Adhesive-less bonding of incompatible thermosetting materials†
Received
18th September 2024
, Accepted 3rd December 2024
First published on 11th December 2024
Abstract
We show that dynamic covalent exchange at the interface of two thermosetting polymers results in strong bonding between the materials via creation of a new material at the interface. Thus, polymers of significantly different polarities can be bonded without the use of adhesives. We also show that such dynamic covalent exchange is not only limited to the interface but also penetrates into the bulk material (ca. 20 microns), thereby creating a strong bond. The creation of a new material at the interface was confirmed by Energy Dispersive X-ray (EDX) elemental mapping as well as a new glass transition temperature at the interface. Using this phenomenon, we show that hydrophobic, compliant polymers can also be used as adhesives for polar, stiff materials. We also show that such dynamic exchange also takes place in the presence of fillers like nano-silica. Lastly, using this technique, we demonstrate the adhesive-less fabrication of layered materials where each layer has vastly different polarities and mechanical properties, thereby tuning the failures modes of the resulting composite material.
1. Introduction
Adhesives have enabled complex manufacturing processes via bonding between materials such as composites, polymers, metals etc.1–4 New adhesive technologies have generated huge interest in the field of composite structure bonding, biological tissue bonding, etc.5 Good interfacial compatibility is extremely important to obtain a strong bond.6–9 In this report, we show that dynamic covalent bond exchange can occur between two thermosetting polymers of significantly different polarities as well as mechanical properties (Fig. 1). Bond exchange between such “incompatible” polymeric networks leads to an exchange zone, i.e. a region where bond exchange creates a new material that penetrates into the bulk region of the thermosets. This type of adhesive-less bonding is fundamentally different from other bonding techniques such as melt-bonding of thermoplastic polymers10,11 which melt and create bonds due to van der Waals attractive forces, intercalation of polymer chains at the interface,12 or partially uncured adhesives which cure on heating.13
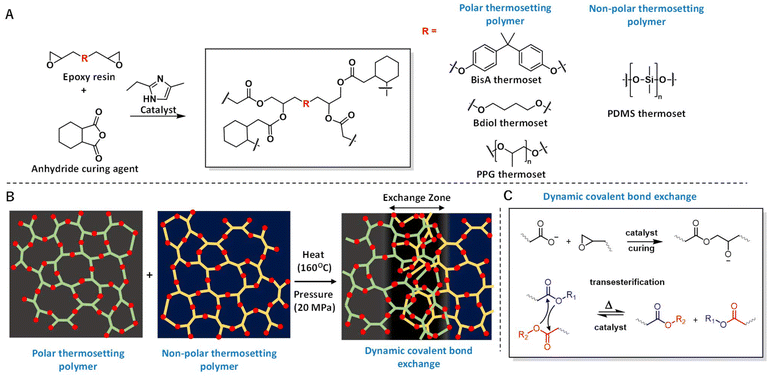 |
| Fig. 1 (A) General scheme for curing of the epoxy resins with an anhydride curing agent, hexahydrophthalic anhydride (HHPA), using 2-ethyl-4-methyl imidazole (EMI) as a catalyst. In this work, three polar thermosetting polymers were fabricated (based on bisphenol A (BisA), butane diol (Bdiol) and polypropylene glycol (PPG)) and their dynamic covalent exchange with a non-polar thermoset of epoxy-terminated polydimethylsiloxane (PDMS) was studied. (B) Schematic representation of dynamic covalent exchange taking place between ester bonds at the interface of materials with drastically different surface energies. (C) Mechanism of dynamic covalent exchange between ester bonds. | |
Bonding of thermosetting polymers of significantly different polarities as well as mechanical properties is challenging and an unsolved problem in the field14 and hence, use of external adhesives is necessary. Surface wetting of the applied adhesive is a key parameter for obtaining a strong bond.15–17 However, when polymeric materials differ drastically in their surface properties (e.g. hydrophobic, low surface energy siloxanes and hydrophilic, high surface energy epoxy thermosets), obtaining adhesion between these dissimilar materials is not straightforward. Moreover, unlike bonding of thermoplastic polymers where heat assisted bonding can be used, thermosetting polymers do not go through a melting phase needed for heat assisted bonding.18
Here, we show strong adhesive-less bonding between two anhydride-cured epoxy thermosetting networks significantly differing in mechanical and chemical properties using dynamic covalent bond exchange. In recent years, epoxy thermosets have become the materials of choice to fabricate composites reinforced with carbon fibres, glass fibres, nanoparticles, etc.19–22
The push towards green energy in automotive and aerospace sectors has led to widespread adoption of fiber reinforced composites which have a favorable strength-to-weight ratio.23 Adhering thermosetting epoxy polymers typically requires adhesives; however, conventional adhesives often fail to establish a strong bond between materials with significantly different polarities and mechanical properties. Recently, there has been a shift towards innovative adhesion technologies, such as induction welding and microwave curing etc.24–27 to replace traditional adhesives.
Leibler et al. introduced the concept of vitrimers, where dynamic covalent bond exchange leads to reprocessable thermosetting polymers.28,29 In subsequent works on vitrimers, research groups applied the concept of dynamic covalent exchange between thermosets to create mechanically strong materials that can be recycled and reprocessed.30 Otsuka et al. recently published a report where they used intercalation of polymer chains to create bonding between thermosets using disulfide bond exchange.12 The mechanism of transesterification in vitrimers has been subject to many studies, and the current assumption is that neighbouring group participation by the –OH group lowers the energy barrier for transesterification.31
Dynamic covalent bonds, essential for enabling reversible bond formation and exchange, play a critical role in self-healing materials by facilitating recovery after damage. These bonds, often utilized in adhesive materials, allow self-healing polymers to autonomously repair or re-bond under specific conditions, such as changes in temperature or pH.32,33 For instance, Wang et al. discuss how imine-based dynamic covalent bonds contribute to self-healing in polymeric hydrogels, highlighting their flexibility and durability in applications that require robust yet adaptable bonding, similar to adhesive systems. The reversible nature of these bonds provides both adhesion and cohesion, allowing materials to regain strength and maintain structural integrity post-damage.34 Similarly, Liu et al. focus on the application of dynamic covalent chemistry in creating materials with both self-healing and recyclable properties, emphasizing how these reversible reactions enable materials to respond dynamically to environmental stressors. Such adaptability underlines the parallels between self-healing and adhesive systems, as both benefit from dynamic covalent mechanisms that manage stress, reduce crack propagation, and allow for material reformation. Together, these studies reinforce the multifunctional potential of dynamic covalent bonds in both adhesion and self-healing, supporting the robustness and reusability of these materials.35
Here, we show that dynamic covalent bond exchange between two thermosetting polymers is possible even in the case of chemically and mechanically dissimilar thermosetting polymeric networks, leading a strong bond between the two thermosetting polymers. An exchange zone of ca. 20 microns is created at the interface of the dissimilar materials, and this zone creates an adhesive bond between these “incompatible” polymers.
Anhydride-cured epoxy materials are well-known for their excellent mechanical properties and UV stability,36 making them widely studied and increasingly popular for consumer-grade applications, such as composite automobile wheels that reduce axle weight and improve fuel efficiency.37–39 In this study, we employ similar anhydride-cured epoxy polymers to highlight their versatility and applicability in both research and commercial contexts. When epoxide resins are crosslinked with anhydride agents (hexahydrophthalic anhydride (HHPA)), they undergo an exothermic ring-opening reaction, forming ester bonds and free hydroxyl groups, which generate a high surface energy in the resulting thermosetting polymer.40 This high surface energy, however, poses a significant challenge when bonding with low surface energy materials, such as silicone polymers.41
2. Materials and instrumentation
Materials
All chemicals were commercially purchased and were used as received without further purification. Bisphenol A diglycidyl ether (DER 332) (epoxide equivalent weight, 172–176), poly(dimethylsiloxane) diglycidyl ether (Mn = 800), 1,4-butanediol diglycidyl ether, poly-(propylene glycol) diglycidyl ether (Mn = 380), hexahydrophthalic anhydride (HHPA), 2-ethyl-4-methylimidazole, 4-(dimethylamino)pyridine (DMAP) and dimethyl aniline were purchased from Sigma-Aldrich. Nano-silica (AEROSIL-RX-200) was purchased from Evonik Opration GmbH.
Instrumentation
Heat press.
AS-ONE heat press machine was used to perform adhesive-less bonding, typically at 160 °C for 4 hours and applied a weight of 200 kg over 100 mm2 overlap area which corresponds to approximately 19.6 MPa pressure on the polymers.
Scanning electron microscopy (SEM) and EDAX analysis.
Low vacuum SEM analysis was conducted using TM 3000 (Hitachi High-Technologies Co., Japan). Carbon and silicon maps were generated using the in-built EDX gun.
Differential scanning calorimetry (DSC).
A SHIMADZU DSC-60 plus instrument was used to monitor the thermal property and glass transition temperatures (Tg) of all polymers under nitrogen atmosphere in a temperature range was of −40 °C to 200 °C with a heating and cooling rate of 10 °C min−1. Aluminium pans were used as sample holders. The Tg values were determined as the midpoint of the slope of phase transition.
Mechanical analysis.
Mechanical analysis of softer samples was performed with a Texture Analyser (Stable Micro Systems) with a load cell of 5 N and that of harder samples was performed with a Shimadzu AG-X plus lap-shear tester with a load cell of 10 kN. Mechanical analysis of samples requiring higher loads was performed with a Shimadzu autograph AG-X plus instrument with a 10 kN load cell. The crosshead speed was 2 mm min−1 for all cases. The reported values are the average of four measurements with standard error for each study. The adhesive strength was determined using following equation:
Adhesive strength (MPa) = Load (N)/Area (mm2). |
Here, area = 10 mm × 10 mm = 100 mm2.
Contact angle.
Water contact angles were measured using a contact angle meter (Kyowa Interface Science, Co Ltd, Japan, Model DMs-401). Distilled water (5 μL) was used as the probe liquid. The images were analyzed for the measurement of the contact angles in Surftens software version 4.5. The measurement of the contact angle was given by measurements of the diameter of the base of the drop and the height of the drop, where each drop was measured five times.
Three point bending tests.
Texture Analyzer (Stable Micro System, TA.XTplusC Texture Analyser) was used with a three-point probe with a 50 N load cell for 3-point bending tests.
3. Experimental procedures
Synthesis of BisA thermosetting polymer (Fig. S1 and S2†)
A 9.0 g of epoxy resin and 7.5 g of hexahydrophthalic anhydride (HHPA) were thoroughly mixed in a Teflon beaker with addition of 0.450 g of 2-ethyl-4-methylimidazole (5% by weight of epoxy resin) as a catalyst. This mixture was placed in a vacuum desiccator for 10 min to remove air bubbles. The mixture was then poured in a rectangular shaped PTFE mold. The thickness of the parts was kept at 2 mm (similar with industry standards). Curing conditions: 120 °C, 4 h.
Synthesis of Bdiol thermoseting polymer (Fig. S3 and S4†)
A 5.0 g of epoxy resin and 7.5 g of hexahydrophthalic anhydride were thoroughly mixed in a Teflon beaker with addition of 0.250 g of 2-ethyl-4-methylimidazole (5% by weight of epoxy resin) as a catalyst. This mixture was placed in a vacuum desiccator for 10 min to remove air bubbles. The mixture was then poured in a rectangular shaped PTFE mold. The thickness of the parts was kept at 2 mm (similar with industry standards). Curing conditions: 120 °C, 4 h.
Synthesis of PPG thermosetting polymer (Fig. S5 and S6†)
A 3.2 g of epoxy resin and 1.54 g of hexahydrophthalic anhydride were thoroughly mixed in a Teflon beaker with addition of 0.160 g of 2-ethyl-4-methylimidazole (5% by weight of epoxy resin) as a catalyst. This mixture was placed in a vacuum desiccator for 10 min to remove air bubbles. The mixture was then poured in a rectangular shaped PTFE mold. The thickness of the parts was kept at 2 mm (similar with industry standards). Curing conditions: 120 °C, 4 h.
Synthesis of PDMS thermosetting polymer (Fig. S5 and S6†)
8 g of poly(dimethylsiloxane) diglycidyl ether and 3.2 g of hexahydrophthalic anhydride were taken in a Teflon beaker with addition of 0.40 g of 2-ethyl-4-methylimidazole (5% by weight of epoxy resin) as catalyst. This mixture was placed in a vacuum desiccator for 30 min to remove air bubbles. The mixture was then poured in a rectangular shaped PTFE mold. The thickness of the parts was kept at 2 mm. Curing conditions: 140 °C, 4 h.
4. Results and discussion
Acid and anhydride curing agents are extensively used industrially to crosslink epoxy resins.42 These curing agents, when used with a catalyst, lead to a nucleophilic ring opening reaction to generate an ester bond. Transesterification in acid cured crosslinked epoxy networks has been used to demonstrate recyclability of these “vitrimers” – a class of thermosetting polymers that undergo dynamic bond exchange without going through a phase transition.28,29,43
In this report, commercially available epoxy resins were cured with HHPA (hexahydro phthalic anhydride) using EMI (2-ethyl-4-methyl-imidazole) as the catalyst (Fig. 1).30 To demonstrate dynamic covalent exchange in incompatible polymers, we chose a siloxane-based epoxide that, when cured, has a significantly different water contact angle and mechanical properties as compared to the other epoxy resins (Fig. 2, S9–S11 and Table S1†). Siloxanes are widely used in material science, industrial components and in biological devices.44,45 Due to the immiscibility of siloxanes with other common carbon-rich polymers, they are incompatible for processing with other polymers and commonly phase separate from polymeric mixtures.46,47 Bonding such siloxanes to common polymers is very difficult due to the hydrophobic nature of the siloxane groups.48,49 While this property is an advantage for many applications such as soft-lithography,50 it is detrimental in cases where bonding of these siloxane polymers to other substrates is required. Another property of siloxane containing polymers is their mechanically compliant behaviour, which has given rise to rapidly emerging field of soft robotics.51
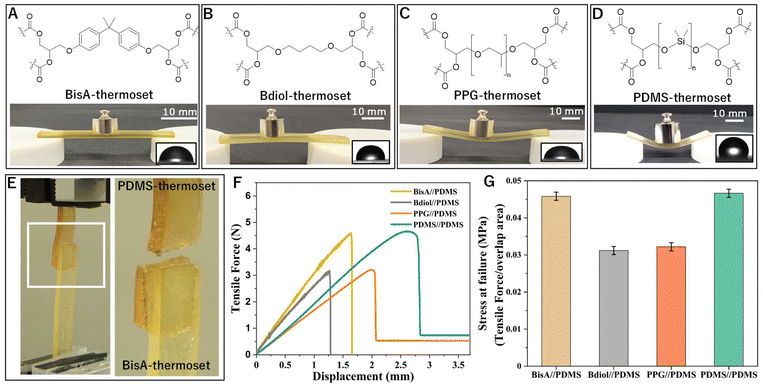 |
| Fig. 2 Chemical structures of the cured epoxy materials with pictures of a rectangular strip (50 mm × 10 mm × 2 mm) of the materials on which a 10 g weight is placed. BisA (A) and Bdiol (B) thermosets are relatively hard and do not display mechanical deformation on placing the weight. PPG (C) and PDMS (D) thermosets are softer thermosets and show mechanical deformation on placement of the weight. Inset pictures show the water contact angles of the polymers. (E) Image of a dynamic covalently bonded composite system of BisA thermoset and PDMS thermoset before (left) and after (right) application of tensile force. The PDMS substrate fails due to stress concentration at the stiffness step before failure of adhesion (F) tensile force vs. displacement graphs of the four different composite systems. (G) The stress at failure values of the four thermoset pairs are similar as, in each case, the substrate fails before failure of adhesion. | |
While the epoxy resins cured with anhydrides incorporate ester groups, an should, in-theory, possess vitrimer-like properties by themselves, the temperatures required for transesterification in these neat polymers is too high and degradation is commonly observed before vitrimeric transitions. In this study, the siloxane-based epoxy polymer provides a low-Tg polymeric network for such vitrimeric exchange and lowers the energy barrier for transesterification, and hence, this low-Tg siloxane polymer was chosen to demonstrate this concept of vitrimeric bonding between incompatible polymers.
The individual epoxy resins were cured separately with the same curing agent HHPA, and the same catalyst, EMI, to generate crosslinked polymeric parts containing ester groups within the thermosets which were confirmed by FTIR (ESI Fig. S35†). When these thermosets were placed in contact with the siloxane-based epoxide polymer at elevated temperature (160 °C for 4 hours) and pressure (200 kgf over 100 mm2 overlap area which corresponds to approximately 19.6 MPa pressure), strong adhesion between these polymers was observed (Fig. 2 and ESI Fig. S23†). Individually, both the adhering parts are crosslinked polymers that contain no reactive groups within their network. However, when heat and pressure is applied to these polymers above their glass transition temperatures (Fig. S11–S18†), ester groups from one network undergo transesterification reactions with the ester groups from the second network, ensuring a strong covalent bond at the interface (Fig. 1C). This dynamic covalent adhesion phenomenon is catalyst-independent (ESI Table S2 and Fig. S24†) and a variety of tertiary amino catalysts can be used (e.g. 1-ethyl 4-methaylimidazoles, N,N-dimethylaminopyridine, N,N-dimethylaniline, etc.).
Strong adhesion is observed without use of any external adhesives which, when measured by tensile elongation, leads to failure of the siloxane substrate without any failure at the interface (Fig. 2F). Bonding with all three carbon-based epoxy resins showed a strong adhesion with similar failure-at-break values. Thus, dynamic covalent bond exchange between dissimilar polymers takes place even when the constituent polymers have vastly different chemical and mechanical properties. Strictly speaking, this failure-at-break value is not the strength of the adhesion because the soft substrate (PDMS) fails before failure of the dynamic covalent adhesion.
As this adhesion based on dynamic covalent exchange is predominantly an interfacial phenomenon, we analyzed the interface of these bonded materials with scanning electron microscopy (SEM) and subsequent elemental mapping using energy dispersive X-ray (EDX) analysis. The elemental composition across the interface of polar epoxy thermosets and non-polar epoxy thermosets was measured by averaging over a line scan of the EDX elemental map across the cross section of the adhesive bond. All the interfaces show a gradient-transition from the siloxane-rich phase to the carbon-rich phase (Fig. 3). Elemental mapping of silicon confirms that there is no bulk-diffusion of silicon from one phase to the other (Fig. 3 and ESI Fig. S25–S27†).
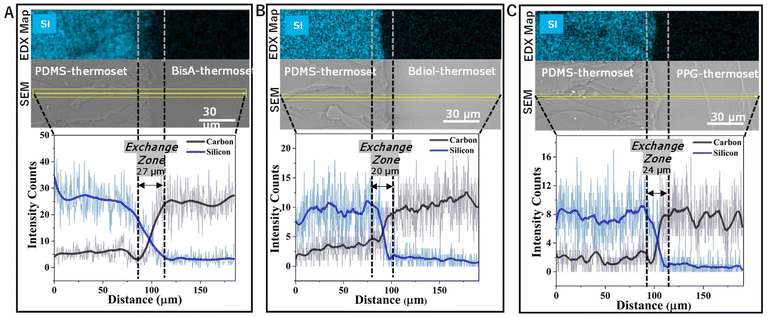 |
| Fig. 3 SEM and superimposed energy dispersive X-ray maps of silicon and carbon of the two thermosetting networks after bonding of BisA thermoset – PDMS thermoset (A), Bdiol thermoset – PDMS thermoset (B) and PPG thermoset – PDMS thermoset (C). Plots at the bottom show the intensity counts of silicon (blue trace) and carbon (black trace) across the cross section at the interface (yellow line). In all the cases, we see an “exchange zone” of ca. 20 microns where there is a gradient-transition from the silicon rich phase to the carbon rich phase. Note that the intensity counts show a qualitative comparison when comparing different elements, as the counts are not normalized. | |
Further evidence of extensive dynamic covalent exchange at the interface was provided by differential scanning calorimetry (DSC). When thin films (50 micrometers) of the two dissimilar polymers were bonded together using the typical adhesive-less bonding procedure, DSC traces (Fig. 4A, B and S20–22†) show not just two glass transition temperatures (of the constituent polymers, i.e. the Tg for BisA thermoset is 115 °C, and that of PDMS thermoset is −25 °C), but also a third glass transition temperature (Tg = 27 °C) occurring between the individual Tgs. Similarly, new glass transition temperatures are observed in the case of Bdiol – PDMS thermoset as well as PPG – PDMS thermoset. Thus, the interfacial dynamic covalent exchange creates an exchange zone which is a new material at the interface with different thermal properties than those of the constituent polymers.
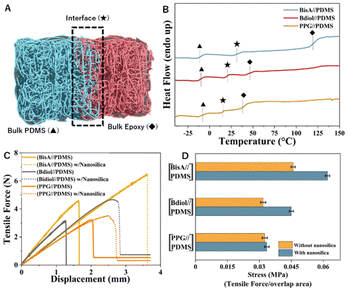 |
| Fig. 4 (A) Schematic representation of an exchange zone created at the interface of the two dissimilar thermosetting polymers. (B) DSC traces of the respective materials show new glass transition temperatures due to creation of dynamic covalent exchange zones. (C) Force – displacement curves of adhered thermosets with and without nano-silica (1% by weight as a filler). Thus, this adhesive-less bonding technique can be applied to reinforced polymeric materials as well. (D) Addition of nano-silica reinforces the polymeric networks, and the bonded materials fail at higher stress as compared to the unreinforced polymeric networks. | |
Commercial thermosetting materials consist not only of the neat polymeric network, but also fillers/plasticizers, etc. Fillers such as nano-silica, titanium dioxide, etc. are extensively used to improve the mechanical properties of the crosslinked networks like impact resistance, improvement in modulus, etc.52,53 To investigate the influence of fillers in dynamic covalent exchange at the interface, we characterized the adhesion between carbon-rich thermosets and siloxane-rich thermosets with nano-silica (1% by weight of the thermoset) (Fig. S28–S30†). As seen in Fig. 4C, D and Table S3† adhesion between these dissimilar thermosets is enhanced on addition of the reinforcements. In all cases, we observed cohesive failure, i.e. the bulk-adhesive fails, and no interfacial delamination was observed.
Film adhesives are thin polymeric films that are one of the many types of adhesives used commercially.54–56 The adhesive film can be cut into tapes of the required areas and can then be laid down by hand or by a robotic tape-laying machine to automate adhesion of materials. Till date, such film adhesives are thermoplastic films which melt on application of high temperature or partially cured polymers which, after curing, adhere the materials that are to be bonded.57,58 Using our concept of adhesive-less bonding, we demonstrate a film adhesive that comprises of a completely cured thermosetting polymer (Fig. S31 and S32†).
Thermosetting adhesives bring many advantages in adhesion, particularly solvent resistance, no creep behavior, thermal stability, etc.59,60 Moreover, adhesives require flexibility to be able to dissipate energy throughout the polymeric network without initiating cracks.61,62 We used our siloxane-epoxy polymer system to fabricate a thin (100 micron) siloxane-rich thermosetting polymer film. When this thermosetting polymer film was used to bond two carbon-rich epoxy polymeric parts, strong adhesion (1.1 MPa, Fig. 5B) could be observed for this adhesive. This adhesive strength is comparable to commercially available silicone adhesives.63 Here, dynamic covalent exchange at two interfaces creates a strong adhesive bond. After failure, a cohesive failure mode is observed where the adhering interfaces do not fail, but instead, the siloxane material fails. This type of failure mode supports the fact of excellent interfacial dynamic covalent bond exchange, which is enhanced by application of external pressure on the adhesive.64 In addition, these de-bonded parts can be re-bonded with heat and pressure, again by dynamic covalent exchange (Fig. 5C). After the first failure of these adhesives, the parts were again kept in contact with each other in the original configuration and subjected to the dynamic bond-exchange conditions (160 °C, 4 hours, 20 MPa pressure, Fig. 5C). Due to inefficient material overlap, the adhesion strength obtained on reuse decreased by 14.11%, 16.85% and 28.68% for BisA-PDMS-BisA, Bdiol-PDMS-Bdiol and PPG-PDMS-PPG respectively, but was still quite strong (Fig. 5C and ESI Fig. S33†).
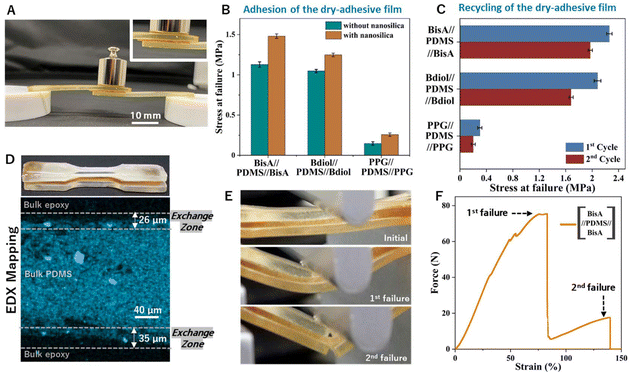 |
| Fig. 5 (A) Image of two BisA thermosets bonded together with a PDMS thermosetting film. The hydrophobic film is dry to touch but can successfully bond two hydrophilic thermosetting polymers. (B) Characterization of the adhesion strength of the PDMS dry adhesive film. (C) The dry adhesive film can be recycled, and the parts can be re-bonded with good retention of the bonding strength. (D) A sandwich structure synthesized using the adhesive-less bonding technique. The soft PDMS thermoset is flanked by two hard BisA thermosets. The bottom image shows the SEM-EDX map of silicon. (E) The dog-bone shaped BisA-PDMS-BisA sandwich structure was subjected to a 3-point bending test to show the unique behavior of such structures on failure. (F) Force vs. strain graph for the 3-point bending test of the sandwich structure shows unique failure modes of the composite structure. | |
This dynamic covalent exchange of incompatible materials can also be used to create novel anisotropic materials, i.e. sandwich structured thermosets wherein mutually incompatible polymers can be stacked on top of one another. We synthesized BisA-PDMS-BisA thermosets as well PDMS-BisA-PDMS thermosets to fabricate sandwich structures from incompatible polymers (Fig. 5D and ESI Fig. S34, S35†). To confirm good interfacial adhesion, we subjected these sandwich structures to 3-point-bending tests until failure, and no interfacial delamination is observed (see video in ESI† and Fig. 5E, F, ESI Fig. S36, S37†). Thus, such novel thermosetting materials are accessible via this adhesive-less bonding approach, wherein, failure modes of these composite structures can be tuned on selection of appropriate materials.
5. Conclusion
In conclusion, we show that dynamic covalent bond exchange can be used to create a strong adhesive bond between polymeric networks of vastly different polarities as well as different mechanical properties, without use of adhesives. The adhesion is a result of an exchange zone created across the interface of both the polymeric networks, where formation of a new polymeric network distinct from the constituent networks is observed. SEM-EDX mapping as well as DSC traces indicate that the new material in the exchange zone has different thermal and chemical properties as compared to the bulk thermosetting materials.
We also show that this strategy of bonding between chemically incompatible thermosetting polymeric networks is compatible with reinforcements such as fillers, which are commonly used in polymer composites. Addition of nano-silica to the individual polymeric networks led not only to an increase in mechanical strength of the individual polymeric networks but also to an increase in the adhesion strength on dynamic covalent exchange.
In addition, we show that non-polar thermosetting polymers can be used for adhesion of two polar thermosetting polymers. This is surprising and challenges the conventional knowledge in adhesives. Due to resistance to crack initiation and propagation,65 flexible thermosetting adhesives may be very well-suited as adhesives for high tensile strength polymeric composites. Moreover, we also show that such a “polymeric adhesive film” can be reused after adhesive failure for re-bonding of the thermosetting polymers.
Such an adhesive-less bonding strategy could simplify complex manufacturing chains and impart new avenues of research in adhesion in a variety of industrial applications, such as aerospace composites, automotive composites, composites for renewable energy, adhesion to electronic coatings, etc.
Author contributions
M. N. and A. N. designed the conceived the project and designed the experiments. All experiments were performed by S. R. K., A. V. P. and S. V. P. Polymer mechanical properties as well as adhesives data was analyzed by S. R. K, A. V. P., and S. V. P. All authors helped in the interpretation of the data and contributed to writing the manuscript.
Data availability
Authors confirmed that the data supporting the findings of this study are available within the article and its ESI.†
Conflicts of interest
The authors certify that there is no conflict of interest for our work.
Acknowledgements
S. R. K. acknowledges funding from National Institute for Materials Science (NIMS), Japan for post-doctoral funding. This work was partially supported by the Core Research for Evolutional Science and Technology (CREST) program “Revolutional material development by fusion of strong experiments with theory/data science” of the Japan Science and Technology Agency (JST), Japan, under Grant JPMJCR19J3.
A. V. P. acknowledges Composites Group, Mechanical Systems Engineering-304, Swiss Federal Laboratories for Materials Science and Technology-Empa, 8600 Dübendorf, Switzerland.
References
- C. Heinzmann, C. Weder and L. M. de Espinosa, Supramolecular polymer adhesives: advanced materials inspired by nature, Chem. Soc. Rev., 2016, 45, 342–358 RSC.
- F. Awajaa, M. Gilbert, G. Kelly, B. Fox and P. J. Pigram, Adhesion of polymers, Prog. Polym. Sci., 2009, 34, 948–968 CrossRef.
- L. Xiang, J. Zhang, J. Chen and H. Zeng, Fundamentals and Advances in the Adhesion of Polymer Surfaces and Thin Films, Langmuir, 2019, 35(48), 15914–15936 CrossRef.
- P. Chakma and D. Konkolewicz, Dynamic Covalent Bonds in Polymeric Materials, Angew. Chem., Int. Ed., 2019, 58, 9682–9695 CrossRef CAS PubMed.
- G. Jeevi, S. K. Nayak and M. A. Kader, Review on adhesive joints and their application in hybrid composite structures, J. Adhes. Sci. Technol., 2019, 33(14), 1497–1520, DOI:10.1080/01694243.2018.1543528.
- Z. Ahmadi, Nanostructured epoxy adhesives: A review, Prog. Org. Coat., 2019, 135, 449–453, DOI:10.1016/j.porgcoat.2019.06.028.
- M. D. Bane, L. F. M. da Silva and R. J. C. Carbas, Debonding on command of adhesive joints for the automotive industry, Int. J. Adhes. Adhes., 2015, 59, 14–20, DOI:10.1016/j.ijadhadh.2015.01.014.
- S. Budhe, M. D. Banea, S. de Barros and L. F. M. da Silva, An updated review of adhesively bonded joints in composite materials, Int. J. Adhes. Adhes., 2017, 72, 30–34 CrossRef CAS.
- M. Liu, Y. Zheng, J. Zhai and L. Jiang, Bioinspired Super-antiwetting Interfaces with Special Liquid - Solid Adhesion, Acc. Chem. Res., 2010, 43(3), 368–377, DOI:10.1021/ar900205g.
- N. Banik, A review on the use of thermoplastic composites and their effects in induction welding method, Mater. Today: Proc., 2018, 5(9), 20239–20249, DOI:10.1016/j.matpr.2018.06.395.
- G. de Avila Bockorny, M. M. C. Forte and S. Stamboroski, Modifying a thermoplastic polyurethane for improving the bonding performance in an adhesive technical process, Appl. Adhes. Sci., 2016, 4, 4, DOI:10.1186/s40563-016-0060-x.
- A. Tsuruoka, A. Takahashi, D. Aoki and H. Otsuka, Fusion of Different Crosslinked Polymers Based on Dynamic Disulfide Exchange, Angew. Chem., Int. Ed., 2019, 59(11), 4294–4298, DOI:10.1002/anie.201913430.
- K. C. Shin, J. J. Lee and D. G. Lee, A study on the lap shear strength of a co-cured single lap joint, J. Adhes. Sci. Technol., 2000, 14(1), 123–139, DOI:10.1163/156856100742140.
- T. Liu, C. Hao, S. Zhang, X. Yang, L. Wang, J. Han, Y. Li, J. Xin and J. Zhang, A Self-Healable High Glass Transition Temperature Bioepoxy Material Based on Vitrimer Chemistry, Macromolecules, 2018, 51(15), 5577–5585, DOI:10.1021/acs.macromol.8b01010.
- L. S. Penn and E. R. Bowler, A new approach to surface energy characterization for adhesive performance prediction, Surf. Interface Anal., 1981, 3(4), 161–164, DOI:10.1002/sia.740030405.
- E. Asmussen and A. Peutzfeldt, Surface energy characteristics of adhesive monomers, Dent. Mater., 1998, 14(1), 21–28, DOI:10.1016/S0109-5641(98)00005-0.
- R. G. Dillingham and B. R. Oakley, Surface Energy and Adhesion in Composite-Composite Adhesive Bonds, J. Adhes., 2006, 82, 407–426, DOI:10.1080/00218460600683944.
- H.-Y. Tsai, Y. Nakamura, T. Fujita and M. Naito, Strengthening epoxy adhesives at elevated temperatures based on dynamic disulfide bonds, Mater. Adv., 2020, 1, 3182, 10.1039/d0ma00714e.
- C. O. Mgbemena, D. Li, M.-F. Lin, P. D. Liddel, K. B. Katnam, V. K. Thakur and H. Y. Nezhad, Accelerated microwave curing of fibre-reinforced thermoset polymer composites for structural applications: A review of scientific challenges, Composites, Part A, 2018, 115, 88–10389, DOI:10.1016/j.compositesa.2018.09.012.
- A. V. Pansare, S. R. Khairkar, A. A. Shedge, S. Y. Chhatre, V. R. Patil and A. A. Nagarkar, In Situ Nanoparticle Embedding for Authentication of Epoxy Composites, Adv. Mater, 2018, 30, 1801523, DOI:10.1002/adma.201801523.
- E. K. W. Tan, P. K. Shrestha, A. V. Pansare, S. Chakrabarti, S. Li, D. Chu, C. R. Lowe and A. A. Nagarkar, Density Modulation of Embedded Nanoparticles via Spatial, Temporal, and Chemical Control Elements, Adv. Mater, 2019, 31, 1901802, DOI:10.1002/adma.201901802.
- A. V. Pansare, S. Y. Chhatre, S. R. Khairkar, J. G. Bell, M. Barbezat, S. Chakrabarti and A. A. Nagarkar, “Shape-Coding”: Morphology-Based Information System for Polymers and Composites, ACS Appl. Mater. Interfaces, 2020, 12(24), 27555–27561, DOI:10.1021/acsami.0c05314.
- S. Hegde, B. S. Shenoy and K. N. Chethan, Review on carbon fiber reinforced polymer (CFRP) and their mechanical performance, Mater. Today: Proc., 2019, 19(2), 658–662, DOI:10.1016/j.matpr.2019.07.749.
- A. C. Marques, A. Mocanu, N. Z. Tomíc, S. Balos, E. Stammen, A. Lundevall, S. T. Abrahami, R. Günther, J. M. M. de Kok and S. T. de Freitas, Review on Adhesives and Surface Treatments for Structural Applications: Recent Developments on Sustainability and Implementation for Metal and Composite Substrates, Materials, 2020, 13, 5590, DOI:10.3390/ma13245590.
- R. Bogue, Recent developments in adhesive technology: a review, Assembly Autom., 2011, 31(3), 207–211, DOI:10.1108/01445151111150532.
- C. O. Mgbemena, D. Li, M.-F. Lin, P. D. Liddel, K. B. Katnam, V. K. Thakur and H. Y. Nezhad, Accelerated microwave curing of fibre-reinforced thermoset polymer composites for structural applications: A review of scientific challenges, Composites, Part A, 2018,(115), 88–103 CrossRef CAS.
- A. Pizzi, Recent developments in eco-efficient bio-based adhesives for wood bonding: opportunities and issues, J. Adhes. Sci. Technol., 2006, 20(8), 829–846, DOI:10.1163/156856106777638635.
- D. Montarnal, M. Capelot, F. Tournilhac and L. Leibler, Silica-Like Malleable Materials from Permanent Organic Networks, Science, 2011, 334(6058), 965–968 CrossRef CAS.
- J. M. Winne, L. Leibler and F. E. D. Prez, Dynamic covalent chemistry in polymer networks: a mechanistic perspective, Polym. Chem., 2019, 10, 6091 RSC.
- M. Röttger, T. Domenech, T. R. van der Weegen, A. Breuillac, R. Nicolaÿ and L. Leibler, High-performance vitrimers from commodity thermoplastics through dioxaborolane metathesis, Science, 2017, 356, 62–65, DOI:10.1126/science.aah5281.
- M. Delahaye, J. M. Winne and F. E. Du Prez, Internal Catalysis in Covalent Adaptable Networks: Phthalate Monoester Transesterification As a Versatile Dynamic Cross-Linking Chemistry, J. Am. Chem. Soc., 2019, 141(38), 15277–15287, DOI:10.1021/jacs.9b07269.
- Y. Chen, Q. Guan, C. Chen, Y. Zhang and W. Zhang, Self-healing polymeric materials: Principles and applications, Chem. Soc. Rev., 2021, 50, 3824–3841, 10.1039/D0CS00345C.
- Z. Li, R. Yu and B. Guo, Shape-Memory and Self-Healing Polymers Based on Dynamic Covalent Bonds and Dynamic Noncovalent Interactions: Synthesis, Mechanism, and Application, ACS Appl. Bio Mater., 2021, 4(8), 5926–5943, DOI:10.1021/acsabm.1c00606.
- W. Wang, J. Zhang and Z. Zhao, Imine-based dynamic covalent hydrogels with rapid self-healing and adaptive properties for biomedical applications, React. Funct. Polym., 2022, 175, 105184, DOI:10.1016/j.reactfunctpolym.2022.105184.
- H. Liu, X. Zhou, S. Yang and W. Huang, Recyclable and self-healing dynamic covalent polymer networks
enabled by exchangeable boronic ester bonds, Chem. Eng. J., 2022, 437, 139992, DOI:10.1016/j.cej.2022.139992.
- M. Ivankovic, L. Incarnato, J. M. Kenny and L. Nicolais, Curing kinetics and chemorheology of epoxy/anhydride system, J. Appl. Polym. Sci., 2003, 90, 3012–3019, DOI:10.1002/app.12976.
- F. Rondina, S. Taddia, L. Mazzocchetti, L. Donati, G. Minak, P. Rosenberg, A. Bedeschi and E. Dolcini, Development of full carbon wheels for sport cars with high - volumetechnology, Compos. Struct., 2018, 192, 368–378369, DOI:10.1016/j.compstruct.2018.02.083.
- F. Long, J. X. Li and S.-J. Park, Synthesis and application of epoxy resins: A review, J. Ind. Eng. Chem., 2015, 29, 1–11, DOI:10.1016/j.jiec.2015.03.026.
- F. Rondin, S. Taddi, L. Mazzocchetti, L. Donati, G. Minak, P. Rosenberg, A. Bedeschi and E. Dolcini, Development of full carbon wheels for sport cars with high-volumetechnology, Compos. Struct., 2018, 192, 368–378369 CrossRef.
- S. K. Rath, J. G. Chavan, S. Sasane, J. M. Patri, A. B. Samui and B. C. Chakraborty, Two component silicone modified epoxy foul release coatings: Effect of modulus, surface energy and surface restructuring on pseudobarnacle and macrofouling behaviour, Appl. Surf. Sci., 2010, 256, 2440–2446, DOI:10.1016/j.apsusc.2009.10.084.
- I. Karapanagiotis, P. N. Manoudis, A. Zurba and D. Lampakis, From Hydrophobic to Superhydrophobic and Superhydrophilic Siloxanes by Thermal Treatment, Langmuir, 2014, 30(44), 13235–13243, DOI:10.1021/la503583c.
- S. Vyazovkin and N. Sbirrazzuoli, Kinetic methods to study isothermal and nonisothermal epoxy–anhydride cure, Macromol. Chem. Phys., 1999, 200, 2294–2303 CrossRef CAS.
- W. Denissen, J. M. Winne and F. E. D. Prez, Vitrimers: permanent organic networks with glass-like fluidity, Chem. Sci., 2016, 7, 30–38, 10.1039/C5SC02223A.
-
Z. Han, A. Fina and G. Camino, Chapter 12 - Organosilicon Compounds as Polymer Fire Retardants, Polymer Green Flame Retardants, 2014, pp. 389–418. DOI:10.1016/B978-0-444-53808-6.00012-3.
-
(a) M. P. Wolf, G. B. S. Beugelaar and P. Hunziker, PDMS with designer functionalities—Properties, modificationsstrategies, and applications, Prog. Polym. Sci., 2018, 83, 97–134, DOI:10.1016/j.progpolymsci.2018.06.001;
(b) M. A. Meyers, P.-Y. Chen, M. I. Lopez, Y. Seki and A. Y. M. Lin, Biological materials: A materials science approach, J. Mech. Behav. Biomed. Mater., 2010, 4(5), 1–32, DOI:10.1016/j.jmbbm.2010.08.005;
(c) K. R. M. S. Chakraborty, PDMS microfluidics: A mini review, J. Appl. Polym. Sci., 2020, 48958, DOI:10.1002/app.48958.
- K. Nakanishi, T. Amatani, S. Yano and T. Kodaira, Multiscale Templating of Siloxane Gels via Polymerization-Induced Phase Separation, Chem. Mater, 2008, 20(3), 1108–1115 CrossRef CAS.
- P. Pandey, R. S. Chauhan, R. P. Semwal, S. Banerjee and R. Jain, Density–based phase–separation asymmetric polyethylene–poly(dimethyl siloxane) blend membranes: Preparation and properties, J. Appl. Polym. Sci., 2004, 91(4), 2278–2287, DOI:10.1002/app.13359.
- I. Karapanagiotis, P. N. Manoudis, A. Zurba and D. Lampakis, From Hydrophobic to Superhydrophobic and Superhydrophilic Siloxanes by Thermal Treatment, Langmuir, 2014, 30(44), 13235–13243, DOI:10.1021/la503583c.
- H. N. Sharma, J. M. Lenhardt, A. Loui, P. G. Allen, W. McLean II, R. S. Maxwell and L. N. Dinh, Moisture outgassing from siloxane elastomers containing surface-treated-silica fillers, npj Mater. Degrad., 2019, 3, 21, DOI:10.1038/s41529-019-0083-4.
- D. Qin, Y. Xia and G. M. Whitesides, Soft lithography for micro- and nanoscale patterning, Nat. Protoc., 2010, 5, 491–502, DOI:10.1038/nprot.2009.234.
- G. M. Whitesides, Soft Robotics, Angew. Chem., Int. Ed., 2018, 57, 4258–4273, DOI:10.1002/anie.201800907.
- L. Chen, S. Chai, K. Liu, N. Ning, J. Gao, Q. Liu, F. Chen and Q. Fu, Enhanced Epoxy/Silica Composites Mechanical Properties by Introducing Graphene Oxide to the Interface, ACS Appl. Mater. Interfaces, 2012, 4(8), 4398–4404, DOI:10.1021/am3010576.
- H. Wang, Y. Bai, S. Liu, J. Wu and C. P. Wong, Combined effects of silica filler and its interface in epoxy resin, Acta Mater., 2002, 50, 4369–4377, DOI:10.1016/S1359-6454(02)00275-6.
- H. Yuk, C. E. Varela, C. S. Nabzdyk, X. Mao, R. F. Padera, E. T. Roche and X. Zhao, Dry double-sided tape for adhesion of wet tissues and devices, Nature, 2019, 575, 169–174, DOI:10.1038/s41586-019-1710-5.
-
J. Bishopp, Adhesives for Aerospace Structures, Handbook of Adhesives and Surface Preparation, Technology, Applications and Manufacturing Plastics Design Library 2011, pp. 301–344. DOI:10.1016/B978-1-4377-4461-3.10013-6.
- S. Sun, M. Li and A. Liu, A review on mechanical properties of pressure sensitive adhesives, Int. J. Adhes. Adhes., 2013, 41, 98–106, DOI:10.1016/j.ijadhadh.2012.10.011.
- J. Eisenhaure and S. Kim, A Review of the State of Dry Adhesives: Biomimetic Structures and the Alternative Designs They Inspire, Micromachines, 2017, 8(4), 125, DOI:10.3390/mi8040125.
- M. Schulz and J. L. Keddie, A critical and quantitative review of the stratification of particles during the drying of colloidal films, Soft Matter, 2018, 14, 6181–6197, 10.1039/C8SM01025K.
- Z. Ahmadi, Nanostructured epoxy adhesives: A review, Prog. Org. Coat., 2019, 135, 449–453, DOI:10.1016/j.porgcoat.2019.06.028.
-
M. A. Clayton, Epoxy Resins: Chemistry and Technology, Marcel Dekker Inc, New York, 7nd edn, 1987, pp. 794.ISBN: 0-8247-7690-9 DOI:10.1002/pol.1988.140261212.
- M. G. Mazzotta, A. A. Putnam, M. A. North and J. J. Wilker, Weak Bonds in a Biomimetic Adhesive Enhance Toughness and Performance, J. Am. Chem. Soc., 2020, 142(10), 4762–4768, DOI:10.1021/jacs.9b13356.
- B. L. Smith, T. E. Schäffer, M. Viani, J. B. Thompson, N. A. Frederick, J. Kindt, A. Belcher, G. D. Stucky, D. E. Morse and P. K. Hansma, Molecular mechanistic origin of the toughness of natural adhesives, fibres and composites, Nature, 1999, 399, 761–763, DOI:10.1038/21607.
- F. Buyl, Silicone sealants and structural adhesives, Int. J. Adhes. Adhes., 2001, 21(5), 411–422, DOI:10.1016/S0143-7496(01)00018-5.
- N. D. A. Watuthanthrige, B. Ahammed, M. T. Dolan, Q. Fang, J. Wu, J. L. Sparks, M. B. Zanjani, D. Konkolewicz and Z. Ye, Accelerating dynamic exchange and self-healing using mechanical forces in crosslinked polymers, Mater. Horiz., 2020, 7, 1581–1587, 10.1039/C9MH01938C.
- Z. Suo and J. W. Hutchinson, Sandwich test specimens for measuring interface crack toughness, Mater. Sci. Eng., A, 1989, 107, 135–143, DOI:10.1016/0921-5093(89)90382-1.
Footnotes |
† Electronic supplementary information (ESI) available: Experimental methods, figures, tables and videos. See DOI: https://doi.org/10.1039/d4lp00288a |
‡ These authors contributed equally. |
|
This journal is © The Royal Society of Chemistry 2025 |
Click here to see how this site uses Cookies. View our privacy policy here.