DOI:
10.1039/D4RA05047A
(Paper)
RSC Adv., 2024,
14, 30378-30384
Improvement of adhesive properties of modified epoxy–novolac resin by acrylonitrile–butadiene rubber grafted poly(chromium methacrylate)
Received
12th July 2024
, Accepted 26th August 2024
First published on 24th September 2024
Abstract
The purpose of this work was to improve the adhesive properties of modified epoxy–novolac resin by acrylonitrile–butadiene rubber (NBR) grafted poly(chromium methacrylate). Chromium methacrylate was prepared by reaction of basic chromium sulfate with sodium methacrylate. Acrylonitrile–butadiene rubber grafted poly(chromium methacrylate) (GNBR) was successfully prepared by solution graft copolymerization to improve the adhesive properties of epoxy–novolac resin. In this copolymerization, the highest graft efficiency was obtained when 50 wt% of chromium methacrylate and 50 wt% of NBR are used for 4 h at 75 °C. The modified epoxy–novolac adhesive (GNBR–epoxy–novolac resin) was prepared by incorporation of GNBR into epoxy–novolac resin. Their chemical structures were characterized by Fourier transform infrared spectroscopy (FTIR) and the thermal properties were analyzed by thermogravimetry (TGA). The mechanical properties of GNBR–epoxy–novolac resins at both room temperature and 233 K were tested. The tensile strength, Young's modulus and failure strain of GNBR–epoxy–novolac resins were estimated from the tensile stress–strain curves and the lap shear strength (LSS) were evaluated using aluminum adherents, and the results showed that they were significantly improved. This is significant because it is one way to improve the disadvantage of high brittleness of epoxy–novolac adhesive.
1. Introduction
Epoxies have been used widely as structural adhesives due to their superb mechanical properties such as high rigidity, adhesive strength and excellent thermal stability. However, epoxies have the disadvantage of high brittleness, so they can easily break under external impact and pressure.
Extensive research has been carried out to overcome this disadvantage by modifying epoxy resin in various ways.1–13
NBR had been widely used to modify epoxy resins, but the miscibility and reactivity of epoxy resin with NBR was poor, so the application was limited.14–20 The miscibility and reactivity were improved by adding various functional groups to the NBR rubber.21–27
Epoxy resin was modified with liquid carboxyl-terminated butadiene–acrylonitrile (CTBN) rubber to improve the LSS and T-peel strength by increasing the flexibility of the epoxy resin.14,15 The carboxyl group, the active group, is distributed at both ends of the CTBN chain, so that the reactivity with epoxy resin is enhanced when tertiary amine catalyst is used as a curing agent. At this time, the nitrile rubber chain is incorporated into the crosslinking structure of epoxy resin, thus increasing the rigidity of the resin. The epoxy resin with increased rigidity improves the resistance to external stresses. Hydroxyl terminated polybutadiene (HTPB) liquid rubber was also used to improve the brittleness of epoxy resin.18
Carboxylated NBR has good modification effect on epoxy resin but manufacturing cost is high. Many methods have been developed to improve the properties of NBR rubber by adding various functional groups. Among the chemical modifications of NBR which have been attempted are epoxidation, hydrogenation, maleinization, and graft copolymerization.21–31 By applying this chemical modification method, the NBR modification can modify the properties of NBR, i.e. its polarity, thermal stability and oxidation resistance. To reduce the cost, graft copolymerization can be applied. The graft copolymerization is an effective method to easily obtain the desired polymer by grafting the functional monomer onto the already prepared polymer. Graft copolymerization of NBR with vinyl monomers such as methyl methacrylate (MMA),28 styrene,29 acrylonitrile,30 dimethylaminoethyl methacrylate (DMAEMA)31 are among the most widely used methods of altering the properties of NBR. Chromium methacrylate has been used as an adhesion promoter because it has double bonds that can be easily grafted onto the polymer molecule and has functional groups such as carboxyl and hydroxyl groups. Therefore, grafting to NBR and its use in epoxy modification can improve the miscibility and compatibility with epoxy resin and improve the adhesive properties. Chromium methacrylate-based adhesion promoters, called the commercial name Volan, have been widely used as glass fiber surface treatment agents.26,27 This product, prepared by the reaction of chromium chloride with methacrylic acid, is a chelate-like structure with two methacrylic acid coordinated to one chromium ion. There are few studies on grafting chromium methacrylate onto NBR rubber to modify epoxy resin.
In this study, GNBR grafted with chromium methacrylate onto NBR rubber was used to modify epoxy–novolac resin to improve the adhesive properties. Chromium methacrylate can be easily grafted to the NBR backbone by double bonding and is effective in modifying the epoxy resin by carboxyl and hydroxyl groups. The influence of chromium methacrylate amount, initiator concentration, reaction temperature and reaction time on the graft copolymerization of chromium methacrylate onto NBR backbond was investigated. The obtained GNBR was applied to the modification of epoxy–novolac resin and its mechanical properties were examined.
2. Materials and methods
2.1 Materials
The basic chromium sulfate and sodium methacrylate used in this study were of analytical grade and purchased from Beijing Chemical Reagent Co., China. NBR with acrylonitrile content of 40 wt% was obtained from Sinopec Qilu Co., China. Epoxy resin (E-44) and novolac resin were purchased from Nanya Plastics Corporation, China. Dicyandiamide, dimethylaniline, acetone, toluene, and benzoyl peroxide (BPO) were purchased from Beijing Chemical Reagent Co., China.
2.2 Graft copolymerization of chrome methacrylate onto NBR backbone
2.2.1 Synthesis of chrome methacrylate. Chromium methacrylate (CrMA) was synthesized according to the following reaction. |
4H2C C(CH3)COONa + Cr2(OH)2(SO4)2 → Cr2(OH)2(O2C–(CH3)C CH2)4 + 2Na2SO4
| (1) |
Sodium methacrylate (28.8 g, 0.4 mol) and 50% aqueous solution of basic chromium sulfate (85.2 g, 0.1 mol) were charged into a 250 mL four-necked-round flask equipped with a magnetic stirrer, a cooler and a feed inlet. The reaction proceeds at 90 °C under mechanical stirring until the solution color changes to blue. Then the reactant was separated by the gradient method and washed with excess distilled water for several times, finally dried in a vacuum dryer to obtain pure chromium methacrylate.
2.3 Preparation of GNBR–epoxy–novolac resin adhesive
First, epoxy and novolac resin were loaded into a reactor at a mass ratio of 6
:
4 and mixed at 120 °C to obtain epoxy–novolac resin. Then, GNBR (20 wt% of epoxy–novolac resin) and the reaction promoter dimethylaniline (1 wt% of epoxy–novolac resin) were added to this reactor and stirred at 130 °C for 1 h to prepare the epoxy–novolac adhesive modified by GNBR. After completion of the reaction, the reaction was removed from this reactor, settled down at 25 °C for 24 h, sealed and stored. The obtained adhesive was solid state. The preparation process of GNBR–epoxy–novolac resin adhesive is shown in Scheme 3.
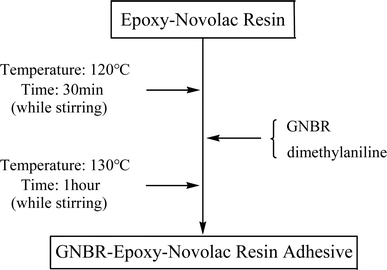 |
| Scheme 3 Preparation of GNBR–epoxy–novolac resin adhesive. | |
2.4 Characterization
2.4.1 Structural characterization. Chemical structures of chromium methacrylate, GNBR and GNBR–epoxy–novolac resin adhesive were characterized by Fourier transform infrared spectroscopy (FTIR). FTIR spectra were recorded with Nicolet 6700 FTIR spectra-photometer (USA) in transmission mode, scanning from 4000 to 500 cm−1.
2.4.2 Thermogravimetric characteristic. Thermo-gravimetric analysis (TGA) of GNBR–epoxy–novolac resins was conducted on a Shimadzu TGA-50H under N2 atmosphere. Thermal analysis was monitored in the temperature range of 20–700 °C with a 10 °C min−1 heating rate.
2.4.3 NBR graft copolymers. To evaluate the completion of the graft copolymerization, the graft efficiency (GE, %) was calculated as follows:23 |
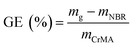 | (2) |
where mNBR represent the initial mass of NBR and mg represent obtained mass of GNBR. And mCrMA represent the mass of chromium methacrylate used in the reaction.
2.4.4 Mechanical testing. GNBR–epoxy–novolac resins were dissolved in a 5
:
5 mixture of acetone and toluene to ensure proper fluidity. And hardener (dicyandiamide, 10 wt% of adhesive) was added and stirred at 50 rpm for 30 min to ensure proper dispersion. The obtained solution was poured onto a ribbon paper and dried to prepare a 0.5 mm thick film adhesive. Chromic acid etched B-51-SWP aluminum alloy substrates were carefully cleaned using a towel and the adhesive film was put on it. And the aluminum specimen was joined in a single overlap. Then the boned specimens were cured at 120 °C and settled down at room temperature (RT) for 24 h. The contact area of the joint is 25 mm × 12.5 mm. The LSS of the cured adhesive was determined by Zwick Z050 extensometer with a speed of 5 mm min−1 according to ASTM D-1002 method.10To obtain tensile test specimens, the adhesive and hardener were mixed in the same manner as above, and the resulting solution was poured into the specimen mold, dried and cured at 120 °C. The tensile tests were performed in an Instron 3366 testing machine (India), at a crosshead speed of 500 mm min−1, according to ASTM D-638.3 The mechanical test values were taken from an average of at least five specimens.
3. Results and discussion
3.1 Influence of the reaction parameters on the graft copolymerization of chrome methacrylate onto NBR backbone
The influence of chromium methacrylate amount, initiator concentration, reaction temperature and reaction time on the graft efficiency (GE) of the graft copolymerization of chromium methacrylate onto NBR backbond was investigated and the results are shown in Fig. 1.
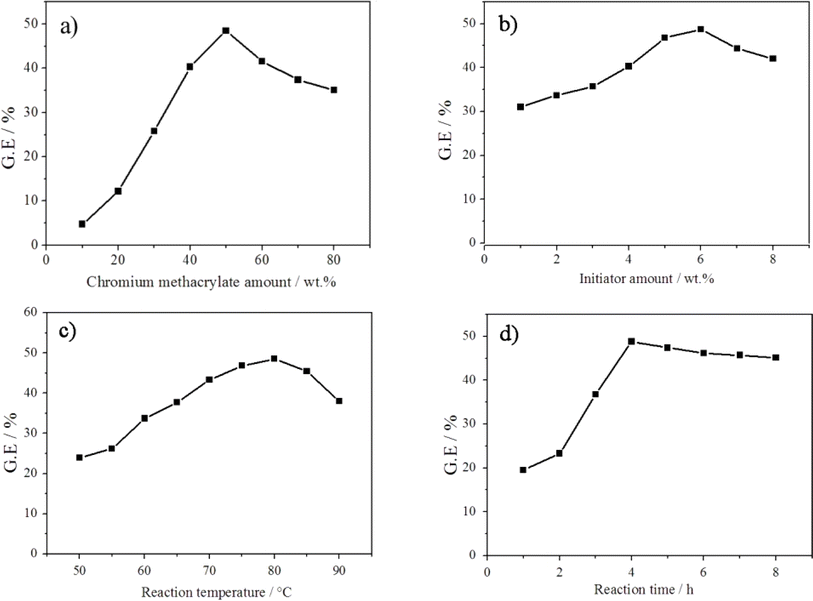 |
| Fig. 1 Influence of (a) chrome methacrylate amount, (b) initiator concentration, (c) reaction temperature and (d) reaction time on the graft copolymerization of chrome methacrylate onto NBR backbone. | |
3.1.1 Influence of chrome methacrylate amount. The influence of chrome methacrylate amount over the range of 10–80 wt% was investigated with a fixed 6 wt% BPO at 80 °C for 4 h. Fig. 1(a) shows the graft efficiencies (GE) of graft copolymerization reactions for different chromium methacrylate contents. In this figure, the GE increased with increasing chromium methacrylate content, reaching a maximum value at 50 wt%, and then decreasing further. When the amount of chromium methacrylate is below 50 wt%, the diffusion of chromium methacrylate onto NBR is enhanced with increasing content, the reaction is better and higher GE is obtained. Above 50 wt% chromium methacrylate amount grafting rate decreases with increasing chromium methacrylate content. The reason is that the grafting reaction rate rapidly increases with increasing chromium methacrylate amount, which leads to a rapid completion of the reaction, promoting gel formation, and increasing the amount of chromium methacrylate homopolymer. Moreover, the higher the methacrylate amount, the more side reactions such as chain transfer to the monomer occur. Therefore, the 50 wt% chromium methacrylate is sufficient and effective for the grafting reaction of chromium methacrylate onto NBR.
3.1.2 Influence of the initiator concentration. The influence of initiator concentration over the range of 1–8 wt% BPO was investigated with a fixed 50 wt% chromium methacrylate at 80 °C for 4 h. Fig. 1(b) shows the GE of graft copolymerization reaction for different BPO initiator concentration. In this figure, the GE increased with increasing initiator concentration, reaching a maximum value of 48.7 at 6 wt% BPO and then decreased. The reason for the increase in GE with an increasing concentration of initiator over the range of 1–6% BPO is that higher amount of initiator generated more active sites on NBR backbone for graft copolymerization. However, the reason for the decrease in GE when using high content of initiator more than 6% BPO is that the more free radicals to generate active sites along the NBR chains, the more possibility of interaction of the rubber macroradicals with each other to produce gel increases. Therefore, 6 wt% BPO was chosen as the optimum concentration to obtain a high GE with no gel content in the graft copolymerization.
3.1.3 Influence of the reaction temperature. The reaction temperature is an important parameter to control the kinetics of graft copolymerization. The influence of reaction temperature was carried out over the range of 50–90 °C with a fixed 6 wt% BPO, 50 wt% chromium methacrylate, reaction time of 4 h. Fig. 1(c) shows the GE at different reaction temperatures. This figure shows that the GE increased with increasing reaction temperature, reaching a maximum of 48.3% at 80 °C and then decreases. This is because when the reaction temperature is higher than 80 °C, the number of monomer radicals as well as the active sites on the NBR backbone increases, resulting in more homopolymers than graft copolymers. The reason is also that various side reactions, such as recombination reactions between the produced NBR macroradicals, promote gel formation. Therefore, we recommended optimal temperature should not be higher 80 °C to synthesis the GNBR with no gel content in graft copolymerization.
3.1.4 Influence of the reaction time. The influence of reaction time over the range of 1–8 h was investigated with a fixed 6 wt% BPO, 50 wt% chromium methacrylate at 60 °C. Fig. 1(d) shows that the GE increased with increasing reaction time. The reason is that the longer the reaction time, the greater the possibility of collisions between excited monomer molecules and rubber macroradicals, and so the graft copolymerization reaction proceeds sufficiently. However, the GE reached a maximum value at a reaction time of 4 h and thereafter decreased slightly. Since the reaction time was longer than 4 h, the steric hindrance of the grafted NBR chains was greater, which could inhibit the entering monomers at the grafting site and promote the chance of self-polymerization to form a homopolymer or cross-linking reaction. The optimum reaction time should be 4 h because of the high GE.
3.2 Structural characterization of adhesive
The chemical structures of CrMA, NBR, GNBR, epoxy–novolac resin and GNBR–epoxy–novolac resin adhesive were compared using FTIR.
As shown in Fig. 2, the IR spectrum of the GNBR showed characteristic absorption bands corresponding to the nitrile group (–C
N) of NBR at 2236 cm−1, and characteristic absorption bands corresponding to the out-of-plane bending vibrations of (–CH) bonded to the trans-double bond of butadiene at 968 cm−1. In addition, the characteristic absorption bands corresponding to the carbonyl (C
O), hydroxyl group (–OH) and carboxyl group (–COOH) of chromium methacrylate were found at 1570 cm−1, 3382 cm−1 and 1568 cm−1. However, by graft copolymerization, the characteristic band corresponding to the carbon–carbon double bond (C
C) of chromium methacrylate disappeared at 1645 cm−1. These results suggest that grafting of chromium methacrylate onto NBR backbond was achieved successfully.
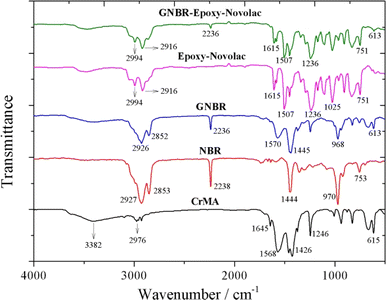 |
| Fig. 2 FTIR spectra of CrMA, NBR, GNBR, epoxy–novolac resin and GNBR–epoxy–novolac resin adhesive. | |
The modification of epoxy–novolac resin by GNBR was also confirmed. The IR spectrum of the GNBR–epoxy–novolac resin adhesive clearly showed both the characteristic absorption bands for GNBR and the characteristic absorption bands for epoxy–novolac resin. The characteristic absorption bands of the –CN group at 2236 cm−1 and the characteristic absorption bands of the benzene ring of the epoxy–novolac resin at 1615 cm−1, 1507 cm−1, and 1236 cm−1 were all observed. The presence of these bands indicates that the GNBR was successfully incorporated into the epoxy–novolac resin.
3.3 Thermal analysis
The curves of TGA of GNBR–epoxy–novolac resin modified with different contents of GNBR are shown in Fig. 3. As shown in Fig. 3, the pyrolysis behavior of all GNBR–epoxy–novolac resins with one main mass loss step is similar.
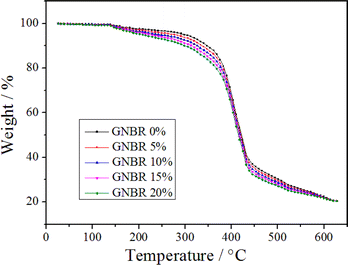 |
| Fig. 3 TGA curves of GNBR–epoxy–novolac resins. | |
Table 1 shows the thermal degradation characteristics of GNBR–epoxy–novolac resin modified with different contents of GNBR at 5%, 10% and 50% mass loss. As shown in Table 1, the temperature values for 5%, 10% and 50% mass loss decreased with increasing GNBR content. This is because of the poor thermal resistance of GNBR compared to epoxy novolac resin. All GNBR–epoxy–novolac resins are stable up to 300 °C and undergo rapid pyrolysis in the range of 370 °C to 400 °C.
Table 1 Thermal degradation characteristics of GNBR–epoxy–novolac resins
Samples |
T5% (°C) |
T10% (°C) |
T50% (°C) |
GNBR 0% |
297.2 |
347.2 |
421.2 |
GNBR 5% |
277.1 |
336.6 |
419.5 |
GNBR 10% |
242.6 |
325.8 |
417.9 |
GNBR 15% |
222.5 |
315.5 |
416.6 |
GNBR 20% |
208.8 |
299.3 |
414.9 |
3.4 Mechanical properties
The tensile stress–strain curves and mechanical properties of GNBR–epoxy–novolac resin with different contents of GNBR at both RT and 233 K are shown in Fig. 4 and Table 2.
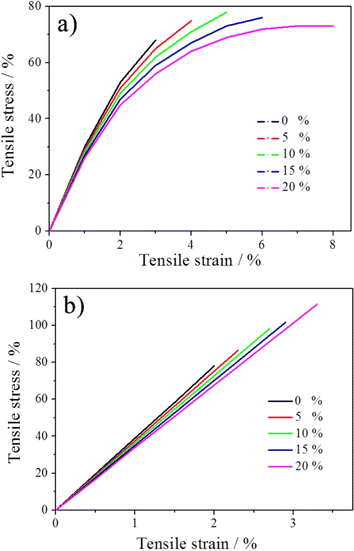 |
| Fig. 4 Typical tensile stress–strain curves of GNBR–epoxy–novolac resins at both RT (a) and 233 K (b). | |
Table 2 Mechanical properties of GNBR–epoxy–novolac resins
GNBR (wt%) |
Tensile strength (MPa) |
Young's modulus (GPa) |
Failure strain (%) |
Lap shear strength (LSS) (MPa) |
RT |
233 K |
RT |
233 K |
RT |
233 K |
RT |
233 K |
0 |
68.1 |
78.7 |
2.27 |
3.91 |
2.88 |
1.93 |
84.6 |
93.3 |
5 |
75.6 |
86.5 |
1.87 |
3.76 |
4.02 |
2.21 |
91.4 |
101.8 |
10 |
78.3 |
98.3 |
1.56 |
3.64 |
4.83 |
2.68 |
93.6 |
113.9 |
15 |
76.7 |
101.8 |
1.27 |
3.51 |
5.87 |
2.85 |
91.7 |
116.4 |
20 |
73.1 |
111.5 |
1.04 |
3.38 |
7.86 |
3.07 |
88.5 |
126.6 |
The data for the tensile strength, Young's modulus and failure strain of GNBR–epoxy–novolac resins with GNBR content at RT and 233 K were obtained from the tensile stress–strain curves using REGER test software and the LSS was determined by Zwick Z050 extensometer according to ASTM D-1002 method.10
As shown in Table 2, the tensile strength and LSS increased with an increase in GNBR content at RT and reached a maximum at 10% and thereafter decreased. Compare to the failure strain of GNBR–epoxy–novolac resins at RT and 233 K, the resin has relatively lower brittleness and higher toughness at RT.
Generally, the introduction of soft rubber material into brittle epoxy–novolac resins would reduce the residual internal stresses in the cured epoxy novolac resins, which increases the strength. Thus, the reason for the increase in tensile strength and LSS of GNBR–epoxy–novolac resins with increasing addition of GNBR is that GNBR increases the ductility of brittle epoxy–novolac resin, thereby decreases the residual internal stresses. The reason is also the physicochemical binding between the hydroxyl groups in GNBR and the epoxy groups of epoxy–novolac resin.
However, GNBR is a soft rubber material with low strength, so that the addition of high content of GNBR results in a decrease in tensile strength and LSS of GNBR–epoxy–novolac resins. As a result, the tensile strength and LSS reached maximum when the GNBR content was 10%. On the other hand, at low temperatures, the tensile strength and LSS increases with increasing the GNBR content, unlike at RT. This indicates that at low temperature, epoxy–novolac resins become more brittle and GNBR with lower glass transition temperature plays a more important role in enhancing tensile strength by eliminating internal residual stress.
Table 2 also shows that the tensile strength and LSS of GNBR–epoxy–novolac resins is higher at 233 K than at RT with the same composition. This can be explained that when the temperature decreases from RT to 233 K, the thermal motion of molecules in the GNBR–epoxy–novolac resins will be weakened, thereby chemical bonds and molecules will shrink and the bonding forces between molecules will become strong. On the other hand, the relatively strong interface bonding between GNBR and epoxy–novolac resins is formed, which requires more energy to break the sample at low temperature. Moreover, the soft GNBR phase has a stronger mechanical strength at 233 K than at RT. As a result, the mechanical strength of the modified epoxy–novolac resins with the same GNBR content is higher at 233 K than at RT. Furthermore, Table 2 shows that the Young's modulus of GNBR–epoxy–novolac resins decreases gradually with increasing GNBR content. This is because GNBR is flexible filler.
4. Conclusions
In this study, GNBR was prepared by solution graft copolymerization of chromium methacrylate and NBR, and the effect of modification of epoxy–novolac resin by GNBR was examined at both RT and 233 K in comparison with the mechanical properties of pure epoxy–novolac resin. The optimum conditions for grafting reaction to obtain the highest grafting efficiency 48.7% were 50/50 wt% CrMA/NBR, 6 wt% initiator BPO, and 4 h reaction time at 80 °C. The graft copolymerization result was confirmed using FTIR.
The results of mechanical test show that the tensile strength, shear strength and failure strain of the modified epoxy–novolac adhesive have been simultaneously enhanced by the introduction of GNBR. The tensile strengths at both RT and 233 K of the modified epoxy–novolac resin with 10% GNBR content were increased by 14.9% and 41.7% respectively compared with that of the pure epoxy–novolac resin. The failure strain was also enhanced by the introduction of GNBR. The Young's modulus was slightly reduced by the introduction of soft GNBR. The simultaneous increase in tensile strength and fracture strain of the GNBR modified epoxy–novolac resin is attributed to the reduction in internal residual stress occurs during the curing and the hindrance of crack propagation during the fracture process by the soft GNBR added to the epoxy–novolac resin. Consequently, the addition of GNBR to epoxy–novolac resin adhesive can improve the adhesive strength.
Data availability
The data that support the findings of this study are available from the corresponding authors upon reasonable request. The results presented in the study have been obtained by using the experiments of graft copolymerization.
Conflicts of interest
There are no conflicts to declare.
Acknowledgements
This work is supported by National Committee of Science and Technology in DPR Korea.
References
- Y. B Gao, W. Zhang, P. Xu, X. M. Cai and Z. Q. Fan, Int. J. Impact Eng., 2018, 122, 60–72 CrossRef.
- A. A. C. Silva, T. I. Gomes, B. D. P. Martins, R. B. R. Garcia, L. D. S. Cvidanes and E. Y. Kawachi, J. Inorg. Organomet. Polym., 2020, 8, 3105–3115 CrossRef.
- T. Trzepiecinski, A. Kubit, R. Kudelski, P. Kwolek and A. Obłój, Int. J. Adhes. Adhes., 2018, 85, 29–36 CrossRef CAS.
- V. Anoop, S. Sankaraiah, S. N. Jaisankar, S. Chakraborty and N. L. Mary, J. Adhes., 2021, 1, 1–18 Search PubMed.
- S. M. J. Razavi, M. R. Ayatollahi, E. Esmaeili and L. F. M. da Silva, Eur. J. Mech. A/Solids, 2017, 65, 349–359 CrossRef.
- Y. Ji, Y. Chen, X. Y. Han, X. Z. Hu, B. Y. Yuan and Y. J. Qiao, Polym. Test., 2020, 86, 106492 Search PubMed.
- S. Bayat, O. M. Jazani, P. Molla-Abbasi, M. Jouyandeh and M. R. Saeb, Prog. Org. Coat., 2019, 136, 105201 CrossRef.
- G. R. Rajkumar, M. Krishna, H. N. Narasimhamurthy and Y. C. Keshavamurthy, J. Inst. Eng. (India): C, 2017, 3, 335–342 Search PubMed.
- C. Gouri, R. Ramaswamy and K. N. Ninan, Int. J. Adhes. Adhes., 2000, 20, 305–314 CrossRef.
- K. K. Hennemann and D. M. Lenz, Int. J. Adhes. Adhes., 2019, 89, 11–18 CrossRef.
- L. Zhou, Y. W. Fu, T. Yin and Z. Y Luo, Tribol. Int., 2019, 129, 314–322 CrossRef.
- R. Thomas, Y. M. Ding, Y. L. He, L. Yang, P. Moldenaers, W. M. Yang, T. Czigany and S. Thomas, Polymer, 2008, 49, 278–294 CrossRef.
- H. Yahyaie, M. Ebrahimi, H. V. Tahami and E. R. Mafi, Prog. Org. Coat., 2013, 76, 286–292 CrossRef.
- A. Dadian and S. Rahnama, Int. J. Adhes. Adhes., 2021, 107, 102854 CrossRef.
- K. Shimamoto, S. Batorova, K. Houjou, H. Akiyama and C. Sato, J. Adhes., 2021, 15, 1388–1403 CrossRef.
- P. Yu, H. He, C. Jiang, Y. C. Jia, D. Q. Wang, X. J. Yao, D. M. Jia and Y. F. Luo, J. Appl. Polym. Sci., 2016, 133, 42922 CrossRef.
- M. Rutnakornpituk, Eur. Polym. J., 2005, 41, 1043–1052 CrossRef.
- Y. S. Wang, Z. Y. Wei, X. F. Leng, K. H. Shen and Y. Li, Polymer, 2016, 92, 74–83 CrossRef.
- H. Yahyaei, M. Ebrahimi, H. V. Tahami, E. R. Mafi and E. Akbarinezhad, Prog. Org. Coat., 2017, 113, 136–142 CrossRef.
- J. Chudzik, D. M. Bielinski, M. Bratychak, Y. Demchuk, O. Astakhova, M. Jedrzejczyk and G. Celichowski, Materials, 2021, 14, 1285 CrossRef.
- S. Salaeh, T. Banda, V. Pongdong, S. Wießner, A. Das and A. Thitithammawong, Eur. Polym. J., 2018, 107, 132–142 CrossRef.
- P. Saramolee, N. Lopattananon and K. Sahakaro, Eur. Polym. J., 2014, 56, 1–10 CrossRef.
- S. Taheri, Y. Hassani, G. M. M. Sadeghi, F. Moztarzadeh and M. C. Li, J. Appl. Polym. Sci., 2016, 133, 43699 CrossRef.
- J. Y. Wang, C. Y. Wan, Y. Zhang, Y. H. Zhai, S. Q. Song, W. T. Ren and Z. L. Peng, J. Appl. Polym. Sci., 2016, 133, 43408 CrossRef.
- K. Yimmut, K. Homchoo and N. Hinchiranan, Colloids Surf., A, 2018, 540, 11–22 CrossRef.
- N. H. Yusof, K. Kosugi, T. K. Song and S. Kawahara, Polymer, 2016, 88, 43–51 CrossRef.
- S. H. Wan, T. X. Li, S. B. Chen, X. Huang, S. W. Cai and X. R. He, Compos. Sci. Technol., 2020, 195, 108193 CrossRef.
- T. Kochthongrasamee, P. Prasassarakich and S. Kiatkamjornwong, J. Appl. Polym. Sci., 2006, 101, 2587–2601 CrossRef.
- S. Kawahara, T. Kawazura, T. Sawada and Y. Isono, Polymer, 2003, 44, 4527–4531 CrossRef.
- F. E. Okieimen and I. N. Urhoghide, J. Appl. Polym. Sci., 1996, 59, 1803–1808 CrossRef.
- P. C. de Oliveira, A. M. de Oliveira, A. Garcia, J. C. de Souza Barboza, C. A. de Cavalho Zavaglia and A. M. dos Santos, Eur. Polym. J., 2005, 41, 1883–1892 CrossRef.
|
This journal is © The Royal Society of Chemistry 2024 |
Click here to see how this site uses Cookies. View our privacy policy here.