DOI:
10.1039/D4TA02916J
(Paper)
J. Mater. Chem. A, 2024,
12, 17350-17359
Facile and scalable fabrication of flexible micro-supercapacitor with high volumetric performance based on ultrathin Co(OH)2 nanosheets†
Received
27th April 2024
, Accepted 5th June 2024
First published on 20th June 2024
Abstract
The rapid miniaturization of portable and wearable electronics has gained increasing demand for flexible and high-performance microscale energy storage devices such as micro-supercapacitors (MSCs) that provide flexibility and portability. Volumetric capacitance is the most significant metric for miniaturized capacitive energy storage units due to the limitations in device volume and active surface area. Herein, we have used an ultrathin (3.5 nm) two-dimensional (2D) Co(OH)2 nanosheet (NS) as an electrode material to fabricate a flexible, solid-state MSC on micropatterned laser-scribed graphene (LSG). On account of the combination of ultrathin morphology, in-plane geometry of interdigitated microelectrodes, and highly conductive and robust interaction of ultrathin Co(OH)2 NS and LSG, the Co(OH)2 NS-LSG-based micro-supercapacitor (CN-LSG MSC) exhibits high rate-capability and delivers a superior volumetric capacitance of 258 F cm−3 at 13 A cm−3 current density. Moreover, the CN-LSG MSC device achieved an excellent energy density of 22 mW h cm−3 at a power density of 6.8 W cm−3 with a remarkable cyclic stability of 96.4% even after 20
000 charge–discharge cycles. The fabricated CN-LSG MSC exhibits unaffected mechanical flexibility under different bending deformations. Additionally, we have demonstrated the possibility of integrating a CN-LSG MSC by connecting it in series and parallel configurations, which amplifies the operating voltage and output current, respectively. Therefore, the present research work opens a new avenue for the simple and scalable manufacture of ultrathin film-based MSCs promising for various lightweight, miniaturized, flexible, and wearable electronics.
1 Introduction
The rapid advancements in portable and wearable electronics have greatly stimulated the development of micro-electrochemical energy storage devices with miniaturized volume, easy modulation, endurable flexibility, and high energy and power densities.1,2 However, commercially available micro-batteries have some limitations, such as low energy density, a slow charge–discharge process, and limited life cycle.3 Moreover, the efficient integration of micro-batteries into electronic circuits remains a significant problem, which restricts the miniaturization of the system.4 Micro-supercapacitors (MSCs) have attracted tremendous research attention due to lower device thickness and size, superior flexibility, fast charge–discharge rate, high power density, long cyclic stability, and, more importantly, safe operation. Notably, the in-plane configuration of the electrode arrays provides several advantages over conventional energy storage devices, including vertical MSCs and thin film batteries. The open-edge feature and high edge-to-surface ratio of in-plane interdigitated MSCs greatly enhance the accessibility of the active electrode material.5 The shorter transport distance between interdigitated finger arrays reduces electrolyte ion transmission resistance, facilitating rapid ion transport and thus increasing high-frequency response.6,7 However, achieving energy density near or higher than that of micro-batteries without compromising the power density and cyclic stability is one of the crucial issues of the miniaturized planar MSCs.1,2,8
Currently, graphene-based MSCs are widely explored due to their excellent electrical conductivity, electron mobility, large surface area, favorable chemical stability, and outstanding flexibility which provides electrical double-layer capacitance (EDLC).9,10 Until now, numerous techniques have been employed to fabricate graphene-based MSCs, including photolithography,11 vacuum filtration,12 inkjet printing,13 3D printing,14 and electrodeposition.15–17 Despite their numerous advantages, these techniques have a few limitations such as slow operation, the requirement of post-processing, substrate conductivity, and ink compatibility. The laser scribing technique outperforms most of the previously mentioned techniques due to its high processing speed, exceptional precision, and ease of integration making it promising for large-scale production.18–21 However, pristine graphene-based MSCs show low capacitance metrics and energy density, which hinders their practical applications.22 To surpass this challenge, much attention has been focused on modifying the electrochemical performance of graphene-based MSCs.23 Since the energy density of energy storage devices (E) is determined by the capacitance (C) and operating voltage window (V), i.e., E = 1/2CV2,24 further upgradation of energy density relies on enhancing either of these characteristics. Pseudocapacitive materials such as transition metal oxides, hydroxides, sulphides, and conducting polymers25–29 have widely emerged in the pursuit of high capacitance due to fast and reversible surface faradaic redox reactions. The surface atoms or a few nanometer-thin layers of the active electrode material play a predominant role in the pseudocapacitive process.30–32 The maximum redox sites in ultrathin pseudocapacitive materials are exposed in the planar two-dimensional sheet geometry, accelerating ion transportation and significantly boosting the capacitance merits.33–37
Recently, it has been reported that high surface area and rapid ion intercalation in two-dimensional (2D) materials, such as graphene, and MXenes, and their composites can make them a prominent candidate for thin films in MSCs.38,39 For instance, Wu et al. reported a graphene thin film-based in-plane MSC which delivered a volumetric capacitance of 17.9 F cm−3 due to the combined effect of increased surface area and high conductivity of graphene and the in-plane configuration of the MSC device.9 Yuan et al. developed a facile and scalable strategy to fabricate the MSC based on laser-scribed in situ heteroatom-doped porous graphene. The resulting MSC exhibited a volumetric capacitance of 11.76 F cm−3.38 Due to their high packing density (4.93 g cm−3), hydrophilicity, and high electrical conductivity (5000 S m−1), MXenes represent an outstanding electrode material having high volumetric capacitance.40 For example, Huang et al. reported freestanding, highly conducting, and flexible Ti3C2Tx (MXene) films with thicknesses ranging from 1 to 2 μm through the vacuum filtration process. The Ti3C2Tx-based flexible solid-state MSC exhibited a maximum volumetric capacitance of 183 F cm−3 and an energy density of 12.4 mW h cm−3.41 Very recently, Fan et al. reported Ti3C2Tx nanosheets via the Langmuir–Blodgett (LB) technique with a controlled number of layers. In particular studies, 20 layers of the MXene film with a thickness of ∼140 nm exhibited a volumetric capacitance of 421 F cm−3.42 Regardless, the high cost, complexity in synthesis, and instability of MXenes are critical challenges when employing MXene-based materials for MSCs.
Cobalt hydroxide (Co(OH)2), as a layered transition metal hydroxide, has become a competitive electrode material for energy storage due to its high theoretical capacitance (3460 A g−1)43 and large interlayer spacing, which promises fast ion transport as well as large surface area and satisfactory stability.31,44 However, conventional approaches to achieve ultrathin films of Co(OH)2 have employed simple particle assembly and usage of polymer additives to synthesize thin film electrodes, which leads to the reduced electrical conductivity, poor interfacial bonding, and degradation of polymer additives in the working potential range, hence sacrificing the overall electrochemical performance.45,46 In addition, the synthesized films are reported to have thicknesses ranging from a few to tens of micrometers. The development of ultrathin films with equivalent or enhanced performance would be significant with the growing demand for portable, lightweight, and miniaturized devices.
Herein, we have reported the binder-free, facile, and scalable synthesis of large area, flat, ultrathin (3.5 nm thin) Co(OH)2 NS via the ionic layer epitaxy (ILE) method.47,48 and transferred onto laser-scribed graphene (LSG) to fabricate an in-plane interdigitated solid-state and flexible MSC. LSG serves as a flexible and conducting matrix for large area, ultrathin Co(OH)2 NS. The CN-LSG MSC in PVA/KOH gel electrolyte delivered a high volumetric capacitance of 258 F cm−3 at a current density of 13 A cm−3 and excellent energy density (22 mW h cm−3). Furthermore, the CN-LSG MSC demonstrates outstanding cyclic stability (96.4%) over 20
000 charge–discharge cycles. Moreover, the CN-LSG MSC exhibited excellent flexibility under bending deformations. Therefore, this binder-free ultrathin Co(OH)2 NS-based MSC paves the way for the simple and scalable fabrication of high-performance flexible solid-state MSCs.
2 Experimental section
2.1 Materials
Polyimide (PI, thickness 0.06 mm) tape and polyethylene terephthalate (PET, thickness 100 μm) sheets were purchased from Eurotapes International Pvt. Ltd, Delhi, India. Cobalt nitrate hexahydrate (Co(NO3)2·6H2O, ≥98% purity) was purchased from SD Fine Pvt. Ltd, India. Hexamethylenetetramine (C6H12N4, ≥99% purity), sodium dodecyl sulphate (NaC12H25SO4, ≥99% purity), potassium hydroxide flakes (KOH, 90% purity), and polyvinyl alcohol (PVA, >95%, MW 85
000–124
000) were purchased from Sigma Aldrich. All the chemicals were used as received without any further purification.
2.2 Fabrication of flexible micro-supercapacitors
Fig. 1a shows the schematic representation of the fabrication process of the LSG MSC and CN-LSG MSC. The fabrication process of CN-LSG-based MSC comprises three significant steps: (i) patterning of the substrate, (ii) transfer of the electrode material, and (iii) device packaging.
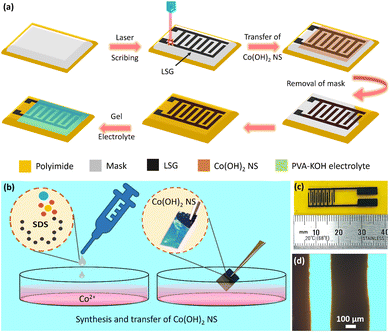 |
| Fig. 1 (a) Schematic illustration of the fabrication process of the CN-LSG MSC, (b) schematic illustration of synthesis and the transfer process of Co(OH)2 NS, (c) digital photograph of the as prepared CN-LSG MSC, and (d) optical microscope image of the electrode arrays (the dark region is the Co(OH)2 NS on LSG and bright region is the bare surface of the PI film). The scale bar is 100 μm. | |
2.2.1 Patterning of the substrate.
The patterning of LSG was carried out as described in previous reports.18 Initially, the PI tape was covered by a PET sheet (thickness: 0.1 mm). A CO2 laser (wavelength: 10.6 μm, pulse duration: ∼14 μs) with an output power of 8.0 Watts and a scan rate of 250 mm s−1 was focused on a horizontally placed PI tape/PET sheet to engrave the programmed pattern. LSG was patterned into 14 interdigitated electrodes (seven per polarity) with a length of 5.67 mm, a width of 0.35 mm, and a gap of 0.56 mm between two adjacent electrodes (total working area = 0.41 cm2). The PET sheet was completely carved, leaving the interdigitated micro-pattern on the PI film. The engraved area of the PI film was effectively converted into graphene. LSG was hydrophilic and could be used as a conducting substrate for versatile electrode materials.
2.2.2 Synthesis of the Co(OH)2 film.
50 mL of an aqueous nutrient solution containing 10 mM of Co(NO3)2·6H2O and HMTA were gently added to the glass culture dish (h = 1.6 cm, opening area of 78.5 cm2). After 20 minutes of standing, 10 μL of a hexane solution containing 0.1 vol% SDS was spread at the water–air interface and equilibrated for 10 minutes. Subsequently, this glass culture dish was covered with a lid and placed in a conventional oven at 60 °C for 2 h to grow ultrathin Co(OH)2 NS at the water–air interface. The glass culture dish was kept for cooling at room temperature (∼28 °C) and scooped on the desired substrate (Fig. 1b).
2.2.3
Device fabrication.
The film at the interface was directly scooped on LSG micropatterns and left to dry at room temperature for 24 hours. Finally, the PET sheet was gently peeled off from the micro-patterns separating two adjacent microelectrodes. PVA/KOH gel was applied to the microelectrodes, and the device was allowed to dry overnight to get the CN-LSG solid-state MSC. The LSG MSC was fabricated similarly to the CN-LSG MSC without the Co(OH)2 NS. Fig. 1c and d show digital photographs and optical microscope images of the fabricated CN-LSG MSC. The details of characterization and experimental and electrochemical measurements are provided in the experimental section in the ESI.†
2.3 Characterization
An optical microscope (Epi-Fluroscence Trinocular Microscope), field emission scanning electron microscope (FE-SEM, JEOL, JSM-7100), transmission electron microscope (TEM, JEOL, JEM-2100 Plus, Japan), and high-resolution transmission electron microscope (HRTEM) were used to study the surface morphology and crystal structure of the Co(OH)2 nanosheet (NS). High-angle annular dark-field scanning transmission electron microscopy (HAADF-STEM) and STEM energy-dispersive X-ray spectroscopy (STEM-EDS) elemental mapping (FEI Titan STEM) were used for elemental mapping of the Co(OH)2 NS. The Co(OH)2 NS thickness was estimated by using an NX20 atomic force microscope (AFM) from Park Systems. X-ray photoelectron spectroscopy (XPS, Kratos Analytical AXIS Ultra DLD) was performed with monochromatic Al Kα X-ray radiation (1486.6 eV) and an electron analyzer operating at a fixed pass energy of 20 eV and the results were fitted using CasaXPS V2.3.24. The Co(OH)2 NS were transferred onto a SiO2-coated Si wafer for SEM, AFM, and XPS analyses. TEM analysis of Co(OH)2 NS was carried out on a 300 mesh Cu TEM grid. The XRD sample of the Co(OH)2 nanosheet was prepared by scooping the film 15 times on a Si wafer due to the ultra-small thickness and XRD analysis was performed using a Rigaku Smart lab (1.54 Å Cu-Kα source). The surface morphology and elemental composition of laser-scribed graphene (LSG) were analyzed using an optical microscope (Epi-Fluroscence Trinocular Microscope), field emission scanning electron microscope (FE-SEM, JEOL, JSM-7100), X-ray diffractometer (XRD, Rigaku Ultima IV) and Raman spectrometer (JY, LabRam HR UV/VIS/NIR photoluminescence) using an excitation wavelength of 532 nm. The tensile tests of LSG and Co(OH)2 NS/LSG electrodes were carried out as per ASTM D 882 using a universal tensile machine (UNITECH-9450) with a constant speed of 10 mm min−1 at ARML Pvt Ltd, Bangalore, India.
2.4 Electrochemical measurements
The electrochemical performance of Co(OH)2 NS/LSG and pristine LSG was measured in a three-electrode system using 1 M KOH aqueous electrolyte and Hg/HgO and Pt wire as the reference and counter electrodes, respectively. The electrochemical performance of the CN-LSG MSC and LSG MSC in PVA/KOH gel electrolyte was investigated using cyclic voltammetry (CV), galvanostatic charge–discharge (GCD), and electrochemical impedance spectroscopy (EIS) using Origalys potentiostat (OrigalysElectroChem SAS, France). The CV of the symmetric CN-LSG MSC and LSG MSC was tested within the potential range of 0 to 0.8 V at scan rates ranging from 5 to 100 mV s−1. The GCD analysis was performed at different current densities from 13 to 110 A cm−3. The EIS measurements were carried out in the frequency range from 0.1 Hz to 10 kHz at a potential of 5 mV.
The areal capacity values of Co(OH)2/LSG and pristine LSG in the three-electrode system were calculated from GCD at different current densities according to eqn (1):20,38
| 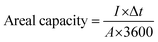 | (1) |
where
I represents the discharge current (A), Δ
t is the discharge time (s),
A is the active area of the working electrode, and Δ
v is a discharge potential window.
The volumetric capacitance (Cvol, F cm−3) of the MSC was calculated by using eqn (2)
|  | (2) |
where
A (cm
2) and
t (cm) are the total area of the active portion of microelectrodes and the thickness of the active material, respectively. The dimensions of 14 electrodes (7 positive and 7 negative) are 5.67 mm in length and 0.5 mm in width. The dimensions of both side arms of the MSC are 11.63 mm in length and 0.6 mm in width. Considering these dimensions, the area of the MSC is calculated to be 0.41 cm
2.
The volumetric energy density (Evol, W h cm−3) and power density (Pvol, W cm−3) of the MSC device were determined from discharge curves at various current densities as given in eqn (3) and (4), respectively.
| 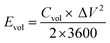 | (3) |
|  | (4) |
where
Cvol is the volumetric capacitance (F cm
−3) calculated from GCD curves. Δ
V is the potential window (V) and Δ
t is the discharge time (s).
3 Results and discussion
3.1 Material characterization
The Co(OH)2 NS was synthesized at the water–air interface using an amphiphilic molecule monolayer.47,48Fig. 1b shows the Co(OH)2NS synthesis and transfer process. The solution of 0.1% SDS in hexane was added to the water–air interface of an aqueous solution containing 10 mM of cobalt nitrate hexahydrate and HMTA (1
:
1 ratio). HMTA decomposes into HCHO and ammonium hydroxide (NH4OH) at 60 °C in the aqueous solution, which offers an alkaline environment. The presence of NH4+ ions was confirmed using Nessler's test.49 Due to the electrostatic interactions, the Co2+ ions were directed underneath the closely packed monolayer of negatively charged dodecyl sulphate ions. The Co2+ ions could reach supersaturation in an alkaline environment and crystalize into an ultrathin crystalline Co(OH)2 layer at the water–air interface. This synthesis strategy ensures the facile and effective synthesis of a large area, 2D Co(OH)2 NS. The resulting Co(OH)2 NS thin film entirely covered the water surface over a large area or was suspended over the surface of silicon wafers, a holey carbon TEM grid, and LSG, implying the high mechanical strength of the Co(OH)2 NS thin film. After being transferred onto a silicon wafer, the as-synthesized Co(OH)2 NS thin film was investigated using optical and field-emission scanning electron microscopy (FESEM), as shown in Fig. 2a and b, respectively. The optical microscopy image suggests that the film covers the complete substrate under investigation (Fig. 2a). The crack region (marked by an arrow) showed contrast variation of the ultrathin film covering the large area on the substrate. The FESEM image also suggests a continuous film covering the large area (Fig. 2b). Few wrinkles are observed in the top-view FESEM image, which are likely to have originated during the transfer and drying process of the Co(OH)2 NS. The uniform distribution of Co(OH)2 NS on LSG is also supported by FESEM-Energy Dispersive X-ray (EDS) analysis and elemental mapping as shown in Fig. S1.† The thickness of the Co(OH)2 NS was measured at the crack using atomic force microscopy (AFM), as shown in Fig. 2c. The AFM image shows a smooth and uniform surface of the as-synthesized NS across the entire area. The inset of Fig. 2c shows two two-line profiles along the cracked area confirming the homogeneity and uniform thickness of 3.5 nm. The calculated average surface roughness factor (Ra) is 0.25 nm. These results conspicuously reveal that the synthesized NS is a continuous rather than a particle-assembled layer. The particle-assembled layer hinders the connectivity throughout the film due to the existing gaps and poor interfacial bonding. The large area, uniformity, and ultrathin Co(OH)2 NS provide better connection pathways in two dimensions, which is beneficial for energy storage.
 |
| Fig. 2 Co(OH)2 NS: (a) optical microscopy image, (b) low-magnification FESEM image, and (c) AFM topography image. Inset shows a height profile along red and green lines. (d) Low-magnification TEM image, (e) HRTEM image, (f) lattice fringes, (g) line intensity profile for the selected line in figure f, (h) SAED pattern, (i–l) TEM-EDS elemental mapping, (i) high-angle annular dark-field (HAADF)TEM image (j) Co (k) O, and (l) C elements, high-resolution XPS spectrum of Co(OH)2 NS in the (m) Co2p and (n) C1s region and (o) O1s spectra of LSG and Co(OH)2/LSG. | |
The morphology of the Co(OH)2 NS was further confirmed by TEM, as shown in Fig. 2d. The contrast difference in the Co(OH)2 NS and carbon TEM grid was not noticeable owing to the film's ultrathin thickness and good uniformity. Moreover, the ultrathin and flexible feature of the Co(OH)2 NS can be clarified from a low-magnification TEM image, which is favorable for the practical application of energy storage devices. The high-resolution TEM image (HRTEM) of the Co(OH)2 NS in Fig. 2e incontestably shows the polycrystalline nature of the Co(OH)2 NS. The Co(OH)2 NS contains 2–3 nm-sized grains. Fig. 2f presents the Fast-Fourier Transform (FFT) selected area shown by the yellow square in Fig. 2e. An inter-planar distance of 0.27 nm corresponding to the (100) plane was computed by the inverse FFT (IFFT) method (Fig. 2g) using Gatan software. The concentric diffraction rings in the SAED pattern further evidence the polycrystallinity of the Co(OH)2 NS (Fig. 2h). These bright spots in the diffraction pattern of the Co(OH)2 NS are indexed to the (101), (111), and (211) atomic planes of hexagonal Co(OH)2. Furthermore, TEM EDS elemental mapping in Fig. 2i–l illustrates the homogeneous distribution of Co and O atoms within the Co(OH)2 NS. The C element in Fig. 2l is assigned to carbon from the TEM grid.
X-ray diffraction was carried out to study the crystal structure of the nanosheet (Fig. S2†). The hkl reflection in the XRD spectrum matches well with a standard crystallographic α-Co(OH)2 spectrum (JCPDS 46-0605) which is consistent with the previous report.50 This phase was found to comprise a brucite-like sheet with hexagonal close-packing of hydroxyl ions in which Co2+ cations occupy the octahedral sites. Furthermore, to study the structure and composition of LSG, XRD and Raman spectroscopy were performed. The XRD pattern of LSG (Fig. S3a†) exhibits an obvious peak at 2θ = 25.7°, which is assigned to the crystal phase (002) reflection with a corresponding interlayer spacing of 0.34 nm.38 The CO2 laser beam triggered ultra-high localized temperature (>2500 °C) leading to graphitized LSG. Raman spectroscopy was used to obtain further information on LSG (Fig. S3b†). The Raman spectrum of LSG exhibited three characteristic bands at 1350 cm−1, 1580 cm−1, and 2690 cm−1, corresponding to characteristic D, G, and 2D bands, respectively. The characteristic peak at 1350 cm−1 corresponds to the D band of residual oxygen functional groups. An intense G band at 1580 cm−1 confirms the sp2 hybridized C–C bonds of LSG. The 2D band of LSG is located at 2700 cm−1. LSG showed intense G and 2D bands confirming the high crystallinity of graphene. It is worth using it as a current collector for the MSC due to its high conductivity and superior flexibility. The XPS survey spectrum of the Co(OH)2 NS transferred onto LSG (Fig. S4†) implies the presence of carbon, oxygen, and cobalt elements. To verify the valence state of Co, the high-resolution Co2p spectrum shows the Co2p3/2 and Co2p1/2, components, and both components qualitatively contain the same chemical information. Thus, only Co2p3/2 bands, including the shake-up satellites of the cobalt ions were curve-fitted using the Shirley background. The fitting curve of Co2p shows two dominant peaks at 781.0 and 796.8 eV corresponding to Co2p3/2 and Co2p1/2, respectively (Fig. 2m). The spin–orbit splitting value of 15.8 eV indicates the Co2+ state of the Co(OH)2 NS. As previously observed by Biesinger et al.,51 the sharp peak at 781.0 eV followed by shake-up peaks at 782.8, 786.0, and 789.4 eV correspond to characteristic peaks of Co(OH)2. Furthermore, the –OH groups from Co(OH)2 might interact with O-containing groups of LSG, and thus the C1s might be informative. The high-resolution C1s spectrum can be deconvoluted into 4 peaks at 284.8, 285.4, 287.1, and 289.7 eV corresponding to C–C, C–O, C
O, and O–C
O from LSG in the Co(OH)2/LSG electrode, respectively (Fig. 3n). The BE of C
O and O–C
O is shifted to the higher energy by ∼0.7 eV as compared to that of the pristine LSG electrode (Fig S5†). Furthermore, there is a significant change in the shape of the band centered at 289.7 eV for O–C
O, and the C–O peak at 285.5–286.5 eV becomes prominent suggesting the change in the chemical environment due to the electrostatic/hydrogen bonding interaction between Co(OH)2 and LSG in the electrode which is further supported by the slight shift of the O1s spectrum of Co(OH)2/LSG as compared to that of LSG only (Fig. 3o). The intensity of the O1s peak is notably increased, as a result of the contribution of O from Co(OH)2 on LSG. The tensile stress–strain test of LSG and the Co(OH)2 NS/LSG electrode was carried out to study the mechanical properties as shown in Fig. S6.† Interestingly, the Co(OH)2 NS/LSG electrode showed a high tensile strength of 6.40 MPa which is 1.3 times more than that of the LSG electrode. The multiple fluctuations in the stress–strain curve are observed due to various stages of electrodes under tensile loading.52 The stress–strain curve and flexibility studies indicate the robust mechanical properties of the Co(OH)2 NS/LSG electrode. The results of tensile test parameters for LSG and Co(OH)2 NS/LSG electrodes are provided in Table S1.†
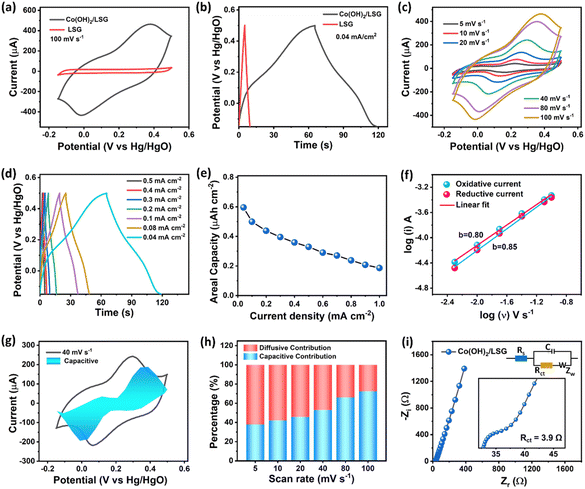 |
| Fig. 3 (a) CV curves of Co(OH)2/LSG and pristine LSG at a scan rate of 100 mV s−1, (b) GCD curve of Co(OH)2/LSG and pristine LSG at 0.04 mA cm−2, (c) CV curve of Co(OH)2/LSG at various scan rates (5–100 mV s−1), (d) GCD curve of Co(OH)2/LSG at different current densities (0.04–0.5 mA cm−2), (e) areal capacity of Co(OH)2/LSG with respect to current densities, (f) log(i) vs. log(ν) plot, (g) contribution of the surface capacitance to the total current response of the CV curve of Co(OH)2/LSG at 40 mV s−1, (h) contribution of surface capacitance and the diffusion-controlled process of Co(OH)2/LSG as a function of scan rate, and (i) Nyquist plot of the Co(OH)2/LSG electrode. The inset shows the fitted equivalent circuit and zoomed image of the Nyquist plot. | |
3.2 Electrochemical characterization of the Co(OH)2 NS/LSG electrode
The Co(OH)2 NS/LSG electrode was prepared by transferring the ultrathin, large area Co(OH)2 NS onto the LSG electrode having an area of 1 cm2. The electrochemical performance of binder-free Co(OH)2 NS/LSG and pristine LSG is measured in the three-electrode system using 1 M KOH aqueous electrolyte in the potential range from −0.15 to 0.5 V using Hg/HgO and Pt wire as the reference and counter electrodes, respectively. Fig. 3a displays the comparative cyclic voltammetry (CV) curves of Co(OH)2 NS/LSG and pristine LSG at a scan rate of 100 mV s−1. Pristine LSG shows an almost rectangular CV curve representing its EDLC behavior. The minimum enclosed area under the CV curve confirms the negligible contribution of pristine LSG in the charge storage performance of the Co(OH)2 NS/LSG electrode. However, the enclosed area significantly increased after Co(OH)2 NS transfer. Fig. 3b shows the galvanostatic charge–discharge (GCD) curves of pristine LSG and Co(OH)2 NS/LSG electrodes at 0.04 mA cm−2. The GCD curve of Co(OH)2 NS/LSG is remarkably wider than that of pristine LSG. The Co(OH)2 NS/LSG shows pseudocapacitive characteristics with well-defined faradaic redox peaks (Fig. 3a). The non-linear GCD curve of the pseudocapacitive Co(OH)2 NS/LSG electrode is observed due to the potential-dependent kinetics of the faradaic process. The faradaic behavior of Co(OH)2 NS/LSG in an alkaline medium can be attributed to the following plausible reaction:
Co(OH)2 + OH− ↔ CoOOH + H2O + e− |
The pseudocapacitive behaviour of Co(OH)2 NS/LSG is also elucidated by the CV curve at different scan rates as shown in Fig. 3c. The shape of the CV curve is well retained even at a high sweep rate of 100 mV s−1, which implies the rapid charge–discharge process and high power density performance of the Co(OH)2NS. This high rate capability is attributed to the ultrathin and uniform thickness of the Co(OH)2 NS where a large number of surface atoms are exposed to the electrolyte ions leading to a fast charge–discharge response. The linear dependence of anodic (Ia) and cathodic peak currents (Ic) on the square root of scan rates indicates the good reversibility of the Co(OH)2 NS/LSG electrode as shown in Fig. S7.† The GCD curve of Co(OH)2 NS/LSG recorded at various current densities also exhibits typical pseudocapacitive behaviour consistent with CV outcomes (Fig. 3d). The GCD profile of Co(OH)2 NS/LSG displays a symmetrical charging and discharging curve shape, representing the good charge–discharge reversibility of the Co(OH)2 NS/LSG electrode. The areal capacity of Co(OH)2 NS/LSG is calculated to be 0.59, 0.51, 0.49, 0.43, 0.39, 0.35, and 0.32 μAh cm−2 at 0.04, 0.08, 0.1, 0.2, 0.3, 0.4 and 0.5 mA cm−2, respectively. The dependence of areal capacity on current density is demonstrated in Fig. 3e which indicates the good capacitive performance of Co(OH)2 NS/LS.
Furthermore, the kinetics of the Co(OH)2 NS/LSG electrode were analyzed by using the CV curve at different sweep rates using the following power formula (eqn (5) and (6)):
| i = aνb, (0.5 ≤ b ≥ 1) | (5) |
where
a and
b are variables. The value of
b is the slope of the log(
ν)
vs. log(
i) plot, reflecting the charge storage mechanism. Particularly,
b values of 0.5 and 1 represent diffusion and surface capacitance-controlled processes, respectively.
b = 1 represents surface-controlled (capacitive)/pseudocapacitive charge storage kinetics, and
b = 0.5 indicates a diffusion-limited process. As shown in
Fig. 3f, the slopes obtained from the fitted curves of the anodic peak and cathodic peaks were 0.8 and 0.85, respectively, implying that the capacitance control of Co(OH)
2 NS/LSG accounts for a significant part of the process. To further estimate the capacitive and diffusion-limited contribution to the total capacitance in Co(OH)
2 NS/LSG, the voltammetric scan rate dependence was systematically investigated using Dunn's method (
eqn (7) and
(8)).
53,54 | i(V)/ν1/2 = k1ν1/2 + k2 | (8) |
Here,
i(
V) is the current at a specified potential, and
k1ν and
k2ν1/2 represent the current contribution from surface capacitive and diffusion-controlled intercalation processes, respectively. The slope and intercept values from the linear fit of
ν1/2vs. i(
V)/
ν1/2 plot correspond to
k1 and
k2, respectively.
Fig. 3g illustrates the typical voltage profile for the capacitive current (blue region) relative to the total current. The prominent contribution at 40 mV s
−1 is derived from the surface capacitive effect, which accounts for 53% of the total capacitance of the Co(OH)
2 NS/LSG electrode. The capacitive controlled contribution increases with respect to the scan rate, as shown in
Fig. 3h. This is unsurprising since the pseudocapacitive contribution plays a key role in the ultrathin Co(OH)
2 NS and LSG. Electrochemical impedance spectroscopy (EIS) was performed to further understand the electrochemical behaviour of the Co(OH)
2 NS/LSG electrode, as shown in
Fig. 3i. The straight line in the low-frequency region of the Nyquist plot represents outstanding conductivity and capacitive-like characteristics of Co(OH)
2 NS/LSG. The EIS curve depicts a small charge transfer resistance (
Rct) of 3.9 Ω (inset of
Fig. 3i).
3.3 Electrochemical performance of the CN-LSG MSC device
To demonstrate the potential application of the CN-LSG MSC in energy storage devices, we have transferred the ultrathin Co(OH)2 NS onto LSG by scooping over 0.41 cm2 working area (see the Experimental section). The freestanding Co(OH)2 NS at the water–air interface were directly deposited twice on micropatterned LSG (current collector) to provide additional connection pathways and better connectivity. For comparison, the electrochemical measurements of the LSG MSC and CN-LSG MSC were carried out in a symmetrical two-electrode setup using PVA/KOH gel electrolyte. As shown in Fig. S8,† the LSG MSC exhibits a negligible contribution to energy storage. The performance of the CN-LSG MSC was tested by cyclic voltammetry (CV) at various scan rates from 5 to 100 mV s−1. The CV curves at all scan rates show a pseudocapacitive and well-maintained shape in the 0 to 0.8 V region (Fig. 4a), indicating the excellent charge storage properties of the CN-LSG MSC device. The outstanding rate-capability of the CN-LSG MSC is predominantly due to the ultrathin morphology of the Co(OH)2 NS, which offers short ion-diffusion pathways for rapid adsorption and desorption of electrolytes and an in-plane interdigital configuration, which leads to free movement of electrolyte ions resulting in superior rate-capability, as shown in Fig. 4b. Fig. 4c shows the galvanostatic charge–discharge curve at different current densities of 13–110 A cm−3, confirming the pseudocapacitive nature of the CN-LSG MSC. Taking into consideration the thickness of the microelectrode (∼7 nm for 2 layers of Co(OH)2 NS), the CN-LSG MSC delivered the highest volumetric capacitance of 258 F cm−3 at a current density of 13 A cm−3 which surpassed that of the state-of-the-art MSC based on other 2D nanomaterials including MXenes (87.68 F cm−3),20 black phosphorous (26.67 F cm−3)33 graphene (11.76 F cm−3 and 30.51 F cm−3),39,55 and their composites (38.1 F cm−3, 77.3 F cm−3, and 110 F cm−3).56–58 The volumetric capacitance of the CN-LSG MSC was calculated to be 258, 252, 242, 234, 228, and 223 F cm−3 at current densities of 13, 16, 19, 22, 25, and 28 A cm−3. Interestingly, the CN-LSG MSC retains 63% of its capacitance value (i.e., 163 F cm−3) even at an exceptionally high current density of 110 A cm−3, which indicates the good rate capability of the device (Fig. 4d).
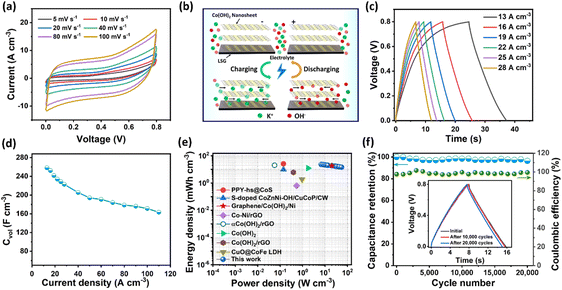 |
| Fig. 4 Electrochemical testing of the CN-LSG MSC. (a) CV curves at scan rates ranging from 5 to 100 mV s−1, (b) schematic of the in-plane CN-LSG MSC, (c) GCD curves at different current densities (from 13 to 28 A cm−3), (d) rate capability with respect to current density, (e) Ragone plot, and (f) long-term cyclic stability of the CN-LSG MSC. The inset shows shows the initial GCD curve, and that after 10 000 and 20 000 GCD cycles. | |
The energy density and power density are important parameters in the practical implications of MSCs. The CN-LSG MSC could achieve an excellent energy density of 22 mW h cm−3 at a power density of 6.8 W cm−3 and it retained up to 14 mW h cm−3 at a power density of 54 W cm−3. The Ragone plot of volumetric energy and power density of the CN-LSG MSC with recent reports on cobalt-based MSCs is shown in Fig. 4e. The energy density and power density of the Co-LSG MSC are superior to those of recently reported cobalt-based MSCs, such as PPY-hs@CoS,59 S-doped CoZnNi–OH/CuCoP/CW,53 graphene/Co(OH)2/Ni,27 Co–Ni/rGO,28 αCo(OH)2/rGO,60 Co(OH)2,61 Co(OH)2/rGO,62 and CuO@CoFe LDH.63 The remarkable performance of the CN-LSG MSC is due to the faster charge transfer kinetics achieved due to the ultrathin Co(OH)2 NS and superior conductivity provided by the LSG support. This is further supported by a low charge transfer resistance (Rct) of 12.2 Ω in the Nyquist plot (Fig. S9†). Besides the excellent capacitive performance, the CN-LSG MSC also showed remarkable long-term cyclic stability. As shown in Fig. 4f, the CN-LSG MSC exhibited 96.4% retention of its initial capacitance even after 20
000 continuous GCD cycles at a current density of 22 A cm−3. The coulombic efficiency was higher than 99% regardless of long-term stability suggesting stable operation of the CN-LSG MSC. Notably, the shape of the GCD curve remained unchanged for nearly 20
000 cycles (inset of Fig. 4f). The self-discharge performance of the CN-LSG MSC was studied as shown in Fig. S10.† The CN-LSG MSC could retain 50% of its initial voltage even after 225 s making it suitable for miniaturized devices that desire a 10–20 s power supply. These results evidence that the overall performance of the CN-LSG MSC is higher than that of recently reported MSCs as shown in Table S2.†
Furthermore, the fabricated CN-LSG MSC device showed outstanding mechanical flexibility. Fig. 5b depicts the well-maintained CV curves of the CN-LSG MSC at bending angles of 0°, 30°, 60°, 90°, 120°, 150°, and 180° as shown in Fig. 5a. The initial capacitance of the CN-LSG MSC is the least affected regardless of bending deformation (Fig. 5b), indicating the mechanical robustness of the CN-LSG MSC device and good adherence of the Co(OH)2 NS on micropatterned LSG. The outstanding performance of the CN-LSG MSC can be elucidated by the combined effects of the ultrathin thickness and in-plane arrangement of the Co(OH)2 NS on a highly conducting current collector, i.e., graphene. Since the practical applications need high energy and power density, the scalable integration capabilities of the CN-LSG MSC devices are systematically investigated in both series and parallel configurations. In the parallel configuration of 3 devices, the output current response and discharge time are noted to be increased three-fold compared to that of a single MSC device, which is attested to the CN-LSG MSC device's good scalability for use in practical scenarios. To comprehensively explain the exceptional performance of solid-state flexible MSCs, the ultrathin Co(OH)2 NS contributes a rapid ion transport pathway and extensive ionic accommodations. The 2D morphology of the Co(OH)2 NS and LSG provides additional flexibility to the MSC. The interdigitated microelectrodes in the CN-LSG MSC enhance the accessible electrochemical surface area of the Co(OH)2 NS providing a superior capacity for charge storage. The in-plane configuration shortens the diffusion pathway, facilitating electron transport. Moreover, the interaction of the Co(OH)2 NS with LSG offers strong adhesion and, subsequently well-maintained stability for the CN-LSG MSC. This simplified and fast fabrication process of flexible and solid-state MSCs can significantly avoid complex and expensive fabrication methods such as multiple-step lithographic fabrication, usage of photoresists, and plasma etching and successfully upturn massive production. Most importantly, the binder-free and conductive additive-free fabrication process of the CN-LSG MSC effectively boosts volumetric performance without sacrificing its mechanical flexibility.
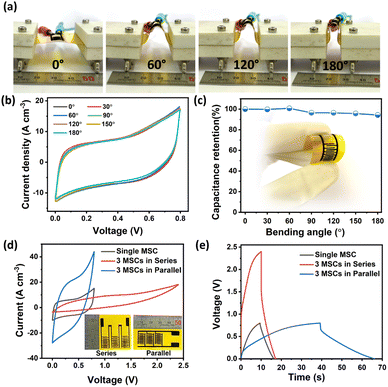 |
| Fig. 5 Flexibility and scalability study of the CN-LSG MSC. (a) Digital photographs of the fabricated CN-LSG MSC device under different bending angles. (b) CV curves at different bending angles from 0 to 180° at a scan rate of 100 mV s−1, (c) capacitance retention under various bending deformations, and (d) CV curves (at 100 mV s−1) of a single MSC and three MSCs connected in series and parallel. The inset shows the digital photographs, and (e) GCD (at 22 A cm−3) of a single MSC and three MSCs connected in series and parallel configurations. | |
4 Conclusions
In conclusion, we developed a simple and scalable strategy to fabricate a solid-state micro-supercapacitor using ultrathin and large area Co(OH)2 NS on LSG. The CN-LSG MSC delivered outstanding volumetric capacitance (258 F cm−3 at 13 A cm−3), and a long-term cyclic stability of 96.4% even after 20
000 GCD cycles. Moreover, the CN-LSG MSC exhibited high energy density (22 mW h cm−3) and power density (6.8 W cm−3), which is superior to that of recently reported cobalt-based MSCs. The CN-LSG MSC showed excellent mechanical flexibility under bending deformations. Moreover, the scalability of the CN-LSG MSC device to meet practical applications was investigated by using the series and parallel configurations of MSCs, which amplified the capacitance value and operating voltage. From a practical standpoint, this novel approach will provide a new avenue for the simple and rational fabrication of advanced high-performance flexible electronics with a wide range of transition metal-based ultrathin films.
Author contributions
PBJ: methodology, experimental work and analysis, investigation, microscopic and electrochemical data acquisition and analysis, draft writing to final version. SAP: help in electrochemical studies. MP: assistance in laser scribing and its analysis. PB: assistance in electrochemistry measurements. AS and S R: XPS, HRTEM characterization, and help in analysis. AKS and CSR: draft proofing, and discussion. PBJ and MS: designed the experiments. MS: conceptualization, supervision, funding acquisition, data analysis, project administration.
Conflicts of interest
There are no conflicts to declare.
Acknowledgements
P. B. J. acknowledges the Chhatrapati Shahu Maharaj Research Training and Human Development Institute, Pune, for financial support (CSMNRF-2021/2021-22/896). MS is grateful to SERB, New Delhi, India, for funding to conduct the research (EMR/2017/003368). The CNRS, the Chevreul Institute (FR 2638), the Ministère de l'EnseignementSupérieur et de la Recherche, the Région Hauts-de-France, the FEDER, and the MEL are acknowledged for supporting this work. Thanks also go to Pardis Simon for XPS facilities and Maya Marinova for TEM facilities.
Notes and references
- D. P. Dubal, N. R. Chodankar, D.-H. Kim and P. Gomez-Romero, Chem. Soc. Rev., 2018, 47, 2065–2129 RSC.
- N. Liu and Y. Gao, Small, 2017, 13, 1701989 CrossRef PubMed.
- K. Fu, Y. Wang, C. Yan, Y. Yao, Y. Chen, J. Dai, S. Lacey, Y. Wang, J. Wan, T. Li, Z. Wang, Y. Xu and L. Hu, Adv. Mater., 2016, 28, 2587–2594 CrossRef CAS PubMed.
- S. Zheng, Z.-S. Wu, F. Zhou, X. Wang, J. Ma, C. Liu, Y.-B. He and X. Bao, Nano Energy, 2018, 51, 613–620 CrossRef CAS.
- H. Zhou, G. Zhu, S. Dong, P. Liu, Y. Lu, Z. Zhou, S. Cao, Y. Zhang and H. Pang, Adv. Mater., 2023, 35, 2211523 CrossRef CAS PubMed.
- D. Qi, Y. Liu, Z. Liu, L. Zhang and X. Chen, Adv. Mater., 2017, 29, 1602802 CrossRef PubMed.
- N. A. Kyeremateng, T. Brousse and D. Pech, Nat. Nanotechnol., 2017, 12, 7–15 CrossRef CAS PubMed.
- K.-H. Lee, S.-S. Lee, D. B. Ahn, J. Lee, D. Byun and S.-Y. Lee, Sci. Adv., 2020, 6, eaaz1692 CrossRef PubMed.
- Z. S. Wu, K. Parvez, X. Feng and K. Müllen, Nat. Commun., 2013, 4, 2487 CrossRef PubMed.
- A. Velasco, Y. K. Ryu, A. Boscá, A. Ladrón-de-Guevara, E. Hunt, J. Zuo, J. Pedrós, F. Calle and J. Martinez, Sustain. Energy Fuels, 2021, 5, 1235–1254 RSC.
- L. Zhang, L. Liu, C. Liu, X. Li, F. Liu, W. Zhao, S. Wang, F. Wu and G. Zhang, J. Appl. Phys., 2019, 126, 164308 CrossRef.
- J. Xu, Y. He, S. Bi, M. Wang, P. Yang, D. Wu, J. Wang and F. Zhang, Angew. Chem., Int. Ed., 2019, 58, 12065–12069 CrossRef CAS PubMed.
- Y. Bräuniger, S. Lochmann, J. Grothe, M. Hantusch and S. Kaskel, ACS Appl. Energy Mater., 2021, 4, 1560–1567 CrossRef.
- X. Li, H. Li, X. Fan, X. Shi and J. Liang, Adv. Energy Mater., 2020, 10, 1903794 CrossRef CAS.
- C. Huang, L. Kang, N. Zhang, S. Wan, X. Zhou and J. Zhang, ACS Appl. Mater. Interfaces, 2019, 11, 38303–38312 CrossRef CAS PubMed.
- X. Li, Y. Ma, Y. Yue, G. Li, C. Zhang, M. Cao, Y. Xiong, J. Zou, Y. Zhou and Y. Gao, Chem. Eng. J., 2022, 428, 130965 CrossRef CAS.
- H. Park, C. Song, S. W. Jin, H. Lee, K. Keum, Y. H. Lee, G. Lee, Y. R. Jeong and J. S. Ha, Nano Energy, 2021, 83, 105837 CrossRef CAS.
- J. Lin, Z. Peng, Y. Liu, F. Ruiz-Zepeda, R. Ye, E. L. G. Samuel, M. J. Yacaman, B. I. Yakobson and J. M. Tour, Nat. Commun., 2014, 5, 5714 CrossRef CAS PubMed.
- X.-Y. Fu, Z.-D. Chen, Y.-L. Zhang, D.-D. Han, J.-N. Ma, W. Wang, Z.-R. Zhang, H. Xia and H.-B. Sun, Nanoscale, 2019, 11, 9133–9140 RSC.
- R. Wang, S. Luo, C. Xiao, Z. Chen, H. Li, M. Asif, V. Chan, K. Liao and Y. Sun, Electrochim. Acta, 2021, 386, 138420 CrossRef CAS.
- M. Kim, M. G. Gu, H. Jeong, E. Song, J. W. Jeon, K.-M. Huh, P. Kang, S.-K. Kim and B. G. Kim, ACS Appl. Energy Mater., 2021, 4, 208–214 CrossRef CAS.
- Y. Rao, M. Yuan, F. Luo, H. Li, J. Yu and X. Chen, J. Colloid Interface Sci., 2022, 610, 775–784 CrossRef CAS PubMed.
- W. Yan, H. Hu, L. Wang and D. Ho, Small Methods, 2022, 6, 2101616 CrossRef CAS PubMed.
- P. Bhol, P. B. Jagdale, A. H. Jadhav, M. Saxena and A. K. Samal, ChemSusChem, 2023, e202301009 Search PubMed.
- L. Li, J. Zhang, Z. Peng, Y. Li, C. Gao, Y. Ji, R. Ye, N. D. Kim, Q. Zhong, Y. Yang, H. Fei, G. Ruan and J. M. Tour, Adv. Mater., 2016, 28, 838–845 CrossRef CAS PubMed.
- G. K. Maron, M. G. Masteghin, V. Gehrke, L. S. Rodrigues, J. H. Alano, J. H. H. Rossato, V. R. Mastelaro, J. Dupont, M. T. Escote, S. R. P. Silva and N. L. V. Carreno, Carbon, 2023, 168, 112490 CAS.
- Z. Zhang, Q. Xia, Y. Chen, X. Pan, E. Pameté, Y. Zhang, V. Presser, Q. Abbas and X. Chen, Electrochim. Acta, 2022, 433, 141247 CrossRef CAS.
- J. Jung, J. R. Jeong, C. Dang Van, K. Kang and M. H. Lee, ACS Appl. Electron. Mater., 2022, 4, 4840–4848 CrossRef CAS.
- N. Li, X. Guo, X. Tang, Y. Xing and H. Pang, Chin. Chem. Lett., 2021, 33, 462–465 CrossRef.
- Y. Gogotsi and R. M. Penner, ACS Nano, 2018, 12, 2081–2083 CrossRef CAS PubMed.
- T. Deng, W. Zhang, O. Arcelus, J.-G. Kim, J. Carrasco, S. J. Yoo, W. Zheng, J. Wang, H. Tian, H. Zhang, X. Cui and T. Rojo, Nat. Commun., 2017, 8, 15194 CrossRef CAS PubMed.
- N. R. Chodankar, H. D. Pham, A. K. Nanjundan, J. F. S. Fernando, K. Jayaramulu, D. Golberg, Y.-K. Han and D. P. Dubal, Small, 2020, 16, 2002806 CrossRef CAS PubMed.
- J. Yang, Z. Pan, Q. Yu, Q. Zhang, X. Ding, X. Shi, Y. Qiu, K. Zhang, J. Wang and Y. Zhang, ACS Appl. Mater. Interfaces, 2019, 11, 5938–5946 CrossRef CAS PubMed.
- F. Zhao, W. Liu, T. Qiu, W.-B. Gong, W. Ma, Q. Li, F. Li and F. Geng, ACS Nano, 2020, 14, 603–610 CrossRef CAS PubMed.
- P. Zhang, F. Wang, M. Yu, X. Zhuang and X. Feng, Chem. Soc. Rev., 2018, 47, 7426–7451 RSC.
- Y. Zheng, S. Zheng, Y. Xu, H. Xue, C. Liu and H. Pang, Chem. Eng. J., 2019, 373, 1319–1328 CrossRef CAS.
- H. Zhou, S. Zheng, X. Guo, Y. Gao, H. Li and H. Pang, J. Colloid Interface Sci., 2022, 628, 24–32 CrossRef CAS PubMed.
- M. Yuan, F. Luo, Z. Wang, H. Li, Y. Rao, J. Yu, Y. Wang, D. Xie, X. Chen and C.-P. Wong, ACS Appl. Mater. Interfaces, 2021, 13, 22426–22437 CrossRef CAS PubMed.
- A. Bouzina, H. Perrot, O. Sel and C. Debiemme-Chouvy, Appl. Nano Mater., 2021, 4, 4964–4973 CrossRef CAS.
- B. Anasori, M. R. Lukatskaya and Y. Gogotsi, Nat. Rev. Mater., 2017, 2, 16098 CrossRef CAS.
- H. Huang, H. Su, H. Zhang, L. Xu, X. Chu, C. Hu, H. Liu, N. Chen, F. Liu, W. Deng, B. Gu, H. Zhang and W. Yang, Adv. Electron. Mater., 2018, 4, 1800179 CrossRef.
- L. Fan, P. Wen, X. Zhao, J. Zou and F. Kim, Appl. Nano Mater., 2022, 5, 4170–4179 CrossRef CAS.
- S. Gao, Y. Sun, F. Lei, L. Liang, J. Liu, W. Bi, B. Pan and Y. Xie, Angew. Chem., Int. Ed., 2014, 53, 12789–12793 CrossRef CAS PubMed.
- C. Nethravathi, C. R. Rajamathi, M. Rajamathi, X. Wang, U. K. Gautam, D. Golberg and Y. Bando, ACS Nano, 2014, 8, 2755–2765 CrossRef CAS PubMed.
- L. Yang, S. Cheng, Y. Ding, X. Zhu, Z. L. Wang and M. Liu, Nano Lett., 2012, 12, 321–325 CrossRef CAS PubMed.
- L. Trotochaud, J. K. Ranney, K. N. Williams and S. W. Boettcher, J. Am. Chem. Soc., 2012, 134, 17253–17261 CrossRef CAS PubMed.
- P. Tian, Y. Yu, X. Yin and X. Wang, Nanoscale, 2018, 10, 5054–5059 RSC.
- F. Wang, J.-H. Seo, G. Luo, M. B. Starr, Z. Li, D. Geng, X. Yin, S. Wang, D. G. Fraser, D. Morgan, Z. Ma and X. Wang, Nat. Commun., 2016, 7, 10444 CrossRef CAS PubMed.
-
A. I. Vogel, Macro and Semimicro Qualitative Inorganic Analysis, 1953 Search PubMed.
- Z. Liu, R. Ma, M. Osada, K. Takada and T. Sasaki, J. Am. Chem. Soc., 2005, 127, 13869–13874 CrossRef CAS PubMed.
- M. C. Biesinger, L. W. M. Lau, A. R. Gerson and R. S. C. Smart, Appl. Surf. Sci., 2010, 257, 887–898 CrossRef CAS.
- P. Chang, H. Mei, Y. Tan, Y. Zhao, W. Huang and L. Cheng, J. Mater. Chem. A, 2020, 8, 13646–13658 RSC.
- L. Naderi and S. Shahrokhian, J. Chem. Eng., 2023, 476, 146764 CrossRef CAS.
- M. Pathak, P. Mane, B. Chakraborty, J. S. Cho, S. M. Jeong and C. S. Rout, Small, 2024, 2310120 CrossRef PubMed.
- A.-K. Lu, H.-Y. Li and Y. Yu, J. Mater. Chem., 2019, 7, 7852–7858 RSC.
- J.-K. Chih, A. Jamaluddin, F. Chen, J.-K. Chang and C.-Y. Su, J. Mater. Chem., 2019, 7, 12779–12789 RSC.
- H. Li, P. Tang, H. Shen, T. Hu, J. Chen, K. Chen, F. Qi, H. Yang, L. Wen and F. Li, Carbon, 2021, 183, 840–849 CrossRef CAS.
- J. Qin, J. Gao, X. Shi, J. Chang, Y. Dong, S. Zheng, X. Wang, L. Feng and Z.-S. Wu, Adv. Funct. Mater., 2020, 30, 1909756 CrossRef CAS.
- Y. Zhao, J. Zheng, J. Yang, W. Liu, F. Qiao, J. Lian, G. Li, T. Wang, J. Zhang and L. Wu, Nano Res., 2023, 16, 555–563 CrossRef CAS.
- Y. Rong, Y. Chen, J. Zheng, Y. Zhao and Q. Li, J. Colloid Interface Sci., 2021, 598, 1–13 CrossRef CAS PubMed.
- S. Wang, Z.-S. Wu, F. Zhou, X. Shi, S. Zheng, J. Qin, H. Xiao, C. Sun and X. Bao, npj 2D Mater. Appl., 2018, 2, 7 CrossRef.
- N. Kurra, Q. Jiang and H. N. Alshareef, Nano Energy, 2015, 16, 1–9 CrossRef CAS.
- Z. Li, M. Shao, L. Zhou, R. Zhang, C. Zhang, J. Han, M. Wei, D. G. Evans and X. Duan, Nano Energy, 2016, 20, 294–304 CrossRef CAS.
|
This journal is © The Royal Society of Chemistry 2024 |
Click here to see how this site uses Cookies. View our privacy policy here.