DOI:
10.1039/D4RA05248J
(Paper)
RSC Adv., 2024,
14, 30971-30981
Novel dithioamide extractant for highly selective separation of Pd from acidic leach liquors of waste auto-catalysts
Received
19th July 2024
, Accepted 17th September 2024
First published on 27th September 2024
1. Introduction
Platinum group metals (PGMs) are widely used in automobile manufacturing, industrial catalysis, petrochemical, aerospace and other industries.1–4 With the stricter regulations on automobile emission issued by many countries, most PGMs are consumed in auto-catalysts to reduce harmful emissions (84% Pd, 41% Pt and 90% Rh in 2023 (ref. 5)). Waste auto-catalysts contain 1–9 g per kg PGMs, thousands of times higher than natural ores.6 On the other hand, natural PGMs resources are limited and concentrated in only a few countries (South Africa 84.5% and Russia 7%7). Recovering PGMs from waste auto-catalysts is an effective way to balance their supply and demand.
Pd separation from leaching solutions of waste auto-catalysts is a key step in PGMs recovery. The commonly used methods include adsorption,8,9 solvent extraction,10,11 membrane separation12,13 and precipitation.14,15 Among them, solvent extraction has merits of low cost, easy operation and high efficiency. PGMs recovery from leaching solutions of waste auto-catalysts by solvent extraction has been extensively studied in recent years. High, efficient Pd recovery lies in research and development of novel extractants.16 The traditional commercialized dialkyl sulfides (DHS and DOS17,18) and oxime extractants (LIX 63, LIX 84I, SME 529 (ref. 19–22)) have drawbacks of very slow extraction kinetics for Pd. Neutral organic phosphorus extractants (TBP, Cyanex 923 (ref. 23–25)) and amines (Alamine 308, Alamine 336 (ref. 26 and 27)) extract Pd through anion exchange extraction mechanism, and the co-existing Pt will also be extracted.
Many novel extractants emerged, such as ionic liquids (iodotrihalide,28 phosphonium,29 and trioctylammonium nitrate30), calixarene derivatives (p-tert-butyl-thiacalix[4]arene tetrathioamide,31 and 5,11,17,23-tetra-tert-butyl-25,26,27,28-tetra[(2-ethylthio)ethoxy]thiocalix[4]arene32), S-containing extractants (dithiophenol-based extractant,33 4-[(hexylsulfanyl)methyl]-3,5-dimethyl-1H-pyrazole,34 benzimidazole and 2-mercaptobenzimidazole,35 DPYF and poly-EDDYPF,36 and N,N′-dimethyl-N,N′-diphenyl sulfide-containing diamide37), amide-containing extractants (1-butyl-3-(2-ethylhexyl)urea,38 N,N′-dimethyl-N,N′-dicyclohexyltetradecylmalonamide,39 and methylamino-bis-N,N-dioctylacetamide40). Most of these extractants have complex structures, high synthetic costs, slow extraction kinetics, poor selectivity, or only suitable for Pd selective extraction from low-acidic solutions (<1 mol per L HCl). The development of novel efficient extractants for Pd recovery from high acidic chloride media leaching solutions has always been an important task.
Thioamide-based extractants have attracted attention due to their fast extraction kinetics, strong extractability, excellent selectivity, and good reusability. Several thioamide extractants have been reported, including structurally simple agents such as TA-813,41 TA-804, TA-806, and TA-826,42 as well as more complex compounds like 1,1′-bis[(dimethylthiocarbamoyl)oxy]-2,2′-thiobis[4-t-butylbenzene]43 and calixarene derivatives 25,26,27,28-tetrakis(N-n-octylthiocarbamoyl)methoxy-5,11,17,23-tetra-tert-butylcalix[4]arene.44 However, there are few thioamide-based pincer extractants having been reported except 1,3-bis(dimethylthiocarbamoyloxy)benzene.45 In this paper, a novel pincer extractant N,N′-dibutyl-m-phenyldithioamide (marked as DBTB-4) was successfully synthesized and characterized by FT-IR, 1H NMR, 13C NMR (DEPT 135) and ESI-MS. The effect of diluent, equilibrium time, acidity, DBTB-4 concentration on Pd extraction were investigated. The selectivity of DBTB-4 was also studied. The possibility of selective separation of Pd using DBTB-4 from leaching liquor of waste auto-catalysts was also evaluated. The palladium (Pd) extraction mechanism using DBTB-4 from chloride media was elucidated through Fourier Transform Infrared Spectroscopy (FT-IR), Proton Nuclear Magnetic Resonance (1H NMR), X-ray Photoelectron Spectroscopy (XPS), Electrospray Ionization High-Resolution Mass Spectrometry (ESI-HRMS), and Elemental Analysis (EA).
Structures of the reported thioamide-based extractants and DBTB-4 are shown in Fig. 1.
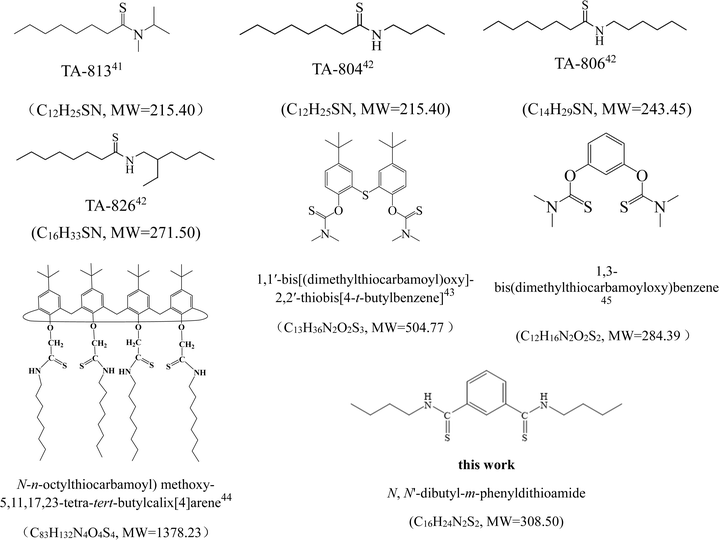 |
| Fig. 1 Structures of thioamide-based extractants. | |
2. Experimental
2.1 Reagents
Isophthaloyl chloride (98%) and n-butylamine (99%) were both bought from Shanghai Macklin Biochemical Co., Ltd (China). Lawesson's reagent (>98%) was supplied by Shanghai Adamas Reagent Co., Ltd (China). Solvents anhydrous ether, absolute ethanol, toluene, petroleum ether (60–90 °C) and ethyl acetate were all analytical reagents (A.R.), and provided by Sinopharm Chemical Reagent Co., Ltd (Beijing, China). Column chromatography silica gel (60–80 mesh) was manufactured by Qingdao Haiyang Chemical Co., Ltd (China).
Metal ion stock solutions were prepared by directly dissolving their chlorides in deionized water. PGMs PdCl2 (Pd ≥ 59%), PtCl4 (Pt ≥ 57%) and RhCl3·3H2O (99%) were bought from Sinopharm Chemical Reagent Co., Ltd (Beijing, China), Shanghai Macklin Biochemical Co., Ltd (China) and Energy Chemical (Shanghai, China), respectively. Non-PGMs ZrCl4 (99.9%), CeCl3·7H2O (99.9%), FeCl3·6H2O (A.R.), AlCl3·6H2O (A.R.), MgCl2·6H2O (A.R.), CuCl2·2H2O (A.R.), ZnCl2 (98%), CoCl2·6H2O (A.R.), NiCl2·6H2O (A.R.) and hydrochloric acid (guarantee reagent, G.R.) were all from Sinopharm Chemical Reagent Co., Ltd (Beijing, China). Diluents chloroform (A.R.), kerosene (reagent grade) and isooctanol (A.R.) were all bought from Shanghai Macklin Biochemical Co., Ltd (China).
2.2 Instrumentation
A DF-101S thermostatic magnetic stirrer with oil bath (Shanghai Lichen Bangxi Instrument Co., Ltd, China) was used to synthesize the extractant. An R-1001-V rotary evaporator (Zhengzhou Great Wall Technology Industry and Trade Co., Ltd, China) was adopted to remove organic solvent. A UMV-2 Multi-tube Vortexer (Beijing Usun Technologies Co., Ltd, China) and a Guanghe TD4C Low-Speed Tabletop Centrifuge (Changzhou, China) were used to mix the aqueous-organic phases and then accelerate their separation, respectively.
The extractant was characterized by a Fourier transform infrared spectrometer (PerkinElmer Frontier, USA), a JEOL JNM-ECA600 spectrometer (Japan), a Bruker Avance III HD 500 MHz (Switzerland), a X-ray Photoelectron Spectroscopy (Thermo Scientific K-Alpha, USA) and a LCMS-IT-TOF spectrometer (Japan) to give the spectra of FT-IR, 1H NMR, 13C NMR (DEPT 135), HSQC and ESI-HRMS, respectively. Elemental analysis was performed using an Elementar Unicube (Germen) in CHNS mode. The metal ion concentration in aqueous phases were tested by an iCAP 7400 ICP-OES (Thermo Fisher Scientific, USA).
2.3 Synthesis
The synthetic route of the extractant N,N′-dibutyl-m-phenyldithioamide (DBTB-4) is shown in Scheme 1. It mainly contains the following two steps: Generation of N,N′-dibutyl-m-phenyldiamide and its thiocarbonylation with Lawesson's reagent.
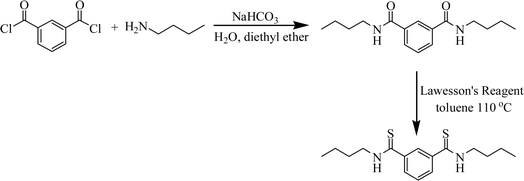 |
| Scheme 1 Synthetic route of N,N′-dibutyl-m-phenyldithioamide. | |
(1) Generation of N,N′-dibutyl-m-phenyldiamide. A portion of 15.0 g isophthaloyl chloride was dissolved in 50 mL anhydrous ether. This solution was slowly dropped into a mixture of 11.3 g n-butylamine (0.155 mol), 15.6 g NaHCO3, 150 mL deionized water and 30 mL anhydrous ether in ice bath using a constant pressure dropping funnel under magnetic stirring. After complete dropping, the mixture was kept stirring for another 4.5 h, during which 50 mL anhydrous ether was added. The generated precipitant was separated by filtration, and washed first with a hot mixture of ethanol and deionized water (v/v = 1
:
3) and then with cold ethanol. After drying, 18.8 g white flocculent solid product was obtained (yield: 92.1%).
(2) Conversion to N,N′-dibutyl-m-phenyldithioamide. A portion of 30.28 g Lawesson's reagent was reacted with 18.8 g of the obtained N,N′-dibutyl-m-phenyldiamide product in 100 mL dry toluene under stirring and reflux conditions for 4 h. When the temperature cooled down to 90 °C, 50 mL deionized water was added and reacted for another 1 h at this condition. Then the mixture was cooled down to room temperature, and the organic phase was separated and washed successively with 4% NaHCO3 and saturated NaCl solutions, and then dried with anhydrous Na2SO4. After removing the solvent in vacuum, a waxy crude product with orange-red hue of 21.74 g N,N′-dibutyl-m-phenyldithioamide was obtained (yield: 87.6%). This product was further purified first by column chromatography packed with silica gel (60–80 mesh) and eluted with a mixture of petroleum ether and ethyl acetate (v/v = 2
:
1) and then by recrystallization in chloroform and dodecane (v/v = 1
:
4). The purified product was washed with petroleum ether (60–90 °C), and then dried at room temperature. Finally, yellowish needle-shaped crystals were obtained.
2.4 Extraction experiments
The extraction experiments were carried out by mixing the aqueous and organic phases, which were sealed in a 10 mL, 15 mL or 20 mL centrifugal tube, on the Multi-tube Vortexer at 2500 rpm for a period of time. After centrifugation at 3000 rpm for 5 min, the aqueous phase was separated and determined by ICP-OES to give its metal ion concentration. All experiments were conducted three times, and the data was averaged. The corresponding metal ion concentration in the organic phase was calculated by mass balance (see eqn (1)). The metal ion extraction percentage (E, %) and distribution ratio (D) were calculated by eqn (2) and (3), respectively. |
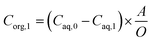 | (1) |
|
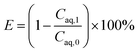 | (2) |
|
 | (3) |
where Caq,0 stands for the metal ion concentration in aqueous phase before extraction; Caq,1 and Corg,1 represent the metal ion concentrations in aqueous and organic phases after extraction, respectively; A/O is phase ratio.
3. Results and discussion
3.1 Characterization
The purified N,N′-dibutyl-m-phenyldithioamide was characterized by FT-IR, 1H NMR, 13C NMR (DEPT 135), ESI-MS and EA. The results are shown in Fig. 2. In the FT-IR spectrum (Fig. 2(a)), the peaks at 3179.25 cm−1 and 3047.31 cm−1 are attributed to N–H stretching vibration, and the peak at 1544.72 cm−1 is caused by N–H bending vibration. The peaks at 2958.16 cm−1 and 2872.14 cm−1 are assigned to unsymmetrical and symmetrical stretching vibrations of CH3, respectively, and the peak at 2929.80 cm−1 is caused by unsymmetrical stretching vibration of CH2. The peaks at 1198.36 cm−1 and 1078.53 cm−1 are attributed to C
S and C–N stretching vibrations, respectively. The peaks at 1448.46 cm−1, 1418.98 cm−1 and 1395.12 cm−1 are skeleton vibration of benzene ring, and those at 690.80 cm−1 and 735.90 cm−1 are assigned to out-of-plane bending vibration of C–H in the benzene ring.45–47
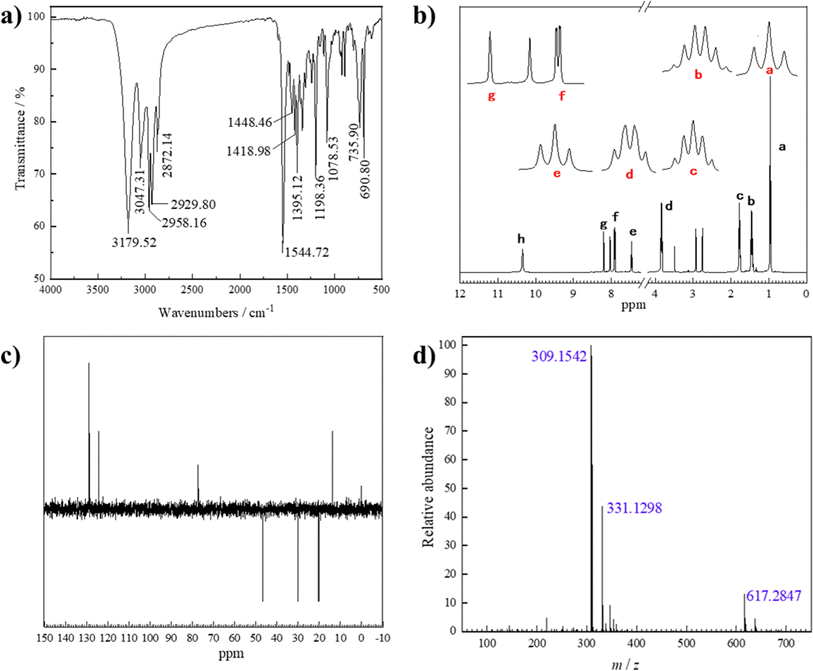 |
| Fig. 2 Characterization results of N,N′-dibutyl-m-phenyldithioamide. (a) FT-IR (b) 1H NMR (c) DEPT 135 (d) ESI-HRMS. | |
1H NMR (600 MHz, DMF-d7) δ/ppm (Fig. 2(b)): 0.96 (t, 6H, –C
3), 1.45 (m, 4H, CH3–C
2), 1.77 (m, 4H, CH3–CH2–C
2), 3.83 (q, 4H, –NH–C
2–), 7.46 (t, 1H, Ar–
), 7.91 (dd, 2H, Ar–
), 8.20 (s, 1H, Ar–
), 10.35 (s, 2H, –N
). The single peak at 3.49 ppm is caused by H2O.
DEPT 135 (125 MHz, CDCl3-d1) δ/ppm (Fig. 2(c)): 13.79 (+, CH3), 20.32 (−, CH2), 30.17(−, CH2), 46.86 (−, CH2), 124.38 (+, CH), 128.77 (+, CH), 128.97 (+, CH). The peaks at 124.38 ppm, 128.77 ppm and 128.97 ppm are assigned to the three kinds of carbon of C–H in the benzene ring.
ESI-HRMS m/z (Fig. 2(d)): 309.1542 (M + H)+, 331.1298 (M + Na)+, 617.2847 (2M + H)+, where M stands for the extractant molecule weight.
The results of the elemental analysis for DBTB-4 are presented in Table 1. The molar ratios of C
:
H
:
N
:
S in the product are 8
:
12
:
1
:
1, consistent with the chemical formula C16H24N2S2 of DBTB-4.
Table 1 Elemental analysis results of DBTB-4
Element |
C |
H |
N |
S |
C : H : N : S |
Content (wt%) |
62.13 |
7.525 |
8.835 |
20.631 |
8 : 12 : 1 : 1 |
Content (mmol g−1) |
51.73 |
74.65 |
6.31 |
6.44 |
All the data are consistent with the structure of N,N′-dibutyl-m-phenyldithioamide.
3.2 Diluent
To find out an appropriate diluent for Pd extraction by the novel extractant N,N′-dibutyl-m-phenyldithioamide, four kinds of diluents (toluene, chloroform, isooctanol, kerosene) and their mixtures were investigated. The extractant concentration was all 1 mmol L−1. The aqueous phase contained 64.48 mg per L Pd and 3 mol per L HCl. The phase ratio A/O was 2
:
1. The vibrating time was 1 h. The results are shown in Table 2. The phenomena after extraction are shown in Fig. 3.
Table 2 Pd extraction behaviors by N,N′-dibutyl-m-phenyldithioamide dissolved in different diluents
|
Toluene |
Chloroform |
Isooctanol |
Kerosene |
Vkerosene/Visooctanol |
1 : 1 |
1 : 3 |
N,N′-Dibutyl-m-phenyldithioamide is nearly insoluble in kerosene. |
E/% |
54.22 |
77.50 |
47.74 |
— |
73.74 |
78.05 |
Phenomena |
Precipitation |
Precipitation |
Clear |
Insolublea |
Precipitation |
Clear |
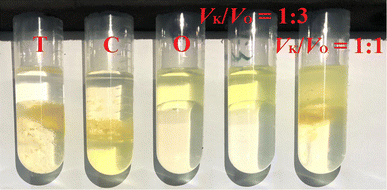 |
| Fig. 3 Phenomena of Pd extraction by N,N′-dibutyl-m-phenyldithioamide dissolved in different diluents (T – toluene, C – chloroform, O – isooctanol, Vk/Vo – Vkerosene/Visooctanol). | |
All the investigated single diluents are not good for Pd extraction: Precipitants are generated with toluene and chloroform; low Pd extraction percentage occurs with isooctanol; the extractant is nearly insoluble in kerosene. Considering kerosene and isooctanol are commonly used in metal ion extraction and separation industries,48,49 their mixtures with Vkerosene/Visooctanol of 1
:
1 and 1
:
3 were investigated as diluents. At Vkerosene/Visooctanol of 1
:
1, precipitation also occurred. Fortunately no precipitants were generated and the Pd extraction percentage was as high as 78.05% at Vkerosene/Visooctanol of 1
:
1, which was the highest among all the investigated diluents. Hence, a mixture of kerosene and isooctanol with Vkerosene/Visooctanol of 1
:
3 was adopted in the following experiments.
3.3 Equilibrium time
To evaluate the extraction speed of Pd by N,N′-dibutyl-m-phenyldithioamide, the effect of vibrating time on Pd extraction percentage (EPd) was investigated. The extractant concentration was 1.5 mmol L−1. The aqueous phase contained 62.50 mg per L Pd and 4 mol per L HCl. The phase ratio A/O was 2
:
1. The results are shown in Fig. 4. The EPd reached more than 80% after vibrating only 10 min. It reached equilibrium at vibrating time of 30 min. The Pd extraction speed by N,N′-dibutyl-m-phenyldithioamide is faster than most of the reported extractants,20,22,26,27 but a little bit slower than octanethioic acid alkyl amides which have only one thioamide group.41,42 In chloride media, Pd ion exists in the form of [PdCl4]2−. S atom is a soft donor, and it has strong coordination ability with Pd.50 The N,N′-dibutyl-m-phenyldithioamide has two thioamide groups locating at the meta-C of the benzene ring. Both two thioamide groups can interact with Pd. Hence, it needs more time to adjust the position of the DBTB-4 and Pd to form an extracted complex.
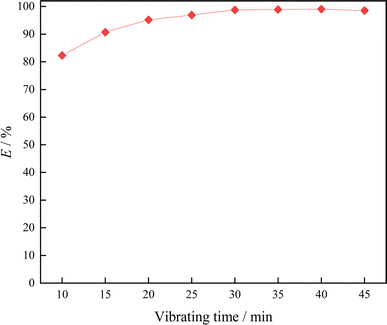 |
| Fig. 4 Effect of vibrating time on Pd extraction by N,N′-dibutyl-m-phenyldithioamide. | |
To assure all the following extractions reach equilibrium, a vibrating time of 40 min was adopted.
3.4 Effect of acidity on Pd extraction
The acidity of the aqueous phase is a key parameter in metal ion extraction process. Considering the relatively high acid concentrations during the PGMs leaching of the waste auto-catalysts, the effect of HCl concentration ranging from 1 to 8 mol L−1 on the Pd extraction by DBTB-4 was investigated. The aqueous phase contained 62 mg per L Pd and 1–8 mol per L HCl. The DBTB-4 concentration in the organic phase was maintained at 1.5 mmol L−1. The phase ratio A/O was 2
:
1. The results are shown in Fig. 5. As the HCl concentration was increased from 1 mol L−1 to 4 mol L−1, the EPd steadily increased from 90.2% to 99.9%. With further increasing the HCl concentration, the Pd were all nearly totally extracted. Higher HCl concentration is beneficial to Pd extraction with DBTB-4.
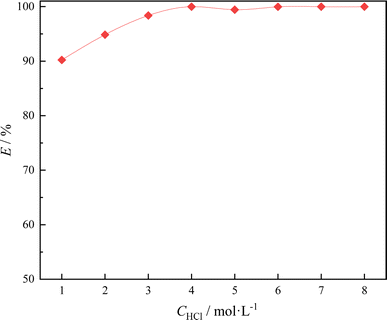 |
| Fig. 5 Effect of HCl concentration on Pd extraction by N,N′-dibutyl-m-phenyldithioamide. | |
3.5 Effect of DBTB-4 concentration on Pd extraction
To investigate the effect of DBTB-4 concentration on Pd extraction efficiency, a series of extraction experiments were conducted by varying the DBTB-4 concentration from 0.25 to 5 mmol L−1. The aqueous phase consisted of 62 mg per L Pd with acidity of 4 mol per L HCl. The A/O ratio was still 2
:
1. The results are shown in Fig. 6.
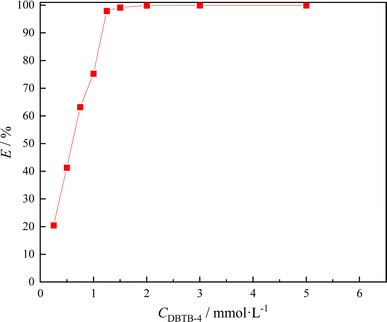 |
| Fig. 6 Effect of N,N′-dibutyl-m-phenyldithioamide concentration on Pd extraction. | |
As the DBTB-4 concentration increased from 0.25 to 1.25 mmol L−1, the EPd rapidly increased from 20.5% to 99.1%. When the DBTB-4 concentration exceeded 1.5 mmol L−1, the Pd in aqueous phase were all totally extracted. When the EPd was less than 100% at the DBTB-4 concentration in the range of 0.25 to 1 mmol L−1, the extractant was of shortage. At these conditions, the Pd concentrations in the organic phase after extraction were calculated according to mass balance, and the molar ratios of DBTB-4/Pd in the organic phase were also calculated. The results are listed in Table 3. The DBTB-4/Pd molar ratios are all around 1, indicating one DBTB-4 molecule probably complexes with one Pd during extraction.
Table 3 The DBTB-4/Pd molar ratio in the organic phase after extraction
CDBTB-4/×10−4 mol L−1 |
CPd(0)/×10−4 mol L−1 |
DBTB-4/Pd molar ratio |
2.5 |
2.4 |
1.0 |
5 |
4.9 |
1.0 |
7.5 |
7.4 |
1.0 |
10 |
8.8 |
1.1 |
3.6 Selectivity
The leaching liquors of waste auto-catalysts usually contain PGMs (Pd, Pt, Rh) as well as base metals, such as Fe, Mg, Ce, Cu, Zr, and Al. Therefore, it is necessary to investigate the selectivity of DBTB-4 for Pd in the presence of Pt, Rh and base metals. Hence, the extraction experiments were carried out from multiple metal feed liquors containing Pd, Pt, Rh, Fe, Mg, Ce, Cu, Zr, and Al. Each metal was 62 ± 2 mg L−1. The acidity was varied from 1 mol per L HCl to 8 mol per L HCl. The DBTB-4 concentration was 1.5 mmol L−1. The phase ratio A/O was still 2
:
1. The results are depicted in Fig. 7.
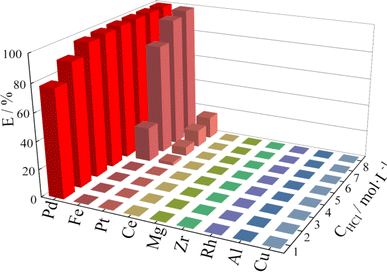 |
| Fig. 7 Selective extraction of Pd from multiple metal feed liquors by N,N′-dibutyl-m-phenyldithioamide. | |
When the acidity was equal to or less than 4 mol per L HCl, only Pd was selectively extracted, and the EPd increased from 77.9% to 99.7% with the HCl concentration increasing in this range. When the acidity was equal to and more than 5 mol per L HCl, nearly all Pd were extracted into the organic phase. Meanwhile, the EFe rapidly increased from 25.4% to 98.8%, the EPt gradually rose from 2.3% to 16.1%, and other metals were hardly extracted. Thus, the optimum acidity was probably 3–4 mol per L HCl for Pd recovery from leaching liquors of waste auto-catalysts by DBTB-4.
3.7 Pd selective separation from simulated leaching solutions of waste auto-catalysts
In real leaching liquors of waste auto-catalysts, the metal ion concentrations are always different. Some base metals, like Al and Mg, may have ten times higher concentration than Pd. Therefore, we investigated the Pd selective extraction from simulated leaching liquor of waste auto-catalysts by DBTB-4 at acidity of 4 mol per L HCl. The simulated leaching liquor was prepared according to ref. 13, and its composition is shown in Table 4. The DBTB-4 concentration was 2 mmol L−1. The phase ratio was 1
:
1. The results are shown in Fig. 8. Pd was also selectively extracted with EPd of 99.62%, while other metals were all hardly extracted except Pt, of which extraction percentage EPt was 4.96% (βPd/Pt = 5100.69). The results confirm that DBTB-4 can efficiently and selectively extract Pd from leaching liquors of waste auto-catalysts.
Table 4 Composition of the simulated leaching liquor of waste auto-catalysts
|
Pd |
Pt |
Rh |
Ce |
La |
Cu |
Fe |
Al |
Mg |
Zn |
CM/mg L−1 |
149.0 |
73.7 |
25.0 |
384.7 |
556.4 |
8.7 |
48.7 |
3339.3 |
1207.6 |
20.8 |
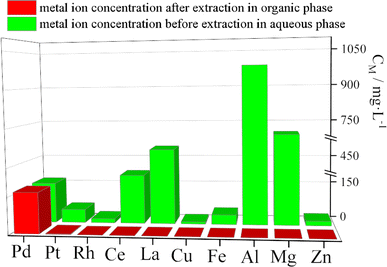 |
| Fig. 8 Pd selective extraction from simulated leaching liquor of waste auto-catalysts by N,N′-dibutyl-m-phenyldithioamide. | |
3.8 Extraction mechanism
To reveal the extraction mechanism of Pd by DBTB-4, the extracted complex DBTB-4–Pd was characterized by FT-IR, 1H NMR, HSQC, XPS, ESI-HRMS and EA, and the results were compared with those of DBTB-4. DBTB-4–Pd was obtained by dissolving DBTB-4 in chloroform, and then extracting Pd to form solid, which was washed with chloroform and deionized water and then dried via rotary evaporation. Unless otherwise noted, all DBTB-4–Pd samples in the figures were extracted under conditions with acidity of 4 mol per L HCl. In the FT-IR spectra shown in Fig. 9(a), the stretching vibration of C
S shifts from 1198.36 cm−1 to 1189.86 cm−1 and becomes weak after extraction. This indicates that C
S is the functional group, of which S atom might coordinate with Pd during extraction. The N–H stretching vibrations of DBTB-4 at 3179.25 cm−1 and 3047.31 cm−1 respectively shift to 3247.53 cm−1 and 3102.90 cm−1 after extraction. This might be caused by the interaction between C
S and Pd as well as protonation of the thioamino group. The broad peak of DBTB-4–Pd at 3436.53 cm−1 is caused by H2O. The out-of-plane bending vibration of C–H in phenyl of DBTB-4 at 690.80 cm−1 and 735.90 cm−1 disappear and a new peak at 711.60 cm−1 emerges after extraction, indicating the hydrogen atom in the phenyl between the two thioamide groups might lose and a new bond of C–Pd generate.
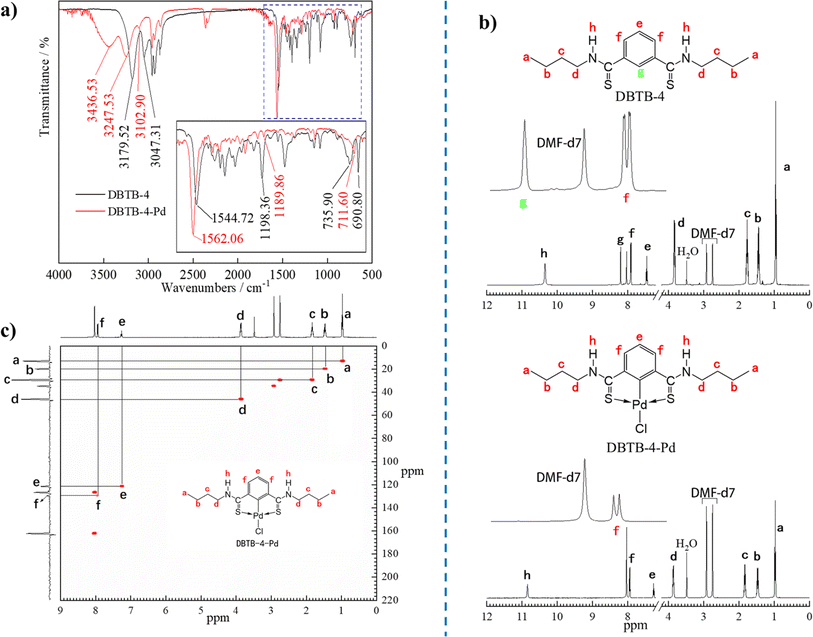 |
| Fig. 9 Characterization results of DBTB-4 and DBTB-4–Pd. (a) FT-IR (b) 1H NMR (c) HSQC. | |
To confirm this, 1H NMR and HSQC were recorded and the results are shown in Fig. 9(b) and (c), respectively. 1H NMR spectra of DBTB-4–Pd (600 MHz, DMF-d7) δ/ppm: 0.97 (t, 6H, –C
3), 1.47 (m, 4H, CH3–C
2), 1.83 (m, 4H, CH3–CH2–C
2), 3.87 (q, 4H, –NH–C
2–), 7.26 (t, 1H, Ar–
), 7.91 (dd, 2H, Ar–
), 10.84 (s, 2H, –N
). The single peak at 3.49 ppm is attributed to H2O. Compared with 1H NMR spectra of DBTB-4, a signal peak at 8.20 ppm disappears, which is the hydrogen atom of Ar–H in the phenyl between the two thioamide groups. This confirms that the H in the phenyl between the two thioamide groups (position g, see Fig. 9(b)) loses during extraction, and the left carbon probably directly interacts with Pd. Besides, the signal peak of –NH– in DBTB-4 does not disappear but shifts from 10.35 ppm to 10.84 ppm after extraction, further confirming it is probably the S atom that interacts with Pd. The HSQC results (Fig. 9(c)) further confirmed the disappearance of the hydrogen atom at position g.
The XPS spectra of DBTB-4 and its complex with Pd DBTB-4–Pd are shown in Fig. 10. The electron binding energies of S 2p3/2 and S 2p1/2 of DBTB-4 respectively shift from 161.92 eV and 163.17 eV to 162.53 eV and 163.69 eV after extraction (Fig. 10(a)), indicating it is probably the two S atoms that directly interact with Pd during extraction. In Fig. 10(b), the electron binding energy of N 1s at 399.72 eV basically remains unchanged after extraction, suggesting that the N atom does not directly participate in interaction with Pd during Pd extraction with DBTB-4 from 3 mol per L HCl. It should be noted that a new peak at 401.29 eV appears in the N 1s fine spectrum of DBTB-4–Pd, which might be caused by protonation of N atom (namely –NH2+–). At acidity of 3 mol per L HCl, the peak at 401.29 eV is relatively weak, showing only a small part of N–H are protonated. It can be inferred that as the acidity increases, more and more N atoms will be protonated. In Fig. 10(b), the electron binding energy of N 1s at 399.72 eV remains basically unchanged across different acidity conditions, suggesting that nitrogen atoms do not directly interact with Pd during extraction from 4 mol per L HCl using DBTB-4. Notably, at 4 mol per L HCl, a new peak at 401.29 eV emerges in the fine spectrum of N 1s in DBTB-4–Pd, likely resulting from the protonation of nitrogen atoms (–NH2+–). At 4 mol per L HCl, the relatively weak peak at 401.29 eV indicates limited protonation of N–H, with a P–NH2+–/P–NH– ratio of 0.30, where “P” denotes peak area. As the acidity increases to 8 mol L−1, the P–NH2+–/P–NH– ratio rises to 0.41, indicating enhanced protonation of nitrogen atoms. This can just explain why the selectivity of DBTB-4 decreases as the HCl concentration exceeds 4 mol L−1. Fig. 10(c) shows the Pd fine spectrum of DBTB-4–Pd. The electron binding energies of Pd 3d5/2 and Pd 3d3/2 are 337.44 eV and 342.71 eV, respectively.
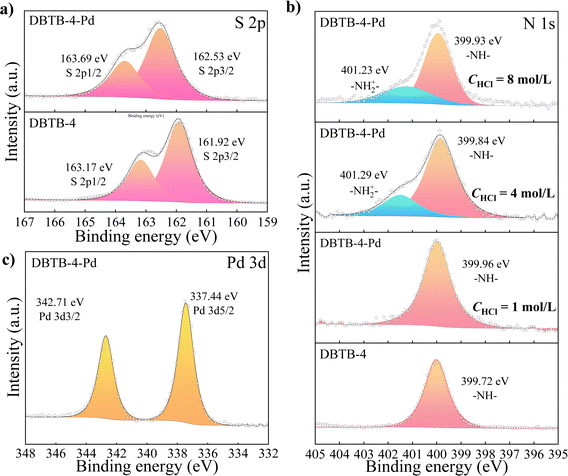 |
| Fig. 10 XPS spectra of DBTB-4 and DBTB-4–Pd. | |
The ESI-HRMS data of DBBT-4–Pd complex also support our speculation (Fig. 11), with peaks at m/z = 170.8336, 307.1334, 343.1103, 446.9988, and 484.9767 corresponding to [L + Cl− − H+]2−, [L − H+]−, [L + Cl−]−, [(L–H)PdCl − H+]−, and [(L–H)PdCl + Cl−]−, respectively.
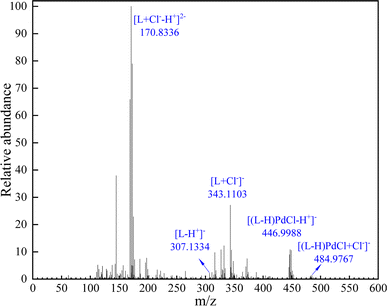 |
| Fig. 11 ESI-HRMS result of DBBT-4–Pd. | |
The elemental analysis results of DBTB-4–Pd complex are shown in Table 5. The total mass minus the mass of C, H, N, and S corresponds to the mass of –PdCl. The molar ratio of N
:
S
:
PdCl at 2
:
2
:
1 further confirms our hypothesis.
Table 5 Elemental analysis results of DBTB-4–Pd complex
Element |
C |
H |
N |
S |
–PdCl |
N : S : PdCl |
Content (wt%) |
41.71 |
59.68 |
5.97 |
14.11 |
32.25 |
2 : 2 : 1 |
Content (mmol g−1) |
34.73 |
59.63 |
42.62 |
44.02 |
22.73 |
Based on the above results, the extraction mechanism of Pd by DBTB-4 from chloride media are confirmed and can be expressed as it is shown in Fig. 12. The extracted complex can be written as (L–H)PdCl, where L stands for one molecule of DBTB-4. The chelation mechanism of DBTB-4 with Pd aligns with the mechanisms reported for S^C^S-type ligands with Pd in the literature.51–53 Protonated DBTB-4 is more hydrophilic, facilitating phase transfer. Additionally, protonated DBTB-4 electrostatically attracts [PdCl4]2−, promoting chelation. This explains why extraction efficiency increases as acidity is increased. However, the protonated amide functional groups exhibit poor selectivity, attracting anions like [PtCl6]2− and [FeCl4]−, which reduce the extractant's selectivity. Therefore, the aqueous phase's acidity should be maintained between 3–4 mol L−1 to ensure the Pd can be selectively extracted.
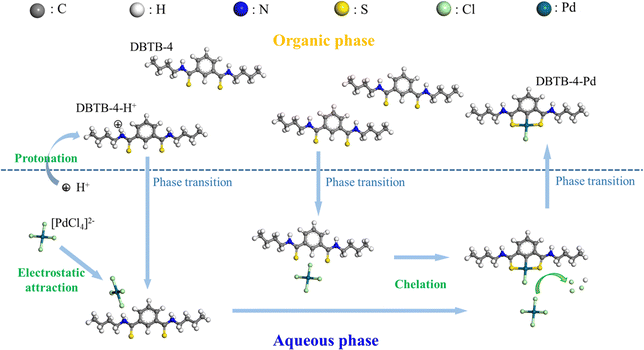 |
| Fig. 12 The extraction mechanism of Pd by DBTB-4 from chloride media. | |
4. Conclusions
A novel pincer extractant N,N′-dibutyl-m-phenyldithioamide (DBTB-4) was successfully synthesized, and its structure was confirmed by FT-IR, 1H NMR, 13C NMR (DEPT 135), ESI-HRMS, and EA. A mixture of kerosene and isooctanol with Vkerosene/Visooctanol of 1
:
3 is suitable as the diluent for Pd extraction by DBTB-4. Neither precipitants nor a third phase is generated. DBTB-4 has rapid extraction kinetics for Pd, and only 30 min is needed to reach equilibrium. DBTB-4 has strong extractability for Pd from chloride media, and it quantitatively extracts Pd with DBTB-4/Pd molar ratio of 1
:
1. DBTB-4 has specific selectivity for Pd at acidities in the range of 1–4 mol per L HCl. When the acidity exceeds 5 mol per L HCl, the selectivity became worse, and Fe and Pt began to be extracted. The higher HCl concentration (>5 mol L−1), the more Fe and Pt being extracted into the organic phase. The optimal acidity for Pd recovery from leaching liquors of waste auto-catalysts is 3–4 mol per L HCl. At this acidity, Pd can be selectively extracted by DBTB-4 leaving nearly all Pt, Rh, Ce, La, Cu, Fe, Al, Mg and Zn in the raffinate. The DBTB-4 extracts Pd from chloride through coordination via the two S atoms and the carbon in the phenyl between the two thioamide groups. The extracted complex can be written as (L–H)PdCl, where L stands for one molecule of DBTB-4.
Data availability
The data supporting this article have been included within the manuscript.
Author contributions
Fan Li: experimentation, writing-original draft, data analysis, revise the manuscript, validation, contact journal; Junlian Wang: writing-review & editing, conceptualization, design of the work, interpretation of data and data analysis, supervision, project administration; Lu Liu: participate in experiments, formal analysis, writing-original draft; Yangge Zhu: contributed materials, validation; Yong Li: participate in experiments, acquisition, analysis.
Conflicts of interest
There are no conflicts to declare.
Acknowledgements
This work was financially supported by the National Key Research and Development Program (2021YFC2901100) and the Open Foundation of State Key Laboratory of Mineral Processing (BGRIMM-KJSKL-2023-28). Special thanks to Peilong Wang for metal ion determination. The authors would like to thank Shiyanjia Lab (https://www.shiyanjia.com) for characterization of 1H NMR, 13C NMR, ESI-HRMS and XPS.
References
- W. B. Li, K. Wu, H. Feng, N. Wang, J. H. Zhang, J. J. Wang and X. F. Li, Tungsten, 2022, 4, 346–355 CrossRef
. - S. R. Bahadori, R. Hart and Y.-W. Hao, Tungsten, 2020, 2, 261–288 CrossRef
. - G. M. Torres, Y. Liu and B. A. Arndtsen, Science, 2020, 368, 318–323 CrossRef CAS PubMed
. - J. Lu, Y. Lei, K. C. Lau, X. Y. Luo, P. Du, J. G. Wen, R. S. Assary, U. Das, D. J. Miller, J. W. Elam, H. M. Albishri, D. Abd El-Hady, Y. K. Sun, L. A. Curtiss and K. Amine, Nat. Commun., 2013, 4, 3290 Search PubMed
. - Johnson Matthey, PGM Market Report May 2023, https://matthey.com/en/products-and-markets/pgms-and-circularity/pgm-markets/pgm-market-reports, accessed 16 April 2024.
- B. Xu, Y. Chen, Y. Zhou, B. Zhang, G. Liu, Q. Li, Y. Yang and T. Jiang, Metals, 2022, 12, 533 CrossRef CAS
. - U.S. Geological Survey, Mineral commodity summaries 2024, https://www.usgs.gov/publications/mineral-commodity-summaries-2024, accessed 16 April 2024.
- C. Kim and H. J. Hong, Ind. Eng. Chem. Res., 2024, 63, 4547–4556 CrossRef CAS
. - S. Shen, T. Pan, X. Liu, L. Yuan, Y. Zhang, J. Wang and Z. Guo, J. Colloid Interface Sci., 2010, 345, 12–18 CrossRef CAS PubMed
. - J. L. Wang, W. Xu, H. Liu, F. S. Yu and H. J. Wang, Miner. Eng., 2021, 163, 106798 CrossRef CAS
. - S. Imdad and R. K. Dohare, Chem. Eng. Process., 2022, 173, 108812 CrossRef CAS
. - C. Fontàs, V. Salvadó and M. Hidalgo, J. Membr. Sci., 2003, 223, 39–48 CrossRef
. - A. T. N. Fajar, T. Hanada and M. Goto, J. Membr. Sci., 2021, 629, 119296 CrossRef CAS
. - K. Matsumoto, Y. Sezaki, S. Yamakawa, Y. Hata and M. Jikei, Metals, 2020, 10, 324 CrossRef CAS
. - J. S. Xia and A. Ghahreman, Sep. Purif. Technol., 2023, 311, 123357 CrossRef CAS
. - Y. K. Taninouchi and T. H. Okabe, Mater. Trans., 2022, 64, 627–637 CrossRef
. - D. Z. Liu and D. X. Deng, J. Southwest China Norm. Univ., Nat. Sci. Ed., 1983, 3, 70–74 Search PubMed
. - L. Pan, G. B. Gu, F. W. Wang and Y. J. Wei, Chin. J. Inorg. Chem., 2008, 24, 520–526 CAS
. - H. T. Truong, M. S. Lee and S. H. Son, Metals, 2017, 7, 541 CrossRef
. - M. V. Rane and V. Venugopal, Hydrometallurgy, 2006, 84, 54–59 CrossRef CAS
. - B. R. Reddy, B. Raju, J. Y. Lee and H. K. Park, J. Hazard. Mater., 2010, 180, 253–258 CrossRef CAS PubMed
. - K. Inoue and T. Maruuchi, Hydrometallurgy, 1986, 16, 93–104 CrossRef CAS
. - R. N. R. Sulaiman, N. Othman, N. Jusoh, N. F. M. Noah, R. Rashid and S. M. Saufi, Chem. Eng. Process., 2021, 168, 108581 CrossRef CAS
. - J. Y. Lee, B. Raju, B. N. Kumar, J.
R. Kumar, H. K. Park and B. R. Reddy, Sep. Purif. Technol., 2010, 73, 213–218 CrossRef CAS
. - B. Gupta and I. Singh, Hydrometallurgy, 2013, 134–135, 11–18 CrossRef CAS
. - T. H. Nguyen, B. N. Kumar and M. S. Lee, Korean J. Chem. Eng., 2016, 33, 2684–2690 CrossRef CAS
. - C. Y. Peng and T. H. Tsai, Desalin. Water Treat., 2014, 52, 1101–1108 CrossRef CAS
. - X. L. Yin, J. Li, X. X. Liu, K. Q. Huang and Y. Z. Yang, J. Hazard. Mater., 2024, 467, 133665 CrossRef CAS PubMed
. - M. Rzelewska-Piekut and M. Regel-Rosocka, Sep. Purif. Technol., 2019, 212, 791–801 CrossRef CAS
. - S. Katsuta and J. Tamura, J. Solution Chem., 2018, 47, 1293–1308 CrossRef CAS
. - S. Ning, R. Xie, L. Zeng and K. Tang, Process Saf. Environ. Prot., 2023, 178, 595–604 CrossRef CAS
. - J. He, Y. Xiong, L. Xu, L. Wang, D. Yao, D. Xia, Y. Tian and Z. Zhao, J. Environ. Chem. Eng., 2022, 10, 108445 CrossRef CAS
. - M. Yamada, T. Ohira, N. Watanabe, H. Katagiri, A. Shibayama and F. J. H. Hamada, Hydrometallurgy, 2022, 215, 105986 CrossRef
. - G. R. Anpilogova, L. A. Baeva, R. M. Nugumanov, A. A. Fatykhov and Y. I. Murinov, Russ. J. Inorg. Chem., 2018, 63, 1100–1106 CrossRef CAS
. - G. Zhang, L. Zhang, Q. Wang, J. Guo, H. Wei and Y. Yang, New J. Chem., 2021, 45, 19467–19475 RSC
. - W. Shi, Y. Hu, Q. Li, T. Q. Lan, X. Y. Zhang and J. Cao, Hydrometallurgy, 2021, 204, 105716 CrossRef CAS
. - H. Narita, K. Morisaku and M. Tanaka, Solvent Extr. Ion Exch., 2021, 39, 533–544 CrossRef CAS
. - Y. Ueda, S. Morisada, H. Kawakita, M. Wenzel, J. J. Weigand and K. Ohto, Sep. Purif. Technol., 2021, 277, 119456 CrossRef CAS
. - M. C. Costa, A. Assunção, A. M. R. da Costa, C. Nogueira and A. P. Paiva, Solvent Extr. Ion Exch., 2013, 31, 12–23 CrossRef CAS
. - M. Matsumiya, Y. Song, Y. Tsuchida and Y. Sasaki, Sep. Purif. Technol., 2020, 234, 115841 CrossRef CAS
. - J. L. Wang, L. Liu, G. D. Xu, P. L. Wang, G. Y. Huang and F. S. Yu, Trans. Nonferrous Met. Soc. China, 2023, 33, 1609–1618 CrossRef CAS
. - J. Wang, L. Liu, G. Xu and F. Li, Miner. Eng., 2023, 202, 108274 CrossRef CAS
. - M. Yamada, M. R. Gandhi, D. Sato, Y. Kaneta and N. Kimura, Ind. Eng. Chem. Res., 2016, 55, 8914–8921 CrossRef CAS
. - M. Yamada, M. R. Gandhi and A. Shibayama, Sci. Rep., 2018, 8, 16909 CrossRef PubMed
. - M. R. Gandhi, M. Yamada, Y. Kondo, A. Shibayama and F. Hamada, RSC Adv., 2016, 6, 1243–1252 RSC
. - P. B. E. Pretsch and M. Badertscher, Structure Determination of Organic Compounds, Springer Berlin, Heidelberg, 2009 Search PubMed
. - W. J. Zhao, S. Zhang, X. Q. An, H. C. Lan, H. J. Liu and J. H. Qu, Chin. J. Environ. Sci., 2022, 43, 8 CrossRef
. - M. Yamada, M. R. Gandhi and A. Shibayama, Sci. Rep., 2018, 8, 16909 CrossRef PubMed
. - Y. Long, G. Zhang, L. Zeng, X. Wu, Z. Li, J. Qin, W. Guan, Q. Li, Z. Cao and S. Wu, Rare Met. Cem. Carbides, 2021, 49, 1–6 CAS
. - L. Chen, K. Wu, M. Zhang, N. Liu, C. Li, J. Qin, Q. Zhao and Z. Ye, Chem. Eng. J., 2023, 466, 143082 CrossRef CAS
. - J. Kuwabara, G. Munezawa, K. Okamoto and T. Kanbara, Dalton Trans., 2010, 39, 6255–6261 RSC
. - T. Murai, Chemistry of Thioamides, Springer, Singapore, 2019 Search PubMed
. - M. Akaiwa, T. Kanbara, H. Fukumoto and T. Yamamoto, J. Organomet. Chem., 2005, 690, 4192–4196 CrossRef CAS
.
|
This journal is © The Royal Society of Chemistry 2024 |
Click here to see how this site uses Cookies. View our privacy policy here.