DOI:
10.1039/D4EY00282B
(Paper)
EES Catal., 2025,
3, 446-458
High-performance and stable NH3 production using a TiO2-protected Si photocathode and patterned Au loading†
Received
16th December 2024
, Accepted 2nd January 2025
First published on 10th January 2025
Abstract
Crystalline silicon (c-Si) is a promising material for photoelectrochemical (PEC) ammonia (NH3) production from nitrate (NO3−) reduction owing to its appropriate band gap and optimal charge-transport properties. However, c-Si is not stable in aqueous solutions, causing the detachment of catalysts from the c-Si photoelectrode and resulting in a dramatic decrease in the performance. Furthermore, electrocatalysts on c-Si block light, therby reducing the PEC NH3-production efficiency. Herein, we stabilized and increased the efficiency of the c-Si photocathode by TiO2 deposition and loaded an optimized amount of Au using an e-beam patterning, respectively. We found that TiO2 not only protects the c-Si photoelectrode from the electrolyte but also promotes strong bonding between Au and the c-Si photoelectrode. Notably, TiO2 showed a synergistic effect with the Au electrocatalyst in increasing the faradaic efficiency (FE) of NO3− reduction for NH3 production, which was further confirmed by density functional theory calculations. Overall, the Au-loaded TiO2-protected c-Si photoelectrode showed a stable and record-high NH3-production rate of 1590 ± 40 μgNH3 cm−2 h−1 with an FE of 83.4% ± 5.6% at −0.35 V vs. the reversible hydrogen electrode.
Broader context
Developing a photoelectrochemical (PEC) device for the conversion of nitrate to ammonia is a promising approach for decentralized ammonia production and sustainable wastewater treatment process. In this work, we developed a highly stable and high-performance photocathode by depositing a gold (Au) pattern on the surface of a silicon (c-Si) wafer using a photolithography technique for NH3 production. Our photoelectrode exhibited a record-high NH3-production rate of 1590 ± 40 μgNH3 cm−2 h−1 with an 83.4% ± 5.6% faradaic efficiency (FE) and stable long-term operation under 44 h continuous illumination. The high production rate of the Si–TiO2–Au photocathode can be attributed to the role of the Au pattern in circumventing the rate-determining step (RDS) in NO3− reduction (NO3− → NO2−) and the excellent catalytic role of the ALD-TiO2 layer in NH3 production. The synergistic effect of Au and TiO2 could be scaled up through photolithography. This offers a promising photocathode for the PEC conversion of nitrate ions into ammonia.
|
1. Introduction
The exponential growth in the global population over the past two decades has posed significant challenges to the expansion of food production.1,2 Nitrogen-based fertilizers, which primarily rely on ammonia (NH3) that comprises 80% of these fertilizers by volume serve as the primary source of nutrition for the agricultural produce within the food supply chain.3,4 Additionally, NH3 offers promise as an energy carrier owing to its notably high volumetric energy density (15.6 MJ L−1), surpassing that of Li-ion batteries (1.73 MJ L−1) and compressed H2 (5.5 MJ L−1 at 70 MPa).3–6 NH3 is predominantly produced using the energy-intensive Haber–Bosch (HB) process that operates under high temperature and pressure over 250 °C and 300 atm, respectively.7,8 This process accounts for more than 1–2% of the world's energy consumption and 1.6% of worldwide CO2 emissions.7,9 Hence, recent efforts have been dedicated to developing more energy-efficient and less CO2-emitting methods for NH3-production processes.10–14 Photoelectrochemical (PEC) NH3 production is a promising technique, because it can be operated at ambient temperature and pressure without the need for expensive H2 and without emitting CO2.15,16
Crystalline silicon (c-Si) is a promising material for PEC NH3 production because it can absorb a wide range of the solar spectrum due to its small band gap of 1.1 eV and high carrier mobility.17–19 Recently, several works have reported on the application of c-Si photoelectrodes for the PEC nitrogen (N2)-reduction reaction (NRR).20–23 For example, MacFarlane et al. utilized Au-electrocatalyst-loaded c-Si and achieved an NH3-production rate of 1.33 μgNH3 cm−2 h−1 under 2 suns illumination.20 Zheng et al. applied the aerophilic polytetrafluoroethylene (PTFE) to a Au-loaded c-Si photocathode to increase the Faraday efficiency (FE) for the NRR, and achieved a NH3-production rate of ∼18.9 μg cm−2 h−1 with 37.8% NH3 selectivity at −0.2 V vs. the reversible hydrogen electrode (RHE).24
To commercialize PEC NH3 production, the NH3-production rate needs to be more than ∼1000 μg NH3 cm−2 h−1, which is equivalent to a current density of approximately 10 mA cm−2.25,26 However, the NRR partial current density in aqueous electrolytes is usually less than 1 mA cm−2, which correspond to less than a 100 μg NH3 cm−2 h−1 NH3 production rate (about 10-times lower compared to the NO3-reduction reaction), because less N2 (0.0001 M) is dissolved in the water and N
N bonds are hard to selectively dissociate.27,28 Replacing N2 with nitrate (NO3−) as a nitrogen-containing source can address some of the drawbacks of the NRR, because NO3− is very soluble in water (0.5–2 M) and NO3− can be easily converted into NH3 through nitrite (NO2−) with a high FE.2 Thus NH3 production from NO3− may be a promising way to not only maximize the NH3 productivity but also for the remediation of NH3 from waste streams and seawater.29
Lee et al. used Au-decorated c-Si nanowires for the PEC reduction of NO3− to NH3, achieving a high NH3 FE of 95.6% at a positive applied potential (0.2 V vs. RHE).16 However, the NH3-production rate remained very low (>10 μgNH3 h−1 cm−2), and both the FE and NH3-production rate gradually decreased due to the detachment of Au nanoparticles (NPs) from the electrode surface.16 Au-loaded c-Si photocathodes showed low stability and performance for PEC NH3 production, due to the severe photocorrosion and chemical etching of the c-Si photoelectrode, especially in alkaline media. The continuous etching of c-Si in the corrosive electrolyte not only diminished its performance but also led to the detachment of the electrocatalyst from the photoelectrode.16
In the present study, we demonstrated high-performance and stable NH3 production by protecting the c-Si photocathode with a TiO2 layer deposited by atomic layer deposition (ALD), followed by patterned Au deposition. The TiO2 layer could not only protect the c-Si surface from electrolyte degradation, but could also improve the adhesion between the Au catalyst and the Si. By optimizing the amount of Au loading through the photolithography technique, we were able to minimize the light absorption by the Au catalyst while maintaining a high selectivity for NH3 production. Our Au-loaded TiO2 protected c-Si photocathode (Si/TiO2/Au) exhibited a record-high production rate of 1590 ± 40 μgNH3 cm−2 h−1, which is higher than the NH3-production rate criteria for the practical application of PEC NH3 production. Moreover, the FE of NH3 was as high as 83.4 ± 5.6%, and Si/TiO2/Au demonstrated stability during long-term operation under 44 h continuous illumination. The high production rate of the Si/TiO2/Au photocathode could be attributed to the role of Au in circumventing the rate-determining step (RDS) in NO3− reduction (NO3− → NO2−) and the catalytic role of the ALD-TiO2 layer in NH3 production, which was further verified by density functional theory (DFT) calculations. These results indicate that TiO2 not only protects the c-Si surface from Au electrocatalyst detachment, but also plays an important role in the selective NO3− reduction reaction to produce NH3.
2. Results and discussion
2.1. Fabrication process and PEC performance of Si/TiO2/Au
A thin layer of TiO2 (∼20 nm) was deposited on the surface of a cleaned HF-treated p-type silicon (p-Si) wafer using the ALD technique (ESI,† Fig. S1). Photolithography was conducted using a Cr photomask to print square patterns with different sizes and densities on the surface of p-Si.30,31 After spin-coating and soft baking of the photoresist, an MIF 300 developer was used to imprint the desired pattern on the Si/TiO2 substrate. Finally, a 100 nm metallic film (Au) was deposited by an e-beam evaporator (ESI,† Fig. S2), and the desired pattern was lifted by washing the resist in acetone solution for 60 s (Fig. 1(a)). To remove any extra photoresist, an oxygen plasma treatment was utilized to clean the photocathode surface. Fig. 1(b) and ESI,† Fig. S3 show top-view microscopy and angled scanning electron microscopy (SEM) images of the Au pattern with a 4% density on the surface of Si/TiO2 (Si/TiO2/Au-4). Energy-dispersive spectroscopy (EDS) elemental mapping indicated that the Au patterns, without any imperfection or missing squares, occupied about 4% of the photoelectrode surface, leaving 96% of the surface free for light penetration into the p-Si/TiO2 substrate and for electron–hole generation (Fig. 1(b) and ESI,† Fig. S4). Using this photolithography method, we also loaded other patterned metals, such as Ag, Cu, and Pd, on Si/TiO2 photoelectrode. Since Au was the most effective in the NO3− reduction reaction to produce NH3, we selected Au as the main electrocatalyst (Fig. 1(c), (d), and ESI,† Fig. S5). The determined band alignments of p-Si with and without metal catalyst doping are depicted in ESI,† Fig. S6. A large downward band bending of 0.4 eV was observed for the p-Si photoelectrode without Cu or Au catalyst doping. The photogenerated electrons are transferred to the conduction band of silicon upon light irradiation. However, due to the small band gap, the photoexcited electrons recombine, likely leading to an inactive surface for NO3− reduction (ESI,† Fig. S6a). After Cu metal doping, the band bending was slightly decreased, resulting in an improvement in the photocurrent density and onset potential (ESI,† Fig. S6b). When Au catalyst was deposited on the surface, the Schottky barrier created due to its high work function facilitated electron transfer to the surface. This barrier reduced the backward flow of electrons from the Au to the p-Si, improving the NITRR kinetics and suppressing the recombination of photogenerated electron–hole pairs (ESI,† Fig. S6c). However, due to the weak Cu work function, some of the photogenerated electrons likely returned to p-Si, reducing the PEC performance.
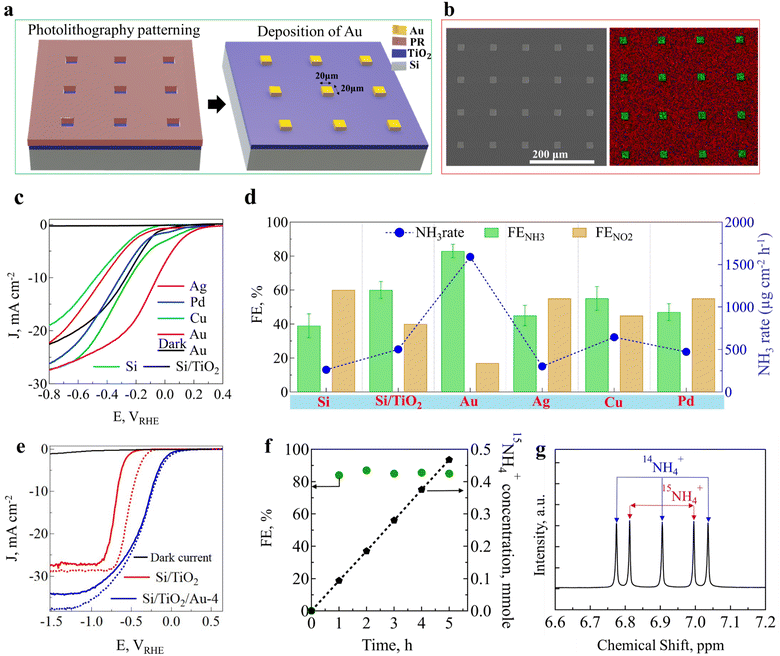 |
| Fig. 1 (a) Schematic of the Si/TiO2/Au-4 photocathode fabrication process. An ultrathin layer of TiO2 was deposited on the surface of p-Si by atomic layer deposition (ALD), and then a low density 20 μm × 20 μm pattern was printed onto the Si/TiO2 substrate using a photolithography process, and then, 100 nm Au was deposited and lifted off in acetone. (b) SEM image and elemental mapping of Au patterns on the Si/TiO2 surface, red (Si) and green (gold). (c) J–V curves for the photocathodes for patterns with different metals in 0.5 M NO3− and 1.0 M KOH (pH = 14). (d) NH3-production rates and FEs for NH3 and NO2− with the Si/TiO2/M-4 photocathode (M: Au, Pd, Cu, Ag) with different metal pattern deposition at −0.35 V vs. RHE after 2 h in 1.0 M KOH and 0.5 M NO3−, (e) J–V curves for SiTiO2 and Si/TiO2/Au-4 for the electrolyte containing 0.5 M KNO3 (solid line) and KNO2 (grid line) at pH = 14. (f) FE% and 15NH4+ concentration for isotopically labelled 0.5 M 15NO3− as a nitrogen-containing source in 1.0 M KOH. (g) 1H-NMR graphs for a control electrolyte containing the same molar ratio of 14NO3− and 15NO3−. | |
We first investigated the role of the TiO2 layer in the PEC NO3− reduction reaction to produce NH3. As shown in Fig. 1(c) and ESI,† Fig. S7a, the onset potential was shifted by 0.21 V toward a more positive potential, and the PEC performance was improved by nearly 27% for Si/TiO2 compared to the Si photoelectrodes. Furthermore, Si/TiO2 demonstrated a higher NH3 FE of 60% compared to 40% for the bare Si (ESI,† Fig. S7b). Therefore, the ALD-deposited TiO2 layer could not only protect the Si surface from chemical etching, but also improved the PEC performance and selectivity for NO3− reduction to NH3. The role of Au on bare p-Si and Si/TiO2 was also examined. In both cases, Au loading improved the onset potential and photocurrent density due to the catalytic activity of Au active sites for the reduction of NO3− ions (ESI,† Fig. S7a). Subsequently, with an optimized Au pattern on the TiO2 layer, the NH3 FE was improved to 83.4 ± 5.6%. This improvement could be attributed to the critical role of the Au pattern in converting NO3− to NO2− ions, which is well-known to be the RDS (eqn (1)).32 To elaborate, the PEC performance was recorded for Si/TiO2 and Si/TiO2/Au-4 in the presence of NO3− and NO2− aqueous solutions. As shown in Fig. 1(e), the onset potential clearly shifted for Si/TiO2 in the presence of NO2− compared to NO3−. In contrast, the onset potential and PEC performance for Si/TiO2/Au-4 changed only slightly, indicating the crucial role of Au in suppressing the activation energy for the sluggish conversion of NO3− to NO2− in the RDS steps.32 Element mapping of the Au pattern after 24 h continuous NO3− conversion to NH3 was performed for the elements N, K, Si, and Au. As shown in ESI,† Fig. S8, only on the surface of the Au pattern were both N and K detected, corresponding to the attachment of KNO3 on the surface, while on the Si surface these elements were missing. This clearly demonstrated the critical role of the Au pattern in the adsorption and conversion of NO3− ions.
Subsequently, it could be concluded that the Au pattern facilitated the sluggish 2e reduction of NO3− to NO2− (eqn (1)). In the next step (eqn (2)), intermediate NO2− ions are converted to NH3 mainly on the TiO2 surface. Therefore, the kinetics and thermodynamics of NO3− reduction to NH3 (eqn (3)) are accelerated due to the synergistic effect of both the Au and TiO2 layers, which enhances the RDS 2e− reduction of NO3− to NO2− (eqn (1)) and the subsequent 6e− reduction reaction to NH3 (eqn (2)). The results and explanations above were further validated through DFT calculations, as reported in the final section.
| NO3− + H2O + 2e− → NO2− + 2OH− | (1) |
| NO2− + 6H2O + 6e− → NH4OH + 7OH− | (2) |
| NO3− + 7H2O + 8e− → NH4OH + 9OH− | (3) |
To elaborate the competitive reactions of the NITRR and HER, which can occur simultaneously on the photocathode surface, the performance of the Si/TiO2/Au-4 photocathode was measured in the presence and absence of NO3− ions under 1 sun illumination (ESI,† Fig. S9a). The onset potential was shifted about 0.25 V toward a more positive potential in the presence of NO3− ions, attributed to the less thermodynamically demanding NO3− reduction reaction (NITRR) compared to the HER.16 Moreover, an increased photocurrent density of about 20% was observed for the NITRR compared to that of the HER. To further assess the performance of Si/TiO2/Au-4, we quantitatively measured the products in the cathode compartment in the presence and absence of NO3− ions (ESI,† Fig. S9b). For this control experiment, an H-cell configuration was used, with the catholyte connected to a gas chromatography (GC) instrument to measure the H2 evolution. Additionally, a syringe sampling system was employed to take samples from the catholyte solution to measure the NH3 and NO2− concentrations using indophenol blue and Griess procedures, respectively (ESI,† Fig. S10–S12). As shown in ESI,† Fig. S9b, in the absence of NO3− ions, only H2 was evolved. In contrast, in the presence of NO3−, the HER reaction was effectively suppressed and NH3 was produced continuously without H2 gas bubbling. The influence of the product evolution during the PEC performance of Si/TiO2/Au-4 is shown in ESI,† Fig. S9c. It can be seen an stable NH3 production rate with no hydrogen gas evolution.
Another critical point is that we precisely identified the source of NH3 production, attributing it to the reduction of NO3− ions rather than contamination (e.g., NH3 in air and human breath) or formation from other nitrogen-containing sources (e.g., N2, nitrite, amines, and nitrogen oxides, as shown in ESI,† Fig. S13). We next conducted 15NO3− isotope labelling, which allowed us to carefully identify and quantify the source and amount of 15NH3 production via a 1H-NMR calibration curve (ESI,† Fig. S14a and b). Specifically, we observed that the 1H-NMR doublet peak intensity increased over time, as shown in ESI,† Fig. S14c, leading to a consistent increase in 15NH4+ concentration, proving that 15NO3− ions were the only source of NH3 production (Fig. 1(f)). Furthermore, a control experiment was carried out with a mixture of 15NO3− and 14NO3− ions as nitrogen-containing sources. The 1H-NMR spectra presented a mixed spectrum of doublet and triplet peaks attributed to the presence of 14NH4+ and 15NH4+ (Fig. 1(g)).
2.2. Optimization of the Au loading amount on Si/TiO2
As depicted in ESI,† Fig. S15, an optimal surface coverage by the Au pattern is critical for NH3 production. When only a small portion of the photoelectrode's surface was covered by the Au pattern, the reduction of NO3− to NH3 was not efficient; while when the coverage percentage of Au was too high, Au blocked the light, resulting in a dramatic loss in PEC performance (ESI,† Fig. S15). Thus, we optimized the amount of the Au in Si/TiO2/Au-X (X = 0.0, 0.5, 4.0, 25, 50, 100) photocathodes (X correlates to the surface percentage of the photoelectrode that was covered by Au, e.g., X = 100 means the entire surface of the photoelectrode was covered by Au, while X = 4 corresponds to only 4% surface coverage, leaving 96% free for light absorption). The morphologies of the different Au-patterned configurations and their surface coverages are shown in Fig. 2(a). It can be seen that with the increase in Au-pattern density, a larger portion of the Si/TiO2 surface was covered, varying between 0.5% to 50%. Fig. 2(b) shows the influence of the Au-pattern coverage on the photocurrent density and onset potential for the Si/TiO2/Au-X photoelectrodes. It can be that the photocurrent density was improved for Si/TiO2/Au-0.5 compared to that of Si/TiO2, and was a maximum for Si/TiO2/Au-4. As shown in Fig. 2(b), the photoelectrodes with a higher density of Au patterns (e.g., Si/TiO2/Au-25 and Si/TiO2/Au-50) showed reduced photocurrent densities due to the decreased carrier generation by Si because of the light blockage by the Au pattern (ESI,† Fig. S16). The roles of the Au-pattern configurations on the FE of NH3 and NO2− and on the selectivity of NH3 are shown in Fig. 2(c) and (d). As shown in Fig. 2(c), the NH3 FE increased with increasing the Au-pattern density, reaching a maximum value of 89% NH3 FE for Si/TiO2/Au-50, while the FE of NO2− continuously decreased to 11%. In contrast, the NH3-production rate was maximized for the 4% Au-pattern photoelectrode (Si/TiO2/Au-4) with an average of 1590 ± 40 μg cm−2 h−1 (Fig. 2(d)). This obtained NH3-production rate is competitive among other reported PEC NO3−-conversion rates for silicon photocathodes used in PEC NH3 production (ESI,† Table S1).
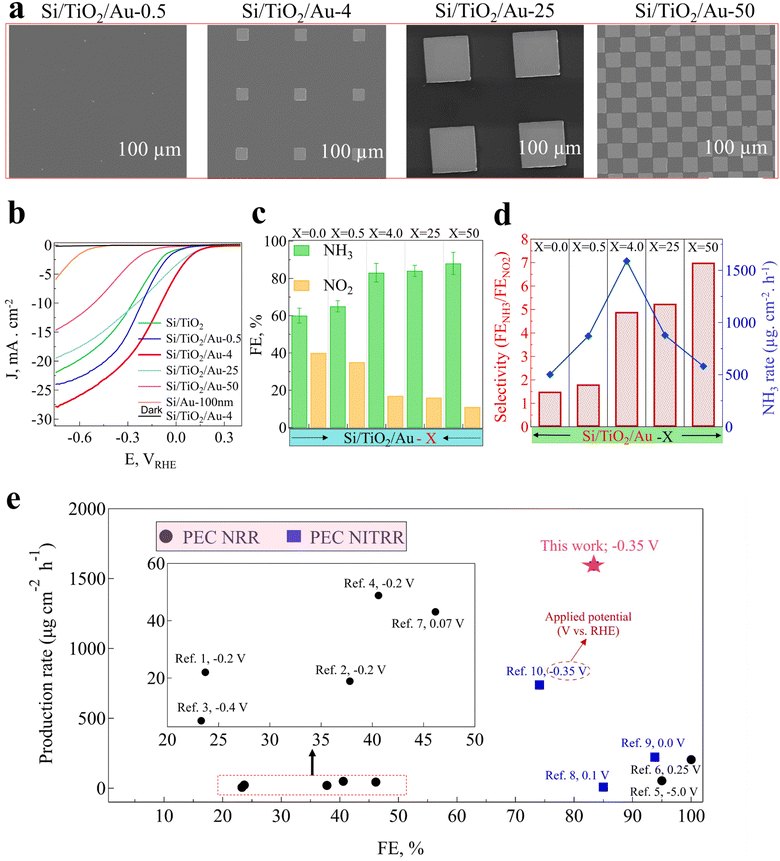 |
| Fig. 2 (a) SEM images of Au pattern with different pattern densities on the surface of Si/TiO2 substrate, (b) J–V curves for photocathodes with different patterns in 0.5 M NO3− and 1.0 M KOH (pH 14), (c) FE%s for NH3, and NO2− for photocathodes with different Au-pattern densities, (d) selectivity and NH3 production rate for different Au-pattern densities at −0.35 V vs. RHE after 2 h in 1.0 M KOH and 0.5 M NO3−, (e) NH3-production rate vs. FE (%), comparison of the current research with previous studies for PEC NH3 production, for more information see ESI,† Table S1 and the references in the supporting file. | |
Although the NH3 FE and FENH3/FENO2 were increased to 88% and 7 for Si/TiO2/Au-50, respectively, the NH3-production rate decreased abruptly to 535 μg cm−2 h−1. This could be attributed to the 50% reduction in light absorption by Si/TiO2/Au-50, consequently leading to deficient electron–hole generation (ESI,† Fig. S16). Next, we quantified the NH3 concentration using both H-NMR and indophenol blue for different Au patterns in order to compare the reliability of the detection procedure. ESI,† Fig. S17 shows there was a good correlation between both detection methods for quantifying NH3 in solution.
To shed more light on the interconnected role of light absorption and pattern density, a COMSOL Multiphysics simulation was carried out.33–35 Here, we calculated the transmitted irradiance and assumed that all transmitted light could participate in charge-carrier generation by p-Si. The detailed computational method presented herein can be found in the “Simulation Method”. ESI,† Fig. S18 and S19 demonstrate that the transmitted light was negligible for the Si/TiO2/Au-100 nm photocathode, leading to the termination of charge-carrier generation by p-Si. However, in the case of Si/TiO2/Au-4 after light illumination, the onset potential was shifted to 0.15 V vs. RHE and the photocurrent density increased to −30 mA cm−2 in −0.9 V vs. RHE, representing a dramatic change with the dark condition (ESI,† Fig. S20). Furthermore, we checked NH3 production under light and dark conditions for Si/TiO2/Au-4 (ESI,† Fig. S21). Under light irradiation, NH3 production followed the theoretical values, under dark conditions the NH3 production dropped to nearly zero. The current densities of the Si/TiO2/Au-4 photoelectrode and the Au electrode alone are shown in ESI,† Fig. S22. The Si/TiO2/Au-4 photoelectrode exhibited an onset potential of 0.15 V vs. RHE for NO3− conversion to NH3, while the Au electrode only showed activity at potentials as low as −0.4 V vs. RHE. Furthermore, the absolute reflectances of the Si/TiO2/Au-X (X = 0, 0.5, 4, 25, 50, 100) photoelectrodes were measured and are shown in ESI,† Fig. S23. It was observed that Si/TiO2 reflected about 31.7% of the incident light due to the shiny surface of both the Si and TiO2 layers. The Au pattern with only 0.5% surface coverage slightly increased the light reflectance, while the Au patterns with 4%, 25%, and 50% coverages increased the incident light proportionally increased the light reflectance in the visible region. Furthermore, 100% surface coverage with Au deposition could reflect 100% of the incident light, effectively acting like a mirror and preventing light transmission into the Si photoelectrode. We next investigated the effect of the applied potential and pH on the activity and NH3 FE of Si/TiO2/Au-4 as the most effective photoelectrode for the conversion of NO3− to NH3. All the possible reduction reactions products, including H2, NH3, and NO2 were measured and are shown in ESI,† Fig. S24a at different applied potentials. ESI,† Fig. S25a indicates that at low cathodic applied potentials, NH3 and NO2 were the main products on the surface of the Si/Ti/Au-4 photocathode. Although the NH3 FE at 0.044 V vs. RHE was comparable to that at −0.35 V vs. RHE, the photocurrent density for the NITRR was much lower, resulting in a lower NH3-production rate (ESI,† Fig. S24b). At an applied potential of −0.35 V vs. RHE, Si/TiO2/Au-4 showed a maximum NH3 FE of 83.4 ± 5.6%. With increasing the applied potential to more negative regions (e.g., −1.05 or −1.35 V vs. RHE), the HER reaction became more competitive with the NITRR, leading to an FE of about 40% corresponding to H2 and 30% related to NH3. One of the most influential operational parameters in the PEC conversion of NO3− to NH3 is the pH of the electrolyte. Consequently, we measured the LSV for Si/TiO2/Au-4 in three different pH media: acidic (0.5 M H2SO4), neutral (0.5 M Na2SO4), and alkaline (1.0 M KOH) with the same concentration of NO3− (0.5 M KNO3). As can be seen in ESI,† Fig. S24c and d, the Si/TiO2/Au-4 photoelectrode showed the highest performance in the alkaline medium. The FEs for the possible products were measured at −0.35 V vs. RHE in both acidic and alkaline media, and are shown in ESI,† Fig. S24d. The results indicated that in the acidic medium, HER became a more competitive reaction with the NITRR, while in the alkaline medium, NH3 was the main product. In the acidic medium, only 25% of the photocurrent was utilized for transforming NO3− to NH3 (FE < 25%), while about 70% of the photocurrent was utilized for the conversion to H2 gas. In the basic solution (KOH 1.0 M), NO3− reduction to NH3 predominantly occurred, with an NH3 FE of >88% ± 5%, while the HER reaction was effectively suppressed and no gas bubble were observed on the surface of the photocathode.
The concentration of NO3− ions can also influence the performance and NH3 FE of Si/TiO2/Au-4, as shown in ESI,† Fig. S25. It could be observed that when the NO3− concentration was decreased to 0.1 M (i.e., 5 times less), the current density decreased by 50% compared to that of the 0.5 M concentration (ESI,† Fig. S25a and b). Surprisingly, the Si/TiO2/Au-4 photoelectrode maintained a high NH3 FE even at the lower concentration of 0.025 M (ESI,† Fig. S25c). This demonstrates the reliability of the photoelectrode for converting low concentrations of NO3− ions into NH3. Furthermore, we measured the performance of Si/TiO2/Au-4 in the presence of SO42− and NO3− with different NO3− concentrations at neutral pH (ESI,† Fig. S26). The results indicated that even in the presence of interfering ions, such as SO42−, the performance of the photoelectrode was only slightly changed with decreasing the NO3− concentration.
2.3. Stability of the Si/TiO2/Au-4 photoelectrode
In order to investigate the stability of the Si/TiO2/Au-4 photoelectrode, its top-view surface morphology was analyzed by SEM before and after PEC NO3− reduction (Fig. 3(a) and (b)). The SEM images of Si before PEC measurement showed it had a smooth surface, while after immersing the photocathode in the electrolyte and starting the experiments in KOH solution, a 3D pyramidal structure was observed on the surface of p-Si. This could be attributed to the anisotropic chemical etching of the silicon surface by the KOH aqueous solution, which is a phenomenon that has been known about for a long time.36–38 After the deposition of a thin TiO2 protective layer, the Si/TiO2 photocathode surface remained unchanged and could sustain its integrity after the PEC NO3−-reduction experiments (Fig. 3(a) and (b)). Moreover, ESI,† Table S2 summarizes the concentrations of Si, Au, and Ti ions in the catholyte solution, in which the Si concentration reached 11.2 ppm for the Si photoelectrode compared to 0.1 ppm for Si/TiO2 (ESI,† Fig. S27). Fig. 3(a) shows the detachment of part of the Au pattern in the Si/Au photoelectrode after the PEC experiments, resulting in an increase in Au ion concentration approaching 0.8 ppm. In contrast, the Au patterns remained unchanged on the surface of Si/TiO2/Au-4 after PEC NO3− reduction, and there were no empty or damaged arrays, leading to a very low Au ion concentration of 0.001 ppm. Furthermore, the ICP results in ESI,† Table S2 indicate there was a very low concentration of Ti ions in the catholyte, highlighting the role of the TiO2 layer as a protective surface. The impact of Au-pattern detachment on the PEC performance and NH3 FE could also be observed in Fig. 3(c) and (d). Chronopotentiometry measurements were next performed, with a constant −0.2 V vs. RHE obtained for the Si/TiO2/Au-4 photoelectrode, while the voltage continuously decreased for Si/Au to sustain the −10 mA cm−2 current density. The NH3 FE measurement also showed a stable trend for Si/TiO2/Au-4, while it decreased for the Si/Au-4 photoelectrode. Finally, the long-term stability for PEC NO3− reduction to NH3 was investigated for Si/TiO2/Au-4 at −0.35 V vs. RHE for 44 h (Fig. 3(e)). A stable NO3−-reduction photocurrent density was recorded, as well as an almost linear increase in NH3 concentration over time. Fig. 3(f) shows that the NH3 FE remained constant over 24 h of operation in the range of 83.4 ± 5.6%. Moreover, we investigated the surface morphology of the Si/TiO2/Au-4 photoelectrode after 44 h continuous operation (ESI,† Fig. S28). Both the AFM and SEM images showed the clean and smooth surface the Au pattern with a height of about 100 ± 5 nm before starting the PEC performance tests. After 44 h PEC conversion of nitrate in the catholyte, the surface of the Au pattern became slightly rough (±10 nm), while the height of the Au pattern stayed in almost the same range.
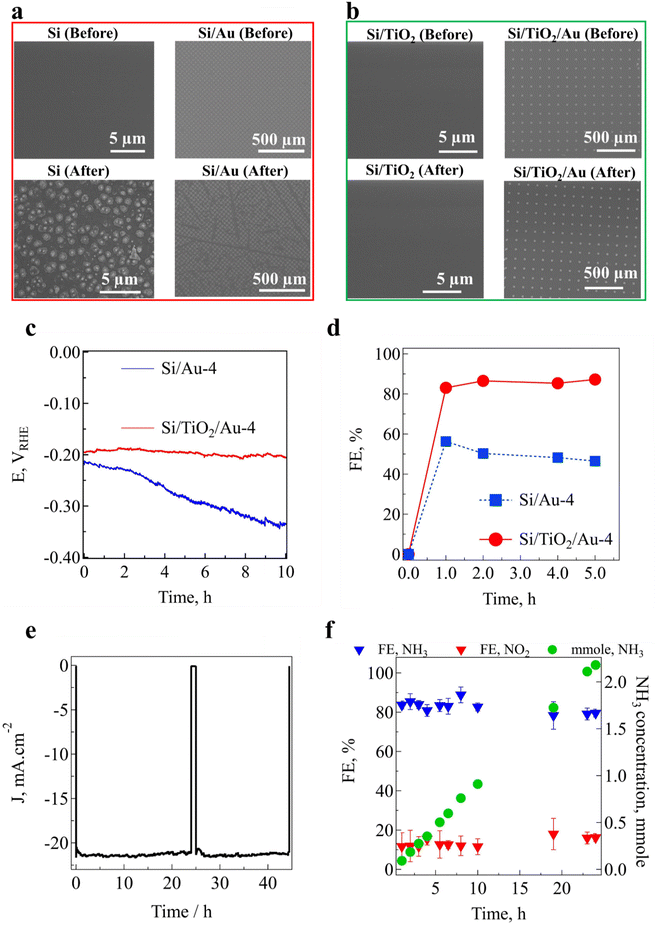 |
| Fig. 3 (a) and (b) Top-view SEM images of photoelectrodes before and after 24 h PEC nitrate (NO3−)-reduction measurements, (c) chronopotentiometry (−10 mA cm−2) curves for Si/Au-4 and Si/TiO2/Au-4 photocathodes in 0.5 M KNO3 at pH 14, (d) FE (%) for Si/Au-4 and Si/TiO2/Au-4 photocathodes in 0.5 M KNO3 at pH = 14 J–V curves, (e) long-term chronoamperometry stability PEC NO3− reduction of Si/TiO2/Au-4 at −0.35 V vs. RHE in 1 M KOH with 0.5 M NO3−, and (f) evolution of the FEs and concentration of NH3 and NO2− for 24 h continuous PEC NITRR. | |
2.4. Theoretical insight into the NO3−-reduction mechanism
Next, we sought to gain an atomistic-scale understanding of the NO3−-reduction reaction using density functional theory (DFT). The stable structures of rutile TiO2(110), Au(111), and Si(111) were taken into account in our simulation (more information is provided in the computational method and ESI,† Fig. S29–S32). Electrochemical NO3− reaction involves an 8 proton–electron coupled mechanism (NO3− + 6H2O + 8e− → NH3 + 9OH−), leading to many intermediate steps and by-products, as well as the competing hydrogen evolution reaction (HER). NO3− adsorption on the catalyst surface is the primary step for NH3 synthesis ahead of the deoxygenation/hydrogenation steps. There are two adsorption modes for NO3− on the surface in which, namely, one or two metal-to-oxygen (M–O) bonds can be formed. As shown in Fig. 4(a), the preferred configuration for NO3− adsorption is on TiO2, while Au is formed with two and one M–O bond, respectively, and Si strongly adsorbs NO3− (ΔG = −1.67 eV) with one M–O bond. The Au surface is a better adsorption site for NO3− than TiO2, according to the free-energy diagram. The charges transferred from the substrate to adsorbed *NO3 on Au and TiO2 are 0.61 e and 0.51 e (Fig. 4(b)), respectively, which is further evidence of the potential of Au to adsorb NO3− ions. The *NO3 protonation step (*NO3 to *HNO3) is downhill for all the catalysts, while on the Si surface the intermediate structure of *NO2 + *OH is generated. The strong *NO3 adsorption on Si causes an easy first protonation step, but the second step (*NO2 + *OH to *NO2) is the potential determining step (PDS) with a barrier energy of 1.46 eV, representing the highest barrier among the three catalysts, as well. First principle calculations disclosed that the desorption of *NO2 species on the Au surface requires overcoming a large barrier of 1.8 eV, ensuring subsequent reactions towards the final product (NH3). The free-energy change of the NO molecule (NO(g) to *NO) on TiO2 (−0.33 eV) is more negative than on Au (−0.12 eV), as shown in Fig. 4(c), demonstrating a better potential of TiO2 for the subsequent reactions (*NO, *NOH, *N, *NH, *NH2, *NH3), most of which are exothermic processes. The free-energy change of *NO to *NOH acted as the PDS on TiO2 with an ultralow limiting potential of −0.14 V, which is much lower than that of Au at −1.12 V. It is worth noting that even employing the DFT+U scheme did not significantly alter the results, in which the free-energy change for the protonation step of *NO to *NOH was downhill as well, with a small change of 0.09 eV for the adsorption energy of NO3− on TiO2.
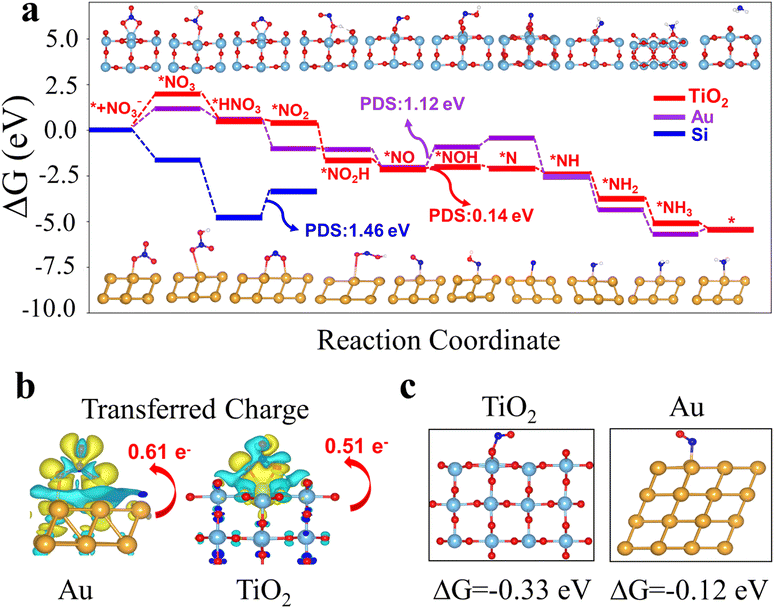 |
| Fig. 4 (a) Free-energy diagram for electrochemical NO3− reduction to ammonia (NH3) on TiO2(110), Au(111), and Si(111) (b) Charge-density difference for Au(111) and TiO2(110), where the yellow and cyan colours depict charge accumulation and charge depletion, respectively. (c) Adsorption free-energy changes of NO(g) to *NO on TiO2(110) and Au(111). Colour code, Ti: light blue, Au: gold, O: red, N: blue, H: white. | |
The suppression of the competing HER reaction is imperative for an efficient NO3− reaction. We calculated the adsorption free energy of *H on the catalysts. The ΔG*H (* + H+ + e− → *H) on Au(111) was +0.26 eV, which was about two times larger than the PDS (0.14 eV) of the NITRR (ESI,† Fig. S33), demonstrating that NH3 was by far the most generated product compared to H2. Furthermore, the results showed that the ΔG*H on TiO2 as the main catalyst was 2.39 eV (metal site), indicating that the HER would be strongly suppressed. The more negative limiting potentials of the HER indicate that the NITRR would be the dominant reaction, leading to outstanding selectivity. In addition, protons (H+) are better nucleophiles than NO3− in the electrolyte, resulting in a better adsorption of NO3− at the electron-deficient metal centres.
In the first step, both Au and TiO2 surfaces can adsorb NO3−, with the adsorption free energy on Au (1.16 eV) being much lower than on TiO2 (1.95 eV). Once the reaction is triggered, subsequent reactions can easily proceed on TiO2 and Au, while NO gas can be chemisorbed on TiO2 with a low limiting potential of −0.14 V for NH3 production. In fact, the Au surface is effective at capturing NO3− ions and transforming them into *NO species, while TiO2 mainly catalyzes NO3− to NH3 with a largely reduced onset potential (0.14 eV). The PDS of Si is very high (1.46 eV), which prevents the efficient reduction of NO3− to NH3, aligning with our experimental results. These DFT results demonstrate the synergistic effect of Au and TiO2 layers for selective NH3 production from NO3− reduction.
3. Conclusion
The synergistic role of Au pattern and TiO2 layer was elaborated for the PEC conversion of NO3− ions into NH3 using Si photocathodes. The ALD-TiO2 layer demonstrated multifunctional duties, including chemical etching protection, serving as an adhesion layer for the catalyst/Si interface, and catalyzing NO3− reduction to NH3. The Au pattern facilitated the 2e− RDS of NO3− to NO2− reduction, resulting in enhanced PEC performance for Si/Au and Si/TiO2/Au after printing the Au pattern on the electrodes. The ideal pattern density of Au was also investigated by determining the NH3 production rate and FE for different pattern configurations. The Si/TiO2/Au-4 photoelectrode, which had a 4% Au-pattern coverage of the Si/TiO2 surface, demonstrated a high NH3 production rate of 1590 ± 40 μgNH3 cm−2 h−1 at −0.35 V vs. RHE, which is the highest value reported yet for PEC NH3 production with silicon photocathodes.
4. Experimental section
4.1. Preparation of p-type silicon
As-supplied p-type boron-doped 〈100〉 silicon wafers (p-Si) with a resistivity of 10–20 Ohm m and 525 μm thickness (Atecom Ltd, Taiwan) were utilized as substrates for the fabrication of the photocathode. To remove the oxide layer (SiO2), the p-Si wafers were immersed in 10% HF aqueous solution just before a thin layer of TiO2 was deposited using the atomic layer deposition (ALD) technique.
4.2. Atomic layer deposition
A 20 nm TiO2 layer was coated by ALD (Lucida D100) onto an HF-treated p-Si wafer using a TTiP precursor and H2O at 150 °C at a flow rate of 6.5 ml min−1. To achieve adequate vapour pressure, the C8H24N4Ti was heated to 75 °C. A sequential process was utilized and adjusted for 20 nm deposition of the TiO2 layer onto the p-Si substrate.
4.3. Photolithography process for the fabrication of Au patterns
The metal frame formation process included the standard photolithography process, metal deposition, and subsequent lift-off. In the photolithography process, the Cr photomask was designed to make patterns of different sizes and densities (5 × 5 μm, 20 × 20 μm low density, 20 × 20 μm high density, and 75 × 75 μm). The photoresist (PR, AZ5214E, positive) was spin-coated at 4000 rpm for 60 s, followed by soft baking at 95 °C for 60 s. The sample was illuminated by a UV lamp in a mask aligner through a Cr mask with an exposure dose of 90 mJ cm2. After the exposure, the sample was developed in MIF 300 (metal-ion tree) developer for more than 50 s.30,31,39
A 100 nm metallic film was deposited by an e-beam evaporator (KVE-E4000) without rotation at a rate of 0.3 Å s−1 to fill the holes of the photoresist patterns. A thin 3 nm layer of Cr was evaporated before the metallic film to increase the adhesion of the metallic layer and TiO2 frame. Finally, the desired pattern was obtained by lifting off the resist in acetone and by oxygen plasma treatment using a plasma asher system to remove extra PR residue.
In the Si/TiO2/Au-X photoelectrode, where X is correlated to the percentage of the photoelectrode surface covered by Au: for example, X = 100 means the entire surface is covered by gold, which leads to minimal light absorption because gold typically absorbs light in the visible and near-infrared range. In the case of 0 < X < 100, as the gold coverage (X) decreases, a larger portion of the surface is exposed, allowing for increased light absorption by the underlying Si material. Finally, for X = 0, with no gold coverage, the photoelectrode has maximum light absorption, but the silicon surface is inactive for nitrate conversion to NH3.
4.4. Characterization
The Si surface and Au pattern morphologies were analyzed by field emission scanning electron microscopy (FE-SEM, S4800, HITACHI) and energy-dispersive X-ray spectroscopy. UV-visible-diffuse reflectance spectroscopy (UV-DRS) was used to measure the reflectance of p-Si and the different patterns on the p-Si substrate using a UV-3600 instrument (Shimadzu). The Si and Au contents in the catholyte solutions were evaluated by inductively coupled plasma optical emission spectrometry (Varian 700-ES).
4.5. Photoelectrochemical nitrogen reduction
The PEC measurements were conducted using a customized H-type cell configuration with a Nafion membrane (Fuel Cell Store) to separate the catholyte and anolyte. The catholyte compartment was equipped with a gas-sealed Ar flow inlet and outlet, and was connected online to a gas chromatography system (GC, X) to detect the evolution of H2 during the PEC measurements. Additionally, a gas-sealed syringe connection was installed in the catholyte for taking liquid samples for measurement of the NH3 and NO2− concentrations using indophenol blue and Griess protocols, respectively. A potentiostat (IviumStat, Ivium Technologies) was used to collect and analyze the PEC data in a three-electrode system with Hg/HgO (or Ag/AgCl) as the reference electrode, Pt wire as the counter electrode, and Si/Ti/Au photocathodes as the working electrode. To simulate 1 sunlight illumination (100 mW cm−2), a 1.5 G filter was placed in front of a Xe lamp (300 W) and the light intensity was calibrated with a reference certified by NREL, USA. The pH of the electrolyte was adjusted using 1.0 M KOH, 0.5 M H2SO4, and K2SO4 for obtaining alkaline, acidic, and neutral electrolytes, respectively. Also, 30 ml of electrolyte containing NO3− at various concentrations was used in the catholyte for the PEC measurements. Before each measurement, the surface of the photocathodes was scanned by J–V to ensure a stable surface of the Si–Ti–Au photocathodes. The Faraday efficiencies (FEs) for NH3 and NO2 and the selectivity for NH3 were calculated as follows: | 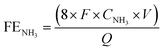 | (4) |
| 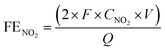 | (5) |
|  | (6) |
4.6. Ammonia detection process
The ammonia concentration was measured using the well-known indophenol blue spectroscopy method.7,8 Samples were appropriately diluted and mixed with 1 ml NaOH (1 M) containing 5 wt% salicylic acid and 5 wt% sodium citrate solution. Next, 0.5 ml of 0.05 M NaClO was added to the solution, followed by 0.1 ml sodium nitroferricyanide solution (1.0 wt%). The mixture was kept in the dark for 1 h before being analyzed with a UV-Vis spectrophotometer. The peak absorbance at 655 nm wavelength was recorded, and the concentrations were calculated using a standard concentration–absorbance calibration curve with NH4Cl solution (ESI,† Fig. S10).
Furthermore, a 500 MHz nuclear magnetic resonance (NMR) spectrometer was used to measure the NH3 concentration according to a previously reported procedure. After diluting the samples to fall within the detection range, they were mixed with 0.1 ml DMSO. The sample was measured with a Liquid Bruker Avance NMR spectrometer (ESI,† Fig. S11).
4.7. Nitrite-detection process
The NO2− concentration was also calculated using a spectroscopy procedure as previously reported.7,8 Here, a 2.0 g solution of p-aminobenzenesulfonamide was dissolved in 50 ml and kept at low temperature (T < 5 °C). Another solution was then prepared by mixing 0.1 g ethylenediamine dihydrochloride with 3.94 ml phosphoric acid in 50 ml deionized water. Before the UV-vis measurements, the volumes of the prepared solutions were mixed and kept in the fridge for detection. Then 1.0 ml of the samples was diluted to fall within the detection range, mixed with 2.0 ml 0.5 M H2SO4 solution, and then combined with 1 ml of the colour reagent. The peak intensity at 540 nm was measured by UV-vis spectrophotometry (UV-2600). The concentration was calculated using the concentration–absorbance calibration curve fitting equation (ESI,† Fig. S12).
4.8. COMSOL multiphysics simulation
We calculated the transmitted irradiance at the Au/Si and water/Si interfaces. Assuming that all the transmitted light is eventually absorbed in the Si substrate, the transmitted irradiance can be regarded as the absorbed irradiance. The transmitted irradiance It can then be written as follows: | 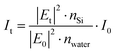 | (7) |
where Et and E0 are the transmitted and incident electric fields, respectively, nSi is the real part of the refractive index of Si, nwater is the refractive index of water, and I0 is the incident irradiance. We set nwater = 1.33 and I0 is given by the reference spectral data in ‘ASTM G173-03’, while |Et|2/|E0|2 can be determined by considering the Fresnel coefficients and multiple reflections.33 For the Au/Si interface, |  | (8) |
where ñAu and ñSi are complex refractive indexes of Au and Si, respectively, k0 is the free-space wavenumber, and h is the Au film thickness. For ñAu and ñSi, we used the previously tabulated data.35 For the water/Si interface, | 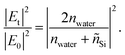 | (9) |
The simulation for the energy flux |Sz/S0| distribution was conducted using COMSOL Multiphysics 6.0 at a wavelength of 480 nm where the transmitted irradiance at the water/Si interface is the maximum. The Au film width was scaled down to 1 μm to reduce the computational burden, but to represent the physical implication yet.
4.9. Computational details
The spin-polarized density functional theory (DFT) implemented in the Vienna ab initio simulation package (VASP) was used for all the calculations.40 The Perdew–Burke–Ernzerhof (PBE)41 functional within the generalized gradient approximation (GGA) was used to model the exchange–correlation interactions, while the van der Waals (vdW) corrections were described by the Tkatchenko–Scheffler (TS) scheme.42 The projector augmented wave method (PAW) was employed to describe the electron–nucleus interactions. The energy cutoff was 500 eV and at least a 15 Å vacuum space was applied to avoid interactions between adjacent layers in the perpendicular direction to the surface. Nine, four and six layers of rutile TiO2(110), Au(111), and Si(111) were utilized to model our slab geometries (Fig. S1, ESI†). Among the catalysts, except for the two bottom layers of TiO2 which were fixed, all other layers were fully relaxed using 2 × 2 × 1, 4 × 4 × 1, and 1 × 1 × 1 Monkhorst–Pack k-point grids for TiO2(110), Au(111), and Si(111) (a supercell of 96 atoms), respectively. The energy convergence and residual force criteria in the self-consistent field (SCF) were set to 10−5 eV and 0.02 eV Å−1, respectively. The Gibbs free energy was calculated based on the computational hydrogen electrode (CHE).43 The free energy change was calculated by ΔG = ΔE + ΔZPE − TΔS + ΔGU, where ΔE is the electronic energy difference, ΔZPE is the difference in the zero-point energy, T is the temperature (298.15 K), ΔS is the entropy change, and ΔGU (−eU) is the free energy related to the applied electrode potential, while U and e are the applied potential and the charge of the electron, respectively. The limiting potential (UL) was employed to evaluate the catalytic activity. Here, UL was obtained by considering the potential determining step (UL = −ΔGPDS/e). Since dealing with charged NO3− species in periodic DFT calculation is challenging, we chose natural HNO3(g) as the reference value as follows:44,45 | * + HNO3(g) → *NO3 + H+ + e− | (10) |
ΔG*NO3 = G*NO3 − GHNO3 − G* + 0.5G*H2 + ΔGcorrection |
where G*, GHNO3, G*NO3, and GH2 are the Gibbs free energy of the substrate, HNO3, NO3− adsorbed on substrates, and H2 molecules in the gas phase, respectively. In addition, ΔGcorrect indicates the correction of the adsorption energy, which is added to eqn (S1) (ESI†) (0.392 eV).46
The elementary steps for the NITRR can be described as follows (in adsorbed *NO, N is attached to the metal):
| *NO3 + H+ + e− → *HNO3 | (12) |
| *HNO3− + H+ + e− → *NO2 + H2O | (13) |
| *NO2 + H+ + e− → *HNO2 | (14) |
| *HNO2 + H+ + e− → *NO + H2O | (15) |
| *NOH + H+ + e− → *N + H2O | (17) |
| *NH2 + H+ + e− → *NH3 | (20) |
Author contributions
A. T. and J.-W. J. conceived and proposed this work. A. T. and J. J. performed and designed the experiments and analysis. M. H. fabricated the Au pattern on Si wafer directed by D. K. J. J. and A. T. measured the PEC performance for NITRR with quantification of products. A. T., J. J., M. T., and Ch. S. characterised and interpreted the photoelectrodes physiochemical and morphological properties. M. Z. and G. L. performed the DFT calculations and wrote the corresponding section. D. L. conducted the COMSOL Multiphysics simulations directed by D. K. A. T. and J.-W. J. co-wrote the manuscript. M. G. L. revised the manuscript and H.-J. G. performed experiments regarding the effect of light. All authors read and commented on the manuscript.
Data availability
All the experimental data are included in the main text or in the ESI.†
Conflicts of interest
The authors declare no competing interests.
Acknowledgements
This work was supported by the National Research Foundation (NRF; RS-2023-00222006, 2019H1D3A1A01103006, 2022H1D3A3A01081140, and RS-2023-00257666), as well as the Research Fund (1.240005.01) of the UNIST, sponsored this study (Ulsan National Institute of Science and Technology). A. T. and M. G. L. acknowledges financial support from the European Union (Marie Skłodowska-Curie Actions, 101107294).
References
- Y. Kojima and M. Yamaguchi, Ammonia as a hydrogen energy carrier, Int. J. Hydrogen Energy, 2022, 47, 22832–22839 CAS
.
- B. H. R. Suryanto,
et al., Challenges and prospects in the catalysis of electroreduction of nitrogen to ammonia, Nat. Catal., 2019, 2, 290–296 CrossRef CAS
.
- M. Wang,
et al., Can sustainable ammonia synthesis pathways compete with fossil-fuel based Haber–Bosch processes?, Energy Environ. Sci., 2021, 14, 2535–2548 RSC
.
- D. R. MacFarlane,
et al., A Roadmap to the Ammonia Economy, Joule, 2020, 4, 1186–1205 CrossRef CAS
.
- J. Zheng, L. Jiang, Y. Lyu, S. P. Jian and S. Wang, Green Synthesis of Nitrogen-to-Ammonia Fixation: Past, Present, and Future, Energy Environ. Mater., 2021, 452–457, DOI:10.1002/eem2.12192
.
- V. Rosca, M. Duca, M. T. DeGroot and M. T. M. Koper, Nitrogen Cycle Electrocatalysis, Chem. Rev., 2009, 109, 2209–2244 CrossRef CAS PubMed
.
- S. Ghavam, M. Vahdati, I. A. G. Wilson and P. Styring, Sustainable Ammonia Production Processes, Front. Energy Res., 2021, 9, 1–19 Search PubMed
.
- V. Kyriakou, I. Garagounis, A. Vourros, E. Vasileiou and M. Stoukides, An Electrochemical Haber–Bosch Process, Joule, 2020, 4, 142–158 CrossRef CAS
.
- C. Arnaiz del Pozo and S. Cloete, Techno-economic assessment of blue and green ammonia as energy carriers in a low-carbon future, Energy Convers. Manage., 2022, 255, 115312 CrossRef CAS
.
- P. M. Krzywda,
et al., Electroreduction of NO3− on tubular porous Ti electrodes, Catal. Sci. Technol., 2022, 3281–3288, 10.1039/d2cy00289b
.
- D. Liu,
et al., Photoelectrochemical Synthesis of Ammonia with Black Phosphorus, Adv. Funct. Mater., 2020, 30, 1–7 Search PubMed
.
- N. C. Kani, A. Prajapati and M. R. Singh, Sustainable Routes for Photo-Electrochemical Synthesis of Ammonia Using Various Nitrogen Precursors, ACS ES&T Eng., 2022, 2, 1080–1087 Search PubMed
.
- R. Daiyan,
et al., Nitrate reduction to ammonium: From CuO defect engineering to waste NOx-to-NH3 economic feasibility, Energy Environ. Sci., 2021, 14, 3588–3598 RSC
.
- H. Okamoto,
et al., Effects of annealing conditions on the oxygen evolution activity of a BaTaO2N photocatalyst loaded with cobalt species, Catal. Today, 2019, 354, 204–210 CrossRef
.
- L. Barrera and R. Bala Chandran, Harnessing Photoelectrochemistry for Wastewater Nitrate Treatment Coupled with Resource Recovery, ACS Sustainable Chem. Eng., 2021, 9, 3688–3701 CrossRef CAS
.
- A. Tayyebi,
et al., Bias-free solar NH3 production by perovskite-based photocathode coupled to valorization of glycerol, Nat. Catal., 2024, 7, 510–521 CrossRef CAS
.
- J. Saari,
et al., Interface Engineering of TiO2 Photoelectrode Coatings Grown by Atomic Layer Deposition on Silicon, ACS Omega, 2021, 6, 27501–27509 CrossRef CAS PubMed
.
- S. Hu,
et al., Amorphous TiO2 coatings stabilize Si, GaAs, and GaP photoanodes for efficient water oxidation, Science, 2014, 344, 1005–1009 CAS
.
- M. Hannula,
et al., Improved Stability of Atomic Layer Deposited Amorphous TiO2 Photoelectrode Coatings by Thermally Induced Oxygen Defects, Chem. Mater., 2018, 30, 1199–1208 CrossRef CAS PubMed
.
- M. Ali,
et al., Nanostructured photoelectrochemical solar cell for nitrogen reduction using plasmon-enhanced black silicon, Nat. Commun., 2016, 7, 1–5 Search PubMed
.
- M. Xu,
et al., Atomic layer deposition technique refining oxygen vacancies in TiO2 passivation layer for photoelectrochemical ammonia synthesis, Compos. Commun., 2022, 29, 101037 CrossRef
.
- H. E. Kim,
et al., Photoelectrochemical Nitrate Reduction to Ammonia on Ordered Silicon Nanowire Array Photocathodes, Angew. Chem., Int. Ed., 2022, 61, e202204117 CrossRef CAS PubMed
.
- H. Huang,
et al., Lithium-Mediated Photoelectrochemical Ammonia Synthesis with 95% Selectivity on Silicon Photocathode, ACS Energy Lett., 2023, 8, 4235–4241 CrossRef CAS
.
- J. Zheng,
et al., Photoelectrochemical Synthesis of Ammonia on the Aerophilic-Hydrophilic Heterostructure with 37.8% Efficiency, Chem, 2019, 5, 617–633 CAS
.
- N. S. Lewis and D. G. Nocera, Powering the planet: Chemical challenges in solar energy utilization, Proc. Natl. Acad. Sci. U. S. A., 2006, 103, 15729–15735 CrossRef CAS PubMed
.
- P. Thangavel,
et al., Graphene-nanoplatelets-supported NiFe-MOF: High-efficiency and ultra-stable oxygen electrodes for sustained alkaline anion exchange membrane water electrolysis, Energy Environ. Sci., 2020, 13, 3447–3458 RSC
.
- J. Li,
et al., Efficient Ammonia Electrosynthesis from Nitrate on Strained Ruthenium Nanoclusters, J. Am. Chem. Soc., 2020, 142, 7036–7046 CrossRef CAS PubMed
.
- X. Zhang,
et al., Regulating intermediate adsorption and H2O dissociation on a diatomic catalyst to promote electrocatalytic nitrate reduction to ammonia, Energy Environ. Sci., 2024, 6717–6727, 10.1039/d4ee02747g
.
- J. M. McEnaney,
et al., Electrolyte engineering for efficient electrochemical nitrate reduction to ammonia on a titanium electrode, ACS Sustainable Chem. Eng., 2020, 8, 2672–2681 CrossRef CAS
.
- G. Choi,
et al., Enhanced Terahertz Shielding of MXenes with Nano-Metamaterials, Adv. Opt. Mater., 2018, 6, 1–6 Search PubMed
.
- W. Park, J. Rhie, N. Y. Kim, S. Hong and D. S. Kim, Sub-10 nm feature chromium photomasks for contact lithography patterning of square metal ring arrays, Sci. Rep., 2016, 6, 1–6 CrossRef PubMed
.
- W. Jung and Y. J. Hwang, Material strategies in the electrochemical nitrate reduction reaction to ammonia production, Mater. Chem. Front., 2021, 5, 6803–6823 RSC
.
- C. Schinke,
et al., Uncertainty analysis for the coefficient of band-to-band absorption of crystalline silicon, AIP Adv., 2015, 5, 067168 CrossRef
.
- H. Li, Y. Hu, Y. Yang and Y. Zhu, Theoretical investigation of broadband absorption enhancement in a-Si thin-film solar cell with nanoparticles, Sol. Energy Mater. Sol. Cells, 2020, 211, 110529 CrossRef CAS
.
- S. Babar and J. H. Weaver, Optical constants of Cu, Ag, and Au revisited, Appl. Opt., 2015, 54, 477 CrossRef CAS
.
- H. Tanaka, S. Yamashita, Y. Abe, M. Shikida and K. Sato, Fast etching of silicon with a smooth surface in high temperature ranges near the boiling point of KOH solution, Sens. Actuators, A, 2004, 114, 516–520 CrossRef CAS
.
- E. Van Veenendaal, K. Sato, M. Shikida and J. Van Suchtelen, Micro-morphology of single crystalline silicon surfaces during anisotropic wet chemical etching in KOH: Velocity source forests, Sens. Actuators, A, 2001, 93, 232–242 CrossRef CAS
.
- R. Rao, J. E. Bradby and J. S. Williams, Patterning of silicon by indentation and chemical etching, Appl. Phys. Lett., 2007, 91, 1–4 Search PubMed
.
- H. S. Kim,
et al., Phonon-Polaritons in Lead Halide Perovskite Film Hybridized with THz Metamaterials, Nano Lett., 2020, 20, 6690–6696 CrossRef CAS PubMed
.
- D. Joubert, From ultrasoft pseudopotentials to the projector augmented-wave method, Phys. Rev. B: Condens. Matter Mater. Phys., 1999, 59, 1758–1775 CrossRef
.
- J. P. Perdew, K. Burke and M. Ernzerhof, Generalized gradient approximation made simple, Phys. Rev. Lett., 1996, 77, 3865–3868 CrossRef CAS PubMed
.
- A. Tkatchenko and M. Scheffler, Accurate molecular van der Waals interactions from ground-state electron density and free-atom reference data, Phys. Rev. Lett., 2009, 102, 6–9 CrossRef PubMed
.
- J. K. Nørskov,
et al., Origin of the overpotential for oxygen reduction at a fuel-cell cathode, J. Phys. Chem. B, 2004, 108, 17886–17892 CrossRef PubMed
.
- J. X. Liu, D. Richards, N. Singh and B. R. Goldsmith, Activity and Selectivity Trends in Electrocatalytic Nitrate Reduction on Transition Metals, ACS Catal., 2019, 9, 7052–7064 CrossRef CAS
.
- S. Guo,
et al., Insights into Nitrate Reduction over Indium-Decorated Palladium Nanoparticle Catalysts, ACS Catal., 2018, 8, 503–515 CrossRef CAS
.
- H. Niu,
et al., Theoretical Insights into the Mechanism of Selective Nitrate-to-Ammonia Electroreduction on Single-Atom Catalysts, Adv. Funct. Mater., 2021, 31, 2008533 CrossRef CAS
.
|
This journal is © The Royal Society of Chemistry 2025 |
Click here to see how this site uses Cookies. View our privacy policy here.