High-purity monomer recovery from commercial engineering plastics by vacuum pyrolysis depolymerization†
Received
1st October 2024
, Accepted 16th October 2024
First published on 17th October 2024
Abstract
Plastic waste pollution is one of the most pressing global issues. Addressing this challenge requires energy transformation through chemical recycling of waste plastics. However, recycling rates remain low. A primary reason for this is that chemical recycling has yet to establish a closed-loop system, largely due to the inability to recover monomers with sufficient purity for reproducing the original products. This study demonstrates that vacuum pyrolysis can recover monomers with purities high enough to produce their materials comparable to those made from pure monomers. Conducted at 1 mmHg and 420 °C, the pyrolysis recovered methyl methacrylate (MMA) with 95% purity and 87% yield. The recovered MMA was used to produce poly(methyl methacrylate) (PMMA) via radical polymerization, resulting in the PMMA with molecular weight characteristics almost identical to those of PMMA produced from pure MMA, with only a slight increase in low-molecular-weight oligomers. The vacuum pyrolysis also successfully recovered high-purity monomers from commercial products such as cross-linked polystyrene (PS), acrylonitrile/styrene (AS) resin and acrylonitrile/butadiene/styrene (ABS) resin. This simple and convenient method, which requires no additional purification or temperature control due to heating with a spirit lamp flame, has the potential to establish a chemical and economic closed-loop recycling system, offering a promising solution to reducing plastic waste pollution.
Sustainability spotlight
To address the increasing emissions from waste plastics, it is critical to establish a closed-loop chemical recycling system involving energy transfer from waste and end-of-life plastics. This study demonstrates that high-purity monomers recovered from commercial engineering plastics using vacuum pyrolysis can serve as alternatives to virgin monomers for reproducing the original polymers, which promises to support the closed-loop system. The simple method—requiring neither further purification of the monomers nor thermal control—enables local recycling initiatives, which create an economic closed-loop system when integrated with company manufacturing processes. This study aligns with the United Nations' Sustainable Development Goals (SDGs), particularly SDG 12 (responsible consumption and production), SDG 7 (affordable and clean energy) and SDG 14 (life below water).
|
Introduction
Plastic pollution has had a serious impact on the global environment. To date, more than 9200 million metric tons (Mt) of plastics have been produced,1 with a global production rate of 460 Mt per year (as of 2019).2–5 Meanwhile, 6900 Mt of plastic waste has been discarded, with a global generation rate of 353 Mt per year. Approximately 40% of this plastic waste has leaked into rivers, lakes, seas and oceans,6 causing significant damage to aquatic ecosystems. Ironically, the lightness of plastic—its most notable and practical property—is a key factor contributing to such severe pollution in aquatic environments.
PMMA is one of the most important engineering plastics (EP) due to its versatile applications, including optical materials, high-voltage materials, outdoor insulators and artificial organs for medical use, owing to its specific features such as high transparency, resistivity, durability and biocompatibility.7–9 The global market size is valued at USD 5.9 billion in 2023, which is a small share of the overall global EP market (USD 133.6 billion in 2023). Nevertheless, PMMA has significantly supported the foundation of modern nanotechnology and innovations.7 The production of MMA, the monomer of PMMA, reached 3.9 million metric tons in 2019 and is estimated to increase to 5.7 million tons by 2028.10 MMA is more expensive compared to other EP materials such as ethylene and styrene;11,12 therefore, recycling PMMA is crucial for enhancing the global economy. However, only 10% of PMMA production is currently recycled, and most of its waste is treated by incineration or landfill due to the low quality of recovered MMA and the high cost of recycling.10,13
Mechanical recycling of PMMA is a convenient and energy-saving method, as it involves merely cleaning and melting without chemical operations or the generation of impurities, offering the potential for a closed-loop system. However, this process reduces the mechanical properties of the recycled PMMA, such as its elastic modulus and hardness, which diminishes its product value.14 Chemical recycling, including upcycling, has developed various pyrolytic and synthetic methods to utilize waste PMMA as energy and material sources. Upcycling is typically based on esterification, which imparts PMMA with functions such as bacterial adhesion, CO2 sorption, proton reduction and desalination.15 The recently reported transesterification-inverse vulcanization of PMMA into durable composites is particularly attractive, as it involves the utilization of sulfur, a by-product from fossil fuel refining, to form mechanically strong structures with thermally recyclable S–S bond networks.16 However, transforming PMMA into such new materials creates an open-loop recycling system and potentially generates new waste from these plastics.
Chemical recycling via pyrolysis is expected to create a closed-loop recycling system by recovering MMA from waste PMMA, followed by reproducing PMMA from the recovered MMA, provided the monomer can be recovered in a quantity and purity sufficient to compare with the original material. PMMA depolymerizes more readily than other plastics manufactured through radical polymerization, due to its relatively low ceiling temperature (Tc = 220 °C) resulting from its α-disubstituted structure.17 Nevertheless, the recycling rate remains low because slight impurities are by-products of the depolymerization process. These impurities significantly reduce the optical transparency and Vickers hardness of PMMA reproduced from recovered MMA, leading to a loss of product value and safety.18 Significant efforts have been made to enhance monomer recovery yield and purity by improving systems and reactors.10,19,20 Research on the depolymerization of PMMA synthesized via reversible-deactivation radical polymerization (RDRP) methods, such as atom transfer radical polymerization (ATRP)21,22 and reversible addition-fragmentation chain transfer (RAFT),23–25 has significantly reduced the depolymerization temperature to below 200 °C due to synergistic effects with photo-depolymerization. However, these methods are not practical for commercial PMMA due to the need for highly dilute conditions and the limited applicability of RDRP-synthesized PMMA depolymerization to commercial PMMA. Incorporating a low molar concentration of phthalimide as a pendant group into PMMA achieved over 95% MMA recovery.26 Pyrolytic depolymerization of PMMA has reached a 98% yield and over 97% purity of MMA recovery by improving reactors, such as fluidized bed reactors and laboratory fixed bed reactors.27,28 However, slight impurities generated during the pyrolysis acted as chain transfer agents during the reproduction of PMMA by radical polymerization, significantly reducing the molecular weight of the reproduced PMMA. Recently, chemically regenerated MMA with very high purity (>99%) has become commercially available, and it has been demonstrated that PMMA reproduced from this MMA compares favorably in terms of thermal, chemical and optical properties with PMMA produced from virgin MMA, although the regeneration process remains undisclosed.29
Vacuum pyrolysis has been reported as an effective method for recovering high-purity styrene monomer from waste expanded polystyrene.30 This success is attributed to slight gaseous impurities escaping from the recovered monomer under high vacuum conditions. As a result, there is no need for further purification of the recovered monomer or for strict temperature control during the pyrolysis, which can be conducted using a simple spirit lamp flame, thereby enabling a closed-loop recycling process. To promote convenient recycling of plastic waste, this study demonstrates that high-purity MMA recovered through the vacuum pyrolysis of PMMA sheet can serve as a viable alternative to virgin MMA in manufacturing processes. This paper describes the chemical recycling of PMMA via vacuum pyrolysis depolymerization into monomer form for PMMA regeneration and its potential application to other EP.
Experimental
Materials
PMMA sheet (Kuraray Co., Ltd, 297 mm length × 21 mm width × 1 mm depth), polystyrene (PS) beads (100–200 mesh) cross-linked with 1% divinylbenzene (Tokyo Chemical Industry Co., Ltd), a dripper of acrylonitrile–styrene (AS) resin (Sanyo Sangyo Co., Ltd) and a round rod of acrylonitrile–butadiene–styrene (ABS) resin (Hikari Mogol Co., Ltd, 1000 mm length × 5 mm diameter) were subjected to the vacuum pyrolysis (ESI, Fig. S1–S3†). The unit molar ratio of the AB resin was determined by 1H NMR (Fig. S3†), while the molar ratio of the ABS resin was calculated using elemental analysis (H: 8.35%, C: 83.65%, N: 4.75%, Ash: 2.90%). MMA was purchased from Fujifilm Wako Pure Chemical Corporation. It was purified by washing with a 5% NaOH aqueous solution and water, drying with anhydrous MgSO4, and then distilling over calcium hydride under reduced pressure to obtain pure MMA. 2,2′-Azobis(isobutyronitrile) (AIBN) was purchased from Fujifilm Wako Pure Chemical Corporation and recrystallized from methanol. A mixed alcohol fuel (76.6% methanol, 21.4% ethanol and 0.3% isopropanol) for the spirit lamp was purchased from Kenei Pharmaceutical Inc. Ethylbenzene, used as a standard for gas chromatography analysis of MMA, was purchased from Fujifilm Wako Pure Chemical Corporation, and ethylene glycol diethyl ether, used as a standard for the analysis of styrene and its mixtures, was purchased from Tokyo Chemical Industry. These chemicals were used as received. Molecular sieves, MS-4A, cylindrical with dimensions of 1.6 mm in diameter and 2–6 mm in length, were purchased from Fujifilm Wako Pure Chemical Corporation.
Characterizations
Gas chromatography (GC) was performed using a Shimadzu GC-8A gas chromatograph equipped with a thermal conductivity detector and a C-R6A Chromatopac recorder. GC was conducted with helium as the carrier gas, using a Shimadzu OV-3 column (3 meters). The injection temperature was set at 80 °C, and the column and final temperatures were both maintained at 50 °C. 1H NMR measurements were conducted using Jeol ECS400 and ECS500 FT NMR spectrometers. The molecular weight (Mn) and polydispersity index (PDI = Mw/Mn) of the PMMA were calculated by gel permeation chromatography (GPC) based on PMMA standards. GPC was performed using a Tosoh GPC-8020 instrument equipped with a DP-8020 dual pump, a CO-8020 column oven and an RI-8020 refractometer. Three PS gel columns, Tosoh TSKGEL G2000HXL, G4000HXL and G6000HXL, were used with tetrahydrofuran as the eluent at 40 °C. The pyrolysis was carried out under suction using a Sato Vac TST-20 oil rotary vacuum pump. The temperature inside an empty Pyrex tube was measured as previously reported.30
Vacuum pyrolysis of PMMA sheet, general procedure
The vacuum pyrolysis was performed in a Pyrex tube connected to a liquid nitrogen-cooled trap, using a spirit lamp for heating (Fig. S4†). Small pieces of PMMA sheet (3.004 g) were placed in a 100 mL Pyrex test tube and heated for 7 min under vacuum using a vacuum pump and a spirit lamp flame. A liquid product (2.606 g) was collected in the trap. The product, purged with nitrogen, was allowed to return to room temperature before being analyzed by GC to determine its purity. The residue (0.163 g) that remained in the tube was subjected to GPC analysis. Similarly, PS beads, an AS resin dripper and an ABS rod were also subjected to the pyrolysis (ESI,† Experimental).
Radical polymerization
The recovered MMA with 95% purity (1.003 g) and AIBN (15.9 mg) were placed in an ampoule. The contents were degassed using a freeze–pump–thaw cycle three times and then purged with nitrogen. Bulk polymerization was carried out at 60 °C for 3 h. The product was dissolved in dichloromethane (15 mL), and a portion (0.5 mL) of the solution was withdrawn to determine monomer conversion by 1H NMR. The remaining solution was poured into hexane (500 mL) to precipitate PMMA. The precipitate was collected by filtration and dried to obtain a white powder (0.891 g). Following the same procedure, PMMA (0.868 g) was obtained from pure MMA (1.005 g) and AIBN (16.7 mg).
Results and discussion
Vacuum pyrolysis of PMMA sheet
A PMMA sheet with 97% purity, Mn = 69
700 and Mw/Mn = 2.10, as determined by GPC based on PMMA standards, was subjected to the vacuum pyrolysis. The process was conducted in a Pyrex tube under 1 mmHg at 420 °C using a spirit lamp flame. The PMMA depolymerized over a 7 minutes period, yielding 87% of a liquid product. This product was identified as MMA monomer with 95% purity, as determined by GC and 1H NMR (Fig. 1). Variations in the yields of MMA, residue and their total over time during the pyrolysis are shown in Fig. 2. The MMA yield reached over 80% within 5 min, after which it gradually reached a steady state. As the MMA yield increased, the residue decreased and also reached a steady state. The total yield of MMA and residue slightly decreased over time, suggesting that gaseous products escaped from the system, likely due to the inability to capture them under such high vacuum conditions. This escape of gaseous products contributed to the high purity of the recovered monomer.
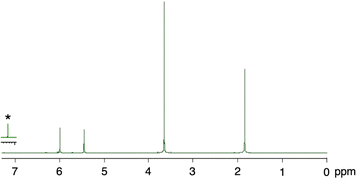 |
| Fig. 1
1H NMR spectrum of MMA recovered from PMMA sheet by the pyrolysis. Solvent: CDCl3. *CHCl3. | |
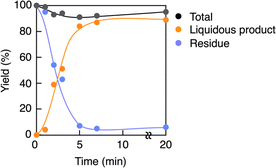 |
| Fig. 2 Variations in yields of MMA, residue and their total over time during the pyrolysis. | |
GPC analysis of the residue elucidated the depolymerization mechanism. Fig. 3 shows the variations in molecular weight and PDI of the residue during the pyrolysis. The molecular weight gradually decreased until reaching a steady state, while the PDI initially increased and then decreased during the process. This irregular change in PDI suggests that the depolymerization is initiated by random scission of the main chain, rather than stepwise degradation from the polymer chain ends. As seen in Fig. 4, the molecular weight decay correlates with the MMA yield, forming a line that connects the initial molecular weight of the PMMA to zero, corresponding to a 100% monomer yield. This linear decay indicates that once the main chain cleaves, the depolymerization proceeds only at the disubstituted α-carbon chain ends. The methylene radical at the β-carbon tends to couple with another methylene radical, forming a head-to-head structure in the main chain, rather than depolymerizing due to the instability of this radical. This head-to-head formation hinders quantitative monomer recovery, as it requires more energy to cleave (Fig. 5). Conversely, the radical at the α-carbon chain end undergoes disproportionation, rather than coupling, at higher temperatures due to steric hindrance. This is supported by evidence from radical polymerization, where the disproportionation increases with temperature.31 The disproportionation produces an olefin terminal and a hydrogen-adduct terminal through hydrogen radical transfer from the terminal methyl group to another chain end radical. The hydrogen-adduct terminal also impedes the depolymerization due to the instability of the resulting hydrogen radical. As shown in Fig. 6, the GPC curves for the PMMA shifted towards lower molecular weights as degradation progressed. This progression is reflected in a decrease in the area percentage of high-molecular-weight polymers (Fig. 7). In contrast, the oligomers with low molecular weights (Mn < 1400), particularly those with Mn ≈ 350, significantly increased during the late stage of pyrolysis. This very low molecular weight product likely contains the head-to-head structures, hydrogen-adducts and a five- or six-membered ring formed by backbiting.30 However, these structures had only a minor effect on the MMA yield, as the final residue amounted to just 5–6%.
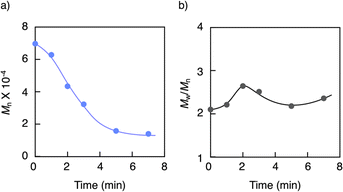 |
| Fig. 3 Variations in (a) molecular weight and (b) PDI of the residue during the pyrolysis. | |
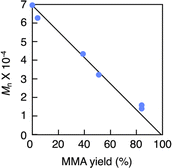 |
| Fig. 4 Plots of the residue molecular weight versus MMA yield. | |
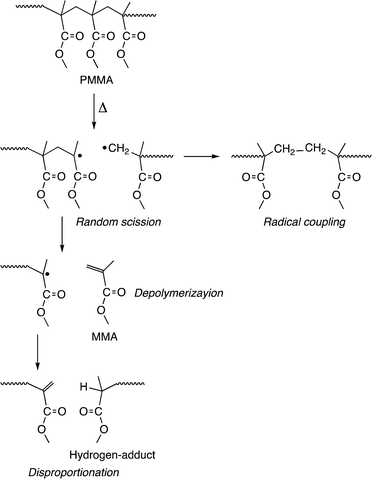 |
| Fig. 5 Mechanisms of depolymerization and side reactions during the pyrolysis. | |
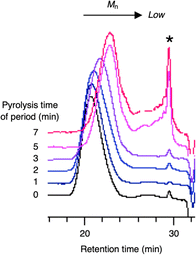 |
| Fig. 6 GPC profiles of the original PMMA and residue for each time. *Indicates the Mn ≈ 350 sample. | |
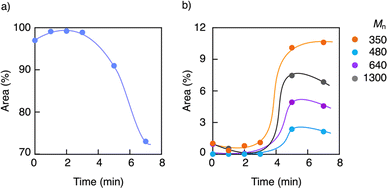 |
| Fig. 7 Variations in area percentages of (a) high-molecular-weight polymers and (b) oligomers with time. | |
Reproduction of PMMA
The high-purity MMA recovered by the vacuum pyrolysis minimized the reduction in molecular weight of the reproduced PMMA. Radical polymerization of the recovered MMA using AIBN at 60 °C for 3 h produced PMMA with Mn = 161
000 and Mw/Mn = 3.66 at a 92% monomer conversion, while pure MMA under the identical conditions provided PMMA with Mn = 221
000 and Mw/Mn = 1.92 at a 90% conversion. The difference in molecular weight between the PMMA from the recovered MMA and pure MMA was relatively small. The PMMA produced from the recovered MMA exhibited an increase in lower molecular weight products due to slight impurities (Fig. 8). However, these impurities caused negligible changes in the molecular weight at the peak top and on the higher molecular weight side of the curve, suggesting that the impurities caused chain transfer during the late stage of polymerization, but had low chain transfer constants. The MMA recovered with 95% purity through the vacuum pyrolysis in this study minimized the decrease in the molecular weight of the reproduced PMMA. There are few studies that have evaluated the reproducibility of recovered MMA for producing the original PMMA, even though the monomer was recovered with an extremely high purity of 99% or more.27,32,33 Achilias reported that MMA recovered with 97% purity significantly reduced the molecular weight of the reproduced PMMA.28,34 Popescu and coworkers demonstrated that impurities in recovered MMA greatly diminished the Vickers hardness and optical transparency of the reproduced PMMA.18
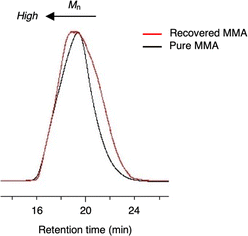 |
| Fig. 8 GPC profiles of the reproduced PMMA and PMMA produced from pure MMA. | |
Recently, Pucci et al. reported that commercially available recovered MMA with 99% purity provided PMMA comparable to the original PMMA when used as a material for luminescent solar concentrators (LSCs); however, the impurities in the MMA accelerated the photodegradation of the reproduced LSC.29 The comparison with these previous studies highlights the importance of the quality of impurities when reproducing PMMA from recovered MMA. Even with very high purity, slight amounts of impurities with large chain transfer constants, such as allyl, benzyl or thio compounds,35,36 can cause a significant reduction in molecular weight, leading to deterioration in the physical properties of the reproduction. Additionally, optically sensitive impurities can cause undesirable photochemical side reactions during PMMA reproduction or even after manufacturing. It is likely that such impurities were not generated during the vacuum pyrolysis in this study. The retention of high molecular weight, which determines the physical properties of the reproduced PMMA, suggests that the monomer recovered through the vacuum pyrolysis could serve as a substitute for virgin MMA in PMMA manufacturing.
Vacuum pyrolysis of commercial EP
This investigation also demonstrated that the pyrolysis of other commercial EP, whether cross-linked or composed of binary or ternary monomers, could recover their component monomers with high purities. The results are summarized in Table 1, and the 1H NMR spectra of the recovered monomers are shown in Fig. 9. The PS beads cross-linked with 1% divinylbenzene were depolymerized by the pyrolysis without any catalysts, recovering styrene monomer with a 56% yield and 91% purity. The cross-linking slightly affected the monomer purity, as non-cross-linked PS produced styrene with a 55% yield and 99% purity.30 The previous study also reported that the presence of molecular sieves during the pyrolysis enhanced styrene recovery. The use of MS-4A molecular sieves increased both the yield and purity of styrene for the cross-linked PS. The AS resin dripper, with a unit molar ratio of A/S = 0.354/0.646, yielded its monomers with an A/S ratio of 0.139/0.861, indicating a styrene-rich component recovery. This suggests that the styrene units depolymerize more readily than the acrylonitrile units. While the monomer purity was very high, the yield was relatively low. The addition of MS-4A increased the monomer yield without altering the composition. Similarly, the ABS resin rod, with a unit molar ratio of A/B/S = 0.253/0.383/0.364, recovered its components as A/B/S = 0.185/0.010/0.805 with high purity. The A/S ratio in the recovered monomers was comparable to that of the monomers recovered from the AS resin dripper. The ABS resin rod recovered only a small amount of butadiene due to its very low boiling point of −4.5 °C, even under standard atmospheric pressure (760 mmHg). The monomer likely escaped the system during the pyrolysis under high vacuum conditions and during the return to ambient temperature, which reduced the overall monomer yield. The use of MS-4A increased the monomer yield with negligible changes to the monomer ratio, although the purity was slightly lower. The presence of MS-4A generated more impurities from the butadiene units; however, the recovered monomers still maintained a high purity of 86%.
Table 1 The vacuum pyrolysis depolymerization of the EPa
Resin |
MS-4Ab |
Recovered monomer |
Yield (%) |
Purityc (%) |
Compositiond |
Pyrolysis for 20 min. PS-CL: PS cross-linked. AS: A/S = 0.354/0.646. ABS: A/B/S = 0.253/0.383/0.364.
MS-4A/resin = 1/1 wt/wt.
Calculated by GC.
Determined by 1H NMR.
|
PS-CL |
— |
56 |
91 |
— |
PS-CL |
1.0 |
70 |
92 |
— |
AS |
— |
32 |
98 |
0.139/0.861 |
AS |
1.0 |
47 |
97 |
0.117/0.883 |
ABS |
— |
29 |
90 |
0.185/0.010/0.805 |
ABS |
1.0 |
35 |
86 |
0.170/0.015/0.815 |
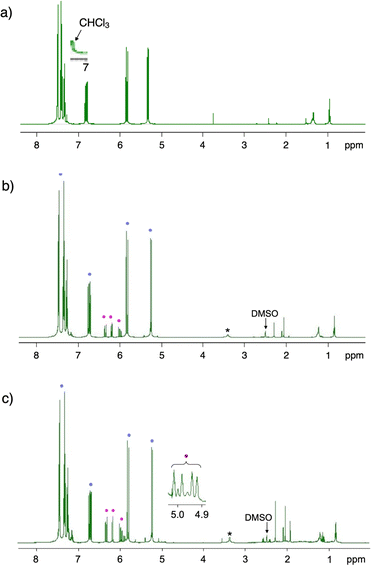 |
| Fig. 9
1H NMR spectra of recovered (a) styrene, (b) acrylonitrile/styrene (A/S) and (c) acrylonitrile/butadiene/styrene (A/B/S) from the pyrolysis. Solvent: CDCl3 for styrene, and DMSO-d6 for A/S and A/B/S. Peaks assigned to styrene ( ), acrylonitrile ( ), and butadiene ( ). *Indicates impurity in DMSO-d6. | |
Conclusions
The vacuum pyrolysis successfully recovered high-purity monomers from commercial engineering plastics. This high-purity recovery is attributed to the escape of slightly generated gaseous products under high vacuum conditions. In the case of the PMMA pyrolysis, the depolymerization competed with side reactions such as radical coupling, disproportionation and backbiting. These reactions generated minor impurities, which slightly hindered quantitative monomer recovery. While the impurities in the recovered MMA caused an increase in low-molecular-weight products during the radical polymerization of the MMA, they produced negligible changes in the molecular weight of the main high-molecular-weight polymers. Therefore, the recovered MMA could serve as an alternative to virgin monomer in PMMA manufacturing. The vacuum pyrolysis requires no additional purification of the recovered monomers and does not necessitate precise temperature control, as the process can be conducted using a simple spirit lamp flame. This convenient method for recovering high-purity monomers from waste plastics facilitates local activities in chemical recycling at their organizations, communities and schools, rather than relying solely on government policies and large-scale corporate waste management. The local recycling initiatives, integrated with company manufacturing processes, could form an economic closed-loop in the recycling system, where governments and companies purchase high-purity monomers recovered by the local activities, with the profits reinvested to further advance the recycling activities. Such a chemical and economic closed-loop system promises to reduce plastic waste pollution and emissions, which will be essential in the near future.
Data availability
The data supporting this article have been included as part of the ESI.†
Conflicts of interest
There are no conflicts to declare.
Acknowledgements
The author extends gratitude to the Open Facility Center at the Tokyo Institute of Technology for conducting the elemental analysis to determine the molar ratio of units in the ABS resin.
References
- N. Singh and T. R. Walker, npj Mater. Sustain., 2024, 2, 17 CrossRef PubMed.
-
Plastics use projections to 2060, Global Plastics Outlook, 2022, DOI:10.1787/65863783-EN.
- D. Kwon, Nature, 2023, 616, 234–237 CrossRef CAS PubMed.
- L. Lebreton and A. Andrady, Palgrave Commun., 2019, 5, 1–11 CrossRef.
- R. Geyer, J. R. Jambeck and K. L. Law, Sci. Adv., 2017, 3, e1700782 CrossRef PubMed.
-
Plastic pollution is growing relentlessly as waste management and recycling fall short, says OECD, 2022, https://www.oecd.org/en/about/news/press-releases/2022/02/plastic-pollution-is-growing-relentlessly-as-waste-management-and-recycling-fall-short.html#:%7E:text=Globalplasticwastegenerationmore,2019to353milliontonnes.
- U. Ali, K. J. B. A. Karim and N. A. Buang, Polym. Rev., 2015, 55, 678–705 CrossRef CAS.
-
L. W. McKeen, The Effect of UV Light and Weather on Plastics and Elastomers, Elsevier, Washington, WA, 4th edn, 2019, p. 254 Search PubMed.
- P. Saxena and P. Shukla, Polym. Bull., 2022, 79, 5635–5665 CrossRef CAS.
- J. D. Tommaso and J.-L. Dubois, Polymers, 2021, 13, 2724 CrossRef PubMed.
- K. Charmondusit and L. Seeluangsawat, Resour., Conserv. Recycl., 2009, 54, 97–103 CrossRef.
- G. X. Xi, S. L. Song and Q. Liu, Thermochim. Acta, 2005, 435, 64–67 CrossRef CAS.
- M. Sponchioni and S. Altinok, Adv. Chem. Eng., 2022, 60, 269–287 CAS.
- S. Mouffok and M. Kaci, Polym. Eng. Sci., 2024, 64, 2905–2916 CrossRef CAS.
- O. Guselnikova, O. Semyonov, E. Sviridova, R. Gulyaev, A. Gorbunova, D. Kogolev, T. Andrii, Y. Yamauchi, R. Boukherroub and P. Postnikov, Chem. Soc. Rev., 2023, 52, 4755–4832 RSC.
- S. K. Wijeyatunga, K. M. Derr, C. P. Maladeniya, P. Y. Sauceda-Oloño, A. G. Tennyson and R. C. Smith, J. Polym. Sci., 2024, 62, 554–563 CrossRef CAS.
-
G. Odian, Principles of Polymerization, John Wiley & Sons Inc., Hoboken, New Jersey, 4th edn, 2004, p. 281 Search PubMed.
- V. Popescu, C. Vasile, M. Brebu, G. L. Popescu, M. Moldovan, C. Prejmerean, L. Stanulet, C. Trisca-Rusu and I. Cojocaru, J. Alloys Compd., 2009, 483, 432–436 CrossRef CAS.
- M. T. Chin and T. Diao, ACS Catal., 2024, 14, 12437–12453 CrossRef CAS PubMed.
- E. K. C. Moens, K. D. Smit, Y. W. Marien, A. D. Trigilio, P. H. M. V. Steenberge, K. M. V. Geem, J.-L. Dubois and D. R. D'hooge, Polymers, 2020, 12, 1667 CrossRef CAS PubMed.
- M. Cvek, A. M. Jazani, F. D. L. Bossa, R. Bernat, K. Kapil and K. Matyjaszewski, Eur. Polym. J., 2024, 220, 113429 CrossRef CAS.
- Z. Arslan, H. C. Kiliclar and Y. Yagci, Des. Monomers Polym., 2022, 25, 271–276 CrossRef CAS PubMed.
- G. Ng, S. W. Prescott, A. Postma, G. Moad, C. J. Hawker, A. Anastasaki and C. Boyer, J. Polym. Sci., 2024, 62, 3920–3928 CrossRef CAS.
- V. Bellotti, K. Parkatzidis, H. S. Wang, N. D. A. Watuthanthrige, M. Orfano, A. Monguzzi, N. P. Truong, R. Simonuttia and A. Anastasaki, Polym. Chem., 2023, 14, 253–258 RSC.
- J. B. Young, J. I. Bowman, C. B. Eades, A. J. Wong and B. S. Sumerlin, ACS Macro Lett., 2022, 11, 1390–1395 CrossRef CAS PubMed.
- R. W. Hughes, M. E. Lott, I. S. Zastrow, J. B. Young, T. Maity and B. S. Sumerlin, J. Am. Chem. Soc., 2024, 146, 6217–6224 CrossRef CAS PubMed.
- B.-S. Kang, S. G. Kim and J.-S. Kim, J. Anal. Appl. Pyrolysis, 2008, 81, 7–13 CrossRef CAS.
- D. S. Achilias, Eur. Polym. J., 2007, 43, 2564–2575 CrossRef CAS.
- A. Picchi, I. Bettini, M. Ilarioni, M. Carlotti and A. Pucci, RSC Appl. Polym., 2024, 2, 624–633 RSC.
- E. Yoshida, RSC Sustain., 2023, 1, 2058–2065 RSC.
- J. C. Bevington, H. W. Melville and R. P. Taylor, J. Polym. Sci., 1954, 14, 463–476 CrossRef CAS.
- M. Newborough, D. Highgate and J. Matcham, Appl. Therm. Eng., 2003, 23, 721–731 CrossRef CAS.
- K. Smolders and J. Baeyens, Waste Manage., 2004, 24, 849–857 CrossRef CAS PubMed.
-
E. Esmizadeh, S. Khalili, A. Vahidifar, G. Naderi and C. Dubois, Waste Polymethyl Methacrylate (PMMA): Recycling and High-Yield Monomer Recovery in Handbook of Ecomaterials, ed. L. M. T. Martínez, O. V. Kharissova and B. I. Kharisov, Springer International Publishing AG, 2018 Search PubMed.
- M. Litt and F. R. Eirich, J. Polym. Sci., 1960, 45, 379–396 CrossRef CAS.
-
G. Odian, Principles of Polymerization, John Wiley & Sons Inc., Hoboken, New Jersey, 4th edn, 2004, p. 247 Search PubMed.
|
This journal is © The Royal Society of Chemistry 2024 |
Click here to see how this site uses Cookies. View our privacy policy here.