DOI:
10.1039/D4PY00851K
(Review Article)
Polym. Chem., 2024,
15, 4375-4415
Polyols from cashew nut shell liquid (CNSL): corner-stone building blocks for cutting-edge bio-based additives and polymers
Received
1st August 2024
, Accepted 29th September 2024
First published on 2nd October 2024
Abstract
Polyols are versatile molecules present in many polymer materials that are used and often essential in daily life. However, most bio-based polyols are derived from sugar or vegetable oil, and thus, their production directly competes with the food industry. In this case, CNSL is a promising non-edible renewable resource, which is directly extracted from the shell of cashew nuts. The interesting chemical structure of CNSL and its derivatives (cardanol and cardol) has led to the synthesis of original polyols with hydrophobic and internal plasticizing properties. Useful for the development of additives such as surfactants and soft polymers, CNSL polyols are progressively occupying a unique position in the polymer industry. This review focuses on the use of CNSL as a building block for various polyols. Many different chemical pathways leading to CNSL-based polyols are reviewed and evaluated. Furthermore, we focus on the use of these CNSL-based polyols as surfactants and polymer precursors and the contribution of their specific chemical structure (aromatic ring and long unsaturated alkyl chain) to the properties of the resulting polyesters or polyurethanes.
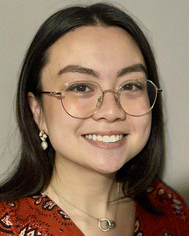 Emilie Rojtman | Emilie Rojtman graduated in 2022 as a chemical engineer at the Ecole Nationale Supérieure de Chimie de Mulhouse (France), specializing in formulation and cosmetology. During her last year, she completed a one-year apprenticeship at Arkema, working on organic peroxide formulation. She is currently employed by Orpia Innovation and is pursuing a PhD at the Institut Charles Gerhardt in Montpellier (France). Her research focuses on the synthesis of building blocks using cashew nut shell liquid compounds based on the principles of green chemistry to develop biobased polyesters. |
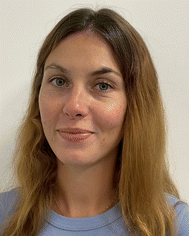 Maxinne Denis | Dr Maxinne Denis received her PhD in 2022 from the University of Montpellier under the supervision of Dr Claire Negrell and Dr Sylvain Caillol in collaboration with a French company, Lixol, on the synthesis of biobased phosphorus flame retardants for alkyd resins. Since 2023, she has been working at Orpia Innovation as a project manager. She focuses on the development of new CNSL-based molecules for use in various polymer syntheses. |
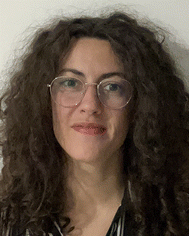 Camille Sirvent | Camille Sirvent received her master's degree in 2022 from the University of Montpellier. After graduating, she worked at Orpia Innovation as an engineer. She studied the synthesis of new CNSL-based molecules used in different polymer synthesis. Since 2024, she has worked at CEA at Fontenay-aux-roses on chemical and nuclear waste sanitation and dismantling. |
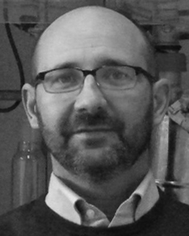 Vincent Lapinte | Vincent Lapinte, Chemist in the polymer field, joined the Institute Charles Gerhardt of Montpellier (ICGM), Department of Polymers, in 2004. He has published around 90 articles and 12 patents (H-index 24). His research mainly covers the chemistry and self-assembly of peptoides such as polyoxazolines and their use as biomaterials. He also investigated biobased polymeric materials and biobased additives (plasticizers, surfactants, and rheological agents) for polymers especially coming from lipids (oils, card(an)ol), etc. |
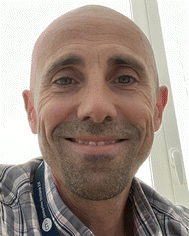 Sylvain Caillol | Sylvain Caillol is Research Director at CNRS. He graduated as an engineer from the National Graduate School of Chemistry of Montpellier in 1998. He obtained his doctorate in 2001 from the University of Bordeaux. Later, he joined the Rhodia Company, where he headed polymer research department at the Paris Research Center. In 2007, he joined the CNRS at the Charles Gerhardt Institute at the University of Montpellier. His research focuses on biobased polymers and the sustainable design of polymers. He won the Green Materials Prize in 2018 and 2020 and the Carnot Prize in 2023. |
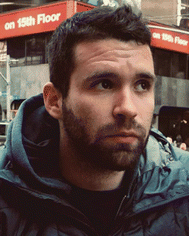 Benoit Briou | Dr Benoit Briou, received his PhD in 2018 from the University of Montpellier supervised by Dr Sylvain Caillol and Dr Vincent Lapinte in France on the valorisation of cardanol in the polymer field. He works as Head of the Research and Development Department of Orpia Innovation. He established a laboratory in Montpellier in 2020 and is supervising a team of researchers and PhD students. The topics of his research concern biobased building blocks and green chemistry for the development of additives and polymer materials, especially cashew nut coproducts. |
I. Introduction
Since their development and commercialization in the last century, polymer materials, commonly known as “plastic”, have become ubiquitous and almost indispensable in our daily lives. Being versatile, lightweight, resistant, practical, and economically affordable, polymers can be found in the automotive, construction, packaging, decoration and medical fields. The increase in the manufacturing and use of these synthetic materials coincides closely with the exploitation of petroleum. For more than 50 years, the chemical industry has been obtaining its building blocks from petrochemicals.2 However, access to this fossil resource is becoming increasingly limited and restrictive. Furthermore, easily accessible stocks are being depleted, increasing the costs of extracting petroleum materials from underground reservoirs or in geographical areas with harsh climates.3 Access to this resource is becoming increasingly strategic from a geopolitical and economic point of view. In addition, health and environmental issues due to pollution are becoming increasingly severe.4 Recently, the Covid pandemic and international crisis are pushing countries to regain control by increasing innovation and developing the resources and knowledge present in their territory.5,6 In addition, the climate crisis looms, and thus, there has been growing interest in finding sustainable and eco-compatible alternatives for societies with an increasing population and economy.7,8
Researchers and industries are now increasingly turning to the development of abundant and renewable biomass, which has been neglected in the last century, to address the problems of the food industry and the preservation of forest areas. To respond to this giant puzzle, several bioresources are being considered, such as vegetable oils, wood, sugars, and agricultural waste. A new field in chemistry also emerged in the 90s—green chemistry, by Anastas and Warner—with the establishment of the definition and principles of more sustainable chemistry.9
Among the many polymer precursors, polyols are of particular interest since they can be found in a multitude of applications. Besides the use of polyols in the food industry as an ingredient or food additive,10,11 they are used in the synthesis of highly convenient polymers such as polyurethanes12,13 and polyesters.14,15 These types of polymers are among the most produced after polyolefins and represent a significant and growing challenge. Given that they are easily functionalized, these molecules are also used in the synthesis of precursors of esters in various fields such as non-ionic surfactants. In the additive sector, the demand for bio-based and non-toxic materials is high. Additives, which are not bound to polymers, eventually migrate, together with surfactants used directly in the presence of water, representing a health and ecological concern.16–19 In view of the fields in which they are involved and considering the current environmental, economic, and climatic issues, particular interest is focused on the synthesis and application of bio-based polyols (Fig. 1a).
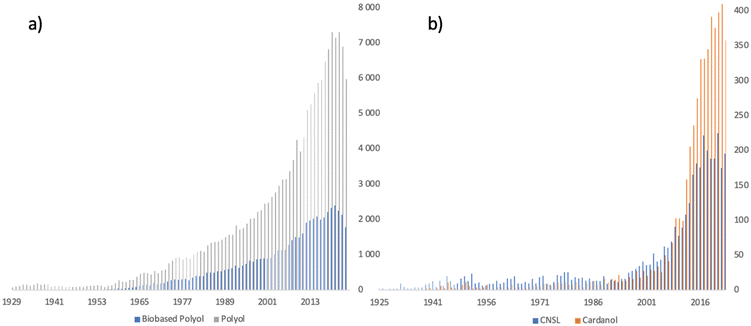 |
| Fig. 1 Graph showing the number of articles concerning polyols/bio-based polyols (a) and CNSL/cardanol (b) from the 20s to the present (source Sci-Finder). | |
Depending on their application, the sources of these bio-based polyols vary and seem to be specialized. For the synthesis of non-ionic surfactants, sugars and some of their derivatives,20–22 vegetable oils23 and even natural phenols such as cardanol23,24 are used. Finally, the monomers and polymers are generally linear derivatives from vegetable oils.25–27 However, the extraction and the production of these molecules (sugar and vegetable oil) directly conflict with the harvests reserved to produce biofuel and those reserved for direct animal and human food or food additives such as erythritol28 and sometimes glycerol.29 This competition tends to accelerate the phenomena of deforestation30 and environmental pollution with the use of dangerous fertilizers or pesticides, making the effort counterproductive in relation to the initial objectives.
The chemical structure of a polyol is of great importance regarding its use for a particular field of application. Whether sugar or vegetable oil derivatives, the extracted chemical molecules generally lack an aromatic ring, which is often provided by co-monomers, isocyanate for polyurethanes or carboxylic acid for polyesters. Generally, these aromatic rings provide structural rigidity and endow the resulting polymer structures with thermal stability. Natural phenols, such as vanillin and eugenol, can serve as platform of molecules for the synthesis of polyols possessing an aromatic ring.31–36 In addition, among the phenols, cashew nut shell oil (CNSL) derivatives have attracted increasing over the last 30 years for the synthesis of polymers or additives (Fig. 1b). These natural lipid phenols are relevant candidates for the synthesis of future bio-based polyols, given that they are obtained from the recovery of a waste product from the already existing agricultural production of cashew nuts.
To the best of our knowledge, CNSL derivatives for the synthesis of polyols are regularly discussed in specialized reviews on bio-based polyols37–39 but the part devoted to them remains small in view of the many developments demonstrated for these derivatives with time. Furthermore, none of these reviews focused on the wide variety of polyol structures that can be obtained from CNSL derivatives, although these molecules are intensively desirable. Also, when they were mentioned, the other components of CNSL were neglected to the detriment of cardanol. Thus, herein, we present a complete overview of the synthesis of polyol precursors based on CNSL derivatives to map and evaluate these various synthesis methods, and subsequently demonstrate the interest of the use of these molecules and their impact on the properties of the materials produced using them in the field of polymers and surfactants, which has never has been done before. Finally, in conclusion, we the possible future developments and perspectives regarding the development of polyols from CNSL.
II. Synthesis of diols from cashew nut shell liquid (CNSL)
1. Cashew nut shell liquid, a versatile bio-based raw material
Cashew nut shell liquid is a natural dark-brown viscous liquid extracted from the shell of the cashew nut, which protects the fruit of the cashew tree (Anacardium Occidentale).40,41 This tree is native to Brazil and the coastal areas of Asia and Africa. Nowadays, it is cultivated in many tropical and subtropical regions. Moreover, cashew nut shell is considered inedible waste from the food industry. The annual world production of cashew nuts is estimated to be around 4M T per year,42 where the shell represents 55–65% of the mass of cashew nuts.43
Natural CNSL mainly contains three components including anacardic acid, cardol and cardanol. The chemical structures of these compounds are presented in Fig. 2. CNSL can be extracted from the shell by different methods such as roasting, hot-oil bath, steam processing at 270 °C, quick roasting at 300 °C, and solvent extraction method.44–46 Thereby, depending on the extraction method used, the composition and the percentage of the CNSL constituents differ, as presented in Fig. 2. The extraction of CNSL at high temperatures leads to the decarboxylation of anacardic acid converted into cardanol (above 140 °C) and releases CO2.47,48 CNSL from these extraction methods is called “technical CNSL”, which is mainly composed of cardol (10–20%) and cardanol (70–80%). Alternatively, the extraction of CNSL at low temperature preserves anacardic acid, leading to “natural CNSL”. Thus, natural CNSL is mainly composed of anacardic acid (60–70%), cardol (10–20%) and cardanol (<10%). Methyl cardol is also present in both CNSLs at a percentage of less than 3% as well as some traces of urushiol. The different compounds of CNSL can be isolated by precipitation or distillation. The former separates anacardic acid from cardanol and cardol, whereas the latter is effective in separating cardanol and cardol.49,50
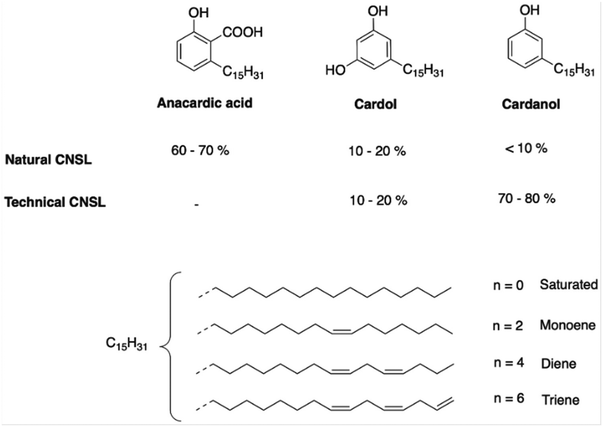 |
| Fig. 2 Chemical structures and compositions of natural and technical CNSL constituents. | |
The aliphatic chain of each molecule of CNSL can be found in four different forms including saturated, monoene, diene and triene. These constituents also contain several reactive sites such as hydroxy functions, an aromatic ring, and unsaturated aliphatic chains, and a carboxylic acid function for the anacardic acid compound. CNSL behaves like vegetable oils due to their unsaturated aliphatic chains; consequently, they exist in oil form, whereas molecules with hydrogenated aliphatic chains exist in solid form.
Due to their various reactive functions, CNSL compounds are promising bio-based phenols, allowing functionalization through numerous reactions, as presented in Scheme 1.40 Mannich,51,52 polycondensation53,54 and nitration reactions55,56 can occur on the aromatic ring. Then, the hydroxy functions can be functionalized through esterification,57 etherification or nucleophilic substitution.58,59 Moreover, epoxidation,59,60 hydrogenation,61–63 carbonation,64 thiol–ene65 and Diels–Alder66 reactions can also take place at the unsaturated sites in the alkyl chain.
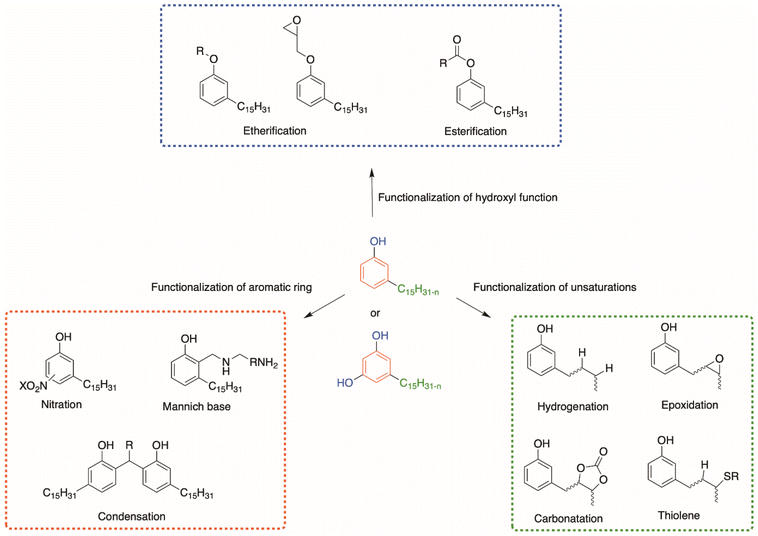 |
| Scheme 1 Overview of different pathways to functionalize CNSL compounds. | |
This review focuses on the numerous pathways described in the literature to functionalize CNSL compounds into reactive polyols. The rigid aromatic ring and flexible long alkyl chains of CNSL molecules differentiate them from other natural polyols such vanillin, eugenol, coumaric acid, saccharides, tannins, glycerol, and vegetable oils (castor oil) (Fig. 3), which exhibit either a rigid or a flexible structure. Thus, CNSL compounds can endow materials with unique properties such plasticizing60,67 and lubricant effects.68,69
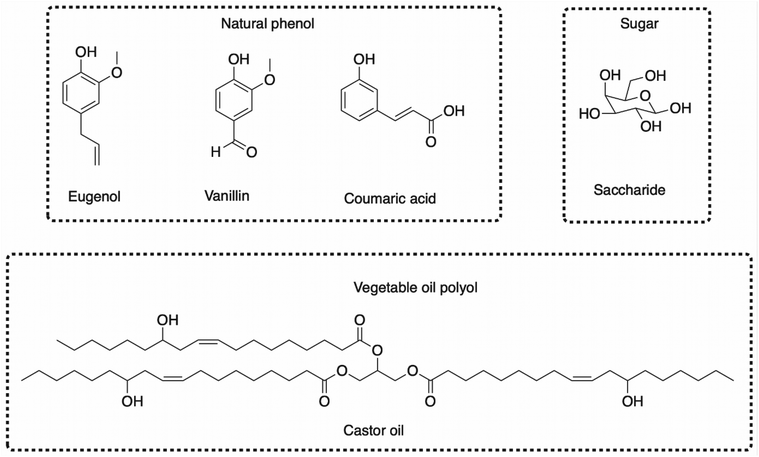 |
| Fig. 3 Structure of different bio-based polyols. | |
Considering all these reasons, CNSL compounds are very attractive as precursors of additives and surfactants or for the synthesis of novel bio-based polymers requiring the use of polyols such as polyurethanes and polyesters.
2. Chemical pathways from CNSL to polyols
a. Modification of the phenolic hydroxy moiety.
Compounds derived from CNSL can be used as “alcohols” or “diols” in the case of cardol, which contains two hydroxy functions. These molecules have been employed for the synthesis of esters60,70 and polyesters71 or as blocking agents in the case of cardanol, which react with isocyanate functions to free the isocyanate moieties later during the synthesis of polyurethanes.72 However, this phenolic hydroxy function has relatively low reactivity compared to the primary alcohol function. In addition, the resulting phenol esters are more sensitive to hydrolysis, which can be an advantage in the design of biodegradable products but also a disadvantage if the desired properties are durability and resistance in the resulting material.
Subsequently, this phenolic hydroxy can be used to introduce primary or secondary alcohol functions by various methods.
Etherification of cardanol.
Another way to provide an alcohol function is by reacting 3-chloropropane-1,2-diol73 (Scheme 2). Cardanol, 3-monochloropropanediol (3-MCPD) and sodium hydroxide were mixed in stoichiometric ratios, producing a viscous liquid in 87% yield. Nevertheless, this reaction used a toxic component, 3 MCPD, which is a chemical food contaminant and suspected to be carcinogenic to humans.
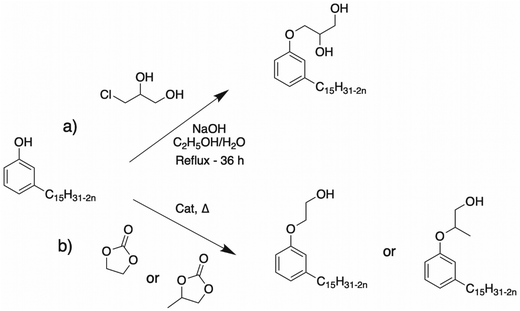 |
| Scheme 2 Synthetic pathway for the etherification of cardanol to form (a) diol73 and (b) alcohol.74 | |
Hydroxyalkylation by ring-opening of cyclocarbonate.
The first way to provide an alcohol function on a derivative of CNSL is to open a cyclocarbonate, particularly ethylene cyclocarbonate. Dia et al. of Cardolite Corp. filed a patent in 1998 on the hydroxyalkylation of cardanol with ethylene carbonate and propylene carbonate using various catalysts such as triethylamine, imidazole derivatives and alkali metal hydroxides and carbonates, as shown in Scheme 2. These reactions were conducted in the temperature range of 140 °C and 180 °C, achieving the minimum of 90% conversion up to 98%, with the products of only mono-ethoxylated derivatives.74 This method has the advantage of producing only the CO2 co-product previously captured and used for the synthesis of the cyclocarbonate itself.75,76 This methods has also been described using other natural phenols such as eugenol for the synthesis of ethoxylated compounds with the use of 1,5-diazabicyclo(4.3.0)non-5-ene (DBN) as the catalyst.77
Epoxidation of cardanol.
Surresh et al. reported a synthetic route using epichlorohydrin and hydrolysis,78,79 as shown in Scheme 3. Cardanol and ZnCl2 were mixed under alkaline conditions at 95 °C. A stoichiometric amount of sodium hydroxide was added and the product named Epicard was obtained in 85% yield. Then, the epoxy ring was opened under acidic conditions.
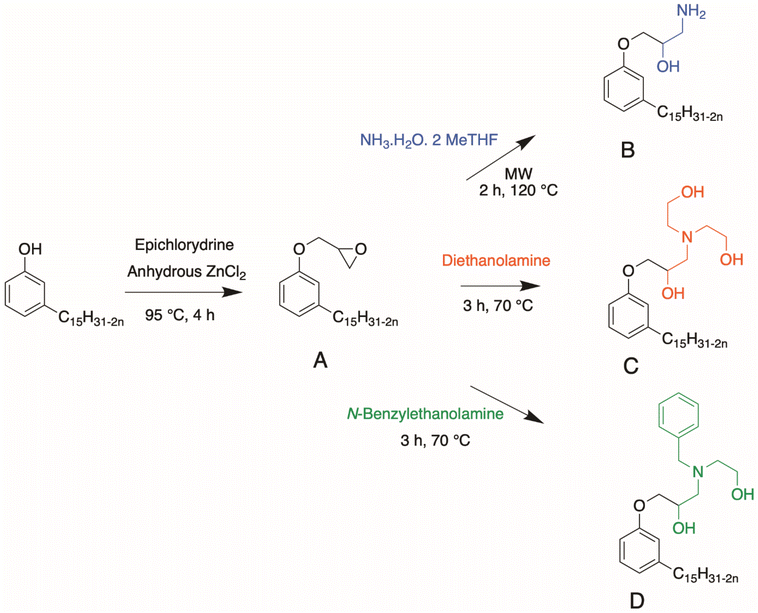 |
| Scheme 3 Synthesis pathways of epoxidation of cardanol and epoxy ring opening to obtain cardanol-based polyols.78–82 | |
In the literature, several syntheses have been described to open an epoxy ring, leading to the formation of at least one hydroxy function. Indeed, the following paragraph deals with epoxy ring opening by amination80–82 or with a thiol compound,83 and also under acid conditions with hydrolysis reaction.1
Amination of epoxy rings..
Mora et al. studied the ring opening of epoxy into hydroxy group leading to the formation of a highly reactive β-hydroxylamine80 (Scheme 3). Epoxidized cardanol and ammonium hydroxide in 2-MeTHF reacted under microwave irradiation for 2 h at 120 °C. A brown, highly viscous compound was obtained in 99% yield. This synthesis was interesting due to the use of the non-toxic amination route and the bio-based origin of the solvent. Huo et al. reported another way to open the epoxy ring into a hydroxy group using amine diols81,82 (Scheme 3). In this article, cardanol glycidyl ether and amine, diethanolamine (DEA) or N-benzylethanolamine (N-BEN) were mixed in equimolar ratios. The final product could be mixed with silicone and isocyanate to produce polyurethanes with high thermal stability.
Epoxy ring opening with a thiol compound..
Another way to open the epoxy ring into the hydroxy group of cardanol and generate cardanol-based polyol is using a thiol alcohol83 (Scheme 4). Cardanol glycidyl ether was mixed with a thiol compound, 2-mercaptoethanol, and 2,2-dimethoxy-2-phenylacetophenone under UV irradiation for 24 h. Then, a catalytic quantity of lithium hydroxide and ethanol were added to the mixture, which was stirred for 4 h at room temperature. The amount of hydroxy in the products was 357 mg KOH g−1. Then, the cardanol-based polyols were mixed with the 1,6-diisocyanatehexane (HDI) trimer to yield polyurethane with good mechanical properties.
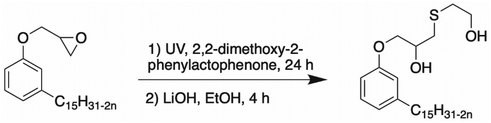 |
| Scheme 4 Epoxy ring opening of a cardanol derivative by a thiol by Wang et al.83 | |
Hydrolysis reaction.
The epoxy ring can also be opened under acid conditions, as described by Somisetti et al.1 using sulfuric acid or phosphoric acid. During this reaction, epoxidized cardanol in isopropyl alcohol was agitated in the presence of a solution of 10% sulfuric acid or 10% phosphoric acid (Scheme 5).
 |
| Scheme 5 Hydrolysis reaction to open epoxy ring by Somisetti et al.1 | |
Thereby, several methods have been described to modify the phenolic hydroxy moiety of CNSL compounds, especially cardanol, leading to the formation of reactive hydroxylated compounds, as presented in Scheme 6. Otherwise, in the literature, numerous studies have also highlighted the functionalization of unsaturated alkyl chains to obtain reactive hydroxy functions.
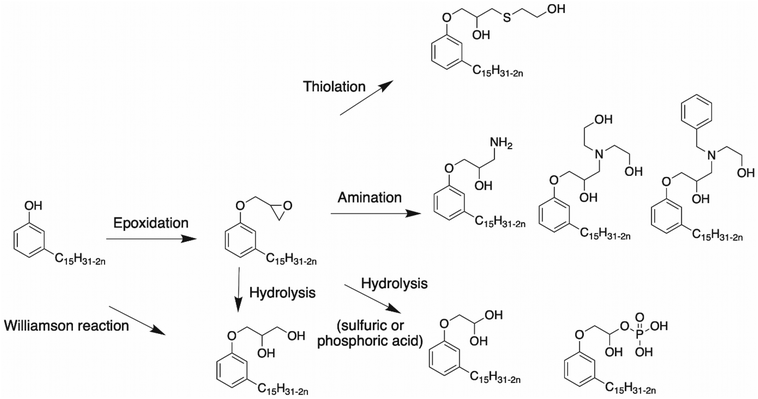 |
| Scheme 6 Synthetic scheme for the formation of reactive hydroxylated CNSL compounds by modifying the phenolic hydroxy moiety. | |
b. Modification of the unsaturated alkyl chain double bonds.
However, the unsaturation of the fatty alkyl chains can also be functionalized to provide higher functionality in hydroxy functions. The most common way to transform double bonds into hydroxy functions involves epoxidation in the presence of peroxide compounds (Scheme 7), followed by opening of the epoxy ring. The use of peroxy acids such as meta-chloroperbenzoic acid (mCPBA), which has versatile oxidizing power and relative ease of handling, constitutes one of the most useful synthetic procedures for the epoxidation of alkenes on a laboratory scale.84 Another peroxide, hydrogen peroxy (H2O2), has also been widely used for the epoxidation of double bonds. Depending on the environment and the position of the double bonds in the alkyl chain, H2O2 is relatively more effective than m-CPBA.85 Indeed, Jaillet et al. demonstrated that terminal double bonds are not epoxidized by mCPBA in contrast to H2O2, which yields a conversion of 25%. These authors also highlighted that the complete epoxidation of the internal and terminal double bonds of cardanol is not possible. Nevertheless, the presence of peroxide in the concentrated product can cause an explosion, explaining why purification of the resulting product to remove all traces of peroxide is required. Thus, this method is not industrially viable. Thiol–ene coupling and oxidative cleavage are also common pathways to form polyol from double bonds.
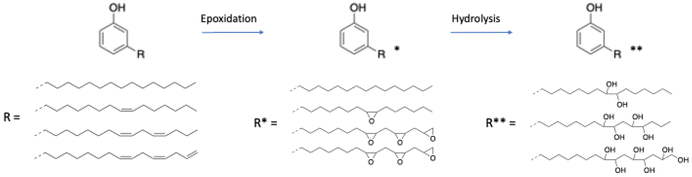 |
| Scheme 7 Epoxidation of cardanol alkyd chain double bonds, followed by hydrolysis. | |
Ring opening of epoxy.
The ring opening of the epoxy function leads to the formation of hydroxy groups. Many articles highlighted the different pathways to open an epoxy ring.
Polyols by hydrolysis of epoxy rings.
The first way to open an epoxy group is hydrolysis, which can occur under acid or basic conditions (saponification) (Scheme 7). Suresh et al. reported the saponification of epoxidized cardanol with a solution of 10% sodium acetate at 80 °C for 4 h even if the quantity of sodium acetate solution was not mentioned.86 The yield was not specified but a hydroxy value of 397 mg KOH g−1 was calculated. This polyol was introduced in the formulation of rigid polyurethane foams with 4,4′-diisocyanate crosslinker and a blowing agent. The resulting foams displayed good compressive strength, and uniform cell structure in the case of foams prepared using modified cardanol.
Somisetti et al. studied epoxy ring opening by hydrolysis under acid conditions.1 Epoxidized cardanol was reacted with 10% sulfuric acid (H2SO4) or 10% phosphoric acid (H3PO4) in isopropyl alcohol at 60–70 °C. Then, the hydroxylated and phosphated cardanol-based polyols (CDOH and CDPOH), as presented in Scheme 8, with a hydroxy value of 420 and 330 mg KOH g−1, respectively, were introduced in the formulation of PU films. The thermo-mechanical analysis showed similar results for both PU films. The presence of the phosphate group in CDPOH-PU increased the adhesion to the metal substrate, and thereby enhanced its surface protection compared to its counterpart polyurethane, CDOH-PU. Moreover, all the films exhibited excellent anti-corrosion and anti-microbial properties.
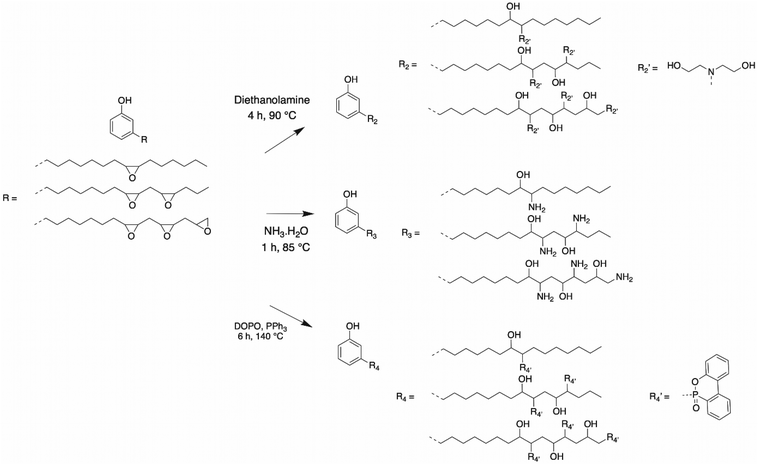 |
| Scheme 8 Amination of the epoxy ring by Huo81 and Mora et al.80 and phosphorylation by Bo et al.87 | |
Polyols by amination of epoxy rings.
Another way to open the epoxy ring on the alkyl chains of CNSL molecules is by reacting amine-bearing pendant hydroxyls. Some articles described the formation of β-hydroxylamines. Huo et al. reported the synthesis of a novel cardanol-based polyol.81 Epoxidized cardanol (PCGE) and diethanolamine (DEA) (molar ratio 1
:
1.2) produced a final product with an epoxy value less than 0.01 mol per 100 g (Scheme 9). This polyol, with a hydroxy value of 553 mg KOH g−1, was employed for the formulation of PU foams with MDI and a blowing agent. The mechanical and thermal properties exhibited better results with cardanol-based PU foam than the reference poly(ethylene glycol) PU foam. This was due to the combination of the hard aromatic structure and long flexible alkyl chain of cardanol. Moreover, due to the numerous reactive sites present on the alkyl chain of cardanol, the viscosity of the cardanol-based PU increased faster and the crosslinking density was higher, leading to a smaller average cell size.
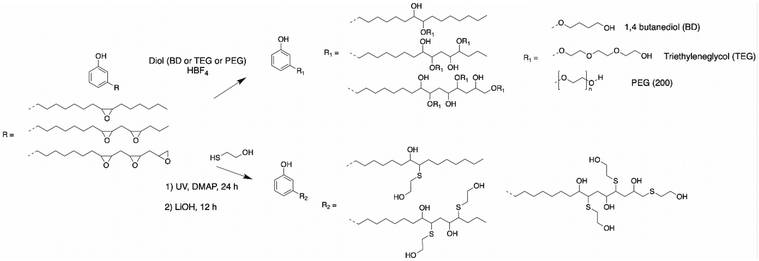 |
| Scheme 9 Formation of polyol cardanol through etherification of epoxy ring by Kim et al.88 and addition of functionalized thiol on the epoxy ring by Wang et al.83 | |
Mora et al. also studied the impact of amine for epoxy ring opening on the alkyl chain of cardanol.80 The epoxidized cardanol reacted under microwave irradiation with excess ammonium hydroxide (Scheme 8), producing a white solid in 99% yield; unfortunately, without any hydroxy value. Nevertheless, this synthesis is very interesting due to its full bio-based origin and the use of a non-toxic amination route. Then, the cardanol-based hydroxy amine was mixed with epoxy prepolymers to obtain epoxy thermosets with good mechanical properties and high thermal stability.
Polyols by phosphorylation of epoxy rings.
Bo et al. reported the synthesis of a phosphorus cardanol-based polyol87 from epoxidized cardanol and a phosphorus compound, 9,10-dihydro-9-oxa-10-phosphaphenanthrene-10-oxide (DOPO), catalyzed by triphenylphosphine (Scheme 8). This phosphorus cardanol-based polyol, with a hydroxy value of 287 mg KOH g−1, demonstrated excellent thermal and flame-retardant properties. Indeed, this compound may release PO° free radicals and o-phenylphenoxyl free radical, acting as scavengers of H° and OH° flame radicals. Moreover, the phosphaphenanthrene group may generate a char residue, acting as a barrier for the polymer matrix. This method has the advantage of synthetizing a bio-based polyol with flame retardant properties, in both the condensed and gas phase for optimum efficiency.
(Polymeric) polyols by etherification of epoxy rings.
The epoxy ring on the alkyl chains of CNSL molecules can also be opened by reacting diol compounds with an acid catalyst, leading to the formation of ether groups and reactive internal hydroxy functions. This etherification reaction was described by Kim et al.88 Epoxidized cardanol and diol reagents such as 1,4-butanediol (BD) and triethylene glycol (TEG) or poly(ethylene glycol) (PEG Mw: 200 g mol−1), were added at a molar ratio of 1
:
5. The reaction was carried out under acid catalyst conditions with 1 wt% of fluoroboric acid at 80 °C for 2 h (Scheme 9). Three bio-polyols bearing both secondary and primary alcohol moieties were successfully synthesized, but the yield of the reactions was not mentioned by the authors, while the hydroxy values were 369, 341, 328 mg KOH g−1 for BD, TEG and PEG cardanol-based polyol, respectively. Then, the cardanol-based polyols were employed as bio-based polyols for the preparation of polyurethane films with excellent mechanical and thermal properties due to the unique structure of cardanol. Thereby, cardanol-based polyols are excellent candidates to replace petroleum-based polyols.
Polyols by addition of thiol on epoxy rings.
Wang et al. reported another way to open the epoxy ring in alkyl chain of cardanol to produce cardanol-based polyol.83 Epoxidized cardanol and a thiol compound, 2-mercaptoethanol, reacted for 24 h under UV irradiation using 2-dimethoxy-2-phenylacetophenone (DMPA) as photoinitiator with a catalytic amount of lithium hydroxide. The conversion reached more than 90% with a hydroxy value of 440 mg KOH g−1 (Scheme 9). The cardanol-based polyols were used as precursors of thermosetting polyurethane films with 1,6-diisocyanatohexane (HDI) trimer, resulting in excellent mechanical properties.
Hydroxy-functionalized thiols can open the epoxy ring, leading to the formation of a tertiary and a primary alcohol. However, thiol–ene coupling between unsaturation and hydroxy functionalized thiols is the key step to synthesize primary hydroxy groups on fatty acid chains to synthesize cardanol-based polyols.
Thiol–ene coupling.
Thiol–ene coupling is a green, practical, and atom-efficient reaction. Several articles focused on thiol–ene coupling using CNSL compounds.
Direct addition of alcohol moieties by thiol–ene reaction.
Fu et al. reported the synthesis of a cardanol-based polyol with 2-mercaptoethanol and 2-hydroxy-2-methylpropiophenone, a UV radical initiator.89 The reaction was carried out under UV irradiation (365 nm) for 15, 22 and 50 h (Scheme 10). The results demonstrated that the longer the reaction time, the greater the conversion, leading to an increase in hydroxy functionality. The hydroxy values were 313, 336 and 386 mg KOH g−1, respectively. Brown liquid cardanol-based polyols were achieved with a yield between 78% and 81%. Thermosetting polyurethane films were shaped with HDI and these polyols endowed them with good thermal and hydrophobic properties, which suggested that they can be useful as hydrophobic materials.
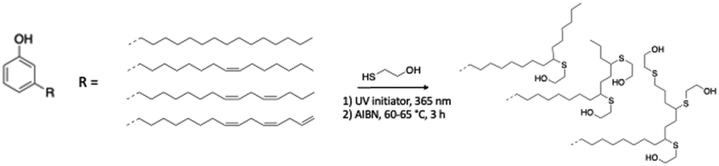 |
| Scheme 10 Thiol–ene coupling on unsaturation of cardanol alkyl chains using a (1) photochemical initiator by Fu et al.89 or (2) thermal initiator by Shrestha et al.90 | |
Thiol–ene coupling can also occur with a thermal radical initiator such as azobisisobutyronitrile (AIBN). Shrestha et al. slowly introduced excess 2-mercaptoethanol in cardanol at 60–65 °C for 3 h (ref. 90) (Scheme 10). A transparent, light brown-red color cardanol-based polyol was synthesized with a hydroxy number of 310 mg KOH g−1 and used with MDI to form rigid PU foams with very good physical-mechanical properties. Thus, they can find versatile applications such as thermal insulation in freezers, buildings, storage tanks and pipes.
These renewable polyfunctional compounds can be very interesting for the synthesis of bio-based polymers, which make them suitable alternatives to petroleum-based materials.
Intramolecular thiol–ene reaction via H2S.
The intramolecular thiol–ene reaction is another way to convert the unsaturation of the alkyl chain of CNSL compounds into thiol groups. The resulting thiols grafted onto the alkyl chain can react with polyols, exhibiting an alkene function to perform a thiol–ene reaction. Shrestha et al. described a photochemical thiol–ene reaction with cardanol and an excess amount of hydrogen sulfite (H2S) in the presence of UV light.91 Due to its high mobility, intramolecular addition of the terminal thiol group to the neighboring double bonds was possible, forming cyclic thioethers containing 5- and 6-membered rings (Scheme 11).
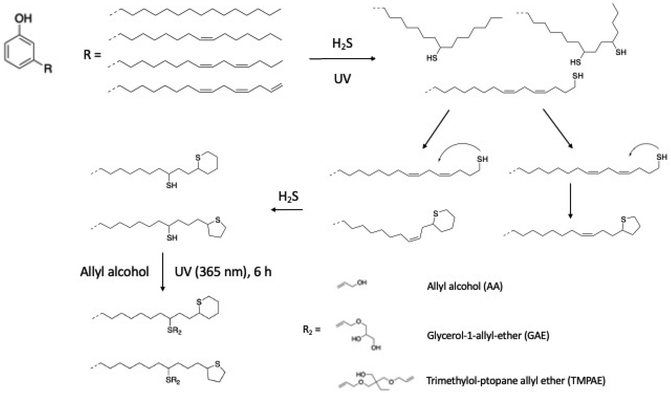 |
| Scheme 11 Intramolecular thiol–ene reaction by Shrestha et al.91 | |
Different allylic alcohols such as allyl alcohol (AA), glycerol-1-allyl-ether (GAE), and trimethylol-propane allyl ether (TMPAE) can undergo a second photochemical thiol–ene reaction in the presence of a photoinitiator (2-hydroxy-2-methylpropiophenone) at room temperature for 6 h under UV light (365 nm) (Scheme 11). The corresponding polyols were produced with a hydroxy number of 300, 389 and 413 mg KOH g−1, respectively. The authors successfully synthesized bio-based polyols for rigid polyurethane foams with excellent physical and mechanical properties. Nevertheless, this synthesis required several steps unlike the thiol–ene couplings previously described.
Oxidative cleavage.
An alternative way to obtain cardanol-based polyols involves oxidative cleavage through ozonation and reduction of the alkyl chain. Tyman et al.92,93 reported the synthesis of cardanol-based polyols through oxidative cleavage and reduction of an aldehyde in a two-steps synthesis (Scheme 12a). Firstly, cardanol was saturated with ozone at −78 °C to complete the ozonation and zinc/acetic acid were added, leading to aldehyde. In the second step, sodium borohydride (NaBH4) reduced the cardanol aldehyde with 74% yield. The reaction was successful even if the experimental conditions do not allow industrial viability. Moreover, the oxidative cleavage provides only one hydroxy group per alkyl chain, whereas the functionality was higher with the previously reported methods. Subsequently, the ozonolysis of cardanol led to a patent filed by Varma and Sivaram from General Electric Company.94
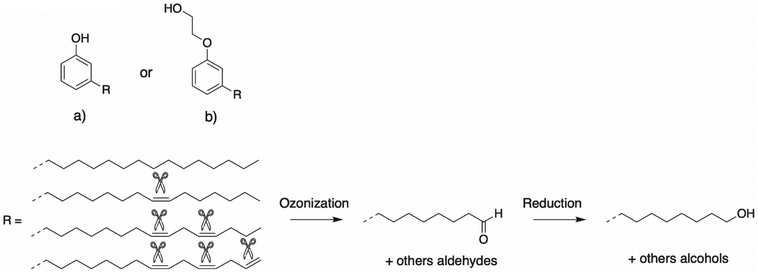 |
| Scheme 12 Oxidative cleavage of the unsaturated alkyl chain of cardanol by Tyman et al. and Dinon et al.92,93,95 | |
Oxidative cleavage can also be conducted on cardanol previously modified by ethoxylation. Indeed, Dinon et al. of Cardolite Corp.95 filed a patent in 2019 about the oxidative cleavage of ethoxylated cardanol with potassium peroxymonosulfate, ozonized air and Sudan Red III as a color indicator at 0 °C (Scheme 12b). The reduction reaction occurred with a reducing agent such as triphenylphosphine; sodium, potassium, or calcium iodide in the presence of acetic acid; dimethyl sulphite; trimethylphosphate; thiourea or zinc/acetic acid mixture. Thus, oxidative cleavage is an interesting industrial way to easily synthesize cardanol-based polyol.
Numerous bio-based polyols have been reported in the literature and are described in this review. Moreover, the functionalization of the unsaturation of the alkyl chain of CNSL compounds leads to the formation of bio-based polyols with a relatively high hydroxy number, which increases the crosslink density of cardanol-based polymers, and therefore enhances their mechanical properties including elastic modulus, tensile strength, and hardness. Moreover, it is possible to functionalize both the hydroxy group of the phenol and the unsaturation of the alkyl chain of CNSL compounds to generate monomers with even more functionality.
c. Formation of bisphenols based on cardanol.
In the literature, several authors have reported the modification of the alkyl chain unsaturation of cardanol with a phenol to give cardanol bisphenol. Ramasri et al.96 reported the synthesis of a cardanol bearing a mono-unsaturated alkyl chain using excess phenol and catalyzed by HClO4 (Scheme 13). More recently, Jing et al.97 described the synthesis of a triphenol using the same strategy with two unsaturations on the alkyl chain, catalyzed by sulfuric acid. This type of strategy can also be used to add phenol functions to the unsaturation of vegetable oils.98
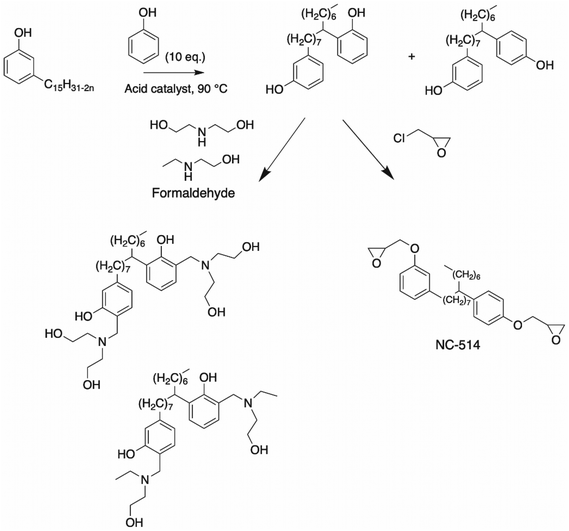 |
| Scheme 13 Synthesis of bisphenol cardanol through alkyl chain unsaturation by Ramasri et al.,96 and the formation of a polyol by Ramasri et al.99 and NC-514 molecule. | |
Ramasri et al.99 described the synthesis of a Mannich base cardanol bisphenol. The cardanol bisphenol was dissolved in ethanol in the presence of an amine such as 2-ethylamino-ethanol solution and diethanolamine, followed by the addition of formaldehyde solution (Scheme 13). Subsequently, these Mannich base cardanol bisphenols were neutralized with acetic acid before being added in paint formulations and used for electrodeposition. As expected, the Mannich base from diethanolamine, which exhibited the highest functionality, showed higher values for adhesion and scratch hardness related to the Mannich base from 2-ethylaminoethanol. Moreover, Cardolite Corp. synthesized a cardanol bisphenol in two steps and commercialized it under the name NC-514 (Scheme 13). The first step was the phenylation of aliphatic chain, followed by the reaction of the phenol hydroxy groups with epichlorohydrin.
Based on this commercial epoxidized cardanol bisphenol, numerous articles described the synthesis of other polyols. Kathalewar et al. reported the synthesis of cardanol-based polyols with variable functionalities by reacting NC-514 with several secondary amines (diethanolamine, diethylamine, and 2-methylaminoethanol)100 (Scheme 14). Although the yield of the reaction was not mentioned by the authors, the hydroxy value of the polyols was estimated to be between 241 and 449 mg KOH g−1. Consequently, the authors synthesized a wide range of polyols with a variable number of hydroxy functionalities. These polyols reacted with polyisocyanates to produce polyurethane coatings with excellent chemical and thermal resistance and anticorrosive performance. As expected, the higher the functionality of polyol, the higher the crosslinking density, and therefore increased physical properties such as hardness, impact, and tensile performance.
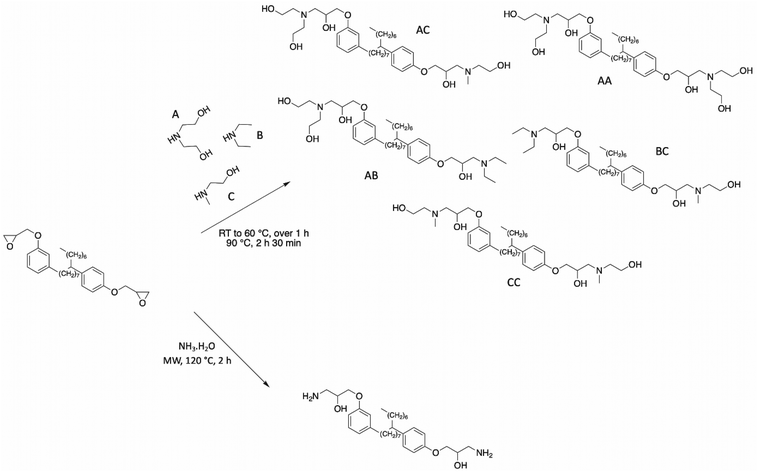 |
| Scheme 14 Synthesis of various polyols based on commercial NC-514 by Kathalewar et al.100 and Mora et al.80 | |
Mora et al. successfully aminated NC-514 using an ammonium hydroxide solution under microwave irradiation80 (Scheme 14). A brown and highly viscous compound was obtained in 99% yield. The functionalized NC-514 cardanol exhibited two different reactive functions including hydroxy and amine groups. These β-hydroxylamines could react with epoxy groups to form epoxy-amine thermosets with good thermomechanical properties and high thermal stability.
Balgude et al. reported the synthesis of polyols based on NC-514, which reacted with different bio-based acids such as tartaric acid, citric acid and adipic acid.101,102 Firstly, epoxy cardanol NC-514 was stirred with one of the above-mentioned acids in the presence of a phase transfer catalyst (tetrabutylammonium bromide). Triphenylphosphine (PPh3) catalyzed the opening of the epoxy ring, involving nucleophilic attack (Scheme 15). The yield of the reactions was not mentioned by the authors but the hydroxy values of the polyols were between 96 and 275 mg KOH g−1. The polyols were mixed with different commercial isocyanates, HDI and isophorone diisocyanate (IPDI) to give bi-component water-based polyurethane coatings. The high crosslinking density of the cured films with the polyols having the highest hydroxy functions showed a great impact on the chemical resistance, thermal stability, and anticorrosive performances of the polyurethane coatings.
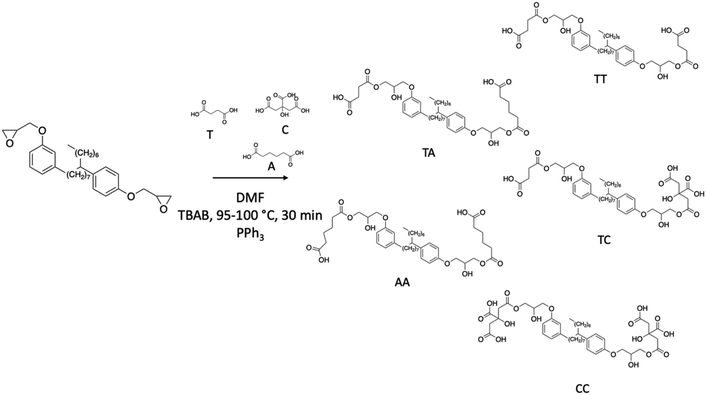 |
| Scheme 15 NC-514 modified with bio-based acid to form novel cardanol-based polyols.101,102 | |
Nevertheless, a study reported by Jaillet et al. in 2014103 highlighted a much higher molar mass of NC-514 than the theoretical molar mass, which indicated that the commercial cardanol NC-514 corresponded to a mix of polymers of epoxidized cardanol.
d. Modification of the aromatic ring.
The last functionalizable reactive site of CNSL compounds is their aromatic ring. Three main methods were reported in the literature including condensation, azo coupling and Mannich reaction, leading to the formation of different CNSL-based polyols.
Condensation.
The condensation of two bio-based phenols was reported by Bassett et al., leading to the formation of a cardanol-based diol.104 Vanillyl alcohol and cardanol were coupled according to an electrophilic aromatic condensation in 70% yield (Scheme 16). However, despite the high amount of renewable atom carbon in the vanillyl alcohol cardanol, the reaction time is very long. Moreover, the hydroxy value was not investigated because the aim of this article was the methacrylation of the alcohol groups before polymerizing the hydroxy function.
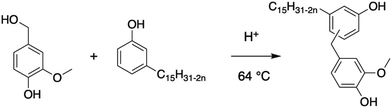 |
| Scheme 16 Condensation of vanillyl alcohol and cardanol to form cardanol-based polyol by Basset et al.104 | |
Azo coupling.
The azo coupling in CNSL compounds bearing hydroxy functions can be performed, leading to a colored conjugated system. Bhunia et al. reported the two-step synthesis of an azo cardanol-based polyol with an aromatic dye containing both hydroxy and amine functions.105–107 The red dye was formed in a yield of 80% (Scheme 17). Nevertheless, the hydroxy value was not mentioned by the authors. A polyurethane was synthesized by reacting the azo cardanol-based diol with a diisocyanate (MDI), leading to the formation of a material with high thermal stability and UV resistance due to the conjugated system. The same compound was synthesized by Nayak et al.108 and mixed with ester polyols and diisocyanates compounds to produce interpenetrating network (IPN) polyurethane with high thermal stability.
 |
| Scheme 17 Synthesis of azo cardanol-based polyol by Bhunia et al.105–107 | |
Mannich reaction.
The most reported reaction to synthesize polyols from an aromatic ring is the Mannich reaction, which involves condensation of an aldehyde, primary or secondary amine and carbonyl compound. Usually, the first step is the building of the cyclic ring, oxazolidine109–111 (Scheme 18). The synthesis of oxazolidine was carried out by reacting diethanolamine with paraformaldehyde.109,112,113
 |
| Scheme 18 Chemical pathway to oxazolidine. | |
Asif et al. synthesized a cardanol-based Mannich polyol with cardanol added dropwise to the oxazolidine intermediate112 (Scheme 19, structure 3). This renewable cardanol-based polyol with a hydroxy number of 187 mg KOH g−1 was further used in the formulation of PU nanocomposite coatings. These materials showed good physico-chemical properties and excellent anti-corrosion and chemical resistance. Their hydrophobic character was also investigated, and the results demonstrated an increase in the value with an increase in the amount of cardanol-based polyol introduced in the formulation.
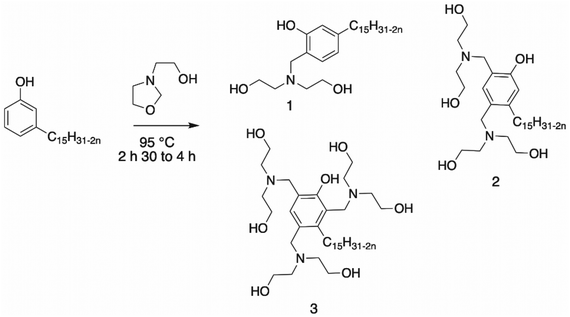 |
| Scheme 19 Synthesis of Mannich-based polyol by Ionescu et al.113 and Asif et al.112 | |
Ionescu et al.113 reported the synthesis of Mannich polyols from cardanol with oxazolidine. Depending on the molar ratio of cardanol/oxazolidine, three structures of Mannich polyol could be synthesized in practically quantitative yields (Scheme 19, structures 1, 2 and 3). The cardanol-based polyols exhibited a hydroxy number of 350 and 436 mg KOH g−1 for structures 1 and 2, whereas this value was not mentioned by the authors for structure 3. The Mannich polyols from cardanol have much lower viscosity and a higher renewable content than petroleum-based Mannich polyols. Moreover, they are very reactive, and thus especially suitable for the formation of spray rigid polyurethane foams, and also be used in molded rigid PU foams and as crosslinkers in many other PU applications such as coatings. Moreover, the obtained rigid PU foams exhibited good physico-mechanical and fire-retardant properties. Ionesco et al. and Asif et al. reported the same cardanol Mannich polyol (Structure 3), but with different hydroxyl values. The method used by these authors was not the same. Indeed, Ionesco et al. determined the hydroxyl value using the p-toluenesulfonyl isocyanate method (ASTM 1899–1997), whereas Asif et al. used the ASTM D 6342-12 method.
The Mannich reaction can also be performed without the formation of the cyclic oxazolidine in the first step. Zhang et al. described this solvent-free synthesis with cardanol and paraformaldehyde but also with melamine to introduce flame-retardant properties114 (Scheme 20). Nevertheless, the yield of the reaction and the hydroxy value of the polyol were not mentioned by the authors. Several rigid polyurethane foams were produced from this cardanol-based polyol with excellent mechanical properties, high thermal stability, and flame-retardant properties.
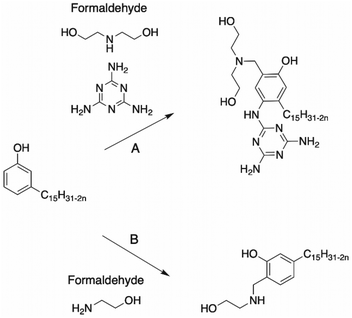 |
| Scheme 20 Synthesis of Mannich-based polyol by Zhang et al.114 (A) and Oh et al.115 (B). | |
Another cardanol-based Mannich reaction reported by Oh et al.115 was described in a Korean patent, where cardanol, formaldehyde and ethanolamine were combined to give a diol aromatic with a hydroxy value of 315 mg KOH g−1 (Scheme 20). However, important information such as the description of the synthesis and temperature and time of the reaction was not mentioned in the patent. Furthermore, the properties of the resulting PU were not described.
The Mannich base reaction can also be used for the synthesis of a dimer cardanol-based polyol. Indeed, this pathway can increase the hydroxy number and increase the crosslinking density, which can enhance the physico-mechanical properties of the polymers.
Dimerization of CNSL through aromatic rings.
Dimers of CNSL compounds can result from the dimerization of cardanol in presence of polyamines. Tyman et al. reported the synthesis of several dimer cardanol diols by Mannich reaction with diethylenetriamine116 (Scheme 21). Aqueous formaldehyde (35–40%) was added dropwise to a mixture of cardanol and dimethylamine. This triamine exhibited two primary amines and one secondary amine, providing a complex isomeric mixture (the ratio of each final cardanol dimer was not mentioned by the authors), as shown in Scheme 21.
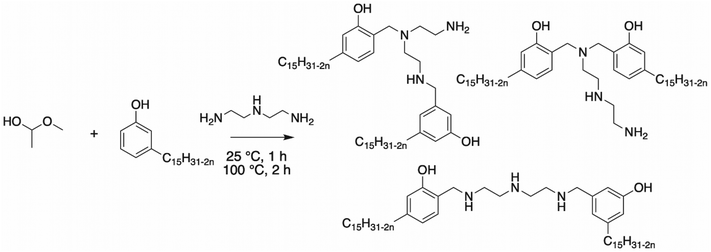 |
| Scheme 21 Dimerization of cardanol by Tyman et al.116 | |
Tan et al. synthesized another dimer by reacting cardanol with glycol and catalyzed by phosphoric acid (2 wt%)117 (Scheme 22). The yield of the reaction and the hydroxy value of the product were not discussed by the authors. A relevant aspect of this synthesis is the absence of formaldehyde, a toxic compound, similar to the Mannich reaction. This reaction can be interesting with other diols, if possible, bio-based, to obtain a fully bio-based cardanol dimer.
 |
| Scheme 22 Dimerization of cardanol by Tan et al.117 | |
A synthetic route towards thiobisphenol was studied by Tyman et al.118 using sulfur dichloride (Scheme 23). The yield of the reaction was not reported by the authors but the use of a catalyst such as iron powder enhanced the conversion of the reaction. The same authors own a patent, demonstrating the commercial interest of the dimer.119 Nevertheless, some solvents are more toxic than others (benzene) and their use tends to be banned.
 |
| Scheme 23 Synthesis of thiobisphenol by Tyman et al.118 | |
The separation and purification of a commercial Cardolite cardanol-based oligomer by column chromatography allowed Hassouma et al. to prepare a cardanol-based dimer120 (Scheme 24). However, this method is not efficient enough to be applied in industry with 20 wt% of the dimers related to the total mass of the Cardolite resin introduced.
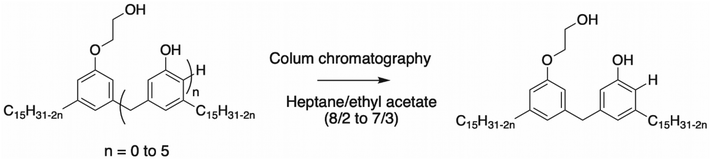 |
| Scheme 24 Separation of Cardolite resin for the preparation of cardanol-based dimer.120 | |
The chemistry of phenolic resins is appropriate for pure dimers, either by varying the number of equivalents or by performing a purification step on a column to isolate the dimers. For example, Briou et al. described the synthesis of a dimer via the condensation of cardanol with nonanal and acid catalysis under dilute conditions121 (Scheme 25a). The monitoring of the reaction by NMR spectroscopy also highlights the addition of the aldehyde on the least substituted ortho position of the aromatic ring. In the first step of the mechanism, a methyl moiety is obtained. Then, the condensation of the methylol group occurs on another ortho position of a free cardanol. Very recently, Yokoyama et al.122 described the synthesis of other cardanol dimers from aliphatic or aromatic aldehydes, and even acetone.
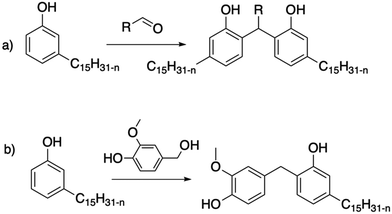 |
| Scheme 25 Synthesis of cardanol dimers from (a) controlled condensation with aldehydes121,122 and (b) condensation with vanillyl alcohol.123 | |
Similarly, a molecule containing a methylol group can be condensed in acidic condition, without the addition of aldehyde first. This is the case for vanillyl alcohol, another natural phenol, which can condense with guaiacol104 and cardanol123 (Scheme 25b).
e. Polyols from CNSL-based polymers.
One of the most reported pathways in the literature is cardanol-based phenolic resins. Usually, phenolic resins result from phenol and formaldehyde at high temperatures, producing two types of phenolic resins, i.e., novolacs, prepared under acid catalysis, and resoles, obtained under basic catalysis. Several articles described the synthesis of polyols from CNSL-based novolac resins with formaldehyde derivatives (Scheme 26). Mythili et al.124 mixed cardanol and formaldehyde using an acid catalyst (glutaric acid) at 120 °C for 3 h. After that, the reaction was heated to 150 °C for an additional 5 h, leading to the formation of cardanol formaldehyde resin with a hydroxy value of 157 KOH g−1. Then, this resin was mixed with diisocyanate (MDI) to form a rigid polyurethane, which improved its mechanical and thermal properties as well as chemical resistance.
 |
| Scheme 26 Polyols from cardanol-based novolac resins synthesized by (A) Mythili et al.,124 (B) Sathiyalekshmi et al.125,126 and (C) Mahajan et al.35 | |
Sathiyalekshmi et al. reported the synthesis of another cardanol formaldehyde resin by mixing cardanol and formaldehyde under acid conditions with adipic acid at 120 °C for 5 h, and then 150 °C for 20 min.125,126 The cardanol resin was epoxidized with epichlorohydrin and treated with 15% alcoholic sodium hydroxide. The epoxidized cardanol formaldehyde resin was further subjected to hydrolysis to convert the epoxy group into a hydroxyalkyl group with hydrochloric acid at 120 °C for 1–2 h (Scheme 26). The authors did not mention the hydroxy value of the final cardanol resin. However, the epoxy ring opening reaction led to an increase in this value compared to the above-mentioned cardanol formaldehyde resins. Finally, rigid polyurethanes were obtained with good aging performances, high thermal stability, and excellent mechanical properties. Mahajan et al. prepared cardanol formaldehyde microcapsules to introduce self-healing properties in polyurethane coatings.35 The microcapsules were synthesized through the in situ polymerization technique using an oil-in-water emulsion. Cardanol and ammonium chloride were added to an aqueous solution containing poly(vinyl alcohol) and sodium lauryl sulphate. The pH of the mixture was maintained between 7 and 8 using sodium hydroxide solution (5 wt%). Linseed oil was added dropwise to form a stable emulsion. Then, formaldehyde was added, and the temperature of the reaction was increased to 85 °C for 3 h. After that, the pH of the reaction was decreased to 3–5 with a hydrochloric acid solution and resorcinol was added as a crosslinker (Scheme 26). The PU coatings on mild steel surface showed enhanced self-healing and corrosion performances with an increase in the content of cardanol formaldehyde microcapsules. Thus, this is a sustainable approach for the protection of metal substrates.
For the preparation of greener CNSL-based novolac resins, formaldehyde, a petro-sourced aldehyde, can be substituted by another bio-based aldehyde. Indeed, Joy et al. reported the synthesis of a polyol with cardanol and furfural in an acid catalyst solution (phthalic acid).127 Then, the solution was heated to 120 °C but the reaction time was not mentioned by the authors (Scheme 27). The obtained polyol multinuclear cardanol furfural resin exhibited a hydroxy value of 174 KOH g−1. Due to the substitution of formaldehyde, a petro-sourced aldehyde, by furfural, a bio-based aldehyde, the amount of renewable atom carbons in the polyol increased. Nevertheless, furfural is a toxic compound, which is classified as carcinogenic, mutagenic, and toxic for reproduction (CMR).
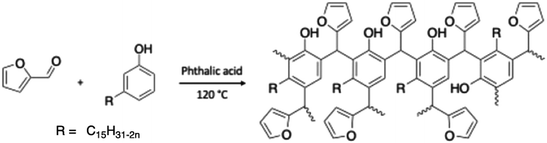 |
| Scheme 27 Polyol-based cardanol furfural resin by Joy et al.127 | |
In the case of polyol-based cardanol phenolic resins, other bio-based and non-toxic aldehyde compounds can be considered.128–130 Moreover, compared to the previously mentioned pathways, the formation of polyols from CNSL-based polymers leads to reactive compounds with a low hydroxy value. Moreover, a decrease in the solubility and an increase in viscosity are some disadvantages that can appear with the high molar masses of polyols derived from CNSL-based polymers.
f. Conclusion.
In this part, many pathways were described to synthetize polyol-based CNSL compounds, as summarized in Scheme 28. The reactive functions of CNSL compounds such as hydroxy group of the phenol, unsaturation of the alkyl chains and aromatic ring can be easily functionalized. Moreover, most of the articles reported the use of cardanol but the synthesis described can be applied to other CNSL compounds (cardol and anacardic acid).
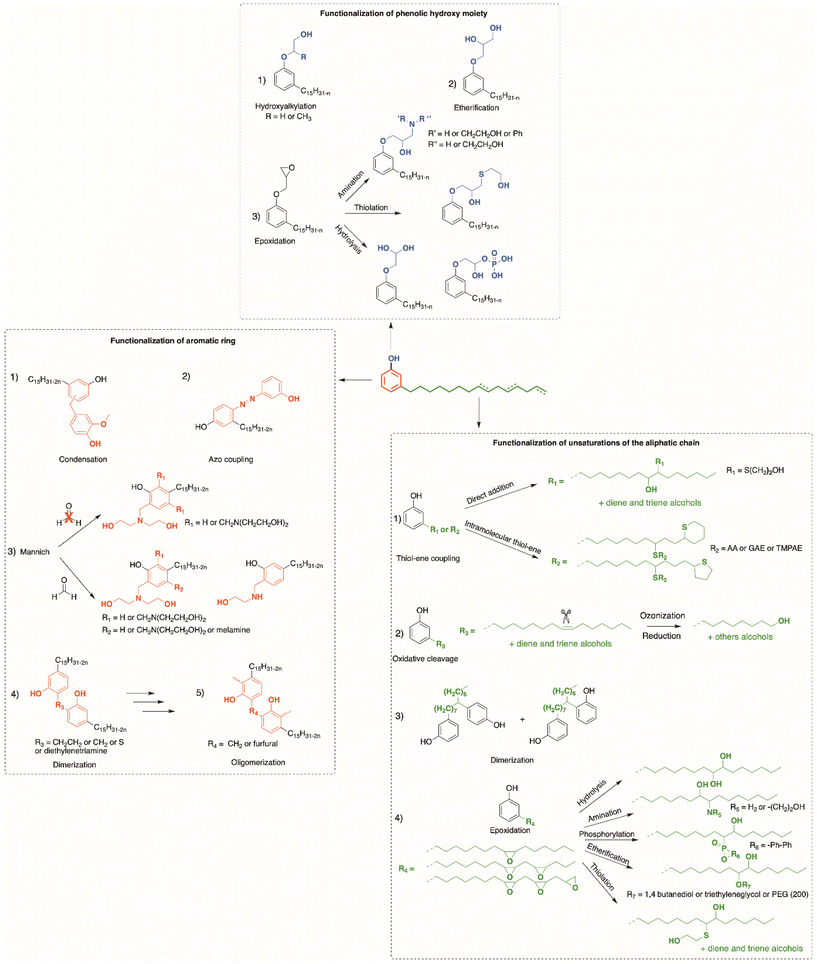 |
| Scheme 28 Several pathways to synthetize polyol-based CNSL compounds. | |
Depending on the structure of the desired final polymer and the intended application, the hydroxy value is very important. Indeed, the higher the hydroxy value, the greater the crosslinking density, leading to high physical–mechanical properties, which are generally suitable for some applications. In this part, numerous polyols with a wide range of hydroxyl values (from 96 to 553 mg KOH g−1), making them versatile for many applications, have been described. Most of the cardanol polyols were used for the preparation of numerous polyurethane materials ranging from rigid PU foams to PU coatings, together with flexible foams. Nevertheless, CNSL compounds can also be versatile polyols for the synthesis of other polymers such as polyesters, although this has scarcely been reported in the literature.
III. Use of CNSL-based polyols in a wide range of applications
In the previous part, we highlighted the diverse methods for the synthesis of polyols from CNSL derivatives, mainly cardanol. Depending on their chemical structure, polyols can be used in a wide variety of applications, ranging from foam to paint and coatings. Due to their special structure, CNSL derivatives are regularly used in the synthesis of polymer materials. The presence of a phenolic ring in their molecules confers enhanced thermal stability, and the long dangling alkyl chain influences the glass transition temperature of the resulting material, thus improving its flexibility. This dangling chain also introduce hydrophobic behavior in CNSL derivatives, enabling the use of these molecules in the synthesis of surfactants or coatings. All these characteristics of CNSL derivatives allow the direct application of polyols from these biobased synthons through the synthesis of polyurethane, polyester, and surfactant (Fig. 4).
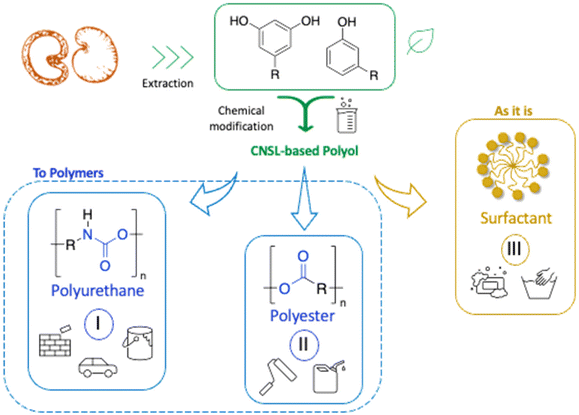 |
| Fig. 4 Figure summarizing the applications of CNSL-derived polyols in the chemical industry. | |
1. Applications and properties of polyurethanes from CNSL-based polyols
Polyurethanes (PUs) are widely used in many applications including foams, coatings, adhesives, and elastomers.131 Considering the PU consumption by product type in 2024,132 it can be seen that foams account for the majority of the market, followed by coatings, elastomers, adhesives and sealants. The global market in volume for PUs was 21 Mt in 2022,133i.e. around 5% of the global plastic production. PUs are unique due to their versatility and the presence of soft and hard segments, which can be modulated to suit the target application.
However, conventional PUs have two major drawbacks. Firstly, they involve the use of isocyanate, which is highly toxic to humans and moisture sensitive.134 PUs release this toxic volatile molecule under harsh conditions. Thus, polymeric isocyanates can be a solution to reduce their toxicity given that they have a high vapor pressure.135 Secondly, PUs are mainly derived from petroleum-based feedstocks.136
a. Synthesis of PU and utilization of bio-based aromatic compounds as polyols.
PUs are characterized by the presence of urethane bonds. They are synthesized from the reaction between an isocyanate and a polyol that contains two or more isocyanate groups and hydroxyl groups. PUs are multiblock copolymers that consist of alternating soft segments (SS) and hard segments (HS). The choice of appropriate monomers allows the SS/HS ratio to be modulated, giving polyurethane properties that can be varied. Polyols with a high molecular weight are mainly used to introduce SS due to the presence of a flexible chain that has a sub-ambient glass transition temperature (Tg), where molecules that introduce HS have a higher Tg.137 A wide variety of polyols are commercially available for this purpose. The most common are polyesters, polyether and acrylic polyols.135 An overview of the polyurethane synthesis features is presented in Scheme 29.
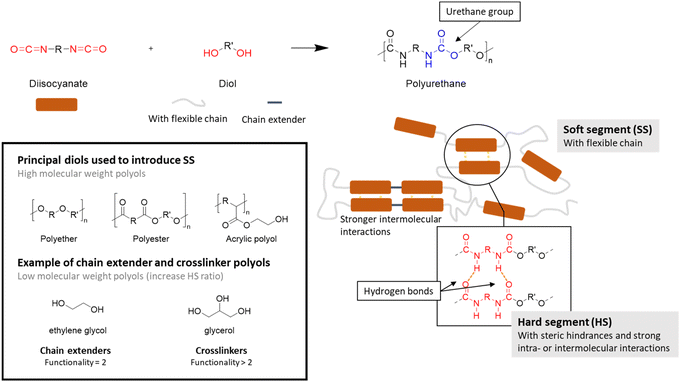 |
| Scheme 29 Overview of polyurethane synthesis features.5,6,137 | |
Isocyanates are mostly responsible for the HS given that they add rigidity to the material due to steric hindrance or strong intra- and intermolecular interactions, such as hydrogen bonds.137 The range of commercially available isocyanates is more limited than for polyols. Aromatic diisocyanates such as toluene diisocyanate (TDI) and methylene diphenyl diisocyanate (MDI) are widely used in the synthesis of PU due to their reactivity and their impact on the properties of the material.138
Low-molar-mass diols can also contribute to the HS and act as chain-extenders (functionality f = 2) or cross-linkers (f = 3 or more).137 In particular, the addition of a cross-linker with several hydroxyl groups increases the proximity between the urethane groups, thereby strengthening the interactions between the chains. Aliphatic low-molar-mass diols are usually chosen for the synthesis of PUs, such as ethylene glycol and 1,4-butanediol (BDO). However, it has been shown that cyclic or aromatic low-molar-mass diols can improve their packing and decrease their mobility. The resulting structures are mechanically strong, thermally stable and fire resistant compared with that obtained with aliphatic diols.135
From the context of sustainable development, efforts have been devoted to the use biobased monomers for the synthesis of PUs. Biobased isocyanates have been reported in the literature but their use on a larger scale is still limited because of the high cost of their synthesis given that they do not exist in nature.136 Therefore, industry has shifted towards the production of bio-based polyols. These molecules are often used as crosslinkers due to their multifunctional behavior. The majority of polyols on the market are aliphatic polyols derived from triglycerides, which are naturally abundant and economically competitive with petrochemical-based polyols. However, the synthesis of aromatic bio-based polyols is still limited on an industrial scale.139
The use of abundant resources such as lignin, tannins and CNSL derivatives opens up interesting perspectives for the synthesis of bio-based aromatic polyols. Lignin is one of the most abundant organic materials, with more than 50 million tons estimated to be produced annually.140 However, its use in the synthesis of PUs has two main drawbacks due to its complex structure including the difficulty in obtaining molecules with homogenous reproducible characteristics and their poor compatibility with other raw materials.141 Alternatively, the global production of cardanol has been estimated to be 800 kt per year in 2022.142 Although its unsaturation composition may differ depending on the geographical origin of the CNSL, it is a small molecule that can be easily modified to obtain a homogeneous raw material. The presence of an alkyl C15 chain has also been studied to improve its compatibility. However, cardanol is monofunctional and needs to be functionalized before its use as a polyol in the synthesis of PUs.40 In particular, cardanol can be easily modified to obtain hydrogenated cardanol. Sakulsaknimitr et al.143 synthesized PUs starting from a cardanol-based polyol and hydrogenated cardanol-based polyol. The presence or absence of double bonds does not appear to influence the thermal properties of the material. No studies have been carried out on the influence of double bonds in cardanol-based polyols on the mechanical properties of the resulting PUs. Depending on the chemical modification of cardanol, it has been reported that both elastomers144 and semi-crystalline107 polyurethanes can be obtained. By adjusting the hydroxyl equivalent weight (HEW) and the functionality of the polyols produced, it is also possible to modulate the rigidity and cross-linking density of the material. Mythili et al.145 found that PUs using cardanol-based phenolic polyols can lead to higher thermal stability and better mechanical strength. Different cardanol/formaldehyde ratios were used, where the greater the cardanol content in the resin, the better the properties of the PU. However, no characterization of the molecular weight of these polymers was carried out, and thus it is not possible to draw any real conclusions. They attributed this to the presence of high cross-linking in the material. As a biphenolic compound, cardol is potentially suitable as a starting material for the production of PUs. However, there are no articles on this subject, probably because of its low availability.
b. Cardanol-based polyols in polyurethane foams (PUFs).
PUFs are polyurethanes that consist of a solid phase and a gas phase. The formulation of this type of material is relatively complex, which is mainly composed of polyol, isocyanate, blowing agent and surfactant. PUFs can be rigid or flexible depending on the cell structure of the foam, which is highly determined by their formulation. The formation of the foam is possible due to the presence of a blowing agent, usually water, which produces CO2 by reacting with isocyanate. A surfactant plays an important role in the stabilization of the foam. Thus, polyols are mainly used to introduce SS in PUFs, where the isocyanates endow them with rigidity. Several characteristics of polyols influence the flexibility of the resulting material, where their main characteristics are reported in Table 1.
Table 1 Properties of polyols used as precursors of PUF146,147
PUF type |
Rigid |
Flexible |
Hydroxyl value (mg KOH g−1) |
200–800 |
15–100 |
Acid value (mg KOH g−1) |
0.05–0.1 |
0.05–0.1 |
Functionality |
2–8 |
2–3 |
Molecular weight (g mol−1) |
300–1000 |
3000–6500 |
Viscosity (Pa s) |
2–50 |
0.2–20 |
To obtain a foam with a homogeneous structure and good mechanical properties, polyols containing primary hydroxyl groups are generally used. In fact, there is a competition between the formation of the urethane bond with primary alcohol and CO2 given that they have similar reactivity (Scheme 30). With a secondary hydroxyl group, given that their reactivity is lower that of water, the formation of urethane bonds will be slowed down and more urea will be produced.
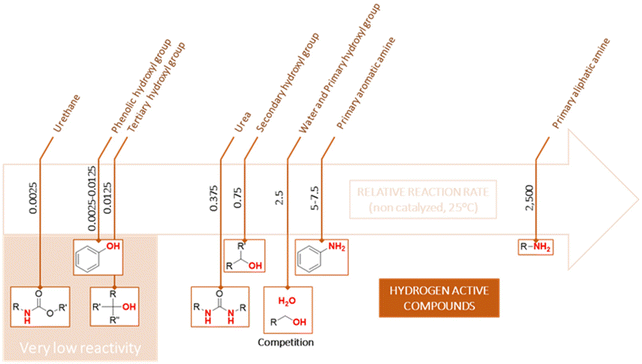 |
| Scheme 30 Relative reactivity of different alcohols, amines or other N–H containing groups against isocyanates.147 | |
Furthermore, the use of polyols with tertiary hydroxyl or phenolic groups is not envisaged due to their very low reactivity. For this purpose, the phenolic group of cardanol was modified by alkoxylation to produce primary or secondary alcohols.82,86,90,91,111,113,114 However, Suresh et al.86 prepared two polyols via the peracid oxidation of the double bonds in cardanol and one of them was epoxidized with epichlorohydrin at the phenolic group, and then hydrolyzed in alcohol. The results showed that characteristic reaction times were not very different. The mechanical properties appear to be altered with the modification of the phenolic group, where the density of the foam increased by 7 kg m−3 and its compressive strength by 15 kPa. This was explained by the greater reactivity linked to the modification of the phenolic group, but also the higher functionality of the polyol, which increased the crosslinking density. The polyol containing a phenolic group displayed two glass transition temperatures due to its heterogeneous hydroxyl nature.
A polyol with low acid value is required because the acid properties can reduce the activity of the tertiary amines, which are used as catalysts especially for the isocyanate–water reaction.147 Then, using cardanol modified by thiol–ene reactions can increase the rise time of the foam due to the unreacted thiol remaining in the monomer structure, as shown by Shrestha et al.91 This acid behavior can also affect the cellular structure of the foam because it disturbs the balance between the gelling reaction and gas formation, where the closed-cell content was 10% lower for the PUF using polyol with an acid value of 13.47 mg KOH g−1 and the cell size was higher. The glass transition temperature (Tg), unlike the mechanical properties, also seemed to be affected, with a decrease of almost 20 °C compared to the foam obtained with practically the same characteristics and an acid value of 0.79 mg KOH g−1. This property was not discussed in this article and no other publication seems to deal with this subject in the field of PUFs.
On the contrary, Mannich-modified cardanol111,113,114 is commonly used in foam formulations because it is extremely reactive in the foaming process due to the presence of a tertiary nitrogen, which helps catalyze the isocyanate–water reaction. Huo et al.82 reported the synthesis of other auto-catalytic polyols by introducing a tertiary amine through epoxide ring-opening with amines and hydrosilated unsaturated alkyl chain bonds using hexamethyltrisiloxane (HMTS), which exhibited similar properties. In addition, it appears that HMTS was introduced to increase the catalytic effect of the polyol and decrease its viscosity.148 However, no comparison between the polyol viscosity containing organosilicon or not and properties for PUF production was realized in their studies. Nevertheless, when the acid value of the polyols formed via a thiol–ene reaction was suitable, the characteristic duration of the PU foam and its mechanical properties were comparable to that obtained with tertiary nitrogen-containing polyols.
The presence of an aromatic ring in the cardanol structure was also considered to be of interest in PUFs given that it can provide a flame-retardant effect, particularly given that it allows the char layer to expand.146 Zhang et al.114 showed that without any flame retardant (FR), polyol from cardanol could have a 22.5% limiting oxygen index (LOI). This value can also be correlated with the potential melamine moiety and is higher than that of other non-flame retardant PUFs, which is around 19%. Thus, it can be very useful in the formulation of PUFs given that the addition of FR can alter its properties, such as thermal conductivity and cell structure.149
The cardanol-based polyols described in the literature82,86,90,91,111,114 for the synthesis of PUFs are mostly low molecular weight molecules, below 1000 g mol−1, leading to the formation of rigid PUFs. Polyether or polyester from cardanol has not been used in the synthesis of polyurethane. Shrestha et al.91 reported the synthesis of cardanol-based novolacs with 2 to 4 units of cardanol, and one of the polyols with a higher molecular weight was tested. They mentioned that polyols with more than 2 units are relatively viscous. Consequently, they limited their study to two polyols with 2 units for PU synthesis. However, the difference in viscosity with the monomer having 3 units was not significant. Modification of the phenolic group with propylene oxide increased the viscosity, with a difference of about 50 Pa s and approximatively the same HEW and acid value. The mechanical properties should be affected by an increase in viscosity because the density and the compression strength at 10% strain increased by about 20 kg m−3 and 100 kPa, respectively. In addition, this difference in viscosity can be explained by the cardanol/formaldehyde ratio in the preparation of the resin used as a polyol. In fact, a greater quantity of formaldehyde can cause alkylation of the aromatic ring of cardanol and increase its molecular weight. This data could have been interesting to explain this phenomenon.
In conclusion, cardanol-based Mannich polyols seem to be the most widely used for the synthesis of PUFs because they are highly reactive and weakly viscous. Comparable results such as thermal and mechanical properties were obtained with other cardanol-based monomers. As a result, no real trend regarding the preferred structure exists but the use of polyols containing a tertiary nitrogen may avoid the use of an external catalyst. If the polyol viscosity is low, adding cardanol units can increase its viscosity to improve the properties of PUFs. The monomer purity also seems to be an important factor, given that the presence of residual reagents such as thiols can interfere with the formation of a foam. However, the results reported in many publications are difficult to compare because of the formulation. Some important data, such as average cell diameter, closed-cell content, characteristic times, thermal conductivity, glass transition temperature, compressive strength and fire resistance of the foams were not recorded. In addition, the results were sometimes not sufficiently discussed to better understand the impact of the polyol parameters on the thermal and mechanical properties of the PUF. All the publications dealt with the formulation of rigid foams, in part due to the use of low molecular weight polyols. Therefore, it will be interesting to study the synthesis of flexible PUFs using, for example, a polyester or polyether synthesized from cardanol.
c. Cardanol-based polyols in coatings.
Polyurethane coatings are attracting significant interest due to their ability to offer improved abrasion resistance, greater hardness, enhanced chemical resistance and superior mechanical properties compared with polyester and polyesteramide coatings.150
Polyols are used as a base binder for the preparation of polyurethane coatings. Different polyols from natural and renewable resources have already been studied.1 Among the main CNSL compounds, only cardanol seems to have been considered as a biobased polyol from CNSL. A wide variety of polyol-based cardanol structures are used in the manufacturing of PU coatings due to their multiple reactive sites.1,83,87,100,101,151–153Scheme 31 summarizes the advantages and disadvantages of employing cardanol-based polyols in the synthesis of coatings based on the current literature.
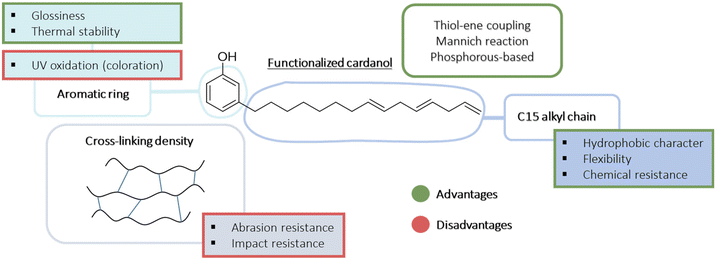 |
| Scheme 31 Summary of the coating properties enhanced by cardanol-based polyol according to the literature to date. | |
The first advantage of using CNSL compounds for coating applications is their long aliphatic chain. Indeed, the C15 chain gives the film hydrophobic character, enhancing its flexibility, chemical resistance and mechanical properties such as tensile strength and elongation, even with a high cross-link density.100 Actually, a high cross-link density can be interesting for films having a certain hardness, chemical and water resistance.152 This cross-link density can be modulated by increasing the number of hydroxyl functions in the polyol structure from modified cardanol. However, a too high cross-link density can lead to the loss of abrasion resistance because of the hardness of the surface. Also, the impact resistance can be reduced but this negative effect can be balanced by the presence of a long aliphatic chain. The aromatic ring in the cardanol structure also confers interesting properties to the film, such as glossiness and thermal stability.151 Moreover, depending on its final application, this can be a disadvantage, given that the color of the film can be altered by prolonged exposure to UV light.
The modification of the cardanol structure can result in different properties. Wazarkar and Sabnis151 demonstrated that polyol-based cardanol modified by thiol–ene coupling can have better mechanical, chemical, thermal and anticorrosive1 properties than different PU coatings based on commercial acrylic. Furthermore, the curing temperature of the film with the cardanol-based polyol seemed to be 10 °C higher than that with commercial acrylics. This may be caused by the low reactivity of the phenolic group. However, the curing can be carried out at lower temperatures, but the reaction time will be affected. Asif et al.112 cured their cardanol Mannich polyol-containing phenolic group film at room temperature for 48 h. Wang et al.83 investigated another cardanol-based polyol by thiol–ene/thiol–epoxy. It was shown that converting the phenolic hydroxyl into aliphatic hydroxyl improved the thermal stability of the resulting PU, and a difference of more than 40 °C was achieved.
Polyols containing phosphorous also appear to increase the mechanical performance of the film and its anticorrosive properties.1,153 This contribution to the structure of cardanol can also confer flame-retardant properties.87,153 It has been reported in the literature that hyperbranched PUs can easily catch fire.131 Therefore, it will be interesting to include flame-retardant tests to study PU coatings given that they are used in numerous applications as high-performance coatings such as automotive appliances and wood industry.150
Athawale and Shetty154 studied the influence of the NCO/OH ratio on the coating properties of a cardanol-based PU coating. The diol used reacted with TDI and IPDI. Independently of the isocyanate used, an NCO/OH ratio of more than 1.6 led to an inflexible, less glossy and slow drying coating. Otherwise, the use of different isocyanates impacted other parameters such as the hardness of the film and its chemical resistance. In fact, the choice of the isocyanate also plays a role in the final properties of the PU coating. If the mechanical properties and the hardness of the film are only slightly modified, its thermal stability can be significantly changed. Using cyclic isocyanate instead of aliphatic isocyanate can increase the degradation temperature of the film by up to 50 °C. There is also an increase in Tg but this is less relevant, increasing by the maximum of 6 °C.112 Consequently, it is difficult to deduce a trend in the thermal stability of coatings with regard to articles using cardanol-based polyols for the process given that no one isocyanate was preferentially chosen.
d. Conclusion.
Cardanol-based polyols have been studied in the synthesis of PUs as aromatic bio-based compounds. The presence of an aromatic ring endows the PU structure with mechanical strength and improves its thermal stability and fire-resistant properties. These cardanol-based monomers have been widely used to produce rigid PU foams. Various structures were obtained, although the current state of the art does not allow us to observe any trends in the use of a particular monomer. Generally, they contain more than two hydroxyl groups, which help increase the crosslinking density, and then improve the mechanical properties. The phenolic group is usually functionalized to improve the reactivity of the monomer. In addition, the complexity of the foam formulation and the lack of basic characterization of PU foams in some cases make it difficult to interpret the results. Standard characterizations should be at least the measurement of material density, cell size and density, tensile and compression tests and thermal analysis by TGA and DSC. Regarding the flammability of PU foams, fire resistance tests can be performed such as LOI measurement. In coating applications, cardanol-based PUs offer advantages such as chemical resistance, thermal stability and surface properties. However, the number of articles is not sufficient to give a trend on the type of monomers preferred and the lack of homogeneity of the characterizations makes their comparison difficult. Here, the presence of the aromatic ring can be problematic if yellowing due to oxidation needs to be avoided. One idea is the use cardanol-based monomers in which the aromatic ring is hydrogenated.
2. Applications and properties of polyesters from CNSL-based polyols
In the context of sustainability and the effort to prevent the accumulation of plastic waste, the synthesis of aliphatic polyesters appears to be a promising solution owing to their ability to easily degrade under external conditions. The most studied degradation pathways for this type of polymer are enzymatic hydrolysis155,156 and microbial degradation,157 known as composting. The biodegradation properties of polyesters result from the capacity of ester bonds to undergo hydrolytic cleavage.158 Furthermore, aliphatic polyesters represent only a small part of the global market compared with aromatic polyesters. In 2022, aliphatic polyesters with poly(lactic acid) (PLA)159 represented 0.35 Mt, whereas aromatic polyesters with poly(ethylene terephthalate) (PET)160 represented 25 Mt. In fact, aromatic polyesters are widely used because of their excellent thermal and mechanical properties. If they are usually resistant against microbial attack under mild conditions, many studies have been done to improve their biodegradable ability such as developing aliphatic-aromatic co-polyesters. Then, the use of renewable resources to produce aromatic polyesters that can compete with PET in terms of properties is challenging. Thus, the addition of cardanol-based compounds appears to be of interest in the development of this type of material. Moreover, Han et al.161 mentioned that improving the chain mobility can contribute to biodegradability. Therefore, adding a C15 alkyl chain can potentially aid this objective. In this part, the use of cardanol-based polyols in different polyester applications and their impact on the material properties are discussed.
a. Synthesis of polyester and utilization of polyols as bio-based aromatic compounds.
Polyesters are characterized by the presence of ester bonds, generally obtained by reacting a diol with a dicarboxylic acid. Polyesters are obtained via step-growth polymerization, and more specifically by polycondensation given that water molecules are produced during the esterification reaction. In step-growth polymerization, the monomers first react to form dimers, subsequently reacting to form tetramers, which is repeated until long-chain polymers are obtained, as shown in Scheme 32. High molecular weights are usually difficult to obtain with this type of polymerization, according to the Carothers equation. In fact, a high conversion rate is required to promote mass growth, implying perfect stoichiometry and the use of monomers with a high degree of purity.
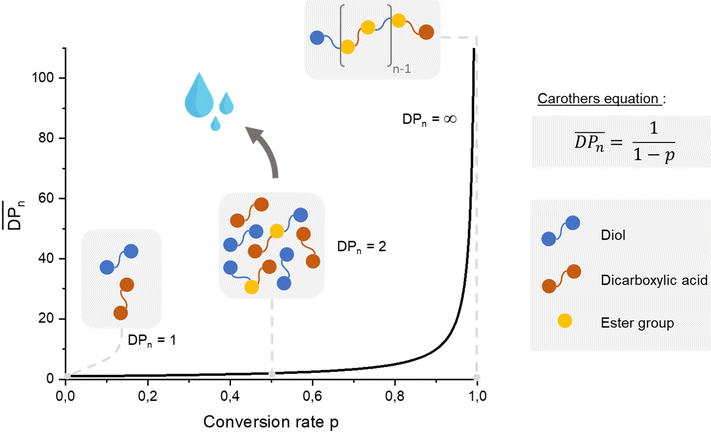 |
| Scheme 32 Explanation of step-growth polymerization with Carothers equation – case of linear polyesters using equimolar quantities. | |
Polyesters can be divided into aliphatic polyesters and aromatic polyesters. Aliphatic polyesters represent one of the most important classes of biodegradable polymers and have received attention from both industry and academia, in particular for biomedical applications.162 Biodegradability is attributed to the ability of ester bonds to be hydrolyzed. However, the thermal and mechanical properties of these polyesters are not always suitable for all applications, especially their low melting point. Thus, the incorporation of aromatic rings into the polymer helps to improve these properties. As shown before, PET is the most used aromatic polyester given that it is widely in the textile and packaging industries and is not considered a biodegradable polyester.163 On the one hand, a significant amount of research is being carried out on the physical and chemical recycling of PET.164 Liu et al.165 performed glycolysis of PET waste with a cardanol-based diol, which has interesting properties for the synthesis of UV-curable coating. On the other hand, efforts are being devoted to finding biobased alternatives to PET.162 In the latter case, dicarboxylic acid is tending to be replaced, but it is also possible to add rigidity to the structure using a biobased aromatic diol. Lignin derivatives such as vanillin are increasingly being studied as a source of bio-based aromatics. Similar to CNSL compounds such cardanol, it needs to be functionalized to obtain a diol. Moreover, the production of vanillin from lignin is still low compared with the production of petroleum-based vanillin, where cardanol can be easily obtained from natural feedstocks.166
Among the CNSL compounds, cardanol is the most widely used in polyester. Only one paper71 described the synthesis of polyester from cardol and none from anacardic acid. More specifically, polyesters were synthesized via polycondensation in solution using two distinct acyl chlorides, adipoyl chloride and terephthaloyl chloride, and cardol as the diol reactant. However, they did not succeed in obtaining a high molecular weight and the lack of data does not allow a conclusion. As mentioned above, the reactivity of the phenolic hydroxyl group is relatively low, which is why it is often functionalized. Therefore, it would have been interesting to carry out additional analyses, such as NMR and SEC analyses, to monitor the polymerization reaction progress. In this way, it would have been possible to compare the reactivity of the cardol phenolic hydroxyl groups towards polycondensation. Using resorcinol and adipoyl chloride to synthesize polyester, Goto and Abe167 succeeded in obtaining an Mn higher than 70
000 g mol−1. Given the structural similarities between resorcinol and cardol, this seems promising for the synthesis of polyesters using cardol as a diol. Moreover, Makame et al. found that their cardol-based polyesters were poorly soluble in chlorinated hydrocarbons, whereas Goto and Abe showed that their resorcinol-based polyesters were soluble in them. This result is surprising given that it has been reported in several articles168–171 that the presence of the C15 alkyl chain improves the solubility of aromatic polyesters in commonly used organic solvents. Indeed, Wadgaonkar et al. worked169–171 on the modification of bisphenol A (BPA) with cardanol derivatives, especially 3-pentadecyl, in particular the hydrogenated cardanols 3-pentadecylphenol and 3-pentacyclohexanone. They studied their impact on the solubility and thermal properties of the synthesized polyesters. The solubility tests and thermal analyses of the polyesters obtained from modified-BPA and terephthaloyl chloride are presented in Table 2. They showed that adding a cardanol segment to the molecule allowed the synthesized polyesters to be solubilized in common organic solvents such as chloroform and tetrahydrofuran. Furthermore, the addition of this segment resulted in a significant reduction in the glass transition temperature, Tg, due to the internal plasticizer effect of the long aliphatic chain of the cardanol derivatives. Also, lower thermal stability was observed with the introduction of the C15 chain, regarding the initial decomposition temperature Tonset. These trends were also confirmed when they produced copolyesters with BPA and cardanol derivative-modified BPA as diols. More specifically, they demonstrated that the solubility in common organic solvents can be significantly improved with only 15 mol% of cardanol derivative-modified BPA.
Table 2 Properties of the polyesters obtained from terephthaloyl chloride and modified-bisphenol A
Starting material for BPA-modification |
Diol monomer |
Resulting polyester |
Solubilitya |
M
n b (kg mol−1) |
T
onset c (°C) |
T
g d (°C) |
Ref. |
Solubility of the polyester at room temperature in various organic solvents at 3 wt% concentration.
Measured through GPC in chloroform, and polystyrene was used as the calibration standard.
Initial decomposition temperature measured through TGA.
Glass transition temperature measured via DSC.
|
BPA |
|
|
— |
— |
487 |
210–234 |
50, 52 and 169 |
Cyclohexanone |
|
|
— |
— |
475 |
— |
169
|
3-Methylcyclohexanone |
|
|
— |
— |
460 |
263 |
169
|
3-Pentadecylcyclohexanone (cardanol derivatives) |
|
|
Dichloromethane, chloroform, trichloroethylene, tetrahydrofuran |
58.4 |
438 |
94 |
169
|
3-Pentadecylphenol (cardanol derivatives) |
|
|
Dichloromethane, chloroform, tetrahydrofuran, pyridine, m-cresol |
48.5 |
370 |
82 |
170
|
3-Pentadecylphenol (cardanol derivatives) |
|
|
Dichloromethane, chloroform, tetrahydrofuran, m-cresol, pyridine |
48.3 |
— |
47 |
171
|
b. Cardanol-based polyol in alkyd resins.
Alkyd resins are a specific class of polyesters modified by unsaturated fatty acids, which are widely used as binders in paints or varnishes formulations.172 They are synthesized by polycondensation between polyols and polyacids.173,174 In these polymers, the polyacids used exhibit a functionality of 1 or 2, whereas polyols may have wide functionality ranging from 1 to 4. The greater the functionality of the monomers, the higher the increase in mass, and therefore the growth of the chains was rapid. CNSL compounds are compatible with alkyd resins due to their hydrophobic alkyl side chain but these compounds are still scarcely used in these polymers. A recent article reported the impact of mono- and difunctional hydroxyl cardanol monomer in the synthesis of novel alkyd resins175 (Scheme 33). Denis et al. demonstrated that the cardanol monomers increased the renewable carbon content (up to 12%) and thermal stability of alkyd resins. The hardness also increased with the amount of aromatic ring provided from cardanol. Nevertheless, the color of the alkyd resins became increasingly darker with an increase in the amount of cardanol used for the synthesis, which is a limitation for the formulations of paints except primers.
 |
| Scheme 33 Structures of alkyd resins with (a) monofunctional hydroxyl cardanol and (b) difunctional hydroxyl cardanol by Denis et al.175 | |
c. Cardanol-based polyester as plasticizer for PLA.
An example of the use of a cardanol-based polyester as a plasticizer for the formulation of PLA films was reported by Vallin et al. in 2023.176 Polyesters from dimethyl succinate (DMS) or dimethyl adipate (DMA) were synthesized using an enzyme catalytic polycondensation by the trans-esterification route or metal-catalyzed polycondensation. A comparison of these two methods showed that the use of a metal catalyst enables higher Mn to be achieved, but results in the pronounced coloring of the samples. However, the number average molar mass is still low for a polymer, around 4000 g mol−1. This may be due to the type of agitation chosen, given that magnetic agitation does not allow proper mixing when the viscosity increases, especially in bulk polycondensation, or because of the too low reaction temperature. Then, the dark color of the metal-catalyzed sample could be improved with an adapted purification process. In fact, they did not mention any purification processes such as precipitation. In terms of thermal properties, their cardanol-based polyesters had a Tg of around −40 °C and a decomposition temperature of around 380 °C with DMS, while that of the diacid was −60 °C and 400 °C using DMA, respectively. Different PLA films were formulated by solvent casting with 2–10% w/w of cardanol-based polyesters inside. The glass transition of the different samples decreased with an increase in the percentage of polyester used. However, this decrease was fairly insignificant, which was about 10 °C. Regarding the mechanical properties, it can be shown that the incorporation of polyester has a significant impact on the ability of the film to elongate before breaking (Scheme 34). The PLA film with 10% w/w DMA-based polyester plasticizer exhibited the best elongation at break. Otherwise, its incorporation decreased the Young's modulus and the tensile strength. These results are in agreement with the literature.177 In fact, the plasticizer provides a higher free volume between the polymer chains, and therefore enhances the chain mobility and film flexibility.
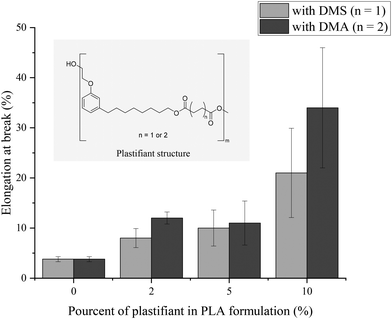 |
| Scheme 34 Influence of the percentage of plasticizer in the PLA film formulation on the elongation at break. | |
d. Conclusion.
There are very few articles on the synthesis of polyesters using CNSL-based polyols. This can be explained by the recent interest in CNSL derivatives, and also the difficulty encountered in performing polycondensation. Alternatively, the development of cardanol-based monomers for polyester synthesis has been widely studied, where they are used to drastically improve the solubility of bisphenol A-based polyesters as an example. These monomers can also be added in the formulation of alkyd resins to enhance their thermal stability and increase their renewable carbon content. An example showed the possibility of using a low molecular mass cardanol-base polyester as a plasticizer for PLA. Finally, there is still a lot of research to be done regarding the development of polyesters based on cardanol, and also cardol to obtain new aromatic biobased polyesters. The use of polyesters for the synthesis of polyurethanes can also be considered.
3. Applications and properties of miscellaneous polymers from CNSL-based polyols
CNSL-based polyols are mainly used for the polymerization of polyurethanes or polyesters, as previously described. However, some CNSL-based polyols were also reported in the literature for the development of other polymers such as polyethers and phenolic foams. More et al.178 synthesized a cardanol-based bisphenol (Fig. 5A) for the synthesis of poly(ether ether ketone) (PEEK) and poly(ether ether ketone ketone) (PEEKK) by polycondensation.
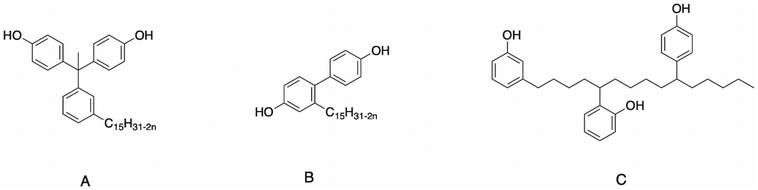 |
| Fig. 5 Structure of cardanol-based bisphenol used in (A) polycondensation of PEEK by More et al.,178 (B) polycondensation of poly(arylene ether) by Tawade et al.179 and (C) phenolic foam by Jing et al.97 | |
Tawade et al.179 introduced another cardanol-based bisphenol (Fig. 5B) in the polycondensation of PEEK.
It is well-known that conventional PEEK derived from bisphenol-A or 4,4′-biphenol is insoluble in common organic solvents. In this study, the authors demonstrated that PEEK containing pendant pentadecyl chains is soluble in common organics solvent such as chloroform, dichloromethane, tetrahydrofuran and pyridine at room temperature. The good solubility of these polymers in both studies can be attributed to their pendant pentadecyl chains, which led to an increase in their free volume, and then it was easy for the solvent to penetrate the polymer chains. Thus, PEEK and PEEKK can be considered as good candidates for applications such as gas separation and microelectronic devices, where the combination of solubility and good thermal properties is desirable. Furthermore, a decrease in the Tg of the polymers was observed, which may be attributed to the pentadecyl chain in the polymer backbone acting as an “internal plasticizer”. Moreover, a large difference between the Tg (35–78 °C) and the initial decomposition temperature (378–455 °C) was observed, thus offering PEEK and PEEKK a wide processing window.
Jing et al.97 modified cardanol with a phenol to obtain a bisphenol (Fig. 5C), which was used to synthetize phenolic foams with paraformaldehyde. The addition of cardanol increased the viscosity of the prepolymer, which was obvious when the dosage of cardanol was over 5 wt%. Moreover, phenolic foams with 5 wt% cardanol had a slight improvement in mechanical performance. Noticeably, the phenolic foams modified with 10 wt% cardanol showed an increase in flexural strength by 22% and 28% in bending modulus compared to the pure phenolic foams, indicating that the incorporation of cardanol improved the toughness of the phenolic foams.
4. Applications and properties of surfactants from CNSL-based polyols
Surfactants are amphiphilic molecules, which means they are composed of both lipophilic and hydrophilic parts.180–182 They are chemical compounds that decrease the surface tension or interfacial tension between two liquids, a liquid and a gas, or a liquid and a solid, allowing the solubilization of two immiscible phases. Moreover, depending on the nature of the hydrophilic part, surfactant compounds are classified into four groups including non-ionic (the molecule has no charge), anionic (hydrophilic part negatively charged), cationic (hydrophilic part positively charged), and zwitterionic (hydrophilic part has a positive charge and a negative charge, the overall charge is zero). Consequently, they have a wide range of applications such as detergent, solubilizing agent, foaming agent, wetting agent, dispersing agent (to avoid flocculation), emulsifying agent, and antibacterial agent.183,184 In the literature, numerous patents or articles have reported the synthesis of CNSL-based surfactants and a recent review lists them.24 They have found various uses in many fields such as detergency, polymerization emulsion, enhanced oil recovery and antimicrobial applications. In the following section, only CNSL-based surfactants with hydroxyl functions are reported. Scheme 35 presents the general structure of a cardanol-based surfactant with hydroxyl function. It should be mentioned that natural cardanol cannot be used as a surfactant, and its phenol has to be modified to obtain a polar head.
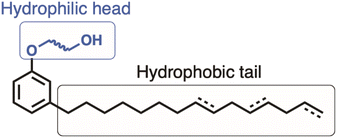 |
| Scheme 35 General structure of cardanol-based surfactant with hydroxyl function. | |
The structures of CNSL-based surfactants are presented in Scheme 36. The relationship between their structure and properties is discussed as well as their applications when mentioned by the authors. The critical micellar concentration (CMC) and surface tension at CMC (γCMC) are important parameters, which can be discussed to analyze the structure–property relationship. Moreover, the nature of the hydrophilic group and its length have an influence on the previously mentioned parameters.
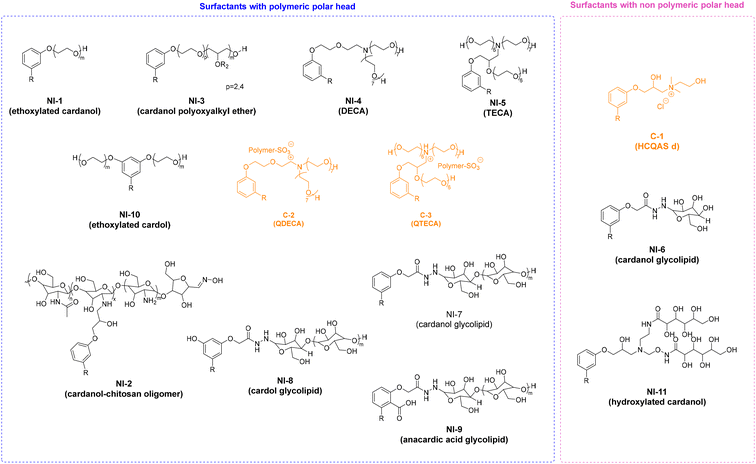 |
| Scheme 36 Structures of polyol CNSL-based cationic (C) and non-ionic (NI) surfactants in orange and black, respectively. | |
a. Wetting agent.
Non-ionic ethoxylated cardanol-based surfactants were also used in a cement formulation as wetting agents, leading to the formation of fine, stable air bubbles to reduce the internal pressure, and thus avoid cracks, and also improve its maneuverability.185 Tarafdar et al.186 developed a cement composition containing ethoxylated cardanol surfactant for use in an oil-contaminated well (NI-1 Scheme 36). A low concentration of surfactant was introduced in an oil in water emulsion (70/30). The compressive strength is an important parameter studied in cement applications and the authors demonstrated that the ethoxylated cardanol surfactants exhibited a higher compressive strength (>1140 psi after 24 h) than that of a commercial ethoxylated phenol surfactant (Stabilizer 434™, 1000 psi after 24 h).
b. Emulsifying agent.
Chapelle et al.187,188 showed that cardanol modified with chitosan oligomer (NI-2 Scheme 36) can be used as an emulsifying agent to stabilize direct oil-in-water emulsions (60/40). The authors demonstrated that the emulsion was stable for at least 24 h with droplets with an average size of 15 μm. Unfortunately, the CMC and surface tension were not discussed. Eventually, the authors demonstrated its promising potential as a new biobased emulsifier for bituminous emulsions.
c. Detergent agent.
CNSL surfactants can also be used in the formulation of detergency solutions.189 Different cardanol poly(oxyethylene ether) (NI-1 Scheme 36) nonionic surfactants have been studied in several patents.190–193 Wang et al.190 used them in detergent applications to reduce the surface tension of the solution with various ethylene oxide repeating units (from 1 to 50). The authors demonstrated that the length of the poly(oxyethylene ether) (POE) head of the nonionic surfactants had an influence on their cloud point, the temperature above which a sample becomes turbid, due to the phase-separation between the rich-phase surfactant and the solution. This phenomenon is due to the PEO chains, whose solubility in water decreases when the temperature is raised. The cloud point values of nonionic CNSL derivative NI-1 increased from 48 °C to 62 °C with an increase in the number of ethylene oxide units in its polar head (m between 7 and 30). Moreover, the CMC increased with an increase in the number of ethylene oxide units. Thereby, this study showed that cardanol PEO had a high cloud point, a low CMC and was easily soluble in water, making it ideal for use in detergents. Nevertheless, CNSL-based PEO usually has a darker color and a pronounced smell. Therefore, it is particularly important to develop a cardanol PEO foaming agent with light color and low odor as well as strong foaming capacity. This was claimed by Wang et al.191 in a recent patent on three different cardanol POE with the ethylene oxide number of 19, 15 and 14. Once introduced in the formula of laundry detergent, they provided good foaming property. The results demonstrated that the higher the ethylene oxide number, the stronger the irritation. Nevertheless, all the non-ionic cardanol-based surfactants claimed in this patent exhibited lower irritation compared to commercial anionic surfactants such as sodium lauryl tetradecanol PEO sulfate. Jin et al.192,193 prepared oil-in-water emulsions containing non-ionic cardanol poly(oxyalkyl ether) (NI-3 Scheme 36). They recorded the time required to observe a definite separated volume of water, where the longer the time, the stronger the emulsification capability. The cardanol derivatives could stabilize O/W emulsions in the same range of time as commercial alkylphenol polyethoxylated surfactants (such as Tergitol™ NP-10). A washing test on soiled cotton fabric proved that NI-3 had similar performances to the petroleum-based Tergitol™ NP-10.
Zhao et al.194 reported the synthesis of novel hydroxylated cardanol quaternary ammonium salts (HCQAS) (Scheme 37) for use in detergent applications. Different cardanol quaternary ammonium salts were studied in a direct emulsion. The best emulsifying ability for paraffin oil was obtained with HCQAS d (C-1, Scheme 36) with two hydroxyl groups, which induced more hydrogen bonds with water molecules, and thus more time was needed to separate it from water. Moreover, with two hydroxyl groups, HCQAS exhibited low surface tension, which facilitated foamability. The authors showed that HCQAS exhibited a contact angle of less than 90° and excellent wettability. Moreover, the detergency studies demonstrated that HCQAS exhibited better results than the standard detergent.
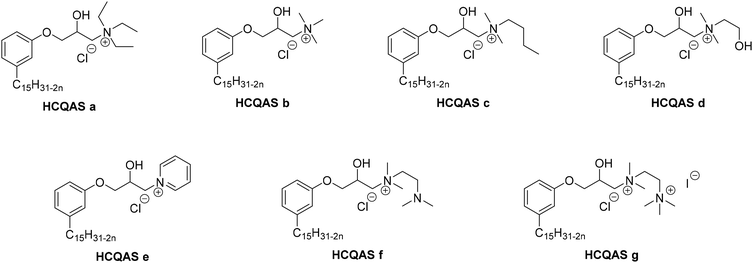 |
| Scheme 37 Structures of different HCQAS used for detergent application by Zaho et al.194 | |
d. Demulsifier agent.
Another application of CNSL surfactants is as demulsifier agents in crude oil emulsions. Demulsifiers are used to separate emulsions, usually in the processing of crude oil. Indeed, this process also produces significant quantities of saline water, which must be removed from the crude oil prior to refining. Moreover, if most of the salt water is not removed, significant corrosion problems can arise during the refining process. Atta et al.195 reported the synthesis of two novel non-ionic cardanol-based surfactants containing an amine group and oxyethylene unit, i.e., di-etherified cardanoxy amine (DECA) (NI-4 Scheme 36) and tri-etherified cardanoxy amine (TECA) (NI-5 Scheme 36). They exhibited different degrees of solubility in water and were used to disperse asphaltene fractions of heavy crude oil. The former resulted in the total demulsification of Arabic crude oil/water emulsions (90/10 vol%) formulated with 50 mg L−1 of DECA. In contrast, TECA showed high demulsification capabilities (at concentration ≥100 mg L−1) for crude oil/water emulsions with higher water contents (50/50 vol%). The authors demonstrated that the oxyethylene repeating unit of TECA expands and interacts with water more than DECA to affect their hydrodynamic diameters at aggregation above their CMC. The strong hydrophobic interaction of the alkyl phenoxy of cardanol at the core of its micelles and the packing of oxyethylene groups at the micelle shell was greater for DECA than TECA. In this study, DECA showed a strong tendency to irreversibly adsorb at the water–oil interface. The lower adsorption of TECA on the asphaltene surfaces caused them to be more polar, decreasing its capacity to interact with heptane aliphatic solvents. The good ability of DECA to act as an asphaltene dispersant facilitated the demulsification of highly stable water in crude oil emulsions with low water contents.
Ezzat et al.196 synthesized cationic cardanol-based surfactants with similar structures as that in the study by Atta et al.,195 as previously discussed. Quaternized di-etherified cardanoxy amine (QDECA) (C-2 Scheme 36) and quaternized tri-etherified cardanoxy amine (QTECA) (C-3 Scheme 36) were also used to disperse asphaltene fractions of heavy crude oil. The demulsification data confirmed that QTECA and QDECA achieved high separation performances and their demulsifying action reached 100% at a low concentration of 10 mg L−1 for crude oil/water (90/10 vol%) emulsion. Moreover, lower dosages of QTECA and QDECA demulsifiers showed a better demulsification performance with low water content crude oil water emulsions. Increasing concentrations of QTECA and QDECA demulsifier reduced the water separation of emulsions, which may be attributed to an overdosing effect. The surface tension measurements showed that QDECA has greater tendency to reduce the surface tension of water than QTECA. Thus, the high reduction in the water surface tension for QDECA than QTECA confirmed the weak intermolecular interaction between ions and the hydrophobicity of the cardanol cations. As in the study by Atta et al., the chemical structure of QDECA was less sterically hindered than QTECA, which increased its tendency to irreversibly adsorb at the water–oil interfaces. Hence, the interfacial activity of QDECA increased more than QTECA when they were dispersed in the water. In conclusion, cationic cardanol-based surfactants have greater ability to reduce the surface tension and can separate water more effectively, thus exhibiting a greater tendency to disperse asphaltene an perform better as a demulsifier than their non-ionic analogues.
e. Antibacterial agent.
Finally, some studies reported the antibacterial properties of CNSL-based surfactants. Prasad et al.197 functionalized cardanol with glucose. This glycolipid self-assembled to produce a gel in hydrophobic solvents and behaved as a surfactant in water by diffusion into the air–water interface, reducing the surface tension of water. The authors showed that cardanol-based glycolipid NI-6 (Scheme 36) could disrupt biofilms formed by pathogens such as Escherichia coli and Salmonella enterica Typhimurium. These bio-based products can be used for surface cleaning in hospital environments or the food processing industry.
f. Miscellaneous.
Besides, the surfactant properties of several non-ionic CNSL-based polyols were studied without reporting their specific applications. França et al.198 synthesized CNSL-based surfactants through glycosylation between cardanol (NI-7, Scheme 36), cardol (NI-8 Scheme 36) or anacardic acid (NI-9 Scheme 36) and saccharide. They demonstrated that the CMC values were low for these three surfactants. However, the concentration indicated that the aggregation behavior of the alkylphenyl glycosides depends on their structural characteristics. Indeed, cardanyl oligoglycoside showed a lower CMC value followed by cardyl oligoglycoside and anacardyl oligoglycoside. Moreover, the area per molecule (A) values indicated that cardyl oligoglycosides (NI-8) are likely to form smaller aggregates than cardanyl oligoglycosides (NI-7) and anacardyl oligoglycosides (NI-9). Thus, cardyl oligoglycosides tended to form inverted micelles, whereas cardanyl and anacardyl oligoglycosides formed vesicles and bilayers. Tyman and Bruce synthesized novel polyethoxylated cardanol and cardol (NI-1 and NX-10, Scheme 36) surfactants with various numbers of ethoxylate (EO) units ranging from 1 to 48.199,200 No specific application was mentioned but interesting analyses were performed to compare the surfactant properties between cardanol and cardol. Moreover, the influence of the polar head length was studied as well as the impact of unsaturation of the side chains. The samples of polyethoxylated cardanol with an EO of 13 and polyethoxylated cardol with an EO of 10 exhibited the greatest reduction in surface tension. Nevertheless, polyethoxylated cardol exhibited a relatively smaller reduction in surface tension (25 Nm−1), and consequently would be expected to be a less effective surfactant than polyethoxylated cardanol, which showed a reduction in surface tension of 34 Nm−1. The authors also demonstrated that polyethoxylated cardanol and its saturated analog appear to show similar surfactant behavior. However, the biodegradation studies showed that hydrophobic chains with unsaturations were beneficial for biodegradation. Thus, even if the authors did not report the precise applications of these surfactants, the study of their biodegradability and performance make it possible to highlight the strong potential of polyethoxylated cardanol in detergent formulations that are more environmentally friendly and can be commonly used in daily life, for example for laundry. Xu et al.201 disclosed the synthesis of a non-ionic cardanol-based (NI-11 Scheme 36) surfactant with a high functionality of hydroxyl functions. The authors highlighted the low surface tension of this surfactant at its CMC, which make it very interesting for many applications. Nevertheless, no specific application was mentioned by the authors.
g. Conclusion.
Table 3 summarized the name, structure, CMC, surface tension, and applications of the different CNSL-based surfactants discussed in this section. A wide range of CNSL-based polyol surfactants has been identified and studied. Indeed, numerous applications have been widely described in this paragraph for CNSL-based polyol surfactants. Once again, most of the CNSL-compounds used were cardanol. This can be explained by the fact that the CMC was usually lower with cardanol-based surfactants than with their analog cardanol- or anacardic acid-based surfactants. Thus, it reduces the price of the formulation, which is an excellent commercial argument for industrial application. Moreover, some of the CNSL-based polyols described in this part as surfactants can be used as monomers for the synthesis of polymers requiring polyols such as polyesters and polyurethanes.
Table 3 Name (cationic surfactants are in orange), structure, CMC, surface tension and applications of different CNSL-based surfactants
Name |
Structure |
CMC (mol L−1) |
γ
CMC (mN m−1) |
Applications |
NI-1186 |
|
— |
— |
Wetting agent in cement |
NI-2187,188 |
|
— |
— |
Emulsifying agent for bituminous |
NI-1190 |
|
5.50 × 10−6–2.40 × 10−5 |
31.90–46.16 |
Detergent |
NI-3192,193 |
|
— |
— |
C-1194 |
|
4.27 × 10−5 |
22.54 |
NI-4 DECA195 |
|
3.40 × 10−4 |
33.35 |
Demulsifier |
NI-5 TECA195 |
|
5.87 × 10−4 |
31.22 |
C-2 QDEACC196 |
|
4.90 × 10−4 |
35.60 |
C-3 QTEACC-29 b196 |
|
1.10 × 10−4 |
43.20 |
NI-6197 |
|
2.10 × 10−3 |
51.00 |
Biofilms |
NI-7198 |
|
6.90 × 10−4 |
42.00 |
Emulsion |
NI-8198 |
|
8.20 × 10−4 |
49.00 |
NI-9198 |
|
9.20 × 10−4 |
39.00 |
NI-10199,200 |
|
— |
— |
— |
NX-10199,200 |
|
— |
— |
— |
NI-11201 |
|
5.00 × 10−3 |
35.27 |
— |
IV. Conclusion
In this review, we highlighted the versatility of cashew nut shell liquid (CNSL). This bioresource, particularly cardanol, due to its unique chemical structure, allows numerous chemical modifications, making it the precursor of choice for the synthesis of polyol. Due to the chemical structure of phenol lipids, the addition of a polar head with several hydroxy functions allows these CNSL polyol derivatives to be a good candidate in the field of surfactants, especially non-ionic surfactants. These CNSL-based polyols have been increasingly investigated as precursors for the synthesis of polyurethanes (foams and coatings), polyesters and alkyd resins. In addition to increasing the ratio of biobased carbon in these polymers, CNSL derivatives impact the final properties of the resulting materials by increasing their thermal stability, flexibility, and hydrophobicity due to the presence of aromatic rings and unsaturations. Furthermore, this structure can provide faster drying in alkyd resins. However, this can also lead to yellowing or unwanted oxidation reactions. Thus, to limit some of the unwanted effects, it is possible to functionalize these unsaturations or add an antioxidant agent. Given that the raw material itself is colored, this may also limit its use in certain applications. Thus, many academic and industrial studies focus on the discoloration of CNSL.202
However, despite the wide variety of polyols described in the literature, few are made from cardol or anacardic acid, a promising difunctional precursor also present in CNSL. In fact, only cardanol is currently being sold on a large scale. Currently, only a small number of companies market cardol or anacardic acid and only in small quantities at prices that make them unattractive for academic studies or industrial use. Although CNSL is relatively inexpensive due to the availability of waste from the cashew nut industry, the techniques used to separate its different components may limit its industrial use at present. The origin of the raw material can also impact the CNSL composition, which affect the properties of materials using these polyols. Thus, to overcome the batch disparities linked to the unsaturation content, it is also possible to carry out a hydrogenation step to obtain a saturated alkyl chain. Additionally, all the polyol syntheses described in the literature are not necessarily economically viable for the applications targeted by companies, given that they involve several synthesis steps and fairly expensive reagents. Therefore, it important to consider this when developing bio-based polyols as an alternative for common applications.
Finally, the synthesized polyols are often only partially bio-based, the other reagents used in the synthesis steps are petroleum-based molecules. The toxicity of these reagents is sometimes questionable, and few reports focus on the toxicity, biodegradability or environmental impact of the resulting CNSL-based polyols described in this review. Efforts still need to be made in this area because “biobased” is not synonymous with “non-toxic” and the sustainability of a product is a complex character that concerns all the reagents and synthesis steps for its formation.
Despite the undeniable acceleration in the study and the use of CNSL and its derivatives in the chemical industry, there is still a long way for their investigation and possible improvement concerning CNSL-based polyols. It is still easy to imagine many new polyol monomers from this abundant and available bioresource that does not conflict with crops intended for human or animal feed. Optimizations and significant urgency are still necessary to develop sustainable, efficient and relevant solutions for diverse applications, suggesting a promising future for CNSL derivatives.
Author contributions
Conceptualization, B. B.; investigation, B. B., E. R. and M. D., writing—original draft preparation, B. B., E. R., M. D and C. S.; writing—review and editing, B. B., S. C., V. L., E. R., and.; visualization, B. B.; supervision, B. B. All authors have read and agreed to the published version of the manuscript.
Data availability
No primary research results, software or code has been included and no new data were generated or analysed as part of this review.
Conflicts of interest
The authors declare no conflict of interest.
References
- V. Somisetti, R. Narayan and R. V. Kothapalli, Multifunctional polyurethane coatings derived from phosphated cardanol and undecylenic acid based polyols, Prog. Org. Coat., 2019, 134, 91–102 CrossRef CAS.
-
B. C. Black, Crude reality: petroleum in world history, Rowman & Littlefield Publishers, 2012 Search PubMed.
- Worldwide Deepwater Petroleum Exploration and Development Prospectivity: Comparative Analysis of Efforts and Outcomes, in SPE Annual Technical Conference and Exhibition?, ed. OO Iledare, SPE, 2009.
-
H. S. Gorman, Redefining Efficiency: Pollution Concerns, Regulatory Mechanisms, and Technological Change in the US Petroleum Industry, The University of Akron Press, 2001 Search PubMed.
-
M. Mazzucato and G. Dibb, Innovation policy and industrial strategy for post-Covid economic recovery, UCL Institute for Innovation and Public Purpose, Policy Brief series (IIPP PB 10), London., 2020 Search PubMed.
- H. L. Moore and H. Collins, Rebuilding the post-Covid-19 economy through an industrial strategy that secures livelihoods, Soc. Sci. Humanit. Open., 2021, 3(1), 100113 Search PubMed.
- T. D. Nielsen, J. Hasselbalch, K. Holmberg and J. Stripple, Politics and the plastic crisis: A review throughout the plastic life cycle, Wiley Interdiscip. Rev.: Energy Environ., 2020, 9(1), e360 CAS.
- V. G. Yadav, G. D. Yadav and S. C. Patankar, The production of fuels and chemicals in the new world: critical analysis of the choice between crude oil and biomass vis-à-vis sustainability and the environment, Clean Technol. Environ. Policy, 2020, 22, 1757–1774 CrossRef.
- P. T. Anastas and J. C. Warner, Green chemistry, Frontiers, 1998, 640, 1998 Search PubMed.
- S. Ghosh and M. Sudha, A review on polyols: new frontiers for health-based bakery products, Int. J. Food Sci. Nutr., 2012, 63(3), 372–379 CrossRef CAS.
- T. Rice, E. Zannini, E. K. Arendt and A. Coffey, A review of polyols–biotechnological production, food applications, regulation, labeling and health effects, Crit. Rev. Food Sci. Nutr., 2020, 60(12), 2034–2051 CrossRef.
- D. S. Kaikade and A. S. Sabnis, Polyurethane foams from vegetable oil-based polyols: a review, Polym. Bull., 2023, 80(3), 2239–2261 CrossRef CAS.
- I. Singh, S. K. Samal, S. Mohanty and S. K. Nayak, Recent advancement in plant oil derived polyol–based polyurethane foam for future perspective: a review, Eur. J. Lipid Sci. Technol., 2020, 122(3), 1900225 CrossRef CAS.
- W. H. Tham, M. U. Wahit, M. R. Abdul Kadir, T. W. Wong and O. Hassan, Polyol-based biodegradable polyesters: a short review, Rev. Chem. Eng., 2016, 32(2), 201–221 CAS.
- K. Lang, R. J. Sánchez-Leija, R. A. Gross and R. J. Linhardt, Review on the impact of polyols on the properties of bio-based polyesters, Polymers, 2020, 12(12), 2969 CrossRef CAS.
- H. Luo, C. Liu, D. He, J. Sun, J. Li and X. Pan, Effects of aging on environmental behavior of plastic additives: Migration, leaching, and ecotoxicity, Sci. Total Environ., 2022, 849, 157951 CrossRef CAS.
- J. N. Hahladakis, C. A. Velis, R. Weber, E. Iacovidou and P. Purnell, An overview of chemical additives present in plastics: Migration, release, fate and environmental impact during their use, disposal and recycling, J. Hazard. Mater., 2018, 344, 179–199 CrossRef CAS.
- R. F. Nunes and A. C. S. C. Teixeira, An overview on surfactants as pollutants of concern: occurrence, impacts and persulfate-based remediation technologies, Chemosphere, 2022, 300, 134507 CrossRef CAS.
- J. Arora, A. Ranjan, A. Chauhan, R. Biswas, V. D. Rajput and S. Sushkova,
al., Surfactant pollution, an emerging threat to ecosystem: Approaches for effective bacterial degradation, J. Appl. Microbiol., 2022, 133(3), 1229–1244 CrossRef CAS.
- K. Hill and O. Rhode, Sugar–based surfactants for consumer products and technical applications, Lipid/Fett, 1999, 101(1), 25–33 CrossRef CAS.
- Y. Li, X. Zhang, Y. Li, C. Li and X. Guo, Micellization of glucose-based
surfactants with different counter ions and their interaction with DNA, Colloids Surf., A, 2014, 443, 224–232 CrossRef CAS.
- H. Lu, G. Pourceau, B. Briou, A. Wadouachi, T. Gaudin and I. Pezron,
et al., Sugar-Based Surfactants: Effects of Structural Features on the Physicochemical Properties of Sugar Esters and Their Comparison to Commercial Octyl Glycosides, Molecules, 2024, 29(10), 2338 CrossRef CAS.
- S. Mohammed and S. Ikiensikimama, Vegetable oils as surfactant feedstocks for enhanced oil recovery: A review, Chem. Eng. Res. Des., 2023, 693–705 CrossRef.
- A. Roy, P. Fajardie, B. Lepoittevin, J. Baudoux, V. Lapinte, S. Caillol and B. Briou, CNSL, a Promising Building Blocks for Sustainable Molecular Design of Surfactants: A Critical Review, Molecules, 2022, 27(4), 1443 CrossRef CAS.
- S. Miao, P. Wang, Z. Su and S. Zhang, Vegetable-oil-based polymers as future polymeric biomaterials, Acta Biomater., 2014, 10(4), 1692–1704 CrossRef CAS.
- C. Zhang, T. F. Garrison, S. A. Madbouly and M. R. Kessler, Recent advances in vegetable oil-based polymers and their composites, Prog. Polym. Sci., 2017, 71, 91–143 CrossRef CAS.
- P. M. Paraskar, M. S. Prabhudesai, V. M. Hatkar and R. D. Kulkarni, Vegetable oil based polyurethane coatings–A sustainable approach: A review, Prog. Org. Coat., 2021, 156, 106267 CrossRef CAS.
- H. Röper and J. Goossens, Erythritol, a new raw material for food and non–food applications, Starch/Staerke, 1993, 45(11), 400–405 CrossRef.
- EFSA Panel on Food Additives and Nutrient Sources added to Food (ANS), A. Mortensen, F. Aguilar, R. Crebelli and A. Di Domenico,
et al., Re–evaluation of glycerol (E 422) as a food additive, EFSA J., 2017, 15(3), e04720 Search PubMed.
- M. V. Chiriacò, N. Galli, M. Santini and M. C. Rulli, Deforestation and greenhouse gas emissions could arise when replacing palm oil with other vegetable oils, Sci. Total Environ., 2024, 914, 169486 CrossRef.
- N. Mahmood, Z. Yuan, J. Schmidt and C. C. Xu, Production of polyols via direct hydrolysis of kraft lignin: Effect of process parameters, Bioresour. Technol., 2013, 139, 13–20 CrossRef CAS.
- M. Fache, E. Darroman, V. Besse, R. Auvergne, S. Caillol and B. Boutevin, Vanillin, a promising biobased building-block for monomer synthesis, Green Chem., 2014, 16(4), 1987–1998 RSC.
- I. Kühnel, J. Podschun, B. Saake and R. Lehnen, Synthesis of lignin polyols via oxyalkylation with propylene carbonate, Holzforschung, 2015, 69(5), 531–538 CrossRef.
- H. Gang, D. Lee, K.-Y. Choi, H.-N. Kim, H. Ryu and D.-S. Lee,
et al., Development of high performance polyurethane elastomers using vanillin-based green polyol chain extender originating from lignocellulosic biomass, ACS Sustainable Chem. Eng., 2017, 5(6), 4582–4588 CrossRef CAS.
- M. S. Mahajan and V. V. Gite, Self-healing polyurethane coatings of eugenol-based polyol incorporated with linseed oil encapsulated cardanol-formaldehyde microcapsules: A sustainable approach, Prog. Org. Coat., 2022, 162, 106534 CrossRef CAS.
- H.-G. Oh, T.-U. Oh, S. Hong and S.-H. Cha, Synthesis and characterization of antibacterial self-healable biopolyurethanes with eugenol-based bio-polyol, Mater. Today Commun., 2023, 35, 106381 CrossRef CAS.
- Y. Ma, Y. Xiao, Y. Zhao, Y. Bei, L. Hu and Y. Zhou,
et al., Biomass based polyols and biomass based polyurethane materials as a route towards sustainability, React. Funct. Polym., 2022, 175, 105285 CrossRef CAS.
- A. Noreen, K. M. Zia, M. Zuber, S. Tabasum and A. F. Zahoor, Bio-based polyurethane: An efficient and environment friendly coating systems: A review, Prog. Org. Coat., 2016, 91, 25–32 CrossRef CAS.
- J. Datta and E. Głowińska, Chemical modifications of natural oils and examples of their usage for polyurethane synthesis, J. Elastomers Plastics, 2014, 46(1), 33–42 CrossRef.
- C. Voirin, S. Caillol, N. V. Sadavarte, B. V. Tawade, B. Boutevin and P. P. Wadgaonkar, Functionalization of cardanol: towards biobased polymers and additives, Polym. Chem., 2014, 5(9), 3142–3162 RSC.
- S. Caillol, Cardanol: A promising building block for biobased polymers and additives, Curr. Opin. Green Sustain. Chem., 2018, 14, 26–32 CrossRef.
- . Which Country Produces the Most Cashew Nuts? 2022 [updated 17 december 2023]. Available from: https://www.helgilibrary.com/charts/which-country-produces-the-most-cashew-nuts/#:~:text=Total%20cashew%20nut%20production%20reached,of%20287%2C535%20tonnes%20in%201961.
- M. Khalid Zafeer and K. Subrahmanya Bhat, Valorisation of agro-waste cashew nut husk (Testa) for different value-added products, Sustainable Chem. Clim. Action, 2023, 2, 100014 CrossRef.
- D. J. Garkal and R. S. Bhande, Review on Extraction and Isolation of Cashew Nut Sh Ell Liquid, Int. J. Innov. Eng. Res. Technol., 2014, 1(1), 1–8 Search PubMed.
-
S. Mlowe and J. Mgaya, Recent Trends of Cashew Nutshell Liquid: Extraction, Chemistry, and Applications, in Plant Biomass Derived Materials: Sources, Extractions, and Applications, 2024, pp. 117–139 Search PubMed.
- N. Emelike, M. Akusu and A. Ujong, Antioxidant and physicochemical properties of oil extracted from cashew (Anacardium occidentale L) kernels, Int. J. Food Sci. Nutr., 2017, 2(6), 122–128 Search PubMed.
-
Isolation and Green Methylation of Cardanol from Cashew Nut Shell Liquid, in Materials Science Forum, ed. M. Anwar, N. D. Rahayu and T. D. Wahyuningsih, Trans Tech Publ, 2022 Search PubMed.
- S. Chatterjee and S. L. Rokhum, Extraction of a cardanol based liquid bio-fuel from waste natural resource and decarboxylation using a silver-based catalyst, Renewable Sustainable Energy Rev., 2017, 72, 560–564 CrossRef CAS.
- A. A. Durrani, G. L. Davis, S. K. Sood, V. Tychopoulos and J. H. Tyman, Long–chain phenols. Part 231 practical separations of the component phenols in technical cashew nut–shell liquid (Anacardium occidentale): Distillation procedures for obtaining cardanol, J. Chem. Technol. Biotechnol., 1982, 32(7–12), 681–690 CrossRef CAS.
- L. Nambela, L. V. Haule and Q. A. Mgani, Anacardic acid isolated from cashew nut shells liquid: A potential precursor for the synthesis of anthraquinone dyes, Cleaner Chem. Eng., 2022, 3, 100056 CrossRef.
- J. Zhang and S. Xu, Curing kinetics of epoxy cured by cardanol-based phenalkamines synthesized from different polyethylenepolyamines by Mannich reaction, Iran. Polym. J., 2017, 26, 499–509 CrossRef CAS.
- J. Song, M. Li, S. Li, K. Huang and J. Xia, Synthesis and phase separation phenomena of cardanol diethers-Mannich base curing agent, Chem. Ind. For. Prod., 2016, 36(5), 61–67 CAS.
- A. Devi and D. Srivastava, Cardanol–based novolac–type phenolic resins. I. A kinetic approach, J. Appl. Polym. Sci., 2006, 102(3), 2730–2737 CrossRef CAS.
- P. Rahmawati, A. H. Ramelan, S. D. Marliyana, N. S. Suharty and S. Wahyuningsih, Synthesis of cardanol-based novolac resin from cashew nut shell liquid, J. Eng. Sci., 2019, 15, 23–33 CrossRef.
- O. A. Attanasi, S. Berretta, C. Fiani, P. Filippone, G. Mele and R. Saladino, Synthesis and reactions of nitro derivatives of hydrogenated cardanol, Tetrahedron, 2006, 62(25), 6113–6120 CrossRef CAS.
- B. Patil, C. Chetta and D. Pinjari, Sono Facilitated Selective Nitration of Naturally Occurring Cardanol Using Phase Transfer Catalyst, Int. J. Chem. Sci., 2017, 15(4), 214 Search PubMed.
- W. Luo, Y. Yang, Y. Han, Y. Weng and C. Zhang, Synergistic effect of thermal stabilization and plasticization of epoxidized cardanol esters on PVC, J. Polym. Environ., 2023, 31(12), 5126–5136 CrossRef CAS.
- J. Chen, X. Nie, Z. Liu, Z. Mi and Y. Zhou, Synthesis and application of polyepoxide cardanol glycidyl ether as biobased polyepoxide reactive diluent for epoxy resin, ACS Sustainable Chem. Eng., 2015, 3(6), 1164–1171 CrossRef CAS.
- X. Li, X. Nie, J. Chen and Y. Wang, Preparation of epoxidized cardanol butyl ether as a novel renewable plasticizer and its application for poly (vinyl chloride), Polym. Int., 2017, 66(3), 443–449 CrossRef CAS.
- B. Briou, S. Caillol, J.-J. Robin and V. Lapinte, Non-endocrine disruptor effect for cardanol based plasticizer, Ind. Crops Prod., 2019, 130, 1–8 CrossRef CAS.
- V. Madhusudhan, M. Sivasamban, R. Vaidyeswaran and M. B. Rao, Kinetics of hydrogenation of cardanol, Ind. Eng. Chem. Process Des. Dev., 1981, 20(4), 625–629 CrossRef CAS.
- B. R. Patil, A. H. Bari, D. V. Pinjari and A. B. Pandit, Kinetic modelling of hydrogenation of cardanol over Pd/C catalyst, Indian Chem. Eng., 2018, 60(1), 88–103 CrossRef CAS.
- Z. Mao, T. Luo, Y. Wang, H. Zhang and G. Liu, Catalytic hydrogenation of cardanol as well as purification and characterization of the product, Chem. Ind. For. Prod., 2010, 30(2), 52–56 CAS.
- F. Jaillet, E. Darroman, A. Ratsimihety, B. Boutevin and S. Caillol, Synthesis of cardanol oil building blocks for polymer synthesis, Green Mater., 2015, 3(3), 59–70 CrossRef.
- J. A. Muldoon, M. D. Garrison, M. A. Savolainen and B. G. Harvey, Ambient temperature cross-linking of a sustainable, cardanol-based cyanate ester via synergistic thiol–ene copolymerization, Polym. Chem., 2022, 13(21), 3091–3101 RSC.
- B. Briou, B. Améduri and B. Boutevin, Trends in the Diels–Alder reaction in polymer chemistry, Chem. Soc. Rev., 2021, 50(19), 11055–11097 RSC.
- A. Greco and A. Maffezzoli, Cardanol derivatives as innovative bio-plasticizers for poly-(lactic acid), Polym. Degrad. Stab., 2016, 132, 213–219 CrossRef CAS.
- M. O. De Almeida, L. R. Silva, L. R. Kotzebue, F. J. Maia, J. S. Acero and G. Mele,
et al., Development of Fully Bio–Based Lubricants from Agro–Industrial Residues under Environmentally Friendly Processes, Eur. J. Lipid Sci. Technol., 2020, 122(5), 1900424 CrossRef CAS.
- J. Ma, X. Chen, Y. Li, L. Hao and G. Li, Bio-Based Antiwear/Extreme Pressure Additive Synthesized from Natural Renewable Cardanol, ACS Sustainable Chem. Eng., 2023, 11(36), 13398–13406 CrossRef CAS.
- A. Greco, D. Brunetti, G. Renna, G. Mele and A. Maffezzoli, Plasticizer for poly (vinyl chloride) from cardanol as a renewable resource material, Polym. Degrad. Stab., 2010, 95(11), 2169–2174 CrossRef CAS.
- Y. Makame, E. Mubofu and M. Kombo, Synthesis and characterization of polyesters from renewable cardol, Bull. Chem. Soc. Ethiop., 2016, 30(2), 273–282 CrossRef CAS.
- P. Campaner, Y. M. Kim, C. Tambe and A. Natesh, Evaluation of Cashew Nut Shell Liquid Derived Isocyanate Blocking Agents, Int. J. Adv. Sci. Eng., 2020, 7(2), 1642–1651 CrossRef CAS.
- N. Rekha and S. K. Asha, Synthesis and FTIR spectroscopic investigation of the UV curing kinetics of telechelic urethane methacrylate crosslinkers based on the renewable resource—Cardanol, J. Appl. Polym. Sci., 2008, 109(5), 2781–2790 CrossRef CAS.
-
Z. Dia and M. J. Chen, Dérivé de cardanol et procédé d'élaboration, EP11377620A1, 1999 Search PubMed.
- M. North, R. Pasquale and C. Young, Synthesis of cyclic carbonates from epoxides and CO2, Green Chem., 2010, 12(9), 1514–1539 RSC.
- A. Rehman, F. Saleem, F. Javed, A. Ikhlaq, S. W. Ahmad and A. Harvey, Recent advances in the synthesis of cyclic carbonates via CO2 cycloaddition to epoxides, J. Environ. Chem. Eng., 2021, 9(2), 105113 CrossRef CAS.
- R. Morales-Cerrada, S. Molina-Gutierrez, P. Lacroix-Desmazes and S. Caillol, Eugenol, a promising building block for biobased polymers with cutting-edge properties, Biomacromolecules, 2021, 22(9), 3625–3648 CrossRef CAS.
- K. I. Suresh and M. Harikrishnan, Effect of cardanol diol on the synthesis, characterization, and film properties of aqueous polyurethane dispersions, J. Coat. Technol. Res., 2014, 11, 619–629 CrossRef CAS.
- K. I. Suresh and V. S. Kishanprasad, Synthesis, structure, and properties of novel polyols from cardanol and developed polyurethanes, Ind. Eng. Chem. Res., 2005, 44(13), 4504–4512 CrossRef CAS.
- A.-S. Mora, R. Tayouo, B. Boutevin, G. David and S. Caillol, Synthesis of biobased reactive hydroxyl amines by amination reaction of cardanol-based epoxy monomers, Eur. Polym. J., 2019, 118, 429–436 CrossRef CAS.
- S. Huo, G. Wu, J. Chen, G. Liu and Z. Kong, Constructing polyurethane foams of strong mechanical property and thermostability by two novel environment friendly bio-based polyols, Korean J. Chem. Eng., 2016, 33(3), 1088–1094 CrossRef CAS.
- S. Huo, C. Jin, G. Liu, J. Chen, G. Wu and Z. Kong, Preparation and properties of biobased autocatalytic polyols and their polyurethane foams, Polym. Degrad. Stab., 2019, 159, 62–69 CrossRef CAS.
- H. Wang and Q. Zhou, Synthesis of cardanol-based polyols via thiol-ene/thiol-epoxy dual click-reactions and thermosetting polyurethanes therefrom, ACS Sustainable Chem. Eng., 2018, 6(9), 12088–12095 CrossRef CAS.
- H. Hussain, A. Al-Harrasi, I. R. Green, I. Ahmed, G. Abbas and N. U. Rehman, meta-Chloroperbenzoic acid (m CPBA): a versatile reagent in organic synthesis, RSC Adv., 2014, 4(25), 12882–12917 RSC.
- F. Jaillet, E. Darroman, B. Boutevin and S. Caillol, A chemical platform approach on cardanol oil: from the synthesis of building blocks to polymer synthesis, OCL: Oilseeds Fats, Crops Lipids, 2016, 23(5), 511–518 CrossRef.
- K. I. Suresh, Rigid polyurethane foams from cardanol: synthesis, structural characterization, and evaluation of polyol and foam properties, ACS Sustainable Chem. Eng., 2013, 1(2), 232–242 CrossRef CAS.
- C. Bo, L. Hu, P. Jia, B. Liang, J. Zhou and Y. Zhou, Structure and thermal properties of phosphorus-containing polyol synthesized from cardanol, RSC Adv., 2015, 5(129), 106651–106660 RSC.
- S.-H. Kim, S. W. Kim and S.-H. Cha, Synthesis and characterization of biopolyol-based polyurethane films derived from modified cardanol through two-step reaction, Polymer, 2016, 40, 1005–1014 CAS.
- C. Fu, J. Liu, H. Xia and L. Shen, Effect of structure on the properties of polyurethanes based on aromatic cardanol-based polyols prepared by thiol-ene coupling, Prog. Org. Coat., 2015, 83, 19–25 CrossRef CAS.
- M. L. Shrestha, M. Ionescu, X. Wan, N. Bilić, Z. S. Petrović and T. Upshaw, Biobased aromatic-aliphatic polyols from cardanol by thermal thiol-ene reaction, J. Renewable Mater., 2018, 6(1), 87–101 CrossRef CAS.
- M. L. Shrestha, M. Ionescu, X. Wan and T. Upshaw, Biobased aromatic-aliphatic polyols by thiol-ene reactions of propoxylated mercaptanized cardanol, J. Renewable Mater., 2018, 6(6), 630–641 CAS.
- A. A. Durrani, G. Cheng sun and J. H. Tyman, Long-chain phenols: XX. Synthesis of oxidative degradation products from the methylated component phenols of Anacardium occidentale and other phenolic lipids: Confirmation of the structure of the parent phenols and of a related material, Lipids, 1982, 17(8), 561–569 CrossRef CAS.
- M. B. Graham and H. Tyman, Ozonization of phenols from Anacardium occidentale (cashew), J. Am. Oil Chem. Soc., 2002, 79(7), 725–732 CrossRef CAS.
-
A. J. Varma and S. Sivaram, (Hydroxyalkyl) phenols, method for their preparation, and uses thereof, US6451957 B1, 2000.
-
F. Dinon, C. Tambe, P. Campaner, A. Natesh and T. Stonis, Oxidized cashew nut shell liquid derivatives and uses thereof, US11053389 B2, 2018.
- M. Ramasri, G. S. Rao, P. Sampatkumaran and M. Shirsalkar, Synthesis and Identification of 1, 8-Bis (hydroxyphenyl) pentadecane from 3-δ8-Pentadecenylphenol, ChemInform, 1988, 19(5) CrossRef.
- S. Jing, T. Li, X. Li, Q. Xu, J. Hu and R. Li, Phenolic foams modified by cardanol through bisphenol modification, J. Appl. Polym. Sci., 2014, 131(4), 39942 CrossRef.
- M. Ionescu and Z. S. Petrović, Phenolation of vegetable oils, J. Serb. Chem. Soc., 2011, 76(4), 591–606 CrossRef CAS.
- M. Ramasri, G. S. Rao, P. Sampathkumaran and M. Shirsalkar, Synthesis and characterization of mannich bases from cardbisphenol, J. Appl. Polym. Sci., 1990, 39(9), 1993–2004 CrossRef CAS.
- M. Kathalewar, A. Sabnis and D. D'Melo, Polyurethane coatings prepared from CNSL based polyols: Synthesis, characterization and properties, Prog. Org. Coat., 2014, 77(3), 616–626 CrossRef CAS.
- D. Balgude, A. Sabnis and S. K. Ghosh, Synthesis and characterization of cardanol based aqueous 2K polyurethane coatings, Eur. Polym. J., 2016, 85, 620–634 CrossRef CAS.
- D. B. Balgude, A. S. Sabnis and S. K. Ghosh, Designing of cardanol based polyol and its curing kinetics with melamine formaldehyde resin, Des. Monomers Polym., 2017, 20(1), 177–189 CrossRef CAS.
- F. Jaillet, E. Darroman, A. Ratsimihety, R. Auvergne, B. Boutevin and S. Caillol, New biobased epoxy materials from cardanol, Eur. J. Lipid Sci. Technol., 2014, 116(1), 63–73 CrossRef CAS.
- A. W. Bassett, C. M. Breyta, A. E. Honnig, J. H. Reilly, K. R. Sweet and J. J. La Scala,
et al., Synthesis and characterization of molecularly hybrid bisphenols derived from lignin and CNSL: Application in thermosetting resins, Eur. Polym. J., 2019, 111, 95–103 CrossRef CAS.
- H. Bhunia, R. Jana, A. Basak, S. Lenka and G. Nando, Synthesis of polyurethane from cashew nut shell liquid (CNSL), a renewable resource, J. Polym. Sci., Part A: Polym. Chem., 1998, 36(3), 391–400 CrossRef CAS.
- H. Bhunia, A. Basak, T. Chaki and G. Nando, Synthesis and characterization of polymers from cashewnut shell liquid: a renewable resource: V. Synthesis of copolyester, Eur. Polym. J., 2000, 36(6), 1157–1165 CrossRef CAS.
- H. Bhunia, G. Nando, T. Chaki, A. Basak, S. Lenka and P. Nayak, Synthesis and characterization of polymers from cashewnut shell liquid (CNSL), a renewable resource II. Synthesis of polyurethanes, Eur. Polym. J., 1999, 35(8), 1381–1391 CrossRef CAS.
- R. R. Nayak, G. Ray, B. Guru and S. Lenka, Comparative Studies of interpenetrating polymer networks derived from soybean oil–based polyurethane and cardanol m-aminophenol dye, Polym.-Plast. Technol. Eng., 2004, 43(1), 261–272 CrossRef CAS.
- T. S. Gandhi, M. R. Patel and B. Z. Dholakiya, Synthesis and characterization of different types of epoxide-based Mannich polyols from low-cost cashew nut shell liquid, Res. Chem. Intermed., 2014, 40, 1223–1232 CrossRef CAS.
- T. S. Gandhi, M. R. Patel and B. Z. Dholakiya, Mechanical, thermal and fire properties of sustainable rigid polyurethane foam derived from cashew nut shell liquid, Int. J. Plast. Technol., 2015, 19, 30–46 CrossRef CAS.
- T. S. Gandhi, M. R. Patel and B. Z. Dholakiya, Synthesis of cashew Mannich polyol via a three step continuous route and development of PU rigid foams with mechanical, thermal and fire studies, J. Polym. Eng., 2015, 35(6), 533–544 CrossRef CAS.
- A. H. Asif, M. S. Mahajan, N. Sreeharsha, V. V. Gite, B. E. Al-Dhubiab and F. Kaliyadan,
et al., Enhancement of anticorrosive performance of cardanol based polyurethane coatings by incorporating magnetic hydroxyapatite nanoparticles, Materials, 2022, 15(6), 2308 CrossRef CAS.
- M. Ionescu, X. Wan, N. Bilić and Z. S. Petrović, Polyols and rigid polyurethane foams from cashew nut shell liquid, J. Polym. Environ., 2012, 20, 647–658 CrossRef CAS.
- M. Zhang, J. Zhang, S. Chen and Y. Zhou, Synthesis and fire properties of rigid polyurethane foams made from a polyol derived from melamine and cardanol, Polym. Degrad. Stab., 2014, 110, 27–34 CrossRef CAS.
- T.-U. Oh, W.-J. Lee and S.-H. Cha, Preparation and Characterization of Polyurethane Using Cardanol-Based Bio-Polyol Obtained from One-Pot Synthetic Method, Polymer, 2022, 46(1), 13–21 CAS.
- J. H. Tyman and M. Patel, Phenolic structure and colour in Mannich reaction products, J. Chem. Res., 2007, 2007(1), 34–37 CrossRef.
- T. T. M. Tan, Cardanol–glycols and cardanol–glycol–based polyurethane films, J. Appl. Polym. Sci., 1997, 65(3), 507–510 CrossRef.
- J. H. Tyman and R. A. Johnson, The synthesis of thiobisphenols from 3-alkylphenols derived from natural phenolic lipids, J. Chem. Res., 2005, 2005(2), 116–118 CrossRef.
-
J. H. P. Tyman, Preparation of thiobisphenols from alkylphenols from natural sources, GB2421503A, 2004.
- F. Hassouma, I. Mihai, L. Fetzer, T. Fouquet, J. M. Raquez and A. Laachachi,
et al., Design of new cardanol derivative: synthesis and application as potential biobased plasticizer for poly (lactide), Macromol. Mater. Eng., 2016, 301(10), 1267–1278 CrossRef CAS.
- B. Briou, S. Caillol, J. J. Robin and V. Lapinte, Cardanol-Based and Formaldehyde-Free Flexible Phenolic Networks, Eur. J. Lipid Sci. Technol., 2018, 120(7), 8 CrossRef.
- Y. Yokoyama, T. Yasui, A. Takeda, S. Kanehashi and K. Ogino, Synthesis of bisphenol compounds from non-edible cashew nut shell liquid, Tetrahedron Lett., 2023, 118, 154384 CrossRef CAS.
- K. M. Hambleton and J. F. Stanzione III, Synthesis and characterization of a low-molecular-weight novolac epoxy derived from lignin-inspired phenolics, ACS Omega, 2021, 6(37), 23855–23861 CrossRef CAS.
- C. Mythili, A. M. Retna and S. Gopalakrishnan, Synthesis, mechanical, thermal and chemical properties of polyurethanes based on cardanol, Bull. Mater. Sci., 2004, 27, 235–241 CrossRef CAS.
- K. Sathiyalekshmi and S. Gopalakrishnan, Synthesis and characterisation of rigid polyurethanes based on hydroxyalkylated cardanol formaldehyde resin, Plast., Rubber Compos., 2000, 29(2), 63–69 CrossRef CAS.
- K. Sathiyalekshmi and S. Gopalakrishnan, Evaluation of performance of polyurethanes based on hydroxy alkylated cardanol formaldehyde resins under aging conditions, Adv. Polym. Technol., 2004, 23(2), 91–102 CrossRef CAS.
- Y. J. Joy, A. M. Retna and R. K. Samuel, Synthesis and characterization of natural fibre reinforced polyurethane composites based on cardanol, Methods, 2015, 1(1), 42–47 Search PubMed.
- B. Briou, L. Jégo, T. De Dios Miguel, N. Duguet and S. Caillol, Eco-friendly synthesis of cardanol-based AB monomer for formaldehyde-free phenolic thermosets, RSC Sustainability, 2023, 1(4), 994–1005 RSC.
- G. Foyer, B.-H. Chanfi, D. Virieux, G. David and S. Caillol, Aromatic dialdehyde precursors from lignin derivatives for the synthesis of formaldehyde-free and high char yield phenolic resins, Eur. Polym. J., 2016, 77, 65–74 CrossRef CAS.
- G. Foyer, B. H. Chanfi, B. Boutevin, S. Caillol and G. David, New method for the synthesis of formaldehyde-free phenolic resins from lignin-based aldehyde precursors, Eur. Polym. J., 2016, 74, 296–309 CrossRef CAS.
- A. Das and P. Mahanwar, A brief discussion on advances in polyurethane applications, Adv. Ind. Eng. Polym. Res., 2020, 3(3), 93–101 Search PubMed.
- . Polyurethane Market Outlook (2024–2034)
2024 [available from: https://www.factmr.com/report/polyurethane-market.
- Plastics - the fast Facts 2023 2024 [available from: https://plasticseurope.org/knowledge-hub/plastics-the-fast-facts-2023/.
- A. Cornille, S. Dworakowska, D. Bogdal, B. Boutevin and S. Caillol, A new way of creating cellular polyurethane materials: NIPU foams, Eur. Polym. J., 2015, 66, 129–138 CrossRef CAS.
-
F. M. de Souza, P. K. Kahol and R. K. Gupta, Introduction to polyurethane chemistry. Polyurethane chemistry: Renewable polyols and isocyanates, ACS Publications, 2021, pp. 1–24 Search PubMed.
- J. Niesiobędzka and J. Datta, Challenges and recent advances in bio-based isocyanate production, Green Chem., 2023, 25(7), 2482–2504 RSC.
- B. Imre, H. Gojzewski, C. Check, R. Chartoff and G. J. Vancso, Properties and Phase Structure of Polycaprolactone–Based Segmented Polyurethanes with Varying Hard and Soft Segments: Effects of Processing Conditions, Macromol. Chem. Phys., 2018, 219(2), 1700214 CrossRef.
- J. O. Akindoyo, M. Beg, S. Ghazali, M. Islam, N. Jeyaratnam and A. Yuvaraj, Polyurethane types, synthesis and applications–a review, RSC Adv., 2016, 6(115), 114453–114482 RSC.
- H. Sardon, D. Mecerreyes, A. Basterretxea, L. Averous and C. Jehanno, From lab to market: current strategies for the production of biobased polyols, ACS Sustainable Chem. Eng., 2021, 9(32), 10664–10677 CrossRef CAS.
- D. Bajwa, G. Pourhashem, A. H. Ullah and S. Bajwa, A concise review of current lignin production, applications, products and their environmental impact, Ind. Crops Prod., 2019, 139, 111526 CrossRef CAS.
- F. R. Vieira, S. Magina, D. V. Evtuguin and A. Barros-Timmons, Lignin as a Renewable Building Block for Sustainable Polyurethanes, Materials, 2022, 15(17), 6182 CrossRef CAS.
- S. Caillol, The future of cardanol as small giant for biobased aromatic polymers and additives, Eur. Polym. J., 2023, 193, 112096 CrossRef CAS.
- W. Sakulsaknimitr, S. Wirasate, K. Pipatpanyanugoon and P. Atorngitjawat, Structure and thermal properties of polyurethanes synthesized from cardanol diol, J. Polym. Environ., 2015, 23, 216–226 CrossRef CAS.
- T. T. M. Tan, Cardanol–lignin–based polyurethanes, Polym. Int., 1996, 41(1), 13–16 CrossRef.
- C. Mythili, A. Malar Retna and S. Gopalakrishnan, Physical, mechanical, and thermal properties of polyurethanes based on hydroxyalkylated cardanol–formaldehyde resins, J. Appl. Polym. Sci., 2005, 98(1), 284–288 CrossRef CAS.
- J. Peyrton and L. Avérous, Structure-properties relationships of cellular materials from biobased polyurethane foams, Mater. Sci. Eng., R, 2021, 145, 100608 CrossRef.
-
M. Ionescu, Chemistry and technology of polyols for polyurethanes, Rapra Technology, 2005 Search PubMed.
- S. Huo, H. Ma, G. Liu, C. Jin, J. Chen and G. Wu,
et al., Synthesis and properties of organosilicon-grafted cardanol novolac epoxy resin as a novel biobased reactive diluent and toughening agent, ACS Omega, 2018, 3(12), 16403–16408 CrossRef CAS.
- L. Liu, Z. Wang and M. Zhu, Flame retardant, mechanical and thermal insulating properties of rigid polyurethane foam modified by nano zirconium amino-tris-(methylenephosphonate) and expandable graphite, Polym. Degrad. Stab., 2019, 170, 108997 CrossRef CAS.
- S. Dutta and N. Karak, Synthesis, characterization of poly (urethane amide) resins from Nahar seed oil for surface coating applications, Prog. Org. Coat., 2005, 53(2), 147–152 CrossRef CAS.
- K. Wazarkar and A. Sabnis, Cardanol-based polyurethane coatings via click chemistry: an eco-friendly approach, J. Renewable Mater., 2018, 6(5), 517–528 CAS.
- C. J. Patel and V. Mannari, Air-drying bio-based polyurethane dispersion from cardanol: Synthesis and characterization of coatings, Prog. Org. Coat., 2014, 77(5), 997–1006 CrossRef CAS.
- S. Mestry, R. Kakatkar and S. Mhaske, Cardanol derived P and Si based precursors to develop flame retardant PU coating, Prog. Org. Coat., 2019, 129, 59–68 CrossRef CAS.
- V. Athawale and N. Shetty, Synthesis and characterisation of low–cost cardanol polyurethanes, Pigm. Resin Technol., 2010, 39(1), 9–14 CrossRef CAS.
-
S. Li and M. Vert, Biodegradation of aliphatic polyesters. Degradable polymers: principles and applications, Springer, 2002, pp. 43–87 Search PubMed.
- A. Rosato, A. Romano, G. Totaro, A. Celli, F. Fava and G. Zanaroli,
et al., Enzymatic degradation of the most common aliphatic bio-polyesters and evaluation of the mechanisms involved: an extended study, Polymers, 2022, 14(9), 1850 CrossRef CAS.
- R. Mouhoubi, M. Lasschuijt, S. Ramon Carrasco, H. Gojzewski and F. R. Wurm, End-of-life biodegradation? how to assess the composting of polyesters in the lab and the field, Waste Manage., 2022, 154, 36–48 CrossRef CAS.
- R.-J. Müller, I. Kleeberg and W.-D. Deckwer, Biodegradation of polyesters containing aromatic constituents, J. Biotechnol., 2001, 86(2), 87–95 CrossRef.
- Decode the Future of Polylactic Acid 2023 [updated Aug 2023. Available from: https://www.chemanalyst.com/industry-report/polylactic-acid-pla-market-673.
- . Market volume of polyethylene terephthalate worldwide from 2015 to 2022, with a forecast for 2023 to 2030 2023 [available from: https://statista.com/statistics/1245264/polyethylene-terephthalate-market-volume-worldwide/.
- Y. Han, Y. Weng and C. Zhang, Development of biobased plasticizers with synergistic effects of plasticization, thermal stabilization, and migration resistance: A review, J. Vinyl Addit. Technol., 2024, 30(1), 26–43 CrossRef CAS.
- Q. Zhang, M. Song, Y. Xu, W. Wang, Z. Wang and L. Zhang, Bio-based polyesters: Recent progress and future prospects, Prog. Polym. Sci., 2021, 120, 101430 CrossRef CAS.
- Y.-M. Tu, X.-M. Wang, X. Yang, H.-Z. Fan, F.-L. Gong and Z. Cai,
et al., Biobased High-Performance Aromatic–Aliphatic Polyesters with Complete Recyclability, J. Am. Chem. Soc., 2021, 143(49), 20591–20597 CrossRef CAS.
- K. Hiraga, I. Taniguchi, S. Yoshida, Y. Kimura and K. Oda, Biodegradation of waste PET. A sustainable solution for dealing with plastic pollution, EMBO Reports, 2019, 20(11), e49365 CrossRef CAS.
- Z. Liu, H. Zhang, S. Liu and X. Wang, Bio-based upcycling of poly(ethylene terephthalate) waste to UV-curable polyurethane acrylate, Polym. Chem., 2023, 14(10), 1110–1116 RSC.
- H. Qiang, J. Wang, H. Liu and Y. Zhu, From vanillin to biobased aromatic polymers, Polym. Chem., 2023, 14(37), 4255–4274 RSC.
- T. Goto and H. Abe, Substituent Effects on Thermal and Mechanical Properties of Resorcinol–Based Semiaromatic Polyesters, Macromol. Chem. Phys., 2022, 223(3), 2100355 CrossRef CAS.
- M. Saminathan, C. Krishna, S. Pillai and C. Pavithran, Synthesis and characterization of main-chain liquid-crystalline polymers containing a p-phenyleneazo group, Macromolecules, 1993, 26(25), 7103–7105 CrossRef CAS.
-
R. Shingte, Synthesis of processable high performance polymers, Savitribai Phule, Pune University, 2006 Search PubMed.
- A. S. More, P. V. Naik, K. P. Kumbhar and P. P. Wadgaonkar, Synthesis and characterization of polyesters based on 1, 1, 1-[bis (4-hydroxyphenyl)–4′–pentadecylphenyl] ethane, Polym. Int., 2010, 59(10), 1408–1414 CrossRef CAS.
- B. V. Tawade, J. K. Salunke, P. S. Sane and P. P. Wadgaonkar, Processable aromatic polyesters based on bisphenol derived from cashew nut shell liquid: synthesis and characterization, J. Polym. Res., 2014, 21, 1–10 CAS.
- A. Hofland, Alkyd resins: From down and out to alive and kicking, Prog. Org. Coat., 2012, 73(4), 274–282 CrossRef CAS.
- F. Chardon, M. Denis, C. Negrell and S. Caillol, Hybrid alkyds, the glowing route to reach cutting-edge properties?, Prog. Org. Coat., 2021, 151, 106025 CrossRef CAS.
- P. P. Chiplunkar and A. P. Pratap, Utilization of sunflower acid oil for synthesis of alkyd resin, Prog. Org. Coat., 2016, 93, 61–67 CrossRef CAS.
- M. Denis, C. Totee, D. Le Borgne, S. Caillol and C. Negrell, Cardanol-modified alkyd resins: novel route to make greener alkyd coatings, Prog. Org. Coat., 2022, 172, 107087 CrossRef CAS.
- A. Vallin, F. Ferretti, P. Campaner, O. Monticelli and A. Pellis, Environmentally Friendly Synthesis of Cardanol-Based Polyesters and Their Application as Poly (lactic acid) Additives, ACS Sustainable Chem. Eng., 2023, 11(26), 9654–9661 CrossRef CAS.
- H. Lim and S. W. Hoag, Plasticizer effects on physical–mechanical properties of solvent cast Soluplus® films, AAPS PharmSciTech, 2013, 14, 903–910 CrossRef CAS.
- A. S. More, S. K. Pasale, P. N. Honkhambe and P. P. Wadgaonkar, Synthesis and characterization of organo–soluble poly (ether ether ketone) s and poly (ether ether ketone ketone) s containing pendant pentadecyl chains, J. Appl. Polym. Sci., 2011, 121(6), 3689–3695 CrossRef CAS.
- B. V. Tawade, S. V. Shaligram, N. G. Valsange, U. K. Kharul and P. P. Wadgaonkar, Synthesis and properties of poly (arylene ether) s based on 3-pentadecyl 4, 4′–biphenol, Polym. Int., 2016, 65(5), 567–576 CrossRef CAS.
- H. Halliday, Surfactants: past, present and future, J. Perinatol., 2008, 28(1), S47–S56 CrossRef CAS.
-
J.-L. Salager, Surfactants types and uses, in FIRP booklet, 2002, vol. 300 Search PubMed.
- K. Holmberg, Natural surfactants, Curr. Opin. Colloid Interface Sci., 2001, 6(2), 148–159 CrossRef CAS.
- Y.-Y. Luk and N. L. Abbott, Applications of functional surfactants, Curr. Opin. Colloid Interface Sci., 2002, 7(5–6), 267–275 CrossRef CAS.
- S. M. Shaban, J. Kang and D.-H. Kim, Surfactants: Recent advances and their applications, Compos. Commun., 2020, 22, 100537 CrossRef.
- E. Gueit, E. Darque-Ceretti, P. Tintillier and M. Horgnies, Influence de tensioactifs sur l’hydratation du ciment à l’interface béton/coffrage, Matériaux, 2010, 2010 Search PubMed.
-
A. Tarafdar, T. Joseph and V. V. Sathe, Cement composition containing a substituted ethoxylated phenol surfactant for use in an oil-contaminated well, US 2012/0024527 A1, 2012.
- C. Chapelle, G. David, S. Caillol, C. Negrell, G. Durand and M. D. le Foll, Functionalization of Chitosan Oligomers: From Aliphatic Epoxide to Cardanol-Grafted Oligomers for Oil-in-Water Emulsions, Biomacromolecules, 2021, 22(2), 846–854 CrossRef CAS.
-
C. Chapelle, M. Desroches Le Foll, G. Durand, G. David, C. Negrell, S. Caillol and I. Faye, Oligomère biosourcé issu du chitosan et son utilisation comme émulsifiant cationique ou non ionique d’émulsion aqueuse de liants bitumineux ou non bitumineux, FR3098218 A1, 2020 Search PubMed.
-
G. L. Hart and A. F. Ahmed, Cleaning compositions containing ethoxylated cardanol, WO1992021741 A1, 1992 Search PubMed.
-
L. Wang, X. Zhao, F. Che, J. Zhang, W. Kang and Z. Huang, et al., Detergent containing cardanol polyoxyethylene ether and preparation method and application of detergent, 2018 Search PubMed.
-
L. Wang, Y. Gong, F. Che, M. Zhang, P. Yang and J. Zhang, Cardanol polyoxyethylene ether as well as preparation method and application thereof, CN112029087A, 2020 Search PubMed.
-
G. Jin, J. Zhu and F. Li, Novel nonionic surfactant, compounding method and application thereof, CN111203150A, 2016 Search PubMed.
-
G. Jin, J. Zhu and F. Li, A kind of nonionic surfactant, synthetic method and its application, 2016 Search PubMed.
- X. Zhao, J. Lv, L. Wang and J. Han, Novel hydroxylated cardanol quaternary ammonium salts from renewable resource and its synergistic vesicles of binary and ternary composite system in detergent, J. Surfactants Deterg., 2021, 24(1), 15–33 CrossRef CAS.
- A. M. Atta, M. M. Abdullah, H. A. Al-Lohedan and A. O. Ezzat, Demulsification of heavy crude oil using new nonionic cardanol surfactants, J. Mol. Liq., 2018, 252, 311–320 CrossRef CAS.
- A. O. Ezzat, A. M. Atta, H. A. Al-Lohedan, M. M. Abdullah and A. I. Hashem, Synthesis and application of poly (ionic liquid) based on cardanol as demulsifier for heavy crude oil water emulsions, Energy Fuels, 2018, 32(1), 214–225 CrossRef CAS.
- Y. S. Prasad, S. Miryala, K. Lalitha, K. Ranjitha, S. Barbhaiwala and V. Sridharan,
et al., Disassembly of bacterial biofilms by the self-assembled glycolipids derived from renewable resources, ACS Appl. Mater. Interfaces, 2017, 9(46), 40047–40058 CrossRef CAS.
- F. C. F. de França, E. d. L. Coelho, A. F. J. Uchôa, F. H. A. Rodrigues, M. E. N. P. Ribeiro, S. d. A. Soares and N. M. P. S. Ricardo, Síntese E Caracterização De surfactantes alquilfenil poliglicosídicos a partir da amilose e alquil fenóis extraídos do lcc natural, Quim. Nova, 2016, 39(7), 771–781 Search PubMed.
- J. H. P. Tyman and I. E. Bruce, Synthesis and characterization of polyethoxylate surfactants derived from phenolic lipids, J. Surfactants Deterg., 2003, 6(4), 291–297 CrossRef CAS.
- J. H. P. Tyman and I. E. Bruce, Surfactant properties and biodegradation of polyethoxylates from phenolic lipids, J. Surfactants Deterg., 2004, 7(2), 169–173 CrossRef CAS.
-
X. Li, L. Guoji, Z. Juan, L. Tingliang and S. Xiaobo, Cashew base nonionic surfactant and preparation method of cashew base nonionic surfactant, CN109158050A, 2012 Search PubMed.
- M. C. Subash, S. Karthikumar, S. N. Begum and C. Manjula, Optimization Studies on Decolourization of Non-Edible Cashew Oil for Industrial Application, Cleaner Circ. Bioecon., 2022, 1, 100006 CrossRef.
|
This journal is © The Royal Society of Chemistry 2024 |
Click here to see how this site uses Cookies. View our privacy policy here.