DOI:
10.1039/D4RA04960H
(Paper)
RSC Adv., 2024,
14, 27481-27487
Highly efficient CuNi–ZrO2 nanocomposites for selective hydrogenation of levulinic acid to γ-valerolactone†
Received
9th July 2024
, Accepted 23rd August 2024
First published on 29th August 2024
Abstract
CuNi–ZrO2 nanocomposites were prepared by a simple coprecipitation technique of copper, nickel and zirconium ions with potassium carbonate. The structures of the nanocomposites were characterized by N2 physical adsorption, XRD, H2-TPR and STEM-EDS. The Cu0.05Ni0.45–ZrO2 nanocomposite showed outstanding catalytic performance in hydrogenation of levulinic acid (LA) to γ-valerolactone (GVL), especially NaOH solution (0.5 mol L−1) as a solvent. 100% LA conversion and > 99.9% GVL selectivity are achieved over Cu0.05Ni0.45–ZrO2 catalyst at 200 °C, 3 MPa for 1.5 h. Characterization results suggest that the excellent reactivity of the Cu0.05Ni0.45–ZrO2 may be due to a better reducibility of nickel oxide in the CuONiO–ZrO2, dispersion of Ni in the Cu0.05Ni0.45–ZrO2 compared to nickel oxide in the NiO–ZrO2 and Ni in the Ni0.5–ZrO2 and promotion of OH−. The results demonstrate that the Cu0.05Ni0.45–ZrO2 nanocomposite has potential to realize high efficiency and low-cost synthesis of liquid fuels from biomass.
Introduction
Our over-reliance on fossil resources for various chemicals and fuels production has caused global fuel supply deficiency and environmental issues.1 Transformation of abundant and reproducible biomass to chemicals and fuels can be a promising solution to both issues. Lignocellulose is the most abundant biomass resource on Earth, and is mainly composed of cellulose and lignin. The former can be decomposed into high concentration guaiacol and polyaromatic hydrocarbons by rapid pyrolysis and hydrothermal liquefaction.1 The latter can be converted into LA, 5-hydroxymethylfurfural and furfural.2 These molecules can further be converted into useful chemicals and fuels.3,4 Catalytic hydrogenation of LA to GVL has attracted much attention in recent years because of GVL's unique properties of low toxicity, high boiling point, excellent stability and high energy density, and widespread application as a fuel and food additives, green solvent for synthesis of pharmaceuticals, a versatile building block for production of polymers, olefins and other chemicals with high added value.5–8
The hydrogenation of LA to GVL has been reported over both homogeneous and heterogeneous catalysts. The homogeneous catalysts are superior to the heterogeneous catalysts in catalytic reactivity and selectivity toward GVL, but the use of noble metal (Ru, Pd, Rh, etc.) complexes limits their applications, and catalyst recovery after reaction is still a major issue. Considering the advantages of the heterogeneous catalysts in recovery and recyclability, different heterogeneous catalysts have been developed to catalyze the hydrogenation of LA toward GVL. Noble metals (Ru,9 Pt,10 Pd,11 Ir,12 etc.) on various supports have been reported to effectively catalyze the reaction. Particularly, supported Ru-based catalysts have been widely investigated for the hydrogenation of LA toward GVL because they exhibited excellent hydrogenation activity and selectivity toward GVL.13–16 However, the Ru-based catalysts showed deactivation during the LA hydrogenation.17,18 Base metal catalysts are usually preferred due to their availability and low price, which are more suitable for large-scale use. Various base metal (Cu,19 Ni,20 Co21) catalysts have been investigated for the LA hydrogenation toward GVL. Rode et al. found that the LA could be transformed to GVL with a 100% selectivity on Cu–ZrO2 catalyst under harsh reaction conditions, i.e., high temperatures (200–265 °C), high pressures (3.0–7.0 MPa H2) and long reaction times (5–10 h).22 Mohan et al. reported that the Ni–SiO2 catalyst showed a high GVL productivity,23 whereas the selectivity toward GVL was 87%.
Herein, we reported the hydrogenation of LA toward GVL on Cu0.05Ni0.45–ZrO2 nanocomposite in a tank reactor. The catalyst showed rather better performance for the hydrogenation of LA to GVL than Ni–ZrO2, especially Cu–ZrO2 and Ni–SiO2 catalysts.
Experimental section
Catalyst preparation
Levulinic acid and Zr(NO3)4·3H2O (99%) were procured from Chengdu Aikeda Chemical Reagent Co. Ltd Cu(NO3)2·3H2O (99%), Ni(NO3)2·6H2O (99%) and K2CO3 (99%) were obtained from Chengdu Cologne Chemicals Co. Ltd.
The NixCuy–ZrO2 nanocomposites with different molar fractions of Cu and Ni (x + y = 0.5) were prepared by a coprecipitation technique. Typically, Cu(NO3)2·3H2O, Ni(NO3)2·6H2O and Zr(NO3)4·3H2O were dissolved in redistilled water according to nanocomposites components and precipitated using 0.2 mol L−1 K2CO3 solution under stirring at room temperature. The precipitate was separated by filtration and washed with redistilled water to remove soluble ions after aging the precipitate for 5 h. The precipitate thus obtained was dried for 10 h at 110 °C and calcined for 4 h at 400 °C in an air flow. Then the calcined catalyst was reduced for 2 h at 400 °C in a H2 flow. The Cu0.05–ZrO2 and Ni0.05–ZrO2 catalysts were prepared in the same manner as that of NixCuy–ZrO2. The molar fractions of Cu and Ni in the Cu0.5–ZrO2, Ni0.5–ZrO2 and Cu0.05Ni0.45–ZrO2 were 0.488, 0.493, 0.049 and 0.446 according to ICP-AES determination, respectively.
Catalyst characterization
XRD patterns of catalysts were recorded on a Rigaku D/Max Ultima IVX-ray diffractometer with a 40 kV accelerating voltage and 30 mA current using CuKα radiation. Their pore structures and specific surface areas were determined via N2 adsorption–desorption on an ASAP 2010 Micromeritics apparatus. Temperature-programmed reduction (TPR) was performed on a Finesorb-3010 chemisorption instrument. 100 mg catalyst was gradually heated to 200 °C and held for 2 h, then cooled to 50 °C in an argon flow of 50 mL min−1. Then the catalyst was heated to 700 °C at 10 K min−1 in a H2/Ar (10% v/v) flow of 40 mL min−1. The effluent gas H2 is analyzed with a thermal conductivity detector. STEM and EDS measurements were performed on a JEOL JEM 2100 transmission electron microscope at a 200 kV accelerating voltage. XPS spectra were recorded by an X-ray photoelectron spectrometer (ESCALAB 250Xi, AlKα, C 1s 284.6 eV).
Catalytic tests
Hydrogenation of LA was performed in a telfon-lined stainless steel autoclave. In each run, 10 mL of LA aqueous solution (5 wt%) and 15 mg catalyst was used. The autoclave was purged one time with nitrogen and four times with hydrogen, then it was pressurized to the desired hydrogen pressure. The reaction mixture was stirred at 1000 rpm. The products were determined by GC9890 gas chromatography with a capillary column (SE-30) and flame ionization detector using 1-butanol as an internal standard.
Results and discussion
Catalyst characterization
The textural properties of the Cu0.5–ZrO2, Ni0.5–ZrO2 and Cu0.05Ni0.45–ZrO2 catalysts were determined by N2 physical adsorption. They showed similar type IV isotherm (Fig. S1†). As displayed in Table S1,† the BET specific surface area, pore volume and mean pore size of the Cu0.05Ni0.45–ZrO2 catalyst were 101 m2 g−1, 0.18 cm3 g−1 and 3.7 nm, respectively. They were larger than those of the Cu0.5–ZrO2 (85 m2 g−1, 0.13 cm3 g−1 and 3.6 nm) and the Ni0.5–ZrO2 (94 m2 g−1, 0.16 cm3 g−1 and 3.5 nm).
The XRD patterns of the Cu0.5–ZrO2, Ni0.5–ZrO2 and Cu0.05Ni0.45–ZrO2 catalysts are shown in Fig. 1. For the Cu0.5–ZrO2 catalyst, four main diffraction peaks were observed. 2θ = 30.3° correspond to tetragonal ZrO2 phase (JCPDS17-0923),24 while 2θ = 43.4°, 50.4° and 74.2° correspond to the Cu(111), Cu(200) and Cu(220) planes of Cu (JCPDS004-0836).25 For the Ni0.5–ZrO2 catalyst, three main diffraction peaks were observed at 2θ = 30.3°, 50.6°, 60.1° which is attributed to tetragonal ZrO2 phase, while 2θ = 44.3° and 76.4° correspond to the Ni(111) and Ni(220) planes of Ni (JCPADS#04-0850).26 The Cu0.05Ni0.45–ZrO2 catalyst showed two main diffraction peaks of tetragonal ZrO2 phase and metallic Ni at 30.3° and 44.3°. The characteristic peaks of Cu do not appear in the Cu0.05Ni0.45–ZrO2 catalyst. It can be suggested that the Cu are highly dispersed in the nanocomposite. Further analysis of Ni(111) reflection with Sherrer's equation, it was found that Ni crystallite sizes in the Cu0.05Ni0.45–ZrO2 and Ni0.5–ZrO2 catalysts are 3.8 nm and 5.7 nm, respectively. The Ni crystallite size in the Cu0.05Ni0.45–ZrO2 is smaller than that of the Ni0.5–ZrO2, which suggests that the replacement of Cu makes Ni more dispersed in the nanocomposite.
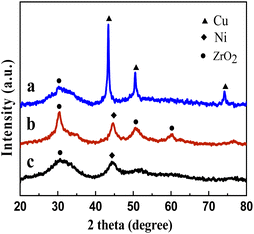 |
| Fig. 1 XRD patterns of the Cu0.5–ZrO2 (a), Ni0.5–ZrO2 (b) and Cu0.05Ni0.45–ZrO2 (c) catalysts. | |
Fig. 2 shows the H2-TPR profiles of CuO–ZrO2, NiO–ZrO2 and CuONiO–ZrO2. For the CuO–ZrO2 (Fig. 2a), there was a reduction peak at 200 °C, which is ascribed to the reduction of CuO.27 The NiO–ZrO2 and CuONiO–ZrO2 show reduction peaks at 328–505 °C, which correspond to the reduction of NiO.28 The reduction peak at 505 °C is probably ascribed to the NiO with relatively strong interaction with ZrO2. For the CuONiO–ZrO2, the reduction temperatures of low temperature peaks were obviously lower than those of NiO–ZrO2, suggesting that the NiO in the CuONiO–ZrO2 was more dispersed. The reduction peak at 196 °C in the CuONiO–ZrO2 is ascribed to the reduction of CuO. The reduction temperature is lower than that of CuO in the CuO–ZrO2. The relatively low reduction temperature is probably due to high dispersion of CuO in the nanocomposite. These are consistent with the results of XRD characterization.
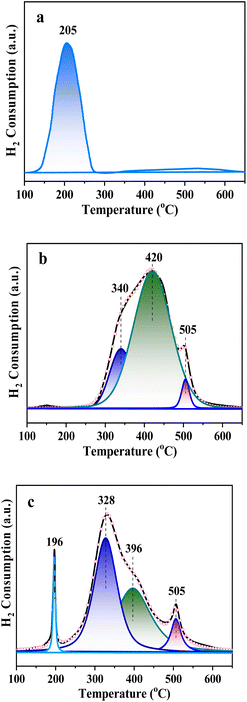 |
| Fig. 2 TPR profiles of the CuO–ZrO2 (a), NiO–ZrO2 (b) and CuONiO–ZrO2 (c) samples. | |
To further identify the microstructures of Cu, Ni and ZrO2, STEM-EDS analysis of the Cu0.5–ZrO2, Ni0.5–ZrO2 and Cu0.05Ni0.45–ZrO2 were carried out. The elemental mapping images of the Cu0.5–ZrO2, Ni0.5–ZrO2 and Cu0.05Ni0.45–ZrO2 show that Cu, Ni are highly dispersed in ZrO2 (Fig. 3b, g and l). For the Cu0.05Ni0.45–ZrO2 nanocomposite, the Ni was evenly separated by Cu and ZrO2 (Fig. 3l), suggesting better dispersion of Ni in the Cu0.05Ni0.45–ZrO2 nanocomposite than that in the Ni0.5–ZrO2. This is consistent with the results of XRD and H2-TPR characterizations.
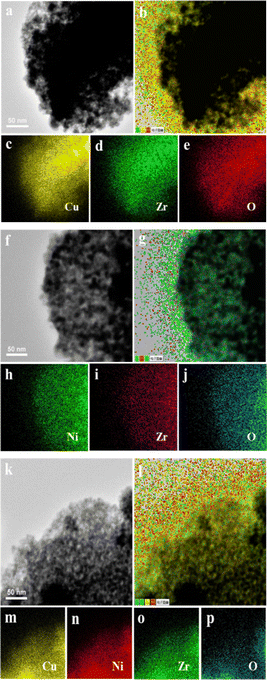 |
| Fig. 3 TEM images and elemental mapping of the Cu0.05–ZrO2 (a–e), Ni0.45–ZrO2 (f–j) and Cu0.05Ni0.45–ZrO2 (k–p) catalysts. | |
XPS analysis was carried out on the Cu0.5–ZrO2, Ni0.5–ZrO2 and Cu0.05Ni0.45–ZrO2 catalysts and the results were shown in Fig. S2 and S3.† The Cu 2p spectra of the Cu0.5–ZrO2 and Cu0.05Ni0.45–ZrO2 can be deconvoluted into two peaks, respectively (Fig. S2†). The peaks located at 932.4 eV and 933.6 are attributed to Cu0 and Cu2+, respectively.29 This indicates the Cu on the surfaces of the Cu0.5–ZrO2 and Cu0.05Ni0.45–ZrO2 catalysts was partially oxidized. The Ni 2p spectra of the Ni0.5–ZrO2 and Cu0.05Ni0.45–ZrO2 can be deconvoluted into two peaks, respectively (Fig. S3†). The Ni 2p3/2 peak at 852 eV belongs to Ni0, while the Ni 2p3/2 peak at 855 eV is assigned to Ni2+.30,31 This indicates the Ni on the surfaces of the Ni0.5–ZrO2 and Cu0.05Ni0.45–ZrO2 catalysts was partially oxidized. The Ni2+/Ni0 ratio for the Ni0.5–ZrO2 catalyst calculated from their corresponding peak area is 5.11, while the Ni2+/Ni0 ratio for the Cu0.05Ni0.45–ZrO2 catalyst is 4.23, indicating that adding a small amount of Cu into the Ni0.5–ZrO2 catalyst can inhibit nickel oxidation.
Catalytic performance
The catalytic performances of the Cu0.5–ZrO2, Ni0.5–ZrO2 and CuNi–ZrO2 catalysts for LA hydrogenation are summarized in Table 1. The conversions of LA over Cu0.5–ZrO2, Ni0.5–ZrO2 and CuNi–ZrO2 catalysts were 12.7%, 33.4% and 48.6% at 200 °C and 3.0 MPa H2 for1.5 h, respectively. No reactivity of LA was found in the absence of catalyst. The conversion of LA (33.4%) on Ni0.5–ZrO2 catalyst is almost 3 times as high as that on Cu0.5–ZrO2 catalyst (12.7%) under the same operating conditions, suggesting Ni with higher intrinsic reactivity for LA hydrogenation than Cu. Interestingly, when a small amount of Ni (0.05 mol) in the Ni0.5–ZrO2 catalyst was replaced by Cu, a much higher conversion (48.6%) was achieved under the same reaction conditions. XRD, H2-TPR and STEM-EDS results show that the replacement of Cu makes NiO in the CuONiO–ZrO2 easier to reduce and Ni more dispersed in the nanocomposite. We think that the excellent reactivity of the Cu0.05Ni0.45–ZrO2 may be due to a better reducibility of NiO in the CuONiO–ZrO2 and dispersion of Ni in the Cu0.05Ni0.45–ZrO2 compared to NiO in the NiO–ZrO2 and Ni in the Ni0.5–ZrO2. Further increasing Cu replacement amount in the Ni0.5–ZrO2 from 0.05 to 0.125 mol had a negligible effect on LA conversion (Table 1). Therefore, the optimum Ni replacement amount with Cu in the Ni0.5–ZrO2 was 0.05 molar fraction.
Table 1 Catalytic performance of the Cu0.5–ZrO2, Ni0.5–ZrO2 and CuNi–ZrO2 for LA hydrogenationa
Entry |
Catalyst |
LA conv./% |
Sel./% |
GVL |
HVAb |
PDOc |
Reaction conditions: 15 mg catalyst, 10 mL 5 vol% levulinic acid aqueous solution, 200 °C, 3.0 MPa H2, 90 min. HVA: 4-hydroxyvaleric acid. PDO: 1,4-pentanediol. |
1 |
Cu0.5–ZrO2 |
12.7 |
>99.9 |
0 |
0 |
2 |
Ni0.5–ZrO2 |
33.4 |
>99.9 |
0 |
0 |
3 |
Cu0.05Ni0.45–ZrO2 |
48.6 |
>99.9 |
0 |
0 |
4 |
Cu0.125Ni0.375–ZrO2 |
41.2 |
>99.9 |
0 |
0 |
LA hydrogenation to GVL proceeds via consecutive reactions of the formation of 4-hydroxypentanoic acid or angelica-lactones as intermediates.27 The reaction pathway mostly depends on used catalyst and reaction conditions.32,33 Various byproducts such as 1,4-pentanediol (PDO) and 4-hydroxyvaleric acid (HVA) are generated from overhydrogenation of GVL when catalyst selectivity is insufficient.34 Therefore, we pay special attention to identify byproducts in the hydrogenation process of LA using GC-MS. Any byproduct in the reaction mixture is unambiguously detected in our product analysis method. Interestingly, an excellent GVL selectivity (>99.9%) at 100% conversion of LA was obtained on the Cu0.05Ni0.45–ZrO2 at 200 °C and 3.0 MPa hydrogen pressure. Overhydrogenation of the target product GVL, which was observed over other catalysts,35–37 was thoroughly avoided over the Cu0.05Ni0.45–ZrO2 catalyst (Table 1). It's also worth mentioning that the selectivity of GVL remained at >99.9% throughout the study, which may suggest that the hydrogenation of LA proceeds via the formation of unstable HVA, then undergoes rapid cyclization to GVL (Fig. 4). The Cu0.05Ni0.45–ZrO2 also exhibited catalytic activity superior to that of conventional catalysts (Table S2†), showing great potential in sustainable GVL production from LA.
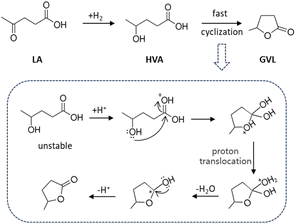 |
| Fig. 4 Reaction pathway for LA hydrogenation to GVL over Cu0.05Ni0.45–ZrO2 catalyst. | |
Effect of reaction conditions
We investigated the effects of reaction temperature, H2 pressure and solvent to ensure the performance of the Cu0.05Ni0.45–ZrO2 catalyst. Fig. 5 shows the performance of LA hydrogenation at different reaction temperatures over the Cu0.05Ni0.45–ZrO2 catalyst. Reaction temperature significantly facilitated LA conversion (Fig. 5). When the reaction temperature rises from 180 °C to 210 °C at 3.0 MPa H2, the conversion of LA increased nearly threefold (from 18.8% to 57.0%). The selectivity of GVL remained at >99.9% throughout the temperature study. No by-products were detected, which demonstrates that the undesired overhydrogenation of GVL to HVA and PDO can be completely suppressed over the Cu0.05Ni0.45–ZrO2 catalyst in a broad window (180–210 °C).
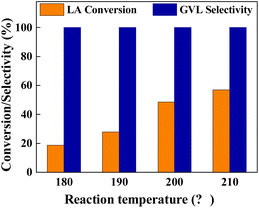 |
| Fig. 5 Catalytic results of the Cu0.05Ni0.45–ZrO2 for LA hydrogenation at various reaction temperatures. | |
The catalytic performance of Cu0.05Ni0.45–ZrO2 catalyst under different H2 pressures was evaluated. As displayed in Fig. 6, hydrogen pressure has a remarkable effect on the hydrogenation of LA catalyzed by Cu0.05Ni0.45–ZrO2. The LA conversion and GVL selectivity were 13.8% and >99.9% at 1.0 MPa H2, respectively. When the H2 pressure increased from 1.0 MPa up to 3.0 MPa, the conversion of LA significantly increased from 13.8% to 48.6%, and the unique selectivity to GVL remained at >99.9%, which suggests that high H2 pressure favor the hydrogenation of LA to GVL on the Cu0.05Ni0.45–ZrO2 catalyst.
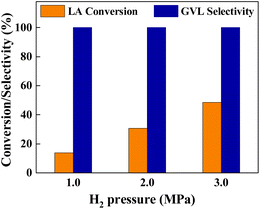 |
| Fig. 6 Catalytic results of the Cu0.05Ni0.45–ZrO2 for LA hydrogenation at various H2 pressures. | |
The performance of Cu0.05Ni0.45–ZrO2 catalyst for LA hydrogenation in polar and non-polar solvents was investigated at 200 °C and 3.0 MPa H2, and the data are listed in Fig. 7. Non-polar solvent like 1,4-dioxane showed GVL selectivity of >99.9%, but it exhibited low LA conversion of 16.3%. All polar solvents showed good LA conversion with ethanol, methanol and water as solvents. The substrate reactivity is very different in various solvents with the order of water > methanol > ethanol. The water gave excellent GVL selectivity of >99.9%, whereas methanol and ethanol showed below 80% GVL selectivity, which is owing to the formation of methyl levulinate (ML) and ethyl levulinate (EL) byproducts from the esterification of LA with corresponding solvent alcohol. The different reactivities of LA and GVL selectivity in these solvents on Cu0.05Ni0.45–ZrO2 catalyst suggest that the solvent polarity have impact on the catalytic performance of the Cu0.05Ni0.45–ZrO2 catalyst. Polar solvent is more beneficial to LA hydrogenation to GVL on Cu0.05Ni0.45–ZrO2 catalyst. In particular, when a certain amount of NaOH (nNaOH/nLA = 1
:
5) was added into the same water, however, a very high LA conversion (100%) was achieved under the same reaction conditions, and an excellent GVL selectivity of >99.9% was obtained.
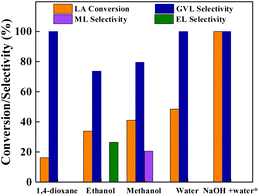 |
| Fig. 7 Catalytic results of the Cu0.05Ni0.45–ZrO2 for LA hydrogenation in various solvents. | |
In order to gain further insight into the promotion of NaOH, the effect of different molar ratios of nNaOH/nLA on catalytic performance of Cu0.05Ni0.45–ZrO2 for LA hydrogenation was investigated at 180 °C and 3.0 MPa H2 (Table 2). The conversion of LA increased from 18.8% to 46.4% when the molar ratio of nNaOH/nLA rose from zero to 1
:
5. Further increasing molar ratios of nNaOH/nLA from 1
:
5 to 1
:
2 had a negligible effect on the conversion of LA. Therefore, the optimum molar ratio of nNaOH/nLA was 1
:
5. We also studied sodium levulinate hydrogenation to GVL on Cu0.05Ni0.45–ZrO2 catalyst. The conversion of sodium levulinate is only 1.7% under the same conditions (Table 2), which suggests that an appropriate amount of OH− can improve activity of the Cu0.05Ni0.45–ZrO2 catalyst for LA hydrogenation to GVL.
Table 2 Effect of NaOH on catalytic performance of the Cu0.05Ni0.45–ZrO2 for LA hydrogenationa
Entry |
n(NaOH)/n(LA) |
Conv./% |
Sel.% |
GVL |
HVAb |
PDOc |
Reaction conditions: 15 mg catalyst, 10 mL 5 vol% levulinic acid aqueous solution, 180 °C, 3.0 MPa H2, 90 min. HVA: 4-hydroxyvaleric acid. PDO: 1,4-pentanediol. |
1 |
0 |
18.8 |
>99.9 |
0 |
0 |
2 |
1 : 10 |
30.1 |
>99.9 |
0 |
0 |
3 |
1 : 5 |
46.4 |
>99.9 |
0 |
0 |
4 |
1 : 2 |
32.9 |
>99.9 |
0 |
0 |
Catalyst reusability
We investigated the reusability of the Cu0.05Ni0.45–ZrO2 catalyst for the LA hydrogenation to GVL at 200 °C, 3.0 MPa H2 pressure, NaOH solution as a solvent for 1.5 h. After the first LA hydrogenation, the used catalyst was separated, washed using ethanol, dried in vacuum and then used for the next cycle. The results of repeated use three times were shown in Fig. 8. The conversions of LA over fresh, used for second, third, fourth times catalysts were 100%, 89.6%, 84.1% and 83.3%, respectively. After the fourth cycle, the conversion of LA showed a slight downward trend, and the outstanding selectivity of GVL remained at >99.9%. This shows good stability of the catalyst even after 4 cycles.
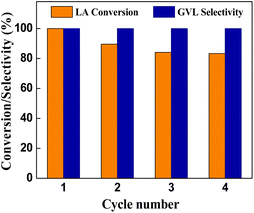 |
| Fig. 8 Reusability of the Cu0.05Ni0.45–ZrO2 for LA hydrogenation. | |
Conclusions
In summary, we have successfully prepared a highly efficient and reusable Cu0.05Ni0.45–ZrO2 catalyst for LA hydrogenation to GVL by a simple coprecipitation technique. The LA hydrogenation with Cu0.05Ni0.45–ZrO2 at 200 °C, 3 MPa for 1.5 h resulted in 100% LA conversion and >99.9% GVL selectivity, which shows prospects of commercialization. The Ni has higher intrinsic reactivity for LA hydrogenation than Cu, and partly substituting Ni with Cu makes NiO in the CuONiO–ZrO2 easier to reduce and Ni more dispersed in the nanocomposite, which may be responsible for excellent reactivity of the Cu0.05Ni0.45–ZrO2. An appropriate amount of OH− can greatly enhance activity of the Cu0.05Ni0.45–ZrO2 catalyst for LA hydrogenation to GVL.
Data availability
The data supporting this article have been included in the main article and the ESI†.
Author contributions
Yufang Ding: methodology, investigation, writing – original draft. Junli Sun: methodology, investigation, writing – original draft. Rongqi Hu: investigation. Daiping He: supervision, writing – review and editing. Xulin Qiu: investigation, data curation. Chengying Luo: investigation. Ping Jiang: writing – review and editing.
Conflicts of interest
There is no conflict of interest to declare.
Acknowledgements
This work was supported by Natural Science Foundation of Chongqing (2023NSCQ-MSX1646 and CSTB2022NSCQ-MSX0265), Science and Technology Research Program of Chongqing Municipal Education Commission (KJZD-K202100501 and KJZD-K2022 00512) and Program for Leading Talents of Scientific Innovation of Chongqing Normal University.
References
- P. H. Yan, J. Mensah, M. Drewery, E. Kennedy, T. Maschmeyer and M. Stockenhuber, Appl. Catal., B, 2021, 281, 119470 CrossRef CAS.
- T. Güney abd and K. Kantar, Int. J. Sustain. Dev. World Ecol., 2020, 27, 762 CrossRef.
- I. V. Andreeva, D. H. Zaitsau, S. Qian, V. V. Turovtzev, A. A. Pimerzin, J. E. Bara and S. P. Verevkin, Chem. Eng. Sci., 2022, 247, 117032 CrossRef CAS.
- Z. H. Yang, X. Y. Chou, H. Y. Kan, Z. H. Xiao and Y. Ding, ACS Sustainable Chem. Eng., 2022, 10, 7418 CrossRef CAS.
- Z. G. Xiao, X. Wang, Z. P. Zhao, Z. Wang, L. L. Gao, Y. Liu and W. G. Zhou, Catal. Commun., 2023, 184, 106790 CrossRef CAS.
- D. P. He, Q. Q. He, P. Jiang, G. B. Zhou, R. Q. Hu and W. S. Fu, Catal. Commun., 2019, 125, 82 CrossRef CAS.
- H. Liu, X. J. Cao, X. Tang, X. H. Zeng, Y. Sun, X. X. Ke and L. Li, Green Chem., 2021, 23, 1983 RSC.
- Y. Zhu, Y. Li, S. P. Zhao, R. Jing, H. Q. Zhang, D. L. Sun and S. Sato, Chem. Lett., 2022, 11, 292 Search PubMed.
- V. S. Jaya, M. Sudhakar, S. N. Kumar and A. Venugopal, RSC Adv., 2015, 5, 9044 RSC.
- N. Siddiqui, C. Pendem, R. Goyal, T. S. Khan, C. Samanta, K. Chiang, K. L. Shah, M. A. Haider and R. Bal, Fuel, 2022, 323, 124272 CrossRef CAS.
- A. Patel, J. Pat and S. Pathan, Inorg. Chem., 2023, 62, 6970 CrossRef CAS PubMed.
- J. R. Wang, Y. Y. Wang, X. L. Tong, Y. W. Wang, G. Q. Jin and X. Y. Guo, Catal. Commun., 2020, 139, 105971 CrossRef CAS.
- C. E. Bounoukta, C. Megias-sayago, N. Rendón, F. Ammari, A. Penkova, S. Ivanova, M. A. Centeno and J. A. Odriozola, Sustain. Energy Fuels, 2023, 7, 857 RSC.
- S. Gyergyek, M. Grilc, B. Likozarr and D. Makovec, Green Chem., 2022, 24, 2788 RSC.
- K. L. Zhang, Q. L. Meng, H. H. Wu, T. Y. Yuan, S. T. Han, J. X. Zhai, B. X. Zheng, C. Y. Xu, W. Wu, M. Y. He and B. X. Han, Green Chem., 2021, 23, 1621 RSC.
- Z. Ruiz-bernal, M. A. Lillo-ródenas and M. D. Román-martínez, Catalysts, 2021, 11, 559 CrossRef CAS.
- A. S. Piskun, J. Ftouni, Z. Tang, B. M. Weckhuysen, P. C. A. Bruijnincx and H. J. Heeres, Appl. Catal., A, 2018, 549, 197 CrossRef CAS.
- J. Feng, X. Gu, Y. Xue, Y. W. Han and X. B. Lu, Sci. Total Environ., 2018, 633, 426 CrossRef CAS PubMed.
- Z. Y. Li, H. G. Hao, J. J. Lu, C. M. Wu, R. Gao, J. F. Li, C. L. Liu and W. S. Dong, J. Energy Chem., 2021, 61, 446 CrossRef CAS.
- K. Sakakibara, K. Endo and T. Osawa, Catal. Commun., 2019, 125, 52 CrossRef CAS.
- S. Shao, Z. Z. Ding, C. L. Shang, S. Y. Zhang, Y. C. Ke, G. L. Zhu and Y. Yang, Chem. Eng. J., 2022, 450, 138153 CrossRef CAS.
- A. M. Hengne and C. V. Rode, Green Chem., 2012, 14, 1064 RSC.
- V. Mohan, V. Venkateshwarlu, C. V. Pramod, B. D. Raju and K. S. Rao, Catal. Sci. Technol., 2014, 4, 1253 RSC.
- H. Q. Wang, H. Chen, B. Ni, K. Wang, T. He, Y. L. Wu and X. Wang, ACS Appl. Mater. Interfaces, 2017, 9, 26897 CrossRef CAS PubMed.
- B. Seemala, C. M. Cai, C. E. Wyman and P. Christopher, ACS Catal., 2017, 7, 1 CrossRef.
- S. F. Li, M. X. Li and Y. H. Ni, Appl. Catal., B, 2020, 268, 118392 CrossRef CAS.
- W. L. Zhang, Y. Yao, S. Q. Xie, K. Gubsch, Y. H. Yang, X. Y. Lan and H. F. Lin, Catal. Today, 2021, 374, 53 CrossRef CAS.
- H. S. Roh, K. Y. Koo, J. H. Jeong, Y. T. Seo, D. J. Seo, W. L. Yoon and S. B. Park, Catal. Lett., 2007, 117, 85 CrossRef CAS.
- P. P. Upare, M. G. Jeong, Y. K. Hwang, D. H. Kim, Y. D. Kim, D. W. Hwang, U. H. Lee and J. S. Chang, Appl. Catal., A, 2015, 491, 127 CrossRef CAS.
- D. R. Jonesa, S. Iqbala, L. Thomasa, S. Ishikawa, C. Reece, P. J. Miedziak, D. J. Morgan, J. K. Bartley, D. J. Willock, W. Ueda and G. J. Hutchings, Catal. Struct. React., 2018, 4, 12 Search PubMed.
- P. P. Upare, M.-G. Jeong, Y. K. Hwang, D. Han Kim, Y. D. Kim, D. W. Hwang, U.-H. Lee and J.-S. Chang, Appl. Catal., A, 2015, 491, 127 CrossRef CAS.
- A. B. Jain and P. D. Vaidya, Can. J. Chem. Eng., 2016, 94, 2364 CrossRef CAS.
- O. A. Abdelrahman, A. Heyden and J. Q. Bond, ACS Catal., 2014, 4, 1171 CrossRef CAS.
- Y. J. Tsou, T. D. To, Y. C. Chiang, J. F. Lee, R. Kumar, P. W. Chung and Y. C. Lin, ACS Appl. Mater. Interfaces, 2020, 12, 54851 CrossRef CAS PubMed.
- M. Maumela, S. Marx and R. Meijboom, Catalysts, 2021, 11, 292 CrossRef CAS.
- A. L. Maximov, A. V. Zolotukhina, A. A. Mamedli, L. A. Kulikov and E. A. Karakhanov, ChemCatChem, 2018, 10, 222 CrossRef CAS.
- L. Xin, Z. Y. Zhang, J. Qi, Z. Y. Zhang, D. Chadderdon and W. Z. Li, ChemSusChem, 2013, 6, 674 CrossRef CAS PubMed.
|
This journal is © The Royal Society of Chemistry 2024 |
Click here to see how this site uses Cookies. View our privacy policy here.