DOI:
10.1039/D4RA00930D
(Paper)
RSC Adv., 2024,
14, 7609-7615
Enhancing enzymatic digestibility of bamboo residues using a combined low severity steam explosion and green liquor-sulfite pretreatment
Received
5th February 2024
, Accepted 26th February 2024
First published on 5th March 2024
Abstract
In this study, the effect of the green liquor (GL)-sulfite pretreatment on bamboo for enzymatic hydrolysis was investigated. The performance characterization of the pretreated bamboo substrates, including the chemical composition, and the structural characteristics was carried out. The results showed that 91.3% of lignin removal was achieved when the sample was treated with a GL loading of 12.0 mL per g-DS at 120 °C for 1 h. After 120 h hydrolysis with 18 FPU per g-cellulose for cellulase and 27 CBU per g-cellulose for glucosidase, the glucose yield increased from 54.6% to 89.6%. The SE-treated bamboo could bind more easily to cellulase than GL-sulfite treated bamboo could. The structural changes on the surface of the samples were characterized by SEM. The results indicated that the surface lignin could be effectively removed during pretreatment, thereby decreasing the enzyme-lignin binding activity.
1 Introduction
Development of biomass energy is crucial in terms of the depletion of fossil resources and environmental protection. Bioethanol is considered as a promising alternative liquid fuel.1 Lignocellulosic waste has emerged as an attractive feedstock for bioethanol production in the last decades.2 Bamboo has the characteristics of rapid growth, high mechanical strength and high biomass production. China is the world's largest producer of bamboo. According to statistics, China's entire bamboo forest area is 7.56 million hectares.3 China produces annually 150 million tons of bamboo, and the output value of the bamboo industry has increased from 82 billion yuan in 2010 to 415.3 billion yuan in 2022, with an average annual growth rate of more than 30%. By 2035, the total output value of China's bamboo industry will exceed 1 trillion yuan. A large amount of bamboo residues, such as bamboo heads and chips, will be produced from the processing of bamboo. These industrial bamboo residues can be utilized to produce bioethanol, which exerts a positive influence on alleviating the energy crisis while also protecting the environment.4
The chemical components of bamboo are similar to wood, consisting of cellulose, hemicellulose, and lignin. High content of carbohydrate make bamboo a good source of lignocellulosic material for glucose and bioethanol production. However, high natural resistance makes cellulose separation and utilization challenging. Pretreatments are the crucial steps to open up the inner structure of bamboo before enzymatic hydrolysis. Many pretreatment methods for improving the enzymatic hydrolysis of bamboo have been investigated. Pretreatment strategies such as steam explosion (SE), liquid hot water extraction, microwave and ultrasonic pretreatment are physical methods. They disrupt the supramolecular structure of cellulose, hemicellulose, and lignin, breaking the internal bonding of lignocellulosic biomass with little carbohydrate loss. They are more appropriate as a pre-step to co-processing.5 Chemical pretreatment can significantly improve the hydrolysis rate of bamboo. Chemicals such as acids, alkalis,6 organic solvents,7 hydrogen peroxide8 and ionic liquids9 have been widely used to break down bamboo materials. Chemical pretreatment is commonly used in industry due to its most simple operation and high efficiency. However, the production of inhibitors and environmental pollution are also common disadvantages in chemical pretreatment.10 By-products of lignocellulose pretreatment inhibit microbial and enzymatic biocatalysts. Combined pretreatment methods seem a good choice to reduce the use of chemical reagents and production of inhibitors.11,12
SE pretreatment could disrupt the physical structure of biomass by an explosive decompression of saturated steam. The SE treated residue has a loose fibre structure.13 The main reason for enhancement of enzymatic hydrolysis is the removal of hemicellulose and relocation of lignin. SE pretreatment is more appropriate as a pre-step to co-processing.5 Lignin content and structure in bamboo is an important factor limiting hydrolysis efficiency.14 Lignin served as a physical shield covering hemicellulose and cellulose chains, limiting the conversion of carbohydrates. Moreover, therefore, an efficient chemical pretreatment is necessary for further improvement of glucose yields due to its simple operation and high efficiency.
Alkaline sulfite pretreatment can significantly improve enzyme accessibility to cellulose by altering the chemical composition, ultrastructure and porosity of the substrate. This method is reported to be an effective lignocellulosic solubilization process that reduces the hydrophobicity of lignin by sulfonation, thereby increasing the hydrolyzability of the substrate. As already mentioned, lignocellulosic materials after SE pretreatment appeared curly fold, loose and messy. Alkaline sulfite pretreatment is suitable for non-woody lignocellulosic biomass with a loose structure.15 Therefore, coupling SE pre-treatment with alkaline sulfite post-treatment of bamboo is a good choice to enhance enzymatic hydrolysis. In recent years, GL pretreatment as a method of the alkaline pretreatment process to produce biofuels has been developed.16,17 GL is an alkaline liquid made by dissolving the molten material recovered from the alkali recovery system in water.18 The main components of GL are sodium carbonate and sodium sulfide, with small amounts of sodium hydroxide and sodium sulfite.15 According to the literature, GL pretreatment has some advantages, such as selective lignin removal and little polysaccharide lose without producing toxic byproducts.19–21
In this study, aiming at improving enzymatic hydrolysis of bamboo, low severe steam explosion and GL-sulfite were combined for the pretreatment of bamboo. The objective of this study was to compare the sugar recoveries of bamboo pretreated by different method, and determine the effect of GL-sulfite pretreatment on the chemical composition and enzymatic hydrolysis of substrates. Simultaneously, changes of functions groups of the solid fractions were characterized by Fourier transform infrared spectroscopy (FT-IR).
2 Materials and methods
2.1. Materials
The bamboo sample was obtained from Jiangxi Province, China. The air-dried stems of bamboo were cut into small pieces, and then ground to the nominal sizes of 40- to 60-mesh. The powder was extracted with ethanol and water using the Soxhlet apparatus for 10 h to remove the waxes and the extract was dried at 105 °C to constant weight before use.
GL was supplied by Chenming Group (Shandong, China). The supernatant of GL was obtained with an overnight precipitation. The main component of GL was sodium carbonate (75.2 ± 0.25 g L−1), making up 75% of the liquid. The sodium hydroxide content was 23.04 ± 0.25 g L−1. There were also other metal elements in GL, such as iron and calcium. The content of iron (1.14 ± 0.08 g L−1) was greater than that of calcium (0.39 ± 0.03 g L−1).
All other chemicals were of analytical grade and were purchased from Beijing Chemical Reagent Company, China, unless otherwise noted.
2.2. Steam explosion (SE) pretreatment
SE pretreatment was carried out in a batch pilot unit equipped with a 7.5 L reaction vessel and exposed to saturated steam at 224 °C for 4 min. After exposure to the saturated steam, a ball valve at the bottom of the reactor was suddenly opened to bring the reactor rapidly to atmospheric pressure. After pretreatment, the biomass was carefully collected and washed with distilled water until the pH was neutral. Then, pretreated materials were stored at 4 °C before enzymatic hydrolysis.
2.3. Pretreatment with combined green liquor and sulfite (GL-sulfite)
GL-sulfite pretreatment was carried out in a 200 mL polytetrafluoroethylene (PTFE) reactor after steam pretreatment. Briefly, 10 g of dried SE treated bamboo was mixed directly with 150 mL of water containing different GL loadings (3–12 mL per g-DS (dry substrate)) and 6 g of sodium sulfite was added to the mixtures. Then the reactor was loaded in a large stainless steel tank and fixed well. The system including reactor and stainless steel tank was placed in a chamber equipped with a shaft. The whole system was heated to desired temperature (e.g. 80 °C, 100 °C and 120 °C) with an average rate of 5 °C min−1. Moreover, one control pretreatment without sodium sulfite (with only addition of 7.5 mL per g-DS GL) were also performed at 100 °C. After 1 h, the insoluble residues were collected by filtration and washed with distilled water until neutral pH. Some of the washed samples were dried in an oven at 105 °C for 6 h to evaluate the yield.
The composition percentage of pretreated bamboos based on the initial bamboos can be obtained by multiplying the yield by the percentage of each component of GL pretreated bamboos.
2.4. Enzymatic hydrolysis
Enzymatic hydrolysis was performed in 100 mL flask using 50 mL of 0.05 M sodium acetate buffer (pH 4.8) at 48 °C. The flasks were agitated at 150 rpm in a rotary shaker (Certomat-R, B-Braun, Germany) for 120 h. Never-dried materials was added at concentration of 2.5% (w/v) on a dry basis. Celluclast 1.5L (Sigma Co., St. Louis) was supplemented with Novozym 188 (Sigma Co., St. Louis) in activity ratio of 1 FPU to 1.5 IU. For each sample, enzymatic hydrolysis was stopped by plunging the tube into boiling water for 5 min and then cooling it to room temperature in water. The mixture was then centrifuged at 5000 rpm for 5 min at 25 °C and the supernatant was collected for glucose analysis by a high-performance liquid chromatography system (Waters 2695e, USA) using an Aminex HPX-87P (Bio-Rad) at 85 °C. The injection volume of the sample was 10 μL and water was used as the eluent, at a flow rate of 0.6 mL min−1. The enzymatic hydrolysis experiments were duplicated (standard deviations were in all cases < 3%) and average results are given. The glucose yield was calculated by assuming that 1 g of cellulose present in the liquid theoretically renders 1.11 g of glucose.22
2.5. Scanning electron microscopy (SEM) and energy-dispersive X-ray (EDX) analysis
EDX is a micro-analytical technique conventionally used in SEM for the local determination of chemical elements in solid samples.23 The freeze-dried samples (untreated and pretreated bamboo) were coated with gold–palladium in a sputter coater (E-1010, HITACHI, Japan). The morphological structure was observed by scanning electron microscopy (SEM) (S-3400N, HITACHI, Japan). The surface chemical composition was determined with an energy-dispersive X-ray analysis (EDX, GENESIS 2000, USA) system attached to the electron microscope.
2.6. Fourier transform infrared spectroscopic analysis
Fourier transform infrared (FTIR) spectroscopy is a vibrational spectroscopy that is useful in the study of a wide range of lignocellulosic material chemical processes.24 The structure characteristic of samples was analyzed by FT-IR. The dried samples mixed with KBr (spectroscopic grade) were pressed uniformly against the diamond surface using a spring-loaded anvil. FT-IR spectrum was recorded between 4000 and 400 cm−1 with four scans recorded at a resolution of 4 cm−1.
2.7. Surface tension test
Surface tension, a specific form of interfacial tension, refers to the tension between gas–liquid or gas–solid interfaces where one phase is the gas phase.25,26 The surface tension of pretreatment liquor samples was determined according to Jian's method27 using an automatic tension meter (model JK99B, Zhongchen digital technology equipment Co, Ltd, Shanghai, China) at 20 °C in aqueous medium.
3 Results and discussion
3.1. Effect of pretreatment methods on chemical composition of bamboos
The untreated bamboo was composed of 45.41% glucan, 17.00% xylan, 26.01% Klason lignin, and 1.16% ash (Table 1). It was noticed that the carbohydrate (glucan and xylan) of bamboo accounted for 62.41% of dry substrate. These values are important since for biorefinery concept, raw materials with high glucan and xylan contents are preferable candidates for using during bio-ethanol production. Lignin contributes significantly to biomass recalcitrance by physically limiting the access of enzymes to carbohydrates, and this could be partially overcome by applying a pretreatment step to directly target lignin.28 Therefore, SE pretreatment was explored to destroy the tight three-dimensional ultrastructure of bamboo. According to the chemical components analysis, it was found that the content of celluloses (represented by glucan) in SE-pretreated substrates was enhanced from 45.41% to 60.33%. SE pretreatment promoted hemicellulose degradation of bamboo. The xylan content decreased from 17.00% to 7.34%.
Table 1 Chemical composition of untreated, SE-treated and SE–GL treated bamboo samples
Samples |
Components |
Yielda/% |
Klason lignin/% |
Glucan/% |
Xylan/% |
Ash/% |
The yield was calculated based on the original weight of raw bamboo. |
Untreated |
26.01 |
45.41 |
17.00 |
1.16 |
98.01 |
SE |
26.47 |
60.33 |
7.34 |
0.42 |
73.02 |
SE–GL |
14.52 |
70.64 |
8.91 |
0.56 |
54.75 |
3.2. Effect of GL loading on chemical composition of bamboos
The retentions of glucan, xylan, lignin, and ash in the residue based on the original weight of the SE-treated bamboo, as well as the pulp yield after different GL-sulfite pretreatments, were shown in Fig. 1. After GL-sulfite pretreatment, the solids yield dropped with the increase of GL and temperature, with the pulp yields being in the range of 59.5–78.5%.
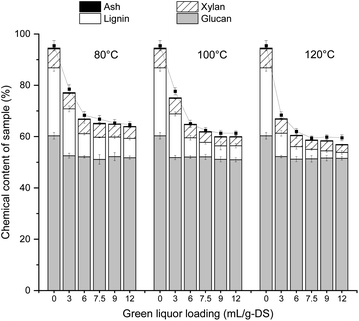 |
| Fig. 1 The effects of green liquor (GL) loading and pretreatment temperature on the solids yield and retention of various components based on the original weight of the SE-treated bamboo residues during GL-S pretreatment of 10.0% substrate. | |
GL pretreatment could efficiently remove lignin in the most lignocellulosic materials examined.29,30 However, most of GL pretreatments were performed at a relative high temperature,20,30,31 which are not conducive to industrial operations. Thus, relatively low temperatures (80 °C, 100 °C, and 120 °C) were chosen for GL-sulfite pretreatment in this study. These mild reaction conditions could help to reduce costs and byproduct generation. According to Fig. 1, the content of lignin decreased sharply with an increase in the amount of GL from 3 to 7.5 mL per g-DS. Further increasing the GL amount did not improve the lignin removal. High temperature could enhance lignin removal during pretreatment. About 71.6% of lignin was removed under the condition of 12 mL per g-DS at 80 °C, whereas 91.2% of lignin was eliminated at 120 °C. During pretreatment, the content of xylan and glucan in the solid fraction was also reduced. Unlike lignin, the reduction of glucan and xylan in the solid fraction was very slow. These results indicated that GL-sulfite pretreatment can effectively remove lignin from bamboo, which can effectively compensate for the deficiency of steam pretreatment. Increasing the temperature also improved the removal of lignin, accompanied by the degradation of polysaccharides. The lignin content of GL-sulfite treated bamboos was 12.90%, 9.05%, and 6.23%, when GL-sulfite pretreatment was performed at 80 °C, 100 °C, and 120 °C with a GL loading of 7.5 mL per g-DS for 1 h. With further increase of GL loading, only a slight decrease in lignin content was obtained. Therefore, pretreatment with a GL loading of 7.5 mL per g-DS was used for the following enzymatic saccharification study.
3.3. Effect of GL-sulfite pretreatment on the enzymatic hydrolysis of bamboos
We examined saccharification yields from bamboo after different pretreatment. Fig. 2 illustrates the effect of GL-sulfite pretreatment on enzymatic saccharification when the pretreatment was performed at 80 °C, 100 °C, and 120 °C with a GL loading of 7.5 mL per g-DS for 1 h. SE-treated bamboo after hydrolysis had a glucose yield of 54.6%. It seems that GL-sulfite pretreatment was effective for delignification. In the early phase of enzymatic hydrolysis, the glucose yield of GL-sulfite bamboo increased sharply. It was found that the higher pretreatment temperature led to the higher efficiency of enzymatic hydrolysis. It suggested that GL-sulfite pretreatment was effective to ease bamboo decomposition, leading to a good hydrolysis performance in the early stage of hydrolysis. After 120 h of hydrolysis, the yield from GL-sulfite bamboo at 80 °C was 71.3%, which was significantly higher than that obtained from SE-bamboo (54.6%). GL-sulfite treated bamboo at 120 °C showed the highest glucose yield (89.6%) after 120 h of hydrolysis. Cellulases need to bind to the surface of cellulose to initiate hydrolysis. Lignin is generally considered to be an inhibitor to the enzymatic hydrolysis of lignocellulosic substrates. Lignin physically blocks the accessibility of cellulose, non-productively adsorbs cellulases, and sterically hinders the enzymatic hydrolysis of cellulose.32,33 Therefore, lignin removal could improve glucose yield efficiently. It can be seen that GL-sulfite pretreatment can significantly increase the enzymatic efficiency of steam-treated bamboo.
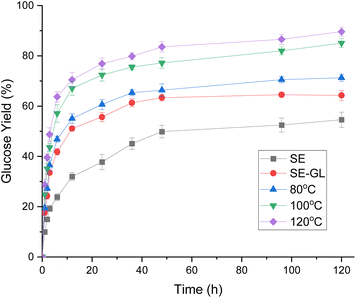 |
| Fig. 2 Glucose yields resulting from substrate pretreated with GL-sulfite at different temperature. The enzymatic hydrolysis was performed at 48 °C, pH 4.8 with a substrate consistency of 2.5% (w/v) using a shaking incubator at 150 rpm. | |
Interestingly, glucose yields of GL-sulfite pretreated substrates at 100 °C and 120 °C continued to increase in 120 h without reaching a platform. In general, the main reason limiting the rate of hydrolysis is the ineffective adsorption between enzyme and lignin. Especially in the late stage of hydrolysis, lignin gradually accumulates and significantly reduces the enzyme activity. However, in this study, enzymatic hydrolysis of GL-sulfite treated substrates continued up to 120 h, indicating that the lignin in the substrate was more hydrophilic.
3.4. Fourier transform infrared
FT-IR analysis demonstrated some peaks related to cellulose, hemicellulose, and lignin, which can further illustrate the component changes of the treated samples. FT-IR spectra of bamboo samples after different treatment are shown in Fig. 3. It can be seen that the cellulose structure did not change remarkably, except for some characteristic groups and bounds, especially for the spectra of R2 and R3.
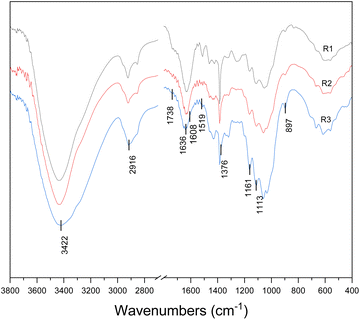 |
| Fig. 3 FT-IR spectra of SE-treated bamboo after GL pretreatments (R1: SE-treated residues; R2: SE–GL-treated residues; R3: SE–GL-sulfite-treated residues). | |
All pretreatments induced obvious changes in the 1738 cm−1 bound which is the characteristic peak of carbonyl band ascribed to hemicellulose. The intensity of the peak was decreased sharply in the spectra of R2 and R3, suggesting the partial degradation of ester bond of the hemicellulose in the cellulose-rich fractions. When bamboo was pretreated in an alkaline environment, hemicellulose containing acetyl groups was hydrolysed easily, resulting in the disappearance of the C
O stretching vibration. The band at 1608 cm−1 and 1519 cm−1 is associated with the aromatic skeletal vibration of lignin. Compared to the SE-treated bamboo, the signal of R2 and R3 was weaker and almost disappeared, which suggested that the lignin decreased sharply with GL-sulfite pretreatment followed by steam explosion. The result was well in line with the chemical composition analysis. The signal at 1161 cm−1 and 897 cm−1 arises from C–O–C stretching of the β-(1,4)-glycosidic linkages. The signal near 3422 cm−1 represents –OH stretching, and 2916 cm−1 is indicative of C–H stretching. The C–H bending occurs at 1376 cm−1. The peak at 1113 cm−1 is indicative of associated OH group from cellulose and hemicellulose.
3.5. Morphological changes
The microstructures of untreated bamboo (R0), SE-pretreated bamboo (b), and SE–GL-pretreated bamboo (c) and SE–GL-S pretreated bamboo (d) detected by SEM were indicated in Fig. 4. The overall surface of untreated bamboo was smooth and fibre possessed a compact structure. There are many fibre bundles in the untreated bamboo. SE pretreatment slightly damaged the fibre surface of bamboo. Some small jagged shapes can be seen on the fibre surface. However, SE pretreatment does not open the dense structure of the bamboo fibres, so glucose yield of SE-pretreated bamboo was only 54.6%. To improve glucose yield, GL pretreatment was employed. The fibre structure pretreated with GL was disrupted greater than that of pretreated with SE. After GL pretreatments, parallel stripes appeared on the surface of fibre (R2). The addition of sulfite in GL pretreatment made the compact fibre porous and slightly peeled. This may result in an increased contact level between cellulose and cellulase.
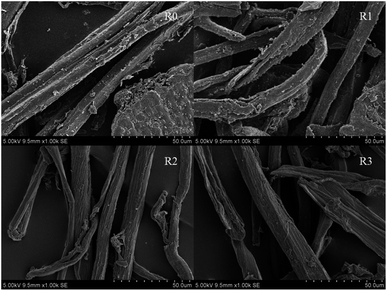 |
| Fig. 4 SEM images of bamboo samples. R0: untreated, R1: SE-pretreated, R2: SE–GL-pretreated, and R3: SE–GL-S-pretreated. All images were taken at 1000× magnification. | |
Energy disperses spectroscopy (EDS) analysis revealed a change in elementary composition on the surface of bamboo before and after pretreatment. The O/C expresses the surface lignin content of the substrate. Research have showed that the theoretical O/C values of cellulose and lignin were 0.83 and 0.33, respectively. Therefore, lower lignin content has a higher O/C value. Based on Table 2, GL-sulfite pretreatment increased the O/C ratio, indicating that the surface lignin was removed. The O/C ratio on the surface of GL-sulfite pretreated substrate (0.44) was higher than that of SE-treated substrate (0.37). Thus, GL-pretreatment could remove more surface lignin.
Table 2 Atomic composition (%) on solid surface of SE-treated and GL-sulfite-treated bamboo
Samples |
C/% |
O/% |
N/% |
O/C |
1.25 MPa |
66.8 ± 1.8 |
24.9 ± 0.8 |
6.1 ± 0.1 |
0.37 |
GL-sulfite |
63.1 ± 1.2 |
28.1 ± 0.2 |
6.4 ± 0.2 |
0.44 |
3.6. Surface tension analysis of pretreatment liquor
Lignosulfonate is a surfactant which is beneficial for reducing the surface tension.34 The surface tensions of pretreatment liquor were assayed to semi-quantify the lignosulfonate content dissolved during pretreatment. Fig. 5 showed the surface tension of pretreatment liquor. Differences in surface tension among various pretreated samples were significant. The surface tensions of pretreatment liquor from GL-sulfite pretreatment are lower than that from GL pretreatment which indicated that lignosulfonate is dissolved in the pretreatment liquor during GL-sulfite pretreatment. Lignosulfonate dissolved in the liquor not only facilitate the impregnation of chemical reagents, but also capture some of the lignin released into the liquid phase, thus reducing the amount redeposited on biomass.35 This could be supported by the compositional analyses (Fig. 1). More lignosulfonate formation (GL-S pretreatment at 120 °C) made higher lignin removal and lower solids yield. The surface tension decreased with increasing temperature. This may be attributed to the fact that the sulfonation reaction of lignin to lignosulfonates occurs mainly under high temperature conditions.
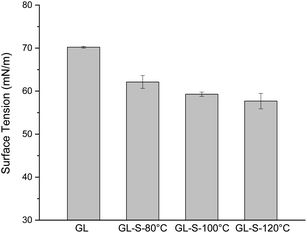 |
| Fig. 5 Surface tension of pretreatment liquor (GL: GL pretreatment without sulfite addition; GL-S-80 °C: GL-sulfite pretreatment at 80 °C; GL-S-100 °C: GL-sulfite pretreatment at 100 °C; GL-S-120 °C: GL-sulfite pretreatment at 120 °C). | |
3.7. Mass balance of glucose production
Fig. 6 shows the mass balance from raw bamboo until enzymatic hydrolysis for the three pretreatments. The mass balances of the process have shown that the best performance was SE–GL-S pretreatment, followed by SE–GL pretreatment. It should be noted that similar cellulose yield was obtained after SE–GL and SE–GL-S pretreatments. However, substrates from SE–GL-S pretreatment showed high hydrolysis ability. The cellulose content in 100 g raw bamboo was about 45.4 g. SE–GL-S pretreatment enabled the obtainment of glucose content of 37.6 g from 100 g bamboo.
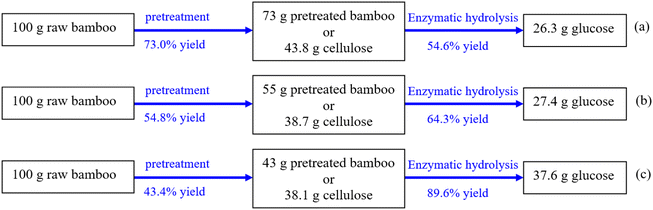 |
| Fig. 6 Mass balance of glucose production (a) SE pretreatment; (b) SE–GL pretreatment; (c) SE–GL-S pretreatment. | |
4 Conclusions
An innovative and efficient pretreatment method using GL-sulfite was proposed to enhance enzymatic hydrolysis of SE-treated bamboo. GL-sulfite has been proven to degrade lignin in bamboo, with a lignin removal of 91.3% under pretreatment conditions of 120 °C and 1 h. Enzymatic hydrolysis was performed on the pretreated samples, resulting in glucose yield of 89.6%. Lower content of lignin, higher hydrophilicity, and more porous structure of GL-sulfite treated bamboo contributed to effectively improving glucose production. The GL-sulfite pretreatment is an innovative high-efficiency technology for bamboo biorefinery.
Author contributions
All authors have contributed to the manuscript. Yang Xing: formal analysis, investigation, validation, visualization, writing – original draft. Hui Li: writing – review and editing. Yushen Jin: writing – review and editing. Jianxin Jiang: conceptualization, resources. Bing Shao: funding acquisition, project administration.
Conflicts of interest
There are no conflicts to declare.
Acknowledgements
We are grateful to Beijing Forestry University for providing pretreatment equipment and for help with HPLC analyse.
References
- P. Padil, M. D. Putra, M. Hidayat, R. S. Kasiamdari, A. Mutamima, K. Iwamoto, M. A. Darmawan and M. Gozan, RSC Adv., 2023, 13, 21403–21413 RSC.
- G. Wu, B. Alriksson and L. J. Jönsson, RSC Adv., 2023, 13, 20023–20030 RSC.
- P. Feng and Y. Li, World Bamboo Rattan (in Chinese), 2023, 21, 100–103 Search PubMed.
- B. Pang, T. Zhou, X.-F. Cao, B.-C. Zhao, Z. Sun, X. Liu, Y.-Y. Chen and T.-Q. Yuan, J. Cleaner Prod., 2022, 375, 134037 CrossRef.
- X. Li, Y. Shi, W. Kong, J. Wei, W. Song and S. Wang, Energy Rep., 2022, 8, 696–709 CrossRef.
- D. Xin, Z. Yang, F. Liu, X. Xu and J. Zhang, Bioresour. Technol., 2015, 175, 529–536 CrossRef CAS.
- C. Huang, J. Ma, C. Liang, X. Li and Q. Yong, Bioresour. Technol., 2018, 263, 17–24 CrossRef CAS PubMed.
- F. Meng, J. Fan, F. Cui, H. Yang, Z. Shi, D. Wang and J. Yang, Bioresour. Technol., 2023, 383, 129230 CrossRef CAS PubMed.
- H. Peng, H. He, L. Liu, L. Shen, G. Fu, Y. Wan, Y. Liu and L. Hu, Ind. Crops Prod., 2023, 194, 116376 CrossRef CAS.
- L. J. Jönsson and C. Martín, Bioresour. Technol., 2016, 199, 103–112 CrossRef PubMed.
- N. S. Ab Rasid, A. Shamjuddin, A. Z. Abdul Rahman and N. A. S. Amin, J. Cleaner Prod., 2021, 321, 129038 CrossRef CAS.
- M. H. Luciano Silveira, A. R. C. Morais, A. M. da Costa Lopes, D. N. Olekszyszen, R. Bogel-Lukasik, J. Andreaus and L. P. Ramos, ChemSusChem, 2015, 8, 3366–3390 CrossRef.
- F. Wan, C. Feng, K. Luo, W. Cui, Z. Xia and A. Cheng, Trends Food Sci. Technol., 2022, 124, 13–24 CrossRef CAS.
- C. Huang, Y. Zhan, J. Cheng, J. Wang, X. Meng, G. Fang and A. J. Ragauskas, Bioresour. Technol., 2022, 359, 127462 CrossRef CAS.
- Z. Zhou, Y. You, F. Lei, P. Li, J. Jiang and L. Zhu, Fuel, 2017, 203, 707–714 CrossRef CAS.
- X. Tan, B. Jiang, Y. Yang, D. Min and Y. Jin, Holzforschung, 2017, 71, 99–108 CrossRef CAS.
- Z. Zhou, W. Xue, F. Lei, Y. Cheng, J. Jiang and D. Sun, Ind. Crops Prod., 2016, 90, 100–109 CrossRef CAS.
- P. Mandal, P. Goel, B. Eswaraswamy, V. K. Shahi and S. Chattopadhyay, J. Environ. Chem. Eng., 2022, 10, 107016 CrossRef CAS.
- A. Alam, Y. Wang, F. Liu, H. Kang, S. W. Tang, Y. Wang, Q. Cai, H. Wang, H. Peng, Q. Li, Y. Zeng, Y. Tu, T. Xia and L. Peng, Renewable Energy, 2020, 159, 1128–1138 CrossRef CAS.
- B. Jiang, W. Wang, F. Gu, T. Cao and Y. Jin, Bioresour. Technol., 2016, 199, 181–187 CrossRef CAS PubMed.
- H. Yu, Y. Xing, F. Lei, Z. Liu, Z. Liu and J. Jiang, Bioresour. Technol., 2014, 167, 46–52 CrossRef CAS PubMed.
- Y. Xing, L. Bu, D. Sun, Z. Liu, S. Liu and J. Jiang, Bioresour. Technol., 2015, 193, 401–407 CrossRef CAS PubMed.
- M. Abd Mutalib, M. A. Rahman, M. H. D. Othman, A. F. Ismail and J. Jaafar, in Membrane Characterization, ed. N. Hilal, A. F. Ismail, T. Matsuura and D. Oatley-Radcliffe, Elsevier, 2017, pp. 161–179, DOI:10.1016/B978-0-444-63776-5.00009-7.
- D. Peak, in Encyclopedia of Soils in the Environment, ed. M. J. Goss and M. Oliver, Academic Press, Oxford, 2nd edn, 2023, pp. 510–518, DOI:10.1016/B978-0-12-822974-3.00230-5.
- W. Musial, E. Szewczyk, K. Karlowicz-Bodalska and S. Han, Rom. Biotechnol. Lett., 2015, 20, 10257–10268 CAS.
- Y. Li, J. Shi, X. Zhang, M. Ji, Y. Ni, R. Han, Z. Li, Y. Xiong, J. Tu, D. He and C. Sun, Int. J. Pharm., 2024, 123848, DOI:10.1016/j.ijpharm.2024.123848.
- H.-l. Jian, X.-x. Liao, L.-w. Zhu, W.-m. Zhang and J.-x. Jiang, J. Colloid Interface Sci., 2011, 359, 487–492 CrossRef CAS PubMed.
- C. Huang, X. Jiang, X. Shen, J. Hu, W. Tang, X. Wu, A. Ragauskas, H. Jameel, X. Meng and Q. Yong, Renewable Sustainable Energy Rev., 2022, 154, 111822 CrossRef CAS.
- H. Gao, Y. Wang, Q. Yang, H. Peng, Y. Li, D. Zhan, H. Wei, H. Lu, M. M. A. Bakr, M. M. Ei-Sheekh, Z. Qi, L. Peng and X. Lin, Renewable Energy, 2021, 175, 1069–1079 CrossRef CAS.
- T. Liu, P. Wang, J. Tian, J. Guo, W. Zhu, F. Seidi, Y. Jin, H. Xiao and J. Song, Bioresour. Technol., 2022, 363, 127904 CrossRef CAS PubMed.
- H. T. T. Pham, N. P. Nghiem and T. H. Kim, Energy, 2018, 157, 894–903 CrossRef CAS.
- C. Cai, C. Zhang, N. Li, H. Liu, J. Xie, H. Lou, X. Pan, J. Y. Zhu and F. Wang, Renewable Sustainable Energy Rev., 2023, 183, 113445 CrossRef CAS.
- C. A. Mooney, S. D. Mansfield, M. G. Touhy and J. N. Saddler, Bioresour. Technol., 1998, 64, 113–119 CrossRef CAS.
- Z. J. Wang, T. Q. Lan and J. Y. Zhu, Biotechnol. Biofuels, 2013, 6, 9 CrossRef CAS PubMed.
- Q. Qing, B. Yang and C. E. Wyman, Bioresour. Technol., 2010, 101, 5941–5951 CrossRef CAS PubMed.
|
This journal is © The Royal Society of Chemistry 2024 |
Click here to see how this site uses Cookies. View our privacy policy here.