DOI:
10.1039/D3RA08238E
(Paper)
RSC Adv., 2024,
14, 4853-4860
A green extraction process for the selective recovery of Sc(III) based on hydrophobic betaine derivative ionic liquids†
Received
2nd December 2023
, Accepted 23rd January 2024
First published on 6th February 2024
Abstract
The efficient extraction recovery of scandium (Sc(III)) is crucial for its application in high-end technology. Two novel hydrophobic carboxylic acid ionic liquids (ILs), namely, [lauryl betaine][bis(trifluoromethanesulphonyl)imide] ([Laur][Tf2N]) and [cocamidopropyl betaine][bis(trifluoromethanesulphonyl)imide] ([Coca][Tf2N]), were synthesized using two inexpensive amphoteric surfactants as cation sources. [Laur][Tf2N] (257 °C) and [Coca][Tf2N] (251 °C) exhibited good thermal stability and strong hydrophobicity. The viscosity of [Coca][Tf2N] (4.29 × 103 mP s) was higher than that of [Laur][Tf2N] (2.55 × 103 mPa s) at 25 °C. The optimal extraction conditions were an extraction equilibrium time of 40 min, an initial Sc(III) concentration of 0.001 mol L−1, a sodium nitrate concentration of 0.5 mol L−1, and a pH of 3. The extraction efficiency of [Laur][Tf2N] and [Coca][Tf2N] could even exceed 98.7% and 96.0%, respectively. The cation exchange extraction mechanism was studied by slope analysis, IR spectroscopy and 13C NMR spectroscopy. Sc(III) extracted using [Laur][Tf2N] and [Coca][Tf2N] could be completely stripped with 0.1 mol L−1 and 0.2 mol L−1 HNO3 once, respectively. The structure of the ILs was not broken after stripping, and the extraction efficiency of the ILs remained almost unchanged after five cycles. In addition, the extraction differences at different pH levels made it possible to separate Sc(III) from other rare earths using ionic liquids [Laur][Tf2N] and [Coca][Tf2N].
Introduction
Scandium (Sc) metal and its compounds have excellent chemical and mechanical properties and are widely used in energy storage, aerospace, electronic devices, medicines, materials, chemical industries etc.1,2 Sc was listed as a mining strategic asset by China in 2016 and was subsequently listed as a critical mineral by the European Union and the United States.3–6 Because Sc is associated with other minerals, its recovery process is complex, inefficient, and expensive, which hampers its further development in high-end technology. Based on the above-mentioned reasons, the development of a green and efficient recovery system for Sc(III) (stable oxidation state in aqueous solution) is crucial.7,8
Compared with the other methods for recovering Sc(III) from its acid leachate,9–13 liquid–liquid extraction is one of the most simple and effective recovery methods.14–16 The commonly used traditional extractants are acidic or neutral organic phosphorus, carboxylic acids, and basic amines in organic diluents.17,18 Nevertheless, the use of volatile organic solvents (sulfonated kerosene, n-heptane, chloroform, etc.) in liquid–liquid extraction is harmful to the environment.19 To avoid danger, ionic liquids (ILs, typically containing organic cations, and inorganic or organic anions) with low vapor pressure and good thermal stability have been developed in the liquid–liquid extraction process.20,21 Efforts have been made to explore the extraction of Sc(III) and other rare earth elements using ILs. Nakashima et al. demonstrated that imidazole-based IL solvents and the extractant CMPO exhibited better extraction ability and selectivity for lanthanide ions than the conventional organic solvents.22 Sun et al. found that the separation factor and distribution ratio of Sc(III) in the Cyanex925-[A336][NO3] system were higher than that in the Cyanex925-[C8mim][PF6] system.23 A series of bifunctional ILs based on A336 and a phosphate/carboxylic acid extractant were synthesized, and [A336][P204] had a higher extraction efficiency than that of A336 and P204 due to the internal synergistic effects.24,25
In general, besides their use as diluents, ILs are used as extractants. Organic diluents are always used in the IL extractant systems due to the viscosity limitation, which goes against the original intention of ILs being “green”.26 Feasible strategies have been discussed in previous studies, for example, designing and synthesizing ILs with shorter alkyl chains. Zhang et al. synthesized two carboxylic acid-functionalized ILs, N-carboxymethylpyridinium bis(trifluoromethylsulfonyl)imide ([HbetPy][Tf2N]) and N-carboxymethyl-N-methylmorpholinium bis(trifluoromethylsulfonyl)imide ([HbetMor][Tf2N]), towards homogeneous liquid–liquid extraction and separation of Sc(III).27 Depuydt et al. reported a carboxyl-functionalized phosphonium IL [P444C1COOH]Cl for Sc(III) extraction in an aqueous biphasic system.28 Onghena et al. used betainium bis(trifluoromethylsulfonyl)imide ([Hbet][Tf2N]) for the extraction of Sc(III) from sulfation-roasted leachate.29 The results of the above-mentioned studies indicate that these carboxylic acid functional ILs without long alkyl chains have a higher mass transfer speed and less extraction equilibrium time, but the dissolution loss of ILs in the aqueous phase is quite high. For example, the solubility of [Hbet][Tf2N] reaches 14 wt% in the aqueous phase at room temperature, which is unfavourable for the environment and IL circulation.19 ILs with long alkyl chains have also been used in direct liquid–liquid extraction without diluents, which requires a simple operation, i.e., elevating extraction temperatures or presaturating ILs with water to reduce the viscosity.26,30,31
Lithium bis(trifluoromethanesulphonyl)imide has often been used as an anion source for ILs due to its hydrophobicity and low viscosity. However, anion exchange during the extraction process could cause loss, thereby disrupting the recyclability of ILs, which is environmentally unfriendly and uneconomical.32,33 For avoiding/reducing the loss, two new and efficient IL extraction systems were developed, and the systems were used to recycle Sc(III) in this work. Cocamidopropyl betaine and lauryl betaine are amphoteric surfactants, which are important raw materials for daily chemical products such as shampoo, shower gel, and hand sanitizer.34,35 Herein, two novel hydrophobic ILs, namely, [cocamidopropyl betaine][bis(trifluoromethanesulphonyl)imide] ([Coca][Tf2N]) and [lauryl betaine][bis(trifluoromethanesulphonyl)imide] ([Laur][Tf2N]), were synthesized using the two betaine-based substances as cation sources and lithium bis(trifluoromethanesulphonyl)imide as an anion source by a simple method in an aqueous solution, and their extraction performance towards Sc(III) without adding organic diluents was explored. The loss of [Tf2N]− during the extraction process was investigated by mechanism research. The factors that influence extraction, selectivity, and recovery efficiency were explored. The effects of amide groups and alkyl chain length on the performance of ILs are discussed.
Experimental
Materials and reagents
Cocamidopropyl betaine (35% w/w water solution), lauryl betaine (30% w/w in water), lithium bis(trifluoromethanesulphonyl)imide (≥98%), and scandium(III) nitrate hydrate (99.99%) were purchased from Adamas Reagent Co., Ltd, China. Sodium hydroxide (≥96%) was obtained from Zhengzhou Pine Chemical Reagent Factory. Sodium nitrate (98%) was obtained from Tianjin Damao Chemical Reagent Factory. Nitric acid (65–68%) was purchased from Luoyang Chemical Reagent Factory. An ethylenediaminetetraacetic acid disodium salt (EDTA) standard solution (0.05 mol L−1) was purchased from Shanghai Titan Technology Co., Ltd. Xylenol orange was obtained from Tixi Ai (Shanghai) Huacheng Industrial Development Co., Ltd. All chemicals were used as received without further purification. Individual RE (La and Lu) stock solutions were prepared by dissolving the corresponding oxides (99.99%, purchased from Adamas Reagent Co., Ltd, China.) with nitric acid and then diluting them with deionized water.
Instrumentation and analysis methods
Viscosities of the ILs were determined using a touch intelligent viscometer NTV-79P (Shanghai Nirun Intelligent Technology Co., Ltd.). Thermogravimetric analysis (TGA) was carried out using a TGA/DSC simultaneous thermal analyzer Q600 (TA Instruments, USA.) at a heating rate of 10 °C min−1. The concentrations of multiple or trace amounts of metal ions in the aqueous phase were determined using an inductively coupled plasma optical emission spectrometer (ICP-OES, Agilent, Inc.). The concentration of metal ions in other aqueous phases was determined by EDTA titration. 1H and 13C nuclear magnetic resonance (NMR) spectra of ILs were recorded in dimethylsulfoxide-d6 (DMSO-d6, C2D6OS) using an AV III HD-400 Bruker (Germany) spectrometer. IR spectra were recorded using a Tensor 37 Fourier transform infrared spectrometer (Bruker, Germany). The pH was measured using a PHS-25 digital pH meter (Shanghai Rex Instruments Factory).
Synthesis of ILs
ILs were prepared by mixing a 35% w/w cocamidopropyl betaine water solution (17.8191 g)/30% w/w lauryl betaine water solution (18.4197 g) with a 15% w/w lithium bis(trifluoromethanesulphonyl)imide (19.1393 g) water solution in a 100 mL round-bottom flask. After stirring at room temperature for 1 h, 1 mol L−1 of HCl solution was added dropwise to the above-mentioned mixed solution until the pH of the solution no longer changed. Stirring was continued for another 1 h to make the reaction more sufficient. The solution was allowed to stand at room temperature until the ionic liquid completely separated from the aqueous phase. The aqueous phase was discarded and the ionic liquid was washed several times with distilled water until there was no Cl− (a AgNO3 solution was used as the detection reagent). The product was dried at 75 °C under vacuum for 12 h to obtain the target ILs. The structures of the two ILs are shown in Fig. 1, and the 1H NMR and 13C NMR characterization data are as follows (the corresponding spectra are shown in Fig. S1–S4†):
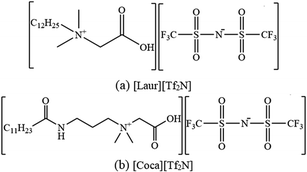 |
| Fig. 1 Structures of the ILs: (a) [Laur][Tf2N] and (b) [Coca][Tf2N]. | |
[Coca][Tf2N]: A light yellow viscous liquid with a yield of 96.31%. 1H NMR (400 MHz, DMSO-d6) δ 0.86 (t, 3H, CH3), 1.26–3.08 (m, 24H, 12CH2), 3.16 (s, 6H, 2N+CH3), 3.45 (m, 2H, NCH2), 4.22 (s, 2H, O
CCH2), 7.93 (t, 1H, NH). 13C NMR (400 MHz, DMSO-d6) δ 14.35, 22.55–42.71, 51.25, 61.42, 62.74, 115.15–124.74, 166.72, 172.84.
[Laur][Tf2N]: A colourless, transparent and viscous liquid with a yield of 98.57%. 1H NMR (400 MHz, DMSO-d6) δ 0.86 (t, 3H, CH3), 1.25–1.63 (m, 20H, 10CH2), 3.15 (s, 6H, 2N+CH3), 3.42 (m, 2H, N+CH2), 4.13 (s, 2H, O
CCH2). 13C NMR (400 MHz, DMSO-d6) δ 14.39, 22.22–42.52, 51.04, 61.81, 64.37, 118.35–121.55, 166.7.
Extraction and stripping procedures for Sc(III)
The extraction process involved placing the water-saturated ILs (organic phase) and aqueous phase in a 15 mL centrifuge tube and shaking them in an oscillator at 25 °C for a certain time. The centrifuge was used for phase separation at 5000 rpm for 5 min. The stripping experiments were carried out by mixing the loaded ionic liquid with different concentrations of the stripping agent (5 mL) in an oscillator at 25 °C for 40 min. The organic phase and aqueous phase after stripping experiments were separated during the extraction process. Extraction efficiency (E%), distribution ratio (D), separation factor (β), and stripping percentage (S%) were used as indicators of the efficiency of extraction and stripping, which can be calculated as follows (eqn (1)–(4)): |
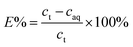 | (1) |
|
 | (2) |
|
 | (3) |
|
 | (4) |
where the volume of the aqueous phase is expected to remain unchanged after extraction and stripping. The calculation of D and β ignores the difference between the volume of ILs and the volume of aqueous phases. ct and caq (mol L−1) represent the initial (the total) and final concentrations of metal ions in the aqueous solution, respectively. cs is the final concentration of metal ions after the stripping process. DM1 and DM2 are the distribution ratios of metal 1 and metal 2, respectively.
Results and discussion
Thermal stability and viscosity of ILs
Thermal stability is crucial to the extraction of metals using ILs. The thermal stability of the ILs was analysed by the TGA decomposition inflection point. The thermal-degradation of [Laur][Tf2N] and [Coca][Tf2N] begins at temperatures of 257 °C and 251 °C (Fig. 2), which can work well for their extraction and stripping processes. The water content of the water-saturated ILs can be measured by holding at 120 °C for 1 h during the thermal analysis process.36 The water content of [Laur][Tf2N] and [Coca][Tf2N] was 1.80% and 4.09%, respectively (Fig. 2), indicating that the presence of amide groups could increase the water content of ILs even if the length of the alkyl chain increases.
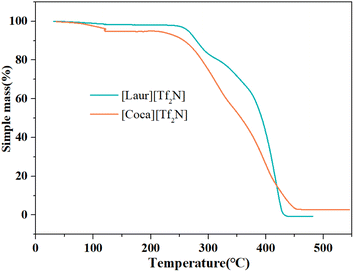 |
| Fig. 2 TGA curves of water-saturated [Laur][Tf2N] and [Coca][Tf2N]. | |
Viscosity is a significant factor that has impacts on IL extraction for metals.37 Fig. 3 shows that the viscosities of water-saturated [Laur][Tf2N] and [Coca][Tf2N] gradually decrease with the increase in temperature. All absolute values of Pearson's r were greater than 0.8, indicating a highly negative correlation between viscosity and temperature within the tested temperature range. The slope values indicate that the temperature has a greater impact on the viscosity of [Coca][Tf2N] than on the viscosity of [Laur][Tf2N], and the influence is more significant when the temperature is below 35 °C for both the ILs. At the selected extraction temperature (25 °C), the viscosity of [Laur][Tf2N] is 2.55 × 103 mPa s, while the viscosity of [Coca][Tf2N] is 4.29 × 103 mP s due to the increase in alkyl chain length. The higher viscosity of [Coca][Tf2N] will be detrimental to the extraction of Sc(III), which has been proved in the section “Effects of extraction conditions on Sc(III) recovery”.
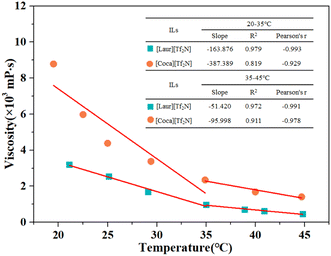 |
| Fig. 3 Viscosity changes and correlation of water-saturated [Laur][Tf2N] and [Coca][Tf2N] with the increase in temperature. | |
Effects of the extraction conditions on Sc(III) recovery
To optimize the recovery strategy, the extraction conditions (time, initial metal ion concentration, salting-out agent, and acidity) were explored. The extraction equilibrium time of both ILs is 40 min, and the Sc(III) extraction efficiency of [Laur][Tf2N] is higher than that of [Coca][Tf2N] at low 20 min (Fig. 4(a)). To explore the optimal dosage ratio of two ILs to Sc(III), the concentration of Sc(III) was varied from 0.001 mol L−1 to 0.015 mol L−1. The optimal operating concentration was 0.001 mol L−1, and the extraction efficiency reached 98.7% ([Laur][Tf2N]) and 96.0% ([Coca][Tf2N]) (Fig. 4(b)), respectively. It is worth mentioning that the extraction efficiency of two ILs could reach 100% with the increase in the ratio of ILs to Sc(III), as proved by the ratio of ILs to Sc(III) in the section “Extraction mechanism”. Herein, 0.005 mol L−1 Sc(III) was chosen for subsequent research to minimize the error in the titration process. Fig. 4(c) shows the effect of the initial salting out agent (NaNO3) concentration on Sc(III) extraction. A minor impact of NaNO3 concentration on the Sc(III) extraction efficiency of [Laur][Tf2N] was found, and there was a certain degree of improvement in the Sc(III) extraction efficiency of [Coca][Tf2N] at 0.1–0.5 mol L−1. Due to the competition between protons and metal ions for interaction with extractants, the pH has a remarkable influence on the extraction efficiency. As shown in Fig. 4(d), the Sc(III) extraction efficiency increases significantly between the pH values of 2 and 3, and the increasing trend becomes gentle after pH 3. For the recovery system of Sc(III) from its acid leachate, the economic benefits obtained from a slight increase in the extraction efficiency in a high pH environment need to be further measured compared with the amount of alkali consumed to increase the pH. A pH of 3 was used in subsequent research based on the above-mentioned analysis. To sum up, the preferred extraction conditions are an extraction equilibrium time of 40 minutes, an initial Sc(III) concentration of 0.001 mol L−1, a NaNO3 concentration of 0.5 mol L−1 and a pH of 3.
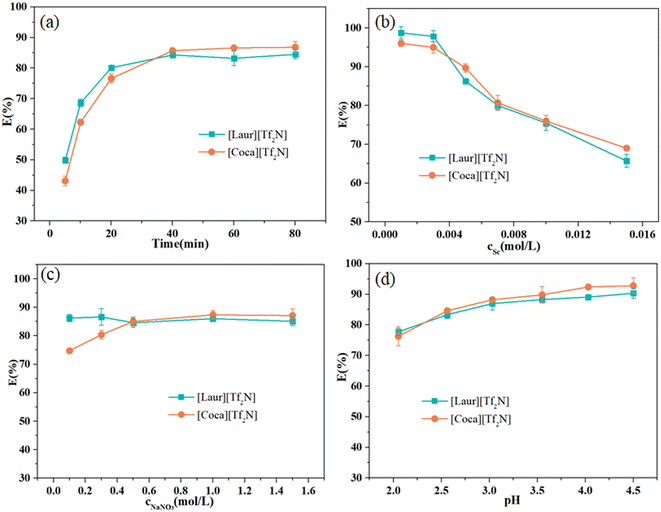 |
| Fig. 4 Effects of (a) time, (b) initial metal concentration, (c) salting-out concentration, and (d) acidity on Sc(III) extraction. Aqueous phase: Vaq = 5 mL, equilibration time = 40 min, cSc = 0.005 mol L−1, cNaNO3 = 0.5 mol L−1, pH = 3. Organic phase: m[Laur][Tf2N] = 0.0816 g, m[Coca][Tf2N] = 0.0921 g. (a) Equilibration time = 5–80 min, (b) cSc = 0.001–0.015 mol L−1, (c) cNaNO3 = 0.1–1.5 mol L−1, and (d) pH = 2–4.5. | |
Extraction mechanism
Ion exchange, salvation, ion association, etc. are possible mechanisms for ionic liquid extraction.38 The slope analysis method was used to explore how many protons need to be released to extract one equivalent of Sc(III). Organic diluents (Vsulfonated kerosene
:
Voctanol = 3.5
:
1.5) were used to ensure that the logD value met the definition. To reduce the effects of extraction reactions on the concentration of organic-phase extractants, the concentration of metal ions in the aqueous phase should be much lower than that of organic-phase extractants.
As can be seen in Fig. 5, the linear relationship between logD and pH is well fitted at pH = 0.57 to 1.63 for [Laur][Tf2N] and [Coca][Tf2N]. The slope of [Laur][Tf2N] is 3.12, which is similar to the previously reported coefficient for carboxylic acid extractants (the ratio is 3).28,39 In the [Coca][Tf2N] system, the slope is 2.05, which is different from that of simple carboxylic acid extractants. This difference may be due to the presence of amide groups, as proved by IR and 13C NMR spectra (Fig. 6).
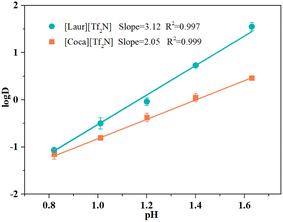 |
| Fig. 5 Plot of logD as a function of pH. Aqueous phase: Vaq = 5 mL, equilibration time = 40 min, cSc = 0.0008 mol L−1, cNaNO3 = 0.5 mol L−1, and pH = 0.82–1.63. Organic phase: Vo = 5 mL, m[Laur][Tf2N] = 0.1996 g, and m[Coca][Tf2N] = 0.1768 g. | |
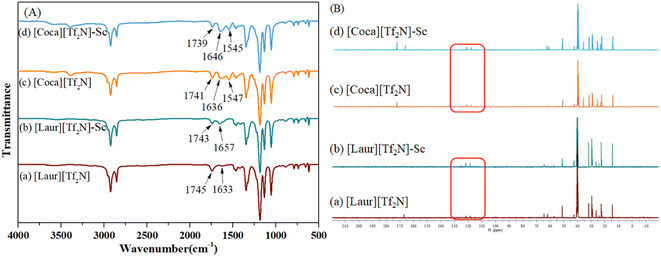 |
| Fig. 6 (A) IR and (B) 13C NMR spectra characterization of ILs before and after loading with Sc(III). | |
As shown in Fig. 6(A)(a) and (b), the peaks at 1745 cm−1 and 1743 cm−1 can be attributed to the stretching vibration of C
O in the carboxyl group, and the movement before and after extraction indicates that the carboxyl group plays a significant role in the [Laur][Tf2N] extraction process. The peaks at 1633 cm−1 and 1657 cm−1 are assigned to the stretching vibrations of S
O in [Tf2N]−, introducing that [Tf2N]− has not been lost and still participates in the extraction process. Compared with Fig. 6(A)(c) and (d), 1741 cm−1 and 1739 cm−1 can also be attributed to the stretching vibration of C
O in the carboxyl group, and the slight movement indicates that the carboxyl group also participates in the [Coca][Tf2N] extraction process. The peaks at 1636 cm−1 and 1646 cm−1 are the overlap of the stretching vibrations of the C
O group in amide and S
O in [Tf2N]−. The difference is not only due to the involvement of [Tf2N]− in the extraction process but also due to the interaction between amide C
O and Sc(III). The peaks at 1547 cm−1 and 1545 cm−1 are attributed to the bending vibrations of N–H, and the slight movement further confirms the involvement of the amide group in the extraction. As can be seen in Fig. 6(B), the quadruple absorption peak (within the red wireframe) is caused by the coupling splitting of fluorine atoms on trifluoromethyl with carbon. By comparing the positions of the two peaks in Fig. 6(B)(a) and (b), as well as Fig. 6(B)(c) and (d), we can observe that both trifluoromethyl carbon peaks exist before and after extraction, indicating that the highly soluble [Tf2N]− anion in the two ILs [Laur][Tf2N] and [Coca][Tf2N] has not been exchanged into the aqueous phase. Accordingly, the extraction mechanism equation of Sc(III) with [Laur][Tf2N] and [Coca][Tf2N] can be proposed by eqn (5) and (6) combining the charge balance.
|
Sc3+aq + 3[Laur][Tf2N]org ⇔ {Sc([Laur][Tf2N])3}org + 3H+aq
| (5) |
|
 | (6) |
Stripping and recycling of Sc(III)
The acidity of the aqueous phase affects the extraction efficiency of ILs for Sc(III), as well as the IL stripping performance. Different concentrations of HNO3 from 0.02 mol L−1 to 0.6 mol L−1 were used as stripping agents. The Sc(III) stripping efficiency gradually increases for [Laur][Tf2N] and [Coca][Tf2N], as shown in Fig. 7. The 100% Sc(III) stripping efficiency for [Laur][Tf2N] and [Coca][Tf2N] can be achieved at 0.1 and 0.2 mol L−1 HNO3, respectively. Based on eqn (5) and (6), the high acidity condition is beneficial for the reverse reaction, resulting in Sc(III) entering the aqueous phase.
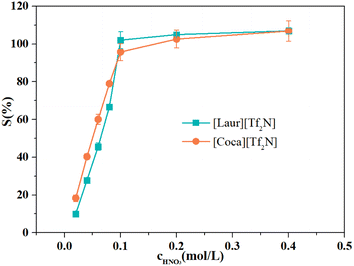 |
| Fig. 7 Stripping efficiency (S%) with different concentrations of HNO3. Extraction process: aqueous phase: Vaq = 5 mL, equilibration time = 40 min, cSc = 0.005 mol L−1, cNaNO3 = 0.5 mol L−1, and pH = 3. Organic phase: m[Laur][Tf2N] = 0.0816 g and m[Coca][Tf2N] = 0.0921 g. Stripping process: aqueous phase: Vaq = 5 mL and cHNO3 = 0.02–0.4 mol L−1. | |
Therefore, IR was used to analyse the changes in ILs before and after stripping, and the results are shown in Fig. 8. In Fig. 8(a) and (b), the characteristic absorption peaks at 1745 cm−1 (stretching vibration of C
O in the carboxyl group) and 1633 cm−1 (stretching vibrations of S
O in [Tf2N]−) are not changed. The peak at 1741 cm−1 ascribed to the stretching vibration of C
O in the carboxyl group, the peak at 1636 cm−1 ascribed to the overlap of the stretching vibrations of the C
O group in amide and S
O in [Tf2N]−, and the peak at 1547 cm−1 ascribed to the bending vibrations of N–H were also not changed (Fig. 8(c) and (d)). The above-mentioned phenomenon indicates that ILs are regenerated during the acid stripping process. The recycling performance of the regenerated ILs is explored in Fig. 9. The Sc(III) extraction efficiency of [Laur][Tf2N] and [Coca][Tf2N] remains almost unchanged after 5 cycles of extraction-stripping-extraction, which indicates that the two ILs have excellent recycling characteristics.
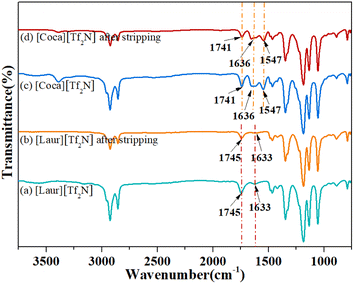 |
| Fig. 8 IR spectra of ILs and ILs after stripping with HNO3. | |
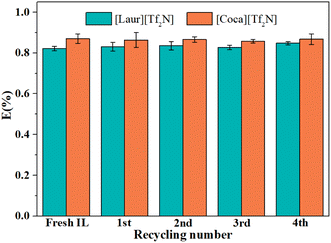 |
| Fig. 9 Sc(III) extraction efficiency (E%) with regenerated ILs. Extraction process: aqueous phase: Vaq = 5 mL, equilibration time = 40 min, cSc = 0.005 mol L−1, cNaNO3 = 0.5 mol L−1, and pH = 3. Organic phase: m[Laur][Tf2N] = 0.0816 g and m[Coca][Tf2N] = 0.0921 g. Stripping process: aqueous phase: Vaq = 5 mL, equilibration time = 40 min, and cHNO3 = 0.1 mol L−1 for [Laur][Tf2N] and 0.2 mol L−1 for [Coca][Tf2N]. | |
Selective separation of Sc(III) from La(III) and Lu(III)
Due to their similar physical and chemical properties, Sc usually coexists with other rare earth metals, so the separation of Sc from other rare earth metals is of great significance. Light rare earth La(III) and heavy rare earth Lu(III) were chosen as examples to investigate the separation effect of the two ILs on Sc(III) and other trivalent rare earth elements. Fig. 10 shows the extraction efficiency of different metals as a function of the aqueous phase pH (from 2 to 4.5) value. The Sc(III) extraction efficiency of [Laur][Tf2N] and [Coca][Tf2N] are 89.3% and 91.8%, respectively, at pH = 4.5. However, the extraction efficiency of [Laur][Tf2N] and [Coca][Tf2N] for both Lu(III) and La(III) are lower than 20%, and no concentration changes of La(III) are detected in the aqueous phase before and after the extraction at pH 2 with [Laur][Tf2N]. Table 1 provides the separation factor (β) between metals with [Laur][Tf2N] and [Coca][Tf2N]. The metal separation factor with [Laur][Tf2N] is higher at low pH, βSc/Lu reaches a maximum value (238), whereas βSc/La is too high to be measured. The metal separation coefficient of [Coca][Tf2N] reaches its maximum value at pH 4, where βSc/La is 61.25 and βSc/Lu is 57.86. These values are much higher than those reported in the latest work of Kaim-Sevalneva et al. βSc/Lu is 17 for [N444 MeOAc][Tf2N] at pH 4.5,40 while close to those reported in the related studies by Sun et al. βSc/La reaches 172.79 at pH 3 in the Cyanex925-[A336][NO3] system.23 The pretty selectivity towards Sc(III) in these systems is mainly due to its smaller ion radius and larger charge density than those of La(III) and Lu(III), which allows it to form more stable complexes via interaction with ILs at lower pH of the aqueous phase.19,41 The above-mentioned results indicate that Sc(III) can be well extracted from La(III) and Lu(III) within the tested pH range.
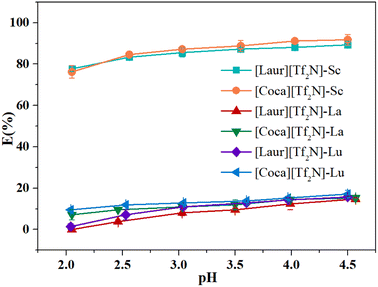 |
| Fig. 10 Extraction efficiency (E%) of metal ions by ILs at different pH values of the aqueous phase. Aqueous phase: Vaq = 5 mL, equilibration time = 40 min, cSc = cLa = cLu = 0.005 mol L−1, cNaNO3 = 0.5 mol L−1, and pH = 3. Organic phase: m[Laur][Tf2N] = 0.0816 g and m[Coca][Tf2N] = 0.0921 g. | |
Table 1 Separation factor (β) between metals with [Laur][Tf2N] and [Coca][Tf2N]
β |
pH |
2.0 |
2.5 |
3.0 |
3.5 |
4.0 |
4.5 |
No concentration of La(III) changes were detected in the aqueous phase before and after extraction. |
[Laur][Tf2N] |
βSc/La |
—a |
126 |
67.0 |
65.3 |
52.0 |
47.1 |
βSc/Lu |
238 |
64.5 |
48.0 |
46.7 |
44.4 |
43.8 |
[Coca][Tf2N] |
βSc/La |
41.4 |
52.3 |
55.4 |
58.4 |
61.3 |
60.7 |
βSc/Lu |
30.5 |
40.7 |
46.3 |
49.5 |
57.9 |
52.6 |
Conclusions
Two novel hydrophobic carboxylic acid ILs, ([Laur][Tf2N] and [Coca][Tf2N]), were successfully synthesized using a simple method in an aqueous solution. The Sc(III) extraction efficiency of [Laur][Tf2N] and [Coca][Tf2N] could even exceed 98.7% and 96.0%, respectively under the optimal extraction conditions (40 min, 0.001 mol L−1 Sc(III), 0.5 mol L−1 NaNO3, and pH 3). The mechanism of extracting Sc(III) using the two ILs was cation exchange based on the results of slope analysis, IR spectroscopy, and 13C NMR spectroscopy. In the [Coca][Tf2N]-based extraction system, the carboxyl and amide groups participated in coordination. Only the carboxyl group participated in the coordination in the [Laur][Tf2N]-based extraction system. The Sc(III) stripping efficiency could reach 100% using nitric acid (0.1 mol L−1 for [Laur][Tf2N] and 0.2 mol L−1 for [Coca][Tf2N]), and the structure of the two ILs remained unchanged before extraction and after stripping. After five cycles, the two ILs maintained a constant extraction efficiency. [Tf2N]− was not transferred into the aqueous phase during the extraction process, demonstrating its environmental friendliness. The presence of an amide group and a longer alkyl chain length in [Coca][Tf2N] reduced both βSc/La and βSc/Lu. Interestingly, βSc/La and βSc/Lu of [Laur][Tf2N] could reach 126 and 238, respectively, or even higher, which provides potential possibilities for the extraction separation of Sc(III) from other rare earth metals. We believe that this investigation could provide a valuable reference for the design and synthesis of efficient and green IL extractants in the future.
Conflicts of interest
There are no conflicts to declare.
Acknowledgements
This work was financially supported by the Doctoral Research Start-up Project of Pingdingshan University (PXY-BSQD-202104 and PXY-BSQD-2023046), the project of Development and Optimization of a New Rare Earth Recycling Agent and Recycling Process (PXY-HX-2022093, supported by Hunan Zhongci New Material Technology Co., Ltd.).
Notes and references
- D. Avdibegović, M. Regadío and K. Binnemans, RSC Adv., 2017, 7, 49664–49674 RSC.
- A. B. Botelho Jr., D. C. R. Espinosa, J. Vaughan and J. A. S. Tenorio, Miner. Eng., 2021, 172, 107148 CrossRef.
- A. D. Salman, T. Juzsakova, S. Mohsen, T. A. Abdullah, P. C. Le, V. Sebestyen, B. Sluser and I. Cretescu, Materials, 2022, 15, 2376 CrossRef CAS PubMed.
- A. Akcil, N. Akhmadiyeva, R. A. Abhilash and P. Meshram, Miner. Process. Extr. Metall. Rev., 2018, 39, 145–151 CrossRef CAS.
- S. M. Fortier, N. T. Nassar, G. W. Lederer, J. Brainard, J. Gambogi and E. A. McCullough, Draft Critical Mineral List—Summary of Methodology and Background Information—U.S. Geological Survey Technical Input Document in Response to Secretarial Order No. 3359, 2018 Search PubMed.
- L. Wang, P. Wang, W. Q. Chen, Q. Q. Wang and H. S. Lu, J. Cleaner Prod., 2020, 270, 122464 CrossRef CAS.
- N. Zhang, H. X. Li and X. M. Liu, Rare Met., 2016, 12, 887–900 CrossRef.
- E. Kalkane, Eng. Geol., 2006, 3, 220–229 CrossRef.
- I. V. Burakova, A. Burakov, A. G. Tkachev and I. Troshkina, J. Mol. Liq., 2018, 253, 277–283 CrossRef CAS.
- J. Roosen, S. Van Roosendael, C. R. Borra, T. Van Gerven, S. Mullens and K. Binnemans, Green Chem., 2016, 18, 2005–2013 RSC.
- X. Zhu, W. Li, S. Tang, M. Zeng, P. Bai and L. Chen, Chemosphere, 2017, 175, 365–372 CrossRef CAS PubMed.
- W. Z. Zhang, R. Koivula, E. Wiikinkoski, J. H. Xu, S. Hietala, J. Lehto and R. Harjula, ACS Sustainable Chem. Eng., 2017, 5, 3103–3114 CrossRef CAS.
- P. K. Parhi, S. S. Behera, R. K. Mohapatra, T. R. Sahoo, D. Das and P. K. Misra, Sep. Sci. Technol., 2019, 54, 1478–1488 CrossRef CAS.
- B. Onghena, C. R. Borra, T. V. Gerven and K. Binnemans, Sep. Purif. Technol., 2017, 176, 208–219 CrossRef CAS.
- J. S. Hu, D. Zou, J. Chen and D. Q. Li, Sep. Purif. Technol., 2020, 233, 115977 CrossRef CAS.
- Y. D. Chen, S. Y. Ma, S. Y. Ning, Y. L. Zhong, X. P. Wang, T. Fujita and Y. Z. Wei, J. Environ. Chem. Eng., 2021, 9, 106226 CrossRef CAS.
- S. Das, S. S. Behera, B. M. Murmu, R. K. Mohapatra, D. Mandal, R. Samantray, P. K. Parhi and G. Senanayake, Sep. Purif. Technol., 2018, 202, 248–258 CrossRef CAS.
- W. Wang and C. Y. Cheng, J. Chem. Technol. Biotechnol., 2011, 86, 1237–1246 CrossRef CAS.
- Y. H. Chen, H. Y. Wang, Y. C. Pei and J. J. Wang, Sep. Purif. Technol., 2017, 178, 261–268 CrossRef CAS.
- T. Makanyire, S. Sanchez-Segado and A. Jha, Adv. Manuf., 2016, 4, 33–46 CrossRef CAS.
- H. Luo, S. Dai and P. V. Bonnesen, Anal. Chem., 2004, 76, 2773–2779 CrossRef CAS PubMed.
- K. Nakashima, F. Kubota, T. Maruyama and M. Goto, Anal. Sci., 2003, 19, 1097–1098 CrossRef CAS PubMed.
- X. Q. Sun, Y. Ji, L. Guo, J. Chen and D. Q. Li, Sep. Purif. Technol., 2011, 81, 25–30 CrossRef CAS.
- X. Q. Sun, Y. Ji, Y. Liu, J. Chen and D. Q. Li, AIChE J., 2010, 56, 989–996 CrossRef CAS.
- X. Q. Sun, Y. Ji, F. C. Hu, B. He, J. Chen and D. Q. Li, Talanta, 2010, 81, 1877–1883 CrossRef CAS PubMed.
- A. Rout and K. Binnemans, Phys. Chem. Chem. Phys., 2016, 18, 16039–16045 RSC.
- Y. Zhang, Y. Deng, W. D. Guo, D. H. Liu and Y. G. Ding, ACS Sustainable Chem. Eng., 2021, 9, 9932–9940 CrossRef CAS.
- D. Depuydt, W. Dehaen and K. Binnemans, Ind. Eng. Chem. Res., 2015, 54, 8988–8996 CrossRef CAS.
- B. Onghenaa, C. R. Borrab, T. Van Gervenb and K. Binnemans, Sep. Purif. Technol., 2017, 176, 208–219 CrossRef.
- R. Banda, F. Forte, B. Onghena and K. Binnemans, RSC Adv., 2019, 9, 4876–4883 RSC.
- T. Vander Hoogerstraete, S. Wellens, K. Verachtert and K. Binnemans, Green Chem., 2013, 15, 919–927 RSC.
- K. Y. Wang, H. Adidharma, M. Radosz, P. Y. Wan, X. Xu, C. K. Russellc, H. J. Tiand, M. H. Fan and J. Yu, Green Chem., 2017, 19, 4469–4493 RSC.
- M. P. Jensen, J. Neuefeind, J. V. Beitz, S. Skanthakumar and L. Soderholm, J. Am. Chem. Soc., 2003, 125, 15466–15473 CrossRef CAS PubMed.
- J. E. Hunter and J. F. Fowler Jr., J. Surfactants Deterg., 1998, 1, 235–239 CrossRef CAS.
- A. H. Syed, A. K. Idris, D. F. Mohshim, N. Yekeen and M. A. Buriro, J. Pet. Explor. Prod. Technol., 2019, 9, 2659–2665 CrossRef CAS.
- S. Raiguel, D. Depuydt, T. V. Hoogerstraete, J. Thomas, W. Dehaen and K. Binnemans, Dalton Trans., 2017, 46, 5269–5278 RSC.
- X. Su, Z. Y. Zhao and X. Q. Sun, Ind. Eng. Chem. Res., 2020, 59, 14075–14084 CrossRef CAS.
- Y. M. Dong, X. Q. Sun, Y. L. Wang, C. Huang and Z. Y. Zhao, ACS Sustain. Chem. Eng., 2016, 4, 1573–1580 CrossRef CAS.
- B. Onghena and K. Binnemans, Ind. Eng. Chem. Res., 2015, 54, 1887–1898 CrossRef CAS.
- V. Kaim-Sevalneva, E. Sariola-Leikas and C. He, Sep. Purif. Technol., 2024, 334, 126038 CrossRef CAS.
- J. S. Preston, Hydrometallurgy, 1985, 14, 171–188 CrossRef CAS.
|
This journal is © The Royal Society of Chemistry 2024 |
Click here to see how this site uses Cookies. View our privacy policy here.