DOI:
10.1039/D3RA08705K
(Paper)
RSC Adv., 2024,
14, 17296-17305
Fabrication and characterization of inorganic–organic hybrid copper ferrite anchored on chitosan Schiff base as a reusable green catalyst for the synthesis of indeno[1,2-b]indolone derivatives†
Received
20th December 2023
, Accepted 29th April 2024
First published on 29th May 2024
Abstract
This study presents a description of the catalytic synthesis of indeno[1,2-b]indolone derivatives. In this method, initially, a Schiff base compound was synthesized from the reaction of acetylacetone with 2-hydroxyaniline. Then, the prepared Schiff base was immobilized on chelated magnetic copper ferrite nanoparticles with a chitosan surface to design and prepare the CuFe2O4@CS-SB nanocomposite. Further, the one-pot multi-component cyclization reaction of aniline, dimedone and ninhydrin was conducted using the synthesized nanocomposite as a heterogeneous acid catalyst in water solvent under thermal conditions. In this reaction, the products were obtained in excellent yields and short reaction times, and the catalyst could be recycled and reused six times without any loss in product yields. By conducting FT-IR spectroscopy, 1H NMR spectroscopy, XRD, FE-SEM, TGA, elemental mapping scanning, EDX and BET analyses, the structure of the nanocatalyst was characterized. In addition, for the identification of organic compounds, FT-IR, 1H NMR, and 13C NMR spectroscopies and melting point analysis were used, which confirmed the synthesis of this class of derivatives.
1. Introduction
Indeno[1,2-b]indolones are a significant class of heterocyclic organic compounds that are used in biology and pharmacology.1,2 The most known simple heterocyclic compounds are pyridine, pyrrole, furan and thiophene.3 Heterocyclic compounds make up about sixty-five percent of organic chemistry, and they play a vital role in the metabolism of all living cells. A large number of heterocyclic compounds, both synthetic and natural, are pharmacologically active.4 Due to their ability to suppress lipid peroxidation, this class of pharmaceuticals has attracted a substantial amount of attention.5,6 Protein kinase inhibitors, in addition to being adenosine triphosphate/guanosine triphosphate-competitive inhibitors, are potassium channel openers and estrogenic drugs.7 Indeno[1,2-b]indolones occupy a special role in a few more non-cancer (diseases associated with angiogenesis, viral infections, inflammatory markers, and neurodegenerative disorders) and cancer ailments (such as prostate, colon, breast and lung cancers).8 In 2016, Liu and colleagues used lactic acid as a homogeneous catalyst to synthesize indeno[1,2-b]indolone compounds. The working method is abrasive and solvent-free, and it is done within 10 minutes at room temperature.9 In 2018, Safari and his co-worker used MMT@Fe3O4 as a heterogeneous catalyst and prepared derivatives of indeno[1,2-b]indolones in water as a solvent at 70 °C.2 In chemical reactions, the use of heterogeneous catalysts is very significant because of their solid form, which is in contrast to the homogeneous catalyst phase.10,11
Recently, a heterogeneous catalyst has been formed with purposeful design and preparation, which has active sites on its surface to enable it to bond to organic compounds to promote the reaction.12
Chitosan is a derivative of chitin and is a polysaccharide.13 It is a type of heteropolymer that is formed from the deacetylation of chitin and acetyl glucosamine groups though its deacetylation is incomplete.14 Stable activities of chitosan in the field of catalysis with magnetic separation capability and a copper ferrite nanocomposite made of chitosan have been reported.15 Chitosan is a substance that is environmentally friendly, and because of the increasing attention toward green chemistry, the use of this substance becomes important.16 Recently, it has been reported that chitosan may be used to inhibit fibroplasia in wound healing and promote tissue growth and differentiation.17 Chitosan can act as a catalytic substrate in many reactions, and it also dissolves in dilute acetic acid and activates its surface.18 The existence of interactions between metal and OH groups on the surface of chitosan has recently attracted increasing attention for the fabrication of complex materials.19 It is due to the presence of NH2 on the surface of chitosan that it allows copolymerization using monomers to achieve unique properties.20 Also, the reason for using magnetic nanoparticles in the synthesis of the catalyst can be attributed to their two general characteristics: effects that are limited to the size of their particles and effects that are superficial and cause special characteristics in magnetic nanoparticles.21
Schiff bases can act as ligands and bind on the chitosan substrate.22 A Schiff base can be formed by the reaction between an aldehyde or a ketone with a primary amine under various conditions.23 Organic compounds used as Schiff bases have attracted the attention of many scientists in various fields, including industry and pharmaceuticals.24 Also, these compounds have biological activities.25
In continuation of our ongoing research works on catalytic reactions,26–31 in this work, we chose to look into the straightforward and efficient synthesis of indeno[1,2-b]indolones utilizing a novel effective heterogeneous nanocatalyst. Initially, copper ferrite nanoparticles were prepared by the co-precipitation method; then, the magnetic nanoparticles of the CuFe2O4@CS-SB nanocomposite were prepared by chelating on the surface of chitosan and a Schiff base. This prepared nanocomposite had the ability to catalyze the one-pot, three-component reaction between ninhydrin, dimedone and aniline derivatives as a nano-solid acid.
2. Experimental section
2.1. Substances and apparatus
The chemicals and solvents used were of high quality from Merck, Fluka and Aldrich Chemical Companies without the need for further purification. FT-IR spectra were recorded using a PerkinElmer 550 spectrometer with KBr pellets in the range of 400–4000 cm−1 to observe the functional groups. Proton and carbon nuclear magnetic resonance spectroscopy was done with the internal reference in DMSO-d6 solvent to determine the structure of the products. The melting point is one of the important physical parameters that is checked for the purity of a given sample and compared with the existing literature, which was done using an Electrothermal Mk3 instrument in this study. The fabricated catalyst was characterized using ATR, XRD, FE-SEM, EDX, VSM, BET and TGA techniques. ATR technique uses the property of internal reflection in the sample along with infrared spectroscopy, where samples are provided in solid or liquid state without preparation. In this study, an iCE 3500 spectrometer made by Thermo Scientific Company was employed. Powder X-ray diffraction (XRD) is a rapid analytical technique for the characterization of the nanostructure, which was utilizing Cu wavelength (1.54 Å). FE-SEM analysis examined minor area contamination spots at 15 kV electron accelerating voltages with well-matched EDS results obtained from a ZEISS SIGMAVP apparatus. VSM was used as a specific device for the determination of the magnetic properties of the nanocatalyst by a PPMS-9 T device at 300 K. BET analysis was done to measure the specific surface area of the materials. TGA was carried out for the samples under controlled temperature conditions in an air atmosphere with a 10 °C min−1 heating rate via a METTLER-810 analyzer.
2.2. Procedure for synthesis of 4-(2-hydroxyaniline)pent-3-en-2-one
Schiff base was formed with an ethanolic solution of 5 mmol acetylacetone and an ethanolic solution of 5 mmol 2-aminophenol. The ethanolic solution obtained from the amine was added dropwise to the ketone ethanolic solution. Thereafter, the reaction mixture was refluxed at 80 °C for 6 h; after that, the reaction was checked by TLC until completion, following which yellow crystals were formed. They were washed with ethanol and diethylether, and the resulting product was obtained with a yield of 97%. ATR (cm−1): 3010, 2721, 2599, 1585, 1552, 1501, 1434, 1308, 1102, 745; 1H NMR (400 MHz, DMSO-d6) (ppm): 12.15 (s, 1H, NH), 9.91 (s, 1H, OH), 7.16 (d, J = 8.0 Hz, 1H), 7.02 (t, J = 4.0 Hz, 1H), 6.91 (d, J = 4.0 Hz, 1H), 6.79 (t, J = 8.0 Hz, 1H), 5.20 (s, 1H), 1.97 (s, 6H, 2 CH3).
2.3. Synthetic process of chitosan-Schiff base (CS-SB)
After dissolving 1.000 g of 4-(2-hydroxyaniline)pent-3-en-2-one in methanolic solution, 1.000 g of weighed chitosan was dissolved in methanol and glacial acetic acid (95
:
5 v/v). After 2 hours, the Schiff base solution was added drop by drop to the chitosan suspension. The reaction mixture was then refluxed for 24 h at 80 °C. After making sure that the reaction was completed, the reaction mixture was centrifuged (5000 rpm for 5 min) and washed several times with methanol and acetone. Soxhlet extraction (using methanol and acetone solvents for 24 h) was used to extract the interfering metals from chitosan. Then, the obtained product was dried in an oven at 60 °C for 24 h, yielding a brown powder that indicated the final synthetic product.
2.4. A procedure for the synthesis of magnetic CuFe2O4 NPs
5.406 g (20 mmol) of FeCl3·6H2O and 1.704 g (10 mmol) of CuCl2·2H2O were mixed together, then subjected to ultrasonic waves for 15 minutes, then stirred for 15 min at room temperature. Next, 3 M NaOH solution was added drop by drop to the obtained mixture until the pH was 13 and a precipitate was obtained. After reaching the desired pH, 3 drops of oleic acid were added to the reaction mixture as a surfactant and refluxed at 80 °C for 50 min. After cooling the reaction mixture, it was centrifuged (5000 rpm for 5 min), washed with deionized water and ethanol several times, and dried in an oven at 80 °C. In order to calcine the product, it was placed in a furnace at 800 °C for 10 h, and the CuFe2O4 NPs (nanoparticles) were formed.
2.5. General procedure for the synthesis of the CuFe2O4@CS-SB catalyst
0.500 g of CuFe2O4 NPs in 100 mL of deionized water was subjected to ultrasonic waves to disperse the nanoparticles in the solvent. 0.500 g of Schiff base-chitosan was added to the previous solution, and the suspension was stirred for 1 h at 50 °C. Then, 0.2 M NaOH solution was added drop by drop to the suspension to form a black precipitate. In the last step, 25% ammonia was added to the solution and the reaction was stirred for 30 minutes at the desired temperature. The product was centrifuged (5000 rpm for 5 min), washed several times with deionized water to neutralize, dried in an oven at 70 °C for 12 h, and stored in a desiccator for future usage (Fig. S1 in the ESI†).
2.6. General procedure for the synthesis of indeno[1,2-b]indolone
Exact amounts of aromatic amine (1 mmol), 1 mmol of dimedone and CuFe2O4@CS-SB catalyst (0.004 g) were stirred in distilled water at 75 °C. Subsequently, 1 mmol of ninhydrin was added and the reaction mixture was stirred again for a suitable time. The reaction progress was checked by thin layer chromatography (TLC), and the reaction mixture was filtered off after completion. With the aim of achieving the CuFe2O4@CS-SB catalyst from the products, the CuFe2O4@CS-SB catalyst was separated from the reaction mixture by a strong external magnet and washed several times with acetone and ethanol to be used as a catalyst in other reactions. Ultimately, the precipitate was washed by petroleum ether and recrystallized from ethanol, if required, to give the absolute target products. Every single product was confirmed by determining its melting point and applying spectroscopic methods such as FT-IR, 1H NMR and 13C NMR.
2.7. Spectroscopic and physical data for the synthesized indeno[1,2-b]indolone derivatives
2.7.1. 4b,9b-Dihydroxy-7,7-dimethyl-5-phenyl-4b,5,6,7,8,9b-hexahydroindeno[1,2-b]indole-9,10-dione (4a). White solid (93% yield); m.prep. = 260–265 °C (ethanol); m.plit. = 255–257 °C;2 IR (KBr) v (cm−1): 3475, 3232, 2931, 2876, 1723, 1606, 1547, 1452, 1277, 1159; 1H NMR (400 MHz, DMSO-d6) δ (ppm) = 7.72 (d, J = 4.0 Hz, 1H, ArH), 7.58–7.45 (m, 5H, ArH), 7.30 (s, 2H, ArH), 7.28 (s, 1H), 6.60 (d, J = 8.0 Hz, 1H, ArH), 6.01 (s, 1H), 2.41 (d, J = 16.0 Hz, 1H), 2.15 (d, J = 16.0 Hz, 1H), 1.91 (d, J = 16.0 Hz, 1H), 1.79 (d, J = 16.0 Hz, 1H), 0.96 (s, 3H, Me), 0.89 (s, 3H, Me).
2.7.2. 5-(4-Ethylphenyl)-4b,9b-dihydroxy-7,7-dimethyl-4b,5,6,7,8,9b-hexahydroindeno[1,2-b]indole-9,10-dione (4b). Light brown solid (92% yield); m.prep. = 145–150 °C (ethanol); IR (KBr) v (cm−1): 3398, 2956, 2876, 1724, 1610, 1551, 1156; 1H NMR (400 MHz, DMSO-d6) δ (ppm) = 7.72 (d, J = 4.0 Hz, 1H, ArH), 7.59–7.51 (m, 2H, ArH), 7.33 (d, J = 8.0 Hz, 3H, ArH), 7.21 (s, 2H, ArH), 7.19 (s, 1H), 6.66 (d, J = 8.0 Hz, 1H, ArH), 5.97 (s, 1H), 2.7 (d, J = 8.0 Hz, 2H, CH2), 2.37 (d, J = 16.0 Hz, 1H), 2.13 (d, J = 16.0 Hz, 1H), 1.90 (d, J = 16.0 Hz, 1H), 1.79 (d, J = 16.0 Hz, 1H), 1.25 (t, J = 8.0 Hz, 3H, Me), 0.88 (s, 3H, Me), 0.86 (s, 3H, Me); 13C NMR (100 MHz, DMSO-d6) δ (ppm) = 198.07, 189.57, 147.73, 144.01, 135.30, 135.20, 133.97, 130.62, 129.76, 128.72, 125.41, 123.62, 105.68, 97.10, 83.87, 51.66, 37.47, 33.87, 29.78, 28.27, 27.03, 15.85.
2.7.3. 5-(3-Chlorophenyl)-4b,9b-dihydroxy-7,7-dimethyl-4b,5,6,7,8,9b-hexahydroindeno[1,2-b]indole-9,10-dione (4c). White solid (90% yield); m.prep. = 220–225 °C (ethanol); m.plit. = 223–226 °C;32 IR (KBr) v (cm−1): 3564, 3391, 2947, 2873, 1719, 1641, 1480, 1159, 731; 1H NMR (400 MHz, DMSO-d6) δ (ppm) = 7.61 (d, J = 4.0 Hz, 1H, ArH), 7.51–7.56 (m, 5H, ArH), 7.30 (s, 1H, ArH), 7.18 (d, J = 8.0, 1H, ArH), 2.48 (d, J = 16.0 Hz, 1H), 2.15 (d, J = 16.0 Hz, 1H), 1.90 (d, J = 16.0 Hz, 1H), 1.81 (d, J = 16.0 Hz,1H), 0.96 (s, 3H, Me), 0.91 (s, 3H, Me).
2.7.4. 5-(4-Bromophenyl)-4b,9b-dihydroxy-7,7-dimethyl-4b,5,6,7,8,9b-hexahydroindeno[1,2-b]indole-9,10-dione (4d). White solid (92% yield); m.prep. = 170–175 °C (ethanol); m.plit. = 160–162 °C;2 IR (KBr) v (cm−1): 3465, 2957, 2883, 1722, 1602, 1489, 1148, 518; 1H NMR (400 MHz, DMSO-d6) δ (ppm) = 7.72 (t, J = 8.0 Hz, 3H, ArH), 7.61 (t, J = 8.0 Hz, 1H, ArH), 7.54 (t, J = 8.0 Hz, 1H), 7.35 (s, 1H), 7.26 (d, J = 8.0 Hz, 2H, ArH, OH), 6.68 (d, J = 8.0 Hz, 1H, ArH), 6.05 (s, 1H, OH), 2.42 (d, J = 16.0 Hz, 1H), 2.15 (d, J = 16.0 Hz, 1H), 1.90 (d, J = 16.0 Hz, 1H), 1.81 (d, J = 16.0 Hz, 1H), 0.95 (s, 3H, Me), 0.90 (s, 3H, Me).
2.7.5. 4b,9b-Dihydroxy-7,7-dimethyl-5-(naphthalene-1-yl)-4b,5,6,7,8,9b-hexahydroindeno[1,2-b]indole-9,10-dione (4e). Light yellow solid: (93% yield); m.prep. = 200–205 °C (ethanol); m.plit. = 186–188 °C;33 IR (KBr) v (cm−1): 3381, 2931, 1712, 1608, 1448, 1157; 1H NMR (400 MHz, DMSO-d6) δ (ppm) = 8.04–8.13 (m, 1H), 7.99 (d, J = 8.0 Hz, 1H, ArH), 7.93 (d, J = 8.0 Hz, 1H, ArH), 7.70–7.81 (m, 2H, ArH), 7.57–7.63 (m, 1H, ArH), 7.40–7.45 (m, 2H, ArH), 7.05–7.17 (m, 2H, ArH, OH), 6.36 (d, J = 8.0 Hz, 1H, ArH), 6.29 (d, J = 4.0 Hz, 1H, ArH), 6.02 (s, 1H, OH), 1.79–2.16 (m, 4H), 0.90 (s, 3H, Me), 0.78 (s, 3H, Me).
2.7.6. 5,5′-(1,4-Phenylene)bis(4b,9b-dihydroxy-7,7-dimethyl-4b,5,6,7,8,9b-hexahydroindeno[1,2-b]indole-9,10-dione) (4f). Smoky solid (95% yield); m.prep. = 305–310 °C (ethanol); IR (KBr) v (cm−1): 3357, 3176, 2960, 1719, 1567, 1507, 1449, 1380, 1157; 1H NMR (400 MHz, DMSO-d6) δ (ppm) = 7.77 (d, J = 8.0 Hz, 2H, ArH), 7.68–7.56 (m, 4H, ArH), 7.45–7.39 (m, 6H, ArH, OH), 6.75–6.79 (m, 2H, ArH), 6.09 (s, 2H, OH), 2.56 (d, J = 16.0 Hz, 2H), 2.18 (d, J = 16.0 Hz, 2H), 1.92 (d, J = 20.0 Hz, 4H), 1.02 (s, 6H, Me), 0.95 (s, 6H, Me); 13C NMR (100 MHz, DMSO-d6) δ (ppm) = 198.06, 189.93, 163.66, 147.75, 136.13, 135.31, 130.93, 130.06, 129.81, 123.93, 106.68, 97.40, 83.91, 51.75, 37.56, 34.17, 34.13, 30.05.
2.7.7. 5-(2-Chlorophenyl)-4b,9b-dihydroxy-7,7-dimethyl-4b,5,6,7,8,9b-hexahydroindeno[1,2-b]indole-9,10-dione (4g). White solid (92% yield); m.prep. = 240–245 °C (ethanol); m.plit. = 230–231 °C;1 IR (KBr) v (cm−1): 3417, 2955, 2874, 1714, 1571, 1446, 1155, 772; 1H NMR (400 MHz, DMSO-d6) δ (ppm) = 7.83 (d, J = 4.0 Hz, 1H, ArH), 7.74 (d, J = 8.0 Hz, 1H, ArH), 7.53–7.55 (m, 5H, ArH), 7.38 (s, 1H, OH), 6.66 (d, J = 4.0 Hz, ArH), 5.96 (s, 1H, OH), 2.08–1.95 (m, 4H), 0.97 (s, 3H, Me), 0.87 (s, 3H, Me).
2.7.8 4b,9b-Dihydroxy-5-(4-methoxyphenyl)-7,7-dimethyl-4b,5,6,7,8,9b-hexahydroindeno[1,2-b]indole-9,10-dione (4h). Gray solid (91% yield); m.prep. = 215–220 °C (ethanol); m.plit. = 224–226 °C;1 IR (KBr) v (cm−1): 3410, 3037, 2951, 2715, 1728, 1607, 1512, 1441, 1149; 1H NMR (400 MHz, DMSO) δ (ppm) = 7.72 (d, J = 8.0 Hz, 1H, ArH), 7.60–7.51 (m, 2H, ArH), 7.31–7.16 (m, 5H, ArH, OH), 6.66 (d, J = 8.0 Hz, 1H, ArH), 5.98 (s, 1H, OH), 2.39 (s, 3H, OMe), 2.35 (s, 1H), 2.13 (d, J = 16.0 Hz, 1H), 1.89 (d, J = 16.0 Hz, 1H), 1.77 (d, J = 16.0 Hz, 1H), 0.91 (s, 3H, Me), 0.88 (s, 3H, Me).
2.7.9. 5-(4-Chlorophenyl)-4b,9b-dihydroxy-7,7-dimethyl-4b,5,6,7,8,9b-hexahydroindeno[1,2-b]indole-9,10-dione (4i). White solid (93% yield); m.prep. = 223–228 °C (ethanol); m.plit. = 235–236 °C;1 IR (KBr) v (cm−1): 3423, 2952, 1713, 1621, 1553, 1449, 1183, 771; 1H NMR (400 MHz, DMSO-d6) δ (ppm) = 7.73 (d, J = 8.0 Hz, 1H, ArH), 7.62–7.52 (m, 4H, ArH), 7.36 (s, 1H, OH), 7.33 (d, J = 8.0 Hz, 2H, ArH), 6.67 (d, J = 8.0 Hz, 1H, ArH), 6.06 (s, 1H, OH), 2.42 (d, J = 20.0 Hz, 1H), 2.15 (d, J = 16.0 Hz, 1H), 1.90 (d, J = 16.0 Hz, 1H), 1.80 (d, J = 20.0 Hz, 1H), 0.96 (s, 3H, Me), 0.90 (s, 3H, Me).
2.7.10. 5,5′-(Pyridine-2,6-diyl)bis(4b,9b-dihydroxy-7,7-dimethyl-4b,5,6,7,8,9b-hexahydroindeno[1,2-b]indole-9,10-dione) (4j). Pale yellow (94% yield); m.prep. = 215–220 °C (ethanol); IR (KBr) v (cm−1): 3389, 3254, 2943, 2879, 1713, 1660, 1607, 1464, 1255, 1164; 1H NMR (400 MHz, DMSO-d6) δ (ppm) = 8.34–8.21 (m, 2H, ArH), 8.87–7.43 (m, 11H, ArH, OH), 6.28 (s, 2H, OH), 2.37–1.99 (m, 8H), 1.03 (s, 6H, Me), 0.85 (s, 6H, Me); 13C NMR (100 MHz, DMSO-d6) δ (ppm) = 197.55, 193.18, 175.94, 152.58, 147.25, 136.62, 134.70, 131.88, 125.30, 123.47, 112.94, 111.67, 91.09, 90.91, 82.60, 51.58, 37.63, 33.45, 27.81.
2.7.11. 5,5′-(Sulfonylbis(4,1-phenylene))bis(4b,9b-dihydroxy-7,7-dimethyl-4b,5,6,7,8,9b-hexahydroindeno[1,2-b]indole-9,10-dione) (4k). White solid (95% yield); m.prep. = 290–295 °C (ethanol); IR (KBr) v (cm−1): 3393, 2959, 2879, 1724, 1624, 1560, 1493, 1432, 1289; 1H NMR (400 MHz, DMSO-d6) δ (ppm) = 8.16–8.19 (m, 3H), 7.72 (d, J = 4.0 Hz, 2H), 7.65 (d, J = 8.0 Hz, 4H), 7.58 (s, 2H), 7.49–7.55 (m, 5H), 6.54–6.58 (m, 2H), 6.19 (s, 2H), 2.53–2.57 (m, 2H), 2.12–2.19 (m, 2H), 1.86–1.94 (m, 4H), 0.94 (s, 6H, Me), 0.88 (s, 6H, Me); 13C NMR (100 MHz, DMSO-d6) δ (ppm) = 197.75, 190.35, 147.37, 142.04, 139.80, 135.51, 135.13, 130.89, 130.04, 129.03, 124.91, 123.85, 113.61, 108.00, 97.82, 83. 98, 51.68, 37.55, 34.25, 29.86.
2.7.12. 4b,9b-Dihydroxy-7,7-dimethyl-5-(o-tolyl)-4b,5,6,7,8,9b-hexahydroindeno[1,2-b]indole-9,10-dione (4l). White solid (92% yield); m.prep. = 215–220 °C (ethanol); m.plit. = 217–216 °C;1 IR (KBr) v (cm−1): 3392, 2959, 1724, 1624, 1493, 1289, 1157; 1H NMR (400 MHz, DMSO-d6) δ (ppm) = 8.34 (s, 1H), 7.66–7.88 (m, 8H), 6.29 (s, 1H), 2.33 (s, 1H), 2.00–2.12 (m, 3H), 1.03 (s, 6H, Me), 0.85 (s, 3H, Me).
3. Results and discussion
3.1. Preparation and characterization of the CuFe2O4@CS-SB catalyst
The preparation of the CuFe2O4@CS-SB catalyst was done in three steps. In the first stage, the 4-(2-hydroxyaniline)pent-3-en-2-one Schiff base was prepared. The second stage is placing the desired Schiff base on the chitosan substrate and the third stage is chelating the copper ferrite nanoparticle with compounds on the chitosan and Schiff-base substrate. The general schematic of nanocatalyst preparation is shown in Scheme 1.
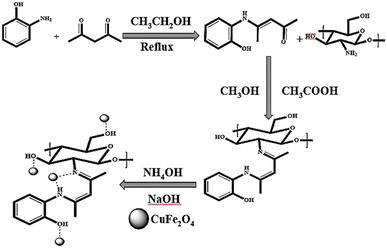 |
| Scheme 1 Preparation of the CuFe2O4@CS-SB catalyst. | |
Furthermore, attenuated total reflectance (ATR), X-ray diffraction (XRD), field emission scanning electron microscopy (FE-SEM), elemental mapping, energy dispersive X-ray (EDX), thermogravimetric analysis (TGA), vibrational sample magnetometry (VSM) and Brunauer–Emmett–Teller (BET) analyses were used to characterize the CuFe2O4@CS-SB nano-composite.
The ATR spectra of the Schiff base, Schiff base-chitosan and CuFe2O4@CS-SB catalyst are provided in the range from 400 to 4000 cm−1 and are shown in Fig. 1. To detect the presence of the stretching vibration of the N–H and O–H bonds in the spectrum of 1a, a wide band was observed at the position of 3010 cm−1. In the spectrum of 1a, two absorption peaks in the region of 2721 and 2599 cm−1 are related to the symmetric and asymmetric stretching vibrations of C–H (sp3), respectively. Due to the conjugated structure, the absorption peaks are 1585 cm−1 and 1552 cm−1 for the carbonyl and CH
NH groups, respectively. Two absorption peaks in the region of 1501 cm−1 and 1434 cm−1 are related to the stretching vibration of C
C in the aromatic ring, and the peak in the region of 745 cm−1 is related to the alkene bond of
C–H (sp2). In the spectrum of 1b, the stretching vibrations of O–H and N–H bonds have a broad peak at 3389 cm−1 and C–H (sp3) as a weak peak at 2869 cm−1. The peak observed at 1665 cm−1 corresponding to the stretching vibrations of imine and the absorbed vibration of C
C of the aromatic ring appeared in the region of 1599 cm−1 and 1428 cm−1 and the stretching vibrations of the C–O–C appeared at 1056 cm−1. In the spectrum of 1c, the stretching vibrations of O–H and N–H bonds are in the region of 3359 cm−1 and the stretching vibration of C–H (sp3) are in the region of 2865 cm−1. The presence of stretching vibrations in the region of 1597 cm−1 is due to the presence of the imine group and in at 1056 cm−1 is related to C–O–C. The bonds related to metals such as Fe–O in the 552 cm−1 region of self-vibration are visible in the ATR spectra.34
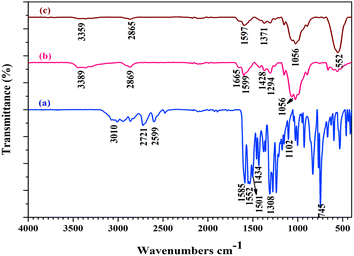 |
| Fig. 1 ATR spectra of (a) Schiff base, (b) chitosan-Schiff base, (c) CuFe2O4@CS-SB catalyst. | |
The X-ray diffraction (XRD) patterns of (a) CuFe2O4 and (b) CuFe2O4@CS-SB catalyst are shown in Fig. 2, which is a non-destructive technique to detect the crystal structure and state of phases. As can be seen in this figure, in the XRD pattern of CuFe2O4, the crystal peaks for (220), (311), (222), (400), (422), (511) and (440) appeared, which is the reason for the presence of cubic CuFe2O4 with Fd-3m space group (JCPDS No. card no 01-077-0010). The calculation of crystal formation using Scherrer's equation is reviewed in Table 1. The average particle size for this structure was measured to be 29.45 nm.
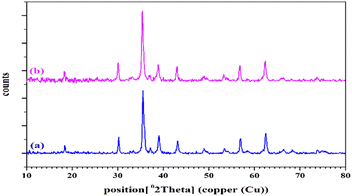 |
| Fig. 2 X-ray diffraction spectra of (a) CuFe2O4 and (b) CuFe2O4@CS-SB catalyst. | |
Table 1 The peak position, full width at half maximum (β½), and calculated crystal size for nanoparticlesa
h k l |
(220) |
(311) |
(222) |
(400) |
(422) |
(511) |
(440) |
λ = 0.154 nm, K = 0.94. |
Peak position 2θ (°) |
30.0907 |
35.4090 |
38.9135 |
42.9803 |
53.3002 |
56.8027 |
62.3422 |
FWHM β (°) |
0.2362 |
0.2952 |
0.2952 |
0.2952 |
0.3542 |
0.3542 |
0.3542 |
Size (nm) |
36.39 |
29.52 |
29.82 |
30.22 |
26.22 |
26.64 |
27.39 |
The field-emission scanning electron microscopy (SE-SEM) analysis for the CuFe2O4@CS-SB catalyst was done and the related images are given in Fig. 3. The surface morphology and particle size of CuFe2O4 nanoparticles and CuFe2O4@CS-SB nanocatalyst were investigated. These images show that the surface of the catalyst is rough, the nanoparticle shapes are mostly capsule-like and the average particle size range is 68.03 nm.
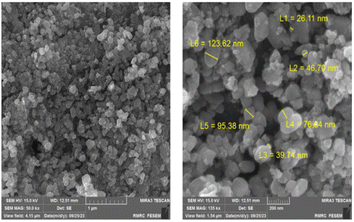 |
| Fig. 3 FE-SEM images of the CuFe2O4@CS-SB catalyst. | |
The elemental mapping analysis of the CuFe2O4@CS-SB catalyst is shown in Fig. 4. With consideration of this figure, the images of elemental mapping show the distribution of C, N, O, Fe and Cu elements in this catalyst. As it is known, the active elements of catalysis are spread homogeneously on the catalyst substrate. The homogeneity of the elements on the catalyst substrate indicates that the entire surface of the catalyst has an active site that can show its catalytic effect by connecting this active site to the reaction.
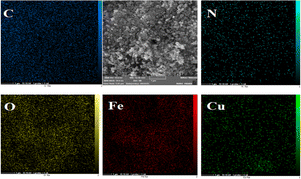 |
| Fig. 4 Elemental mapping of the CuFe2O4@CS-SB catalyst. | |
Energy dispersive X-ray (EDX) analysis of the present catalyst is shown in Fig. 5. As seen in this pattern and the EDX specification table, there are carbon, oxygen, nitrogen, iron and copper in this catalyst and CuFe2O4 nanoparticles are uniformly dispersed on the chitosan-Schiff base (C K = wt%: 34.89 and at%: 51.48, N K = wt%: 5.82 and at%: 7.36, O K = wt%: 28.58 and at%: 31.66, Fe K = wt%: 24.36 and at%: 7.73, Cu K = wt%: 6.35 and at%: 1.77) (Table 2).
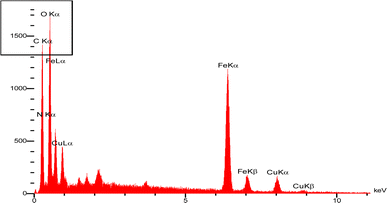 |
| Fig. 5 The EDX of the CuFe2O4@CS-SB catalyst. | |
Table 2 EDX catalyst weight percent
Element |
wt% |
at% |
C K |
34.89 |
51.48 |
N K |
5.82 |
7.36 |
O K |
28.58 |
31.66 |
Fe K |
24.36 |
7.73 |
Cu K |
6.35 |
1.77 |
To investigate the thermal stability of chitosan and other organic materials, the thermogravimetric analysis (TGA) of the catalyst was done by increasing the temperature under nitrogen atmosphere (Fig. 6). As seen in this figure, the first weight loss at temperature below 200 °C, with a decrease of 1.58%, refers to the removal of the absorbed water moisture. The second weight change from 245 to 600 °C, with the maximum peak of endothermic decomposition, proves the presence of organic groups and Schiff base attached to the chitosan. The third weight loss from 639 to 800 °C is related to the breaking of the chitosan polymer bonds.35
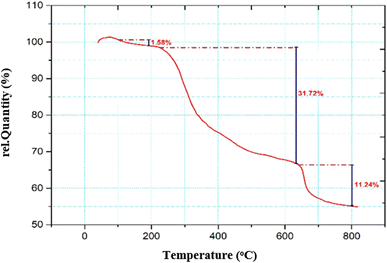 |
| Fig. 6 TGA curve of the CuFe2O4@CS-SB catalyst. | |
Fig. 7 shows the vibrational sample magnetometry (VSM) curve of copper ferrite and the CuFe2O4@CS-SB catalyst. The saturation magnetism of the copper ferrite sample (a) is 33.50 emu g−1 and that of the CuFe2O4@CS-SB catalyst sample (b) is 13.63 emu g−1. It can be concluded that by introducing different groups on the catalyst substrate, 19.87 emu g−1 of the saturation magnetism of the nanocatalyst has been reduced, but the magnetism of the nanocatalyst is still maintained.
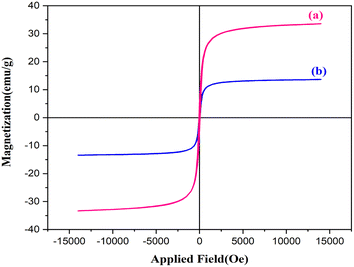 |
| Fig. 7 The VSM curve of CuFe2O4 (a), CuFe2O4@CS-SB catalyst (b). | |
The Brunauer–Emmett–Teller (BET) in Fig. 8a for the CuFe2O4@CS-SB catalyst shows that the surface area was 35.34 m2 g−1, which increased the contact surface of the catalyst with the environment. The average pore diameter of the CuFe2O4@CS-SB catalyst is 15.06 nm and the total pore volume is 0.1331 cm3 g−1, where the imine, hydroxyl, amino groups and copper ferrite nanoparticles have active adsorption, which is related to the type III adsorption–desorption isotherm (Fig. 8b). Also, the aggregates of the CuFe2O4@CS-SB catalyst are slit-like, according to this diagram (Fig. 8b). Based on the Barrett–Joyner–Halenda (BJH) method, Fig. 8c shows that the total pore volume (VP) in the CuFe2O4@CS-SB catalyst is 0.1269 cm3 g−1.
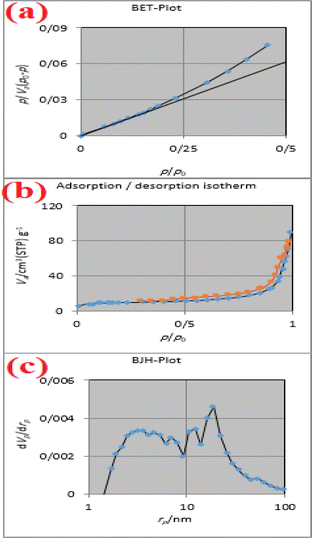 |
| Fig. 8 The BET curve (a), adsorption/desorption isotherm (b), the BJH curve (c) of the CuFe2O4@CS-SB catalyst. | |
3.2. Catalytic activity evaluation of CuFe2O4@CS-SB
The multi-component cyclization reaction of aniline derivatives, dimedone and ninhydrin with a molar ratio of 1
:
1
:
1 using the CuFe2O4@CS-SB catalyst for the synthesis of indeno[1,2-b]indolones was carried out. First, the best reaction conditions were obtained from the optimization of the catalyst amount, solvent and temperature in the synthesis of these organic compounds after comparison and detailed studies. Initially, different amounts of the catalyst in the reaction of dimedone (1 mmol), aniline (1 mmol) and ninhydrin (1 mmol) as a model reaction were investigated, and the best amount of the catalyst was reported to be 0.004 g (Table 3, entry 5).
Table 3 Optimization of the catalyst amount for the synthesis of 4aa
Entry |
Catalyst amount (g) |
Time (min) |
Yieldb (%) |
Reaction conditions: dimedone (1 mmol), aniline (1 mmol), ninhydrin (1 mmol) and CuFe2O4@CS-SB catalyst (0.004 g) at 75 °C. Isolated yields. |
1 |
— |
120 |
20 |
2 |
0.001 |
25 |
62 |
3 |
0.002 |
12 |
79 |
4 |
0.003 |
7 |
90 |
5 |
0.004 |
6 |
92 |
6 |
0.005 |
10 |
92 |
Moreover, the model reaction was done in the presence of 0.004 g nanocatalyst at different temperatures, and the results are reported to Table 4. As indicated in this table, the best temperature at which excellent yield was obtained for this reaction was 75 °C (Table 4, entry 6).
Table 4 Optimization of temperature for the synthesis of 4aa
Entry |
Temperature (°C) |
Time (min) |
Yieldb (%) |
Reaction conditions: dimedone (1 mmol), aniline (1 mmol), ninhydrin (1 mmol) and CuFe2O4@CS-SB catalyst (0.004 g) in double distilled H2O as the solvent at 75 °C. Isolated yields. |
1 |
r.t |
120 |
20 |
2 |
35 |
30 |
55 |
3 |
45 |
25 |
68 |
4 |
55 |
18 |
70 |
5 |
65 |
9 |
89 |
6 |
75 |
6 |
92 |
7 |
85 |
15 |
92 |
Also, different polar and non-polar solvents were investigated to find out the best product yield and low reaction time, which gave the water as the solvent with excellent product yield formed in this reaction (Table 5, entry 9).
Table 5 Optimization of solvent for the synthesis of 4aa
Entry |
Solvent |
Time (min) |
Yieldb (%) |
Reaction conditions: dimedone (1 mmol), aniline (1 mmol), ninhydrin (1 mmol) in the presence of CuFe2O4@CS-SB catalyst (0.004 g) in the selected solvent at 75 °C. Isolated yields. |
1 |
DMSO |
19 |
73 |
2 |
DMF |
43 |
60 |
3 |
EtOH |
10 |
69 |
4 |
Acetone |
60 |
28 |
5 |
THF |
80 |
21 |
6 |
PEG |
67 |
52 |
7 |
Toluene |
100 |
17 |
8 |
CH3CN |
70 |
49 |
9 |
H2O |
6 |
92 |
10 |
H2O/ethanol (1 : 1) |
8 |
82 |
After optimization, in order to check the general applicability and develop the method, all kinds of aniline derivatives including electron donor and acceptor groups were used to prepare the indeno[1,2-b]indolone derivatives under the optimized conditions. The corresponding results are summarized in Scheme 2. As indicated in this scheme, the electron donating groups on the aniline ring are led to higher yields. As can be seen, short reaction times and excellent yields of the products are obtained due to the presence of the efficient catalyst. The physical and spectral data obtained from these compounds is the proof of the formation of these products.
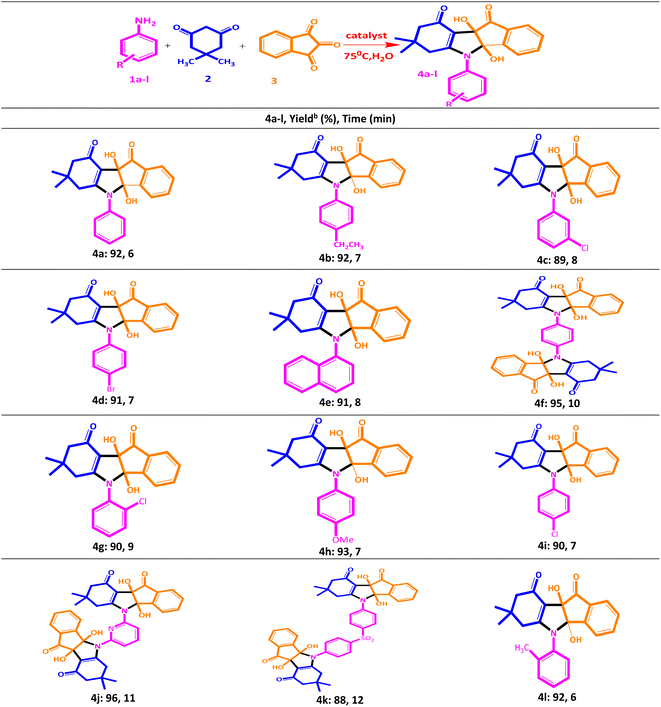 |
| Scheme 2 Synthesis of indeno[1,2-b]indolone derivativesa. | |
The results of the comparison of each of the four different products obtained using the current catalyst with four other previously reported catalysts for this reaction based on the product yield are shown in Table 6. It was concluded that with the CuFe2O4@CS-SB catalyst, shorter reaction time with excellent yield could be obtained under better thermal conditions.
Table 6 Comparison of the catalytic activity of the CuFe2O4@CS-SB catalyst with other reported catalysts for the synthesis of indeno[1,2-b]indolone
Entry |
Product |
Conditions |
Time (min) |
Yielda (%) |
Ref. |
Isolated yield. |
1 |
4i |
MMT@Fe3O4 (0.02 g, water, 70 °C) |
7 |
90 |
This work |
2 |
35 |
90 |
2 |
3 |
4d |
SnO2 QDs (10 mol%, water, 70 °C) |
7 |
91 |
This work |
4 |
270 |
87 |
32 |
5 |
4a |
Lactic acid (0.15 mmol, grind, 10 min, r.t) |
6 |
92 |
This work |
6 |
10 |
87 |
9 |
7 |
4b |
C@TiO2-SO3H-ILs (0.1 g, water, 60 °C) |
7 |
92 |
This work |
8 |
60 |
92 |
1 |
3.3. Reusability of the catalyst
Since it is very important to recover the catalyst and reuse it, Fig. 9 shows the results of six runs of catalyst reuse. It has been concluded that during six runs of recycling, the yield decreased the least and the performance of the catalyst was excellent. To reuse the catalyst in subsequent reactions, the catalyst was separated using an external magnet, washed several times with ethanol and acetone, dried at 70 °C for 6 h and then can be reused. The short reaction times and excellent product yields are attributed to the efficiency of the catalyst. The physical and spectral data obtained from these compounds is the proof of the formation of these products.
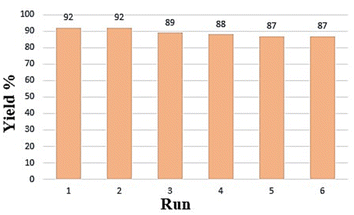 |
| Fig. 9 The reusability of the CuFe2O4@CS-SB catalyst. | |
In order to study the stability of the nanocatalyst, the FE-SEM image of the recovered catalyst was provided and is shown in Fig. 10. According to the image in Fig. 10a, the morphology of the catalyst did not change during reuse, indicating the structural resistance of the catalyst. Also, by examining the XRD pattern of the recovered catalyst, as shown in Fig. 10b, it is clear that after several steps of using the catalyst, it can be reused because the metals are still bound on the chitosan substrate.
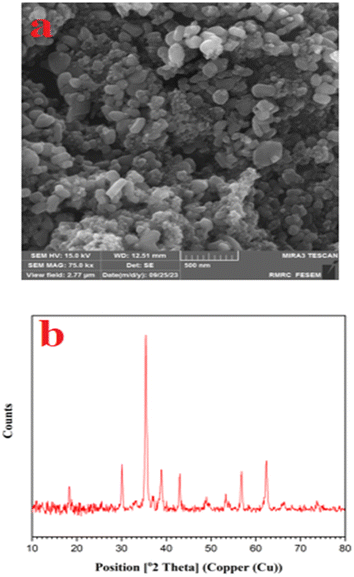 |
| Fig. 10 FE-SEM (a) and XRD (b) images after reuse of the CuFe2O4@CS-SB catalyst. | |
In addition, the hot filtration method was used for the model reaction for the synthesis of 4a to investigate the leaching of the CuFe2O4@CS-SB catalyst. After 3 min of reaction time, the nanocatalyst was separated from the reaction mixture using a strong external magnet. The development of the reaction was monitored by thin layer chromatography (TLC), which concluded that no progress occurred in the reaction after the removal of the catalyst and so that leaching did not occur for the used catalyst.
4. Conclusion
In this study, chitosan was prepared based on a Schiff base and chelated with copper ferrite. The FE-SEM, 1H NMR, FT-IR, TGA, elemental mapping, EDX, BET and XRD analysis results confirmed that the CuFe2O4@CS-SB catalyst was successfully synthesized. By comparing the FT-IR peaks of the catalyst in different stages of synthesis and also checking the ranges of CuFe2O4 and Schiff base in XRD analysis, the formation of the catalyst was confirmed. As a result of these studies, the CuFe2O4@CS-SB catalyst was employed for the synthesis of indeno[1,2-b]indolone derivatives under thermal conditions using water as the solvent.
Data availability
ESI† contains 1H NMR, FT-IR and microscopy data.
Conflicts of interest
This paper's authors declare that they do not have any competing financial interests or personal relationships to influence their work.
Acknowledgements
The authors are grateful to the University of Kashan for supporting this work by Grant No. 159148/86.
References
- M. Kour, M. Bhardwaj, H. Sharma, S. Paul and J. H. Clark, New J. Chem., 2017, 41, 5521–5532 RSC.
- J. Safari and N. Hosseini Nasab, Res. Chem. Intermed., 2019, 45, 1025–1038 CrossRef CAS.
- R. R. Gupta, M. Kumar and V. Gupta, in Heterocyclic Chemistry, Springer Berlin Heidelberg, Berlin, Heidelberg, 1999, pp. 181–355 Search PubMed.
- A. W. Czarnik, Anal. Chem., 1998, 70, 378A–386A CrossRef.
- D. H. Kita, N. Guragossian, I. F. Zattoni, V. R. Moure, F. G. de M. Rego, S. Lusvarghi, T. Moulenat, B. Belhani, G. Picheth, S. Bouacida, Z. Bouaziz, C. Marminon, M. Berredjem, J. Jose, M. B. Gonçalves, S. V. Ambudkar, G. Valdameri and M. Le Borgne, Sci. Rep., 2021, 11, 1788 CrossRef CAS PubMed.
- X. Qian, R. Yan, C. Xu, L. Shao, H. Li and L. Hou, J. Power Sources, 2016, 332, 103–110 CrossRef CAS.
- G. Lobo, M. Monasterios, J. Rodrigues, N. Gamboa, M. V. Capparelli, J. Martínez-Cuevas, M. Lein, K. Jung, C. Abramjuk and J. Charris, Eur. J. Med. Chem., 2015, 96, 281–295 CrossRef CAS PubMed.
- S. Haidar, Z. Bouaziz, C. Marminon, T. Laitinen, A. Poso, M. Le Borgne and J. Jose, Pharmaceuticals, 2017, 10, 8 CrossRef PubMed.
- X. Chen and Y. Liu, Heterocycl. Commun., 2016, 22, 161–163 CrossRef CAS.
- B.-C. Hong, Y.-F. Jiang, Y.-L. Chang and S.-J. Lee, J. Chin. Chem. Soc., 2006, 53, 647–662 CrossRef CAS.
- A. H. Ghasemi and H. Naeimi, New J. Chem., 2020, 44, 5056–5063 RSC.
- L. C. Meher, C. P. Churamani, M. Arif, Z. Ahmed and S. N. Naik, Renewable Sustainable Energy Rev., 2013, 26, 397–407 CrossRef CAS.
- R. A. A. Muzzarelli, J. Boudrant, D. Meyer, N. Manno, M. DeMarchis and M. G. Paoletti, Carbohydr. Polym., 2012, 87, 995–1012 CrossRef CAS.
- A. H. Anwer, A. Ahtesham, M. Shoeb, F. Mashkoor, M. Z. Ansari, S. Zhu and C. Jeong, Adv. Colloid Interface Sci., 2023, 318, 102955 CrossRef CAS PubMed.
- H. Veisi, T. Tamoradi, A. Rashtiani, S. Hemmati and B. Karmakar, J. Ind. Eng. Chem., 2020, 90, 379–388 CrossRef CAS.
- J. Zhou, Z. Dong, H. Yang, Z. Shi, X. Zhou and R. Li, Appl. Surf. Sci., 2013, 279, 360–366 CrossRef CAS.
- M. N. V. Ravi Kumar, Bull. Mater. Sci., 1999, 22, 905–915 CrossRef CAS.
- F. Ali, S. B. Khan, T. Kamal, K. A. Alamry, E. M. Bakhsh, A. M. Asiri and T. R. A. Sobahi, Carbohydr. Polym., 2018, 192, 217–230 CrossRef CAS PubMed.
- F. G. Göze Özdemir, H. Çevik, J. C. Ndayiragije, T. Özek and İ. Karaca, Int. J. Agric. Environ. Food. Sci., 2022, 6, 410–416 Search PubMed.
- Q. Wei, Y. Wang, H. Wang, L. Qiao, Y. Jiang, G. Ma, W. Zhang and Z. Hu, Carbohydr. Polym., 2022, 278, 119000 CrossRef CAS PubMed.
- C. C. Berry, J. Mater. Chem., 2005, 15, 543–547 RSC.
- Z. Guo, R. Xing, S. Liu, Z. Zhong, X. Ji, L. Wang and P. Li, Carbohydr. Res., 2007, 342, 1329–1332 CrossRef CAS PubMed.
- K. C. Gupta and A. K. Sutar, Coord. Chem. Rev., 2008, 252, 1420–1450 CrossRef CAS.
- P. Przybylski, A. Huczynski, K. Pyta, B. Brzezinski and F. Bartl, Curr. Org. Chem., 2009, 13, 124–148 CrossRef CAS.
- A. O. de Souza, F. C. S. Galetti, C. L. Silva, B. Bicalho, M. M. Parma, S. F. Fonseca, A. J. Marsaioli, A. C. L. B. Trindade, R. P. F. Gil, F. S. Bezerra, M. Andrade-Neto and M. C. F. de Oliveira, Quim. Nova, 2007, 30 DOI:10.1590/S0100-40422007000700012.
- R. Ghahremanzadeh, Z. Rashid, A. H. Zarnani and H. Naeimi, Appl. Catal., A, 2013, 467, 270–278 CrossRef CAS.
- S. Kazempour and H. Naeimi, Appl. Organomet. Chem., 2022, 36 DOI:10.1002/aoc.6903.
- S. Mousavi, H. Naeimi, A. H. Ghasemi and S. Kermanizadeh, Sci. Rep., 2023, 13, 10840 CrossRef CAS PubMed.
- A. Farazin, M. Mohammadimehr and H. Naeimi, Int. J. Biol. Macromol., 2023, 241, 124572 CrossRef CAS PubMed.
- S. Kermanizadeh, H. Naeimi and S. Mousavi, Dalton Trans., 2023, 52, 1257–1267 RSC.
- A. H. Ghasemi, A. Farazin, M. Mohammadimehr and H. Naeimi, Mater. Today Commun., 2022, 31, 103513 CrossRef CAS.
- K. Pradhan, S. Paul and A. R. Das, RSC Adv., 2015, 5, 12062–12070 RSC.
- M. U. Khan, R. A. Rather and Z. N. Siddiqui, RSC Adv., 2020, 10, 44892–44902 RSC.
- A. Massoud-Sharifi, G. K. Kara and M. Rabbani, in The 4th International Electronic Conference on Water Sciences, MDPI, Basel Switzerland, 2019, p. , p. 17 Search PubMed.
- R. Antony, S. Theodore David, K. Saravanan, K. Karuppasamy and S. Balakumar, Spectrochim. Acta, Part A, 2013, 103, 423–430 CrossRef CAS PubMed.
|
This journal is © The Royal Society of Chemistry 2024 |
Click here to see how this site uses Cookies. View our privacy policy here.