DOI:
10.1039/D3RA06912E
(Paper)
RSC Adv., 2023,
13, 33107-33113
Room temperature esterification of high-free fatty acid feedstock into biodiesel†
Received
11th October 2023
, Accepted 5th November 2023
First published on 9th November 2023
Abstract
The esterification of a high-free fatty acid feedstock to biodiesel is often performed in high-temperature conditions using either homogeneous or heterogeneous acid catalysts. Thus, this study attempts to esterify oleic acid to biodiesel in room temperature conditions using sulphuric acid as a catalyst and a homogenizer device. The influences of process parameters including the molar ratio of oleic acid to methanol, catalyst concentration and rotational speed on biodiesel conversion were determined in different reaction times. The maximum conversion of 96.1 ± 0.4% was obtained in the presence of a molar ratio of 1
:
12, catalyst concentration of 0.7 mol L−1, a rotational speed of 4000 rpm and a reaction time of 30 minutes. The catalytic reusability test showed that the addition of fresh methanol is required to maintain the catalytic activity. However, the homogenizer-intensify esterification of oleic acid to biodiesel showed better performance than other methods as the reaction could conducted at room temperature and at a short reaction time. The predicted biodiesel properties meet the international standard except for oxidative stability. However, the flow properties revealed that the biodiesel can be used in winter season.
Introduction
As a renewable alternative fuel, the consumption of biodiesel as a substitute for diesel fuel remains low and limited.1 The high biodiesel production cost is suspected to limit the utilization.2 The petro-diesel fuel price is 36.6% lower than biodiesel in the United States of America in January 2023.3 Currently, the biodiesel industry is using vegetable oil as feedstock which consumes 75–88% of the total cost.4,5 An alternative solution to reduce biodiesel price is using low-cost feedstock such as waste cooking oil (WCO) and animal fat.1,6 However, limited stock limits the use of animal fat. In contrast, WCO is abundant due to the increasing demand for vegetable oil.7 The worldwide consumption of vegetable oils in 2022 is 213 million metric tons and it is predicted to rise with a compound annual growth rate of 7.68% in 2023–2027.8 However, WCO contains a high content of free fatty acids (FFA) which prevents the transesterification reaction to apply.7 Commonly esterification reaction using a homogeneous acid catalyst is performed to reduce the FFA content less than 2% prior the transesterification reaction.7,9
Despite the disadvantages of homogeneous acid-catalyzed esterification reactions such as equipment corrosion problems, non-reusability and required neutralization processes, the high biodiesel yield was achieved in short reaction time and mild reaction conditions compared to other types of catalysts such as heterogeneous substances and enzymes.10 For instance, Yin, et al. (2012) investigated ethyl oleate synthesis using aminophosphonic acid resin and obtained an optimum conversion of 92% under reaction condition of molar ratio oleic acid to alcohol of 1
:
14, catalyst weight of 10.2 wt%, reaction temperature of 115 °C and reaction time of 10 hours.11 The long reaction time could be shortest through the impregnation of the heterogeneous substance with the sulfonic group.12–14 Yu, et al. (2016) demonstrated the esterification of oleic acid using a sulfonated coal-based heterogeneous catalyst and achieved a conversion of 97.29% after 4 hours reaction time.12 In contrast, Aranda, et al. (2008) achieve biodiesel conversion of 90% after 1 hour reaction time in esterification of palm fatty acid using sulfuric acid as a catalyst.15 However, the esterification reaction using either homogeneous or heterogeneous catalyst is performed at a high reaction temperature, hence increasing the total biodiesel production cost.16
Homogenizer has proven could increase reaction rate through higher shear stress and vigorous turbulence.17–20 A biodiesel conversion of 98% was achieved in only 1 minute reaction time in homogenizer-intensified transesterification of soybean oil at room temperature using homogeneous base catalyst.18 Furthermore, our previous result in the transesterification of palm oil to biodiesel using palm bunch ash as a catalyst showed that homogenizer could save 67–87% of reaction time compared with other biodiesel production methods.21 To the best of our knowledge no work has been reported regarding the esterification of high acid value feedstocks for biodiesel production using homogenizer. Hence in this study, the significant parameters influencing the esterification process performed under homogenizer at room temperature were determined. The factorial design was established to study the interaction effect between reaction time and with molar ratio of oleic acid to methanol, catalyst concentration and rotational speed. The reusability of sulphuric acid as a catalyst was also determined.
Experimental
Materials
Oleic acid, methanol, sulphuric acid and other chemicals were purchased from Sigma-Aldrich and were used as received.
Homogenizer-intensified biodiesel production from oleic acid
The esterification reaction using a homogenizer apparatus was conducted following the previous report.21 All experiments were performed in a cavitation reactor consisting of a rotor–stator with a diameter of 25 mm and 35 mm, respectively. The molar ratio of oleic acid to methanol of 1
:
6, 1
:
9 and 1
:
12, catalyst concentration of 0.1; 0.2; 0.3; 0.5 and 0.7 M, and rotational speeds of 3000, 4000 and 5000 rpm were systematically varied at reaction time of 5, 15, 30, 45, 60, 75 and 90 minutes. Initially, 80 mL of oleic acid was mixed with the investigated volume of methanol and catalyst. The reaction was dispersed at 4000 rpm for different reaction times at room temperature. After completion, the biodiesel product was separated using a centrifuge, washed with warm water twice and dried using anhydrous sodium sulphate. The biodiesel product was collected and stored in a desiccator for conversion analysis.
Reusability test of acid catalyst
The homogeneous acid catalyst reusability was investigated at biodiesel maximum conversion reaction condition at a molar ratio of oleic acid to methanol of 1
:
12, catalyst concentration of 0.7 M, rotational speed of 4000 rpm and reaction time of 30 minutes. The reusability test was conducted in two different methods. First, after each process, the mixture of methanol–catalyst–water was collected in the bottom layer of the centrifuge tube and was used directly without any treatment for the next reaction. The second method was performed following a previous report suggested by Britton and Raston (2014) in which the leftover mixture was evaporated to dryness.22 The residue which contains the catalyst was added with 61.5 mL of methanol to ensure the molar ratio was the same and was used for the next reaction. The biodiesel product was purified for conversion analysis.
Biodiesel conversion analysis
The biodiesel content was determined based on the acid value of the initial and reacted sample following the ISO 660:2020 procedure. The acid value was subsequently calculated as follows:
where AV is the acid value (mg KOH per g sample), V is the consumed volume of KOH (mL), N is the concentration of KOH (mol L−1) and W is the mass of sample (g). The conversion (C) of oleic acid to methyl oleate was determined by:
where AVi and AVf are the initial and final acid values of the samples, respectively.
Furthermore, the maximum biodiesel conversion achieved was confirmed using gas chromatography analysis. The procedure for GC analysis following previous research published.5,20,23
Biodiesel formation analysis
The Fourier transform infrared (FT-IR) spectroscopy (PerkinElmer FT-IR 100) was used to confirm the formation of biodiesel. Further, gas chromatography (GC) analysis was used to determine the conversion of the final maximum sample. GC (Shimadzu type 2010) is equipped with a flame ionization detector (FID) and capillary column (length 15 m × 0.25 mm ID). The carrier gas helium was used with a flow rate of 1 mL min−1. The injector and detector temperature was set to 260 °C and the oven temperature was programmed initially at 90 °C for 1 min, then heated with a heating rate of 7 °C min−1.
Statistical analysis
All the experiments were conducted in three replicates and the data were analysed using Statistica v13. Differences between means were calculated using analysis of variance (ANOVA) and Tukey test post hoc at a significance level of <0.05.
Results and discussion
Effect of molar ratio
The molar ratio of oil/fatty acid to alcohol is an important parameter that could directly affect the biodiesel yield and production cost.10 Stoichiometrically, one mole of alcohol is required to react with one mole of fatty acid in an esterification reaction. However, to drive the reaction toward the product, an excess amount of alcohol is used.10,24 Hence, in this study the molar ratio of oleic acid to methanol of 1
:
6, 1
:
9 and 1
:
12 was investigated in varied reaction time from 5 to 90 minutes, catalyst concentration of 0.2 M and rotational speed of 4000 rpm. Initially, low biodiesel conversion was achieved from the entire ratio molar tested. It can be observed in Fig. 1A that the biodiesel conversion in a molar ratio of 1
:
12 was 43% higher than in 1
:
6 in a similar reaction time. This can be attributed that an excess volume of methanol could decrease the viscosity of the reactants which enhances the mass transfer rate.24 Next, the conversion was increased sharply in the increasing reaction time up to 45 minutes or all ratio molars tested and gradually rose to achieve maximum biodiesel conversion of 86.9 ± 0.4% using a ratio molar of 1
:
12 in reaction time of 75 minutes. However, due to increasing water as a by-product, the esterification reverses to the left side causing decreasing biodiesel conversion.25,26 Due to this, the molar ratio of 1
:
12 was selected to study the effect of catalyst concentration and rotational speed on biodiesel conversion. Further, the analysis of variance result showed that the molar ratio of oleic acid to methanol has a significant effect on biodiesel conversion which was driven by all the ratios tested.
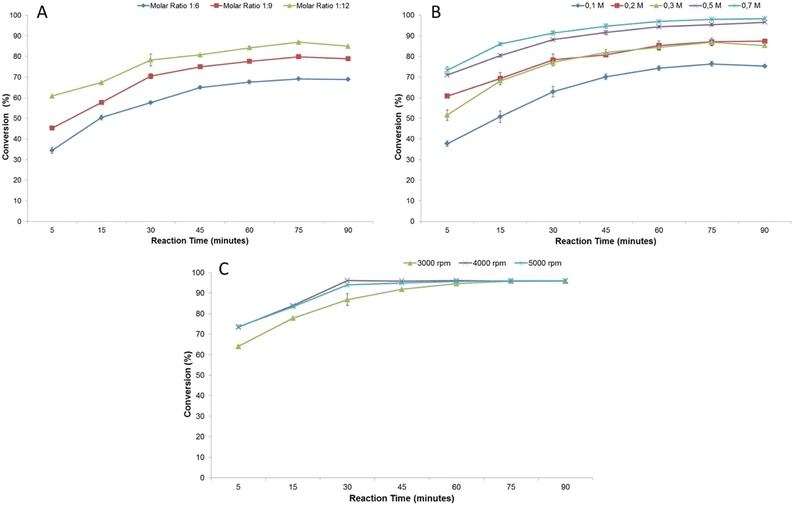 |
| Fig. 1 Effect of (A) molar ratio; (B) catalyst concentration; and (C) rotational speed on biodiesel conversion. | |
Effect of catalyst concentration
The catalyst plays a crucial role in the esterification reaction as it can accelerate the reaction rate.20 Catalyst concentration has a linear relation with the biodiesel conversion. It has been reported that increasing catalyst concentration could increase biodiesel conversion until reaches the maximum point.5,27,28 Hence, the concentration of sulphuric acid as catalyst was varied as 0.1, 0.2, 0.3, 0.5 and 0.7 mol L−1 which was studied under reaction conditions of molar ratio of 1
:
2 and rotational speed of 4000 rpm. As expected the biodiesel conversion was increased in the increasing of catalyst concentration. The conversion has increased 49% from 37.7 ± 1.4% to 73.3 ± 1.6% using catalyst concentrations of 0.1 mol L−1 and 0.7 mol L−1, respectively at a reaction time of 5 minutes (Fig. 1B). Interestingly, the biodiesel conversion for all catalyst concentrations tested was increased in the prolonged reaction time. When a catalyst concentration of 0.7 mol L−1 was used the biodiesel conversion of >90% was achieved after a reaction time of 30 minutes and the conversion slightly increased to achieve a maximum conversion of 98.3 ± 0.0% at reaction time of 90 minutes. Further, increasing catalyst concentration does not influence biodiesel conversion. This can be explained that dehydration could occur in high concentrations of acid catalysts affecting the biodiesel conversion.24 This result is in agreement with a previous study that uses trifluoroacetic acid as a catalyst in the transesterification of soybean oil to biodiesel.29 Similarly, Olkiewicz et al. (2016) obtained the same result in the esterification of sewage sludge lipids using a Brønsted acidic ionic liquid.30 The heterogeneous catalyst also showed a similar pattern in the effect of catalyst concentration. The study in homogenizer intensified biodiesel production from palm oil using calcined waste banana peels showed decreasing biodiesel conversion in increasing catalyst loading after reaching the maximum point.20 The significant effect of changing catalyst concentration and reaction time on the biodiesel conversion was identified using ANOVA. Tukey's test revealed that all the parameters tested were significantly affecting the conversion.
Effect of rotational speed
The effect of rotational speed on biodiesel conversion is one of the main objectives of this study. When the esterification or transesterification reaction was performed without agitation, no biodiesel was achieved.31,32 It is well known that mixing intensity could increase the interaction between reactants increasing the reaction rate.20 Thus, experiments were carried out with rotational speeds of 3000, 4000 and 5000 rpm at a constant catalyst concentration of 0.7 mol L−1 and ratio molar of 1
:
12. The observed changes in biodiesel conversion related to rotational speed have been depicted in Fig. 1C. The results indicate that increasing rotational speed from 3000 rpm to 4000 rpm could increase biodiesel conversion by 12.7% at a reaction time of 5 minutes. However, the effect was vanished in increasing rotational speed as the biodiesel conversion using a rotational speed of 4000 rpm relatively similar when using a rotational speed of 5000 rpm. It is worth noting that, when reaction time increased, the biodiesel conversion also increased as the reactants had more time to contact to produce biodiesel.18 However, the conversion begins to plateau after a certain period. This is presumably due to the concentration gradient of oleic acid and methanol in the reaction system was decreased slowing the reaction rate. Similar results were reported by Joshi et al. (2017) that observed the biodiesel conversion did not significantly increase in increasing rotational speed after reaching the maximum conversion.33 Interestingly a biodiesel conversion of >94% could achieve in reaction time of 30 minutes for either rotational speed of 4000 or 5000 rpm. The highest biodiesel conversion of 96.1 ± 0.4% was achieved using a rotational speed of 4000 rpm at a reaction time of 30 minutes and this condition was used to investigate the reusability study and biodiesel confirmation. Further, the factorial ANOVA revealed a significant effect of rotational speed on biodiesel conversion which was driven by all the values tested as stated by the Tukey test.
Biodiesel characterization and confirmation conversion
The biodiesel conversion of 96.1 ± 0.4% which was established using differentiation of acid value before and after esterification reaction was confirmed by gas chromatography analysis. The GC analysis was performed following the EN 14103:2011 standard.20,27 The conversion of 97.1 ± 0.7% was determined using GC analysis which was quite similar to the conversion determined based on acid value. Further, the biodiesel formation was confirmed using a spectrophotometer FT-IR. As shown in Fig. 2, the FT-IR spectra of oleic acid and biodiesel are almost identical as both exhibit absorption at a wavelength of 2800–3000 cm−1 representing the stretching vibration of CH3, CH2 and CH groups and 1750 cm−1 which is assigned to C
O stretching vibration. The establishment of biodiesel was affirmed by the appearance of new bands at 1435 and 1195 cm−1 indicating the stretching vibration of –C–O–C– ester.
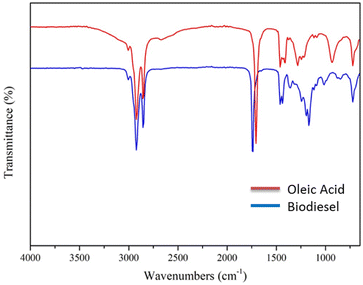 |
| Fig. 2 The FT-IR spectra of oleic acid and biodiesel. | |
Reusability test of the catalyst
One of the main disadvantages of the utilization of homogeneous acid catalysts is non-reusable.28 However, throughout the literature search no study reported on the reusability test of sulphuric acid as a catalyst in esterification or transesterification process to produce biodiesel. Hence, the reusability of the homogeneous acid catalyst was studied using two different methods under reaction conditions of molar ratio of 1
:
12, concentration catalyst of 0.7 mol L−1, rotational speed of 4000 rpm and reaction time of 30 minutes. As predicted the biodiesel conversion decrease in the following cycles (Fig. 3). The conversion dropped sharply from 96.1 ± 0.4% to 60.9 ± 0.9% after the first run. The sulphuric acid lost its catalytic activity due to being diluted by water as the esterification product. To clarify this issue, the concentration of the acid catalyst after the first cycle was determined using acid–base titration. The result showed that the concentration was decreased from 0.7 mol L−1 to 0.43 mol L−1. Another possible explanation for this result may be the lack of methanol amount in the reaction at the second cycle. The remaining methanol in the reaction at the fifth cycle was only 11.2 mL which was decreased by 82%. This is presumably due to methanol having been reacted and evaporated. To learn more about this, the second method of reusability study of the homogeneous acid catalyst was conducted. In this second method, fresh methanol was added to the leftover catalyst to ensure the molar ratio of oleic acid to methanol remained the same. As shown in Fig. 3, the catalyst showed efficient biodiesel conversion of 96.1, 93.9, and 91.9% for three cycles, respectively. However, the biodiesel conversion decreased to 86% after the fourth run. This finding is in agreement with a previously published study by Britton and Raston (2014) in biodiesel production from soybean oil using a vortex fluid device.22 Further, Tarigan et al. (2022) in the study of room-temperature biodiesel production using waste passion fruit peel as a heterogeneous catalyst suggested adding a certain amount of the catalyst to preserve the high biodiesel conversion.27
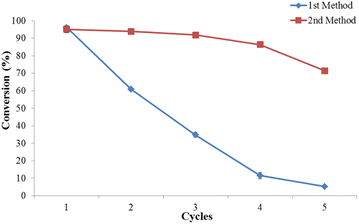 |
| Fig. 3 The reusability study of the acid catalyst. | |
Comparison of biodiesel production from high-free fatty acid feedstock
A study on biodiesel production from high-free fatty acid feedstock through esterification reaction has been conducted either in non-catalytic or catalytic processes. Table 1 summarizes the reaction conditions and biodiesel conversion of this study with other data reported. A high biodiesel conversion of >92 is achieved for all studies except for the non-catalytic electrolysis method. This is understandable considering the non-catalytic reaction was conducted at room temperature. In non-catalytic reaction particularly the supercritical solvent method, a high temperature and pressure is required to increase mass transfer between reactant.34 Recently, many researchers have focused their study on the utilization of heterogeneous substances as catalysts in esterification reactions. Some advantages provided by the heterogeneous catalyst, particularly its reusability driven the researchers to explore more. Liu et al. (2021) reported the CaO solid base catalyst could be reused 26 times without losing its catalytic activity and maintain the biodiesel conversion >90%.35 However, all the heterogeneous catalyzed esterification reactions have to be conducted at high temperatures to decrease mass transfer limitation.24 Only two studies that used the electrochemical method and homogenizer were performed at room temperature while others were conducted at temperatures varied from 40–115 °C. In terms of the molar ratio of oleic acid to methanol, the ratio varied from 1
:
4 to 1
:
24. Enzymatic esterification reactions usually use low-volume methanol to avoid enzyme inhibition.36 For reaction time, this study was performed in short reaction time compared to other studies. The homogenizer acid catalyst esterification method could save reaction time by 50–98%.
Table 1 Summary of biodiesel production from high free fatty acid feedstock studies
Catalyst |
Reaction conditions (molar ratio of oleic acid : methanol, catalyst concentration, reaction time, temperature) |
Biodiesel conversion (%) |
Ref. |
Non-catalyst |
1 : 20, 120 min, RT, electrolysis |
42 |
37 |
Sulphuric acid |
1 : 20, 13 wt%, 120 min, RT, electrolysis |
95 |
37 |
Sulphated lanthanum oxide |
1 : 5, 10 wt%, 360 min, 100 °C |
98 |
38 |
Aminophosphonic acid resin D418 |
1 : 14, 10.2 wt%, 600 min, 115 °C |
92 |
11 |
Sulfonated Oryza sativa husk |
1 : 24, 8 wt%, 60 min, 80 °C, microwave-assisted |
99.6 |
39 |
CaO solid base (NCS) |
1 : 9, 5 wt%, 60 min, 90 °C |
98 |
35 |
Enzyme lipase |
1 : 4, 0.2 wt%, 1440 min, 40 °C |
97 |
40 |
Sulphuric acid |
1 : 12, 0.7 mol L−1, 30 min, RT, 4000 rpm, homogenizer assisted |
95.2 |
This study |
Biodiesel properties
The biodiesel properties of methyl oleate could be predicted using an equation that has been published elsewhere.31,41,42 Some main physicochemical properties of biodiesel are presented in Table 2. Based on that table, the biodiesel properties of methyl oleate achieved from the esterification of oleic acid and methanol using a homogeneous acid catalyst and homogenizer met the international standard except for oxidative stability. This is understandable because of the presence of double bonds in the hydrocarbon chain. Oleic contains one double bond which is susceptible to oxidation.43 However, this double bond provides an advantage in terms of pour and cloud points. The methyl oleate has better flow properties than palm oil biodiesel which can be used in winter.44
Table 2 Biodiesel properties of methyl oleate and comparison with biodiesel from palm oil
Properties |
Units |
EN 14214 |
ASTM D6751 |
Methyl oleate |
Palm oil |
Ester content |
% |
>96.5 |
— |
96.1 |
98 |
Cetane number |
— |
>51 |
>47 |
57 |
60 |
Density |
25 °C, kg m−3 |
860–900 |
— |
822 |
858 |
Viscosity |
40 °C, mm2 s−1 |
3.5–5.0 |
1.9–6.0 |
3.7 |
3.9 |
Oxidative stability |
H |
8 |
>3 |
<1 |
19 |
Pour point |
°C |
Report |
Report |
−9.7 |
13.1 |
Cloud point |
°C |
Report |
Report |
−2.6 |
7.4 |
References |
This study |
45 |
Conclusions
A homogenizer device has been used to intensify the esterification high free fatty acid feedstock to biodiesel using homogeneous sulphuric acid as a catalyst. The maximum biodiesel conversion of 96.1 ± 0.4% was achieved under reaction conditions of molar ratio of 1
:
12, catalyst concentration of 0.7 mol L−1, reaction time of 30 minutes and rotational speed of 4000 rpm. Analysis of variance revealed that all the parameters have a significant effect on biodiesel conversion. However, sulphuric acid as an esterification catalyst could not be reused directly as the concentration decreased sharply after the first run. Interestingly, adding fresh methanol to the catalyst could hold the conversion remains similar to the first run. A comparison study showed that homogenizer-assisted acid-catalyzed esterification of high-free fatty acid feedstocks to biodiesel could be conducted at room temperature and in a short reaction time. In addition, the physicochemical properties of the biodiesel met the international standard.
Author contributions
Minto Supeno: conceptualization, methodology, writing-original draft. John P. Sihotang: investigation, formal analysis. Yolinda V. Panjaitan: investigation, resources. Dian S. Y. Damanik: investigation, project administration. Juliati Br. Tarigan: formal analysis, validation, supervision, writing-review & editing and Eko K. Sitepu: formal analysis, writing-original draft.
Conflicts of interest
There are no conflicts to declare.
Acknowledgements
The authors would like to acknowledge Universitas Sumatera Utara for a Talenta research grant no. 50/UN5.2.3.1/PPM/KP-TALENTA/2023.
References
- Y. Zhang, L. Duan and H. Esmaeili, Biomass Bioenergy, 2022, 158, 106356 CrossRef CAS.
- E. K. Nazloo, N. R. Moheimani and H. Ennaceri, Sci. Total Environ., 2023, 859, 160000 CrossRef CAS PubMed.
- E. Bourbon, Clean Cities Alternative Fuel Price Report, January 2023, U.S. Department of Energy, Maryland, 2023 Search PubMed.
- M. J. Haas, A. J. McAloon, W. C. Yee and T. A. Foglia, Bioresour. Technol., 2006, 97, 671–678 CrossRef CAS PubMed.
- E. K. Sitepu, S. Perangin-angin, G. J. Ginting, S. Machmudah, R. N. Sari and J. B. Tarigan, Heliyon, 2023, 9, e16402 CrossRef CAS PubMed.
- A. Attari, A. Abbaszadeh-Mayvan and A. Taghizadeh-Alisaraei, Biomass Bioenergy, 2022, 158, 106357 CrossRef CAS.
- G. Manikandan, P. R. Kanna, D. Taler and T. Sobota, Energies, 2023, 16, 1739 CrossRef CAS.
- Statista, Consumption of Vegetable Oils Worldwide From 2013/14 to 2022/2023, by Oil Type (in Million Metric Tons), accessed 17th May 2023 Search PubMed.
- M. G. Weldeslase, N. E. Benti, M. A. Desta and Y. S. Mekonnen, Sci. Rep., 2023, 13, 4430 CrossRef CAS PubMed.
- R. Ahmed and K. Huddersman, J. Ind. Eng. Chem., 2022, 110, 1–14 CrossRef CAS.
- P. Yin, L. Chen, Z. Wang, R. Qu, X. Liu, Q. Xu and S. Ren, Fuel, 2012, 102, 499–505 CrossRef CAS.
- H. Yu, S. Niu, C. Lu, J. Li and Y. Yang, Energy Convers. Manage., 2016, 126, 488–496 CrossRef CAS.
- Y.-T. Wang, X.-X. Yang, J. Xu, H.-L. Wang, Z.-B. Wang, L. Zhang, S.-L. Wang and J.-L. Liang, Renewable Energy, 2019, 139, 688–695 CrossRef CAS.
- M. Hara, Top. Catal., 2010, 53, 805–810 CrossRef CAS.
- D. G. Aranda, R. P. Santos, N. O. Tapanes, A. Ramos and O. Antunes, Catal. Lett., 2008, 122, 20–25 CrossRef CAS.
- E. K. Sitepu, K. Heimann, C. L. Raston and W. Zhang, Renewable Sustainable Energy Rev., 2020, 123, 109762 CrossRef CAS.
- V. Vikash, K. D. P. Nigam and V. Kumar, Chem. Eng. Sci., 2021, 232, 116296 CrossRef CAS.
- M. Sánchez-Cantú, M. Morales Téllez, L. M. Pérez-Díaz, R. Zeferino-Díaz, J. C. Hilario-Martínez and J. Sandoval-Ramírez, Renewable Energy, 2019, 130, 174–181 CrossRef.
- M.-C. Hsiao, S.-S. Hou, J.-Y. Kuo and P.-H. Hsieh, Energies, 2018, 11, 2622 CrossRef.
- J. B. Tarigan, S. Perangin-angin, S. R. Simanungkalit, N. P. Zega and E. K. Sitepu, RSC Adv., 2023, 13, 6217–6224 RSC.
- E. K. Sitepu, Y. Sembiring, M. Supeno, K. Tarigan, J. Ginting, J. A. Karo-karo and J. B. Tarigan, S. Afr. J. Chem. Eng., 2022, 40, 240–245 Search PubMed.
- J. Britton and C. L. Raston, RSC Adv., 2014, 4(91), 49850–49854 RSC.
- R. Devasan, J. V. L. Ruatpuia, S. P. Gouda, P. Kodgire, S. Basumatary, G. Halder and S. L. Rokhum, Sci. Rep., 2023, 13, 2570 CrossRef CAS PubMed.
- Z. Khan, F. Javed, Z. Shamair, A. Hafeez, T. Fazal, A. Aslam, W. B. Zimmerman and F. Rehman, J. Ind. Eng. Chem., 2021, 103, 80–101 CrossRef CAS.
- I. Tankov, Z. Mustafa, R. Nikolova, A. Veli and R. Yankova, Fuel, 2022, 307, 121876 CrossRef CAS.
- H. Im, B. Kim and J. W. Lee, Bioresour. Technol., 2015, 193, 386–392 CrossRef CAS PubMed.
- J. B. Tarigan, K. Singh, J. S. Sinuraya, M. Supeno, H. Sembiring, K. Tarigan, S. M. Rambe, J. A. Karo-karo and E. K. Sitepu, ACS Omega, 2022, 7, 7885–7892 CrossRef CAS PubMed.
- V. Mandari and S. K. Devarai, BioEnergy Res., 2021, 15, 935–961 CrossRef PubMed.
- X. Miao, R. Li and H. Yao, Energy Convers. Manage., 2009, 50, 2680–2684 CrossRef CAS.
- M. Olkiewicz, N. V. Plechkova, M. J. Earle, A. Fabregat, F. Stüber, A. Fortuny, J. Font and C. Bengoa, Appl. Catal., B, 2016, 181, 738–746 CrossRef CAS.
- J. B. Tarigan, R. Anggraini, R. P. Sembiring, M. Supeno, K. Tarigan, J. Ginting, J. A. Karo-karo and E. K. Sitepu, RSC Adv., 2022, 12, 2094–2101 RSC.
- H. I. El-Shimi, N. K. Attia, S. T. El-Sheltawy and G. I. El-Diwani, J. Sustainable Bioenergy Syst., 2013, 3, 224–233 CrossRef CAS.
- S. Joshi, P. R. Gogate, P. F. Moreira and R. Giudici, Ultrason. Sonochem., 2017, 39, 645–653 CrossRef CAS PubMed.
- P. Andreo-Martínez, V. M. Ortiz-Martínez, N. García-Martínez, A. P. de los Ríos, F. J. Hernández-Fernández and J. Quesada-Medina, Appl. Energy, 2020, 264, 114753 CrossRef.
- X. Liu, S. Xing, L. Yang, J. Fu, P. Lv, X. Zhang, M. Li and Z. Wang, Fuel, 2021, 302, 121094 CrossRef CAS.
- M. F. Kamel Ariffin and A. Idris, Renewable Energy, 2022, 185, 1362–1375 CrossRef CAS.
- P. Moradi, M. Saidi and A. T. Najafabadi, Process Saf. Environ. Prot., 2021, 147, 684–692 CrossRef CAS.
- S. S. Vieira, Z. M. Magriotis, N. A. V. Santos, A. A. Saczk, C. E. Hori and P. A. Arroyo, Bioresour. Technol., 2013, 133, 248–255 CrossRef CAS PubMed.
- G. Yadav, N. Yadav and M. Ahmaruzzaman, Chem. Eng. Process., 2023, 187, 109327 CrossRef CAS.
- M. Y. Chang, E.-S. Chan and C. P. Song, Fuel, 2021, 283, 119266 CrossRef CAS.
- K. Krisnangkura, J. Am. Oil Chem. Soc., 1986, 63, 552–553 CrossRef CAS.
- L. F. Ramírez-Verduzco, J. E. Rodríguez-Rodríguez and A. d. R. Jaramillo-Jacob, Fuel, 2012, 91, 102–111 CrossRef.
- W. Wang, F. Li and Y. Li, J. Mater. Res. Technol., 2020, 9, 2727–2736 CrossRef CAS.
- C. Caldeira, F. Freire, E. A. Olivetti and R. Kirchain, Fuel, 2017, 196, 13–20 CrossRef CAS.
- M. C. Nongbe, T. Ekou, L. Ekou, K. B. Yao, E. Le Grognec and F.-X. Felpin, Renewable Energy, 2017, 106, 135–141 CrossRef CAS.
|
This journal is © The Royal Society of Chemistry 2023 |
Click here to see how this site uses Cookies. View our privacy policy here.