DOI:
10.1039/D4GC04535A
(Communication)
Green Chem., 2025, Advance Article
Direct synthesis of 2-pyrone-4,6-dicarboxylic acid and trans-aconitic acid from renewable gallic acid and tannic acid†
Received
10th September 2024
, Accepted 11th December 2024
First published on 17th December 2024
Abstract
2-Pyrone-4,6-dicarboxylic acid and trans-aconitic acid, both molecules of high interest for the synthesis of biobased and biodegradable polyesters, could be accessed through the oxidative cleavage of abundant and renewable gallic acid and tannic acid. By optimizing the reaction conditions the selectivity of the reaction could be shifted to either product and the procedure transferred to readily available derivatives of gallic acid.
Introduction
Facing climate change and shortage of fossil resources, it is evident that the chemical industry needs to explore alternative sources for fine chemicals and develop sustainable methods to replace existing processes.1 A focus of research in this area lies in the valorisation of lignin, a polyphenolic biopolymer omnipresent in plants and trees.2 Currently, lignin is processed during pulping on a multi-Mt-scale and accumulates as a side product, being burned on site for the production of energy and recovery of inorganic chemicals. Depolymerization of technical lignin is considered difficult due to structural changes during the harsh process conditions, but several oxidative,3 reductive,4 thermal,5,6 and electrochemical7–12 methods have been developed.13,14 Another side stream of these pulping plants is represented by barks and the tannins therein, which are currently not employed as a chemical feedstock. Besides chemical transformation, biological transformations have received attention, transforming biomass into fine chemicals through fermentation with genetically engineered bacteria. In 1979, 2-pyrone-4,6-dicarboxylic acid (2), was discovered as a product of the enzyme α-hydroxy-γ-carboxymuconic-ε-semialdehyde dehydrogenase, being linked to the bacterial metabolism of protocatechuic acid.15 Noteworthy, protocatechuic acid can be easily obtained from various types of lignin.16 In the early 2000s, 2 received further attention, as it was discovered that sphingomonas paucimobilis SYK-6 could metabolize low-molecular weight compounds derived from lignin to pyrone 2.17 Several follow-up publications detailed efforts to genetically engineer bacteria to produce higher quantities of 2, and change the feedstock to simple glucose.18,19 2-Pyrones are an interesting class of compounds that can undergo a variety of transformations and have been of high interest for synthetic chemists.20 Due to its two carboxylic acids and slightly aromatic feature, it is also a very promising monomer for polyester synthesis. It can be polymerised with glycol resulting in a polymer with similar properties to PET or be used in polyurethanes showing strong adhesive properties.21,22 The inherent advantages of 2 as a monomer, are that it stems from biogenic, underutilized and renewable sources. In addition, this moiety shows a rapid biodegradation and biocompatibility (Fig. 1).23,24
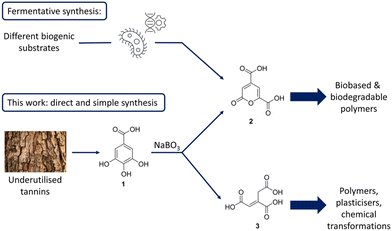 |
| Fig. 1 Current methods for the synthesis of 2 and its use as a monomer. | |
Many publications dealing with the fermentative production or polymerization of 2 remark, that there is no chemical process for the synthesis of this compound reported yet. Due to this, it is not commercially available, and almost not accessible even though it has been mentioned in over 100 publications in the recent years. Although, the polymers of 2 show very interesting properties, research is limited due to the unavailability of 2, as synthetic research labs generally do not possess the necessary equipment for fermentation. Thus, an easy access to this compound would greatly spark the interest in further research on its use as a monomer or building block for synthetic transformations. Within this work, we enabled a single step access to pyrone 2, from renewable and readily available gallic acid (1) in a simple procedure using sodium perborate and acetic acid. Our procedure does not require any elaborate set-up.
Another compound used as a monomer is trans-aconitic acid (3), included in the list of top-30 value-added chemical by the US Department of Energy.25 Industrially, 3 is produced by dehydration of citric acid with sulfuric acid, but again efforts have been made to genetically engineer bacteria, to produce 3 by fermentation.26 Due to its availability, it has a multitude of uses in industrially e.g. as a cross-linker for polyesters or as a building block for other value-added chemicals.
Another class of natural compounds that has gained an increased interest as a potential renewable feedstock for the chemical industry, has been the class of tannins. They can be found in most parts of plants, but accumulate in the bark of trees and especially in oak galls, having a high potential to serve as a renewable source of aromatics, that could serve as platform chemicals next to lignin.27 Tannins are divided into two subclasses: hydrolysable tannins; made up of either gallic or ellagic acid esterified to a sugar core and condensed tannins bearing a flavan core moiety with up to 50 repeating units, linked by a C–C bond.28,29 Hydrolysable tannins have been explored as a natural source for gallic acid with recent developments in extractive procedures with solvents or hot water giving a sustainable access to gallic acid (1).30,31 Since there are only few chemical procedures to make use of these compounds, our investigations started with finding a chemical transformation of gallic acid (1) to value-added compounds.
Results and discussion
In early experiments with 1 it was found that products originating from oxidative ring cleavage could be accessed by using peroxodicarbonate, an electrochemically generated oxidizer established by the Waldvogel group.9,32–34 The mechanism of the oxidative cleavage of catechols was investigated intensively in the 20th century, due to interest in the transformations of catechols by the enzyme pyrocatechase.35,36 A similar reaction was used recently for the oxidative cleavage of lignin-derived catechols, using toxic and precarious reagents such as formic acid and hydrogen peroxide combined with an iron(III) catalyst.37 In our case a system with non-hazardous and readily available sodium perborate (NaBO3·4H2O) and acetic acid, which can be considered a green solvent with no environmental risk, proofed to be most efficient.38 Sodium perborate is a mild oxidiser used on a large scale for its bleaching properties and can be synthesized electrochemically.39,40 It is known, that if sodium perborate is mixed with acetic acid, peracetic acid is formed after some time.41 However, the actual active species remains unclear, since the reactivity differs from peracetic acid.41 The postulated reaction sequence for the oxidative ring cleavage of 1 according to literature42,43 is depicted in Scheme 1 and proceeds through the initial formation of ortho-quinone I. However, this intermediate I gives rise to various side reactions such as oligo- and polymerization. Subsequently, I is cleaved in a Baeyer–Villiger-type oxidation, leading to the cyclic anhydride II, which readily hydrolyses to the tricarboxylic acid III. The ring-opened intermediate can react in two different ways: cyclization after double-bond rotation to form the lactone 2 or oxidative decarboxylation, either by CO extrusion or an oxidant assisted mechanism, to 3.
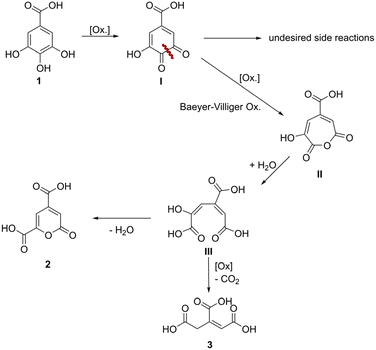 |
| Scheme 1 Proposed reaction sequence for the oxidative conversion of gallic acid (1) to 2 and 3. | |
In a one-variable-at-a-time (OVAT) screening approach, we tried to increase the yield of 2 and the results are depicted in Fig. 2. At the lowest investigated temperature of 25 °C, the formation of 2 is decreased to a yield of 6% meanwhile the yield of 3 is increased to 32%. By increasing the temperature, the yield of 2 increases to 14% at 70 °C, while the yield of 3 continuously drops until it reaches 1% at 100 °C. Regarding the optimization of the equivalents of sodium perborate, a full conversion of starting material 1 was achieved with 3.5 eq. of the oxidizer, while the theoretical amount for the formation of 2 is 2.0 eq. Further equivalents of oxidizer lead to no decrease of product yield, demonstrating their stability towards over-oxidation. The reaction time also showed only little influence. After 1 h 1 is consumed and the products do not degrade at prolonged reaction times. Next, we investigated the influence of the substrate concentration, which showed to have the highest influence on the yield of 2. It was expected, that the yield of observable products could be greatly increased by lowering the concentration of starting material, to suppress oligomerization reactions of the intermediary formed quinone. By decreasing the concentration of 1 from 49 to 12 mM the yield of 2 was increased to 33% while the yield of 3 dropped to 8%. Further dilution hindered the reaction, decreasing the conversion and product formation. Interestingly, the overall yield of observable products never exceeded 41%. With a similar rationale, it was tested if slow addition of starting material could improve the yields. Through this, the yield could not be further increased, but it allowed to use a lower volume of solvent (Fig. 3).
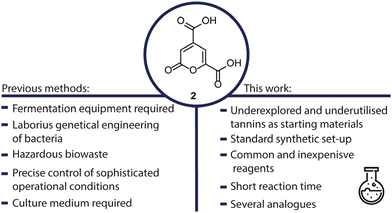 |
| Fig. 2 Comparison of fermentative and novel method for the production of 2. | |
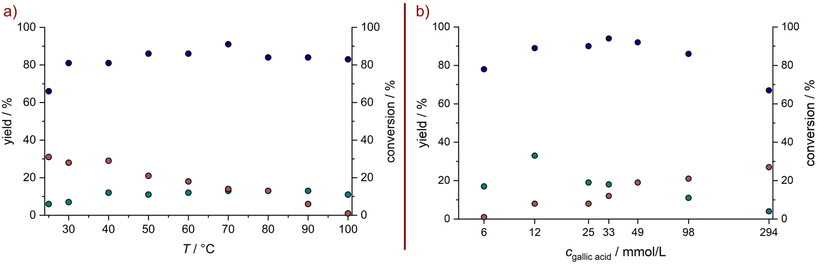 |
| Fig. 3 Optimization of reaction temperature and substrate concentration. Yield of 2 [ ], 3 [ ] and conversion of 1 [ ]. Cond.: (a) 4 h, 2.5 eq. of NaBO3·4H2O, 33 mmol L−1; (b) 4 h, 70 °C, 3.5 eq. of NaBO3·4H2O. Yields were determined by 1H NMR with 1,3,5-trimethoxybenzene as internal standard. | |
Then, the influence of different additives and solvents on the oxidative cleavage was tested and the results are displayed in Table 1.
Table 1 Influence of different additives and solvents on the oxidative cleavage of gallic acid (1). Yields were determined by 1H NMR with 1,3,5-trimethoxybenzene as internal standard
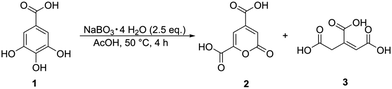
|
Deviation from standard conditions |
Conversion of 1 |
Yield 2 |
Yield 3 |
None |
85% |
11% |
23% |
5 eq. H2SO4 |
40% |
Traces |
Traces |
Peracetic acid |
35% |
n.d. |
n.d. |
20 vol% HFIP |
80% |
8% |
30% |
20 vol% TFE |
77% |
8% |
24% |
Formic acid |
48% |
1% |
1% |
Trifluoroacetic acid |
77% |
4% |
n.d. |
Propionic acid |
80% |
4% |
32% |
Pivalic acid |
58% |
Traces |
8% |
A mixture of sodium perborate in carboxylic acids, provides the corresponding peracids trough a mixed perborate-acid intermediate as postulated by McKillop et Sanderson. Notably, these mixed species were also isolated for use as peracetic acid-releasing detergents.44 The formation of peracetic acid by sodium perborate can be greatly accelerated by adding sulfuric acid, but in our case the yield dropped significantly with addition of sulfuric acid.41 When commercial peracetic acid was used for the reaction, no formation of ring-opened products was observed, emphasizing the essential role of a mixed perborate–acetic acid species. Furthermore, the use of different co-solvent mixtures of acetic acid and fluorinated alcohols were tested, since latter proofed to be beneficial in the hydrogen peroxide mediated Baeyer–Villiger oxidation and other oxidative transformations.45 Here, the presence of fluorinated alcohols showed only adverse effects in different solvent ratios (Table S5†). Different organic acids as mediators in place of acetic acid were also tested, but pure acetic acid performed the best, though propionic acid lead to a 32% yield of 3.
Under optimized conditions, the reaction was conducted on a 1.5 mmol scale and 2 was isolated in a yield of 36%, utilizing a method described by Michinobu et al., who were able to crystallize the compound as its sodium salt from an aqueous brine solution.46 To investigate the scalability of the protocol, the reaction was scaled-up with 55 mmol of starting material 1, yielding 3.13 g (30%) of pyrone 2 in a slightly decreased yield.
The reaction was then transferred to common and readily available derivatives of gallic acid (1). Methyl gallate (1a) gave the corresponding pyrone 2a in a yield of 64%. Interestingly the reaction with amide 1b yielded 51% of pyrone 2b, while it is described in literature, that it preferably produces ellagic acid with various reagents containing active oxygen.47 The bromo-derivative 2c was obtained in a yield of 66%, which has already been used in the synthesis of APIs, but had to be synthesised in multiple steps with a low yield.48 Furthermore, pyrogallol (1d) could be converted to the monosubstituted pyrone 2d in a yield of 54%.
Additionally, tannic acid, the mother compound, from which gallic acid is isolated, was used under the optimized conditions, but pyrone 2 was only received in a yield of 11%. During the dropwise addition of tannic acid to the perborate acetic acid mixture, a solid formed immediately after the drop reached the reaction mixture, which also did not disappear during the reaction and was not susceptible to analysis and likely stems from intramolecular reactions. Thus, a prior hydrolysis to gallic acid (1) would provide 2 in higher yields (Scheme 2).
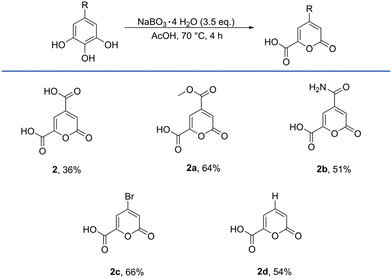 |
| Scheme 2 Application of the optimized reaction conditions to gallic acid (1) and readily available derivatives. | |
Conclusions
By this work a direct and simple access to trans-aconitic acid (3) and 2-pyrone-4,6-dicarboxylic acid (2) was established, which is to date only produced through laborious fermentation processes and not available by chemical means. As a starting material, renewable and inexpensive gallic acid (1), which can be isolated from bark of trees, was used. This underutilized feedstock was oxidized with a mixture of acetic acid and sodium perborate. With this new access to pyrone 2, further transformations of this compound to chemicals or polymers from renewable resources are made possible. Furthermore, readily available derivatives of gallic acid (1) were also successfully converted to the corresponding pyrones in satisfying yields.
Author contributions
F.M. designed and optimized the reaction, and analysed the data. S.R.W. supervised this work. S.R.W. and F.M. wrote and revised the manuscript. All authors agreed to this version of the manuscript.
Data availability
All additional data can be found in the ESI.†
Conflicts of interest
There are no conflicts to declare.
References
- I. T. Horvath and P. T. Anastas, Chem. Rev., 2007, 107, 2169–2173 CrossRef CAS PubMed.
- J. Zakzeski, P. C. Bruijnincx, A. L. Jongerius and B. M. Weckhuysen, Chem. Rev., 2010, 110, 3552–3599 CrossRef CAS.
- O. Y. Abdelaziz, I. Clemmensen, S. Meier, C. A. E. Costa, A. E. Rodrigues, C. P. Hulteberg and A. Riisager, ChemSusChem, 2022, 15, e202201232 CrossRef CAS PubMed.
- D. Bourbiaux, J. Pu, F. Rataboul, L. Djakovitch, C. Geantet and D. Laurenti, Catal. Today, 2021, 373, 24–37 CrossRef CAS.
- C. Amen-Chen, H. Pakdel and C. Roy, Bioresour. Technol., 2001, 79, 277–299 CrossRef CAS PubMed.
- R. Behling, S. Valange and G. Chatel, Green Chem., 2016, 18, 1839–1854 RSC.
- M. Breiner, M. Zirbes and S. R. Waldvogel, Green Chem., 2021, 23, 6449–6455 RSC.
- J. Klein and S. R. Waldvogel, ChemSusChem, 2023, 16, e202202300 CrossRef CAS PubMed.
- M. Zirbes, T. Grassl, R. Neuber and S. R. Waldvogel, Angew. Chem., Int. Ed., 2023, 62, e202219217 CrossRef CAS.
- M. Zirbes, L. L. Quadri, M. Breiner, A. Stenglein, A. Bomm, W. Schade and S. R. Waldvogel, ACS Sustainable Chem. Eng., 2020, 8, 7300–7307 CrossRef CAS.
- M. Zirbes, D. Schmitt, N. Beiser, D. Pitton, T. Hoffmann and S. R. Waldvogel, ChemElectroChem, 2018, 6, 155–161 CrossRef.
- L. M. Lindenbeck, V. C. Barra, S. Dahlhaus, S. Brand, L. M. Wende, B. B. Beele, N. H. Schebb, B. V. M. Rodrigues and A. Slabon, ChemSusChem, 2024, 17, e202301617 CrossRef CAS.
- R. Rinaldi, R. Jastrzebski, M. T. Clough, J. Ralph, M. Kennema, P. C. Bruijnincx and B. M. Weckhuysen, Angew. Chem., Int. Ed., 2016, 55, 8164–8215 CrossRef CAS PubMed.
- M. Zirbes and S. R. Waldvogel, Curr. Opin. Green Sustainable Chem., 2018, 14, 19–25 CrossRef.
- K. Maruyama, J. Biochem., 1979, 86, 1671–1677 CrossRef CAS PubMed.
- F. Moeller, J. Klein and S. R. Waldvogel, ChemSusChem, 2024, e202400759 CrossRef CAS PubMed.
- Y. Otsuka, M. Nakamura, K. Shigehara, K. Sugimura, E. Masai, S. Ohara and Y. Katayama, Appl. Microbiol. Biotechnol., 2006, 71, 608–614 CrossRef CAS PubMed.
- Z. W. Luo, W. J. Kim and S. Y. Lee, ACS Synth. Biol., 2018, 7, 2296–2307 CrossRef CAS PubMed.
- D. Zhou, F. Wu, Y. Peng, M. A. Qazi, R. Li, Y. Wang and Q. Wang, Biotechnol. Biofuels Bioprod., 2023, 16, 92 CrossRef CAS.
- D. Dobler, M. Leitner, N. Moor and O. Reiser, Eur. J. Org. Chem., 2021, 6180–6205 CrossRef CAS.
- T. Michinobu, M. Hishida, M. Sato, Y. Katayama, E. Masai, M. Nakamura, Y. Otsuka, S. Ohara and K. Shigehara, Polym. J., 2007, 40, 68–75 CrossRef.
- Y. Cheng, K. Kuboyama, S. Akasaka, T. Araki, E. Masai, M. Nakamura and T. Michinobu, Polym. Chem., 2022, 13, 6589–6598 RSC.
- M. Bito, T. Michinobu, Y. Katayama, Y. Otsuka, M. Nakamura, S. Ohara, E. Masai and K. Shigehara, Trans. Mater. Res. Soc. Jpn., 2008, 33, 1165–1168 CrossRef CAS.
- T. Michinobu, M. Bito, Y. Yamada, M. Tanimura, Y. Katayama, E. Masai, M. Nakamura, Y. Otsuka, S. Ohara and K. Shigehara, Polym. J., 2009, 41, 1111–1116 CrossRef CAS.
- G. O. Bruni and K. T. Klasson, Foods, 2022, 11, 573 CrossRef CAS.
- Q. Li, P. Zhao, H. Yin, Z. Liu, H. Zhao and P. Tian, Microb. Cell Fact., 2020, 19, 174 CrossRef CAS.
- G. De Smet, X. Bai and B. U. W. Maes, Chem. Soc. Rev., 2024, 53, 5489–5551 RSC.
- L. J. Porter, in Natural Products of Woody Plants, ed. J. W. Rowe, Springer, Berlin, Heidelberg, 1989, ch. 18, pp. 651–690 Search PubMed.
- E. Haslam, in Natural Products of Woody Plants, ed. J. W. Rowe, Springer, Berlin, Heidelberg, 1989, ch. 13, pp. 399–438 Search PubMed.
- P. L. de Hoyos-Martínez, J. Merle, J. Labidi and F. Charrier – El Bouhtoury, J. Cleaner Prod., 2019, 206, 1138–1155 CrossRef.
- Y. Shirmohammadli, D. Efhamisisi and A. Pizzi, Ind. Crops Prod., 2018, 126, 316–332 CrossRef CAS.
- A. K. Seitz, P. J. Kohlpaintner, T. van Lingen, M. Dyga, F. Sprang, M. Zirbes, S. R. Waldvogel and L. J. Goossen, Angew. Chem., Int. Ed., 2022, 61, e202117563 CrossRef CAS.
- T. Horsten and S. R. Waldvogel, RSC Sustainability, 2024, 2, 1963–1968 RSC.
- T. Rücker, N. Schupp, F. Sprang, T. Horsten, B. Wittgens and S. R. Waldvogel, Chem. Commun., 2024, 60, 7136–7147 RSC.
- O. Hayaishi, M. Katagiri and S. Rothberg, J. Am. Chem. Soc., 1955, 77, 5450–5451 CrossRef CAS.
- R. R. Grinstead, Biochemistry, 1964, 3, 1308–1314 CrossRef CAS PubMed.
- F. Coupé, L. Petitjean, P. T. Anastas, F. Caijo, V. Escande and C. Darcel, Green Chem., 2020, 22, 6204–6211 RSC.
- M. Tobiszewski, J. Namieśnik and F. Pena-Pereira, Green Chem., 2017, 19, 1034–1042 RSC.
- K. Arndt, Z. Angew. Chem., 1915, 28, W621 Search PubMed.
- O. Liebknecht, US Pat, US1268369A, 1918 Search PubMed.
- A. McKillop and W. R. Sanderson, Tetrahedron, 1995, 51, 6145–6166 CrossRef CAS.
- P. Karrer and L. Schneider, Helv. Chim. Acta, 1947, 30, 859–861 CrossRef CAS.
- J. Böeseken and G. Slooff, Recl. Trav. Chim. Pays-Bas, 1930, 49, 91–94 CrossRef.
- R. Roesler, S. Schelle, M. Gnann, W. Zeiss and P. R. Harrison, German Pat., EP0488090A1, 1992 Search PubMed.
- A. A. Berkessel, M. R. M., H. Schmickler and J. Lex, Angew. Chem., Int. Ed., 2002, 41, 4481–4484 CrossRef CAS.
- T. Michinobu, M. Bito, Y. Yamada, Y. Katayama, K. Noguchi, E. Masai, M. Nakamura, S. Ohara and K. Shigehara, Bull. Chem. Soc. Jpn., 2007, 80, 2436–2442 CrossRef CAS.
- L. Zhijun, F. Bing and Z. Yongmin, CN108395440A, 2018.
- R. Beveridge, J. Burch, L. Fader, M.-O. Boily, M. St-Onge, S. Dorich, F. Chagnon and G. Duret, WO2023081441A1, p. 2023.
|
This journal is © The Royal Society of Chemistry 2025 |
Click here to see how this site uses Cookies. View our privacy policy here.