An overview of various critical aspects of low-cobalt/cobalt-free Li-ion battery cathodes
Received
30th August 2024
, Accepted 7th December 2024
First published on 10th December 2024
Abstract
Cathodes of lithium-ion batteries (LIBs) significantly impact the environmental footprint, cost, and energy performance of the battery-pack. Hence, sustainable production of Li-ion battery cathodes is critically required for ensuring cost-effectiveness, environmental benignity, consumer friendliness, and social justice. Battery chemistry largely determines individual cell performance as well as the battery pack cost and life cycle greenhouse gas emission. Continuous manufacturing platforms improve production efficiency in terms of product yield, quality and cost. Spent-battery recycling ensures the circular economy of critical elements that are required for cathode production. Innovations in fast-charging LIBs are particularly promising for sustainable e-mobility with a reduced carbon footprint. This article provides an overview of these research directions, emphasizing strategies for low-cobalt cathode development, recycling processes, continuous production and improvement in fast-charging capability.
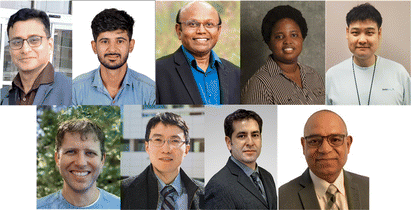 From left to right (top row followed by bottom row) | Dr Sourav Mallick, a post-doctoral scholar in the Department of Chemical and Life Science Engineering (CLSE), Virginia Commonwealth University (VCU), USA, is working in the field of electrochemical energy storage. Arjun Patel is pursuing his PhD in the same department under the supervision of Prof. Ram B. Gupta since 2021 and interested in battery research. Dr M. Parans Paranthaman, a corporate fellow and a renowned battery scientist, is working at the Oak Ridge National Laboratory, USA. Dr Jethrine H. Mugumya is a former PhD student of VCU and currently pursuing her post-doctoral research on battery technology in Brookhaven National Laboratory, USA. Sunuk Kim is a chemical engineering PhD student at VCU. Dr Michael L. Rasche is a research scientist at VCU and interested in mathematical models of chemical reaction. Dr Mo Jiang is an assistant professor in the CLSE, VCU, working on the scalable manufacturing of essential (bio)pharmaceutical ingredients and active cathode materials using slug flow. Dr Herman Lopez is the co-founder and CTO of Ionblox Inc., leading high-power silicon-based LIB-research. Dr Ram B. Gupta is a professor and the associate dean for research in the College of Engineering, VCU, and known as a leading researcher in the fields of sustainable energy, materials, and technologies. |
1. Introduction
The rapid expansion of the global electric vehicle (EV) market demands increased production of high-performance Li-ion batteries (LIBs). In 2022 alone, there was a 55% rise in new EV registration, which was also coupled with an increase in the global automotive lithium-ion battery demand by 65%.1 The global LIB market is predicted to reach up to $91.9 billion by 2026.2 Among the various components of a complete LIB pack, the cathode active material (CAM) is responsible for about 25% of the total mass and cost.3 Hence, attaining sustainability in LIB cathode production is the very first step towards sustainable e-mobility, which is supported by three interlinked fundamental pillars: economic, environmental and social viabilities. Significant reduction in the cost of CAMs without affecting their charge storage performance can make LIB technology affordable and consumer friendly. Owing to their benefit of possessing multiple oxidation states, various transition metals, such as nickel, cobalt, manganese, and iron, are needed to produce stable and high performance cathodes. Among them, cobalt has been the most expensive but important element. Hence, scientific innovations integrated with serious industrial efforts are required to produce EV-relevant low-cobalt or cobalt-free CAMs. Moreover, production of cobalt-free cathodes has socio-political significance. Presently, Democratic Republic of Congo (DRC) is the single source of about 75% of cobalt used for cathode manufacturing. Severe violation of human rights, brutal and militia-controlled mining practices, involvement of child labor and human trafficking for cobalt mining in DRC have placed the socio-political viability of the LIB industry in serious doubt.4 The other reliable domestic source for cobalt is recycling of spent batteries. Hence, the recycling aspects of spent batteries are discussed later. In addition, serious efforts are required to make LIB cathodes free of cobalt. Technical issues arising upon elimination of cobalt include cation mixing, irreversible phase change, and poor cycling performance, which should be judiciously managed.5
Although LIB technology is considered greener than fossil fuel-based technologies, the extraction and refining of raw materials for battery cathode production can cause several environmental impacts, including degradation of land and biodiversity as well as contamination of water, soil, and air with hazardous wastes. These issues can be reduced significantly by using less hazardous chemicals, water-based green synthesis processes, minimizing chemical wastage during the production of electrode materials, and development of advanced direct recycling processes. Selection of cost-effective and eco-friendly synthesis procedures together with efficient reactor design is one of the important aspects of battery cathode production, which needs special attention. In this context, it is worth mentioning that continuous manufacturing techniques have proven to be advantageous compared to the batch processes for reducing waste generation, energy use and chemical consumption when successfully implemented in various other industries such as pharmaceuticals, food-processing, papers, pastes, and oil refining.6 Hence, development of suitable continuous manufacturing platforms for electrode active materials has great significance. On the other hand, it is predicted that a huge amount of spent batteries will be generated in the near future, up to the rate of 2 million metric tons per year.7 Therefore, development of efficient battery recycling techniques could effectively mitigate the supply-chain constraints of individual elements, including cobalt recovery, required in the manufacturing of a new battery pack and largely reduce the battery production cost as well as the mining-related environmental impacts. For example, the industrial market size of LIB recycling in China reached $2.18 billon with a year-on-year growth rate of 183% in the year 2022 8 and the demand for global lithium-ion battery will grow approximately 33% annually, reaching around 4.7 TW h by 2030.9 Thus, development of cost-effective and advanced recycling technologies will facilitate the sustainability of the LIB industry. Another crucial concern of the existing EV-batteries is their slower charging rate. Hence, there is a tremendous scope to upgrade LIB technology to the fast-charging standard to reduce the mileage anxiety and demand for high energy electrodes, leading towards sustainable e-mobility by supporting consumers' everyday life. Currently, a third-generation charging station of 250 kW is used by Tesla and it can charge for traveling about 250 km distance in 15 min.10 However, a significant improvement in fast-charging technology is needed.
This perspective article is focused on the current critical aspects of LIB technology: low cobalt or cobalt-free cathode active material production, cathode recycling, and fast-charging LIBs. Comparative studies on commercialized cathode materials, batch versus continuous manufacturing processes, and various recycling technologies for recovering all critical elements such as lithium, nickel, and cobalt (e.g., hydrometallurgical, pyrometallurgical and direct recycling) are discussed here. The prospects of fast-charging LIB technology are also elaborated in this article.
2. Journey towards low-cobalt/cobalt-free cathodes
Li-ion intercalation behavior was first observed in a cobalt-free layered material, TiS2, by Prof. M. S. Whittingham in the year 1976.11 However, a low discharge voltage of <2.5 V and short-circuiting caused by the dendritic growth of lithium at the Li-metal anode electrolyte interface impeded the successful demonstration of the sulphide cathode based LIB. In order to increase the cell voltage by lowering the cathode energy as much as possible compared to the Li anode, transition metal oxides were explored as LIB cathodes.12 Finally, in 1980 Prof. J. B. Goodenough and his team successfully demonstrated the use of LiCoO2 (LCO) as the LIB cathode with a higher operating voltage of 3.9 V and a high theoretical capacity of 274 mA h g−1.13 This was the first commercialized CAM (in 1991) containing a significant amount of cobalt. The primary limitations of the LiCoO2-based LIB cathodes were a low practical charge capacity of ∼149 mA h g−1 and severe interlayer repulsion in the high voltage range causing structural damage. Although the other congeners of lithiated mono-metallic oxides, such as LiNiO2 and LiMnO2, with a high theoretical capacity within the range of 275–285 mA h g−1 are investigated as layered cathode active materials during the years 1990–2000, they also suffer from a number of intrinsic drawbacks, which limits their commercial use. The LiNiO2 faced the issue of Ni2+/Li+ mixing during the synthesis and low thermal stability in the delithiated state,14,15 whereas the LiMnO2 structure shows poor stability upon consecutive Li+ intercalation/deintercalation and transforms to a spinel and finally to a cubic structure.16,17 Moreover, the disproportionation of Mn3+ to Mn2+ and Mn4+ causes severe cation mixing and cathode dissolution related issues.18 In order to mitigate the issues of mono-metallic oxides, lithiated bi-metallic oxides, such as Li(Ni,Co)O2, Li(Ni,Mn)O2 and Li(Co,Mn)O2, were synthesized.17 Among the three, the Li(Ni,Co)O2 showed improved electrochemical performance in terms of specific capacity (∼180 mA h g−1), rate capability and stability of the layered structure in the charged state. Actually, in this case the presence of Co3+ effectively prevents the Ni3+ to Ni2+ transition followed by cation mixing.18,19 In order to ensure a tradeoff between the chemical stability, structural stability and the energy storage performance of the layered cathode material, LiNi1/3Mn1/3Co1/3O2 (NCM111) was first synthesized in 2001.20 The NCM111 based LIB showed promising electrochemical performance in terms of a practical achievable capacity of ∼150 mA h g−1 (within 2.5–4.2 V vs. Li+/Li), good rate capability and stable cycling performance, and hence was used in several commercial products.21,22 However, the high cost and socio-political turmoil related to the extensive cobalt-mining and the requirement for high energy density cathode materials for EV technology stimulate the search for alternate materials. Current research on low-cobalt/cobalt-free cathodes is directed towards developing (i) Li-rich cathodes, (ii) Ni-rich cathodes, and (iii) Co-free alternatives (as shown in Fig. 1).
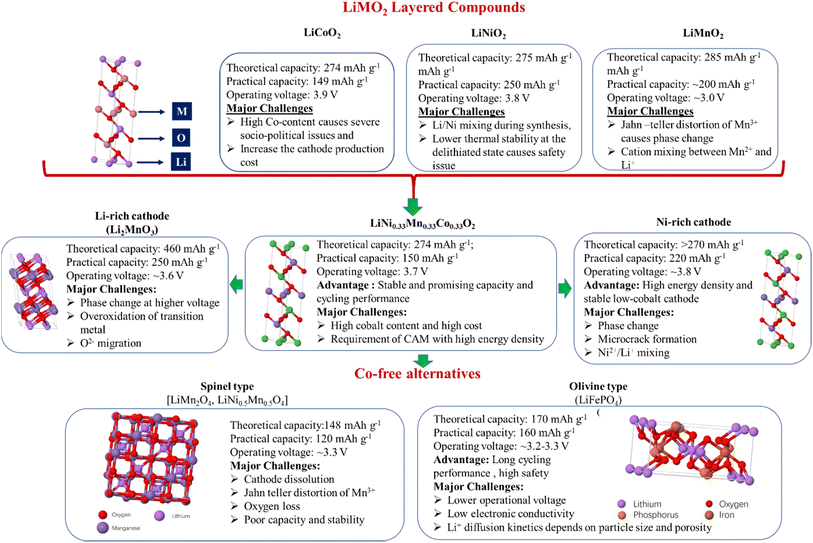 |
| Fig. 1 Various lithium-ion battery (LIB) cathodes. | |
2.1 Li-rich cathodes
Li-rich layered cathodes are considered as excess Li+-substituted materials in the transition metal layer with the general formula of Li(LixNi1−x−y−zMnyCoz)O2 and an O3-type monoclinic crystal structure.23 Among the various Li-rich cathodes, Li2MnO3 has been explored the most.24,25 It is worth mentioning that although the Li-rich layered cathode possesses a very high theoretical capacity of 460 mA h g−1, the structural degradation caused by the parasitic side reactions with the electrolyte limits its practical capacity to ∼250 mA h g−1. Primarily, the stepwise formation of Li+ vacancies in octahedral sites and migration of Mn to the Li layer at >4.5 V cause irreversible phase transition from a layered to spinel structure.26 Besides this, chemical changes, including O2− migration, and overoxidation of transition metals limited the commercialization of the Li-rich layered cathodes.18
2.2 Ni-rich cathodes
Ni-rich layered oxide cathodes, with the general formula of Li(Ni1−x−yMnxCoy)O2, where (0 < x + y ≤ 0.5), are attractive due to their high energy density and low cost. The theoretical capacity of Ni-rich NCMs is 270 mA h g−1. Various Ni-rich layered cathodes are already explored, including NCM442, NCM532, NCM622 and NCM811.27 Except NCM811, most of them are almost commercially utilized in the EV industry.28 On the other hand aluminium containing Ni-rich layered oxide Li[Ni0.8Co0.15Al0.05]O2 (NCA) has also been utilized in EV production by Tesla Motors.28 However, LIBs based on the Ni-rich NCMs, specifically NCM-811, faced some major challenges, including severe cation mixing, microcrack formation, and phase change related issues. A detailed discussion on those issues and probable remedies are already elaborated in our previously published review article.5
2.3 Cobalt-free alternatives
Spinels and olivine type cathodes can be categorized as Co-free alternative CAM for LIB, as described below.
Spinels: the spinel, precisely LiMn2O4 (LMO), was first utilized as the LIB cathode in 1986.29 This material is advantageous due to its low cost, environmental benignity, and high natural abundance. However, Jahn–Teller distortion of Mn3+, Mn2+ dissolution, O2− migration and poor stability are few of the bottlenecks of this kind of material. Incorporation of Ni into the spinel structure (LNMO) increases the capacity and working voltage up to ∼4.7 V. Unfortunately, parasitic side reactions with the electrolyte in the higher voltage region cause severe performance decay.30 Although surface coating and doping in the spinel crystal lattice significantly mitigate those issues, large scale production of the modified spinel structure is still a challenging task.
Olivine: olivine-type compounds with a general formula of LiMPO4, where M = Ni, Co, Fe, or Mn, are proven to be a promising class of cathode materials for commercial LIB production. Among all, LiFePO4 (LFP) is already utilized in EV technology due to its several advantages, such as low cost of raw materials, high thermal stability and safety, long cycling stability and rate capability.31 It was first discovered by Prof. J. B. Goodenough's group in 1997.32 It offers a moderate capacity of 170 mA h g−1 with an operating voltage of 3.2–3.3 V. The primary reason behind the high structural stability of the LiFePO4 cathode during cycling lies in the fact that the orthorhombic structure of LiFePO4 remains unchanged upon complete delithiation (FePO4 formation) in the higher voltage region, leading to a small volume change of only ∼7%.33 Among others, the LiFePO4 is also a good choice as a fast-charging cathode. On the other hand, poor electronic conductivity, a low Li+ diffusion co-efficient and a low volumetric energy density are the primary drawbacks of this material.34 In spite of all these issues, LiFePO4 is a good option as a cheap and safe cobalt-free cathode material for EV applications.
2.4 Challenges of low-cobalt cathodes and effective remedies
2.4.1 Cation mixing.
Possession of Li+ sites by the transition metals, precisely Ni2+/3+ in the layered structure of Ni-rich NCM cathode materials, is one of the major challenges, which severely deteriorates the cycling and rate performance of the battery. The primary reasons for cation mixing are similarity in size, and superexchange interaction, which are already discussed in our previously published review article.5 Presence of a sufficient amount of cobalt (Co3+) plays an important role in mitigating the issue. In case of low-cobalt containing layered materials, cation mixing can take place both at the time of material synthesis and during the electrochemical charge–discharge process. The high temperature (700–850 °C) and long (10–12 h) lithiation process during the synthesis of CAM cause thermal diffusion of the transition metals, leading to increasing occupancy of the Ni2+/3+ at the Li+-sites. On the other hand, during the charging process the Li+ ions are completely de-intercalated from the layered structure and the Ni2+/3+ ions get the chance to occupy the Li+ sites and resist Li+ re-intercalation during the discharge process. The thermal diffusion of cations during lithiation can be partially prevented by optimizing the calcination temperature and time. The mixing-related issue can be significantly mitigated by doping of suitable cations, such as non-transition metal cations (such as Na+, K+, Mg2+, Al3+, Si4+, etc.) or transition metal cations (such as Nb5+, V5+, Fe3+, W6+, Mo6+, Zr4+, Ti4+, etc.), in the Ni-rich NCM-moiety.5
2.4.2 Side reactions and irreversible phase change.
The thermal or potential-induced migration of Ni2+/3+ may cause the irreversible phase change of the Ni-rich layered oxide to a spinel and rock salt structure. This phase transition is primarily promoted by the escape of lattice oxygen in a highly delithiated state. The chance of electrolyte oxidation also increases at this point. On the other hand, a NiO-based rock salt phase may also form during the incomplete oxidation of Ni2+ during the lithiation process of precursors. This phenomenon severely affects Li+ diffusion and deteriorates the charge storage performance. Ni-rich cathodes also suffer from various parasitic side reactions during high temperature applications. The Ni-rich materials become more reactive towards the LiPF6-based electrolyte and Al-current collector, which may finally lead to thermal runaway of the cell. As previously mentioned, the cation migration and related issues can be effectively mitigated by cation doping. The issue of incomplete oxidation of Ni2+ during lithiation can be avoided by maintaining a continuous oxygen flow during synthesis. Surface coating and synthesis of a core–shell or concentration gradient structure with a Ni-rich core and Mn-rich shell are efficient strategies to stop the side reactions between the electrode and electrolyte.5
2.4.3 Formation of microcracks.
Microcrack formation is one of the primary issues for the Ni-rich NCM cathodes, which adversely affects the cycling performance of the battery. The key reason behind this is the severe volume change of the NCM crystal moiety during the consecutive charge–discharge processes due to Li+ deintercalation/intercalation. Besides this, H2 to H3 phase transition, lattice oxygen escape, etc. also facilitate the microcrack formation. Once a microcrack forms on the surface of the primary particles, it starts to propagate towards the core. The issue is more aggravated due to the high reactivity of the surface Ni4+ with the electrolyte in the high voltage charged state. The propagation of microcracks can be effectively mitigated by coating the surface with various functional materials, including metal oxides, conducting polymers, Li-containing compounds, phosphides and fluorides, which simultaneously protects the electrode from direct contact with the electrolyte and facilitates Li+ diffusion by offering the Li-transport path. Core–shell and concentration gradient structures are also effective. Synthesis of single crystal NCMs can effectively reduce the number of grain boundaries in each of the secondary particles and prevent the electrolyte from penetrating inside the core, thus improving the structural robustness.5
2.5 Comparison of commercialized cathodes used in the EV industry
Cathodes with high energy density, low cost, and high thermal as well as cycling stability are critically needed for a sustainable EV industry. Although the NCM111 performs well in many aspects, the high cobalt content and low energy density limit its widespread application as an EV battery. Hence, various Ni-rich cathodes are developed. Besides the NCM based cathodes, LIBs based on LCO, LMO, NCA and LFP cathodes are also utilized by various EV manufacturers. Qualitative comparison between NCM (Fig. 2a) and other commercialized cathode materials (Fig. 2b) is made based on six critical parameters: cost, energy density, cycling stability, safety, specific capacity and rate capability. Names of manufactures and corresponding EV models are also shown with their preferred cathode materials.
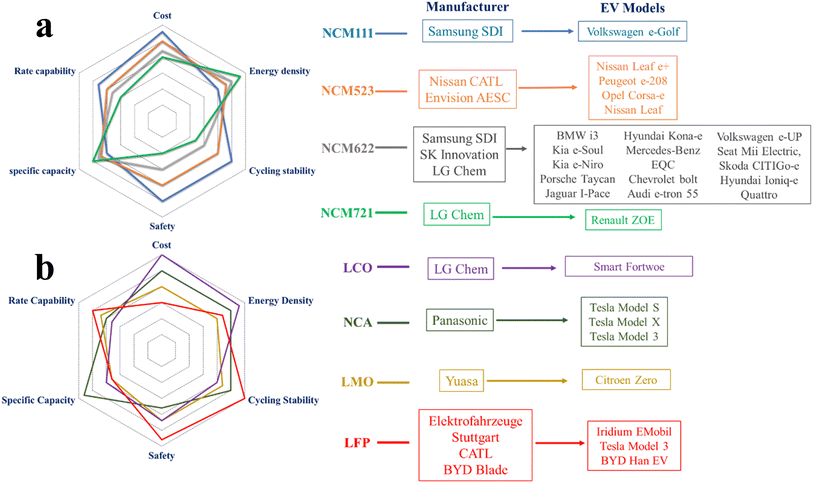 |
| Fig. 2 Comparison between the commercialized (a) NCM-based cathodes and (b) other cathodes used for EV production. The qualitative radar plots are made based on ref. 27 and 28. The list of manufacturers and EV models is included in the figure based on ref. 28. | |
3. Continuous production of cathodes
Continuous production of LIB cathodes with high purity and particle uniformity can help improve the economic and environmental sustainability of the battery industry. Various synthesis methods, including co-precipitation, solid-state synthesis, spray pyrolysis, sol–gel method, hydrothermal method, etc., are developed to produce high quality cathode precursor materials.5 However, except co-precipitation and solid-state process, most of them are limited to lab-scale production due to their complexity, expensive feedstock and poor reproducibility. Solid-state synthesis also has some intrinsic drawbacks, such as low homogeneity, impurity and high energy consumption. Hence, among all the synthesis methods, the co-precipitation method is used for the industrial scale production of cathode precursors due to its virtues of cost-effectiveness, controllable size, morphology and composition and scalability. The stirred tank reactor (STR) based batch process is an early manufacturing platform for the co-precipitation synthesis of NCM based cathode precursors.35 Although the process is easy to handle and good for low-scale production, the batch-to-batch variation of the products limits the reproducibility. Besides this, agglomeration and breakage of particles, inhomogeneity of reaction conditions and formation of dead zones at different parts of the reaction vessels are the bottlenecks for the tank-based reactors.5 Hence, serious efforts to develop a continuous manufacturing platform for battery cathode precursors are highly needed. Fig. 3 shows a few of the continuous manufacturing platforms developed so far.
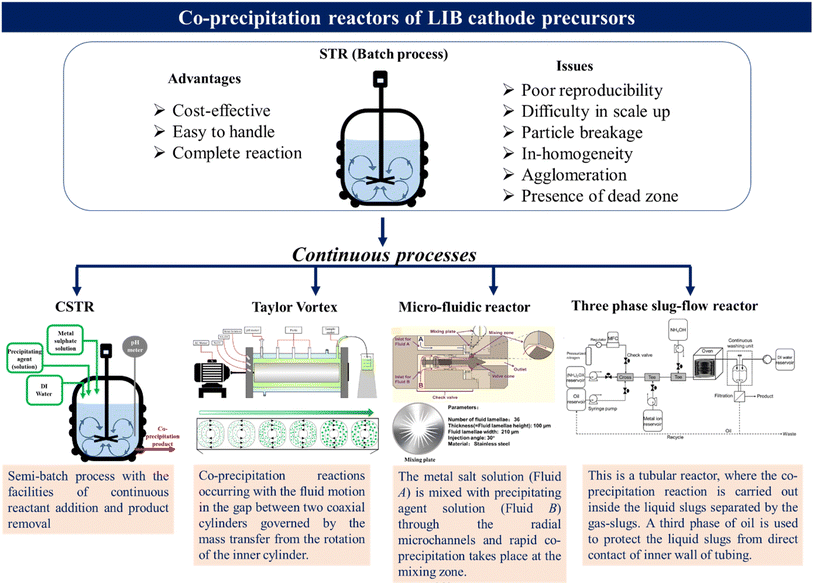 |
| Fig. 3 Various reactors used for synthesizing LIB-cathode precursors using co-precipitation methods [Taylor vortex: reproduced from ref. 40 with permission from Elsevier, copyright 2020; micro-fluidic: reproduced from ref. 42 with permission from Elsevier, copyright 2023]. | |
3.1 Continuous stirred-tank reactor (CSTR)
The CSTR is an extension of batch reactors with the facilities for continuous input of reactants and output of products in a controlled fashion. This is a commercially used process for bulk scale production of various LIB cathode precursors.35–37 Together with factors like pH, NH4OH and metal-ion concentration, and temperature, which are common for tank-based reactors, some additional factors like feeding rate of reactants, removal rate of products, stirring rate, and shape of the impeller, and baffle also play a crucial role in determining the product quality. The co-precipitation synthesis of NCM-precursors in CSTR can be divided into nucleation, dissolution, growth and maturation.35 Ideally, to achieve a steady state in the CSTR, the reactant concentrations and temperature should be uniform throughout the reactor. Although the temperature and concentration variations are less for the CSTR compared to the batch reactor, it is not completely free from all of those limitations, causing some inhomogeneity in particle size and morphology.
3.2 Taylor vortex reactor
This is a continuous flow reactor based on the working principal of the Taylor–Couette mechanism.38,39 Taylor vortex flow is generated in the small gap between the two concentric cylinders when the inner cylinder is rotated and the outer cylinder remains stationary. Tremendous eddy current generated by the counter-rotating toroidal vortices ensures high mass and heat transfer, intense micro-mixing zones, homogeneity in particle size, and fast reaction kinetics.38 Within the last few years, the Taylor vortex reactor is successfully utilized as a continuous manufacturing platform for the co-precipitation synthesis of Ni-rich NCM-based LIB cathode precursors.40,41 In this case, the reactor is first filled with water and then all the reagents, including metal salt solution, NH4OH and NaOH solutions, are injected into the reactor through the front port. The hydrodynamic condition of the reactor can be varied by two ways: (a) controlling the inner-cylinder rotation speed, and (b) the flow rates of the injected solutions. The co-precipitation product is continuously drained out from the outlet port in a round bottom flask (filled with DI water) to cease the reaction. The vigorousness of the toroidal vortices and the dimensions of the cylinders are the crucial parameters that determine the fluid motion as well as the quality of the co-precipitation product.
3.3 Micro-fluidic reactor
This reactor is composed of two syringe pumps used to feed metal-salt solution (A) and precipitating agent solution (B), which pump solutions into the valve simultaneously through inlets A and B, respectively. First, solution B forms an annular flow along the mixing zone around the valve cone. Then solution A is pumped through inlet A, which mixes with solution B through the radially distributed microchannels at the mixing zone to form the co-precipitation product, which is collected continuously through the outlet. An inert atmosphere is maintained by continuous N2 flow and a constant temperature is maintained inside the reactor. The involvement of the microchannel platform enhances the mixing efficiency, facilitates the mass and heat transfer kinetics, and ensures the formation of cathode precursors with controlled size. The dimensions of the fluid lamellae on the mixing plate, such as height, width, number and the injection angle, play important roles in determining the product quality. This reactor has been tested for producing both poly- and single-crystalline Ni-rich NCMs.42,43
3.4 Slug-flow reactor
The slug-flow based continuous manufacturing platform has been explored to produce pharmaceutical organic and inorganic materials.44,45 Our group has implemented the slug-flow based continuous flow reactor in cathode material manufacturing.46 The working principal of the reactor is based on microliter sized slug formation by the immiscible liquids and gas alternatively inside the tube, where each of the slugs work as a micro-reactor with very good internal mixing. It is observed that to synthesize the NCM-based inorganic cathode precursors, the three-phase slug-flow (composed of mineral oil, aqueous solutions of reactants and N2-gas) outperforms the two-phase slug flow (composed of aqueous solutions of reactants and N2-gas) in terms of mixing efficiency and lower clogging. Here, the oil phase protects the aqueous slugs from direct contact with the inner tube wall. Proper injection ensures the complete mixing of metal salts with chelating and precipitating agents inside the aqueous slugs. The advantages of this continuous manufacturing platform include (a) the possibility of the sequential addition of reagents, (b) controllable chemical and flow parameters during the course of reaction, (c) uniform reaction condition, (d) better mass and heat transfer, and (e) tunable production rate based on the feed rates. We observed that the slug-flow derived NCM precursors show a narrower particle size distribution with higher tapped density compared to batch-derived products.47 Our group successfully produced Ni-rich NCM precursors of various compositions using the continuous slug-flow reactor.48–50
The above mentioned continuous reactors function based on the co-precipitation chemistry and are to date demonstrated only for the synthesis of various compositions of NCM-precursors. In all the cases the final lithiated oxide materials are synthesized through high temperature calcination of the precursor in the presence of lithium salt. These reactors are obviously applicable for the production of other types of low cobalt/cobalt-free cathode materials/precursors that involves co-precipitation chemistry. However, solvothermal/hydrothermal, solid-state and sol–gel methods are generally used for the synthesis of LiMn2O4-based spinel cathode materials. On the other hand, the industrial production of LFP can be classified into two major categories, such as solid phase and liquid phase syntheses. High temperature calcination, carbothermal reduction, microwave synthesis and mechanical alloying are widely explored as the solid-phase synthesis of LFP. The liquid phase synthesis involves the co-precipitation, solvothermal and sol–gel methods.
4. Cathode recycling: to achieve economic/environmental sustainability and recovery of cobalt
The increasing growth of the EV industry requires cost-effective production of low cobalt/Ni-rich LIB cathode materials, which requires an increasing supply of the various cathode components, such as lithium and transition metals. This huge demand can be partially fulfilled by rational recovery of the spent battery cathodes and judicious recycling of those for new cell production. The cobalt recovered from the spent cells can be utilized to produce low-cobalt cathode materials and this will significantly decrease the cobalt mining related issues and expenses. Recycling of spent batteries is considered as the domestic source of cobalt. Recently, Apple Inc. set a goal to use 100% recycled cobalt in all of its batteries by 2025.51 The US government also announced investments in the field of cathode recycling through the Department of Energy. Hence, development of green and efficient cathode recycling technology is highly recommended. There are three types of major cathode recycling techniques: (i) pyrometallurgical, (ii) hydrometallurgical, and (iii) direct recycling.
4.1 Pyrometallurgical process
High heating is the main driver in the pyrometallurgical process where a temperature of ∼1500 °C is used to recover the critical metals from the spent batteries.52 The spent LIBs are treated at elevated temperature in a smelting furnace in which organic solvents, carbon additives and polymers are all burned to supply energy to the recycling process. The process involves three major steps: (a) roasting in air to produce metal oxides and gases, (b) smelting to reduce the metal oxides to metals with the removal of oxygen as CO2, and (c) refining to separate metals based on their chemical and metallurgical properties. The metal elements are recycled in the form of metals or alloys. With the help of carbon reductant, metal species like Ni, Co, and Cu are reduced to alloys, while Li, Al, Si, Ca, and Fe stay in the slag.53,54 This method in combination with the hydrometallurgical treatment is adopted by Umicore, Sony, Onto, Accurec.55 Disadvantages of the process include the inability to recover Li effectively, failure to recycle the electrolyte, emissions, high energy consumption, and limited applicability, which make this process difficult to deploy widely.
4.2 Hydrometallurgical process
The pretreated cathode material is leached as constituent metal-ions in solution and reused to synthesize the cathode precursors. This is an efficient recycling process and widely utilized in the industry due its good recovery efficiency, low complexity, high technology readiness, and moderate energy consumption.56,57 Leaching is the key step in the hydrometallurgical regeneration method and ineffective leaching may cause poor recovery. The leaching can further be categorized based on the leaching agent used: (a) organic acid, (b) inorganic acid, (c) ammonia-based, and (d) bioleaching. It is worth mentioning that a comprehensive knowledge about the leaching process is helpful in selecting the appropriate leaching agent for a given cathode.58 It is important to understand the dependency of leaching rate and leaching efficiency on the reaction conditions and material composition for effective recycling of cathode materials. The leached metals are recovered from the solution either by precipitation or by the solvent extraction process.59 However, use of very strong acid and alkaline solution leads to large volumes of hazardous wastes with potential environmental impacts.
4.3 Direct recycling
Among the available options, direct recycling is the most eco-friendly and cost-effective process with a high future prospect.60 Here the battery active materials are separated through physical means such as gravity separation and flotation without any chemical treatment. Next, a stoichiometric amount of lithium is added to the material and subjected to thermal or solvothermal treatment for regeneration of the cathode material in original composition. Limitations such as contamination, Li-deficiency, and transition metal dissolution are few of the technological concerns of the direct recycling process.61 However, the major advantage of this method is that the spent cathode regains its initial electrochemical performance without being deconstructed into elemental components. The following methods have been tested for direct recycling:
• Solid-state: the spent cathode material is mixed with excess Li salt and subjected to a high temperature sintering process.
• Eutectic mixture: the spent cathode material is mixed with an eutectic solution containing a certain ratio of mixed Li salts, which allows sintering at a lower temperature, even at <120 °C.
• Electrochemical: the spent cathode material is relithiated electrochemically using Li2SO4 electrolyte and Ag/AgCl reference electrode.
• Solvothermal: the spent cathode material is treated with specific Li-containing liquid reagents solvothermally followed by sintering.
Fig. 4a shows various recycling methods for LIB-cathode materials. Before proceeding to the main recycling step, the spent LIBs are discharged, and dismantled and the black mass of the cathode material is delaminated from the Al-foil current collector. All of the three recycling processes have their intrinsic pros and cons. The radar plot shown in Fig. 4b compares the three recycling processes in terms of six parameters, including cost, energy consumption, waste generation, technology readiness, complexity and cathode material recovery efficiency.62 Although the hydrometallurgical process is the most widely used recycling technology in commercial scale, the direct recycling is superior in terms of low energy consumption, low waste generation and complete cathode recovery. An advanced and cost-effective technology is required to be developed to utilize the direct recycling on a bulk scale.
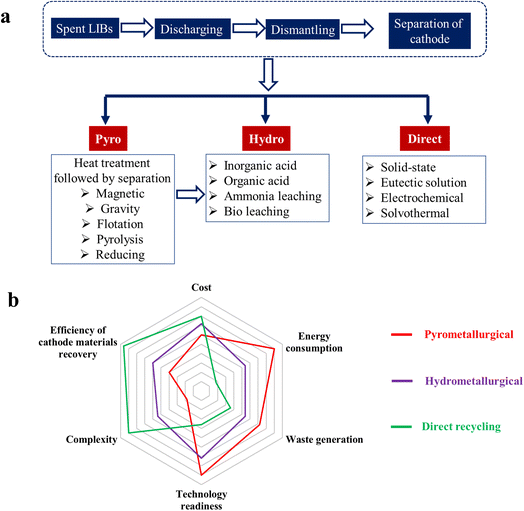 |
| Fig. 4 (a) Classification and (b) comparison of the three major cathode recycling strategies, including pyrometallurgical, hydrometallurgical and direct recycling. The qualitative plot is constructed based on ref. 62. | |
5. Fast-charging LIBs: a rational mean to achieve sustainable e-mobility
The main goals for fast-charging LIBs for EVs proposed by United States Advanced Battery Consortium (USABC) are fast charge rate of 80% useable energy in 15 min (4C rate) with a power target of 275 W h kg−1; 550 W h l−1 at the cell level and a battery life of 10 years and a cost of $75 per kW h−1 in a temperature range of −40 to +66 °C.63 The current battery architecture of graphite anodes and standard cathodes including low-cobalt or cobalt-free materials described earlier in baseline liquid electrolytes cannot achieve fast charging without compromising the electrochemical performance and safety. Hence, new modifications and changes are needed to achieve the fast charging targets. More understanding of the degradation mechanism of the electrode materials and various anode/electrolyte and cathode/electrolyte interfaces at the cell level is necessary.
5.1 Strategies to improve the performance of fast-charging LIBs
5.1.1 Cathode modification.
Although the traditional low-cobalt/cobalt free cathodes, such as NCM532, NCM811, LMO, LFP, etc., can be utilized for fast-charging applications, most of them suffer from structural pulverization or poor electronic conductivity.64 Nano-structuring with suitable surface modification of cathode materials with carbon and metal oxides can improve the stability of cathode electrolyte interphases (CEI) by facilitating the charge transfer at the particle surface needed for fast charging.64 Studying the correlation of ion solvation with CEI properties and design of electrolytes with wider electrochemical voltage windows are needed. Advanced tooling is needed to visualize the lattice structure and chemical valency, and study the rapid transport mechanism during charge–discharge cycles.65 Recently, photo-assisted charging leads to fast charging.64 For example, direct exposure of LMO cathodes during cycling leads to the improvement of charge rates by a factor of two or more.65 This is mainly due to the presence of enhanced charge states of Mn4+ and electrons by microseconds during charging. Inorganic lithium compounds with high lithium-ion conductivity have been successfully utilized in fast-charging LIBs as electrolytes, active filters, coating materials and interface governing layers.66
5.1.2 Anodes and electrolytes for fast-charging LIBs.
The challenges with graphite anodes are electrode polarization, mechanical cracking of electrodes, and side reaction with the electrolyte by lithium plating at the interface during fast charging. These are mainly due to poor kinetics and low operating potential close to that of Li/Li+.67 The electrical conductivity and lithium diffusion coefficients of modified graphite and carbon composite anodes, intercalation transition metal oxides (Ti-based and Nb-based oxides), conversion transition metal oxides (α-Fe2O3 and Co3O4), transition metal dichalcogenides (TMDs), silicon and germanium alloyed anodes, and phosphorus-based anodes are plotted in Fig. 5.67 Even though significant progress has been made with fast-charging anodes, there are still challenges in improving the fast kinetics and ionic and electronic conductivities through electrode architecture design, and electrolyte additives and coatings. The critical value of ionic and electronic conductivity identified for fast-charging LIBs is about 5 × 10−5 S cm−1.68 Anything less than that is not recommended for fast charging. Several materials such as carbon materials (modified graphite, graphene, carbon nanotubes and other carbon-types),69 titanium oxides (TiO2 (ref. 70) and TiNb2O7 (ref. 71)), and rock salt anodes72 have been identified as potential fast-charging anodes.
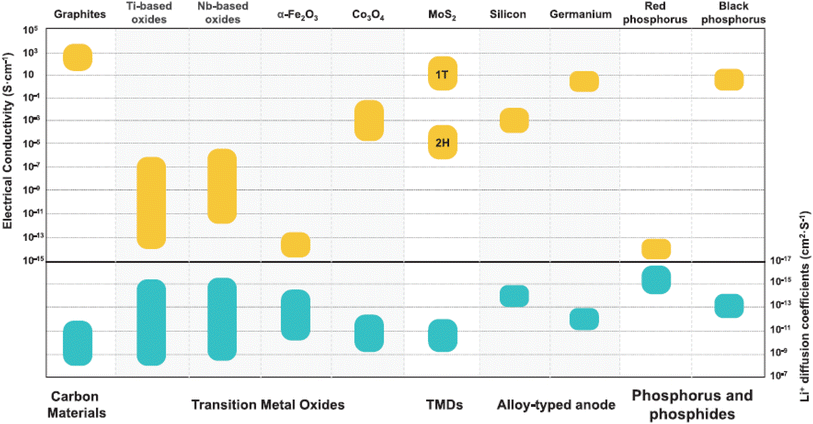 |
| Fig. 5 Plot of electrical conductivity and lithium diffusion coefficients of selected fast-charging anode materials (carbon, intercalation transition metal oxides (Ti-based and Nb-based oxides), conversion transition metal oxides (α-Fe2O3 and Co3O4), transition metal dichalcogenides (TMDs), silicon and germanium alloyed anodes, and phosphorus-based anodes) reported in the literature67 (reproduced from ref. 67 with permission from Wiley, copyright 2022). | |
Recently, fast-charging LIBs have been reported by combining asymmetric temperature modulation with thermally stable dual-salt electrolytes and achieved an energy density of 265 W h kg−1 to 75% charge in 12 min for 900 cycles.73 The thermal management strategy has been reported to cool batteries during charging and preheat batteries in cold weather.74 A novel fluorinated ester-based electrolyte with improved cycling stability at wider temperatures (−50 to −60 °C) and with 5C charge rates with graphite and NMC811 battery have been reported.75 Recently, improved reductive stability of superconcentrated acetonitrile solution (>4 M) has been demonstrated to produce reversible lithium intercalation into a graphite electrode.76 Various lithium compounds such as Li6.4La3Zr1.4Ta0.6O12, Li1.5Al0.5Ge1.5(PO4)3, and Li1.3Al0.3Ti1.7(PO4)3 are widely utilized as electrolytes in fast-charging LIBs.66
5.1.3 SEI modification and improvement of Li-ion diffusion.
The electrolyte plays a major role in transporting lithium ions faster through the concentration graded electrolytes during charging. Electrolyte additives can improve the lithium-ion conductivity. For example, addition of 20 wt% methyl acetate can increase the ionic conductivity by 50% compared to the baseline electrolytes for NCM532 cathodes/graphite cells, which can improve the charge rate to 2C.77 In general, short chain esters can provide electrolyte stability with reduced solid-electrolyte interphase (SEI) formation. In addition, reducing the Li+- diffusion distances in the active materials through novel electrode designs, reducing lithium plating through novel charging rates, and incorporating sensors and thermal management at the cell/module levels are needed to achieve the fast charging targets.77 The control of particle morphology in layered cathodes can lead to microstructures with optimum porosity and low diffusive tortuosity towards improved ionic and electronic conductivities.78 The overpotential to charge transfer lithium across the electrode–electrolyte interface depends on the reaction pathway of active electrode materials, where electrolyte additives play a major role.78 Another strategy to shorten the lithium-ion diffusion distance is to reduce the particle size of the active materials, which can lead to the elimination of lithium plating and improve the lithium intercalation kinetics.79 Alternatively, replacing the standard graphite anodes with lithium titanate (e.g., Li4Ti5O12, TiO2, and TiNb2O7) can eliminate the formation of SEI layers and hence provide more stability with fast charging. However, these electrode materials will compromise the high voltage and energy density that are achieved with standard electrode architectures. Also, suitable binders with high zeta potentials are needed to enable the electro-kinetics of the electrodes.79 Separators can also reduce the lithium transport rate across the pore space. To increase the transport rate, few modifications such as UV/electron beam curing and atomic layer deposition of suitable polymer/oxide coatings are practised.79 An asymmetric temperature modulation strategy has been utilized where the charging of the batteries is carried out at 60 °C for a short duration of 10 min for each cycle followed by discharging at room temperature.80 This method improved the kinetics and transport while reducing the SEI formation. This demonstration led to a high energy density of 209 W h kg−1 with retaining 91.7% capacity after 2500 cycles, far exceeding the USABC goal.80
Several types of microgrid facilities have been proposed for charging EVs, which include the following: isolated and grid connected; bus types: AC, DC, and hybrid; sources: renewable and non-renewable; and usage: residential and commercial.81 To conclude, several new electrode formulations, electrolyte additives, coatings and thermal management strategies have been reported for meeting the goal of fast charging rates soon.
6. Economic and environmental impacts of cathode chemistry
The cathode chemistry has a direct impact on the battery cost and life cycle emission of EV. The utilization of low-cobalt or cobalt-free cathodes is found to have significantly increased worldwide during the last few years. Fig. 6a describes the region-based variation of the share of EV battery capacity during the past three years (2021–2023).82 According to this, there is a rapid increase of LFP-based batteries for EV production, which is primarily contributed by China. On the other hand, Europe and the USA mostly rely on Ni-rich cathodes (low-cobalt) due to their high energy performance. However, a decreasing trend in Ni-rich cathodes and an increasing trend in LFP-based battery production are noticed in the USA during the last three years. The trend of transfer of battery chemistry from high cobalt to low cobalt-based Ni-rich cathodes significantly affects the cost of individual elements as well as the overall battery pack (Fig. 6b).83–85 Noticeably, the cost of cobalt steadily increased from 2015 to 2018 when it reached its highest value, due to the increasing gap between the supply and demand of cobalt sulfate, mostly in the production of LCO and NCM111-based cathodes. After that, due to the application of Ni-rich cathodes (i.e., low cobalt) in EV battery production, the price of cobalt salt started to decrease slowly, but the nickel price reached a high value in 2023. As lithium carbonate is the most common lithiating agent irrespective of the cathode material, an ∼8 fold increase in LiCO3 price is observed from 2015 to 2023. In the case of overall cell price, it is observed that the price dropped to almost half in 2020 compared to its initial value in 2015. Although the shift of battery chemistry towards low cobalt is the primary driving force for lowering the cell price, other improvements related to cell manufacturing, including anode capacity, cycle life, improved cathode production technology, electrolyte and separator manufacturing, also played a role here. Now, the high demand of lithium-based salt has triggered the shift of the battery industry towards the Na-ion battery. In order to maintain a circular economy and resolve the high demand of critical metals, efficient strategies and policies are critically required for the end-of-life management of the EV batteries. Hence, a significant expansion of the battery recycling industry is observed during the last few years. Presently, the global battery recycling capacity is >300 GW h, which will reach >1500 GW h by 2030 if all the announced projects materialize (Fig. 6c).82 Although the battery recycling capacity is increasing worldwide, China is holding the top position with ∼70% contribution. Noteworthily, the battery chemistry has a crucial impact on the battery recycling landscape. The NMC-based cathodes are richer in valuable minerals compared to LFP and hence more profitable in terms of residual value. In terms of environmental impact, it is observed that the lifecycle emission per kW h of NCM-based cathodes (mostly NCM811) is ∼3 times higher compared to the LFP cathode. In the case of NCM-based LIBs the critical metal processing is responsible for <50% of the total emission, whereas the battery manufacturing process primarily accounts for 50% of the emission of the LFP-based battery (Fig. 6d).82 The lifecycle emission of the NCM-based batteries can be effectively reduced by increasing the efficiency of critical metal processing, active material production, and battery manufacturing in terms of energy and time. Recycling of spent batteries has the potential to decrease the emission. It is predicted that there will be a 35% decrease in the lifecycle emission within the next 10 years, which will be an integrated outcome of electrodes with a high energy density, decarbonization of power grids, advanced manufacturing techniques, and recycling.
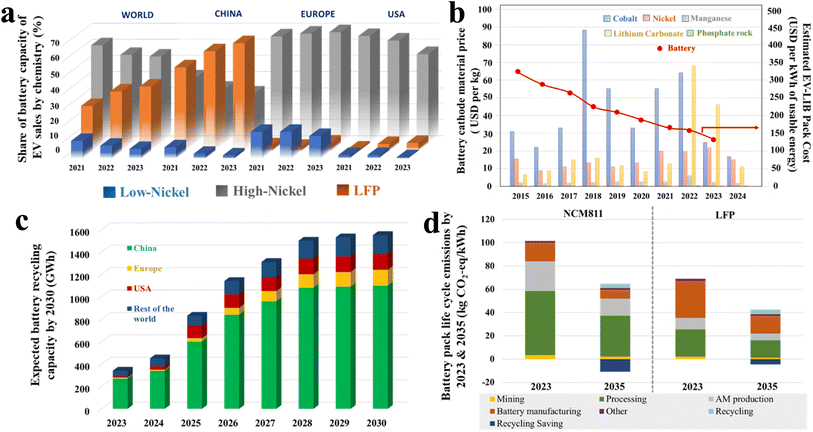 |
| Fig. 6 Plots illustrating (a) the last three years' share of battery capacity of EV sales by chemistry (%); (b) ten-year trend in cathode material and LIB pack cost; (c) expected growth of the recycling market by 2030; and (d) life cycle CO2 emission of NCM811 and LFP [ref. 82 is used to draw (a, c and d). Ref. 83–85 are used to draw profile (b)]. | |
7. Summary and future scope
Various critical aspects of LIB research together with the effect of cathode chemistry on the cost and environment are discussed here. Undoubtedly, decreasing/eliminating the cobalt-content in the active cathode material is the most essential step to achieve sustainability in the LIB-industry. Among the various low cobalt cathodes Ni-rich NCMs, more precisely NCM-622, are widely utilized by many of the EV manufacturers. Attempts to further decrease the Co-content in the NCM moiety are also in progress and excellent progress has been made in the production of NCM-811 during the last three years. However, keeping the crucial role of cobalt in preventing the cation mixing and cracking related issues in mind, suitable modification techniques are required to be developed. Cation/anion doping, functional coating, synthesis of single crystal, core–shell and gradient structured materials are some promising modification strategies to improve the chemical and structural robustness of low cobalt materials, which are already discussed in detail in our previously published review article.5 However, most of the modification techniques are effective in laboratory scale production and the reproducibility is poor in pilot scale manufacturing. Moreover, the effect of modification techniques on the stability and electrochemical performance of the low-cobalt cathode materials is required to be studied at both surface and bulk levels using various advanced in situ characterization techniques. Besides this, a significant performance improvement is required for cobalt-free alternative cathodes. Although LFP is emerging as a high prospect material for long cycling stability and fast charging, the low specific capacity is one of the primary limitations for this material. Significant scientific and industrial efforts are required to make a trade-off between the production and raw material cost and the electrochemical performance determining parameters, including the specific capacity, rate capability, and cycling performance.
There is a high prospect for developing continuous manufacturing platforms for the LIB cathode materials. Due to the cost-effectiveness, scalability, and good control over particle size and morphology, the co-precipitation chemistry is widely adopted for both the batch and continuous production of cathode precursors. Development of suitable equilibrium models to predict the interdependence between reactant concentrations and pH and product yield is useful in controlling reactions and improving product quality.22 The development of continuous production platforms is needed in the following three directions: (i) proper optimization of the flow as well as chemical parameters, including kinetic and thermodynamic aspects, is crucial to obtain good quality products. Collaborative efforts of engineers and chemical scientists are essential to improve the product quality and yield and reduce the manufacturing cost of the existing reactors. Artificial intelligence-controlled modelling of flow dynamics will be helpful in predicting and optimizing the co-precipitation condition inside the continuous reactor. (ii) Development of new continuous manufacturing platforms for cathode precursor particles based on co-precipitation or other reaction chemistries. (iii) The existing co-precipitation-based continuous manufacturing platforms are limited to cathode precursor production only. The final lithiated NCM oxide materials are produced by high temperature calcination under oxygen flow, which is not a continuous process. Hence, the final product quality and total yield can vary. Single-step manufacturing platforms for the continuous production of NCM and other lithiated TMO-based cathode materials can improve the product quality and reproducibility of the material performance.
One of the paramount requirements to improve the economic and social sustainability in the battery industry is to upgrade the existing recycling technology and to develop efficient alternative recycling routes for spent LIB cathodes. Among various emerging recycling processes, the hydrometallurgical recovery process has good efficiency, component recovery, and technology readiness. However, the energy and chemical costs are too high due to the full deconstruction of NCM to metal ions followed by separation and reconstruction of similar cathode materials. In most of these cases the goal is to reproduce the material with a composition and crystal structure similar to those of the parent material. Hence, there is no improvement in the electrochemical performance of the recycled materials compared to original ones. Significant scientific and technological efforts are needed to make hydrometallurgical recycling technology more cost-effective and environmentally benign by developing alternative less acidic leaching solutions and continuous reactors with enhanced metal recovery efficiency. The precipitation and solvent extraction processes for the recovery of transition metals from the spent cathode also require significant improvement. A promising way to make the recycling more sustainable is by applying the direct recycling process on the industrial scale, where the recycling is done without destroying the original crystal structure of the cathode material. However, in order to achieve commercial success, the direct recycling methods are required to be less complex and suitable technologies for large scale application are required. Deep eutectic solution (DES)-based direct recycling is promising, as it plays a dual role of both the reducing and leaching agent and thus offers an environment friendly green recycling process free of hazardous acids and strong reducing agents, like H2O2.86 Proper formulation of DES composition based on the cathode material and optimization of the reaction condition are the crucial part of its success.87
The fast-charging LIBs can increase EV adoption and ensure environmental sustainability by reducing carbon footprint with satisfactory mobility. An improvement in fast-charging LIB technology can be achieved by judiciously resolving the issues at the cell level (including cathode, anode and electrolyte), internal heat management, fast-charging techniques, and fast-charging infrastructure. The material level advancement requires more attention to understand the degradation mechanism of the standard cathodes in the fast-charging condition. In terms of cathode materials, the abrupt and fast volume change during charge/discharge processes leads to microcrack formation and deteriorates the battery performance. Hence, materials which undergo a lower extent of volume change during Li+ intercalation/de-intercalation are suitable for fast-charging LIBs. Although LFP is widely utilized as the fast-charging cathode, poor ionic and electronic conductivity is hampering its commercial success.88 Rational modification of the LFP and searching for suitable alternatives are needed. In the case of anodes, specifically for graphite, the increasing rate of Li-plating with increasing the C rate significantly affects the battery performance. Rational selection of anode materials and formulation of electrolytes is the only way to achieve lower Li+-intercalation overpotential, which is critical to reduce the Li-plating.10 Thermal management is another key aspect to mitigate Li-plating related issues during fast charging. It is observed that the demand for the optimal temperature of the battery increases with the increase of charging rate and proper management of the temperature is required to keep the battery components unaffected.89 Upgradation of publicly accessible fast charging infrastructure, in terms of number of charging stations and quality of DC fast charging facilities, is also necessary to achieve sustainable e-mobility.
This perspective article focused on few of the critical aspects of current LIB cathode research, which have high industrial significance. Specifically, they are playing an important role as an active or passive driver of cell manufacturing cost, supply-chain stability, and environmental benignity and thus interlinked with the overall sustainability of the LIB cathode research (Fig. 7).
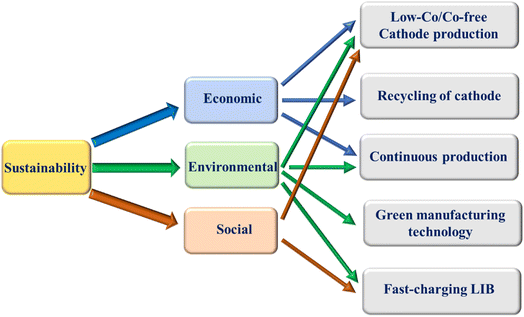 |
| Fig. 7 Inter-relations among the various critical aspects of the LIB cathode and sustainability. | |
Data availability
No primary research results, software or code has been included and no new data were generated or analyzed as part of this perspective article. The plots are constructed based on the publicly available data, and the corresponding references and links are included in the reference list.
Author contributions
S. M. collected the literature, prepared the schematics and wrote the original draft of the manuscript. A. P. contributed to write the “Cathode Recycling” section and reviewing. M. P. P wrote the “Fast-charging LIBs” section and review the manuscript. J. M. and S. K. contributed to review the manuscript. M. J. developed the “slug-flow manufacturing”. M. L. R. contributed to the mathematical modelling part of the co-precipitation synthesis. H. L. helped with the experimental design of scaling up process. R. B. G. and M. J. conceived the idea and supervised the project. All of the authors approved the final version of the manuscript.
Conflicts of interest
The authors declare no conflict of interest.
Acknowledgements
This material is based upon work supported by Virginia Commonwealth University, National Science Foundation under Grant No. CMMI-1940948 and government support under contract number DE-EE0009110 awarded by the Advanced Materials and Manufacturing Technologies Office (AMMTO) of the Office of Energy Efficiency and Renewable Energy (EERE) under the US department of energy. This manuscript has been authored by UT-Battelle, LLC under Contract No. DEAC05-00OR22725 with the U.S. Department of Energy. The United States Government retains and the publisher, by accepting the article for publication, acknowledges that the United States Government retains a non-exclusive, paid-up, irrevocable, worldwide license to publish or reproduce the published form of this manuscript, or allow others to do so, for United States Government purposes. The Department of Energy will provide public access to these results of federally sponsored research in accordance with the DOE Public Access Plan (https://www.energy.gov/doe-public-access-plan).
References
-
https://www.iea.org/reports/global-ev-outlook-2023/trends-in-batteries
.
-
Statista, Projected size of the global lithium-ion battery market from 2020 to 2026 (in billion U.S. dollars), June 23, 2021 Search PubMed.
-
P. A. Nelson, S. Ahmed, K. G. Gallagher and D. W. Dees, Modeling the Performance and Cost of Lithium-Ion Batteries for Electric-Drive Vehicles, United States, 3rd edn, 2019 Search PubMed.
-
S. Kara, Cobalt Red: How the Blood of the Congo Powers Our Lives, 2023 Search PubMed.
- S. Mallick, A. Patel, X.-G. Sun, M. P. Paranthaman, M. Mou, J. H. Mugumya, M. Jiang, M. L. Rasche, H. Lopezc and R. B. Gupta, J. Mater. Chem. A, 2023, 11, 3789–3821 RSC.
- L. Rogers and K. F. Jensen, Green Chem., 2019, 21, 3481–3498 RSC.
- M. Jacoby, Chem. Eng. News, 2019, 97(28), 29–32 Search PubMed.
-
L. Yukun, EV Battery Recycling a Growing Niche, China Daily, Updated: 2023-06-01 09:07 Search PubMed.
-
https://www.mckinsey.com/industries/automotive-and-assembly/our-insights/battery-2030-resilient-sustainable-and-circular#/
.
- J. He, J. Meng and Y. Huang, J. Power Sources, 2023, 570, 232965 CrossRef.
- M. S. Whittingham, Science, 1976, 192, 1126 CrossRef.
- A. Manthiram, Nat. Commun., 2020, 11, 1550 CrossRef PubMed.
- K. Mizushima, P. C. Jones, P. J. Wiseman and J. B. Goodenough, Mater. Res. Bull., 1980, 15, 783–789 CrossRef.
- R. Kanno, H. Kubo, Y. Kawamoto, T. Kamiyama, F. Izumi, Y. Takeda and M. Takano, J. Solid State Chem., 1994, 110, 216–225 CrossRef.
- A. Rougier, P. Gravereau and C. Delmas, J. Electrochem. Soc., 1996, 143(4), 1168–1175 CrossRef.
- G. Vitins and K. West, J. Electrochem. Soc., 1997, 144, 2587–2592 CrossRef.
- P. He, H. Yu, D. Li and H. Zhou, J. Mater. Chem., 2012, 22, 3680–3695 RSC.
- P. Rozier and J. M. Tarascon, J. Electrochem. Soc., 2015, 162(14), A2490–A2499 CrossRef.
- G. X. Wang, J. Horvat, D. H. Bradhurst, H. K. Liu and S. X. Dou, J. Power Sources, 2000, 85, 279–283 CrossRef.
- T. Ohzuku and Y. Makimura, Chem. Lett., 2001, 30, 642 CrossRef.
- A. C. Wagner, N. Bohn, H. Geßwein, M. Neumann, M. Osenberg, A. Hilger, I. Manke, V. Schmidt and J. R. Binder, ACS Appl. Energy Mater., 2020, 3(12), 12565–12574 CrossRef CAS.
- J. H. Mugumya, M. L. Rasche, R. F. Rafferty, A. Patel, S. Mallick, M. Mou, J. A. Bobb, R. B. Gupta and M. Jiang, Energy Fuels, 2022, 36, 12261–12270 CrossRef CAS.
- V. Pimenta, M. Sathiya, D. Batuk, A. M. Abakumov, D. Giaume, S. Cassaignon, D. Larcher and J. M. Tarascon, Chem. Mater., 2017, 29, 9923–9936 CrossRef CAS.
- H. Yu and H. Zhou, J. Phys. Chem. Lett., 2013, 4(8), 1268–1280 CrossRef CAS.
- W. He, W. Guo, H. Wu, L. Lin, Q. Liu, X. Han, Q. Xie, P. Liu, H. Zheng, L. Wang, X. Yu and D. L. Peng, Adv. Mater., 2021, 33, 2005937 CrossRef CAS.
- D. Mohanty, J. Li, D. P. Abraham, A. Huq, E. A. Payzant, D. L. Wood and C. Daniel, Chem. Mater., 2014, 26(21), 6272–6280 CrossRef CAS.
- C. A. Heck, M.-W. v. Horstig, F. Huttner, J. K. Mayer, W. Haselrieder and A. Kwade, J. Electrochem. Soc., 2020, 167, 160521 CrossRef CAS.
- R. M. Salgado, F. Danzi, J. E. Oliveira, A. E. Azab, P. P. Camanho and M. H. Braga, Molecules, 2021, 26, 3188 CrossRef PubMed.
- W. David, M. Thackeray, L. De Picciotto and J. B. Goodenough, J. Solid State Chem., 1987, 67(2), 316–323 CrossRef.
- Z. I. Radzi, K. H. Arifin, M. Z. Kufian, V. Balakrishnan, S. R. S. Raihan, N. A. Rahim and R. Subramaniam, J. Electroanal. Chem., 2022, 920, 116623 CrossRef.
- L. X. Yuan, Z. H. Wang, W. X. Zhang, X. L. Hu, J. T. Chen, Y. H. Huang and J. B. Goodenough, Energy Environ. Sci., 2011, 4, 269–284 RSC.
- A. K. Padhi, K. S. Nanjundaswamy and J. B. Goodenough, J. Electrochem. Soc., 1997, 144, 1188 CrossRef.
- J. Hu, W. Huang, L. Yang and F. Pan, Nanoscale, 2020, 12, 15036–15044 RSC.
- S. Y. Chung, J. T. Bloking and Y. M. Chiang, Nat. Mater., 2002, 1, 123–128 CrossRef PubMed.
- W. Liang, Y. Zhao, L. Shi, Z. Wang, Y. Wang, M. Zhang and S. Yuan, Particuology, 2024, 86, 67–85 CrossRef.
- Q. Zhu, H. Xiao, R. Zhang, S. Geng and Q. Huang, Electrochim. Acta, 2019, 318, 1–13 CrossRef.
- H. Dong and G. M. Koenig Jr, CrystEngComm, 2020, 22, 1514–1530 RSC.
-
G. Krumdick, International Battery Seminar, https://cii-resource.com/cet/FBC-05-04/Presentations/BAT/Krumdick_Greg.pdf, 2017, accessed on December 7, 2023.
- D. K. Thai, Q.-P. Mayra and W.-S. Kim, Powder Technol., 2015, 274, 5–13 CrossRef.
- M. Seenivasan, C.-C. Yang, S.-h. Wu, W.-C. Chien, Y.-S. Wu, R. Jose and S. J. Lue, J. Alloys Compd., 2021, 857, 15759 CrossRef.
- S. Lee, H. W. Park, J. P. Hong, S.-C. Nam, D. H. Jeon and J. H. Song, Solid State Ionics, 2022, 386, 116042 CrossRef.
- W. Liang, F. Jin, Y. Zhao, L. Shi, Q. Liu, Z. Wang, Y. Wang, M. Zhang, J. Zhu and S. Yuan, Chem. Eng. J., 2023, 464, 142656 CrossRef.
- H. Liang, S. Yuan, L. Shi, Y. Zhao, Z. Wang and J. Zhu, Chem. Eng. J., 2020, 394, 124846 CrossRef.
- M. Jiang, Z. Zhu, E. Jimenez, C. D. Papageorgiou, J. Waetzig, A. Hardy, M. Langston and R. D. Braatz, Cryst. Growth Des., 2014, 14, 851–860 CrossRef.
- M. Abolhasani, C. W. Coley, L. Xie, O. Chen, M. G. Bawendi and K. F. Jensen, Chem. Mater., 2015, 27, 6131–6138 CrossRef.
-
M. Jiang and R. B. Gupta, Slug-Flow manufacturing of uniform and controllable microparticles for battery cathodes, US pat., US20220410112A1, 2022, https://patents.google.com/patent/US20220410112A1/en Search PubMed.
- J. H. Mugumya, S. Mallick, A. Patel, M. L Rasche, A. V. Sakpal, E. D. Huchler, S. Kim, R. B. Gupta and M. Jiang, J. Alloys Compd., 2024, 994, 174720 CrossRef.
- M. Mou, A. Patel, S. Mallick, J. Mugumya, M. L. Rasche, M. Parans Paranthaman, H. Lopez, G. P. Pandey, R. B. Gupta and M. Jiang, ACS Omega, 2022, 7(46), 42408–42417 CrossRef PubMed.
- M. Mou, A. Patel, S. Mallick, K. Jayanthi, X.-G. Sun, M. P. Paranthaman, S. Kothe, E. Baral, S. Saleh, J. H. Mugumya, Mi. L. Rasche, R. B. Gupta, H. Lopez and M. Jiang, ACS Appl. Energy Mater., 2023, 6(6), 3213–3224 CrossRef PubMed.
- A. Patel, S. Mallick, J. H. Mugumya, N. L. Riveira, S. Kim, M. Jiang, M. P. Paranthaman, M. L. Rasche, H. Lopez and R. B. Gupta, Mater. Today Energy, 2024, 41, 101545 CrossRef.
-
https://www.batterytechonline.com/battery-recycling/apple-will-use-100-recycled-cobalt-in-batteries-by-2025
.
- M. Assefi, S. Maroufi, Y. Yamauchi and V. Sahajwalla, Curr. Opin. Green Sustainable Chem., 2020, 24, 26–31 CrossRef.
- W. Wang, Y. Han, T. Zhang, L. Zhang and S. Xu, ACS Sustain. Chem. Eng., 2019, 7, 16729–16737 CrossRef.
- S. Maroufi, M. Assefi, R. K. Nekouei and V. Sahajwalla, Sustainable Mater. Technol., 2020, 23, e00139 CrossRef.
- P. Meshram, B. D. Pandey and T. R. Mankhand, Waste Manag., 2015, 45, 306–313 CrossRef PubMed.
- J. C.-Y. Jung, P.-C. Sui and J. Zhang, J. Energy Storage, 2021, 35, 102217 CrossRef.
- B. Huang, Z. Pan, X. Su and L. An, J. Power Sources, 2018, 399, 274–286 CrossRef.
- J. Tan, Q. Wang, S. Chena, Z. Li, J. Sun, W. Liu, W. Yang, X. Xiang, X. Sun and X. Duan, Energy Storage Mater., 2021, 41, 380–394 CrossRef.
- Y. Wang, N. An, L. Wen, L. Wang, X. Jiang, F. Hou, Y. Yin and J. Liang, J. Energy Chem., 2021, 55, 391–419 CrossRef.
- P. Xu, D. H. S. Tan, B. Jiao, H. Gao, X. Yu and Z. Chen, Adv. Funct. Mater., 2023, 33, 2213168 CrossRef.
- G. Wei, Y. Liu, B. Jiao, N. Chang, M. Wu, G. Liu, X. Lin, X. F. Weng, J. Chen, L. Zhang, C. Zhu, G. Wang, P. Xu, J. Di and Q. Li, iScience, 2023, 26, 107676 CrossRef PubMed.
- G. Harper, R. Sommerville, E. Kendrick, L. Driscoll, P. Slater, R. Stolkin, A. Walton, P. Christensen, O. Heidrich, S. Lambert, A. Abbott, K. Ryder, L. Gaines and P. Anderson, Nature, 2019, 575, 75–86 CrossRef PubMed.
-
https://uscar.org/wp-admin/admin-ajax.php?juwpfisadmin=false&action=wpfd&task=file.download&wpfd_category_id=246&wpfd_file_id=12840&token=&preview=1
.
- M. Yuan, H. Liu and F. Ran, Mater. Today, 2023, 63, 360–379 CrossRef.
- A. Lee, M. Vörös, W. M. Dose, J. Niklas, O. Poluektov, R. D. Schalle, H. Iddir, V. A. Maroni, E. Lee, B. Ingram, A. Curtis and C. S. Johnson, Nat. Commun., 2019, 10, 4946 CrossRef PubMed.
- N. Xue, C. Zhang and W. Liu, J. Solid State Electrochem., 2024 DOI:10.1007/s10008-024-05833-6.
- S. Li, K. Wang, G. Zhang, S. Li, Y. Xu, X. Zhang, X. Zhang, S. Zheng, X. Sun and Y. Ma, Adv. Funct. Mater., 2022, 32, 2200796 CrossRef.
- G.-L. Zhu, C.-Z. Zhao, J.-Q. Huang, C. He, J. Zhang, S. Chen, L. Xu, H. Yuan and Q. Zhang, Small, 2019, 15, 1805389 CrossRef PubMed.
- L. Li, D. Zhang, J. Deng, Y. Gou, J. Fang, H. Cui, Y. Zhao and M. Cao, Carbon, 2021, 183, 721–734 CrossRef.
- H. Liu, Z. Bi, X.-G. Sun, R. R. Unocic, M. P. Paranthaman, S. Dai and G. M. Brown, Adv. Mater., 2011, 23, 3450–3454 CrossRef.
- S. Gong, Y. Wang, M. Li, Y. Wen, B. Xu, H. Wang, J. Qiu and B. Li, Materials, 2023, 26, 333 Search PubMed.
- H. Li, Z. Zhu, Q. Yan, S. Yu, X. He, Y. Chen, R. Zhang, L. Ma, T. Liu, M. Li, R. Lin, Y. Chen, Y. Li, X. Xing, Y. Choi, L. Gao, H. S. Cho, K. An, J. Feng, R. Kostecki, K. Amine, T. Wu, J. Lu, H. L. Xin, S. P. Ong and P. Liu, Nature, 2020, 585, 63 CrossRef.
- C.-Y. Wang, T. Liu, X.-G. Yang, S. Ge, N. V. Stanley, E. S. Rountree, Y. Leng and B. D. McCarthy, Nature, 2022, 611, 485 CrossRef.
- A. Tomaszewska, Z. Chu, X. Feng, S. O'Kane, X. Liu, J. Chen, C. Ji, E. Endler, R. Li, L. Liu, Y. Li, S. Zheng, S. Vetterlein, M. Gao, J. Du, M. Parkes, M. Ouyang, M. Marinesc, G. Offer and B. Wu, eTransportation, 2019, 1, 1000011 CrossRef.
- Y. Zou, Z. Ma, G. Liu, Q. Li, D. Yin, X. Shi, Z. Cao, Z. Tian, H. Kim, Y. Guo, C. Sun, L. Cavallo, L. Wang, H. N. Alshareef, Y.-K. Sun and J. Ming, Angew. Chem., Int. Ed., 2023, 62, e202216189 CrossRef.
- Y. Yamada, K. Furukawa, K. Sodeyama, K. Kikuchi, M. Yaegashi, Y. Tateyama and A. Yamada, J. Am. Chem. Soc., 2014, 136, 5039–5046 CrossRef.
- Y. Liu, Y. Zhu and Y. Cui, Nat. Energy, 2019, 4, 540–550 CrossRef.
- M. Weiss, R. Ruess, J. Kasnatscheew, Y. Levartovsky, N. R. Levy, P. Minnmann, L. Stolz, T. Waldmann, M. Wohlfahrt-Mehrens, D. Aurbach, M. Winter, Y. Ein-Eli and J. Janek, Adv. Energy Mater., 2021, 11, 2101126 CrossRef.
- G. Li, Adv. Energy Mater., 2021, 11, 2002891 CrossRef.
- X. G. Yang, T. Liu, Y. Gao, S. Ge, Y. Leng, D. Wang and C.-Y. Wang, Joule, 2019, 3, 3002–3019 CrossRef.
- D. S. Abraham, R. Verma, L. Kanagaraj, S. Raman, N. Rajamanickam, B. Chokkalingam, K. Sekar and L. Mihet-Pop, Electronics, 2021, 10, 1895 CrossRef.
-
https://www.iea.org/reports/global-ev-outlook-2024, visited on 07/02/24.
- N. Muralidharan, E. C. Self, M. Dixit, Z. Du, R. Essehli, R. Amin, J. Nanda and I. Belharouak, Adv. Energy Mater., 2022, 12, 2103050 CrossRef.
-
Lithium carbonate price 2023 | Statista (visited on 07/02/24)
.
-
Phosphate rock price forecast 2015-2024 | Statista (visited on 07/02/24)
.
- A. Zhu, X. Bian, W. Han, D. Cao, Y. Wen, K. Zhu and S. Wang, Resour., Conserv. Recycl., 2023, 188, 106690 CrossRef.
- C. Padwal, H. D. Pham, S. Jadhav, T. T. Do, J. Nerkar, L. T. M. Hoang, A. Kumar Nanjundan, S. G. Mundree and D. P. Dubal, Adv. Energy Sustainability Res., 2022, 3, 2100133 CrossRef.
- J. Wang and X. Sun, Energy Environ. Sci., 2015, 8, 1110 RSC.
- M. Weiss, R. Ruess, J. Kasnatscheew, Y. Levartovsky, N. R. Levy, P. Minnmann, L. Stolz, T. Waldmann, M. W. Mehrens, D. Aurbach, M. Winter, Y. E. Eli and J. Janek, Adv. Energy Mater., 2021, 11, 2101126 Search PubMed.
|
This journal is © The Royal Society of Chemistry 2025 |
Click here to see how this site uses Cookies. View our privacy policy here.