DOI:
10.1039/D3RA00256J
(Paper)
RSC Adv., 2023,
13, 7867-7876
Synthesis and performance evaluation of slow-release fertilizers produced from inverse vulcanized copolymers obtained from industrial waste†
Received
13th January 2023
, Accepted 21st February 2023
First published on 9th March 2023
Abstract
To improve crop nutrient uptake efficacy (NUE) and better manage fertilization, slow-release fertilizers (SRFs) are developed by either coating the urea granules or making a composite. Several materials have already been developed, nevertheless, scalability of those materials is still a challenge due to their inherit drawbacks (such as hydrophilicity, crystallinity, non-biodegradability, etc.). Herein, we utilized a biodegradable, green and sustainable copolymer produced from industrial waste (sulfur-petroleum industry waste and myrcene-citrus industry waste) to coat the urea using a facile coating method to develop novel SRFs and achieve better agronomic and environmental advantages. The copolymer was first synthesized using a facile, solvent-free one-pot method called inverse vulcanization followed by Fourier transform infrared spectroscopy (FTIR) analysis to confirm the successful reaction between myrcene and sulfur subsequently coating the copolymer on urea granule. The morphology and coating thickness of coated fertilizers were analysed using scanning electron microscopy (SEM), followed by a nitrogen release test in distilled water and a soil burial test to confirm the biodegradability. The nitrogen release test revealed that the SRF with the maximum coating thickness of 1733 μm releases only 16% of its total nitrogen after 4 days of incubation compared to the pristine urea which releases all its nutrient within 1 day. The soil burial test confirms the biodegradability of the copolymer, as after 50 days of incubation in soil the copolymer loses almost 18.25% of its total weight indicating that the copolymer is degrading.
1 Introduction
The rapid increase in World population accompanied by a recent hike in inflation rate, swift urbanization, and land degradation due to massive floods are major roots for food shortage and a rise in food prices. These factors demand sustainable and efficient agricultural practices. To meet the food demand, agriculture sectors are consuming a massive amount of fertilizers. Urea is a well-known nitrogen (macronutrient required by plants) enriched fertilizer commonly used to boost the crop yield. However, owing to its hygroscopic nature it releases the nutrients at a pace that is too fast for the plants to absorb, prompting the loss of nutrients (due to nitrification–denitrification, volatilization, surface run-off and nitrate leaching) and pollution of the environment through leaching to underground water sources leading to low nutrient use efficiency (NUE) (30–70%).1 One remedy to control this issue and better manage fertilization, is to develop slow-release fertilizers (SRFs).2
Slow- or controlled-release fertilizers (SRFs/CRFs) are designed such that the active fertilizing agent is released in a delayed/controlled way, specifically taking into consideration plants' nutrient requirement therefore providing superior nutrient use efficiency (NUE) and halting the environmental pollution caused by leaching of surplus nutrient into soil and water.3,4 NUE refers to the capacity of crops to absorb and consume nutrients for maximum yield.5 An ideal SRF/CRF would be biodegradable, environmentally friendly, cost-effective, and would slow-down the nutrient release speed such that a single application would be enough for the entire life span of crop.
The approach used for the manufacture of SRFs is either coating the fertilizer with hydrophobic material or making composites by infusing urea in macromolecule that would slow down the nutrient release process.6 Over the years, numerous classes of coating materials, ranging from inorganic materials to synthetic and natural polymers, have been explored. The drawbacks associated with these coatings include brittleness of inorganic materials,4 hazardous and nonbiodegradable nature of synthetic polymers7,8 and hydrophilicity of natural polymers.9 Therefore, an investigation needs to be done in order to find a biodegradable, stable, and cheap alternative coating to mitigate these problems.
According to an estimate elemental sulfur is produced as a waste by-product of the crude oil and natural gas processing facilities at a rate of 70 million tons per year and this amount is expected to rise as more contaminated petroleum feedstocks are being utilized to meet global energy demand.10 Sulfur is being used as a coating material for the production of SRFs for several decades.11 It can reduce the caking tendency of several fertilizers during storage and transportation and delay the nutrient release with the additional advantage of being secondary plant nutrient required for plant growth.12 However, crystalline nature of sulfur and exposure to higher temperature in the soil results in the formation of microscopic pores which leads to brittleness and higher friability which causes abrupt release of the nutrients.13
Inverse vulcanization, a solvent-free copolymerization process, is a relatively new technique which is being explored to produce sulfur-based polymers that are resistant to depolymerization by producing sustainable polymer chains. This technique can convert sulfur-the main monomer which acts as solvent and initiator in the molten form-into stable polymeric chains by addition of organic crosslinker or co-monomer.14 The crosslinkers can be sourced from industrial feedstock (such as divinylbenzene (DVB),15 1,3-diisopropenylbenzene (DIB),16 and dicyclopentadiene (DCPD)10) or from renewable bio-based sources (such as vegetable oil,17 limonene,18 myrcene,10 and diallyl disulfide19). These copolymers have already been utilized in several application which includes Li–S batteries, water purification and CO2 capturing. Recently Ghumman et al.,13,20,21 utilized inverse vulcanized copolymer prepared from Jatropha and rubber seed oil as a coating material for urea to produce SRFs. The produced SRF demonstrated promising results in terms of biodegradability and nutrient release efficiency. However, the unreacted sulfur present in the structure of the copolymer causes the generation of pores which promotes the sharp release of nutrient compromising the nutrient release efficiency of the coated fertilizer. Therefore, it arises a need to produce a copolymer which does not possesses any unreacted sulfur particle and can be considered as a sustainable copolymer.20
The current research work aims to produce urea as slow-release fertilizer (SRF) by dip-coating of inverse vulcanized copolymer composed of petroleum industry waste sulfur as monomer and citrus industry waste myrcene as bio-based organic cross-linker. Thus prepared, inverse vulcanized copolymer was analyzed by Fourier-Transform Infrared Spectroscopy (FTIR). The morphology of urea SRF was analyzed by means of Scanning Electron Microscopy (SEM) and the nutrient-release efficiency of nitrogen was investigated in distilled water by using diacetyl monoxime (DAM) calorimetry method.
2 Methods
The overall flow of the research is illustrated in Fig. 1.
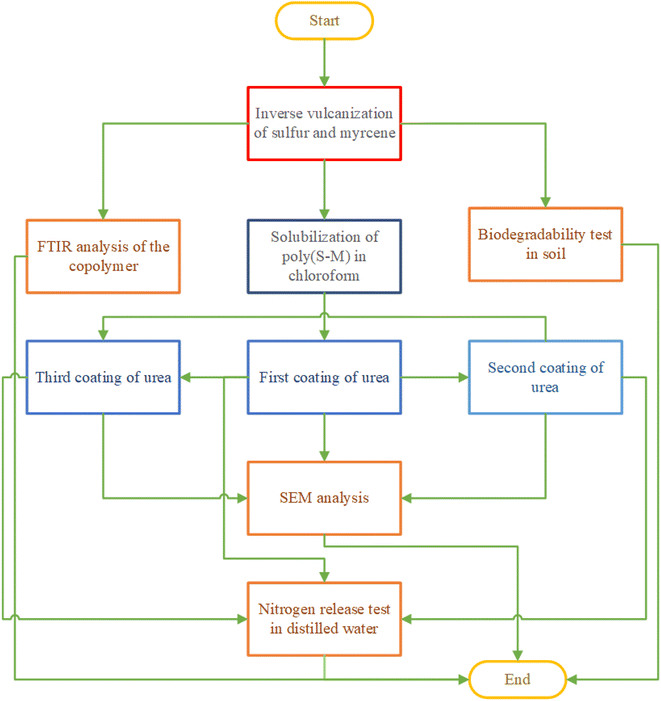 |
| Fig. 1 Overall research flowchart. | |
2.1 Materials
Chloroform, diacetyl monoxime, myrcene, elemental sulfur (reagent grade), urea (AR grade), thiosemicarbazide (TSC), phosphoric acid and sulfuric acid were procured from Merck, Malaysia. No material was further purified, they were used as received.
2.2 Methodology
2.2.1 Synthesis of the copolymer (poly(S–M)). Synthesis procedure for poly(S–M) has been adopted from previous literature on inverse vulcanized copolymers.22–24 Sulfur (S) was melted to produce the thiyl radicals in a 30 ml glass vial using a thermoset oil at a temperature of 170 °C under continuous stirring.19 The production of thiyl radical is indicated by the color change of the melted sulfur from yellow to orange. As the liquid turned to orange myrcene was added in the glass in a dropwise manner to avoid the sudden temperature drop. The plaque mixture was then allowed to react for 1 hour, after which the product was allowed to cool down to room temperature.22,23,25 Afterwards the copolymer was extracted from the glass vial. Initial sulfur ratio was varied to produced two different copolymers, one with 50 wt% S and other with 60 wt% S.
2.2.2 Characterization of copolymer. Confirmation of the successful reaction of myrcene and sulfur, and chemical composition of the produced copolymer was analysed using Fourier transform infrared spectroscopy (FTIR) employing PerkinElmer frontier spectrometer. Using attenuated total reflectance (ATR) methods total 8 scans were performed at scanning range of 4000–500 cm−1 frequency with 4 cm−1 resolution.
2.2.3 Coating of urea. Coated urea was produced using a dip-coating method, for which 4 g of produced copolymer was overnight dissolved in 4 ml of chloroform solvent to obtain homogenous coating solution.20,21,26 Afterwards, 8 g of urea granules (2–2.5 mm) was added in coating solution and carefully mixed using glass rod to ensure the uniform coating of the urea, followed by overnight drying. Same process was repeated twice or thrice to obtain different coating thickness.
2.2.4 Morphology of the coated fertilizer. Zeiss SUPRA 55VP microscope was used to estimate the coating thickness of the coated urea. The coated urea was dipped in liquid nitrogen and cut using a sharp knife to get the cross-section. Followed by the gold coating to the samples and placing in the device chamber sample holder and the gap was set to 4 mm.
2.2.5 Nitrogen release test in distilled water. To estimate the nitrogen release from the coated urea, firstly the total available nitrogen content of the coated urea was evaluated using Kjeldahl. The detail of this method can be found elsewhere.27 Diacetyl monoxime (DAM) calorimetry method was used to estimate the amount of nitrogen leached out from the coated urea. This method involves the usage of color reagent, which was prepared by mixing the 25 ml of DAM solution (prepared by dissolving 2.5 g of diacetyl monoxime in 100 ml of distilled water), 15 ml of TSC solution (prepared by dissolving 0.25 g of thiosemicarbazide in 100 ml of distilled water) and 460 ml of acid reagent (prepared by mixing 10 ml of sulfuric acid, 240 ml of distilled water and 250 ml of phosphoric acid).20,21,28 2 g of coated urea was placed in a conical flask containing 200 ml of distilled water. To estimate the amount of the nitrogen released in distilled water from coated urea, after every 24 h 2.5 ml of the aliquot was taken and mixed with 7.5 ml of the color reagent and heated to a temperature of 85 °C for 30 min in a water bath followed by cooling at room temperature. The obtained red color solutions were then analysed using Shimadzu UV-1800 UV-Vis spectrophotometer at 526 nm wavelength.13,20,21
2.2.6 Biodegradability test in soil. For biodegradability test same procedure was followed as explained in our previous reports.13,20,21
3 Results and discussion
3.1 FTIR of the copolymer
Fig. 2 depicts FTIR-ATR spectra of produced copolymers and myrcene (monomer). The spectrum of myrcene shows the band representing double bond at 3090 cm−1 (due to C–H stretching), 1646 cm−1 (due to C–H bending) and at 947 cm−1 and 885 cm−1 (due to the out of plan vibrations). Spectrum of myrcene also showed signals between 2800–3000 cm−1 representing the methyl carbon vibrations for C–H stretching and at 1399 cm−1 for C–H stretching which belongs to –CH2– group. However, the spectra of both copolymers evident the disappearance of the signals representing double bonds (as shown in figure) and no new signal appeared. Findings are similar to the previous reported literature on inverse vulcanized copolymers.19,29,30 Therefore, it can be concluded that, double bonds have been successfully utilized for C–S bond formation and the formation of copolymer is successful.
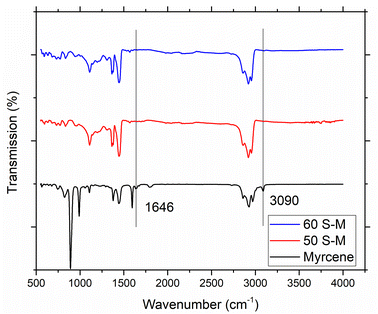 |
| Fig. 2 FTIR-ATR spectra of myrcene, copolymer with 50 wt% S (50 S–M) and 60 wt% S (60 S–M). | |
3.2 Morphology of coated fertilizers
Morphological properties and coating thickness of coated fertilizers were analyzed using scanning electron microscopy (SEM). Obtained SEM micrographs are shown in Fig. 3–6. Two copolymers with different sulfur ratio (i.e., 50 wt% S and 60 wt% S) were utilized to coat the urea. Using 50 wt% S copolymer, three different coating thicknesses were achieved by repeating the same coating process and were named as 50 S–M-I (one coat), 50 S–M-II (two coat) and 50 S–M-III (three coat). In case of 60 wt% S copolymer coating process was not repeated as the adhesion of the copolymer was less compared to 50 wt% S copolymer which did not let the second coat to adhere with the previous coating, the fertilizer coated with this copolymer was named as 60 S–M-I. Fig. 3 depicts the cross-section of the coated fertilizers, in which red circle represents the urea and copolymer coating is marked by red circle.
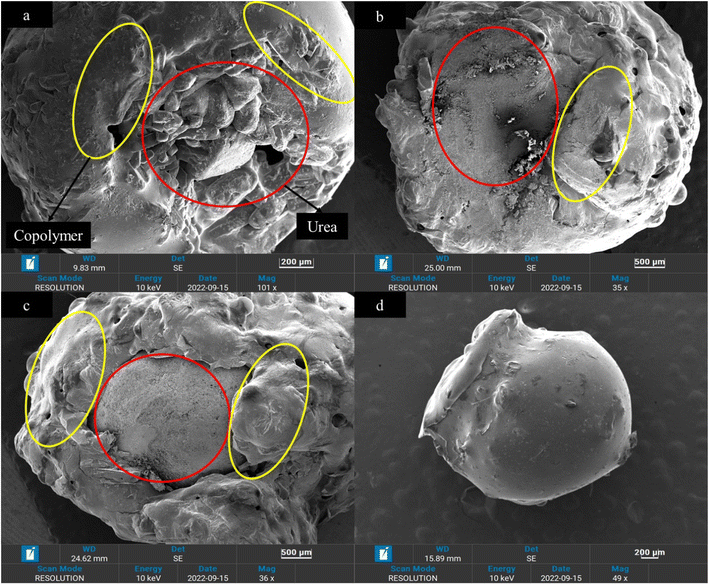 |
| Fig. 3 Cross-section of the coated fertilizers (a) 50 S–M-I, (b) 50 S–M-II, (c) 50 S–M-III and (d) 60 S–M-I. | |
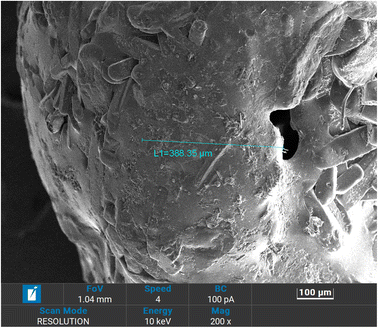 |
| Fig. 4 Thickness of coating for 50 S–M-I. | |
For the 50 S–M-I coated fertilizer thickness was estimated to be 388.35 μm and it was observed that the coating was consistent, and uniform compared to other coated fertilizers. With repeating the coating process significant increase in coating thickness can be evident from Fig. 5, which increased from 355.35 to 1593.72 μm. However, with this increase the non-uniformity of coating also increased which may lead to abrupt release of the nutrient from the thinner side. The observed non-uniformity of coating can be because of adhering of the coated urea with other. Fig. 6 presents the 50 S–M-III coated fertilizer, from which it can be seen that the coating thickness is not same from all side of the coating. The coating thickness for this sample was estimated to be 1733.5 μm from one side, the other side observed to have 1585.6 μm thick coating and the third side possesses 849.8 μm thick layer. This observed inconsistency of the coating can cause damage to the integrity of the copolymer coating leading to sudden release of the nitrogen.
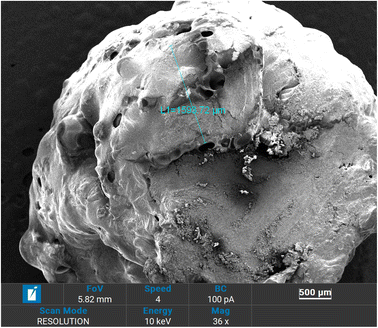 |
| Fig. 5 Thickness of coating for 50 S–M-II. | |
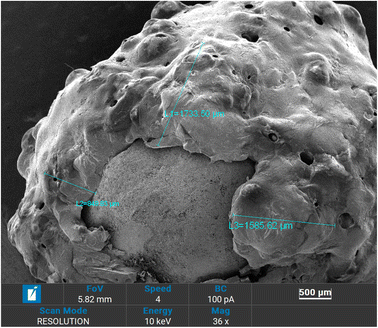 |
| Fig. 6 Thickness of coating for 50 S–M-III. | |
3.3 Nitrogen release test
Fig. 7 depicts the cumulative nitrogen release from developed coated fertilizers and pristine urea in distilled water at room temperature (The primary data for nitrogen release test is given in Table S1†). Initial nutrient release rate reflects the robustness of the coating film on urea. The consistent, thicker, and meticulous the film is, lesser will be the initial nutrient release rate. The pristine urea released almost 99.6% of its total nutrients in less than 24 h whereas coated fertilizers 50 S–M-I, 50 S–M-II, 50 S–M-III and 60 S–M-I released almost 45% of its total nitrogen in 9 days, 15 days, 17 days, and 8 days, respectively.
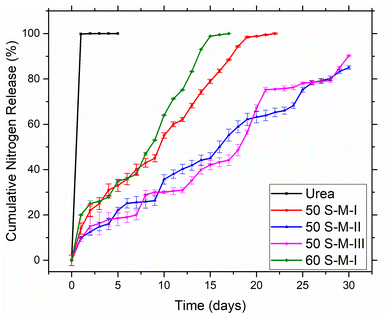 |
| Fig. 7 Cumulative nitrogen release of the developed slow-release fertilizers in distilled water. | |
As Fig. 7 illustrate that in case of coated fertilizer 50 S–M-III sharp increase in nutrient release at some points which could be because of the inconsistent coating film achieved as shown in Fig. 6, the thickness of this coated ranges from 849–1733 μm. In case of 60 S–M-I initial release rate was high compared to other coated, it may be due to the higher percentage of the sulfur in the copolymer which increases the crystallinity of copolymer resulting in pores generation of the film surface promoting the nitrogen loss. Similarly results were achieved in our previous work.13,20,21
3.4 Biodegradability test
Fig. 8 depicts the weight loss % of the 50 S–M copolymer in soil (The primary data for biodegradability test is given in Table S2†). Figure illustrates that with the increase of incubation time weight loss increases. The weight loss of the 50 S–M copolymer reaches to 18.25% on the 50th day of the incubation, which reveals that the 50 S–M copolymer is decaying steadily in soil but will take more time to get fully decomposed. This slow degradation may be happening because of the sulfur oxidation and/or because of depolymerization of the loosely bonded S–S chain as observed during experimentation. Bacteria called Aspergillus niger is present in soil which helps the sulfur to oxidize and convert into sulfate which is a secondary nutrient required by the plants. Thus, adding another benefit in using copolymer as an effective coating as it will not only reduce the nutrient loss but also will provide secondary for plant without producing any soil or water pollution. Further this test establish that this copolymer is biodegradable.
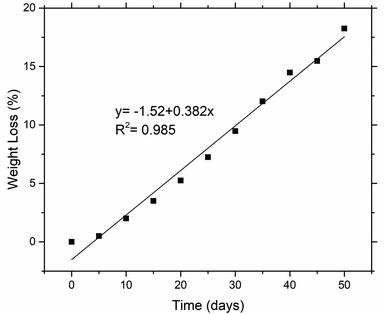 |
| Fig. 8 Weight loss of the copolymer in soil over time. | |
4 Comparison of newly developed and other coated urea
To elaborate the properties of prepared coated urea fertilizer the comparison has been made with the other coated urea reported in literature as summarized in Table 1.
Table 1 Summary of developed slow-release fertilizers
Material |
Base fertilizer |
Nitrogen release |
Biodegradability |
Coating method |
Reference |
Synthetic polymer based |
Polyester/urea inclusion complex |
Urea |
82% in 1 h |
No |
Mechanical mixing |
31 |
Polyurethane nanocomposite |
Urea |
1.9% in 24 h |
Not studied |
Rotating drum |
40 |
Epoxidized vegetable oil cured by triethylenetetramine |
Urea |
50% in 120 min |
Yes |
Fluidized bed coating |
6 |
Polyvinyl alcohol hydrogels |
Urea |
10% in 4 days |
Not studied |
In situ polymerization |
41 |
![[thin space (1/6-em)]](https://www.rsc.org/images/entities/char_2009.gif) |
Natural polymer based |
Bio polyurethane |
Urea |
8% in 24 h |
Yes |
Rotary drum |
3 |
80% in 30 days |
Lignin-clay modified bio polyurethane |
Urea |
3.6% in 24 h |
Yes |
Rotary drum |
3 |
70% in 30 days |
Borassus aethiopum starch (BAS-SRF) |
Urea |
76% in 24 h |
Yes |
Chemical gelation |
32 |
Maesopsis eminii (ME-SRF) hydrogels |
Urea |
68% in 96 h |
Yes |
Chemical gelation |
32 |
Lignin/montmorillonite |
Urea |
34.6% in 4 days |
Yes |
Dip coating |
34 |
Chitosan/alginate (Ch–Al) composites |
Urea |
10% N release in 3 h and 14% in 5 h |
Yes |
Copolymerization |
42 |
Gelatin/alginate composites |
Urea |
6% in 3 h and 8% in 5 h |
Yes |
Copolymerization |
42 |
Modified bentonite/polyurethane composite |
Urea |
3% in 24 h |
Not studied |
Rotary drum |
33 |
![[thin space (1/6-em)]](https://www.rsc.org/images/entities/char_2009.gif) |
Hybrid coatings |
Hydrogels of cassava starch-g-polyacrylic acid/natural rubber/polyvinyl alcohol |
Urea |
38.5% at 30 days |
Yes |
Rotary drum |
36 |
Starch-g-poly(styrene-co-butylacrylate) |
Urea |
45% in 60 min |
Not studied |
Rotary drum |
35 |
![[thin space (1/6-em)]](https://www.rsc.org/images/entities/char_2009.gif) |
Inorganic/S based |
Vulcanized castor oil based polyurethane |
Urea |
60% in 7 days |
Yes, sulfur oxidation not studied |
Rotary drum |
11 |
Polysulfone (SO2 and eugenol based) |
Urea |
65% in 30 days |
Yes |
Copolymerization |
38 |
Inverse vulcanized copolymer using Jatropha oil |
Urea |
13.7% in 24 h |
Yes |
Ex situ mixing |
13 |
Sulfur and rubber seed oil {poly(S-RSO)} |
Urea |
17% in 20 days |
Yes, and promotes sulfur oxidation |
Dip coating method |
21 |
65% in 43 days |
Sulfur and myrcene (S–M) |
Urea |
18% in 5 days |
Yes, promotes sulfur oxidation |
Dip coating method |
This study |
78% in 30 days |
Coating materials can be categorized into 3 types namely, (i) polymer-based (natural and synthetic), (ii) hybrid and (iii) sulfur-based coating. Synthetic polymer-based materials have been employed for control release of nutrient and only few of them showed satisfactory control release rate polyester/urea inclusion complex released 82% N in 1 hour which doesn't meet the European Standard for slow-release fertilizer (>15% in 24 h).31 In addition, the rate of release of nutrients from synthetic polymer coated urea fertilizer can be difficult to control and may not match the requirements of different crops, leading to inefficient use of fertilizer. Moreover, most reported such coating materials were not tested for their biodegradable nature which limits their practical applicability. So, synthetic coatings are expensive, non-biodegradable and toxic (due to chemicals involved in synthesis) and not effective for control/slow-release fertilizers.
Biopolymers attracted lot of attention recently because of their non-toxicity and biodegradability but they have inherent shortcoming of being hydrophilic in nature which needs further modification for slow release of nutrients. Gungula et al.32 prepared hydrogels by incorporating urea into Borassus aethiopum starch and Maesopsis eminii starch by using borax as binding material which is not ecofriendly. The nitrogen release efficiency (NSE) of prepared hydrogels was also higher than the minimum criteria in first 24 h. Although many natural polymers based slow-release fertilizers have shown excellent nutrient release behavior, the coating method (spray coating in rotary drum) requires organic solvent which not only enhances the capital and recovery cost of solvent but also poses threat to the environment.33,34 Another significant point is that there is a lack of accord regarding definition of biopolymer some researchers grafted bio-based polymers into synthetic latex and called it bio polymer which raises serious questions regarding environmental safety when it comes to the practical soil applications.35
Researchers have also focused on employing hybrid coating materials (polymer/wax composites, polymer/clay composites and polymer zeolite composites) for urea to improve release of nutrient, reduce leaching of nitrogen and extend fertilization period.36 However, complexity of production, compatibility of different materials, difficulty in controlling release rate and environment concerns related to disposal are major drawback in this field.
Sulfur was initially employed as coating material, owing to that fact that it is also essential secondary macronutrient for plant growth, for urea granules to synthesize SRF/CRF and results demonstrated slow nutrient release of only 1% in first 24 h.37 However, sulfur coating was found not to be uniform, even with sealant sub-coating, that can lead to formation of fissures which can cause early nutrient release. The vulcanized castor oil-based polyurethane prepared by one-pot method showed smooth coating surface, but nutrient release was 60% in 7 days which is faster than required. Urea coated with poly(eugenol sulfone) released only 65% N in 30 days, but sulfur oxidation was not improved.38 Sulfur and soybean oil base coating demonstrated improved sulfur oxidation and uptake as fertilizer, but soybean is an edible oil and not a cost-effective option.39 Previously, our group has prepared inverse vulcanized copolymers by using Jatropha oil and rubber seed oil (both are nonedible) by mechanical mixing and dip-coating method, respectively and demonstrated their potential as SRF.
The now prepared sulfur–myrcene copolymer exhibit excellent N release rate of only 18% in 5 days and enhanced sulfur oxidation potential. Myrcene is by-product of citrus industry, hence it's a biodegradable and sustainable option to use in inverse vulcanization process. However, morphology study shows non-uniformity which can lead to sudden release of N. So, there is a need to further investigate it. Researchers need to focus on applicability of these coated fertilizers in real soil conditions where lot of factors can affect the biodegradation and nutrient release rate such as pH, toxicity, and action of microorganisms.
5 Conclusions
Novel coated urea was developed using dip-coating method utilizing sustainable copolymer poly(S–M) as a coating material. The SEM images of the coated fertilizer revealed the non-uniform coating which could be because of the adhering coated urea with other particles. Which may pose challenge to its saleable process. The nitrogen release tests the SRF with maximum coating thickness of 1733 μm releases only 16% of its total nitrogen after 4 days of incubation compared to the pristine urea which releases all its nutrient within 1 day. Which shows that the newly developed coated fertilizer perfectly follows the European Standard (EN 1326/2001) as it releases less than 15% nutrient in first 24 h. The soil burial test confirms the biodegradability of the copolymer, as after 50 days of incubation in soil the copolymer losses almost 18.25% of its total weights indicating that the copolymer is degrading. The inconsistency of the coating thickness affects the nutrient release rate which should be addressed in future study.
Conflicts of interest
The authors declare that they have no conflict of interest.
Acknowledgements
This research was carried out under a research grant (015ME0-314) International Collaborative Research Funds UTP-Kyutech. The authors would also like to acknowledge Universiti Teknologi PETRONAS, Malaysia, for providing the research facilities.
References
- R. R. Karnakar, P. P. Shankapal, R. D. Suryawanshi and V. V. Gite, Coating of urea granules with epoxidized vegetable oil cured by triethylenetetramine for control release: A green approach, Mater. Today Proc., 2022, 60, 1165–1171, DOI:10.1016/j.matpr.2022.03.212
. - R. R. Mohamed, M. E. Fahim and S. M. A. Soliman, Development of hydrogel based on Carboxymethyl cellulose/poly(4-vinylpyridine) for controlled releasing of fertilizers, BMC Chem., 2022, 16, 1–12, DOI:10.1186/s13065-022-00846-6
. - S. Zhang, M. Yang, S. Meng, Y. Yang, Y. C. Li and Z. Tong, Biowaste-derived, nanohybrid-reinforced double-function slow-release fertilizer with metal-adsorptive function, Chem. Eng. J., 2022, 450 DOI:10.1016/j.cej.2022.138084
. - S. Fertahi, M. Ilsouk, Y. Zeroual, A. Oukarroum and A. Barakat, Recent trends in organic coating based on biopolymers and biomass for controlled and slow release fertilizers, J. Controlled Release, 2021, 330, 341–361, DOI:10.1016/j.jconrel.2020.12.026
. - G. N. Nguyen, S. Joshi and S. Kant, Nitrogen Use in Plants, Elsevier Inc., 2017 Search PubMed
. - N. Zafar, M. B. K. Niazi, F. Sher, U. Khalid, Z. Jahan, G. A. Shah and M. Zia, Starch and polyvinyl alcohol encapsulated biodegradable nanocomposites for environment friendly slow release of urea fertilizer, Chem. Eng. J. Adv., 2021, 7, 100123, DOI:10.1016/j.ceja.2021.100123
. - Y. C. Yang, M. Zhang, Y. Li, X. H. Fan and Y. Q. Geng, Improving the quality of polymer-coated urea with recycled plastic, proper additives, and large tablets, J. Agric. Food Chem., 2012, 60, 11229–11237, DOI:10.1021/jf302813g
. - Q. Li, S. Wu, T. Ru, L. Wang, G. Xing and J. Wang, Synthesis and performance of polyurethane coated urea as slow/controlled release fertilizer, J. Wuhan Univ. Technol., Mater. Sci. Ed., 2012, 27, 126–129, DOI:10.1007/s11595-012-0421-7
. - B. Azeem, K. Kushaari, Z. B. Man, A. Basit and T. H. Thanh, Review on materials and methods to produce controlled release coated urea fertilizer, J. Controlled Release, 2014, 181, 11–21, DOI:10.1016/j.jconrel.2014.02.020
. - D. J. Parker, H. A. Jones, S. Petcher, L. Cervini, J. M. Griffin, R. Akhtar and T. Hasell, Low cost and renewable sulfur-polymers by inverse vulcanisation, and their potential for mercury capture, J. Mater. Chem. A, 2017, 5, 11682–11692, 10.1039/c6ta09862b
. - X. Zhao, X. Qi, Q. Chen, X. Ao and Y. Guo, Sulfur-Modified Coated Slow-Release Fertilizer Based on Castor Oil: Synthesis and a Controlled-Release Model, ACS Sustain. Chem. Eng., 2020, 8, 18044–18053, DOI:10.1021/acssuschemeng.0c06056
. - G. M. Blouin, D. W. Rindt and O. E. Moore, Sulfur-Coated Fertilizers for Controlled Release: Pilot Plant Production, J. Agric. Food Chem., 1971, 19, 801–808, DOI:10.1021/JF60177A039/ASSET/JF60177A039.FP.PNG_V03
. - A. S. M. Ghumman, R. Shamsuddin, M. M. Nasef, C. Maucieri, O. U. Rehman, A. A. Rosman, M. I. Haziq and A. Abbasi, Degradable Slow-Release Fertilizer Composite Prepared by Ex Situ Mixing of Inverse Vulcanized Copolymer with Urea, Agronomy, 2022, 12(1), 12010065, DOI:10.3390/agronomy12010065
. - X. Wu, J. A. Smith, S. Petcher, B. Zhang, D. J. Parker, J. M. Griffin and T. Hasell, Catalytic inverse vulcanization, Nat. Commun., 2019, 10(1), 1–9, DOI:10.1038/s41467-019-08430-8
. - M. Arslan, B. Kiskan, E. Ceylan, R. Demir-cakan and Y. Yagci, Inverse vulcanization of bismaleimide and divinylbenzene by elemental sulfur for lithium sulfur batteries, Eur. Polym. J., 2016, 80, 70–77, DOI:10.1016/j.eurpolymj.2016.05.007
. - W. J. Chung, J. J. Griebel, E. T. Kim, H. Yoon, A. G. Simmonds, H. J. Ji, P. T. Dirlam, R. S. Glass, J. J. Wie, N. A. Nguyen, B. W. Guralnick, J. Park, Á. Somogyi, P. Theato, M. E. Mackay, Y. E. Sung, K. Char and J. Pyun, The use of elemental sulfur as an alternative feedstock for polymeric materials, Nat. Chem., 2013, 56(5), 518–524, DOI:10.1038/nchem.1624
. - A. Hoefling, Y. J. Lee and P. Theato, Sulfur-Based Polymer Composites from Vegetable Oils and Elemental Sulfur: A Sustainable Active Material for Li-S Batteries, Macromol. Chem. Phys., 2017, 218, 1600303, DOI:10.1002/macp.201600303
. - M. P. Crockett, A. M. Evans, M. J. H. Worthington, I. S. Albuquerque, A. D. Slattery, C. T. Gibson, J. A. Campbell, D. A. Lewis, G. J. L. Bernardes and J. M. Chalker, Sulfur-Limonene Polysulfide: A Material Synthesized Entirely from Industrial By-Products and Its Use in Removing Toxic Metals from Water and Soil, Angew. Chemie., 2016, 128, 1746–1750, DOI:10.1002/ANGE.201508708
. - I. Gomez, O. Leonet, J. A. Blazquez and D. Mecerreyes, Inverse Vulcanization of Sulfur using Natural Dienes as Sustainable Materials for Lithium–Sulfur Batteries, ChemSusChem, 2016, 9, 3419–3425, DOI:10.1002/cssc.201601474
. - A. S. M. Ghumman, R. Shamsuddin, M. M. Nasef, E. G. Krivoborodov, S. Ahmad, A. A. Zanin, Y. O. Mezhuev and A. Abbasi, A Degradable Inverse Vulcanized Copolymer as a Coating Material for Urea Produced under Optimized Conditions, Polymers, 2021, 13(22), 13224040, DOI:10.3390/polym13224040
. - A. S. M. Ghumman, R. Shamsuddin, M. M. Nasef, W. Z. N. Yahya, A. Abbasi and H. Almohamadi, Sulfur enriched slow-release coated urea produced from inverse vulcanized copolymer, Sci. Total Environ., 2022, 846, 157417, DOI:10.1016/j.scitotenv.2022.157417
. - A. S. M. Ghumman, R. Shamsuddin, M. M. Nasef, W. Z. Nisa Yahya and A. Abbasi, Optimization of synthesis of inverse vulcanized copolymers from rubber seed oil using response surface methodology, Polymer, 2021, 219, 123553, DOI:10.1016/j.polymer.2021.123553
. - A. S. M. Ghumman, M. R. Shamsuddin, M. M. Nasef, W. Z. N. Yahya, M. Ayoub, B. Cheah and A. Abbasi, Synthesis and Characterization of Sustainable Inverse Vulcanized Copolymers from Non-Edible Oil, ChemistrySelect, 2021, 6, 1180–1190, DOI:10.1002/slct.202004554
. - A. Abbasi, M. M. Nasef, W. Z. N. Yahya, M. Moniruzzaman and A. S. Ghumman, Preparation and characterization of green polymer by copolymerization of corn oil and sulphur at molten state, Polym. Polym. Compos., 2020, 959536, DOI:10.1177/0967391120959536
. - S. Petcher, D. J. Parker and T. Hasell, Macroporous sulfur polymers from a sodium chloride porogen - A low cost, versatile remediation material, Environ. Sci.: Water Res. Technol., 2019, 5, 2142–2149, 10.1039/c9ew00477g
. - J. Li, M. Wang, D. She and Y. Zhao, Structural functionalization of industrial softwood kraft lignin for simple dip-coating of urea as highly efficient nitrogen fertilizer, Ind. Crops Prod., 2017, 109, 255–265, DOI:10.1016/j.indcrop.2017.08.011
. - C. F. Uzoh, O. D. Onukwuli, I. H. Ozofor and R. S. Odera, Encapsulation of urea with alkyd resin-starch membranes for controlled N2 release: Synthesis, characterization, morphology and optimum N2 release, Process Saf. Environ. Prot., 2019, 121, 133–142, DOI:10.1016/j.psep.2018.10.015
. - B. Azeem, K. KuShaari, M. Naqvi, L. K. Keong, M. K. Almesfer, Z. Al-Qodah, S. R. Naqvi and N. Elboughdiri, Production and characterization of controlled release urea using biopolymer and geopolymer as coating materials, Polymers, 2020, 12(2), 12020400, DOI:10.3390/polym12020400
. - A. S. M. Ghumman, M. M. Nasef, M. R. Shamsuddin and A. Abbasi, Evaluation of properties of sulfur-based polymers obtained by inverse vulcanization: Techniques and challenges, Polym. Polym. Compos., 2021, 29(8), 1333–1352, DOI:10.1177/0967391120954072
. - A. Abbasi, M. M. Nasef, W. Z. N. Yahya, M. Moniruzzaman and A. S. M. Ghumman, Preparation and characterization of sulfur-vinylbenzyl chloride polymer under optimized reaction conditions using inverse vulcanization, Eur. Polym. J., 2021, 143, 110202, DOI:10.1016/j.eurpolymj.2020.110202
. - H. M. Ye, H. F. Li, C. S. Wang, J. Yang, G. Huang, X. Meng and Q. Zhou, Degradable polyester/urea inclusion complex applied as a facile and environment-friendly strategy for slow-release fertilizer: Performance and mechanism, Chem. Eng. J., 2020, 381, 122704, DOI:10.1016/j.cej.2019.122704
. - D. T. Gungula, F. P. Andrew, J. Joseph, S. A. Kareem, J. T. Barminas, E. F. Adebayo, A. M. Saddiq, V. T. Tame, I. Dere, W. J. Ahinda and R. Ator, Formulation and characterization of water retention and slow-release urea fertilizer based on Borassus aethiopum starch and Maesopsis eminii hydrogels, Results Mater., 2021, 12, 100223, DOI:10.1016/j.rinma.2021.100223
. - M. Zhao, Y. Wang, L. Liu, L. Liu, M. Chen, C. Zhang and Q. Lu, Green coatings from renewable modified bentonite and vegetable oil based polyurethane for slow release fertilizers, Polym. Compos., 2018, 39, 4355–4363, DOI:10.1002/pc.24519
. - H. Gu, Y. Zhang, X. Li, W. Li and S. Huang, Lignin improves release behavior of slow-release fertilizers with high content of urea, J. Appl. Polym. Sci., 2019, 136, 48238, DOI:10.1002/APP.48238
. - M. Salimi, E. Motamedi, M. Safari and B. Motesharezadeh, Synthesis of urea slow-release fertilizer using a novel starch-g-poly(styrene-co-butylacrylate) nanocomposite latex and its impact on a model crop production in greenhouse, J. Clean. Prod., 2021, 322, 129082, DOI:10.1016/j.jclepro.2021.129082
. - W. Tanan, J. Panichpakdee, P. Suwanakood and S. Saengsuwan, Biodegradable hydrogels of cassava starch-g-polyacrylic acid/natural rubber/polyvinyl alcohol as environmentally friendly and highly efficient coating material for slow-release urea fertilizers, J. Ind. Eng. Chem., 2021, 101, 237–252, DOI:10.1016/j.jiec.2021.06.008
. - G. M. Blouin, D. W. Florence and S. Rindt, Sulfur-coated fertilizer pellet having controlled dissolution rate and inhibited against microbial decomposition, 1966 Search PubMed
. - L. Liu, Y. Ni, Y. Zhi, W. Zhao, M. Pudukudy, Q. Jia, S. Shan, K. Zhang and X. Li, Sustainable and Biodegradable Copolymers from SO2 and Renewable Eugenol: A Novel Urea Fertilizer Coating Material with Superio Slow Release Performance, Macromolecules, 2020, 53, 936–945, DOI:10.1021/acs.macromol.9b02202
. - S. F. Valle, A. S. Giroto, R. Klaic and G. G. F. Guimar, Sulfur fertilizer based on inverse vulcanization process with soybean oil, Polym. Degrad. Stab., 2019, 162, 102–105, DOI:10.1016/j.polymdegradstab.2019.02.011
. - M. Pang, Q. Zuo, B. Cao, H. Li, L. Liang and L. Li, Understanding the role of a silane-coupling agent in bio-based polyurethane nanocomposite-coated fertilizers, ACS Omega, 2021, 6, 32663–32670, DOI:10.1021/acsomega.1c04348
. - K. Sarkar and K. Sen, Polyvinyl alcohol based hydrogels for urea release and Fe(III) uptake from soil medium, J. Environ. Chem. Eng., 2018, 6, 736–744, DOI:10.1016/j.jece.2018.01.004
. - I. Sathisaran and M. Balasubramanian, Physical characterization of chitosan/gelatin-alginate composite beads for controlled release of urea, Heliyon, 2020, 6(11), e05495, DOI:10.1016/j.heliyon.2020.e05495
.
|
This journal is © The Royal Society of Chemistry 2023 |
Click here to see how this site uses Cookies. View our privacy policy here.