DOI:
10.1039/D3EE03638C
(Review Article)
Energy Environ. Sci., 2024,
17, 4390-4425
All-perovskite tandem solar cells: from fundamentals to technological progress†
Received
25th October 2023
, Accepted 7th May 2024
First published on 10th May 2024
Abstract
Organic–inorganic perovskite materials have gradually progressed from single-junction solar cells to tandem (double) or even multi-junction (triple-junction) solar cells as all-perovskite tandem solar cells (APTSCs). Perovskites have numerous advantages: (1) tunable optical bandgaps, (2) low-cost, e.g. via solution-processing, inexpensive precursors, and compatibility with many thin-film processing technologies, (3) scalability and lightweight, and (4) eco-friendliness related to low CO2 emission. However, APTSCs face challenges regarding stability caused by Sn2+ oxidation in narrow bandgap perovskites, low performance due to Voc deficit in the wide bandgap range, non-standardisation of charge recombination layers, and challenging thin-film deposition as each layer must be nearly perfectly homogenous. Here, we discuss the fundamentals of APTSCs and technological progress in constructing each layer of the all-perovskite stacks. Furthermore, the theoretical power conversion efficiency (PCE) limitation of APTSCs is discussed using simulations.
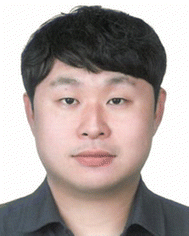
Jaekeun Lim
| Jaekeun Lim is a PhD student at the Institute for Photovoltaics (ipv) at the University of Stuttgart, Germany. He received his MSc in Solar Energy Engineering from Freiburg University, Germany, in 2022, with research experiences in perovskite solar cells at Fraunhofer-Institut für Solare Energiesysteme (Fraunhofer ISE) and École polytechnique fédérale de Lausanne (EPFL). He received his BSc from the School of Energy, Materials & Chemical Engineering at the Korea University of Technology and Education (KOREATECH) in 2018. His current research interests include perovskite structure-based optoelectronics. |
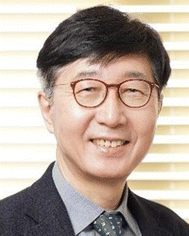
Nam-Gyu Park
| Nam-Gyu Park is a Distinguished Professor at the School of Chemical Engineering and a Director of the SKKU Institute of Energy Science and Technology (SIEST), Sungkyunkwan University (SKKU). He earned his BS degree in chemical education in 1988, followed by MS and PhD degrees in chemistry from Seoul National University in 1992 and 1995, respectively. Prof. Park served as a postdoctoral researcher at ICMCB-CNRS, France, from 1996 to 1997 and at the National Renewable Energy Laboratory (NREL), USA, from 1997 to 1999. Prior to his current role, Prof. Park held key positions, including the director of the solar cell research center at the Korea Institute of Science and Technology (KIST) from 2005 to 2009 and the senior researcher at the Electronics and Telecommunications Research Institute (ETRI) from 2000 to 2005. He joined SKKU as a full professor in 2009. Prof. Park has been recognized as an elected fellow of the Korean Academy of Science and Technology (KAST) since 2017. His expertise lies in the field of photovoltaics, with a career spanning back to 1997. Notably, he made groundbreaking contributions by being the first to report a long-term stable perovskite solar cell in 2012, thereby initiating the research domain of perovskite photovoltaics. Acknowledging his significant impact in the scientific community, Prof. Park was honored as a Citation Laureate (top 0.01% scientist), a New Class of Nobel Prize-Worthy Scientist, on September 20, 2017, and consistently recognized in the highly cited researchers (HCR, top 1% scientists) list from 2017 to 2023 by Clarivate Analytics. Throughout his career, Prof. Park has received numerous awards, including the Scientist Award of the Month (2008), the KIST Award of the Year (2009), the Dupont Science and Technology Award (2010), the SKKU Fellowship (awarded three times in 2013, 2018, and 2021), the PVSEC Hamakawa Award (2015), the Dukmyung KAST Engineering Award (2016), the Samsung Ho-Am Prize (2018), the Rank Prize (UK, 2022), and the NAEK Main Award (2024). Beyond his research contributions, Prof. Park actively contributes to the scientific community as the Senior Editor of ACS Energy Letters and serves on the Editorial Advisory Board for Chem. Rev., ChemSusChem, and Solar RRL. |
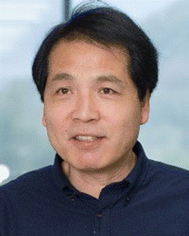
Sang Il Seok
| Sang Il Seok is currently a Distinguished Professor at the Department of Energy and Chemical Engineering, Ulsan National Institute of Science and Technology (UNIST), Korea. Before he joined UNIST in 2015, he served as the principal investigator of the Korea Research Institute of Chemical Technology (KRICT) and as a professor at the Department of Energy Science, Sungkyunkwan University. He obtained his PhD degree from Seoul National University, Korea. His specializes in functional inorganic–organic hybrid materials and energy devices, notably pioneering advancements in perovskite solar cells. |
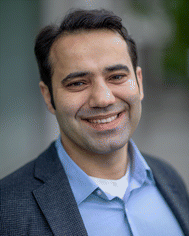
Michael Saliba
| Michael Saliba is a Full Professor and the Director of the Institute for Photovoltaics (ipv) at the University of Stuttgart. He holds a dual appointment at the Helmholtz Research Center Jülich, Germany. His research focuses on a deeper understanding and improvement of optoelectronic properties of photovoltaic materials with an emphasis on emerging perovskites for a sustainable energy future. Prof. Saliba's seminal work on multicomponent perovskites has introduced a general strategy for the combinatorial synthesis and exploration of novel materials. Michael Saliba is also the Speaker of a Graduate School for “Quantum Engineering” of the German Research Foundation (DFG). He was awarded a Starting Grant by the European Research Council. Prof. Saliba held positions at TU Darmstadt, Fribourg University and EPFL with research stays at Cornell and Stanford. He obtained his PhD from Oxford University and MSc degrees in Physics and Mathematics from Stuttgart University together with the Max Planck Institute for Solid State Research. Prof. Saliba has published 200 works attracting 50 000 citations and filed 5 patents in the fields of plasmonics, lasers, LEDs and perovskite optoelectronics. He was on the Early Career Board of Nano Letters, is on the Editorial Advisory Board of ACS Energy Letters and a Senior Editorial Board Member of Materials Today. Clarivate has listed him as a Highly Cited Researcher six times in a row since 2018. He was awarded the Heinz-Maier-Leibnitz prize by the DFG and the Early Career Prize in Semiconductors by IUPAP and named one of the World's 35 Innovators Under 35 by the MIT Technology Review. He is also a Fellow of the International Science Council. In addition, Prof. Saliba received the Kavli Foundation Early Career Lectureship in Materials Science from the Materials Research Society, the Curious Minds Award from Merck, the EU-40 Materials Award from the European Materials Research Society, the Stuart R. Wenham Young Professional Award of the IEEE PVSC, and the High Impact Award from the Helmholtz Association. |
Broader context
Global warming caused by the excessive use of fossil fuels has accelerated the necessity for renewable energy sources. Metal halide perovskites are considered a promising next-generation technology for photovoltaics with rapid progress in performances in recent years and involve manufacturing processes with a low carbon footprint. All-perovskite tandem photovoltaics, constructed using multiple perovskite layers deposited on top of each other, are of particular interest because they permit more efficient use of available areas, require less consumption of materials and demonstrate an improved energy harvest. This is all the more compelling as recently all-perovskite tandems have exceeded the performances of both single-junction perovskite and silicon solar cells. In this review, we outline the theory and advantages of all-perovskite tandems as well as their potential to achieve even higher performances in the future.
|
1. Introduction
Organic–inorganic perovskites have shown great promise for photovoltaics (PVs). Perovskite single junction solar cells have been recently certified at >26% efficiency close to established silicon at >27% efficiency.1 Moreover, certified perovskite-based tandem solar cells have made improvements in a short period of time from 4.6% in 2014 to the current world record of 33.9%.2,3 Even perovskite–perovskite–silicon triple junction solar cells have been recently reported with an efficiency of 27.1%.4
Recently, APTSCs have been gaining attention with rapidly increasing performances, with 28.5% (certified: 28.0%) efficiency for a perovskite–perovskite tandem (double junction) (Fig. 1a–d).5 Although the efficiencies of APTSCs are still lower than silicon–perovskite tandems, they have several benefits. Here, we present the fundamentals of the APTSCs, providing the current research state as well as the future outlook.
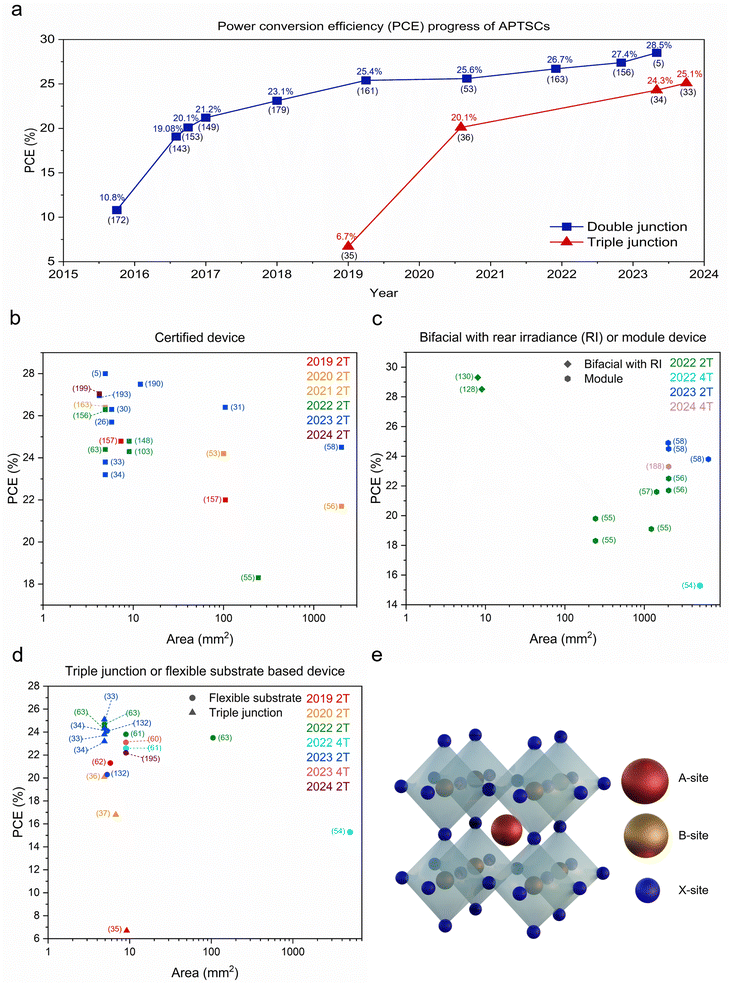 |
| Fig. 1 Summary graphs regarding efficiencies and active areas of APTSCs and the structure of perovskite. (a) This graph shows the power conversion efficiency progress of APTSCs regarding double and triple junctions with efficiency and according reference number just below (in brackets). The bifacial APTSCs are not included. (b) The scatter graph showing the efficiency (vertical axis) and area (horizontal axis) of APTSCs, regarding certified devices showing also the reference numbers. (c) The scatter graph showing the efficiency (vertical axis) and area (horizontal axis) of 2T and 4T APTSCs, containing the following information: bifacial and module device as well as the reference numbers. (d) The scatter graph showing the efficiency (vertical axis) and area (horizontal axis) of 2T and 4T APTSCs involving flexible substrate APTSC and triple junction APTSC information with the reference numbers. Device details (PCE, active area, terminal, and note) are in Table S1 (ESI†) regarding Fig. 1a–d. (e) The standard ABX3 perovskite structure. | |
Perovskites have remarkable material properties: direct bandgap, long diffusion length, long minority carrier life time, tunable bandgap and high defect tolerance.6–10 The ABX3 perovskite crystal structure comprises A, B, and X sites, where the A ion is positioned in the cuboctahedra vacancy formed by the X atoms in cuboctahedral AX12. The B site is occupied as an octahedron in a BX6 structure. The organic–inorganic metal halide perovskites are typically composed of (1) a monovalent A-site cation: caesium (Cs+), methylammonium (MA+) or formamidinium (FA+); (2) a divalent B-site metal: the lead(II) (Pb2+) or tin(II) (Sn2+) ion; and (3) a monovalent X-site anion: chloride (Cl−), bromide (Br−) or iodide (I−), superhalides or pseudohalides (Fig. 1e). The impact of the different components on the perovskite framework determines the motifs and properties of the perovskite crystal structure. For instance, large A-cations lead to 2-dimensional (2D) metal–organic sheets, which can alter electronic properties.11–13 Over time, some leitmotifs for perovskite were found, which predict the formability of the 3-dimensional (3D) organic–inorganic perovskite structure: the A-site component has a size constraint decided by the cuboctahedral vacancies created by the corner-sharing BX6 octahedra. The Goldschmidt tolerance factor (t) can be used to predict the stability of the 3D perovskite structure indirectly given by the ionic radii of elements A, B and X in the equation
, where, rA,B,X are the respective ionic radii.14
Experimentally, most 3D organic–inorganic perovskites have a Goldschmidt tolerance factor in the range of 0.80 ≤ t ≤ 1.00. If t > 1.00, the perovskites form a hexagonal structure. If t < 0.80, due to the small A cation, a non-perovskite structure is formed. A second restriction of the perovskite structure is the octahedral factor (μ), given by μ = rB/rX.15 Generally, in the range of 0.44 ≤ μ ≤ 0.90 a stable octahedral structure is formed.
The tolerance factor and octahedral factor inform about the formability of the perovskite structure. Much research concentrates on multi-component perovskites with any of the A, B, and X-sites rather than the pure structures of MAPbI3, FAPbI3, and CsPbI3, as they frequently suffer from phase instability (FAPbI3 and CsPbI3) or volatility (MAPbI3).
2. Advantages of APTSCs
2.1. High performance (tunability)
Tunable properties with compositional engineering boost research on perovskite solar cells (PSCs). In the organic–inorganic based perovskite structure (ABX3), the perovskite absorber layer from every A, B, and X position can modify the optical bandgap.16–18 For instance, in the A-site case, going from FA+, MA+ to Cs+ widens the bandgap (Fig. 3a). In the B-site case, generally, Sn2+ can create a narrower bandgap than Pb2+. At specific points of tin–lead mixed perovskite films, lower bandgaps than the pure tin-based perovskite film are observed.19 Lastly, in the X-site case, going from I−, Br− to Cl− widens the bandgap. Also, additive engineering with bulky organic molecules slightly changes the bandgap.20–22 The bandgap tunability of the perovskite solar cells (PSCs) allows to extend to the field of tandem technology.23–26 Especially, APTSCs have much potential for performance increase compared to single junction PSCs; however, dedicated bandgap alignment engineering is required. Recently, many studies have shown all-perovskite tandems (double junctions) with optimised narrow bandgaps between 1.21 and 1.26 eV and wide bandgaps between 1.73 and 1.78 eV with PCEs of 26.0–28.5%.5,27–32 On the other hand, the all-perovskite multi-junction bandgaps are not optimised yet for the highest performances, which will be a critical issue in the future.33–37
2.2. Low cost
Compared to conventional silicon solar cells, PSCs have the potential to be a competitive technology owing to: (1) low-temperature manufacturing, where most fabrication steps are below 150 °C, e.g., in the so-called planar architecture that does not require high temperatures (since no mesoporous TiO2 is used). Although, compared with the conventional PV industry, even a 500 °C step (for mesoporous TiO2) could be considered as relatively low. (2) PSCs are a thin-film technology that need only a small amount of material.
Furthermore, studies calculated the economic efficiency of perovskites at a relatively low cost with a levelized cost of energy (LCOE).38,39 For example, one study calculated the LCOE of two types of double junction and two types of single junction solar modules by adopting a bottom-up cost model to estimate the module cost (Fig. 2a–d). It claimed that the all-perovskite tandem solar module showed the most economical cost (Fig. 2e). All-perovskite tandem solar module showed the lowest LCOE with 4.22 US cents kWh−1 (Fig. 2d) compared to other modules (5.50, 4.34 and 5.22 US cents kWh−1; Fig. 2a–c).40 Another study calculated the LCOE of 2-terminal (2T) all perovskite tandem and 4-terminal (4T) all perovskite tandem PV modules. 2T all-perovskite tandem PV modules are slightly more competitive (US $33.8 per m2) than the 4T ones (US $42.3 per m2). However, the overall studies argued that perovskite solar cells have highly competitive prices.41
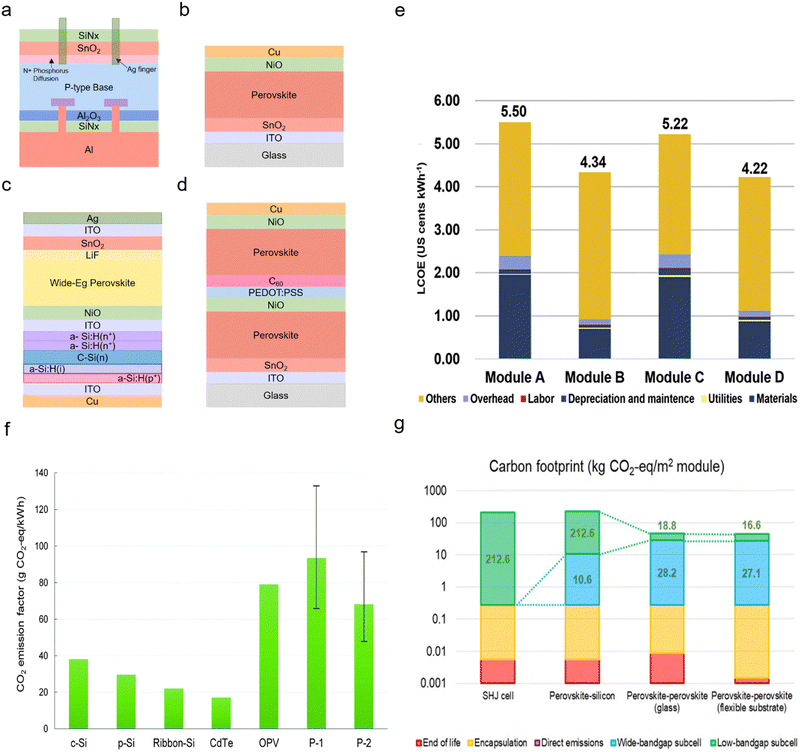 |
| Fig. 2 Low cost and low carbon footprint APTSCs: (a) conventional multi-crystalline silicon solar module. (b) The n–i–p planar structure of a perovskite single junction module. (c) The silicon/perovskite tandem solar module. (d) The perovskite/perovskite solar module. (e) Comparison of LCOE from figure (a)–(d). © 2018. Elsevier All rights reserved.40 (f) The past carbon footprint of c-Si, p-Si, ribbon-Si, CdTe, organic photovoltaic (OPV), and perovskite (P1: TiO2 based perovskite module, P2: ZnO based module). © 2018. Royal Society of Chemistry All rights reserved.64 (g) The recent carbon footprint of a silicon heterojunction (SHJ) cell, perovskite–silicon tandem (wide-bandgap perovskite: (Cs, FA)Pb(I, Br)3), perovskite–perovskite tandem with a glass substrate and perovskite–perovskite tandem with a flexible substrate consisting of a wide-bandgap (Cs, FA, MA)Pb(I, Br)3 and narrow-bandgap (FA, MA)(Sn, Pb)I3 perovskite. © 2020. American Association for the Advancement of Science All rights reserved.66 | |
However, in the LCOE simulation, the stability of perovskite solar cells is a critical factor as longer lifetime devices mean lower LCOE values.38–40,42 In general, in the photovoltaic market, companies warrant the durability of, e.g., 20 years with over 80% of the initial module PCE. Research of perovskite single junction solar cells demonstrated, e.g., 4500 h of stability under illumination for PCEs >22% retaining more than 96% of the initial performance.43 Nonetheless PSCs (and thus APTSCs) still need more robust durability in the future to reach conventional PV module stability of 20 years with over 80% of the initial PCE.
The durability issues of APTSCs are more severe due to the different compositions of the perovskite absorbers. In the literature, most simulations for APTSCs assume long-term stability like conventional photovoltaics, which may be too optimistic for now although the durability of APTSCs is currently also rapidly developing. Hence, realistic LCOE simulations are essential. Furthermore, offering the LCOE results regarding outdoor-based APTSCs is important, as degradation rates can directly affect the LCOE output.
2.3. Scalable and lightweight
The scalability of solar cells is a critical issue for commercialisation escaping from the small lab scale. Many methods can be used for manufacturing large-area PSCs: blade coating, slot-die-coating, spray coating, inkjet printing, screen printing, and electro- and vapour-phase deposition.44–50 Spin coating is often used for lab scale fabrication, although there are examples of large-area PSCs using spin coating.51 Currently, it is challenging to determine which methods will be the frontrunner for commercialisation in the future since all fabrication strategies are developed in parallel. Moreover, most deposition techniques are rapidly advancing with better device performances, e.g., blade coating reaching 23.2% (certified) at 7.3 mm2 in the cell and 18.2% at 3580 mm2 in the module.52 This scalability for the single-junction PSCs can also be extended to APTSCs similarly. Some studies demonstrated decent device performance with APTSCs in large areas. From 2016 to now, six research papers have been reported for large areas (>1000 mm2), including 2T and 4T. The large all-perovskite tandem solar modules' active areas reported in papers are 1200 mm2 (using a stack of glass/ITO/NiO/FA0.8Cs0.2Pb(I0.6Br0.4)3/C60/ALD-SnO2/Au/PEDOT-PSS/FA0.7MA0.3Pb0.5Sn0.5I3/C60/ALD-SnO2/Cu), 1225 mm2 (with a stack of MgF2/glass/IO:H/2PACz/wide bandgap perovskite/LiF/C60/SnOx/ITO and Au/PEDOT:PSS/narrow bandgap perovskite/PCBM/C60/BCP/Cu), 1430 mm2 (using a stack of glass/ITO/PTAA/wide bandgap perovskite/C60/SnO2/Au/PEDOT:PSS/narrow bandgap perovskite/PCBM/C60/BCP/Cu), 2025 mm2 (using a stack of glass/ITO/VNPB/NiO/Cs0.35FA0.65PbI1.8Br1.2/C60/ALD-SnO2/Au/PEDOT:PSS/FA0.7MA0.3Pb0.5Sn0.5I3/C60/ALD-SnO2/Ag), 2025 mm2 (using a stack of glass/ITO/NiO/VNPB/Me-4PACz/wide bandgap perovskite/C60/ALD-SnO2/Au/PEDOT:PSS/narrow bandgap perovskite/C60/ALD-SnO2/Cu) and 5000 mm2 (using a stack of wide bandgap: PET/ITO/SnO2/wide bandgap perovskite/Spiro-MeOTAD/VOx/IMI; of narrow bandgap: PET/ITO/PEDOT:PSS/narrow bandgap perovskite/C60/BCP/Cu), which demonstrated the PCEs of 21.4%, 19.1%, 21.6%, 22.5%, 24.5% and 15.3%, respectively.53–58 Except for the active area of 1200 mm2 (spin coating), all perovskite–perovskite tandem solar cells or modules were fabricated with blade coating.
Yet, the APTSCs still have particular challenges when using scalable fabrication methods, e.g., when transferring optimised spin coating (lab scale) to the blade coating (industry scale) process. Firstly, the higher bromide concentrations in wide bandgap perovskite precursor solutions hinder high-quality, scalable fabrication due to the low solubility showing variable crystallisation kinetics. One study conducted by Xiao et al. attempted to tune the caesium concentration using a gas-assisted blade coating method, which resulted in enlarged average grain sizes from 290 to 380 nm.56 Secondly, it is challenging to eliminate excess perovskite precursor solvents such as DMF or DMSO after depositing perovskite layers due to low vapour pressure. The excess solvents disturb the formation of a uniform film and can be a challenge to process the narrow bandgap perovskite on top of the wide bandgap perovskite as those solvents can also dissolve the underlying wide bandgap perovskite layer. Fundamentally, selecting solvents with low boiling points can be achieved more easily than changing the blade coating parameters such as blade speed, the gap between the blade and the top layer or quenching gas pressure. Thirdly, both the top and bottom cells suffer from stability issues. Typically, Sn–Pb-based narrow bandgap perovskite bottom solar cells have a more critical stability challenge. In the future, large-area APTSCs may need to be manufactured in controlled atmospheres, which may be under nitrogen gas conditions or other controlled environments. Alternatively, the perovskite inks can be made more robust against outside variations. Finally, all perovskite tandem modules face challenges regarding module interconnection as described in Section 4.3 (Module interconnection of APTSCs). These reported papers indicated that APTSCs have the potential for commercial scale-up.54,55
Lightweight or flexible substrate-based architectures are another desired property in perovskite research. Flexible PSCs are a promising high-power-per-weight application.59 The flexible substrate-based APTSCs were reported in the papers using polyethylene naphthalate (PEN) or polyethylene terephthalate (PET) substrates with decent PCEs (Fig. 1d).54,60–63 These flexible or thin metal-based architectures may aid in developing economic roll-to-roll processing including an encapsulation process for APTSCs.54 However, all fabrication steps of APTSCs need to be checked for compatibility with roll-to-roll processing because of the speed and lower cost.
2.4. CO2 footprint (energy use)
The carbon footprint is the total amount of carbon dioxide along the entire value chain. At the beginning of the perovskite research, environmental research claimed that PSCs or organic solar cells have an issue with carbon dioxide (CO2) emission compared to other types of conventional photovoltaics such as Si-based solar cells or CdTe owing to a short lifetime (Fig. 2f). They considered the lifetime of the PSCs as approximately two years. Hence, the study mentioned that PSCs have 2–3 times higher carbon dioxide emissions than silicon photovoltaics.64 However, as perovskites have been quickly improving, recent research showed that <100 kg CO2eq per kWp for single-junction PSCs and <200 kg CO2eq per kWp for double junction APTSCs are among the lowest carbon dioxide emissions per kilowatt.65 Moreover, PSCs have the shortest energy payback time (EPBT) of 0.35 years among different types of solar cells. A study regarding the carbon dioxide footprint compared silicon/perovskite tandem solar modules and perovskite/perovskite tandem solar modules. It postulated a perovskite/silicon tandem with 25.2% efficiency and a perovskite/perovskite tandem with 23.1% efficiency as 2T architectures. Despite the perovskite/perovskite tandem modules having a lower efficiency than the perovskite/silicon tandem modules, carbon footprint calculations showed that perovskite/perovskite tandem modules emit less carbon than silicon heterojunction (SHJ) solar modules (212.6 kg CO2eq per m2) or perovskite–silicon tandems (223.2 kg CO2eq per m2) considering the lifetime of modules. When using the flexible substrate for perovskite/perovskite tandem solar modules (43.7 kg CO2eq per m2), a slightly less carbon footprint was observed compared to a glass substrate (47.0 kg CO2eq per m2) (Fig. 2g).66
3. Fundamentals of tandem solar cells
3.1. What are tandem solar cells?
Tandem (double junction) or multi-junction solar cells have been studied intensively over the years and are now a reliable technology, e.g. for space solar cells. The concept of tandem solar cells is to stack different absorber layers on top of each other so that each layer sequentially absorbs light close to its bandgap. Thus, the sunlight goes through the stack from the wide to the narrow bandgap material. This way, photons with energies lower than the bandgap are transmitted through the material. The photons with energies higher than the bandgap get absorbed while any excess energies beyond the bandgap are lost to internal thermal conversion.
The tandem solar cell avoids excessive losses in thermal energy by absorbing the higher energy photons in a suited material with a higher bandgap. Accordingly, architectures with two or three different absorber layers can be targeted adding complexity but also reducing the amount of heat loss.
3.2. Perovskite-based tandem or multi-junction solar cells
Ever since the concept of multi-junction solar cells was suggested in 1955, various tandem (double-junction) or multi-junction solar cells have been demonstrated to facilitate the development of highly efficient photovoltaics.67 For example, the highest efficiency of a multi-junction solar cell is 47.6% using optimised metal contacts and antireflection layers in a complex four-junction gallium indium phosphide (GaInP)/aluminium gallium arsenide (AlGaAs)/gallium indium arsenide phosphide (GaInAsP)/gallium indium arsenide (GaInAs) in a wide light spectral range between 300 and 1780 nm at a concentration of 665 suns.68
As the perovskite bandgap can be tuned from 1.2 to 3.0 eV, it can be flexibly employed with other absorber layers, such as perovskite/silicon solar cells, perovskite/organic solar cells, perovskite/copper indium gallium selenide (CIGS) solar cells, perovskite/dye-sensitized solar cells (DSSCs), perovskite/cadmium telluride (CdTe) solar cells and all-perovskite stacks.23,24,69–71
3.3. Theoretical performance limit of tandem solar cells
The Shockley–Queisser (S–Q) limit was calculated for the maximum efficiency in single junction solar cells considering only the radiative recombination loss while neglecting non-radiative recombination caused, e.g., by Auger recombination and Shockley–Read–Hall recombination. Moreover, the S–Q limit assumes that each absorbed photon creates one electron/hole pair and that internal thermal conversion occurs, i.e., photon energy in excess of the bandgap is lost as heat. Open-circuit voltage (Voc), short-circuit current (Jsc) and fill factor (FF), which are factors of device efficiencies, show different trends with increased bandgap. Voc increases linearly until a bandgap of 4 eV. Jsc decreases steeply, and around a bandgap of 3.5 eV reaches nearly 0. The FF can reach theoretically over 90% at 1.5 eV and a higher bandgap. According to the S–Q limit, the best possible theoretical efficiency is 33.16% with a bandgap of 1.34 eV under standardised air mass (AM) 1.5G illumination conditions (Fig. 3a–d).72
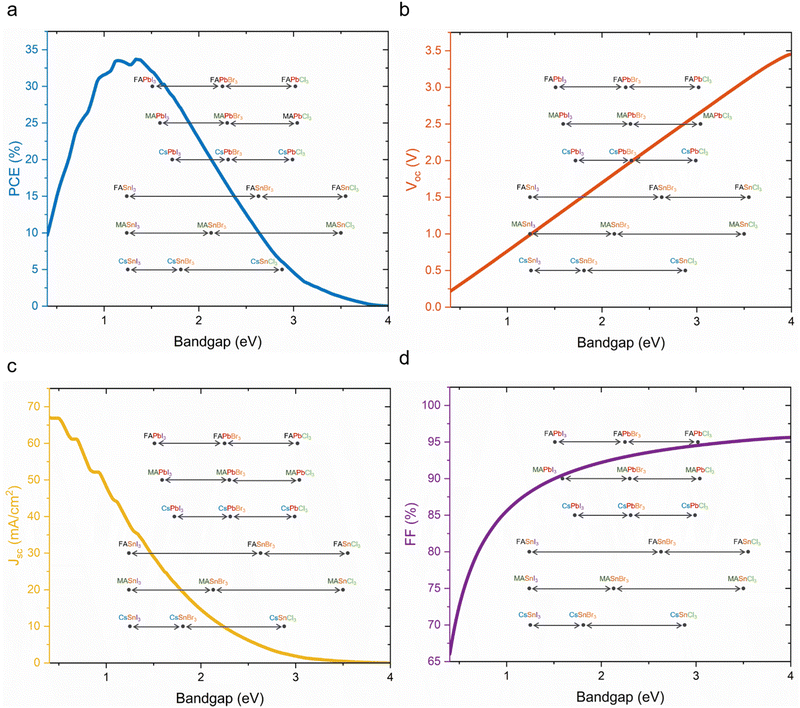 |
| Fig. 3 Prediction of single junction solar cells. (a) Shockley–Queisser limit graphs in terms of PCE, (b) Voc, (c) Jsc and (d) FF with the bandgaps of the different A-site, B-site and X-site perovskite compositions (the same colour indicates the same mono or polyatomic ions). | |
For higher efficiencies, a tandem solar cell with multiple materials is required. Although the ideal bandgap for the wide bandgap perovskite is close to 1.7 eV for Si or CIGS bottom cells (bandgap 1.1 eV), a higher bandgap of around 1.8 eV is preferred to pair with the bottom narrow-bandgap (around 1.2–1.3 eV) perovskite solar cells.24 The highest efficiencies that can be achieved with double junction tandems are 46% and 46.1% for 2T and 4T considering bandgaps from 0.5–2.5 eV, respectively.73 However, achieving perovskite bandgaps <1 eV, needed for high multi-junction stacks, is challenging. All perovskite tandem solar cell studies are restricted to the narrowest perovskite bandgap at 1.2 eV (using mixtures of Sn and Pb).19 Many studies employed a well-optimised narrow bandgap of 1.22 eV. Therefore, utilising a top cell with 1.82 eV and a bottom cell with 1.22 eV enables a theoretical 43% PCE for a 2T tandem, which is similar to a 4T tandem, where the bandgap of the top cell can range from 1.75 to 2.08 eV, under AM 1.5G illumination as shown in Fig. 4a–d. So far, 1.22 eV and 1.25 eV as bottom bandgaps were used for triple junction all perovskite solar cells. In the theoretical PCE limit calculation, when a bottom bandgap of 1.22 eV was employed, an intermediate bandgap of 1.59–1.61 eV and a wide bandgap of 2.08–2.11 eV combination can achieve over 46% PCE. When a bottom bandgap of 1.25 eV was used, an intermediate bandgap of 1.62–1.65 eV and a wide bandgap of 2.1–2.13 eV combination can theoretically achieve over 45% PCE, under AM 1.5G illumination as shown in Fig. 5a–d. Although this calculation does not include the thickness of absorber layers, recent APTSC research showed that around 400 nm is desired for a wide bandgap, over 1000 nm for a narrow bandgap in a double junction and approximately 300 nm for a wide bandgap and over 1000 nm for intermediate and narrow bandgaps in a triple junction as shown in Table S2A and B (ESI†). Many works have optimised the thicknesses of double-junction perovskite absorber layers. However, there is not sufficient research yet on the optimised thicknesses for triple junction APTSCs. This review provides APTSC simulation information regarding potential efficiency in Section 7 and Table 3 considering the electrical properties of real devices' stacks.
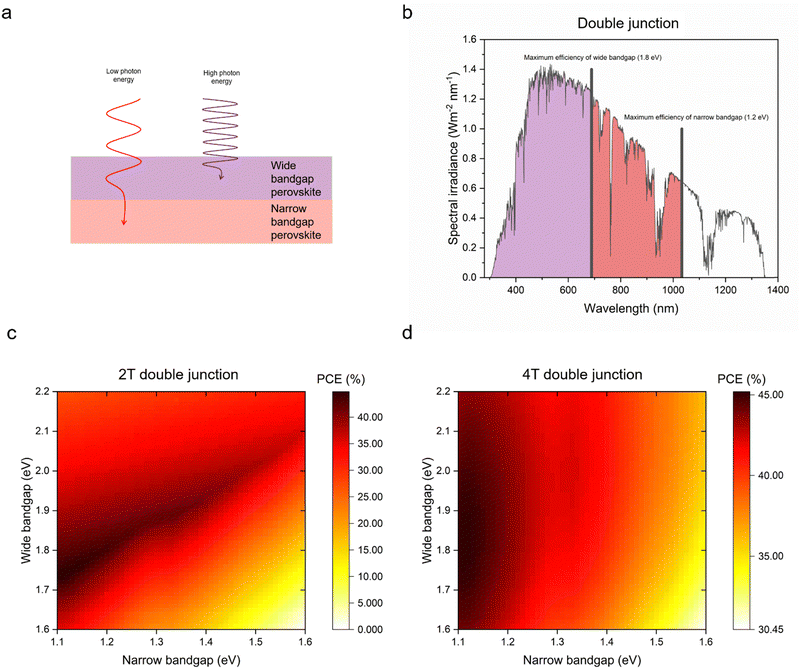 |
| Fig. 4 Prediction of double junction (tandem) solar cells: (a) scheme of photon energy absorption by wide and narrow bandgap perovskites in double junctions, (b) spectral irradiance graph showing theoretical maximum power conversion efficiency bandgaps for a 2-terminal (2T) double junction, (c) theoretical efficiency limit of tandem solar cells in 2T, which is a monolithic structure considering narrow bandgaps (1.1–1.6 eV) and wide bandgaps (1.6–2.2 eV), and (d) theoretical efficiency limit of tandem solar cells in 4-terminal (4T), which is a stacked structure mechanically considering narrow bandgaps (1.1–1.6 eV) and wide bandgaps (1.6–2.2 eV). | |
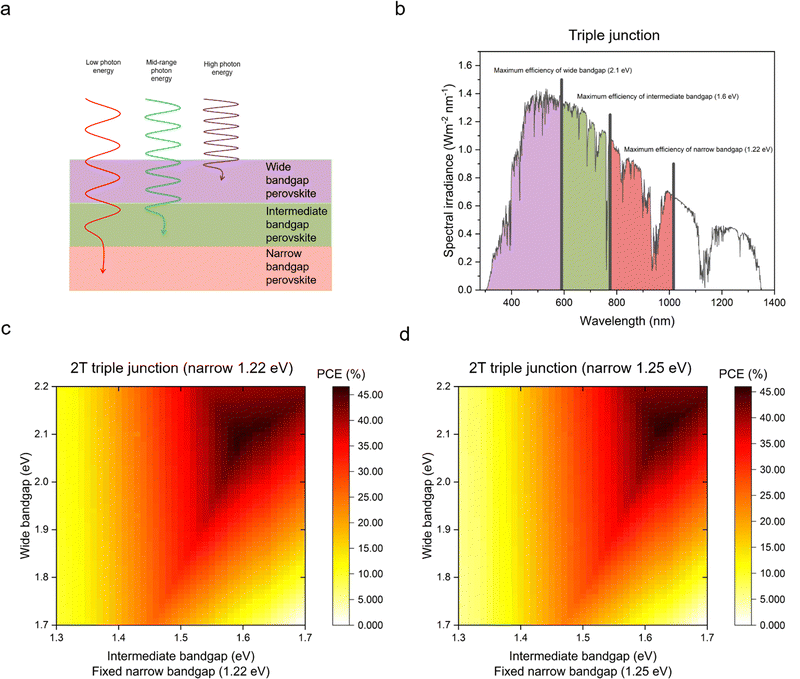 |
| Fig. 5 Prediction of triple junction (multi-junction) solar cells. (a) Scheme of photon energy absorption by wide and narrow bandgap perovskites in triple junctions, (b) spectral irradiance graph showing theoretical maximum power conversion efficiency bandgaps for a triple junction with a 1.22 eV narrow bandgap. (c) Theoretical efficiency limit of triple junction solar cells with a monolithic structure considering the narrow bandgap (the fixed value is 1.22 eV), intermediate bandgap (1.3–1.7 eV) and wide bandgap (1.7–2.2 eV), and (d) theoretical efficiency limit of triple junction solar cells in a monolithic architecture considering the narrow bandgap (a fixed value of 1.25 eV), intermediate bandgap (1.3–1.7 eV) and wide bandgap (1.7–2.2 eV). | |
3.4. Wide bandgap perovskite solar cells
Wide bandgap perovskite solar cells had already been successfully integrated with narrow-bandgap absorbers such as Si (1.12 eV), CIGS (1.1 eV), and tin (Sn)–lead (Pb)-based-perovskites (1.25 eV), resulting in tandem architectures with promising efficiencies of 33.9%, 24.2%, and 28.5%, respectively.5,24
However, unlike well-investigated perovskites with bandgaps of 1.4–1.6 eV for single junction or narrow bandgap perovskites (1.2–1.4 eV), wide bandgap perovskites have a relatively large Voc deficit, e.g., a Voc of 1.7 V (theoretical limit is 1.98 V) for a bandgap of 2.3 eV contrasting narrow bandgap perovskites with 1.26 V (theoretical limit is 1.32 V) for a bandgap of 1.6 eV.74,75 The Voc is a key performance indicator towards higher efficiency of APTSCs.
Especially, 2T APTSCs have a significant opportunity to improve efficiencies as the total Voc in the series connection is the sum of the individual subcell's Voc. In a study, FACs-based (1.77 eV bandgap) PSCs were tested to determine the cause of the Voc deficit. Although the theoretical Voc is 1.49 V at 1.77 eV, the device showed 1.03 V. It was concluded that trap-assisted, non-radiative recombination (∼400 mV) and photoinduced phase segregation (∼100 mV) reduce the Voc. The main reason for the Voc deficit is the non-radiative recombination within the perovskite absorber and interface between perovskite and charge extraction layers such as electron transport layers or hole transport layers.76 Up to now, using new materials for the charge extraction layer, additive engineering in perovskite precursors and passivation layers between the perovskite absorber layer and charge extraction layer have been applied to reduce non-radiative recombination.77–81
Here, the wide bandgap perovskites are discussed within the context of inorganic perovskites and organic–inorganic hybrid perovskites with mixed halides and cations.
3.4.1. Inorganic perovskite solar cells.
Incorporating fully Cs+ in a perovskite crystal as an A-site instead of MA+ or FA+ organic molecules increases thermal stability.82–86 CsPbX3-based (X: halides) structures have bandgaps from 1.72 eV to 2.99 eV (Fig. 3a).17 As a side note, inorganic perovskites may be suited for space applications due to thermal stability at temperatures >200 °C.87
However, in inorganic perovskites, stability challenges arise when devices are exposed to humidity, oxygen and illumination conditions.88 The most extensively studied inorganic perovskites are CsPbI3, CsPbBr3, and halide mixtures thereof CsPbI3−xBrx, where x is 0 < x < 3.
CsPbI3 has four different types of phases, one photoinactive yellow phase, which is the orthorhombic δ-phase, and three photoactive black phases: cubic phase (α-phase), tetragonal phase (β-phase), and orthorhombic phase (γ- phase). α-phase CsPbI3 has the ideal bandgap (1.73 eV). To convert from the δ-phase of CsPbI3 to the α-phase, a high temperature of 360 °C is needed. In the process of cooling after annealing, CsPbI3 transforms into the original yellow δ-phase. However, in the process of phase change, CsPbI3 shows a series of metastable black polymorphs. The symmetry α-phase begins to transit to the β-phase at 260 °C, followed by a further loss of symmetry to the γ-phase at 175 °C. During the α → β → γ transition, the high symmetry is removed because of octahedral tilting and macroscopic strains. Consequently, stable CsPb(I1−xBrx)3-based solar cells were demonstrated with various deposition techniques and surface or additive engineering. Simultaneously, this inorganic perovskite-based wide bandgap APTSC showed relatively high performance with 25.6% PCE.89
3.4.2. Mixed halide or cation-based wide bandgap solar cells.
Not only Cs-based perovskite films but also standard organic cation-based perovskite films can contribute to tandem solar cells. They are favourable due to their wide bandgaps utilising mixed halide. The crystallisation of a mixed halide perovskite with Br− and I− (MA0.9Cs0.1Pb(I0.6Br0.4)4) can achieve a bandgap of 1.8 eV following the Ostwald ripening crystal growth.90 Another example demonstrated reaching a wide bandgap ultimately under Cs+ free conditions and modifying only the halide part, i.e., MAPbIxBr3−x. The composition allows the optical bandgap to reach around 1.70–1.75 eV.91,92
However, the I–Br mixed halide perovskites have shown phase segregation resulting in different bandgap energies.93,94 This photoinduced phase segregation forms the I-rich and Br-rich domains on surfaces and grain boundaries under illumination resulting from ion migration.95 This phenomenon can affect the production of photoinduced traps, reduction of charge mobility, and short carrier lifetime causing Voc loss.
Hence, typically CsxFA1−xPbI3 (x is from 0 to 1) perovskites have been investigated to avoid the halide segregation problem.96 After photoinduced segregation, a self-healing phenomenon can be observed to recover from the damage of two-photon microscopy.97 When Cs is >0.5 in CsxFA1−xPbI3, a potentially higher stability than pure CsPbI3 was observed due to a more appropriate tolerance factor. However, because of the different phase transition temperatures between FAPbI3 and CsPbI3 perovskites, and the large lattice mismatch of perovskite structure, the quest for phase stable materials without segregation is still ongoing.98
3.5. Narrow bandgap PSCs
The development of narrow bandgap PSCs is also one of the main factors responsible for the compatible APTSCs replacing the silicon or CIGS bottom cells. In recent research, tin-based PSCs or tin–lead mixed PSCs provided promising results.99–102 Partial substitution of Sn into Pb perovskites forming the mixed Sn–Pb perovskites can tune the bandgap to the near-infrared region (1.2 to 1.4 eV), which can be employed for ideal bandgap single-junction PSCs or be paired with wide bandgap PSCs to fabricate APTSCs.16 The mixed Sn–Pb perovskites possessed unique optoelectronic properties, such as high conductivity, likely due to high background carrier concentrations, and the bandgap bowing effect (not following the Vegard law) that showed non-linearity of the bandgap graphs.103,104 This shows that Sn–Pb perovskites (Pb0.25Sn0.75 alloy) have a lower bandgap than pure Sn perovskite.105 Moreover, Sn or Sn–Pb perovskites have been developed for fabricating low-toxicity PSCs.106–108
3.5.1. Pure Sn (lead-free)-PSCs.
A pure Sn-based perovskite absorber layer is in the spotlight due to the broad absorption range with a bandgap of 1.24 eV, thus including the infrared region, high charge mobilities, long carrier diffusion, and lifetimes.109,110 MA+ is hygroscopic.111,112 Hence, MA+ can react with water caused by the degradation of MASnI3 perovskite devices. Sn–O bonds are produced between water molecules and the surface Sn atoms, breaking Sn–I bonds with the I atoms of the closet MAI layer.113 Therefore, pure Sn-perovskites suffer from instability due to the Sn2+ to Sn4+ oxidation, leading to the defect formation of Sn vacancies in the crystal structure and resulting in high p-doping.114 The tin vacancies act as the main recombination sites for charge carriers causing much-shortened durability and poor operational stability of 500 h (under 75% relative humidity conditions) compared with their wider bandgap (>1.5 eV) counterparts, which are, e.g., stable for 1200 h (at 85 °C and 85% relative humidity) retaining 86% of the initial efficiency.115,116 This imposes challenges for the monolithic APTSC structure.117
3.5.2. Sn–Pb mixed PSCs.
MASnI3 perovskites did not demonstrate significant photovoltaic properties for a long time because of the unstable Sn2+. Hence, a small content of Pb is often added to fabricate PSCs and stabilise Sn2+. The alloyed perovskite with MASnI3 and lead analogue attracted interest as a narrow bandgap absorber exhibiting 1.2–1.3 eV for single-junctions and the bottom cells for APTSCs. The PCEs of Sn–Pb mixed-perovskites have improved from 7.37% for MASn0.25Pb0.75I3 at 1.24 eV in 2014 to 23.2% for MASnxPb1−xI3 (x is from 0 to 1) at 1.21 eV in 2022.16,118 Sn–Pb-mixed perovskites have exhibited a better stability than pure Sn-based perovskites due to reduced (unwanted) tin oxidation, improving film quality and binding energies. Nevertheless, the stability issue still remains a challenge for Sn-containing perovskites.119 One facile solution is compositional engineering. Instead of the pure MA+, adding FA+ or Cs+ improved the efficiency to 21% and 1000 h of thermal stability under air and dark conditions at 85 °C without encapsulation.120,121 Currently, Pb–Sn-mixed-perovskite is the only viable narrow bandgap absorber and thus, the only option for the bottom cell in APTSCs. Therefore, many methods were used for studying the Sn2+ instability, which thus will be elaborated below.
4. Architectures of APTSCs
Each configuration of the tandem solar cells has advantages and disadvantages. APTSCs have a similar architecture to silicon/perovskite tandem solar cells.122 Commonly, 2T and 4T were demonstrated in many studies.
4.1. 2T APTSCs
The concept of 2T APTSCs is to fabricate all the layers on the same substrates, i.e. a monolithic architecture. The stack follows back electrode/narrow-bandgap perovskite (bottom cell)/interconnecting layer (charge recombination layer)/wide-bandgap perovskite (top cell)/transparent electrode (Fig. 6a). Thus, 2T tandems only need one substrate, which is one of the cost advantages. However, when the top layers of the overall tandem are deposited, it is crucial not to damage the underlying layers, e.g., by solvent addition or sputtering. In addition, the configuration of the interconnecting layers is important. Three different interconnection viewpoints should be considered to create the high-quality interconnecting layers: electrical, optical and mechanical. Electrical interconnection is considered to extract carriers from the near subcells and to facilitate the recombination in the subcells. Optical interconnection needs to address optical transparency issues to reduce absorption losses. Mechanical interconnection is required in order not to damage the underneath subcells during the device fabrication.123 This review describes the main strategies for manufacturing interconnecting layers in Section 6.3.
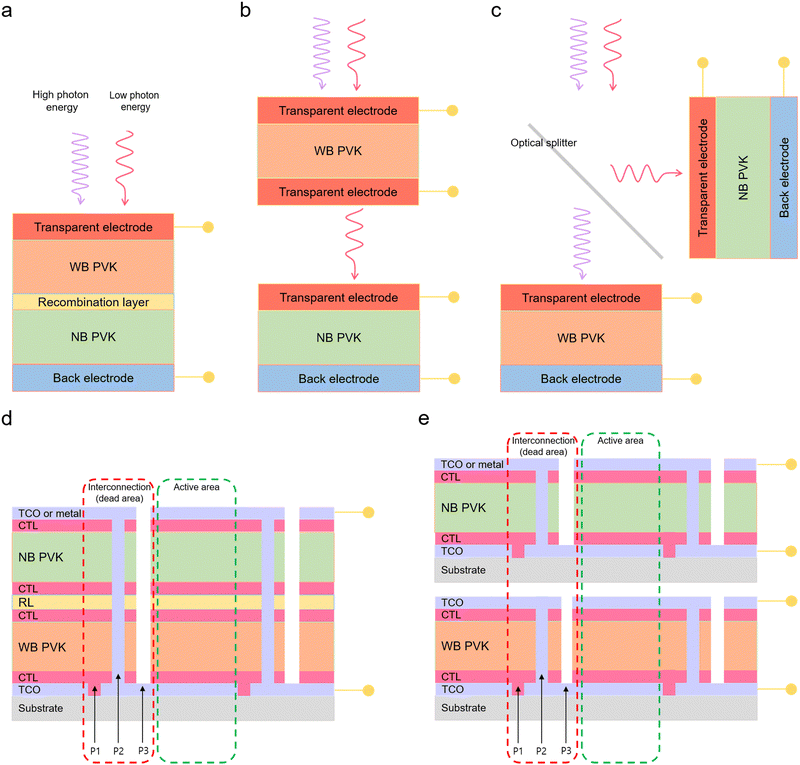 |
| Fig. 6 Standard double junction configuration of tandem solar cells and configuration of all perovskite tandem modules. (a) 2-Terminal (2T) configuration. (b) 4-Terminal (4T) mechanically stacked, (c) and 4-terminal-optically splitting configuration. The optical splitter separates the high photon energies and low photon energies. High photon energies are absorbed by wide bandgap perovskite layers and low photon energies are absorbed by narrow bandgap perovskite layers. © 2021. John Wiley and Sons All rights reserved.127 (d) Scheme of 2-terminal all-perovskite-based tandem module configuration with interconnection (dead area indicated by red dashed lines) consisting of patterns 1, 2 and 3 (P1, P2 and P3) and active area (green dashed lines). (e) Scheme of 4-terminal all-perovskite-based tandem module configuration. TCO is the transparent conductive oxide. CTL is the charge transport layer. WB PVK is the wide bandgap perovskite layer. RL is the recombination layer. | |
4.2. 4T APTSCs
4T tandems use two different substrates (Fig. 6b and c). Moreover, 4T APTSCs do not require current matching as there is no series interconnection mechanically. Thus, the fabrication process of 4T tandems is more convenient than that of 2T tandems, although it employs more materials and is prone to higher optical losses from parasitic absorption and unwanted reflection. 4T tandems have two types of designs. One type is similar to 2T but requires four electrodes. However, the used area is the same as 2T tandems. Another type is an installed optical splitter between two subcells, which are located perpendicularly. Therefore, one subcell absorbs high energies of photons, another absorbs low energies of photons. This method can be more efficient when it comes to large areas for commercialisation, although the additional costs for the optical splitter needs to be factored in as well.123
4.3. Module interconnection of APTSCs
Perovskite solar modules are commonly manufactured by an integrated series interconnection of subcells. Fig. 6d and e show the scheme of 2T and 4T all-perovskite tandem modules, respectively. For fabricating all-perovskite modules, a scribing process with three patterning steps P1, P2 and P3 is used:
P1 scribing is carried out on a transparent conductive oxide (TCO) based substrate. P2 scribing is implemented before depositing the last conductive layers, which means removing all layers except the bottom TCO. These P2 lines interconnect the subcells. After the top electrode deposition, such as TCO or metal, P3 lines are scribed to isolate the top electrode from adjacent cells. Although this patterning process is necessary, it comes with drawbacks, such as dead areas where the scribing was applied (not creating electricity). Therefore, the dead areas must be minimised without producing shunting losses. A study demonstrated how the subcell width can affect the performance of all-perovskite tandem modules. Increasing the subcell width (6.4–15.0 mm) resulted in having higher geometric fill factors (88.3–95.0%) and instantly affected higher module efficiencies (the highest efficiency is 21.2% with a width of 11.25 mm and a geometric fill factor of 93.3%). However, from the width of 7.5 mm, series resistance increased, and consequently, the fill factor of the module was reduced following a parabolic shape.
After the P3 lines, each small cell is exposed to ambient atmospheres such as oxygen or moisture causing degradation. In perovskite tandem modules, halides from the perovskite absorbers can react with the metal electrodes at the interconnecting subcells. This may create deep defects, which can be mitigated using, e.g., a thin conformal diffusion barrier deposited, e.g., by atomic layer deposition.56 As a result, the conformal diffusion barrier hampered halide–metal interdiffusion avoiding the reaction between the perovskite layer and the metal electrodes improving stability. Finally, 4T all-perovskite tandem modules consist of two submodules. Hence, it is important to align the patterned areas carefully to prevent power losses.54,55,57,124–126
5. More specific APTSCs
Less standard configurations use bifacial APTSCs, inorganic-based APTSCs, flexible APTSCs, substrate configured or multi-junction designs.
5.1. Bifacial all-perovskite tandems
A bifacial solar cell generates more electricity using light from the front and rear side. The bifacial APTSCs were reported in various studies in the literature: Li et al. suggested the initial design of bifacial APTSCs using TCO as the back electrode (Fig. 7a). Moreover, the optimised current matching design for mono-facial APTSCs resulted in the current mismatch in the bifacial configuration because the current of the bottom side will be increased with albedo in bifacial monolithic tandems. Besides, the back side TCO led to a reduced current as there was no light reflection parts like metals to guide more light into the perovskite absorber. For example, at the wide bandgap of 1.77 eV, mono-facial APTSCs showed 24.36% and bifacial APTSCs showed 23.34% and 25.25% without and with 30 mW cm−2 rear irradiance (RI) conditions respectively. Although under the RI conditions, a 1.68 eV bandgap indicated the highest efficiency of 28.51%, without RI, only 19.29% efficiency was obtained.128 Another study also focused on creating TCO electrodes for both sides, demonstrating a PCE of 20% (Fig. 7b).129 Chen et al. implemented several techniques for improving energy yield: by decreasing the optical bandgap of a wide bandgap cell to 1.65 eV instead of 1.78 eV and by specially embedding a light-scattering micrometre-sized particle layer into a narrow bandgap perovskite (Fig. 7c). As the embedding particles, the cation-exchange resin particles were employed to obtain the light-scattering function to lock the Pb in perovskite devices, which is important for leakage cases. This particle layer supported solving the removal of the reflection back metal electrode and the reduction in the photon path length. This method effectively absorbed 5 to 15% in the infrared region. The highest efficiency of a bifacial APTSC was obtained at a wide bandgap of 1.65 eV with 29.3% under the 30% albedo light conditions. However, without albedo light conditions, the bandgap of 1.65 eV (16.7%) led to a lower efficiency than the bandgap of 1.78 eV (20.6%).130
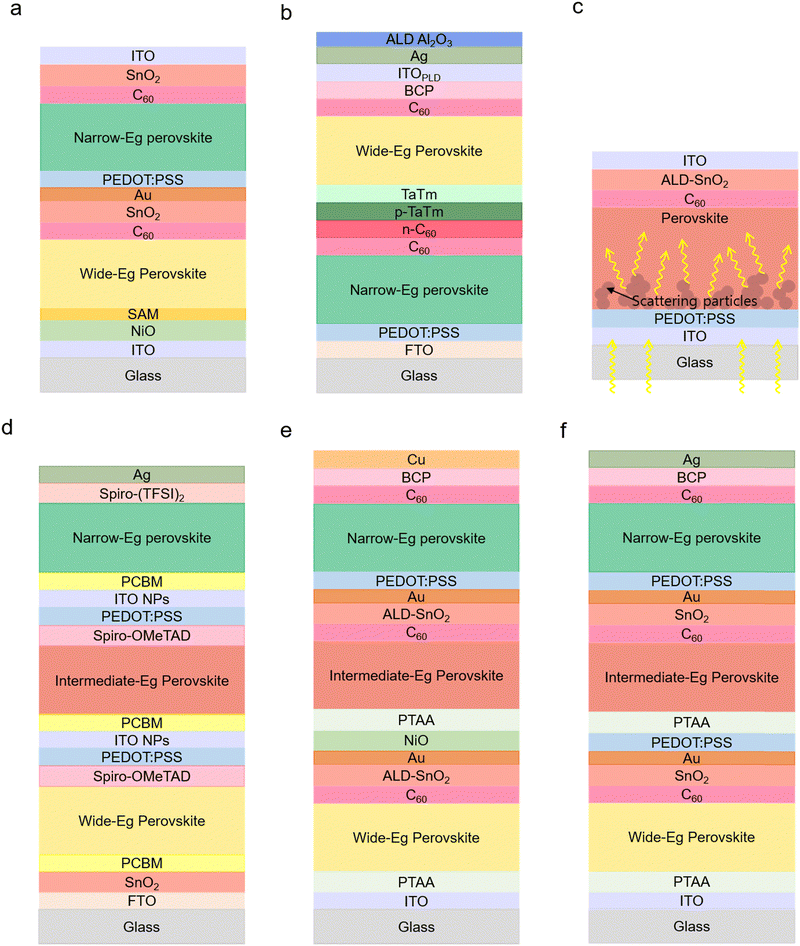 |
| Fig. 7 Various types of APTSCs. (a) Scheme of the bifacial APTSC configuration. © 2022. Springer Nature All rights reserved.128 (b) Another type of bifacial APTSC configuration. © 2022. American Chemical Society All rights reserved.129 (c) Illustration of the scattering particles (resin) functioning with increasing photon path length in the narrow bandgap perovskite film. © 2022. American Association for the Advancement of Science All rights reserved.130 (d) The APTSC structure of a fully solution-processed triple junction.35 (e) (f) Other types of solution-processed triple junction APTSC configurations. © 2020. American Chemical Society All rights reserved. © 2020. Springer Nature All rights reserved.36,37 | |
5.2. Inorganic APTSCs
As mentioned above, inorganic perovskites have a favourable optical bandgap (∼1.77 eV) for wide bandgap solar cells and high thermal stability. Until now, one publication demonstrated APTSC with an inorganic wide bandgap subcell. However, the interface between the transport layer and inorganic perovskite has challenges of a significant energetic mismatch and limited charge extraction. To solve this, interfacial engineering was applied.131 Furthermore, a study demonstrated fully inorganic-based APTSCs in a 4T integration.232
5.3. Flexible APTSCs
Flexible APTSCs provide the opportunity for mass production by a roll-to-roll process in the future. Currently, various works use a flexible substrate, such as polyethylene naphthalate (PEN) or polyethylene terephthalate (PET), although the loss of open-circuit voltage at a wide bandgap is more distinct than that on rigid substrates. Another challenge is depositing layers uniformly on the flexible substrate since flexible substrates typically have rougher surfaces than the rigid ones. To resolve these issues, primarily interfacial layer engineering or additive engineering was implemented. These flexible substrate-based APTSCs were tested on the 4T and 2T configurations, e.g., with the largest area being at 5000 mm2 on a PET substrate with a PCE of 15.3% in 4T APTSCs. The highest efficiency on a flexible PET substrate with a 4.9 mm2 active area was 24.7% in 2T APTSCs.54,60–63
5.4. Substrate-configured APTSCs
The generally used superstrate configuration, where the wide bandgap subcell comes first followed by the narrow bandgap subcell, has stability challenges in the fabrication. Especially, the narrow bandgap perovskite comprises tin–lead mixtures, which are particularly exposed to the oxygen environment, to which they are more sensitive compared to the wide-bandgap perovskite at the bottom. A substrate-configured device is fabricated by depositing the first narrow-bandgap perovskite and subsequently the wide-bandgap perovskite. Hence, the narrow bandgap perovskite embedded at the bottom is more protected from oxygen conditions. This can improve oxidation resistance and thus stability. Furthermore, this configuration can utilise all substrates flexibly, from transparent substrates such as glass, PET, PEN, and polyimide (PI) to opaque substrates like polymers, stainless steel or metal foils.132
5.5. Multi-junction APTSCs
Multi-junction (three or more junction) APTSCs have the potential for even higher PCEs beyond 33%. Among the main works published thus far, the reported efficiencies, although lower than the double-junction tandem solar cell, were: 6.7% (Glass/FTO/SnO2/PC61BM/wide bandgap perovskite (WB PVK)/Spiro-MeOTAD/PEDOT:PSS/ITO NPs/PC61BM/intermediate bandgap perovskite (IB PVK)/Spiro-MeOTAD/PEDOT:PSS/ITO NPs/PC61BM/narrow bandgap perovskite (NB PVK)/Sprio-(TFSI)2/Ag), 16.8% (Glass/ITO/PTAA/WB PVK/C60/SnO2/Au/PEDOT:PSS/PTAA/IB PVK/C60/SnO2/Au/PEDOT:PSS/NB PVK/C60/BCP/Ag), 20.1% (Glass/ITO/PTAA/WB PVK/C60/ALD-SnO2/Au/NiO/PTAA/IB PVK/C60/ALD-SnO2/Au/PEDOT:PSS/NB PVK/C60/BCP/Cu), 24.3% (Glass/ITO/NiOx/Me-4PACz/WB PVK/PEAI-EDAI2/PCBM/PEIE/SnOx/ITO/NiOx/Me-4PACz/IB PVK/PEAI-EDAI2/PCBM/PEIE/SnOx/Au/PEDOT:PSS/NB PVK/C60/SnOx/Ag) and 25.1% (Glass/IO:H/NiOx/Me-4PACz/WB PVK/PCBM/PEI/ALD-SnOx/ITO/NiOx/Me-4PACz/IB PVK/C60/ALD-SnOx/Au/PEDOT:PSS/NB PVK/C60/ALD-SnOx/Ag).
Selecting the appropriate bandgap will be particularly important for the triple junction APTSCs as three different absorbers are needed (wide/intermediate/narrow bandgap). For example, publications demonstrated triple junction all-perovskite solar cells with bandgaps, as shown in Table 1. (Fig. 7d–f). Furthermore, the best stability of triple junction all-perovskite solar cells is currently 420 h, retaining 80% of their initial efficiency under illuminating and room temperature conditions from the literature. Hence, this triple junction field has promising potential for development of highly efficient and stable devices.33–37
Table 1 The bandgap data of triple junction perovskite solar cells
PCE (%) |
Wide bandgap (eV) |
Intermediate bandgap (eV) |
Narrow bandgap (eV) |
6.735 |
1.94 |
1.57 |
1.34 |
16.837 |
1.99 |
1.6 |
1.22 |
20.136 |
1.73 |
1.57 |
1.23 |
24.333 |
2 |
1.6 |
1.22 |
25.134 |
1.97 |
1.61 |
1.25 |
Table 2 The chronological database of APTSCs
Device structure |
Junction |
Method |
WBb PCE (%) |
WB (eV) |
IBc PCE (%) |
IB (eV) |
NBd PCE (%) |
NB (eV) |
Tandem PCE (%) |
Active area (mm2) |
Terminal |
Substrate |
Accepted date (Ref.) |
PVK: perovskite.
WB: wide bandgap.
IB: intermediate bandgap.
NB: narrow bandgap.
RI: rear irradiance.
Certified device (marked in WB PCE (%), NB PCE (%) and tandem PCE (%)).
Module (marked in the active area).
Bandgap information (WB, IB or NB) was extracted manually from EQE or IPCE graphs.Accepted data: if there is no accepted date, the date of “version of record online” was used.Ref. 182 paper is not the accepted paper. Hence the submission date was used instead of the accepted date. |
Glass/FTO/TiO2/WB PVKa/PTAA/PCBM/NB PVK/PEDOT:PSS/ITO |
Double |
Li-TFSI + tBP in HTM (P3HT or PTAA) |
8.4 |
2.25 |
— |
— |
18 |
1.55 |
10.8 |
9.6 |
2T |
Glass |
Oct 2015172 |
Glass/FTO/c-TiO2/m-TiO2/WB PVK/Spiro-MeOTAD/PEDOT:PSS/PEI/PCBM:PEI/NB PVK/transparent hc-PEDOT:PSS |
Double |
Novel CRL |
11.7 |
N/A |
— |
— |
11.4 |
N/A |
7 |
4–10 |
2T |
Glass |
Dec 2015174 |
WB: glass/ITO/NiOx/WB PVK/PCBM/bis-C60/ITO |
Double |
Solvent washing and compositional engineering |
14.19 |
1.57h |
— |
— |
14.35 |
1.33 |
19.08 |
3.14 or 10 |
4T |
Glass |
Aug 2016143 |
NB: glass/ITO/PEDOT:PSS/NB PVK/PCBM/bis-C60/Ag |
Glass/ITO/NiO/WB PVK/ZTO/SnO2/PCBM/PEDOT:PSS/NB PVK/C60/BCP/Ag |
Double |
Bandgap optimisation |
9.8 |
1.8 |
— |
— |
14.1 |
1.2 |
16.9 |
20 |
2T |
Glass |
Oct 2016153 |
20.1 |
20 |
4T |
13.3 |
100 |
2T |
16 |
100 |
4T |
Glass/ITO/TiO2/IPH/WB PVK/TaTm/TaTm:F6-TCNNQ/C60:Phlm/C60/NB PVK/TaTm/TaTm:F6-TCNNQ/Au |
Double |
Doped organic semiconductors |
10.7 |
2 |
— |
— |
19.4 |
1.55 |
15.6 |
6 |
2T |
Glass |
Dec 2016176 |
WB: glass/FTO/SnO2/C60-SAM/WB PVK/Spiro-MeOTAD/MoOx/Au/MoOx |
Double |
Optimisation of PVK thickness |
18.3 |
1.58 |
— |
— |
17.6 |
1.25 |
21.2 |
8.5 |
4T |
Glass |
Jan 2017149 |
NB: glass/ITO/PEDOT:PSS/NB PVK/C60/BCP/Ag |
17.01f |
Glass/ITO/NiO2/WB PVK/C60/Bis-C60/Sputtered ITO/PEDOT:PSS/NB PVK/IC60BA/Bis-C60/Ag |
Double |
Indene-C60 bis-adduct (IC60BA) interface layer |
12.5 |
1.82 |
— |
— |
14.4 |
1.22 |
18.4 |
10 |
2T |
Glass |
Jul 2017181 |
Glass/FTO/c-TiO2/m-TiO2/WB PVK/Spiro-MeOTAD/PEDOT:PSS/C60/NB PVK/Spiro-MeOTAD/Au |
Double |
Solution-processed organic charge recombination layer |
5.2 |
2.3 |
— |
— |
12.7 |
1.55 |
5.1 |
N/A |
2T |
Glass |
Dec 2017175 |
WB: glass/FTO/SnO2/C60-SAM/WB PVK/Spiro-MeOTAD/MoOx/ITO |
Double |
MoOx/ITO transparent electrodes |
15.7 |
1.75 |
— |
— |
17.5 |
1.25 |
23.1 |
10 |
4T |
Glass |
Jan 2018179 |
NB: glass/ITO/PEDOT:PSS/NB PVK/C60/BCP/Ag |
ITO/PTAA/WB PVK/C60/SnO2/ITO/PEDOT:PSS/NB PVK/C60/BCP/Ag |
Double |
Compositional engineering using Cs+ replacing MA+ |
14.6 |
1.76 |
— |
— |
13.1 |
1.14 |
19.1 |
N/A |
2T |
Glass |
Aug 2018144 |
Glass/ITO/PTAA/WB PVK/C60/BCP/Ag/MoOx/ITO/PEDOT:PSS/NB PVK/C60/BCP/Ag |
Double |
Incorporation of Cl− for NB PVK |
14 |
1.75 |
— |
— |
18.1 |
1.25 |
21 |
10.5 |
2T |
Glass |
Oct 2018146 |
Glass/ITO/TiOx/PC61BM/WB PVK/ICL (PTAA/HMB-Doped PC61BM)/NB PVK/HTL/Ag/Encapsulation |
Double |
Solution-processed interconnecting layer (ICL), HTL doping |
18.29 |
1.58 |
— |
— |
15.55 |
1.26 |
18.69 |
12 |
2T |
Glass |
Oct 2018173 |
16.2 |
120 |
2T |
ITO/NiOx/WB PVK/FSIP/C60/BCP/Cu/Au/PEDOT:PSS/NB PVK/polystyrene/C60/BCP/Ag |
Double |
Thermionic emission-based interconnecting layer (PSIP) |
12.32 |
1.83 |
— |
— |
13.61 |
1.24 |
17.9 |
10 |
2T |
Glass |
Nov 2018177 |
Glass/FTO/SnO2/PC61BM/WB PVK/Spiro-MeOTAD/PEDOT:PSS/ITO NPs/PC61BM/IB PVK/Spiro-MeOTAD/PEDOT:PSS/ITO NPs/PC61BM/NB PVK/Spiro-(TFSI)2/Ag |
Triple |
Fully solution processed triple junction tandem |
11.6 |
1.94 |
N/A |
1.57 |
11.1 |
1.34 |
6.7 |
9.19 |
2T |
Glass |
Jan 201935 |
WB: glass/ITO/PTAA/WB PVK/C60/BCP/Ag |
Double |
Guanidinium thiocyanate additive in NB PVK |
18.5 |
1.63 |
— |
— |
20.5 |
1.25 |
23.1 |
10.5 |
2T |
Glass |
Apr 2019161 |
NB: glass/ITO/PEDOT:PSS/NB PVK/C60/BCP/Ag |
25.4 |
10.5 |
4T |
Glass |
PEN/ITO or glass/ITO/polytpd/PFN-Br/WB PVK/LiF/C60/PEIE/Aluminium-doped zinc oxide/ITO/PEDOT:PSS/NB PVK/C60/BCP/Au |
Double |
Recombination layer modification and cation tuning |
19.2 |
1.7 |
— |
— |
16.5 |
1.27 |
23.1 |
5.8 |
2T |
Glass |
May 201962 |
21.3 |
5.8 |
2T |
PEN |
Glass/ITO/PTAA/WB PVK/C60/BCP/ICL (Ag/MoO3/ITO)/PEDOT:PSS/NB PVK/C60/BCP/Ag |
Double |
Chlorine incorporation bulk-passivation |
N/A |
1.75 |
— |
— |
N/A |
1.25 |
21.1 |
12 |
2T |
Glass |
Jun 2019145 |
Glass/ITO/PTAA/WB PVK/C60/ALD-SnO2/Au/PEDOT:PSS/NB PVK/C60/BCP/Cu |
Double |
Comproportionation reaction |
16.5 |
1.77 |
— |
— |
21.1 |
1.22 |
24.8f |
7.3 |
2T |
Glass |
Aug 2019157 |
22.1f |
105 |
2T |
22.3 |
105 |
2T |
Glass/ITO/poly-TPD/PFN-Br/WB PVK/LiF/C60/PEIE/Aluminium-doped zinc/NB PVK/C60/BCP/Ag |
Double |
Band alignment of ITO-PVK heterojunction |
16.6 |
N/A |
— |
— |
15.4 |
1.29 |
20.8 |
5.8 |
2T |
Glass |
Aug 2019120 |
Glass/ITO/PTAA/WB PVK/C60/SnO2/Sputtered ITO/PEDOT:PSS/PTAA/NB PVK/C60/BCP/Cu |
Double |
Cadmium ion additive in NB PVK |
16.3 |
1.8 |
— |
— |
20.3 |
1.22 |
23 |
6.84 |
2T |
Glass |
Sep 2019158 |
WB: glass/ITO/PTAA/WB PVK/C60/BCP/Ag |
Double |
Diluted PEDOT:PSS as a HTL |
19.5 |
1.6 |
— |
— |
19.58 |
1.2 |
23.26 |
6 |
4T |
Glass |
Nov 2019168 |
NB: glass/ITO/PEDOT:PSS/NB PVK/C60/BCP/Ag |
WB: glass/ITO/SnO2/WB PVK/Spiro-MeOTAD/MoO3/ITO/MgF2 |
Double |
Vacuum-assisted nucleation growth |
18.5 |
1.63 |
— |
— |
18.2 |
1.27 |
23 |
100 |
4T |
Glass |
Dec 2019147 |
NB: glass/ITO/PEDOT:PSS/NB PVK/PCBM/C60/BCP/Ag |
Glass/ITO/PTAA/WB PVK/C60/ALD-SnO2/Au/PEDOT:PSS/NB PVK/C60/BCP/Cu |
Double |
Ultra-thin 2D layer using phenethylammonium cation for NB PVK |
16.1 |
1.75 |
— |
— |
19.4 |
1.25 |
23.7 |
4.9 |
2T |
Glass |
Feb 2020165 |
18.95f |
Glass/ITO/PTAA/WB PVK/(n+) C60/(n) SnO2−x/NB PKV/C60/BCP/Cu |
Double |
Simplified tandem structure |
21.5 |
1.78 |
— |
— |
20.2 |
1.21 |
24.4 |
5.9 |
2T |
Glass |
Jun 2020178 |
22.2 |
115 |
Glass/ITO/PTAA/WB PVK/C60/ALD-SnO2/Au/NiO/PTAA/IB PVK/C60/ALD-SnO2/Au/PEDOT:PSS/NB PVK/C60/BCP/Cu |
Triple |
Triple multi-junction |
10.4 |
1.99 |
19 |
1.6 |
20.1 |
1.22 |
20.1 |
4.9 |
2T |
Glass |
Aug 202036 |
Glass/ITO/NiO/VNPB/WB PVK/C60/ALD-SnO2/Au/PEDOT:PSS/NB PVK/C60/ALD-SnO2/Cu |
Double |
Surface-anchoring zwitterionic molecules with formamidine sulfinic acid (FSA) |
15.9 |
1.77 |
— |
— |
21.7 |
1.22 |
25.6 |
4.9 |
2T |
Glass |
Sep 202053 |
24.2f |
100 |
2T |
20.7f |
21.4 |
1200 |
2T |
Triple junction: Glass/ITO/PTAA/WB PVK/C60/SnO2/Au/PEDOT:PSS/PTAA/IB PVK/C60/SnO2/Au/PEDOT:PSS/NB PVK/C60/BCP/Ag |
Triple |
Versatile two-step solution process |
8.1 |
1.73 |
16.5 |
1.57 |
14.6 |
1.23 |
16.8 |
6.76 |
2T |
Glass |
Sep 202037 |
Double junction: Glass/ITO/PTAA/WB PVK/C60/SnO2/Au/PEDOT:PSS/NB PVK/C60/BCP/Ag |
Double |
19.2 |
WB: glass/ITO/np-SnO2/WB PVK/Spiro-MeOTAD/MoOx/ITO/MgF2 |
Double |
Triple cation |
18 |
1.65 |
— |
— |
18.2 |
1.26 |
23.6 |
10.5 |
4T |
Glass |
Oct 2020154 |
NB: glass/ITO/PTAA/NB PVK/PCBM/C60/BCP/Ag |
Glass/ITO/VNPB/WB PVK/C60/ALD-SnO2/Au/PEDOT:PSS/NB PVK/C60/BCP/Cu |
Double |
N
4,N4'-di(naphthalen-1-yl)-N4,N4'-bis(4-vinylphenyl)biphenyl-4,4'-diamine (VNPB) as a HTL |
16.7 |
1.77 |
— |
— |
15.9 |
1.16 |
24.9 |
4.9 |
2T |
Glass |
Jun 2021169 |
WB: glass/IO:H front electrode/np-SnO2/WB PVK/Spiro-MeOTAD/MoOx/IZO rear electrode/MgF2 |
Double |
Hydrogen-doped indium oxide In2O3:H (IO:H) front electrode |
19 |
1.62 |
— |
— |
17.3 |
1.26 |
24.8 |
N/A |
4T |
Glass |
Sep 2021180 |
NB: glass/IO:H front electrode/NB PVK/PCBM/C60/BCP/Ag |
Glass/ITO/W-NiOx/WB PVK/C60/ALD-SnO2/ITO NCs/E-NiOx/NB PVK/C60/ALD-SnO2/Cu |
Double |
Metal oxides for HTLs and ETLs. E-NiOx (nanocrystals NiOx in ethanol) and W-NiOx (nanocrystals NiOx in water) |
16.5 |
1.8h |
— |
— |
17.4 |
1.24h |
23.5 |
4.9 |
2T |
Glass |
Oct 2021171 |
WB: glass/IO:H/SnO2/WB PVK/Spiro-MeOTAD/MoOx/IZO/MgF2 |
Double |
Interfacial engineering using indene-C60-propionic acid hexyl ester (IPH) |
19 |
1.63 |
— |
— |
18.6 |
1.26 |
24.8 |
10.5 |
4T |
Glass |
Dec 2021155 |
NB: glass/ITO/PTAA/NB PVK/IPH/C60/BCP/Ag |
Glass/ITO/NiO/VNPB/WB PVK/C60/ALD-SnO2/Au/PEDOT:PSS/NB PVK/C60/BCP/Cu |
Double |
Passivation using 4-trifluoromethyl-phenylammonium (CF3-PA) |
17.3 |
1.76 |
— |
— |
22.2 |
1.22h |
26.7 |
4.9 |
2T |
Glass |
Dec 2021163 |
26.4f |
Glass/ITO/NiO/VNPB/WB PVK/C60/ALD-SnO2/Au/PEDOT:PSS/NB PVK/C60/ALD-SnO2/Ag |
Double |
Blade coating and Cs additive |
17.2 |
1.8 |
— |
— |
19 |
1.22h |
25.1 |
4.9 |
2T |
Glass |
Apr 202256 |
22.5 |
2025g |
2T |
21.7f |
2025g |
2T |
Glass/ITO/PTAA/WB PVK/C60/ALD-SnO2/Au/PEDOT:PSS/NB PVK/C60/BCP/Cu |
Double |
Steric engineering using alloying dimethylammonium and chloride |
17.7 |
1.8 |
— |
— |
20.7 |
1.2 |
26.2 |
N/A |
2T |
Glass |
Apr 2022152 |
Glass/MeO-2PACz/WB PVK/LiF/C60/SnOx/Au/PEDOT:PSS/NB PVK/C60/BCP/Ag |
Double |
Quasi-2D with bulky organic cations phenethylammonium and guanidinium |
16.6 |
1.75 |
— |
— |
22.2 |
1.25 |
25.5 |
9 |
2T |
Glass |
May 2022103 |
24.3f |
PEN/ITO/MB-NiO/WB PVK/C60/ALD-SnO2/Au/PEDOT:PSS/NB PVK/C60/BCP/Cu |
Double |
Mixture of two hole-selective molecules (MB-NiO referred to a molecule-bridged NiO) |
16.2 |
1.75 |
— |
— |
N/A |
1.22 |
24.7 |
4.9 |
2T |
Flexible |
May 202263 |
24.4f |
4.9 |
23.5 |
105 |
MgF2/glass/IO:H/2PACz/WB PVK/LiF/C60/SnOx/ITO or Au/PEDOT:PSS/NB PVK/PCBM/C60/BCP/Cu |
Double |
Up-scaling with blade coating and vacuum deposition |
N/A |
1.78 |
— |
— |
N/A |
1.26h |
23.5 |
10 |
2T |
Glass |
May 202255 |
19.1 |
1225g |
2T |
19.8 |
243g |
2T |
18.3f |
243g |
2T |
WB: PET/ITO/SnO2/WB PVK/Spiro-MeOTAD/VOx/IMI |
Double |
Guanidinium thiocyanate additives in PVK |
9.52 |
1.71 |
— |
— |
9.27 |
1.26 |
15.3 |
5000g |
4T |
Flexible |
Jun 202254 |
NB: PET/ITO/PEDOT:PSS/NB PVK/C60/BCP/Cu |
Glass/ITO/PTAA/WB PVK/C60/SnO2/ITO/PEDOT:PSS/NB PVK/C60/BCP/Ag |
Double |
Close-space annealing |
18.58 |
1.57 |
— |
— |
21.51 |
1.25 |
25.15 |
9 |
4T |
Glass |
Jun 2022148 |
25.05 |
9 |
2T |
24.79f |
9 |
2T |
Glass/ITO/SnO2/(2D/3D)WB PVK/Spiro-MeOTAD/PEDOT:PSS/C60/NB PVK/Spiro-OMeTAD/Ag |
Double |
In situ growth using n-butylammonium bromide |
16.07 |
1.57 |
— |
— |
15.07 |
1.59 |
10.22 |
4 |
2T |
Glass |
Jun 2022164 |
Glass/ITO/PTAA/WB PVK/C60/SnO2/Au/PEDOT:PSS/NB PVK/PCBM/C60/BCP/Cu |
Double |
Hot gas-assisted blade-coating |
16.4 |
1.67 |
— |
— |
20.3 |
1.22 |
23.1 |
8 |
2T |
Glass |
Jul 202257 |
21.6 |
1430g |
2T |
WB: PEN/ITO/2PACz/PTAA/WB PVK/TEACl/PCBM/np-ZnO/IZO |
Double |
Post-treatment using 2-thiopheneethylammonium chloride (TEACl) |
15.1 |
1.77 |
— |
— |
18.2 |
1.24 |
22.6 |
9 |
4T |
Flexible |
Sep 202261 |
NB: PEN/ITO/PEDOT:PSS/NB PVK/C60/BCP/Cu |
23.8 |
9 |
2T |
2T: PEN/ITO/2PACz/PTAA/WB PVK/TEACl/PCBM/ALD-SnO2/ITO/PEDOT:PSS/NB PVK/C60/BCP/Cu |
Glass/ITO/NiO/SAM/WB PVK/C60/SnO2/Au/PEDOT:PSS/NB PVK/C60/SnO2/ITO |
Double |
Bifacial tandem |
N/A |
1.68 |
— |
— |
N/A |
1.22 |
28.51 (bifacial with RIe) |
9 |
2T |
Glass |
Sep 2022128 |
Glass/ITO/MeO-2PACz/WB PVK/C60/Au/SnOx/PEDOT:PSS/NB PVK/C60/BCP/Cu |
Double |
Dual interface treatment using MeO-2PACz self-assembled monolayer (SAM) and ethylenediammonium diiodide |
17.8 |
1.76 |
— |
— |
19.6 |
1.28 |
24.1 |
20 |
2T |
Glass |
Sep 2022182 |
WB: Glass/ITO/SnO2/WB PVK/Spiro-MeOTAD/MoOx/ITO NB: Glass/ITO/PEDOT:PSS/NB PVK/PCBM/BCP/Ag |
Double |
Tuning bandgap and fully inorganic PVK film of WB and NB |
11.26 |
1.98 |
— |
— |
13.8 |
1.39 |
18.07 |
10 |
4T |
Glass |
Oct. 2022232 |
Glass/ITO/MeO-2PACs/WB PVK/C60/ALD-SnO2/graphene oxide/PEDOT/resin/NB PVK/C60/ALD-SnO2/ITO |
Double |
Bifacial tandem |
N/A |
1.65 |
— |
— |
19.4 |
1.21 |
24.4 (mono) |
8 |
2T |
Glass |
Oct 2022130 |
29.3 (bifacial with RI) |
Glass/ITO/NiO/VNPB/WB PVK/C60/ALD-SnO2/ITO NCs/NB PVK/C60/ALD-SnO2/Cu |
Double |
Fully FA A-site ion based perovskite film |
17.3 |
1.77 |
— |
— |
21 |
1.26 |
26.3 |
4.9 |
2T |
Glass |
Oct 2022121 |
Glass/FTO/PEDOT:PSS/NB PVK/C60/n-C60/p-TaTm/TaTm/WB PVK/C60/BCP/ITO PLD/Ag/ALD Al2O3 |
Double |
Vacuum-deposited organic charge recombination layer |
12.7 |
1.68 |
— |
— |
17.5 |
1.26 |
20.1 |
N/A |
2T |
Glass |
Nov 2022129 |
Glass/ITO/NiOx/Me-4PACz/WB PVK/C60/ALD-SnOx/Au/PEDOT:PSS/NB PVK/C60/ALD-SnOx/Ag |
Double |
Passivation using 1,3-propane diammonium |
20.2 |
1.79 |
— |
— |
21.5 |
1.22 |
27.4 |
4.9 |
2T |
Glass |
Nov 2022156 |
19.3f |
26.29f |
4.9 |
Glass/ITO/SAM/CuBr/WB PVK/CuBr/LiF/C60/ALD-SnO2/Au/PEDOT/NB PVK/C60/BCP/Cu |
Double |
PSS-free PEDOT |
20.5 |
1.75 |
— |
— |
20.1 |
1.25 |
21.5 |
7.06 |
2T |
Glass |
Nov 2022167 |
WB: PEN/ITO/2PACz/WB PVK/PCBM/ZnO/IZO |
Double |
SnF2 additive |
15.2 |
1.78 |
— |
— |
18.5 |
1.24 |
23.1 |
9 |
4T |
Flexible |
Jan 202360 |
NB: PEN/ITO/PEDOT:PSS/NB PVK/C60/BCP/Cu |
N/A |
Double |
Tris(2,4-pentanedionato)gallium additive |
17.03 |
1.74 |
— |
— |
20.76 |
1.25 |
23.14 |
8 |
4T |
Glass |
Mar 2023162 |
6.11 (filtered) |
Glass/ITO/2PACz/WB PVK/C60/SnO2/ITO/PEDOT:PSS/CysHCl-D&P NB PVK/C60/BCP/Cu |
Double |
Passivation using cysteine hydrochloride (CysHCl) |
17.48 |
1.77 |
— |
— |
22.15 |
1.27 |
25.7f |
5.76 |
2T |
Glass |
Mar 202326 |
Glass/ITO/PTAA/PFMBr/WB PVK/C60/SnO2/ITO/PEDOT:PSS/NB PVK/C60/BCP/Cu |
Double |
PbCl2 and phenethylammonium chloride (PMACl) additive |
20.22 |
1.73 |
— |
— |
21.97 |
1.25 |
26.68 |
9 |
2T |
Glass |
Mar 202328 |
Glass/ITO/NiO/SAM/WB PVK/C60/ALD-SnO2/Au/PEDOT:PSS/NB PVK/C60/BCP/Cu |
Double |
Passivation using 4-(Trifluoromethyl) phenethylammonium |
18.5 |
1.78 |
— |
— |
21.7 |
1.22 |
25.6 |
4.9 |
2T |
Glass |
Mar 2023131 |
WB: ITO/MeO-2PACz/WB PVK/C60/ALD-SnO2/ITO |
Double |
Antimony potassium tartrate additive |
20.35 |
1.67 |
— |
— |
20.8 |
1.24h |
26.3 |
11.88 |
4T |
Glass |
Mar 202329 |
NB: ITO/PEDOT:PSS/NB PVK/C60/BCP/Cu |
7.6 (filtered) |
Glass/Cu/ITO/PEDOT:PSS/NB PVK/C60/ALD-SnO2/ITO/NiO/SAM/C60/ALD-SnO2/IZO/Anti-reflection layer |
Double |
GuaBF4 additive |
19.1 |
1.77 |
— |
— |
19.6 |
1.22 |
25.3 |
5.29 |
2T |
Glass |
Mar 2023132 |
24.1 |
5.29 |
2T |
Flexible (Cu-PEN) |
20.3 |
5.29 |
2T |
Flexible (Cu foil) |
Glass/ITO/novel HTL/WB PVK/C60/SnO2/IZO/NB PVK/C60/SnO2/Cu |
Double |
hole-selective layer using self-assembled monolayer of (4-(7H-dibenzo[c,g]carbazol-7-yl)butyl)phosphonic acid |
18.22 |
1.77 |
— |
— |
21.27 |
1.25 |
27 |
104.4 |
2T |
Glass |
Mar 202331 |
26.4f |
Glass/ITO/NiOx/Me-4PACz/WB PVK/PEAI-EDAI2/PCBM/PEIE/SnOx/ITO/NiOx/Me-4PACz/IB PVK/PEAI-EDAI2/PCBM/PEIE/SnOx/Au/PEDOT:PSS/NB PVK/C60/SnOx/Ag |
Triple |
Rb/Cs mixed cation inorganic perovskite |
13.4 |
2 |
N/A |
1.6 |
N/A |
1.22 |
24.3 |
4.9 |
2T |
Glass |
Mar 202334 |
23.2f |
Glass/ITO/PTAA/4,3BuPACz/WB PVK/C60/ALD-SnO2/IZO/PEDOT:PSS/NB PVK/C60/BCP/Ag |
Double |
PTAA/monomolecular substrate |
16.57 |
1.77 |
— |
— |
N/A |
1.25h |
25.24 |
10 |
2T |
Glass |
Mar 2023170 |
Glass/ITO/2F/WB PVK/C60/ALD-SnO2/IZO/PEDOT:PSS/2F/NB PVK/C60/ALD-SnO2/Cu |
Double |
hole selective contact using 4-(7-(4-(bis(4-methoxyphenyl)amino)-2,5-difluorophenyl)benzo[c][1,2,5]thiadiazol-4-yl) benzoic acid (2F) |
19.33 |
1.77 |
— |
— |
23.24 |
1.25 |
27.22 |
5.76 |
2T |
Glass |
May 202330 |
19.09f |
26.3f |
Glass/ITO/2PACz/WB PVK/C60/SnOx/Au/PEDOT:PSS/NB PVK/C60/BCP/Cu |
Double |
Natural SnOx doping |
N/A |
1.78 |
— |
— |
22.16 |
1.25 |
26.01 |
9.48 |
2T |
Glass |
May 202332 |
Glass/ITO/NiO/SAM/WB PVK/C60/ALD-SnO2/Au/PEDOT:PSS/NB PVK/full-lead WB/C60/BCP or ALD-SnO2/Cu |
Double |
3D/3D bilayer |
18.6 |
1.78 |
— |
— |
23.8 |
1.25 |
28.5 |
4.9 |
2T |
Glass |
May 20235 |
28f |
Glass/ITO/2PACz-SAM/WB PVK/LiF/C60/SnO2/Au/PEDOT:PSS/NB PVK/C60/PEIE/Ag |
Double |
Carbazole moiety-based ([2-(9H-carbazol-9-yl)ethyl]phosphonic acid) self-assembled monolayer treatment (2PACz-SAM) for WB PVK |
17.62 |
1.77 |
— |
— |
18 |
1.24 |
24.66 |
9.3 |
2T |
Glass |
Sep 2023183 |
16.72f |
Glass/IO:H/NiOx/Me-4PACz/WB PVK/PCBM/PEI/ALD-SnOx/ITO/NiOx/Me-4PACz/IB PVK/C60/ALD-SnOx/Au/PEDOT:PSS/NB PVK/C60/ALD-SnOx/Ag |
Triple |
Diammonium halide salt and propane-1,3-diammonium iodide |
15.5 |
1.97 |
21.3 |
1.36 |
20.1 |
1.25 |
25.1 |
4.9 |
2T |
Glass |
Oct 202333 |
23.8f |
Glass/ITO/NiOx/Me-4PACz/WB PVK/C60/ALD-SnO2/Au/PEDOT:PSS/NB PVK/C60/ALD-SnO2/Ag |
Double |
Potassium hypophosphite additive into the wide bandgap perovskite solution |
20.06 |
1.79 |
— |
— |
21.73 |
1.25 |
26.08 |
7.8 |
2T |
Glass |
Nov 2023184 |
WB: glass/ITO/DCB-BPA/WB PVK/C60/SnO2/IZO |
Double |
Self-assembled monolayer of (4-(5,9-dibromo-7H-dibenzo[c,g]carbazo-7-yl)butyl)phosphonic acid (DCB-BPA) as the hole-selective layer |
18.88f |
1.77 |
— |
— |
20.53 |
1.25 |
26.9 |
9.75 |
4T |
Glass |
Nov 2023185 |
NB: glass/PEDOT:PSS/NB PVK/C60/BCP/Cu |
WB: glass/ITO/MeO-2PACz/WB PVK/C60/SnO2/ITO |
Double |
Dodecyl-benzene-sulfonic acid additive in wide bandgap perovskite precursor solution |
22.4 |
1.66 |
— |
— |
21.24 |
1.25 |
28.06 |
7.022 |
4T |
Glass |
Nov 2023186 |
21.97f |
NB: glass/ITO/PEDOT:PSS/NB PVK/C60/BCP/Cu |
20.13 |
Glass/ITO/(4-(7H-dibenzo[c,g]carbazole-7-yl)butyl) phosphonic acid/WB PVK/C60/ALD-SnO2/ITO/Taurine/NB PVK/C60/BCP/Cu |
Double |
HTL free NB PVK using 2-aminoethanesulfonic acid |
N/A |
1.72h |
— |
— |
22.5 |
1.25 |
26.03 |
9.75 |
2T |
Glass |
Nov 2023187 |
Glass/ITO/NiOx/SAMs/WB PVK/HF-WB PVK/ALD-SnO2/Au/PEDOT:PSS/NB PVK/HF-NB PVK/ALD-SnO2/CDB/Cu |
Double |
Hybrid fullerenes comprising a mixture of fullerene, phenyl C61 butyric acid methylester, and indene-C60 bisadduct |
19 |
1.8 |
— |
— |
20.6 |
1.25 |
23.3 |
2025g |
4T |
Glass |
Nov 2023188 |
Glass/FTO/NiO2/MeO-2PACz/LiF/C60/ALD-SnO2/Au/IE-PEDOT:PSS/NB PVK/C60/PEIE/Ag |
Double |
Doping MAI-DMSO in PEDOT:PSS |
N/A |
1.77 |
— |
— |
21.28 |
1.25 |
23.52 |
17.64 |
2T |
Glass |
Nov 2023189 |
Anti-reflection foil/glass/ITO/2PACz/WB PVK/C60/SnO2/ITO/PEDOT:PSS/NB PVK/C60/PEIE/SnO2/Cu |
Double |
Piperazinium iodide surface treatment for wide bandgap perovskite and rubidium iodide additive for narrow bandgap perovskites |
20.3 |
1.8 |
— |
— |
20.6 |
1.26 |
27.5f |
12 |
2T |
Glass |
Nov 2023190 |
WB: glass/ITO/PTAA/WB PVK/C60/ZnO |
Double |
Triethanolamine borate additive in wide bandgap precursor solution |
21.55 |
1.65 |
— |
— |
21.41 |
1.25 |
26.48 |
N/A |
4T |
Glass |
Nov 2023191 |
NB: glass/ITO/PEDOT:PSS/NB PVK/C60/BCP/Ag |
7.32 (filtered) |
Glass/ITO/NiOx/Me-4PACz/WB PVK/C60/ALD-SnO2/ITO/PEDOT:PSS/NB PVK/C60/BCP/Ag |
Double |
Surface reaction layer with ethanediamine dihydroiodide |
23.1 |
1.67 |
— |
— |
22.1 |
1.25 |
26.1 |
7 |
2T |
Glass |
Dec 2023192 |
22.95f |
1.67 |
19.7 |
1.75 |
18.81f |
1.75 |
Glass/ITO/NiOx/MeO-2PACz/WB PVK/C60/SnOx/Au/PEDOT:PSS/NB PVK/C60/BCP/Ag |
Double |
Chloromethylphosphonic acid additive in tin–lead perovskites |
19.6 |
1.79 |
— |
— |
21.6 |
1.25 |
27.3 |
4.2 |
2T |
Glass |
Dec 2023193 |
26.96f |
Glass/ITO/NiO/VNPB/Me-4PACz/WB PVK/C60/ALD-SnO2/Au/PEDOT:PSS/NB PVK/C60/ALD-SnO2/Cu |
Double |
Aminoacetamide hydrochloride additive in Sn–Pb perovskite film |
17.9 |
1.8 |
— |
— |
21.4 |
1.25 |
26.8 |
10 |
2T |
Glass |
Dec 202358 |
24.9 |
2000g |
24.5f |
2025g |
23.8 |
6400g |
WB: glass/ITO/MeO-2PACz/WB PVK/C60/SnO2/ITO |
Double |
Blade coated perovskite and post-treatment with 1,3-propane-diammonium iodide and formamidinium iodide |
18.71 |
1.77 |
— |
— |
9.3 (filtered) |
1.25 |
27.64 |
102 |
4T |
Glass |
Jan 2024194 |
NB: glass/ITO/PEDOT:PSS/NB PVK/C60/BCP/Cu |
Substrate/ITO/NiOx/N719/WB PVK/C60/ALD-SnO2/Au/PEDOT:PSS/NB PVK/C60/BCP/Cu |
Double |
Methylene diphenyl diisocyanate polyurethane and PJ71 in wide and narrow bandgap perovskite solution |
17.6 |
1.8 |
— |
— |
20.9 |
1.2 |
26.1 |
9 |
2T |
Glass |
Jan 2024195 |
22.2 |
9 |
2T |
PEN |
11.6 |
9 |
2T |
Silk-derived substrate |
Glass/ITO/NiOx/Me-4PACz/WB PVK/C60/ALD-SnOx/1nm Au/PEDOT:PSS/NB PVK/C60/ALD-SnOx/Ag |
Double |
Oleic acid treatment for Sn–Pb perovskite film |
20 |
1.79 |
— |
— |
23 |
1.24 |
27.3 |
4.9 |
2T |
Glass |
Jan 2024196 |
26.4f |
Glass/ITO/Me-4PACz/WB PVK/C60/SnO2/Au/PEDOT:PSS/NB PVK/C60/SnO2/Ag |
Double |
Tin(II) oxalate additive in tin–lead perovskite solution |
N/A |
N/A |
— |
— |
23.36 |
1.25 |
27.56 |
9 |
2T |
Glass |
Jan 2024197 |
Glass/ITO/Me-4PACz/WB PVK/SEBr/LiF/C60/ALD-SnO2/Au/PEDOT:PSS/NB PVK/C60/BCP/Ag |
Double |
Surface treatment using S-ethylisothiourea hydrobromide (SEBr) for WB PVK |
22.47 |
1.67 |
— |
— |
N/A |
1.25 |
27.1 |
5.8 |
2T |
Glass |
Jan 2024198 |
19.9 |
1.77 |
Glass/ITO/NiOx/2PACz/WB PVK/C60/SnO2/PEDOT:PSS/NB PVK/C60/BCP/Ag |
Double |
Surface treatment using the solution combined 3-fluorophenethylammonium iodide and ethane-1,2-diammonium iodide |
19.31f |
1.77 |
— |
— |
21.39 |
1.25 |
27.04f |
4.2 |
2T |
Glass |
Feb 2024199 |
Glass/ITO/PTAA/WB PVK/C60/ALD-SnO2/Au/PEDOT:PSS/NB PVK/C60/BCP/Ag |
Double |
Benzyl viologen post-treatment of narrow bandgap perovskites |
17.83 |
1.78 |
— |
— |
22.58 |
1.25 |
26.33 |
6 |
2T |
Glass |
Feb 2024200 |
WB: Glass/ITO/NiOx/Me-4PACz/WB PVK/C60/SnO2/ITO |
Double |
Octane-1,8-diamine dihydroiodide additive in wide bandgap perovskite solution |
20.06 |
1.67 |
— |
— |
22.75 |
1.25 |
28.35 |
100 |
4T |
Glass |
Mar 2024201 |
NB: glass/ITO/PEDOT:PSS/NB PVK/C60/BCP/Cu |
8.29 (filtered) |
Glass/ITO/NiOx/2PACz/WB PVK/C60/ALD-SnO2/ITO nano crystals/PEDOT:PSS/NB PVK/C60/SnO2/Cu |
Double |
2D passivation using 2-(4-fluorophenyl)ethylamine hydroiodide on WB PVK |
19.4 |
1.78 |
— |
— |
21.5 |
1.22 |
27 |
6.84 |
2T |
Glass |
Apr 2024202 |
WB: glass/ITO/PTAA/WB PVK/C60/PEI/ITO |
Double |
Polyethylenimine (PEI) for high energy sputtered ITO |
19.17 |
1.66 |
— |
— |
22.1 |
1.24 |
26.89 |
4 |
4T |
Glass |
Apr 2024203 |
NB: glass/ITO/PEDOT:PSS/NB PVK/C60/BCP/Ag |
18.09f |
7.72 (filtered) |
WB: glass/ITO/MeO-2PACz/WB PVK/PDAI2/C60/ALD-SnO2/ITO/Ag |
Double |
Surface passivation using 1,3-propane-diammonium iodide (PDAI2) for WB PVK |
20.11 |
1.68 |
— |
— |
21.26 |
1.21h |
28.07 |
11.88 |
4T |
Glass |
Apr 2024204 |
NB: glass/ITO/PEDOT:PSS/NB PVK/C60/BCP/Cu |
7.96 (filtered) |
Table 3 The database of simulated APTSCs
Device structure |
Junction |
Method |
Ideal Voc (V) |
Ideal Jsc (mA cm−2) |
Ideal FF (%) |
Ideal PCE (%) |
Type |
Year (Ref.) |
2-junction: MgF2/glass/ITO/NiOx/WB PVK 1.5–2 eV/C60/SnO2/ITO/PEDOT:PSS/NB PVK (0.9–1.35 eV)/C60/Ag |
Double |
Bandgap optimisation of PVK absorber layer |
2.17 |
18.3 |
84 |
33.4 |
2T |
2017205 |
3-junction: MgF2/glass/ITO/NiOx/WB PVK (1.9–2.3 eV)/C60/SnO2/ITO/NiOx/IB PVK (1.5–1.9 eV)/C60/SnO2/ITO/PEDOT:PSS/PVK (1.22 eV)/C60/Ag |
Triple |
3.54 |
12 |
86 |
36.6 |
2T |
NiO/WB PVK/PCBM/recombination layer/PEDOT:PSS/NB PVK/C60 |
Double |
Bandgap and thickness optimisation of PVK absorber layer and study of contact energy levels, charge carrier mobility, and transport layer doping |
N/A |
N/A |
N/A |
36.6 |
2T |
2019206 |
WB: NiO/Cs2AgBi0.75Sb0.25Br6 |
Double |
Thickness optimisation of PVK absorber layer |
1.83 |
14.9 |
63.57 |
17.35 |
4T |
2020209 |
NB: PEDOT:PSS/FACsPb0.55Sn0.5I3/C60/BCP |
WB: Spiro-MeOTAD/Cs2AgBi0.75Sb0.25Br6/PCBM/ZnO |
Double |
Thickness optimisation of PVK absorber layer |
1.94 |
15.55 |
68.48 |
24.86 |
4T |
2020210 |
NB: Cu2O/CH3NH3SnI3/ZnO |
FTO/ZnO/CH3NH3GeI3/p+/n+/FAMASnGeI3/Cu2O/Au |
Double |
Thickness optimisation of PVK absorber layer and the study of influence of defect density on photovoltaic performance |
1.07 |
28.36 |
84.46 |
26.72 |
2T |
2020211 |
Glass/ITO/NiOx/WB PVK/SnO2/PCBM/ITO/PEDOT:PSS/NB PVK/C60/Ag |
Double |
Thickness optimisation of layer and optical optimisation considering materials |
N/A |
N/A |
N/A |
37 |
2T |
2020214 |
2T: glass/FTO/PCBM/WB PVK CsSn0.5Ge0.5I3 (1.5 eV)/Spiro-MeOTAD/recombination layer/TiO2/NB PVK CsSnI3 (1.3 eV)/PTAA/Au |
Double |
Thickness optimisation of PVK absorber layer |
WB: 0.85 |
21.22 |
71.18 |
18.32 |
2T |
2021212 |
4T: WB: glass/PCBM/WB CsSn0.5Ge0.5I3 (1.5 eV)/Spiro-MeOTAD |
NB: 0.35 |
WB: 25.49 |
WB: 73.36 |
Sum: 19.86 |
4T |
NB: TiO2/NB CsSnI3 (1.3 eV)/PTAA |
Sum: 1.21 |
NB: 18.54 |
NB: 61.12 |
TiO2/MAGeI3/Spiro-MeOTAD/ITO/FTO/TiO2/FASnI3/Spiro-MeOTAD |
Double |
Thickness optimisation of PVK absorber layer |
2.63 |
14.6 |
80 |
30.85 |
2T |
2021213 |
N/A |
Double |
Thickness optimisation of transparent electrode layer |
N/A |
N/A |
N/A |
24.4 |
2T |
2021215 |
Glass/FTO/ZnOS/CsPbIBr2/GuAlO2/ITO/TiO2/MAPbI3/Spiro-MeOTAD/Au |
Double |
Thickness optimisation of PVK absorber layer and study of interface defects |
2.6 |
12.21 |
86.42 |
27.4 |
2T |
2021207 |
ITO/Cu2O/WB PVK FA0.8Cs0.2Pb(I0.7Br0.3)3/PCBM/SnO2/ITO/PEDOT:PSS/NB PVK (FASnI3)0.6(MAPbI3)0.4:Cl/PCBM/SnO2/Ag |
Double |
Thickness optimisation of various transport layers |
2.05 |
18.3 |
86.23 |
32.3 |
2T |
2022216 |
WB: ITO/TiO2/WB MAGeI3/Spiro-MeOTAD/ITO/MoOx |
Double |
Study regarding buffer layer and anti-reflection layer as well as nano texture pattern |
WB: 1.7 |
WB: 8.63 |
WB: 92 |
WB: 13.5 |
4T |
2022217 |
NB: ITO/TiO2/NB MASnI3/Spiro-MeOTAD/Ag |
NB: 0.93 |
NB: 23.83 |
NB: 75 |
NB: 16.64 |
PET (flexible) substrate |
Sum: 30.1 |
TiO2/WB PVK/Spiro-MeOTAD/C60 & IC60BA/NB PVK/PEDOT:PSS |
Double |
Optimisation of the transport layers and thickness of PVK absorber layers |
1.95 |
15.21 |
74.09 |
21.97 |
2T |
2022218 |
Glass/ITO/NiO/VNPB/WB PVK (1.77 eV)/C60/ALD-SnO2/Au 1 nm/PEDOT:PSS/NB (1.22 eV) PVK/C60/ALD-SnO2/Cu |
Double |
Thickness optimisation of PVK absorber layers and research regarding trap density and carrier mobilities |
N/A |
N/A |
N/A |
>30 |
2T |
2022219 |
2T: Antirefelction coating (ARC)/ITO/NiO/WB PVK/SnO2/ITO/PEDOT:PSS/NB PVK/C60/Ag |
Double |
Researching all-inorganic based-APTSCs |
WB: 1.37 |
WB: 18.05 |
WB: 84.64 |
WB: 20.91 |
4T |
2023220 |
NB: 9.54 |
4T WB: Antireflection coating/ITO/NiO/WB PVK/SnO2/ITO |
NB: 0.81 |
NB: 14.73 |
NB: 79.68 |
Sum: 30.5 |
2T |
NB: ITO/PEDOT:PSS/NB PVK/C60/Ag |
Sum: 2.16 |
16 |
80.68 |
27.86 |
|
Monofacial: ARC/glass/IO:H/WB PVK/C60/SnO2/ITO/PEDOT/NB PVK/PCBM/C60/Ag |
Double |
Monofacial (MF) and bifacial (BF) modelling study |
2.25 (MF) |
17.6 (MF) |
81 (MF) |
31.9 (MF) |
2T (MF) |
2023221 |
Bifacial: ARC/glass/IO:H/WB PVK/C60/SnO2/ITO/PEDOT/NB PVK/PCBM/C60/ITO/encapsulation/glass/ARC |
2.25 (BF) |
17.0 (BF) |
81 (BF) |
30.8 (BF) |
2T (BF) |
ITO/SnO2/PFN-Br/WB PVK (1.75 eV)/Cu2O/ITO/SnO2/PCBM/NB PVK (1.25 eV)/PEDOT:PSS/Ag |
Double |
Beyond 2V in APTSCs |
WB: 0.804 |
WB: 18 |
WB: 87.61 |
WB: 19.63 |
2T |
2023222 |
NB: 2.049 |
NB: 18 |
NB: 84.21 |
NB: 12.19 |
Sum: 2.05 |
Sum: 18 |
Sum: 86.3 |
Sum: 31.8 |
LiF/PET/ITO/NiOx/WB PVK/C60/SnO2/ITO/PEDOT:PSS/NB PVK/C60/SnO2/Ag |
Double |
Flexible APTSCs |
2.0328 |
18.38 |
93.21 |
34.83 |
2T |
2023223 |
MgF2/FTO/TiO2/WB PVK (MAGeI3: 1.9 eV)/Spiro-MeOTAD/MoOx/IOH/TiO2/NB PVK (MASnI3: 1.3 eV)/Spiro-MeOTAD/Au |
Double |
Lead free perovskite and |
2.71 |
14.06 |
87 |
33.14 |
2T |
2024224 |
thickness optimisation |
ITO/SnO2/C60/PCBM/WB PVK(1.99 eV)/Me-4PACz/IB PVK(1.6 eV)/C60/PCBM/ITO/Spiro-MeOTAD/NB PVK(1.2 eV)/PCBM/C60 |
Triple |
Thickness optimisation |
3.76 |
10.7 |
69 |
26.24 |
2T |
2024225 |
WB: FTO/TiO2/WB PVK (MAGeI3: 1.9 eV)/Au |
Double |
HTL free, non-toxic perovskite and |
1.3681 |
15.85 |
75.95 |
25.69 |
4T |
2024226 |
NB: FTO/ZnO/NB PVK (FASnI3: 1.4 eV)/Au |
thickness optimisation |
ITO/NiOx/WB PVK/ZnO/NB PVK (CuO/Cu/Al2O3)/SnO2/Ag |
Double |
Three-terminal |
WB: 1.34 |
WB: 16.05 |
WB: 82.04 |
WB: 17.64 |
3T |
2024227 |
NB: 0.806 |
NB: 21.75 |
NB: 82.83 |
NB: 14.52 |
Sum: 2.146 |
Sum: N/A |
Sum: N/A |
Sum: 32.16 |
WB: FTO/TiO2/WB PVK (CsGeI3: 1.6 eV)/Spiro-MeOTAD/Au |
Double |
Lead free perovskite and |
2.12 |
16.71 |
85.87 |
30.42 |
4T |
2024228 |
NB: FTO/ZnO/NB PVK (FASnI3: 1.41 eV)/Spiro-MeOTAD/Au |
thickness optimisation |
WB: TiO2/WB PVK (MAPbI3)/Cu2O |
Double |
Thickness optimisation and |
1.68 |
24.6 |
79.39 |
32.74 |
4T |
2024229 |
NB: ZnO/NB PVK (MASnI3)/Cu2O |
effect of defect density |
6. Challenges and solutions for APTSCs
PSCs have rapidly developed efficiency and stability. The latest research has demonstrated that APTSCs showed efficiencies higher than single-junction PSCs. However, in APTSCs, the stability-related degradation issue still remains a challenge, i.e., the phase transition from the original crystal structure to the constituent components or a side phase caused by heat, freezing, moisture, or illumination. Herein, various methods were described on how APTSCs accelerated efficiency and stability. Furthermore, we detailed recent research trends in comprehensive summary graphs and tables (Fig. 1a–d, Table 2 and Table S1, ESI†).
6.1. Perovskite absorber layers
The perovskite absorber layer is among the most challenging to modify in the APTSC architecture, as it is the core layer directly correlated to efficiency and stability. For example, Sn-based perovskites generally used for achieving narrow bandgaps have poor moisture stability due to the oxidation of Sn2+ to Sn4+. Another example is that many defects exist on the perovskite surface area, which may cause non-radiative recombination. Additionally, wide bandgap perovskites have a Voc loss challenge.
6.1.1. Crystal growth control.
Crystal growth control is crucial for the device performances. The crystal nuclei originate from particles such as organic molecules or ions in the perovskite precursor solution. These particles move randomly in a perovskite precursor solution, forming (statistically and at a low percentage) clusters, which typically disappear rapidly in an unsaturated solution system. If the perovskite precursor is oversaturated, the seed crystal from clusters can grow and exceed the critical seed size to trigger crystal growth.133
The LaMer mechanism and Ostwald ripening are well-established theories regarding crystal growth. The LaMer mechanism consists of three steps. The first step is to increase the concentration of the solution until a critical point. The next step shows rapid nucleation and crystal growth formation once the concentration is oversaturated, which means crossing a certain energy barrier. Meanwhile, the concentration will start reducing. If the concentration of the solution is sufficiently low, the nucleation starts reducing. In the final step, the diffusion in the solution dominates.134 As another crystal growth model, Ostwald ripening occurs when small particles dissolve into larger particles due to the high surface energy and high solubility of small particles.135–137 Especially, some perovskite studies applied a digestive ripening model theory, which is the inverse of Ostwald ripening, expecting the increase of bonds with ligands on the surface or prevention of organic component loss during thermal annealing.138–141
Generally, the small grain size is a potential challenge for efficiency and stability because grain boundaries are potentially the sites for defects, which can affect the performances through increased recombination and thus limit the open-circuit voltage.142 For these reasons enlarging the grain size is a strategy for improving the efficiency and stability of PSCs.
Dimethyl sulfoxide (DMSO) is often used as a co-solvent in the perovskite precursor due to its property of retarding crystallisation while forming intermediate complexes.89 In the 25% tin incorporated narrow bandgap perovskite precursor (MAPb0.75Sn0.25I3), the DMSO co-solvent created the intermediate phase, SnI2·3DMSO. This phase led to the production of high-quality perovskite films by slow crystallisation.143 In contrast, the volatile acetonitrile (CH3CN)/methylamine (CH3NH2) (ACN/MA) solvent-based perovskite solution process was demonstrated to have a faster drying speed than DMF.35
Methylammonium chloride (MACl) vapour surface treatment affected grain growth significantly to the micron size and can heal defects like cracks.144 Chloride (Cl−) is one of the favourable elements in the single junction perovskite composition, as it enhances the grain size. Cl− has also improved the device performance of monolithic all-perovskite solar cells by increasing the grain size and reducing the electronic disorder in the Sn–Pb-based narrow bandgap perovskite layers.145,146
The vacuum-assisted growth control (VAGC) method showed reproducible film quality by enlarging the grain size from <400 nm to 2 μm in the narrow bandgap perovskite solar cell (FA0.8MA0.2Sn0.5Pb0.5I3). The primary purpose of the VAGC method was to form large columnar grains with reduced grain boundaries perpendicularly to the thin film surfaces because the oriented columnar grains supported the fast transportation of charge carriers to the selective layers such as the ETL and HTL.147
The annealing strategy is the main factor in controlling crystallisation. The close-space annealing strategy (CSA) allowed the grain size to enlarge due to Ostwald ripening and thus enhanced the crystallinity with high-quality optoelectronic properties of APTSCs (narrow bandgap and wide bandgap).148
The thickness of the perovskite absorber can control the performance of the PSCs. For a narrow bandgap perovskite (FASnI3)0.6(MAPbI3)0.4, 620 nm perovskite thickness was suggested for optimised results.149 Thickness also increases with a higher concentration of the perovskite precursor, e.g., a 2.0 M concentration yielded a thickness of 700 nm with 13.1% PCE for a narrow bandgap perovskite (FA0.75Cs0.25Sn0.5Pb0.5I3).144
6.1.2. Bandgap and band alignment.
The bandgaps and band alignments are essential for improving performances.
Steric, additive, or compositional engineering can assist in finding suitable bandgaps. The A-site cation can fine-tune the bandgap, while the X-site as part of the metal-halide octahedron can tune the bandgap over a wider range. The dimethylammonium cation (DMA+) was reported as a promising option considering the modified tolerance factor of less than 4.18 for the Cs0.82DMA0.18PbI3 composition.150,151 DMA+ allowed the larger cation to be incorporated before forming a non-photoactive phase. Although the bulky organic molecule led to a decrease in the charge-carrier mobility, lifetime increases from <150 ns to >250 ns.62 Another work demonstrated APTSCs by alloying dimethylammonium (DMA+) and chloride (Cl−) into the perovskite precursor. Using the DMA+ and Cl− and reducing Br− in a wide bandgap perovskite, an appropriate bandgap of 1.8 eV was obtained. Simultaneously, the lattice strain and trap densities were minimised. Additionally, this method prevented light-induced halide segregation because the halides were less equimolar.152 In a study, antimony potassium tartrate (APTA) was used as an additive in the perovskite precursor expecting multi-functions not only for better band energy alignment but also for suppression of non-radiative recombination and protection against phase segregation utilising the coordination with unbonded lead and blocking the halide migration in perovskites.29 FA cation-based perovskite films manifested a narrower bandgap than the MA cation-based ones with 1.31 eV instead of 1.35 eV. The reduction of the bandgap effect was observed in the MA–Sn-based perovskite film (MAPb0.75Sn0.25I3), including the FA cation (MA0.5FA0.5Pb0.75Sn0.25I3).143 FASnI3 composition engineering was demonstrated with a standard MAPbI3 perovskite precursor (FASnI3)0.6(MAPbI3)0.4, with a bandgap of 1.25 eV.56,149 A MA-free, FA–Sn-based perovskite film showed a narrower bandgap of ∼1.2 eV compared to a MA–FA–Sn-based perovskite (FA0.8MA0.2Sn0.5Pb0.5I3) film with a bandgap of 1.26 eV. The MA–free, FA–Sn-based perovskite (FASn0.5Pb0.5I3) can increase the bandgap by incorporating the Cs cation (FA0.75Cs0.25Sn0.5Pb0.5I3). This strategy improved performance, providing a slightly better-adjusted bandgap, morphology, charge carrier diffusion length and crystal structure.153,154
6.1.3. Buffer layer for energy level matching.
Interfacial engineering was also implemented to obtain a favourable energy level. Indene-C60-propionic acid hexyl ester (IPH) was used as an interlayer between the perovskite and C60, resulting in a conduction band offset of approximately 0.2 eV and a reduced trap density.155 Another modification was 1,3-propane diammonium iodide (PDA). PDA suppressed cross-interface recombination by reducing the band offset between C60 and the perovskite. It reduced the minority carriers at the interface. Finally, quasi-Fermi-level splitting increased by 90 meV using a wide bandgap of 1.79 eV with Voc values of 1.33 V in single junctions and 2.19 V in APTSCs.156 Another research demonstrated that ([2-(9H-carbazol-9yl)ethyl]phosphonic acid) (2PACz) and ([2-(3,6-dimethoxy-9H-carbazol-9-yl)ethyl]phosphonic acid) (MeO-2PACz) were used to bridge the interface. These two chemicals have distinctly different molecular dipole moments. 2PACz and MeO-2PACz molecules anchor on the surface of oxides of NiO, using the phosphonic acid group. This led the molecule-bridged NiO (MB-NiO) to tune the energy-level alignment between NiO and wide bandgap perovskites (Fig. 8a).63
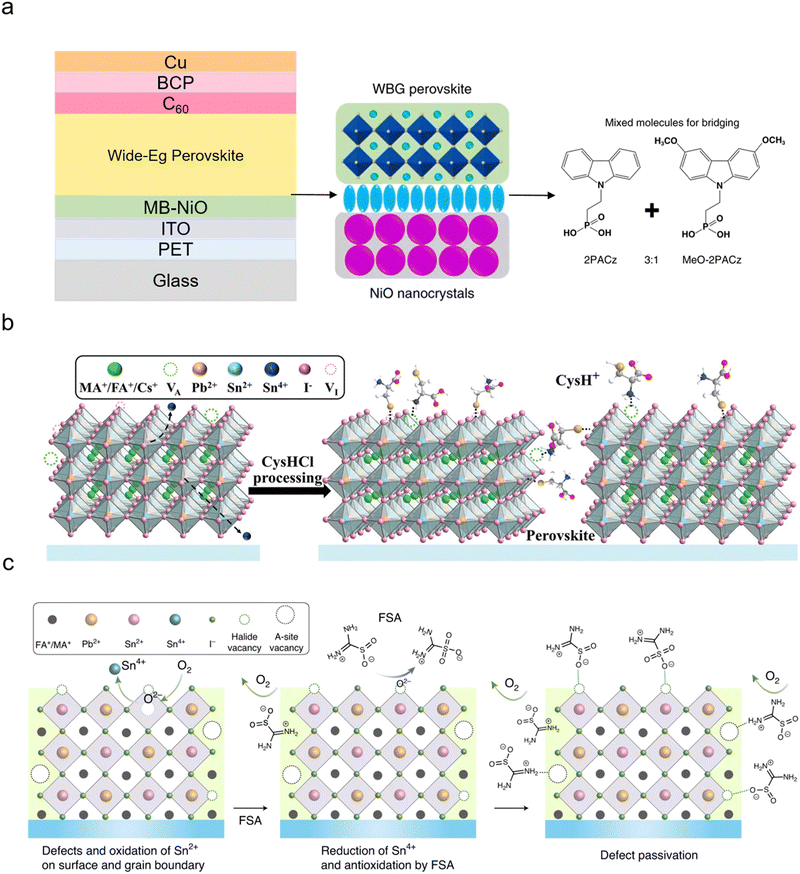 |
| Fig. 8 Interfacial type of perovskite film treatment. (a) Bridge structure formed using mixed molecules of 2PACz and MeO-2PACz between a wide bandgap perovskite and a NiO nanocrystal layer. © 2022. Springer Nature All rights reserved.63 (b) Illustration of the crystal growth process employing CysHCl in the Sn–Pb perovskite. © 2023. John Wiley and Sons All rights reserved.26 (c) Illustration of antioxidation using formamidine sulfinic acid (FSA) in the Sn–Pb perovskite. © 2020. Springer Nature All rights reserved.53 | |
6.1.4. Treatment of defects.
The defects of the perovskite absorber layer and interface (such as vacancies or grain boundaries) generally deteriorate perovskite crystallinity and affect morphology, diffusion length and recombination leading to low stability and device efficiencies. In order to resolve these defects, mainly two methods were applied. One was additive engineering and the other was (interfacial) passivation engineering.
Due to the oxidation tendency of tin(II), the Sn-based narrow bandgap perovskite layer had a significant issue with vacancy defects for which various solutions have been proposed. Studies demonstrated potential solutions to solve the unwanted oxidation reaction.157 0.03 mol% of cadmium ions were able to fill the Sn vacancies to de-dope Sn-based perovskites. Although the grain size did not differ from the reference owing to the small amount of cadmium ion, it reinforced electronic properties: the minority carrier recombination lifetime, carrier mobility and diffusion length.158 Guanidinium thiocyanate (GuaSCN) has been a popular chemical in single-junction solar cells, and many groups had previously demonstrated high-efficiency devices accordingly.159,160 This GuaSCN manifested excellent performances in the tin–lead-based perovskite solar cell (FASnI3)0.6(MAPbI3)0.4, improving the optoelectronic properties, reducing energetic disorder and surface recombination velocity, increasing carrier lifetimes, and providing better morphology with suppression of defects in APTSCs.54,161 Cysteine hydrochloride (CysHCl) was employed as a bulky passivation and a surface anchoring agent for tin–lead perovskites, reducing trap density and non-radiative recombination and increasing carrier diffusion lengths. This multifunctional organic chemical consists of three functional groups: –NH3+, –COOH, and –SH. –NH3+ had the strongest electrostatic potential. –NH3+ was prone to participate in electrophilic reactions filling the FA+/MA+/Cs+ vacancies. The oxygen and sulfur atoms from –COOH and –SH had lone pair electrons, which coordinated with Sn2+ or Pb2+, passivating undercoordinated Sn2+ or Pb2+ and halide vacancies (Fig. 8b).26 Use of tin fluoride (SnF2) as an additive in Sn–Pb-based perovskites was also studied as a passivation method because the fluorine anion had a strong coordinating ability resulting from its hard Lewis base nature. Therefore, the SnF2 additive suppressed tin vacancy formation, creating an SnO1.2F(0.2–0.5) based interface.60 Guanidine tetrafluoroborate (GuaBF4) was demonstrated to prohibit the formation of halogen vacancy defects with a minimal effect on the perovskite lattice in an additive method for narrow bandgap perovskites.132 Another strategy was to use anchored passivation. The zwitterionic molecules allowed for this surface-anchored passivation. This zwitterionic antioxidant hindered Sn2+ oxidation, passivating the surface and improving the uniformity of the film. The formamidine sulfinic acid (FSA) additive acted as a zwitterionic molecule in a tin–lead-based perovskite precursor coordinating to form complexes through dative bonding. This FSA has the ability to passivate both sides of defects, such as electron-donating (FA+/MA+ vacancies) and electron-accepting (halide vacancies, under-coordinated Pb2+/Sn2+) (Fig. 8c).53 Organic metal coordination compounds can also be employed for additive engineering to make better-quality perovskite films. For example, tris(2,4-pentanedionato)gallium (TPGa) was used for the expected heterovalent substitution and antioxidant effect in Sn-based narrow bandgap perovskites.162 A study especially demonstrated utilising the natural SnOx for doping in a Sn–Pb-based narrow-bandgap perovskite, resulting in good morphology, defect treatment, and improved carrier recombination. The natural SnO2 was produced by exposing the SnI2 powder to an oxygen and humid environment and washing it with toluene.32
More research on interfacial engineering demonstrated successful treatment of defects. A study reported a quasi-two-dimensional structure (PEA)2GAPb2I7 by adding bulky organics such as phenethylammonium iodide (PEAI) and guanidinium thiocyanate (GASCN) to control defects. This strategy led to improved optoelectronic quality of the Sn–Pb-based perovskite films.103 4-Trifluoromethyl-phenyl ammonium (CF3-PA) was used for the surface treatment by anchoring CF3-PA on the grain surfaces. This mechanism of passivation adsorption stemmed from that of Lewis base molecules. Hence, the perovskite film was prevented from undergoing surface Sn2+ oxidation.163 In the inorganic-based wide-bandgap perovskite (CsPbI3−xBrx), using high-polarity 4-(trifluoromethyl)phenethyl ammonium (CF3-PEA) molecules, a strongly bonding electric dipole interlayer was formed to passivate surface defects and regulate interfacial energy-level alignment, resulting in suppressed non-radiative recombination and improved charge extraction.131 A surface-anchored passivating molecule also improved the suppression of Sn2+ in a narrow bandgap perovskite. 2-thiopheneethylammonium chloride was used as the 2D perovskite to heal the defects of the perovskite surface. It performed relatively well mitigating interfacial recombination, reducing non-radiative recombination and simultaneously offering band alignment between the perovskite and phenyl-C60-butyric acid methyl ester (PCBM).61 Using the n-butylammonium bromide (BABr), a 2D perovskite was created on the 3D perovskite showing a good open-circuit voltage of 2.33 V.164 As another 2D phase passivation layer, lead chloride (PbCl2) and phenethylammonium chloride (PMACl) were demonstrated by combining both chemicals. Cl− functioned by decreasing the halide vacancies and suppressing ion migration in the crystal lattice of perovskite film. PMA+ facilitated the formation of a 2D perovskite phase on the surface of the perovskite film.28 Although the established 2D/3D structure had generally been shown to reduce surface recombination, the approach suffered from transport losses resulting in fill factor reduction. An immiscible 3D/3D bilayer perovskite provided better functions to suppress the interfacial non-radiative recombination and activate charge extraction in the interface between the Sn–Pb-based perovskite and ETL.5
Antisolvents were employed for defect passivation as well. When an antisolvent was used, the solvent can simultaneously react with the perovskite bulk and surface, employing a phenethylammonium ligand, i.e., phenethylammonium iodide (PEAI) in ethyl acetate (EA).165
6.2. HTL (hole transport layer)
In APTSCs, polyethylenedioxythiophene:polystyrenesulfonate (PEDOT:PSS) is a typical choice for the HTL. However, this HTL has challenges including acidity, hygroscopicity, anisotropic charge injection and irreproducibility regarding electrical and physical properties.166 Hence, many papers described their own solutions in terms of PEDOT:PSS for APTSCs.
The presence of water in PEDOT:PSS affected the underlying layers, e.g. resulting in pinholes and nonuniformity in thin films. The water and PSS-free PEDOT-based HTLs showed good performances with 21.5% efficiency.167 In addition, PEDOT:PSS reacted with a tin–lead-based perovskite leading to charge extraction issues during thermal ageing. The indium tin oxide–perovskite heterojunction (without the HTL) showed a good thermal stability of 1000 h at 85 °C, retaining 95% of initial efficiency while suppressing oxidative degradation due to a larger grain size of 350 nm and compactness of tin–lead perovskite films.120 Another study showed that simple diluted PEDOT:PSS decreased the work function value in UPS spectra from −4.85 eV to −5.04 eV. This helped energy band alignment improving the performance because of mitigating the unmatched work function.168 In recent studies, a ternary Sn(II) alloy of SnOCl was used as the HTL replacing PEDOT:PSS to obtain bigger grain sizes.118 A study demonstrated non-acidic PEDOT:PSS as the HTL because acidic PEDOT:PSS resulted in the formation of I2 and quickly oxidised Pb–Sn. Hence using non-acidic PEDOT:PSS, the device showed better thermal stability.130
Apart from PEDOT:PSS, other organic or inorganic chemicals were used as HTLs: The in situ cross-linked small molecule N4,N′-di(naphthalen-1-yl)-N4,N4′-bis(4-vinylphenyl)biphenyl-4,4′-diamine (VNPB) had strong interaction and lower trap density at the interface between VNPB and a wide bandgap perovskite. This resulted in improved device performance with a PCE of 24.9%.169 [2-(9H-carbazole-9-yl)ethyl] phosphonic acid (2PACz) was employed for wide band gap perovskites to overcome the Voc loss at the HTL/perovskite interface reducing the Voc-deficit of 480 mV at a 1.80 eV bandgap. It resulted in high film uniformity on ITO-based polymer foil.61 MeO-2PACz was demonstrated as a HTL reducing the nonradiative losses. This method resulted in a PCE of 24.1% in 2T APTSCs.27 Surface treatment using a monomolecular layer, [4-[3-(carbazole-9-yl)carbazole-9-yl]butyl]phosphonic acid (4,3BuPACz) on the poly[bis(4-phenyl)(2,4,6-trimethylphenyl)amine] (PTAA), as a buffer layer for wide bandgap perovskites (single junctions) demonstrated good performance improvement of 16.38% from 14.05% PCE. The nitrogen of the PTAA has a lone pair of electrons as a base. The –P–OH from –PO3H2 has acidic properties. Therefore, it formed ionic products from the acid and base.170 In addition to the molecules mentioned above, 4-(7-(4-(bis(4-methoxyphenyl)amino)-2,5-difluorophenyl)benzo[c][1,2,5]thiadiazol-4-yl) benzoic acid (MPA2Ph-BT-BA) and (4-(7H-dibenzo[c,g]carbazole-7-yl)butyl)phosphonic acid (4PADCB) were also used for improving the quality of HTLs.30,31
Inorganic HTLs are a good choice for replacing conventional organic HTLs like PEDOT:PSS because of their high thermal stability. The nickel oxide (NiOx) nanocrystal (NC) is a good candidate due to its dispersibility in water and good thermal stability. The NiOx NC was dissolved in ethanol and used as a HTL in APTSC applications. Ethanol dissolved NiOx more than water since ethanol has less intense polarity and protected the previous front subcell during the fabrication. This resulted in improving the thermal stability, i.e., 2500 h at 85 °C, retaining >80% of the initial efficiency.171 Another work also demonstrated that NiOx is a suitable HTL candidate; NiOx was utilised with PTAA as a bilayer. In this configuration, the thick NiOx modified the surface of the sub-cells treating defects. This method was used for double and triple junctions.35
6.3. CRLs (charge recombination layers)
The charge recombination layer (CRL), also called the interconnection layer or tunnel junction, is essential to fabricate a working device in a series connection for a monolithic tandem. To create high-quality CRLs, holes are supposed to transport from the wide bandgap side to the electron transport layer from the narrow bandgap perovskite side. Electrons, conversely, have to be conveyed from the narrow bandgap side to the hole transport layer from the wide bandgap perovskite side. Here, several high-performance cases of CRLs in APTSCs are described.
6.3.1. Initial CRLs.
Initial APTSC architecture did not have CRLs. Instead of CRLs, only p-type HTLs and n-type ETLs existed between narrow bandgap perovskites and wide bandgap perovskites as p–n junctions or tunnel junctions. Therefore, there was an issue with decreasing the open-circuit voltage. To solve this problem, research focused on the hole transport material (HTM) layers. First, HTMs such as PTAA or poly(3-hexylthiophene-2,5-diyl) (P3HT) with lithium bis(trifluoromethanesulfonyl)imide (Li-TFSI) and tert-butylpyridine (t-BP) additives functioned as quasi-solid electrolytes with the properties of conductive hole conductors due to their Li/Li+ redox shuttle. These additives led to more conductivity between the HTM and PCBM interface. Hence, the HTM, including additives, can improve the recombination layer quality.172 Second, HTM research demonstrated a new type of novel HTL additive. This was the cross-linked p-doped hole transport layer consisting of 1,2-bis[4-(azido-methyl)phenyl]-1,2-diphenylethene (TPE-MN3) and molybdenum tris-[1-(trifluoroethanoyl)-2-(trifluoromethyl)ethane-1,2-dithiolene] (Mo(tfdCOCF3)3) doped in PTAA. This HTL was a part of the CRL in the APTSC architecture and showed good solvent protection, appropriate energy level and a high electrical conductivity of 8.5 × 10 S cm−1 at 1 wt% doping compared to the non-doped one (2.5 × 10−7 S cm−1). The authors assumed that the azide group would react with reactive nitrene species upon ultraviolet exposure, which was able to be inserted into the C–H bonds in PTAA. It formed insoluble cross-linked networks.173
6.3.2. Current CRLs.
Firstly, the CRL was configured with several layers (spiro-MeOTAD/PEDOT:PSS/PEI(polyethylenimine)/PCBM:PEI) matching with essential functions such as a large work function between the top and bottom surfaces, low-temperature processes, orthogonal solvents, and suitable protective layers for the same solvent (Fig. 9a).174 Secondly, another example with several layer configured solution-processed organic-based chemicals (Spiro-MeOTAD/PEDOT:PSS/C60) has demonstrated an excellent open-circuit voltage of 1.96 V with high CRL quality. Spiro-MeOTAD and C60 acted as p-type and n-type layers, respectively, and thin PEDOT:PSS acted as a recombination layer (Fig. 9b).175 Thirdly, organic doping for CRLs is a great option. By doping 2,2′-(perfluoronaphthalene-2,6-diylidene) dimalononitrile (F6-TCNNQ) in N4,N4,N4′′,N4′′-tetra([1,1′-biphenyl]-4-yl)-[1,1′:4′,1′′-terphenyl]-4,4′′-diamine (TaTm), TaTm:F6-TCNNQ was deposited as a p-doped HTL. In contrast, N1,N4-bis(tri-p-tolylphosphoranylidene) benzene-1,4-diamine (PhIm) was doped in C60 as an n-type ETL. These two organic doped layers functioned nicely as CRLs (Fig. 9c).176 Fourthly, a thermionic emission-based CRL structure composed of four layers was demonstrated, FSIP/ETL(C60/BCP)/ultrathin transparent metal alloy (Cu/Au), and HTL (PEDOT:PSS). Here, FSIP had critical roles in solvent resistance due to its hydrophobicity and good optoelectrical properties. FSIP was considered an ultrathin insulating layer (∼5 nm) because it consisted of fluoride silane and polyethylenimine ethoxylated (PEIE) where trichloro(3,3,3-trifluoropropyl)silane (FPTS) was proposed as a silanising agent incorporated on PEIE (Fig. 9d).177 Lastly, a study has successfully tested the simplification of a CRL because the conventional CRL consisted of four or more layers. The layers for CRLs had issues regarding device performance. For example, ITO, indium-doped zinc oxide (IZO) or gold resulted in current density losses due to parasitic absorption and reflection at the interface forming the multilayers, while the sputtering deposition processes damaged the underlying layers, reducing the fill factor. A complex to simple CRL was achieved using the C60/SnO1.76 layer. In the fabrication process, C60 was fortuitously n-doped by iodine ions from the previous perovskite layer, which functioned as an effective electron-selective layer. The incomplete oxidation of tin had the property of ambipolar carrier transport due to the large density of Sn2+ (Fig. 9e and f).178
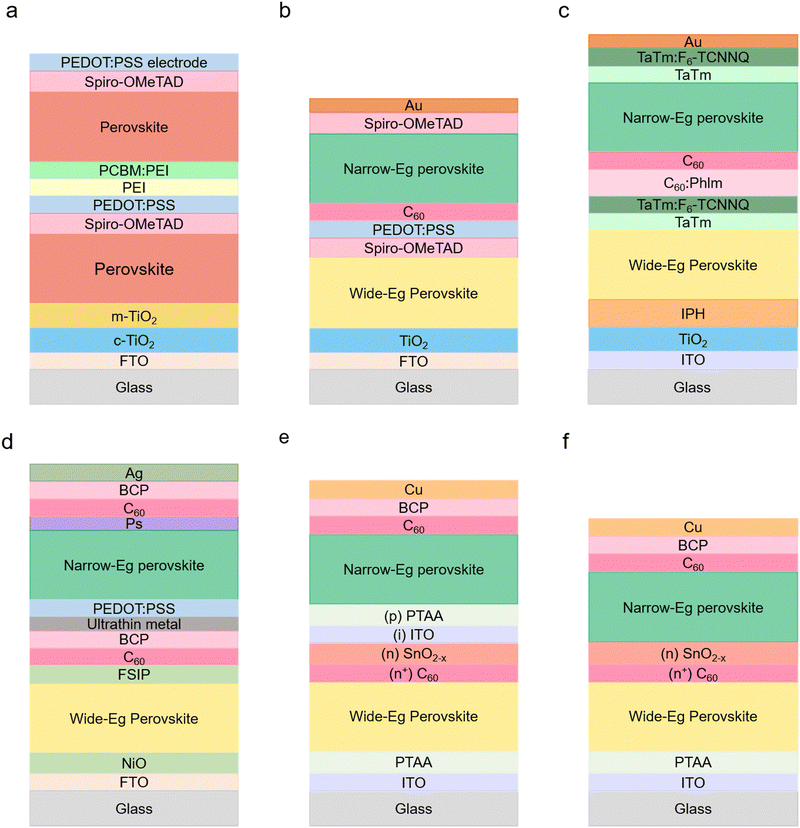 |
| Fig. 9 Several configurations of charge recombination layers. (a) Device configuration including the charge recombination layer of spiro-MeOTAD/PEDOT:PSS/PEI (polyethylenimine)/PCBM:PEI. © 2020. Royal Society of Chemistry. All rights reserved.174 (b) Cell structure including the charge recombination layer of Spiro-MeOTAD/PEDOT:PSS/C60. © 2017. American Chemical Society All rights reserved.175 (c) Device structure including an organic dopant (F6-TCNNQ) in TaTm for the charge recombination layer configuration. © 2016. John Wiley and Sons. All rights reserved.176 (d) Device configuration including the charge recombination layer of (fluoride silane and polyethylenimine ethoxylated (PEIE) in trichloro(3,3,3-trifluoropropyl)silane) FPTS/C60/BCP/Cu:Au alloy/PEDOT:PSS. © 2018. John Wiley and Sons. All rights reserved.177 (e) Device structure before simplifying the charge recombination layer of C60/SnO2−x/ITO/PTAA. (f) Device structure after simplifying the charge recombination layer of C60/SnO2−x. © 2020. Springer Nature. All rights reserved.178 | |
6.4. Electrodes
In 4T-based APTSCs, the research regarding electrodes on the HTL in wide bandgap-based perovskite solar cells is necessary owing to the optoelectrical losses. The conventional MoOx/Au/MoOx electrode limited the transmittance due to parasitic absorption from the thin metal layer. Replacing MoOx/Au/MoOx with transparent MoOx/indium tin oxide (ITO) led to an improved transmittance in the infrared range. Consequently, the light transparency of the infrared range in the top cell was enhanced up to 70%.179 Another electrode study used highly transparent hydrogen-doped indium oxide (IO:H) to replace ITO as the electrode, which was an option with the HTL-free configuration in 4T APTSCs. IO:H improved photocurrent, thus reducing ultra-low near-infrared optical loss and increasing high charge carrier mobility with the HTL-free configuration.180
7. Simulated models of APTSCs
Since 2017, the number of simulation models has increased attempting a full APTSC model.205 Many simulations have attempted to optimise the thickness of the layers. Another increasing trend is the simulation of lead-free perovskite materials. Here, the research in terms of thickness simulation with lead and without lead is briefly described.
7.1. Lead-containing perovskite simulations
One simulation study derived that the ideal thickness of the subcells was 350 nm, reaching the maximum output efficiency of 36.6%, with the bandgap of the top cell being 1.5 eV and the bottom cell bandgap being 0.95 eV.206 Another study introduced CsPbIBr2 at 2.05 eV for the top cell and MAPbI3 at 1.55 eV for the bottom cell. The optimised thickness was 600 nm for the top cell and 500 nm for the properties of CsPbIBr2. A maximum PCE of 27.4% was calculated.207
7.2. Lead-free perovskite simulations
Although Pb-based PSCs are a promising state-of-the-art technology in the field of photovoltaics, due to lead toxicity, many groups are interested in lead-free perovskites. Concerns are focused on the leakage of lead from broken modules due to natural disasters/phenomena such as earthquakes, hail or heavy rain, even though the overall lead content of PSCs is low at 0.4 g m−2.208 Thus, many simulations were conducted to study possible lead-free alternatives.
There are several papers regarding the thickness optimisation of lead-free perovskite absorbers. One work simulated a perovskite with a wide bandgap (Cs2AgBi0.75Sb0.25Br6) of 1.8 eV and a low Pb content-based perovskite (FACsPb0.5Sn0.5I3) with a narrow bandgap of 1.2 eV. In the APTSC configuration, the optimised thicknesses of the wide bandgap and the narrow band gap perovskites are 380 nm and 400 nm, respectively, reaching the PCE of 17.35%.209 When the MASnI3 perovskite with a narrow bandgap of 1.3 eV and Cs2AgBi0.75Sb0.25Br6 with a wide bandgap of 1.8 eV were employed, the simulation indicated that a maximum PCE of 24.86% can be achieved.210 Another work utilised germanium to replace Pb for achieving a wide bandgap. A combination of methyl ammonium germanium halide was produced with a wide bandgap of 1.9 eV. Germanium slightly increased the narrow bandgap (FA0.75MA0.25Sn0.25Ge0.5I3), reaching the bandgap of 1.4 eV. The optimised APTSC efficiency was 26.72% considering the different ETLs such as SnO2, IGZO, PCBM and ZnO.211 Another simulation also employed germanium in the perovskite composition (CsSn0.5Ge0.5I3) for achieving a wide bandgap of 1.5 eV. In contrast, only Sn was used instead of tin–lead mixed perovskite solution showing 1.3 eV for a narrow bandgap perovskite. The optimised perovskite thickness of 2T is 450 nm and 812 nm for wide and narrow bandgap perovskites, respectively, achieving a PCE of 18.32%. On the other hand, for 4T APTSCs, optimised perovskite thickness was thicker than the thickness of 2T at 1300 nm and 900 nm for wide and narrow bandgaps showing a PCE of 19.86%.212 Another simulation used germanium for lead-free APTSCs as an alternative to lead. The optimised thickness of the wide bandgap (MAGeI3) was 983 nm, and the thickness of the narrow bandgap was 1600 nm. With this structure, the calculation showed a PCE of 30.85%.213
8. Conclusion and perspectives
Many state-of-the-art PV technologies have gradually progressed from single-junction solar cells to double or triple-junction solar cells. The increasing attention on the APTSCs has been proven by the number of published papers annually and the improved device performances. In this review, we introduced the fundamentals of APTSCs, the approaches for the current issues, and the potential of APTSCs in the future.
The tandem technology is one of the key methods beyond the single junction S–Q limit. The tunable bandgap of the perovskite provides the privilege of high efficiency towards ideally 45% instead of 33%. Additionally, the low cost originating from the thin film technology, lightweight, scale-up chances, and eco-friendly technology related to a low CO2 footprint are highly attractive.
We elaborated on various types of APTSCs considering 2T and 4T architectures and classified APTSCs into bifacial, inorganic, flexible substrate-based, substrate configured and multi-junction APTSCs beyond the double junctions.
However, these high-tech APTSCs faced several issues regarding stability caused by Sn2+ oxidation of narrow bandgap perovskites, Voc loss of wide bandgap perovskites, non-standardisation of CRLs, and inhomogeneity in the layers during the deposition of a multilayer stack. We also offered information regarding each layer of the APTSC configuration and solutions. Most of the resolutions consisted of using additives or passivation processes for controlling the crystal growth rate, managing bandgaps and band alignment, and treating the defects.
Furthermore, to show the potential of the APTSCs, we summarised the simulation studies. A variety of simulations were implemented with diverse APTSC conditions. Mainly, the simulation research demonstrated the possibility of improving the performance of the APTSCs beyond 30%.
In the journey to commercialising APTSCs, we suggest possible milestones to achieve PCEs >30% with all-perovskite tandem modules.
Blade-coating (instead of spin-coating) methods are currently demonstrated for the scale-up. In addition, slot-die coating, spray coating, inkjet printing, and screen printing also have the potential towards scaling APTSCs.
Furthermore, we need more studies on the flexible substrate-based APTSCs for mass production. The roll-to-roll process can accelerate perovskite market growth.
To develop high-performance scaled APTSCs, we consider three main engineering aspects: buried interface engineering, simplifying the charge recombination layer, and reducing the vacuum process. The first technical method is buried interface engineering (so-called additive engineering), which provides several advantages. Buried interface engineering enables fast device manufacturing speed as it does not demand an extra-thin passivation layer. Additionally, it does not demand high-quality super-thin layer technology for the passivation layers. It can not only improve the quality of the perovskite, ETL, or HTL bulk layer but also achieve the passivation effect.58,189,197,201 The second technical method is to simplify the charge recombination layer. The complicated structure of the charge recombination layer constructed using different deposition techniques can retard the commercialisation of APTSCs regarding the design of the manufacturing execution system (MES). The third technical method is to reduce the vacuum process as much as possible during device fabrication. Although using atomic layer deposition or sputtering deposition can provide excellent layers, as mentioned above, the different deposition techniques can hinder production efficiency. Moreover, a vacuum can be detrimental to perovskite solar cells, affecting their device lifetime.230,231
However, considering the low durability of perovskites against humidity and oxygen, a plant may require an inert gas system (or an otherwise controlled environment) until encapsulation is applied.
In addition, for commercialising APTSCs, highly efficient and stable all-perovskite module technologies are crucial, such as cell-to-module (CTM) technology. In this case, interconnection development will be necessary to minimise dead areas, thus increasing the geometric fill factors to reduce CTM loss.
Author contributions
All authors contributed to the discussion of this content. J. L. wrote the initial manuscript. N. P., S. S. and M. S. revised and edited the manuscripts before submission.
Conflicts of interest
There are no conflicts to declare.
Acknowledgements
M. S. thanks the Helmholtz Young Investigator Group FRONTRUNNER. M.S. thanks the German Research Foundation (DFG) for funding (SPP2196, 431314977/GRK 2642). M. S. acknowledges funding by ProperPhotoMile. Project ProperPhotoMile is supported under the umbrella of SOLARERA.NET cofunded by The Spanish Ministry of Science and Education and the AEI under Project PCI2020-112185 and CDTI Project IDI-20210171, the Federal Ministry for Economic Affairs and Energy based on a decision by the German Bundestag Projects FKZ 03EE1070B and FKZ 03EE1070A and the Israel Ministry of Energy with Project 220-11-031. SOLAR-ERA.NET is supported by the European Commission within the EU Framework Programme for Research and Innovation HORIZON 2020 (Cofund ERA-NET action number 786483) funded by the European Union. M. S. acknowledges funding from the European Research Council under the Horizon Europe program (LOCAL-HEAT, Grant Agreement 101041809). M. S. acknowledges funding from the German Bundesministerium für Bildung and Forschung (BMBF), project “NETPEC” (01LS2103E). S. I. S. acknowledges financial support from the Basic Science Research Program (NRF-2018R1A3B1052820) through the National Research Foundation of Korea (NRF), funded by the Ministry of Science, ICT & Future Planning (MSIP).
References
- J. Park, J. Kim, H.-S. Yun, M. J. Paik, E. Noh, H. J. Mun, M. G. Kim, T. J. Shin and S. Il Seok, Nature, 2023, 616, 724–730 CrossRef CAS PubMed.
- Best Research-Cell Efficiency Chart | Photovoltaic Research | NREL, https://www.nrel.gov/pv/cell-efficiency.html, (accessed 11 January 2024).
- T. Todorov, T. Gershon, O. Gunawan, C. Sturdevant and S. Guha, Appl. Phys. Lett., 2014, 105(17), 173902 CrossRef.
- S. Liu, Y. Lu, C. Yu, J. Li, R. Luo, R. Guo, H. Liang, X. Jia, X. Guo, Y.-D. Wang, Q. Zhou, X. Wang, S. Yang, M. Sui, P. Müller-Buschbaum and Y. Hou, Nature, 2024, 628, 306–312 CrossRef CAS PubMed.
- R. Lin, Y. Wang, Q. Lu, B. Tang, J. Li, H. Gao, Y. Gao, H. Li, C. Ding, J. Wen, P. Wu, C. Liu, S. Zhao, K. Xiao, Z. Liu, C. Ma, Y. Deng, L. Li, F. Fan and H. Tan, Nature, 2023, 620, 994–1000 CrossRef CAS PubMed.
- J. Kang and L.-W. Wang, J. Phys. Chem. Lett., 2017, 8, 489–493 CrossRef CAS PubMed.
- J. H. Noh, S. H. Im, J. H. Heo, T. N. Mandal and S. Il Seok, Nano Lett., 2013, 13, 1764–1769 CrossRef CAS PubMed.
- R. E. Brandt, V. Stevanović, D. S. Ginley and T. Buonassisi, MRS Commun., 2015, 5, 265–275 CrossRef CAS.
- S. D. Stranks, G. E. Eperon, G. Grancini, C. Menelaou, M. J. P. Alcocer, T. Leijtens, L. M. Herz, A. Petrozza and H. J. Snaith, Science, 2013, 342, 341–344 CrossRef CAS PubMed.
- T. Wang, B. Daiber, J. M. Frost, S. A. Mann, E. C. Garnett, A. Walsh and B. Ehrler, Energy Environ. Sci., 2017, 10, 509–515 RSC.
- S. Bai, P. Da, C. Li, Z. Wang, Z. Yuan, F. Fu, M. Kawecki, X. Liu, N. Sakai, J. T.-W. Wang, S. Huettner, S. Buecheler, M. Fahlman, F. Gao and H. J. Snaith, Nature, 2019, 571, 245–250 CrossRef CAS PubMed.
- S. Sahayaraj, E. Radicchi, M. Ziółek, M. Ścigaj, M. Tamulewicz-Szwajkowska, J. Serafińczuk, F. De Angelis and K. Wojciechowski, J. Mater. Chem. A, 2021, 9, 9175–9190 RSC.
- W. Zhao, J. Xu, K. He, Y. Cai, Y. Han, S. Yang, S. Zhan, D. Wang, Z. Liu and S. Liu, Nano-Micro Lett., 2021, 13, 169 CrossRef CAS PubMed.
- V. M. Goldschmidt, Naturwissenschaften, 1926, 14, 477–485 CrossRef CAS.
- D. Ji, S. Feng, L. Wang, S. Wang, M. Na, H. Zhang, C. Zhang and X. Li, Vacuum, 2019, 164, 186–193 CrossRef CAS.
- F. Hao, C. C. Stoumpos, R. P. H. Chang and M. G. Kanatzidis, J. Am. Chem. Soc., 2014, 136, 8094–8099 CrossRef CAS PubMed.
- L. Protesescu, S. Yakunin, M. I. Bodnarchuk, F. Krieg, R. Caputo, C. H. Hendon, R. X. Yang, A. Walsh and M. V. Kovalenko, Nano Lett., 2015, 15, 3692–3696 CrossRef CAS PubMed.
- Q. A. Akkerman, V. D’Innocenzo, S. Accornero, A. Scarpellini, A. Petrozza, M. Prato and L. Manna, J. Am. Chem. Soc., 2015, 137, 10276–10281 CrossRef CAS PubMed.
- A. Goyal, S. McKechnie, D. Pashov, W. Tumas, M. Van Schilfgaarde and V. Stevanović, Chem. Mater., 2018, 30, 3920–3928 CrossRef CAS.
- J. Jeong, M. Kim, J. Seo, H. Lu, P. Ahlawat, A. Mishra, Y. Yang, M. A. Hope, F. T. Eickemeyer, M. Kim, Y. J. Yoon, I. W. Choi, B. P. Darwich, S. J. Choi, Y. Jo, J. H. Lee, B. Walker, S. M. Zakeeruddin, L. Emsley, U. Rothlisberger, A. Hagfeldt, D. S. Kim, M. Grätzel and J. Y. Kim, Nature, 2021, 592, 381–385 CrossRef CAS PubMed.
- S. Nagane, U. Bansode, O. Game, S. Chhatre and S. Ogale, Chem. Commun., 2014, 50, 9741–9744 RSC.
- J. Chen, S.-G. Kim and N.-G. Park, Adv. Mater., 2018, 30, 1801948 CrossRef PubMed.
- K. O. Brinkmann, T. Becker, F. Zimmermann, C. Kreusel, T. Gahlmann, M. Theisen, T. Haeger, S. Olthof, C. Tückmantel, M. Günster, T. Maschwitz, F. Göbelsmann, C. Koch, D. Hertel, P. Caprioglio, F. Peña-Camargo, L. Perdigón-Toro, A. Al-Ashouri, L. Merten, A. Hinderhofer, L. Gomell, S. Zhang, F. Schreiber, S. Albrecht, K. Meerholz, D. Neher, M. Stolterfoht and T. Riedl, Nature, 2022, 604, 280–286 CrossRef CAS PubMed.
- M. Jošt, E. Köhnen, A. Al-Ashouri, T. Bertram, Š. Tomšič, A. Magomedov, E. Kasparavicius, T. Kodalle, B. Lipovšek, V. Getautis, R. Schlatmann, C. A. Kaufmann, S. Albrecht and M. Topič, ACS Energy Lett., 2022, 7, 1298–1307 CrossRef.
- T. Duong, T. Nguyen, K. Huang, H. Pham, S. G. Adhikari, M. R. Khan, L. Duan, W. Liang, K. C. Fong, H. Shen, A. D. Bui, A. O. Mayon, T. Truong, G. Tabi, V. Ahmad, S. Surve, J. Tong, T. Kho, T. Tran-Phu, T. Lu, J. Zheng, U. W. Paetzold, U. Lemmer, A. H. Baillie, Y. Liu, G. Andersson, T. White, K. Weber and K. Catchpole, Adv. Energy Mater., 2023, 13, 2203607 CrossRef CAS.
- J. Luo, R. He, H. Lai, C. Chen, J. Zhu, Y. Xu, F. Yao, T. Ma, Y. Luo, Z. Yi, Y. Jiang, Z. Gao, J. Wang, W. Wang, H. Huang, Y. Wang, S. Ren, Q. Lin, C. Wang, F. Fu and D. Zhao, Adv. Mater., 2023, 2300352 CrossRef CAS PubMed.
- Y.-H. Chiang, K. Frohna, H. Salway, A. Abfalterer, L. Pan, B. Roose, M. Anaya and S. D. Stranks, ACS Energy Lett., 2023, 8, 2728–2737 CrossRef CAS PubMed.
- Y. Zhao, C. Wang, T. Ma, L. Zhou, Z. Wu, H. Wang, C. Chen, Z. Yu, W. Sun, A. Wang, H. Huang, B. Zou, D. Zhao and X. Li, Energy Environ. Sci., 2023, 16, 2080–2089 RSC.
- X. Hu, J. Li, C. Wang, H. Cui, Y. Liu, S. Zhou, H. Guan, W. Ke, C. Tao and G. Fang, Nano-Micro Lett., 2023, 15, 103 CrossRef CAS PubMed.
- J. Zhu, Y. Luo, R. He, C. Chen, Y. Wang, J. Luo, Z. Yi, J. Thiesbrummel, C. Wang, F. Lang, H. Lai, Y. Xu, J. Wang, Z. Zhang, W. Liang, G. Cui, S. Ren, X. Hao, H. Huang, Y. Wang, F. Yao, Q. Lin, L. Wu, J. Zhang, M. Stolterfoht, F. Fu and D. Zhao, Nat. Energy, 2023, 8, 714–724 CrossRef CAS.
- R. He, W. Wang, Z. Yi, F. Lang, C. Chen, J. Luo, J. Zhu, J. Thiesbrummel, S. Shah, K. Wei, Y. Luo, C. Wang, H. Lai, H. Huang, J. Zhou, B. Zou, X. Yin, S. Ren, X. Hao, L. Wu, J. Zhang, J. Zhang, M. Stolterfoht, F. Fu, W. Tang and D. Zhao, Nature, 2023, 618, 80–86 CrossRef CAS PubMed.
- L. Huang, H. Cui, W. Zhang, D. Pu, G. Zeng, Y. Liu, S. Zhou, C. Wang, J. Zhou, C. Wang, H. Guan, W. Shen, G. Li, T. Wang, W. Zheng, G. Fang and W. Ke, Adv. Mater., 2023, 35(32), 2301125 CrossRef CAS PubMed.
- J. Wang, L. Zeng, D. Zhang, A. Maxwell, H. Chen, K. Datta, A. Caiazzo, W. H. M. Remmerswaal, N. R. M. Schipper, Z. Chen, K. Ho, A. Dasgupta, G. Kusch, R. Ollearo, L. Bellini, S. Hu, Z. Wang, C. Li, S. Teale, L. Grater, B. Chen, M. M. Wienk, R. A. Oliver, H. J. Snaith, R. A. J. Janssen and E. H. Sargent, Nat. Energy, 2024, 9, 70–80 CrossRef CAS.
- Z. Wang, L. Zeng, T. Zhu, H. Chen, B. Chen, D. J. Kubicki, A. Balvanz, C. Li, A. Maxwell, E. Ugur, R. dos Reis, M. Cheng, G. Yang, B. Subedi, D. Luo, J. Hu, J. Wang, S. Teale, S. Mahesh, S. Wang, S. Hu, E. D. Jung, M. Wei, S. M. Park, L. Grater, E. Aydin, Z. Song, N. J. Podraza, Z. H. Lu, J. Huang, V. P. Dravid, S. De Wolf, Y. Yan, M. Grätzel, M. G. Kanatzidis and E. H. Sargent, Nature, 2023, 618, 74–79 CrossRef CAS PubMed.
- D. P. McMeekin, S. Mahesh, N. K. Noel, M. T. Klug, J. C. Lim, J. H. Warby, J. M. Ball, L. M. Herz, M. B. Johnston and H. J. Snaith, Joule, 2019, 3, 387–401 CrossRef CAS.
- K. Xiao, J. Wen, Q. Han, R. Lin, Y. Gao, S. Gu, Y. Zang, Y. Nie, J. Zhu, J. Xu and H. Tan, ACS Energy Lett., 2020, 5, 2819–2826 CrossRef CAS.
- J. Wang, V. Zardetto, K. Datta, D. Zhang, M. M. Wienk and R. A. J. Janssen, Nat. Commun., 2020, 11, 5254 CrossRef CAS PubMed.
- Z. Song, C. L. McElvany, A. B. Phillips, I. Celik, P. W. Krantz, S. C. Watthage, G. K. Liyanage, D. Apul and M. J. Heben, Energy Environ. Sci., 2017, 10, 1297–1305 RSC.
- M. Cai, Y. Wu, H. Chen, X. Yang, Y. Qiang and L. Han, Adv. Sci., 2017, 4, 1600269 CrossRef PubMed.
- Z. Li, Y. Zhao, X. Wang, Y. Sun, Z. Zhao, Y. Li, H. Zhou and Q. Chen, Joule, 2018, 2, 1559–1572 CrossRef CAS.
-
Z. Song, A. B. Phillips, I. Celik, G. K. Liyanage, D. Zhao, D. Apul, Y. Yan and M. J. Heben, in 2018 IEEE 7th World Conference on Photovoltaic Energy Conversion (WCPEC) (A Joint Conference of 45th IEEE PVSC, 28th PVSEC & 34th EU PVSEC), 2018, pp. 1134–1138.
- M. De Bastiani, V. Larini, R. Montecucco and G. Grancini, Energy Environ. Sci., 2022, 16, 421–429 RSC.
- J. Suo, B. Yang, E. Mosconi, D. Bogachuk, T. A. S. Doherty, K. Frohna, D. J. Kubicki, F. Fu, Y. Kim, O. Er-Raji, T. Zhang, L. Baldinelli, L. Wagner, A. N. Tiwari, F. Gao, A. Hinsch, S. D. Stranks, F. De Angelis and A. Hagfeldt, Nat. Energy, 2024, 9, 172–183 CrossRef CAS PubMed.
- P. Du, J. Li, L. Wang, L. Sun, X. Wang, X. Xu, L. Yang, J. Pang, W. Liang, J. Luo, Y. Ma and J. Tang, Nat. Commun., 2021, 12, 4751 CrossRef CAS PubMed.
- I. J. Park, G. Kang, M. A. Park, J. S. Kim, S. W. Seo, D. H. Kim, K. Zhu, T. Park and J. Y. Kim, ChemSusChem, 2017, 10, 2660–2667 CrossRef CAS PubMed.
- L. Chu, R. Hu, W. Liu, Y. Ma, R. Zhang, J. Yang and X. Li, Mater. Res. Bull., 2018, 98, 322–327 CrossRef CAS.
- Z. Li, P. Li, G. Chen, Y. Cheng, X. Pi, X. Yu, D. Yang, L. Han, Y. Zhang and Y. Song, ACS Appl. Mater. Interfaces, 2020, 12, 39082–39091 CrossRef CAS PubMed.
- M. Park, W. Cho, G. Lee, S. C. Hong, M. Kim, J. Yoon, N. Ahn and M. Choi, Small, 2019, 15, 1804005 CrossRef PubMed.
- S. Y. Abate, Z. Yang, S. Jha, J. Emodogo, G. Ma, Z. Ouyang, S. Muhammad, N. Pradhan, X. Gu, D. Patton, D. Li, J. Cai and Q. Dai, ACS Appl. Mater. Interfaces, 2023, 15, 25495–25505 CrossRef CAS PubMed.
- J. Yang, E. L. Lim, L. Tan and Z. Wei, Adv. Energy Mater., 2022, 12, 2200975 CrossRef CAS.
- G. S. Han, J. Kim, S. Bae, S. Han, Y. J. Kim, O. Y. Gong, P. Lee, M. J. Ko and H. S. Jung, ACS Energy Lett., 2019, 4, 1845–1851 CrossRef CAS.
- S. Chen, X. Xiao, H. Gu and J. Huang, Sci. Adv., 2021, 7, eabe8130 CrossRef CAS PubMed.
- K. Xiao, R. Lin, Q. Han, Y. Hou, Z. Qin, H. T. Nguyen, J. Wen, M. Wei, V. Yeddu, M. I. Saidaminov, Y. Gao, X. Luo, Y. Wang, H. Gao, C. Zhang, J. Xu, J. Zhu, E. H. Sargent and H. Tan, Nat. Energy, 2020, 5, 870–880 CrossRef CAS.
- V. Babu, M. A. Mejia Escobar, R. Fuentes Pineda, M. Ścigaj, P. Spinelli and K. Wojciechowski, Mater. Today Energy, 2022, 28, 101073 CrossRef CAS.
- B. Abdollahi Nejand, D. B. Ritzer, H. Hu, F. Schackmar, S. Moghadamzadeh, T. Feeney, R. Singh, F. Laufer, R. Schmager, R. Azmi, M. Kaiser, T. Abzieher, S. Gharibzadeh, E. Ahlswede, U. Lemmer, B. S. Richards and U. W. Paetzold, Nat. Energy, 2022, 7, 620–630 CrossRef CAS.
- K. Xiao, Y.-H. Lin, M. Zhang, R. D. J. Oliver, X. Wang, Z. Liu, X. Luo, J. Li, D. Lai, H. Luo, R. Lin, J. Xu, Y. Hou, H. J. Snaith and H. Tan, Science, 2022, 376(6594), 762–767 CrossRef CAS PubMed.
- X. Dai, S. Chen, H. Jiao, L. Zhao, K. Wang, Z. Ni, Z. Yu, B. Chen, Y. Gao and J. Huang, Nat. Energy, 2022, 7, 923–931 CrossRef CAS.
- H. Gao, K. Xiao, R. Lin, S. Zhao, W. Wang, S. Dayneko, C. Duan, C. Ji, H. Sun, A. Dinh Bui, C. Liu, J. Wen, W. Kong, H. Luo, X. Zheng, Z. Liu, H. Nguyen, J. Xie, L. Li, M. I. Saidaminov and H. Tan, Science, 2024, 383(6685), 855–859 CrossRef CAS PubMed.
- S. Kang, J. Jeong, S. Cho, Y. J. Yoon, S. Park, S. Lim, J. Y. Kim and H. Ko, J. Mater. Chem. A, 2019, 7, 1107–1114 RSC.
- J. Kurisinkal Pious, Y. Zwirner, H. Lai, S. Olthof, Q. Jeangros, E. Gilshtein, R. K. Kothandaraman, K. Artuk, P. Wechsler, C. Chen, C. M. Wolff, D. Zhao, A. N. Tiwari and F. Fu, ACS Appl. Mater. Interfaces, 2023, 15(7), 10150–10157 CrossRef CAS PubMed.
- H. Lai, J. Luo, Y. Zwirner, S. Olthof, A. Wieczorek, F. Ye, Q. Jeangros, X. Yin, F. Akhundova, T. Ma, R. He, R. K. Kothandaraman, X. Chin, E. Gilshtein, A. Müller, C. Wang, J. Thiesbrummel, S. Siol, J. M. Prieto, T. Unold, M. Stolterfoht, C. Chen, A. N. Tiwari, D. Zhao and F. Fu, Adv. Energy Mater., 2022, 12(45), 2202438 CrossRef CAS.
- A. F. Palmstrom, G. E. Eperon, T. Leijtens, R. Prasanna, S. N. Habisreutinger, W. Nemeth, E. A. Gaulding, S. P. Dunfield, M. Reese, S. Nanayakkara, T. Moot, J. Werner, J. Liu, B. To, S. T. Christensen, M. D. McGehee, M. F. A. M. van Hest, J. M. Luther, J. J. Berry and D. T. Moore, Joule, 2019, 3, 2193–2204 CrossRef CAS.
- L. Li, Y. Wang, X. Wang, R. Lin, X. Luo, Z. Liu, K. Zhou, S. Xiong, Q. Bao, G. Chen, Y. Tian, Y. Deng, K. Xiao, J. Wu, M. I. Saidaminov, H. Lin, C. Q. Ma, Z. Zhao, Y. Wu, L. Zhang and H. Tan, Nat. Energy, 2022, 7, 708–717 CrossRef CAS.
- J. Gong, S. B. Darling and F. You, Energy Environ. Sci., 2015, 8, 1953–1968 RSC.
- E. Leccisi and V. Fthenakis, Prog. Photovoltaics Res. Appl., 2021, 29, 1078–1092 CrossRef CAS.
- X. Tian, S. D. Stranks and F. You, Sci. Adv., 2020, 6, eabb0055 CrossRef CAS PubMed.
-
E. D. Jackson, Trans. Intern. Conf. on the Use of Solar Energy-The Scientific Basis, 1955, 5, 122.
-
I. S. E. Fraunhofer Develops the World's Most Efficient Solar Cell with 47.6 Percent Efficiency - Fraunhofer ISE, https://www.ise.fraunhofer.de/en/press-media/press-releases/2022/fraunhofer-ise-develops-the-worlds-most-efficient-solar-cell-with-47-comma-6-percent-efficiency.html, (accessed 27 August 2023).
- S. Rühle, Phys. Status Solidi A, 2017, 214, 1600955 CrossRef.
- M. Hosseinnezhad, J. Electron.
Mater., 2019, 48, 5403–5408 CrossRef CAS.
- M. A. Green, E. D. Dunlop, M. Yoshita, N. Kopidakis, K. Bothe, G. Siefer and X. Hao, Prog. Photovoltaics Res. Appl., 2023, 31(7), 651–663 CrossRef.
- B. Ehrler, E. Alarcón-Lladó, S. W. Tabernig, T. Veeken, E. C. Garnett and A. Polman, ACS Energy Lett., 2020, 5, 3029–3033 CrossRef CAS.
- G. E. Eperon, M. T. Hörantner and H. J. Snaith, Nat. Rev. Chem., 2017, 1(12), 0095 CrossRef CAS.
- Z. Liu, L. Krückemeier, B. Krogmeier, B. Klingebiel, J. A. Márquez, S. Levcenko, S. Öz, S. Mathur, U. Rau, T. Unold and T. Kirchartz, ACS Energy Lett., 2019, 4, 110–117 CrossRef CAS.
- Q. Zhou, J. Duan, J. Du, Q. Guo, Q. Zhang, X. Yang, Y. Duan and Q. Tang, Adv. Sci., 2021, 8(19), 2101418 CrossRef CAS PubMed.
- S. Mahesh, J. M. Ball, R. D. J. Oliver, D. P. McMeekin, P. K. Nayak, M. B. Johnston and H. J. Snaith, Energy Environ. Sci., 2020, 13, 258–267 RSC.
- T. Nie, J. Yang, Z. Fang, Z. Xu, X. Ren, X. Guo, T. Chen and S. Frank Liu, Chem. Eng. J., 2023, 468, 143341 CrossRef CAS.
- D. B. Khadka, Y. Shirai, M. Yanagida, T. Noda and K. Miyano, ACS Appl. Mater. Interfaces, 2018, 10, 22074–22082 CrossRef CAS PubMed.
- P. Ferdowsi, E. Ochoa-Martinez, S. S. Alonso, U. Steiner and M. Saliba, Sci. Rep., 2020, 10(1), 22260 CrossRef CAS PubMed.
- Y. Lin, B. Chen, F. Zhao, X. Zheng, Y. Deng, Y. Shao, Y. Fang, Y. Bai, C. Wang and J. Huang, Adv. Mater., 2017, 29(26), 1700607 CrossRef PubMed.
- N. Yan, Y. Gao, J. Yang, Z. Fang, J. Feng, X. Wu, T. Chen and S. Liu, Angew. Chem., Int. Ed., 2022, 62(11), e202216668 CrossRef PubMed.
- J. K. Wang, H. Y. Hou, Y. Q. Li and J. X. Tang, Nanoscale, 2020, 12, 17149–17164 RSC.
- Y. Wang, Y. Chen, T. Zhang, X. Wang and Y. Zhao, Adv. Mater., 2020, 32, 2001025 CrossRef CAS PubMed.
- N. A. N. Ouedraogo, Y. Chen, Y. Y. Xiao, Q. Meng, C. B. Han, H. Yan and Y. Zhang, Nano Energy, 2020, 67, 104249 CrossRef CAS.
- G. Niu, W. Li, J. Li, X. Liang and L. Wang, RSC Adv., 2017, 7, 17473–17479 RSC.
- D. Liu, Z. Shao, C. Li, S. Pang, Y. Yan and G. Cui, Small Struct., 2021, 2, 2000089 CrossRef CAS.
- H. Gaonkar, J. Zhu, R. Kottokkaran, B. Bhageri, M. Noack and V. Dalal, ACS Appl. Energy Mater., 2020, 3, 3497–3503 CrossRef CAS.
- Z. Yao, W. Zhao and S. Liu, J. Mater. Chem. A, 2021, 9, 11124–11144 RSC.
- N. J. Jeon, J. H. Noh, Y. C. Kim, W. S. Yang, S. Ryu and S. Il Seok, Nat. Mater., 2014, 13, 897–903 CrossRef CAS PubMed.
- Y. M. Xie, C. Ma, X. Xu, M. Li, Y. Ma, J. Wang, H. T. Chandran, C. S. Lee and S. W. Tsang, Nano Res., 2019, 12, 1033–1039 CrossRef CAS.
-
E. Vega, M. Mollar and B. Mari, 2015 3rd International Renewable and Sustainable Energy Conference (IRSEC) DOI:10.1109/IRSEC.2015.7455117.
- M. Hu, C. Bi, Y. Yuan, Y. Bai and J. Huang, Adv. Sci., 2016, 3, 1500301 CrossRef PubMed.
- P. Kour, M. Chenna Reddy, R. Naphade and S. Ogale, APL Mater., 2018, 6, 50 Search PubMed.
- A. J. Knight, J. Borchert, R. D. J. Oliver, J. B. Patel, P. G. Radaelli, H. J. Snaith, M. B. Johnston and L. M. Herz, ACS Energy Lett., 2021, 6, 799–808 CrossRef CAS PubMed.
- H. Zhang, X. Fu, Y. Tang, H. Wang, C. Zhang, W. W. Yu, X. Wang, Y. Zhang and M. Xiao, Nat. Commun., 2019, 10(1), 1088 CrossRef CAS PubMed.
- Z. Li, M. Yang, J. S. Park, S. H. Wei, J. J. Berry and K. Zhu, Chem. Mater., 2016, 28, 284–292 CrossRef CAS.
- D. R. Ceratti, Y. Rakita, L. Cremonesi, R. Tenne, V. Kalchenko, M. Elbaum, D. Oron, M. A. C. Potenza, G. Hodes and D. Cahen, Adv. Mater., 2017, 30(10), 1706273 CrossRef PubMed.
- X. Wang, Y. Chen, T. Zhang, X. Wang, Y. Wang, M. Kan, Y. Miao, H. Chen, X. Liu, X. Wang, J. Shi, L. Zhang and Y. Zhao, ACS Energy Lett., 2021, 6, 2735–2741 CrossRef CAS.
- T. Imran, S. Rauf, H. Raza, L. Aziz, R. Chen, S. Liu, J. Wang, M. A. Ahmad, S. Zhang, Y. Zhang, Z. Liu and W. Chen, Adv. Energy Mater., 2022, 12, 2200305 CrossRef CAS.
- T. Wang, Q. Tai, X. Guo, J. Cao, C. K. Liu, N. Wang, D. Shen, Y. Zhu, C. S. Lee and F. Yan, ACS Energy Lett., 2020, 5, 1741–1749 CrossRef CAS.
- T. Wu, X. Liu, X. He, Y. Wang, X. Meng, T. Noda, X. Yang and L. Han, Sci. China: Chem., 2020, 63, 107–115 CrossRef CAS.
- Q. Tai, X. Guo, G. Tang, P. You, T. W. Ng, D. Shen, J. Cao, C. K. Liu, N. Wang, Y. Zhu, C. S. Lee and F. Yan, Angew. Chem., Int. Ed., 2019, 58, 806–810 CrossRef CAS PubMed.
- J. Tong, Q. Jiang, A. J. Ferguson, A. F. Palmstrom, X. Wang, J. Hao, S. P. Dunfield, A. E. Louks, S. P. Harvey, C. Li, H. Lu, R. M. France, S. A. Johnson, F. Zhang, M. Yang, J. F. Geisz, M. D. McGehee, M. C. Beard, Y. Yan, D. Kuciauskas, J. J. Berry and K. Zhu, Nat. Energy, 2022, 7, 642–651 CrossRef CAS.
- H. Dong, C. Ran, W. Gao, M. Li, Y. Xia and W. Huang, eLight, 2023, 3, 1–16 CrossRef PubMed.
- A. Rajagopal, R. J. Stoddard, H. W. Hillhouse and A. K. Y. Jen, J. Mater. Chem. A, 2019, 7, 16285–16293 RSC.
- Y. Zheng, R. Su, Z. Xu, D. Luo, H. Dong, B. Jiao, Z. Wu, Q. Gong and R. Zhu, Sci. Bull., 2019, 64, 1255–1261 CrossRef CAS PubMed.
- S. Aina, B. Villacampa and M. Bernechea, Mater. Adv., 2021, 2, 4140–4151 RSC.
- W. Ke and M. G. Kanatzidis, Nat. Commun., 2019, 10, 965 CrossRef PubMed.
- C. C. Stoumpos, C. D. Malliakas and M. G. Kanatzidis, Inorg. Chem., 2013, 52, 9019–9038 CrossRef CAS PubMed.
- H. H. Fang, S. Adjokatse, S. Shao, J. Even and M. A. Loi, Nat. Commun., 2018, 9, 1–8 CrossRef PubMed.
- G. E. Eperon, S. N. Habisreutinger, T. Leijtens, B. J. Bruijnaers, J. J. Van Franeker, D. W. Dequilettes, S. Pathak, R. J. Sutton, G. Grancini, D. S. Ginger, R. A. J. Janssen, A. Petrozza and H. J. Snaith, ACS Nano, 2015, 9, 9380–9393 CrossRef CAS PubMed.
- S. Wozny, M. Yang, A. M. Nardes, C. C. Mercado, S. Ferrere, M. O. Reese, W. Zhou and K. Zhu, Chem. Mater., 2015, 27, 4814–4820 CrossRef CAS.
- W. Kaiser, D. Ricciarelli, E. Mosconi, A. A. Alothman, F. Ambrosio and F. De Angelis, J. Phys. Chem. Lett., 2022, 13, 2321–2329 CrossRef CAS PubMed.
- Y. Liu, P. A. Chen, X. Qiu, J. Guo, J. Xia, H. Wei, H. Xie, S. Hou, M. He, X. Wang, Z. Zeng, L. Jiang, L. Liao and Y. Hu, iScience, 2022, 25(4), 104109 CrossRef CAS PubMed.
- Y. Yang, C. Liu, Y. Ding, B. Ding, J. Xu, A. Liu, J. Yu, L. Grater, H. Zhu, S. S. Hadke, V. K. Sangwan, A. S. R. Bati, X. Hu, J. Li, S. M. Park, M. C. Hersam, B. Chen, M. K. Nazeeruddin, M. G. Kanatzidis and E. H. Sargent, Nat. Energy, 2024, 9(3), 316–323 CrossRef CAS.
- Z. Zhu, X. Jiang, D. Yu, N. Yu, Z. Ning and Q. Mi, ACS Energy Lett., 2022, 7, 2079–2083 CrossRef CAS.
- W. Ayaydah, E. Raddad and Z. Hawash, Micromachines, 2023, 14(4), 806 CrossRef PubMed.
- Z. Yu, J. Wang, B. Chen, M. A. Uddin, Z. Ni, G. Yang and J. Huang, Adv. Mater., 2022, 34(49), 2205769 CrossRef CAS PubMed.
- H. Lee, S. B. Kang, S. Lee, K. Zhu and D. H. Kim, Nano Convergence, 2023, 10(1), 27 CrossRef CAS PubMed.
- R. Prasanna, T. Leijtens, S. P. Dunfield, J. A. Raiford, E. J. Wolf, S. A. Swifter, J. Werner, G. E. Eperon, C. de Paula, A. F. Palmstrom, C. C. Boyd, M. F. A. M. van Hest, S. F. Bent, G. Teeter, J. J. Berry and M. D. McGehee, Nat. Energy, 2019, 4, 939–947 CrossRef CAS.
- P. Wu, J. Wen, Y. Wang, Z. Liu, R. Lin, H. Li, H. Luo and H. Tan, Adv. Energy Mater., 2022, 12(48), 2202948 CrossRef CAS.
- Q. Wali, N. K. Elumalai, Y. Iqbal, A. Uddin and R. Jose, Renewable Sustainable Energy Rev., 2018, 84, 89–110 CrossRef CAS.
- M. Zhang and Z. Lin, Energy Environ. Sci., 2022, 15, 3152–3170 RSC.
- M. Yang, D. H. Kim, T. R. Klein, Z. Li, M. O. Reese, B. J. Tremolet De Villers, J. J. Berry, M. F. A. M. Van Hest and K. Zhu, ACS Energy Lett., 2018, 3, 322–328 CrossRef CAS.
- Z. Li, T. R. Klein, D. H. Kim, M. Yang, J. J. Berry, M. F. A. M. Van Hest and K. Zhu, Nat. Rev. Mater., 2018, 3(4), 18017 CrossRef CAS.
- R. K. Kothandaraman, Y. Jiang, T. Feurer, A. N. Tiwari and F. Fu, Small Methods, 2020, 4(10), 2000395 CrossRef CAS.
-
Z. Song and Y. Yan, Hybrid Perovskite Solar Cells, Wiley, 2021, pp. 509–539 Search PubMed.
- H. Li, Y. Wang, H. Gao, M. Zhang, R. Lin, P. Wu, K. Xiao and H. Tan, eLight, 2022, 2(1), 21 CrossRef.
- L. Gil-Escrig, S. Hu, K. P. S. Zanoni, A. Paliwal, M. A. Hernández-Fenollosa, C. Roldán-Carmona, M. Sessolo, A. Wakamiya and H. J. Bolink, ACS Mater. Lett., 2022, 4, 2638–2644 CrossRef CAS PubMed.
- B. Chen, Z. Yu, A. Onno, Z. Yu, S. Chen, J. Wang, Z. C. Holman and J. Huang, Sci. Adv., 2022, 8, eadd0377 CrossRef CAS PubMed.
- T. Li, J. Xu, R. Lin, S. Teale, H. Li, Z. Liu, C. Duan, Q. Zhao, K. Xiao, P. Wu, B. Chen, S. Jiang, S. Xiong, H. Luo, S. Wan, L. Li, Q. Bao, Y. Tian, X. Gao, J. Xie, E. H. Sargent and H. Tan, Nat. Energy, 2023, 8(6), 610–620 CrossRef CAS.
- Y. Wang, R. Lin, X. Wang, C. Liu, Y. Ahmed, Z. Huang, Z. Zhang, H. Li, M. Zhang, Y. Gao, H. Luo, P. Wu, H. Gao, X. Zheng, M. Li, Z. Liu, W. Kong, L. Li, K. Liu, M. I. Saidaminov, L. Zhang and H. Tan, Nat. Commun., 2023, 14, 1819 CrossRef CAS PubMed.
-
J. A. Dantzig and M. Rappaz, Solidification, EPFL Press, 2nd edn, 2016 Search PubMed.
- F. Yang, D. Jang, L. Dong, S. Qiu, A. Distler, N. Li, C. J. Brabec and H. J. Egelhaaf, Adv. Energy Mater., 2021, 11 Search PubMed.
- Z. Lin, Y. Su, R. Dai, G. Liu, J. Yang, W. Sheng, Y. Zhong, L. Tan and Y. Chen, ACS Appl. Mater. Interfaces, 2021, 13, 15420–15428 CrossRef CAS PubMed.
- X. Cao, L. Zhi, Y. Li, F. Fang, X. Cui, L. Ci, K. Ding and J. Wei, ACS Appl. Energy Mater., 2018, 1, 868–875 CrossRef CAS.
- Y. Yang, J. Wu, X. Wang, Q. Guo, X. Liu, W. Sun, Y. Wei, Y. Huang, Z. Lan, M. Huang, J. Lin, H. Chen and Z. Wei, Adv. Mater., 2020, 32(7), 1904347 CrossRef CAS PubMed.
- N. T. K. Thanh, N. Maclean and S. Mahiddine, Chem. Rev., 2014, 114, 7610–7630 CrossRef CAS PubMed.
- C. Liu, Y. B. Cheng and Z. Ge, Chem. Soc. Rev., 2020, 49, 1653–1687 RSC.
- Y. Yuan, J. Ni, J. Yin, J. Guan, X. Zhou, Y. Liu, Y. Ding, H. Cai and J. Zhang, ACS Appl. Mater. Interfaces, 2020, 12, 48861–48873 CrossRef PubMed.
- Y. Yun, F. Wang, H. Huang, Y. Fang, S. Liu, W. Huang, Z. Cheng, Y. Liu, Y. Cao, M. Gao, L. Zhu, L. Wang, T. Qin and W. Huang, Adv. Mater., 2020, 32(14), 1907123 CrossRef CAS PubMed.
- Q. An, F. Paulus, D. Becker-Koch, C. Cho, Q. Sun, A. Weu, S. Bitton, N. Tessler and Y. Vaynzof, Matter, 2021, 4, 1683–1701 CrossRef CAS.
- Z. Yang, A. Rajagopal, C. C. Chueh, S. B. Jo, B. Liu, T. Zhao and A. K. Y. Jen, Adv. Mater., 2016, 28, 8990–8997 CrossRef CAS PubMed.
- T. Leijtens, R. Prasanna, K. A. Bush, G. E. Eperon, J. A. Raiford, A. Gold-Parker, E. J. Wolf, S. A. Swifter, C. C. Boyd, H. P. Wang, M. F. Toney, S. F. Bent and M. D. McGehee, Sustain, Energy Fuels, 2018, 2, 2450–2459 CAS.
-
Z. Song, D. Zhao, C. Chen, R. H. Ahangharnejhad, C. Li, K. Ghimire, N. J. Podraza, M. J. Heben, K. Zhu and Y. Yan, in 2019 IEEE 46th Photovoltaic Specialists Conference (PVSC), 2019, pp. 743–746.
- D. Zhao, C. Chen, C. Wang, M. M. Junda, Z. Song, C. R. Grice, Y. Yu, C. Li, B. Subedi, N. J. Podraza, X. Zhao, G. Fang, R. G. Xiong, K. Zhu and Y. Yan, Nat. Energy, 2018, 3, 1093–1100 CrossRef CAS.
- B. Abdollahi Nejand, I. M. Hossain, M. Jakoby, S. Moghadamzadeh, T. Abzieher, S. Gharibzadeh, J. A. Schwenzer, P. Nazari, F. Schackmar, D. Hauschild, L. Weinhardt, U. Lemmer, B. S. Richards, I. A. Howard and U. W. Paetzold, Adv. Energy Mater., 2020, 10(5), 1902583 CrossRef CAS.
- C. Wang, Y. Zhao, T. Ma, Y. An, R. He, J. Zhu, C. Chen, S. Ren, F. Fu, D. Zhao and X. Li, Nat. Energy, 2022, 7, 744–753 CrossRef CAS.
- D. Zhao, Y. Yu, C. Wang, W. Liao, N. Shrestha, C. R. Grice, A. J. Cimaroli, L. Guan, R. J. Ellingson, K. Zhu, X. Zhao, R. G. Xiong and Y. Yan, Nat. Energy, 2017, 2(4), 17018 CrossRef CAS.
- C. J. Bartel, C. Sutton, B. R. Goldsmith, R. Ouyang, C. B. Musgrave, L. M. Ghiringhelli and M. Scheffler, Sci. Adv., 2024, 5, eaav0693 CrossRef PubMed.
- A. R. Marshall, H. C. Sansom, M. M. McCarthy, J. H. Warby, O. J. Ashton, B. Wenger and H. J. Snaith, Sol. RRL, 2021, 5, 2000599 CrossRef CAS.
- J. Wen, Y. Zhao, Z. Liu, H. Gao, R. Lin, S. Wan, C. Ji, K. Xiao, Y. Gao, Y. Tian, J. Xie, C. J. Brabec and H. Tan, Adv. Mater., 2022, 34(26), 2110356 CrossRef CAS PubMed.
- G. E. Eperon, T. Leijtens, K. A. Bush, R. Prasanna, T. Green, J. T.-W. Wang, D. P. McMeekin, G. Volonakis, R. L. Milot, R. May, A. Palmstrom, D. J. Slotcavage, R. A. Belisle, J. B. Patel, E. S. Parrott, R. J. Sutton, W. Ma, F. Moghadam, B. Conings, A. Babayigit, H.-G. Boyen, S. Bent, F. Giustino, L. M. Herz, M. B. Johnston, M. D. McGehee and H. J. Snaith, Science, 1979, 2016(354), 861–865 Search PubMed.
- S. Moghadamzadeh, I. M. Hossain, T. Duong, S. Gharibzadeh, T. Abzieher, H. Pham, H. Hu, P. Fassl, U. Lemmer, B. A. Nejand and U. W. Paetzold, J. Mater. Chem. A, 2020, 8, 24608–24619 RSC.
- H. Hu, S. Moghadamzadeh, R. Azmi, Y. Li, M. Kaiser, J. C. Fischer, Q. Jin, J. Maibach, I. M. Hossain, U. W. Paetzold and B. Abdollahi Nejand, Adv. Funct. Mater., 2022, 32(12), 2107650 CrossRef CAS.
- H. Chen, A. Maxwell, C. Li, S. Teale, B. Chen, T. Zhu, E. Ugur, G. Harrison, L. Grater, J. Wang, Z. Wang, L. Zeng, S. M. Park, L. Chen, P. Serles, R. A. Awni, B. Subedi, X. Zheng, C. Xiao, N. J. Podraza, T. Filleter, C. Liu, Y. Yang, J. M. Luther, S. De Wolf, M. G. Kanatzidis, Y. Yan and E. H. Sargent, Nature, 2023, 613, 676–681 CrossRef CAS PubMed.
- R. Lin, K. Xiao, Z. Qin, Q. Han, C. Zhang, M. Wei, M. I. Saidaminov, Y. Gao, J. Xu, M. Xiao, A. Li, J. Zhu, E. H. Sargent and H. Tan, Nat. Energy, 2019, 4, 864–873 CrossRef CAS.
- Z. Yang, Z. Yu, H. Wei, X. Xiao, Z. Ni, B. Chen, Y. Deng, S. N. Habisreutinger, X. Chen, K. Wang, J. Zhao, P. N. Rudd, J. J. Berry, M. C. Beard and J. Huang, Nat. Commun., 2019, 10(1), 4498 CrossRef PubMed.
- Q. Wang, Y. Xu, L. Zhang, A. Yang, T. Bai, F. Liu, M. Lyu and J. Zhu, ACS Appl. Energy Mater., 2022, 5, 3110–3118 CrossRef CAS.
- N. D. Pham, V. T. Tiong, D. Yao, W. Martens, A. Guerrero, J. Bisquert and H. Wang, Nano Energy, 2017, 41, 476–487 CrossRef CAS.
- J. Tong, Z. Song, D. Hoe Kim, X. Chen, C. Chen, A. F. Palmstrom, P. F. Ndione, M. O. Reese, S. P. Dunfield, O. G. Reid, J. Liu, F. Zhang, S. P. Harvey, Z. Li, S. T. Christensen, G. Teeter, D. Zhao, M. M. Al-Jassim, M. F. A. M. van Hest, M. C. Beard, S. E. Shaheen, J. J. Berry, Y. Yan and K. Zhu, Science, 2019, 364(6439), 475–479 CrossRef CAS PubMed.
- Z. Chang, D. Zheng, S. Zhao, L. Wang, S. Wu, L. Liu, Z. Li, L. Zhang, Q. Dong, H. Wang, S. Wang, K. Wang and S. Liu, Adv. Funct. Mater., 2023, 33(22), 2214983 CrossRef CAS.
- R. Lin, J. Xu, M. Wei, Y. Wang, Z. Qin, Z. Liu, J. Wu, K. Xiao, B. Chen, S. M. Park, G. Chen, H. R. Atapattu, K. R. Graham, J. Xu, J. Zhu, L. Li, C. Zhang, E. H. Sargent and H. Tan, Nature, 2022, 603, 73–78 CrossRef CAS PubMed.
- L. Yan, Y. Li, S. Li, X. Sun, Y. Li, X. Han, M. Huang and X. Tao, J. Mater. Chem. A, 2022, 10, 14799–14809 RSC.
- M. Wei, K. Xiao, G. Walters, R. Lin, Y. Zhao, M. I. Saidaminov, P. Todorović, A. Johnston, Z. Huang, H. Chen, A. Li, J. Zhu, Z. Yang, Y. K. Wang, A. H. Proppe, S. O. Kelley, Y. Hou, O. Voznyy, H. Tan and E. H. Sargent, Adv. Mater., 2020, 32(12), 1907058 CrossRef CAS PubMed.
- J. Cameron and P. J. Skabara, Mater. Horiz., 2020, 7, 1759–1772 RSC.
- M. A. Mahmud, J. Zheng, S. Tang, C. Liao, G. Wang, J. Bing, T. L. Leung, A. D. Bui, H. Chen, J. Yi, S. P. Bremner, H. T. Nguyen and A. W. Y. Ho-Baillie, ACS Energy Lett., 2023, 8, 21–30 CrossRef CAS.
- Y. Yao, F. Lv, L. Luo, L. Liao, G. Wang, D. Liu, C. Xu, G. Zhou, X. Zhao and Q. Song, Sol. RRL, 2020, 4, 1900396 CrossRef CAS.
- Y. Wang, S. Gu, G. Liu, L. Zhang, Z. Liu, R. Lin, K. Xiao, X. Luo, J. Shi, J. Du, F. Meng, L. Li, Z. Liu and H. Tan, Sci. China: Chem., 2021, 64, 2025–2034 CrossRef CAS.
- H. Bi, Y. Fujiwara, G. Kapil, D. Tavgeniene, Z. Zhang, L. Wang, C. Ding, S. R. Sahamir, A. K. Baranwal, Y. Sanehira, K. Takeshi, G. Shi, T. Bessho, H. Segawa, S. Grigalevicius, Q. Shen and S. Hayase, Adv. Funct. Mater., 2023, 33(32), 2300089 CrossRef CAS.
- H. Gao, Q. Lu, K. Xiao, Q. Han, R. Lin, Z. Liu, H. Li, L. Li, X. Luo, Y. Gao, Y. Wang, J. Wen, Z. Zou, Y. Zhou and H. Tan, Sol. RRL, 2021, 5(12), 2100814 CrossRef CAS.
- J. H. Heo and S. H. Im, Adv. Mater., 2016, 28, 5121–5125 CrossRef CAS PubMed.
- C.-Y. Chang, B.-C. Tsai, Y.-C. Hsiao, M.-Z. Lin and H.-F. Meng, Nano Energy, 2019, 55, 354–367 CrossRef CAS.
- F. Jiang, T. Liu, B. Luo, J. Tong, F. Qin, S. Xiong, Z. Li and Y. Zhou, J. Mater. Chem. A, 2016, 4, 1208–1213 RSC.
- R. Sheng, M. T. Hörantner, Z. Wang, Y. Jiang, W. Zhang, A. Agosti, S. Huang, X. Hao, A. Ho-Baillie, M. Green and H. J. Snaith, J. Phys. Chem. C, 2017, 121, 27256–27262 CrossRef CAS.
- D. Forgács, L. Gil-Escrig, D. Pérez-Del-Rey, C. Momblona, J. Werner, B. Niesen, C. Ballif, M. Sessolo and H. J. Bolink, Adv. Energy Mater., 2017, 7(8), 1602121 CrossRef.
- C. Li, Z. S. Wang, H. L. Zhu, D. Zhang, J. Cheng, H. Lin, D. Ouyang and W. C. H. Choy, Adv. Energy Mater., 2018, 8(36), 1801954 CrossRef.
- Z. Yu, Z. Yang, Z. Ni, Y. Shao, B. Chen, Y. Lin, H. Wei, Z. J. Yu, Z. Holman and J. Huang, Nat. Energy, 2020, 5, 657–665 CrossRef CAS.
- D. Zhao, C. Wang, Z. Song, Y. Yu, C. Chen, X. Zhao, K. Zhu and Y. Yan, ACS Energy Lett., 2018, 3, 305–306 CrossRef CAS.
- S. Moghadamzadeh, I. M. Hossain, M. Loy, D. B. Ritzer, H. Hu, D. Hauschild, A. Mertens, J. P. Becker, A. A. Haghighirad, E. Ahlswede, L. Weinhardt, U. Lemmer, B. A. Nejand and U. W. Paetzold, ACS Appl. Mater. Interfaces, 2021, 13, 46488–46498 CrossRef CAS PubMed.
- A. Rajagopal, Z. Yang, S. B. Jo, I. L. Braly, P. W. Liang, H. W. Hillhouse and A. K. Y. Jen, Adv. Mater., 2017, 29(34), 1702140 CrossRef PubMed.
-
Y.-H. Chiang, K. Frohna, H. Salway, A. Abfalterer, B. Roose, M. Anaya and S. D. Stranks, Efficient all-perovskite tandem solar cells by dual-interface optimisation of vacuum-deposited wide-bandgap perovskite, arXiv, 2022, preprint, arXiv:2208.03556 DOI:10.48550/arXiv.2208.03556.
- D. Vidyasagar, Y. Yun, J. Yu Cho, H. Lee, K. Won Kim, Y. Tae Kim, S. Woong Yang, J. Jung, W. Chang Choi, S. Kim, R. Kumar Gunasekaran, S. B. Kang, K. Heo, D. H. Kim, J. Heo and S. Lee, J. Energy Chem., 2024, 88, 317–326 CrossRef CAS.
- L. Qiao, T. Ye, P. Wang, T. Wang, L. Zhang, R. Sun, W. Kong and X. Yang, Adv. Funct. Mater., 2024, 34(7), 2308908 CrossRef CAS.
- Z. Yi, W. Wang, R. He, J. Zhu, W. Jiao, Y. Luo, Y. Xu, Y. Wang, Z. Zeng, K. Wei, J. Zhang, S. W. Tsang, C. Chen, W. Tang and D. Zhao, Energy Environ. Sci., 2023, 17, 202–209 RSC.
- H. Guan, S. Zhou, S. Fu, D. Pu, X. Chen, Y. Ge, S. Wang, C. Wang, H. Cui, J. Liang, X. Hu, W. Meng, G. Fang and W. Ke, Adv. Mater., 2024, 36(1), 2307987 CrossRef CAS PubMed.
- T. Ma, H. Wang, Z. Wu, Y. Zhao, C. Chen, X. Yin, L. Hu, F. Yao, Q. Lin, S. Wang, D. Zhao, X. Li and C. Wang, Adv. Mater., 2024, 36(3), 2308240 CrossRef CAS PubMed.
- H. Sun, K. Xiao, H. Gao, C. Duan, S. Zhao, J. Wen, Y. Wang, R. Lin, X. Zheng, H. Luo, C. Liu, P. Wu, W. Kong, Z. Liu, L. Li and H. Tan, Adv. Mater., 2024, 36(2), 2308706 CrossRef CAS PubMed.
- S. Lee, M. Y. Woo, C. Kim, K. W. Kim, H. Lee, S. B. Kang, J. M. Im, M. J. Jeong, Y. Hong, J. W. Yoon, S. Y. Kim, K. Heo, K. Zhu, J. S. Park, J. H. Noh and D. H. Kim, Chem. Eng. J., 2024, 479, 147587 CrossRef CAS.
- F. Yang, P. Tockhorn, A. Musiienko, F. Lang, D. Menzel, R. Macqueen, E. Köhnen, K. Xu, S. Mariotti, D. Mantione, L. Merten, A. Hinderhofer, B. Li, D. R. Wargulski, S. P. Harvey, J. Zhang, F. Scheler, S. Berwig, M. Roß, J. Thiesbrummel, A. Al-Ashouri, K. O. Brinkmann, T. Riedl, F. Schreiber, D. Abou-Ras, H. Snaith, D. Neher, L. Korte, M. Stolterfoht and S. Albrecht, Adv. Mater., 2024, 36(6), 2307743 CrossRef CAS PubMed.
- G. Su, R. Yu, Y. Dong, Z. He, Y. Zhang, R. Wang, Q. Dang, S. Sha, Q. Lv, Z. Xu, Z. Liu, M. Li and Z. Tan, Adv. Energy Mater., 2024, 14(4), 2303344 CrossRef CAS.
- S. Li, Z. Zheng, J. Ju, S. Cheng, F. Chen, Z. Xue, L. Ma and Z. Wang, Adv. Mater., 2024, 36(9), 2307701 CrossRef CAS PubMed.
- D. Yu, M. Pan, G. Liu, X. Jiang, X. Wen, W. Li, S. Chen, W. Zhou, H. Wang, Y. Lu, M. Ma, Z. Zang, P. Cheng, Q. Ji, F. Zheng and Z. Ning, Nat. Energy, 2024, 9(3), 298–307 CrossRef CAS.
- D. Pu, S. Zhou, H. Guan, P. Jia, G. Chen, H. Fang, S. Fu, C. Wang, H. Hushvaktov, A. Jumabaev, W. Meng, X. Wang, G. Fang and W. Ke, Adv. Funct. Mater., 2024, 34(17), 2314349 CrossRef CAS.
- Z. Xie, S. Chen, Y. Pei, L. Li, S. Zhang and P. Wu, Chem. Eng. J., 2024, 482, 148638 CrossRef CAS.
- A. Maxwell, H. Chen, L. Grater, C. Li, S. Teale, J. Wang, L. Zeng, Z. Wang, S. M. Park, M. Vafaie, S. Sidhik, I. W. Metcalf, Y. Liu, A. D. Mohite, B. Chen and E. H. Sargent, ACS Energy Lett., 2024, 9, 520–527 CrossRef CAS.
- W. Yan, C. Li, C. Peng, S. Tan, J. Zhang, H. Jiang, F. Xin, F. Yue and Z. Zhou, Adv. Mater., 2024, 36(18), 2312170 CrossRef CAS PubMed.
- X. Lv, W. Li, J. Zhang, Y. Yang, X. Jia, Y. Ji, Q. Lin, W. Huang, T. Bu, Z. Ren, C. Yao, F. Huang, Y. B. Cheng and J. Tong, J. Energy Chem., 2024, 93, 64–70 CrossRef CAS.
- X. Jiang, Q. Zhou, Y. Lu, H. Liang, W. Li, Q. Wei, M. Pan, X. Wen, X. Wang, W. Zhou, D. Yu, H. Wang, N. Yin, H. Chen, H. Li, T. Pan, M. Ma, G. Liu, W. Zhou, Z. Su, Q. Chen, F. Fan, F. Zheng, X. Gao, Q. Ji and Z. Ning, Natl. Sci. Rev., 2024, 11(5), nwae055 CrossRef PubMed.
- Q. Sun, Z. Zhang, H. Yu, J. Huang, X. Li, L. Dai, Q. Wang, Y. Shen and M. Wang, Energy Environ. Sci., 2024, 17(7), 2512–2520 RSC.
- P. Jia, G. Chen, G. Li, J. Liang, H. Guan, C. Wang, D. Pu, Y. Ge, X. Hu, H. Cui, S. Du, C. Liang, J. Liao, G. Xing, W. Ke and G. Fang, Adv. Mater., 2024, 2400105 CrossRef PubMed.
- J. Zhou, T. Wen, J. Sun, Z. Shi, C. Zou, Z. Shen, Y. Li, Y. Wang, Y. Lin, S. Yang, F. Liu and Z. Yang, ACS Energy Lett., 2024, 1984–1992 CrossRef CAS.
- Y. Dong, R. Yu, G. Su, Z. Ma, Z. He, R. Wang, Y. Zhang, J. Yang, Y. Gong, M. Li and Z. Tan, Adv. Mater., 2023, 2312704 Search PubMed.
- X. Hu, F. Yao, C. Wang, H. Cui, P. Jia, S. Du, S. Zhou, H. Guan, Q. Lin, W. Ke, C. Tao and G. Fang, Chem. Eng. J., 2024, 151379 CrossRef CAS.
- M. T. Hörantner, T. Leijtens, M. E. Ziffer, G. E. Eperon, M. G. Christoforo, M. D. McGehee and H. J. Snaith, ACS Energy Lett., 2017, 2, 2506–2513 CrossRef.
- A. Singh and A. Gagliardi, Sol. Energy, 2019, 187, 39–46 CrossRef CAS.
- L. Liu, P. Liu, S. Ullah, S. E. Yang, H. Guo, L. Wang, X. Wang and Y. Chen, Sol. Energy, 2021, 228, 274–281 CrossRef CAS.
- C. E. Torrence, C. S. Libby, W. Nie and J. S. Stein, iScience, 2023, 26(1), 105807 CrossRef PubMed.
- J. Madan, Shivani, R. Pandey and R. Sharma, Sol. Energy, 2020, 197, 212–221 CrossRef CAS.
-
A. Hossain, M. M. Hasan, S. Rahman and M. A. M. Hossain, Fully Lead-Free All Perovskite Tandem Solar Cell with Improved Efficiency: Device Simulation Using SCAPS-1D, 2020 IEEE Region 10 Symposium (TENSYMP), Dhaka, Bangladesh, 2020, pp. 1221–1224 DOI:10.1109/TENSYMP50017.2020.9230927.
- N. Singh, A. Agarwal and M. Agarwal, Sol. Energy, 2020, 208, 399–410 CrossRef CAS.
- M. T. Islam, M. R. Jani, S. Rahman, K. M. Shorowordi, S. S. Nishat, D. Hodges, S. Banerjee, H. Efstathiadis, J. Carbonara and S. Ahmed, SN Appl. Sci., 2021, 3(4), 504 CrossRef CAS.
- A. U. Duha and M. F. Borunda, Opt. Mater., 2022, 123, 111891 CrossRef CAS.
- M. Soldera, A. Koffman-Frischknecht and K. Taretto, J. Phys. D: Appl. Phys., 2020, 53, 315104 CrossRef CAS.
- H. Q. Tan, X. Zhao, E. Birgersson, F. Lin and H. Xue, Sol. Energy, 2021, 216, 589–600 CrossRef CAS.
- G. Shankar, P. Kumar and B. Pradhan, Mater. Today Sustainable, 2022, 20, 100241 CrossRef.
- M. Moradbeigi and M. Razaghi, Sci. Rep., 2022, 12(1), 6733 CrossRef CAS PubMed.
- R. Pandey, S. Sharma, J. Madan and R. Sharma, J. Micromech. Microeng., 2022, 32, 014004 CrossRef CAS.
- S. Yadav, M. A. Kareem, H. K. Kodali, D. Agarwal, A. Garg, A. Verma and K. S. Nalwa, Sol. Energy Mater. Sol. Cells, 2022, 242, 111780 CrossRef CAS.
- X. Luo, Y. Hu, Z. Lin, X. Guo, S. Zhang, C. Shou, Z. Hu, X. Zhao, Y. Hao and J. Chang, Sol. RRL, 2023, 7(10), 2300081 CrossRef CAS.
- F. Gota, S. X. An, H. Hu, B. Abdollahi Nejand and U. W. Paetzold, Adv. Opt. Mater., 2023, 11(3), 2201691 CrossRef CAS.
- G. Shankar, P. Kumar and B. Pradhan, Energy Fuels, 2023, 37(16), 12291–12300 CrossRef CAS.
- W. Wang, G. Yu and S. Attique, Sol. RRL, 2023, 7(7), 2201064 CrossRef CAS.
- Y. El Arfaoui, M. Khenfouch and N. Habiballah, J. Opt., 2024 DOI:10.1007/s12596-023-01647-3.
- N. Shrivastav, J. Madan, M. Khalid Hossain, M. D. Albaqami and R. Pandey, Mater. Lett., 2024, 362, 136169 CrossRef CAS.
- M. Moradbeigi and M. Razaghi, Renewable Energy, 2024, 220, 119723 CrossRef CAS.
- X. Yang, W. Zhou, Y. He, Z. Sun, Q. Zeng, H. Yan, Z. Zheng, X. Chen, Z. Tang and J. Zhang, Adv. Funct. Mater., 2024, 2401508 CrossRef.
- Y. El Arfaoui, M. Khenfouch and N. Habiballah, Optik, 2024, 300, 171638 CrossRef CAS.
- S. Ahmed, N. Rahman, M. Dulal Haque, M. Hasan Ali and A. Zafor Md Touhidul Islam, Phys. Scr., 2024, 99, 055520 CrossRef.
- Y. Jiang, S.-C. Yang, Q. Jeangros, S. Pisoni, T. Moser, S. Buecheler, A. N. Tiwari and F. Fu, Joule, 2020, 4, 1087–1103 CrossRef CAS.
- R. Guo, D. Han, W. Chen, L. Dai, K. Ji, Q. Xiong, S. Li, L. K. Reb, M. A. Scheel, S. Pratap, N. Li, S. Yin, T. Xiao, S. Liang, A. L. Oechsle, C. L. Weindl, M. Schwartzkopf, H. Ebert, P. Gao, K. Wang, M. Yuan, N. C. Greenham, S. D. Stranks, S. V. Roth, R. H. Friend and P. Müller-Buschbaum, Nat. Energy, 2021, 6, 977–986 CrossRef CAS.
- Q. Sun, Z. Zhang, T. Zhang, Y. Feng, A. Gu, H. Yu, M. Zhang, X. L. Zhang, J. Zhu, Y. Shen and M. Wang, ACS Energy Lett., 2022, 7, 4215–4223 CrossRef CAS.
|
This journal is © The Royal Society of Chemistry 2024 |
Click here to see how this site uses Cookies. View our privacy policy here.