper metal has been used as a catalyst in the click reaction in several forms, such as metal salt,12 copper nanoparticles (NPs),13 copper stabilized on polymer substrates,14 CuSO4-ascorbate systems,15 and nanostructured copper oxide.16 According to reports, heterogeneous catalytic systems have attracted much attention in both micro and nanoscales due to the high surface area for chemical reactions between the reactants and the catalytic substrate.17
One of the essential features in constructing heterogeneous catalysts is their easy separation from the reaction flask.18 In this regard, heterogeneous catalytic systems based on MNPs are widely used due to their easy separation by using an external magnet.19–36 Over the past few decades, MNPs with a unique size and structure have garnered significant attention due to their distinct physical and chemical properties.37,38 A multitude of strategies have been developed to synthesize a variety of magnetic nanomaterials, including iron, cobalt, nickel, alloys, iron oxide, metal ferrite, and more.39–41 Among all magnetic materials, magnetite (Fe3O4) is the most important and widely utilized in numerous fields.42 When engineered into well-defined nanoscale structures, Fe3O4 exhibits vast potential for practical applications in various domains, such as biomolecular separation,43 chemical sensing,44 energy storage,45 catalysis,46–51 absorption,52,53 biomedicine/biotechnology,54–61 and environmental remediation. Fe3O4 MNPs can be synthesized using various methods, such as coprecipitation of Fe2+ and Fe3+, thermal decomposition, microemulsion, and hydrothermal/solvothermal techniques. Of all the methods mentioned, coprecipitation is the favored option for most researchers due to its ability to be conducted under mild conditions using water as a solvent.62–65 Due to the high importance of the environment and green chemistry, researchers are looking to make catalysts based on biodegradable and environmentally friendly materials. Accordingly, heterogeneous catalytic systems are modified by different components such as natural polymers, minerals, and biological structures so that more catalytic sites are available.25,66–70
AG has a natural origin from wild trees primarily found in Somalia.71,72 Using natural polymer (AG) is a direct approach to successfully synthesize the aqueous phase of various metal NPs.73,74 This polymer is widely used as a stabilizer, reducing agent, emulsifying agent, and additive in various NP syntheses.75–78 The functional hydroxyl groups in the structure of this natural polymer can make a physicochemical hydrogen bond with hydroxyl groups on the surface of MNPs.79 Other hydroxyl groups not involved in hydrogen bonds can be functionalized by covalent bonds with various linkers.80 From a green and sustainable chemistry perspective, a recent surge of interest has been in designing efficient and cost-effective chemical processes that utilize heterogeneous catalysts to synthesize fine chemicals and pharmaceutical products through multicomponent reactions (MCRs).81–83 However, the limited catalytic activity of these catalysts remains a significant challenge. Minimizing the particles' size in the heterogeneous catalyst is crucial to overcome this issue.84,85 Nanostructured catalysts, which lie at the interface of homogeneous and heterogeneous catalysis, are known as “quasi-homogeneous” or “soluble heterogeneous” catalysts due to their nanoscale nature and high surface area.86,87
Nonetheless, conventional separation techniques such as filtration and centrifugation become problematic for suspensions containing particles smaller than 100 nm, making it difficult to separate the catalyst.88,89 Today, magnetic nanocatalysts are widely used to develop sustainable and green processes due to easy separation, low energy loss, and economic efficiency.90,91 Fe3O4 MNPs have gained prominence due to their unique properties, including easy preparation from low-cost precursors, high surface area, low toxicity, excellent reusability, and biocompatibility.92 Usually, these NPs are protected by surface functionalization with biological coatings to prevent oxidation and self-assembly and increase stability.93,94
In this work, a novel magnetic nanocatalyst is designed based on AG as a natural polymer with low toxicity. First, Fe3O4 MNPs were selected as a central core of the nanocatalyst to prepare a magnetic nanocatalyst with easy separation.95 AG was chosen as the primary cover. The MNPs were incorporated into the AG matrix polymer to improve stability and prevent accumulation. Also, the dispersibility of the nanocomposite can be increased due to the presence of hydrophilic functional groups such as hydroxyl (–OH) and carbonyl (–COOH) groups in the AG structure.96 For this purpose, Fe3O4 MNPs were synthesized in a flask reaction and fixed in situ inside the matrix polymer.97 Following this, the Fe3O4@AG nanocomposite surface was modified by CPTMS so that the anchor molecules (AP) could be attached to it. CPTMS was added to the Fe3O4@AG solution in this stage and kept under reflux treatment. The AP molecule with a unique dual nucleophilic structure was selected as an anchor to place Cu(I) ions by coordination bonds.98 Also, this stage was performed by adding AP and triethylamine to the Fe3O4@AG@CPTMS solution under reflux conditions. Finally, the Cu(I) ion chelated with nitrogen atoms of the AP compound to act as the active sites for the click reaction. Fourier-transform infrared spectroscopy (FTIR), X-ray diffraction analysis (XRD), energy dispersive X-ray (EDX) spectroscopy, thermogravimetric analysis (TGA), vibrating-sample magnetometry (VSM), and field emission scanning electron microscopy (FESEM) were performed to characterize the Fe3O4@AG/AP-Cu(I) nanocomposite and all of them proved its successful synthesis. The synthesis process of the [1,2,3]-triazole derivatives was evaluated in the presence of the Fe3O4@AG/AP-Cu(I) nanocatalyst. The highest efficiency (95%) was obtained with optimization parameters such as 50.0 mg (catalyst dosage), 60 min (time reaction), H2O (solvent), and room temperature. The novel and environmentally friendly nanocatalyst prepared by our research group could be an effective nanocatalyst for synthesizing triazole derivatives. This nanocatalyst's turnover number (TON) and turnover frequency (TOF) values were calculated to be 48.66 and 0.0135, respectively. The novel and environmentally friendly nanocatalyst our research group prepared could be an effective nanocatalyst for synthesizing [1,2,3]-triazole derivatives.
2. Experimental
2.1. Materials and equipment
All the chemical materials, solvents, and reagents were purchased from Sigma-Aldrich and Merck companies. The FTIR analysis was performed by using a Shimadzu FTIR-8400S spectrometer via the KBr pellet method. The XRD analysis was performed with a DRON-8 X-ray diffractometer. The EDX spectrum was obtained by using a VEGA-TESCAN-XMU. Also, TGA, inductively coupled plasma optical emission spectroscopy (ICP-OES), and vibrating-sample magnetometry (VSM) were performed by using a Bahr-STA 504 instrument under an argon atmosphere, Varian VIST-MPX with an axial torch, and LBKFB model-magnetic Kashan Kavir (5000 Oe) instrument, respectively.
2.2. Preparation of Fe3O4@AG nanopowder
0.64 g of iron(II) and 1.20 g of iron(III) chloride salts were initially dissolved in 10.0 mL of deionized water at an ambient temperature. Afterward, 0.60 g of AG powder was poured and dissolved in the reaction flask. In the next stage, iron ions were precipitated through the co-deposition method, and the formed Fe3O4 MNPs were composed of the AG polymer. Finally, the in situ method provides a better composition, and immobilization of the dark Fe3O4 MNPs was carried out by using an ammonia solution to increase the pH value to 12.25
2.3. Preparation of the Fe3O4@AG@CPTMS magnetic nanocomposite
Fe3O4@AG (1.0 g) was poured into a round bottom flask containing 20.0 mL dry toluene. First, the obtained mixture was sonicated for 20 min. Next, MNP modification with 3-chloropropyltrimethoxysilane (CPTMS) was accomplished by adding 3.0 mL of CPTMS (16.45 mmol) into the mixture under stirring and reflux in toluene (110 °C) for 24 h, under a N2 atmosphere. Then, the resultant product was rinsed with absolute ethanol to remove unattached substrates and eventually dried at 100 °C for 12 h.79
2.4. Preparation of the Fe3O4@AG/AP magnetic nanocomposite
The prepared Fe3O4@AG@CPTMS was sonicated for 30 min. Then, 0.4 g AP and 2.0 mL triethylamine were added to a round bottom flask containing 40.0 mL ethanol, and refluxed for 24 h at 70 °C under an N2 atmosphere to prepare the Fe3O4@AG/AP magnetic nanocomposite.
2.5. Preparation of the Fe3O4@AG/AP-Cu(I) magnetic nanocomposite
Finally, the catalyst was synthesized by reacting Fe3O4@AG/AP with 0.8 g copper(I) chloride. The Cu particles in the prepared Fe3O4@AG/AP-Cu(I) act as the active sites for the one-pot synthesis of 1,2,3 triazole derivatives.99
2.6. General process of the synthesis of triazole derivatives (4a–q) in the presence of Fe3O4@AG/AP-Cu(I)
For the synthesis of triazole derivatives, 1.0 mmol, 1.1 mmol, and 1.0 mmol of each reactant, such as alkyne, sodium azide, and 2-chloro-N-phenyl-acetamide, respectively, were mixed in the presence of distilled water (2.0 mL), and 50.0 mg of the prepared nanocatalyst was added to it. The solution mixture was stirred for an appropriate time at room temperature. Next, the nanocatalyst was separated magnetically from the reaction flask. Finally, the product was isolated by filtration and washed several times with ethanol, and the recrystallization process was performed to obtain the pure product.
3. Results and discussion
3.1. Preparation of the Fe3O4@AG/AP-Cu(I) magnetic nanocomposite
Our primary objective in this research was to uphold the tenets of green chemistry while enhancing the catalyst's efficacy in synthesizing essential biological compounds like triazoles. To this end, a novel catalyst was developed using a natural polymer and copper ions. This innovation offers numerous benefits, such as being cost-effective and having low toxicity. Our findings demonstrate that this ground-breaking catalyst is exceptionally proficient in synthesizing triazole compounds through click reactions, achieving an unparalleled efficiency rate of 95.0% compared to other catalysts. This high efficiency was achieved only by applying 0.05 g of adsorbent dose.
Furthermore, the presence of the natural AG polymer in the catalyst's structure, which possesses an abundance of hydrophilic groups (–OH and –COOH), results in exceptional performance in water as a green solvent. This aspect aligns with the principles of green chemistry and highlights the potential of this innovative catalyst in promoting environmentally conscious practices. The general method of the designed nanocatalyst synthesis is as follows. First, the Fe3O4@AG nanopowder was prepared via a mixture of the iron(II) and iron(III) chloride solution and AG solution under basic conditions. In this phase, the Fe3O4 MNPs are immobilized within the polymer matrix via electrostatic interactions between the carboxylic group of AG and the surface hydroxyl group of Fe3O4, thereby ensuring optimal stability and functionality. In the second stage, the Fe3O4@AG powder was dissolved in dry toluene, and CPTMS was added to it. Then, the solution mixture was refluxed for 24 h. In the third step, the Fe3O4@AG@CPTMS solution was dispersed by sonication. CPTMS was employed to attach AP onto the Fe3O4@AG composite surface. This procedure was achieved by forming a covalent bond between the hydroxyl groups present on the composite surface and the Si atoms of the CPTMS structure. Next, AP and trimethylamine were added to Fe3O4@AG@CPTMS solution in ethanol and refluxed under an N2 atmosphere. To facilitate the placement of Cu ions, trimethylamine and AP were utilized to activate the amino group within the AP structure and serve as an anchor. In the final step, the fabricated Fe3O4@AG/AP magnetic nanocomposite was reacted with CuCl and Cu(I) placed on the AP via coordination interaction with N-donor ligands. The preparation process of the Fe3O4@AG/AP-Cu(I) magnetic nanocomposite is displayed in Scheme 1. Eventually, the final product was characterized by FTIR, XRD, TGA, EDX, VSM, and FESEM analyses.
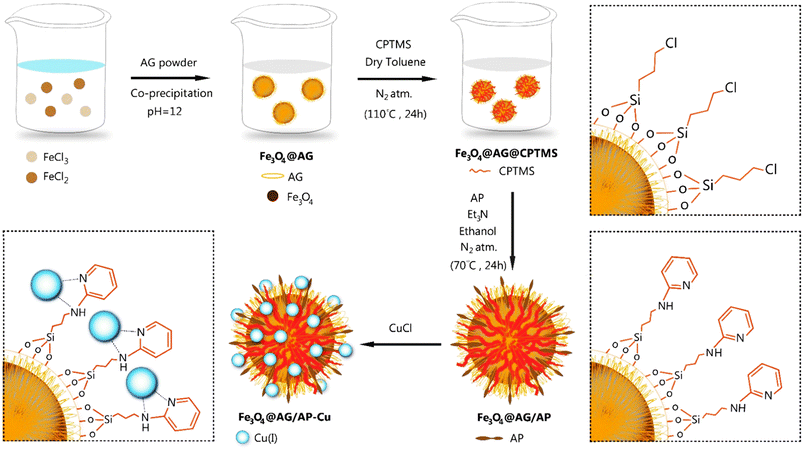 |
| Scheme 1 The preparation process of the Fe3O4@AG/AP-Cu(I) magnetic nanocomposite. | |
3.2. Characterization of the Fe3O4@AG/AP-Cu(I) magnetic nanocomposite
3.2.1. FTIR analysis.
To characterize the basic functional groups in the structure of Fe3O4@AG/AP-Cu(I) magnetic nanocomposite, Fourier-transform infrared (FTIR) spectra of the AG (spectrum I), Fe3O4@AG nanopowder (spectrum II), the Fe3O4@AG@CPTMS magnetic nanocomposite (spectrum III), the Fe3O4@AG/AP magnetic nanocomposite (spectrum IV), and the Fe3O4@AG/AP-Cu(I) magnetic nanocomposite (spectrum V) are displayed in Fig. 1a. In spectrum I, the absorbance peaks at around 3422 and 2939 cm−1 are related to the stretching vibration of O–H and C–H (hybridization sp3) bonds. Two strong peaks at 1603 and 1424 cm−1 confirm the presence of the COO− group.25,100 In spectrum II, the absorbance peak at around 558 cm−1 confirms the presence of Fe3O4 MNPs in the Fe3O4@AG magnetic nanocomposite. In spectrum III, the existent peaks at 1116, 1043, and 2933 cm−1 are ascribed to the Si–O and C–H stretching bonds in the CPTMS structure.101 In spectrum IV, the characterized absorption peaks occurring at 1690–1560 cm−1 and 1405 cm−1 are attributed to the bending vibration of the N–H bond, and stretching vibration of C
N, and C–N bonds of AP in the structure of the Fe3O4@AG/AP magnetic nanocomposite.102–104 In addition, the stretching vibrations of Cu–O bonds in the structure of the Fe3O4@AG/AP-Cu(I) nanocomposite appear at ∼635 cm−1, which overlapped with the peak related to the stretching vibrations of Fe–O bonds.14
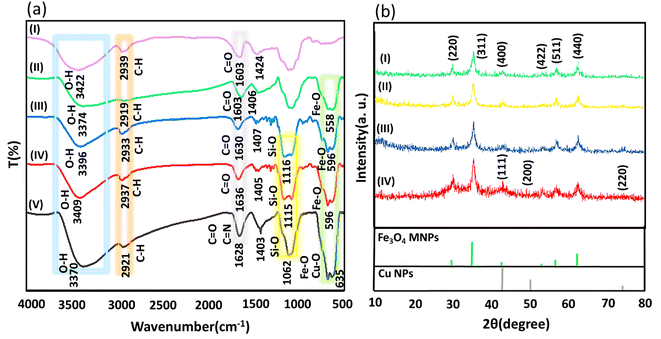 |
| Fig. 1 FTIR spectra of AG (I), Fe3O4@AG (II), Fe3O4@AG@CPTMS (III), Fe3O4@AG/AP (IV), and Fe3O4@AG/AP-Cu(I) (V) (a) and XRD patterns of Fe3O4@AG (I), Fe3O4@AG@CPTMS (II), Fe3O4@AG/AP (III), and Fe3O4@AG/AP-Cu(I) (IV) nanocomposites (b). | |
3.2.2. XRD analysis.
The XRD patterns of the Fe3O4@AG (I), Fe3O4@AG@CPTMS (II), Fe3O4@AG/AP (III), and Fe3O4@AG/AP-Cu(I) (IV) nanocomposites are illustrated in Fig. 1b. All diffraction patterns have a fine match with the reference pattern of the Fe3O4 MNPs. It confirms that they have been well distributed onto the AG textures. These peaks appear at 2θ = 30.22°, 35.55°, 43.28°, 53.56°, 57.19°, and 62.81° that are related to the (220), (311), (400), (422), (511), and (400) Miller indices, respectively, with 00-19-0629 JCPDS card number.105 In the diffraction pattern attributed to the Fe3O4@AG/AP-Cu(I) (IV) nanocomposite, three essential peaks at 2θ = 43.28°, 50.18°, and 74.68° with (111), (200), and (220) Miller indices confirmed the presence of Cu NPs in the final product (JCPDS card no. 00-004-0836).106
3.2.3. EDX analysis.
Energy-dispersive X-ray (EDX) analysis was also performed to characterize the prepared compositions' constituent elements, as shown in Fig. 2. Based on Fig. 2a, oxygen, carbon, and iron peaks confirm the presence of AG as a natural polymer and Fe3O4 MNPs in the structure of Fe3O4@AG nanocomposite. In Fig. 2b, the assigned Si and Cl peaks can be related to the presence of the CPTMS structure and its successful connection to the Fe3O4@AG nanocomposite. In Fig. 2c, the presence of N, C, and O peaks in the spectrum is attributed to the AG and AP structures. In addition, the other peaks, such as those of Fe, Si, and Cl, are related to Fe3O4 and CPTMS in the Fe3O4@AG/AP nanocomposite structure. The EDX spectrum of the final product shows the poor peaks of Cu that confirm the interaction between N atoms in the AP and Cu NPs and the formation of the Fe3O4@AG/AP-Cu(I) nanocomposite (Fig. 2d).
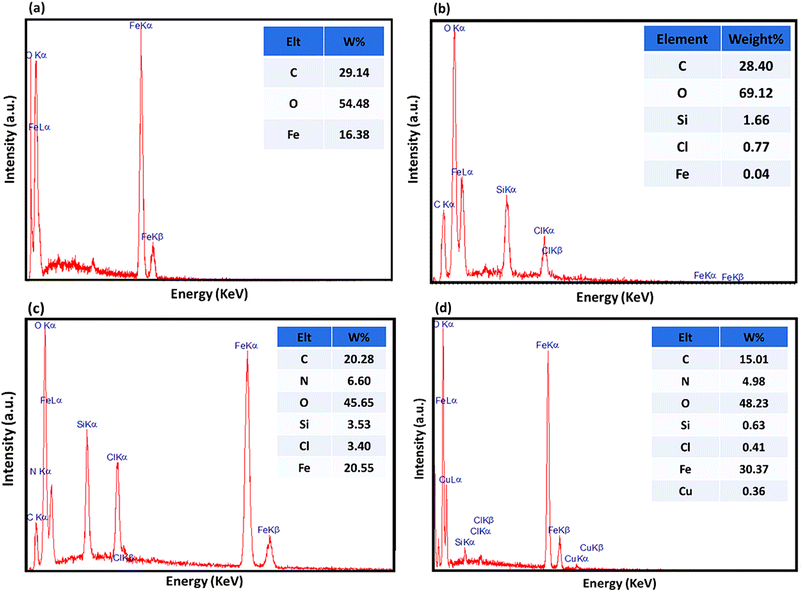 |
| Fig. 2 Results of the energy dispersive X-ray (EDX) analysis of Fe3O4@AG (a), Fe3O4@AG@CPTMS (b), Fe3O4@AG/AP (c), and Fe3O4@AG/AP-Cu(I) (d) nanocomposites. | |
3.2.4. TGA analysis.
The thermogravimetric analysis (TGA) was performed in a thermal range of 50–600 °C to evaluate the thermal stability of the prepared Fe3O4@AG/AP-Cu(I) nanocomposite (Fig. 3a). As can be seen, initially, a weight increase occurs with the increase in temperature up to about 60 °C, which can occur due to the device's buoyancy effect.107 As the temperature increases, a 13.0% weight decrease occurs at 214–388 °C, which can be attributed to the decomposition of organic compounds such as the polysaccharide backbone and AP structure.108 Accordingly, the prepared catalyst will not be destroyed under the experimental conditions because the reaction temperature was about 100 °C.
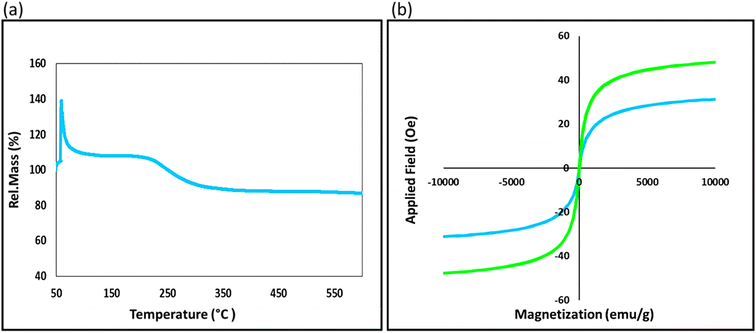 |
| Fig. 3 The TGA of the Fe3O4@AG/AP-Cu(I) nanocomposite (a), and the M–H curves of the Fe3O4@AG (green curve) and Fe3O4@AG/AP-Cu(I) nanocomposites (blue curve) at room temperature (b). | |
3.2.5. VSM analysis.
Vibrating-sample magnetometry (VSM) was used to evaluate the magnetic properties of the obtained products, as illustrated in Fig. 3b. As can be seen, a comparison has been made between Fe3O4@AG and Fe3O4@AG/AP-Cu(I) nanocomposites. Both samples rendered a superparamagnetic behavior. Initially, the saturation magnetization value of NPs coated with natural polymer was recorded as 48.06 emu g−1 (green curve). Subsequently, the magnetic characteristics of Fe3O4@AG were analyzed after the attachment of CPTMS, AP, and Cu ions onto its surface, resulting in a decrease of ca. 17 emu g−1, ultimately reaching a value of 31.21 emu g−1 for the Fe3O4@AG/AP-Cu(I) nanocomposite (blue curve). This significant reduction corroborates the effective functionalization of the AG surface with copper ions. The saturation magnetization value of the final nanocomposite is sufficient for performing a magnetically suitable separation process.
3.2.6. FESEM analysis.
The FESEM analysis was performed to identify the morphology of the products step by step and is illustrated in Fig. 4. In Fig. 4a, the spherical morphology of Fe3O4 MNPs can be seen. The image reveals a homogeneous distribution of NPs within the polymer matrix, exhibiting a consistent morphology and dimensions. The mean particle diameter was determined to be 65.87 nm. Fig. 4b shows particle agglomeration that occurs after adding CPTMS. This can be attributed to the adhesive nature of the silicate compounds.15 The spherical morphology is completely lost after adding AP as anchor molecules, and a sheet structure appears (Fig. 4c). In the final step, the Cu ions were placed on the surface of the Fe3O4@AG/AP nanocomposite (Fig. 4d).
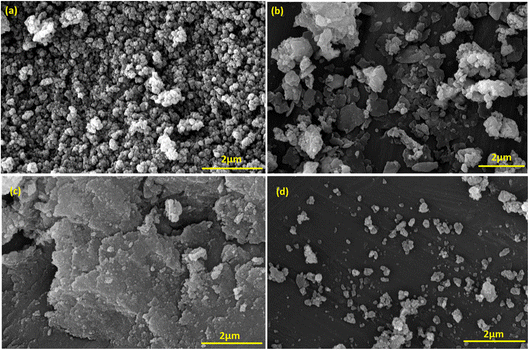 |
| Fig. 4 FESEM images of Fe3O4@AG (a), Fe3O4@AG@CPTMS (b), Fe3O4@AG/AP (c), and Fe3O4@AG/AP-Cu(I) (d) nanocomposites. | |
3.3. Application of the Fe3O4@AG/AP-Cu(I) nanocomposite
3.3.1. Optimization of essential parameters in a catalyzed click reaction with the Fe3O4@AG/AP-Cu(I) nanocomposite.
The effective and essential parameters such as solvent, reaction time, temperature, and product efficiency were evaluated for promoting catalyzed [1,2,3]-triazole compound preparation reactions. In this regard, 1.0 mmol of alkyne, 1.1 mmol of sodium azide, and 1.0 mmol of 2-chloro-N-phenyl-acetamide derivatives were applied under different conditions, and experiments were performed in the presence and absence of several amounts of the Fe3O4@AG/AP-Cu(I) nanocatalyst. The reaction was investigated in water, ethanol, toluene, acetonitrile, chloroform, isopropanol, and 1,4-dioxane solvents. The results showed that the highest efficiency of 95.0% was obtained in water solvent and at room temperature (Table 1). Increasing the catalyst dosage to 50.0 mg was very effective in enhancing reaction efficiency and had a direct relationship. The evaluation of the laboratory results showed that the designed nanocatalyst having AG chains as a natural hydrophilic polymer in its structure was dispersed well in a water solvent. Therefore, Fe3O4@AG/AP-Cu(I) particles can interact significantly with available reactants in water solvents and increase the reaction efficiency.17 The catalytic process is heavily influenced by the solvent's characteristics, particularly its dipolarity or polarity, as well as its proticity and basicity, which determine its ability to donate and accept hydrogen bonds. In the prepared nanocatalyst structure, the AG natural polymer is endowed with numerous hydrophilic groups, such as –OH and –COOH, which enable it to achieve a superior dispersion in the solvent by forming hydrogen bond networks with water molecules.109,110 These interactions enhance reaction efficiency, surpassing that of other solvents like toluene, acetonitrile, and chloroform, which were subjected to comparative testing. Furthermore, the superior catalytic performance observed in aqueous solvents, as opposed to other protic solvents like ethanol and isopropanol, can be attributed to the elevated dipolarity of water, which is because two hydrogen atoms are covalently bonded to a single oxygen atom in the water molecular structure. In contrast, each alcohol molecule only has one hydrogen atom attached to an oxygen atom, with the remaining portion being an alkyl group.111
Table 1 The reaction condition optimization of [1,2,3]-triazole compound synthesis in the presence of the Fe3O4@AG/AP-Cu(I) nanocatalyst
3.3.2. Evaluation of the catalytic efficiency of the Fe3O4@AG/AP-Cu(I) nanocomposite in the [1,2,3]-triazole click reaction.
To investigate the performance of the prepared catalyst in the click reaction, a wide range of 2-chloro-N-phenyl-acetamide derivatives with alkyne and sodium azide were used to synthesize [1,2,3]-triazole derivatives. All reactions were performed under optimal conditions, and the results showed high yields at 60 min, 50.0 mg catalyst dosage, and room temperature (Table 2). The 1H-NMR and 13C-NMR spectra of these compounds are shown in the ESI File (2a–2e).†
Table 2 Synthesis of [1,2,3]-triazole derivatives in the presence of the Fe3O4@AG/AP-Cu(I) nanocomposite
Entry |
Alkyne |
Sodium azide |
2-Chloro-N-phenyl-acetamide derivatives |
Product |
Yield (%) |
Number of compounds |
1 |
|
NaN3 |
|
|
95 |
2a
|
2 |
|
NaN3 |
|
|
97 |
2b
|
3 |
|
NaN3 |
|
|
96 |
2c
|
4 |
|
NaN3 |
|
|
90 |
2d
|
5 |
|
NaN3 |
|
|
96 |
2e
|
6 |
|
NaN3 |
|
|
97 |
2f
|
7 |
|
NaN3 |
|
|
97 |
2g
|
3.3.3. Suggested mechanism.
As exhibited in Scheme 2, the proposed mechanism of this reaction is a cyclic and multi-stage reaction in which copper stabilized in an AG polysaccharide substrate plays a fundamental role in forming carbon–nitrogen bonds. At the beginning of the catalytic cycle, the alkyne in the presence of copper stabilized in the natural polymer substrate is converted into copper acetylide (1), an active compound, during a rapid reaction. Also, sodium azide binds to 2-chloro-N-phenyl-acetamide through formation of a carbon–nitrogen bond and leaving a chlorine atom, constituting an alkyl azide compound (2). Then, the copper(I) acetylide structure reacts with the formed alkyl azide, and 1, 3-dipolar cyclization is performed. This process leads to the formation of the final product (3).
 |
| Scheme 2 The synthesis reaction mechanism of triazole derivatives in the presence of the Fe3O4@AG/AP-Cu(I) nanocomposite. | |
3.3.4. Catalyst recycling.
Catalyst recyclability was evaluated to investigate economic and environmental aspects. For this purpose, the prepared nanocatalyst was separated with an external magnet after multicomponent synthesis and washed several times with distilled water and ethanol. Then, it was reused. The results showed that this nanocatalyst acted with high efficiency after even six runs of recycling, and a trivial reduction in the yield was observed. Therefore, it can be concluded that the prepared nanocatalyst can be introduced as a suitable candidate for increasing efficiency and reducing the desired reaction time (Fig. 5a). In order to assess the integrity of the catalyst that was prepared, a series of advanced analytical techniques were employed after six runs of successive recycling. The VSM, FTIR, XRD, TGA, and FESEM analyses were conducted to determine the structural properties of the catalyst. The VSM analysis results indicated that the catalyst's saturation magnetism following six runs was 15.46 emu g−1, a satisfactory value for effectively isolating the catalyst from the reaction solution (Fig. 5b). The FTIR analysis revealed that all the functional groups associated with the synthesized catalyst's structure were well-preserved, indicating that the structure has remained intact even after repeated washing and six reaction cycles. Hence, the structure has not collapsed (Fig. 5c). The XRD pattern shows the presence of Fe3O4 MNPs and Cu NPs in the catalyst structure (Fig. 5d). Furthermore, the TGA analysis demonstrates that the prepared nanocomposite exhibits exceptional thermal stability up to 240 °C, comparable to that of the original sample before recycling (Fig. 5e). In addition, the FESEM images obtained from the sample after undergoing six reaction cycles exhibit preserved catalyst integrity indistinguishable from that in the FESEM images obtained before multiple runs (Fig. 6a and b).
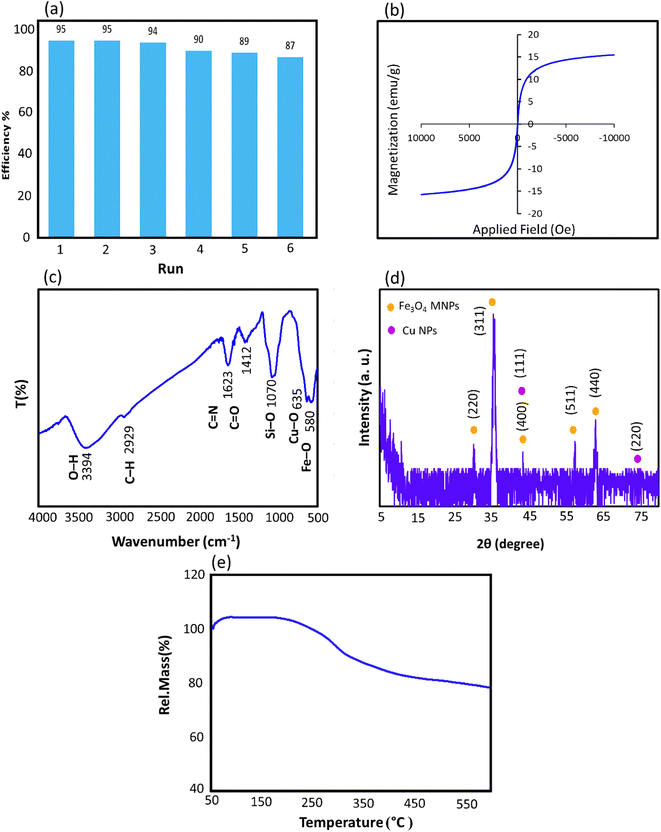 |
| Fig. 5 Catalyst recycling results after six consecutive cycles of [1,2,3]-triazole compound synthesis (a), VSM (b), FTIR (c), XRD (d), and TGA (e) analyses of the nanocatalyst after six sequential recycling cycles. | |
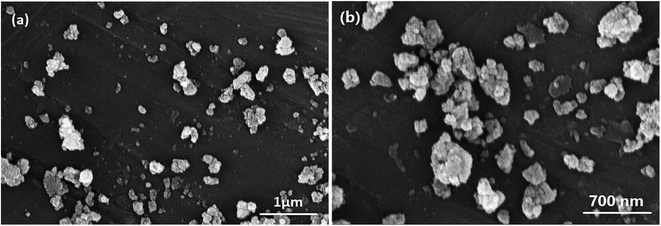 |
| Fig. 6 FESEM images of the nanocatalyst after six sequential recycling cycles on two scales, 1.0 μm (a) and 700.0 nm (b). | |
For the hot test filtration execution, the desired solvent (distilled water) was warmed to reach its boiling point (100 °C). Afterward, the boiled solvent (10.0 mL) was poured on the Fe3Os@AG/AP-Cu(I) nanocatalyst, and after cooling down the reaction temperature to 25 °C, it was filtered by using filter paper. In this regard, the filtration paper was rinsed with boiling water, the reaction mixture was filtered, and the ICP test of the supernatant was carried out. The ICP-OES test was performed to specify the Fe3+ and Cu+ ion amounts released into the supernatant solution under optimized reaction conditions. According to the ICP test results, the released Fe3+ and Cu+ ion concentration in the supernatant solution was measured to be 0.21 ppm and 95.22 ppm, respectively, which can be ascribed to the insufficient magnetic isolation of the magnetic nanocatalyst from the reaction mixture after the accomplishment of the catalytic reaction. Therefore, the meager leaching percentage of the Fe3O4@AG/AP-Cu(I) nanocatalyst or Fe3+ and Cu+ ions into the reaction solution can be neglected; hence, the magnetic nanocatalyst can be employed many times without a decline in the catalytic performance, as authenticated by recyclability tests.
3.3.5. Comparisons of the fabricated Fe3O4@AG/AP-Cu(I) nanocomposite with other catalytic systems.
Here, a general comparison has been made between the designed nanocatalyst and other previously prepared systems that can accelerate the synthesis of triazole derivatives with acceptable yields. As shown in Table 3, the prepared catalyst has significant advantages compared to other catalysts described in the following description. High efficiency (95.0%) has occurred in an appropriate period of 60 min, which was a better performance than that of other catalyst systems (entries 1, 2, and 5). In addition, due to the importance of green chemistry, it is very important to design catalytic systems based on natural and low-toxic materials. In this work, the prepared nanocatalyst is based on AG as a natural hydrophilic polymer, which can cover this issue well compared to other designed catalysts (entries 2, 4, and 5). In addition, this nanocatalyst has the highest efficiency in water as a green solvent compared with the others (entry 1). One of the notable advantages of the designed nanocatalyst is its high performance at ambient temperature, which makes it highly different from many previously designed catalysts and aimed at preventing energy loss (entries 2, 3, 4, and 5).
Table 3 The comparison of the prepared Fe3O4@AG/AP-Cu(I) nanocatalyst and previously reported nanocatalytic systems for click chemistry azide-alkyne cycloaddition
Entry |
Catalyst |
Condition |
Cat.a (mg) |
Time(min) |
Yield (%) |
Ref. |
Catalyst amount.
Waste fishbone powder supported CuBr.
CuO included hollow mesoporous silica spheres.
|
1 |
Cellulose–copper(II) oxide |
r.t./EtOH |
30 |
10 |
92 |
112
|
2 |
Au–Cu core–shell nanocubes |
50 °C/H2O |
3 |
180 |
91 |
113
|
3 |
FBPs-CuBrb |
80 °C/H2O/under MW |
5.50 |
30 |
96 |
114
|
4 |
CuO–HMSSc |
80 °C/H2O |
40 |
8 |
96 |
115
|
5 |
Fe3O4@TiO2/Cu2O |
Reflux/H2O |
20 |
15 |
93 |
116
|
6 |
Fe3O4@AG/AP-Cu(I) |
r.t./H2O |
50 |
60 |
95 |
This work |
4. Conclusion
The click reaction has emerged as a crucial one-pot method for synthesizing triazole heterocyclic compounds, which are highly significant in pharmaceuticals. We have developed a heterogeneous and hydrophilic nanocatalyst to synthesize [1,2,3]-triazole derivatives. The nanocatalyst is based on an AG natural polymer, which enhances its biocompatibility and reduces its toxicity, thereby conforming to the principles of green chemistry. In addition, the nanocatalyst exhibits magnetic properties, which enable it to be easily separated from the reaction flask and reused after washing. The reaction was carried out in water as a green solvent at ambient temperature, and the efficiency of the nanocatalyst was found to be high. Various structural analyses (FTIR, EDX, XRD, TGA, VSM, and FESEM) were conducted to confirm the characteristics of the designed nanocatalyst, and VSM analysis determined the saturation magnetization value to be 31.21 emu g−1. The reaction conditions were optimized, and a reaction yield of 95.0% was achieved for 50.0 mg of catalyst at 60 min. The performance of the nanocatalyst was investigated for [1,2,3]-triazole derivative synthesis, and the results demonstrated its excellent catalytic performance (Table 2). Finally, the recyclability of the nanocatalyst was examined after six successive runs, and all results confirmed the structural stability.
Author contributions
N. Khaleghi: conceptualization and bench work (all synthesis steps), A. Mohammadi: writing the manuscript and preparation of supplementary files,† M. Forouzandeh-Malati: bench work (all synthesis steps), planning to carry out synthesis steps and analyses, Z. Sadat Mojtabapour: bench work (2.2, 2.3, 2.4, and 2.5 Sections of nanocatalyst preparation), analyses and supplying the required materials, F. Ganjali: bench work (all synthesis steps), analysis, and writing the Materials and equipment section, S. Z. Rashvandi: graphics, Simindokht Zarei-Shokat: bench work (2.2, 2.3, 2.4, and 2.5 Sections of nanocatalyst preparation) and follow up to prepare materials, A. Kashtiaray: revision, R. Taheri-Ledari: supervision, project administration, reviewing, editing, and revision, and A. Maleki: supervision, and financial support.
Conflicts of interest
The authors have no conflict of interest.
Acknowledgements
The authors gratefully acknowledge the partial support from the Iran University of Science and Technology (IUST).
References
- P. Shiri and J. Aboonajmi, Beilstein J. Org. Chem., 2020, 16, 551–586 CrossRef CAS PubMed.
- F. Laffafchi, M. Tajbakhsh, Y. Sarrafi, B. Maleki and M. Ghani, Polycyclic Aromat. Compd., 2022, 43, 1–17 Search PubMed.
- E. Arefi, A. Khojastehnezhad and A. Shiri, Sci. Rep., 2021, 11, 20514 CrossRef CAS PubMed.
- C. Zhou, Y. Wang, E. Wong, E. Fonkem, T. Hsieh, J. Wu and E. Wu, Curr. Med. Chem., 2012, 19, 239–280 CrossRef CAS PubMed.
- V. I. Böhmer, W. Szymanski, K. O. van den Berg, C. Mulder, P. Kobauri, H. Helbert and P. H. Elsinga, Eur. J. Chem., 2020, 26, 10871–10881 CrossRef PubMed.
- A. Dondoni, Chem.–Asian J., 2007, 2, 700–708 CrossRef CAS PubMed.
- K. Kowalski, Coord. Chem. Rev., 2023, 479, 214996 CrossRef CAS.
- V. D. Bock, H. Hiemstra and J. H. Van Maarseveen, Eur. J. Org. Chem., 2006, 2006, 51–68 CrossRef.
- V. K. Tiwari, B. B. Mishra, K. B. Mishra, N. Mishra, A. S. Singh and X. Chen, Chem. Rev., 2016, 116, 3086–3240 CrossRef CAS PubMed.
- R. U. Islam, A. Taher, M. Choudhary, M. J. Witcomb and K. Mallick, Dalton Trans., 2015, 44, 1341–1349 RSC.
- T. Kitanosono, K. Masuda, P. Xu and S. Kobayashi, Chem. Rev., 2018, 118, 679–746 CrossRef CAS PubMed.
- C. W. Tornøe, C. Christensen and M. Meldal, J. Org. Chem., 2002, 67, 3057–3064 CrossRef PubMed.
- G. Molteni, C. L. Bianchi, G. Marinoni, N. Santo and A. Ponti, New J. Chem., 2006, 30, 1137–1139 RSC.
- L. Jiang, Z. Wang, S.-Q. Bai and T. A. Hor, Dalton Trans., 2013, 42, 9437–9443 RSC.
- V. O. Rodionov, S. I. Presolski, S. Gardinier, Y.-H. Lim and M. Finn, J. Am. Chem. Soc., 2007, 129, 12696–12704 CrossRef CAS PubMed.
- J. Y. Kim, J. C. Park, H. Kang, H. Song and K. H. Park, ChemComm, 2010, 46, 439–441 RSC.
- R. ta-Ledari, M. Saeidirad, F. S. Qazi, A. Fazeli, A. Maleki and A. E. Shalan, RSC Adv., 2021, 11, 25284–25295 RSC.
- N. Kerru, S. V. Bhaskaruni, L. Gummidi, S. N. Maddila and S. B. Jonnalagadda, Synth. Commun., 2019, 49, 2437–2459 CrossRef CAS.
- A. Maleki, R. Taheri-Ledari, R. Ghalavand and R. Firouzi-Haji, J. Phys. Chem. Solids, 2020, 136, 109200 CrossRef CAS.
- A. Maleki, R. Taheri-Ledari and M. Soroushnejad, ChemistrySelect, 2018, 3, 13057–13062 CrossRef CAS.
- A. Poursattar Marjani, F. Asadzadeh and A. Danandeh Asl, Sci. Rep., 2022, 12, 22173 CrossRef CAS PubMed.
- A. Ghorbani-Choghamarani, H. Aghavandi and S.M. Talebi, Sci. Rep., 2022, 12, 20775 CrossRef PubMed.
- S. Mirani Nezhad, E. Nazarzadeh Zare, A. Davarpanah, S.A. Pourmousavi Seied Ali Pourmousavi, M. Ashrafizadeh Milad Ashrafizadeh and A.P. Kumar, Molecules, 2022, 27, 1748 CrossRef CAS PubMed.
- Z. Hajizadeh, K. Valadi, R. Taheri-Ledari and A. Maleki, ChemistrySelect, 2020, 5, 2441–2448 CrossRef CAS.
- R. Taheri-Ledari, S. M. Hashemi and A. Maleki, RSC Adv., 2019, 9, 40348–40356 RSC.
- R. Taheri-Ledari, A. Maleki, E. Zolfaghari, M. Radmanesh, H. Rabbani, A. Salimi and R. Fazel, Ultrason. Sonochem., 2020, 61, 104824 CrossRef CAS PubMed.
- R. Taheri-Ledari, K. Valadi, S. Gharibi and A. Maleki, Mater. Res. Bull., 2020, 130, 110946 CrossRef CAS.
- R. Taheri-Ledari and A. Maleki, New J. Chem., 2021, 45, 4135–4146 RSC.
- V. Adimule, B. C. Yallur, M. M. Pai, S. R. Batakurki and S. S. Nandi, Top. Catal., 2022 DOI:10.1007/s11244-022-01672-9.
- V. Soltaninejad, M. R. Ahghari, R. Taheri-Ledari and A. Maleki, Langmuir, 2021, 37, 4700–4713 CrossRef CAS PubMed.
- S. Naghash-Hamed, N. Arsalani and S. B. Mousavi, Sci. Rep., 2023, 13, 3329 CrossRef CAS PubMed.
- R. Taheri-Ledari, S. S. Mirmohammadi, K. Valadi, A. Maleki and A. E. Shalan, RSC Adv., 2020, 10, 43670–43681 RSC.
- F. FarhKhanmohammadi-Sarabi, A. Ghorbani-Choghamarani, H. Aghavandi and M. A. Zolfigol, New J. Chem., 2023, 47, 4252–4266 RSC.
- A. Bahadoran, S. Ramakrishna, B. Oryani, L. Ahmed Al-Keridis, H. Rashidi Nodeh and S. Rezania, Fuel, 2022, 319, 123858 CrossRef CAS.
-
R. Taheri-Ledari and A. Maleki, in Magnetic Nanoparticle-Based Hybrid Materials, Elsevier, 2021, pp. 619–636 Search PubMed.
- R. Taheri-Ledari, F. R. Asl, M. Saeidirad, A. Kashtiaray and A. Maleki, Sci. Rep., 2022, 12, 4719 CrossRef CAS PubMed.
- P. Guardia, A. Labarta and X. Batlle, J. Phys. Chem. C, 2011, 115, 390–396 CrossRef CAS.
- M. Zhu and G. Diao, Nanoscale, 2011, 3, 2748–2767 RSC.
- Q. Li, H. Li, V. G. Pol, I. Bruckental, Y. Koltypin, J. Calderon-Moreno and A. Gedanken, New J. Chem., 2003, 27, 1194–1199 RSC.
- X. Chen, K. M. Unruh, C. Ni, B. Ali, Z. Sun, Q. Lu and J. Q. Xiao, J. Phys. Chem. C, 2011, 115, 373–378 CrossRef CAS.
- T. Hyeon, Commun. Chem., 2003, 8, 927–934 RSC.
- M. D. Nguyen, H. V. Tran, S. Xu and T. R. Lee, Appl. Sci., 2021, 11, 11301 CrossRef CAS PubMed.
- Y. C. Li, Y. S. Lin, P. J. Tsai, C. T. Chen, W. Y. Chen and Y. C. Chen, Anal. Chem., 2007, 79, 7519–7525 CrossRef CAS PubMed.
- J. Chen, L. Xu, W. Li and X. Gou, Adv. Mater., 2005, 17, 582–586 CrossRef CAS.
- N. A. Frey, S. Peng, K. Cheng and S. Sun, Chem. Soc. Rev., 2009, 38, 2532–2542 RSC.
- S. Bikas, A. Poursattar Marjani, S. Bibak and H. Sarreshtehdar Aslaheh, Sci. Rep., 2023, 13, 2564 CrossRef CAS PubMed.
- H. Boroumand, H. Alinezhad, B. Maleki and S. Peiman, Polycyclic Aromat. Compd., 2022, 1–17 Search PubMed.
- M. Jarrahi, B. Maleki and R. Tayebee, RSC Adv., 2022, 12, 28886–28901 RSC.
- M. Tarahomi, H. Alinezhad and B. Maleki, Appl. Organomet. Chem., 2019, 33, e5203 CrossRef CAS.
- R. Taheri-Ledari, F. S. Qazi, M. Saeidirad and A. Maleki, Sci. Rep., 2022, 12, 14865 CrossRef CAS PubMed.
- N. Khaleghi, M. Forouzandeh-Malati, F. Ganjali, Z. Rashvandi, S. Zarei-Shokat, R. Taheri-Ledari and A. Maleki, Sci. Rep., 2023, 13, 5225 CrossRef CAS PubMed.
- F. Ganjali, A. Kashtiaray, S. Zarei-Shokat, R. Taheri-Ledari and A. Maleki, Functionalized hybrid magnetic catalytic systems on micro-and nanoscale utilized in organic synthesis and degradation of dyes, Nanoscale Adv., 2022, 4, 1263–1307 RSC.
- M. Ghani, S. Khodkavandi, Z. Jafari, B. Maleki and H. F. Tabari, Microchem. J., 2023, 187, 108368 CrossRef CAS.
- D. Shi, Adv. Funct. Mater., 2009, 19, 3356–3373 CrossRef CAS.
- R. Qiao, C. Yang and M. Gao, J. Mater. Chem., 2009, 19, 6274–6293 RSC.
- R. Taheri-Ledari and A. Maleki, J. Pept. Sci., 2020, 26, e3277 CrossRef CAS PubMed.
- R. Taheri-Ledari, E. Zolfaghari, S. Zarei-Shokat, A. Kashtiaray and A. Maleki, Commun. Biol., 2022, 5, 995 CrossRef CAS PubMed.
- M. Peyvandtalab, E. N. Zare, M. Jabbari and G. Heidari, Eur. Polym. J., 2023, 186, 111862 CrossRef CAS.
- W. Zhang, R. Taheri-Ledari, Z. Hajizadeh, E. Zolfaghari, M. R. Ahghari, A. Maleki and Y. Tian, Nanoscale, 2020, 12, 3855–3870 RSC.
- R. Taheri-Ledari, J. Rahimi and A. Maleki, Mater. Res. Express, 2020, 7, 015067 CrossRef CAS.
- R. Taheri-Ledari, W. Zhang, M. Radmanesh, S. S. Mirmohammadi, A. Maleki, N. Cathcart and V. Kitaev, Small, 2020, 16, 2002733 CrossRef CAS PubMed.
- M. Zhu and G. Diao, J. Phys. Chem. C, 2011, 115, 18923–18934 CrossRef CAS.
- A. H. Lu, E. E. Salabas and F. Schüth, Angew. Chem., Int. Ed., 2007, 46, 1222–1244 CrossRef CAS PubMed.
- U. Jeong, X. Teng, Y. Wang, H. Yang and Y. Xia, Adv. Mater., 2007, 19, 33–60 CrossRef CAS.
- A. S. Teja and P. Y. Koh, Prog. Cryst. Growth Charact. Mater., 2009, 55, 22–45 CrossRef CAS.
- A. Maleki, S. Gharibi, K. Valadi and R. Taheri-Ledari, J. Phys. Chem. Solids, 2020, 142, 109443 CrossRef CAS.
- S. S. Soltani, R. Taheri-Ledari, S. M. F. Farnia, A. Maleki and A. Foroumadi, RSC Adv., 2020, 10, 23359–23371 RSC.
- A. Maleki, R. Taheri-Ledari and R. Ghalavand, Comb. Chem. High Throughput Screening, 2020, 23, 119–125 CrossRef CAS PubMed.
- J. Rahimi, R. Taheri-Ledari and A. Maleki, Curr. Org. Synth., 2020, 17, 288–294 CrossRef CAS PubMed.
- V. Soltaninejad, M. R. Ahghari, R. Taheri-Ledari, A. Maleki and A. E. Shalan, J. Mol. Struct., 2022, 1256, 132456 CrossRef CAS.
- A. Islam, G. Phillips, A. Sljivo, M. Snowden and P. Williams, Food Hydrocolloids, 1997, 11, 493–505 CrossRef CAS.
- P. Supriya, B. T. V. Srinivas, K. Chowdeswari, N. V. S. Naidu and B. Sreedhar, Mater. Chem. Phys., 2018, 204, 27–36 CrossRef CAS.
- C. M. Niemeyer, Angew. Chem., Int. Ed., 2001, 40, 4128–4158 CrossRef CAS.
- E. Katz and I. Willner, Angew. Chem., Int. Ed., 2004, 43, 6042–6108 CrossRef CAS PubMed.
- R. Bandyopadhyaya, E. Nativ-Roth, O. Regev and R. Yerushalmi-Rozen, Nano Lett., 2002, 2, 25–28 CrossRef CAS.
- V. Kattumuri, K. Katti, S. Bhaskaran, E. J. Boote, S. W. Casteel, G. M. Fent, D. J. Robertson, M. Chandrasekhar, R. Kannan and K. V. Katti, Small, 2007, 3, 333–341 CrossRef CAS PubMed.
- K. P. Velikov, G. E. Zegers and A. van Blaaderen, Langmuir, 2003, 19, 1384–1389 CrossRef CAS.
- D. N. Williams, K. A. Gold, T. R. P. Holoman, S. H. Ehrman and O. C. Wilson, J. Nanopart. Res., 2006, 8, 749–753 CrossRef CAS.
- S. Amirnejat, A. Nosrati, S. Javanshir and M. R. Naimi-Jamal, Int. J. Biol. Macromol., 2020, 152, 834–845 CrossRef CAS PubMed.
- M. Anvari and D. Chung, Food Hydrocolloids, 2016, 60, 516–524 CrossRef CAS.
- I. V. Machado, J. R. Dos Santos, M. A. Januario and A. G. Corrêa, Ultrason. Sonochem., 2021, 78, 105704 CrossRef CAS PubMed.
- H. T. Nguyen, V. A. Truong and P. H. Tran, RSC Adv., 2020, 10, 25358–25363 RSC.
- A. Maleki, Z. Hajizadeh and K. Valadi, Green Chem. Lett. Rev., 2021, 14, 62–72 CrossRef CAS.
- G. Bosica and R. Abdilla, Catalysts, 2022, 12, 725 CrossRef CAS.
- S. Chaturvedi, P. N. Dave and N. K. Shah, J. Saudi Chem. Soc., 2012, 16, 307–325 CrossRef CAS.
- J. Cheng, J. Zhou, Z. Wang and M. Zhang, Catal. Sci. Technol., 2020, 10, 6387–6392 RSC.
- L. Wang, T. Chen, J. Zhang, Y. Jiao, J. Wang, Q. Zhu and X. Li, Fuel, 2020, 268, 117384 CrossRef CAS.
- M. Filella and J. Buffle, Colloids Surf., A, 1993, 73, 255–273 CrossRef CAS.
- M. Faraji, Y. Yamini, A. Saleh, M. Rezaee, M. Ghambarian and R. Hassani, Anal. Chim. Acta, 2010, 659, 172–177 CrossRef CAS PubMed.
- M.-N. Chen, L.-P. Mo, Z.-S. Cui and Z.-H. Zhang, Curr. Opin. Green Sustainable Chem., 2019, 15, 27–37 CrossRef.
- S. Berensmeier, Appl. Microbiol. Biotechnol., 2006, 73, 495–504 CrossRef CAS PubMed.
- A. R. Liandi, A. H. Cahyana, R. T. Yunarti and T. P. Wendari, Ceram. Int., 2022, 48, 20266–20274 CrossRef CAS.
- H. Veisi, T. Ozturk, B. Karmakar, T. Tamoradi and S. Hemmati, Carbohydr. Polym., 2020, 235, 115966 CrossRef CAS PubMed.
- M. Esmaeilpour, A. R. Sardarian and H. Firouzabadi, J. Organomet. Chem., 2018, 873, 22–34 CrossRef CAS.
- P. Chandane, J. Ladke, C. Jori, S. Deshmukh, S. Zinjarde, M. Chakankar and U. Jadhav, J. Environ. Chem. Eng., 2019, 7, 103083 CrossRef CAS.
- D. Hou, T. Yang, J. Tang and S. Li, Phys. Chem. Chem. Phys., 2018, 20, 8773–8789 RSC.
- M. Aamir, M. Farooq, J. Ambreen, N. Ahmad, M. Iqbal, A. Haleem and M. Siddiq, J. Environ. Chem. Eng., 2019, 7, 103280 CrossRef CAS.
- M. Ariannezhad, D. Habibi and S. Heydari, Polyhedron, 2019, 160, 170–179 CrossRef CAS.
- M. A. Ashraf, Z. Liu, W.-X. Peng and C. Gao, Catal. Lett., 2020, 150, 683–701 CrossRef CAS.
- M. Venkatesham, D. Ayodhya, A. Madhusudhan and G. Veerabhadram, Int. J. Green Nanotechnol., 2012, 4, 199–206 CrossRef CAS.
- A. Mazaheri and M. Bostanian, Res. Chem. Intermed., 2020, 46, 2327–2350 CrossRef CAS.
- K. Arora, D. Kumar, K. Burman, S. Agnihotri and B. Singh, J. Saudi Chem. Soc., 2011, 15, 161–165 CrossRef CAS.
- Y. Suneetha, B. N. Kumar, Y. Harinath, D. H. K. Reddy and K. Seshaiah, Mikrochim. Acta, 2012, 176, 169–176 CrossRef CAS.
- R. K. Sharma, R. Gaur, M. Yadav, A. Goswami, R. Zbořil and M. B. Gawande, Sci. Rep., 2018, 8, 1901 CrossRef PubMed.
- J. Kalidass, S. Anandan and T. Sivasankar, Crystals, 2023, 13, 557 CrossRef CAS.
- K.-H. Tseng, H.-C. Ke and H.-C. Ku, Nanomater. Nanotechnol., 2021, 11, 18479804211035190 CAS.
- T. Shamsi, A. Amoozadeh, S. M. Sajjadi and E. Tabrizian, Appl. Organomet. Chem., 2017, 31, e3636 CrossRef.
- C. Cozic, L. Picton, M.-R. Garda, F. Marlhoux and D. Le Cerf, Food Hydrocolloids, 2009, 23, 1930–1934 CrossRef CAS.
- A. Grein, B. C. da Silva, C. F. Wendel, C. A. Tischer, M. R. Sierakowski, A. B. D. Moura and I. C. Riegel-Vidotti, Carbohydr. Polym., 2013, 92, 312–320 CrossRef CAS PubMed.
- B. Niemczyk-Soczynska, A. Gradys and P. Sajkiewicz, Polymers, 2020, 12, 2636 CrossRef CAS PubMed.
- P. J. Dyson and P. G. Jessop, Catal. Sci. Technol., 2016, 6, 3302–3316 RSC.
- S. F. Hamzavi, S. Gerivani, S. Saeedi, K. Naghdipari and G. Shahverdizadeh, Mol. Diversity, 2020, 24, 201–209 CrossRef CAS PubMed.
- M. Madasu, C. F. Hsia and M. H. Huang, Nanoscale, 2017, 9, 6970–6974 RSC.
- X. Xiong, Z. Tang, Z. Sun, X. Meng, S. Song and Z. Quan, Appl. Organomet. Chem., 2018, 32, e3946 CrossRef.
- M. Rajabzadeh, R. Khalifeh, H. Eshghi and M. Sorouri, Catal. Lett., 2019, 149, 1125–1134 CrossRef CAS.
- F. Nemati, M. M. Heravi and A. Elhampour, RSC Adv., 2015, 5, 45775–45784 RSC.
Footnotes |
† Electronic supplementary information (ESI) available: Supplementary information such as 1HNMR and 13C-NMR spectra of the synthetic products, can be acquired in the online version of this article on the publisher's website. See DOI: https://doi.org/10.1039/d3na00326d |
‡ Co-first author. |
|
This journal is © The Royal Society of Chemistry 2023 |
Click here to see how this site uses Cookies. View our privacy policy here.