DOI:
10.1039/D3TC03329E
(Review Article)
J. Mater. Chem. C, 2024,
12, 1609-1624
Advances in the optical and electronic properties and applications of bismuth-based semiconductor materials
Received
13th September 2023
, Accepted 18th December 2023
First published on 22nd December 2023
Abstract
In recent years, bismuth-based semiconductors have become a research hotspot in the new semiconductor field due to their unique optical and electronic properties. In addition, due to the simple fabrication process and controllable shape and size of these materials, they are widely used in the fields of optoelectronic devices, electrocatalysis, photocatalysis, biomedicine, etc. However, the current review papers on bismuth-based semiconductors mainly focus on the field of photocatalysis, while the applications of other fields are rarely reported, and the comprehensive summary of optical and electronic properties and applications of bismuth-based semiconductors are also lacking. Therefore, in this review, a variety of typical bismuth-based semiconductor materials are introduced in detail, including their lattice structures, optical and electronic properties and modification studies. In addition, the relationship between the bulk composition and photoelectric properties is analyzed, which will promote the future research on how to systematically control the photoelectric properties of bismuth-based materials. Secondly, the preparation methods of different bismuth-based semiconductor materials and applications in the field of optoelectronics are evaluated. Finally, the challenges faced by bismuth-based semiconductor materials in academic studies and industrial applications are pointed out, and the future work is prospected.
1. Introduction
Traditional semiconductor materials such as silicon, germanium, and gallium nitride have ignited an information technology revolution in integrated circuits and digital communications, profoundly impacting human society and economic development.1 However, these conventional semiconductors face issues such as low photoelectric conversion efficiency, susceptibility to thermal damage, high production costs, and environmental pollution, inhibiting their applications in emerging fields like new energy, environmental protection and biomedicine.2,3 To address these limitations, much efforts have been exerted on exploring various new semiconductor materials, such as InSe,4 TiO2,5 and Ga2O3.6 Nonetheless, these alternatives also have inherent drawbacks that hinder their applications in optoelectronics. For example, two-dimensional semiconductor materials often exhibit unstable lattice structures7 and organic semiconductors suffer from low crystallinity, making it challenging to control their morphologies and sizes.8 In addition, perovskite materials with excessively large band gaps result in poor visible light absorption.9 In contrast, bismuth-based semiconductors offer several advantages, including facile synthesis, affordability, environmental compatibility, high stability, and exceptional visible light activity; therefore, they are gaining much more attention in the fields of photocatalysis, solar cells, and photoelectrochemistry.10–13 Especially in the field of photocatalysis, bismuth-based semiconductors have been demonstrated to exhibit promising photocatalytic performance in many reactions (such as CO2 reduction, degradation of organic pollutants) under visible light because of their unique electronic and optical properties.14,15 In comparison to typical photocatalysts, these bismuth-based materials show appropriate band gaps or a wide range of visible light response which can promote the absorption of visible light and separation of photogenerated electron–hole pairs, ultimately leading to enhanced photocatalytic efficiency.16,17 Besides, some bismuth-based semiconductor photocatalysts with unique hierarchical porous structures can increase the diffusion of reactants and provide additional reaction sites, resulting in improved photocatalytic performance. On the other hand, for those typical photocatalysts, due to either an inappropriate band gap or insufficient response to visible light, they often encounter low photocatalytic activity or selectivity of desirable product problems. For example, TiO2 as one of the most commonly utilized photocatalysts is predominantly active in the ultraviolet light range since its wide band gap restricts its practical applications under solar light. Although several modification methods through doping have been employed on TiO2 to enhance its visible light absorption, doped materials are introduced as recombination centres leading to decreased photocatalytic activity.18 In addition, recently, CdS, WO3, and AgVO3 have also been hotspots in photocatalytic research due to their narrow band gaps and strong absorption in the visible light region. However, the rapid radiative recombination of photogenerated electrons and holes of CdS coupled with the high kinetic barrier for hydrogen evolution on surface hinders the direct conversion of solar energy to fuels.19 Another example, WO3 with a band gap ranging from 2.4 to 2.8 eV is also a notable candidate in visible-light-driven photocatalysis, while its lower conduction band level poses a limitation in the photocatalytic reduction potential of the electrons, resulting in a decrease in product selectivity and light-energy conversion efficiency.20 Moreover, in the case of AgVO3, the photogenerated electrons tend to reduce Ag+ to Ag nanoparticles which introduces a photo-corrosion risk for silver-based catalysts.21 Hence, bismuth-based photocatalysts with appropriate band gaps, visible light response, high stability, resistance to photo-corrosion, and tunable and controllable electronic and optical properties are explored.
Although the community is continuing to conduct extensive investigations into physical and chemical properties of bismuth-based semiconductors, their synthesis methodologies and applications, numerous opportunities and challenges still need further breakthroughs, especially the in-depth study on how to control their morphology and crystal structures and optimize optical and electronic properties. In addition, these published review papers on bismuth-based semiconductors mainly concentrate on the area of photocatalysis and there is a lack of complete picture of the recent advances in the optical and electronic properties and applications of bismuth-based semiconductors, as well as the latest developments and breakthroughs in this field.16–18,22–36 Therefore, this review will focus on comprehensive introduction and analysis of these aspects. As shown in Fig. 1, firstly, we will give discussions of distinctive characteristics of various types of bismuth-based semiconductors, including their unique crystal structures and electronic structures. Then the commonly utilized synthesis techniques for bismuth-based semiconductor materials will be outlined with the analysis of effect of material morphology on the photoelectronic properties. Additionally, applications of bismuth-based semiconductors in different fields such as optoelectronic devices, electrocatalysis, photocatalysis, and medical applications will be presented. Lastly, the article provides a summary of the prevailing research challenges associated with bismuth-based semiconductors in terms of their properties, synthesis methodologies, practical applications as well as prospects.
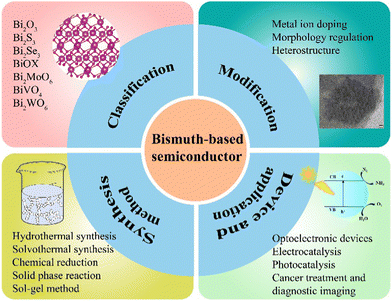 |
| Fig. 1 The schematic diagram outlining the main content of this review. | |
2. Classification of bismuth-based semiconductors
2.1. Bismuth oxide
Bismuth trioxide (Bi2O3) as the simplest and most pivotal type of bismuth-based compounds (Fig. 2(a)),17,37 shows a relatively narrow band gap (ranging from 2.2 to 2.8 eV, see Fig. 3(a)) and a robust capacity for deep valence band oxidation, positioning it as a potential photocatalyst under visible light. Furthermore, the cost-effective preparation, commendable oxygen ion conductivity, chemical and biological inertness, resistance to photo-corrosion, and its ability to absorb visible light all contribute to making Bi2O3 a promising optoelectronic material for environmental and energy-related applications.38 For example, Zhang's group has demonstrated the ability of Bi2O3 nanoparticles to generate highly functional free radicals under exposure to visible light, which enables oxidative degradation of organic pollutants when they are adsorbed on the surface of these nanoparticles.39 Other researchers also have reported that Bi2O3 can degrade various substances such as rhodamine B (RhB), methyl orange (MO), methylene blue, dichlorophenol, textile printing and dyeing wastewater, nitrite-containing wastewater, and volatile organic pollutants.40–47
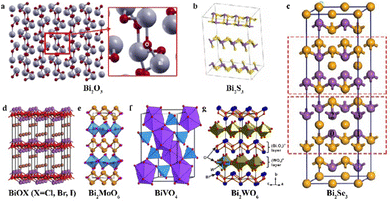 |
| Fig. 2 The crystal structures of (a) Bi2O3, reproduced from ref. 37 with permission from Elsevier, copyright 2017. (b) Bi2S3, reproduced from ref. 55 with permission from Elsevier, copyright 2022. (c) Bi2Se3, reproduced from ref. 66 with permission from Elsevier, copyright 2023. (d) BiOX (X = Cl, Br, I), reprinted with permission from ref. 73. Copyright 2014 American Chemical Society. (e) Bi2MoO6, reproduced from ref. 93 with permission from Elsevier, copyright 2014. (f) BiVO4, reproduced from ref. 107 with permission from Royal Society of Chemistry, copyright 2011. (g) Bi2WO6, reproduced from ref. 119 with permission from Springer Nature, copyright 2020. | |
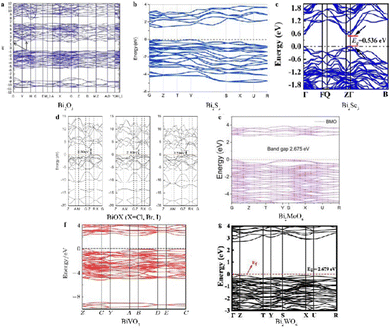 |
| Fig. 3 The energy band structures of (a) Bi2O3, reproduced from ref. 37 with permission from Elsevier, copyright 2017. (b) Bi2S3, reproduced from ref. 54 with permission from Elsevier, copyright 2020. (c) Bi2Se3, reproduced from ref. 66 with permission from Elsevier, copyright 2023. (d) BiOX (X = Cl, Br, I), reproduced from ref. 78 with permission from Elsevier, copyright 2012. (e) Bi2MoO6, reproduced from ref. 95 with permission from Elsevier, copyright 2022. (f) BiVO4, reproduced from ref. 106 with permission from IOP Publishing Ltd, copyright 2017. (g) Bi2WO6, reproduced from ref. 117 with permission from Elsevier, copyright 2022. | |
However, because of its inherent material properties, Bi2O3 shows ready electron–hole recombination48 and unstable crystal phases,17 which significantly limits its optoelectronic applications and development. In particular, the chemical instability of Bi2O3 readily causes an α to δ phase transition during heating reactions, and even further to (BiO)2CO3, significantly deactivating relative performances. To address these problems, researchers have modified Bi2O3 through approaches like metal ion doping, morphology control, and heterostructure construction to enhance photoelectric performance.49–53 For example, Nd-doped Nd/Bi2O3 nanocomposites can change original band structure of Bi2O3 and inhibit internal electron–hole recombination, leading to improved photocatalytic activity, excellent catalytic stability and reproducibility for hydrogen production.49 Moreover, flower-like Bi2O3/TiO2 made by Zhu's group enriched with Bi2O3 quantum dots on the surface enhances light absorption, photosensitivity, and hydrothermal stability due to its special morphology, which results in stronger photocatalytic activity and stability.50 Additionally, heterostructures like Bi2O3/BiOCl,51 Bi2O3/Bi2SiO552 and Bi2O3/PbS53 have also been reported which exhibit higher charge separation and transfer efficiency, improved photocatalytic activity, and enhanced photoelectrochemical performance.
2.2. Bismuth chalcogenide
Bismuth sulfide (Bi2S3) is a typical transition metal sulfide semiconductor (Fig. 2(b)) with a wide visible light response range (absorption coefficient of 104–105 cm−1 and around 5% photoelectric conversion rate), high biocompatibility, and low toxicity. Additionally, Bi2S3 shows a narrow and variable band gap (1.3–1.7 eV, see Fig. 3(b)) depending on its morphology (nanoplates, nanorods, nanowires, etc.).12,54,55 Bao et al. synthesized Bi2S3 nanowire arrays hydrothermally, exhibiting nonlinear current–voltage characteristics and good light response.56 Later, Hu et al. assembled flower-like Bi2S3 nanorods and achieved controlled synthesis of monodispersed nanorods with excellent electrochemical hydrogen storage.57 Bi2S3 nanorods produced by Zhou's group can enable sensitive detection of DNA methylation in novel PEC biosensors.58 Thus, Bi2S3 shows great potential for application in solar cells, hydrogen storage, photocatalysis, optical detection, and memristors.59 However, the narrow band gap of Bi2S3 leads to fast electron–hole recombination, reducing response speed and photocatalytic efficiency.12 To suppress recombination, approaches like element doping,60 conductive material modification,61 and heterojunction structures62–65 have been investigated. For example, modified SrTiO3/Bi2S3 heterojunctions exhibit lower carrier recombination and electron transfer resistance than pure SrTiO3 and Bi2S3, promoting UV-driven hydrogen production by effectively separating photogenerated carriers.62 Combining Bi2S3 with the other wide-bandgap photocatalysts like TiO2,63,64 Bi2WO6,64 and CdS65 can also reduce electron–hole recombination and enhance visible light photocatalytic performance.
Bismuth selenide (Bi2Se3), another noteworthy bismuth chalcogenide, has been recognized for its remarkable characteristics as a visible-light-responsive semiconductor. As shown in Fig. 2(c) and 3(c), the layered structure, coupled with a narrow band gap ranging from 0.35 to 1.2 eV, makes it attractive for the photocatalytic degradation of organic pollutants.23,66 Additionally, Bi2Se3 exhibits an insulating bulk state and massless Dirac surface states, contributing to its unique optical and electrical properties. The nanostructure of Bi2Se3 enhances surface state properties, particularly its metallic surface states with a zero band gap, facilitating the presence of a substantial number of itinerant electrons on its surface—a feature advantageous for photocatalytic reactions.67,68 For instance, Lei et al. demonstrated enhanced photodegradative activity by preparing Bi2Se3-deposited TiO2 nanobelts, surpassing the performance of pure TiO2. This improvement was attributed to the quantum size effect of Bi2Se3.69 Furthermore, to address the poor redox capacity and rapid carrier recombination of Bi2Se3, a Bi2Se3/g-C3N4 composite photocatalyst with an S-scheme configuration was prepared to enhance charge separation. This configuration resulted in a higher photocatalytic activity compared to pristine Bi2Se3 and g-C3N4 in the removal of phenol.68 In summary, the outstanding light absorption, metallic surface, and high conduction-band properties of Bi2Se3 are attributed to the growing attention in the field of photocatalysis,68,69 infrared detection,70 and electrocatalysis.71
2.3. Bismuth-based oxyhalides
BiOX (X = Cl, Br, I) belongs to the V–VI–VIII ternary semiconductor group and has an orthorhombic structure (space group P4/nmm) like PbFCl (see Fig. 2(d)).72,73 The BiOX crystal layered structure contains [Bi2O2]2+ layers and double X atom layers stacked along the C-axis, connected through van der Waals interactions,74 which generates an internal electrostatic field along the [001] direction, facilitating photogenerated charge migration within the crystal and leading to enhanced photocatalytic activity and photoconductivity.75 Due to these excellent photoelectric properties, unique layered structure, good photocatalytic activity, and stability, BiOX materials have attracted much academic community interest.76
To deeply study photoelectric properties and applications of BiOX, the band structure and photo-response have been systematically investigated using density functional theory (DFT). DFT calculations (see Fig. 3(d)) show an interesting decrease of the band gap as the atomic number of X increases from Cl to I (2.50, 2.10 and 1.59 eV for BiOCl, BiOBr, and BiOI, respectively) which is related to their photocatalytic activity.77,78 The wide band gap of BiOCl provides excellent photocatalytic activity solely under UV irradiation, while the narrowest band gap of BiOI enables visible and near-infrared activation but with relatively weak photocatalytic activity due to high electron–hole recombination. In contrast, BiOBr with moderate band gap shows potential as a visible light-responsive catalyst for solar energy conversion.79 DFT results also indicate BiOX (X = Cl, Br, I) with an indirect band gap where photogenerated electrons must transit through intermediate k-layers before recombining with valence band holes can reduce electron–hole recombination rates.80
In summary, the unique layered structure and indirect band gap of BiOX enable high charge transfer rates and low carrier recombination, which promotes excellent performance for organic pollutant degradation,81,82 alcohol oxidation,82 and water splitting.79 For example, it has been demonstrated that BiOCl can elevate photocatalytic Hg0 oxidation under UV irradiation,83 while BiOBr can drive degradation of ciprofloxacin (CIP) under visible light.81 Like BiOX, bismuth-rich oxyhalides BixOyXz (e.g. Bi3O4Cl, Bi4O5Br2, Bi5O7I) also possess layered structures with weak interlayer interactions, attracting increasing attention for their unique photoelectric properties.84 Bi4O5Br2, for instance, degrades ciprofloxacin at 91% in 150 minutes, around 1.5 times faster than BiOBr, while extending visible light absorption from 440 nm to 500 nm.85
2.4. Bismuth-based metal oxides
2.4.1. Bismuth molybdate.
Bismuth molybdate (Bi2MoO6) belongs to the Aurivillius oxide family, with the general formula Bi2O3·nMoO3.14 When n equals 3, 2, and 1, it corresponds to three phases: α-Bi2MO3O12, β-Bi2MO2O9, and γ-Bi2MoO6. For α-Bi2MO3O12 and β-Bi2MO2O9, the presence of defects and abundant active sites makes them effective catalysts for reactions like propylene oxidation to acrolein86,87 and 1-butene conversion to butadiene and 2-butene.88 On the other hand, γ-Bi2MoO6 possesses a layered structure,89 with [Bi2O2]2+ layers alternating with MoO6 perovskite layers,90 exhibiting excellent visible light absorption and charge separation (see Fig. 2(e)).91–93 This unique property has been confirmed in the DFT study by Lai's group that γ-Bi2MoO6 is a direct band gap (2.5–2.8 eV, see Fig. 3(e)) semiconductor and enables visible light response.94,95 In addition, people found that γ-Bi2MoO6 can be applied to many applications like organic degradation,96 water splitting,97 and CO2 reduction.98 For example, Bi2MoO6 can catalyse visible light-driven phenol degradation,96 but suffers from fast carrier recombination and insufficient visible light absorption.89 To address this problem, Li et al. synthesized mesoporous Bi2MoO6 spheres with increased specific surface area and charge transfer efficiency.99 Additionally, Phuruangrat et al. claimed that tungsten-doped Bi2MoO6 boosted rhodamine B degradation rates by 1.69 times in comparison to Bi2MoO6.100 Thus, approaches like morphology control,99 metal doping,101 and heterojunction structures102 can effectively improve Bi2MoO6 photoelectric properties.
2.4.2. Bismuth vanadate.
As an important bismuth-based oxide semiconductor, bismuth vanadate (BiVO4) shows excellent visible light absorption, suitable band edge position, electrochemical stability, non-toxicity, and resistance to photochemical/chemical corrosion.103,104 BiVO4 has three crystal structures: tetragonal scheelite, monoclinic scheelite, and tetragonal zircon.28 The monoclinic scheelite structure (m-BiVO4, see Fig. 2(f)) exhibits the highest thermodynamic stability and catalytic activity, making it the most utilized photoelectrocatalyst.103,105 Theoretical DFT calculations indicate that m-BiVO4 is an indirect band gap semiconductor with a band gap of 2.4 eV, as illustrated in Fig. 3(f), which leads to full visible light absorption and utilization.106 For m-BiVO4, the conduction band is mainly derived from the V 3d orbitals, while the valence band arises from hybridized Bi 6s and O 2p orbitals.104 Two distinct V–O bond lengths (1.77 Å and 1.69 Å) exist in m-BiVO4, affected by Bi 6s/O 2p lone pair hybridization at the valence band maximum, causing distortions in the BiO8 dodecahedra and VO4 octahedra and displacing the positive and negative charge centres. Thus the resulting internal electric field promotes separation of photogenerated electrons and holes, enhancing the photoelectric properties of m-BiVO4.103,107 An earlier study by Kudo et al.108 has shown that BiVO4 exhibits broad-spectrum absorption under ultraviolet and visible light, causing high photocatalytic activity. Since then, significant studies have been carried out on the unique and excellent photoelectric properties of BiVO4 and suggest a wide range of applications in fields such as organic pollutant degradation,109 water splitting,110 CO2 reduction,111 and photoanodes.112 In order to further improve the photocatalytic activity, visible light absorption intensity, and other photoelectric properties of BiVO4, researchers have also attempted to improve the high electron–hole recombination rate and poor electron mobility of BiVO4 by element doping,113 vacancy introduction,114 or heterostructure construction.115 Furthermore, the low raw material cost and versatile preparation methods of BiVO4, such as solid-phase reaction (SSR), high-temperature melting reaction, precipitation, and hydrothermal methods,17 make it more promising and widely studied in the field of photocatalysis.
2.4.3. Bismuth tungstate.
Bismuth tungstate (Bi2WO6) is another common bismuth-based oxide semiconductor with a perovskite layered structure, narrow band gap (2.8 eV, see Fig. 3(g)), strong visible light harvesting ability, non-toxicity, and high chemical stability.116,117 Its crystal structure belongs to the orthorhombic space group Pca2(1)17 and is formed by the superposition of [Bi2O2]2+ and [WO4]2− layers,118,119 as depicted in Fig. 2(g). The layered structure of Bi2WO6 leads to sufficient adsorption sites and generates a built-in electric field between layers, which is beneficial to the separation of photogenerated electrons and holes.120 According to the DFT calculation results, the valence band of Bi2WO6 is composed of the hybrid orbitals of Bi 6p and O 2p, while the conduction band is mainly contributed by the W 5d orbital, with the contribution of Bi 6p being small.121 This kind of electronic structure brings about a broad dispersion of the valence bands, which increases the mobility of photogenerated holes and facilitates the oxidation reaction.118
As early as 1999, Akihiko et al. first synthesized Bi2WO6via traditional solid-state reaction for photocatalytic O2 generation.122 After that, various methods like solid-state reaction, liquid-phase precipitation, hydrothermal methods, and solvothermal methods have been developed to produce Bi2WO6.123 Currently, the application range of Bi2WO6 has covered organic pollutant degradation,124 selective organic synthesis125 and bacteria inactivation in aqueous solutions,126 such as the photocatalytic degradation of rhodamine B/phenol mixtures124 or Escherichia coli inactivation.126 However, high photogenerated electron–hole recombination limits its photocatalytic performance. Strategies to address this include morphology control,127 doping,128 and heterojunction construction.129 For instance, metal doping (Fe, Zn, and Mo) improves the visible light absorption and charge transfer of Bi2WO6.128 Notably, the photocurrent density of Mo-doped Bi2WO6 is 57 times higher than that of pure Bi2WO6, dramatically enhancing the photoelectric properties.
3. Synthesis of bismuth-based materials
3.1. Hydrothermal method
Hydrothermal synthesis involves crystallization of single crystal materials from high-temperature aqueous solutions130 and is commonly used to prepare bismuth-based compounds.131 Compared to other methods, hydrothermally prepared nanoparticles often exhibit superior performance for targeted applications.131 The process is energy-efficient and economical, yielding appropriately sized and shaped nanoparticles.28 Moreover, effective control of product crystal phase, particle size, and morphology can be achieved by tuning parameters like solvent, temperature, time, pH, and reactant concentrations.130 However, specialized autoclave reactors mean longer production times and lower efficiency than other methods.132 Still, the hydrothermal synthesis method is important for bismuth-based single crystals and nanostructures since particles synthesized using this method show high crystallization and well-controlled morphology.
For example, tubular defective bismuth oxide (BiO2) microtubes with a hierarchical hollow structure (see Fig. 4(a) and (b)) were first synthesized by Su et al. via hydrothermal synthesis,133 which promotes efficient photogenerated electron–hole separation, enabling degradation of dyes like methyl orange and malachite green. Additionally, bismuth-based oxyhalides and metal oxides with controllable crystal facets and morphologies were prepared by using hydrothermal methods such that their optical properties can be systematically manipulated, which will be beneficial for specific applications in different fields. Zhang et al. selectively synthesized BiOCl {001} and {010} single crystal nanosheets using a 160 °C hydrothermal process.134 In the case of {001}-exposed nanosheets, it exhibited higher ultraviolet pollutant degradation, while visible light favoured {010}-exposed nanosheets for dye degradation. Lin et al. hydrothermally synthesized monoclinic BiVO4 with diverse morphologies like hollow spheres, decahedrons, coral-like particles, and needles (see Fig. 4(c)–(f)) by tuning pH and showed desirable photocatalytic degradation efficiency toward rhodamine B solution.135 Among them, BiVO4 synthesized at pH 7 exhibited the best photocatalytic degradation efficiency under visible light, which demonstrates that pH can alter the BiVO4 microstructure and photocatalytic performance. Furthermore, Zhang et al. tried microwave-assisted hydrothermal synthesis to shorten reaction times and reduce energy costs vs. traditional hydrothermal methods.136 The resulting Bi2CrO6 crystals with exposed {001} planes and regular flake morphologies were demonstrated to exhibit enhanced photogenerated charge separation and photocatalytic hydrogen production owing to their high crystallinity and uniformity. However, hydrothermal method faces a challenge for the formation of low-dimensional materials (e.g., 0D nanoparticles, 1D nanorods or nanoribbons, and 2D nanosheets).
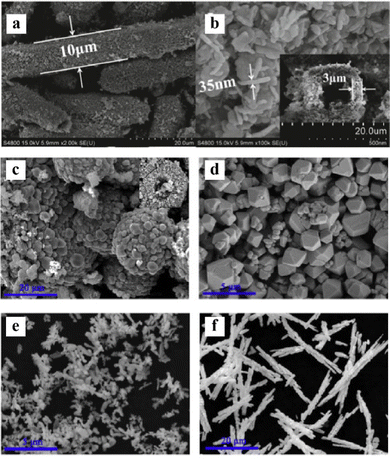 |
| Fig. 4 (a) and (b) SEM images of the as-prepared BiO2 microtubes. Reproduced from ref. 133 with permission from Elsevier, copyright 2018. SEM images of BiVO4 powder prepared at different pH: (c) 0.5, (d) 2, (e) 7, and (f) 12. Reproduced from ref. 135 with permission from Elsevier, copyright 2019. | |
3.2. Solvothermal method
The solvothermal method offers a solution to the challenge encountered in the hydrothermal method by applying organic solvents like polyols and citric acid instead of water to induce directional nucleus growth and nanoparticle assembly into 3D hierarchical structures. Mixed solvents of ethylene glycol with water, ethanol, or isopropanol can also increase anionic salt solubility and adjust ethylene glycol viscosity to improve product morphology and crystallinity.137–139 As a result, solvothermal routes are more prevalent for preparing bismuth-based photocatalysts than the hydrothermal method.131,140
Solvothermal methods have been conducted to produce bismuth-based materials like metal-modified bismuth oxyhalides which exhibit unique electronic and optical properties. For example, Huang et al. successfully loaded Bi nanoparticles (∼4.0 nm diameter) onto BiOBr nanoplates by reducing Bi(NO3)3 in ethylene glycol reductant via a solvothermal approach, as shown in Fig. 5(a)–(c).141 The obtained Bi/BiOBr Schottky junction promotes interfacial electron transfer and nitrogen adsorption. Additionally, Chen et al. solvothermally synthesized Bi-modified Bi4O5I2 microspheres in ethylene glycol (see Fig. 5(d)),142 which generates a built-in electric field between Bi and Bi4O5I2 that improves carrier separation efficiency. Owing to the synergistic effects of oxygen vacancies and this built-in field, the Bi/Bi4O5I2 microspheres exhibit excellent mercury removal, performance stability, and sulfur resistance. However, like hydrothermal methods, solvothermal approaches still have long production cycles and lower yields. They also show the risks of harmful solvent emissions and environmental pollution.143
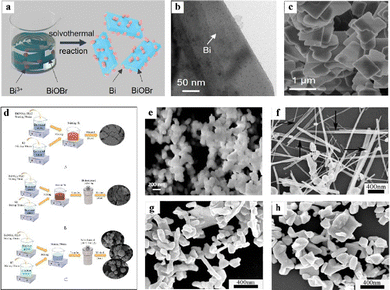 |
| Fig. 5 (a) Schematics of the preparation of Bi/BiOBr composites. (b) TEM and (c) SEM image Bi/BiOBr. Reproduced from ref. 141 with permission from John Wiley and Sons, copyright 2021. (d) The preparation process of BiOI, Bi4O5I2 and Bi/Bi4O5I2. Reproduced from ref. 142 with permission from Elsevier, copyright 2021. (e) Top-view FESEM of the as-synthesized Bi2(CrO4)3 nanoparticles. Reproduced from ref. 144 with permission from Elsevier, copyright 2020. FESEM images of Bi nanostructures synthesized at different temperatures: (f) 50 °C, (g) 70 °C, and (h) 80 °C. Reproduced from ref. 145 with permission from Elsevier, copyright 2012. | |
3.3. Chemical reduction method
Chemical reduction is another common synthesis method for bismuth-based nanomaterials. Similar to hydrothermal approaches, chemical reduction method is relatively inexpensive and can be operated under mild conditions (low temperature and pressure), enabling simple and green chemistry.28,143 For example, Hamza et al. chemically synthesized Bi2(CrO4)3 spherical nanoparticles with uniform size using a simple template-free and stabilizer-free chemical reduction at room temperature,144 as depicted in Fig. 5(e). Photocatalytic tests revealed these spherical Bi2(CrO4)3 nanoparticles can enhance hydrogen production activity in comparison to other reported Bi-based photocatalysts.
However, in chemical reduction methods, many factors including reducing agents, temperature, time, pH, precursor concentration, and surfactants can readily influence nanomaterial size, morphology, and structure, and therefore careful control over these parameters is essential.143 For instance, Ma et al. used NaH2PO2 to prepare 1D bismuth nanostructures at low temperature,145 but they found the dosage of tartaric acid (H2C4H4O6) and reaction temperature significantly affected their morphologies (curled, bundled, and irregular particulate structures were obtained under different conditions, as shown in Fig. 5(f)–(h)).
3.4. Solid phase reaction method
Although hydro/solvothermal methods can precisely control the morphology and size of products, they require substantial water and expensive organic solvents. In contrast, solid-state reactions can overcome these issues through direct mechanical energy absorption during the chemical reaction, also known as mechanochemical synthesis.131 In solid-state reactions, ground reactant powders undergo solid-state reactions during inter-particle contact, eliminating solvent needs and enabling large-scale production.132 However, direct exposure of nanoparticles to the environment raises safety and environmental concerns with this method.146 Moreover, uncontrollable preparation conditions lead to relatively broad nanoparticle size distributions.147 Nevertheless, solid-state reactions have been used for successful synthesis of bismuth-based semiconductors in recent years.131 For example, Cuéllar et al. prepared γ-Bi2MoO6 powder from Bi2O3 and MoO3 at 550 °C, and then fabricated γ-Bi2MoO6 films with strong photocatalytic performance via thermal decomposition/evaporation.148 As Fig. 6(a) and (b) show, using this method, heat treatment can promote a densified film and reduced pore size. Additionally, Bijanzad et al. used bismuth nitrate and potassium bromide to produce BiOBr nanosheets.149 With increased preparation time, morphologies transformed from irregular chunks to uniform, thin, and separated nanoplates, which show the ability for photocatalytic rhodamine B and pentachlorophenol degradation.
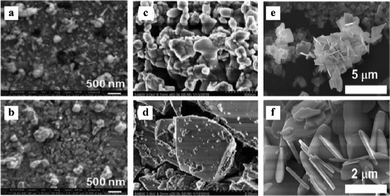 |
| Fig. 6 SEM images of (a) metal films without heat treatment and (b) γ-Bi2MoO6 films formed after heat treatment on a glass substrate. Reproduced from ref. 148 with permission from Elsevier, copyright 2011. FESEM images of (c) Sr1−xBixTi1−xFexO3, x = 0.1, (d) x = 0.2. Reproduced from ref. 150 with permission from Elsevier, copyright 2017. (e) and (f) FESEM images of BiOCl1−xBrx (x = 0.5). Reproduced from ref. 151 with permission from Elsevier, copyright 2023. | |
Beyond basic bismuth compounds, solid-state reactions like grinding or grinding-assisted methods can also prepare heterojunctions and solid solutions to enhance the photoelectric properties of materials.131 For instance, as Fig. 6(c) and (d) shown, the SrTiO3–BiFeO3 solid solution synthesized by Lu et al. via grinding shows high density with 100–1000 nm particle sizes.150 Compared to SrTiO3, the SrTiO3–BiFeO3 solid solution has a smaller band gap, broader visible light absorption, and stronger photocatalytic hydrogen production. Similarly, BiOCl1−xBrx nanosheet solid solution synthesized by Thi et al. via a simple room temperature water vapor solid-state reaction can significantly improve organic pollutant photocatalytic degradation compared with BiOCl and BiOBr (see Fig. 6(e) and (f)).151 Additionally, Bi and Bi2S3 modified semiconductors usually require two steps including reduction and sulfurization to be prepared, but Bi(Bi2S3)/BiOCl heterojunction photocatalyst was successfully synthesized by Shen et al. using a one-step room temperature solid-state reaction method and showed high rhodamine B and malachite green degradation efficiency under visible light.152
3.5. Sol–gel method
In addition, the sol–gel method is also commonly utilized to synthesize various nanostructures, especially metal oxide nanoparticles. In this approach, metal alkoxide molecular precursors are uniformly mixed in water or alcohol, then hydrolyzed/alcoholized via heating and stirring to form a gel. Subsequent steps involve drying and calcining the gel powder to produce nanostructured materials.153 Compared to other routes, sol–gel offers many advantages like controllable material structures, sizes and surface properties, facile implementation, cost-effectiveness, and high surface areas.154 In recent years, sol–gel synthesis has been widely applied to bismuth-based compounds. For instance, Sánchez et al. used sol–gel methods to prepare BiOCl–TiO2 composites, where BiOCl micro-flakes were irregularly nested on TiO2 nanoparticle agglomerates.155 Moreover, Cui et al. recently employed sol–gel spin coating to fabricate sheet-like Bi4Ti3O12 optoelectronic electrodes, which exhibited high carrier injection efficiency and surface activity after heat treatment.156 Furthermore, processing sol–gel precursors via methods like electrospinning, template deposition, heating, and spin coating can produce nanoparticles with different morphologies such as nanowires, nanotubes, thin films, and spherical nanoparticles.28 For example, William et al. employed sol–gel spin coating to fabricate high-purity (BiFeO3)x–(BiCrO3)1−x composite films on glass substrates.157 Similarly, Xian et al. used a polyacrylamide gel approach to synthesize BiFeO3 nanoparticles with varying diameters.158
4. Optical and electronic properties and potential applications of bismuth-based materials
4.1. Optoelectronic devices
Bismuth-based semiconductor materials have received significant attention from both academia and industry due to their unique photoelectric properties, which makes them ideal for use in manufacturing optoelectronic devices such as field effect transistors, laser devices, sensors, nanogenerators, and photodetectors.159 Bi2S3, for instance, is widely used in solar cells, optical detection, memristors, and other fields because of its direct band gap, wide visible light range response, and high photoelectric conversion efficiency.12 As shown in Fig. 7(a)–(c), by using pulsed laser deposition (PLD) technology, Bi2S3 quantum dots can be directly deposited on TiO2 nanorods to prepare quantum dot-sensitized solar cells (QDSSCs), which show strong controllability, high energy conversion efficiency, and excellent stability.160 In addition to Bi2S3, other layered bismuth-based nanomaterials such as Bi2O2Se have also been extensively studied in the field of optoelectronics (Fig. 7(d)). Bi2O2Se has high air stability, a suitable band gap (∼0.8 eV), and high carrier mobility. Photodetectors prepared based on this material show excellent photoelectric characteristics such as a high sensitivity of 65 A W−1 at 1200 nm, ultrafast optical response of approximately 1 ps at room temperature, and an inherent bandwidth limit of up to 500 GHz. Researchers also designed a flexible two-dimensional Bi2O2Se photodetector array that showed a consistent photo-response when the substrate bending strain was as high as 1%, confirming that 2D Bi2O2Se photodetectors can work on flexible substrates.161 2D Bi2Se3 flakes, with a narrow band gap of 0.3 eV, have been identified as a promising material for infrared telecommunication photodetectors, as reported by Wang et al. Their Bi2Se3-based photodetector demonstrates an outstanding on/off ratio of 972.5, a high responsivity of 23.8 A W−1, and an impressive external quantum efficiency of 2035%. These remarkable performance metrics suggest that Bi2Se3-based photodetectors hold significant potential in communications, military, and remote sensing.162 Ferroelectric materials such as BiFeO3 with spontaneous polarization characteristics allow for various functions to be realized by adjusting the polarization state of ferroelectric materials through an external electric field. Therefore, resistive switching devices, ferroelectric diodes, and resistive random access memory (RRAM) devices based on ferroelectric materials have been reported.163 For example, the Ag/BiFeO3/FTO (FTO, fluorine-doped tin oxide) RRAM device with a low-voltage bipolar switch (a maximum on–off ratio of 450) exhibits good reproducibility, robustness, and durability (Fig. 7(e)–(h)),164 thus resulting in a great potential for storage applications.
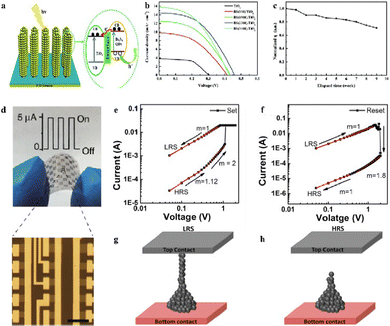 |
| Fig. 7 (a) Illustration of charge separation and transport in the Bi2S3-QDSSCs. (b) J–V characteristics, and (c) time stability of the normalized energy conversion efficiency (η) of QDSSCs assembled with B2S3/TiO2 photoelectrodes. Reproduced from ref. 160 with permission from Royal Society of Chemistry, copyright 2017. (d) Photograph of 2D Bi2O2Se photodetector arrays on mica and optical image of 3 × 5 multi-pixel array of 2D Bi2O2Se photodetectors. Inset shows photo-response of one typical photodetector when bending the substrate with strain up to 1%. Reproduced from ref. 161 with permission from Springer Nature, copyright 2018. Current–voltage logarithmic plots for (e) set process and (f) reset process; schematic representation of (g) Ag atom mediated conductive filament formation and (h) rupturing of the filament. Reproduced from ref. 164 with permission from Elsevier, copyright 2018. | |
4.2. Electrocatalysis
Electrocatalysis is a technology that converts electronic energy into chemical energy by forming chemical bonds.165 However, the current electrocatalysts predominantly rely on noble metal-based materials like Pt, IrO2 and RuO, which hinders their widespread application in the field of electrocatalysis.166 Fortunately, bismuth-based materials show the possibility of being promising alternatives since they are abundant in reserves, easy to synthesize, and exhibit excellent safety and stability, thus providing an opportunity to develop efficient and cost-effective electrocatalysts.167
For example, bismuth formate oxide nanowires (BiOCOOH NWS) were synthesized using a simple solvothermal method and reconstituted into ultrathin bismuth nanosheets covered with a thin layer of amorphous oxide (Bi/BiOX NSS) in KHCO3 solution. Compared to rough porous bismuth nanowires (Bi NWs), there are more active sites in the case of Bi/BiOX NSS, leading to stronger CO2 adsorption and charge transfer ability; thus excellent activity, selectivity, and stability were observed in the electrocatalytic reduction reaction of CO2 to formate.168 However, the high energy consumption limits their practicality. To address this issue, as shown in Fig. 8(a)–(c), Bi2O2CO3 nanosheets (VO-BOC-NS) with oxygen vacancies reported by Zhang et al. exhibited a partial current density of approximately 286 mA cm−2 with an operating potential of −0.62
V (vs. RHE).169 More importantly, in a two-electrode electrolyser, only an operating voltage of 2.27 V is required to obtain a current density of 50 mA cm−2 and the faradaic efficiency is greater than 90%. This is better than the independent half-reaction and lays the foundation for the practical application of the two-electrode cell in the industry. Similarly, the Bi1–Co9–BO3@450 electrocatalyst was produced by Thomas et al. by doping metallic bismuth into cobalt borate, which resulted in the formation of a cooperative catalytic active centre between Bi atoms and Co or B atoms, driving the hydrogen evolution reaction with a current density of 10 mA cm−2 and a minimum overpotential of 318 mV (see Fig. 8(d)–(f)).170 Additionally, it has been reported that BiFeO3 with a twisted perovskite structure exhibits good catalytic performance for the production of NH3 by nitric acid reduction.171 The highest faradaic efficiency of this catalyst is 96.85%, and the NH3 yield is 90.45 mg h−1 mgcat−1. During the nitric acid reduction reaction, crystalline BiFeO3 rapidly transforms into an amorphous phase, which remains stable for a long time in the reaction. In summary, these examples highlight the development of various bismuth-based electrocatalysts and their applications for specific reactions, primarily in the context of CO2 reduction, the hydrogen evolution reaction, and production of NH3. They also clearly demonstrated the unique properties of bismuth-based electrocatalysts and the importance of designing electrocatalysts with enhanced activity, selectivity, and stability. The established understanding provides a new approach for designing more active and durable electrocatalysts.
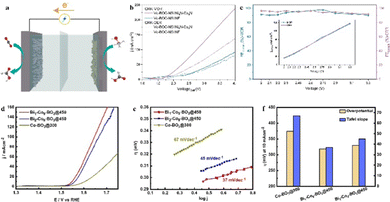 |
| Fig. 8 (a) Schematic diagram of a two-electrode electrolyser. (b) LSV curve. (c) Efficiency of cathode CO2 reduction reaction (CRR) and anode methanol oxidation reaction (MOR), the inset is the corresponding bias current density. Reproduced from ref. 169 with permission from John Wiley and Sons, copyright 2023. (d) LSV curves of OER over Bi1–Co9–BO3@450, Bi2–Co8–BO3@450, and Co–BO3@300 (non-doped) catalysts. (e) Their corresponding Tafel slopes. (f) The overpotentials needed for the reaction at 10 mA cm−2versus RHE (left) on each catalyst and the corresponding Tafel slopes (right). Reproduced from ref. 170 with permission from John Wiley and Sons, copyright 2023. | |
4.3. Photocatalysis
As human society continues to develop, non-renewable energy sources such as coal, oil, and natural gas are being rapidly depleted. Environmental pollution and the shortage of renewable energy resources have become two major challenges in the world. To address these issues, the development of clean, renewable energy has become a social priority. Solar energy is one of the most abundant renewable energy sources that can be converted into electronic and chemical energy. Among the various solar energy technologies, photocatalysis, which uses solar energy to drive chemical and energy processes, is a major advancement.172,173 However, common photocatalytic materials such as TiO2 with a large band gap and low utilization of visible light limit their application in the field of photocatalysis.174 Other visible light absorbing photocatalysts also face challenges, with materials like CdS (Eg = ∼2.4 eV) exhibiting rapid radiative recombination of photogenerated electrons and holes and inadequate photo-corrosion resistance.19 WO3 (Eg = 2.4–2.8 eV) is constrained by its lower conduction band level, leading to diminished light energy conversion efficiency.20 Therefore, in recent decades, bismuth-based materials have been explored and have gained popularity in the field of photocatalysis due to their tunable and controllable electronic and optical properties, suitable band edge position, high stability, photo-corrosion resistance, and excellent catalytic performance,11,17,175 as illustrated in Fig. 9. The recent advancements of bismuth-based photocatalysts are summarized in Table 1 and will be discussed in detail in the following sections. Also, since the compositional space of bismuth-based semiconductors is vast by selecting constituent elements and adjusting element ratio, promising semiconductors with appropriate electronic and optical properties can be explored for specific photocatalytic reactions.
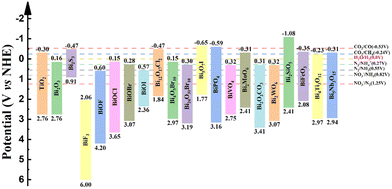 |
| Fig. 9 Band diagram of selected bismuth-based semiconductors and their redox potential of typical reduction reactions. Reproduced from ref. 175 with permission from Royal Society of Chemistry, copyright 2023. | |
Table 1 Summary of the photocatalytic activity of bismuth-based semiconductors
Photocatalytic applications |
Photocatalyst |
Structure or morphology |
Photocatalytic performance |
Ref. |
CO2 reduction |
Cs3Bi2X9 |
Quantum dots |
CO yield: 134.76 μmol g−1, CO selectivity: 98.7% |
14
|
Bi4O5Br2 |
Nanosheets |
CO yield: 63.13 μmol g−1, CO selectivity: 99.5% |
177
|
Co–BiVO4 |
Co-doped BiVO4 |
CH4 production rate: 23.8 μmol g−1 h−1 |
178
|
BiVO4/Bi4Ti3O12 |
Heterostructure |
CH3OH and CO production rate: 16.6 and 13.29 μmol g−1 h−1 |
179
|
|
Degradation of organic pollutants |
Bi7O9I3 |
Hierarchical micro-architecture |
Phenol degradation efficiency: 94% after 4 h |
13
|
Bi4O5Br2 |
Ultrathin nanosheets |
CIP degradation efficiency: 75% after 2 h |
182
|
α/β-Bi2O3 |
Heterostructure |
RB 198 and RB 5 degradation efficiency: both 90% after 30 min |
184
|
Bi2MoO6 |
Nanosheet |
CIP and phenol degradation efficiency: 99.4% and 78.6% after 2 h |
185
|
BiFeO3/AgVO3 |
Nanocomposites |
RhB degradation efficiency: 70% after 90 min |
186
|
Bi3O4Cl |
Ag–Bi3O4Cl plasmon |
CIP and TBPA degradation efficiency: 93.8% and 94.9% after 2 h |
187
|
|
Water splitting |
Bi24O31Br10 |
Nanoplate |
H2 yield: 133.9 μmol |
189
|
BP/BiVO4 |
Heterostructure |
H2 and O2 production rate: 160 and 102 μmol g−1 h−1 |
190
|
Bi2O2Se/TiO2 |
Heterostructure |
H2 production rate: 1240.7 μmol h−1 g−1 |
191
|
|
Artificial nitrogen fixation |
Br–BiOCl |
Br-doped oxygen vacancy-rich BiOCl micro-sheets |
NH3 production rate: 6.3 μmol h−1 |
193
|
Bi2MoO6/BiOBr |
Heterostructure |
NH3 yield: 412.18 mol L−1 |
194
|
(BiO)2CO3 |
Nanosheets with Au nanoparticles |
NH3 production rate: 38.23 μmol (cm−2 h)−1 |
195
|
RB 198 and RB 5: carcinogenic reactive blue 198 and reactive black 5 dyes |
4.3.1. CO2 reduction.
Excessive carbon dioxide emissions and the use of fossil fuels have led to serious environmental problems and energy crises.11 To eliminate excess CO2 and reduce the greenhouse effect, the photocatalytic CO2 reduction technology has emerged,176 which is a green and efficient way to convert carbon dioxide into renewable hydrocarbon fuels and utilize solar energy to cycle carbon resources.175 However, low solar energy utilization and catalytic efficiency, as well as low selectivity of CO2 reduction products, are the main obstacles limiting the development of photocatalytic CO2 reduction technology.11,175 To overcome these problems, various bismuth-based photocatalysts have been developed, and significant progress has been made in the field of photocatalytic CO2 reduction.
Sheng et al.14 prepared a series of bismuth halide perovskite quantum dots Cs3Bi2X9 (X = Cl, Br, I) for the photocatalytic reduction of CO2 to CO at the gas–solid interface. These bismuth-based quantum dot materials have unique structures and excellent optical and electronic properties. Under sunlight irradiation, the CO yield is 134.76 μmol g−1, and the selectivity is as high as 98.7%. Additionally, by controlling the molar ratio of reactants, ultrathin Bi4O5Br2 nanosheets (Bi4O5Br2-UN) synthesized using the precursor method exhibit as high as 99.5% CO selectivity and 2.3 times higher CO production rate than bulk Bi4O5Br2 under UV-visible light irradiation, as shown in Fig. 10(a)–(c).177 Furthermore, another researcher found that Co-doped BiVO4 can produce about 3 times CH4 in comparison to undoped BiVO4 because of the new defect levels above the Fermi level.178 A similar phenomenon was observed by Wang et al. in the study of CO2 reduction over the BiVO4/Bi4Ti3O12 heterojunction structure. Because the BiVO4/Bi4Ti3O12 heterojunction structure effectively improves the charge separation efficiency and carrier lifetime, a synergistic effect between water oxidation on Bi4Ti3O12 and CO2 reduction on BiVO4 is introduced, which can promote the reduction of CO2 and H2O to CH3OH and CO.179
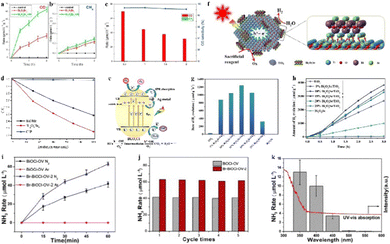 |
| Fig. 10 (a) Rates of CO and CH4 generation over Bi4O5Br2 and Bi4O5Br2-UN and (b) under UV-vis light irradiation for 2 h. (c) CO generation and the selectivity over Bi4O5Br2-UN under UV-vis light irradiation for 2 h. Reproduced from ref. 177 with permission from Elsevier, copyright 2019. (d) Photocatalytic degradation of CIP in the presence of Bi4O5Br2 and BiOBr under visible light irradiation. Reproduced from ref. 182 with permission from Royal Society of Chemistry, copyright 2015. (e) Mechanism of Ag–Bi3O4Cl degrading contaminants. Reproduced from ref. 187 with permission from Frontiers, copyright 2023. (f) The scheme of Bi2O2Se/TiO2 for photoreduction of hydrogen evolution. (g) and (h) Rates of H2 evolution reaction by Bi2O2Se, TiO2 and various Bi2O2Se/TiO2 at room temperature under UV light with 5 vol% of glycerol as a sacrificial reagent. Reproduced from ref. 191 with permission from Elsevier, copyright 2020. (i) NH3 generation by the as-prepared BiOCl-OV and the Br-BiOCl-OV under Ar and N2 atmospheres. (j) Cycling stability of BiOCl-OV and Br-BiOCl-OV. (k) N2 fixation by Br-BiOCl-OV under monochromatic light in compared with its light absorption spectrum. Reproduced from ref. 193 with permission from Elsevier, copyright 2019. | |
4.3.2. Degradation of organic pollutants.
The problem of environmental pollution has escalated with the rapid economic growth along with the industrial emissions of various organic pollutants, such as phthalates, polycyclic aromatic hydrocarbons (PAH), phenolic sulfonamides, tetracycline (TC), methylene blue (MB), and rhodamine B, leading to severe consequences for human health and the environment.180 Photocatalytic technology, recognized as an advanced oxidation process, has emerged as an effective solution for mitigating this issue by harnessing solar energy to decompose and eliminate these harmful pollutants.181
Many studies have demonstrated the role of bismuth-based materials in the process of degradation of organic pollutants, especially bismuth oxyhalides. For instance, Bi7O9I3 with a unique flaky micro-structure conducts remarkable oxidation capabilities in the degradation of phenol that a 94% removal rate was achieved after just 4 hours of irradiation.13 Similarly, ultrathin nanosheets of Bi4O5Br2 boast a variable energy band structure, which facilitates the generation of oxygen anions and efficient separation of electron–hole pairs. Consequently, these nanosheets demonstrate superior photocatalytic performance compared to BiOBr, particularly in the degradation of the colourless antibiotic ciprofloxacin under visible light as shown in Fig. 10(d).182 Additionally, various other materials, including Bi2O3,183,184 Bi2MoO6,185 and BiFeO3,186 have also been investigated for their photocatalytic potential. For instance, Zhang et al.185 prepared small-sized two-dimensional Bi2MoO6 nanosheets that exhibited excellent photocatalytic activity, showing a rapid degradation rate for a variety of pollutants under visible light irradiation. Within just 2 hours, impressive degradation rates of 99.4% for ciprofloxacin and 78.6% for phenol were observed with a 20 times higher reaction rate than that of larger bismuth molybdate nanosheets. Moreover, the deposition of metallic silver on the surface of Bi3O4Cl (see Fig. 10(e)) significantly enhanced the removal efficiencies of ciprofloxacin and tetrabromobisphenol A (TBPA), reaching 93.8% and 94.9%, respectively. This enhancement can be attributed to the surface plasmon resonance effect of Ag, which inhibits the recombination of electron–hole pairs and simultaneously promotes photocarrier migration and separation to improve both light absorption efficiency and catalytic performance.187
4.3.3. Water splitting.
Hydrogen (H2) stands out as a promising secondary energy source due to its numerous advantages, including high energy density, zero carbon emissions, renewability, and the ability to be stored efficiently. Various methods have been investigated to produce H2, such as steam reforming, coal gasification, and photocatalytic water splitting. Among these, photocatalytic water splitting powered by solar energy is regarded as the greenest and the most efficient technique. Notably, it has the capacity to concurrently generate both H2 and O2, underscoring its substantial potential for industrial applications.188
The reason of bismuth-based photocatalysts is promising for water splitting lies in their unique electronic properties and band structures. Specifically, the conduction band position of bismuth-based materials, such as Bi24O31Br10, has been found to meet the potential requirements for decomposing water into H2 through first-principles calculations by Shang et al.,189 which agrees well with experimental observations that Bi24O31Br10 has a certain photocatalytic water splitting ability, with 133.9 μmol of H2 precipitated from Bi24O31Br10 after 40 hours of visible light irradiation. In addition, Zhu et al.190 reported a new BP/BiVO4 two-dimensional heterostructure photocatalyst, which has a staggered band structure facilitating charge separation allowing water to be reduced and oxidized on BP and BiVO4, respectively. The optimal H2 and O2 yields over the BP/BiVO4 catalyst are approximately 160 and 102 μmol g−1 h−1, respectively, without using any sacrificial agent or external bias. To further improve the photocatalytic activity, researchers deposited bismuth selenide oxide (Bi2O2Se) on TiO2 nanoparticles, which significantly suppressed the recombination of photogenerated electrons and holes in Bi2O2Se/TiO2 compared to pure TiO2. The hydrogen production rate of Bi2O2Se/TiO2 is 1240.7 μmol h−1 g−1, which is about 50 times higher than that of pure TiO2 (see Fig. 10(f)–(h)).191
4.3.4. Artificial nitrogen fixation.
Ammonia is a crucial raw material in the production of fertilizers, chemicals, and energy. However, the traditional ammonia synthesis process has many drawbacks, such as high temperature, high pressure, and a large amount of CO2 emissions. As a result, researchers have to explore new sustainable alternatives and find photocatalytic nitrogen fixation for ammonia synthesis can be a candidate.192
To address the commonly encountered problems of slow carrier transmission and low surface reaction efficiency in the photocatalytic synthesis of ammonia, Wu et al. reported that Br-doped oxygen vacancy-rich BiOCl micro-sheets (Br-BiOCl-OV) were synthesized using a solvothermal method and ion exchange treatment, which exhibits a high charge separation efficiency and ammonia generation rate (6.3 μmol h−1) under visible light irradiation, indicating a stable N2 fixation ability, as illustrated in Fig. 10(i)–(k).193 Moreover, Zhang et al.194 introduced bismuth vacancies into the surface of BiOBr nanospheres with oxygen vacancies and constructed a Bi2MoO6/BiOBr composite structure. The synergistic effect of bismuth vacancies and oxygen vacancies significantly improves the efficiency of photogenerated electron–hole pairs and the light absorption capability of the composite material. The hierarchical Bi2MoO6/BiOBr nanosheet assembly structure is beneficial to the surface adsorption and activation of N2 on the catalyst leading to a four times higher yield of NH3 under visible light irradiation than BiOBr with oxygen vacancies. On the other hand, Xiao et al.195 found that gold nanoparticles and (BiO)2CO3 nanosheets also have a strong synergistic effect that can break the strong triple bond of nitrogen to form ammonia. Because modification of (BiO)2CO3 nanosheets with gold nanoparticles not only generates hot electrons but also significantly enhances light capture and charge separation efficiency, thereby improving the conversion efficiency of photocatalytic nitrogen oxidation.
4.4. Cancer treatment and diagnostic imaging
In recent years, there has been a surge of interest in the use of bismuth-based nanomaterials due to their promising applications and potential for clinical use, such as combined tumour therapy, multi-modal imaging, antibacterial activities, and biosensing.196 For example, Li et al.197 investigated the use of bismuth sulfide nanorods (Bi2S3 NRs) as contrast agents (CAs) for dual-energy computed tomography (DECT) (see Fig. 11(a)). The results showed that the X-ray attenuation characteristics of Bi2S3 NRs in dual-energy imaging were superior to those of clinically commonly used iohexanol, particularly at higher energies. Additionally, Bi2S3 NRs exhibited a high photothermal conversion rate and could be utilized for photothermal therapy (PTT) under the guidance of DECT imaging to destroy osteosarcoma cells and inhibit tumour growth. Overall, the combination of DECT imaging and photothermal therapy strategies using Bi2S3 NRs as contrast agents holds great potential for the treatment of bone diseases. Bi2Se3 also exhibits significant promise in cancer treatment, demonstrated by the successful development of an efficient colorimetric biosensor utilizing highly catalytic active Bi2Se3 nanosheets decorated with Au nanoparticles (Au/Bi2Se3), as shown in Fig. 11(b). This innovative approach serves as an alternative method for cancer diagnosis. The intrinsic low redox potential and distinctive topological insulating properties of Bi2Se3 nanosheets enable the provision and accumulation of electrons on their surface, which fosters robust synergistic catalytic effects in conjunction with Au nanoparticles. The resulting sensor exhibits exceptional sensitivity and selectivity for cancer biomarkers.198 In addition, a novel type of ultrathin iron-doped bismuth chloride nanosheets (BOC-Fe NSs) was demonstrated to be a highly efficient sonosensitizer for tumour treatment through sonodynamic therapy, as shown in Fig. 11(c).199 The iron-doped bismuth chloride nanosheets with specific oxygen vacancies can act as electron capture sites to promote the generation of reactive oxygen species (ROS) under the influence of ultrasonic waves. The toxic ROS produced can effectively kill cancer cells. Both vitro and vivo experimental studies indicate that the prepared BOC-Fe NSs can effectively inhibit the growth of breast cancer cells. The successful development of BOC-Fe NSs provides a new nano-sonosensitizer option for SDT treatment of cancer.
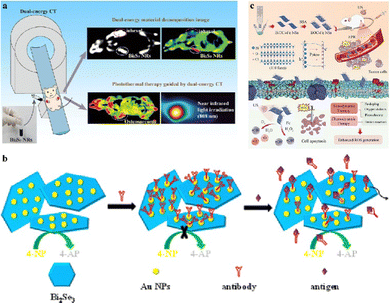 |
| Fig. 11 (a) Schematic diagram of Bi2S3 nanorods for DECT-guided photothermal treatment of osteosarcoma. Reproduced from ref. 197 with permission from Springer Nature, copyright 2023. (b) Schematic illustration of a versatile and colorimetric biosensor based on the tunable smart interface of catalytic Au/Bi2Se3 nanosheets. Reprinted with permission from ref. 198. Copyright 2017 American Chemical Society. (c) Schematic diagram of iron-doped bismuth chloride nanosheets for enhanced tumour sonodynamic therapy (SDT). Reproduced from ref. 199 with permission from John Wiley and Sons, copyright 2023. | |
5. Concluding remarks and outlook
Bismuth-based semiconductor materials have attracted significant attention from both academia and industry due to their unique electronic and optical properties. The studies on these materials are not only the cutting edge of scientific research but also the hotspot for industrial applications owing to their cost-effectiveness, environmental friendliness, and sustainability. To provide an understanding of how to modify and efficiently utilize these unique bismuth-based materials so that they can be applied to more fields, a comprehensive introduction to their crystal structures, electronic structures, photoelectric characteristics, modification techniques, and commonly employed synthesis methods as well as potential applications in electrocatalysis, photocatalysis, and medical fields is given.
Firstly, since bismuth-based semiconductor materials commonly encounter several challenges that impact their performance (such as high rates of photogenerated electron–hole recombination, limited capacity to absorb visible light, and susceptibility to chemical instability), low photoelectric conversion efficiency quite restricts their practical applications. Therefore, various modification techniques (including metal ion doping, morphology regulation, and the construction of heterostructures) are introduced to overcome these problems. Through these approaches, it becomes possible to optimize the band structure, enhance light absorption capabilities, and improve carrier separation efficiency. Specifically, with regard to certain bismuth-based semiconductors with layered structures, it is needful to explore the hierarchical porous structure concept because this kind of innovative morphology can increase the diffusion of reactants and provide additional reaction sites, leading to enhanced absorption of incident light. Ultimately, these enhancements significantly contribute to improved photoelectric performance and increased photoelectric conversion efficiency. These refined methodologies offer valuable guidance and direction for the continued development and practical utilization of bismuth-based semiconductors.
Secondly, although various synthesis methods have been developed for bismuth-based semiconductors, these approaches still show inherent shortcomings and require further refinement. For instance, the solid-state reaction method faces challenges in adjusting the microstructure and morphology of bismuth-based materials, while the hydrothermal/solvothermal method suffers from limitations in production efficiency and the inability to facilitate large-scale manufacturing. Additionally, during the design and synthesis of bismuth-based semiconductors, it is also imperative to consider factors such as safety, environmental sustainability, and economic viability. Particularly in the industry, the demand to synthesize bismuth-based semiconductors with outstanding photoelectric properties using a straightforward, large-scale, and high-yield approach is still a substantial challenge.
Moreover, in recent years, remarkable advancements in bismuth-based semiconductors have been witnessed, particularly in the realm of photocatalysis. However, it is important to note that despite these achievements, many photocatalytic technologies are stuck in the experimental investigation section and fall short of meeting the demands of practical production applications. In addition, the complicated photocatalytic reaction mechanism still needs further deep investigation for optimization of photocatalysts to achieve excellent performance. Therefore, building an understanding of the effect of electronic structure or bulk composition of materials on their photocatalytic performance, and unraveling the kinetics of electron transfer and surface chemistry in photocatalytic reactions, are the critical questions asked in the community. Based on these studies, expanding beyond photocatalysis, bismuth-based semiconductors will hold more potential for diverse applications in biological, medical, and other domains. For example, since bismuth possesses exceptional antibacterial properties, bismuth-based compounds will present more chances in the field of photocatalytic bacterial inactivation (such as treating ulcers and bacterial infections) compared with other photocatalysts. They can also be integrated with electrochemical technology to foster the development of novel biosensors and detection devices, capable of identifying cells, organic molecules. Additionally, their utility can also be extended to the field of thin-film technology for high-efficiency photoelectric conversion and storage devices or in the field of biotechnology as promising candidates with a high photothermal conversion rate for the applications of photodynamic therapy and photothermal therapy.
Author contributions
Conceptualization, T. Z.; writing – original draft preparation, P. X., and Y. S.; writing – review & editing, Y. L., M. L., C. Y. and X. Z.; supervision, T. Z.; project administration, T. Z.
Conflicts of interest
The authors declare no conflict of interest.
Acknowledgements
Funding: This research was funded by NSFC (grant no. 22102023 and 62275047), the National Key R&D Program of China (grant no. 2021YFB2800700), the Natural Science Foundation of Jiangsu Province (grant BK20220816) and the fellowship of China Postdoctoral Science Foundation (grant no. 2021M700768 and 2022M710672).
Notes and references
- B. Biswas and B. Saha, Phys. Rev. Mater., 2019, 3, 25 Search PubMed.
- B. Du, J. L. Hudgins, E. Santi, A. T. Bryant, P. R. Palmer and H. A. Mantooth, IEEE Trans. Power Electron., 2010, 25, 237–248 Search PubMed.
- A. Zakutayev, J. Mater. Chem. A, 2016, 4, 6742–6754 RSC.
- Z. N. Guo, R. Cao, H. D. Wang, X. Zhang, F. X. Meng, X. Chen, S. Y. Gao, D. K. Sang, T. H. Nguyen, A. T. Duong, J. L. Zhao, Y. J. Zeng, S. Cho, B. Zhao, P. H. Tan, H. Zhang and D. Y. Fan, Natl. Sci. Rev., 2022, 9, nwab098 CrossRef CAS PubMed.
- J. R. Chen, F. X. Qiu, W. Z. Xu, S. S. Cao and H. J. Zhu, Appl. Catal., A, 2015, 495, 131–140 CrossRef CAS.
- X. Q. Ji, C. Lu, Z. Y. Yan, L. Shan, X. Yan, J. J. Wang, J. Y. Yue, X. H. Qi, Z. Liu, W. H. Tang and P. G. Li, J. Phys. D: Appl. Phys., 2022, 55, 443002 CrossRef.
- D. Wang, X. B. Li and H. B. Sun, Nano Lett., 2021, 21, 6298–6303 CrossRef CAS PubMed.
- W. H. Lee and Y. D. Park, Polymers, 2014, 6, 1057–1073 CrossRef.
- P. Chen, W. J. Ong, Z. Shi, X. Zhao and N. Li, Adv. Funct. Mater., 2020, 30, 1909667 CrossRef CAS.
- S. Y. Yu, L. Zhang, L. B. Zhu, Y. Gao, G. C. Fan, D. M. Han, G. Chen and W. W. Zhao, Coord. Chem. Rev., 2019, 393, 9–20 CrossRef CAS.
- X. Liu, J. Xiao, S. Ma, C. Shi, L. Pan and J. J. Zou, ChemNanoMat, 2021, 7, 684–698 CrossRef CAS.
- Y. L. Zhou, H. S. Yin and S. Y. Ai, TrAC, Trends Anal. Chem., 2023, 158, 116876 CrossRef CAS.
- X. Xiao and W. D. Zhang, RSC Adv., 2011, 1, 1099–1105 RSC.
- J. Sheng, Y. He, J. Li, C. Yuan, H. Huang, S. Wang, Y. Sun, Z. Wang and F. Dong, ACS Nano, 2020, 14, 13103–13114 CrossRef CAS PubMed.
- X. Xiao and W. Zhang, RSC Adv., 2011, 1, 1099–1105 RSC.
- X. Liu, J. Xiao, S. Ma, C. Shi, L. Pan and J. Zou, ChemNanoMat, 2021, 7, 684–698 CrossRef CAS.
- X. Meng and Z. Zhang, J. Mol. Catal. A: Chem., 2016, 423, 533–549 CrossRef CAS.
- S. Sun and W. Wang, RSC Adv., 2014, 4, 47136–47152 RSC.
- F. Ma, Y. Wu, Y. Shao, Y. Zhong, J. Lv and X. Hao, Nano Energy, 2016, 27, 466–474 CrossRef CAS.
- Z. Zhao and M. Miyauchi, Angew. Chem., Int. Ed., 2008, 47, 7051–7055 CrossRef CAS PubMed.
- G. Dai, J. Yu and G. Liu, J. Phys. Chem. C, 2012, 116, 15519–15524 CrossRef CAS.
- L. Chen, J. He, Y. Liu, P. Chen, C. Au and S. Yin, Chin. J. Catal., 2016, 37, 780–791 CrossRef CAS.
- S. C. Wang, L. Z. Wang and W. Huang, J. Mater. Chem. A, 2020, 8, 24307–24352 RSC.
- K. Qin, Q. Zhao, H. Yu, X. Xia, J. Li, S. He, L. Wei and T. An, Environ. Res., 2021, 199, 111360 CrossRef CAS PubMed.
- L. Zhang, Y. Li, Q. Li, J. Fan, S. A. C. Carabineiro and K. Lv, Chem. Eng. J., 2021, 419, 129484 CrossRef CAS.
- R. Kumar, P. Raizada, N. Verma, A. Hosseini Bandegharaei, V. K. Thakur, Q. V. Le, V. H. Nguyen, R. Selvasembian and P. Singh, J. Cleaner Prod., 2021, 297, 126617 CrossRef CAS.
- S. Song, Z. Xing, H. Zhao, Z. Li and Z. Wei, Green Energy Environ., 2023, 8, 1232–1264 CrossRef CAS.
- P. Sivasubramanian, J. H. Chang, S. Nagendran, C. D. Dong, M. Shkir and M. Kumar, Chemosphere, 2022, 307, 135652 CrossRef CAS PubMed.
- R. a He, S. Cao, P. Zhou and J. Yu, Chin. J. Catal., 2014, 35, 989–1007 CrossRef CAS.
- R. He, D. Xu, B. Cheng, J. Yu and W. Ho, Nanoscale Horiz., 2018, 3, 464–504 RSC.
- R. A. He, S. W. Cao and J. G. Yu, Acta Phys.-Chim. Sin., 2016, 32, 2841–2870 CAS.
- R. Kumar, P. Raizada, N. Verma, A. Hosseini-Bandegharaei, V. K. Thakur, L. Quyet Van, N. Van-Huy, R. Selvasembian and P. Singh, J. Cleaner Prod., 2021, 297, 126617 CrossRef CAS.
- J. Xiong, P. Song, J. Di, H. Li and Z. Liu, J. Mater. Chem. A, 2019, 7, 25203–25226 RSC.
- M. Li, H. Huang, S. Yu, N. Tian and Y. Zhang, ChemCatChem, 2018, 10, 4477–4496 CrossRef CAS.
- K. Xu, L. Wang, X. Xu, S. X. Dou, W. Hao and Y. Du, Energy Storage Mater., 2019, 19, 446–463 CrossRef.
- L. Sun, M. Hu, M. Liang, Y. Wu and L. Liu, Chem. Ind. Eng. Prog., 2022, 41, 4813–4830 Search PubMed.
- R. Sharma, M. Khanuja, S. N. Sharma and O. P. Sinha, Int. J. Hydrogen Energy, 2017, 42, 20638–20648 CrossRef CAS.
- A. H. Zahid and Q. Han, Nanoscale, 2021, 13, 17687–17724 RSC.
- L. S. Zhang, W. Z. Wang, J. O. Yang, Z. G. Chen, W. Q. Zhang, L. Zhou and S. W. Liu, Appl. Catal., A, 2006, 308, 105–110 CrossRef CAS.
- B. Yu, Chem. Eng. J., 2018, 32, 57–61 CAS.
- W. Zou, W. C. Hao, X. Xin and T. M. Wang, Chin. J. Inorg. Chem., 2009, 25, 1971–1976 CAS.
- T. Karnan and S. Samuel, Ceram. Int., 2016, 42, 4779–4787 CrossRef CAS.
- S. D. Khairnar and V. S. Shrivastava, SN Appl. Sci., 2019, 1, 762 CrossRef.
- Q. Hao, R. T. Wang, H. J. Lu, C. A. Xie, W. H. Ao, D. M. Chen, C. Ma, W. Q. Yao and Y. F. Zhu, Appl. Catal., B, 2017, 219, 63–72 CrossRef CAS.
- T. P. Xie, J. Yang, Y. Penga, J. K. Wang, S. L. Liu, L. J. Xu and C. L. Liu, Mater. Technol., 2019, 34, 843–850 CrossRef CAS.
- M. Chen, J. T. Bi, X. Huang, T. Wang, Z. Wang and H. X. Hao, Chemosphere, 2021, 278, 130386 CrossRef CAS PubMed.
- S. M. Wang, Y. Guan, R. H. Zeng, Z. J. Zhang, L. Liu, Z. Y. Li, W. An and Y. Fu, ChemSusChem, 2019, 12, 4874–4881 CrossRef CAS PubMed.
- Q. Yang, J. B. Zhong, J. Z. Li, J. F. Chen, Z. Xiang, T. Wang and M. J. Li, Curr. Appl. Phys., 2017, 17, 484–487 CrossRef.
- K. S. Al-Namshah and R. M. Mohamed, Appl. Nanosci., 2018, 8, 1233–1239 CrossRef CAS.
- J. A. Zhu, S. H. Wang, J. U. Wang, D. Q. Zhang and H. X. Li, Appl. Catal., B, 2011, 102, 120–125 CrossRef CAS.
- D. Kim and D. Jung, Chem. Phys. Lett., 2017, 674, 130–135 CrossRef CAS.
- H. Lu, Q. Hao, T. Chen, L. Zhang, D. Chen, C. Ma, W. Yao and Y. Zhu, Appl. Catal., B, 2018, 237, 59–67 CrossRef CAS.
- S. Majumder, N. D. Quang, T. T. Hien, N. D. Chinh, H. Yang, C. Kim and D. Kim, J. Alloys Compd., 2021, 870, 159545 CrossRef CAS.
- G. S. Jiang, X. D. Zhang, C. Liu, H. Ma, H. Yu and F. Wang, Vacuum, 2020, 181, 109759 CrossRef CAS.
- Y. N. Bai, T. Y. Ouyang, X. R. Li, Y. W. Yan, Z. S. Kong, X. L. Ma, Z. Li, Z. D. Li, X. M. Cai, J. M. Cai and H. L. Tan, J. Alloys Compd., 2023, 933, 167814 CrossRef CAS.
- H. F. Bao, X. Q. Cui, C. M. Li, Y. Gan, J. Zhang and J. Guo, J. Phys. Chem. C, 2007, 111, 12279–12283 CrossRef CAS.
- P. Hu, Y. Cao and B. Lu, Mater. Lett., 2013, 106, 297–300 CrossRef CAS.
- Y. Zhou, M. Wang, Z. Yang, H. Yin and S. Ai, Sens. Actuators, B, 2015, 206, 728–734 CrossRef CAS.
- Z. M. Li and Y. Tian, Photonics, 2022, 9, 790 CrossRef CAS.
- J. Gao, Y. Ding, K. Yan and J. Zhang, J. Mater. Chem. B, 2022, 10, 3524–3530 RSC.
- M. Wang, Y. Xue, J. H. Zhu, A. J. Wang, L. P. Mei and P. Song, New J. Chem., 2021, 45, 22833–22838 RSC.
- M. Ganapathy, Y. Hsu, J. Thomas, L. Y. Chen, C. T. Chang and V. Alagan, Energy Fuels, 2021, 35, 14995–15004 CrossRef CAS.
- Y. Bessekhouad, D. Robert and J. V. Weber, J. Photochem. Photobiol., A, 2004, 163, 569–580 CrossRef CAS.
- X. Li, R. Huang, Y. Hu, Y. Chen, W. Liu, R. Yuan and Z. Li, Inorg. Chem., 2012, 51, 6245–6250 CrossRef CAS PubMed.
- I. M. Kobasa and G. P. Tarasenko, Theor. Exp. Chem., 2002, 38, 255–258 CrossRef CAS.
- S. Zheng, Z. Li, T. Lu, J. Wang, Y. Wang, Y. Cui, Z. Zhang, M. He and B. Song, Comput. Theor. Chem., 2023, 1225, 114170 CrossRef CAS.
- H. Steinberg, D. R. Gardner, Y. S. Lee and P. Jarillo-Herrero, Nano Lett., 2010, 10, 5032–5036 CrossRef CAS PubMed.
- R. He, S. Ou, Y. Liu, Y. Liu and D. Xu, Chin. J. Catal., 2022, 43, 370–378 CrossRef CAS.
- J. Lei, N. Qie, J. Zhou, Y. Hua and T. Ji, Mater. Lett., 2012, 83, 108–111 CrossRef CAS.
- Y. H. Chuai, Y. F. Wang and Y. Bai, Opt. Mater., 2023, 140, 113804 CrossRef CAS.
- D. Li, J. Lao, C. Jiang, C. Luo, R. Qi, H. Lin, R. Huang, G. I. N. Waterhouse and H. Peng, Int. J. Hydrogen Energy, 2019, 44, 30876–30884 CrossRef CAS.
- Z. M. Yuan and Z. Y. Jiang, Molecules, 2023, 28, 4400 CrossRef CAS PubMed.
- Z. Zhao and W. Dai, Inorg. Chem., 2014, 53, 13001–13011 CrossRef CAS PubMed.
- Z. Wang, Z. Chu, C. Dong, Z. Wang, S. Yao, H. Gao, Z. Liu, Y. Liu, B. Yang and H. Zhang, ACS Appl. Nano Mater., 2020, 3, 1981–1991 CrossRef CAS.
- H. An, Y. Du, T. Wang, C. Wang, W. Hao and J. Zhang, Rare Met., 2008, 27, 243–250 CrossRef CAS.
- X. M. Chen, P. Y. Chen, S. M. Yang and H. W. Gao, Nanotechnology, 2023, 34, 052001 CrossRef PubMed.
- W. L. Huang and Q. Zhu, Comput. Mater. Sci., 2008, 43, 1101–1108 CrossRef CAS.
- L. Zhao, X. Zhang, C. Fan, Z. Liang and P. Han, Phys. B, 2012, 407, 3364–3370 CrossRef CAS.
- Y. Liu, B. Yang, H. He, S. Yang, X. Duan and S. Wang, Sci. Total Environ., 2022, 804, 150215 CrossRef CAS PubMed.
- K. L. Zhang, C. M. Liu, F. Q. Huang, C. Zheng and W. D. Wang, Appl. Catal., B, 2006, 68, 125–129 CrossRef CAS.
- X. Zhang, R. Li, M. Jia, S. Wang, Y. Huang and C. Chen, Chem. Eng. J., 2015, 274, 290–297 CrossRef CAS.
- X. Xiao, J. Jiang and L. Zhang, Appl. Catal., B, 2013, 142–143, 487–493 CrossRef CAS.
- J. Zhang, J. Wu, P. Lu, Q. Liu, T. Huang, H. Tian, R. Zhou, J. Ren, B. Yuan, X. Sun and W. Zhang, Mater. Lett., 2017, 186, 353–356 CrossRef CAS.
- M. Zhao, C. Q. Fu, K. J. Wang, Y. Zhang, Y. M. Xia, Q. Zhang, C. D. Li, M. C. Liu, Z. H. Zhang and W. J. Wang, J. Alloys Compd., 2021, 852, 156698 CrossRef CAS.
- X. Su and D. Wu, Mater. Sci. Semicond. Process., 2018, 80, 123–130 CrossRef CAS.
- M. T. Le, J. Van Craenenbroeck, I. Van Driessche and S. Hoste, Appl. Catal., A, 2003, 249, 355–364 CrossRef CAS.
- D. H. He, W. Ueda and Y. Moro-Oka, Catal. Lett., 1992, 12, 35–44 CrossRef CAS.
- A. Bhakoo, G. C. Bond, R. D. Rees, B. Sauerhammer, A. O. Taylor and I. York, Catal. Lett., 1999, 57, 55–60 CrossRef CAS.
- C. Q. Zhang, Q. Zhou, C. Xu, X. Liu, Y. Tan and W. Y. Huang, Nonferrous Met. Mater. Eng., 2021, 12, 56–65 CAS.
- Y. F. Zhao, Q. Y. Mao, X. Y. Zhai and G. Y. Zhang, Prog. Chem., 2021, 33, 1331–1343 CAS.
- Y. Jia, Y. Lin, Y. Ma and W. Shi, Mater. Lett., 2019, 234, 83–86 CrossRef CAS.
- D. D. Wang, Z. X. Lin, H. J. Gu and H. Y. Li, Prog. Chem., 2023, 35, 606–619 CAS.
- B. Senthilkumar, R. K. Selvan, L. Vasylechko and M. Minakshi, Solid State Sci., 2014, 35, 18–27 CrossRef CAS.
- K. Lai, W. Wei, Y. Zhu, M. Guo, Y. Dai and B. Huang, J. Solid State Chem., 2012, 187, 103–108 CrossRef CAS.
- Y. X. Qin, S. C. Liu, X. Shen, H. Y. Gui and Y. N. Bai, J. Alloys Compd., 2022, 894, 162534 CrossRef CAS.
- M. Z. Sun, P. Y. Guo, M. Wang and F. Y. Ren, Optik, 2019, 199, 163319 CrossRef CAS.
- S. N. Lou, J. Scott, A. Iwase, R. Amal and Y. H. Ng, J. Mater. Chem. A, 2016, 4, 6964–6971 RSC.
- Y. P. Zhou, W. Y. Jiao, Y. Xie, F. He, Y. Ling, Q. Yang, J. S. Zhao, H. Ye and Y. Hou, J. Colloid Interface Sci., 2022, 608, 2213–2223 CrossRef CAS PubMed.
- J. L. Li, X. J. Liu, Z. Sun and L. K. Pan, Ceram. Int., 2015, 41, 8592–8598 CrossRef CAS.
- A. Phuruangrat, S. Buapoon, T. Bunluesak, P. Suebsom, S. Thongtem and T. Thongtem, J. Aust. Ceram. Soc., 2022, 58, 71–82 CrossRef CAS.
- A. Phuruangrat, P. Dumrongrojthanath, S. Thongtem and T. Thongtem, Mater. Lett., 2017, 194, 114–117 CrossRef CAS.
- Z. Dai, F. Qin, H. P. Zhao, F. Tian, Y. L. Liu and R. Chen, Nanoscale, 2015, 7, 11991–11999 RSC.
- L. N. Wang, X. Q. Shi, Y. F. Jia, H. F. Cheng, L. Wang and Q. Z. Wang, Chin. Chem. Lett., 2021, 32, 1869–1878 CrossRef CAS.
- S. Gofurov, N. Uezono, L. G. Oktariza, J. Q. Liu, S. Pawar, M. M. Islam and T. Sakurai, Jpn. J. Appl. Phys., 2023, 62, SK1051 CrossRef.
- T. D. Nguyen, V. H. Nguyen, S. Nanda, D. V. N. Vo, V. H. Nguyen, T. V. Tran, L. X. Nong, T. T. Nguyen, L. G. Bach, B. Abdullah, S. S. Hong and T. V. Nguyen, Environ. Chem. Lett., 2020, 18, 1779–1801 CrossRef CAS.
- A. Ul Islam, M. N. H. Liton, H. M. T. Islam, M. Al Helal and M. Kamruzzaman, Chin. Phys. B, 2017, 26, 036301 CrossRef.
- Z. Zhao, Z. Li and Z. Zou, Phys. Chem. Chem. Phys., 2011, 13, 4746–4753 RSC.
- A. Kudo, K. Omori and H. Kato, J. Am. Chem. Soc., 1999, 121, 11459–11467 CrossRef CAS.
- G. S. Kamble, T. S. Natarajan, S. S. Patil, M. Thomas, R. K. Chougale, P. D. Sanadi, U. S. Siddharth and Y. C. Ling, Nanomaterials, 2023, 13, 1528 CrossRef CAS PubMed.
- J. Su, L. Guo, N. Bao and C. A. Grimes, Nano Lett., 2011, 11, 1928–1933 CrossRef CAS PubMed.
- Y. Liu, B. Huang, Y. Dai, X. Zhang, X. Qin, M. Jiang and M. H. Whangbo, Catal. Commun., 2009, 11, 210–213 CrossRef CAS.
- S. Okunaka, H. Kameshige, S. Oozu, K. Sayama and H. Tokudome, Jpn. J. Appl. Phys., 2023, 62, SK1030 CrossRef.
- K. Ding, B. Chen, Z. Fang, Y. Zhang and Z. Chen, Phys. Chem. Chem. Phys., 2014, 16, 13465–13476 RSC.
- X. Zhang, Y. Huang, F. Ma, Z. Zhang and X. Wei, J. Phys. Chem. Solids, 2018, 121, 85–92 CrossRef CAS.
- Y. Hu, D. Li, Y. Zheng, W. Chen, Y. He, Y. Shao, X. Fu and G. Xiao, Appl. Catal., B, 2011, 104, 30–36 CrossRef CAS.
- H. Y. Jiang, J. H. He, C. Y. Deng, X. D. Hong and B. Liang, Molecules, 2022, 27, 8698 CrossRef CAS PubMed.
- J. Ning, J. Zhang, R. Dai, Q. Wu, L. Zhang, W. B. Zhang, J. F. Yan and F. C. Zhang, Appl. Surf. Sci., 2022, 579, 152219 CrossRef CAS.
- A. Elaouni, M. El Ouardi, A. BaQais, M. Arab, M. Saadi and H. Ait Ahsaine, RSC Adv., 2023, 13, 17476–17494 RSC.
- Y. Liang and J. W. Shi, J. Inorg. Organomet. Polym. Mater., 2020, 30, 2872–2880 CrossRef CAS.
- T. Chen, L. Liu, C. Hu and H. Huang, Chin. J. Catal., 2021, 42, 1413–1438 CrossRef CAS.
- K. Lai, W. Wei, Y. Dai, Z. Ruiqin and B. Huang, Rare Met., 2011, 30, 166–172 CrossRef CAS.
- K. Akihiko and H. Satoshi, Chem. Lett., 1999, 1103–1104 Search PubMed.
- L. Zhang and Y. Zhu, Catal. Sci. Technol., 2012, 2, 694–706 RSC.
- S. Murcia-López, M. C. Hidalgo and J. A. Navío, Photochem. Photobiol., 2013, 89, 832–840 CrossRef PubMed.
- Y. H. Zhang and Y. J. Xu, RSC Adv., 2014, 4, 2904–2910 RSC.
- J. Ren, W. Wang, L. Zhang, J. Chang and S. Hu, Catal. Commun., 2009, 10, 1940–1943 CrossRef CAS.
- X. Guo, D. Wu, X. Long, Z. Zhang, F. Wang, G. Ai and X. Liu, Mater. Charact., 2020, 163, 110297 CrossRef CAS.
- S. Bera, S. Samajdar, S. Pal, P. S. Das, L. A. H. Jones, H. Finch, V. R. Dhanak and S. Ghosh, Ceram. Int., 2022, 48, 35814–35824 CrossRef CAS.
- M. Shang, W. Wang, L. Zhang, S. Sun, L. Wang and L. Zhou, J. Phys. Chem. C, 2009, 113, 14727–14731 CrossRef CAS.
- Y. Yang, R. Z. Ouyang, L. N. Xu, N. Guo, W. W. Li, K. Feng, L. Ouyang, Z. Y. Yang, S. Zhou and Y. Q. Miao, J. Coord. Chem., 2015, 68, 379–397 CrossRef CAS.
- Q. F. Han, Chem. Eng. J., 2021, 414, 127877 CrossRef CAS.
- M. Xu, J. Yang, C. Sun, L. Liu, Y. Cui and B. Liang, Chem. Eng. J., 2020, 389, 124402 CrossRef CAS.
- S. Su, Q. Han, X. Wang and J. Zhu, Appl. Surf. Sci., 2018, 455, 616–621 CrossRef CAS.
- J. Jiang, K. Zhao, X. Xiao and L. Zhang, J. Am. Chem. Soc., 2012, 134, 4473–4476 CrossRef CAS PubMed.
- Y. Lin, C. Lu and C. Wei, J. Alloys Compd., 2019, 781, 56–63 CrossRef CAS.
- C. B. Zhang, X. P. Tao, W. C. Jiang, J. X. Guo, P. F. Zhang, C. Li and R. G. Li, Acta Phys.-Chim. Sin., 2024, 40, 2303034 Search PubMed.
- B. Wang, L. Guo and T. He, RSC Adv., 2016, 6, 30115–30124 RSC.
- W. Shi, M. Li, X. Huang, H. Ren, F. Guo, Y. Tang and C. Lu, Chem. Eng. J., 2020, 394, 125009 CrossRef CAS.
- Y. Huo, J. Zhang, M. Miao and Y. Jin, Appl. Catal., B, 2012, 111–112, 334–341 CrossRef CAS.
- J. Di, J. Xia, H. Li, S. Guo and S. Dai, Nano Energy, 2017, 41, 172–192 CrossRef CAS.
- Y. Huang, Y. Zhu, S. Chen, X. Xie, Z. Wu and N. Zhang, Adv. Sci., 2021, 8, 2003626 CrossRef CAS PubMed.
- L. P. Chen, C. E. Li, Y. F. Zhao, J. Wu, X. K. Li, Z. W. Qiao, P. He, X. M. Qi, Z. H. Liu and G. Q. Wei, Chem. Eng. J., 2021, 425, 131599 CrossRef CAS.
- S. S. Wu, Z. F. Xu, J. L. Zhang and M. S. Zhu, Sol. RRL, 2021, 5, 2100668 CrossRef CAS.
- M. A. Hamza, A. N. El-Shazly, S. A. Tolba and N. K. Allam, Chem. Eng. J., 2020, 384, 123351 CrossRef CAS.
- D. Ma, J. Zhao, Y. Zhao, X. Hao and Y. Lu, Chem. Eng. J., 2012, 209, 273–279 CrossRef CAS.
- F. Gottschalk and B. Nowack, J. Environ. Monit., 2011, 13, 1145–1155 RSC.
- B. Stieberova, M. Zilka, M. Ticha, F. Freiberg, P. Caramazana-González, J. McKechnie and E. Lester, J. Cleaner Prod., 2019, 241, 118325 CrossRef.
- E. L. Cuéllar, A. Martínez-de la Cruz, K. H. L. Rodríguez and U. O. Méndez, Catal. Today, 2011, 166, 140–145 CrossRef.
- K. Bijanzad, A. Tadjarodi, O. Akhavan and M. M. Khiavi, Res. Chem. Intermed., 2016, 42, 2429–2447 CrossRef CAS.
- L. W. Lu, M. L. Lv, G. Liu and X. X. Xu, Appl. Surf. Sci., 2017, 391, 535–541 CrossRef CAS.
- L. N. Thi, H. Tran Huu, T. N. Ngoc, N. S. M. Viswanath, H. T. T. Le, T. T. T. Phan, L. T. Nguyen, Q. T. H. Ta, H. Le Han, L. N. Tan and V. Vo, J. Alloys Compd., 2023, 960, 170503 CrossRef CAS.
- Z. Shen, Q. Han, W. Liu, X. Wang and J. Zhu, J. Mater. Sci., 2019, 54, 613–624 CAS.
- D. Bokov, A. Turki Jalil, S. Chupradit, W. Suksatan, M. Javed Ansari, I. H. Shewael, G. H. Valiev and E. Kianfar, Adv. Mater. Sci. Eng., 2021, 2021, 5102014 Search PubMed.
- D. Navas, S. Fuentes, A. Castro-Alvarez and E. Chavez-Angel, Gels, 2021, 7, 275 CrossRef CAS PubMed.
- D. Sánchez-Rodríguez, M. G. Méndez Medrano, H. Remita and V. Escobar-Barrios, J. Environ. Chem. Eng., 2018, 6, 1601–1612 CrossRef.
- Y. F. Cui, P. P. Dang, F. H. Wang, P. P. Yuan, W. Liu and Y. P. Pu, Vacuum, 2023, 210, 111899 CrossRef CAS.
- R. V. William, A. Marikani and P. Thiruramanathan, J. Mater. Sci.: Mater. Electron., 2018, 29, 10129–10140 CrossRef CAS.
- T. Xian, H. Yang, J. F. Dai, Z. Q. Wei, J. Y. Ma and W. J. Feng, Mater. Lett., 2011, 65, 1573–1575 CrossRef CAS.
- Y. Xi, C. G. Hu, X. M. Zhang, Y. Zhang and Z. L. Wang, Solid State Commun., 2009, 149, 1894–1896 CrossRef CAS.
- M. Han, H. Guo, B. Li, J. Jia and W. Wang, New J. Chem., 2017, 41, 4820–4827 RSC.
- J. Yin, Z. Tan, H. Hong, J. Wu, H. Yuan, Y. Liu, C. Chen, C. Tan, F. Yao, T. Li, Y. Chen, Z. Liu, K. Liu and H. Peng, Nat. Commun., 2018, 9, 3311 CrossRef PubMed.
- F. Wang, L. Li, W. Huang, L. Li, B. Jin, H. Li and T. Zhai, Adv. Funct. Mater., 2018, 28, 1802707 CrossRef.
- J. Li, Z. X. Tang, X. G. Tang, Q. X. Liu and Y. P. Jiang, FlatChem, 2021, 28, 100266 CrossRef CAS.
- C. Kumari, I. Varun, S. Prakash Tiwari and A. Dixit, Superlattices Microstruct., 2018, 120, 67–74 CrossRef CAS.
- R. F. Service, Science, 2019, 365, 108 CrossRef CAS PubMed.
- J. Gao, Q. Huang, Y. Wu, Y. Q. Lan and B. Chen, Adv. Energy Sustainability Res., 2021, 2, 2100033 CrossRef CAS.
- Y. M. Xin, C. F. Me and Y. Q. Miu, Nonferrous Met. Mater. Eng., 2020, 41, 38–45 Search PubMed.
- Y. Jiang, Q. Chen, D. Wang, X. Li, Y. Xu, Z. Xu and G. Guo, Nano Res., 2023, 16, 6661–6669 CrossRef CAS.
- Y. Zhang, Y. Chen, R. Liu, X. Wang, H. Liu, Y. Zhu, Q. Qian, Y. Feng, M. Cheng and G. Zhang, InfoMat, 2023, 5, e12375 CrossRef CAS.
- B. Thomas, C. Tang, M. Ramírez-Hernández and T. Asefa, ChemPlusChem, 2023, 88, e202300104 CrossRef CAS PubMed.
- J. Wang, D. J. Wu, M. H. Li, X. B. Wei, X. M. Yang, M. H. Shao and M. Gu, Nano Lett., 2022, 22, 5600–5606 CrossRef CAS PubMed.
- L. Ge, Y. Ke and X. Li, Chem. Commun., 2023, 59, 5795–5806 RSC.
- Q. Guo, C. Zhou, Z. Ma and X. Yang, Adv. Mater., 2019, 31, 1901997 CrossRef CAS PubMed.
- W. J. Shin, A. H. Granados, H. Hu and M. Tao, ECS Meeting Abstracts, 2015, 2, 790 CrossRef.
- M. Shi, H. Yang, Z. Zhao, G. Ren and X. Meng, Chem. Commun., 2023, 59, 4274–4287 RSC.
- X. Jin, L. Ye, H. Xie and G. Chen, Coord. Chem. Rev., 2017, 349, 84–101 CrossRef CAS.
- Y. Bai, P. Yang, L. Wang, B. Yang, H. Xie, Y. Zhou and L. Ye, Chem. Eng. J., 2019, 360, 473–482 CrossRef CAS.
- K. Wang, L. Zhang, Y. Su, S. Sun, Q. Wang, H. Wang and W. Wang, Catal. Sci. Technol., 2018, 8, 3115–3122 RSC.
- X. Wang, Y. Wang, M. Gao, J. Shen, X. Pu, Z. Zhang, H. Lin and X. Wang, Appl. Catal., B, 2020, 270, 118876 CrossRef CAS.
- X. Fan, Crit. Rev. Environ. Sci. Technol., 2022, 52, 2227–2269 CrossRef.
- F. Saadati, N. Keramati and M. M. Ghazi, Crit. Rev. Environ. Sci. Technol., 2016, 46, 757–782 CrossRef CAS.
- J. Di, J. Xia, M. Ji, S. Yin, H. Li, H. Xu, Q. Zhang and H. Li, J. Mater. Chem. A, 2015, 3, 15108–15118 RSC.
- T. Kanagaraj, P. S. M. Kumar, R. Thomas, R. Kulandaivelu, R. Subramani, R. N. Mohamed, S. Lee, S. W. Chang, W. J. Chung and D. D. Nguyen, Environ. Res., 2022, 205, 112439 CrossRef CAS PubMed.
-
S. Iyyapushpam, S. T. Nishanthi and D. P. Padiyan, International Conference on Advanced Nanomaterials and Emerging Engineering Technologies (ICANMEET), Chennai, India, 2013.
- J. Zhang, Y. Wang, Y. Wang, X. Shuai, R. Zhao, U. A. Abubakr Yasin, T. Guo, J. Du and J. Li, Environ. Sci.: Nano, 2022, 9, 2979–2989 RSC.
- T. Bavani, J. Madhavan, S. Prasad, M. S. AlSalhi and M. J. AlJaafreh, Environ. Pollut., 2021, 269, 116067 CrossRef CAS PubMed.
- Z. Long, T. Guo, C. Chen, G. Zhang and J. Zhu, Front. Microbiol., 2023, 14, 1210790 CrossRef PubMed.
- Y. Wei, Z. Zhang, W. Wang, Z. Song, M. Cai and S. Sun, ChemPhysChem, 2023, 24, e202300216 CrossRef CAS PubMed.
- J. Shang, W. Hao, X. Lv, T. Wang, X. Wang, Y. Du, S. Dou, T. Xie, D. Wang and J. Wang, ACS Catal., 2014, 4, 954–961 CrossRef CAS.
- M. Zhu, Z. Sun, M. Fujitsuka and T. Majima, Angew. Chem., Int. Ed., 2018, 57, 2160–2164 CrossRef CAS PubMed.
- D. Ding, Z. Jiang, D. Ji, M. Nosang Vincent and L. Zan, Chem. Eng. J., 2020, 400, 125931 CrossRef CAS.
- Y. Huang, N. Zhang, Z. Wu and X. Xie, J. Mater. Chem. A, 2020, 8, 4978–4995 RSC.
- D. Wu, R. Wang, C. Yang, Y. An, H. Lu, H. Wang, K. Cao, Z. Gao, W. Zhang, F. Xu and K. Jiang, J. Colloid Interface Sci., 2019, 556, 111–119 CrossRef CAS PubMed.
- Y. Zhang, S. Gu, X. Zhou, K. Gao, K. Sun, D. Wu, J. Xia and X. Wang, Catal. Sci. Technol., 2021, 11, 4783–4792 RSC.
- C. Xiao, H. Hu, X. Zhang and D. R. MacFarlane, ACS Sustainable Chem. Eng., 2017, 5, 10858–10863 CrossRef CAS.
- Q. Wang, J. Du, R. Ouyang, B. Liu, Y. Miao and Y. Li, Coord. Chem. Rev., 2023, 492, 215281 CrossRef CAS.
- Y. Li, X. Tan, H. Wang, X. Ji, Z. Fu, K. Zhang, W. Su, J. Zhang and D. Ni, Nano Res., 2023, 16, 9885–9893 CrossRef CAS.
- L. Xiao, A. Zhu, Q. Xu, Y. Chen, J. Xu and J. Weng, ACS Appl. Mater. Interfaces, 2017, 9, 6931–6940 CrossRef CAS PubMed.
- M. Wu, J. Yong, H. Zhang, Z. Wang, Z. P. Xu and R. Zhang, Adv. Healthcare Mater., 2023, 2301497 CrossRef CAS PubMed.
Footnote |
† These authors contributed equally. |
|
This journal is © The Royal Society of Chemistry 2024 |
Click here to see how this site uses Cookies. View our privacy policy here.