Na-decorated binary spinel ferrite catalysts for the hydrogenation of CO2 to olefins†
Received
13th January 2025
, Accepted 18th February 2025
First published on 19th February 2025
Abstract
Spinel ferrite catalysts, recognized for their unique physicochemical properties, have been extensively employed in CO2 hydrogenation reactions. However, the specific roles of different transition metals in Na-decorated spinel ferrite for CO2 hydrogenation to olefins remain underexplored. In this study, we designed a series of Na-decorated binary spinel ferrites by varying the type of the secondary metals. We found that doping with zinc reduces the hydrogenation ability, which enhances olefin selectivity. Conversely, adding copper facilitates catalyst reduction through H2-spillover, with the CuFe interface increasing alcohol products. CoFe2O4 demonstrated the highest activity and olefin yield. Additionally, CoFe2O4 was found to promote the formation of the carbide phase and enhance the activation and dissociation of hydrogen, significantly boosting catalytic performance. Our findings pave the way for developing Na-decorated spinel catalysts tailored for selective olefin synthesis, with important implications for improving the efficiency of CO2 hydrogenation processes.
Introduction
The increasing concentration of CO2 in the atmosphere is closely related to climate issues such as global warming.1 From a sustainability standpoint, CO2 is a readily available and cost-effective carbon-based resource.2 As a result, substantial effort has been invested in developing efficient CO2 capture and utilization systems.3 The direct hydrogenation of CO2 into value-added chemicals has garnered considerable attention during the past decades.4–9 Among the various carbon cycle options, the catalytic hydrogenation of CO2 to olefins, using inexpensive hydrogen derived from renewable energy sources, stands out a promising route.10 However, CO2 hydrogenation typically results in the formation of C1 products, presenting a significant challenge for controlled C–C coupling to produce C2+ olefins.11 This challenge has driven the scientific community to focus on designing and developing more effective catalysts.
Fe-based catalysts are generally recognized as highly active and cost-effective in CO2 hydrogenation to olefins, due to their intrinsic activity in both the reverse water gas shift (RWGS) reaction and the Fischer–Tropsch synthesis (FTS) process.12 It is widely accepted that Fe3O4 and Fe5C2 are the primary active phases responsible for the RWGS reaction and the FTS process, respectively. Recently, the addition of secondary metals such as Zn2+, Co2+, Fe2+, Cu2+, and Mg2+ to trivalent Fe (Fe3+) forming lattice Fe oxides with spinel structure has emerged as an innovative strategy for designing efficient catalysts to drive the CO2 hydrogenation reaction.13 These catalysts possess unique composition and tunable properties that distinguish them significantly from conventional bulk Fe materials. For instance, Zhang et al. demonstrated that ZnFe2O4 catalyst can enable the RWGS through the in situ formation ZnO and the ultrahigh dispersion of FeOx on the surface, enabling C–C coupling and olefins synthesis over FeCx species.14 Similarly, Kim et al. synthesized the carbon nanotube-supported Na-promoted CoFe2O4 catalysts (Na–CoFe2O4/CNT), which can facilitate the formation of the bimetallic alloy carbide (Fe1−xCox)5C2 phase, differing from the typical χ-Fe5C2 active sites found in Fe-based catalysts, and exhibiting high CO2 conversion and light olefin selectivity.15 Cu is widely used as a reduction promoter and promotes CO2 hydrogenation to alcohols while suppressing the RWGS reaction. Choi et al. used delafossite-CuFeO2 as the catalyst precursor to synthesize CuFe catalyst, achieving high selectivity for liquid hydrocarbons (C5+) and extremely low selectivity for CH4, attributed to rapid reduction and selective carburization to form the Hägg iron carbide (χ-Fe5C2).16 However, previous research on ferrite spinel has mainly focused on the specific spinel catalysts, and a systematic study of different binary spinel ferrites during CO2 hydrogenation process remains largely unexplored.
In this work, we prepared Na-decorated transition metals (Zn, Cu, Co) spinel ferrite catalysts for CO2 hydrogenation to olefins. We investigated the promoting effects of different transition metals with spinel structures using a series of characterization techniques. The NaZnFe catalyst enhances olefin selectivity through electronic interactions, while the CuFe interface in the NaCuFe catalyst increases the production of higher alcohol products. Notably, the NaCoFe catalyst exhibits the best catalytic performance, achieving a CO2 conversion of 33.2% alongside 68.8% olefin selectivity under mild conditions of 320 °C, 1 MPa, and 3000 mL gcat−1 h−1.
Results and discussion
Catalytic performance of Fe-based catalysts in CO2 hydrogenation
Fig. 1 and Table S1† present the catalytic performance of Fe-based catalysts for CO2 hydrogenation under reaction conditions of 320 °C, 1 MPa and 3000 mL gcat−1 h−1. Prior to the incorporation of transition metals, the NaFe catalyst exhibits high selectivity toward olefins (74.8%) at a CO2 conversion of 27.7% and a CO selectivity of 16.8%. The chain growth factor was calculated, yielding an α value of 0.67 for the NaFe catalyst (Fig. S1†). Among the Na-modulated binary spinel ferrite catalysts, the NaZnFe catalyst exhibits similar CO2 conversion rates and CO selectivity, but with an increase in methane production. The findings suggest that the ZnFe2O4 precursor does not significantly enhance Fe-based catalysts for olefin production. The NaCuFe catalyst demonstrates relatively low olefin selectivity (62.2%), while significantly improving alcohol selectivity. Given that CuFe-based catalysts are typically active in synthesizing higher alcohols, we speculate that CuFe2O4 catalyst can regulate the dissociation of CO by forming a Cu–FexCy interface,17,18 promoting the generation of alcohols. The phase separation between Cu and Fe species also results in a decrease in α value (0.64).19 It is worth noting that the CO2 conversion rate increases to 33.2% and the CO selectivity decreases to 12.8% on the NaCoFe catalyst. This indicates that the existence of CoFe2O4 makes an evident contribution to the FTS rate, which will accelerate the consumption of CO intermediate species and further increase the CO2 conversion. However, the increased CH4 selectivity reflects the decrease in chain growth probabilities, which can be evidenced by the α value of 0.54 (Fig. 1c). After comparing the reaction performance of these catalysts, the NaCoFe catalyst emerges as the most effective. Consequently, we explored the effect of varying Co content on the NaCoFe catalyst's performance. With increasing Co content (Fig. 1d and S2†), CO2 conversion gradually rises from 33.2 to 36.0%, and the CO selectivity decreases from 12.8 to 9.1%. Notably, the selectivity of undesirable CH4 further increases, with the NaCoFe (1
:
2) catalyst yielding predominantly CH4 at a selectivity of 56.8%, leading to a further decrease in the α value.
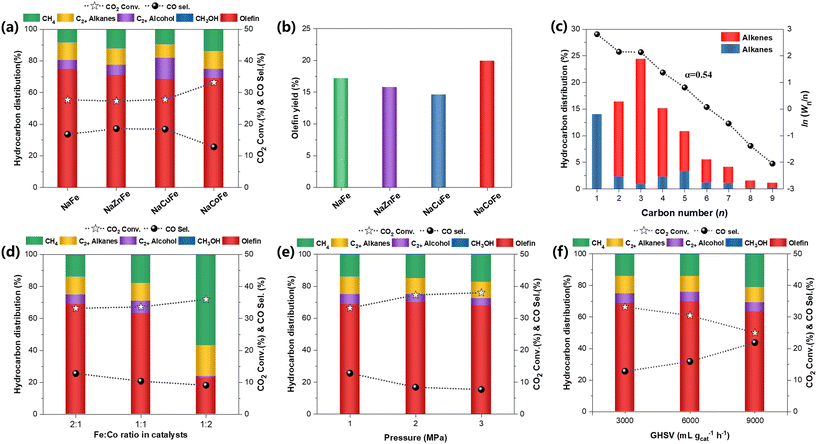 |
| Fig. 1 Catalytic behaviors of CO2 hydrogenation. (a) CO2 conversion, CO selectivity, and CO-free selectivity for the organic product; (b) olefin yield over Fe-based catalysts. (c) the detailed alkane and olefin distribution, the ASF plot and the corresponding α value (α represents the probability of chain growth) over NaCoFe catalyst at 320 °C, 1 MPa, and 3 L gcat−1 h−1; (d) effect of different Fe : Co molar ratio on the catalytic performance at 320 °C, 1 MPa, 3 L gcat−1 h−1; (e) effect of reaction pressure (1–3 MPa) on the catalytic performance at 320 °C, 3 L gcat−1 h−1; (f) effect of gas hourly space velocity (GHSV) on the catalytic performance at 320 °C, 1 MPa. | |
We further investigated the effect of different reaction conditions on the activity of the optimal NaCoFe catalyst. As the reaction pressure increases (Fig. 1e and S3†), the CO2 conversion rate gradually increases while the CO selectivity decreases. Under a pressure of 3 MPa, the CO2 conversion rate and CO selectivity reached 38.0% and 7.7%, respectively. Since the RWGS reaction is a gas volume invariant reaction, the amount of CO generated should be constant. The catalytic results indicate that high pressure promotes more CO molecules for subsequent conversion, thereby further promoting the conversion of CO2. We also tested the reaction performance at different temperatures and found that higher reaction temperatures improve both CO2 conversion and olefin yield (Fig. S4†). This is because the RWGS reaction is endothermic while the hydrogenation reactions of CO are exothermic, thus, raising the temperature favors RWGS reaction, increasing the CO2 conversion. As the reaction gas space velocity gradually increases (Fig. 1f and S5†), the CO2 conversion rate of NaCoFe catalyst decreases, while its CO selectivity increases. The shortened contact time can also lead to an increased selectivity for methane, as C–C coupling becomes more difficult, resulting in a decrease in olefin selectivity from 69.8% to 63.4%. As the GHSV increases from 3 to 9 L gcat−1 h−1, the olefin STY rises from 91 to 169 mg gcat−1 h−1. Despite the decrease in CO2 conversion rate and increase in CO selectivity due to shortened contact time, the overall rate of olefin synthesis significantly improves due to the increased number of CO2 and CO molecules participating in the reaction within the same timeframe. In summary, high temperature, high pressure, and low gas velocity are all beneficial for the conversion of CO2, thereby improving the catalytic activity for olefin synthesis.
Physicochemical properties of Fe based catalysts
The precursor of spinel structure was synthesized by an organic combustion method,20 with Na modified catalysts prepared via impregnation. By controlling the impregnation process, the Na content in all catalysts was maintained at 2 wt%, and the molar ratio of Fe
:
M (M = Zn, Cu, or Co) was adjusted to closely match the stoichiometric ratio of spinel structure for the modified catalysts.
The XRD patterns (Fig. 2a) confirm the successful synthesis of spinel structure (MFe2O4). The XRD analysis of fresh catalyst (Fig. 2b) shows that the spinel structure is still retained after sodium modification. The absence of discrete diffraction peaks relevant to Na2O or MOx (M = Zn, Cu, or Co) indicates that Na species are present in low concentration and are high dispersion within the MFe2O4 bulk matrix. Using the Scherrer equation, we calculated the average crystallite size of a series of catalysts based on the diffraction peak position and half-width of Fe2O3 (110) and MFe2O4 (311). As shown in Table 1, compared to NaFe, the average crystallite size of NaMFe is significantly reduced, with NaCoFe catalyst having the smallest particle size of 7.8 nm, facilitating the formation of more active sites. After H2 reduction (Fig. 2c), XRD patterns for NaFe catalyst show a predominance of metallic iron (Fe0) peaks. For the reduced NaZnFe catalyst, the diffraction peaks belonging to ZnFe2O4 were negligible, whereas those corresponding to α-Fe (PDF#87-0721) and ZnO (PDF#79-2205) were clearly observable. In addition to the presence of α-Fe, the reduced NaCuFe was also found to contain metallic Cu, as evidenced by the peaks located at 43.3° and 50.4° (PDF#70-3039). It is worth noting that CoFe2O4 in NaCoFe catalyst is converted into CoFe alloy (PDF#49-1568) after reduction (Fig. 2d), which is much easier to be carburized than monometallic Fe or Co.21 Upon reaction (Fig. 2e), the spent sample was mainly composed of mainly Fe3O4 and Fe5C2, which is considered as the active phase for RWGS and subsequent FT reaction. The ZnO phase was still visible in the spent NaZnFe catalyst, which has been reported to promote RWGS reaction and enhance stability.14 In the case of the spent NaCuFe catalyst, the Cu remained in metallic form, and Cu–Fe5C2 interface generally considered as the active site for CO2 hydrogenation to alcohol species. It is noteworthy that the diffractions related to Fe3O4 for spent NaCoFe catalyst are weaker than those for other spent catalysts, indicating that the CoFe alloy phase is more prone to carbonization rather than oxidation during CO2 hydrogenation.
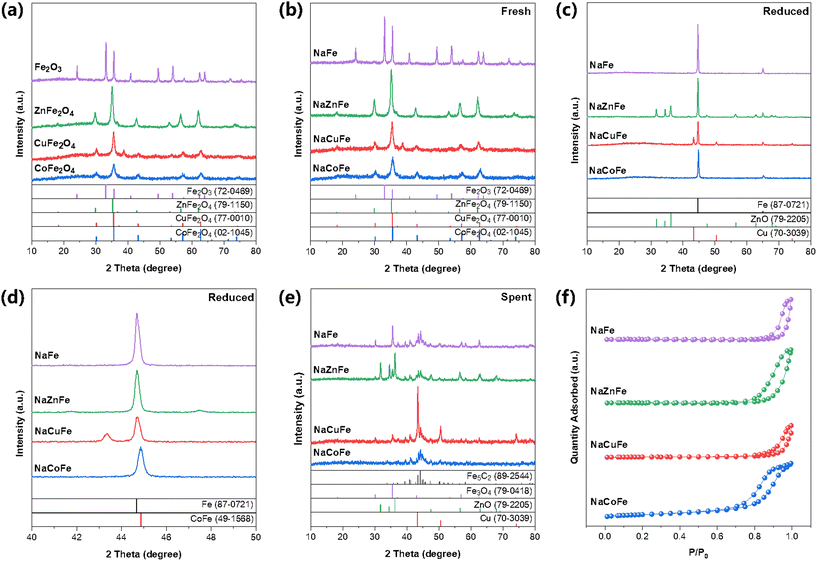 |
| Fig. 2 XRD patterns of the Fe-based catalysts. (a) MFe2O4; (b) after calcination; (c and d) after H2 reduction; (e) after reaction. (f) N2 adsorption–desorption isotherms of fresh catalysts. | |
Table 1 Physical and chemical properties of the Fe-based catalysts
Catalysts |
S
BET
(m2 g−1) |
V
(cm3 g−1) |
D
(nm) |
d
fresh
(nm) |
Nae (wt%) |
A
CO2
(×10−8 a.u.) |
A
H2
(×10−7 a.u.) |
A
C2H4
(×10−6 a.u.) |
BET surface area calculated by the BET method.
BJH Desorption cumulative volume of pores.
BJH Desorption average pore width (4V/SBET).
Calculated by Scherrer equation.
Detected by ICP-AES.
Desorption peak area of CO2 in CO2-TPD.
Desorption peak area of H2 in H2-TPD.
Desorption peak area of C2H4 in C2H4-TPD.
|
NaFe |
7.4 |
0.15 |
28.8 |
43.1 |
1.9 |
17.7 |
3.9 |
4.2 |
NaZnFe |
15.6 |
0.21 |
17.4 |
13.4 |
2.1 |
11.8 |
3.6 |
2.4 |
NaCuFe |
10.5 |
0.13 |
27.7 |
11.7 |
2.0 |
10.4 |
4.3 |
2.2 |
NaCoFe |
55.3 |
0.22 |
11.1 |
7.8 |
1.9 |
10.7 |
4.8 |
1.5 |
SEM images and the corresponding elemental mapping images of the fresh catalysts are shown in Fig. S6 and S7.† These images reveal that Zn (Cu, Co), Fe, and O are uniformly dispersed across the catalysts, while Na is scarcely observed due to its low concentration. Notably, the Na element in NaZnFe is detectable, which may be due to the aggregation of Na and Zn.14,21,22 The N2 adsorption–desorption isotherms of all catalysts exhibit a IV-type isotherm, indicating a characteristic mesoporous structure (Fig. 2f). The formation of spinel structure clearly contributes to an increase in specific surface area (Table 1). Notably, the specific surface area increases significantly from 7.4 m2 g−1 to 55.3 m2 g−1 for the NaCoFe catalyst. Consequently, catalysts with larger specific surface areas are likely to demonstrate improved catalytic performance.
To elucidate specific active sites of spent catalyst, we employed TEM characterizations. TEM images of the spent NaCoFe catalyst (Fig. 3a) show that the catalyst structure consists of numerous nanoparticles with different particle sizes by stacking, which contributes to the formation of abundant mesopores. According to the uniform distribution of three metal elements in the spent NaCoFe catalyst as reflected from the element mapping of their scanning transmission electron microscopy (STEM) images (Fig. 3b), the Co and Fe species are observed to be in close proximity to each other, indicated by the presence of Fe in nearly all areas where Co was detected. As shown in Fig. S9,† Cu and Fe are uniformly distributed in the spent NaCuFe catalyst. However, for the spent NaZnFe catalysts, Zn and Na are predominantly distributed in regions complementary to those of Fe, suggesting a phase separation (Fig. S10†). The above results indicate that Co and Cu are beneficial for the dispersion of active metals. Furthermore, high-resolution transmission electron microscopy (HRTEM) was used to characterize the catalysts after the reaction (Fig. 3c). The lattice spacing of 0.213, 0.208, and 0.205 nm are observed in the spent NaCoFe catalyst, corresponding to Co2C (111), Fe5C2 (021), and Fe5C2 (510) species, respectively. It is important to note that no obvious diffraction peaks of Co2C were observed in the XRD spectrum, indicating that Co2C is well dispersed and has a small particle size. It has been reported that small Co2C nanoparticles with the Co2C (111) surface exposed, favor methane selectivity,23 consistent with our activity testing experimental observations (Fig. 1a). These results suggested that the presence of CoFe alloy phase promotes the formation of Fe5C2 and Co2C during CO2 hydrogenation process. Notably, all four catalysts exhibited a core–shell structure after the reaction, which can be attributed to carbon deposition on the surface of Fe5C2 particles.24,25 The two peaks at 1364 cm−1 and 1585 cm−1 in Raman spectra also confirmed the existence of carbon deposition (Fig. S11†).14
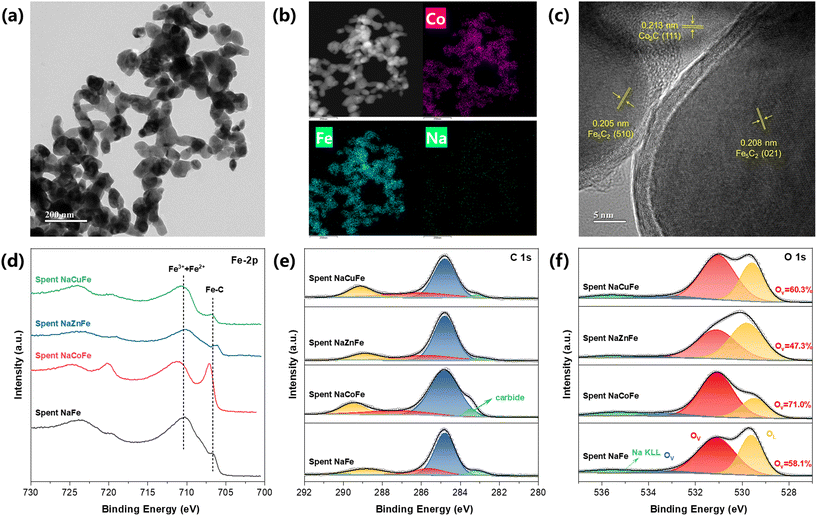 |
| Fig. 3 (a) TEM images; (b) STEM images with corresponding elemental mapping of Co, Fe, Na and (c) HRTEM images of the spent NaCoFe sample. (d) Fe 2p; (e) C 1s and (f) O 1s XPS spectra of the spent Fe-based catalysts. | |
Chemical state and surface analysis of Fe-based catalysts
XPS analysis was performed on the spent samples to determine the chemical state of surface and surface iron carbide. For Fe 2p spectra (Fig. 3d), the spent samples show two broad peak centers, one near 710.5 eV and the other around 724.0 eV, representing Fe 2p3/2 and Fe 2p1/2 spin–orbit, respectively.26 The peak centered around 710.5 eV also suggests that Fe3+ and Fe2+ species are the predominant components present on the surfaces of these spent catalysts.27 The peak centered at 706.6 eV can be assigned to the Fe–C of the Fe5C2 phase.26 Compared to the spent NaFe and NaCuFe, the lowered binding energy of iron carbide species in the spent NaZnFe is due to the electron interactions between Zn and iron species. Notably, an emerging component at 707.0 eV and 720.1 eV is identified in the spent NaCoFe catalyst, corresponding to the alloy carbide phase formed during the reaction.15,28 The increased intensity of the Fe5C2 peak in the spent NaCoFe indicates further progress in surface Fe species carburization, facilitated by the CoFe alloy. C 1s XPS spectra for spent catalysts (Fig. 3e) display four peaks corresponding to C
O, C–O, C
C, and carbides,21 respectively. The abundant iron carbide in the spent NaCoFe is further confirmed by the C 1s spectra, which show a prominent carbide feature at 283.4 eV.29 The O 1s spectrum (Fig. 3f) can be deconvoluted into peaks corresponding to adsorbed oxygen species (OA) at 533.0 eV, oxygen vacancy (OV) at 531.0 eV and oxygen lattice (OL) at 529.5 eV.30 The relative contents of oxygen vacancies among the three oxygen species increase in the order of NaZnFe (47.3%) < NaFe (58.1%) < NaCuFe (60.3%) < NaCoFe (71.0%). This indicates that the intensity of oxygen vacancy peaks is highest in the NaCoFe catalyst. It has been reported that catalysts containing spinel structures can exhibit high catalytic performance for light olefins through oxygen vacancies.31 The surface of NaCoFe catalyst has a higher proportion of oxygen vacancy concentration, which is favorable for catalytic performance.
Reduction and adsorption behavior of Fe-based catalysts
H2-TPR measurements were used to study the promoting effect of transition metals on the catalysts reduction behaviors. As shown in Fig. 4a, the unpromoted NaFe catalyst displays three distinguishable reduction peaks, which reflects the stepwise nature of the reduction of Fe2O3 to metallic Fe. Specifically, the first H2 consumption peak at 431 °C corresponds to the reduction of Fe2O3 to Fe3O4, while the peak around 560 °C and 770 °C are ascribed to the reductions of Fe3O4 to FeO and FeO to metallic Fe, respectively.32,33 The addition of Zn or Co enhances the reducibility of iron oxide species within the ferrite spinel structure. For NaZnFe, the reduction process mirrors that of NaFe, but the peaks shift slightly to lower temperatures due to the formation of small ZnO clusters during synthesis, which further improves the dispersion of the Fe phase and the reduction behavior of the iron catalyst.34 The reduction peaks of NaCoFe also shift towards lower temperatures, but a strong peak is clearly observed at 512 °C, which is due to the overlap between the reduction of CoO to metal Co and the reduction of Fe3O4.35 For NaCuFe, two distinct reduction peaks are observed. The first peak at low temperature (<300 °C) corresponds to the reduction of CuO to Cu and Fe2O3 to Fe3O4, while the broad peak (>400 °C) is ascribed to subsequent conversion of Fe3O4. The shift to lower temperature (or increased reducibility of the catalyst) is likely linked to the H2-activation of Cu site via H2-spillover. The dissociation of hydrogen molecules on the Cu site is much easier than on the iron site, and the dissociated H can overflow from Cu and adsorb onto surrounding iron species, promoting the reduction of the catalyst.36,37
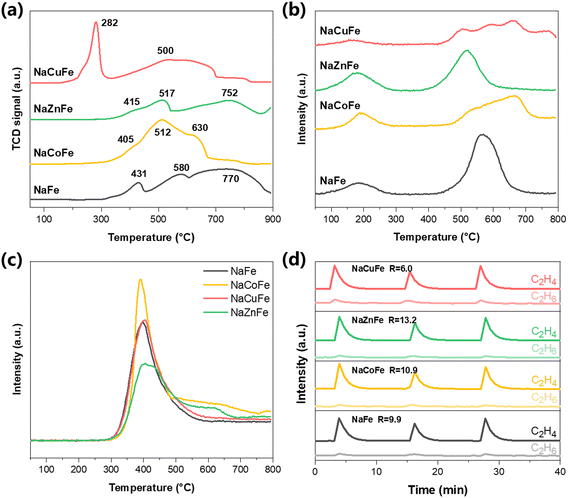 |
| Fig. 4 (a) H2-TPR; (b) CO2-TPD; (c) H2-TPD and (d) C2H4-PTH profiles of the Fe-based catalysts. | |
The effects of transition metals on the spent catalysts were examined using the CO2-TPD measurements, as the CO2 adsorption capacity of Fe-based catalysts is crucial for their performance in CO2 hydrogenation reactions. The adsorption of CO2 by catalysts can be divided into three intensities: weak adsorption at 100–300 °C; medium adsorption at 300–500 °C and strong adsorption at 500–800 °C. As shown in Fig. 4b, all TPD profiles exhibit a broad and low peak at 180 °C, which is indicative of the desorption of CO2 molecules weakly adsorbed within the bulk phase. The main desorption peak located at 500–800 °C corresponds to the desorption of CO2 that strongly interacts with the surface basic sites.38 Obviously, the four catalysts have different strong adsorption sites for CO2, and we calculated the desorption peak area in the high-temperature region, as listed it in Table 1. Although the CO2 adsorption capacity decreases with the formation of spinel structure, the conversion rate of CO2 has not decreased (Fig. 1a). This suggests that CO2 conversion is not solely dependent on its adsorption capacity.
It is well known that the H2 adsorbed onto the catalyst surface enhances the RWGS reaction and facilitates subsequent FT synthesis. To investigate the activation of H2 on the catalyst, H2-TPD experiments were conducted, with the results presented in Fig. 4c and Table 1. It is found that the desorption of H2 from the spent NaCoFe catalyst and NaCuFe catalyst is higher than that of the spent NaFe catalyst, whereas Zn reduces the adsorption capacity of H2. This suggests that CoFe2O4 and Cu2FeO4 effectively trigger H2 spillover, resulting in improved H2 desorption on the NaCoFe and NaCuFe catalysts. Furthermore, the largest amount of H2 desorption is attributed to the highest iron carbide content formed on the used NaCoFe catalyst,39 as corroborated by XPS results. These experimental results indicate that the CO2 conversion rate of different transition metal spinel catalysts is largely constrained by their hydrogenation ability.
Reabsorption reaction behavior of olefins
As a product of FTS reaction, olefins adsorb on the catalyst surface and can re-enter the reaction. Although the hydrogenation ability of the catalyst can promote the improvement of its CO2 conversion rate, excessive hydrogenation ability may also lead to secondary hydrogenation of olefin products on the catalyst surface to form paraffins. Therefore, understanding whether olefins preferentially undergo desorption or hydrogenation on the catalyst is crucial. For this purpose, temperature-programmed desorption of C2H4 measurements (C2H4-TPD) were performed on the spent catalysts. As shown in Fig. S12† and Table 1, the introduction of transition metals reduces the adsorption strength of the catalyst for C2H4, which may facilitate the desorption of olefin products on the catalyst surface.
To further elucidate the impact of transition metals on the secondary hydrogenation capacity of olefins under the reaction conditions, pulse transient hydrogenation (PTH) experiments were employed using C2H4 as the study gas. Before conducting the measurements, the spent catalysts were in situ reduced. Fig. 4d reveals that each catalyst possesses the ability to convert olefins into paraffins under a continuous stream of H2/Ar. The R-value reflects the ability of olefins to undergo secondary hydrogenation on the catalyst surface, with lower R values indicating easier conversion of olefins to alkanes. The ratio of C2H4/C2H6 peak area increases in the order of NaCuFe (6.0) < NaFe (9.9) < NaCoFe (10.9) < NaZnFe (13.2). The highest R value of NaZnFe catalyst may be due to the electron-donating effect from Zn to Fe5C2,40 as confirmed by XPS results (Fig. 4a). According to reports, the presence of Na can hinder the secondary hydrogenation of olefins by reducing the adsorption of olefins on the surface of iron catalysts.19 In this work, the sodium content of the fresh catalysts and spent catalysts is around 2 wt%, as evidenced by ICP-AES analysis (Table 1). This finding suggests that the secondary hydrogenation of olefins to paraffins is suppressed with the addition of Zn or Co, whereas the Cu promoter enhances the capability of secondary hydrogenation of olefins leading to lower selectivity. It is worth noting that in the catalyst activity test, we did not observe a significant increase in the olefin selectivity of NaZnFe and NaCoFe, which may be due to their excessive methane products.
Discussion on the role of transition metals in spinel
Based on our experimental findings, the precursors of spinel structure increase the specific surface area and reduce particle size of the resulting catalysts. Furthermore, these precursors facilitate improved reducibility while promoting dispersion of both transition metal species and active iron sites. Then we propose the following structural evolution for various Na-decorated binary spinel ferrite catalysts (Scheme 1). ZnFe2O4 effectively promotes the reduction of Fe species, transforming into metallic iron and ZnO upon H2 activation. The electronic interactions between ZnO and Fe species in the spent NaZnFe catalyst inhibit secondary olefins hydrogenation, which is beneficial for enhancing olefin selectivity. However, in this work, Zn additive seems to suppress the catalytic performance. This may be due to its weaker dissociation activation ability towards the reactant hydrogen (H2-TPD) and the phase segregation of Zn and Fe (STEM). Conversely, CuFe2O4 significantly enhances catalyst reduction through H2-spillover at the Cu site. However, the strong hydrogenation capability and the Cu–Fe5C2 interface in the spent NaCuFe catalyst lead to increased alcohol production, which reduces olefin yield. CoFe2O4 facilitates the reduction of Co and Fe species, resulting in the formation of CoFe alloy. This alloy readily carbides into Fe5C2 and Co2C during the reaction, and its robust hydrogen activation and dissociation abilities further boost the CO2 conversion rate. Moreover, Co species in CoFe2O4, known for their activity in CO2/CO hydrogenation, accelerate the consumption of intermediates, thereby further increasing CO2 conversion. As a result, the NaCoFe catalyst demonstrates the highest CO2 hydrogenation activity and olefin yield.
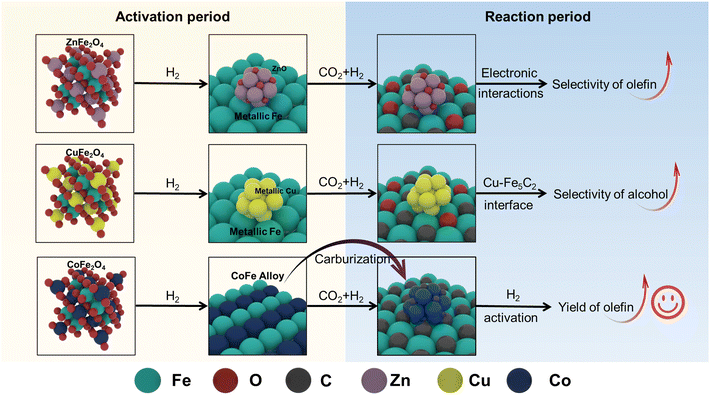 |
| Scheme 1 The structure evolution of different binary spinel ferrite catalysts during the activation and reaction period. | |
Conclusion
In summary, we investigated the effects of different transition metals on the physicochemical properties and catalytic performance of spinel structures during the hydrogenation of CO2. ZnFe2O4 and CuFe2O4 were found to facilitate reduction but decrease olefin yield, whereas CoFe2O4 significantly enhanced both CO2 conversion and olefin yield. Characterization techniques such as physical adsorption, XRD, and chemical adsorption revealed that the CoFe alloy promotes the formation of the carbide phase and enhances the activation and dissociation of hydrogen. This work not only provides new insights into the role of spinel structures in promoting catalytic reactions but also offers fresh perspectives for designing Fe-based catalysts for CO2 hydrogenation.
Data availability
The data supporting this article have been included as part of the ESI.†
Author contributions
The manuscript was written through the contributions of all authors. All authors have approved the final version of the manuscript.
Conflicts of interest
The authors declare no competing financial interest.
Acknowledgements
The support for this project from the Department of Applied Biology and Chemical Technology at the Hong Kong Polytechnic University (PolyU P0049034) is gratefully acknowledged.
Notes and references
- G. A. Meehl, W. M. Washington, W. D. Collins, J. M. Arblaster, A. X. Hu, L. E. Buja, W. G. Strand and H. Y. Teng, Science, 2005, 307, 1769–1772 CrossRef CAS PubMed.
- A. Kätelhön, R. Meys, S. Deutz, S. Suh and A. Bardow, Proc. Natl. Acad. Sci. U. S. A., 2019, 116, 11187–11194 CrossRef PubMed.
- E. V. Kondratenko, G. Mul, J. Baltrusaitis, G. O. Larrazábal and J. Pérez-Ramírez, Energy Environ. Sci., 2013, 6, 3112 RSC.
- R.-P. Ye, J. Ding, W. Gong, M. D. Argyle, Q. Zhong, Y. Wang, C. K. Russell, Z. Xu, A. G. Russell, Q. Li, M. Fan and Y.-G. Yao, Nat. Commun., 2019, 10, 5698 CrossRef CAS PubMed.
- X. Jiang, X. Nie, X. Guo, C. Song and J. G. Chen, Chem. Rev., 2020, 120, 7984–8034 CrossRef CAS PubMed.
- Z. Ma and M. D. Porosoff, ACS Catal., 2019, 9, 2639–2656 CrossRef CAS.
- G. Tian, X. Liang, H. Xiong, C. Zhang and F. Wei, EES Catal., 2023, 1, 677–686 RSC.
- P. Gao, L. Zhang, S. Li, Z. Zhou and Y. Sun, ACS Cent. Sci., 2020, 6, 1657–1670 CrossRef CAS PubMed.
- D. Xu, Y. Wang, M. Ding, X. Hong, G. Liu and S. C. E. Tsang, Chem, 2021, 7, 849–881 CAS.
- D. Goud, R. Gupta, R. Maligal-Ganesh and S. C. Peter, ACS Catal., 2020, 10, 14258–14282 CrossRef CAS.
- Z. Zhang, G. Huang, X. Tang, H. Yin, J. Kang, Q. Zhang and Y. Wang, Fuel, 2022, 309, 122105 CrossRef CAS.
- J. Jiang, C. Wen, Z. Tian, Y. Wang, Y. Zhai, L. Chen, Y. Li, Q. Liu, C. Wang and L. Ma, Ind. Eng. Chem. Res., 2020, 59, 2155–2162 CrossRef CAS.
- J. I. Orege, G. A. Kifle, Y. Yu, J. Wei, Q. Ge and J. Sun, Matter, 2023, 6, 1404–1434 CrossRef CAS.
- C. Zhang, C. Cao, Y. Zhang, X. Liu, J. Xu, M. Zhu, W. Tu and Y.-F. Han, ACS Catal., 2021, 11, 2121–2133 CrossRef CAS.
- K. Y. Kim, H. Lee, W. Y. Noh, J. Shin, S. J. Han, S. K. Kim, K. An and J. S. Lee, ACS Catal., 2020, 10, 8660–8671 CrossRef CAS.
- Y. H. Choi, Y. J. Jang, H. Park, W. Y. Kim, Y. H. Lee, S. H. Choi and J. S. Lee, Appl. Catal., B, 2017, 202, 605–610 CrossRef CAS.
- D. Xu, M. Ding, X. Hong, G. Liu and S. C. E. Tsang, ACS Catal., 2020, 10, 5250–5260 CrossRef CAS.
- T. Liu, D. Xu, M. Song, X. Hong and G. Liu, ACS Catal., 2023, 13, 4667–4674 CrossRef CAS.
- H. Yang, Y. Dang, X. Cui, X. Bu, J. Li, S. Li, Y. Sun and P. Gao, Appl. Catal., B, 2023, 321, 122050 CrossRef CAS.
- H. Yang, Z. Wei, J. Zhang, Y. Dang, S. Li, X. Bu, Z. Zhou, C. Gong, H. Wang, J. Li, Y. Liu, Y. Yang, T. Xiao, C. Liu, Y. Sun and P. Gao, Chem, 2024, 10, 2245–2265 CAS.
- Q. Xu, X. Xu, G. Fan, L. Yang and F. Li, J. Catal., 2021, 400, 355–366 CrossRef CAS.
- P. Zhai, C. Xu, R. Gao, X. Liu, M. Li, W. Li, X. Fu, C. Jia, J. Xie, M. Zhao, X. Wang, Y. Li, Q. Zhang, X. Wen and D. Ma, Angew. Chem., Int. Ed., 2016, 55, 9902–9907 CrossRef CAS PubMed.
- Y. Dai, Y. Zhao, T. Lin, S. Li, F. Yu, Y. An, X. Wang, K. Xiao, F. Sun, Z. Jiang, Y. Lu, H. Wang, L. Zhong and Y. Sun, ACS Catal., 2018, 9, 798–809 CrossRef.
- Y. Zhang, C. Cao, C. Zhang, Z. Zhang, X. Liu, Z. Yang, M. Zhu, B. Meng, J. Xu and Y. Han, J. Catal., 2019, 378, 51–62 CrossRef CAS.
- J. Xu and C. H. Bartholomew, J. Phys. Chem. B, 2005, 109, 2392–2403 CrossRef CAS PubMed.
- J. I. Orege, J. Wei, Y. Han, M. Yang, X. Sun, J. Zhang, C. C. Amoo, Q. Ge and J. Sun, Appl. Catal., B, 2022, 316, 121640 CrossRef CAS.
- Y. Xu, P. Zhai, Y. Deng, J. Xie, X. Liu, S. Wang and D. Ma, Angew. Chem., Int. Ed., 2020, 59, 21736–21744 CrossRef CAS PubMed.
- Y. Liu, Q. Cheng, S. Lyu, X. Li, S. Song, T. Ding, Y. Tian and X. Li, Chem. Eng. J., 2024, 494, 152936 CrossRef CAS.
- P. Du, R. Qi, Y. Zhang, Q. Gu, X. Xu, Y. Tan, X. Liu, A. Wang, B. Zhu, B. Yang and T. Zhang, Chem, 2022, 8, 3252–3262 CAS.
- M. K. Khan, P. Butolia, H. Jo, M. Irshad, D. Han, K.-W. Nam and J. Kim, ACS Catal., 2020, 10, 10325–10338 CrossRef CAS.
- J. Ding, L. Huang, W. Gong, M. Fan, Q. Zhong, A. G. Russell, H. Gu, H. Zhang, Y. Zhang and R.-p. Ye, J. Catal., 2019, 377, 224–232 CrossRef CAS.
- S. Ma, M. Li, G. Wang, L. Zhang, S. Chen, Z. Sun, J. Hu, M. Zhu and W. Xiang, Chem. Eng. J., 2018, 346, 712–725 CrossRef CAS.
- Y. Yang, W. Qian, H. Zhang, Z. Han, H. Ma, Q. Sun and W. Ying, Catal. Sci. Technol., 2022, 12, 4624–4636 RSC.
- J. Zhang, S. Lu, X. Su, S. Fan, Q. Ma and T. Zhao, J. CO2 Util., 2015, 12, 95–100 CrossRef CAS.
- C. Yang, S. Liu, Y. Wang, J. Song, G. Wang, S. Wang, Z.-J. Zhao, R. Mu and J. Gong, Angew. Chem., Int. Ed., 2019, 58, 11242–11247 CrossRef CAS PubMed.
- Z. H. Chonco, L. Lodya, M. Claeys and E. van Steen, J. Catal., 2013, 308, 363–373 CrossRef CAS.
- N. Chaipraditgul, T. Numpilai, C. Kui Cheng, N. Siri-Nguan, T. Sornchamni, C. Wattanakit, J. Limtrakul and T. Witoon, Fuel, 2021, 283, 119248 CrossRef CAS.
- C. Zhang, Y. Yang, B. Teng, T. Li, H. Zheng, H. Xiang and Y. Li, J. Catal., 2006, 237, 405–415 CrossRef CAS.
- Q. Yang, V. A. Kondratenko, S. A. Petrov, D. E. Doronkin, E. Saraci, H. Lund, A. Arinchtein, R. Kraehnert, A. S. Skrypnik, A. A. Matvienko and E. V. Kondratenko, Angew. Chem., Int. Ed., 2022, 61, e202116517 CrossRef CAS PubMed.
- C. Zhang, M. Xu, Z. Yang, M. Zhu, J. Gao and Y.-F. Han, Appl. Catal., B, 2021, 295, 120287 CrossRef CAS.
Footnote |
† Electronic supplementary information (ESI) available: Additional catalytic activity, SEM images, and TPD profiles (PDF). See DOI: https://doi.org/10.1039/d5cy00033e |
|
This journal is © The Royal Society of Chemistry 2025 |
Click here to see how this site uses Cookies. View our privacy policy here.