DOI:
10.1039/D4TA05343E
(Paper)
J. Mater. Chem. A, 2024,
12, 25887-25895
Boosted Li2CO3 reversible conversion utilizing Cu-doped TiB MBene/graphene for Li–CO2 batteries†
Received
31st July 2024
, Accepted 2nd September 2024
First published on 2nd September 2024
Abstract
Two-dimensional transition metal borides (MBenes), particularly TiB, hold promise as electrocatalysts for CO2-related reactions. However, their bifunctional catalytic performance for reversible Li2CO3 conversion in Li–CO2 batteries remains inferior to that of Ru-based catalysts. We addressed this issue by introducing tensile strain and doping late transition metal atoms (Mn, Fe, Co, Ni, Cu) into the basal plane of a TiB MBene/graphene heterostructure. Spin-polarized density functional theory (DFT) calculations revealed that the Cu-doped TiB/graphene catalyst (Cu/Ti17B18/G) exhibits an ultralow CO2 reduction and evolution overpotential of 0.66 V, enhancing Li2CO3 nucleation and reversible conversion with carbon products. This improvement is attributed to weakened adsorption of O-containing intermediates on the Cu-doped surface, facilitated by the down-shifted d-band center and increased antibonding state occupancy. Consequently, Cu/Ti17B18/G emerges as a promising bifunctional electrocatalyst for Li–CO2 batteries, outperforming pristine TiB/G and other reported catalysts. Furthermore, its bifunctional activity can be further improved by applying x-direction tensile strain. Molecular dynamics simulations combined with explicit solvent models further confirmed the catalytic durability and stability of Cu/Ti17B18/G in solution. This work provides valuable atomic-scale insights for exploring advanced Li–CO2 battery catalysts.
1. Introduction
The aprotic Li–CO2 battery, owing to its high theoretical energy density of up to 1876 mA h g−1 and its CO2 neutralization capability, is one of the most promising energy storage and conversion technologies.1–3 The discharge/charge process involves a reversible Li2CO3 nucleation/decomposition reaction (i.e., CO2 reduction/evolution reaction, CO2RR/CO2ER), represented by the reaction: 4Li + 3CO2 ⇄ 2Li2CO3 + C.4–6 However, the sluggish kinetics and incomplete reactions lead to the accumulation of Li2CO3 products and the generation of reactive oxygen species, which can block active sites and diminish battery efficiency.7–10 Additionally, the inert nature of CO2 and the wide bandgap of Li2CO3 present pronounced activation energy barriers, directly limiting the reversible Li2CO3 conversion in Li–CO2 batteries.11,12 Therefore, it is desirable yet challenging to develop highly active and stable bifunctional electrocatalysts that not only drive the CO2 activation but also facilitate the Li2CO3 nucleation and reversible decomposition with carbon products.13–15
Two-dimensional (2D) orthorhombic transition metal borides (MBenes) have been widely explored as potential catalysts in diverse electrochemical reactions ascribed to their outstanding electrical conductivity and abundance of active sites.16–19 Among these, titanium boride (TiB) stands out as it has been successfully synthesized and is the lightest MBene, making it highly suitable for portable and lightweight battery applications.16,20 Notably, Mir et al. demonstrated that TiB exhibits stronger adsorption energies compared to VB, CrB, MnB, and FeB, along with excellent electrical conductivity and dynamic stability, making it highly effective for CO2 capture and activation.20,21 Our recent research further revealed the inherent catalytic activity of 2D TiB basal plane for converting CO2 into Li2CO3 and carbon products.22 This activity is facilitated by the bidirectional electron transfer between CO2 reactants and the TiB surface. Unfortunately, the bifunctional catalytic performance of TiB still lags behind that of noble metal Ru-based catalysts. A significant limitation is the excessive adsorption of Li/C/O intermediates on the TiB plane, which hampers the reversible conversion of Li2CO3.
In this study, we aim to overcome these limitations by doping late transition metals (TM = Mn, Fe, Co, Ni, Cu) into the basal plane of TiB MBene and coupling this modified structure with graphene to form a stable heterostructure. The use of late transition metals with paired d electrons can facilitate electron compensation with the empty or unpaired d orbitals of Ti atoms in the TiB plane, which is expected to balance the adsorption strength of intermediates on the catalytic surface.22 In addition, among the catalysts studied so far, Cu remains the only heterogeneous electrocatalyst for selective CO2 electroreduction to multicarbon (C2+) products.23,24 Therefore, doping with late transition metals, particularly Cu, which has fully paired d-electrons, is anticipated to reshape the electronic structure of TiB and alleviate the excessive adsorption of Li/C/O intermediates on the TiB plane. Using spin-polarized density functional theory (DFT) calculations, we first investigate the stability of late transition metals-doped TiB/graphene heterostructures (TM/Ti17B18/G, TM = Mn, Fe, Co, Ni, Cu). Subsequently, we explore the electrochemical reaction mechanisms in Li–CO2 batteries. Notably, the Cu/Ti17B18/G catalyst delivers optimal bifunctional catalytic activity for Li2CO3 nucleation and reversible conversion, achieving an ultralow overpotential of 0.66 V. Furthermore, tensile strain is applied to tailor the d-band center and enhance the bifunctional activity of the catalyst. Finally, molecular dynamics simulations are conducted to assess the catalytic durability of the Cu/Ti17B18/G heterostructure in solution. This research provides valuable insights into the atomic-level interactions and mechanisms that drive the improved Li2CO3 reversible conversion performance of Cu-doped TiB MBene/graphene electrocatalysts, paving the way for the development of advanced multifunctional catalysts for next-generation Li–CO2 batteries.
2. Computational methods and models
Utilizing the Vienna Ab initio Simulation Package (VASP),25–27 spin-polarized density functional theory (DFT) calculations were conducted to investigate the structural stability and electrocatalytic properties. The ALKEMIE28 and VASPKIT29 codes were implemented to postprocess the computational data. The PBE-D3 exchange–correlation30 was chosen to elucidate the interaction dynamics between reaction intermediates and catalytic active sites.31 The plane wave cut-off energy was set at 500 eV. All configurations were based on a 4 × 4 supercell of graphene and 3 × 3 supercell of TiB with a vacuum slab of 25 Å inserted in the z direction to prevent interaction between two neighboring surfaces. Crystal orbital Hamilton population (COHP) analyses were performed using the LOBSTER package.32 Furthermore, the Bader charge analysis was applied to quantify the charge transfer.33,34 To capture each saddle-point structure and the associated minimum energy path during the oxidative dissociation of Li2CO3, climbing image nudged elastic band (CINEB) calculations were performed.35Ab initio molecular dynamics (AIMD) simulations were conducted to assess the thermodynamic stability under reaction conditions at 300 K for a duration of 10 ps, with a time step of 2 fs.36 In this simulation, tetraethylene glycol dimethyl ether (TEGDME, CH3O(CH2CH2O)4CH3), with a density of 1.007 g cm−3 and low dielectric permittivity of 7.79,37 was utilized as the organic solvation medium.38 The radial distribution function g(r) and the coordination number39 were obtained using the VASPKIT code.
The TiB/G heterostructure consists of 18 Ti atoms, 18 B atoms, and 32 C atoms; the lattice parameters of TiB and graphene are outlined in Table S1 of (ESI).† Subsequently, a single Ti atom was removed from TiB/G to anchor a late transition metal (TM) atom, such as Mn, Fe, Co, Ni and Cu. The thermodynamic stability of TM/Ti17B18/G systems was confirmed by the negative formation energy (Ef) (Table S2†), which was calculated using the following equation:
| Ef = ETM/Ti17B18/G − ETi17B18/G − EbulkTM | (1) |
where
ETM/Ti17B18/G and
ETi17B18/G denote the energies of TM/Ti
17B
18/G composite and Ti
17B
18/G substrate, respectively, and
EbulkTM represents the total energy of the bulk metal. Additionally, the electrochemical stability of the TM/Ti
17B
18/G catalysts was evaluated using the following formula:
| Udiss = U0diss − Eb/Ne | (2) |
where
U0diss and
Ne refer to the standard electrode potential of bulk metal and the number of electrons transferred in the dissolution process, respectively. As shown in Table S3,
† the
Udiss is greater than 0 V (
vs. SHE), indicating that the considered TM/Ti
17B
18/G catalysts are electrochemically stable. The
Eb represents the binding energy obtained from the following equation:
| Eb = ETM/Ti17B18/G − ETi17B18/G − EisolatedTM | (3) |
where
EisolatedTM is the energy of an isolated transition metal. A more negative
Eb value denotes stronger adsorption of the metal atom on the defective TiB/G substrate. In addition, the stress–strain and energy–strain methodologies were employed to investigate the mechanical properties.
40–43 When a uniaxial stress was imposed in the
x or
y directions, the strain was defined as:
| 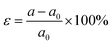 | (4) |
here,
a and
a0 signify the lattice constants of the strained and unstrained systems.
To monitor the reaction process on different catalysts, the Gibbs free energies of Li–CO2 reaction intermediates were calculated using eqn (5).44 Particularly, in the Li–CO2 batteries, Li+ + e− ⇄ Li is in equilibrium with bulk Li at 0 V.
| ΔG = ΔEDFT + ΔEZPE − TΔS + neU | (5) |
where Δ
EDFT, Δ
EZPE and Δ
S are the DFT total energy difference, zero-point energy change, and entropy change at
T = 298.15 K, respectively, which are given in Tables S4–S6.
† The term
U stands for the applied electrode potential, and
n represents the number of transferred electrons. For the Li–CO
2 battery, the discharge potential (
UDC) during CO
2RR and charge potential (
UC) during CO
2ER correspond to the minimum/maximum potentials required to sustain the redox processes. The deviation between the discharge/charge potential and theoretical equilibrium potential (
Ueq = 2.87 V) signifies the CO
2RR/CO
2ER overpotentials,
i.e.,
ηCO2RR =
Ueq −
UDC and
ηCO2ER =
UC −
Ueq. Herein, we applied the total overpotentials for CO
2RR and CO
2ER (
ηtot =
ηCO2RR +
ηCO2ER) as a quantitative metric to assess the bifunctional activity of targeted catalysts for Li–CO
2 redox.
3. Results and discussion
3.1. Insight into TiB MBene material design
Fig. 1a presents the material design idea of late transition metal Cu doped TiB MBene/graphene heterostructure to alleviate the adsorption strength of Li/C/O intermediates. Taking advantage of the unique electronic configuration of late transition metals, Cu dopant is expected to serve as a d-electron buffer. Moreover, the maximum lattice mismatch between TiB with 3 × 3 supercell and graphene with
supercell was found to be 4.18%, demonstrating they are good counterparts for establishing high-quality heterostructures. The negative formation energy in Fig. 1b signifies the thermodynamical stability of transition metals Mn, Fe, Co, Ni, Cu doped TiB/graphene heterostructures (TM/Ti17B18/G). As demonstrated by Jang et al.,45 sp2 hybridized graphene can capture electrons from the metal layer, resulting in strong interface coupling that stabilizes the metal catalyst and modifies its electronic properties. Indeed, there are abundant electrons localized at the Cu/Ti17B18/G heterointerface, and graphene capture 3.46 electrons from the Cu/Ti17B18 layer (Fig. S1†), suggesting a strong coupling between them. The Cu dopant exhibits a lower d-band center (εd) of −2.78 eV in comparison with pristine TiB/G (εd = −2.55 eV). According to the d-band center theory,46–48 the down-shifted εd signifies a weakened binding capability of the active site for reaction intermediates. Therefore, a lower d-band center in Cu/Ti17B18/G holds promise for alleviating the intense intermediate adsorption issue on the pristine TiB surface. Next, we will confirm this idea using the spin-polarized DFT calculations and constant potential solvation models in ESI.†
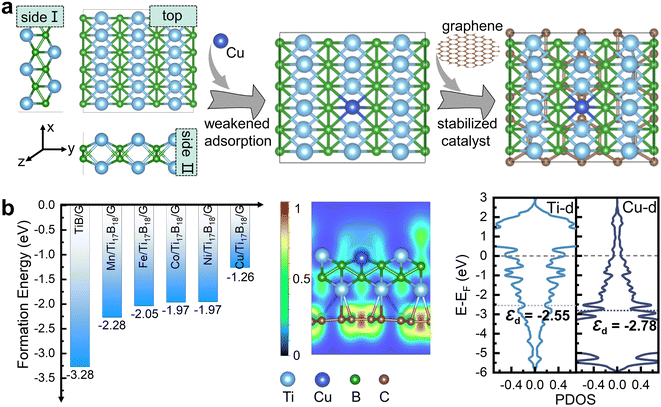 |
| Fig. 1 (a) Schematic of the TiB MBene/graphene heterostructure design. (b) Formation energy of late transition metal atoms (Mn, Fe, Co, Ni, Cu) doped TiB/G heterostructure and electronic properties of Cu/Ti17B18/G. | |
3.2. Reaction mechanism and electrocatalytic performance
Promising bifunctional catalysts should strike a balance between the CO2 reduction and evolution, i.e., Li2CO3 generation and its reversible dissociation. Fig. S2† lists several possible pathways for CO2 reduction to Li2C2O4 and Li2CO3 during the initial 2e− step of the discharging process. Prior studies have shown that the nucleation selectivity of Li2CO3 and Li2C2O4 is dependent on the applied catalysts.5,49 For each reaction intermediate, distinct adsorption configurations are taken into account in Fig. S3† and the energetically optimal one is displayed in Fig. 2a. Worth noting that the *Li2C2O4 nucleation is not as stable as that of *Li2CO3 on both TiB/G and Cu/Ti17B18/G surfaces, which is prone to decompose into *Li2CO3 and *CO, regardless of the specific CO2 reduction pathway. This disproportionation splitting is energetically favorable, with an exothermic free energy change of −1.25 eV on TiB/G surface and −2.21 eV on Cu/Ti17B18/G surface. Thus, *Li2CO3 is identified as the final discharge product for TiB/G and Cu/Ti17B18/G use in Li–CO2 batteries, analogue to Ru(0001) catalyst.50 Generally, a catalyst with Li2CO3 nucleation selectivity is promising for achieving efficient four-electron (4e−) CO2 reduction (4Li+ + 3CO2 + 4e− → 2Li2CO3 + C) in Li–CO2 batteries.51,52
 |
| Fig. 2 (a) Nucleation selectivity of *Li2C2O4 and *Li2CO3 on pristine and Cu-doped TiB/G catalysts. (b) Self-decomposition of Li2CO3 to evolve O2. (c) The co-decomposition of Li2CO3 and carbon to regenerate original reactants, where the rate-determining step is highlighted. | |
For the reverse CO2 evolution process, the dissociation of Li2CO3 and the participation of amorphous carbon products play a decisive role in the cycling stability of Li–CO2 batteries.53 If amorphous carbon is not involved in the Li2CO3 decomposition, aggressive oxygen species will be generated and accumulated, passivating the electrocatalysts.54 As depicted in Fig. S4,† Cu/Ti17B18/G exhibits a much lower energy barrier (1.09 eV) for Li2CO3 decomposition, in comparison with that of graphene-based single-atom catalyst Cr@G (1.67 eV), single-layer MoS2 (2.63 eV), and ReS2 (2.36 eV) catalysts.55,56 The free energy changes associated with the self-decomposition of Li2CO3 or its co-oxidative dissociation with carbon products are graphically illustrated in Fig. 2b and c. Evidently, when carbon products engage in the Li2CO3 decomposition through the oxidative reaction 2Li2CO3 + C → 4Li+ + 3CO2 + 4e−, the Cu/Ti17B18/G catalyst presents the lowest rate-determining step (RDS) energy barrier of 2.74 eV. These findings indicate that the Cu/Ti17B18/G catalyst possesses the dual capability of facilitating the selective Li2CO3 nucleation and efficiently promoting its reversible dissociation to original reactants, meriting further exploration.
Therefore, to assess the bifunctional CO2RR/CO2ER activity of TiB/G and Cu/Ti17B18/G in Li–CO2 batteries, a continuous four-electron transfer mechanism is adopted in Fig. 3a. During the initial 2e− step of the discharge process, CO2 and Li+ are co-adsorbed on the catalyst surface to yield *LiCO2 intermediate, which then reacts with additional Li+ and CO2 to form the first Li2CO3 product and *CO intermediate. In the subsequent 2e− step, the *CO further reacts with two Li+ and one CO2 molecule to produce the second Li2CO3 and amorphous C.13 As seen in Fig. S5,† the CO2RR/CO2ER overpotential of TiB/G reaches 2.43 V. During discharging, the potential-determining step (PDS) corresponds to the third electron transfer step (i.e., the formation of carbon products), while the PDS during charging is the Li2CO3 decomposition on TiB/G surface. Notably, the introduction of Cu into the TiB/G plane effectively balances the adsorption and desorption of LixCyOz (x = 0–2, y = 1–2, z = 1–3) reaction intermediates, leading to a shift in the PDS from the latter 2e− transfer step to the initial 2e− steps. Of greater interest is that the Cu/Ti17B18/G catalyst delivers a dramatically decreased CO2RR/CO2ER overpotential as low as 0.66 V (Fig. 3b). Fig. 3c summarizes the overpotentials of other excellent Li–CO2 battery electrode catalysts. This performance surpasses that of pristine TiB/G and previously reported carbon nanotubes (1.94 V), graphene (1.56 V),57,58 noble metal Ru (1.07 V)50 and single-atom modified MXenes like Zn/Mo2CO2 (0.97 V).13 Besides, Fig. S6† depicts their Gibbs free energy for Li–CO2 electrochemistry via a continuous 4e− transfer pathway for other late transition metal modified TiB/G catalysts such as Mn, Fe, Co, and Ni. Remarkably, compared to pristine TiB/G (ηtot = 2.43 V), the obtained Mn/Ti17B18/G, Fe/Ti17B18/G, Co/Ti17B18/G, and Ni/Ti17B18/G catalysts exhibit dramatically narrowed CO2RR/CO2ER overpotential as low as 0.92, 0.75, 0.99 and 0.84 V. This validates that doping engineering can be used as a guideline for the rational design of bifunctional electrocatalysts aimed at achieving reversible CO2 and Li2CO3 conversion in Li–CO2 batteries.
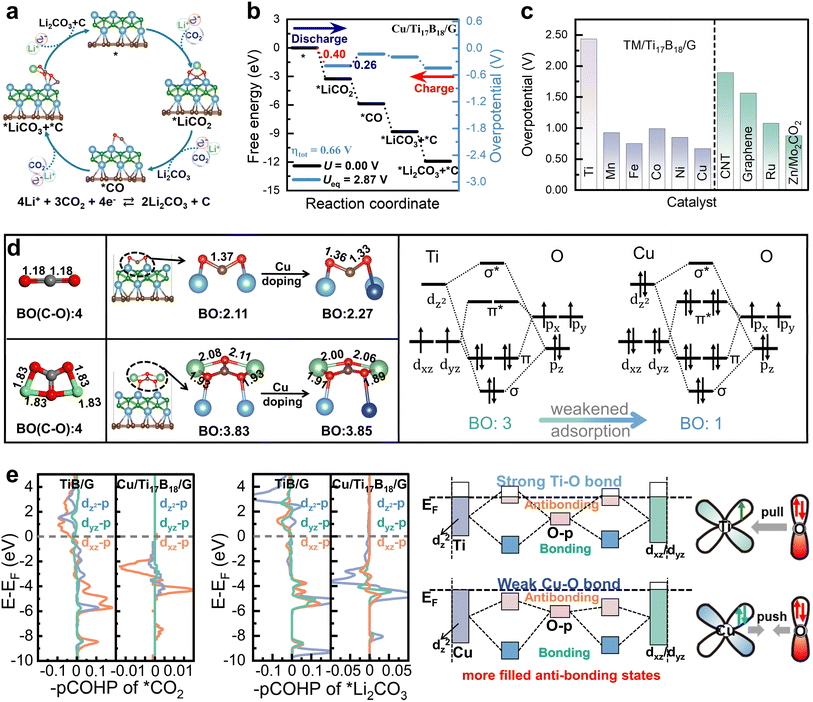 |
| Fig. 3 (a) Continuous four-electron transfer pathway. (b) Free energy diagrams for Cu/Ti17B18/G, where blue and red numbers represent CO2RR overpotential (ηCO2RR) during discharge and CO2ER overpotential (ηCO2ER) during charge, respectively, and ηtot represents the total overpotential. (c) Comparation of total overpotential with available references. (d) Cu as a dopant reducing bond order (BO) in CO2 and Li2CO3 adsorbates. (e) Evolutions of bonding and antibonding states in p–d orbital interactions, where the spin-up and spin-down channels are identical in the projected crystal orbital Hamilton population (pCOHP) due to the zero magnetic moment of the system. | |
Given the pivotal role of CO2 and Li2CO3 as reactants and products in Li–CO2 batteries, we further explored the intricate relationship between p- and d-electron interactions and bifunctional activity at the atomic orbital level by focusing on their adsorption on TiB/G and Cu/Ti17B18/G surfaces. A striking similarity emerges: CO2 and Li2CO3 are adsorbed via O p orbitals interacting with Ti or Cu d orbitals. As seen in Fig. S7,† there are three possible modes of p–d orbital interactions based on the principle of maximum overlap.59 Specifically, the metal dz2 orbitals hybridize with the O pz orbitals to form σ bonds, whereas the dxz/dyz orbitals hybridize with px/py to form π bonds (Fig. 3d).60 It is seen that the dz2, dxz and dyz electrons of Ti are occupied near the Fermi level (Fig. S8†), triggering the donation of d-electrons to the empty CO2 antibonding orbitals, yielding robust Ti–O bonding and excessive intermediate adsorption on the TiB/G plane. In sharp contrast, Cu d electrons are almost concentrated below the Fermi level (Fig. S9†) with a lower d-band center than Ti, yielding weakened interactions with O-containing intermediates. Further analysis of the projected crystal orbital Hamilton population (pCOHP) in Fig. 3e reveals that the orbital interactions between Cu d orbitals and O p orbitals induce more filled antibonding states below the Fermi level, indicating a weakened Cu–O bonding. Analogous trends are observed in the case of Li2CO3 adsorption. The reduced d-band center and increased antibonding state occupancy highlight the role of Cu dopants in mitigating the strong LixCyOz adsorption on TiB/G. Therefore, the Cu/Ti17B18/G catalyst achieves enhanced bifunctional activity for the CO2 reduction to Li2CO3 and its reversible conversion with carbon products.
3.3. Strain effects
We continue investigated the bifunctional catalytic performance of TiB/G and Cu/Ti17B18/G for Li2CO3 reversible conversion under uniaxial strain with a magnitude from −4% to +4%. The uniaxial stress–strain curves in Fig. S10a† illustrate that these TiB/G and Cu/Ti17B18/G materials can endure ultimate tensile strains of up to 22% and 26% along the x-direction, respectively, while withstanding up to 22% along the y-direction, delivering superior mechanical flexibility comparable to graphene. Furthermore, the differences in Young's modulus between the x- and y-directions (Fig. S10b†) highlight the anisotropic mechanical properties of TiB/G and Cu/Ti17B18/G.
Unlike transition metal doping, which significantly alters the PDS, applying uniaxial strain in the x-direction hardly changes the PDS for a given catalyst. As shown in Fig. S11 and S12,† the PDS during the discharge–charge process for TiB/G is almost maintained at the latter 2e− transfer step under x-direction strain ranging from −4% to +4%, while the PDS for Cu/Ti17B18/G remains at the initial 2e− transfer step. This indicates that the primary effect of x-direction strain is to lower the energy barrier of the PDS, rather than altering the PDS itself. This explains why the increase of d-band center under x-direction strain, which signifies stronger interactions with reaction intermediates,61 results in a decrease in overpotential of the catalyst (Fig. 4a). Consequently, the overpotential for TiB/G decreases from 2.00 V to 1.83 V as strain varies from −4% to +4%, and for Cu/Ti17B18/G, it decreases from 0.72 V to 0.45 V. Similar enhancement of catalytic activity by strain engineering has been observed in other studies.62,63
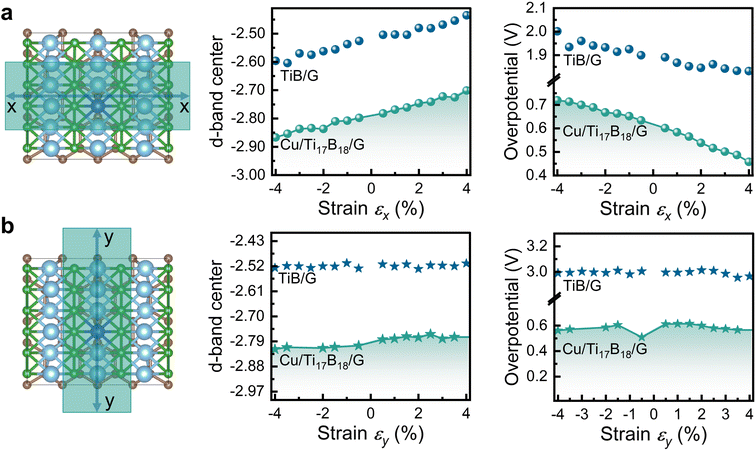 |
| Fig. 4 The d-band centers (εd) shifts and overpotentials of TiB/G and Cu/Ti17B18/G under (a) x-direction and (b) y-direction strains with a magnitude from −4% to +4%. | |
In contrast, y-direction strain induces minimal changes in the d-band center, leading to a less significant impact on overpotential, as shown in Fig. 4b. The different strain effects in the x- and y-directions on overpotentials are due to the anisotropic mechanical properties of TiB/G and Cu/Ti17B18/G. As shown in Table S7† for TiB/G, the Young's modulus in the y-direction (562.5 N m−1) is approximately 1.3 times higher than in the x-direction (431.6 N m−1), which is much higher than that of isotropic materials like graphene (342 N m−1) and MoS2 (130 N m−1).64 This mechanical anisotropy, coupled with the ultrahigh Young's modulus, results in the relatively stable d-band center and overpotential for TiB/G and Cu/Ti17B18/G under external y-axial strains. Overall, direction-specific strain engineering, along with metal doping, proves to be an effective strategy for enhancing the bifunctional catalytic properties of TiB-based materials in Li–CO2 batteries.
3.4. Stability in solution
To evaluate the durability of catalysts in an organic solvation medium, we assessed the thermal stability of TiB/G in a TEGDME solution at 300 K for 10 ps using AIMD simulations. TEGDME delivers flexible linear chain structure, low viscosity, and moderate dielectric constant (7.79) to enhance Li-ion mobility, making it an ideal solvent for Li–CO2 batteries.65,66 As shown in Fig. 5a, after 10 ps, the final TiB/G structure remained intact, with no bond breakage or structural rearrangement. Additionally, both temperature and total energy fluctuations were minimal, remaining within a narrow range (Fig. 5b). The Ti–B bond length maintained consistent at approximately 2.31 Å throughout the AIMD process (Fig. 5c). The radial distribution function g(r), presented in Fig. 5d, indicates that the TiB/G heterostructure maintained excellent crystallization post-annealing, with Ti atoms predominantly coordinated by B atoms, and an average coordination number of approximately 5.97. These findings confirm that the TiB/G catalyst structure is robustly stable in the solution. Notably, the explicit solvent model depicted in Fig. 5e demonstrates that Cu doping significantly reduces the overpotential for Li2CO3 reversible conversion to 1.09 V, compared to 4.17 V for pristine TiB/G as Li–CO2 battery catalyst.
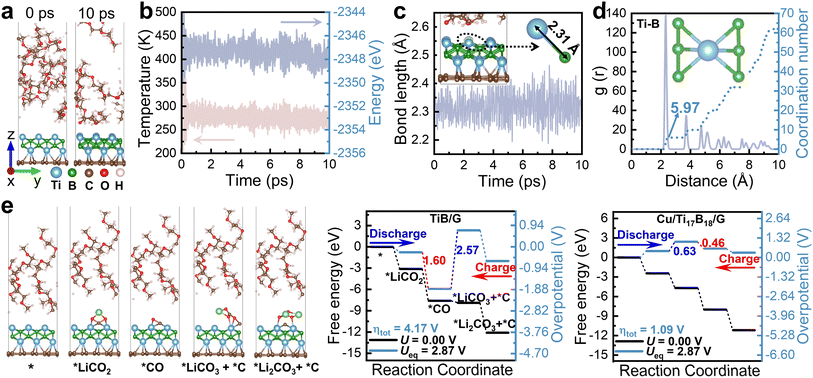 |
| Fig. 5 (a–d) Evolutions of TiB/G structure, temperature and energy, Ti–B bond length, radial distribution function g(r) and coordination number during AIMD simulations at 300 K. (e) Optimized intermediates and free energy diagrams under the explicit TEGDME solvent environment. | |
The potential influence of other solvents, such as ethylene carbonate (EC) also examined. EC has a rigid cyclic structure, a high dielectric constant (approximately 90), and higher viscosity compared to TEGDME, which leads to strong interactions with lithium ions.67 As shown in Fig. S13,† the AIMD results demonstrate that due to the presence of a carbon–oxygen ring with an ester linkage in EC molecules, EC strongly interacts with TiB/G over time, making EC unsuitable as a solvent for TiB-based catalysts in Li–CO2 batteries. To provide a more solid reference to the experiments, the constant potential implicit solvent model68,69 is employed to investigate the catalytic selectivity and bifunctional activity of both pristine and Cu-doped TiB/G catalysts (see ESI†).
4. Conclusions
In summary, we uncovered the origins of the enhanced activity of Cu-doped TiB MBene/graphene heterostructure in Li–CO2 electrochemistry. By incorporating late transition metals with paired d electrons into the TiB/G structure, we achieved significantly improved bifunctional activity for the reversible conversion of Li2CO3. Specifically, the Cu/Ti17B18/G catalyst demonstrated an ultralow overpotential of 0.66 V for both CO2 reduction and evolution reactions. This enhancement is attributed to the down-shifted d-band center and increased antibonding state occupancy in the dz2–pz, dxz–px and dyz–py orbital hybridizations, which mitigates excessive intermediate adsorption on the TiB plane. Remarkably, applying tensile strain along the x-direction to the catalyst not only elevates its d-band center but also lowers the CO2RR/CO2ER overpotential, further boosting the bifunctional activity of Cu/Ti17B18/G for Li2CO3 conversion. Finally, AIMD simulations combined with explicit solvent models confirmed that these catalysts exhibit excellent electrochemical stability and durability in a practical solvent environment. This research highlights the critical role of tuning electronic structures through doping and strain engineering in the design of advanced catalysts, with potential applications across diverse fields.
Data availability
The data supporting this article have been included as part of the ESI.† Raw data is available by contacting the corresponding author.
Author contributions
Tingting Luo, Qiong Peng, Mengmeng Yang and Haojie Hu: conceptualization, investigation, visualization, methodology, writing – original draft. Junfei Ding, Yanli Chen and Xiu Gong: data curation, formal analysis, visualization. Jing-Liang Yang, Yunpeng Qu and Zeyou Zhou: supervision, writing – review & editing. Xiaosi Qi and Zhimei Sun: supervision, funding acquisition, resources, software. All authors contributed to the whole study.
Conflicts of interest
The authors declare no conflict of interest.
Acknowledgements
This work was financially supported by the National Natural Science Foundation of China (No. 52101010, 22005071 and 11964006), Natural Science Special (Special Post) Research Foundation of Guizhou University (No. 2020-020), Platform of Science and Technology and Talent Team Plan of Guizhou province (No. GCC[2023]007), Fok Ying Tung Education Foundation, Major Research Project of innovative Group of Guizhou province (No. 2018-013), Natural Science Foundation of Guizhou province [No. ZK 2022-044].
References
- Y. Liu, P. Shu, M. Zhang, B. Chen, Y. Song, B. Lu, R. Mao, Q. Peng, G. Zhou and H.-M. Cheng, ACS Energy Lett., 2024, 9, 2173–2181 CrossRef CAS.
- D. Wang, J. Yang, P. He and H. Zhou, Energy Environ. Sci., 2021, 14, 4107–4114 RSC.
- J. Lin, J. Ding, H. Wang, X. Yang, X. Zheng, Z. Huang, W. Song, J. Ding, X. Han and W. Hu, Adv. Mater., 2022, 34, 2200559 CrossRef CAS PubMed.
- J. Chen, X.-Y. Chen, Y. Liu, Y. Qiao, S.-Y. Guan, L. Li and S.-L. Chou, Energy Environ. Sci., 2023, 16, 792–829 RSC.
- Y. Yang, K. Guo, D. Yuan, J. Cheng and B. Wang, J. Am. Chem. Soc., 2020, 142, 6983–6990 CrossRef PubMed.
- Y. Wang, J. Zhou, C. Lin, B. Chen, Z. Guan, A. M. Ebrahim, G. Qian, C. Ye, L. Chen, Y. Ge, Q. Yun, X. Wang, X. Zhou, G. Wang, K. Li, P. Lu, Y. Ma, Y. Xiong, T. Wang, L. Zheng, S. Chu, Y. Chen, B. Wang, C.-S. Lee, Y. Liu, Q. Zhang and Z. Fan, Adv. Funct. Mater., 2022, 32, 2202737 CrossRef CAS.
- X. Zhang, Y. Wang and Y. Li, J. Phys. Chem. Lett., 2023, 14, 1604–1608 CrossRef CAS PubMed.
- X. Xiao, Z. J. Zhang and P. Tan, Proc. Natl. Acad. Sci. U. S. A., 2023, 120, e2217454120 CrossRef CAS PubMed.
- S. Chen, K. Yang, H. Zhu, J. Wang, Y. Gong, H. Li, M. Wang, W. Zhao, Y. Ji, F. Pan, S. R. P. Silva, Y. Zhao and L. Yang, Nano Energy, 2023, 117, 108872 CrossRef CAS.
- J. Zhou, T. Wang, L. Chen, L. Liao, Y. Wang, S. Xi, B. Chen, T. Lin, Q. Zhang, C. Ye, X. Zhou, Z. Guan, L. Zhai, Z. He, G. Wang, J. Wang, J. Yu, Y. Ma, P. Lu, Y. Xiong, S. Lu, Y. Chen, B. Wang, C. S. Lee, J. Cheng, L. Gu, T. Zhao and Z. Fan, Proc. Natl. Acad. Sci. U. S. A., 2022, 119, e2204666119 CrossRef CAS PubMed.
- R. Huang, Z. Zhai, X. Chen, Q. Liu, H. Yu, B. Li and S. Yin, Chem. Eng. J., 2024, 489, 151191 CrossRef CAS.
- J. Xie, Z. Zhou and Y. Wang, Adv. Funct. Mater., 2020, 30, 1908285 CrossRef CAS.
- Y. Shi, B. Wei, D. Legut, S. Du, J. S. Francisco and R. Zhang, Adv. Funct. Mater., 2022, 32, 2210218 CrossRef CAS.
- B. Lu, X. Wu, X. Xiao, B. Chen, W. Zeng, Y. Liu, Z. Lao, X.-X. Zeng, G. Zhou and J. Yang, Adv. Mater., 2024, 36, 2308889 CrossRef CAS PubMed.
- J. Zhou, X. Li, C. Yang, Y. Li, K. Guo, J. Cheng, D. Yuan, C. Song, J. Lu and B. Wang, Adv. Mater., 2019, 31, 1804439 CrossRef PubMed.
- T. Xu, Y. Wang, Z. Xiong, Y. Wang, Y. Zhou and X. Li, Nano-Micro Lett., 2023, 15, 6 CrossRef CAS PubMed.
- X. Bai, Z. Zhao and G. Lu, J. Phys. Chem. Lett., 2023, 14, 5172–5180 CrossRef CAS PubMed.
- T. Zhang, B. Zhang, Q. Peng, J. Zhou and Z. Sun, J. Mater. Chem. A, 2021, 9, 433–441 RSC.
- M. Zafari, A. S. Nissimagoudar, M. Umer, G. Lee and K. S. Kim, J. Mater. Chem. A, 2021, 9, 9203–9213 RSC.
- S. H. Mir, V. K. Yadav and J. K. Singh, ACS Appl. Mater. Interfaces, 2022, 14, 29703–29710 CrossRef CAS PubMed.
- M. Ozkan, K. A. M. Quiros, J. M. Watkins, T. M. Nelson, N. D. Singh, M. Chowdhury, T. Namboodiri, K. R. Talluri and E. Yuan, Chem, 2024, 10, 443–483 CAS.
- P. Shu, Q. Peng, T. Luo, J. Ding, X. Gong, J. Zhou, Y. Yu, X. Qi and Z. Sun, J. Mater. Chem. A, 2024, 12, 6515–6526 RSC.
- W. Guo, X. Tan, S. Jia, S. Liu, X. Song, X. Ma, L. Wu, L. Zheng, X. Sun and B. Han, CCS Chem., 2024, 6, 1231–1239 CrossRef CAS.
- Y. Yang, S. Louisia, S. Yu, J. Jin, I. Roh, C. Chen, M. V. Fonseca Guzman, J. Feijóo, P.-C. Chen, H. Wang, C. J. Pollock, X. Huang, Y.-T. Shao, C. Wang, D. A. Muller, H. D. Abruña and P. Yang, Nature, 2023, 614, 262–269 CrossRef CAS PubMed.
- G. Kresse and J. Furthmüller, Phys. Rev. B, 1996, 54, 11169 CrossRef CAS PubMed.
- J. Hafner, J. Comput. Chem., 2008, 29, 2044–2078 CrossRef CAS PubMed.
- G. Kresse, J. Non-Cryst. Solids, 1995, 192–193, 222–229 CrossRef.
- G. Wang, L.-q. Peng, K. Li, L. Zhu, J. Zhou, N. Miao and Z. Sun, Comput. Mater. Sci., 2021, 186, 110064 CrossRef CAS.
- V. Wang, N. Xu, J.-C. Liu, G. Tang and W.-T. Geng, Comput. Phys. Commun., 2021, 267, 108033 CrossRef CAS.
- S. Grimme, J. Antony, S. Ehrlich and H. Krieg, J. Chem. Phys., 2010, 132, 154104 CrossRef PubMed.
- L. Liu and H. Xiao, J. Am. Chem. Soc., 2023, 145, 14267–14275 CrossRef CAS PubMed.
- S. Steinberg and R. Dronskowski, Crystals, 2018, 8, 225 CrossRef.
- R. F. W. Bader, Chem. Rev., 1991, 91, 893–928 CrossRef CAS.
- G. Henkelman, A. Arnaldsson and H. Jónsson, Comput. Mater. Sci., 2006, 36, 354–360 CrossRef.
- G. Henkelman, B. P. Uberuaga and H. Jónsson, J. Chem. Phys., 2000, 113, 9901–9904 CrossRef CAS.
- S. Nosé, J. Chem. Phys., 1984, 81, 511–519 CrossRef.
- C. Laoire, S. Mukerjee, E. J. Plichta, M. A. Hendrickson and K. M. Abraham, J. Electrochem. Soc., 2011, 158, A302 CrossRef CAS.
- M. A. Rivas, T. P. Iglesias, S. M. Pereira and N. Banerji, J. Chem. Thermodyn., 2006, 38, 245–256 CrossRef CAS.
- J. Holoubek, H. Liu, Z. Wu, Y. Yin, X. Xing, G. Cai, S. Yu, H. Zhou, T. A. Pascal, Z. Chen and P. Liu, Nat. Energy, 2021, 6, 303–313 CrossRef CAS PubMed.
- G. N. Greaves, A. L. Greer, R. S. Lakes and T. Rouxel, Nat. Mater., 2011, 10, 823–837 CrossRef CAS PubMed.
- Y. Zhu and X. Wu, Prog. Mater. Sci., 2023, 131, 101019 CrossRef CAS.
- B. Mortazavi, M. Silani, E. V. Podryabinkin, T. Rabczuk, X. Zhuang and A. V. Shapeev, Adv. Mater., 2021, 33, 2102807 CrossRef CAS PubMed.
- Q. Peng, K. Hu, B. Sa, J. Zhou, B. Wu, X. Hou and Z. Sun, Nano Res., 2017, 10, 3136–3150 CrossRef CAS.
- Y. Luo, Z. Ma, X. Xia, J. Zhong, P. Wu and Y. Huang, ChemSusChem, 2023, 16, e202202209 CrossRef CAS PubMed.
- J. Cho, A. Medina, I. Saih, J. Il Choi, M. Drexler, W. A. Goddard Iii, F. M. Alamgir and S. S. Jang, Angew. Chem., Int. Ed., 2024, 63, e202320268 CrossRef CAS PubMed.
- P. Shu, X. Qi, Q. Peng, Y. Chen, X. Gong, Y. Zhang, F. Ouyang and Z. Sun, Mol. Catal., 2023, 539, 113036 CrossRef CAS.
- S. Jiao, X. Fu and H. Huang, Adv. Funct. Mater., 2022, 32, 2107651 CrossRef CAS.
- J. K. Nørskov, F. Abild-Pedersen, F. Studt and T. Bligaard, Proc. Natl. Acad. Sci. U. S. A., 2011, 108, 937–943 CrossRef PubMed.
- Y. Hou, J. Wang, L. Liu, Y. Liu, S. Chou, D. Shi, H. Liu, Y. Wu, W. Zhang and J. Chen, Adv. Funct. Mater., 2017, 27, 1700564 CrossRef.
- J. Hu, C. Yang and K. Guo, J. Mater. Chem. A, 2022, 10, 14028–14040 RSC.
- W. Zhao, Y. Yang, Q. Deng, Q. Dai, Z. Fang, X. Fu, W. Yan, L. Wu and Y. Zhou, Adv. Funct. Mater., 2023, 33, 2210037 CrossRef CAS.
- X. Sun, X. Mu, W. Zheng, L. Wang, S. Yang, C. Sheng, H. Pan, W. Li, C. H. Li, P. He and H. Zhou, Nat. Commun., 2023, 14, 536 CrossRef CAS PubMed.
- A. Ahmadiparidari, R. E. Warburton, L. Majidi, M. Asadi, A. Chamaani, J. R. Jokisaari, S. Rastegar, Z. Hemmat, B. Sayahpour, R. S. Assary, B. Narayanan, P. Abbasi, P. C. Redfern, A. Ngo, M. Vörös, J. Greeley, R. Klie, L. A. Curtiss and A. Salehi-Khojin, Adv. Mater., 2019, 31, 1902518 CrossRef CAS PubMed.
- Y. Liu, R. Mao, B. Chen, B. Lu, Z. Piao, Y. Song, G. Zhou and H. M. Cheng, Mater. Today, 2023, 63, 120–136 CrossRef CAS.
- Y. Liu, S. Zhao, D. Wang, B. Chen, Z. Zhang, J. Sheng, X. Zhong, X. Zou, S. P. Jiang, G. Zhou and H. M. Cheng, ACS Nano, 2022, 16, 1523–1532 CrossRef CAS PubMed.
- B. Chen, D. Wang, J. Tan, Y. Liu, M. Jiao, B. Liu, N. Zhao, X. Zou, G. Zhou and H.-M. Cheng, J. Am. Chem. Soc., 2022, 144, 3106–3116 CrossRef CAS PubMed.
- S. Li, Y. Dong, J. Zhou, Y. Liu, J. Wang, X. Gao, Y. Han, P. Qi and B. Wang, Energy Environ. Sci., 2018, 11, 1318–1325 RSC.
- Z. Zhang, Q. Zhang, Y. Chen, J. Bao, X. Zhou, Z. Xie, J. Wei and Z. Zhou, Angew. Chem., Int. Ed., 2015, 54, 6550–6553 CrossRef CAS PubMed.
- Y. Qian, Y. Liu, Y. Zhao, X. Zhang and G. Yu, EcoMat, 2020, 2, e12014 CrossRef CAS.
- Q. Jing, Z. Mei, X. Sheng, X. Zou, Q. Xu, L. Wang and H. Guo, Adv. Funct. Mater., 2024, 34, 2307002 CrossRef CAS.
- M. Gsell, P. Jakob and D. Menzel, Science, 1998, 280, 717–720 CrossRef CAS PubMed.
- Y. Yan, J. Lin, K. Huang, X. Zheng, L. Qiao, S. Liu, J. Cao, S. C. Jun, Y. Yamauchi and J. Qi, J. Am. Chem. Soc., 2023, 145, 24218–24229 CrossRef CAS PubMed.
- C. Zhao, Y. Huang, B. Jiang, Z. Chen, X. Yu, X. Sun, H. Zhou, Y. Zhang and N. Zhang, Adv. Energy Mater., 2024, 14, 2302586 CrossRef CAS.
- Q. Peng, Z. Guo, B. Sa, J. Zhou and Z. Sun, Int. J. Hydrogen Energy, 2018, 43, 15995–16004 CrossRef CAS.
- X.-P. Zhang, Y.-N. Li, Y.-Y. Sun and T. Zhang, Angew. Chem., Int. Ed., 2019, 58, 18394–18398 CrossRef CAS PubMed.
- Y. Chen, J. Li, B. Lu, Y. Liu, R. Mao, Y. Song, H. Li, X. Yu, Y. Gao, Q. Peng, X. Qi and G. Zhou, Adv. Mater., 2024 DOI:10.1002/adma.202406856.
- N. Lespes and J.-S. Filhol, J. Chem. Theory Comput., 2015, 11, 3375–3382 CrossRef CAS PubMed.
- L. Miao, W. Jia, X. Cao and L. Jiao, Chem. Soc. Rev., 2024, 53, 2771–2807 RSC.
- X. Hu, S. Chen, L. Chen, Y. Tian, S. Yao, Z. Lu, X. Zhang and Z. Zhou, J. Am. Chem. Soc., 2022, 144, 18144–18152 CrossRef CAS PubMed.
|
This journal is © The Royal Society of Chemistry 2024 |
Click here to see how this site uses Cookies. View our privacy policy here.