Constructing polyamide/ceramic composite membranes for highly efficient and selective separation of dyes and salts from solution†
Received
21st February 2024
, Accepted 26th May 2024
First published on 3rd June 2024
Abstract
Membrane separation technology has been recognized as an effective approach to remove dyes from dyeing wastewater that are crucial for improving the quality of the pigmentation effect in the printing and dyeing industry. However, the trade-off between membrane permeability and selectivity is an inherent drawback of molecular separation membranes, which hampers the development of large-scale applications of the membrane separation process. In this work, we provide a facile approach to construct a highly selective polyamide (PA) layer on a ceramic membrane through the interfacial polymerization of branched polyethylenimine (PEI) and trimesoyl chloride (TMC) for the selective separation of dyes and salts from wastewater. With high positive surface zeta-potential (100 mV) and excellent hydrophilicity, the PA/ceramic composite membranes exhibit ultra-high solution permeance (496.4 L m−2 h−1 bar−1) while treating simulated dye/salt aqueous solutions containing 40 ppm Congo red (CR) and 1 g L−1 NaCl, which is 30 times higher compared with commercial polyamide nanofiltration membranes. Interestingly, the separation factor of NaCl to CR of the PA/ceramic composite membranes reaches above 980, which is far superior to the state-of-the-art nanofiltration membranes reported recently. Moreover, PA/ceramic membranes possess a relatively ideal long-term stability, with their permeance remaining at 280 L m−2 h−1 bar−1 after 10 h of testing. Taken together, the PA/ceramic composite membranes are highly promising for dye desalination and purification.
Water impact
The pollution of the environment caused by saline dye wastewater is a critical issue that needs to be addressed urgently. Recovering and purifying dyes via innovative polyamide/ceramic composite membranes is a green and sustainable strategy. We focus on the performance and mechanism of polyamide/ceramic membranes for dye desalination, emphasizing their limitations and future opportunities.
|
1. Introduction
With the vigorous development of the textile industry, the demand for dyes has increased gradually.1,2 Owing to the complex composition and high salinity, a large amount of dyes in dye-contaminated wastewater are difficult to degrade, posing a serious threat to human and animal health and leading to a large waste of resources.3–7 Traditional treatment methods such as biological treatment, oxidation, electrochemical destruction and adsorption have low separation efficiency and cannot obtain valuable resources from textile wastewater.3,8,9 Therefore, it is necessary to develop suitable methods to recycle high value-added materials rather than just remove contaminants.5,10,11 Membrane filtration systems, playing a vital role in wastewater treatment, can be an alternative to achieve this objective, which is gradually replacing traditional separation technology because of its simple operation process and low cost.12–17
Scheme of electrospinning-assisted fabrication of asymmetric PAN supported hydrophilic composite membrane with PEA/PEGDGE/GPTMS functionalized selective layer for oil–water emulsion separation.
Nanofiltration membranes can selectively remove the pollutants in sewage and have high application potential in the advanced treatment of wastewater and can be prepared via interfacial polymerization (IP),18 surface coating,19 and layer-by-layer methods.20 Surface coating is considered a viable option for the preparation of composite membranes and has been extensively investigated. For instance, the permeability of loose nanofiltration membranes based on the active layer of tannin-polyethyleneimine co-deposition is as high as 40.6 L m−2 h−1 bar−1 and has excellent salt and dye separation properties.21 However, the deposition time is extremely long, resulting in a low practical application value in dye and salt separation. Besides, novel porous materials such as covalent organic frameworks (COFs) are also used to fabricate nanofiltration membranes owing to their ordered channel structure. The membranes prepared by Fan et al.22 loaded with COFs had an excellent water permeance of nearly 760 L m−2 h−1 MPa−1 and a dye rejection rate greater than 90%. Moreover, traditional methods of interfacial polymerization with the development of new functional monomers have also been applied for the preparation of composite membranes for dye removal. Wang et al.23 prepared a composite membrane by the conventional interfacial polymerization of 2,2′-benzidinedisulfonic acid (BDSA) and 1,3,5-benzenetricarbonyl trichloride (TMC) and found that the obtained membranes had excellent separation effect on dyes/salt mixtures. Cheng et al.24 improved the membrane permeability by introducing multiple reaction monomers to enlarge the length between the crosslinked networks and modulate the chemical structure of the polyamide active separation layer. But the above methods are not easy to control, and it is still difficult for the separation performance of the obtained membranes to meet the needs. For the manufacture of composite membranes used in the field of textile wastewater, simpler strategies are still needed to achieve higher membrane fluxes while balancing the rejection rates.
Although the role of the support layer has often been overlooked, several studies suggest that substrates can crucially regulate the transport pathway of water and solutes through the composite membrane.25 Wei et al.26 deposited polydimethylsiloxane (PDMS) on macroporous ceramic supports and organic supports, respectively, and found that the ethanol/water permeable evaporation flux of PDMS/Al2O3–ZrO2 was about two times higher than that of the PDMS/blend cellulose acetate (BCA) membrane. Macroporous ceramic membranes are beneficial for providing higher porosity and water permeance. However, there are few reports of polyamide composite membrane formation on a macroporous ceramic membrane substrate using interfacial polymerization methods.
The ceramic support offers excellent chemical and mechanical stability along with favorable water permeability, which are key benefits for separation applications. However, the large pore size, characteristic of the substrates, presents a challenge for the fabrication of composite membranes. A novel method for the preparation of high-performance composite membranes by the interfacial polymerization of polyethyleneimine (PEI) and TMC directly on ceramic supports was explored. PEI with a large number of amine groups can be used as an aqueous monomer to react with TMC and form positively charged selective layers.24,27–29 Charged composite membranes tend to show better hydrophilicity, which are conducive to improving the permeance.25 The long-chain structure and adhesion properties of macromolecular polyethyleneimine reduced the pore size of the ceramic substrate to a certain degree, improved the entanglement of the polyamide with the ceramic-based membranes, and enhanced the compatibility between inorganic materials and organic materials. The PEI filled the ceramic substrate surface, and the chemical bonding and mechanical interlocking at the interface resulted in improved interlayer adhesion between the subsequently formed polyamide (PA) selective layer and the ceramic support layer.30 Furthermore, an appropriate amount of PEI applied to the rough ceramic surface can reduce its roughness, leading to the formation of a defect-free PA membrane. Additionally, the surface of the ceramic support contains a large number of hydroxyl (–OH) groups, and the prepared composite membranes have advantages over polymer-based PA membranes in terms of water permeability and dye/salt separation.
As shown in Fig. 1, a brief fabrication process for nanofiltration membranes and the possible interface reaction between PEI and TMC are presented in detail. The porous ceramic membrane is used as a support due to its low resistance to transport and solvents as well as its excellent chemical and thermal stability. As shown in Fig. 1a, the ceramic membrane is first immersed in the aqueous PEI solution, whereby the long-chain PEI, which contains a large number of amine groups, can bind well to the substrate and carries amine groups on its surface. Then, the ceramic membrane is immersed in an organic solution containing TMC, and the amine groups on the surface of the ceramic membrane undergo an interfacial polymerization reaction with the acyl chloride groups of the organic phase (the reaction process is shown in Fig. 1b), resulting in the formation of a dense selective polyamide layer on the surface of the membrane. The combination of the porous ceramic substrate and the polyamide layer leads to lower transport resistance and the higher separation of dyes and salts, and the solution permeability of the membrane is 30 times higher than that of commercial nanofiltration membranes. Our work provides a new direction for the modification of polyamide membranes, which have great potential for the recovery of high-value substances from dye wastewater.
 |
| Fig. 1 (a) Schematic diagram of the synthesis process of the PA/ceramic membrane. (b) The possible interface reaction that may occur between PEI and TMC. | |
2. Materials and methods
2.1 Materials and chemicals
Polyethyleneimine (PEI), sodium dodecyl benzene sulfonate (SDBS), triethylamine (TEA), 1,3,5-benzenetricarbonyl trichloride (TMC) and hyaluronic acid (HA) were brought from Aladdin company (China). Inorganic salts (MgSO4, MgCl2, Na2SO4, NaCl), dyes (Congo red (CR), Rose Bengal (RB), Brilliant blue (BB), Eriochrome black T (EBT)), ethanol and n-hexane were all brought from Aladdin company (China). No further purification was required for all the chemicals. Organic commercial membranes with molecular weight cut-offs of 500 Da and 700 Da, marked as GC-1 and GC-2, respectively, were purchased from Guochu Technology (Xiamen) Co., Ltd. ceramic film was bought from Shandong Zhong-Europe Membrane Technology Research Co., Ltd. the initial water permeance of the ceramic support was 5000 ± 300 L m−2 h−1 bar−1.
2.2 The manufacture process of the PA/ceramic composite membrane
The preparation process of the PA/ceramic membrane was consistent with the traditional interfacial polymerization methods. Firstly, the ceramic membrane was immersed into a mixed aqueous solution of PEI, SDBS (2.0 wt%) and TEA (2.0 wt%) for 20 min. Subsequently, if there was excess solution on the surface of the film, it was removed with an air spatula. After that, the membrane was immersed into n-hexane solution containing TMC for the reaction. Finally, the modified membrane was stored in RO water until further experiment. All properties of polyamide membranes prepared via interfacial polymerization are influenced by the membrane preparation conditions. Therefore, as shown in Fig. S1,† optimal interfacial polymerization conditions were obtained by regulating the TMC concentration (0.1 wt%, 0.2 wt%, 0.3 wt%, 0.4 wt%, 0.5 wt%), PEI concentration (4 wt%, 6 wt%, 8 wt%, 10 wt%, 12 wt%) and reaction time (1 min, 2 min, 3 min, 4 min, 5 min). The PA/ceramic membranes prepared under optimal conditions were subjected to further separation experiments.
2.3 Separation properties of the composite membranes
The membranes were positioned in the dead-end stirred filter device and sealed to assess the permeation. The effective membrane area of a stainless-steel filtration cell was 8.30 cm2. All the tests were conducted under room temperature, and all the membranes were operated under pressure for 30 min before testing to obtain a stable permeance. The permeate volume was collected over a certain period, and the permeance was calculated (P) by eqn (1).where P is the permeance of the solution (L m−2 h−1 bar−1), V is the solution volume (L), A is the effective filtration area (m2), Δt is the test time (h), and ΔP is the operating pressure (bar), respectively.
Separate properties of membranes were tested using solutions of a variety of dyes and salts. The salt solutions configured during the test were all at a concentration of 1000 ppm. Besides, the concentration of the dye solution was 40 ppm if there is no special explanation. The solute rejection (R) and separation factor (α) was calculated using eqn (2) and (3), respectively.
|
R = (1 − Cp/Cf) × 100% | (2) |
|
α = (1 − Rsalt)/(1 − Rdye) | (3) |
where
R is the rejection of the dye or salt,
Cp and
Cf are the permeate and feed concentration, respectively, and
α refers to the separation factor of salt and dye.
2.4 Long-time stability testing
Using a mixed solution of RB and NaCl as the feed solution, the optimized composite membrane was used in a 10-hour long-term stability.
2.5 Adsorption capacity testing
The composite membrane was immersed in 20 mL of dye solution (20 mg L−1) for 24 h. The equilibrium adsorption capacity (qe) of the composite membrane to the dye can be calculated according to eqn (4) by determining the dye concentration of the feed solution and permeate solution.where qe is the adsorption capacity of the membrane (mg g−1), Cf and Cp are the feed and permeate concentration (mg L−1), respectively, V is the solution volume (L), and m is the quantity of the composite membrane (g).
3. Results and discussion
3.1 Chemical composition
The FTIR spectra of the prepared membrane are given in Fig. 2a. All the PA/ceramic membranes prepared at different PEI concentrations had similar characteristic bands and they are consistent with the typical polyamide membrane. C
O stretching vibrations at approximately 1665 cm−1 were observed, which was the characteristic peak of the amide. This indicated that a polymerization reaction occurred on the ceramic support, forming a complete polyamide separation layer. A broad band at about 3450 cm−1 appeared in all the three membrane spectra, indicating –OH stretching due to the addition of deionized water during the test.
 |
| Fig. 2 (a) FTIR spectra of the membranes, (b) XPS full-spectrum scan of membranes, high resolution XPS spectra: (c) N 1s in the PA/ceramic membrane and (d) C 1s in the PA/ceramic membrane. | |
The surface chemical composition of the prepared membrane was further confirmed by XPS analysis, and the corresponding results are given in Fig. 2b–d. The wide scan elemental spectra of the membranes exhibited that compared with the ceramic membrane, the TFC membrane lacked the characteristic peaks of Al 2p, Al 2s and Si 2s, while it had a stronger characteristic peak of N 1s (Fig. 2b). Fig. 2c and d shows the XPS spectra of N 1s and C 1s of the TFC membrane. The peak at 398.2 eV in Fig. 2c was attributed to the amide bond in the polyamide. The peak appearing at 400.0 eV corresponds to –NH3+, formed by the hydrolysis of unreacted amino groups. The characteristic peaks of 283.8 eV, 284.9 eV and 286.9 eV in Fig. 2d represent C–C, C–N and C
O, respectively. The chemical composition analysis of the PA/ceramic membrane successful confirmed the synthesis of a polyamide active separation layer on the ceramic support.
3.2 Membrane surface characteristics
The surface topography of the ceramic carrier and the PA/ceramic membrane are presented in Fig. 3. From the surface images in Fig. 3a–d, it was observed that the organic separation layers were successfully coated onto the supports. Unlike the abundant spherical particles on the ceramic support surface, the surface of the composite membrane was smoother and uniform because the hole of the substrate was completely covered, which was also verified from the CLSM characterization results (Fig. 3e and f). After interfacial polymerization, the roughness (Ra) of the membrane was reduced from 10.7 nm to 7.7 nm, indicating that the surface became smoother. In addition, polyamide/ceramic composite membranes showed a looser organic separation layer than commercial organic nanofiltration membranes (Fig. S2†) because the ceramic substrate is hydrophilic and the synergistic effect of the strong hydrophilicity of the substrate and the low localized concentration of PEI resulted in the formation of a thinner and looser nanofiltration membrane polyamide layer,31 with a correspondingly higher permeability. It was possible to be verified by the penetration of the water solution into it. Fig. S3† shows the cross sections of the composite membranes, GC-1 and GC-2, respectively. In general, the PA selective layer was constructed on the ceramic substrate successfully.
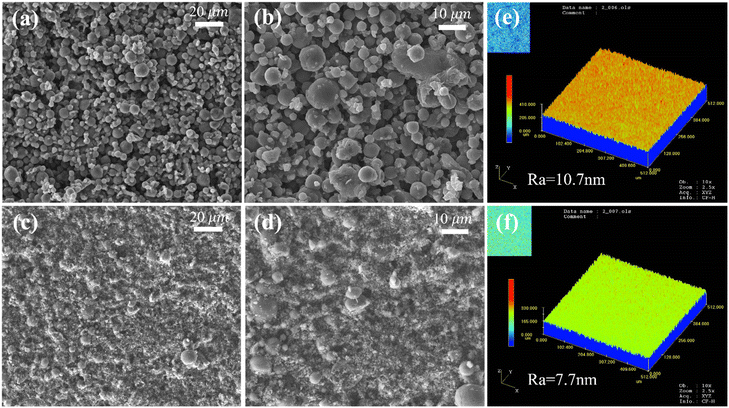 |
| Fig. 3 (a and b) SEM images of the ceramic support, (c and d) SEM images of the polyamide/ceramic membrane. (e and f) CLSM images of the ceramic support and polyamide/ceramic membrane. | |
3.3 Surface properties
The surface potential of commercial NF membranes, the ceramic support and the PA/ceramic membrane are illustrated in Fig. 4. The surface of the ceramic carrier presented a negative charge (the isoelectric point was close to pH = 3), which could be attributed to the hydroxylation reaction after alumina absorbed water. While the PA/ceramic membrane shifts to a strong positive potential (100 mV) due to a large amount of unreacted amine positive groups (–NH3+) from PEI, which was corroborated by the characteristic peak of NH3+ in the XPS data (Fig. 2c). Composite membranes had a stronger charge density than commercial nanofiltration membranes and tended to have better separation performance owing to the Donnan effect.
 |
| Fig. 4 The zeta potential of the ceramic support, the PA/ceramic membrane and two types of commercial NF membrane. | |
The hydrophilicity analysis results of the four membranes mentioned above are illustrated in Fig. 5. Comparing with two types of commercial NF membranes' water contact angle of 31.7° and 38.6°, a water droplet was absorbed rapidly after touching the PA/ceramic composite membrane, leaving a water contact angle of about 0°, which suggested that the modified membrane showed better hydrophilicity. This can be explained by the remaining amino groups in the polyamide, which supports excellent permeability.32–34
 |
| Fig. 5 Hydrophilic characterization: (a) the ceramic support, (b) the PA/ceramic membrane, (c) GC-1, and (d) GC-2. | |
3.4 Separation properties
The separation performance of PA/ceramic composite membranes and two commercial nanofiltration membranes was tested for comparison. As shown in Fig. 6a, the water permeance of PA/ceramic composite membranes was 487.3 L m−2 h−1 bar−1, which was more than 30 times the water permeance of commercial NF membranes with similar rejection properties. The excellent permeability confirmed that ceramic supports were a suitable substrate for the formation of loose composite membranes. At the same time, the interception effect of the three membranes on mixed solutions of different salts and CR was investigated. The results demonstrated that CR was intercepted completely by all the membranes, while the salt rejection showed different performance. Compared to commercial membranes, PA/ceramic composite membranes with a loose structure exhibited satisfactory low-salt repulsion (<2%, all salts) and near-complete interception of the dye, indicating their potential for dye/salt selective separation. However, commercial membranes showed high rejection for several salts, especially for divalent salts with a rejection rate of more than 80%, which made it difficult to meet the needs of selective separation.
 |
| Fig. 6 (a) The separation performance of three types of membranes. The separation performance of PA/ceramic membranes: (b) single salt, (c) single dye, and (d) mixed solutes (dye and salt). | |
The separation performance of the PA/ceramic composite membranes against a single different solute is shown in Fig. 6b and c. The rejection rate of PA/ceramic composite film was in the order NaCl (0.3%) < Na2SO4 (3.3%) < MgCl2 (3.4%) < MgSO4 (5.3%), which was mainly influenced by the Donnan effect35 and the size sieving. According to the results of zeta potential characterization, the polyamide/ceramic composite film is a membrane with a large amount of positive charge. Its repulsion force of the divalent cation (Mg2+) was stronger than that of the monovalent cation (Na+), and the interception capacity of the magnesium salt was stronger than that of sodium salt. Combined with the size screening effect, the hydration radius of SO42− (0.38 nm) was greater than the hydration radius of Cl− (0.33 nm); thus, it was easier for Cl− to pass through the composite membrane than SO42−, finally showing a significant trend of rejection rate. The permeability properties of the composite membrane to different dye solutions were quite different due to the physical structure and chemical properties of the dyes. For example, BB and CR have larger or longer molecular structures, which are easier to tangle or reunite in the membrane surface or pores, thus blocking the membrane pores and causing a decrease in permeance. However, RB and EBT are less branching and cause less degree of membrane fouling.36 Interestingly, the PA/ceramic membranes completely removed all the dyes tested, which revealed that the modified membranes had excellent rejection performance for dyes. Fig. S4† provides the adsorption performance of composite membranes to dyes of different molecular weights. After a 24 h adsorption process, the PA/ceramic composite membranes reached the adsorption equilibrium state for all the four dyes. The adsorption efficiency of the composite film to RB, BB, CR and EBT was less than 0.05 mg g−1, indicating that the interception of the dye by the composite film was mainly due to size sieving and Donnan exclusion.
The filtration effect of the dye/salt binary mixture is further shown in Fig. 6d. The removal rate of binary mixture solutions was similar to that of a single dye or salt solution of its constituents. Moreover, in terms of permeance, the water permeance of the mixed solution was even higher than that of the individual dye, which should be ascribed to the reduction of membrane fouling due to the better distribution of the dye in the salt-water and its interaction with the dye.21 The permeation of all salts was as high as more than 98%, resulting in a separation factor of NaCl to CR for the PA/ceramic composite membranes ranging from 980 to 996. The water permeability and dye/NaCl dehydration rate of PA/ceramic composite films, commercial NF membranes and advanced PA membranes are compared in Fig. 7. Notably, the comprehensive performance of the PA/ceramic composite membrane far exceeded that of the other membranes. Meanwhile, such high permeability can significantly accelerate their salts permeation and thus lead to an efficient dyes/salt separation.
 |
| Fig. 7 Comparison of various membrane separation performances.21,22,37–43 | |
3.5 Stability of the membranes
The effect of filtration pressure on dye desalination was investigated. Membrane filtration performance was evaluated by mixed aqueous solutions of 0.02 g L−1 RB and 1 g L−1 NaCl solution. As shown in Fig. 8a, with the pressure increasing, the permeance decreased accordingly from 430.9 to 387.0 L m−2 h−1 bar−1 since the driving force of permeation was enhanced. The probable cause is loose nanofiltration membranes being compacted under high pressure, contributing to the clogging of the membrane pores. Therefore, the operating pressure of the membrane needs to be controlled in a suitable range, preferably less than 1 bar. Given that the membrane permeance of our developed membrane was much higher than that reported in the literature, our membranes operating at pressures below 1 bar still have highly competitive permeance and contribute to save energy and reduce costs. Overall, the dye/salt separation capacity of the PA/ceramic membranes was maintained at a high level under different pressure conditions.
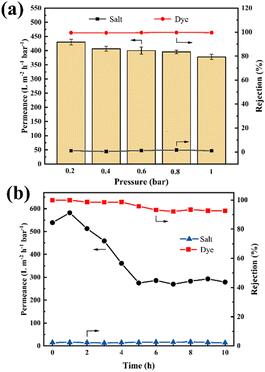 |
| Fig. 8 (a) The effects of filtration pressure on the filtration performance of the membranes. (b) The long-time stability of the PA/ceramic membrane separation performance. | |
The stability of the membrane was also studied with pure water and a mixed solution of RB and NaCl. The membrane was used at 0.1 bar for 10 h to evaluate the stability of the PA/ceramic membrane. As shown in Fig. S5,† the composite membrane kept the permeance stable in pure water. However, the membrane permeance decreased significantly when filtering the dye/salt mixed solution. The permeability of the PA/ceramic membrane decreased by 50% in the first 5 hours due to the dye adhering to the membrane surface and the pores. As the test time continued to increase, the membrane permeance remained stable. However, the permeance of the stabilized membrane still reached about 270 L m−2 h−1 bar−1. With the extension of the operation time, the removal of the dye decreased slightly, which was the result of defects in the selected layer. After filtration for 10 h, the rejection of RB and NaCl was nearly 92.6% and 2.1%, respectively. Obviously, the polyamide selection layer was well combined with the ceramic support to form a stable structure. Thus, the stability of the PA/ceramic composite membrane can be considered satisfactory.
4. Conclusion
In summary, we have generated a facile strategy by conducting the interfacial polymerization reaction of PEI and TMC directly on a ceramic support to break the trade-off between permeance and rejection. The successfully prepared composite membrane is rich in positively charged –NH3+ and has excellent hydrophilicity, resulting in high water permeance and excellent separation of dyes and salts. As a result, the prepared composite membrane exhibited a high rejection of 99.9% for 40 ppm RB, BB and CR aqueous solutions. Meanwhile, the membrane also achieved low salt rejection of 0.6%, 3.3%, 3.4%, and 5.3% for 1 g L−1 NaCl, Na2SO4, MgCl2, and MgSO4, respectively. The optimized PA/ceramic membranes show excellent water permeance (496.4 L m−2 h−1 bar−1) and a separation factor of 980 for salt and dye in treating dye/salt aqueous solutions containing 40 ppm CR and 1 g L−1 NaCl. We believe that modified membranes have made meaningful contributions in the preparation of high-performance composite membranes and have great application prospects in recovering high-value substances from dye wastewater.
Author contributions
Yujie Zang: performing the experiment, writing, data curation. Linlin Yan: writing – reviewing and editing. Tieying Yang: performing the experiment, writing. Kai Wang: reviewing & editing. Yingjie Zhang: reviewing & editing. Enrico Drioli: reviewing & editing. Jun Ma: reviewing & editing. Yonggang Li: supervision, reviewing. Shanshan Ji: supervision, reviewing. Xiquan Cheng: conceptualization, supervision, writing – reviewing & editing.
Conflicts of interest
There are no conflicts to declare.
Acknowledgements
This work was supported by the State Key Laboratory of Urban Water Resource and Environment (Harbin Institute of Technology) (No. 2022TS43), Science and Technology Project of the Hebei Academy of Sciences (24702), the Fundamental Research Funds for the Central Universities (HIT.OCEF.2024031) and Guangxi First-class Disciplines (Agricultural Resources and Environment).
Notes and references
- A. Gopalakrishnan, M. L. Mathew, J. Chandran, J. Winglee, A. R. Badireddy and M. Wiesner,
et al., Sustainable Polyelectrolyte Multilayer Surfaces: Possible Matrix for Salt/Dye Separation, ACS Appl. Mater. Interfaces, 2015, 7, 3699–3707 CrossRef CAS.
- G. Jiang, S. Zhang, Y. Zhu, S. Gao, H. Jin and L. Luo,
et al., Hydrogel-embedded tight ultrafiltration membrane with superior anti-dye-fouling property for low-pressure driven molecule separation, J. Mater. Chem. A, 2018, 6, 2927–2934 RSC.
- V. Katheresan, J. Kansedo and S. Y. Lau, Efficiency of various recent wastewater dye removal methods: A review, J. Environ. Chem. Eng., 2018, 6, 4676–4697 CrossRef CAS.
- I. De Vreese and B. Van der Bruggen, Cotton and polyester dyeing using nanofiltered wastewater, Dyes Pigm., 2007, 74, 313–319 CrossRef CAS.
- J. Lin, W. Ye, H. Zeng, H. Yang, J. Shen and S. Darvishmanesh,
et al., Fractionation of direct dyes and salts in aqueous solution using loose nanofiltration membranes, J. Membr. Sci., 2015, 477, 183–193 CrossRef CAS.
- J. Zhu, M. Tian, J. Hou, J. Wang, J. Lin and Y. Zhang,
et al., Surface zwitterionic functionalized graphene oxide for a novel loose nanofiltration membrane, J. Mater. Chem. A, 2016, 4, 1980–1990 RSC.
- X. Feng, D. Peng, J. Zhu, Y. Wang and Y. Zhang, Recent advances of loose nanofiltration membranes for dye/salt separation, Sep. Purif. Technol., 2022, 285, 120228 CrossRef CAS.
- T. Tavangar, M. Karimi, M. Rezakazemi, K. R. Reddy and T. M. Aminabhavi, Textile waste, dyes/inorganic salts separation of cerium oxide-loaded loose nanofiltration polyethersulfone membranes, Chem. Eng. J., 2020, 385, 123787 CrossRef CAS.
- T. Tavangar, K. Jalali, M. A. A. Shahmirzadi and M. Karimi, Toward real textile wastewater treatment: Membrane fouling control and effective fractionation of dyes/inorganic salts using a hybrid electrocoagulation - Nanofiltration process, Sep. Purif. Technol., 2019, 216, 115–125 CrossRef CAS.
- X.-A. Ning, M.-Q. Lin, L.-Z. Shen, J.-H. Zhang, J.-Y. Wang and Y.-J. Wang,
et al., Levels, composition profiles and risk assessment of polycyclic aromatic hydrocarbons (PAHs) in sludge from ten textile dyeing plants, Environ. Res., 2014, 132, 112–118 CrossRef CAS PubMed.
- X. Cheng, T. Li, L. Yan, Y. Jiao, Y. Zhang and K. Wang,
et al., Biodegradable electrospinning superhydrophilic nanofiber membranes for ultrafast oil-water separation, Sci. Adv., 2023, 9, eadh8195 CrossRef CAS PubMed.
- R. P. Lively and D. S. Sholl, From water to organics in membrane separations, Nat. Mater., 2017, 16, 276–279 CrossRef CAS PubMed.
- M. A. Shannon, P. W. Bohn, M. Elimelech, J. G. Georgiadis, B. J. Marinas and A. M. Mayes, Science and technology for water purification in the coming decades, Nature, 2008, 452, 301–310 CrossRef CAS PubMed.
- X. Q. Cheng, Z. X. Wang, X. Jiang, T. Li, C. H. Lau and Z. Guo,
et al., Towards sustainable ultrafast molecular-separation membranes: From conventional polymers to emerging materials, Prog. Mater. Sci., 2018, 92, 258–283 CrossRef CAS.
- J. H. Huang, X. Q. Cheng, Y. D. Wu, Y. Q. Zhang, S. W. Li and C. H. Lau,
et al., Critical operation factors and proposed testing protocol of nanofiltration membranes for developing advanced membrane materials, Adv. Compos. Hybrid Mater., 2021, 4, 1092–1101 CrossRef.
- Y. Zhang, H. Wang, J. Guo, X. Cheng, G. Han and C. H. Lau,
et al., Ice-confined synthesis of highly ionized 3D-quasilayered polyamide nanofiltration membranes, Science, 2023, 382, 202–206 CrossRef CAS PubMed.
- J. H. Huang, L. Shao, Y. Q. Zhang, Y. J. Zhang, K. Wang and J. Ma,
et al., Relationship between the Hansen solubility parameter and changes in membrane mass-transfer channels: A quantitative model, Chem. Eng. Sci., 2022, 263, 118071 CrossRef CAS.
- Q. Li, Z. Liao, X. Fang, J. Xie, L. Ni and D. Wang,
et al., Tannic acid assisted interfacial polymerization based loose thin-film composite NF membrane for dye/salt separation, Desalination, 2020, 479, 114343 CrossRef CAS.
- X. Q. Cheng, Z. X. Wang, J. Guo, J. Ma and L. Shao, Designing Multifunctional Coatings for Cost-Effectively Sustainable Water Remediation, ACS Sustainable Chem. Eng., 2018, 6, 1881–1890 CrossRef CAS.
- D. Saeki, M. Imanishi, Y. Ohmukai, T. Maruyama and H. Matsuyama, Stabilization of layer-by-layer assembled nanofiltration membranes by crosslinking via amide bond formation and siloxane bond formation, J. Membr. Sci., 2013, 447, 128–133 CrossRef CAS.
- Q. Li, Z. Liao, X. Fang, D. Wang, J. Xie and X. Sun,
et al., Tannic acid-polyethyleneimine crosslinked loose nanofiltration membrane for dye/salt mixture separation, J. Membr. Sci., 2019, 584, 324–332 CrossRef CAS.
- H. Fan, J. Gu, H. Meng, A. Knebel and J. Caro, High-Flux Membranes Based on the Covalent Organic Framework COF-LZU1 for Selective Dye Separation by Nanofiltration, Angew. Chem., Int. Ed., 2018, 57, 4083–4087 CrossRef CAS PubMed.
- M. Li, Y. Yao, W. Zheng, J. Zheng, X. Zhang and L. Wang, Fractionation and Concentration of High-Salinity Textile Wastewater using an Ultra-Permeable Sulfonated Thin-film Composite, Environ. Sci. Technol., 2017, 51, 9252–9260 CrossRef CAS PubMed.
- X. Cheng, Y. Qin, Y. Ye, X. Chen, K. Wang and Y. Zhang,
et al., Finely tailored pore structure of polyamide nanofiltration membranes for highly-efficient application in water treatment, Chem. Eng. J., 2021, 417, 127976 CrossRef CAS.
- L. E. Peng, Z. Yang, L. Long, S. Zhou, H. Guo and C. Y. Tang, A critical review on porous substrates of TFC polyamide membranes: Mechanisms, membrane performances, and future perspectives, J. Membr. Sci., 2022, 641, 119871 CrossRef CAS.
- W. Wei, S. Xia, G. Liu, X. Dong, W. Jin and N. Xu, Effects of polydimethylsiloxane (PDMS) molecular weight on performance of PDMS/ceramic composite membranes, J. Membr. Sci., 2011, 375, 334–344 CrossRef CAS.
- P. Xu, W. Wang, X. Qian, H. Wang, C. Guo and N. Li,
et al., Positive charged PEI-TMC composite nanofiltration membrane for separation of Li + and Mg2+ from brine with high Mg2+/Li+ ratio, Desalination, 2019, 449, 57–68 CrossRef CAS.
- Z. Wang, X. You, C. Yang, W. Li, Y. Li and Y. Li,
et al., Ultrathin polyamide nanofiltration membranes with tunable chargeability for multivalent cation removal, J. Membr. Sci., 2022, 642, 119971 CrossRef CAS.
- M. R. S. Kebria, M. Jahanshahi and A. Rahimpour, SiO2 modified polyethyleneimine-based nanofiltration membranes for dye removal from aqueous and organic solutions, Desalination, 2015, 367, 255–264 CrossRef CAS.
- W. Wei, S. Xia, G. Liu, X. Gu, W. Jin and N. Xu, Interfacial Adhesion Between Polymer Separation Layer and Ceramic Support for Composite Membrane, AIChE J., 2009, 56, 1584–1592 CrossRef.
- R. Dai, Z. Yang, Z. Qiu, L. Long, C. Y. Tang and Z. Wang, Distinct impact of substrate hydrophilicity on performance and structure of TFC NF and RO polyamide membranes, J. Membr. Sci., 2022, 662, 120966 CrossRef CAS.
- L. Shen, W.-S. Hung, J. Zuo, X. Zhang, J.-Y. Lai and Y. Wang, High-performance thin-film composite polyamide membranes developed with green ultrasound-assisted interfacial polymerization, J. Membr. Sci., 2019, 570, 112–119 CrossRef.
- C. Yang, U. Tartaglino and B. N. J. Persson, Influence of surface roughness on superhydrophobicity, Phys. Rev. Lett., 2006, 97, 132–142 Search PubMed.
- M. F. Ismail, B. Khorshidi and M. Sadrzadeh, New insights into the impact of nanoscale surface heterogeneity on the wettability of polymeric membranes, J. Membr. Sci., 2019, 590, 117270 CrossRef.
- P. Saini, V. K. Bulasara and A. S. Reddy, Performance of a new ceramic microfiltration membrane based on kaolin in textile industry wastewater treatment, Chem. Eng. Commun., 2019, 206, 227–236 CrossRef CAS.
- S. Karan, Z. Jiang and A. G. Livingston, Sub-10 nm polyamide nanofilms with ultrafast solvent transport for molecular separation, Science, 2015, 348, 1347–1351 CrossRef CAS PubMed.
- S. Zhao and Z. Wang, A loose nano-filtration membrane prepared by coating HPAN UF membrane with modified PEI for dye reuse and desalination, J. Membr. Sci., 2017, 524, 214–224 CrossRef CAS.
- J. Zhang, L. Yang, Z. Wang, S. Yang, P. Li and P. Song,
et al., A highly permeable loose nanofiltration membrane prepared via layer assembled in-situ mineralization, J. Membr. Sci., 2019, 587, 117159 CrossRef CAS.
- S. Liu, Z. Wang and P. Song, Free Radical Graft Copolymerization Strategy to Prepare Catechin-Modified Chitosan Loose Nanofiltration (NF) Membrane for Dye Desalination, ACS Sustainable Chem. Eng., 2018, 6, 4253–4263 CrossRef CAS.
- L. Wang, S. Ji, N. Wang, R. Zhang, G. Zhang and J.-R. Li, One-step self-assembly fabrication of amphiphilic hyperbranched polymer composite membrane from aqueous emulsion for dye desalination, J. Membr. Sci., 2014, 452, 143–151 CrossRef CAS.
- J. Ding, H. Wu and P. Wu, Preparation of highly permeable loose nanofiltration membranes using sulfonated polyethyleneimine for effective dye/salt fractionation, Chem. Eng. J., 2020, 396, 115199 CrossRef.
- Q. Zhang, L. Fan, Z. Yang, R. Zhang, Y.-n. Liu and M. He,
et al., Loose nanofiltration membrane for dye/salt separation through interfacial polymerization with in-situ generated TiO2 nanoparticles, Appl. Surf. Sci., 2017, 410, 494–504 CrossRef CAS.
- T. Pei, M. Deng, C. Ma, H. Yan, A. Zhu and L. Ye,
et al., Loose nanofiltration membranes based on interfacial glutaraldehyde-amine polymerization for fast and highly selective dye/salt separation, Chem. Eng. J., 2022, 450, 138057 CrossRef CAS.
|
This journal is © The Royal Society of Chemistry 2024 |
Click here to see how this site uses Cookies. View our privacy policy here.