DOI:
10.1039/D4MA00565A
(Paper)
Mater. Adv., 2024,
5, 6222-6233
High-performance anthracene-linked covalent triazine frameworks with dual functions for CO2 capture and supercapacitor applications†
Received
2nd June 2024
, Accepted 21st June 2024
First published on 22nd June 2024
Abstract
Porous nitrogen-rich materials with high conductivity have enormous potential as electrode materials for supercapacitors. However, the effectiveness of these materials depends on their N content and surface area. To overcome these challenges, by employing an ionothermal reaction at 500 °C and utilizing different molar ratios of ZnCl2, we successfully synthesized porous covalent triazine frameworks (ANT-CTFs) using 2,3,6,7,9,10-hexacyanoanthracene (ANT-6CN) units. This synthetic approach led to the formation of two distinct microporous materials known as ANT-CTF-10-500 and ANT-CTF-20-500. The thermogravimetric analysis (TGA) and BET tests confirmed that the ANT-CTFs possessed substantial surface areas, falling within the range of 106 to 170 m2 g−1. Additionally, these materials exhibited remarkable thermal stability, resulting in char yields of up to 81 wt%. Additionally, ANT-CTF-10-500 exhibited an impressive capacitance of 81.2 F g−1, along with excellent cycle stability (up to 87% capacitance retention). Furthermore, the material showed CO2 adsorption capabilities, with an uptake of up to 2.14 mmol g−1. The ANT-CTFs offer a competitive option for applications involving CO2 uptake and electrochemical energy storage.
Introduction
In recent years, environmental awareness has risen, and renewable energy is seen as a key to sustainable development. One of the problems faced by the development of renewable energy is the capacity improvement of energy storage systems. Supercapacitors belong to one of the electromagnetic energy storage systems.1 The energy storage of supercapacitors uses a special electrode structure such as porous materials, which possess a high specific surface area, thereby generating a large capacitance. The technical characteristics are fast charging and discharging speed, high cycle usage, and that when used in transportation, they can quickly discharge during acceleration and recover energy during braking. Even frequent acceleration and braking will not affect the battery life, but the high cost is still the key factor that prevents it from being widely used. Scientists worldwide are searching for stable and high-capacitance materials for energy storage devices. Electric double-layer capacitors (EDLCs), a specific type of supercapacitor, are an emerging technology that offers a wide range of operating temperatures, high energy densities, substantial power densities, and stable cycling performance.2–5 EDLCs utilize mobile electrolyte ions to store charged particles at the interface between the electrolyte and electrode.2–7 Researchers have evaluated numerous studies to develop energy storage systems that are both highly sustainable and efficient. These studies have focused on a range of materials, including metal oxides and their hybrid materials,8–13 metal–organic frameworks (MOFs),14–18 porous organic polymers (POPs),19–23 and other carbon-based materials.24–32 The majority of porous carbon materials have distinct specific capacitance, but when the surface area and porosity increase owing to the breakdown of conductive pathways the electrical conductivity declines. This limits their power capability. To improve the energy density and power output, investigations have been carried out by researchers to explore the incorporation of functional groups or heteroatoms into porous materials to induce pseudocapacitance.33–38 When incorporated, these heteroatoms can alter the properties of porous materials by acting as electron donors and acceptors, leading to the manifestation of pseudocapacitive behavior.39,40 Environmental issues are increasingly drawing scholarly attention, especially with the rise of global warming and the ongoing industrial revolution being highlighted as significant problems. The main drivers of global warming are greenhouse gases such as CO2, N2O, and CH4.41–44 Among these, CO2 is undeniably the principal contributor to both climate change and global warming, with its atmospheric concentration rising rapidly.41–44 Therefore, novel POPs and CTFs are gaining attention for their potential use in energy storage, gas capture, and other applications. This kind of material possesses distinctive characteristics, including high surface area, extensive porosity, high mechanical stability, and low density.45–51
Under ionothermal conditions, CN groups undergo cyclotrimerization, giving rise to CTFs that find applications across various disciplines, such as gas storage application, sensing, heterogeneous catalysis, and electrocatalysis for oxygen reduction reactions, CO2 absorption and conversion, lithium batteries, and supercapacitors.52–57 Li et al. documented the synthesis of COF materials demonstrating remarkable characteristics, including high surface area, well-defined pore structures, and exceptional cycling stability, even after undergoing 7000 cycles.58 Bhanja et al. synthesized COFs using triazine units that displayed high porosity and conjugation, resulting in a capacitance of 354 F g−1. The material also demonstrated exceptional cycling stability, maintaining 95% capacity retention after numerous cycles.59 Apart from the above research, Vargheese et al. synthesized a category of triazine-based COFs, exhibiting noteworthy attributes such as high specific capacitance, excellent cycling stability, and a substantial surface area of 711 m2 g−1.60 The rigid, π-conjugated surface of the anthracene (ANT) molecule contributes to its high charge transfer efficiency and significant fluorescence emission.61 Mohamed et al. discovered that An-CTF-10-500 exhibits a capacitance of 589 F g−1 and a high CO2 adsorption capacity.62 Hence, we developed a new type of material called nitrogen-enriched CTF using the ANT moiety and molten ZnCl2 at a high temperature of 500 °C with two different molar ratios (1
:
10 and 1
:
20), as presented in Fig. 1. We selected molten ZnCl2 as the reaction medium for the trimerization of ANT-6CN due to its high solubility and moderate Lewis acidity.63 Subsequently, a comprehensive investigation was conducted on the various attributes of the ANT-CTFs. This encompassed the examination of their chemical structure, composition, thermal stability, crystallinity, surface area, and porosity. To achieve this, a diverse array of analytical techniques such as FTIR, TGA, XRD, Raman spectroscopy, XPS, SEM, TEM, and BET theory were employed. Furthermore, we also tested their electrochemical performance for energy storage and CO2 uptake for gas storage applications.
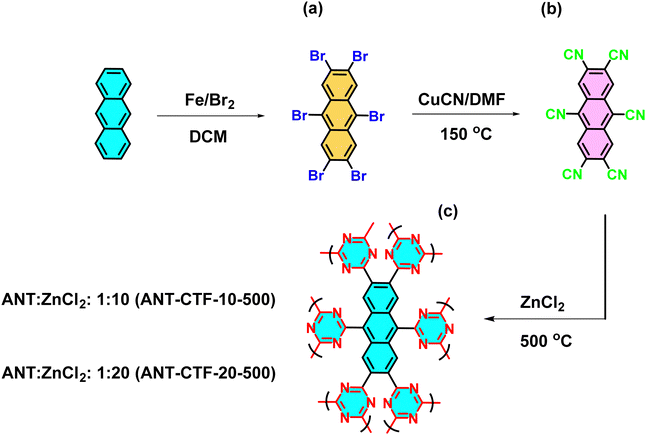 |
| Fig. 1 Preparation method and reaction conditions of ANT-Br6 (a), ANT-6CN (b), and ANT-CTFs (c) from ANT monomer. | |
Experimental section
Materials
Copper(I) cyanide (CuCN), ethylenediamine, iron (Fe) powder, anthracene (ANT), bromine solution (Br2), dichloromethane (DCM), sodium thiosulfate (Na2S2O3), N,N-dimethylformamide (DMF), zinc chloride (ZnCl2), HCl solution (37%), methanol, and ethanol were purchased from different companies (Sigma-Aldrich, USA and Alfa Aesar, UK).
Preparation of 2,3,6,7,9,10-hexabromoanthracene (ANT-Br6)64
In 190 mL of dry DCM, a flask containing ANT (2 g), iron powder (4.23 g), and Br2 (4.11 mL) was agitated under nitrogen for 6 h at room temperature. The mixture was quenched with Na2S2O3 (10%). After the reaction, the obtained gray solid was washed with water to produce ANT-Br6 (71%) as a gray powder. The gray product was not further purified due to its poor insolubility.
Preparation of 2,3,6,7,9,10-hexacyanoanthracene (ANT-6CN)
CuCN (8.9 g) and ANT-Br6 (5 g) were blended and refluxed at 150 °C for two days in the presence of 150 mL of DMF in a flask. The resulting DMF solution was combined with ethylenediamine and water, leading to the formation of a brown solid after cooling and the subsequent removal of excess CuCN by filtration. The brown solid was further boiled and crystallized in DMF solution, resulting in the formation of brown needle-like ANT-6CN.
Preparation of ANT-CTFs
To prepare ANT-CTFs, we mixed ANT-6CN with anhydrous ZnCl2, and regulating the molar ratios of 0.1 and 0.05, respectively. The mixture was subjected to a specific temperature of 500 °C and maintained under the same conditions in a nitrogen atmosphere for 2 days to obtain ANT-CTFs (Fig. 1). The obtained black solid was immersed in HCl (1 M), water, and acetone for 48 h, yielding ANT-CTFs in the form of a black powder.
Results and discussion
Preparation and characterization of ANT-6CN and ANT-CTFs
Based on previous research, the CTF materials exhibited remarkable characteristics, such as thermal stability, outstanding cycling stability, and porosity properties.62 Therefore, we were keen to extend the research by increasing the triazine content and strengthening the crosslinking framework to investigate whether these properties improved. Fig. 1 shows the preparation procedure of the ANT-CTFs used in this research. The ANT compound [Fig. 1(a)] was converted into ANT-Br6 through a bromine reaction in DCM and Fe powder [Fig. 1(b)]. Then, the ANT-Br6 compound was converted into ANT-6CN in the presence of dry DMF and CuCN [Fig. 1(c)].
After that, the ionothermal synthesis was conducted for trimerization of the CN groups of ANT-6CN in different ratios of ZnCl2 at 500 °C, acquiring ANT-CTF materials [Fig. 1(c)]. The FTIR spectra of ANT-6CN and the obtained ANT-CTFs are shown in Fig. 2(a). The band positioned at 2223 cm−1 on the FTIR profile corresponds to the nitrile group in the ANT-6CN structure, which also confirmed its successful synthesis. In addition, aromatic stretching signals were also found at 1600 and 1455 cm−1. On the other hand, the presence of bands at 1566 and 1384 cm−1 in the FTIR spectra played a crucial role in identifying the presence of triazine units in each ANT-CTF, which also confirms that the nitrile group underwent cyclization.65,66 For further study on thermal stability, the synthesized ANT-6CN and ANT-CTFs were introduced to perform TGA analysis from 40 to 800 °C under N2. As shown in Fig. 2(b), the ANT-6CN monomer had a Td10 of 234 °C and a 62 wt% char yield. After calcination, the Td10 of ANT-CTF-10-500 and ANT-CTF-20-500 improved to reach 588 °C and 630 °C, and their char yields increased to 77 and 81 wt%; respectively. All TGA data of ANT-6CN and ANT-CTFs are collected in Table S1 (ESI†). Fig. 2(c) shows the XRD patterns of the ANT-CTFs, where the (002) and (100) planes of hexagonal graphitic carbon are represented by the two distinctive diffraction peaks at around 2θ = 26° and 43°, respectively.67 To evaluate the graphitization degree and defective properties of carbon materials, Raman spectroscopy is often considered a crucial approach. Fig. 2(d) shows the Raman spectra of the ANT-CTFs, recorded from 800 to 2000 cm−1. Both ANT-CTFs exhibit two prominent peaks at around 1335 cm−1 (D band) and 1590 cm−1 (G band), which indicate the presence of a graphitic structure.68–70 For ANT-CTF-10-500 and ANT-CTF-20-500, the ID/IG ratios were found to be 1.55 and 1.48, respectively. This suggests that ANT-CTF-10-500 has a higher degree of graphitization, indicating a lower level of defects in its morphology and a greater condensed aromatic structure than ANT-CTF-20-500 and other reported CTFs.65,66,71–74 The XPS spectra of the synthesized ANT-CTFs are shown in Fig. 3. There were three peaks corresponding to the carbon atom, the C–N bond for the N 1s orbital belonging to the triazine unit and the O 1s orbital belonging to moisture and oxygen, which were located at 284 eV, 400 eV, and 530 eV, respectively.65,66,71–74Fig. 4(a–d) and Table S2 (ESI†) provide the XPS curve fitting for N 1s and O 1s orbitals, enabling the assessment of the chemical composition of the ANT-CTFs. Based on the investigation, three different N species were found: hexagonal pyridinic N species, quaternary N species (at 401.5 eV), and pyrrolic species (at 400 eV). After analyzing the data, it was found that pyridinic N was the most abundant type of nitrogen in ANT-CTF-10-500 [Fig. 4(a)], while pyrrolic N dominated in ANT-CTF-20-500 [Fig. 4(c)]. Furthermore, the surface of these ANT-CTFs revealed the presence of three different oxygen species, as indicated by the distinct peaks observed in Fig. 4(b) and (d). These peaks were associated with absorbed oxygen (531.5 eV), moisture (533 eV), and a C–O single bond (535 eV), respectively.65,75
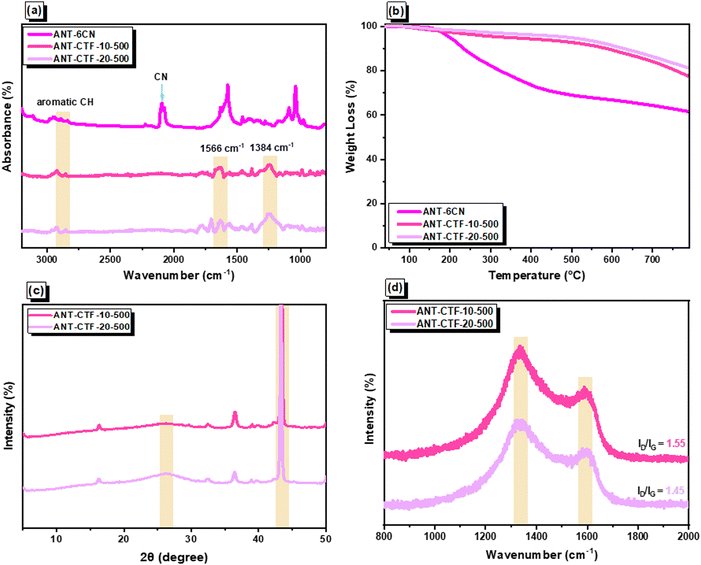 |
| Fig. 2 (a) FTIR and (b) TGA profiles ANT-6CN, ANT-CTF-10-500, and ANT-CTF-20-500. (c) XRD and (d) Raman profiles of ANT-CTF-10-500, and ANT-CTF-20-500. | |
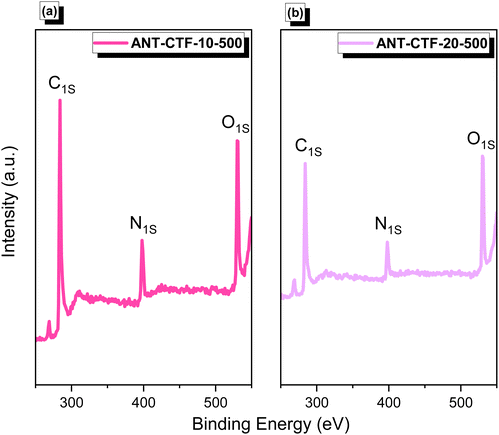 |
| Fig. 3 XPS profiles of ANT-CTF-10-500 (a) and ANT-CTF-20-500 (b). | |
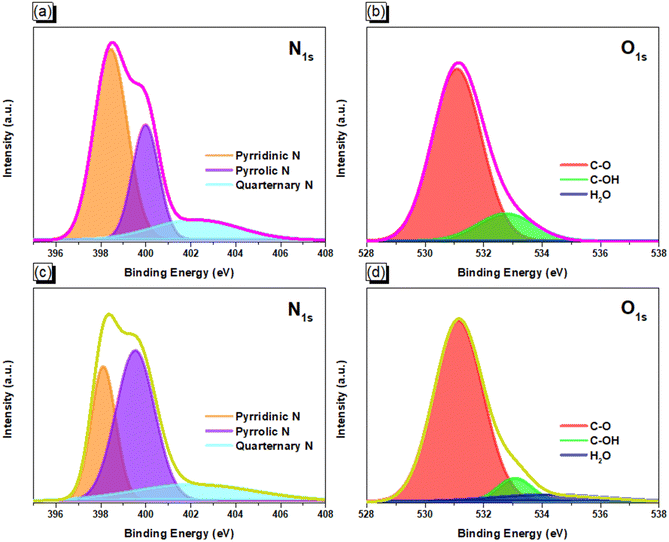 |
| Fig. 4 XPS fitting curves of N 1s and O 1s orbitals for ANT-CTF-10-500 (a) and (b) and ANT-CTF-20-500 (c) and (d). | |
Porosity and CO2 capture ability of ANT-CTF-10-500 and ANT-CTF-20-500
After confirming the synthesis of ANT-CTFs, we proceeded with our study to measure the porosity of the ANT-CTF materials [Fig. 5(a–d)]. As shown in Fig. 5(a) and (b), both ANT-CTFs had type I isotherms according to the IUPAC classification of BET isotherms. The results shown in Table 1 illustrate the surface areas for both ANT-CTF precursors. ANT-CTF-10-500 and ANT-CTF-20-500 had BET surface areas (SABET) of 170 and 106 m2 g−1, respectively. The anticipated factors contributing to the diminished surface area and crystallinity in ANT-CTF materials are the triazine groups, which can, in part, result from significant steric hindrance effects during synthesis, potentially leading to structural disorder. The higher SABET of ANT-CTF-10–500 as compared to ANT-CTF-20-500 can be attributed to the denser nanoparticle packing and the higher number of defects in the ANT-CTF-10-500 framework.62,65,75 Furthermore, the pore sizes of both ANT-CTFs based on NLDFT theory were all 1.28–1.6 nm [Fig. 5(c) and (d)], which were classified as micropores and observed reasonably on the BET curves increasing sharply at lower relative pressure. The SEM images of the obtained ANT-CTFs are presented in Fig. 6(a–d). Focusing on ANT-CTF-10-500, although it seems to have an irregular block shape and there are no obvious cavities on the surface of the material [Fig. 6(a)], the porous structure was found on the section of the bulk shown in Fig. 6(b). As shown in Fig. 6(c) and (d), ANT-CTF-20-500 exhibits an irregular, rough surface with obvious cavities. Furthermore, HR-TEM revealed the presence of random micropores of these ANT-CTF samples shown in Fig. 7(a–f), which corresponds to the pore size analysis. The presence of C, N, and O atoms and their distribution in the ANT-CTF frameworks were identified by the SEM–EDS mapping data displayed in Fig. S1 and S2 (ESI†). We examined the stability of ANT-CTFs in a 1 M KOH solution, employing XRD, SEM, and BET analyses, with the results presented in Fig. S3–S6 (ESI†). From Fig. S3 (ESI†), it is evident that two distinctive diffraction peaks at around 2θ = 26° and 43° have persisted. Notably, both ANT-CTF variants, specifically ANT-CTF-10-500 and ANT-CTF-20-500, featured a framework containing O, N, and C atoms, as exemplified in Fig. S4 and S5 (ESI†). ANT-CTF-10-500 exhibited a SBET of 160 m2 g−1, while ANT-CTF-20-500 displayed a slightly lower SBET of 95 m2 g−1 [Fig. S6, ESI†]. We obtained CO2 uptake profiles for all of these ANT-CTFs at 298 K and 273 K to determine their potential for CO2 uptake. ANT-CTF-10-500 and ANT-CTF-20-500 demonstrated CO2 capture performances of 1.45 and 0.88 mmol g−1 at 298 K, respectively, as shown in Fig. 8(a), Table 1, and Table S3 (ESI†). At 273 K, the CO2 capture capacities of ANT-CTF-10-500 and ANT-CTF-20-500 were 2.14 and 1.29 mmol g−1, respectively, shown in Fig. 8(b). The greater SBET of 170 m2 g−1 for ANT-CTF-10-500 enhanced the interaction between CO2 and the material framework, thereby increasing the CO2 absorption compared to ANT-CTF-20-500.65,66,75
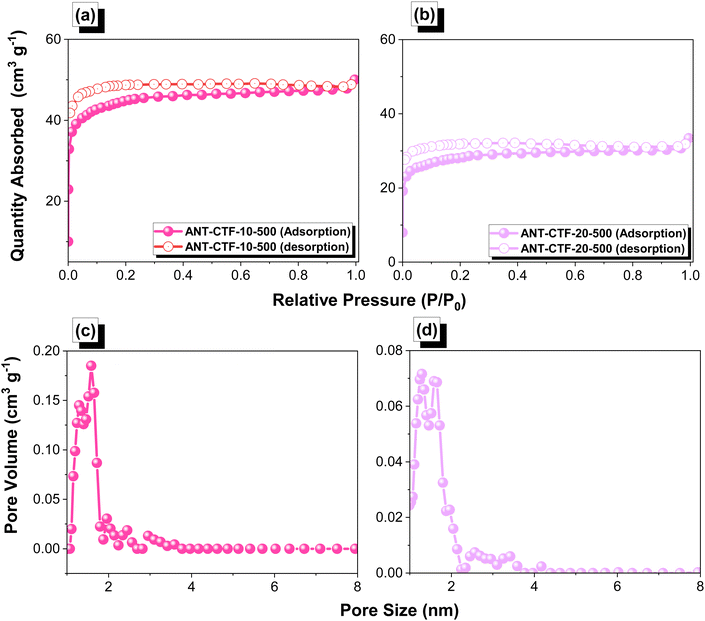 |
| Fig. 5 (a, b) N2 adsorption–desorption isotherms and (c, d) pore size analyses of ANT-CTF-10-500 (a, c) and ANT-CTF-20-500 (b, d). | |
Table 1 Surface area, pore size, and CO2 uptake of ANT-CTFs
Sample |
Surface area (m2 g−1) |
Pore size (nm) |
CO2 uptake (298 K) (mmol g−1) |
CO2 uptake (273 K) (mmol g−1) |
ANT-CTF-10-500 |
170 |
1.28, 1.55 |
1.45 |
2.14 |
ANT-CTF-20-500 |
106 |
1.26, 1.6 |
0.88 |
1.29 |
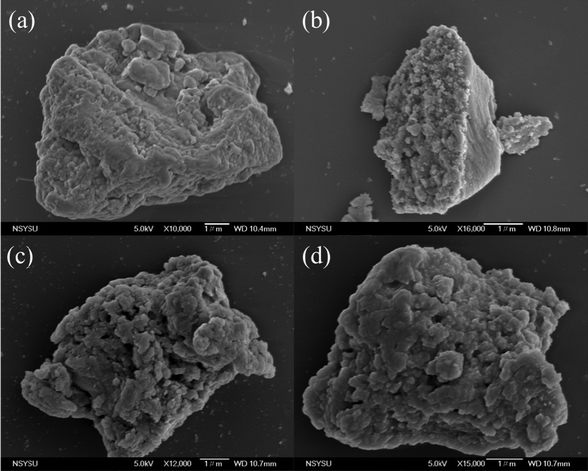 |
| Fig. 6 SEM images of ANT-CTF-10-500 (a) and (b) and ANT-CTF-20-500 (c) and (d). | |
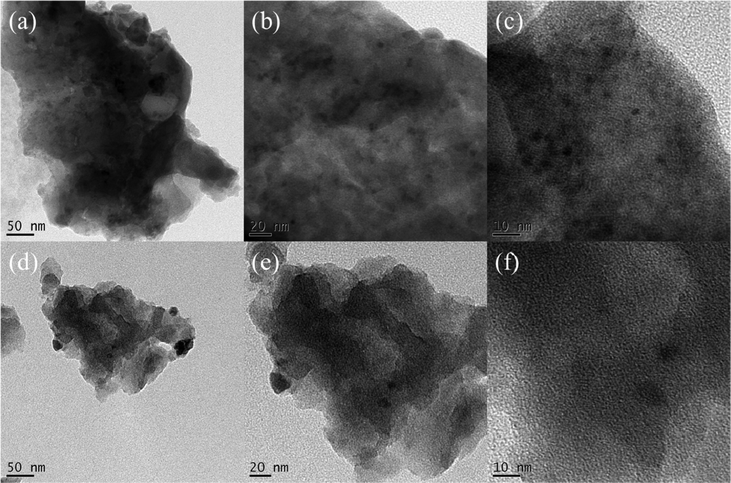 |
| Fig. 7 TEM images at different scales of ANT-CTF-10-500 (a)–(c) and ANT-CTF-20-500 (d)–(f). | |
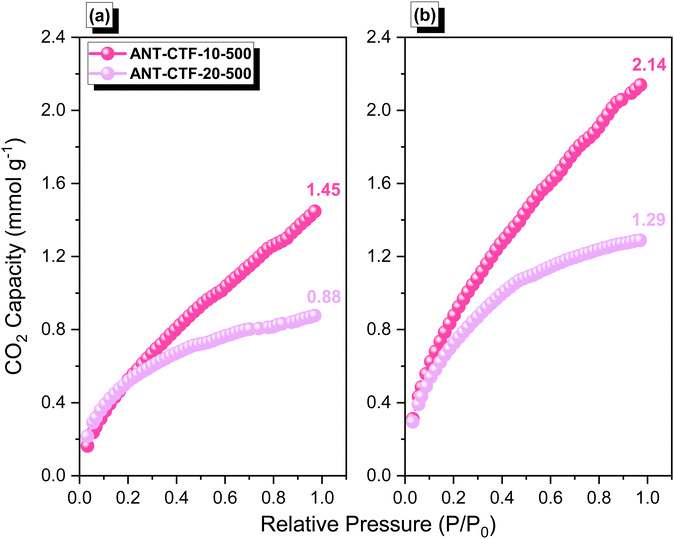 |
| Fig. 8 CO2 adsorption performance of ANT-CTF-10-500 and ANT-CTF-20-500 at 298 K (a) and 273 K (b). | |
Table S3 (ESI†) provides a summary of the performance of ANT-CTFs in terms of their CO2 uptake capabilities, offering a comparative assessment against other porous precursors. Table S3 (ESI†) shows that our ANT-CTF-10-500 exhibited a higher CO2 adsorption capacity compared to FEC-Mel POP, FEC-PBDT POP, RIO-13, RIO-12, RIO-11 m, and RIO-11, but it was lower than those of CTF-5-400 and CTF-10-400.62,75–77 According to the Clausius–Clapeyron equation, the isosteric heat of adsorption (Qst) for ANT-CTF-10-500 and ANT-CTF-20-500 was determined to be 27 kJ mol−1 and 19 kJ mol−1, respectively, at a low CO2 adsorption level of approximately 0.4 mmol g−1 based on their CO2 adsorption results at 298 K and 273 K. The data highlight a significant level of interaction between the CO2 molecules and our ANT-CTF frameworks, as detailed in Table S4 (ESI†). The results show that the numerical value for ANT-CTF-10-500 exceeds that of ANT-CTF-20-500, which correlates with the superior CO2 adsorption performance observed for ANT-CTF-10-500. Additionally, the isosteric heat of adsorption value for ANT-CTF-10-500 not only surpasses the liquefaction heat of bulk CO2 (17 kJ mol−1) but also exceeds those of several other CTF materials. This indicates relatively strong interactions between CO2 and our ANT-CTFs, more so than some other reported porous organic frameworks. After six measurement cycles at 25 °C [Fig. S7, ESI†], the CO2 adsorption capacity of ANT-CTF-10-500 decreased from 1.45 to 0.88 mmol g−1, while ANT-CTF-20-500 exhibited a reduction from 0.88 to 0.69 mmol g−1.
Electrochemical performance of the ANT-CTF-10-500 and ANT-CTF-20-500
The electrochemical performance of the ANT-CTF samples as supercapacitor electrode materials was carefully investigated through cyclic voltammetry (CV) and galvanostatic charge–discharge (GCD). The tests were conducted in a 1 M KOH aqueous electrolyte within the potential range of −1 to 0.2 V. The corresponding CV patterns of the ANT-CTF samples are presented in Fig. 9(a) and (b), recorded at various sweep rates ranging from 5 to 200 V s−1. The rectangle-like shape with an anodic peak in the CV curves of both ANT-CTF samples suggested that their capacitive response was mainly due to electric double-layer capacitance (EDLC), with minimal pseudocapacitance resulting from different nitrogen and oxygen species.58,59 The reaction of ANT-6CN with ZnCl2 produces a unique carbon framework with pyridinic nitrogen atoms akin to those found in N-doped carbon materials.65,66 XPS, SEM–EDS mapping, and BET investigations all revealed that the ANT-CTF samples had N-heteroatom frameworks and high specific surface areas. As shown in Fig. 9(c) and (d), the GCD curves of ANT-CTF samples were examined at various current densities ranging from 0.5 to 20 A g−1. The curves exhibited a triangular form and a few small bends, which showed that both EDLC and pseudocapacitance properties were present.64–86 The capacitances of ANT-CTF samples which were calculated and determined from the GCD curves are shown in Fig. 10(a). At 0.5 A g−1, ANT-CTF-10-500 displayed a superior capacitance value of 81.20 F g−1. The enhanced performance observed can be attributed to multiple factors such as increased SABET, higher pore size, and the presence of various functional groups, including phenolic OH groups, and pyridinic and pyrrolic nitrogen atoms, within the graphitic microporous carbon structures of ANT-CTF-10-500. These structural characteristics improve the interactions between the electrolyte and the electrode material, which in turn can enhance the overall performance and ionic conductivity of the storage system. In contrast, ANT-CTF-20-500 exhibited almost half the specific capacitance of the former. As the current density increased from 0.5 to 20 A g−1, Fig. 10(a) demonstrates that the specific capacitances of ANT-CTF samples tended to gradually decrease. This was likely caused by the electrolyte ions adhering quickly to the electrodes. On the other hand, ANT-CTF-10-500 performed better due to its larger surface area during the cycling test. The long-term stability of the ANT-CTF electrode materials was also evaluated by analyzing the GCD profiles of both ANT-CTF materials at 10 A g−1 (over 5000 cycles). Fig. 10(b) displays the extraordinary stability of ANT-CTF-10-500 in the KOH electrolyte, which still retained 86.5% of its original capacity after the cycling test.
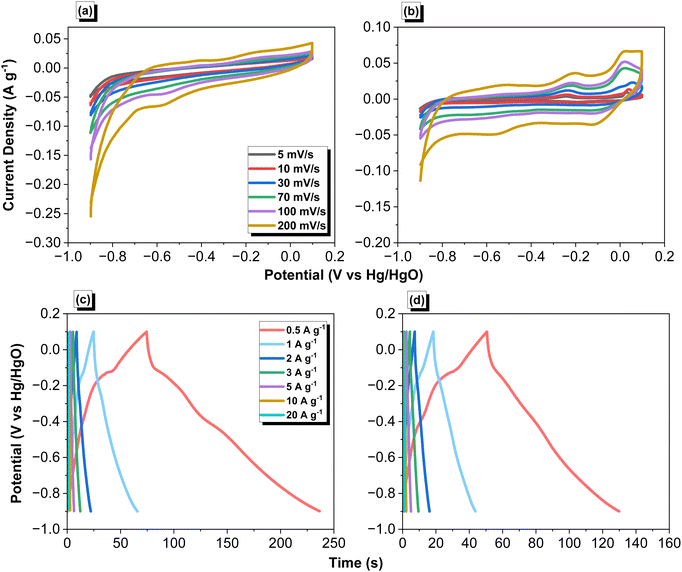 |
| Fig. 9 Electrochemical performance of ANT-CTF-10-500 (a) and (c) and ANT-CTF-20-500 (b) and (d) through (a) and (b) CV and (c) and (d) GCD. | |
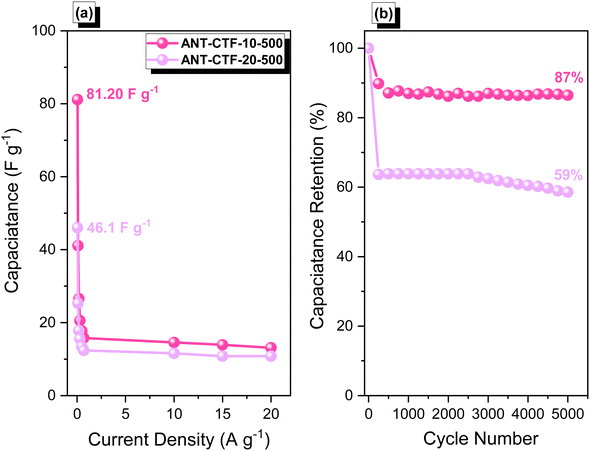 |
| Fig. 10 Specific capacitance (a) and capacitance retention (b) of ANT-CTF-10-500 and ANT-CTF-20-500. | |
From Fig. 11, it is evident that ANT-CTF materials outperform other porous organic electrode precursors, showing significantly higher capacitance values.
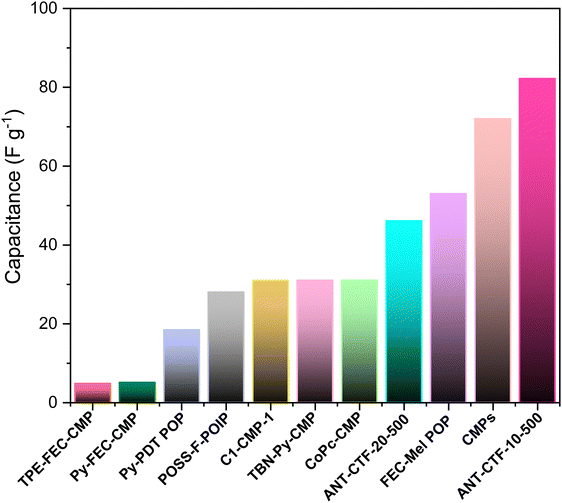 |
| Fig. 11 ANT-CTF materials showing significantly superior capacitance values compared to other porous organic electrode precursors. | |
Conclusions
We have successfully developed porous covalent triazine frameworks (ANT-CTFs) as potential electrode materials for gas capture and supercapacitors. By utilizing ANT-6CN under an ionothermal reaction in the presence of ZnCl2 at 500 °C, we obtained two distinct microporous materials: ANT-CTF-10-500 and ANT-CTF-20-500. TGA and BET analyses revealed exceptional thermal stability with char yields of up to 81 wt% and high specific surface areas ranging from 106 to 170 m2 g−1 for these ANT-CTFs. ANT-CTF-10-500 displayed a notable CO2 adsorption capacity of up to 2.14 mmol g−1 (273 K) and showed impressive electrochemical properties, including a specific capacitance of 81.20 F g−1 and a remarkable cycle stability of 87% after 5000 cycles. These results demonstrate the considerable potential of ANT-CTF-10-500 for both CO2 uptake and electrochemical energy storage applications.
Author contributions
Ming-Chieh Lin: investigation, methodology. Shiao-Wei Kuo: supervision. Mohamed Gamal Mohamed: investigation, methodology, conceptualization, supervision, writing – original draft.
Data availability
Data are presented within the article or the ESI.†
Conflicts of interest
There are no conflicts to declare.
Acknowledgements
This study was supported financially by the National Science and Technology Council, Taiwan, under contracts NSTC 112-2223-E-110-002- and 112-2218-E-110-007. The authors thank the staff at National Sun Yat-sen University for their assistance with the TEM (ID: EM022600) experiments.
Notes and references
- M. Ejaz, M. G. Mohamed, Y. T. Chen, K. Zhang and S. W. Kuo, J. Energy Storage, 2024, 78, 110166 CrossRef.
- M. G. Mohamed, T. H. Mansoure, Y. Takashi, M. M. Samy, T. Chen and S. W. Kuo, Microporous Mesoporous Mater., 2021, 328, 111505 CrossRef CAS.
- M. M. Samy, M. G. Mohamed, T. H. Mansoure, T. S. Meng, M. A. R. Khan, C. C. Liaw and S. W. Kuo, J. Taiwan Inst. Chem. Eng., 2022, 132, 104110 CrossRef CAS.
- M. Ejaz, M. G. Mohamed and S. W. Kuo, Polym. Chem., 2023, 14, 2494–2509 RSC.
- M. G. Mohamed, W. C. Chang, S. V. Chaganti, S. U. Sharma, J. T. Lee and S. W. Kuo, Polym. Chem., 2023, 14, 4589–4601 RSC.
- L. Yao, Q. Wu, P. Zhang, J. Zhang, D. Wang, Y. Li, X. Ren, H. Mi, L. Deng and Z. Zheng, Adv. Mater., 2018, 30, 1706054 CrossRef PubMed.
- M. G. Mohamed, E. C. Atayde Jr, B. M. Matsagar, J. Na, Y. Yamauchi, K. C. W. Wu and S. W. Kuo, J. Taiwan Inst. Chem. Eng., 2020, 112, 180–192 CrossRef CAS.
- C. An, Y. Zhang, H. Guo and Y. Wang, Nanoscale Adv., 2019, 1, 4644–4658 RSC.
- Y. Wang, J. Guo, T. Wang, J. Shao, D. Wang and Y. W. Yang, Nanomaterials, 2015, 5, 1667–1689 CrossRef CAS PubMed.
- T. Cottineau, M. Toupin, T. Delahaye, T. Brousse and D. Bélanger, Appl. Phys. A: Mater. Sci. Process., 2006, 82, 599–606 CrossRef CAS.
- C. Lokhande, D. Dubal and O. S. Joo, Curr. Appl. Phys., 2011, 11, 255–270 CrossRef.
- Y. Ma, X. Xie, W. Yang, Z. Yu, X. Sun, Y. Zhang, X. Yang, H. Kimura, C. Hou and Z. Guo, Adv. Compos. Hybrid Mater., 2021, 1–19 Search PubMed.
- X. Lang, A. Hirata, T. Fujita and M. Chen, Nat. Nanotechnol., 2011, 6, 232–236 CrossRef CAS PubMed.
- L. Niu, T. Wu, M. Chen, L. Yang, J. Yang, Z. Wang, A. A. Kornyshev, H. Jiang, S. Bi and G. Feng, Adv. Mater., 2022, 34, 2200999 CrossRef CAS PubMed.
- K.-B. Wang, Q. Xun and Q. Zhang, EnergyChem, 2020, 2, 100025 CrossRef.
- L. Wang, Y. Han, X. Feng, J. Zhou, P. Qi and B. Wang, Coord. Chem. Rev., 2016, 307, 361–381 CrossRef CAS.
- T. TQiu, Z. Liang, W. Guo, T. Tabassum, S. Gao and R. Zou, ACS Energy Lett., 2020, 5, 520–532 CrossRef.
- K. M. Choi, H. M. Jeong, J. H. Park, Y. B. Zhang, J. K. Kang and O. M. Yaghi, ACS Nano, 2014, 8, 7451–7457 CrossRef CAS PubMed.
- A. I. Said, M. G. Mohamed, M. Madhu, P. N. Singh, S. V. Chaganti, M. H. Elsayed, W. L. Tseng, F. M. Raymo and S. W. Kuo, Polymer, 2024, 300, 126988 CrossRef.
- M. G. Mohamed, M. M. Samy, T. H. Mansoure, C. J. Li, W. C. Li, J. H. Chen, K. Zhang and S. W. Kuo, Int. J. Mol. Sci., 2021, 23, 347 CrossRef PubMed.
- M. G. Mohamed, A. M. Elewa, M. S. Li and S. W. Kuo, J. Taiwan Inst. Chem. Eng., 2023, 150, 105045 CrossRef CAS.
- S. Y. Chang, A. M. Elewa, M. G. Mohamed, I. M. A. Mekhemer, M. M. Samy, K. Zhang, H. H. Chou and S. W. Kuo, Mater. Today Chem., 2023, 33, 101680 CrossRef CAS.
- M. M. Samy, I. M. A. Mekhemer, M. G. Mohamed, M. H. Elsayed, K. H. Lin, Y. K. Chen, T. L. Wu, H. H. Chou and S. W. Kuo, Chem. Eng. J., 2022, 446, 137158 CrossRef.
- A. B. Fuertes and M. Sevilla, ChemSusChem, 2015, 8, 1049–1057 CrossRef CAS PubMed.
- L. Liu, Z. Niu and J. Chen, Chem. Soc. Rev., 2016, 45, 4340–4363 RSC.
- R. J. Mo, Y. Zhao, M. Wu, H. M. Xiao, S. Kuga, Y. Huang, J. P. Li and S. Y. Fu, RSC Adv., 2016, 6, 59333–59342 RSC.
- J. Tang, T. Wang, R. R. Salunkhe, S. M. Alshehri, V. Malgras and Y. Yamauchi, Chem. – Eur. J., 2015, 21, 17293–17298 CrossRef CAS PubMed.
- Y. Zhu, S. Murali, M. D. Stoller, K. J. Ganesh, W. Cai, P. J. Ferreira, A. Pirkle, R. M. Wallace, K. A. Cychosz and M. Thommes, Science, 2011, 332, 1537–1541 CrossRef CAS PubMed.
- M. M. Samy, M. G. Mohamed and S. W. Kuo, Eur. Polym. J., 2020, 138, 109954 CrossRef CAS.
- C. Gu, N. Huang, Y. Chen, H. Zhang, S. Zhang, F. Li, Y. Ma and D. Jiang, Angew. Chem., Int. Ed., 2016, 55, 3049–3053 CrossRef CAS PubMed.
- J. Tang, R. R. Salunkhe, J. Liu, N. L. Torad, M. Imura, S. Furukawa and Y. Yamauchi, J. Am. Chem. Soc., 2015, 137, 1572–1580 CrossRef CAS PubMed.
- R. R. Salunkhe, J. Lin, V. Malgras, S. X. Dou, J. H. Kim and Y. Yamauchi, Nano Energy, 2015, 11, 211–218 CrossRef CAS.
- D. Hulicova-Jurcakova, M. Seredych, G. Q. Lu and T. J. Bandosz, Adv. Funct. Mater., 2009, 19, 438–447 CrossRef CAS.
- J. Han, L. L. Zhang, S. Lee, J. Oh, K. S. Lee, J. R. Potts, J. Ji, X. Zhao, R. S. Ruoff and S. Park, ACS Nano, 2013, 7, 19–26 CrossRef CAS PubMed.
- Z. S. Wu, A. Winter, L. Chen, Y. Sun, A. Turchanin, X. Feng and K. Müllen, Adv. Mater., 2012, 24, 5130–5135 CrossRef CAS PubMed.
- L. F. Chen, X. D. Zhang, H. W. Liang, M. Kong, Q. F. Guan, P. Chen, Z. Y. Wu and S. H. Yu, ACS Nano, 2012, 6, 7092–7102 CrossRef CAS PubMed.
- X. Zhao, Q. Zhang, C. M. Chen, B. Zhang, S. Reiche, A. Wang, T. Zhang, R. Schlögl and D. S. Su, Nano Energy, 2012, 1, 624–630 CrossRef CAS.
- X. Zhao, Q. Zhang, B. Zhang, C. M. Chen, A. Wang, T. Zhang and D. S. Su, J. Mater. Chem., 2012, 22, 4963–4969 RSC.
- L. Zhao, L. Z. Fan, M. Q. Zhou, H. Guan, S. Qiao, M. Antonietti and M. M. Antonietti, Adv. Mater., 2010, 22, 5202–5206 CrossRef CAS PubMed.
- S. L. Candelaria, B. B. Garcia, D. Liu and G. Cao, J. Mater. Chem., 2012, 22, 9884–9889 RSC.
- A. O. Mousa, M. G. Mohamed, C. H. Chuang and S. W. Kuo, Polymers, 2023, 15, 1891 CrossRef CAS PubMed.
- M. G. Mohamed, W. C. Chang and S. W. Kuo, Macromolecules, 2022, 55, 7879–7892 CrossRef CAS.
- B. Ray, S. R. Churipard and S. C. Peter, J. Mater. Chem. A, 2021, 9, 26498–26527 RSC.
- R. D. Piacentini and A. S. Mujumdar, Dry. Technol., 2009, 27, 629–635 CrossRef CAS.
- J. F. Mike and J. L. Lutkenhaus, J. Polym. Sci., Part B: Polym. Phys., 2013, 51, 468–480 CrossRef CAS.
- A. Halder, M. Ghosh, A. Khayum M, S. Bera, M. Addicoat, H. S. Sasmal, S. Karak, S. Kurungot and R. Banerjee, J. Am. Chem. Soc., 2018, 140, 10941–10945 CrossRef CAS PubMed.
- M. H. Gharahcheshmeh and K. K. Gleason, Adv. Mater. Interfaces, 2019, 6, 1801564 CrossRef.
- S. W. Kuo, Polym. Int., 2022, 71, 393–410 CrossRef CAS.
- M. G. Mohamed, M. H. Elsayed, A. M. Elewa, A. F. M. EL-Mahdy, C. H. Yang, A. A. Mohammed, H. H. Chou and S. W. Kuo, Catal. Sci. Technol., 2021, 11, 2229–2241 RSC.
- M. Ejaz, M. G. Mohamed, W. C. Huang and S. W. Kuo, J. Mater. Chem. A, 2023, 11, 22868–22883 RSC.
- M. G. Mohamed, M. M. Ahmed, W. T. Du and S. W. Kuo, Molecules, 2021, 26, 738 CrossRef CAS PubMed.
- P. Katekomol, J. Roeser, M. Bojdys, J. Weber and A. Thomas, Chem. Mater., 2013, 25, 1542–1548 CrossRef CAS.
- A. Bhunia, V. Vasylyeva and C. Janiak, Chem. Commun., 2013, 49, 3961–3963 RSC.
- L. Hao, S. Zhang, R. Liu, J. Ning, G. Zhang and L. Zhi, Adv. Mater., 2015, 27, 3190–3195 CrossRef CAS PubMed.
- S. N. Talapaneni, T. H. Hwang, S. H. Je, O. Buyukcakir, J. W. Choi and A. Coskun, Angew. Chem., Int. Ed., 2016, 55, 3106–3111 CrossRef CAS PubMed.
- C. Krishnaraj, H. S. Jena, K. Leus and P. Van Der Voort, Green Chem., 2020, 22, 1038–1071 RSC.
- L. Guo, X. Wang, Z. Zhan, Y. Zhao, L. Chen, T. Liu, B. Tan and S. Jin, Chem. Mater., 2021, 33, 1994–2003 CrossRef CAS.
- L. Li, F. Lu, R. Xue, B. Ma, Q. Li, N. Wu, H. Liu, W. Yao, H. Guo and W. Yang, ACS Appl. Mater. Interfaces, 2019, 11, 26355–26363 CrossRef CAS PubMed.
- P. Bhanja, K. Bhunia, S. K. Das, D. Pradhan, R. Kimura, Y. Hijikata, S. Irle and A. Bhaumik, ChemSusChem, 2017, 10, 921–929 CrossRef CAS PubMed.
- S. Vargheese, M. Dinesh, K. V. Kavya, D. Pattappan, R. T. R. Kumar and Y. Haldorai, Carbon Lett., 2021, 31, 879–886 CrossRef.
- Y. Liu, Z. Zhao, W. Xu and W. Gong, Catal. Sci. Technol., 2024, 14, 3211–3218 RSC.
- M. G. Mohamed, S. U. Sharma, N. Y. Liu, T. H. Mansoure, M. M. Samy, S. V. Chaganti, Y. L. Chang, J. T. Lee and S. W. Kuo, Int. J. Mol. Sci., 2022, 23, 3174 CrossRef CAS PubMed.
- P. Kuhn, A. Thomas and M. Antonietti, Macromolecules, 2009, 42, 319–326, DOI:10.1021/ma802322j.
- A. O. Mousa, Z. I. Lin, C. H. Chuang, C. K. Chen, S. W. Kuo and M. G. Mohamed, Int. J. Mol. Sci., 2023, 24, 8966 CrossRef CAS PubMed.
- M. G. Mohamed, A. F. M. EL-Mahdy, M. M. M. Ahmed and S. W. Kuo, ChemPlusChem, 2019, 84, 1767–1774 CrossRef CAS PubMed.
- M. G. Mohamed, A. F. M. El-Mahdy, Y. Takashi and S. W. Kuo, New J. Chem., 2020, 44, 8241–8253 RSC.
- Z. Qinglan, W. Xianyou, W. Chun, L. Jing, W. Hao, G. Jiao, Z. Youwei and S. Hongbo, J. Power Sources, 2014, 254, 10–17 CrossRef.
- J. Hong, W. Xiaomin, G. Zhengrong and P. Joseph, J. Power Sources, 2013, 235, 285–292 Search PubMed.
- X. Pan and D. C. Webster, ChemSusChem, 2012, 5, 419–429 CrossRef CAS PubMed.
- P. Kuhn, M. Antonietti and A. Thomas, Angew. Chem., Int. Ed., 2008, 47, 3450–3453 CrossRef CAS PubMed.
- S. Mukherjee, M. Das, A. Manna, R. Krishna and S. Das, Chem. Mater., 2019, 31, 3929–3940 CrossRef CAS.
- L. Hao, J. Ning, B. Luo, B. Wang, Y. Zhang, Z. Tang, J. Yang, A. Thomas and L. Zhi, J. Am. Chem. Soc., 2015, 137, 219–225 CrossRef CAS PubMed.
- M. M. Samy, M. G. Mohamed and S. W. Kuo, Eur. Polym. J., 2020, 138, 109954 CrossRef CAS.
- M. G. Mohamed, M. Y. Tsai, W. C. Su, A. F. M. EL-Mahdy, C. F. Wang, C. H. Huang, L. Dai, T. Chen and S. W. Kuo, Mater. Today Commun., 2020, 24, 101111 CrossRef CAS.
- G. Wang, K. Leus, S. Zhao and P. Van Der Voort, ACS Appl. Mater. Interfaces, 2018, 10, 1244–1249 CrossRef CAS PubMed.
- A. O. Mousa, C. H. Chuang, S. W. Kuo and M. G. Mohamed, Int. J. Mol. Sci., 2023, 24, 12371 CrossRef CAS PubMed.
- R. A. Maia, F. L. Oliveira, V. Ritleng, Q. Wang, B. Louis and P. M. Esteves, Chem. – Eur. J., 2021, 27, 8048–8055, DOI:10.1002/chem.202100478.
- M. Ejaz, M. M. Samy, Y. Ye, S. W. Kuo and M. G. Mohamed, Int. J. Mol. Sci., 2023, 24, 2501 CrossRef CAS PubMed.
- M. M. Samy, M. G. Mohamed, S. U. Sharma, S. V. Chaganti, J. T. Lee and S. W. Kuo, J. Taiwan Inst. Chem. Eng., 2024, 158, 104750 CrossRef CAS.
- M. M. Samy, M. G. Mohamed, S. U. Sharma, S. V. Chaganti, T. H. Mansoure, J. T. Lee, T. Chen and S. W. Kuo, Polymer, 2023, 264, 125541 CrossRef CAS.
- M. G. Mohamed, M. H. Elsayed, Y. Ye, M. M. Samy, A. E. Hassan, T. H. Mansoure, Z. Wen, H. H. Chou, K. H. Chen and S. W. Kuo, Polymers, 2023, 15(15), 182 CAS.
- M. M. Samy, M. G. Mohamed and S. W. Kuo, Polymers, 2023, 15, 1095 CrossRef CAS PubMed.
- M. G. Mohamed, S. Y. Chang, M. Ejaz, M. M. Samy, A. O. Mousa and S. W. Kuo, Molecules, 2023, 28, 3234 CrossRef CAS PubMed.
- M. Madhu, S. Santhoshkumar, C. W. Hsiao, W. L. Tseng, S. W. Kuo and M. G. Mohamed, Macromol. Rapid Commun., 2024, 2400263 CrossRef PubMed.
- T. H. Weng, M. G. Mohamed, S. U. Sharma, I. M. A. Mekhemer, H. H. Chou and S. W. Kuo, ACS Appl. Energy Mater., 2023, 6, 9012–9024 CrossRef CAS.
- P. N. Singh, M. G. Mohamed, S. V. Chaganti, S. U. Sharma, M. Ejaz, J. T. Lee and S. W. Kuo, ACS Appl. Energy Mater., 2023, 6, 8277–8287 CrossRef CAS.
|
This journal is © The Royal Society of Chemistry 2024 |
Click here to see how this site uses Cookies. View our privacy policy here.