Solvent based dissolution–precipitation of waste polyethylene terephthalate: economic and environmental performance metrics†
Received
6th July 2023
, Accepted 6th September 2023
First published on 8th September 2023
Abstract
Polyethylene terephthalate (PET) is one of the highest production volume polymer resins, with wide ranging applications in consumer packaging. Due to challenges in closed-loop recycling of PET, recycle rates in the U.S. are low (13% compared to PET resin converted), with the vast majority landfilled or leaked to the environment at the end of life. Solvent based dissolution and precipitation recycling technology has the potential to achieve closed-loop recycling of PET in food packaging and help achieve a circular economy for plastics. However, this technology is still in the early stages of development and there is an urgent need to understand the economic costs and environmental impacts to select promising process pathways. In this study, we analyze three precipitation process configurations for production of high-quality PET resin from post-consumer waste PET using gamma-valerolactone as the solvent: (i) anti-solvent using water, (ii) solvent evaporation, and (iii) cooling of the dissolved polymer solution. The process conditions and yields were obtained from literature sources, and process simulation was employed to estimate energy consumption and process economics. Using standard chemical engineering techno-economic analysis (TEA) assumptions and current market prices, the anti-solvent process was found to be the least profitable compared to evaporation or cooling precipitation methods, although all exhibited positive net present values. The environmental life cycle assessment (LCA) results revealed that the anti-solvent process produced 60% higher greenhouse gas (GHG) emissions compared to fossil virgin PET, but the evaporation and cooling processes reduced GHG emissions by about 50%. The sensitivity of the results to process and recycling system parameters were thoroughly investigated.
Sustainability spotlight
In the U.S., 9% of total plastic waste generated is collected for sorting and recycling, 76% is being landfilled, and remaining 19% is incinerated for energy recovery. Such low recycling rates of plastics demands more fossil-derived plastics, which further elevates the impacts of climate change. More than 1000 organizations and 175 plus nations have realized the need to end plastic waste crisis and transition from a fossil-dependent economy towards a more sustainable circular economy. Solvent-based dissolution recycling technology is one of the recycling technologies for plastics that is proposed to help advance the circular economy by creating high-quality recycled plastics, thereby reducing the need for fossil-derived plastics. Our work evaluated six economic and two environmental performance metrics of the mentioned recycling technology with different process configurations. The presented work aligns with the following United Nations (UN) Sustainable Development Goals (SDGs): SDG 9 (industry, innovation and infrastructure), 12 (responsible consumption and production), and 13 (climate action).
|
1. Introduction
Plastics have become an integral part of our day-to-day life and are often preferred to other materials due to their low price, lightweight, chemical resistance, and durability. Polyethylene terephthalate (PET, resin code #1) is one such plastic resin that is frequently used in various product manufacturing sectors. In the United States (U.S.), PET is mainly used for packaging applications (bottles, sheets, thermoforms), films, clothing, carpets, insulation for wires etc. Unfortunately, the high consumption and production in tandem with mismanagement of plastic products pose a significant challenge to the global plastic waste crisis.1,2 In the U.S., PET waste accounts for 14.8% (4.8 million metric tons (MMT)) of the total plastic waste generation and a majority (66%) of this is landfilled, 15% is incinerated with energy recovery, and 19% is collected for sorting and recycling.3 The existing PET mechanical reclamation capacity in the U.S., as of 2020, was 1.14 MMT,4 which is approx. three times lower than the total PET packaging waste that is available today. Even though mechanical recycling of plastics is associated with lower environmental impacts than fossil derived plastics, it results in degradation of inherent material properties of plastics, thus limiting its use. Most of the existing mechanical reclamation capacity is for converting high quality PET resin into low quality plastic products (“downcycling to fibers mostly”), which ultimately end up being landfilled or incinerated.1 With downcycling and high discard rates, supply chains rely more on fossil resources,5 which further elevates the impacts of climate change.6 The production of PET resin using fossil resources contributed over 53% to the total energy consumed by the U.S. PET supply chains and 44% to the total GHG emissions released by the U.S. PET supply chains in 2019.1
Emerging chemical recycling technologies, also called advanced or molecular recycling technologies, have been proposed to shift from this fossil-dependent linear economy to a sustainable circular economy by creating high-quality “virgin-grade” plastic resins. However, a systems approach is required to evaluate the optimum combination of recycling technologies and understand the sustainability of this transition. Various frameworks integrating different tools have been developed to evaluate the sustainability of emerging technologies.7–9 Our previously published framework,5,10 stated that systems analysis integrates various tools such as material flow analysis (MFA), process simulation, technoeconomic analysis (TEA), life cycle assessment (LCA), supply chain logistics and geographic information system (GIS), and optimization.1 This framework enables multiple stakeholders of plastics supply chains to gain a high-level understanding of the system by studying the effect of process level changes on the entire system. The chemical recycling technologies for which TEA and LCA data are lacking from the industry could be modeled using process simulation tools to understand the process level data, including energy requirements. Furthermore, simulations could be integrated with TEA and LCA to understand the economics and environmental impacts of the chemical recycling processes themselves. Section 1 of the ESI† provides a brief summary of these identified data gaps and provides a compiled list of the reviewed literature in Table S1.†
Solvent-based dissolution–precipitation is a promising “plastic-to-plastic” recycling technology that enables a circular economy in one single step. Other process technologies, such as depolymerization, pyrolysis, or gasification require additional processing steps to produce plastics again.11 In the dissolution–precipitation process, post-consumer or post-industrial waste plastics are dissolved into a solvent followed by a filtration step to remove any undissolved contaminants such as dirt, fillers, other polymers, etc.11–18 The dissolved polymer can be recovered as a pure resin via three methods: (1) addition of an anti-solvent; (2) evaporating the solvent from the polymer solution; (3) reducing the temperature of polymer solution to recover the polymer as a precipitate.13,19,20 One of the advantages of this recycling technology is higher product yields compared to conventional mechanical recycling.21 Another advantage is that it can deal with multi-layered plastics, as discussed in the next paragraph, which are difficult to process via mechanical recycling.
Prior studies have reported the TEA and LCA of dissolution with precipitation via anti-solvent and cooling approaches only. For example, Walker et al.20 provided a snapshot of the TEA of the Solvent Targeted Recovery and Precipitation (STRAP) process for post-industrial multi-layer PET based film with recovery via the anti-solvent approach. Sánchez-Rivera et al.19 compared the TEA of the same process but with polymer recovery via anti-solvent and cooling approaches. Both of these studies reported the minimum selling price (MSP) and effect of economy of scale on capital costs and MSP. It was concluded that the MSP of recycled polymers was comparable against the market price of virgin polymers at a processing capacity higher than 15
000 MT per year.19 Also, the MSP of STRAP process with polymer recovery via cooling approach had lower MSP than that of the anti-solvent approach.19 del Carmen Munguía-López et al.22 conducted LCA of STRAP process, reporting greenhouse gas (GHG) emissions and energy demand along with other LCA indicators. Sánchez-Rivera et al.23 studied TEA and LCA of STRAP process for post-industrial multi-layer colored film with polymers recovery via cooling approach. Their study23 used gamma-valerolactone (GVL) solvent for selectively removing polyurethane (PU)-based ink, but without dissolving PET. It was concluded that the STRAP process had lower environmental impacts than virgin polymer films22,23 and could be economically feasible at a processing capacity higher than 6000 MT per year.23 Yu et al.24 conducted TEA and LCA of the STRAP process for polypropylene based (PP) disposable face masks with polymer recovery via a cooling approach. The majority of the above-mentioned studies on STRAP processes looked at multi-layer films containing PET along with other resins such as polyethylene (PE), ethylene vinyl alcohol (EVOH), and ethylene vinyl acetate (EVA). However, it is important to note that PET was not dissolved in the STRAP process, instead it was recovered at the last after removing all other components of the multi-layer film. On the other hand, Uekert et al.21 reported TEA and LCA of chemically recycled PET (CR-PET) via solvent based dissolution–precipitation with anti-solvent approach reporting MSP and various LCA indicators. Their study21 used benzyl alcohol as a solvent and methanol as an anti-solvent. Their study showed higher GHG emissions but lower total energy demand than fossil PET resin. For a capacity of 150 metric tons per day facility, the MSP of recycled PET was found to be $0.87 per kg, which was lower than that of fossil PET resin ($1.19 per kg).21 No TEA and LCA studies were found that looked at dissolution with polymer recovery via evaporation approach.
The above-mentioned studies also lacked information on the effects of process improvements, like heat integration. Additionally, the studies that looked at economy of scale analysis, ignored the effects of increasing transportation distances and costs with increasing capacity. Finally, these studies also lacked multivariate analysis i.e., effect of varying more than one parameter on the economic performance metrics. Based on our literature review, we determine that there is a need for a more comprehensive evaluation of solvent based dissolution and precipitation of waste PET using a green solvent, compare all three different resin recovery options, and conduct a thorough interrogation of process and system parameters.
Therefore, the purpose of this study is to simulate the three dissolution–precipitation recycling processes and compare their economic and environmental performance using TEA and LCA. This study will expand on our previous work25 to explore the parameter space for these processes to uncover the key economic and environmental impact drivers. The presented study here looks at the effects of heat integration as one strategy to potentially improve the processes. We also developed a simple yet useful transportation model to account for the effects of hauling feedstock over longer distances as a function of increasing processing capacity, which has been lacking in prior TEA and LCA studies for chemical recycling technologies.
2. Methods
2.1 Process simulation
The basic process flow diagram shown in Fig. 1 describes the solvent-based recycling of waste PET with three polymer recovery techniques: addition of anti-solvent (water) (referred as ‘anti-solvent approach’), evaporation of solvent (referred as ‘evaporation approach’) and cooling of the dissolved polymer solution to room temperature (referred as ‘cooling approach’). Based on the experimental conditions in the literature,26 the swelling and dissolution of PET in gamma-valerolactone (GVL) solvent occurred at 120 °C and 170 °C, respectively, at atmospheric pressure with a PET to GVL ratio of 1 to 4 (w/w). For the anti-solvent process, GVL to water ratio of 1
:
1 (w/w) was employed. For the evaporation process, the polymer solution was heated to 207 °C to evaporate GVL solvent. GVL solvent is considered to be a green solvent, which is obtained from renewable biomass.26–28 These processes were simulated in the CHEMCAD software29 without and with heat integration to produce 1 metric ton (MT) per hour of chemically recycled PET (CR-PET). This represents a yearly production capacity of 8400 MT per year. Based on the PET packaging waste that is disposed in the U.S. per capita,3 the feedstock demand for a plant of this size could be satisfied by a population of about 1.2 million people. Based on the guidelines for using thermodynamic packages,30,31 the UNIFAC thermodynamic package was selected for the range of process temperatures and pressures, and the nature of the components (polarity, non-electrolyte) used in the process. A contamination level of 10% was assumed in the baled feedstock,32,33 and removed in the pretreatment stage. This contamination could be plastics (#2, #4, #5) rigid packaging materials, aluminum cans, loose paper or cardboard, liquid residues etc.32,33 Also, within the process a loss of polymer and solvent was assumed to be 1% and 1.5%, respectively, based on prior studies.21,34,35 The process waste generated during the pretreatment and dissolution process was assumed to be 80% landfilled and 20% incinerated with energy recovery, based on the typical U.S. waste management system.3
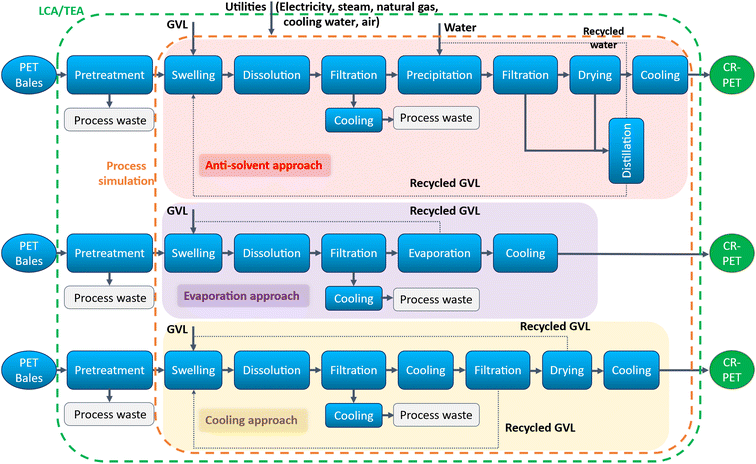 |
| Fig. 1 Solvent based dissolution–precipitation processes for waste PET with different polymer recovery approaches. Notes: LCA/TEA system boundary is shown with green dashed line. Orange dashed line represents the system boundary for process simulation. GVL: gamma-valerolactone; CR-PET: chemically recycled PET. Adapted from Chaudhari et al.25 | |
2.2 Technoeconomic analysis (TEA)
The TEA was conducted to evaluate and compare the economic performance metrics without and with process heat integration. These metrics included net present value (NPV), minimum selling price (MSP) of product, fixed capital investment (FCI), discounted internal rate of return (IRR), return on investment (ROI), and payback period. The discounted cash flow analysis over a period of 30 years was conducted with an internal rate of return of 20% using commonly found technoeconomic assumptions and parameters in the literature, including chemical engineering books36,37 and national laboratory reports.38 These assumptions and parameters along with pricing data for raw materials, products, and utilities are summarized in Table S2 in Section 2 of the ESI.† An additional description of the above-mentioned economic performance metrics is given in Section 2 of the ESI.† The cost of bale pretreatment (bale breakage, size reduction, separation) was assumed to be $100 per MT, which has been previously assumed to range from $100 to $419 per MT.21,39,40 The cost of baled PET feedstock represents a 10-year average price of $377 per MT, which ranged from $237 to $566 per MT.41
The effect of scaling up process capacity was also explored in our TEA using the formula below:
where, FCI is the fixed capital investment. The value of scaling factor (‘
n’) was 0.6 for capital investments based on the literature.
37 For the operating labor costs, 4.8 operators were assumed to be needed per shift for three shifts with an average annual salary of $58
![[thin space (1/6-em)]](https://www.rsc.org/images/entities/char_2009.gif)
000 per year per operator.
42 As the relationship between labor requirements and capacity is not always linear,
43 we also adjusted and accounted for the labor costs with varying capacity. In our economies of scale analysis, we utilized the labor cost scaling factor of 0.23,
43 which typically ranges between 0.2 and 0.25.
44 Similarly, increasing capacity demands more feedstock for the process, which would need to be sourced and transported over longer distances. We adopted a simple transportation model, based on the literature,
45,46 to account for the costs and environmental burdens of supplying and transporting the feedstock over longer distances. Please refer to Section 3 of the ESI
† for more information on this transportation model.
A sensitivity analysis of various input parameters and assumptions was also conducted on the NPV and MSP of products. These parameters included raw material costs, feedstock costs, product prices, bale contamination level, pretreatment cost, solvent loss, polymer loss, waste treatment cost, transportation costs, ISBL costs, IRR, and federal corporate tax rate. These parameters were varied independently one at a time by +20% (high scenario) and −20% (low scenario) to see the corresponding change in the NPV and MSP of products. We also conducted a multivariate analysis on the NPV by varying two parameters at a time. This multivariate analysis specifically explored the NPV as a function of capacity and feedstock costs, capacity and pretreatment costs, and feedstock and pretreatment costs.
2.3 Life cycle assessment (LCA)
Consistent with the TEA system boundary, the goal and scope of this LCA is to compare the “cradle-to-gate” environmental and energy impacts of CR-PET via the three dissolution processes compared to fossil-derived PET. The system boundary for the LCA is shown Fig. 1 and the functional unit was defined on the output (product) basis of 1 kg of CR-PET produced. The waste PET material is assumed to have no fossil or upstream burdens (“cut-off” approach), however, the environmental burdens of collection, sorting and/or baling associated with the feedstock were included.47 The LCA impacts associated with the pretreatment step were sourced from the literature.47 The LCA input data were sourced from the Ecoinvent database48 wherever possible and inventory tables for all the processes are shown in Table S3 in Section 4 of the ESI.† The electricity used in the processes were based on 2020 U.S. average electricity grid mix.1 The life cycle impact assessment (LCIA) methods of Intergovernmental Panel on Climate Change (IPCC) 2021 Global Warming Potential (GWP) over 100-year time frame and Cumulative Energy Demand (CED) were used to evaluate GHG emissions and total energy demand, respectively. The LCA was conducted using the SimaPro® software version 9.4.0.2.49 The waste from all the modeled processes was assumed to be 80% landfilled and 20% incinerated with energy recovery, based on the typical U.S. waste disposal system.3
3. Results and discussions
3.1 Process simulation
The input and output mass and energy balances for all the processes closed within 1%. The mass balance for each of the processes is shown in the ESI (Fig. S1 and Tables S4–S6†) along with the process flow diagrams (Fig. S2–S4†). For the heat integration scenario in anti-solvent and evaporation processes, the hot recycled GVL stream was used to pre-heat the stream going to the dissolution tank (see Fig. S2 and S3†). For production of 1 MT CR-PET per hour, the base case total heating utilities for the anti-solvent process were the highest (26 GJ per hour), followed by the evaporation (2.7 GJ per hour), and then the cooling process (1.6 GJ per hour) (see Table S7†). After heat integration, the heating utilities were reduced by 2% (to 25.5 GJ per hour), and 22% (to 2.2 GJ per hour) for the anti-solvent and evaporation processes, respectively. There were no heat integration opportunities for the cooling process that would benefit from the hot or cold process streams. The base cooling utilities for anti-solvent, evaporation and cooling processes were 25.6 GJ per hour, 2.3 GJ per hour, and 1.3 GJ per hour, respectively. These cooling utilities reduced by 2% (25.1 GJ per hour) and 22% (1.8 GJ per hour) for the anti-solvent and evaporation process, respectively, after heat integration. Heat integration resulted in higher savings of cooling utilities than the heating utilities. For the anti-solvent process, most of these utilities (greater than 94%) were associated with the distillation column for the separation and recovery of solvent and anti-solvent.
3.2 TEA results
The TEA metrics such as NPV, MSP, ROI, payback period, discounted IRR, and FCI, for solvent based dissolution–precipitation process for waste PET are summarized in Fig. 2. These economic indicators reveal positive results for all of the processes at the capacity of 8400 MT of CR-PET per year. The polymer recovery by evaporation and cooling processes were found to be more profitable than the anti-solvent process.
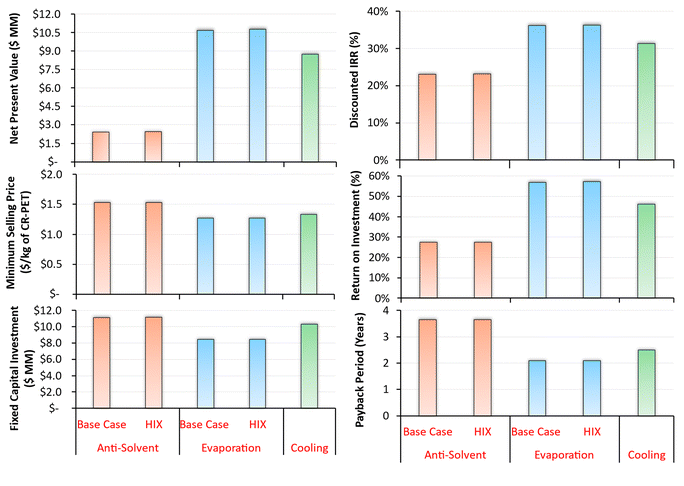 |
| Fig. 2 Summary of TEA metrics for the base case and heat integrated solvent based dissolution–precipitation processes for PET. Note: the term ‘HIX’ refers to heat integration case. Base case is without any heat integration. $ MM is millions of US dollars. ‘CR-PET’ refers to chemically recycled PET. All of these results are based on the CR-PET production capacity of 8400 MT per year. | |
The NPV for all of these processes were positive, ranging from $2.4 MM to $10.8 MM, with the highest NPV observed for dissolution with evaporation process ($10.8 MM), followed by cooling ($8.7 MM) and then anti-solvent ($2.5 MM) process (see Tables S8–S10† for the discounted cash flow tables over the 30-year project life). After heat integration, the NPV increased slightly by 0.8–1.8% compared to the base case due to reduction in the annual utilities cost, despite higher capital costs.
The MSP of CR-PET via these technologies ranged from $1.27 to $1.53 per kg of CR-PET and was found to be lower than virgin PET resin ($1.55 per kg) at the base capacity. It was found to be the least for dissolution with evaporation process ($1.27 per kg of CR-PET), followed by cooling ($1.33 per kg of CR-PET) and then anti-solvent process ($1.53 per kg of CR-PET). The FCI costs ranged from $8.4 to $11.2 MM with the maximum for anti-solvent process ($11.2 MM) followed by cooling ($10.3 MM) and then evaporation ($8.5 MM). The anti-solvent process has higher FCI due to greater number of processing steps and equipment, as compared to cooling and evaporation processes.
The discounted IRR was found to be in the range of 23.1% to 36.3%, which is higher than the assumed value of 20%. The ROI ranged from 27.4% to 57.2% and increased by less than 1% after the heat integration. The payback period was the longest for the anti-solvent process (3.6 years) and the least for evaporation (2.1 years), which can also be seen from Fig. S5.† Total annual fixed and variable operating costs are shown in Table S11 of the ESI.†
Overall, the dissolution of PET with polymer precipitation via evaporation and cooling processes were found to be more economically favorable than the anti-solvent process. As there were only a few heat integration opportunities in these processes, heat integration increased the profitability metrics by less than 2%, indicating a small effect on the economic performance. The price of CR-PET was found to be lower than virgin PET resin at a base capacity of 8400 MT per year. Our results also align with other studies, which concluded that the economics of anti-solvent process is less favorable than a cooling process,19 however ours is the first to compare evaporation in the same study. Other studies have also concluded that the solvent based dissolution–precipitation process can be economically feasible at a capacity higher than 5000–6000 MT per year.23,24
3.2.1 Minimum selling price.
Fig. 3 shows the contribution of different cost factors to the MSP. For all processes, feedstock cost, fixed operating costs, and fixed capital investment costs contributed the most to the MSP of CR-PET. The utility costs for the anti-solvent process contributed about 12% to the MSP, whereas that for evaporation and cooling processes contributed less than 2%. For the evaporation and cooling processes, bale pretreatment, raw material costs, and taxes contributed more to the MSP than utilities costs. The cost of waste treatment and transporting PET bales contributed the least to MSP at less than 1% each.
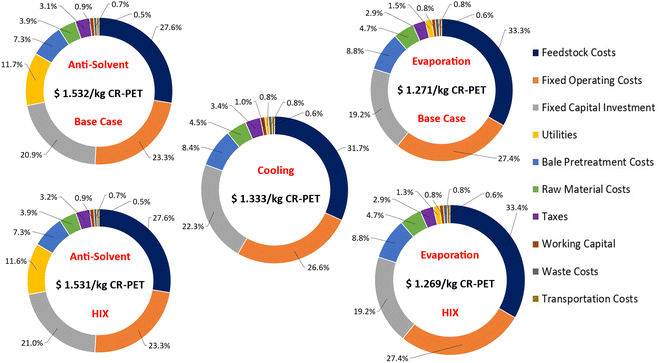 |
| Fig. 3 Cost components of MSP of CR-PET for the base case and heat integrated (HIX) processes. | |
3.2.2 Economies of scale.
Fig. 4 shows the effect of increasing production capacity on the total capital costs (Fig. 4A), MSP of CR-PET (Fig. 4A), transportation costs ($MM per year) (Fig. 4B), and average roundtrip distance travelled for the transportation of feedstock (Fig. 4B). Fig. 4A shows that increasing the capacity increases the total capital costs and reduces the MSP of CR-PET due to smaller capital and labor costs per unit of CR-PET produced. For the capacity of 8400 MT per year, the annual capital costs per metric ton of CR-PET produced were found to be $1326, $1227, and $1005 per MT per year for anti-solvent, cooling, and evaporation processes, respectively. These costs for the anti-solvent process at the same capacity are lower than Walker et al.20 by a factor of two mainly due to the differences in their feedstock and number of process equipment. Over the studied range of capacities, the MSP of CR-PET was found to range from $2.95 per kg to $0.90 per kg and was found to be lower than the 10-year average price of virgin PET resin ($1.55 per kg) at the base capacity (8400 MT CR-PET per year).
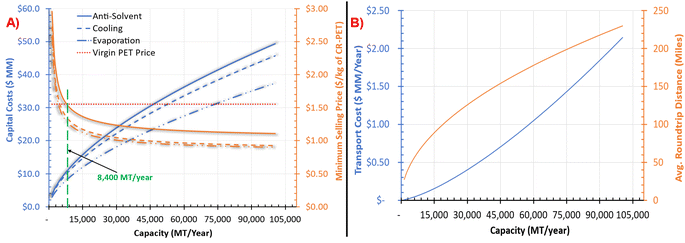 |
| Fig. 4 Economies of scale analysis for heat integrated PET dissolution processes: (A) total capital costs and MSP as a function of capacity; (B) feedstock transportation cost ($MM per year) and average roundtrip distance travelled as a function of capacity. Note: The green dashed line shows the base case production capacity of 8400 MT per year. | |
Increasing capacity would mean collecting feedstock over longer distances, which would further increase the cost of transportation and associated GHG emissions and total energy consumption. Fig. 4B shows the transportation costs of PET feedstock ($MM per year) and average roundtrip distance travelled in miles as a function of capacity. The average roundtrip distance travelled ranged from 27 to 230 miles, whereas the maximum roundtrip distance ranged from 34 to 287 miles over the studied range of capacities. For the base capacity, the average and maximum roundtrip distance of 67 and 83 miles, respectively, would be needed to travel for the collection of the feedstock, including a contamination of 10% and a polymer loss of 1% (as mentioned in the Methods section). The annual average transportation costs for the base capacity were found to be $67
800 per year. In a hypothetical situation where there is zero contamination, the average roundtrip distance would be 63 miles and the transportation costs would be reduced by 14%. Please refer to Fig. S6 in Section 5 of the ESI† for transportation costs in $ per MT of PET bale and unit delivery cost as a function of capacity. The average transportation costs ranged from $3.56 per MT to $19.03 per MT of PET bale over the studied range of capacities (see Fig. S6†). Our analysis found that the transportation costs ($ MM per year) varies with the capacity raised to a power of 1.4 (see Fig. S6†), which is consistent with Nguyen et al.50
Over the studied range of capacities, Fig. 5 shows that the NPV for these technologies could range from −$9 MM at lower capacity to $305 MM at the higher capacity. The minimum required capacity for processes to breakeven (NPV equal to zero) and still achieve the initially assumed profitability targets is represented by the point at which the NPV equals zero. For example, the production capacity of the anti-solvent process would need to be at least 8400 MT per year. Similarly, the production capacity of cooling and evaporation processes would need to be at least 5400 MT per year and 4400 MT per year, respectively. The total cost of production at the base capacity was the highest for the anti-solvent process ($1396 per MT of CR-PET), followed by cooling ($1211 per MT of CR-PET) and then evaporation process ($1166 per MT of CR-PET). These costs were lower than the assumed selling price of PET ($1608 per MT), resulting in profitable economic metrics. The contribution of different cost factors to the total cost of production is shown in Fig. S7 in the ESI.†
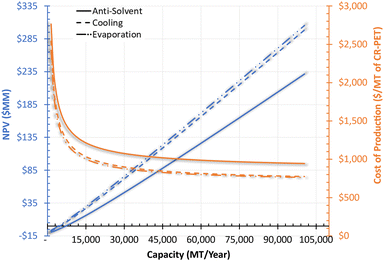 |
| Fig. 5 Effect of increasing production capacity on the NPV (blue color) and the cost of production (orange color). | |
3.2.3 Sensitivity and multivariate analysis.
The sensitivity analysis of key input parameters and assumptions (±20%) on the NPV and MSP of CR-PET for heat integrated dissolution processes is shown in Fig. 6. For the NPV, the sensitivity analysis revealed that the selling price of CR-PET, plant capacity, IRR, feedstock cost, and ISBL costs affected the NPV the most. The bale pretreatment cost and tax rate are nearly the same in importance. Increase in CR-PET selling price and capacity favors the NPV, whereas increase in all other parameters results a decrease in NPV.
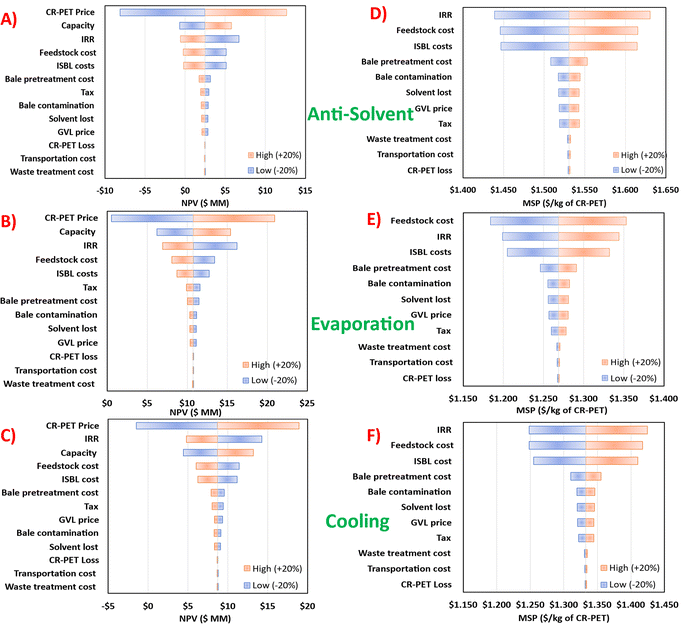 |
| Fig. 6 Sensitivity analysis of TEA assumptions and parameters on NPV (A)–(C) and MSP (D)–(F) for dissolution and precipitation of PET via three polymer recovery techniques. | |
The sensitivity analysis for the MSP revealed that the feedstock cost, IRR, and ISBL costs affect the MSP the most. Also, an increase in any of the listed parameters for the MSP would further increase the MSP. For the anti-solvent process, a 20% increase in the IRR, feedstock cost, and ISBL costs would lead to higher MSP of CR-PET than the price of virgin PET ($1.55 per kg) (see Fig. 6D). Similarly, for the anti-solvent and cooling process, a 20% decrease in the selling price of CR-PET would lead to a negative NPV at the base capacity (see Fig. 6A and C). The NPV and MSP were the least sensitive to waste treatment costs, loss of polymer, and transportation costs.
Multivariate analyses in Fig. 7A–C show the NPV as a function of production capacity and feedstock cost at a constant pretreatment cost of $100 per MT. The NPV = 0 line is at the interface between the purple and blue colors. This interface represents the minimum capacity to achieve profitability. For example, for the antisolvent case (Fig. 7A), at a PET bale feedstock cost of 700 per MT, minimum capacity would have to be about 20
000 MT per year. Similarly, at the same feedstock cost, this minimum capacity would have to be about 10
000 MT per year for evaporation and cooling processes (Fig. 7B and C). Fig. 7D–F shows the NPV as a function of feedstock cost and pretreatment costs at the base capacity of 8400 MT per year, in which the NPV = 0 line is shown in bold red color. As mentioned in the methods section, the PET feedstock cost over the period of 2012–2019 ranged from $237 to $566 per MT and the pretreatment costs ranged from $100 to $419 per MT.
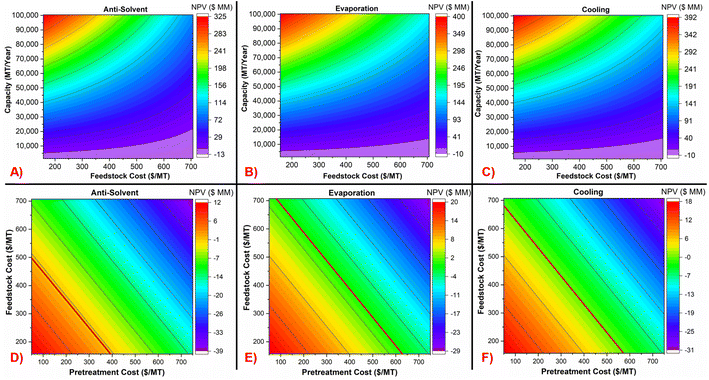 |
| Fig. 7 Multivariate analysis of capacity and feedstock cost, and pretreatment and feedstock cost on the NPV of heat integrated dissolution processes with different polymer recovery approaches. Notes: for (A)–(C): pretreatment cost is $100 per MT. The shaded/dotted violet region represents negative NPV. For 7(D)–(F): capacity is 8400 MT per year. The bold red line represents NPV equal to zero and the region above that line represents negative NPV. | |
Fig. 7A–C reveals that increase in feedstock cost decreases the NPV, but at the same time increase in capacity increases the NPV, because of economies of scale. The change in NPV with change in production capacity is strongly positive compared to the effect of feedstock cost, which is weakly negative. Fig. 7D–F shows that the NPV decreases linearly with an increase in both feedstock and pretreatment costs. Fig. S8 in Section 5 of the ESI† shows the NPV as a function of capacity and pretreatment cost, at a constant feedstock cost of $377 per MT. It shows that the anti-solvent process can be profitable for a pretreatment cost lower than $650 per MT over the studied capacity range and at the assumed feedstock cost.
3.3 Environmental performance metrics: GHG emissions and total energy demand
Our LCA results in Fig. 8 show that the PET dissolution process with polymer recovery via cooling and evaporation processes have lower GHG emissions and total energy demand than the anti-solvent process. In addition, CR-PET from evaporation and cooling processes have lower GHG emissions than fossil-based virgin PET resin. But all dissolution processes exhibited lower total energy demand than fossil virgin PET resin. Heat integration (HIX cases) shows only very minor improvement (1.4–4.4% savings) compared to the processes with no HIX. The main causes for environmental impacts are, in descending order of importance, utilities, raw materials (GVL), bale to flake pretreatment, and collection/sorting. Transport of PET bales as well as landfill and incineration operations were very minor in comparison. The only LCA input that scales with the capacity is the transport of bales, which for all capacities studied is less than 2% in terms of the total GHG emissions and energy demand. In terms of comparing to mechanically-recycled PET (MR-PET), the cradle-to-gate GHG emissions and total energy demand for all of these modeled processes were found to be higher (0.91 kg CO2-eq. per kg of MR-PET and 14.8 MJ kg−1 of MR-PET resin47).
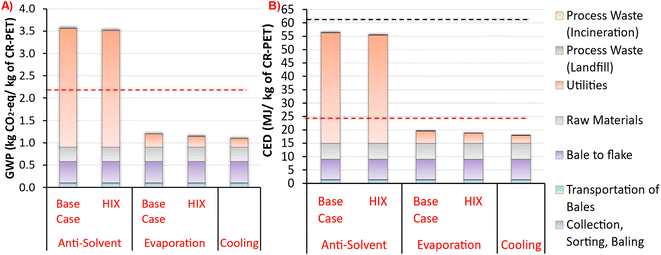 |
| Fig. 8 GHG emissions (A) and CED impacts (B) of PET dissolution processes with different polymer recovery approaches. Note: HIX refers to heat integrated process; (A): the red dashed line represents the impacts of virgin PET; for (B): the red dashed line represents only the process and fuel energy demand of virgin PET, whereas the black line represents total energy demand including material feedstock energy. | |
The cradle-to-gate GHG emissions and total energy demand for PET dissolution processes ranged from 1.08 to 3.55 kg CO2-eq. per kg of CR-PET and 17.86–56.22 MJ kg−1 of CR-PET, respectively. These impacts were the highest for polymer recovery via anti-solvent process. The environmental impacts of the three processes for PET precipitation vary due to their differences in utility consumption. The GHG emissions of CR-PET via anti-solvent process were found to be 1.6 times higher than the virgin PET impacts (2.23 kg CO2-eq. per kg of virgin PET51). Dissolution of PET with polymer recovery by cooling has the highest GHG emissions savings of 51%, when compared against virgin PET.
It is important to note from Fig. 8B that the total energy demand for virgin PET is 61.4 MJ kg−1 of virgin PET51 (dark dashed line), however, 40% of this total energy is associated with process and fuel energy (red dashed line), and the remaining 60% is associated with the material feedstock energy, which is the energy content of oil and gas that is used to produce virgin PET.51 As waste PET is assumed to have zero fossil or upstream burdens (“cut-off” approach), the total energy impacts of CR-PET could also be compared against only the process and fuel energy of virgin PET as another metric. For the anti-solvent process, the process and fuel energy of CR-PET was found to be 2.3 times higher than that of virgin PET resin (24.56 MJ kg−1 of virgin PET). The CR-PET produced via evaporation and cooling processes had lower process and fuel energy than virgin PET resin.
For the anti-solvent process, most of these impacts were due to the utilities consumed during the dissolution process, particularly the use of high-pressure steam for the solvent and anti-solvent recovery in the distillation column. The GVL solvent used for the process is considered a green and renewable solvent, but has a high boiling point of 207 °C, thereby increasing the total reboiler heat duty. Therefore, the amount and choice of solvent and anti-solvent used for the process plays an important role.19,22 The impacts related to raw materials (GVL solvent), as shown in Fig. 8, are uncertain due to lack of available LCA data for the GVL solvent (Table S3†). A surrogate compound (butyrolactone) was used for the GVL, which was selected based on their structural similarities and boiling points. This lack of LCA data for the GVL solvent has also been previously noted in a recent study by Sánchez-Rivera et al.,23 which looked at the LCA of STRAP process. To fill this data gap, their study considered average impacts of certain organic solvents, which are not clear from their study.23 However, their study found that these impacts were less than 1% of the total GHG emissions of the STRAP process.
As mentioned earlier, the environmental impacts associated with transportation would increase with increasing capacity due to transportation of feedstock over longer distances. Fig. S9 in Section 5 of the ESI† shows that both GHG emissions and total energy demand associated only with the transportation of feedstock varies with the capacity raised to the power of 0.5. For the studied range of capacities, these GHG emissions and total energy demand ranged from 0.002 to 0.02 kg CO2-eq. per kg of CR-PET and 0.03–0.27 MJ kg−1 of CR-PET, respectively. These transportation related GHG emissions could range up to 2% of the observed range for the GHG emission totals, as shown in Fig. 8. Similarly, the total energy demand could range up to 1%, over the studied range of capacities.
The LCA in this study shows that the recovery of dissolved polymer via anti-solvent approach showed higher environmental burdens than either the evaporation or cooling approaches. These conclusions are also supported by other researchers22 who conducted process simulation based LCA of the STRAP process for post-industrial multi-layered PET based film. Their study22 looked at environmental impacts of the STRAP process with 3 different polymer recovery techniques: addition of anti-solvent (STRAP-A), temperature reduction (STRAP-B; cooling) and a combination of both (STRAP-C). The functional unit for their study was production of multi-layer PET based film via STRAP process. Their study found the environmental impacts of anti-solvent (STRAP-A) process to be the highest (6.73 kg CO2-eq. per kg of film; 100.8 MJ kg−1 of film), followed by STRAP-C (2.07 kg CO2-eq. per kg of film; 32 MJ kg−1 of film) and then STRAP-B process (1.18 kg CO2-eq. per kg of film; 19 MJ kg−1 of film). Another study by Uekert et al.21 conducted process simulation based LCA of dissolving of PET in a benzyl alcohol solvent and precipitation via methanol as an anti-solvent. Their study21 found the GHG emissions and CED to be 4.5 kg CO2-eq. per kg of CR-PET and 83 MJ kg−1 of CR-PET, respectively. Their results align well with our anti-solvent results in Fig. 8, although are somewhat higher.
4. Conclusions
This study investigated the economic and environmental performance of solvent-based dissolution of waste PET using a renewable solvent, GVL, with three different polymer recovery approaches. A total of six economic and two environmental performance metrics were evaluated for the modeled processes. The assessment was improved using a simple transportation model to account for changes in feedstock transportation costs and impacts with increasing processing capacity, which has been neglected in prior TEA and LCA studies for chemical recycling technologies. Our results showed that the choice of polymer precipitation method affects the overall environmental and economic feasibility of the dissolution process. All of the modeled processes were economically feasible at the baseline capacity of 8400 MT per year, however the anti-solvent process showed much higher GHG emissions compared to fossil derived PET resin. The recovery of dissolved polymer via evaporation and cooling processes was found to be both environmentally favorable and economically profitable compared to the anti-solvent process as well as to virgin PET resin. The MSP of CR-PET, at 8400 MT per year, was found to be ranging from $1.27 to $1.53 per kg of CR-PET, which was lower than virgin PET ($1.55 per kg). Heat integration had a small effect on the overall economic (<2%) and environmental (<5%) performances of these process, as there were only a few heat integration opportunities. The average transportation costs were determined to range from $3.56 per MT to $19.03 per MT over the studied range of capacities. The feedstock transportation costs, and environmental impacts were found to have a small effect (<2%) on the NPV, MSP, GHG emissions and total energy demand. Depending on CR-PET precipitation method, the GHG emissions and total energy demand of CR-PET ranged from 1.08 to 3.55 kg CO2-eq. per kg of CR-PET and 17.86 to 56.22 MJ kg−1 of CR-PET, respectively. More research efforts are needed to evaluate the environmental impacts of GVL solvent and to strengthen the LCA impacts observed in this study. The parametric studies, particularly the effects of processing capacity, clearly show desired ranges of profitability for recycling of waste PET using dissolution and precipitation techniques, thus aiding decision-making in the circular economy of waste PET plastics.
Author contributions
Utkarsh Chaudhari: writing – original draft, conceptualization, methodology, software, investigation, formal analysis, data curation, visualization. Daniel Kulas: methodology, software, investigation, formal analysis, validation, writing – review & editing, supervision. Alejandra Peralta: resources, software, validation, writing – review & editing. Tasmin Hossain: resources, transportation methodology, writing – review & editing. Anne Johnson: resources, writing – review & editing. Damon Hartley: resources, transportation methodology, writing – review & editing. Robert Handler: resources, methodology, writing – review & editing. Barbara Reck: writing – review & editing. Vicki Thompson: writing – review & editing. David Watkins: writing – review & editing. David Shonnard: project administration, funding acquisition, conceptualization, methodology, resources, supervision, validation, writing – review & editing.
Conflicts of interest
The authors declare that there are no conflicts to declare.
Acknowledgements
We thank the REMADE Institute for providing financial support to carry out this research. This material is based upon work supported by the U.S. Department of Energy's Office of Energy Efficiency and Renewable Energy (EERE) under the Advanced Manufacturing Office Award Number DE-EE0007897. Disclaimer: “This report was prepared as an account of work sponsored by an agency of the United States Government. Neither the United States Government nor any agency thereof, nor any of their employees, makes any warranty, express or implied, or assumes any legal liability or responsibility for the accuracy, completeness, or usefulness of any information, apparatus, product, or process disclosed, or represents that its use would not infringe privately owned rights. Reference herein to any specific commercial product, process, or service by trade name, trademark, manufacturer, or otherwise does not necessarily constitute or imply its endorsement, recommendation, or favoring by the United States Government or any agency thereof. The views and opinions of authors expressed herein do not necessarily state or reflect those of the United States Government or any agency thereof.”
References
- U. S. Chaudhari, A. T. Johnson, B. K. Reck, R. M. Handler, V. S. Thompson, D. S. Hartley, W. Young, D. Watkins and D. Shonnard, ACS Sustainable Chem. Eng., 2022, 10, 13145–13155 CrossRef CAS.
- J. Di, B. K. Reck, A. Miatto and T. E. Graedel, Resour., Conserv. Recycl., 2021, 167, 105440 CrossRef CAS.
-
U.S. EPA, Advancing Sustainable Materials Management: 2018 Tables and Figures Report, https://www.epa.gov/facts-and-figures-about-materials-waste-and-recycling/advancing-sustainable-materials-management, accessed July 4, 2023 Search PubMed.
-
National Association for PET Container Resources (NAPCOR), 2019 PET Recycling Report, https://napcor.com/reports-resources/, accessed July 4, 2023 Search PubMed.
- U. S. Chaudhari, Y. Lin, V. S. Thompson, R. M. Handler, J. M. Pearce, G. Caneba, P. Muhuri, D. Watkins and D. R. Shonnard, ACS Sustainable Chem. Eng., 2021, 9, 7403–7421 CrossRef CAS.
-
National Research Council, Informing an Effective Response to Climate Change, The National Academies Press, Washington, DC, 2010 Search PubMed.
- S. R. Nicholson, J. E. Rorrer, A. Singh, M. O. Konev, N. A. Rorrer, A. C. Carpenter, A. J. Jacobsen, Y. Román-Leshkov and G. T. Beckham, Annu. Rev. Chem. Biomol. Eng., 2022, 13, 301–324 CrossRef PubMed.
- S. Van Schoubroeck, G. Thomassen, S. Van Passel, R. Malina, J. Springael, S. Lizin, R. A. Venditti, Y. Yao and M. Van Dael, Green Chem., 2021, 23, 1700–1715 RSC.
- U. R. Gracida-Alvarez, H. Xu, P. T. Benavides, M. Wang and T. R. Hawkins, ACS Sustain. Chem. Eng., 2023, 11, 514–524 CrossRef CAS.
- D. Shonnard, E. Tipaldo, V. Thompson, J. Pearce, G. Caneba and R. Handler, Procedia CIRP, 2019, 80, 602–606 CrossRef.
- J.-P. Lange, ACS Sustainable Chem. Eng., 2021, 9, 15722–15738 CrossRef CAS.
-
D. Triebert, H. Hanel, M. Bundt and K. Wohnig, in Circular Economy of Polymers: Topics in Recycling Technologies, ACS Publications, 2021, pp. 33–59 Search PubMed.
- I. Vollmer, M. J. Jenks, M. C. Roelands, R. J. White, T. van Harmelen, P. de Wild, G. P. van der Laan, F. Meirer, J. T. Keurentjes and B. M. Weckhuysen, Angew. Chem., Int. Ed., 2020, 59, 15402–15423 CrossRef CAS.
-
R. Kol, M. Roosen, S. Ügdüler, K. M. Van Geem, K. Ragaert, D. S. Achilias and S. De Meester, in Waste Material Recycling in the Circular Economy-Challenges Developments, ed. D. S. Achilias, 2021, ch. 2, pp. 29–53 Search PubMed.
- I. S. Lase, D. Tonini, D. Caro, P. F. Albizzati, J. Cristóbal, M. Roosen, M. Kusenberg, K. Ragaert, K. M. Van Geem and J. Dewulf, Resour., Conserv. Recycl., 2023, 192, 106916 CrossRef CAS.
- S. Ügdüler, K. M. Van Geem, M. Roosen, E. I. Delbeke and S. De Meester, Waste Manage., 2020, 104, 148–182 CrossRef PubMed.
-
E. B. Nauman and J. C. Lynch, CA Pat., 2065046C, 1994 Search PubMed.
-
G. W. Huber, K. L. Sánchez-Rivera, R. C. Van Lehn, T. Walker and P. Zhou, US Pat., 20230174736A1, 2023 Search PubMed.
- K. L. Sánchez-Rivera, P. Zhou, M. S. Kim, L. D. González Chávez, S. Grey, K. Nelson, S. C. Wang, I. Hermans, V. M. Zavala and R. C. Van Lehn, ChemSusChem, 2021, 14, 4317–4329 CrossRef PubMed.
- T. W. Walker, N. Frelka, Z. Shen, A. K. Chew, J. Banick, S. Grey, M. S. Kim, J. A. Dumesic, R. C. Van Lehn and G. W. Huber, Sci. Adv., 2020, 6, eaba7599 CrossRef PubMed.
- T. Uekert, A. Singh, J. S. DesVeaux, T. Ghosh, A. Bhatt, G. Yadav, S. Afzal, J. Walzberg, K. M. Knauer and S. R. Nicholson, ACS Sustainable Chem. Eng., 2023, 965–978 CrossRef CAS.
- A. del Carmen Munguía-López, D. Göreke, K. L. Sánchez-Rivera, H. A. Aguirre-Villegas, S. Avraamidou, G. W. Huber and V. M. Zavala, Green Chem., 2023, 25, 1611–1625 RSC.
- K. L. Sánchez-Rivera, A. del Carmen Munguía-López, P. Zhou, V. S. Cecon, J. Yu, K. Nelson, D. Miller, S. Grey, Z. Xu and E. Bar-Ziv, Resour., Conserv. Recycl., 2023, 197, 107086 CrossRef.
- J. Yu, A. del Carmen Munguía-López, V. S. Cecon, K. L. Sánchez-Rivera, K. Nelson, J. Wu, S. Kolapkar, V. M. Zavala, G. W. Curtzwiler and K. L. Vorst, Green Chem., 2023, 25, 4723–4734 RSC.
-
U. S. Chaudhari, D. G. Kulas, A. Peralta, T. Hossain, A. T. Johnson, D. S. Hartley, R. M. Handler, B. K. Reck, V. S. Thompson, D. Watkins and D. R. Shonnard, Technology Innovation for the Circular Economy: Recycling, Remanufacturing, Design, System Analysis and Logistics, Wiley-Scrivener, 2023 Search PubMed.
- W. Chen, Y. Yang, X. Lan, B. Zhang, X. Zhang and T. Mu, Green Chem., 2021, 23, 4065–4073 RSC.
- D. M. Alonso, S. H. Hakim, S. Zhou, W. Won, O. Hosseinaei, J. Tao, V. Garcia-Negron, A. H. Motagamwala, M. A. Mellmer and K. Huang, Sci. Adv., 2017, 3, e1603301 CrossRef PubMed.
- D. M. Alonso, S. G. Wettstein and J. Dumesic, Green Chem., 2013, 15, 584–595 RSC.
-
Chemstations Inc., CHEMCAD, https://www.chemstations.com/CHEMCAD/, accessed July 4, 2023 Search PubMed.
-
Chemstations Inc., CHEMCAD User Guide, https://www.chemstations.com/Support/Software_Updates_and_Notes/CHEMCAD_NXT_Support/, accessed July 4, 2023 Search PubMed.
- E. C. Carlson, Chem. Eng. Prog., 1996, 92, 35–46 CAS.
-
The Association of Plastic Recyclers, Model Bale Specifications, https://plasticsrecycling.org/model-bale-specifications, accessed July 4, 2023 Search PubMed.
-
I. Institute of Scrap Recycling Industries, ISRI Scrap Specifications Circular: Guidelines for Plastic Scrap, https://www.isri.org/recycled-commodities/scrap-specifications-circular, accessed July 4, 2023 Search PubMed.
- J. Poulakis and C. Papaspyrides, J. Appl. Polym. Sci., 2001, 81, 91–95 CrossRef CAS.
- D. Achilias, A. Giannoulis and G. Papageorgiou, Polym. Bull., 2009, 63, 449–465 CrossRef CAS.
-
R. C. B. Richard Turton, W. B. Whiting, J. A. Shaeiwitz and D. Bhattacharya, Analysis Synthesis and Design of Chemical Processes, 5th edn, 2018, https://richardturton.faculty.wvu.edu/publications/analysis-synthesis-and-design-of-chemical-processes-5th-edition, accessed July 4, 2023 Search PubMed.
-
G. Towler and R. Sinnott, Chemical engineering design: principles, practice and economics of plant and process design, Butterworth-Heinemann, 2021 Search PubMed.
-
A. Dutta, A. Sahir, E. Tan, D. Humbird, L. J. Snowden-Swan, P. A. Meyer, J. Ross, D. Sexton, R. Yap and J. Lukas, Process design and economics for the conversion of lignocellulosic biomass to hydrocarbon fuels: thermochemical research pathways with in situ and ex situ upgrading of fast pyrolysis vapors, Pacific Northwest National Lab. (PNNL), Richland, WA, USA, 2015 Search PubMed.
-
Closed Loop Partners, Cleaning the rPET Stream, https://www.closedlooppartners.com/foundation-articles/cleaning-the-rept-stream/, accessed July 4, 2023 Search PubMed.
- D. G. Kulas, A. Zolghadr, U. S. Chaudhari and D. R. Shonnard, J. Cleaner Prod., 2022, 135542 Search PubMed.
-
Resource Recycling Systems (RRS), https://recycle.com/, accessed July 4, 2023.
-
U.S. Bureau Of Labor Statistics, National Occupational Employment and Wage Estimates, https://www.bls.gov/oes/current/oes_nat.htm#00-0000, accessed July 4, 2023 Search PubMed.
- K. Lan and Y. Yao, Communications Earth & Environment, 2022, 3, 1–11 Search PubMed.
-
M. S. Peters and K. D. Timmerhaus, Plant design and economics for chemical engineers, McGraw-Hill International, 2018 Search PubMed.
- M. M. Wright, R. C. Brown and A. A. Boateng, Biofuels, Bioprod. Biorefin., 2008, 2, 229–238 CrossRef CAS.
- M. Wright and R. C. Brown, Biofuels, Bioprod. Biorefin., 2007, 1, 191–200 CrossRef CAS.
-
Franklin Associates, Life cycle impacts for postconsumer recycled resins: PET, HDPE, and PP, https://plasticsrecycling.org/images/apr/2018-APR-Recycled-Resin-Report.pdf, accessed April 23, 2022 Search PubMed.
- G. Wernet, C. Bauer, B. Steubing, J. Reinhard, E. Moreno-Ruiz and B. Weidema, Int. J. Life Cycle Assess., 2016, 21, 1218–1230 CrossRef.
-
PRé, SimaPro Database Manual Methods Library, https://simapro.com/wp-content/uploads/2020/06/DatabaseManualMethods.pdf, accessed July 4, 2023 Search PubMed.
- M. Nguyen and R. Prince, Biomass Bioenergy, 1996, 10, 361–365 CrossRef CAS.
-
N. Franklin Associates, Cradle-to-Resin Life Cycle Analysis of Polyethylene Terephthalate Resin Final Revised Report, https://napcor.com/wp-content/uploads/2020/05/Final-Revised-Virgin-PET-Resin-LCA.pdf, accessed July 4, 2023 Search PubMed.
|
This journal is © The Royal Society of Chemistry 2023 |
Click here to see how this site uses Cookies. View our privacy policy here.