DOI:
10.1039/D4RA07970A
(Review Article)
RSC Adv., 2025,
15, 406-419
3D-printed silicon nitride ceramic implants for clinical applications: the state of the art and prospects
Received
9th November 2024
, Accepted 18th December 2024
First published on 3rd January 2025
Abstract
Si3N4 ceramic has received great attention because of its sound biological performances, which make it an attractive ceramic implant material in healthcare, particularly in orthopedic surgery. With the advancement of 3D printing technology, Si3N4 ceramics can now be fabricated into customized implants with precise anatomical shapes, sizes, and microstructures, catering to the individual needs of patients. We, therefore, conducted a comprehensive review of how 3D printing enables complex-shaped Si3N4 ceramic implants for clinical applications. Firstly, commonly used 3D printing technologies are introduced. Then, the state of the art of the 3D-printed Si3N4 ceramic implants are summarized. Finally, we forward the prospects towards the 3D printing of Si3N4 ceramic implants, including high mechanical properties, composites, drug loading, and economics and low cost. We hope that this review will provide a thorough examination and helpful guidance to related scientists, clinicians, and dentists in this field.
1. Introduction
Silicon nitride (Si3N4) is a non-oxide ceramic extensively used in system parts subjected to high stress and/or high temperatures, owing to its outstanding properties such as low density, high strength, high fracture toughness, high hardness, excellent wear resistance and creep behavior, and excellent resistance at elevated temperatures.1–3 Recently, in addition to its excellent physicochemical and mechanical properties, Si3N4 ceramic has received great attention because of its sound biological performances, which make it an attractive implant material in healthcare, particularly in orthopedic surgery.4–6 Si3N4 ceramic is used clinically in developing bearings in total hip and knee joint replacement, spinal space fusion devices, and so on (as shown in Fig. 1).7 Some transnational corporations, such as CeramTec Industrial, SINTX Technologies, and so on, have achieved great success in the field of Si3N4 ceramic hip and knee joint replacement. In addition, Si3N4 ceramic implants have also been reported to be used in dental clinics. According to some market reports, Si3N4 ceramic implants will increase at a compound annual growth rate of over 17.5% from 2024 to 2031, perhaps reaching over USD 10 billion. Table 1 lists the possible clinical applications of 3D-printed Si3N4 ceramic implants, including these dental implants, orthopedic implants, and other customized implants, which show great potential and value.
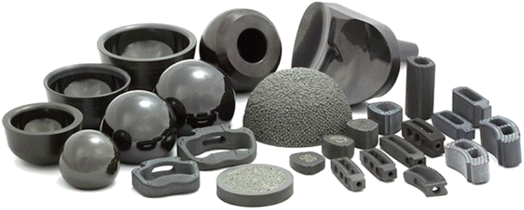 |
| Fig. 1 Clinical applications of Si3N4 ceramic components (SINTX Technologies).7 | |
Table 1 Possible clinical applications of 3D-printed Si3N4 ceramic implants
Implants |
Description |
Dental application |
Post-core crown |
3D-printed Si3N4 ceramic implants are promising new implants for restoring large-area dental defects, which can serve as the post portion of a post-and-core crown, providing stable retention force |
Bone screws, surgical plates, screw shafts, and other devices |
3D-printed Si3N4 ceramic implants can be used as bone screws, surgical plates, screw shafts, and other devices. Si3N4 ceramic can effectively integrate with surrounding tissues and promote new bone formation |
Orthopedic application |
Hip and knee replacements |
3D-printed Si3N4 ceramic implants can be used as components for hip and knee replacements. Si3N4 ceramic is an ideal choice for replacing traditional Al2O3 ceramics |
Cervical spacers and spinal fusion cages |
3D-printed Si3N4 ceramic implants can be used as cervical spacers and spinal fusion cages. Especially in spinal surgery, porous Si3N4 ceramic scaffolds for intervertebral body fusion have achieved remarkable clinical effects |
Other clinical applications |
3D-printed Si3N4 ceramic implants with precise anatomical shapes, sizes, and microstructures can be applied for other clinical applications |
As is known, ceramic implants are always complex in geometry, sometimes even with porous, gradient, and other shape features. It is a difficult task to manufacture complex-shaped Si3N4 ceramic components. At present, 3D complex-shaped Si3N4 ceramic components are commonly produced through two approaches: sintering and machining,8,9 and near-net forming and sintering.10,11 Fig. 1 clearly shows the traditionally prepared Si3N4 ceramic components for all kinds of possible clinical applications. However, for the sintering and machining approach, bulk Si3N4 ceramic is firstly fabricated by various sintering technologies, such as pressureless sintering, hot pressing, and so on. Complex-shaped Si3N4 components are subsequently obtained through grinding, turning, and other machining methods. Inevitable defects and damages exist owing to the deadly brittleness and hardness of ceramic during machining, which greatly deteriorate its properties and life.12–14 In addition, expensive diamond or superalloy machining tools are needed for machining, which greatly increases the costs.9,12 For the near-net forming and sintering approach, a complex-shaped Si3N4 green body is usually prepared via near-net colloidal processing technologies, such as slip casting, tape casting, injection molding, gel casting, and so on.11,15,16 After that, the Si3N4 component is subsequently obtained by using pressureless sintering. However, molds are usually needed, which increase the production cycles and cost. Moreover, extremely complex-shaped Si3N4 components may contain internal holes or internal surfaces, which are very difficult to achieve. In one word, both these sintering and machining and near-net forming and sintering approaches cannot meet the manufacturing requirement of 3D complex-shaped Si3N4 ceramic components.
Additive manufacturing (AM), also known as 3D printing, is promising for net- and near-net shaping of Si3N4 ceramic components.17,18 Recently, many studies have shown that geometrically complex SiOC,19 oxide,20 hydroxyapatite,21 SiC,22 and ceramic composite23 components are readily fabricated by 3D printing. Fig. 2 shows published paper numbers with the topics “3D printing” and “Si3N4” to papers with the topic “Si3N4” (Web of Science database from 2014.01 to 2024.11). It is found that, in the past 10 years, the 3D printing of Si3N4 ceramic has drawn increasing attention and has been subjected to intensive research. Among these studies, an increasing number of novel 3D-printed Si3N4 ceramic implants have been investigated and used in the biomedical field. However, on the one hand, the state of the art of the 3D printing of Si3N4 ceramic lacks a comprehensive review and summary. On the other hand, there are still many challenges and issues regarding the 3D printing of Si3N4 ceramic implants and their biomedical clinic applications, which need to be systematically discussed.
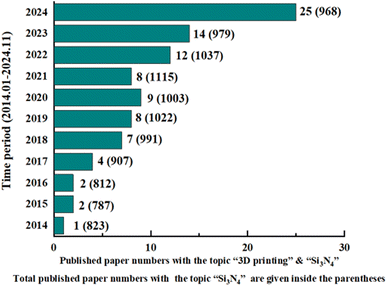 |
| Fig. 2 Published paper numbers with the topics “3D printing” and “Si3N4” to papers with the topic “Si3N4” (Web of Science database from 2014.01 to 2024.11). | |
Therefore, this paper aims to systematically review the recent state of the art to assess the prospects for novel 3D-printed Si3N4 ceramic implants for biomedical applications. The authors hope to provide a deep review and helpful guidance for the related scientists, clinicians, and dentists in this field.
2. 3D-printed Si3N4 ceramics
According to the ISO/ASTM 52900:2015—Additive manufacturing,24 3D printing technologies can be divided into seven categories: vat photopolymerization (VPP), material extrusion (MEX), material jetting (MJ), binder jetting (BJ), powder bed fusion (PBF), direct energy deposition (DED), and sheet lamination (SL). In this paper, commonly used 3D printing technologies for Si3N4 ceramics that were published recently are summarized as follows.
2.1 Vat photopolymerization (VPP) 3D-printed Si3N4 ceramics
Vat photopolymerization (VPP) 3D printing process is a technique in which photosensitive ceramic slurries are exposed to radiation/light in a controlled manner to obtain polymerized material layers, as shown in Fig. 3a. Subsequent layers combine to form a 3D ceramic green object. After that, debinding and sintering are further conducted to obtain the final ceramic parts. Usually, VPP 3D printing processes can further be classified into stereolithography (SLA, as shown in Fig. 3a(i)),25 digital light processing (DLP, as shown in Fig. 3a(ii)),25 two-photon polymerization (2PP, not shown here),31 volumetric 3D printing,32 and so on. Recently, Si3N4 ceramics have been widely reported to be fabricated by VPP 3D printing. Schwarzer-Fischer et al. successfully prepared Si3N4 ceramic and its complex structures, such as discs and triple periodic minimal surfaces (TPMS),33 as shown in Fig. 4a. Zhou et al. also fabricated Si3N4 ceramic by VPP 3D printing. Combined with following air pressure liquid-phase sintering, the as-obtained Si3N4 ceramic had a relatively high strength of 382.67 MPa and a density of 2.95 g cm−3.34 They further investigated the effect of thermosetting resin coating modification on the properties of Si3N4 ceramics, as shown in Fig. 4b.
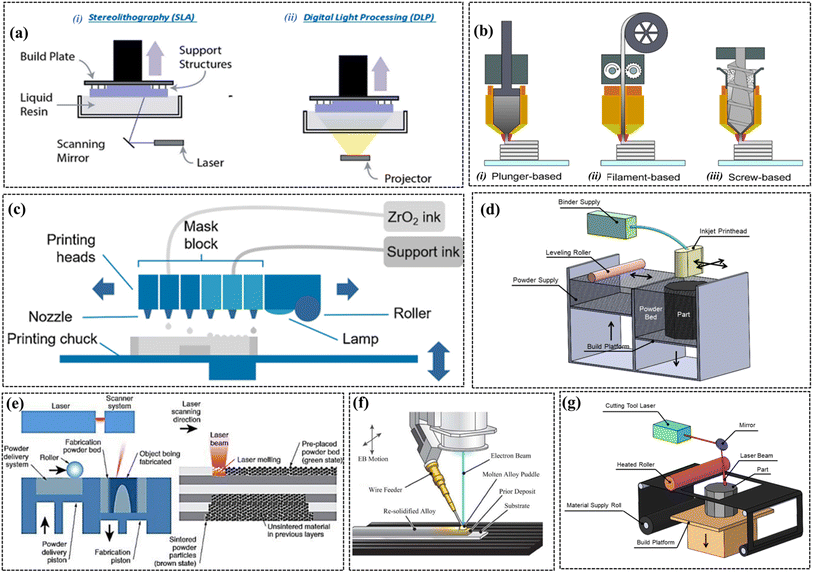 |
| Fig. 3 3D printing technologies: (a) VPP,25 (b) MEX,26 (c) MJ,27 (d) BJ,28 (e) PBF,29 (f) DED,30 and (g) SL.28 | |
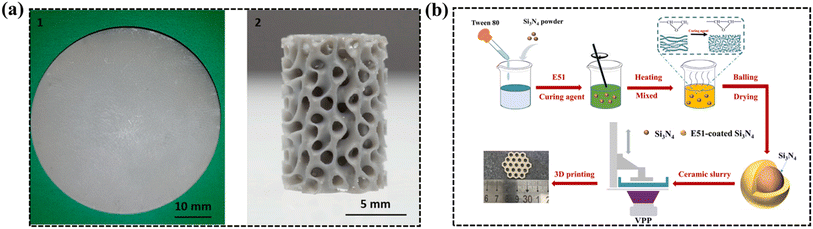 |
| Fig. 4 VPP 3D printing of Si3N4 ceramic: (a) discs and TPMS33 and (b) thermosetting resin coating modification during 3D printing.34 | |
2.2 Materials extrusion (MEX) 3D-printed Si3N4 ceramics
Materials extrusion (MEX) 3D printing of ceramics requires continual feeding of material within a moving nozzle. This process enables simple extrusion via the nozzle, molding layers along a preset path. After finishing a layer, the build platform or the extrusion head moves up or down, allowing for the deposition and adhesion of another material layer to the previous one. After ceramic green parts are obtained, debinding and sintering are subsequently conducted. Usually, MEX 3D printing of ceramics can usually be classified into three types (as shown in Fig. 3b): filament-based, plunger-based, and screw-based.26 Clarkson et al. used a UV-assisted direct ink writing (DIW), which is a type of MEX 3D printing, to prepare Si3N4/SiC from preceramic polymer suspensions.35 After post-pyrolysis, hexagonal arrays, lattice or log pile structures, and twisted vases were obtained (as shown in Fig. 5a). Jiang et al. also prepared Si2N2O–Si3N4 ceramics via DIW and following low-temperature sintering.36 Spina et al. also obtained some Si3N4 ceramic parts, including a rectangular bar, turbine rotor, gear, and swirl fan,26 by MEX 3D printing, as shown in Fig. 5b.
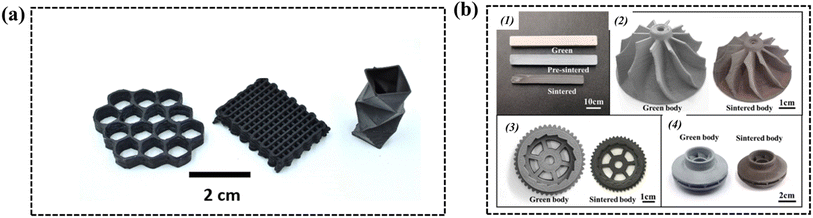 |
| Fig. 5 MEX 3D printing of Si3N4 ceramic: (a) hexagonal array, lattice or log pile structure, and twisted vase;35 (g) rectangular bar, turbine rotor, gear, and swirl fan.26 | |
2.3 Material jetting (MJ) 3D-printed Si3N4 ceramics
Material jetting (MJ), also known as direct inkjet printing, is shown in Fig. 3c. This technique makes use of an organic binder to shape the green body component and requires postprocessing such as debinding and sintering to obtain the final densified object.27 Willems et al. attempted to prepare 3Y-TZP ceramic by using MJ 3D printing, with an as-printed green density of 58% and nearly fully sintered density of 6.03 g cm−3 (99.7% relative density).27 Complex-shaped ceramic components were successfully achieved by MJ 3D printing, as shown in Fig. 6; however, there has been no report on the MJ 3D printing of Si3N4 ceramic until now.
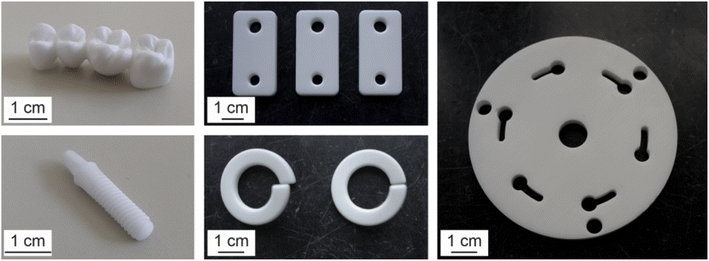 |
| Fig. 6 MJ 3D printing of ceramic components.27 | |
2.4 Binder jetting (BJ) 3D-printed Si3N4 ceramics
Strictly speaking, binder jetting (BJ) 3D printing technology is a type of MJ. Fig. 3d shows the BJ 3D printing of ceramic. The roller spreads the ceramic powder of the powder tank under the nozzle. After that, the nozzle jets the binder to the predetermined areas. Then, the forming platform descends to a certain height, so back and forth. Finally, a 3D ceramic green body is formed on the forming platform.28 Rabinskiy et al. fabricated porous Si3N4 ceramic using BJ 3D printing technology.37 Sintered Si3N4 ceramic had a porosity up to 70%. This work provided some ideas for the 3D printing of dense or porous Si3N4 ceramic components.
2.5 Powder bed fusion (PBF) 3D-printed Si3N4 ceramics
As shown in Fig. 3e, powder bed fusion (PBF) methods, such as selective laser sintering (SLS), can be employed for 3D printing of ceramics. Normally, ceramic powders are laid on the forming platform. The heat source (laser, plasma, etc.) moves according to the setting path to irradiate the ceramic powders. The temperature of the irradiated ceramic powders hence rises sharply to a temperature lower than the melting point, and sintering occurs. Then, the ceramic powders are spread by a doctor blade and sintered layer by layer, and finally form a 3D complex-shaped ceramic component.29 Minasyan et al. fabricated Si3N4-based complex geometry parts by SLS.38 They first used SLS on silicon powder to provide the required shape, and then conducted nitridation on the as-shaped silicon parts to fabricate the Si3N4 component. Wang et al. prepared a high-strength Si3N4 ceramic antenna window using SLS, combined with cold isostatic pressing (CIP) after debinding before final sintering,39 as shown in Fig. 7a. The porosity, bulk density, and bending strength of the 3D-printed Si3N4 ceramic were 18.7%, 3.11 g cm−3, and 685 MPa, respectively. Wu et al. applied AlN as an inorganic binder during the SLS of porous Si3N4 ceramic, with a total porosity of 33.6% and a flexural strength of 23.9 MPa, respectively.40 Finally, they prepared complex-shaped porous Si3N4 ceramic components, as shown in Fig. 7b.
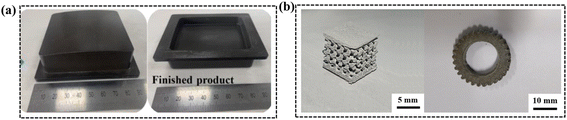 |
| Fig. 7 PBF 3D printing of Si3N4 ceramic: (a) Si3N4 ceramic antenna window39 and (b) complex-shaped porous Si3N4 ceramic components.40 | |
2.6 Direct energy deposition (DED) 3D-printed Si3N4 ceramics
Fig. 3f shows the DED 3D printing.30 Supply material is directed at the heat source, at the point of deposition. Without the use of hard tooling, this innovative process provides a solution to build complex parts with near-net shapes at a much faster rate than the aforementioned processes. However, there have rarely been any reports on the DED 3D printing of ceramics so far.
2.7 Sheet lamination (SL) 3D-printed Si3N4 ceramics
Sheet lamination (SL), also called laminated object manufacturing (LOM), is a 3D printing process in which consecutive layers of paper sheets covered by adhesive applied to one side are continuously bonded and cut with a laser to form a 3D component, as demonstrated in Fig. 3g.28 Liu et al. prepared Si3N4 ceramic components by aqueous tape casting in combination with LOM.41 Homogeneous green Si3N4 ceramic sheets consisting of 48.7 vol% ceramic particles were prepared by tape casting. Then, Si3N4 ceramic components with complex shapes were fabricated by layer-by-layer stacking of the green sheets and a subsequent pressureless sintering, as shown in Fig. 8.
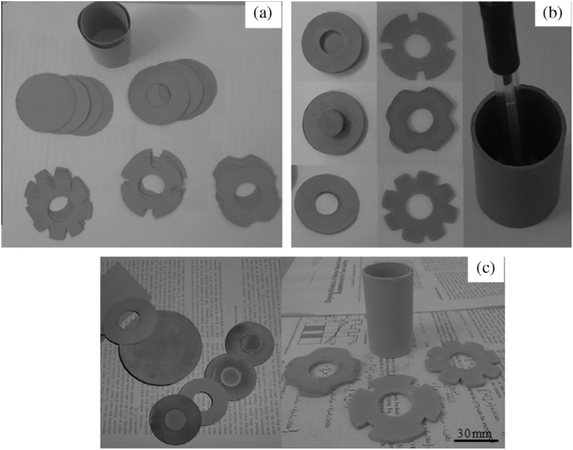 |
| Fig. 8 SL 3D printing of Si3N4 ceramic: (a) green pieces, (b) green bodies, and (c) sintered components.41 | |
To sum up, we summarized the characteristics and advantages/disadvantages of different 3D-printed Si3N4 ceramics, as listed in Table 2. Each 3D printing technology has its printing accuracy, advantages, and disadvantages. From the comparison between different 3D printing technologies for Si3N4 ceramics, it is found that VPP and MEX have the most notable accuracy and advantages, resulting in them being widely reported for the preparation of Si3N4 ceramic implants.
Table 2 Comparison between different 3D printing technologies for Si3N4 ceramics
3D printing |
Accuracy |
Advantages |
Disadvantages |
VPP |
μm |
High accuracy |
Hard to burn out the resin |
MEX |
μm–mm |
Easy forming |
Low accuracy, low strength |
MJ |
mm |
— |
Low accuracy, low strength |
BJ |
mm |
— |
Low accuracy, low strength |
PBF |
μm–mm |
— |
High thermal stress, high number of defects and cracks |
DED |
μm–mm |
— |
High thermal stress, high number of defects and cracks |
SL |
mm |
— |
Hard to form ceramic sheet |
3. 3D-printed Si3N4 ceramic implants
Although Si3N4 ceramic has been widely manufactured by various 3D printing technologies in the past 10 years, the most common 3D-printed Si3N4 ceramic implants for biomedical applications are mainly obtained by VPP 3D printing and MEX 3D printing.
3.1 VPP 3D-printed Si3N4 implants
In 2019, Lithoz GmbH, a famous ceramic 3D printing company, fabricated dense, strong, and precise Si3N4 ceramic parts by a so-called “lithography-based ceramic manufacturing (LCM)” 3D printing technology, which is a type of VPP 3D printing.42 They mixed Si3N4 ceramic particles, solvent, and a photopolymer network together, and then the as-prepared slurry mixture was cured under 460 nm light. Si3N4 green parts were 3D-printed, and Si3N4 final parts were successfully fabricated after debinding and sintering. The LCM 3D-printed Si3N4 ceramic was reported to have a high relative density (99.8%), high biaxial strength (σf = 764 MPa), and high hardness (HV10 = 1500). They also verified the potential biomedical implant applications, such as dental two-piece implants with M1.6 inner threads, of the LCM 3D-printed Si3N4 ceramic, as shown in Fig. 9a. After that, many researchers made tremendous efforts in the field of VPP 3D-printed Si3N4 implants and achieved great progress. In 2023, Zou et al. used another kind of VPP 3D printing, digital light processing (DLP), and prepared high-performance VPP 3D-printed Si3N4 implants for dental use.43 They first prepared ceramic slurry from Si3N4 powder, photosensitive resin monomer (HDDA and TMPTA), photoinitiator (Omnirad 380), and sintering additives (yttrium oxide and alumina), with a high solid loading of 40 vol%. Si3N4 ceramic parts were 3D-printed, debinded, and sintered. The as-prepared Si3N4 ceramic has a high three-point flexural strength of 770 MPa and an excellent fracture toughness of 13.3 MPa m1/2 (as shown in Fig. 9b). They continued to investigate the VPP 3D-printed Si3N4 implants by in vitro biological experiments and found the implants exhibited good biocompatibility. A hemolysis test, oral mucous membrane irritation test, and acute systemic toxicity test (oral route) further confirmed that the VPP 3D-printed Si3N4 implants did not exhibit hemolysis reaction, oral mucosal stimulation, or systemic toxicity. These findings indicated that VPP 3D-printed Si3N4 dental implant restorations with personalized structures had good mechanical properties and biocompatibility, which has great application potential in the future.
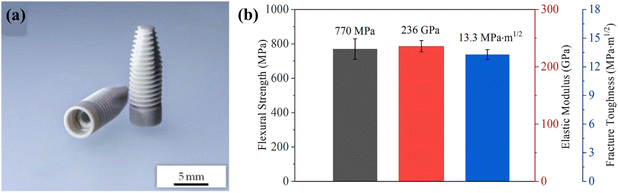 |
| Fig. 9 (a) LCM 3D-printed Si3N4 ceramic dental two-piece implants;42 (b) high-performance VPP 3D-printed Si3N4 implants for dental use.43 | |
In addition, porous Si3N4 ceramic implants were also reported by VPP 3D printing, since porous ceramic structures were beneficial for the following biocompatibility and biomedical applications. In 2023, Huang et al. reported a porous Si3N4 ceramic by VPP 3D printing.44 They added hawthorn nuclear powder as the pore former and used Al2O3 and Y2O3 as the sintering additives. The maximum porosity of the VPP 3D-printed Si3N4 ceramic was 58.48% (as given in Fig. 10a), and the compressive strength and Young's modulus were 79 MPa and 18 GPa, respectively. In vitro cytotoxicity assays were performed, and cell viability was assessed. Finally, they 3D-printed porous Si3N4 ceramic bone for verification (as presented in Fig. 10b and c). The VPP 3D-printed porous Si3N4 ceramic did not exhibit significant cytotoxicity and was capable of supporting the growth of rat bone marrow mesenchymal stem cells (rBMSC), which indicated excellent biocompatibility and potential for bone application.
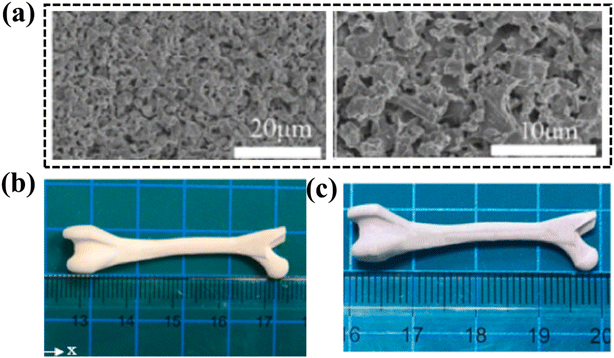 |
| Fig. 10 (a) Porous microstructure, (b) green bone, and (c) sinter bone of VPP 3D-printed porous Si3N4 ceramic.44 | |
3.2 MEX 3D-printed Si3N4 implants
In 2016, Zhao et al. prepared Si3N4 ceramic with controlled shape and architecture for biomedical application by using a so-called robocasting technology, which was a kind of materials extrusion 3D printing.45 In their study, an aqueous paste composed of Si3N4 powder and sintering additives was prepared with the requisite rheology and formed into structures with different geometry and architecture by using robocasting (as given in Fig. 11a and b). Sintering and hot isostatic pressing produced an almost fully dense Si3N4 phase (density = 3.23 g cm−3) with a fibrous microstructure. Four-point bending tests of as-fabricated dense Si3N4 ceramic beams showed a flexural strength of 552 MPa. The as-printed Si3N4 ceramic parts had a controlled surface roughness, and the average surface roughness (Ra) found by AFM was 0.75 μm (as shown in Fig. 11c). They found the Si3N4 parts fabricated in their study were adequate for orthopedic applications.
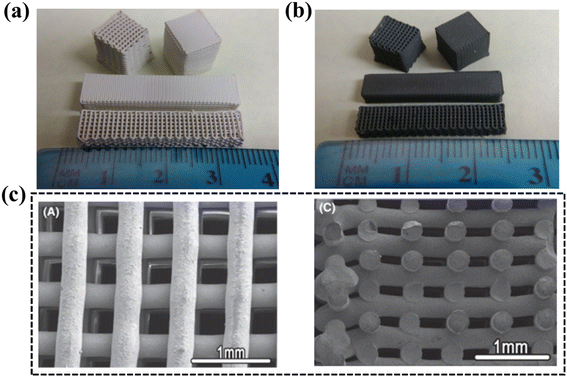 |
| Fig. 11 (a) MEX 3D-printed Si3N4 ceramic green parts, (b) sintered parts, and (c) microstructures of the architecture.45 | |
In 2020, Sainz et al. prepared Si3N4 ceramic scaffolds intended for bone tissue engineering by direct ink writing (DIW),46 which was also a kind of MEX 3D printing, as shown in Fig. 12a. Si3N4 ceramic scaffolds reached densities above 95%, as shown in Fig. 12b and c. The bioactivity of these structures was addressed by evaluating the ion release rate in simulated body fluid. In parallel, atomic force microscopy was used to determine the effect of the filaments surface roughness on protein adsorption (Bovine Serum Albumin) for assessing the potential application of MEX 3D-printed Si3N4 ceramic scaffolds in bone regeneration.
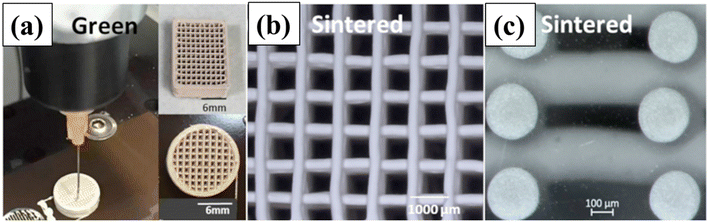 |
| Fig. 12 (a) DIW MEX 3D printing of Si3N4 ceramic scaffolds and (b and c) microstructures of the green and sintered parts.46 | |
An improved screw extrusion fused deposition modeling (FDM), which is also a type of MEX 3D printing, was reported to fabricate Si3N4 ceramic (as given in Fig. 13a).47 The authors used 3D printing to achieve customized molding and gas pressure sintering to prepare dense Si3N4 ceramic and investigated the mechanical properties as well as biological activity. Compared with Ti-alloy, Al2O3, and PEEK, 3D-printed Si3N4 ceramic had significant advantages in mechanical properties with a bending strength of 803 MPa, a fracture toughness of 8.86 MPa m1/2, a Vickers hardness of 15.1 GPa, and a compressive strength of 2725 MPa. Meanwhile, the MEX 3D-printed Si3N4 ceramic had an excellent and more stable biocompatibility compared to biomedical materials and had obvious advantages in antibacterial performance, with an antibacterial rate of 94.6% (as illustrated in Fig. 13b). On the surface of MEX 3D-printed Si3N4 ceramic, cells had good morphology and normal migration and were more conducive to cell spreading, adhesion, and crosslinking. Their study showed that the melting deposition filling characteristics of the 3D printing method, the crystal-oriented growth microstructure characteristics of 3D-printed Si3N4 ceramic, and the beneficial effects of silicon and nitrogen elements were the main reasons for achieving these advantages.
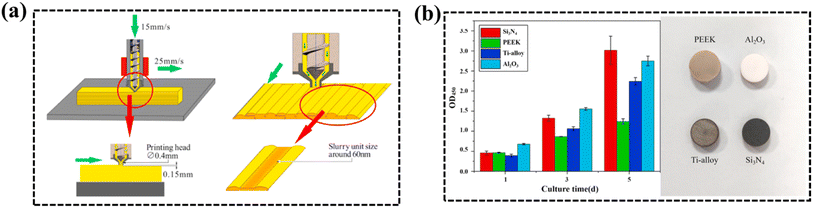 |
| Fig. 13 (a) Improved screw extrusion fused deposition modeling (FDM); (b) excellent biocompatibility of the 3D-printed Si3N4 ceramic.47 | |
In fact, except for the aforementioned 3D printing, other 3D printing technologies, such as SLS, DED, and so on, can also be applied to the 3D printing of Si3N4 ceramic implants. Indeed, dense or porous Si3N4 ceramic has been widely reported to be 3D-printed using different technologies.48–51 We believe that there will be more reports on the Si3N4 ceramic prepared by different 3D printing technologies and more studies on their microstructure, mechanical properties, biological properties, and real clinical applications.
4. Challenges and prospects
Although the 3D printing of Si3N4 ceramic implants has achieved great developments, there are still many aspects that need to break through in the near future to advance their real clinical applications.
4.1 High mechanical properties
Generally, ceramic orthopedic implants need to have excellent mechanical properties, including high mechanical strength, high fracture toughness, good fatigue performance, good creep performance, etc.
On the one hand, the strength and toughness need to improve. Table 3 lists some of the reported strength and fracture toughness of 3D-printed Si3N4 ceramic. Fig. 14 further gives the comparison of the relative density and strength of 3D-printed Si3N4 ceramics by different 3D-printed methods (some relative density or strength data are missing in the references). It is clearly found that most of the 3D-printed Si3N4 ceramics had a relatively low density, low strength, and low toughness relative to traditional sintered dense Si3N4 ceramic (usually >99.9% density and >800 MPa strength)48,49,61 and ZrO2 ceramic (usually >99.9% density and even >1000 MPa strength)62,63 for clinical implant applications. Fortunately, some studies achieved high-performance Si3N4 ceramic using 3D printing. In order to apply it to real applications in the human body, especially the hips, knee, and dental implants, both high strength and high toughness are needed. Therefore, how to further improve the mechanical properties of materials, especially the strength and toughness, will be the future research focus. On the other hand, in actual human implantation environments, ceramic implants need to withstand fatigue, creep, and other service environments. Unfortunately, there has been no report about the fatigue and/or creep behavior of 3D-printed Si3N4 ceramic so far. How to improve the fatigue resistance and creep resistance of 3D-printed Si3N4 ceramic implants will also be the future focus for applications.
Table 3 Strength and fracture toughness of 3D-printed Si3N4 ceramics
Material |
3D printing |
Relative density (%) |
Strength (MPa) |
Fracture toughness (MPa m1/2) |
Ref. |
3-Point flexural strength. 3-Point flexural strength. Biaxial strength. Compressive strength. |
Si3N4 |
VPP |
99.4 |
323a |
— |
52 |
Si3N4 |
VPP |
88.43 |
57.3b |
— |
53 |
Si3N4 |
VPP |
95 |
— |
5.82 |
54 |
Si3N4 |
VPP |
85.4 |
149.2b |
— |
55 |
Si3N4 |
VPP |
95.8 |
— |
6.57 |
56 |
Si3N4 |
VPP |
99.8 |
764c |
— |
42 |
Si3N4 |
VPP |
— |
770b |
13.3 |
43 |
Porous Si3N4 |
VPP |
41.52 |
79d |
— |
44 |
Si3N4 |
MEX |
— |
552b |
— |
45 |
Si3N4 |
MEX |
— |
803b |
8.86 |
46 |
Porous Si3N4 |
MEX |
60–70 |
53b |
— |
57 |
Porous Si3N4 |
BJ |
63.98 |
47b |
— |
58 |
Porous Si3N4 |
BJ |
39 |
95b |
2.4 |
59 |
Si3N4 |
LOM |
93.7 |
475b |
— |
41 |
Si3N4 |
LOM |
99.72 |
725 ± 26b |
7.6 ± 0.4 |
60 |
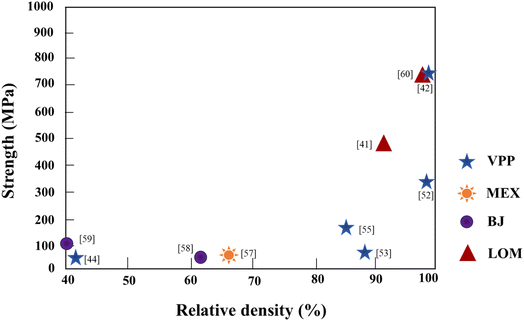 |
| Fig. 14 Comparison of the relative density and strength of 3D-printed Si3N4 ceramics by different 3D-printed methods (some relative density or strength data are missing in the references).41,42,44,52–60 | |
4.2 Composites
Compositing ceramic materials with other materials (such as polymers, metals, etc.) is another path to achieving high-performance implants. In 2021, Marin et al. prepared PMMA/Si3N4 composites by VPP 3D printing and investigated their antibacterial effects.64 In 2023, Vidakis et al. also prepared polylactic acid/Si3N4 nanocomposites by MEX 3D printing, and their biodegraded and biomedical behaviors were further discussed.65 In 2023, Afrouzian et al. fabricated Si3N4-reinforced Ti6Al4V composites by direct energy deposition (DED) 3D printing technology and studied their bio-tribo-corrosion and antibacterial properties.66 However, more detailed studies about the 3D-printed composite implants need to be performed.
Moreover, the 3D printing of organic composite implants with ceramics is currently the most promising candidate for bone/chondral repair. Usually, the organics, such as hydrogels and polymers, provide a cell-like living environment that more closely resembles natural tissue. In the future, in vitro and in vivo experiments of the 3D-printed bioceramic/organic implants need to be extensively investigated.
4.3 Drug loading
In order to further improve the biocompatibility of the 3D-printed Si3N4 ceramic implants, loading them with bioactive factors, such as drugs, is an effective approach. Conventional drug therapy often requires systematic administration of higher doses to achieve the therapeutic dose for the target tissue, resulting in the entire body being affected by side effects. A significant benefit of local drug release is that adequate drug doses can be obtained over a longer period at hard-to-reach sites of action with minimal side effects. Fig. 15 shows the schematic of drug release from the scaffold during bone repair.67 Drug loading will be an important topic of the 3D-printed Si3N4 ceramic scaffold implants in future work. It has been demonstrated that biopolymer scaffolds68,69 and bioceramic scaffolds (hydroxyapatite70 and tricalcium phosphate71) are supportive of drug release, which gives a good reference for 3D-printed Si3N4 implants.
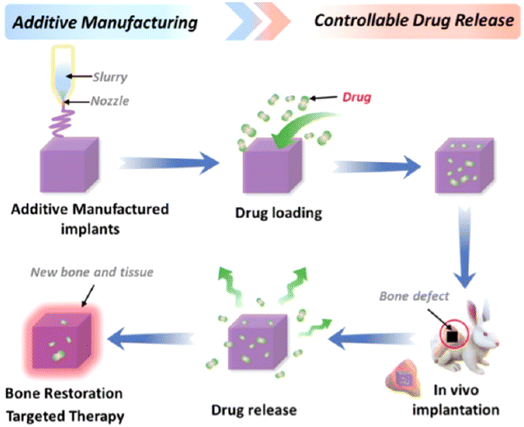 |
| Fig. 15 Schematic representation of drug release from the scaffold during bone restoration.67 | |
4.4 Economics and low cost
Of course, current implants are basically made of polymers, metals, etc. The real clinical application of ceramic implants, especially silicon nitride ceramic implants, still faces the challenge of high costs and high prices. How to reduce the price of medical-grade Si3N4 powders, how to improve the efficiency and reduce the cost of 3D printing of Si3N4 ceramic, and how to reduce the cost of biological and clinical evaluation will be the key to the next step in the clinical application of Si3N4 ceramic implants.
5. Conclusions
Si3N4 ceramic is an attractive ceramic implant material in healthcare, particularly in orthopedic surgery. With the advancement of 3D printing technology, Si3N4 ceramics can now be fabricated into customized implants with precise anatomical shapes, sizes, and microstructures, catering to the individual needs of patients. Therefore, we conducted a comprehensive review of how 3D printing enables complex-shaped Si3N4 ceramic implants for clinical applications, with the aim of providing helpful guidance for related scientists, clinicians, and dentists in this field. The main conclusions are as follows:
(1) There are seven categories of 3D printing, including VPP, MEX, MJ, BJ, PBF, DED, and SL, that are used to prepare complex-shaped ceramic components. Among them, VPP, MEX, and BJ are the most used 3D printing methods for Si3N4 ceramic.
(2) The recent state of the art in novel 3D-printed Si3N4 ceramic implants was summarized. The most common 3D-printed Si3N4 ceramic implants for biomedical applications are mainly obtained by VPP and MEX 3D printing.
(3) Challenges toward 3D printing of Si3N4 ceramic implants are discussed. It is clearly found that most of the 3D-printed Si3N4 ceramic had a relatively low density, low strength, and low toughness compared to traditional sintered dense Si3N4 ceramic and ZrO2 ceramic for clinical implant applications. How to improve the density, strength, toughness, as well as fatigue resistance and creep resistance of 3D-printed Si3N4 ceramic implants will also be the future focus for applications.
(4) Prospects for the 3D printing of Si3N4 ceramic implants, such as composites and drug loading, were further analyzed.
Data availability
All data included in this study are available upon request by contacting the corresponding author.
Conflicts of interest
There are no conflicts to declare.
References
- H. Yang and F. Ye, Microtexture, microstructure evolution, and thermal insulation properties of Si3N4/silica aerogel composites at high temperatures, RSC Adv., 2022, 12, 12226–12234 RSC.
- J. Zhang, G. Liu, W. Cui, Y. Ge, S. Du, Y. Gao, Y. Zhang, Z. Chen, S. Du and K. Chen, Plastic deformation in silicon nitride ceramics via bond switching at coherent interfaces, Science, 2022, 378(6618), 371–376 CrossRef CAS PubMed.
- J. Tatami, M. Uda, T. Takahashi, T. Yahagi, M. Iijima, K. Matsui, T. Ohij and H. Nakano, Microscopic mechanical properties of silicon nitride ceramics corroded in sulfuric acid solution, J. Eur. Ceram. Soc., 2024, 44(9), 5415–5421 CrossRef CAS.
- R. B. Heimann, Silicon nitride, a close to ideal ceramic material for medical application, Materials, 2021, 4(2), 208–223 CAS.
- X. Zeng, C. S. Sipaut, N. M. Ismail, Y. Liu, Y. Y. Farm, B. Feng and J. He, Preparation of 3D printed silicon nitride bioceramics by microwave sintering, Sci. Rep., 2024, 14, 15825 CrossRef CAS PubMed.
- H. Mahammadi, S. Beddu, M. Petrů, M. Sepantafar, M. Ebadi, B. K. Yap, L. T. Bang, T. C. Yong, S. Ramesh and S. S. R. Koloor, Advances in silicon nitride ceramic biomaterials for dental applications – A review, J. Mater. Res. Technol., 2024, 28, 2778–2791 CrossRef.
- SINTX Technologies, available online: accessed on 30 July 2024.
- C. Wu, T. Zhang, W. Guo, X. Meng, Z. Ding and S. Liang, Laser-assisted grinding of silicon nitride ceramics: micro-groove preparation and removal mechanism, Ceram. Interfaces, 2022, 48(21), 32366–32379 CrossRef CAS.
- L. Huang, Y. Dong, Z. Wang, D. Zhang and Z. Yu, Study on the effect of multi-walled carbon nanotube (MWCNT) addition on the microstructure, mechanical and cutting performance of silicon nitride ceramic tools, Int. J. Refract. Met. Hard Mater., 2024, 125, 106907 CrossRef CAS.
- H. Yang, Z. Wang, M. Sun, F. Chen, J. Ji, S. Chen, Y. Chen, D. Ma, Z. Zhang, B. Pan, Y. Wei and Q. Li, Effect of pH, milling time, and Isobam content on porous silicon nitride ceramics prepared by gel casting, Adv. Powder Technol., 2023, 2(1), 100060 Search PubMed.
- T. G. Aguirre, C. L. Cramer and D. J. Mitchell, Review of additive manufacturing and densification techniques for the net-and near net-shaping of geometrically complex silicon nitride components, J. Eur. Ceram. Soc., 2022, 42(3), 735–743 CrossRef CAS.
- Y. S. Kwon, J. H. Kim, H. Lee, S. S. Scherrer and H. H. Lee, Strength-limiting damage and defects of dental CAD/CAM full-contour zirconia ceramics, Dental Mater, 2024, 40(4), 653–663 CrossRef CAS PubMed.
- A. Sharama, A. Babbar, Y. Tian, B. P. Pathri, M. Gupta and R. Singh, Machining of ceramic materials: a state-of-the-art review, Int. J. Interact. Des. Manuf., 2022, 17, 2891–2911 CrossRef.
- Y. Ran, J. Sun, R. Kang, Z. Dong and Y. Bao, Towards understanding the machining process in grinding of ceramic matrix composites: A review, Composites, Part B, 2024, 284, 111657 CrossRef CAS.
- S. Yin, W. Wan, X. Fang, H. Ma, X. Xie, C. Zhou, T. Li and R. Zuo, Mechanical and thermal properties of Si3N4 ceramics prepared by gelcasting using high-solid-loading slurries, Ceram. Interfaces, 2023, 49(24A), 40930–40941 CrossRef CAS.
- J. Ye, B. Zhang, H. Zhang, Z. Zhong, Y. Wang, Q. Liu and F. Ye, Tuning the dielectric properties of porous BN/Si3N4 composites by controlling porosity, J. Eur. Ceram. Soc., 2023, 43(2), 370–377 CrossRef CAS.
- X. Dong, J. Wu, H. Yu, Q. Zhou, W. Wang, X. Zhang, L. Zhang, L. Li and R. He, Additive manufacturing of silicon nitride ceramics: A review of advances and perspectives, Int. J. Appl. Ceram. Technol., 2022, 19(6), 2929–2949 CrossRef CAS.
- Y. Lakhdar, C. Tuck, J. Binner, A. Terry and R. Goodridge, Additive manufacturing of advanced ceramic materials, Prog. Mater. Sci., 2021, 116, 100736 CrossRef CAS.
- R. Su, J. Chen, X. Zhang, X. Gao, W. Wang, Y. Li and R. He, Accuracy controlling and mechanical behaviors of precursor-derived ceramic SiOC microlattices by projection micro stereolithography (PμSL) 3D printing, J. Adv. Ceram., 2023, 12(11), 2134–2147 CrossRef CAS.
- X. Zhai, J. Chen, R. Su, X. Gao, X. Zhang and R. He, Vat photopolymerization 3D printing of Al2O3 ceramic cores with strip-shaped pores by using polyamide 6 fiber template, J. Am. Ceram. Soc., 2024, 107(8), 5400–5411 CrossRef CAS.
- Y. Shan, Y. Bai, S. Yang, Q. Zhou, G. Wang, B. Zhu, Y. Zhou, W. Fang, N. Wen, R. He and L. Zhao, 3D-printed strontium-incorporated β-TCP bioceramic triply periodic minimal surface scaffolds with simultaneous high porosity, enhanced strength, and excellent bioactivity, J. Adv. Ceram., 2023, 12(9), 1671–1684 CrossRef CAS.
- W. Wang, Z. Li, X. Gao, Y. Huang and R. He, Material extrusion 3D printing of large-scale SiC honeycomb metastructure for ultra-broadband and high temperature electromagnetic wave absorption, Addit. Manuf., 2024, 85, 104158 CAS.
- W. Wang, X. Gao, Z. Li, C. Shen and R. He, Effects of ceramic layer height on the mechanical properties of Cf/SiC ceramic matrix composites fabricated by fiber-laying-assisted material extrusion 3D printing, Compos. Commun., 2024, 48, 101926 CrossRef.
- ISO/ASTM 52900: 2015-Additive manufacturing, available online: https://www.iso.org/standard/69669.html, accessed on 30 July 2024.
- A. A. Rashid, W. Ahmed, M. Y. Khalid and M. Koç, Vat photopolymerization of polymers and polymer composites: Processes and applications, Addit. Manuf., 2021, 47, 102279 Search PubMed.
- R. Spina and L. Morfini, Material extrusion additive manufacturing of ceramics: A review on filament-based process, Materials, 2024, 17(11), 2779 CrossRef CAS PubMed.
- E. Willems, M. Turon-Vinas, B. C. dos Santos, B. V. Hooreweder, F. Zhang, B. V. Meerbeek and J. Vleugels, Additive manufacturing of zirconia ceramics by material jetting, J. Eur. Ceram. Soc., 2021, 41(10), 5292–5306 CrossRef CAS.
- A. Razavykia, E. Brusa, C. Delprete and R. Yavari, An overview of additive manufacturing technologies—a review to technical synthesis in numerical study of selective laser melting, Materials, 2020, 13(17), 3895 CrossRef CAS PubMed.
- M. S. Korium, H. Roozbahani, M. Alizadeh, S. Perepelkina and H. Handroos, Direct metal laser sintering of precious metals for jewelry applications: process parameter selection and microstructure analysis, IEEE Access, 2021, 9, 126530–126540 Search PubMed.
- A. Selema, M. N. Ibrahim and P. Sergeant, Metal additive manufacturing for electrical machines: Technology review and latest advancements, Energies, 2022, 15(3), 1076 CrossRef.
- G. Konstantinou, E. Kakkava, L. Hagelüken, P. V. W. Sasikumar, J. Wang, M. G. Makowska, G. Blugan, N. Nianias, F. Marone, H. V. Swygenhoven, J. Brugger, D. Psaltis and C. Moser, Additive micro-manufacturing of crack-free PDCs by two-photon polymerization of a single, low-shrinkage preceramic resin, Addit. Manuf., 2020, 35, 101343 CAS.
- M. Regehly, Y. Garmshausen, M. Reuter, N. F. König, E. Israel, D. P. Kelly, C. Y. Chou, K. Koch, B. Asfari and S. Hecht, Xolography for linear volumetric 3D printing, Nature, 2020, 588, 620–624 CrossRef CAS PubMed.
- E. Schwarzer-Fischer, E. Zschippang, W. Kun, C. Koplin, Y. M. Löw, U. Scheithauer and A. Michaelis, CerAMfacturing of silicon nitride by using lithography-based ceramic vat photopolymerization (CerAM VPP), J. Eur. Ceram. Soc., 2023, 43(2), 321–331 CrossRef CAS.
- F. L. Zhou, J. M. Wu, C. Tian, W. K. Li, L. Guo, Y. Y. Qin, X. Lin, F. Wang, H. S. Xu and Y. S. Shi, Effect of thermosetting resin coating modification on the properties of Si3N4 ceramics prepared by vat photopolymerization, J. Eur. Ceram. Soc., 2024, 44(13), 7465–7473 CrossRef CAS.
- C. M. Clarkson, C. Wyckoff, M. J. S. Parvulescu, L. M. Rueschhoff and M. B. Dickerson, UV-assisted direct ink writing of Si3N4/SiC preceramic polymer suspensions, J. Eur. Ceram. Soc., 2022, 42(8), 3374–3382 CrossRef CAS.
- Q. Jiang, D. Yang, H. Yuan, R. Wang, M. Hao, W. Ren, G. Shao, H. Wang, J. Cui and J. Hu, Fabrication and properties of Si2N2O-Si3N4 ceramics via direct ink writing and low-temperature sintering, Ceram. Int., 2022, 48(1), 32–41 CrossRef CAS.
- L. Rabinskiy, A. Ripetsky, S. Stinikov, Y. Solyaev and R. Kahramanov, Fabrication of porous silicon nitride ceramics using binder jetting technology, IOP Conf. Ser.: Mater. Sci. Eng., 2006, 140(1), 012023 Search PubMed.
- T. Minasyan, L. Liu, M. Aghayan, L. Kollo, N. Kamboj, S. Aydinyan and I. Hussainova, A novel approach to fabricate Si3N4 by selective laser melting, Ceram. Inter., 2018, 44(12), 13689–13694 CrossRef CAS.
- K. Wang, C. Bao, C. Zhang, Y. Li, R. Liu, H. Xu, H. Ma, J. Man and S. Song, Preparation of high-strength Si3N4 antenna window using selective laser sintering, Ceram. Inter., 2022, 47(22), 31277–31285 CrossRef.
- Y. R. Wu, J.-H. He, L.-J. Cheng, J.-M. Wu and Y.-S. Shi, Effects of AlN inorganic binder on the properties of porous Si3N4 ceramics prepared by selective laser sintering, Ceram. Inter., 2022, 48(20), 29900–29906 CrossRef CAS.
- S. Liu, F. Ye, L. Liu and Q. Liu, Feasibility of preparing of silicon nitride ceramics components by aqueous tape casting in combination with laminated object manufacturing, Mater. Design, 2015, 16, 331–335 Search PubMed.
- A. A. Altun, T. Prochaska, T. Konegger and M. Schwentenwein, Dense, strong, and precise silicon nitride-based ceramic parts by lithography-based ceramic manufacturing, Appl. Sci., 2020, 10(3), 996 CrossRef CAS.
- R. Zou, L. Bi, Y. Huang, Y. Wang, Y. Wang, L. Li, J. Liu, L. Feng, X. Jiang and B. Deng, A biocompatible silicon nitride dental implant material prepared by digital light processing technology, J. Mech. Behav. Biomed. Mater., 2023, 141, 105756 CrossRef CAS PubMed.
- S. Huang, P. Yang, P. Sheng, T. Ning and S. Wu, Additive manufacturing of complex-shaped and porous silicon nitride-based components for bionic bones, Ceram. Int., 2023, 49(15), 25025–25034 CrossRef CAS.
- S. Zhao, W. Xiao, M. N. Rahaman, D. O'Brien, J. W. Seitz-Sampson and B. S. Bal, Robocasting of silicon nitride with controllable shape and architecture for biomedical applications, Int. J. Appl. Ceram. Technol., 2017, 14(2), 117–127 CrossRef CAS.
- M. A. Sainz, S. Serena, M. Belmonte, P. Miranzo and M. I. Osendi, Protein adsorption and in vitro behavior of additively manufactured 3D-silicon nitride scaffolds intended for bone tissue engineering, Mater. Sci. Eng. Carbon, 2020, 115, 110734 CrossRef CAS PubMed.
- N. Vidakis, M. Petousis, N. Michailidis, V. Papadakis, N. Mountakis, A. Argyros, E. Dimitriou, C. Charou and A. Moutsopoulou, Polylactic acid/silicon nitride biodegradable and biomedical nanocomposites with optimized rheological and thermomechanical response for material extrusion additive manufacturing, Adv. Biomed. Eng., 2023, 6, 100103 CrossRef.
- H. Marulcuoglu and F. Kara, Microstructure and mechanical properties of dense Si3N4 ceramics prepared by direct coagulation casting and cold isostatic pressing, J. Mater. Sci. Eng. A, 2022, 854, 143782 CrossRef CAS.
- K. Kumar, M. J. Kim, H. M. Oh, Y. J. Park, H. N. Kim, H. J. Ma, J. W. Lee and J. W. Ko, Fabrication of highly dense Si3N4 via record low-content additive system for low-temperature pressureless sintering, J. Am. Ceram. Soc., 2022, 105(7), 4669–4680 CrossRef CAS.
- L. Zhang, W. Ma, Z. Ren, H. Tang, Y. Yu, L. Wang, T. Li, W. Liu and Z. Qiao, Porous Si3N4 ceramics with surface roughness for bone repair, Ceram. Int., 2024, 50(5), 7558–7566 CrossRef.
- N. Kota and S. Roy, Effect of H3PO4 content and processing temperature on the structure and mechanical properties of porous Si3N4, Ceram. Int., 2023, 49(23), 37174–37186 CrossRef CAS.
- J. Lüchtenborg, T. Mühler, F. Leonard and J. Günster, Laser-induced slip casting (LIS)–a new additive manufacturing process for dense ceramics demonstrated with Si3N4, J. Ceram. Sci. Technol., 2017, 8(4), 531–540 Search PubMed.
- M. Wang, C. Xie, R. He, G. Ding, K. Zhang, G. Wang and D. Fang, Polymer-derived silicon nitride ceramics by digital light processing based additive manufacturing, J. Am. Ceram. Soc., 2019, 102(9), 5117–5126 CrossRef CAS.
- Y. Liu, L. Zhan, Y. He, J. Zhang, J. Hu, L. Cheng, Q. Wu and S. Liu, Stereolithographical fabrication of dense Si3N4 ceramics by slurry optimization and pressure sintering, Ceram. Int., 2020, 46(2), 2063–2071 CrossRef CAS.
- M. Li, H.-L. Huang, J.-M. Wu, Y.-R. Wu, Z.-A. Shi, J.-X. Zhang and Y.-S. Shi, Preparation and properties of Si3N4 ceramics via digital light processing using Si3N4 powder coated with Al2O3-Y2O3 sintering additives, Addit. Manuf., 2022, 53, 102713 CAS.
- W.-D. Rao, Y. Liu, L.-J. Cheng and S.-J. Liu, Densification mechanism of stereolithographical dense Si3N4 ceramics with CeO2 as sintering additive by field assisted sintering, J. Cent. South Univ., 2021, 28(4), 1233–1243 CrossRef CAS.
- L. N. Rabinskiy, S. A. Sitnikov, V. A. Pogodin, A. A. Ripetskiy and Y. O. Solyaev, Binder jetting of Si3N4 ceramics with different porosity, Solid State Phenom., 2017, 269, 37–50 Search PubMed.
- X. Li, L. Zhang and X. Yin, Microstructure and mechanical properties of three porous Si3N4 ceramics fabricated by different techniques, Mater. Sci. Eng. A., 2012, 549, 43–49 CrossRef CAS.
- X. Li, L. Zhang and X. Yin, Effect of chemical vapor infiltration of Si3N4 on the mechanical and dielectric properties of porous Si3N4 ceramic fabricated by a technique combining 3-D printing and pressureless sintering, Script Mater, 2012, 67(4), 380–383 CrossRef CAS.
- F. Niu, X. Yang, Y. Li, J. Guo, P. Liu, Z. Xie and X. Yang, Fused deposition modeling of Si3N4 ceramics: a cost-effective 3D-printing route for dense and high performance non-oxide ceramic materials, J. Eur. Ceram. Soc., 2022, 42(15), 7369–7376 CrossRef CAS.
- L. Fu, H. Engqvist and W. Xia, Spark plasma sintering of biodegradable Si3N4 bioceramic with Sr, Mg and Si as sintering additives for spinal fusion, J. Eur. Ceram. Soc., 2018, 38(4), 2110–2119 CrossRef CAS.
- C. Santos, I. F. Coutinho, J. E. V. Amarante, M. F. R. P. Alves, M. M. Coutinho and C. R. M. Silva, Mechanical properties of ceramic composites based on ZrO2 co-stabilized by Y2O3–CeO2 reinforced with Al2O3 platelets for dental implants, J. Mech. Behav. Biomed., 2021, 116, 104372 CrossRef CAS PubMed.
- M. Li, S. Cokic, B. V. Meerbeek, J. Vleugels and F. Zhang, Novel zirconia ceramics for dental implant materials, J. Mater. Sci. Technol., 2025, 210, 97–108 CrossRef CAS.
- E. Marin, F. Boschetto, M. Zanocco, T. Honma, W. Zhu and G. Pezzotti, Explorative study on the antibacterial effects of 3D-printed PMMA/nitrides composites, Mater. Design, 2021, 206, 109788 CrossRef CAS.
- N. Vidakis, M. Petousis, N. Michailidis, V. Papadakis, N. Mountakis, A. Argyros, E. Dimitriou, C. Charou and A. Moutsopoulou, Polylactic acid/silicon nitride biodegradable and biomedical Nanocomposites with optimized rheological and thermomechanical response for material extrusion additive manufacturing, Biomed. Eng. Adv, 2023, 6, 100103 CrossRef.
- A. Afrouzian and A. Bandyopadhyay, 3D printed silicon nitride, alumina, and hydroxyapatite ceramic reinforced Ti6Al4V composites-Tailored microstructures to enhance bio-tribo-corrosion and antibacterial properties, J. Mech. Behav. Biomed. Mater., 2023, 144, 105973 CrossRef CAS PubMed.
- Q. Zhou, X. Su, J. Wu, X. Zhang, R. Su, L. Ma, Q. Sun and R. He, Additive manufacturing of bioceramic implants for restoration bone engineering: Technologies, advances, and future perspectives, ACS Biomater. Sci. Eng., 2023, 9(3), 1164–1189 CrossRef CAS PubMed.
- I. Serris, P. Serris, K. M. Frey and H. Cho, Development of 3D-printed layered PLGA films for drug delivery and evaluation of drug release behaviors, AAPS PharmSciTech, 2020, 21, 256 CrossRef CAS PubMed.
- C. Liu, Z. Wang, X. Wei, B. Chen and Y. Luo, 3D printed hydrogel/PCL core/shell fiber scaffolds with NIR-triggered drug release for cancer therapy and wound healing, Acta Biomater., 2021, 131, 314–325 CrossRef CAS PubMed.
- S. Chen, Y. Shi, Y. Luo and J. Ma, Layer-by-layer coated porous 3D printed hydroxyapatite composite scaffolds for controlled drug delivery, Colloids Surf., B, 2019, 179, 121–127 CrossRef CAS PubMed.
- J. Yuan, P. Zhen, H. Zhao, K. Chen, X. Li, M. Gao, J. Zhou and X. Ma, The preliminary performance study of the 3D printing of a tricalcium phosphate scaffold for the loading of sustained release anti-tuberculosis drugs, J. Mater. Sci., 2015, 50, 2138–2147 CrossRef CAS.
|
This journal is © The Royal Society of Chemistry 2025 |
Click here to see how this site uses Cookies. View our privacy policy here.