Superior conductive 1D and 2D network structured carbon-coated Ni-rich Li1.05Ni0.88Co0.08Mn0.04O2 as high-ion-diffusion cathodes for lithium-ion batteries†
Received
8th August 2024
, Accepted 10th November 2024
First published on 5th December 2024
Abstract
Numerous studies have addressed the low electrical conductivity of Li1.05Ni0.88Co0.08Mn0.04O2 (Ni-rich NCM). Among these approaches, surface treatment using multiwalled carbon nanotubes (MWCNTs) has emerged as a promising strategy for enhancing the depolarization of Ni-rich NCM and improving its electrochemical performance. However, MWCNT coatings applied by various methods often result in agglomeration and increase the ion-transfer resistance of the coating layer, leading to degraded electrochemical performance. In this study, 1D and 2D network structures are assembled on Ni-rich NCM surfaces using a MWCNT solution dispersed in ethanol solvent by an incipient method. The resulting highly conductive network structure facilitates electron movement without interfering with Li-ion transport, enhancing the depolarization of Ni-rich NCM and enabling high electrochemical performance. The 1D and 2D network structure coated Ni-rich NCM exhibits an excellent rate capability of 87.64% at 3C/0.2C and a cycle retention of 94.53% after 50 cycles at 1C/1C. Moreover, the incipient method used herein effectively maximizes the electrochemical performance with less coating weight than other methods. These findings highlight the potential of the 1D and 2D network structure coated Ni-rich NCM for advanced energy storage applications.
1. Introduction
The development of high-performance cathode materials is crucial for advancing lithium-ion batteries (LIBs) with improved energy densities, power densities, and cycle retention performance. Ni-rich layered-oxide cathodes have emerged as promising candidates for next-generation LIBs owing to their high specific capacities and lower cost compared to other cathode materials. Ni-rich NCM (nickel, cobalt, and manganese) cathodes offer a combination of advantages: Ni provides high specific capacity, while Co and Mn enhance the layered structure and structural integrity.1–4 However, a significant challenge of using Ni-rich NCM cathodes is their poor electronic conductivity, which limits overall battery performance. To address this issue, various strategies have been developed, including the incorporation of conductive additives like multiwalled carbon nanotubes (MWCNTs), single-walled carbon nanotubes (SWCNTs), and carbon coatings through surface modifications of the cathode active materials.5–8 In this study, we present a novel approach to improve the electrical conductivity of the Ni-rich NCM cathode by surface modification with a small amount of MWCNTs. We systematically investigate the effects of MWCNT loading on the electrochemical performance of the Ni-rich NCM cathode, focusing on specific capacity, rate capability, and cycling stability. Our results demonstrate that the 1D and 2D network structures formed on the surfaces of the cathode materials via incipient and mechano-fusion coating methods significantly enhance electronic conductivity, suppress side reactions with electrolytes, and facilitate Li+ mobility, leading to improved electrochemical performance.9–12 The study employs various characterization techniques, including X-ray diffraction (XRD), Raman spectroscopy, and scanning electron microscopy (SEM), to analyze the impacts of these surface modifications on the cathode materials. The incipient and mechano-fusion coating methods, which achieve uniform 1D and 2D network structures on the cathode surface, exhibit superior electrochemical performances compared to other methods. Electrochemical evaluations revealed that the incipient method exhibited the highest initial discharge capacity, excellent rate capability, and superior capacity retention after 50 cycles. Electrochemical impedance spectroscopy (EIS) analysis confirmed that the incipient method effectively reduced polarization and charge transfer resistance (RCT), contributing to the improved electrochemical performance.
This study provides valuable insights into the design of high-performance cathode materials for next-generation LIBs, with important implications for the development of practical and cost-effective energy storage devices.
2. Experimental
2.1. Preparation of MWCNT-coated Ni-rich NCM
Li1.05Ni0.88Co0.08Mn0.04O2 (Umicore Co., Ltd, Belgium) powder was used in the experiments. MWCNTs (purchased, length: 5–15 μm) were coated over the NCM powder using four different methods, namely ball milling (BM), only mechano-fusion (OM), division, and incipient methods, as detailed in Fig. S1 (ESI†).
2.1.1. Ball milling (BM) method.
The Ni-rich NCM material was coated with MWCNTs using a ball milling machine (GLBM-G, GLOBAL LAB, Korea). The NCM powder and 0.5 wt% MWCNTs were mixed in a weight ratio of 80
:
20. Several 1 mm sized zirconia balls and a 45 ml zirconia ball were used for the BM process. The rotation speed was set to 200 rpm, and the milling duration was 24 h. After ball milling, the powder was mixed using a Spheric Coater (KM Tech, Korea) at 3000 rpm for 30 min.
2.1.2. Only mechano-fusion (OM) method.
The Ni-rich NCM material was coated with MWCNTs using a Spheric Coater (KM Tech, Korea). A rotating four-way coating blade, positioned 5 mm from the wall, operated at a high rotational speed of 3000 rpm. The 0.3 wt% MWCNTs and NCM were subjected to shear stress and compressive force in the gap between the container and blade, allowing the MWCNTs to acquire sufficient thermal energy to fuse onto the NCM surfaces, thus achieving coating.
2.1.3. Division method.
This method is similar to the OM method, but with 0.5 wt% of MWCNT divided into six parts and added sequentially. This approach optimizes the coating process and prevents uneven coating of the MWCNTs on the active material surface when introduced into the mechano-fusion equipment at once.
2.1.4. Incipient method.
The maximum amount of solvent absorbable by the Ni-rich NCM was first determined. The NCM active material was evenly spread in a 400 ml beaker, and MWCNTs dispersed in ethanol solution were gradually added. The solution was uniformly added dropwise for absorption after wetting the active material along the beaker wall. Once the entire material was in contact with the solution, additional material was added until the solution overflowed. About 0.4 wt% MWCNTs dispersed in ethanol was uniformly added to 0.05 wt% of the active material using the described method and dried in an oven at 120 °C for 4 hours. The dried powder, now mixed with CNTs, was coated by mechano-fusion using a Spheric Coater (KM Tech, Korea) at 3000 rpm for 30 min.
2.2. Electrochemical measurement of coin half cells
Electrochemical properties were tested using R2032-type coin cells with a Li-metal anode. Composite electrodes containing 92 wt% active materials, 4 wt% conductive carbon (Super P), and 4 wt% polyvinylidene fluoride (PVdF) binder were cast onto 20 μm aluminum foil as current collectors, with an active material loading of approximately 7 mg cm−2 (±3%). The electrodes were dried at 120 °C and pressed to achieve an electrode density of 3.6 mg cm−3 (±3%). The electrolyte used was 1 mol L−1 of LiPF6 dissolved in a mixture of ethylene carbonate and diethylene carbonate (EC
:
DEC = 1
:
1). The R2032-type coin cells were assembled in a glove box under an argon atmosphere.
2.3. Electrochemical measurement of pouch cells
For pouch cells, one side-coated NCM88 electrodes composed of 92 wt% active material, 4 wt% carbon black, and 4 wt% PVdF with an aerial mass loading of 13.82–14.07 mg cm−2 were prepared, resulting in an areal capacity of 3.084 mA h cm−2. Two side-coated graphite electrodes at a mass loading of 8.40 mg cm−2 and an areal capacity of 3.24 mA h cm−2 were used as the anode, with an N/P ratio balanced at 1.05. The separators and electrodes were stacked using a z-folding machine (Wellcos WCR-ZS-M). Each cell contained two cathode sheets, one anode sheet, and a 15 μm separator. Aluminum and copper tabs were welded to the cathode and anode, respectively, using the z-folding machine. The z-folded electrode-separator compound was sealed in a pouch after adding 400 μl of electrolyte (1.0 M LiPF6 in EC
:
DEC, 1
:
1 vol%). Galvanostatic cycling was performed at 1C (180 mA g−1) and 45 °C using a WONIK PNE CC 05–10 cycler.
3. Results and discussion
Fig. 1 describes the roles of the 1D and 2D network structures on the surface of Li1.05Ni0.88Co0.08Mn0.04O2 (Ni-rich NCM). Electron movements in the MWCNTs are not affected by the 1D and 2D network structures as the MWCNTs have less agglomerations than the cathode surface coated with Ni-rich NCM by the usual dry-coating methods. Therefore, an increase in electron conductivity and suppression of side reactions with electrolytes can be achieved effectively. Additionally, due to the complex 1D and 2D structures, there is less interference to Li+ ion movement than those with other surface modifications covering the entire active material,13–15 which may contribute to an increase in the overall electrochemical performance. Fig. 2(a) presents the XRD pattern of each cathode active material, including pristine NCM, for the BM, OM, division, and incipient methods of coating NCM. All peaks in the XRD patterns are indexed based on a layered hexagonal α-NaFeO2 structure with the R
m space group, and no impurity peaks are observed.5,16 The split peaks of (006)/(102) and (018)/(110) are clearly observed in all samples at around 38° and 65°, respectively, indicating well-ordered layered structures with rare cation mixing and well-defined layered structures.6,16,17 The ratios of the (003)/(104) values are summarized in Table 1 and noted to vary slightly depending on the MWCNT content, with values between 1.2 and 1.5. High ratios of the (003)/(104) values indicate excellent layered structures with high cation ordering. Therefore, it can be concluded that the structure of the Ni-rich NCM is not affected by appropriate amounts of the MWCNT surface modifications.5,16–18 Raman measurements were performed to analyze the structural and chemical states of the carbon layer and Ni-rich NCM. Fig. 2(b) shows the Raman spectra of the pristine and incipient samples. The peaks observed at 1351, 1587, and 2704 cm−1 are assigned to the 1D, G, and G′(2D) bands of the MWCNTs, respectively.5,18–21 The D band, which is commonly induced by the disorder phonon mode vibrations of the sp2 carbon atoms, originates from the defects. The relative strength of the D band reflects the degree of defects contained in the carbon material.18,19 The G band is caused by a first-order Raman scattering process within carbon, which is related to a doubly degenerate phonon mode at the Brillouin zone center. The 2D or G′ band is related to the second-order Raman scattering spectra of carbon. The obtained results confirm that the MWCNTs are adequately coated on the surface of the Ni-rich NCM.5,18,19,21 The presence or absence of the MWCNT coating and morphology according to the coating method was confirmed through SEM, as shown in Fig. 3. SEM images of the pristine NCM, as well as BM, OM, division, and incipient methods of NCM are presented in Fig. 3(a–j). The particle shapes before and after coating are similar, and the average particle has a similar shape with a diameter of 2–4 μm. Impurities are observed on the pristine surface in Fig. 3(a and b); however, no impurities are seen in the CNT-coated samples in Fig. 3(c–j). Furthermore, it was confirmed that MWCNTs were agglomerated on the surfaces of the cathode active material of the samples coated with CNTs by the BM and OM methods, as shown in Fig. 3(c–f). The division method was used to solve the MWCNT agglomeration phenomenon; however, agglomeration was still found, as shown in Fig. 3(g and h). In addition, unlike OM, it can be confirmed that the coating method is performed by adding MWCNTs little by little and it is layered. On the other hand, the incipient method did not show MWCNT agglomeration, and it was confirmed that the surface was uniformly coated in 1D (fiber, yellow) and 2D (dot, red) patterns, as shown in Fig. 3(i and j). Therefore, the 1D and 2D CNT coatings by the incipient method are expected to produce excellent electrochemical performances due to the smooth mobility of Li+ ions by suppression of MWCNT aggregation and the existing network of fibers and dots. The incipient method allows uniform surface modifications with MWCNT dispersion on the Ni-rich NCM cathode materials, which prevents agglomeration of the MWCNTs and relatively uniformly distributes the MWCNTs on the surface of the cathode active material in the form of 1D structures like fibers. In addition, the OM method is used to apply mechanical heat and shear stress to mash the MWCNTs so that they exist on the cathode active material surface in the form of 2D-structured dots. This means that the MWCNTs must be configured in the right direction to provide high electronic conductivity by overcoming the disadvantages.22,23 When coating the surface of the cathode active material by a general surface-treatment method, Li+ ion mobility can be disturbed by the coating material during (de)lithiation of Li+ ions during charge/discharge cycling, thereby increasing the Li+ ion-transfer resistance.4,12,24,25 However, the 1D and 2D network structures created by surface coating of the cathode active material using the intensive and OM methods not only improve electron conductivity but also interfere with the relatively low Li+ ion mobility owing to the structural characteristics, thereby improving electrochemical performance.
 |
| Fig. 1 The role of 1D and 2D network structures on the surface of the Ni-rich NCM. | |
 |
| Fig. 2 (a) XRD patterns of the pristine, OM, division, BM, incipient samples and (b) Raman spectra of the pristine and incipient samples. | |
Table 1
I
(003)/I(104) ratios of the pristine and MWCNT-coated Ni-rich NCM samples
|
Pristine |
BM |
OM |
Division |
Incipient |
I
(003)/I(104) |
1.39 |
1.19 |
1.21 |
1.48 |
1.39 |
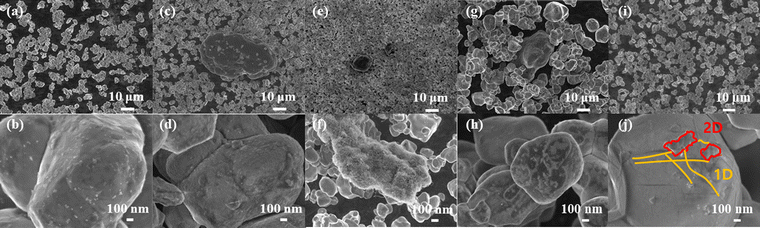 |
| Fig. 3 The SEM images of the samples using the (a) and (b) Ni-rich NCM pristine, (c) and (d) Ball milling method (BM), (e) and (f) only mechano-fusion (OM), (g) and (f) division and (i) and (j) incipient methods. | |
To confirm the effects of the MWCNT coating uniformity, electrochemical evaluations were conducted, as shown in Fig. 4. Fig. 4(a) presents the initial charge/discharge capacity in the range of 2.8–4.3 V at 0.1C and 25 °C. The initial discharge capacities of pristine as well as BM, OM, division, and incipient NCM were 207.35, 201.62, 207.96, 200.09, and 209.4 mA h g−1, respectively, with the incipient method exhibiting the highest discharge capacity. Fig. 4(b) shows the rate capability range of 0.2–3C, where the discharge capacity of the pristine NCM ranged from 197.13 to 171.76 mA h g−1. Furthermore, the discharge capacities of the BM, OM, division, and incipient methods were 193.66–171.16 mA h g−1, 205.62–160.87 mA h g−1, 191.76–167.63 mA h g−1, and 202.04–177.57 mA h g−1 for 0.2–3C, respectively. The rate capabilities of the pristine, BM, OM, division, and incipient samples were 87.13%, 78.24%, 88.38%, 87.89%, and 87.42%, respectively, with the incipient method exhibiting the best performance. Fig. 4(c) shows the cycle retention performances of the pristine, BM, OM, division, and incipient samples at a rate of 1C in the range of 2.8–4.3 V. The initial discharge capacities were 193.23 mA h g−1 (pristine), 188.06 mA h g−1 (BM), 187.02 mA h g−1 (OM), 185.97 mA h g−1 (division), and 194.51 mA h g−1 (incipient). After the 50th cycle, the discharge capacity retentions of the pristine, BM, OM, division, and incipient samples were 91.27%, 94.38%, 93.19%, 94.53%, and 94.42%, respectively. Consequently, the incipient method, which exhibited excellent electrochemical performance, demonstrates facile electronic and ion conductivities with uniformly coated 1D and 2D network multidimensional structures.
 |
| Fig. 4 (a) Initial charge–discharge curves at 0.1C/0.1C and 25 °C, cycled between 2.8 V and 4.3 V with the Li metal anode, and (b) rate capabilities at 25 °C with an increase in the discharge current from 0.2C to 3C and 0.2C and (c) cycling performances at 25 °C for the pristine and BM, OM, division, and incipient samples. | |
The Nyquist plots of all samples after the 1st, 25th, and 50th cycles are shown in Fig. 5(a–c), respectively, and the impedance behaviors of the resistances were analyzed using the IviumSoft program based on the equivalent circuit shown in each plot. The resistance between the electrode and electrolyte, RS, was observed, and the semicircle in the high-frequency range represents the surface layer resistance, RSEI.26 The semicircle in the mid-frequency range indicates the charge-transfer resistance at the electrode–electrolyte interface, RCT. Additionally, the Warburg line, W, observed in the low-frequency range, is attributed to Li+ ion diffusion into the bulk electrode material, and the capacitances or constant phase elements, CPESEI and CPECT, are respectively coupled with RSEI and RCT.9,10,27 The impedance behaviors of the pristine NCM and incipient methods are well described by the Nyquist plots.28,29Table 2 presents the fitted data of RS and RCT. The change ratio of RCT is reduced due to the improved electronic conductivity of the incipient sample. Fig. 5(c) displays the Nyquist plots of the pristine NCM and incipient samples after 50 cycles. As observed in the figure, RCT occupies a significant portion of the resistance compared to RS, indicating that RCT is a crucial factor for the capacity retention of the cathode active material. According to Table 2, the incipient sample exhibits a lower RCT increase rate than the pristine sample after the 50th cycle, indicating that the coating material forms a protective layer on the surface of the cathode active material to reduce side reactions and maintain reversibility of the electrochemical reaction by increasing the electrical conductivity.9,30,31 Therefore, the 1D and 2D network structures on the surface of the Ni-rich NCM not only suppress side reactions with the electrolyte but also effectively reduce polarization.5,16,31
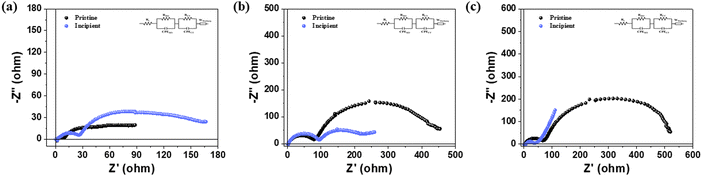 |
| Fig. 5 EIS spectra of the pristine and incipient samples at 25 °C in the (a) initial state, (b) after 25 cycles and (c) after 50 cycles. | |
Table 2 EIS-based RS and RCT values of the pristine and incipient samples at the 1st, 25th, and 50th cycles in the Nyquist plots
|
1st cycle |
25th cycle |
50th cycle |
R
S (Ω) |
R
CT (Ω) |
R
S (Ω) |
R
CT (Ω) |
R
S (Ω) |
R
CT (Ω) |
Pristine |
2.28 |
49.51 |
2.97 |
362.5 |
3.62 |
464.46 |
Incipient |
2.31 |
112.2 |
3.28 |
120.6 |
7.28 |
225.0 |
The galvanostatic intermittent titration technique (GITT) curves of the pristine, BM, OM, division, and incipient electrode samples after the formation cycle in the voltage range of 2.8–4.3 V (versus Li+/Li) are shown in Fig. 6(a). The cell was cycled using a current of 0.2C for 2400 s, followed by open-circuit relaxation of 2400 s to achieve a steady-state voltage (Es).
 |
| Fig. 6 (a) GITT curves of the pristine, BM, OM, division and incipient samples, (b) t vs. E profile of each sample for a single GITT titration and (c) chemical diffusion coefficient in the charge cycling. | |
Fick's 2nd law of diffusion assumes that chemical diffusion follows a certain pattern.28,29Fig. 6(b) shows a typical t vs. E profile for a single titration. On the basis of the GITT measurements, the diffusion equation of DLi+ can be written as follows:
|  | (1) |
where
mB,
Vm, and
MB are the mass, molecular volume, and molecular weight of the active material, respectively,
S is the contact area between the electrode and electrolyte, and
L is the thickness of the electrode without the Al substrate. Herein,
eqn (1) can be simplified as
| 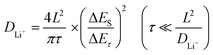 | (2) |
From
eqn (2), it can be observed that the Li-ion chemical diffusion in pristine NCM is 1.41 × 10
−8 cm
2 s
−1, and those for the BM, OM, division, and incipient samples are 9.22 × 10
−9, 9.68 × 10
−9, 9.14 × 10
−9, and 1.03 × 10
−8 cm
2 s
−1, respectively, in the voltage range of 2.8–4.3 V.
29 Furthermore, as depicted in
Fig. 1, the incipient method with surface treatment of 1D and 2D structures demonstrates higher ion diffusivity due to less disturbance in the Li
+ ion transfer path than the usual island-type dry-coated (BM, OM, division) methods. As the concentration of Li increased to approximately half the voltage range, the chemical diffusion reached its maximum around 3.7 V.
32Fig. 6(c) shows the variation of

as a function of the voltage during charge cycling. The chemical diffusion coefficients strongly depended on the electrochemical process, as shown in
Fig. 6(c); the reactions in the plateau area are very complex, which include not only Li
+ ion diffusion but also oxygen loss and structural phase changes. In this region, the obtained

values should be regarded as pseudo or apparent diffusion coefficients.
28,29 The extremely small

values observed in the plateau region indicate that the electrochemical reactions involved in this process are severely sluggish; this may be attributed to the high kinetic barriers associated with concurrent Li
+ ion extraction, oxygen loss, and structural rearrangement. Any oxygen losses and structural rearrangements would be complete after two GITT cycles.
33 It is thus shown that the incipient method not only improves Li
+ ion mobility but also prevents phase change and acceleration of oxygen release compared to other CNT coating methods. Moreover, we assessed the full cell electrochemical cycling performances using the Ni-rich NCM pristine and incipient samples with a graphite anode in the pouch-type cell (Fig. S2, ESI
†). After degassing and formation cycling, the 0.2C/0.2C discharge capacities of the pristine and incipient samples are shown in
Fig. 7(a); the pristine and incipient samples deliver 62.495 and 57.333 mA h, respectively. The cycling retentions of the pristine and incipient samples in the pouch-type cell are presented in
Fig. 7(b). It is verified that unlike the capacity difference in early cycling due to the initial capacity difference shown in
Fig. 7(a), the capacity retention rate in the incipient sample is higher as the 1.0C/1.0C charge/discharge continues. In particular, even after 100 cycles, the incipient sample showed a capacity retention rate exceeding 87.6% at 45 °C compared to 80.9% for the pristine sample at 45 °C.
 |
| Fig. 7 (a) Volumetric capacity curves of pristine and incipient pouch full cells at 0.2C/0.2C and 45 °C, cycled between 3.0 V and 4.2 V, and (b) cycling performances of pristine and incipient pouch full cells at 45 °C. | |
4. Conclusion
This study investigated the roles of 1D and 2D network structures on the surfaces of Ni-rich NCM cathode materials and their impacts on the electrochemical performance.22 It is demonstrated that the 1D and 2D network structures do not interfere with electron movements in the MWCNTs, which effectively increase electron conductivity and suppress side reactions with electrolytes. Furthermore, these structures showed less interference to Li+ ion movement than other surface modifications, resulting in an enhanced overall electrochemical performance. Various characterization methods, including XRD, Raman spectroscopy, SEM, and electrochemical evaluations, were used to reveal that the incipient coating method provided the most uniform 1D and 2D network multidimensional structures, leading to superior electrochemical performance.5,16,18 Electrochemical evaluations showed that the incipient sample had the highest initial discharge capacity, excellent rate capability, and superior capacity retention after 50 cycles. EIS analysis was used to confirm that the incipient method effectively reduced polarization and RCT, contributing to improved electrochemical performance. Overall, the present study demonstrates that the 1D and 2D network structures on the surface of Ni-rich NCM achieved through the incipient coating method enhance the electrochemical performance by providing high electronic conductivity, suppressing the side reactions, and facilitating smooth Li+ mobility. These findings provide valuable insights for the development of high-performance cathode materials for next-generation LIBs.
Data availability
All data are provided in the paper.
Conflicts of interest
There are no conflicts to declare.
Acknowledgements
This research was supported by the Research Institute of Industrial Science & Technology (RIST, GCU-202209320001). This work was supported by the Gachon University research fund of 2022(GCU-202208780001).
References
- F. Schipper, E. M. Erickson, C. Erk, J.-Y. Shin, F. F. Chesneau and D. Aurbach, J. Electrochem. Soc., 2017, 164, A6220–A6228 CrossRef CAS.
- B. L. Ellis, K. T. Lee and L. F. Nazar, Chem. Mater., 2010, 22, 691–714 CrossRef CAS.
- A. Konarov, S. T. Myung and Y. K. Sun, ACS Energy Lett., 2017, 2, 703–708 CrossRef CAS.
- A. O. Kondrakov, H. Geßwein, K. Galdina, L. De Biasi, V. Meded, E. O. Filatova, G. Schumacher, W. Wenzel, P. Hartmann, T. Brezesinski and J. Janek, J. Phys. Chem. C, 2017, 121, 24381–24388 CrossRef CAS.
- J. Hwang, K. Do and H. Ahn, J. Chem. Eng., 2021, 406, 126813 CrossRef CAS.
- X. Li, X. Zhao, M. S. Wang, K. J. Zhang, Y. Huang, M. Z. Qu, Z. L. Yu, D. S. Geng, W. G. Zhao and J. M. Zheng, RSC Adv., 2017, 7, 24359–24367 RSC.
- A. Varzi, C. Täubert, M. Wohlfahrt-Mehrens, M. Kreis and W. Schütz, J. Power Sources, 2011, 196, 3303–3309 CrossRef CAS.
- H. R. Ong, C. W. Woon, M. S. Ahmad, A. Yousuf, C. K. Cheng and M. M. R. Khan, Int. J. Electrochem. Sci., 2018, 13, 7789–7799 CrossRef CAS.
- K. Park, J. H. Park, S. G. Hong, B. Choi, S. Heo, S. W. Seo, K. Min and J. H. Park, Sci. Rep., 2017, 7, 1–10 CrossRef PubMed.
- H. H. Ryu, G. T. Park, C. S. Yoon and Y. K. Sun, Small, 2018, 14, 1–8 Search PubMed.
- Y. Ma, M. Xu, J. Zhang, R. Liu, Y. Wang, H. Xiao, Y. Huang and G. Yuan, J. Alloys Compd., 2020, 848, 1–8 Search PubMed.
- D. Arumugam and G. P. Kalaignan, Electrochim. Acta, 2010, 55, 8709–8716 CrossRef CAS.
- H. Yang, K. Du, G. Hu, Z. Peng, Y. Cao, K. Wu, Y. Lu, X. Qi, K. Mu and J. Wu, Electrochim. Acta, 2018, 289, 149–157 CrossRef CAS.
- K. Wu, K. Du and G. Hu, J. Mater. Chem. A, 2018, 6, 3444–3453 RSC.
- C. W. Park, J. H. Lee, J. K. Seo, W. Y. Jo, D. Whang, S. M. Hwang and Y. J. Kim, Nat. Commun., 2021, 12, 2145 CrossRef CAS PubMed.
- S. J. Sim, S. H. Lee, B. S. Jin and H. S. Kim, Sci. Rep., 2020, 10, 11114 CrossRef CAS PubMed.
- K.-S. Lee, S.-T. Myung, K. Amine, H. Yashiro and Y.-K. Sun, J. Electrochem. Soc., 2007, 154, A971 CrossRef CAS.
- Y. Gao, L. Y. Li, P. H. Tan, L. Q. Liu and Z. Zhang, Chin. Sci. Bull., 2010, 55, 3978–3988 CrossRef CAS.
- L. M. Malard, M. A. Pimenta, G. Dresselhaus and M. S. Dresselhaus, Phys. Rep., 2009, 473, 51–87 CrossRef CAS.
- A. C. Ferrari, J. C. Meyer, V. Scardaci, C. Casiraghi, M. Lazzeri, F. Mauri, S. Piscanec, D. Jiang, K. S. Novoselov, S. Roth and A. K. Geim, Phys. Rev. Lett., 2006, 97, 187401 CrossRef CAS PubMed.
- A. Keszler, L. Nemes, A. M. Keszler, L. Nemes, S. R. Ahmad and X. Fang, J. Optoelectron. Adv. Mater., 2004, 6, 1269–1274 CAS.
- S. H. Park, P. J. King, R. Tian, C. S. Boland, J. Coelho, C. Zhang, P. McBean, N. McEvoy, M. P. Kremer, D. Daly, J. N. Coleman and V. Nicolosi, Nat. Energy, 2019, 4, 560–567 CrossRef CAS.
- Y. S. Zhang, H. L. Zhu, D. Yao, P. T. Williams, C. Wu, D. Xu, Q. Hu, G. Manos, L. Yu, M. Zhao, P. R. Shearing and D. J. L. Brett, Sustainable Energy Fuels, 2021, 5, 4173–4208 RSC.
- B. C. Park, H. B. Kim, S. T. Myung, K. Amine, I. Belharouak, S. M. Lee and Y. K. Sun, J. Power Sources, 2008, 178, 826–831 CrossRef CAS.
- Y. S. Lee, W. K. Shin, A. G. Kannan, S. M. Koo and D. W. Kim, ACS Appl. Mater. Interfaces, 2015, 7, 13944–13951 CrossRef CAS PubMed.
- S. Na and K. Park, Int. J. Energy Res., 2022, 46, 7389–7398 CrossRef CAS.
- H. H. Sun and A. Manthiram, Chem. Mater., 2017, 29, 8486–8493 CrossRef CAS.
- A. Nickol, T. Schied, C. Heubner, M. Schneider, A. Michaelis, M. Bobeth and G. Cuniberti, J. Electrochem. Soc., 2020, 167, 090546 CrossRef CAS.
- W. Zheng, M. Shui, J. Shu, S. Gao, D. Xu, L. Chen, L. Feng and Y. Ren, Bull. Mater. Sci., 2013, 36, 495–498 CrossRef CAS.
- W. Tang, Z. Chen, H. Huang, M. Irfan, C. Huang, Z. Yang and W. Zhang, Chem. Eng. Sci., 2021, 229, 116126 CrossRef CAS.
- Q. Gan, N. Qin, Y. Zhu, Z. Huang, F. Zhang, S. Gu, J. Xie, K. Zhang, L. Lu and Z. Lu, ACS Appl. Mater. Interfaces, 2019, 11, 12594–12604 CrossRef CAS PubMed.
- A. Van der Ven and G. Ceder, J. Power Sources, 2001, 97–98, 529–531 CrossRef CAS.
- Z. Li, F. Du, X. Bie, D. Zhang, Y. Cai, X. Cui, C. Wang, G. Chen and Y. Wei, J. Phys. Chem. C, 2010, 114, 22751–22757 CrossRef CAS.
|
This journal is © the Owner Societies 2025 |
Click here to see how this site uses Cookies. View our privacy policy here.