Polymer vessels in mechanochemical syntheses: assessing material performance†
Received
29th May 2024
, Accepted 10th July 2024
First published on 12th July 2024
Abstract
This work provides an overview of sixteen different polymers potentially applicable as vessel materials in mechanochemical reactions, facilitating the selection of the optimal material tailored to each system individually. The investigation focused on the chemical resistances, especially under simultaneous mechanical stress, and the long-term stability of the utilized polymers. To assess these aspects, two reference reactions were employed: the direct mechanocatalytic Suzuki coupling of iodobenzene and phenylboronic acid, and the acid-catalysed acetalization reaction of ethylene glycol and 3-nitrobenzaldehyde. The palladium abrasion of the precious milling ball material used in the Suzuki reaction was examined through ICP-OES measurements for the polymers studied. Additionally, the temperature resistance of the polymers was discussed, along with their aptitude for in situ monitoring.
Introduction
In the last decades, mechanochemistry has emerged as an increasingly important method in various fields of chemical research. Outstanding results can be reported for a large number of inorganic,1 as well as organic2–4 reactions, while enabling a more sustainable approach in modern day chemistry.4,5 As this novel field of chemistry continues to develop, the demands on the milling materials used are also altering, as particle size reduction is no longer the main objective.6 While most established materials like steel and zirconium oxide are well-suited for a range of simple chemical reactions due to their easily modifiable energy input and inert, chemical-resistant properties, there are advanced methods in mechanochemistry like thermomechanochemistry, direct mechanocatalysis and in situ monitoring, requiring tailored vessel materials. Especially in direct mechanocatalysis, whereby the milling material itself serves as catalyst, the vessel material needs to be sufficiently soft, to prevent excess abrasion of the precious metal catalyst and contamination of the product.7,8 For in situ monitoring the materials need to be transparent to laser light, as well as X-ray radiation. While combining external heating with mechanochemistry, the demand on the vessel is again different, as the materials need to be temperature stable and need to possess sufficient heat conductivity. It becomes clearly apparent that the commercially available materials in use are not optimized for numerous applications, therefore, a suitable alternative is mandatory. The optimal vessel material not only need to combine a sufficient density and chemical resistance, but also transparency regarding laser light and X-ray radiation, and further feature low hardness and elevated stability under these demanding chemical, mechanical and thermal conditions (Fig. 1). In the past, polymers like PMMA (polymethyl methacrylate), PTFE (polytetrafluoroethylene) or PFA (perfluoroalkoxy polymer) have been successfully used in various mechanochemical reactions, highlighting the fact that this group of materials could be an excellent choice for a vessel material.7–14 The used polymers, however, are exhibiting disadvantages as well, as PMMA for example, is not resistant against various organics, and PFA and PTFE are expensive and are currently encountering restrictions that might impede their future utilization.15 Considering the diverse range of polymers available, we aim to present an overview of sixteen distinct polymeric materials and their properties. Currently lacking a comprehensive guideline for material selection, we explore the six key parameters mentioned crucial for an ideal vessel material: cost-effectiveness, environmental impact, mechanical resilience, resistance to high temperatures and chemicals, and transparency regarding laser-, and X-ray radiation.
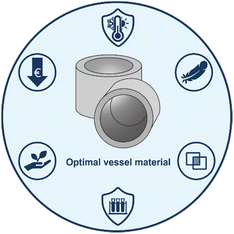 |
| Fig. 1 Summary of the optimum properties that a reaction vessel should possess to establish ideal conditions for various types of mechanochemical reactions. The optimal reaction vessel needs to possess sufficiently high density, while being soft, transparent, cost-efficient, environmentally friendly, resistant to low and high temperatures, as well as against various organic and inorganic chemicals. | |
Results and discussion
Prolog
All vessels employed in this work were produced through lathe processing, based on a uniform prototype. These vessels measure 66.0 mm in length and comprise an outer diameter of 29.8 mm, along with an inner diameter of 19.0 mm. To circumvent severe deformation of the vessel during the milling process, a wall thickness of 5 mm was chosen. The vessels are composed of two equal parts with identical dimensions, connected by a straightforward plug-in mechanism (Fig. 2B). Sixteen different thermoplastics were studied, which can be classified into three subgroups considering their temperature resistance, as well as their field of application: standard- (≤100 °C), construction- (≤150 °C) and high-performance (>150 °C) polymers.16,17 Here, both amorphous and semicrystalline polymers were chosen from the three polymer classes mentioned. Regarding the standard thermoplastics, one amorphous thermoplastic, PVC (polyvinylchloride), was employed. Additionally, PP (polypropylene), PE-HD (high-density polyethylene) and PE-UHMW (polyethylene with ultra-high molecular weight) were selected from the pool of semicrystalline standard thermoplastics. In case of semicrystalline construction thermoplastics, PA6 (polyamide 6), PA66 (polyamide 66), PET (polyethylene terephthalate) and POM C (polyoxymethylene copolymer) were chosen. To achieve an increased hardness and heat deflection temperature due to an improved support of the nylon matrix, glass fibre reinforced thermoplastics were included in this study. Thereto, PA6 GF30 (polyamide 6 reinforced with 30% glass fibres), as well a PA66 GF30 (polyamide 66 reinforced with 30% of glass fibres) were utilized. A solid lubricant modified polyethylene (PET GX) has been chosen for its advantageous sliding properties. Additionally, the amorphous construction thermoplastic PC (polycarbonate) and its glass fibre reinforced counterpart PC GF were tested, as well as PFA, PEEK (polyetheretherketone) and PEEK GF from the group of semicrystalline, high-performance thermoplastics.
 |
| Fig. 2 Schematic representation of the vessel dimensions (A) and the straight-forward plug-in mechanism (B). | |
To gain an initial overview of the features of the materials tested, certain material properties are considered in the next chapter. However, as the emphasis lies on performance under real conditions, the stability of the vessel underwent testing not only during extended milling periods but also through the execution of two distinct reactions, aiming to encompass a broad spectrum of requirements. Here, the acetalization reaction of 3-nitrobenzaldehyde and ethylene glycol served as measure of the vessel materials performance regarding the yields obtained under these demanding chemical and mechanical conditions. The Suzuki coupling, on the other hand, was conducted to investigate their abrasion resistance. Furthermore, an overview of their suitability regarding in situ measurements, as well as thermomechanochemistry is given.
Material properties
One of the most important characteristics a reaction vessel needs to possess is high chemical resistance. The properties shown in Fig. 3A indicate varying suitability of the chosen materials for different reactions, emphasizing the need to tailor the vessel material selection individually to achieve optimal conditions. PFA, PP and PE-HD are exhibiting high chemical resistance, rendering them suitable materials for a wide range of reactions. Especially considering the low price of PP and PE-HD (Fig. 3C) compared to PFA, they should be shortlisted if strong oxidizing acids are not necessary in the regarded system. Despite PP and PE-HD being only partially resistant to certain organics, durability may be elevated, as mechanochemistry primarily operates with little to no solvent and the reactants are typically dispersed within a solid bulk material. This also applies to PE-UHMW, despite its diminished persistence to halogenated hydrocarbons compared to PE-HD. The chosen polyamides are exhibiting high resistance to most organics, although halogenated hydrocarbons, as well as strong and oxidizing acids should be avoided, or only used in small amounts, diluted in an appropriate bulk material. PC, PET GX and PVC on the other hand are exhibiting rather low chemical resistance, nonetheless, especially PET GX and PVC could be favourable alternatives for one-time use due to their low price (Fig. 3C). The price, but also the potential impact of the different materials on the environment, are important factors that need to be considered as well. Therefore, the global warming potential (GWP) serves as simplified measure, as the assessment of the sustainability of a material or a process is complex. Risks regarding for example human health, or the pollution of soil, groundwater or seas are not included in this value. The studied polyamides, their glass fibre reinforced counterparts, as well as PC show higher GWPs, as well as slightly higher prices compared to PP, PE-HD, PET and PVC (Fig. 3C). Therefore, especially PP, PE-HD and PVC could be suitable alternatives for one time use as well. Comparing the prices of PEEK, PEEK GF and PFA to the other thermoplastics utilized, it is apparent, that these materials should only be considered when sufficient durability can be ensured.
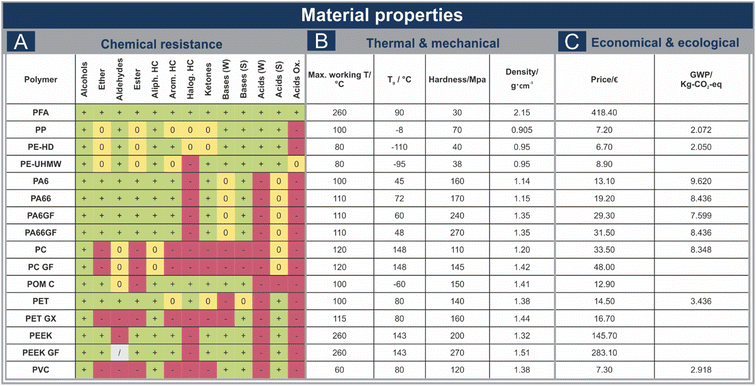 |
| Fig. 3 (A) Table of chemical properties including the chemical resistance of the 16 different polymers used. Green (+) indicates excellent chemical resistance of the material, while yellow (0) is representing partial resistance. Red boxes (−) demonstrate poor resistance of the material regarding the substance group stated. Additionally, the maximum working and glass transition temperature, the hardness as well as the density of the materials used are shown (B). Economical and ecological factors are additionally considered, namely the price and the global warming potential. (C) The global warming potential was ascertained through the software “open LCA” using the database “exiobase”. The missing data still need to be determined. | |
Material performance under mechanical stress
In preparation for initial use, the vessels were pre-milled for one hour at 35 Hz each using K2CO3 and ethanol, along with a steel ball. Ensuring the smoothness of the vessel surface is crucial to prevent remaining shavings from the manufacturing process, thus minimizing the risk of heightened contamination. Furthermore, vessels that cannot withstand the mechanical stress can be immediately ejected from the study. After this procedure, the PC and PC GF vessels already showed considerable damage, consequently precluding their continued utilization (ESI, Fig. S2C and D†).
Further PET displayed extensive damage (ESI, Fig. S2A†) after prolonged reaction times. This is likely to be caused by the high hydrolysis sensitivity of the material and the alkaline conditions applied during milling. After repeating this experiment using sodium chloride instead of potassium carbonate, PET proved satisfactory durability, showing that basic bulk materials should only be used short-term, to ensure sufficient stability. In case of the PEEK vessel, metal particles of the ball material used were incorporated into the vessel ends during the milling process (ESI, Fig. S2B†). Hence, the possibility of contamination and the occurrence of side reactions in subsequent experiments should be contemplated. The remaining materials employed proved contenting long-term stability, rendering them suitable for use in mechanochemical reactions, even under high frequencies and extended reaction times. This is also reflected in the approximate polymer abrasion, which was determined through gravimetrical tests (ESI, Fig. S1†).
Material performance during mechanochemical reaction
To investigate the influence of the exposure of different chemicals in addition to the simultaneously occurring mechanical impact, the first reference reaction selected is a simple acid catalysed acetalization reaction of 3-nitrobenzaldehyde and ethylene glycol (Fig. 4A). Here, the influence of a strong acid, as well as different organic species can be detected while mechanical stress is simultaneously affecting the durability of the vessels. The yields attained for various vessels, considering the material densities, are illustrated in Fig. 4B. Interestingly, there is no correlation observable regarding the yield and the densities of the materials investigated. It needs to be considered, however, that the densities of the tested materials are significantly lower compared to the commonly used materials like steel (7.87 g cm−3) or ZrO2 (5.89 g cm−3). The densities of the polymers tested, on the other hand, are highly similar, which is why the influence of these is presumably not decisive. The results show that the tested thermoplastics display slightly lower yields compared to PFA, but primarily higher, or similar yields compared to the commercially available steel and zirconia jars. Nevertheless, PP, PA66, PE-HD and PE-UHMW can potentially be used as alternatives to the commonly used polymers. PA66 GF shows similar yields to PA66, but there was severe abrasion of the polymer, as well as the ball material observable, which possibly leads to the contamination of the product. This is further discussed in the next chapter.
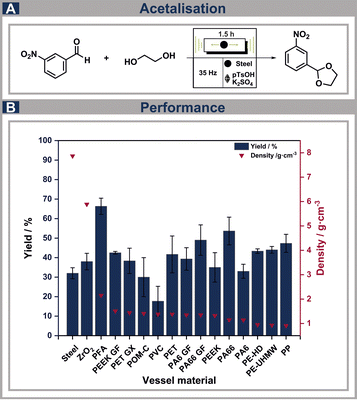 |
| Fig. 4 (A) Reaction scheme of the acetalization reaction. (B) Yields of the acetalization reaction of 3-nitrobenzaldehyde and ethylene glycol using the different vessel materials, as well as their respective densities. Further, a 14 ml steel vessel, as well as a 10 ml ZrO2 jar were used as reference. All reactions were repeated 3 times to ensure reproducibility. The reactions were conducted in a MM500 mixer mill by Retsch at a milling frequency of 35 Hz for 1.5 h and one steel ball with a diameter of 10 mm was used. In case of the zirconia jar, one ZrO2 ball (Ø 10 mm) was used. | |
Material performance regarding milling ball abrasion
The direct mechanochemical Suzuki coupling (Fig. 5A) was performed to incorporate the impact of the vessel material's hardness, which is of significant importance in direct mechanocatalytical reactions, as this is crucial for minimizing the abrasion of the precious metal catalyst employed. Fig. 5 displays the ICP-OES (Inductively Coupled Plasma – Optical Emission Spectroscopy) data obtained from measuring the palladium content of the Suzuki reaction in dependence of the material hardness (Fig. 5B). It is apparent, that most thermoplastics investigated exhibit low abrasion of the valuable ball material, due to the inherent softness of thermoplastics. Along with the softness of thermoplastic polymers, these are susceptible to deformation which can be an obstacle. This issue was addressed by incorporating glass fibre reinforced materials to enhance the vessel stability. Nevertheless, material reinforcement results in increased density and hardness, along with the potential for additional ball damage from glass fibre fragments that may be present on the vessel surfaces, making these materials highly abradant. It is observable, that all glass fibre reinforced polymers are associated with a strikingly high palladium abrasion, which clearly shows that these materials are unsuitable for numerous mechanochemical reactions due to the elevated contamination of the generated product, as well as the substantial losses of the precious ball material involved in direct mechanocatalytic reactions. Only one of the non-glass fibre reinforced polymers, namely PEEK, showed an elevated ball abrasion, due to the slightly increased hardness of this material compared to the other thermoplastics utilized. This indicates the importance of choosing materials for direct mechanocatalysis with hardness values not surpassing that of PA66 (approx. 170 MPa). Following the reactions, further damage to some of the materials used was detected. The glass fibre-reinforced polymers, specifically PA6 GF and PA66 GF, but also PVC and PEEK exhibited polymer fragments distinctly observable in the solution during the work-up process, which is also apparent through EDS (energy dispersive spectroscopy) measurements (Fig. 5C). This leads to the materials being unsuitable due to poor vessel stability, as well as further contamination of the reaction products. For the yields of the Suzuki coupling using the tested polymers, similar trends can be observed, as for the acetalization reaction (ESI, Fig. S26†).
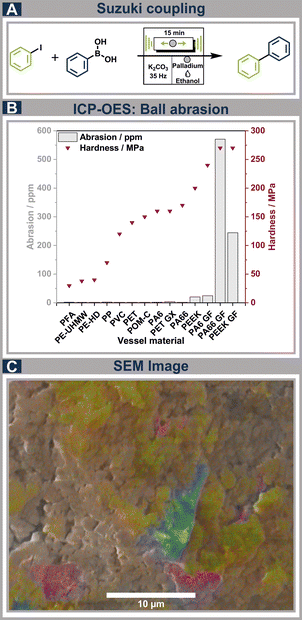 |
| Fig. 5 (A) Illustrates the reaction scheme of the Suzuki coupling. (B) Shows the Pd abrasion in ppm for the tested polymers in dependence of their respective hardness. As reference reaction, a simple Suzuki coupling of iodobenzene and phenylboronic acid was conducted. (C) Shows an EDS measurement of the raw reaction mixture of the Suzuki coupling using a PA6 GF vessel. Si (blue) was detected in the mixture, which shows that the material itself got abraded. | |
In situ monitoring
In order to conduct Raman measurements, the materials need to be transparent, which already excludes certain materials studied, however PP, PE-HD, PE-UHMW, PA6 and PA66 were tested to observe their suitability. As previously shown with PFA, despite being opaque featuring a wall thickness of 5 mm, reducing the wall thickness to 2 mm results in the material's transparency being sufficient to conduct in situ Raman measurements.7 Therefore, the other semi-transparent materials mentioned could be suitable as well.
The results display product peaks with low intensities, generally the range of possible measurable peaks is comparable to these of PFA and PMMA (ESI, Fig. S20–S25†). Under optimised conditions, all tested materials could be alternatives to PFA, as well as PMMA (Fig. 6A), but possible interferences with the measured substances need to be contemplated. Additionally, PXRD spectra were obtained for the semicrystalline polymers to assess their potential suitability for in situ measurements (Fig. 6B). Notably, PFA exhibited one single, distinct reflection at approximately 17°, minimizing the probability of overlapping reflections of numerous substrates, which is also reflected in several in situ measurements conducted.8,18 Moreover, PA6, PA66 and their glass fibre reinforced counterparts, as well as PE-HD, PE-UHMW, PET GX and PP are emerging as promising candidates for in situ monitoring, whereas POM C, PET, PEEK and PEEK GF are displaying reflections ranging from 20° to 50°, which may intersect with the substances being measured. PVC, generally being the only amorphous thermoplastic, is the most appropriate alternative if no additives are used in the manufacturing process, as no interference with substance peaks is possible.
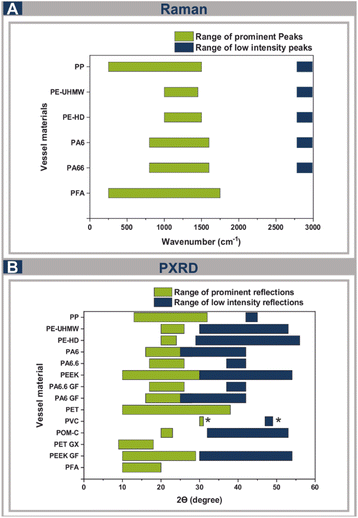 |
| Fig. 6 (A) Shows the regions with prominent (green) and low intensity (blue) peaks in the Raman spectra of the tested polymers. (B) Shows the areas of prominent (green) and low intensity (blue) reflections in the PXRD spectra of the tested polymers. *Reflections are caused by an additive, as PVC itself is amorphous. | |
Material performance under elevated temperatures
While mechanochemistry typically operates without heating the reaction mixture, there are instances where external heating becomes an effective tool to increase reaction efficiency.19,20 As the vessel material in thermomechanochemical transformations experiences simultaneous mechanical stress, the vessels can potentially not be employed continuously at their maximum working temperatures (Fig. 3B). This became particularly evident, as some vessels were displaying minor damage while heating to the maximum working temperature recommended by the manufacturer (ESI, Fig. S5†). All standard and construction polymers could, however, be used at temperatures 10 °C below their maximum working temperature. For the chosen high-performance polymers, temperature elevation beyond 240 °C was precluded, as in the case of PFA observable melting of the vessel was evident. PEEK and PEEK GF, however, were successfully used at 240 °C under milling conditions. To maintain safety standards and ensure the durability of the vessels, it is recommendable to limit the temperature during milling to approx. 200–240 °C for PEEK and PEEK GF, as well as 190 °C for PFA and to ensure sufficient ventilation.
Performance assessment
The overall performance (Fig. 7G) of the materials is quantified by comparing the most important properties a reaction vessel in mechanochemical transformations needs to possess. The ball abrasion, the chemical resistance, the long-term and temperature stability, their suitability regarding in situ measurements, as well as their price were considered and compared to be able to facilitate the decision of the determination of the most appropriate material for every system individually (Fig. 7A–F). An excellent performance is highlighted by numbers between 2 and 5, depending on which property was evaluated. As performance declines, so do the associated values. The assessment demonstrates that especially PP, PE-HD, PE-UHMW, as well as PA 6, PA 66 and PFA are combining various of the properties important in mechanochemical reactions (Fig. 7H). Especially their softness, and their long-term stability making these materials highly interesting for this solid-state technique. All tested materials are possible alternatives for in situ Raman and PXRD measurements and show high chemical resistances, therefore, being an applicable choice for various organic, as well as inorganic reactions. PE-HD, PP, PE-UHMW and the polyamides PA 6 and PA 66 are especially beneficial due to their low costs. PFA, but also the polyamides are an appropriate choice if slightly elevated temperatures are needed. On the contrary, materials reinforced with glass fibres exhibit notably inferior performance. As a result, these materials are not advisable for mechanochemical transformations.
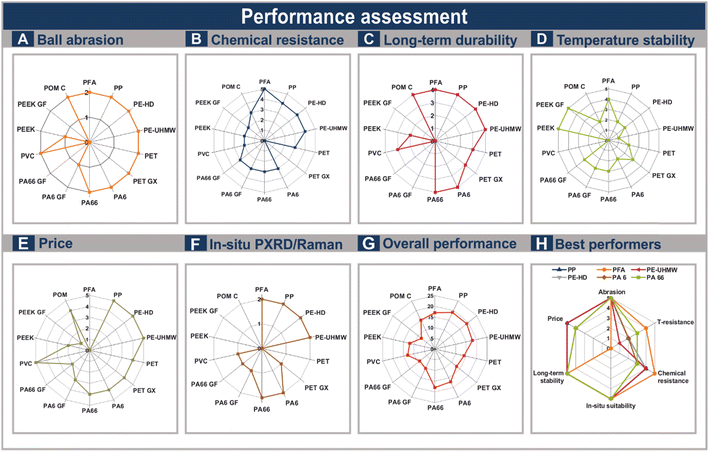 |
| Fig. 7 Performance assessment of the tested polymers. (A) Shows the potential for ball abrasion. Therefore, values from 0 to 3 were assigned to the materials, with 3 corresponding to low abrasion and 0 to high abrasion. (B) Compares the chemical resistances of the tested thermoplastics. Values of 0 to 5 were assigned, whereby 5 corresponds to highest chemical resistance. Diminished chemical resistances are represented by decreasing numbers. (C) Is quantifying the long-term stability of the materials compared. Values of 5 are assigned to materials featuring high long-term stability. (D) Is showing the comparison of the stability of the materials tested regarding elevated temperatures. A number of 5 is representing excellent temperature stabilities, while decreasing numbers are showing lower durability under elevated temperatures. (E) Compares the price of the materials investigated. A value of 5 is assigned to materials with low prices. More expensive materials are assigned to lower values. (F) Compares the materials regarding their suitability either for in situ Raman or in situ PXRD measurements. A material that can be used as vessel material for both techniques are assigned to a number of 2, while materials that can only be used for one of the techniques are ranked with a 1. Materials that cannot be used for these in situ techniques are assigned to a value of 0. (G) Is quantifying the material's overall performance. Therefore, the values of (A–F) were added. The six best performing materials, namely PP, PE-HD, PE-UHMW, PA6, PA66 and PFA were compared in (H). To ensure good comparability between the different properties in this diagram, the scale was adjusted to a maximum of 5 for all properties compared. | |
Conclusions
This study offers a comprehensive overview of 16 polymers, highlighting their potential suitability as vessel materials in mechanochemistry. Each tested material showcases a diverse array of properties, showing that the vessel material can be altered depending on the system. Among the materials tested, PP and PE-HD combine several critical parameters essential for mechanochemistry. Additionally, PE-UHMW, PA66, PA6 and PFA demonstrate excellent performances. For direct mechanocatalysed reactions, all six materials are appropriate choices, whereas PA66, PP, PE-HD and PE-UHMW are arguably the most appropriate selection, due to their low price combined with sufficient yields and low abrasion of the precious ball material. In thermomechanochemical applications, PFA stands out as an exceptional vessel material, capable of withstanding temperatures up to 190 °C under milling conditions. For applications requiring only slightly elevated temperatures, the other best-performing polymers also prove to be viable options. Overall, while material selection should be tailored to the specific reaction, the tested polymers present highly promising alternatives to the currently established materials.
Data availability
The data supporting this article have been included as part of the ESI.†
Author contributions
Marisol Fabienne Rappen: conceptualization, data curation, formal analysis, investigation, methodology, verification, visualization, writing – original draft. Lars Beissel: formal analysis, investigation, verification. Jonathan Geisler: formal analysis, investigation, verification. Simeon Theodor Tietmeyer: formal analysis, investigation, verification. Sven Grätz: conceptualization, data curation, funding acquisition, project administration, resources, supervision, writing – review & editing. Lars Borchardt: conceptualization, data curation, funding acquisition, project administration, resources, supervision, writing – review & editing.
Conflicts of interest
There are no conflicts to declare.
Acknowledgements
We gratefully acknowledge the German Research Foundation, Deutsche Forschungsgesellschaft (DFG), for the funding of the project BO 4538/6-1. We acknowledge Iris Henkel and Marén Schwandt from TU Dortmund for performing ICP-OES measurements. Furthermore, we want to thank Stefanie Hutsch for conducting EDS and PXRD measurements.
References
- E. Boldyreva, Mechanochemistry of inorganic and organic systems: what is similar, what is different?, Chem. Soc. Rev., 2013, 42, 7719–7738 RSC.
- Z. Li, Z. Jiang and W. Su, Fast, solvent-free, highly enantioselective three-component coupling of aldehydes, alkynes, and amines catalysed by the copper(II)pybox complex under high-vibration ball-milling, Green Chem., 2015, 17, 2330–2334 RSC.
- C. Wang, M. Hill, B. Theard and J. Mack, A solvent-free mechanochemical synthesis of polyaromatic hydrocarbon derivatives, RSC Adv., 2019, 9, 27888–27891 RSC.
- G.-W. Wang, Mechanochemical organic synthesis, Chem. Soc. Rev., 2013, 42, 7668–7700 RSC.
- K. J. Ardila-Fierro and J. G. Hernández, Sustainability Assessment of Mechanochemistry by Using the Twelve Principles of Green Chemistry, ChemSusChem, 2021, 14, 2145–2162 CrossRef CAS.
-
A. J. Lynch and C. A. Rowland, The History of Grinding, Society for Mining, Metallurgy, and Exploration, Littleton, Colo, 1st edn, 2005 Search PubMed.
- W. Pickhardt, C. Beaković, M. Mayer, M. Wohlgemuth, F. J. L. Kraus, M. Etter, S. Grätz and L. Borchardt, The Direct Mechanocatalytic Suzuki-Miyaura Reaction of Small Organic Molecules, Angew. Chem., Int. Ed. Engl., 2022, 61, e202205003 CrossRef CAS.
- W. Pickhardt, E. Siegfried, S. Fabig, M. F. Rappen, M. Etter, M. Wohlgemuth, S. Grätz and L. Borchardt, The Sonogashira Coupling on Palladium Milling Balls-A new Reaction Pathway in Mechanochemistry, Angew. Chem., Int. Ed. Engl., 2023, 62, e202301490 CrossRef CAS PubMed.
- D. M. Baier, C. Spula, S. Fanenstich, S. Grätz and L. Borchardt, The regioselective Solid-State Photo-Mechanochemical Synthesis of Nanographenes with UV light, Angew. Chem., Int. Ed., 2023, 62, e202218719 CrossRef CAS PubMed.
- M. Juribašić, K. Užarević, D. Gracin and M. Ćurić, Mechanochemical C–H bond activation: rapid and regioselective double cyclopalladation monitored by in situ Raman spectroscopy, Chem. Commun., 2014, 50, 10287–10290 RSC.
- A. A. L. Michalchuk and F. Emmerling, Time-Resolved In Situ Monitoring of Mechanochemical Reactions, Angew. Chem., Int. Ed. Engl., 2022, 61, e202117270 CrossRef CAS PubMed.
- J. G. Hernández, Mechanochemical borylation of aryldiazonium salts; merging light and ball milling, Beilstein J. Org. Chem., 2017, 13, 1463–1469 CrossRef PubMed.
- D. Gracin, V. Štrukil, T. Friščić, I. Halasz and K. Užarević, Laboratory real-time and in situ monitoring of mechanochemical milling reactions by Raman spectroscopy, Angew. Chem., Int. Ed. Engl., 2014, 53, 6193–6197 CrossRef CAS.
- S. T. Emmerling, L. S. Germann, P. A. Julien, I. Moudrakovski, M. Etter, T. Friščić, R. E. Dinnebier and B. V. Lotsch,
In situ monitoring of mechanochemical covalent organic framework formation reveals templating effect of liquid additive, Chem, 2021, 7, 1639–1652 CAS.
- T. Thomas, A. Malek, J. Arokianathar, E. Haddad and J. Matthew, Global Regulations Around PFAS: The Past, the Present and the Future, International Chemical Regulatory and Law Review, 2023, 6, 3–17 Search PubMed.
-
M. Biron, Thermoplastics and thermoplastic composites. Technical Information for Plastics Users, Butterworth-Heinemann, Amsterdam, Boston, 2007 Search PubMed.
-
D. K. Platt, Engineering and High Performance Plastics Market Report. A Rapra Market Report, Rapra Technology Ltd, Shawbury, Shrewsbury, Shropshire, UK, 2003 Search PubMed.
- M. Sander, S. Fabig and L. Borchardt, The Transformation of Inorganic to Organic Carbonates: Chasing for Reaction Pathways in Mechanochemistry, Chemistry, 2023, 29, e202202860 CrossRef CAS PubMed.
- J. Alić, T. Stolar, Z. Štefanić, K. Užarević and M. Šekutor, Sustainable Synthesis of Diamondoid Ethers by High-Temperature Ball Milling, ACS Sustainable Chem. Eng., 2023, 11, 617–624 CrossRef.
- V. Martinez, T. Stolar, B. Karadeniz, I. Brekalo and K. Užarević, Advancing mechanochemical synthesis by combining milling with different energy sources, Nat. Rev. Chem, 2023, 7, 51–65 CrossRef CAS PubMed.
|
This journal is © The Royal Society of Chemistry 2024 |
Click here to see how this site uses Cookies. View our privacy policy here.