DOI:
10.1039/D4RA01816H
(Paper)
RSC Adv., 2024,
14, 39740-39746
Controllable synthesis of Co/NC catalysts with high-density Co–Nx active sites derived from Co/Zn-ZIF for cyclopropanation†
Received
9th March 2024
, Accepted 22nd October 2024
First published on 17th December 2024
Abstract
Novel Co/NC heterogeneous catalysts were prepared by simply employing self-made Co/Zn-ZIF (zeolitic imidazolate framework) through pyrolysis. The samples were characterized by XRD, XPS, Raman, TEM and BET, and were successfully applied in a cyclopropanation reaction with a yield of 85%. Furthermore, this one-pot synthesized catalyst could be recycled several times without apparent deactivation. The content of Co–Nx active sites could be modified by adjusting the Co/Zn molar ratio of the ZIF precursor. The generation of Co–Nx could be attributed to the evaporation of Zn species, which provides rich micropores.
Introduction
The cyclopropane ring structure exhibits specific bioactivity in many medical materials and has become an important structural unit in pharmaceutical chemistry, attracting great research interest.1–3 Meanwhile, the highly strained energy of the three-numbered ring makes cyclopropane a valuable candidate for the synthesis of high-energy-density fuels. Various synthetic methods for cyclopropanation have been developed, such as Simmons–Smith reaction, diazo-derived cyclopropanation, free carbenes via α-Elimination and Kulinkovich reaction.4–8 Particularly, the cyclopropanation of alkenes with diazo compounds stands out as the most atom-economic strategy.9 However, most studies have employed homogeneous catalysts, such as Fe, Ru, Rh, Co and Cu complexes, leading to problems like difficulty in separation, low reusability and high costs.10–16 To tackle these challenges, developing highly active, recyclable heterogeneous catalysts using inexpensive metal is desirable.
To date, a few reports describe the use of heterogeneous catalysts for cyclopropanation, such as CuO–TiO2/Al2O3, CuNPs–Al2O3, core–shell Cu–Fe NPs and silver/copper foil.17–21 Nevertheless, these catalysts, originating from complex preparation methods, display low catalytic efficiency due to lack of controllable active sites.22–25 The preparation of high-performance heterogeneous catalysts for cyclopropanation calls for a simple method to produce abundant active sites. Recently, a new design involving 3d transition metals and an N-doped carbon system (M–N–C) has garnered attention in materials sciences.26–28 More specifically, engineering abundant active sites via the evaporation of Zn species during the pyrolysis of zeolitic imidazolate frameworks (ZIFs) has generated significant interest for producing more complex microstructures. 29–34 We believe that applying this method to prepare heterogeneous catalysts could increase the number of active sites, leading to better yields in cyclopropanation.35,36 In this paper, we report on Co-based heterogeneous catalysts for cyclopropanation and present an in situ method for the controllable production of Co–Nx active sites on these Co/NC catalysts by adjusting the Co/Zn molar of Co/Zn-ZIFs.
Experimental
Preparation of catalysts
Co@N-doped carbon materials labeled as Cox/NC-T (where x represents the molar ratio and T indicates the calcination temperature), were synthesized using a simple method, as shown in Scheme 1. Co/Zn-ZIFs were synthesized from an aqueous solution at room temperature. Typically, a total of 10 mmol mixture of Zn(NO3)2·6H2O and Co(NO3)2·6H2O, with designed molar ratios of 25
:
75, 50
:
50, 75
:
25 and 100
:
0, was dissolved in 200 mL of methanol. Then, a solution of 80 mmol 2-methylimidazole dissolved in 200 mL of methanol was added to the flask. The brown mixture was stirred continuously for 12 h at room temperature (25 °C). After centrifugation, the product was washed with methanol several times and dried at 80 °C overnight. Then, these Co/Zn-ZIF precursors were annealed under nitrogen flow for carbonization by thermal treatment at 900 °C, and the samples were denoted as Co0/NC-900, Co0.25/NC-900, Co0.50/NC-900, Co0.75/NC-900 and Co1.00/NC-900.
 |
| Scheme 1 Synthesis of Co/NC catalysts. | |
Catalytic tests
The prepared catalyst (10.0 mg) was placed in an oven-dried Schlenk tube evacuated and backfilled with nitrogen (Scheme 2). Solvent 1,2-dichloroethane (2 mL) was added, followed by styrene (2.50 mmol) and a stock solution of ethyl diazoacetate (EDA, 0.5 mmol). The mixture was heated at 60 °C under an N2 atmosphere; then, the cyclopropanation reaction lasted for 4 h with stirring. After the reaction, the catalyst was separated by centrifugation, and enantiomeric excess and yields were determined by chiral gas chromatography (GC) using an AgilentJ&WDB-35 column on a Shimadzu GC-2014C instrument equipped with an FID detector. The flow rate was set to 3.0 mL min−1 for all tested compounds. The injector was in split mode 100
:
1, the injection volume was 1 μL and the injector temperature was set to 100 °C, while the detector temperature was set to 280 °C. The conditions for separating individual product enantiomers can be found in the compound characterization section.
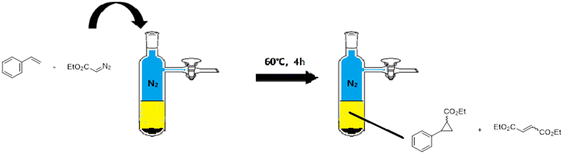 |
| Scheme 2 Catalytic tests of Co/NC catalysts. | |
Catalyst characterisation
X-ray powder diffractometer (XRD, Rigaku D/Max 2500 VB2 + PC) with 2θ range from 10° to 90° characterized the catalyst powder. Raman spectra were recorded on a LabRAM HR Evolution (Renishaw Invia Raman, UK, 532 nm, 1 cm−1, 100 s). X-ray photoelectron spectroscopy (XPS, Pekin-Elmer PHI-1600) characterized the surface elemental composition and valence using an X-ray source of mono-chromatic Al Kα (1486.6 eV) 150 W (spot size 500 μm). Transmission electron microscopy (TEM, FEI Tecnai-G2F20) characterized the microstructure, combined with Energy Dispersive X-Ray Spectroscopy (EDS) to obtain elemental mapping within the micro-region of the material. The nitrogen adsorption–desorption was performed using a Micromeritics ASAP 2020 at 77 K. Brunauer–Emmett–teller (BET) equiv. was used to calculate the final specific surface area.
Results and discussion
Characterisation of catalysts
The crystal structure investigation of products with different molar ratios of Zn/Co was conducted using powder X-ray diffraction (XRD). Fig. 1a illustrates the results, revealing broad diffraction peaks at 2θ of 25.4° corresponding to the graphitic carbon (002) in all samples.37 Notably, no discernible peaks characteristic of zinc or zinc compounds were evident in the patterns, indicating the effective removal of Zn through evaporation during pyrolysis at 900 °C. By increasing the cobalt content in Zn/Co-ZIF, distinct diffraction peaks associated with metallic Co became evident in the Co/NC samples. Specifically, the peaks at 44.2°, 51.5° and 75.8° were well-indexed to the (111), (200), and (220) planes of fcc-structured metallic Co.38 According to the Scherrer equation, the calculated diameters of metallic Co in Co0.25/NC-900, Co0.50/NC-900, Co0.75/NC-900, and Co1.00/NC-900 were 5.24 nm, 19.6 nm, 21.2 nm, and 27.9 nm, respectively. When the molar ratios of Co content in Co/Zn-ZIF surpassed 50%, there was a significant increase in the size of Co metal particles in the Co/NC materials. This phenomenon was further validated through TEM images, suggesting that a higher cobalt proportion (beyond 50%) triggers the thermal polymerization of metallic cobalt during pyrolysis, ultimately diminishing the catalyst's reaction activity.
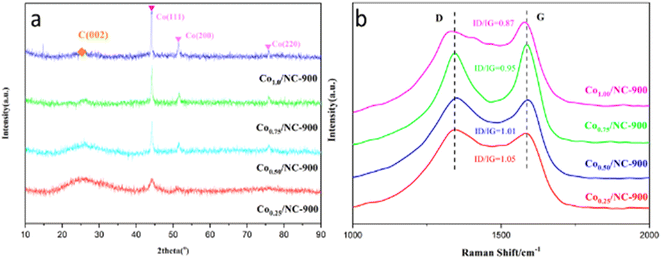 |
| Fig. 1 (a) XRD pattern of Co/NC catalysts and (b) Raman spectra of the Co/NC catalysts. | |
The Raman spectra of Co/NC samples are presented in Fig. 1b, revealing the characteristic G band (at 1585 cm−1) associated with graphitic carbon, and the D band (at 1353 cm−1) indicates disordered carbon.39 The relative peak intensity ratio of D to G (ID/IG) serves as a measure of the graphitization degree of carbon materials. The ID/IG ratios for these samples (Co/Zn, 0.25
:
0.75, 0.5
:
0.5, 0.75
:
0.25, 1.0
:
0) are observed to be 1.05, 1.01, 0.95, and 0.87, respectively. This trend suggests that an increase in Co content and a decrease in Zn content result in the generation of more graphitic carbon and fewer defects. This phenomenon may be attributed to the porous structure formed through the high-temperature evaporation of metallic zinc during the process.40
The morphologies and microstructures of the samples were further tested using TEM. The TEM images of Co/NC are shown in Fig. 1a–e. There are no obvious lattice fringes, suggesting the low crystallinity of carbon. Meanwhile, no obvious metal Co NPs were observed in Co0/NC-900 and Co0.25/NC-900. When the content of Co increases to 50%, several Co metal particles are clearly visible, which agrees with the results of XRD. A high-resolution TEM image of an individual Co NP shows that the Co NP is wrapped by graphitized NC nanosheets (Fig. 2f), which can be reasonably explained by the fact that the sintered Co metal nanoparticles are covered by a graphite layer produced by carbonization. The lattice spacing of the Co0.50/NC-900 was 0.24 nm, which was in accordance with the (111) planes of metallic Co fcc crystals. No lattice fringes ascribed to metal oxide of Co are found, which is in accordance with the result of XRD. Another group of fringes with d spacings 0.34 nm matched well with the (002) planes of graphitic carbon.41
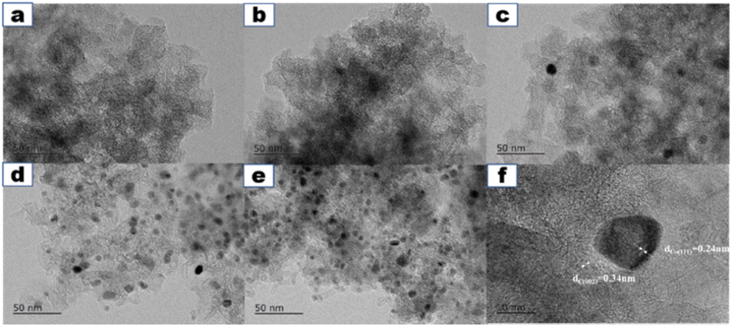 |
| Fig. 2 (a–f) HRTEM images of Co0/NC-900, Co0.25/NC-900, Co0.50/NC-900, Co0.75/NC-900 and Co1.00/NC-900; (f) particle Co size distributions of Co1.00/NC-900. | |
As depicted in Fig. 3, the related elemental maps show the presence of Co, N, and O on the carbon support. The elemental mapping images reveal the homogeneous distribution of Co, C, and N elements, and many microstructures in Fig. 3a with the Co atoms are surrounded by nitrogen atoms, which shows the presence of dispersed Co–Nx clusters at the nitrogen-doped carbonaceous support.
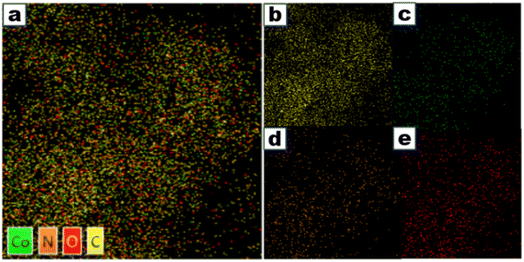 |
| Fig. 3 (a) EDS and elemental mapping of Co0.50/NC-900, and (b–e) the distribution of the C, Co, N, and O elements. | |
XPS was further applied to explore the composition of surface elements and the chemical states of Co/NC samples. A typical XPS survey of the as-obtained composites demonstrates the presence of C, N, O and Co elements in the samples, as shown in Table 1. The results of Co0.75/NC-900 and Co1.00/NC-900 with N and Co content on the surface were reduced significantly when the Co/Zn ratio increased. However, XRD detection confirms a large diameter cobalt metal, which means that the Co content on the surface becomes metallic cobalt in bulk by thermal polymerization.
Table 1 Texture properties of Co/NC catalysts
Catalyst |
C [at%] |
N [at%] |
O [at%] |
Co [at%] |
Co0.25/NC-900 |
81.55 |
10.77 |
6.65 |
0.74 |
Co0.25/NC-900 |
79.72 |
11.71 |
7.57 |
0.94 |
Co0.25/NC-900 |
87.08 |
7.64 |
4.81 |
0.28 |
Co0.25/NC-900 |
95.33 |
0.20 |
4.33 |
0.14 |
As shown in Fig. 4a, an additional peak at 780.8 eV in the Co 2p spectrum was observed, corresponding to Co–Nx. The binding energies of samples Co/NC located at 782.3 eV and 799.2 eV correspond to Co2+ 2p3/2 and Co2+ 2p1/2, respectively.42 The shake-up satellite peaks at around 5 eV above the main peaks can be further proved by the presence of surface Co2+ species, such as Co–O.36 The Co–Nx peak became more dominant and reached the maximum with an increase in the Co/Zn molar ratio to 1
:
1. Then, excessive Co content resulted in a decrease in the Co–N component. When the Co/Zn molar ratio increased, the peaks situated at the binding energies of 778.3 eV and 793.7 eV were observed, which can be consistent with Co 2p3/2 and Co 2p1/2 of metallic Co, respectively.
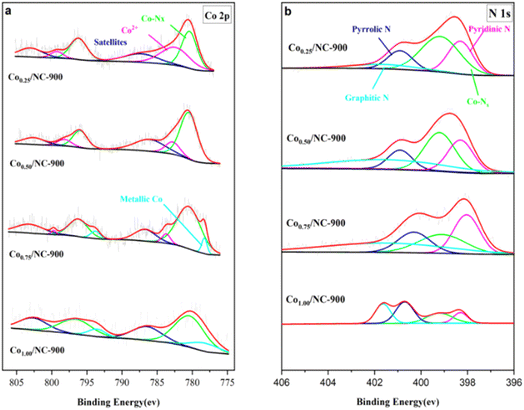 |
| Fig. 4 XPS spectra for the Co/NC catalysts: (a) Co 2p spectrum and (b) N 1 s spectrum. | |
Fig. 4b illustrates the N 1s XPS spectrum, revealing intriguing details about the composition. An additional peak, discernible at 399.2 eV, is identified as Co–Nx content within the N 1s spectrum, mirroring a similar trend observed in the Co 2p spectrum. Moreover, the N 1s spectra for all samples undergo deconvolution, unveiling distinct peaks at 398.3 eV, 400.8 eV, and 401.6 eV, which correspond to pyridinic N, pyrrolic N, and graphitic N, respectively.43 Notably, the Co0.50/NC-900 catalyst exhibits the highest percentage of Co–Nx, aligning with its notable activity in the cyclopropanation reaction. Conversely, as the Co content surpasses 50%, there is a noticeable reduction in Co–Nx content. This decline is attributed to the thermal aggregation of cobalt components, leading to the formation of metal particles. Catalysts with lower Co–Nx content demonstrate diminished activity, emphasizing the pivotal role of Co–Nx content as the active site for cyclopropanation Table 3.
The N2 gas adsorption–desorption isotherm and the corresponding pore size distribution curve of Co/NC-900 are illustrated in Fig. 5. Previous studies show that the ligands can be converted into porous nitrogen-doped carbon materials during the carbonization process, while others decompose into small molecules, such as NH3 gas; simultaneously, the Co2+ and Zn2+ ions are reduced in situ to metallic Co and Zn NPs.40 Then, Zn was removed during pyrolysis at 900 °C by evaporation. The formation of a porous structure is related to the evaporation of Zn at a high temperature, which is beneficial to the transmission of NH3 molecules and promotes the contact between self-generated NH3 and tiny amounts of Co particles to form Co–Nx species. As shown in Table 2, when the content of Co is increased by over 50%, less evaporation of Zn content causes a reduction in the pore size and pore volume, and the thermal polymerization of Co metal particles destroys the original high-surface-area zeolite structure of the ZIF precursor, which means that the surface areas of the catalysts decrease significantly.
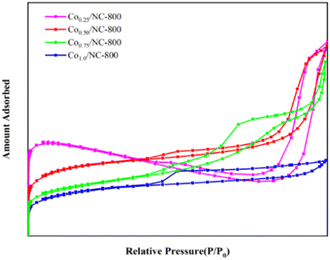 |
| Fig. 5 Nitrogen adsorption–desorption isotherms of Co/NC catalysts. | |
Table 2 Texture properties of Co/NC catalysts
Catalyst |
SBET (m2 g−1) |
VP (cm2 g−1) |
dP (nm) |
Co0.25/NC-900 |
81.55 |
10.77 |
6.65 |
Co0.25/NC-900 |
79.72 |
11.71 |
7.57 |
Co0.25/NC-900 |
87.08 |
7.64 |
4.81 |
Co0.25/NC-900 |
95.33 |
0.20 |
4.33 |
Table 3 Optimization of Co/NC catalysed cyclopropanation of styrene and EDA
The above characterization result shows that it is a feasible method to achieve the controllable Co–Nx content in Co/NC by precisely adjusting the molar ratio of the Co/Zn species in the Co/Zn-ZIF precursor. A lower Co/Zn ratio (less than 50%) in Co/Zn-ZIF precursor could inhibit the thermal polymerization of metallic cobalt, then promote the generation of active components (Co–Nx) in Co/NC catalyst, and is also beneficial for improving the porosity and specific surface area of the catalyst.
Evaluation of the catalyst for cyclopropanation
The Co/NC catalysts of the cyclopropanation activity of Co/NC catalysts were studied through the cyclopropanation of ethyl diazoacetate (EDA) and styrene. All the experiments were performed at 60 °C with 5 mol% of catalyst in 1,2-dichloroethane, containing 5 equiv. of olefin (2.50 mmol) and 1 equiv. of EDA (0.5 mmol). The activity of Co/NC catalysts was compared in the cyclopropanation of styrene conducted under identical conditions. The results show that the Co-ZIF precursor and Co0/NC-900 did not have cyclopropanation catalytic activity at all because the yield of the product is 0. The catalytic activity increased with an increased amount of cobalt. The Co0.50/NC-900 catalyst results in the highest yield (85%, Table 1). However, when the ratio of Co is over 50%, the Co–NC catalyst shows a declined activity. This could be related to a decrease in the specific surface area of the Co–NC catalyst and a decrease in the Co–Nx content on the surface.
However, when we use the Co/NC catalyst prepared by applying the impregnation method in this reaction, the Co/NC catalyst shows low activity significantly. By treating these Co/NC catalysts at different calcination temperatures, the Co0.50/NC-550 catalyst increases its yield to 33%, though its activity is remains much lower than that of MOF-derived Co/NC catalysts.
Through systematic adjustments in the olefin-to-EDA ratio, we conducted a comparative analysis between MOF-derived Co/NC and Fe/NC catalysts (Table 4). The findings indicate that under conditions where olefins are in excess, the Co–NC catalyst exhibits slightly higher activity than its Fe–NC counterpart, with both demonstrating similar selectivity. However, as the ratio of EDA increases, a substantial decrease in both activity and selectivity is observed for Fe–NC, while the Co–NC catalyst maintains remarkable performance in both aspects. This notable difference is likely attributed to the Co(III)-carbene intermediate state of the catalyst, and a hypothesis is further supported by a detailed comparison of the Co–Nx and Fe–Nx complexes. The sustained high activity and selectivity of the Co–NC catalyst under varying olefin-to-EDA ratios underscore the significance of the Co(III)–carbene intermediate state in influencing catalytic performance, providing valuable insights into the superior behavior of Co–NC compared to Fe–NC in these experimental conditions.
Table 4 Catalytic performance for the cyclopropanization of Fe and Co catalysts
Stability and recyclability
To demonstrate the practical utility of this catalyst, scalability and recyclability were studied.44–46 The model reaction was successfully scaled up to 10-fold without significant variations in activity and selectivity compared to the small-scale run. A slight decrease in the activity was observed after the 5th run (Scheme 3). ICP analysis of the solution showed a negligible (ca. 0.1%) loss of cobalt from the catalyst, which means that the Co/NC catalyst is a real heterogenous catalyst.
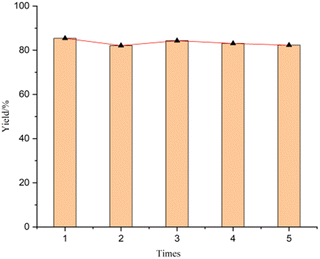 |
| Scheme 3 Recycling of Co/NC catalyst for 5 runs. | |
Conclusions
In summary, we present the first Co-based heterogeneous catalyst derived from Co/Zn-ZIF by high-temperature pyrolysis. These Co/NC catalysts were characterized and applied in the cyclopropanation reaction of diazo compounds with a good yield. Furthermore, the catalysts could be easily recovered and reused at least five times without obvious deactivation. Notably, by increasing the Zn content in a molar ratio of Co/Zn of the ZIF precursor, the Co–Nx active sites were effectively regulated, which significantly improved cyclopropanation activity. This simple strategy was developed to regulate active sites, which could contribute to adjusting the activity of catalysts for typical organic reactions with sluggish kinetic processes.
Data availability
All relevant data are within the manuscript and its additional files.
Author contributions
Xin Yue: conceptualization, formal analysis, writing – original. Jiangwei Li: writing – review & editing, Chunying Li: data curation, formal analysis. Zhixuan Wang: visualization, investigation. Yongmei Du: investigation. Daoan Sun: funding acquisition. Hui Ma: investigation. Jian Lu: resources.
Conflicts of interest
There are no conflicts to declare.
Acknowledgements
We thank Specialized National Science Foundation of China (GNTQXL) for financial support.
Notes and references
- J. M. Fraile, B. García, J. I. García, J. A. Mayoral and F. Figueras, Stud. Surf. Sci. Catal., 1997, 108, 571–578 CrossRef CAS.
- L. A. Wessjohann, W. Brandt and T. Thiemann, J. Chem. Rev., 2003, 103, 1625–1648 CrossRef CAS PubMed.
- C. J. Thibodeaux, W.-c. Chang and H.-w. Liu, Chem. Rev., 2012, 112, 1681–1709 CrossRef CAS.
- H. E. Simmons and R. D. Smith, J. Am. Chem. Soc., 1959, 81, 4256–4264 CrossRef CAS.
- H. Nozaki, S. Moriuti, M. Yamabe and R. Noyori, J. Tetrahedron Lett., 1966, 7, 59–63 CrossRef.
- W. R. Moser, J. Am. Chem. Soc., 1969, 91, 1135–1140 CrossRef CAS.
- W. v. E. Doering and A. K. Hoffmann, J. Am. Chem. Soc., 1954, 76, 6162–6165 CrossRef CAS.
- O. G. Kulinkovich, S. V. Sviridov, D. A. Vasilevskii and T. S. Pritytskaya, Zh. Org. Khim., 1989, 25, 2244–2245 CAS.
- G. Bartoli, G. Bencivenni and R. Dalpozzo, Synthesis, 2014, 46, 979–1029 CrossRef.
- S. Inoue, K. Nagatani, H. Tezuka, Y. Hoshino and M. Nakada, Synlett, 2017, 28, 1065–1070 CrossRef CAS.
- M.-I. Picher and B. Plietker, Org. Lett., 2020, 22, 340–344 CrossRef CAS.
- S.-F. Zhu and Q.-L. Zhou, Natl. Sci. Rev., 2014, 1, 580–603 CrossRef CAS.
- H. S. A. Mandour, Y. Nakagawa, M. Tone, H. Inoue, N. Otog, I. Fujisawa, S. Chanthamath and S. Iwasa, Beilstein J. Org. Chem., 2019, 15, 357–363 CrossRef CAS PubMed.
- A. DeAngelis, R. Panish and J. M. Fox, Acc. Chem. Res., 2016, 49, 115–127 CrossRef CAS PubMed.
- Y. Wang, X. Wen, X. Cui, L. Wojtas and X. P. Zhang, J. Am. Chem. Soc., 2017, 139, 1049–1052 CrossRef CAS.
- S. Inoue, K. Nagatani, H. Tezuka, Y. Hoshino and M. Nakada, Synlett, 2017, 28, 1065–1070 CrossRef CAS.
- X. Liu, Y. Liu, X. Li, S. Xiang, Y. Zhang, P. Ying, Z. Wei and C. Li, Appl. Catal., A, 2003, 239, 279–286 CrossRef CAS.
- M. L. Kantam, V. S. Jaya, M. J. Lakshmi, B. R. Reddy, B. M. Choudary and S. K. Bhargava, Catal. Commun., 2007, 8, 1963–1968 CrossRef CAS.
- S. Ishikawa, R. Hudson, M. Masnadi, M. Bateman, A. Castonguay, N. Braidy, A. Moores and C.-J. Li, Tetrahedron, 2015, 71, 2585 CrossRef CAS.
- L. Chen, M. O. Bovee, B. E. Lemma, K. S. M. Keithley, S. L. Pilson, M. G. Coleman and J. Mack, Angew. Chem., Int. Ed., 2015, 54, 11084–11087 CrossRef CAS PubMed.
- L. R. Chen, D. Leslie, M. G. Coleman and J. Mack, Chem. Sci., 2018, 9, 4650–4661 RSC.
- H. Luo, C. Lin, H. B. Zhou, Y. J. Zhao, X. M. Wang, D. W. Zhang and Y. Yu, Adv. Mater. Interfaces, 2022, 9, 2102110 CrossRef CAS.
- R. L. Safiullin, V. A. Dokichev, L. R. Yakupova, R. M. Sultanova, S. L. Khursan, R. N. Zaripov and Y. V. Tomilov, Kinet. Catal., 2008, 49, 43–51 CrossRef CAS.
- B. J. Anding, A. Ellern and L. K. Woo, Organometallics, 2012, 31, 3628–3635 CrossRef CAS.
- M. M. Díaz-Requejo, M. C. Nicasio and P. J. Pérez, Organometallics, 1998, 17, 3051–3057 CrossRef.
- J. Rong, E. R. Gao, N. C. Liu, W. Y. Chen, X. S. Rong, Y. Z. Zhang, X. D. Zheng, H. S. Ao, S. L. Xue, B. Huang, Z. Y. Li, F. X. Qiu and Y. T. Qian, Energy Storage Mater, 2023, 56, 165–173 CrossRef.
- X. Yang, J. Chen, W. Yang, H. Lin and X. Luo, J. Inorg. Chem. Front., 2019, 6, 3475–3481 RSC.
- X. Chen, N. Wang, K. Shen, Y. Xie, Y. Tan and Y. Li, ACS Appl. Mater. Interfaces, 2019, 11, 25976–25985 CrossRef CAS PubMed.
- S. Zhou, X. Wang, P. Zhao, J. Zheng, M. Yang, D. Huo and C. Hou, Microchim. Acta, 2021, 188, 383 CrossRef CAS.
- Y. Zhang, J. Y. Wu, S. H. Zhang, N. Z. Shang, X. X. Zhao, S. M. Alshehri, T. Ahamad, Y. Yamauchi, X. T. Xu and Y. Bando, Nano Energy, 2022, 97, 107870 Search PubMed.
- Y. T. Zhang, S. Y. Li, N. N. Zhang, G. Lin, R. Q. Wang, M. N. Yang and K. K. Li, New Carbon Mater., 2023, 38, 200–210 CrossRef CAS.
- Q. Xu, R. Q. Qiu, H. Jiang and X. M. Wang, J. Electroanal. Chem., 2019, 839, 247–255 CrossRef CAS.
- Y. F. Zhu, D. Y. Zhu, Y. Chen and Q. Q. Yan, et al., Porphyrin-based donor–acceptor cofs as efficient and reusable photocatalysts for pet-raft polymerization under broad spectrum excitation, Chem. Sci., 2021, 12, 16092–16099 RSC.
- Z. Fu, X. Wang and A. M. Gardner, et al., A stable covalent organic framework for photocatalytic carbon dioxide reduction[J].Royal Society of Chemistry, Chem. Sci., 2020, 11, 543–550 RSC.
- A. Sarkar, D. Formenti, F. Ferretti, C. Kreyenschulte, S. Bartling, K. Junge, M. Beller and F. Ragaini, Chem. Sci., 2020, 11, 6217–6221 RSC.
- H. Zhou, S. Hong, H. Zhang, Y. Chen, H. Xu, X. Wang, Z. Jiang, S. Chen and Y. Liu, J. Appl. Catal., B, 2019, 256, 117767 CrossRef.
- X. Wang, Y. Sun, R. Cai, Z. Jiang, J. Ren, L. Zhang, D. Li, X. Zhao and D. Yang, J. Alloys Compd., 2022, 908, 164638 CrossRef CAS.
- J. Hu, J. Chen, H. Lin, R. Liu and X. Yang, J. Solid State Chem., 2018, 259, 1–4 CrossRef CAS.
- O. Maslova, M. Ammar, G. Guimbretière, J.-N. Rouzaud and P. Simon, Phys. Rev. B: Condens. Matter Mater. Phys., 2012, 86, 134205 CrossRef.
- S. J. Lai, L. Xu, H. L. Liu, S. Chen, R. S. Cai, L. J. Zhang, W. Theis, J. Sun, D. J. Yang and X. L. Zhao, J. Mater. Chem. A, 2019, 7, 21884–21891 RSC.
- X. Song, L. Guo, X. Liao, J. Liu, J. Sun and X. Li, J. Small, 2017, 13, 1700238 CrossRef PubMed.
- Z. Meng, S. Cai, R. Wang, H. Tang, S. Song and P. Tsiakaras, J.Appl. Catal., B, 2019, 244, 120–127 CrossRef CAS.
- L. Zhang, Z. Su, F. Jiang, L. Yang, J. Qian, Y. Zhou, W. Li and M. Hong, J. Nanoscale, 2014, 6, 6590–6602 RSC.
- P. Kate, V. Pandit, V. Jawale and M. Bachute, L-proline catalyzed one-pot three-component synthesis and evaluation for biological activities of tetrahydrobenzo[b]pyran: evaluation by green chemistry metrics, J. Chem. Sci., 2022, 134(1), 1–11 CrossRef.
- P. Chhattise, S. Saleh, V. Pandit, S. Arbuj and V. Chabukswar, Zno nanostructures: a heterogeneous catalyst for the synthesis of benzoxanthene and pyranopyrazole scaffolds via a multi-component reaction strategy, Mater. Adv., 2020, 1, 2339–2345 RSC.
- S. S. Pandit, V. U. Pandit and B. P. Bandgar, Rapid and efficient synthesis of sulfonamides from sulfonic acid and amines using cyanuric chloride-dmf adduct, Sulfur Rep., 2008, 29(6), 619–622 CrossRef CAS.
|
This journal is © The Royal Society of Chemistry 2024 |
Click here to see how this site uses Cookies. View our privacy policy here.