Biomass-based ionic liquids efficiently catalyzed the cycloaddition reaction of epoxides with CO2 by hydrogen-bonding and the anion cooperative effect†
Received
22nd January 2024
, Accepted 4th March 2024
First published on 14th March 2024
Abstract
Several novel biomass-based ionic liquids having hydroxyl derived from 5-hydroxymethylfurfural (5-HMF) were designed, synthesized, and applied to develop a single-component, multifunctional, and efficient catalytic system for the generation of cyclic carbonates from CO2 and epoxides. The system was suitable for the transformation of terminal and internal epoxides, providing a yield of up to 95%. A biomass-based ionic liquid ([5-HMFD–NMeEt2]I) exhibited excellent recyclability and stability, which was further proved by nuclear magnetic resonance (NMR) of the ionic liquid before and after use. Control experiments using catalysts with different functional groups indicated that the hydroxyl of the biomass-based ionic liquids had a hydrogen bonding effect and multifunctional groups such as hydroxyl and anions showed synergistic catalytic influences on the activation of the substrates. At the same time, the peak of the carbonyl in infrared (IR) spectra indicated that CO2 could be captured by the ionic liquid to promote the reaction.
Sustainability spotlight
Carbon dioxide (CO2) is not only one of the main greenhouse gases, but also a rich, inexpensive, and renewable C1 resource. And the conversion of CO2 into cyclic carbonates as high value-added chemicals is of great significance. Developing recyclable, highly efficient and environmentally friendly catalysts is an important aspect in sustainable chemistry. Several novel biomass-based ionic liquids derived from 5-HMF as a biomass platform molecule were designed and applied as recyclable, single-component and multifunctional catalysts for the cycloaddition of epoxides and CO2 to synthesize cyclic carbonates. Our technologies are in line with the United Nations Sustainable Development Goals, particularly Goals 9, 12, and 13, which focus on sustainable industrialization, sustainable consumption and production patterns, and combating climate change, respectively.
|
Introduction
Carbon dioxide (CO2), as one of the main greenhouse gases, has threatened the social environment of humans. Meanwhile, CO2 is a rich, inexpensive, and renewable C1 resource. So, the transformation of CO2 into high value-added chemicals has attracted much attention,1–3 such as dimethyl carbonate, urethanes, formic acid, methanol, carbonates, etc.4–8 And the cycloaddition of CO2 and epoxides to synthesize cyclic carbonates is one of the most feasible approaches, due to their extensive industrial application value as battery electrolytes, nonproton polar solvents, fine chemical intermediates, polymer and functional materials, etc.9 Tremendous efforts have been made to develop a series of catalytic systems for the transformation, such as onium salts,10 metal salts,11,12 organic catalysts,13,14 metal oxides,15 metal complexes,16,17 and organic framework materials.18,19
Recently, Andrea and Kerton completed the reaction with BPh3 as the catalyst and PPNCl (hexaphenyldiphosphazenium chloride) as the co-catalyst.20 A deep eutectic solvent (DES) comprising choline chloride and urea was utilized to achieve the transformation to provide spiro-cyclic carbonates in 67–98% yields under 1 atm CO2 at 70 °C.21 A synergistic catalytic system including an amino acid-based copper containing MOF and tetrabutylammonium bromide for the reaction of epoxides with CO2 without solvents was exploited.22 Liu developed chromium complexes containing hybridized ligand sites (O, N, and S) with TBAB as a new catalytic system for the coupling reaction.23 Seiji Shirakawa et al. achieved a cycloaddition reaction of epoxides with CO2 using triethylamine hydroiodide as a bifunctional catalyst at 35 °C under 1 atm CO2 for 24 h and the conversion would reduce to 62% from 97% after five runs.24 Although significant progress has been made, there are still some drawbacks, such as poor efficiency, difficulty in recycling, and a multicomponent catalytic system, which would limit the application in industry. Therefore, developing an efficient, recyclable, and single-component catalytic system remains challenging for the reaction.
An excellent approach to activate the substrate to achieve a catalytic system has been developed via a hydrogen bond donor (HBD).25–27 It has been found that hydrogen bond donor groups (e.g. hydroxyl or carboxyl groups) are associated with the ease of hydrogen bonding with oxygen atoms on the epoxide, activating the epoxide to facilitate the reaction.28 Rostami et al. also established a binary catalytic system for the preparation of cyclic carbonates from epoxides and CO2 with 2-picolinic acid as the HBD catalyst and n-Bu4NI as the co-catalyst.29 As we know, the halogen anion can be used as a nucleophilic reagent to attack the epoxide and activate the substrate.30 On the other hand, 5-hydroxymethylfurfural (5-HMF), as an important biomass-based platform molecule, has the advantages of wide source and easy availability.31,32 At present, it is generally transformed into a series of high-value chemicals and fuels.33,34 However, few 5-HMF derived catalysts were exploited to build a catalytic system for organic synthesis. Ionic liquids (ILs) exhibiting excellent properties such as low volatility, thermal stability, good solubility etc. have strongly attracted researchers' attention. Among them, the designability of ionic liquids is of greater concern as they can be designed according to needs.35–37 Therefore, we wanted to design a variety of biomass-based ionic liquids via retaining the hydroxyl group (–OH) of 5-HMF to realize HBD catalysis, and introducing quaternary ammonium salt with halide ions on the aldehyde group of 5-HMF for the synthesis of cyclic carbonates from epoxides and CO2. Fortunately, several biomass-based 5-hydroxymethylfurfural derived ionic liquids (5-HMFD ILs) containing hydroxyl have been successfully synthesized and applied as single-component multifunctional catalysts for the cycloaddition reaction between CO2 and epoxide (Scheme 1). Under relatively mild conditions, the system achieved an efficient, single-component, metal-free catalytic conversion, avoiding the use of cocatalysts, and achieving a 95% yield. The ionic liquid was easy to separate and recover and had high stability, and the yield had no significant drop after four runs. Control experiments demonstrated the hydrogen bonding and synergistic effect of multifunctional groups.
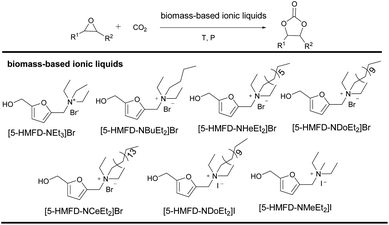 |
| Scheme 1 Developed biomass-based 5-hydroxymethylfurfural derived ionic liquids and their application for the cycloaddition between CO2 and epoxide. | |
Results and discussion
Investigation of the reaction conditions for the cycloaddition of CO2 and styrene oxide
We began our investigation for the cycloaddition of styrene oxide 1a with CO2 catalyzed by [5-HMFD–NMeEt2]I (Table 1). Delighted, 68% yield was afforded with 0.6 mol% [5-HMFD–NMeEt2]I as the catalyst under 1 MPa CO2 at 100 °C for 6 h (Table 1, entry 1). With the dosage increase of [5-HMFD–NMeEt2]I, the product yield also increased. When the catalyst dosage was 2 mol%, the yield of 2a reached 96% (Table 1, entry 3). There was no obvious change by adding up to 3 mol% catalyst, and the reaction was inert under catalyst-free conditions (Table 1, entries 4 and 5). Prolonging the reaction time led to no significant change in yield, and shortening the reaction time resulted in a decrease in yield (Table 1, entries 6–8). And the optimal reaction time was 6 h, reaching a yield of 96% (Table 1, entry 3).
Table 1 Investigation of the reaction conditions for the cycloaddition of CO2 and phenyl epoxide (1a) catalyzed by [5-HMFD–NMeEt2]Ia
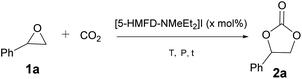
|
Entry |
Cat. (mol%) |
T (°C) |
P (MPa) |
t (h) |
Yieldb (%) |
Reaction conditions: 1a (10 mmol) and [5-HMFD–NMeEt2]I (x mol%) by adding CO2 were stirred at a certain temperature for several hours.
Isolated yield.
NR: no reaction.
|
1 |
0.6 |
100 |
1 |
6 |
68 |
2 |
1 |
100 |
1 |
6 |
73 |
3 |
2 |
100 |
1 |
6 |
96 |
4 |
3 |
100 |
1 |
6 |
95 |
5 |
— |
100 |
1 |
6 |
NRc |
6 |
2 |
100 |
1 |
2 |
86 |
7 |
2 |
100 |
1 |
4 |
91 |
8 |
2 |
100 |
1 |
8 |
95 |
9 |
2 |
100 |
0.1 |
6 |
37 |
10 |
2 |
100 |
0.5 |
6 |
95 |
11 |
2 |
100 |
2 |
6 |
97 |
12 |
2 |
r.t. |
0.5 |
6 |
<10 |
13 |
2 |
60 |
0.5 |
6 |
32 |
14 |
2 |
80 |
0.5 |
6 |
73 |
15 |
2 |
120 |
0.5 |
6 |
96 |
When the pressure of CO2 was screened, the product yield changed significantly from 0.1 to 0.5 MPa, increasing from 37% to 95% (Table 1, entries 9 and 10). As the CO2 pressure continued to increase, the yield of 2a changed slightly (Table 1, entry 11). So, the optimal reaction pressure was determined to be 0.5 MPa. Furthermore, the influence of the reaction temperature was investigated (Table 1, entries 10 and 12–15), and the yield of the desired product increased by increasing the temperature to 100 °C. Interestingly, there was nearly no influence on selectivity on changing the reaction conditions. Therefore, the optimal conditions for the cycloaddition reaction were the following: 2 mol% [5-HMFD–NMeEt2]I, 100 °C, 0.5 MPa, 6 h.
Investigation of the activities of different biomass-based ionic liquids for the cycloaddition reaction
The influence of different anions and alkyl chain lengths of the biomass-based ionic liquids on the cycloaddition reaction was further examined (Table 2). When the anion was Br−, the yield gradually improved by increasing the alkyl chain length (Table 2, entries 1–4). Only 27% yield could be afforded with no byproduct detected, and most of the styrene oxide was recovered. The reaction worked well to provide a 94% yield when the alkyl chain length was increased to 12 carbons (Table 2, entry 4). This phenomenon may be attributed to the fact that lengthening the chain will increase electron density and steric hindrance, and decrease the binding force on Br− to make it leave for easy nucleophilic attack.39 When the alkyl chain length was 16 carbons, there was nearly no obvious variation in yield (Table 2, entry 5). Upon replacing Br− by I−, only 81% yield of the desired product could be achieved (Table 2, entry 6). However, [5-HMFD–NMeEt2]I exhibited excellent activity, resulting in a 95% yield (Table 2, entry 7). Taking into account the complicated post-treatment process of ionic liquids with too long alkyl chains, [5-HMFD–NMeEt2]I was chosen as the best catalyst.
Table 2 Investigation of the activities of different biomass-based ionic liquids for the cycloaddition reactiona
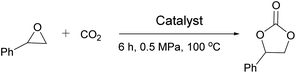
|
Entry |
Catalyst |
Yieldb (%) |
Reaction conditions: 1a (10 mmol) and biomass-based ionic liquid (2 mol%) by adding 0.5 MPa CO2 were stirred at 100 °C for 6 h.
Isolated yield.
|
1 |
[5-HMFD–NEt3]Br
|
27 |
2 |
[5-HMFD–NBuEt2]Br
|
75 |
3 |
[5-HMFD–NHeEt2]Br
|
92 |
4 |
[5-HMFD–NDoEt2]Br
|
94 |
5 |
[5-HMFD–NCeEt2]Br
|
93 |
6 |
[5-HMFD–NDoEt2]I
|
81 |
7 |
[5-HMFD–NMeEt2]I
|
95 |
Examination of the substrate scope
Subsequently, the substrate scope for the cycloaddition reaction was explored (Table 3). Apart from aromatic epoxides which gave good results, good yields could be achieved for aliphatic epoxides with simple structures and small molecular weights (Table 3, entries 1–3). And 1d or 1e as the substrate having an ether bond also performed well when the reaction time was up to 8 h, providing yields above 90% (Table 3, entries 4 and 5). However, cyclopentane epoxide and cyclohexane epoxide could not work well, just generating 20% and 18% yields, even on prolonging the reaction time and increasing the CO2 pressure (Table 3, entries 6 and 7). It was speculated that the steric hindrance of the substrates prevented the contact between the catalyst and the substrate and reduced the activity of the reaction. According to the literature, NMR data and IR spectra (see Fig. S14, S15, S17 and S18†),40–42 the products 2f and 2g should be cis isomers. Moreover, there were no byproducts generated in the reaction, and the selectivities were excellent with different substrates.
Table 3 Substrate scope for the cycloaddition reaction of CO2 with epoxidesa
Recyclability of [5-HMFD–NMeEt2]I
The recyclability of the catalyst ([5-HMFD–NMeEt2]I) was investigated with propylene oxide 1b as the substrate under optimal reaction conditions. When the reaction was over in every cycle, the catalyst needed to be washed several times with ethyl acetate, dried, and then reused. As shown in Fig. 1, there was no significant drop in yield and no change in the structure of the biomass-based ionic liquid after 4 cycles. It can be seen that the catalyst exhibits excellent recyclability and stability for the cycloaddition reaction.
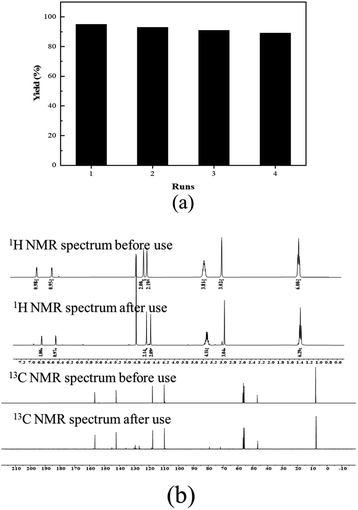 |
| Fig. 1 Recyclability of [5-HMFD–NMeEt2]I for the cycloaddition reaction of CO2 with propylene oxide: (a) The yields of four recycles and (b) NMR spectra of [5-HMFD–NMeEt2]I before and after use. | |
Reaction mechanism
To explore the effect of functional groups in [5-HMFD–NMeEt2]I, we synthesized several compounds in the absence of hydroxyl ([2-FD–NMeEt2]I), quaternization with anions (5-HMFD–NEt2), or hydroxyl and quaternization with anions (2-FD–NEt2) and their activities for the cycloaddition are shown in Scheme 2. When [2-FD–NMeEt2]I having no hydroxyl was used as the catalyst under optimal reaction conditions, the yield significantly decreased. The result demonstrated that our design with hydroxyl acting as an HBD catalyst would activate the epoxide via hydrogen bonding, and had a synergistic promoting effect on the reaction. Besides, there were nearly no reactions using 2-FD–NEt2 without hydroxyl and quaternization with anions or 5-HMFD–NEt2 having no quaternization with anions as the catalyst for the reaction, which further indicated that the hydroxyl group and halide ion significantly affected the reaction.
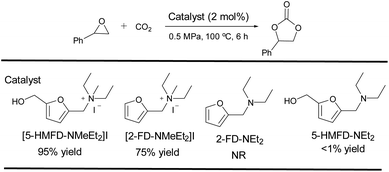 |
| Scheme 2 Control experiments to test the functional group influence on the catalytic activities of the catalysts. | |
Besides, IR spectra were used to test the interaction between CO2 and ionic liquids (Fig. 2). Interestingly, the peak of the carbonyl was obviously detected when the pressure of CO2 was up to 2.5 MPa (green line). The result indicated that an unstable adduct was formed during the reaction. And the hydrogen bonding effect was also investigated by IR and NMR. There was a shift of hydroxyl from 3333 cm−1 to 3317 cm−1 in the IR spectrum, when [5-HMFD–NMeEt2]I and styrene oxide were mixed (Fig. S16†). The results proved the hydrogen bonding effect between [5-HMFD–NMeEt2]I and epoxide. However, there was no obvious change in the NMR spectra.
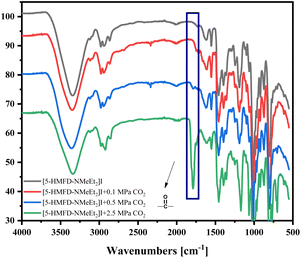 |
| Fig. 2 The peaks of the carbonyl in IR spectra of the adduct between ionic liquids [5-HMFD–NMeEt2]I and CO2 (just 0.2 mmol of [5-HMFD–NMeEt2]I with different pressures of CO2 was stirred at 100 °C for 6 h. At the end of the reaction, the IR test was immediately performed.). | |
According to our experiments and previous reports,28,38 a possible mechanism for the cycloaddition of CO2 and epoxides is proposed (Scheme 3). First, the epoxide will be activated by hydrogen bonding of hydroxyl or quaternary ammonium salt to form I or I′, which will be attacked by I− from the less steric hindrance side. The ring opening of the epoxide will occur due to a synergistic promoting effect of activation and nucleophilic attack. Therefore, the activity will become poor when internal epoxide with steric hindrance was used as the substrate, which was consistent with the results (Table 3, entries 6 and 7). The results in Fig. 2 demonstrated that ionic liquids had a trapping effect on CO2, which facilitated the activation of CO2. Then, the negatively charged oxygen atoms in II or II′ attack the carbon of CO2 to generate a carbonate III or III′, which undergoes internal cyclization to generate cyclic carbonates, remove iodine anions and regenerate the catalyst.
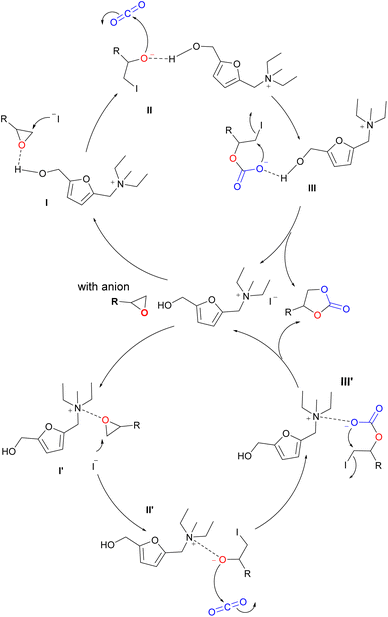 |
| Scheme 3 A possible mechanism of the [5-HMFD–NMeEt2]I catalyzed cycloaddition reaction. | |
Conclusions
In this paper, a series of new multifunctional biomass-based ionic liquids have been designed and synthesized from 5-HMF as an important biomass-based platform molecule, and an environmentally friendly and renewable raw material. Under a pressure of 0.5 MPa CO2 at 100 °C for 6 h, the cycloaddition of styrene oxide with CO2 was catalyzed by 2 mol% of [5-HMFD–NMeEt2]I, giving the cyclic carbonate in a 95% yield. [5-HMFD–NMeEt2]I was easy to synthesize, separate and recover, and exhibited excellent recyclability and stability. The activities of the catalysts having different functional groups demonstrated the hydrogen bonding and synergistic effect. A mechanism involving the activation of epoxides via hydrogen bonding of hydroxyl or quaternary ammonium salt, and nucleophilic attack with I− to realize ring opening has been reasonably speculated. The application of the developed biomass-based ionic liquids for CO2 fixation is expected to have broad prospects.
Experimental section
Materials
CO2 was supplied by Tai'an Yingchun Gas Co., Ltd with a purity of 99.99%. 5-hydroxymethylfurfural, diethylamine, iododecane, bromoethane, bromobutane, bromooctane, bromododecane, hexadecane bromide, and various epoxides were purchased from Shanghai McLean Biochemical Technology Co., Ltd. and Yongda Chemical Reagent Co., Ltd. The other chemicals were obtained from Kaitong Reagent Company. And all chemicals were used as received.
Experimental instruments
Analytical thin layer chromatography (TLC) plates were bought from Qingdao Hailang. Column chromatography was performed using 200–300 mesh silica gels from Qingdao Hailang, and the eluent was a mixture of ethyl acetate and petroleum ether. Unless noted, all reactions were carried out in reactors purchased from Tianjin Boost Tech. Co., Ltd. 1H NMR and 13C NMR were recorded on a Bruker AVANCE III 400 MHz spectrometer in CDCl3 or D2O. TMS or D2O residual signals were used as the internal standard. Chemical shift values (δ) were reported in ppm and coupling constants (J values) were reported in hertz (Hz). IR spectra were measured on an FT-IR spectrometer Nexus 870. High resolution mass spectra (HRMS) were obtained on a Bruker micrOTOF-QII mass spectrometer with an ESI source.
General procedure to synthesize biomass-based ionic liquids39,43,44
Taking the preparation of [5-HMFD–NMeEt2]I as an example, the detailed procedures for other ILs are shown in the ESI.† To 5-hydroxymethylfurfural (0.63 g, 0.005 mol) dissolved in 30 mL methanol was added diethyl amine (0.38 g, 0.0052 mmol) and then stirred for 30 min at room temperature. Subsequently, sodium borohydride (NaBH4, 0.006 mmol) was added to the above mixture in an ice water bath and reacted at room temperature for 5 h. At the end of the reaction, a rotary evaporator was used to remove the solvent. The reaction was quenched with saturated sodium chloride aqueous solution, extracted with water/ethyl acetate (3 × 20 mL), and dried with anhydrous sodium sulfate for 6 h. The corresponding tertiary amine (intermediate) was obtained by using a silica gel column (petroleum ether/ethyl acetate = 5
:
1). Next, to 5 mmol tertiary amine dissolved in 20 mL EtOAc was added 5.5 mmol iodomethane (CH3I), and reacted at room temperature for 12 h. After the reaction, EtOAc was used to wash the crude product many times to get [5-HMFD–NMeEt2]I as a bright yellow compound (Scheme 4).
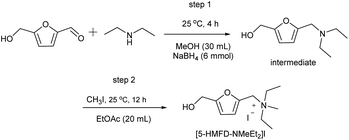 |
| Scheme 4 Synthetic procedures of [5-HMFD–NMeEt2]I. | |
(5-((Diethylamino)methyl)furan-2-yl)methanol.
Light yellow oily liquid, 54% yield, 1H NMR (400 MHz, CDCl3) δ 6.20 (d, J = 2.8 Hz, 1H), 6.12 (d, J = 3.2 Hz, 1H), 4.56 (s, 2H), 3.62 (s, 2H), 2.53 (q, J = 7.1 Hz, 4H), 1.06 (t, J = 6.2 Hz, 6H); 13C NMR (101 MHz, CDCl3) δ 153.8, 152.2, 109.3, 108.0, 57.3, 49.0, 46.7, 11.6.
[5-HMFD–NEt3]Br
.
White solid, 90% yield; 1H NMR (400 MHz, D2O) δ 6.65 (d, J = 3.2 Hz, 1H), 6.37 (d, J = 3.1 Hz, 1H), 4.47 (s, 2H), 4.35 (s, 2H), 3.15 (q, J = 6.7 Hz, 6H), 1.24 (t, J = 6.8 Hz, 9H). 13C NMR (101 MHz, D2O) δ 156.3, 142.1, 117.1, 109.5, 55.6, 52.6, 52.5, 6.8. HRMS m/z: [M + H]+ calcd for C12H22NO2+: 212.1645, found: 212.1643.
[5-HMFD–NBuEt2]Br
.
Yellow oil, 76% yield; 1H NMR (400 MHz, D2O) δ 6.68 (d, J = 3.8 Hz, 1H), 6.39 (d, J = 3.2 Hz, 1H), 4.48 (s, 2H), 4.38 (s, 2H), 3.18 (q, J = 7.4 Hz, 4H), 3.07–2.99 (m, 2H), 1.67 (p, J = 7.7 Hz, 2H), 1.26 (t, J = 6.8 Hz, 6H), 0.98 (t, J = 7.3 Hz, 2H), 0.87 (t, J = 7.3 Hz, 3H); 13C NMR (101 MHz, D2O) δ 156.4, 142.1, 117.2, 109.6, 57.3, 55.7, 53.2, 46.4, 23.2, 19.2, 13.0, 7.1. HRMS m/z: [M + H]+ calcd for C14H26NO2+: 240.1958, found: 240.1965.
[5-HMFD–NHeEt2]Br
.
Yellow oil, 70% yield; 1H NMR (400 MHz, D2O) δ 6.65 (d, J = 3.3 Hz, 1H), 6.34 (d, J = 3.3 Hz, 1H), 4.43 (d, J = 4.7 Hz, 2H), 4.37 (s, 2H), 3.16 (q, J = 7.2 Hz, 4H), 3.00–2.90 (m, 2H), 1.66 (dq, J = 18.8, 6.7 Hz, 2H), 1.20 (dt, J = 18.5, 5.5 Hz, 16H), 0.76 (t, J = 6.4 Hz, 3H). 13C NMR (101 MHz, D2O) δ 156.8, 142.0, 117.3, 109.0, 57.6, 55.9, 53.3, 47.4, 31.5, 28.7, 26.0, 22.5, 21.5, 13.9, 7.3. HRMS m/z: [M + H]+ calcd for C18H34NO2+: 296.2584, found: 296.2591.
[5-HMFD–NDoEt2]Br
.
White solid, 67% yield; 1H NMR (400 MHz, D2O) δ 6.65 (d, J = 3.3 Hz, 1H), 6.32 (d, J = 3.2 Hz, 1H), 4.70 (s, 2H), 4.40 (s, 2H), 3.18 (q, J = 10.3, 9.2 Hz, 4H), 2.94 (d, J = 15.8 Hz, 2H), 1.67 (dh, J = 16.1, 8.3, 7.6 Hz, 2H), 1.29–1.14 (m, 24H), 0.78 (t, J = 6.3 Hz, 3H); 13C NMR (101 MHz, D2O) δ 156.8, 142.0, 117.3, 109.0, 57.6, 55.9, 53.3, 47.4, 31.5, 28.8, 28.7, 26.0, 22.5, 21.5, 13.9, 7.3. HRMS m/z: [M + H]+ calcd for C22H42NO2+: 352.3210, found: 352.3220.
[5-HMFD–NCeEt2]Br
.
White solid, 61% yield; 1H NMR (400 MHz, D2O) δ 6.72 (d, J = 3.2 Hz, 1H), 6.36 (d, J = 3.1 Hz, 1H), 4.77 (s, 2H), 4.44 (s, 2H), 3.23 (q, J = 8.8, 7.8 Hz, 4H), 3.03 (t, J = 12.1 Hz, 2H), 1.79–1.65 (m, 2H), 1.36–1.14 (m, 32H), 0.84 (t, J = 6.5 Hz, 3H). 13C NMR (101 MHz, D2O) δ 155.1, 139.9, 115.4, 107.3, 77.0, 55.7, 53.9, 51.5, 30.1, 28.0, 28.0, 27.9, 27.8, 27.6, 27.2, 24.4, 20.8, 19.9, 12.0, 5.4. HRMS m/z: [M + H]+ calcd for C26H50NO2+: 408.3836, found: 408.3837.
[5-HMFD–NDoEt2]I
.
White solid, 71% yield; 1H NMR (400 MHz, D2O) δ 6.65 (d, J = 3.3 Hz, 1H), 6.32 (d, J = 3.2 Hz, 1H), 4.40 (s, 4H), 3.18 (q, J = 7.2 Hz, 4H), 2.96 (t, J = 8.1 Hz, 2H), 1.65 (d, J = 9.5 Hz, 2H), 1.26–1.16 (m, 24H), 0.78 (t, J = 6.4 Hz, 3H). 13C NMR (101 MHz, D2O) δ 156.7, 141.9, 117.3, 108.9, 57.6, 55.8, 53.3, 47.4, 31.4, 28.8, 28.6, 25.9, 22.4, 21.5, 13.9, 7.2. HRMS m/z: [M + H]+ calcd for C22H42NO2+: 352.3210, found: 352.3220.
[5-HMFD–NMeEt2]I
.
Bright yellow oily liquid, 90% yield; 1H NMR (400 MHz, D2O) δ 6.76 (d, J = 5.4 Hz, 1H), 6.44 (d, J = 5.3 Hz, 1H), 4.54 (s, 2H), 4.47 (s, 2H), 3.29 (q, J = 7.2 Hz, 4H), 2.92 (s, 3H), 1.33 (t, J = 7.1 Hz, 6H). 13C NMR (101 MHz, D2O) δ 156.5, 142.1, 117.7, 109.8, 56.7, 56.4, 55.9, 47.0, 7.7. HRMS m/z: [M + H]+ calcd for C11H20NO2+: 198.1489, found: 198.1479.
Typical procedure for the synthesis of cyclic carbonates
In the experiment, a certain amount of ionic liquid and 10 mmol epoxide were successively added into the lining of a 25 mL high-pressure reactor. Then, a certain pressure of CO2 was introduced into the reactor. The high-pressure reactor was placed in a heating module and stirred at the required temperature for a certain time. When the reaction was over, excess gas was slowly released from the reactor cooled with an ice bath. Finally, the product was obtained by using a silica gel column (petroleum ether/ethyl acetate = 15
:
1).
Recycling and reuse of the catalyst
To a high-pressure reactor, 1a (1.2015 g, 10 mmol), [5-HMFD–NMeEt2]I (0.0648 mg, 0.2 mmol), and 0.5 MPa CO2 were added. After the reaction mixture was stirred at 100 °C for 6 h, it was cooled to room temperature and detected by TLC. Then, [5-HMFD–NMeEt2]I retained in the glass insert was extracted and washed with petroleum ether three times, and dried. Subsequently, [5-HMFD–NMeEt2]I was reused directly by adding 1a (1.2015 mg, 10 mmol) and 0.5 MPa CO2 to the high-pressure reactor. Even after the above steps were repeated four times, the yield did not significantly decrease.
Author contributions
Feng Han: conceptualization, methodology, supervision, validation, writing-reviewing and editing, project administration, funding acquisition. Chengxia Miao: conceptualization, methodology, supervision, validation, writing-reviewing and editing, project administration, funding acquisition. Kaixin Guo: investigation, visualization, data curation, writing-original draft preparation. Na Ji: investigation, visualization, data curation, writing-original draft preparation. Qingfeng Yang: supervision, investigation, funding acquisition. Ning Wang: investigation, visualization. The manuscript was written through the contributions of all authors. All authors have given approval to the final version of the manuscript.
Conflicts of interest
The authors declare no competing financial interest.
Acknowledgements
This work was financially supported by the National Natural Science Foundation of China (21972079, 22272094 and 21961027), Fluorosilicone Materials Joint Funds of Shandong Provincial Natural Science Foundation (ZR2019LFG009), Natural Science Foundation of Shandong Province (ZR2019MB002), and Incubation Program of Youth Innovation in Shandong Province.
References
- L.-Q. Qiu, H.-R. Li and L.-N. He, Acc. Chem. Res., 2023, 56, 2225–2240 CrossRef CAS PubMed.
- K. Zhang, D. Guo, X. Wang, Y. Qin, L. Hu, Y. Zhang, R. Zou and S. Gao, J. CO2 Util., 2023, 72, 102493 CrossRef CAS.
- Y. Chen and T. Mu, Green Chem., 2019, 21, 2544–2574 RSC.
- X. X. Yu, Z. Z. Yang, B. Qiu, S. E. Guo, P. Yang, B. Yu, H. Y. Zhang, Y. F. Zhao, X. Z. Yang, B. X. Han and Z. M. Liu, Angew. Chem., Int. Ed., 2019, 58, 632–636 CrossRef CAS PubMed.
- W. Schilling and S. Das, ChemSusChem, 2020, 13, 6246–6258 CrossRef CAS.
- S. Bertini, M. Rahaman, A. Dutta, P. Schollhammer, A. V. Rudnev, F. Gloaguen, P. Broekmann and M. Albrecht, Green Chem., 2021, 23, 3365–3373 RSC.
- S. I. Rybchenko, D. Touhami, J. D. Wadhawan and S. K. Haywood, ChemSusChem, 2016, 9, 1660–1669 CrossRef CAS PubMed.
- C. Claver, M. B. Yeamin, M. Reguero and A. M. Masdeu-Bultó, Green Chem., 2020, 22, 7665–7706 RSC.
- W. Guo, J. E. Gómez, À. Cristòfol, J. Xie and A. W. Kleij, Angew. Chem., Int. Ed., 2018, 57, 13735–13747 CrossRef CAS PubMed.
- G. Li, S. Dong, P. Fu, Q. Yue, Y. Zhou and J. Wang, Green Chem., 2022, 24, 3433–3460 RSC.
- L. Shi, S. Xu, Q. Zhang, T. Liu, B. Wei, Y. Zhao, L. Meng and J. Li, Ind. Eng. Chem. Res., 2018, 57, 15319–15328 CAS.
- Y. Nie, X. Gong, H. Gao, X. Zhang and S. Zhang, Sci. China: Chem., 2014, 57, 1766–1773 CrossRef CAS.
- T. Werner and N. Tenhumberg, J. CO2 Util., 2014, 7, 39–45 CrossRef CAS.
- L. Guo, K. J. Lamb and M. North, Green Chem., 2021, 23, 77–118 RSC.
- V. K. Tomazett, G. Chacon, G. Marin, M. V. Castegnaro, R. P. das Chagas, L. M. Lião, J. Dupont and M. I. Qadir, J. CO2 Util., 2023, 69, 102100 Search PubMed.
- K. Kiatkittipong, M. A. A. M. Shukri, W. Kiatkittipong, J. W. Lim, P. L. Show, M. K. Lam and S. Assabumrungrat, Processes, 2020, 8, 548 CrossRef CAS.
- V. Paradiso, V. Capaccio, D. H. Lamparelli and C. Capacchione, Catalysts, 2020, 10, 825 CrossRef CAS.
- Y.-R. Du, X. Yang, Y.-F. Wang, P.-X. Guan, R. Wang and B.-H. Xu, Mol. Catal., 2022, 520, 112164 CrossRef CAS.
- K. A. Cychosz, A. G. Wong-Foy and A. J. Matzger, J. Am. Chem. Soc., 2009, 131, 14538–14543 CrossRef CAS PubMed.
- K. A. Andrea and F. M. Kerton, ACS Catal., 2019, 9, 1799–1809 CrossRef CAS.
- R. K. Tak, P. Patel, S. Subramanian, R. I. Kureshy and N. H. Khan, ACS Sustainable Chem. Eng., 2018, 6, 11200–11205 CrossRef CAS.
- G. S. Jeong, A. C. Kathalikkattil, R. Babu, Y. G. Chung and D. W. Park, Chin. J. Catal., 2018, 39, 63–70 CrossRef CAS.
- J. Xie, F. Chen, M. Li and N. Liu, J. CO2 Util., 2022, 62, 102100 CrossRef CAS.
- Y. Kumatabara, M. Okada and S. Shirakawa, ACS Sustainable Chem. Eng., 2017, 5, 7295–7301 CrossRef CAS.
- I. Alabugin, J. Am. Chem. Soc., 2010, 132, 6863–6864 CrossRef CAS.
- S. Mukherjee, J. W. Yang, S. Hoffmann and B. List, Chem. Rev., 2007, 107, 5471–5569 CrossRef CAS PubMed.
- J. Alemán, A. Parra, H. Jiang and K. A. Jørgensen, Chem.–Eur. J., 2011, 17, 6890–6899 CrossRef PubMed.
- Y. Liu, Y. Song, J. Zhou and X. Zhang, Mol. Catal., 2020, 492, 111008 CrossRef CAS.
- A. Rostami, A. Ebrahimi, M. Al-Jassasi, S. Mirzaei and A. Al-Harrasi, Green Chem., 2022, 24, 9069–9083 RSC.
- J. Peng and Y. Deng, New J. Chem., 2001, 25, 639–641 RSC.
- Z. Miao, Y. Zhang, X. Pan, T. Wu, B. Zhang, J. Li, T. Yi, Z. Zhang and X. Yang, Catal. Sci. Technol., 2015, 5, 1314–1322 RSC.
- D. A. Kotadia and S. S. Soni, Catal. Sci. Technol., 2013, 3, 469–474 RSC.
- J.-M. Ha, K.-R. Hwang, Y.-M. Kim, J. Jae, K. H. Kim, H. W. Lee, J.-Y. Kim and Y.-K. Park, Renewable Sustainable Energy Rev., 2019, 111, 422–441 CrossRef CAS.
- X. Liu, M. Zhang and Z. Li, ACS Sustainable Chem. Eng., 2020, 8, 4801–4808 CrossRef CAS.
- H. Maciejewski, Catalysts, 2021, 11, 367 CrossRef CAS.
- J. J. Raj, C. D. Wilfred, S. N. Shah, M. Pranesh, M. I. Abdul Mutalib and K. C. Lethesh, J. Mol. Liq., 2017, 225, 281–289 CrossRef CAS.
- S.-D. Lee, B.-M. Kim, D.-W. Kim, M.-I. Kim, K. R. Roshan, M.-K. Kim, Y.-S. Won and D.-W. Park, Appl. Catal., A, 2014, 486, 69–76 CrossRef CAS.
- J. Weng, C. Wang, H. Li and Y. Wang, Green Chem., 2006, 8, 96–99 RSC.
- C. Li, F. Liu, T. Zhao, J. Gu, P. Chen and T. Chen, Mol. Catal., 2021, 511, 111756 CrossRef CAS.
- C.-X. Miao, J.-Q. Wang, Y. Wu, Y. Du and L.-N. He, ChemSusChem, 2008, 1, 236–241 CrossRef CAS PubMed.
- D. J. Darensbourg, S. J. Lewis, J. L. Rodgers and J. C. Yarbrough, Inorg. Chem., 2003, 42, 581–589 CrossRef CAS PubMed.
- A. Buchard, M. R. Kember, K. G. Sandeman and C. K. Williams, Chem. Commun., 2011, 47, 212–214 RSC.
- A. Cukalovic and C. V. Stevens, Green Chem., 2010, 12, 1201–1206 RSC.
- M. M. Seitkalieva, A. V. Vavina, A. V. Posvyatenko, K. S. Egorova, A. S. Kashin, E. G. Gordeev, E. N. Strukova, L. V. Romashov and V. P. Ananikov, ACS Sustainable Chem. Eng., 2021, 9, 3552–3570 CrossRef CAS.
Footnotes |
† Electronic supplementary information (ESI) available: Procedures for synthesizing biomass-based ionic liquids, NMR data and spectra of biomass-based ionic liquids and products, and IR spectra to test the hydrogen bonding effect and confirm the configurations of 2f and 2g. See DOI: https://doi.org/10.1039/d4su00033a |
‡ These authors contributed equally. |
|
This journal is © The Royal Society of Chemistry 2024 |
Click here to see how this site uses Cookies. View our privacy policy here.