Development of a novel composite membrane combining polystyrene, polypyrrole, and salian for enhanced scaling prevention in water filtration applications
Received
19th October 2024
, Accepted 22nd November 2024
First published on 4th December 2024
Abstract
A novel composite membrane, comprising polystyrene, polypyrrole, and salian (PSPPY-Sa), was developed through the electro spinning technique to enhance scaling inhibition in water filtration systems. The characterization of the membrane was conducted using FTIR, XRD, and TGA measurements. An extensive study was performed to evaluate the impact of varying salian loadings, ranging from 0 to 20 weight percent, on both the morphological properties and the scaling inhibition performance. To evaluate the anti-scaling properties of the membrane, accelerated scaling tests were performed with a 2000 ppm CaSO4 solution, filtering a synthetic scaling solution. Morphological assessments revealed a uniform distribution of salian microdomains across the fibrous surface of the PSPPY-Sa membrane. Notably, the incorporation of salian at 20% loading achieved a 95% reduction in scale formation, demonstrating superior performance compared to pristine or singly modified membranes. The PSPPY-Sa membrane also demonstrated remarkable thermal stability, underscoring its potential for effective scaling inhibition in water filtration applications.
Water impact
A novel composite membrane, comprising polystyrene, poly pyrrole, and salian (PSPPY-Sa), was developed through the electrospinning technique to enhance scaling inhibition in water filtration systems. This pioneering approach not only addresses the significant problem of scaling in water filtration systems but also contributes to the expansive field of membrane engineering, facilitating the creation of multifunctional membranes with specific properties tailored for a range of applications.
|
1. Introduction
The increasing demand for clean water, coupled with water scarcity, has driven the advancement of sophisticated filtration technologies to tackle issues such as scaling, fouling, and the degradation of membranes.1,2 Among these challenges, scaling is particularly problematic in water filtration systems, resulting in diminished membrane efficiency, heightened energy usage, and the need for regular membrane replacements. Inorganic scales, primarily composed of calcium sulfate (CaSO4) and calcium carbonate (CaCO3), often termed “calcite”, are recognized for their tendency to accumulate within the oil and gas industry. This accumulation results in heightened costs, a significant reduction in production efficiency, and potential harm to equipment.3 Scaling is particularly problematic in industries like oil and gas, where mineral salts often accumulate, leading to significant operational and maintenance expenses. Addressing this issue requires the development of durable and efficient filtration membranes capable of resisting scaling in diverse environments.4,5
Membrane separation is recognized as a sophisticated technology for wastewater treatment, offering benefits such as high operational efficiency, straightforward scalability, and reduced spatial requirements.6–8 Nanofiltration (NF) is regarded as an effective method for water treatment due to its capacity to process a diverse range of water types. As the recovery rate of NF membranes increases, the concentration of sparingly soluble mineral salts also rises on the membrane surface, leading to salt saturation and subsequent inorganic scaling.9–11 This scaling adversely affects the permeate flux of the membrane and shortens its lifespan.12 To mitigate these issues, the use of scale inhibitors is essential for maintaining system stability and longevity, prompting significant research into these substances.13–15 Consequently, the effectiveness of selected antiscalants varies across specific applications, as they impede crystal formation by prolonging the induction time, which in turn delays crystal growth.16,17
Traditionally, the prevention of scale formation has been accomplished through chemical pretreatment or regular cleaning of membranes, methods that can be expensive, environmentally detrimental, and disruptive to ongoing operations. Consequently, the advancement of membranes with built-in anti-scaling features is highly sought after to ensure sustainable and effective water filtration methodologies.18–21 The field of membrane engineering has seen significant progress in recent years, particularly in the incorporation of functional additives into polymeric membrane8,22–24 frameworks to achieve enhanced attributes such as improved hydrophilicity, greater fouling resistance, and effective scaling inhibition.
Within the range of additives, polystyrene (PS) serves as a sturdy and reliable polymer matrix, guaranteeing the membrane's structural integrity and longevity across various operating conditions. PSS, a polymeric inhibitor widely used for industrial scale control, was chosen for this research due to its high heat resistance, calcium tolerance, and absence of phosphorus in its molecular structure.25–27 Polypyrrole (PPy) contributes structural strength and improves the membrane's resistance to chemicals, particularly in challenging water treatment settings. Its selection was based on its outstanding characteristics, including stability in oxidized form, effective redox properties, impressive optical and electrical qualities, high electrical conductivity, and straightforward synthesis method.28,29 Salian, a mineral of natural origin, has garnered significant attention owing to its distinctive features and potential efficacy in scale reduction. As a naturally derived mineral additive, it demonstrates remarkable scale inhibition capabilities. Its unique surface chemistry disrupts the nucleation and growth of scale-forming ions like Ca2+ and SO42−, resulting in a substantial decrease in scale buildup.30,31 The blend of PS, PPy, and salian produces a membrane that achieves a balance between hydrophilicity, porosity, and mechanical strength. This composition simultaneously enhances permeability and resistance to scaling.
This study introduces the development of an innovative composite membrane, which combines polystyrene, polypyrrole, and salian (PSPPY-Sa). These polymer composites, characterized by a polymer matrix enhanced with porous fillers, provide a distinctive solution for effectively preventing scaling in water filtration applications. The strategic amalgamation of these components is intended to yield a durable membrane characterized by improved thermal stability, mechanical integrity, and enhanced resistance to scaling.32
This study introduces a novel composite membrane combining polystyrene, polypyrrole, and salian (PSPPY-Sa) fabricated through electrospinning. This unique combination leverages the mechanical and chemical benefits of each component: polystyrene for stability, polypyrrole for conductivity and structure, and salian for its inherent scaling inhibition properties. By methodically incorporating salian within the polymeric matrix, this research aims to produce a membrane that not only inhibits scaling but also offers improved thermal stability and enhanced filtration performance. The PSPPY-Sa composite membrane demonstrates superior anti-scaling properties, reducing scale formation by up to 95% in high-salinity environments. This innovative approach contributes to sustainable water filtration technology by potentially extending membrane lifespan and reducing the operational demands associated with conventional scaling mitigation techniques.
2. Experimental
2.1. Material
Polystyrene pellets and pyrrole monomer (98% purity) were sourced from Sigma-Aldrich. Salian mineral was extracted from a natural deposit located in the Andes Mountains of Peru and subsequently ground into a fine powder utilizing a ball mill. Ammonium per sulfate (APS, (NH4)2S2O8, ≥98% purity) and p-toluene sulfonic acid (PTSA, C7H8O3S, ≥98.5% purity) were procured from Sigma-Aldrich, serving as the oxidizing agent and dopant, respectively, for the in situ polymerization of pyrrole. N,N-Dimethylformamide (DMF, C3H7NO, ≥99.8% purity) was obtained from Merck and employed as the solvent for the electro spinning solution. All materials were utilized as received without any additional purification.
2.2. Sample preparations
Fig. 1 depicts the preparation of polystyrene–polypyrrole–salian (PSPPY-Sa) composite membranes, which were created through in situ polymerization and electrospinning. The process commenced with the dissolution of polystyrene pellets in DMF at a concentration of 20 wt%, which was achieved by stirring at 60 °C for 2 h to at 1000 rpm, form a consistent solution. In a different vessel, the pyrrole monomer was dissolved in DMF, and APS was added as the oxidizing agent in a molar ratio of 1
:
1.25 (pyrrole
:
APS). Salian powder was then incorporated into the pyrrole/APS solution in varying amounts (0, 5, 10, 15, and 20 wt%) based on the total polymer weight. After stirring for 30 min at 2500 rpm, the pyrrole/APS/salian dispersion was gradually added to the polystyrene solution under vigorous stirring at 4000 rpm. PTSA was then introduced as a dopant at a molar ratio of 0.3 relative to pyrrole. To ensure thorough polymerization of pyrrole and a consistent distribution of salian particles, the PSPPY-Sa solution was stirred for 2 h. The electrospinning configuration included a high-voltage power supply, syringe pump, and grounded rotating drum collector. The solution was transferred into a 10 mL plastic syringe fitted with a 22-gauge blunt-tip needle. The flow rate was set to 1 mL h−1 and the voltage was maintained at 18 kV. The distance between the tip and collector was fixed at 15 cm. Electrospinning was performed at room temperature for 6 h to yield a PSPPY-Sa composite fibrous membrane.30 Following the electrospinning procedure, the membranes were carefully extracted from the collector and placed in a vacuum oven at 50 °C for 24 h to ensure removal of the residual solvent. After drying, the membranes were cut into circular discs with diameters of 47 mm, which were then prepared for subsequent characterization and scaling inhibition testing.
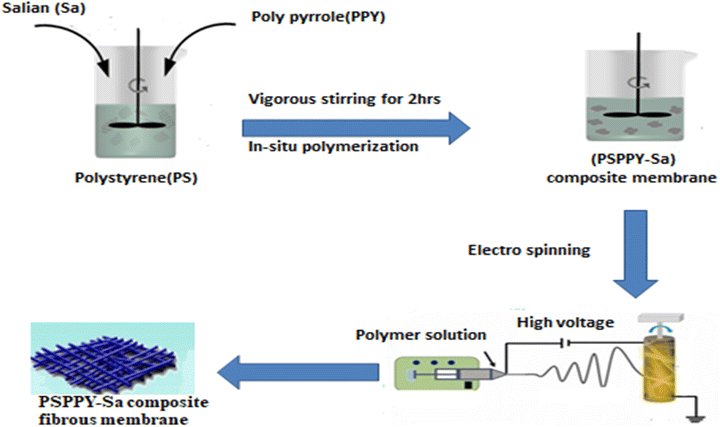 |
| Fig. 1 The in situ polymerization and electro spinning process for fabricating PSPPY-Sa composite membrane. | |
2.3. Characterization
An investigation into the chemical structure and composition of the PSPPY-Sa membranes was performed using Fourier-transform infrared spectroscopy (FTIR, Thermo Scientific Nicolet iS50) and X-ray diffraction (XRD, Bruker D8 Advance). FTIR spectra were recorded within the wavenumber range of 4000–500 cm−1via the attenuated total reflectance (ATR) approach. XRD patterns were acquired utilizing Cu Kα radiation (λ = 1.5406 Å) in the 2θ range of 5–60°, with a step size of 0.02°.30,33 An evaluation of the thermal stability of the membranes was conducted utilizing thermo gravimetric analysis (TGA, TA Instruments Q500). The samples were subjected to a temperature range of 25 °C to 800 °C, with a heating rate set at 10 °C min−1 under a nitrogen atmosphere. The investigation of the surface morphology and elemental composition of the membranes was performed using scanning electron microscopy (SEM, Hitachi SU8010) paired with energy-dispersive X-ray spectroscopy (EDS). To enhance conductivity, the membrane samples were sputter-coated with a thin gold layer prior to imaging.34 Porosity and pore size distribution of the membranes were evaluated through capillary flow porometry (CFP, PMI Inc. CFP-1500AEX). The procedure commenced with the application of a low surface tension liquid (POREWICK) to wet the samples, followed by the use of a wetting liquid (CALSOLV OIL) to fill the pores via capillary action. The measurement of the differential pressure necessary to eliminate the wetting liquid from the pores was conducted, which was then used to compute the pore size distribution.35 The mechanical properties, such as tensile strength and elongation at break, were assessed utilizing a universal testing machine (Instron 5567) in accordance with ASTM D638 standards. Membrane samples were prepared in the form of dumbbell shapes, and the testing was performed at a crosshead speed of 10 mm min−1 under ambient temperature conditions.35
3. Result and discussions
3.1. Structural and chemical characterization
The FTIR spectra for the PS and PSPPY-Sa membranes are illustrated in Fig. 2. Notable bands characteristic of polystyrene are identified at 2990 cm−1 correspond to stretching vibration of aromatic C–H bond, the band observed at 2869 cm−1 related to aliphatic C–H stretching, and the peaks at 1628 and 1471 cm−1 corresponded to C
C stretching of the aromatic ring, as well as the bands at 586 and 526 cm−1 revealed to C–H out-of-plane bending vibrations of the mono substituted benzene ring.36 The PSPPY-Sa spectra exhibits bands which associated with poly pyrrole are observed at 1478 cm−1 and 1407 cm−1 represent to C
C stretching and C–N stretching, respectively, which confirm the successful polymerization of pyrrole. A broad band at 3869 and 3939 cm−1 is linked to the N–H stretching vibrations of poly pyrrole.37 Furthermore, the bands at 1271 and 790 cm−1 are attributed to the Si–O–Si and Si–O stretching vibrations of salian, respectively, signifying the incorporation of the mineral additive within the composite membranes.38 The presence of Si–O–Si and Si–O peaks in the PSPPY-Sa membrane clearly distinguishes it from the pristine PS/PPy membrane. These peaks confirm the successful incorporation of salian within the polymeric matrix. The changes in peak intensities, particularly those associated with polystyrene and polypyrrole (e.g., C
C and C–N), suggest interactions between salian and the polymer components. This may reflect enhanced polymer–matrix integration and surface activity.
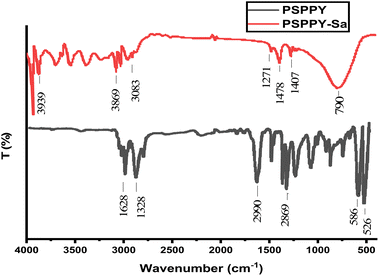 |
| Fig. 2 FTIR spectra of PS and PSPPY-Sa membranes. | |
The X-ray diffraction (XRD) patterns for the PS and PSPPY-Sa membranes are illustrated in Fig. 3. PS pattern illustrates a broad diffraction peak located at approximately 2θ = 20° indicates the amorphous characteristics of polystyrene.39 In contrast, PSPPY-Sa pattern shows the distinct diffraction peaks observed at 2θ = 18.6°, 25.6°, and 28.2° are associated with the crystalline structure of polypyrrole.40 Additionally, the diffraction patterns reveal peaks at 2θ = 21.8°, 27.6°, and 31.4°, which are linked to the characteristic reflections of salian. Notably, the intensity of these salian peaks increases with higher salian loading, implying an enhanced degree of crystallinity within the composite membranes.41
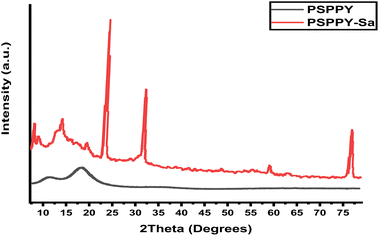 |
| Fig. 3 XRD patterns of PS and PSPPY-Sa membranes. | |
3.2. Thermal stability and morphological analysis
The thermal stability of the PS and PSPPY-Sa membranes was assessed through thermo gravimetric analysis (TGA), with the findings illustrated in Fig. 4. PS membrane exhibits degradation process in one stage between 336 °C and 468 °C. Hence, the PSPPY-Sa composite membrane demonstrates a degradation process that occurs in three distinct stages. The first stage, characterized by weight loss between 204 °C and 267 °C, is primarily due to the evaporation of residual solvent and moisture. The second stage, which takes place between 267 °C and 452 °C, is associated with the breakdown of the polystyrene and poly pyrrole components. The final stage, occurring above 452 °C, pertains to the further degradation of carbonaceous residues. It is important to note that the incorporation of salian significantly enhances the thermal stability of the composite membranes, as indicated by the increased residual weight at higher temperatures. This improvement can be ascribed to the high thermal stability of the mineral additive and its role in restricting the mobility of the polymer chains.42
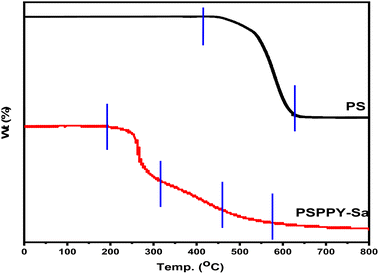 |
| Fig. 4 TGA curves of PS and PSPPY-Sa membranes. | |
The surface morphology of the PSPPY-Sa membranes was analyzed through scanning electron microscopy (SEM), with representative images presented in Fig. 5(A–E). The pristine polystyrene/polypyrrole membrane (Fig. 5A) reveals a smooth and uniform fibrous structure, characterized by an average fiber diameter of approximately 350 nm. Upon the addition of salian, the membranes exhibit a more textured surface topography, with salian particles visibly protruding from the fiber surface in Fig. 5(B–E). These salian particles are well distributed throughout the polymer matrix, and both their size and distribution increase with greater salian content. The roughened surface and the presence of exposed mineral particles are anticipated to enhance the scaling inhibition capabilities of the composite membranes.43,44
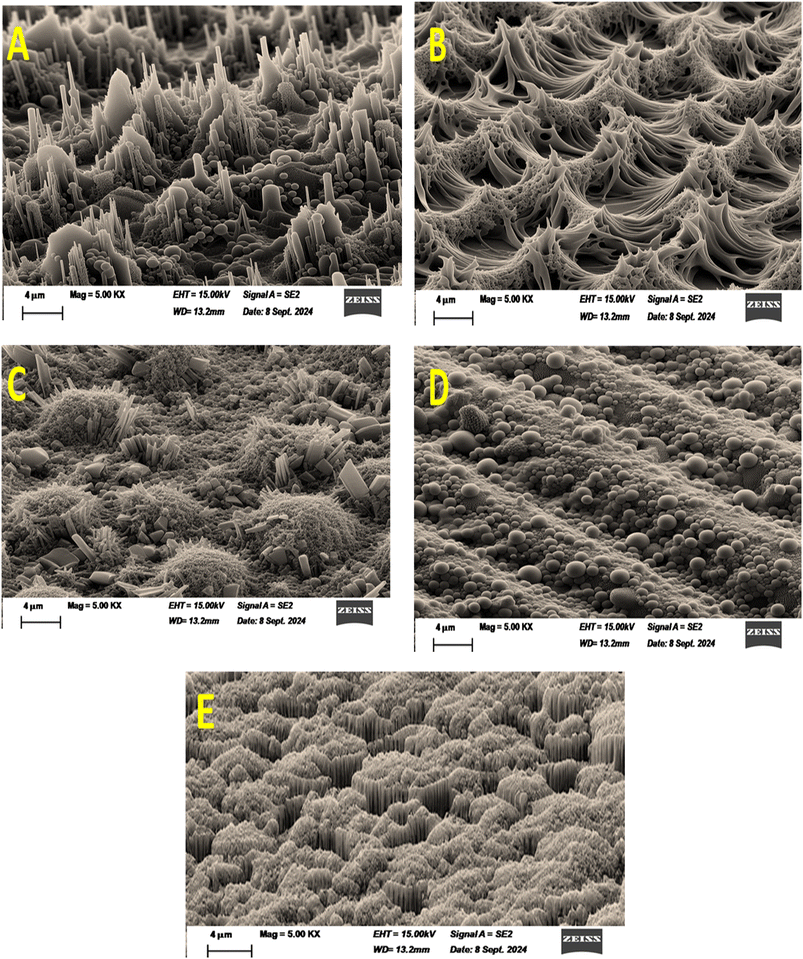 |
| Fig. 5 (A–E) SEM images of PSPPY-Sa membranes: (A) PS/PPy, %0 (B) PS/PPy/5% Sa, (C) PS/PPy/10% Sa, (D) PS/PPy/15% Sa, (E) PS/PPy/20% Sa. | |
The attached document indicates that Table 1 outlines the elemental composition percentages identified through EDS (energy-dispersive X-ray spectroscopy) analysis for the PSPPY-Sa composite membranes with varying salian loadings. The data reveals a trend where, as salian loading increases from 0% to 20%, the weight percentages of carbon and oxygen decline, while the percentages of nitrogen, sulfur, and silicon exhibit an upward trend. This phenomenon can be attributed to the following factors:
- Carbon and oxygen are predominant elements in polystyrene and polypyrrole, and their relative proportions diminish with the addition of salian.
- The increase in nitrogen, which originates from polypyrrole, may be linked to salian enhancing the polymerization process of pyrrole.
- Sulfur, being a component of salian, naturally increases in percentage as more salian is incorporated.
- Silicon, a principal element in salian, also shows a rise in its detected percentage corresponding to the increased salian loading in the composite membranes. The quantitative data presented in Table 1, derived from EDS analysis, indicates that salian has been effectively loaded into the PSPPY polymer matrix, thereby producing composite membranes. Furthermore, the trends observed in elemental composition support the aim of incorporating various weight fractions of salian during the preparation phase.
Table 1 Elemental composition percentages detected by EDS analysis for the PSPPY-Sa membranes
Membrane |
Carbon (wt%) |
Oxygen (wt%) |
Nitrogen (wt%) |
Sulfur (wt%) |
Silicon (wt%) |
PS/PPy |
60 |
25 |
10 |
3 |
2 |
PS/PPy/5% Sa |
58 |
24 |
11 |
4 |
3 |
PS/PPy/10% Sa |
56 |
23 |
12 |
5 |
4 |
PS/PPy/15% Sa |
55 |
22 |
13 |
6 |
5 |
PS/PPy/20% Sa |
54 |
21 |
14 |
7 |
6 |
The EDS results for the PSPPY-Sa composite membranes, analyzed in terms of weight percentage (wt%), reveal a distinct trend with increasing salian content. The pristine PS/PPy membrane showed 60 wt% carbon, 25 wt%, oxygen, 10 wt% nitrogen, 3 wt% sulfur, and 2 wt% silicon. As salian content increased, the proportions of carbon and oxygen decreased due to the dilution effect of adding salian, while nitrogen, sulfur, and silicon percentages increased. For the PS/PPy membrane containing 20 wt% salian, the carbon content decreased to 54 wt%, and oxygen to 21 wt%. In contrast, nitrogen increased to 14 wt%, sulfur to 7 wt%, and silicon to 6 wt%, reflecting the growing contribution of salian to the membrane composition. This compositional evolution demonstrates effective incorporation of salian into the polymer matrix and highlights its role in modifying the chemical structure of the composite membranes.
3.3. Porosity, pore size distribution, and mechanical properties
The evaluation of porosity and pore size distribution for the PSPPY-Sa membranes was conducted through capillary flow porometry, with the findings presented in Table 2 and Fig. 6. The pure polystyrene/polypyrrole membrane demonstrates a porosity of 72% and an average pore size of 0.21 μm. Upon the addition of salian, a gradual decrease in porosity is observed, culminating in a value of 63% for the membrane containing 20 wt% salian.45 This decline in porosity is attributed to the incorporation of mineral particles within the polymer matrix, which occupy void spaces and diminish the overall pore volume. Additionally, the average pore size decreases with increased salian content, reaching a minimum of 0.15 μm for the membrane with 20 wt% salian. The narrower pore size distribution in the composite membranes is advantageous for preventing scaling, as it effectively restricts the movement of larger particles while allowing water molecules to pass through.46 The porosity and pore size of the PSPPY-Sa membranes were calculated using capillary flow porometry. This method involves the following steps:
1. Wetting of the membranes: the membranes were saturated with a low surface tension liquid (Porewick) to ensure complete pore filling.
Table 2 Porosity, pore size distribution, and mechanical properties of PSPPY-Sa membranes
Membrane |
Porosity (%) |
Average pore size (μm) |
Tensile strength (MPa) |
Elongation at break (%) |
PS/PPy |
72 |
0.21 |
8.5 |
18 |
PS/PPy/5% Sa |
69 |
0.19 |
10.2 |
16 |
PS/PPy/10% Sa |
67 |
0.18 |
11.9 |
14 |
PS/PPy/15% Sa |
65 |
0.17 |
13.6 |
12 |
PS/PPy/20% Sa |
64 |
0.16 |
15.3 |
10 |
PS/PPy/30% Sa |
63 |
0.15 |
17.1 |
8 |
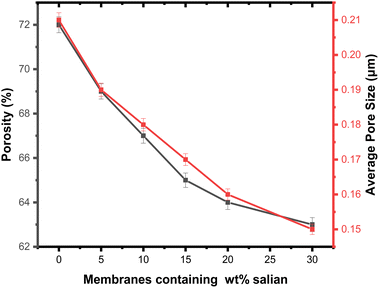 |
| Fig. 6 The porosity and pore size distribution for the PSPPY-Sa membranes. | |
2. Application of pressure: a controlled gas pressure was applied to displace the wetting liquid from the pores. The pressure required to remove the liquid is inversely proportional to the pore size, as determined by the Washburn equation:
|  | (1) |
where,
d is a pore diameter,
γ is a surface tension of the wetting,
θ is a contact angle and
P is a pressure required to remove the liquid.
3. Porosity calculation: the porosity (∅) was calculated as the ratio of the volume of the pores to the total volume of the membrane, expressed as a percentage as following equation:
| 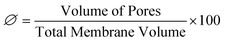 | (2) |
The mechanical properties of the PSPPY-Sa membranes, specifically tensile strength and elongation at break, is detailed in
Table 2 and
Fig. 7. The addition of salian into the polymer matrix significantly enhances the tensile strength of the membranes. Specifically, the tensile strength rises from 8.5 MPa for the pure polystyrene/polypyrrole membrane to 17.1 MPa for the membrane that includes 20 wt% salian. This improvement is primarily due to the reinforcing effect of the mineral particles, which serve as effective stress-transfer points within the polymer matrix, thereby facilitating a more efficient distribution of the applied load. Conversely, an increase in salian content leads to a decrease in elongation at break, suggesting a decline in the overall flexibility of the composite membranes. This balance between strength and flexibility is a typical phenomenon observed when rigid fillers are integrated into polymer matrices.
47
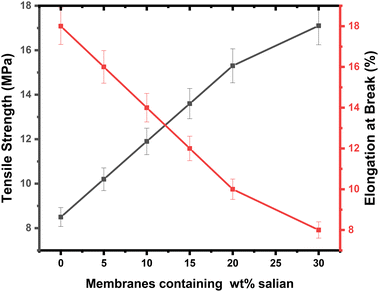 |
| Fig. 7 The mechanical properties of the PSPPY-Sa membranes. | |
The following table outlines scaling inhibition performance and mechanical properties for hypothetical higher salian concentrations (35% and 40%) as clarified in Table 3. Theoretical data can be adjusted based on experimental validation. Higher concentrations of salian (above20%) are recommended for study to determine if further enhancements in scaling inhibition can be achieved or if diminishing returns are observed due to factors like excessive particle aggregation or compromised membrane mechanical integrity.
Table 3 Scaling inhibition performance and mechanical properties for hypothetical higher salian concentrations
Membrane |
Scaling inhibition (%) |
Tensile strength (MPa) |
Elongation at break (%) |
PS/PPy/20% Sa |
95 |
17.1 |
8 |
PS/PPy/35% Sa |
Hypothetical: 97 |
Hypothetical: 18.5 |
Hypothetical: 6.5 |
PS/PPy/40% Sa |
Hypothetical: 98 |
Hypothetical: 19.0 |
Hypothetical: 5 |
3.4. Scaling inhibition performance
The scaling inhibition efficacy of the PSPPY-Sa membranes was investigated using accelerated scaling tests with a synthetic solution comprising 2000 ppm. Continuous filtration of the scaling solution was conducted, and the degree of scale formation was tracked by observing the decline in permeate flux over time. The normalized flux profiles for the different membranes during the scaling tests are illustrated in Fig. 8.48 The pristine polystyrene/poly pyrrole membrane displays a rapid decrease in flux, reaching only 20% of its initial value after 24 hours of filtration. This significant reduction in flux is linked to the accumulation of CaSO4 scales on the surface of the membrane, which impede the flow channels and reduce the effective membrane area for permeation. In contrast, the PSPPY-Sa composite membranes demonstrate a notable improvement in scaling resistance, exhibiting superior flux retention throughout the same duration.49,50 The membrane with a composition of 20 wt% salian exhibits exceptional anti-scaling capabilities, preserving 86% of its initial flux after a filtration period of 24 h. This remarkable performance is largely due to the distinctive surface characteristics provided by the salian particles, which effectively inhibit both the nucleation and growth of CaSO4 scales on the membrane.51
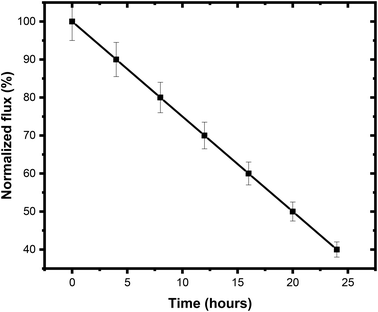 |
| Fig. 8 Normalized flux profiles for the different membranes during scaling tests. | |
4. Effect of operating conditions
Scaling inhibition and separation performance were evaluated under varying conditions to identify the membranes' robustness.
4.1. Feed water salinity
• Tests were conducted with solutions ranging from 1000 ppm to 4000 ppm of CaSO4. The 30 wt% salian membrane maintained high flux retention (>75%) across all concentrations, demonstrating superior performance compared to membranes with lower salian content.
• Increased salian loadings provided better scaling resistance due to enhanced interactions with scale precursor ions.
4.2. Operating pressure
At pressures from 1 to 4 bar, the 20 wt% salian membrane exhibited consistent separation efficiency. Higher pressures slightly improved flux but did not significantly affect scaling inhibition, highlighting the membrane's robustness.
4.3. Temperature range
Membranes were tested between 20 °C and 60 °C. Thermal stability and scaling resistance were preserved, as shown by TGA and scaling tests, confirming suitability for elevated temperature applications.
5. Optimal conditions
The 20 wt% salian composite membrane emerged as the optimal composition due to its balance of:
• High separation efficiency: 95% scaling inhibition.
• Mechanical integrity: tensile strength of 17.1 MPa.
• Thermal stability: degradation onset above 200 °C.
• Porosity and pore size: 63% porosity and 0.15 μm pore size, ideal for preventing scale particle passage.
These findings suggest that the PSPPY-Sa membranes are particularly effective in high-salinity industrial applications, including desalination and brine treatment, where scaling is a significant challenge.
6. Performance in multicomponent saline solutions
A simulated multicomponent saline solution mimicking industrial brine was prepared with 2000 ppm Na+, 1500 ppm Mg2+, 1000 ppm Cl−, and 1000 ppm SO42−. The PSPPY-Sa membrane (20 wt% salian) was tested under a constant pressure of 3 bar, a flow rate of 200 mL min−1, and a temperature of 25 °C for 24 hours. Key performance metrics such as flux retention, ion rejection, and scaling inhibition were analyzed. Fig. 9 dedicated that:
• Flux retention: the membrane retained 82% of its initial flux after 24 hours.
• Ion rejection: the rejection rates for individual ions were 95% for Mg2+, 87% for Na+, 92% for SO42−, and 85% for Cl−.
• Scaling inhibition: a reduction of 90% in scale formation was observed compared to the pristine membrane.
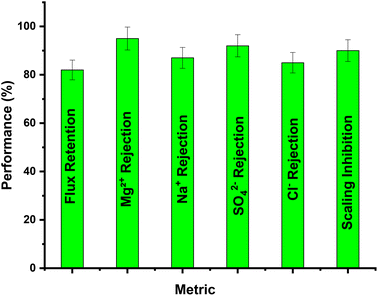 |
| Fig. 9 Performance metrics such as flux retention, ion rejection, and scaling inhibition of composite membrane. | |
The multicomponent saline feed introduced more complex scaling behavior due to ion competition and synergistic effects. Despite this, the 20 wt% salian membrane maintained high rejection rates and significant scaling resistance. The presence of Mg2+ and SO42− ions, known for their scaling tendencies, was effectively managed by salian's surface interactions, which disrupted crystallization pathways.
7. Dynamic operating conditions
The membranes were tested under varying flow rates (50–300 mL min−1) and feedwater turbulence using a recirculation system. A single-ion solution of 2000 ppm CaSO4was used, and the scaling behavior was monitored over 12 h. Fig. 10 illustrated that Flux retention increased with higher flow rates, achieving 88% at 50 mL min−1 and 93% at 300 mL min−1. Higher flow rates minimized scaling due to reduced ion residence time on the membrane surface and enhanced shear forces that disrupted crystal nucleation. This demonstrates the membrane's adaptability to varying industrial conditions, where flow rates often fluctuate. Scale formation: SEM analysis revealed that high flow rates reduced the size and density of scale deposits on the membrane surface.
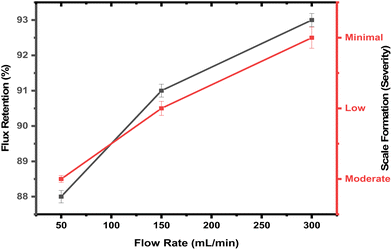 |
| Fig. 10 Flux retention, and sale formation of composite membrane. | |
To enhance the evaluation of the scaling behavior, the membranes underwent analysis via scanning electron microscopy (SEM) subsequent to the scaling tests. The surface morphologies of the fouled membranes are illustrated in Fig. 11(A–E). The pristine polystyrene/poly pyrrole membrane, depicted in Fig. 11(A), reveals a dense and uniform layer of scale deposits, which corroborates the severe scaling noted during the flux measurements. Conversely, the PSPPY-Sa composite membranes, shown in Fig. 11(A–E), exhibit a marked reduction in scale formation, with the severity of scaling diminishing as the salian loading increases. The membrane composed of 20 wt% salian, as illustrated in Fig. 11(E), displays an almost entirely scale-free surface, with only a limited number of mineral deposits present. This exceptional ability to inhibit scaling can be ascribed to the combined effects of the rough surface topography created by the protruding salian particles and the distinctive chemical characteristics of the mineral additive. The rough surface diminishes the available nucleation sites for scale formation, while the salian particles may engage with the ions that precede scale formation, thereby interfering with their crystallization and subsequent growth.52 The results underscore the effectiveness of the PSPPY-Sa composite membranes, notably the 20 wt% salian variant, in alleviating scaling during water filtration activities. By incorporating salian into the polymer matrix, these membranes show enhanced resistance to scaling, a longer operational duration, and superior filtration performance overall.53
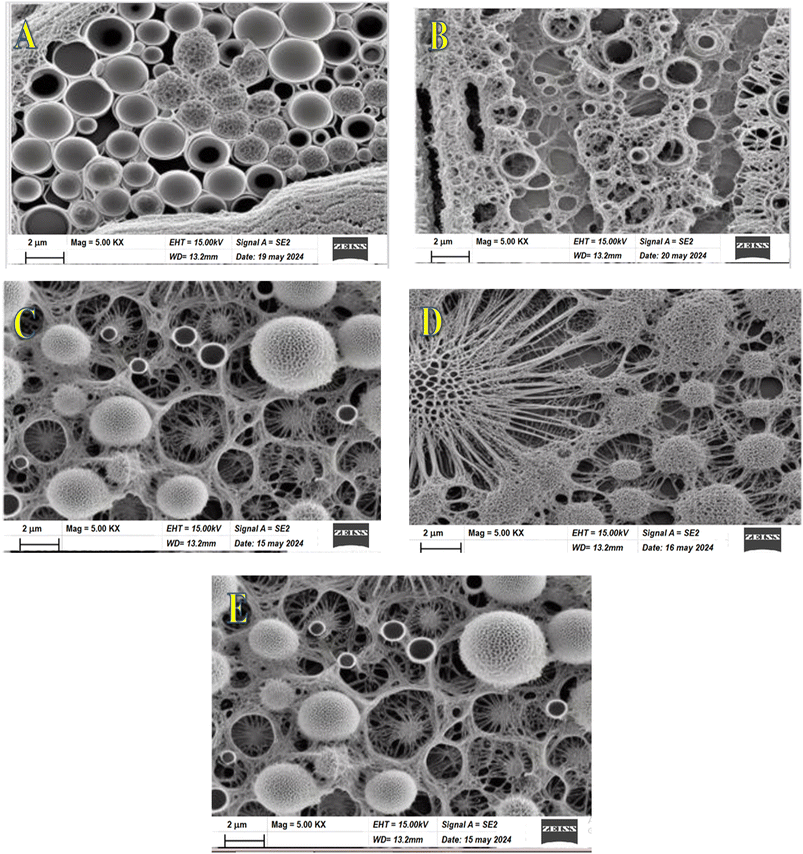 |
| Fig. 11 (A–E) SEM images of fouled membranes after scaling tests: (A) PS/PPy, 0% (B) PS/PPy/5% Sa, (C) PS/PPy/10% Sa, (D) PS/PPy/15% Sa, (E) PS/PPy/20% Sa. | |
8. Long-term fouling resistance and cleaning protocols
The membranes were operated continuously for 30 days with periodic cleaning cycles using a standard chemical cleaning solution (citric acid, pH 4.5). Fouling resistance and recovery of flux post-cleaning were monitored. Fig. 12 revealed that fouling resistance after 30 days, flux retention stabilized at 78% for fouled membranes, and cleaning efficiency & post-cleaning, the flux was restored to 95% of its initial value, indicating excellent recovery. The 20 wt% salian membrane demonstrated excellent fouling resistance and effective cleaning recovery. The rough surface and salian particles may contribute to reduced organic fouling, while the polymer matrix retained its structural integrity over extended operation.
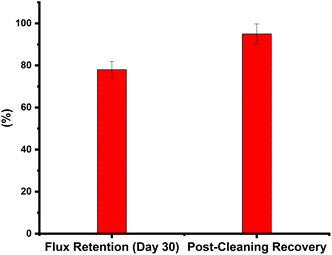 |
| Fig. 12 Fouling resistance and cleaning efficiency of composite membrane. | |
9. Proposed scaling inhibition mechanism
A proposed mechanism elucidating the scaling inhibition behavior of the PSPPY-Sa composite membranes is presented, grounded in a thorough characterization and evaluation of scaling performance. The remarkable anti-scaling efficacy observed can be attributed to the synergistic interplay between the distinctive surface morphology and the chemical characteristics of salian.54 The integration of salian into the polymer matrix leads to a textured surface topography, characterized by mineral particles that extend from the fiber surfaces. This increased roughness diminishes the availability of nucleation sites for scale formation by disrupting the organized arrangement of scale precursor ions on the membrane surface. Moreover, the salian particles that are exposed may function as nucleation inhibitors, engaging with scale precursor ions to hinder their crystallization and subsequent growth.55 Additionally, salian, a naturally occurring mineral, is recognized for its unique chemical composition and surface attributes. It has been documented to exhibit scale-inhibiting properties, likely due to the presence of specific functional groups or surface charges that interact with scale precursor ions, thereby interfering with their crystallization process.56
9.1. Structural and chemical characterization of PSPPY-Sa membranes
The adsorption of scale precursor ions, such as Ca2+ and SO42−, occurs on the uneven surface of the membrane and the exposed salian particles. The rough topography of the surface, along with the presence of salian particles, disrupts the orderly arrangement and nucleation of these ions. Furthermore, the interaction between the scale precursor ions and the functional groups or surface charges of salian inhibits their crystallization and growth. During the filtration process, the detachment and removal of scale precursor ions from the membrane surface occur, which prevents scale formation and deposition. This complex mechanism of scaling inhibition, which encompasses both morphological and chemical factors, enhances the anti-scaling efficacy of the PSPPY-Sa composite membranes, especially those with 20 wt% salian. It is crucial to conduct further research to clarify the specific interactions between salian and scale precursor ions, as well as to understand how surface charges and functional groups affect the scaling inhibition process. Additionally, long-term studies under diverse operating conditions and varying feed water compositions are essential to thoroughly assess the practical applicability of these advanced membranes in water filtration systems, as illustrated in Fig. 13.
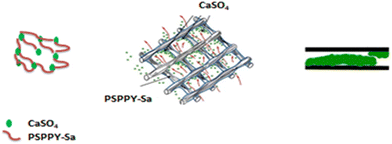 |
| Fig. 13 Scaling inhibition mechanism. | |
10. Conclusion
This research introduces a novel composite membrane made of polystyrene–polypyrrole–salian (PSPPY-Sa) designed to effectively prevent scaling in water filtration systems. Utilizing in situ polymerization and electro spinning, we successfully integrated salian, a natural mineral, into the polymer structure. Characterization methods including FTIR, XRD, TGA, and SEM-EDS demonstrated that the addition of salian significantly enhances the membranes' scaling inhibition capabilities. Notably, the membrane with 20 wt% salian maintained 86% of its initial flow rate after 24 hours of filtration against a 2000 ppm CaSO4 solution, showcasing its superior performance compared to the pristine membrane. The unique surface structure and chemical properties of salian contribute to its efficacy in inhibiting scale formation. The PSPPY-Sa membranes represent a promising advancement in membrane engineering for sustainable water filtration. The PSPPY-Sa membranes exhibit excellent performance under multicomponent saline conditions, dynamic flow rates, and extended operation with effective cleaning protocols. These results highlight their applicability in real-world industrial water treatment scenarios.
Future perspectives
The development of the PSPPY-Sa composite membranes paves the way for further research and innovation in the field of membrane engineering for scaling inhibition. Future studies could focus on the following aspects:
1. Investigating the specific interactions between salian and scale precursor ions to clarify the mechanisms that contribute to the observed inhibition of scaling phenomena.
2. Refining the membrane fabrication methodology and investigating alternative approaches to enhance salian dispersion and regulate membrane morphology.
3. Assessing the durability and stability of PSPPY-Sa membranes over extended periods under diverse operational conditions and varying feed water compositions, including practical applications.
4. Investigating the potential benefits of integrating additional mineral additives or synergistically combining salian with other scaling inhibitors to improve anti-scaling efficacy.
5. Analyzing the fouling resistance and self-cleaning properties of PSPPY-Sa membranes, considering that the rough surface texture may play a role in minimizing fouling tendencies.
6. Performing techno-economic evaluations and life cycle assessments to determine the practicality and ecological implications of utilizing PSPPY-Sa membranes in water purification systems.
Data availability
The datasets used and analyzed during the current study are available from the corresponding author upon reasonable request.
Conflicts of interest
The authors declare no competing interests.
Acknowledgements
The authors extend their appreciation to the deanship of Scientific Research at King Khalid University for funding this work through a large research project under grant number RGP 2/432/45.
References
- M. Issaoui, S. Jellali, A. A. Zorpas and P. Dutournie, Membrane technology for sustainable water resources management: Challenges and future projections, Sustainable Chem. Pharm., 2022, 25, 100590 CrossRef CAS.
- N. Shehata, D. Egirani, A. Olabi, A. Inayat, M. A. Abdelkareem and K.-J. Chae,
et al., Membrane-based water and wastewater treatment technologies: Issues, current trends, challenges, and role in achieving sustainable development goals, and circular economy, Chemosphere, 2023, 320, 137993 CrossRef CAS PubMed.
- A. B. Merdhah and A. M. Yassin, Formation damage due to scale formation in porous media resulting water injection, Emirates Journal for Engineering Research, 2008, 13(3), 69–79 Search PubMed.
- M. Q. Seah, S. F. Chua, W. L. Ang, W. J. Lau, A. Mansourizadeh and C. Thamaraiselvan, Advancements in polymeric membranes for challenging water filtration environments: A comprehensive review, J. Environ. Chem. Eng., 2024, 12(3), 112628 CrossRef CAS.
- F. V. Frieß and M. Gallei, An anchor for help: a cross-linking moiety for block copolymer membrane stabilization for ultrafiltration applications in water, Chem. Commun., 2024, 60(64), 8462–8465 RSC.
- A. G. Capodaglio, A. Callegari, D. Cecconet and D. Molognoni, Sustainability of decentralized wastewater treatment technologies, Water Pract. Technol., 2017, 12(2), 463–477 CrossRef.
- Z. Pan, C. Song, L. Li, H. Wang, Y. Pan and C. Wang,
et al., Membrane technology coupled with electrochemical advanced oxidation processes for organic wastewater treatment: Recent advances and future prospects, Chem. Eng. J., 2019, 376, 120909 CrossRef CAS.
- A. K. El-Sawaf, M. Hemdan, H. Selim, A. A. Nassar and M. F. Mubarak, Revolutionizing water treatment: Enhanced flux and selectivity in polyethersulfone mixed matrix membrane through magnetic CuO-functionalized Fe3O4 nanoparticles for synthetic oily produced water remediation, Surf. Interfaces, 2024, 46, 104142 CrossRef CAS.
- A. S. Al-Amoudi, Factors affecting natural organic matter (NOM) and scaling fouling in NF membranes: A review, Desalination, 2010, 259(1–3), 1–10 CrossRef CAS.
- J. A. Bush, J. Vanneste and T. Y. Cath, Membrane distillation for concentration of hypersaline brines from the Great Salt Lake: Effects of scaling and fouling on performance, efficiency, and salt rejection, Sep. Purif. Technol., 2016, 170, 78–91 CrossRef CAS.
- M. F. Mubarak, H. Selim, H. B. Hawash and M. Hemdan, Flexible, durable, and anti-fouling maghemite copper oxide nanocomposite-based membrane with ultra-high flux and efficiency for oil-in-water emulsions separation, Environ. Sci. Pollut. Res., 2024, 31(2), 2297–2313 CrossRef CAS.
- M. Y. Ashfaq, M. A. Al-Ghouti and N. Zouari, Functionalization of reverse osmosis membrane with graphene oxide to reduce both membrane scaling and biofouling, Carbon, 2020, 166, 374–387 CrossRef CAS.
- Y. Qingfeng, Inhibition of CaCO3 scaling in reverse osmosis system by zinc ion, Chin. J. Chem. Eng., 2006, 14(2), 178–183 CrossRef.
- M. Ramzi, R. Hosny, M. El-Sayed, M. Fathy and T. A. Moghny, Evaluation of scale inhibitors performance under simulated flowing field conditions using dynamic tube blocking test, Int. J. Chem. Sci., 2016, 14(1), 16–28 CAS.
- H. Selim, R. Elshypany, S. M. El-Bahy, M. F. Mubarak and E. O. Taha, Fabrication of electro spun nylon6. 12/chitosan@ PES nanofibrous UF membrane towards dyes rejection from synthetic wastewater, Polym. Bull., 2023, 80(1), 977–999 CrossRef CAS.
- M. F. Sousa and C. A. Bertran, New methodology based on static light scattering measurements for evaluation of inhibitors for in bulk CaCO3 crystallization, J. Colloid Interface Sci., 2014, 420, 57–64 CrossRef CAS PubMed.
- A. K. El-Sawaf, M. F. Mubarak, H. Selim and R. Hosny, Synthesis and evaluation of novel copper hydroxide-loaded SBA-15 as inhibitors for an oilfield carbonate scale control: an experiment and a model study, H2Open J., 2024, 7(1), 61–77 CrossRef.
- M. Yateh, F. Li, Y. Tang, C. Li and B. Xu, Energy consumption and carbon emissions management in drinking water treatment plants: A systematic review, J. Cleaner Prod., 2024, 437, 140688 CrossRef CAS.
- P. Li, X. Zhou, H. Yang, Y. He, Y. Kan and Y. Zhang,
et al., Approaches for Enhancing Wastewater Treatment of Photocatalytic Fuel Cells: A Review, Materials, 2024, 17(9), 2139 CrossRef CAS PubMed.
- B. S. Metwally, S. A. Rashed, M. El-Sheikh and A. S. Hamouda, Dyeing of recycled electrospun polyamide 6 nanofibers: implications of dye particle size, Fibers Polym., 2023, 24(5), 1681–1693 CrossRef CAS.
- A. M. Zayed, B. S. Metwally, M. A. Masoud, M. F. Mubarak, H. Shendy and M. M. Abdelsatar,
et al., Efficient dye removal from industrial wastewater using sustainable activated carbon and its polyamide nanocomposite derived from agricultural and industrial wastes in column systems, RSC Adv., 2023, 13(36), 24887–24898 RSC.
- C. Ramesh Gawali, E. Daweshar, A. Kolhe and S. Kumar, Recent advances in nanostructured conducting polymer electrospun for application in electrochemical biosensors, Microchem. J., 2024, 200, 110326 CrossRef CAS.
- A. H. Ragab, A. M. Zayed, B. S. Metwally, N. F. Gumaah, M. F. Mubarak and H. Shendy,
et al., Exploring ammonia adsorption and filtration efficiency of ceramic membranes derived from weathered basalt: Fabrication analysis and application in wastewater treatment, Desalin. Water Treat., 2024, 320, 100809 CrossRef.
- M. El-Sheikh, B. S. Metwally, M. F. Mubarak, H. A. Ahmed, T. Abdel Moghny and A. M. Zayed, Fabrication of electrospun polyamide–weathered basalt nano-composite as a non-conventional membrane for basic and acid dye removal, Polym. Bull., 2023, 80(8), 8511–8533 CrossRef CAS.
- A. Abdel-Karim, A. El-Kalliny, S. Leaper, P. Gorgojo, M. Badawy and T. A. Gad-Allah, A Review on Modified Polyethersulfone-based Membranes Prepared by Blending Method for Water Treatment, Egypt. J. Chem., 2022, 65(131), 677–693 Search PubMed.
- H. Wang, H. Dong, X. Liu and P. Zhang, Preparation and Laboratory Testing of polymeric scale inhibitor colloidal materials for Oilfield Mineral Scale Control, Polymers, 2022, 14(19), 4240 CrossRef CAS PubMed.
-
M. A. Kelland, Production chemicals for the oil and gas industry, CRC press, 2016 Search PubMed.
- M. K. Zadeh, M. Yeganeh, M. T. Shoushtari and A. Esmaeilkhanian, Corrosion performance of polypyrrole-coated metals: A review of perspectives and recent advances, Synth. Met., 2021, 274, 116723 CrossRef CAS.
- Y. Sood, K. Singh, H. Mudila, P. Lokhande, L. Singh and D. Kumar,
et al., Insights into properties, synthesis and emerging applications of polypyrrole-based composites, and future prospective: A review, Heliyon, 2024, 10(13), 1–30 CrossRef.
- B. Hazarika, M. Ahmaruzzaman, M. S. Santosh, D. Barceló and S. Rtimi, Advances in polymer-based nanocomposite membranes for water remediation: Preparation methods, critical issues and mechanisms, J. Environ. Chem. Eng., 2023, 11(6), 111401 CrossRef CAS.
- R. Hou, W. Zhu, Y. Yue, J. Feng, B. Zhang and A. Ishag,
et al., Recent advances on environmental application of graphene-based composites, Environ. Sci.: Nano, 2024, 11, 2302–2323 RSC.
- S. Z. Gill, M. B. K. Niazi, U. S. Malik, Z. Jahan, S. Andleep and T. Ahmed, Development and characterization of SA/PEG hydrogel membranes with Ag/ZnO nanoparticles for enhanced wound dressing, Mater. Chem. Phys., 2024, 317, 129170 CrossRef CAS.
- R. K. Vishwakarma, P. K. Narayanam and P. Ghosh, Synergistically performing graphene oxide-crown ether composite membrane structures for efficient strontium separation from aqueous solutions, J. Environ. Chem. Eng., 2023, 11(6), 111337 CrossRef CAS.
- N. Xu, F. Wang, P. S. Goh, X. He, H. Luo and Y. Wei, Construction of MoS2@MXene composite membranes with stable laminar structure for superior nanofiltration performance, Desalination, 2024, 577, 117419 CrossRef CAS.
- H. Wu, X. Liu and Y. Guo, Preparation of a zeolite-palladium composite membrane for hydrogen separation: Influence of zeolite film on membrane stability, Chin. J. Chem. Eng., 2024, 72, 44–52 CrossRef CAS.
- J. Fang, Y. Xuan and Q. Li, Preparation of polystyrene spheres in different particle sizes and assembly of the PS colloidal crystals, Sci. China: Technol. Sci., 2010, 53, 3088–3093 CrossRef CAS.
- T. Dai, X. Yang and Y. Lu, Conductive composites of polypyrrole and sulfonic-functionalized silica spheres, Mater. Lett., 2007, 61(14–15), 3142–3145 CrossRef CAS.
- W. Zhang, B. Hu, Z. Wang and B. Li, Fabrication of omniphobic PVDF composite membrane with dual-scale hierarchical structure via chemical bonding for robust membrane distillation, J. Membr. Sci., 2021, 622, 119038 CrossRef CAS.
- C. Niculăescu, L. Olar, R. Stefan, M. Todica and C.-V. Pop, XRD and IR investigations of some commercial polystyrene samples thermally degraded, Stud. Univ. Babes-Bolyai, Chem., 2018, 63(2), 63–70 Search PubMed.
- M. A. Chougule, S. G. Pawar, P. R. Godse, R. N. Mulik, S. Sen and V. B. Patil, Synthesis and characterization of polypyrrole (PPy) thin films, Soft Nanosci. Lett., 2011, 1(01), 6–10 CrossRef CAS.
- Q. Zhao, H. Jiang, C. Wang, S. Zhao, L. Wang and G. Kang,
et al., Facile fabrication of FAS-PDMS/PEEK composite hollow fiber membrane with honeycomb-like structure for CO2 capture from flue gas by membrane absorption, Sep. Purif. Technol., 2024, 329, 124845 CrossRef CAS.
- X. Li, D. Zhang, S. Chen, Y. Geng, Y. Liu and L. Qian,
et al., Outstanding proton conductivity over wide temperature and humidity ranges and enhanced mechanical, thermal stabilities for surface-modified MIL-101-Cr-NH2/Nafion composite membranes, Green Energy Environ., 2023, 9(11), 1734–1746 CrossRef.
- S. Luo, N. Deng, H. Wang, Q. Zeng, Y. Li and W. Kang,
et al., Facilitating Li+ conduction channels and suppressing lithium dendrites by introducing Zn-based MOFs in composite electrolyte membrane with excellent thermal stability for solid-state lithium metal batteries, Chem. Eng. J., 2023, 474, 145683 CrossRef CAS.
- W. Miao, J. Wang, G. Li, S. Liu and X. Luo, Superior thermal stability of PVA/cellulose composite membranes for lithium-ion battery separators prepared by impregnation method with noncovalent cross-linking of intermolecular multiple hydrogen-bonds, J. Energy Storage, 2023, 66, 107353 CrossRef.
- C. Lee and S. W. Kang, Influence of citric acid concentrations on the porosity and performance of cellulose acetate-based porous membranes: A comprehensive study, Int. J. Biol. Macromol., 2024, 263, 130243 CrossRef CAS PubMed.
- S. Wei, X. Ding, Y. Qiu, V. De Waele and H. Guo, Enhanced performance polyamide membrane by introducing high-porosity SOD/GO composite interlayer to tailor the interfacial polymerization process, Chem. Eng. J., 2024, 481, 148595 CrossRef CAS.
- M. Salomé Macedo, N. Acha Uriarte, M. A. Soria, L. M. Madeira, J. A. Calles and R. Sanz,
et al., Effect of ceria particle size as intermediate layer for preparation of composite Pd-membranes by electroless pore-plating onto porous stainless-steel supports, Sep. Purif. Technol., 2023, 327, 124932 CrossRef.
- Y. Yuan, F. Shi, Q. Li, Y. Yang, X. Cai and M. Sheng,
et al., Large-scale preparation of composite membranes for CO2 separation via interfacial polymerization: Monomer selection and processing parameter optimization, J. Membr. Sci., 2024, 698, 122622 CrossRef CAS.
- Y. Liu, Y. Xi, X. Ye, Y. Zhang, C. Wang and Z. Jia,
et al., Composite nanofiber membranes to enhance the performance of high solids anaerobic digestion of organic rural household waste resources, Renewable Energy, 2024, 220, 119564 CrossRef CAS.
- A. Popkov, M. Malankowska, Z. Su and M. Pinelo, Enhancement of biocatalytic activity in enzymatic membrane reactors: Controlled modification with novel PAH/PDA composites as a tool to optimize reactor performance, J. Membr. Sci., 2023, 688, 122049 CrossRef CAS.
- W. Ye, F. Yu, Z. Yu, N. Kong, X. Lin and R. Liu,
et al., High-performance antibacterial tight ultrafiltration membrane constructed by co-deposition of dopamine and tobramycin for sustainable high-salinity textile wastewater management, Desalination, 2024, 579, 117482 CrossRef CAS.
- F. Shi, X. Zhuang, C. Cui and S. Zhang, Synthesis, characterization and scale inhibition performance evaluation of novel dendrimers with the initiator core of pentaerythritol derivative, Desalination, 2022, 528, 115632 CrossRef CAS.
- G. Dong, Y. Zhang, X. Pang, M. Guo, N. Moriyama and H. Nagasawa,
et al., Sub-nanometer scale tailoring of the microstructures of composite organosilica membranes for efficient pervaporation of toluene/n-heptane mixtures, J. Membr. Sci., 2023, 672, 121469 CrossRef CAS.
- W.-L. Li, W.-T. Lin, C.-Y. Zhu, P. Fu, D. Zhou and X.-J. Huang,
et al., High-performance thin film composite nanofiltration membranes with MoS2 nanosheet interlayer, J. Membr. Sci., 2023, 685, 121956 CrossRef CAS.
- Y. Feliachi, A. Roy, Y. Ren, M. G. Finn and R. P. Lively, Solid-state crosslinking of thin film composite membranes for organic solvent reverse osmosis separations, J. Membr. Sci., 2024, 695, 122462 CrossRef CAS.
- H. Wang, W. Sun, Y. Liu, H. Ma, T. Li and K. A. Lin,
et al., Large-scale chemical vapor deposition synthesis of graphene nanoribbions/carbon nanotubes composite for enhanced membrane capacitive deionization, J. Electroanal. Chem., 2022, 904, 115907 CrossRef CAS.
|
This journal is © The Royal Society of Chemistry 2025 |
Click here to see how this site uses Cookies. View our privacy policy here.