DOI:
10.1039/D5SM00297D
(Perspective)
Soft Matter, 2025, Advance Article
Materials science underpinnings of micro and nanoplastics
Received
20th March 2025
, Accepted 23rd June 2025
First published on 26th June 2025
Abstract
There is considerable interest in microplastics and nanoplastics (MNPL) due to their ubiquity and their potential for serious health consequences. A framework that allows us to consider all relevant aspects of MNPL requires us to enunciate (a) their formation mechanisms, their sizes, shapes, and chemical functionalities (upstream properties); and (b) their health and environmental consequences (downstream properties). In this perspective, we discuss the materials science underpinnings of MNPL formation, and the current open questions that need immediate attention from the research community. Specifically, we highlight the lack of understanding of how angstrom-level environmentally triggered bond-breaking events lead to the formation of ∼10 nm–1 mm-sized fragments. Are there universal theoretical ideas that unify MNPL formation in disparate situations? What is the role of external stressors, polymer morphology, and molecular weight? Answering these questions requires us to develop a suite of novel metrologies – from accurate, accelerated aging tests that mimic natural MNPL creation processes but speed up these rare events into the normal laboratory time scales; to the extension of standard physicochemical characterization tools which are hard to apply in the context of MNPL formation due to small sample masses.
1. Introduction
Plastics and synthetic polymers are a ubiquitous part of modern human society with a global production approaching 500 Mt year−1. Despite their usefulness, plastics have unintended negative consequences, such as the creation of plastic waste.1,2 While primary microplastics – i.e., engineered particulate plastics a few mm in size or smaller, often employed in cosmetic products in the past – have been widely banned,3 this perspective focuses on secondary microplastics that form due to plastic degradation. There is increasing awareness4 that plastics, in use and at their end of life, generate secondary microplastics (sizes between 1 μm and 1 mm)5 and nanoplastics (sizes <1 μm)6 [MNPL].6,7 The presence of MNPL in the environment (air, water, and land) has now been well-established,8,9 and analytical methods are currently being developed to characterize some features of these pollutants, such as size, shape, and physico-chemical properties.10,11
Similarly, the potential health consequences of MNPL have become evident, although this research is still in its nascent stage.9,12–14 Given the ubiquity of plastics in our daily lives, the fact that these materials can release micrometer and smaller-sized objects with the potential to accumulate in human and animal bodies15,16 is alarming. Notably, MNPL have been found in the human heart,17 brain,18 blood,19 liver,20 placenta,21,22 breast milk,23 kidneys,24 and testicles25 where they are expected to have significant health effects.15,16,26–31 While evidence suggests that the toxicity of MNPL is related to their physical characteristics32 (size, shape, surface chemistry), we also note that they can act as carriers of other harmful substances such as additives (stabilizers, antioxidants, plasticizers) and heavy metals which can leach into humans/animals with deleterious health consequences.33
1.1. Formation mechanisms
Although the “downstream” effects of MNPL (i.e., their environmental prevalence and their health consequences) are a subject of intense research, the “upstream” side (i.e., the processes by which they are created) is significantly less explored. It is well-accepted that MNPL creation must be triggered by bond-breaking events (i.e., polymer chain scission) caused by wave and/or wind action, exposure to air, water34,35, and/or light (specifically UV radiation),12,36 mechanical wear, among other factors. However, a thorough understanding of how such angstrom-scale events lead to the formation of these much larger-sized pollutants remains an open question for the materials science community. This is the key topic of this perspective. A comprehensive understanding of MNPL formation must address how the underpinning fragmentation physics depends on:
(a) Morphology, i.e., the physical “state” of the polymer determined by molecular and microscale structure (e.g., semicrystalline, amorphous glassy, crosslinked rubbers, or filled polymers; orientation and residual stress) as well as its macroscopic form and fabrication protocols (packaging films, molded objects, fibers; use of additive stabilizer packages).
(b) Forcing fields, i.e., (i) mechanical stresses generated by either external flow fields, abrasion, or solvent swelling, and (ii) chemical reactions induced by polymer–environment interaction (including UV irradiation, oxidation, hydrolysis, enzymatic action).
1.2. Metrologies
An intimately related question is how one can monitor and quantify MNPL formation. Recognizing that real-life MNPL formation, especially under quiescent conditions, can be a rare event motivates us to develop accelerated aging tests that faithfully mimic the environmental creation of these materials. In addition to speeding up these processes, such accelerated tests also allow us to create sufficient amounts of MNPLs that can be characterized by available in situ and ex situ experimental probes. Looking ahead, there is a pressing need to develop experimental methods that determine MNPL size and shape distributions, but more importantly the accumulation of chemical and structural changes that accompany both the local degradation processes and the associated release of the MNPL under environmental conditions where their concentrations are low, at the edge of detection by conventional probes.
This perspective begins with a detailed discussion of formation mechanisms, especially focusing on the postulated roles of morphology and external drivers. We then have a brief consideration of metrologies, followed by a final section focused on the open questions that we believe need to be immediately addressed by the research community to understand and mitigate MNPL pollution.
2. Formation of micro and nanoplastics
2.1. Definitions
It is important that we define what we mean by micro and nanoplastics. These are loosely defined in the literature as objects in the size ranges discussed above. To provide more context, we first recognize that MNPLs are formed by the degradation of polymeric materials and hence they must have the chain-like molecular structure of the starting, parent material. Further, each possesses its own size and shape, although samples of secondary micro and nanoplastics invariably assume rather polydisperse size distributions. A degrading polymeric material could yield oligomeric fragments, which are commonly accepted to have liquid-like behavior. Additionally, they sometimes result in objects comprised of longer chains, with entanglements, crystals, or crosslinks holding the sample together. These objects are usually thought to be solid-like. While both types of degradation products warrant interest due to their potential toxicity, their persistence as clearly defined objects depends strongly on the environmental conditions that they encounter. For example, a droplet of oligomers could coalesce with other droplets or could dissolve in the surrounding medium at low concentrations.
To rigorously distinguish between these two types of degradation products (i.e., liquid vs. solid-like), we adapt a definition of a transient solid proposed by Rubinstein and Semenov in the context of reversibly associating polymers.37 These workers define two relevant time scales: first, is the lifetime of a network that is formed by the reversible association of polymers into a percolating structure. Second, is the relaxation time of this percolating cluster. The material is considered to be solid-like in its mechanical response when its relaxation time is larger than its lifetime (i.e., the time it persists in the environment).
By analogy, we propose a refined definition of a micro/nanoplastic as a finite-sized object in the nm to mm range whose relaxation time is longer than its lifetime in the environment.
Thus, a semicrystalline fragment has a relaxation time that is typically much longer than its lifetime. Fragments comprised only of oligomeric species, which have shorter relaxation times than their lifetimes, are considered to be liquids. These liquid-like fragments represent pollutants whose environmental fate is incompletely understood.38 It is possible that such liquid-like species, especially when they arise from oxidative degradation, might be metabolized by microbes – they could also lead to compounds with potential carcinogenecity.39,40 Thus, while liquid-like oligomeric fragments have their own interesting behavior, below we focus on solid-like objects that we shall exclusively term MNPLs.
2.2. MNPL formation mechanisms
Fig. 1 top panel shows an overview of the formation pathways of MNPL from bulk plastics. However, we do not know when the underpinning bond-breaking events lead only to the formation of oligomers and smaller fragments versus when they additionally form MNPL. What are the relevant time scales for these processes?
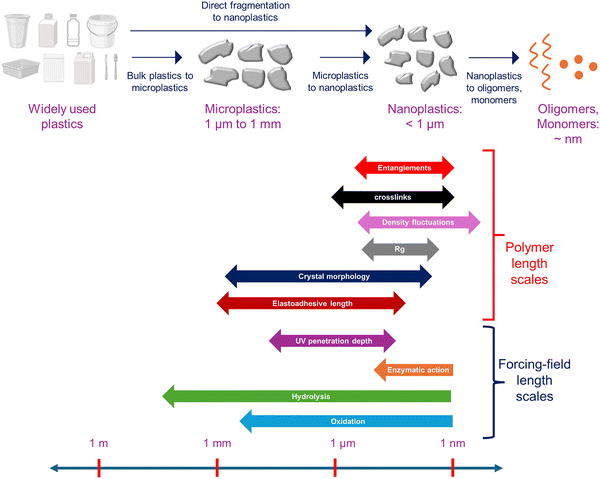 |
| Fig. 1 Micro- and nanoplastics (MNPL) generation from bulk plastics and the relevant length scales. The top panel shows an overview of MNPL generation pathways from bulk plastics, including bulk plastics to microplastics, microplastics to nanoplastics, bulk plastics to nanoplastics, and nanoplastics to oligomers and monomers. The bottom panel shows the relevant length scales which underpin the formation and persistence of MNPL including forcing field length scales such as hydrolysis, oxidation, enzymatic action, UV irradiation, and polymer-based length scales such as crystal morphology, elastoadhesive length, chain radius of gyration (Rg), crosslink density, entanglement length, size of density fluctuations etc. | |
Although there has been some research into the processes responsible for MNPL generation via fragmentation,41 a unifying framework elucidating the role of different forcing fields (e.g., mechanical forces, chemical reactions, photooxidation among others) and polymer morphology (e.g., semicrystalline, amorphous, crosslinked) is not established. While research is needed to delineate a comprehensive picture, ideas borrowed from materials science and polymer physics qualitatively anticipate the size and shape distributions of MNPL fragments formed under the control of these different variables.
There are two key concepts in this context: the length scales that describe the material microstructure, including the chain radius of gyration, Rg, entanglement length, and crystal/amorphous sizes, and those that describe the forcing fields, including reaction-induced changes in the elastoadhesive length.42 These length scales provide approximate bounds for the maximum size of the fragments generated. Clearly, their impact on the MNPL properties is determined by comparison of their magnitude with the object's linear dimension (L).
2.2.1. Role of forcing fields. Forcing fields can be applied to samples either under quiescent conditions or when an external (mechanical) force is applied to the polymer. Since the physics in these situations are likely different, we discuss MNPL under these two conditions separately.
2.2.1.1. Quiescent degradation. Under quiescent conditions, MNPL formation occurs when the failure stress of the material becomes negligibly small. These poor mechanical properties arise due to successive bond-breaking events. Such bond-breaking can be driven by a variety of factors, e.g., by hydrolysis, oxidation, enzymatic action, and UV irradiation. In photooxidation, one natural length scale is the absorption length λBL of the UV radiation, which limits the depth at which oxidative damage can occur. Similarly, in chemical degradation (e.g., oxidation or hydrolysis), the reaction–diffusion length
(where D is the reactant's diffusivity and K a characteristic reaction rate) determines the linear size of the degraded region. Previous work has used such ideas to decide if degradation is a surface effect or occurs throughout the bulk of the polymer.43 Such concepts are also likely relevant to MNPL creation, especially deciding if it is a surface phenomenon or a bulk one, and to the sizes of the resulting fragments – however these ideas have not been tested to date in this field.Provided that the fragmentation driving force acts homogeneously on a material and is scale-invariant, theoretical arguments by Kolgomorov44 and more recent authors demonstrate that the fragment sizes should tend towards a log-normal distribution at intermediate times and a power law distribution at long times for one-dimensional processes. This concept was recently demonstrated in the formation of chemically etched cellulose nanocrystals.45 However, the hypothesis of scale invariance must inevitably break down at small enough scales where either the external forces are unable to cause bond breaking or material inhomogeneities become apparent.
2.2.1.2. MNPL formation under external stresses. Next we discuss the role of stresses. When the externally imposed stress is (locally) larger than the failure stress of the material, a crack can nucleate and eventually cause the formation of a fragment. Ideas inspired by Eyring46 and Zhukov47 allow us to develop connections between macroscopically imposed stresses and bond scission events. For example, the activation energy associated with bond breaking can be lowered by an imposed stress (scaled with an appropriate molecular volume) in an anisotropic manner. Such an approach has recently been employed in the context of chain failure in elastomers48 and polymer melts.49 We propose that these ideas should be extended to MNPL formation.Since fragmentation ultimately entails localized failure of a material, a particularly important class of polymer length scales are those obtained by appropriately combining continuum-level material constants relevant to fracture mechanics. In general, the propensity of a material to fragment arises from the competition of elastic and adhesive forces. This principle is central to Griffith's theory of linear elastic fracture50 and is implemented in tribological models of abrasion such as Rabinowicz's criterion for fragment release in adhesive wear. One example of such a material-specific length scale is the elastoadhesive length λEA = Gc/E,42 i.e., the ratio of the critical strain energy release rate needed to propagate a crack during fracture (Gc, with dimensions of surface energy) and Young's modulus (E, with dimensions of energy density). This quantity characterizes the linear size of the deformed region ahead of a crack tip and is known for several polymeric materials (ranging from microns to millimeters). Note that Gc in polymers depends on the velocity of crack propagation and on the fracture mode, implying that the characteristic size of the fragments is expected to vary depending on the mechanical process involved (e.g., collisional impact or abrasion). Further, other quantities with dimension of energy density (such as the yield stress σY) can be used instead of E to obtain additional length scales.
Thus, in stress-driven fragmentation of bulk plastics, MNPLs with a characteristic size are generated for a given applied stress. Recent work51,52 suggests that the length scales obtained with this prescription are strongly correlated with the mean size of MNPL released by polymers under diverse mechanical actions. Other work,53–55 primarily using sonication or blending, suggests that the mean particle size decreases monotonically with increasing power input. Thus, for large power, NPLs of size 100 nm can be found. Also, the number of particles produced is large (typically between 1011 and 1013 particles liter−1), with this quantity increasing with increasing power input into the system. While it has been postulated that this is a direct manifestation of fracture mechanics, this picture is not found to capture the size variations with input power, even to the level of predicting the right power law scaling for this relationship. Thus, new ideas need to be developed to understand the physics in these situations.
2.2.1.3. Wear. In addition to such fracture-related ideas, another relevant concept is one of wear. Rubber tires wear during use and in these cases, they generate MNPL.56 That tire wear can create fragments that get washed into water streams in a well-accepted concept, but the newer findings are that they also create airborne MNPL that are charge stabilized. While concepts such as Archard's law,57 which determines the amount of rubber worn by the applied stress, and Griffith's ideas of fracture50 all appear to be relevant in these cases, the underpinning physics is not clear. Additionally, there are no control studies that look first purely at unfilled rubbers and then at the role of added filler.Biomedical polymer implants such as radiation-crosslinked ultrahigh molecular weight polyethylene hip implants experience high stresses and cyclic loading during their use life. Their wear has been extensively studied and rationalized using classical tribological theories.58–61 Biomedical joints wear at their surfaces when they abrade against each other, or when there are particles between abrading surfaces. Tribology suggests that wear is governed by abrasion, adhesion between surfaces, and the nature of loading (for example cyclic loading).62 While there are many wear studies, how these relate to MNPL sizes and shapes that result remain less well-explored at this time.
2.2.2. Role of morphology, molecular weight, and structure. The previous section highlights the fact that fragments generated by polymers can be of very different size if their Gc values are different. This can happen even if other length scales of the fragmentation process match. Since Gc's are very much determined by polymer morphology, we next discuss the role of this variable.Fig. 2 illustrates the three major morphologies, glassy, semicrystalline, and rubbers, and schematically sketches the mechanisms by which bond breaking leads to MNPLs in each of these cases. Glassy amorphous polymers are homogeneous at all scales greater than the typical range of density fluctuations (of the size scale of a Kuhn length, i.e., 1 nm) – thus, since there is no large length scale in the problem, we expect that only oligomeric products are generated early in the fragmentation process. A second scale is one defined by entanglements – glassy, entangled polymers can transmit shear and tensile stresses internally through their entanglement network.63 As degradation or wear proceeds, a decrease in entanglement density should occur due to a decrease in chain length. When the molecular weight drops below about 4–5 times critical entanglement molecular weight Me, the material as a whole should turn brittle and fragment readily under external shear64 leading to polydisperse objects with no characteristic size.
 |
| Fig. 2 Mechanistic pathways of micro- and nanoplastic (MNPL) formation from bulk polymers. (A) (Semi-) Crystalline MNPL are predominantly expected to be formed as a result of tie-chain scission of semicrystalline polymers. (B) Amorphous plastics form micro- and nanoplastics by random scission of polymer chains into smaller fragments. (C) Cross-linked micro- and nanoplastics are formed by the fragmentation of cross-linked polymers such as rubbers and thermosets. | |
Meanwhile, the morphologies of semicrystalline65 or highly crosslinked66 polymers have inherent structural features (e.g. crystalline domains or crosslinks) that might be more resistant to degradation and also have characteristic sizes that may play a critical role in the sizes of the MNPLs formed. In these cases, the enhanced stability of the crystals (as compared to amorphous MNPL) must have a measurable impact on their accumulation in the environment and living organisms. This aspect is particularly relevant since semicrystalline materials comprise ∼70% of all consumer plastics.65 It is well-accepted that chain scission events accumulate in the amorphous phase of a semicrystalline polymer. We have shown that this leads to mechanical failure and the concurrent release of particulate MNPLs comprised of polydisperse stacks of lamellae even under quiescent conditions.65 The precise conditions under which this failure occurs are unclear and remain a topic of continuing interest.
Rubbers represent a distinct morphology that is between amorphous melts and brittle, highly crosslinked networks – the elasticity of these lightly crosslinked materials is expected to affect the fragmentation behavior. With sparse crosslinking, rubbers may not degrade completely to oligomeric molecules, but may instead yield small particles, e.g., via tire wear that is aerosolized or that deposits on roads as discussed above.63
Furthermore, a significant fraction of consumer plastics utilize fillers for property improvements. Some of these fillers may be benign, but others, such as silica, could pose health hazards.67,68 Degradation and fragmentation of these composites may free these fillers into the environment, exposing their hazardous form, compounding potential toxicity from the MNPL and filler.
These broad classes convey some key differences between different polymer morphologies. Nevertheless, there is also a further distinction to be made within each morphology class based on polymer properties and processing conditions used to create a plastic product. These tunable details may alter degradation and fragmentation behavior. For example, different industrial processes applied to the production of semicrystalline thermoplastics can result in spherulitic morphologies (e.g., extrusion, injection molding69) or oriented shish-kebab morphologies (e.g. fiber spinning, blow molding70). Orientation could result in highly anisotropic mechanical and barrier properties, but could also qualitatively change the connectivity of the amorphous and crystalline regions.71 It is not obvious if these stiffer plastics would be more resistant to MNPL formation, or if the change in semicrystalline morphology and the residual stresses due to orientation would render these more susceptible to fragmentation. Alternatively, in polymer composites, the dispersion of fillers is more important for the mechanical reinforcement of the polymer72 and homogenous dispersion versus heterogenous aggregation may play important roles in MNPL formation and persistence. More detailed studies and information on morphological and processing considerations may, in the future, help us to understand what factors play key roles in MNPL formation and toxicity, and may lead to ways to mitigate their release (or potentially accelerate their degradation once released).
Independent of these factors, all polymers possess key features such as molecular weight and architecture (e.g., branching and stereoregularity) that can also influence the properties and stress transmission (i.e., fragmentation behavior) in these materials. Higher molecular weight polymers possess higher entanglement density as entanglement density increases with molecular weight before plateauing73 and, in the case of semicrystalline materials, higher tie chain content (stress transmitters between crystalline lamella).74 Similar effects are seen with branching in linear low-density polyethylene.75,76 An increase in stress transmitters should lead to less MNPL release as the bulk material will be less susceptible to breakdown.
3. Metrology of micro and nanoplastics
The number density of MNPL in nature is small, and hence it is difficult to collect them in sufficient quantities for standard characterization. Thus, if we assume that we have spherical 100 nm MNPL at a concentration of 106 particles liter−1 in water, then 1000 liters of solution would only yield ng of MNPL! This is a very small quantity, and applying standard characterization tools is difficult. Further, environmental samples are invariably contaminated by other substances or populated by microorganisms. Thus, there is a key need to mimic natural processes in a laboratory setting, which can simultaneously address the quantity issue and those arising from contaminants. While the mimics of natural processes are useful to understand the formation and persistence of MNPL in nature, these have the same issues in terms of amounts generated as discussed above. Alternatively, accelerated aging protocols for the generation of MNPL can result in larger quantities needed for studying the persistence and the consequences of MNPL. Below, we address these accelerated aging protocols; we also sketch the characterization tools that have already been developed, with some notes on how they may be improved to handle the typically low concentrations of environmental MNPLs.
3.1. Accelerated aging protocols
Fig. 3 details the different pathways for the generation of MNPL, including their generation in natural environments, lab-based mimics, and accelerated generation of MNPL.56,65 In natural environments, MNPL are produced by processes including hydrolysis, oxidation, UV irradiation, mechanical wear, wave action, and microbial degradation, as discussed above. These processes can be mimicked in the lab using hydrolysis below the glass transition temperature (Tg), chemical oxidation, simulated UV irradiation, low-intensity water shear, low-concentration microbial degradation, and simulated wear and tear, respectively. While natural processes can take years or decades for the MNPL generation, lab mimics can be made significantly faster, yielding realistic MNPL samples in months or weeks. This can be achieved by raising the temperature or increasing the concentration of degrading agents. While these processes are accelerated relative to their natural analogs, they proceed via the same underpinning bond-breaking mechanisms. Thus, we have used accelerated aging protocols on a variety of polymers to generate MNPL and to further study them.65 Going further, in principle, data from these accelerated aging tests can be mapped into real-life natural processes using concepts such as the venerable time-temperature superposition principle. These ideas were used, for example, by Arhant et al.35 whose ideas can be used to show that PET can be expected to generate MNPLs by ester hydrolysis under quiescent, room temperature conditions over time frames of 50–100 years. While such natural time scales are outside the purview of most normal experiments, the use of accelerated aging along with well-established ideas in the polymer community allow us to readily reproduce these rare events in nature and anticipate their rates under natural conditions.
 |
| Fig. 3 MNPL metrology for studying naturally formed MNPL, lab mimics of natural processes and MNPL generated via accelerated processes in the lab. | |
We mention in passing that several recent studies also report methods for MNPL generation through wear under controlled conditions that afford mechanistic insights into the governing mechanisms for particle formation. Our recent work on tire wear77 demonstrated that MNPL formation was governed by the energy input for tire rotation on the road. The tribology community has reported test methods to examine the effect of surface roughness, adhesion, and cyclic loading on MNPL formation.78–83
3.2. Characterization
For a detailed and thorough characterization of the physical, chemical, mechanical, and mobility characteristics and toxicity of MNPLs produced naturally or in lab studies, multiscale characterization tools are needed. In the context of this perspective, we (briefly) focus on MNPL characterization for a range of properties that impact their environmental persistence and stability. Notably, several other reviews cover the characterization of MNPL in detail.8,10,84–87 Among the different physical characteristics of MNPL, molecular weight, crystallinity, crosslink density, size and shape distributions, mechanical properties, and chemical functionalities are expected to play an important role in dictating their stability, persistence, and biological interactions. Notably, MNPL with higher polymer molecular weight, crystallinity, and crosslinking density are expected to be more stable as compared to their counterparts with lower molecular weight, crystallinity, and crosslinking density.
MNPL polymer molecular weight can be measured using gel permeation chromatography (GPC),10 otherwise known as size exclusion chromatography (SEC), and nuclear magnetic resonance (NMR).10 The crystallinity of MNPL, crystallite size, and interlamellar spacing can be quantified using (small and wide angle) X-ray scattering,65 differential scanning calorimetry (DSC),65 and Raman spectroscopy.23 The crosslinking density of MNPL can be measured via time-domain NMR and spectroscopy techniques.10 Optical and electron microscopy, atomic force microscopy (AFM),8 and scattering techniques8 are relevant for the measurement of MNPL size and shape. MNPL mechanical properties, which are expected to be dependent on polymer molecular weight, polymer type, crystallinity, and crosslinking, can be measured using AFM and nanoindentation techniques.88 The chemical functionalities of MNPL can be determined using spectroscopy techniques.10,11
Notably, there are significant challenges associated with MNPL characterization. Most commonly, the low sample volume10 of environmental samples limits the use of many of the above-mentioned techniques, such as GPC, DSC, etc. Such samples might require pre-concentration and the use of sensitive techniques for MNPL characterization. MNPL present in biological tissues, for example, needs to be separated, isolated, and concentrated before analysis.89,90 Furthermore, MNPL contamination with extraneous materials causes additional problems for characterization,84,89 and pre-treatment might be needed to remove contaminants. Commercial plastics usually have additives such as plasticizers, flame retardants, antioxidants, and pigments, and these additives can end up in the MNPL, thus causing further challenges for characterization. Given these challenges, MNPL characterization should be performed with care, with pre-concentration and pre-treatment where needed, such that the effects are impurities and additives can be delineated during characterization.
4. Outlook and open questions
Although a considerable amount has been learned about MNPL over the past few years, a detailed understanding of MNPL generation pathways, their environmental and health consequences, and strategies to mitigate them have yet to be developed. Currently, there are a number of open questions in the field of MNPLs that need immediate attention from the research community. Below, we frame a list of open questions that we deem critical for developing a thorough mapping of the relevant parameter space.
(1) What leads from local bond-breaking events in a polymer at the sub-nanometer scale (that occur due to environmental cues) to the formation of MNPL?
(2) Is fragmentation a unifying concept in determining the formation of micro and nanoplastics?
(3) Does MNPL generation cause the release of additional harmful chemicals, including additives, catalysts, fillers, and other secondary products?
(4) What are the health consequences of MNPL? Do fragments with different morphologies (crystalline vs. amorphous vs. crosslinked) possess different bioactivity?
(5) How long do MNPL persist in the environment and living organisms before undergoing degradation to molecular-level species? Does this process depend on the crystalline vs. amorphous nature of the micro and nanoplastics?
(6) Can MNPL accumulating in human and animal bodies degrade using enzymatic or other degradation routes?
(7) How can this knowledge be translated to the design of better materials that are less prone to the generation of MNPL?
Given that there is growing evidence of the accumulation of MNPL in living organisms and their deleterious health consequences, there is an urgent need to develop strategies for degrading or removing MNPL in living organisms. Alternatively, developing lightweight materials and plastics not prone to the generation of MNPL would be a viable long-term strategy. However, it has been noted that replacing lightweight plastic materials with heavier glass, ceramic, or metal-based products increases greenhouse gas emissions.91
As we learn more about the breakdown of plastics it is clear that we will need multi-faceted approaches to design and create plastic products considering their fate at their ‘end-of-life’. In this developing field of research, it is imperative to look for unifying behaviors across plastics but also to look at where those unifying behaviors break down and the underlying physics that controls these differences.
Conflicts of interest
The authors declare no competing interests.
Data availability
There is no additional data associated with the manuscript.
Acknowledgements
The authors graciously acknowledge funding from NSF award #2301348.
References
- M. MacLeod, H. P. H. Arp, M. B. Tekman and A. Jahnke, The global threat from plastic pollution, Science, 2021, 373(6550), 61–65 CrossRef CAS PubMed.
- L. T. J. Korley, T. H. Epps, B. A. Helms and A. J. Ryan, Toward polymer upcycling—adding value and tackling circularity, Science, 2021, 69, 66–69 CrossRef PubMed.
- D. M. Mitrano and W. Wohlleben, Microplastic regulation should be more precise to incentivize both innovation and environmental safety, Nat. Commun., 2020, 11(1), 1–12, DOI:10.1038/s41467-020-19069-1.
- N. B. Hartmann, T. Hüffer, R. C. Thompson, M. Hassellöv, A. Verschoor and A. E. Daugaard, et al., Are We Speaking the Same Language? Recommendations for a Definition and Categorization Framework for Plastic Debris, Environ. Sci. Technol., 2019, 53(3), 1039–1047 CrossRef CAS PubMed.
- J. P. G. L. Frias and R. Nash, Microplastics: finding a consensus on the definition, Mar. Pollut. Bull., 2019, 138, 145–147 CrossRef CAS PubMed.
- D. M. Mitrano, P. Wick and B. Nowack, Placing nanoplastics in the context of global plastic pollution, Nat. Nanotechnol., 2021, 16(5), 491–500, DOI:10.1038/s41565-021-00888-2.
- J. Gigault, H. El Hadri, B. Nguyen, B. Grassl, L. Rowenczyk and N. Tufenkji, et al., Nanoplastics are neither microplastics nor engineered nanoparticles, Nat. Nanotechnol., 2021, 16(5), 501–507, DOI:10.1038/s41565-021-00886-4.
- W. Fu, J. Min, W. Jiang, Y. Li and W. Zhang, Separation, characterization and identification of microplastics and nanoplastics in the environment, Sci. Total Environ., 2020, 721, 137561, DOI:10.1016/j.scitotenv.2020.137561.
- Microplastics are everywhere—we need to understand how they affect human health, Nat. Med., 2024, 304, 913 Search PubMed.
- N. P. Ivleva, Chemical Analysis of Microplastics and Nanoplastics: Challenges, Advanced Methods, and Perspectives, Chem. Rev., 2021, 121(19), 11886–11936 CrossRef CAS PubMed.
- M. C. Celina, E. Linde and E. Martinez, Carbonyl Identification and Quantification Uncertainties for Oxidative Polymer Degradation, Polym. Degrad. Stab., 2021, 188, 109550 CrossRef CAS.
- B. Gewert, M. M. Plassmann and M. Macleod, Pathways for degradation of plastic polymers floating in the marine environment, Environ. Sci.: Processes Impacts, 2015, 17(9), 1513–1521 RSC.
- J. L. Xu, S. Wright, C. Rauert and K. V. Thomas, Are microplastics bad for your health? More rigorous science is needed, Nature, 2025, 639, 300–302 CrossRef CAS PubMed.
- M. Raffaele, P. Francesco, S. Celestino, F. Gianluca, G. Laura and S. Tatiana, et al., Microplastics and Nanoplastics in Atheromas and Cardiovascular Events, N. Engl. J. Med., 2024, 390(10), 900–910, DOI:10.1056/NEJMoa2309822.
- Y. Li, L. Tao, Q. Wang, F. Wang, G. Li and M. Song, Potential Health Impact of Microplastics: A Review of Environmental Distribution, Human Exposure, and Toxic Effects, Environ. Health, 2023, 1(4), 249–257 CAS.
- J. L. Xu, X. Lin, J. J. Wang and A. A. Gowen, A review of potential human health impacts of micro- and nanoplastics exposure, Sci. Total Environ., 2022, 851, 158111, DOI:10.1016/j.scitotenv.2022.158111.
- R. Marfella, F. Prattichizzo, C. Sardu, G. Fulgenzi, L. Graciotti and T. Spadoni, et al., Microplastics and Nanoplastics in Atheromas and Cardiovascular Events, N. Engl. J. Med., 2024, 390(10), 900–910 CrossRef CAS PubMed.
- A. J. Nihart, M. A. Garcia, E. El Hayek, R. Liu, M. Olewine and J. D. Kingston, et al., Bioaccumulation of microplastics in decedent human brains, Nat. Med., 2025, 31, 1114–1119, DOI:10.1038/s41591-024-03453-1.
- H. A. Leslie, M. J. M. van Velzen, S. H. Brandsma, A. D. Vethaak, J. J. Garcia-Vallejo and M. H. Lamoree, Discovery and quantification of plastic particle pollution in human blood, Environ. Int., 2022, 163, 107199, DOI:10.1016/j.envint.2022.107199.
- T. Horvatits, M. Tamminga, B. Liu, M. Sebode, A. Carambia and L. Fischer, et al., Microplastics detected in cirrhotic liver tissue, EBioMedicine., 2022, 82, 1–10 CrossRef PubMed.
- T. Braun, L. Ehrlich, W. Henrich, S. Koeppel, I. Lomako and P. Schwabl, et al., Detection of microplastic in human placenta and meconium in a clinical setting, Pharmaceutics, 2021, 13(7), 1–12 CrossRef PubMed.
- M. A. Garcia, R. Liu, A. Nihart, E. E. Hayek, E. Castillo and E. R. Barrozo, et al., Quantitation and identification of microplastics accumulation in human placental specimens using pyrolysis gas chromatography mass spectrometry, Toxicol. Sci., 2024, 199(1), 81–88 CrossRef CAS PubMed.
- A. Ragusa, V. Notarstefano, A. Svelato, A. Belloni, G. Gioacchini and C. Blondeel, et al., Raman Microspectroscopy Detection and Characterisation of Microplastics in Human Breastmilk, Polymers, 2022, 14(13), 1–14 CrossRef PubMed.
- S. Massardo, D. Verzola, S. Alberti, C. Caboni, M. Santostefano and E. Eugenio Verrina, et al., MicroRaman spectroscopy detects the presence of microplastics in human urine and kidney tissue, Environ. Int., 2024, 184, 108444, DOI:10.1016/j.envint.2024.108444.
- C. J. Hu, M. A. Garcia, A. Nihart, R. Liu, L. Yin and N. Adolphi, et al., Microplastic presence in dog and human testis and its potential association with sperm count and weights of testis and epididymis, Toxicol. Sci., 2024, 200(2), 235–240 CrossRef CAS PubMed.
- T. Ö. Sökmen, E. Sulukan, M. Türkoğlu, A. Baran, M. Özkaraca and S. B. Ceyhun, Polystyrene nanoplastics (20 nm) are able to bioaccumulate and cause oxidative DNA damages in the brain tissue of zebrafish embryo (Danio rerio), Neurotoxicology, 2020, 77, 51–59 CrossRef PubMed.
- R. Martin-Folgar, M. C. González-Caballero, M. Torres-Ruiz, A. I. Cañas-Portilla, M. de Alba González and I. Liste, et al., Molecular effects of polystyrene nanoplastics on human neural stem cells, PLoS One, 2024, 19, 1–19 CrossRef PubMed.
- C. Q. Y. Yong, S. Valiyaveettil and B. L. Tang, Toxicity of microplastics and nanoplastics in Mammalian systems, Int. J. Environ. Res. Public Health, 2020, 17(5), 1509, DOI:10.3390/ijerph17051509.
- L. Liu, K. Xu, B. Zhang, Y. Ye, Q. Zhang and W. Jiang, Cellular internalization and release of polystyrene microplastics and nanoplastics, Sci. Total Environ., 2021, 779, 146523, DOI:10.1016/j.scitotenv.2021.146523.
- A. Sun and W. X. Wang, Human Exposure to Microplastics and Its Associated Health Risks, Environ. Health, 2023, 1(3), 139–149 CAS.
- A. Khan and Z. Jia, Recent insights into uptake, toxicity, and molecular targets of microplastics and nanoplastics relevant to human health impacts, iScience, 2023, 26(2), 106061, DOI:10.1016/j.isci.2023.106061.
- J. Chen, Z. Xu, Y. Liu, A. X. Mei, X. Wang and Q. Shi, Cellular absorption of polystyrene nanoplastics with different surface functionalization and the toxicity to RAW264.7 macrophage cells, Ecotoxicol. Environ. Saf., 2023, 252, 114574, DOI:10.1016/j.ecoenv.2023.114574.
- L. Trasande, R. Krithivasan, K. Park, V. Obsekov and M. Belliveau, Chemicals Used in Plastic Materials: An Estimate of the Attributable Disease Burden and Costs in the United States, J. Endocr. Soc., 2024, 8(2), 1–9, DOI:10.1210/jendso/bvad163.
- L. N. Woodard and M. A. Grunlan, Hydrolytic Degradation and Erosion of Polyester Biomaterials, ACS Macro Lett., 2018, 7(8), 976–982 CrossRef CAS PubMed.
- M. Arhant, M. L. Gall and P. Y. L. Gac, Fracture test to accelerate the prediction of polymer embrittlement during aging – Case of PET hydrolysis, Polym. Degrad. Stab., 2022, 196, 109848 CrossRef CAS.
- A. A. de Souza Machado, W. Kloas, C. Zarfl, S. Hempel and M. C. Rillig, Microplastics as an emerging threat to terrestrial ecosystems, Global Change Biol., 2018, 24(4), 1405–1416 CrossRef PubMed.
- M. Rubinstein and A. N. Semenov, Thermoreversible Gelation in Solutions of Associating Polymers. 2. Linear Dynamics, Macromolecules, 1998, 31, 1386–1397 CrossRef CAS.
- C. Shi, M. Wang, Z. Wang, G. Qu, W. Jiang and X. Pan, et al., Oligomers from the Synthetic Polymers: Another Potential Iceberg of New Pollutants, Environ. Health, 2023, 1(4), 228–235 CAS.
- K. P. Sullivan, A. Z. Werner, K. J. Ramirez, L. D. Ellis, J. R. Bussard and B. A. Black, et al., Mixed plastics waste valorization through tandem chemical oxidation and biological funneling, Science, 2022, 378(6616), 207–211 CrossRef CAS PubMed.
- Y. Huang, T. Hu, B. Lin, Y. Ke, J. Li and J. Ma, Microplastics-biofilm interactions in biofilm-based wastewater treatment processes: a review, Environ. Pollut., 2024, 361, 124836 CrossRef CAS PubMed.
- H. Nakatani, Y. Ohshima, T. Uchiyama and M. Suguru, Degradation and fragmentation behavior of polypropylene and polystyrene in water, Sci. Rep., 2022, 12(1), 1–7, DOI:10.1038/s41598-022-23435-y.
- C. W. Barney, I. Sacligil, G. N. Tew and A. J. Crosby, Linking cavitation and fracture to molecular scale structural damage of model networks, Soft Matter, 2022, 18(22), 4220–4226 RSC.
- F. von Burkersroda, L. Schedl and A. Göpferich, Why degradable polymers undergo surface erosion or bulk erosion, Biomaterials, 2002, 23(21), 4221–4231 CrossRef CAS PubMed.
- A. N. Kolmogorov, On the log-normal distribution of particles sizes during break-up process, Dokl Akad Nauk, 1941, SSSR XXXI, pp. 99–101 Search PubMed.
- S. Elazzouzi-Hafraoui, Y. Nishiyama, J. L. Putaux, L. Heux, F. Dubreuil and C. Rochas, The shape and size distribution of crystalline nanoparticles prepared by acid hydrolysis of native cellulose, Biomacromolecules, 2008, 9(1), 57–65 CrossRef CAS PubMed.
- W. Kauzman and H. Eyring, The Viscous Flow of Large Molecules, J. Am. Chem. Soc., 1940, 62(11), 3113–3125 CrossRef.
- S. N. Zhurkov and V. E. Korsukov, Atomic mechanism of fracture of solid polymers, J. Polym. Sci., Polym. Phys. Ed., 1974, 12, 385–398 CrossRef CAS.
- S. Q. Wang, Z. Fan, C. Gupta, A. Siavoshani and T. Smith, Fracture Behavior of Polymers in Plastic and Elastomeric States, Macromolecules, 2024, 57(9), 3875–3900 CrossRef CAS.
- S. Q. Wang, Letter to the Editor: Melt rupture unleashed by few chain scission events in fully stretched strands, J. Rheol., 2019, 63(1), 105–107, DOI:10.1122/1.5054655.
- A. A. Griffith, VI. The phenomena of rupture and flow in solids, Philos. Trans. R. Soc., A, 1921, 221(582–593), 163–198 Search PubMed.
- A. Boersma, K. Grigoriadi, M. G. A. Nooijens, S. Henke, I. M. Kooter and L. A. Parker, et al., Microplastic Index—How to Predict Microplastics Formation?, Polymers, 2023, 15(9), 2185, DOI:10.3390/polym15092185.
- K. Grigoriadi, M. Nooijens, A. Taşlı, M. Vanhouttem, S. Henke and L. Parker, et al., Experimental Validation of the Microplastic Index—Two Approaches to Understanding Microplastic Formation, Microplastics, 2023, 2(4), 350–370 CrossRef.
- S. Monira, R. Roychand, M. A. Bhuiyan and B. K. Pramanik, Role of water shear force for microplastics fragmentation into nanoplastics, Environ. Res., 2023, 237(P1), 116916, DOI:10.1016/j.envres.2023.116916.
- S. Monira, R. Roychand, F. I. Hai, M. Bhuiyan and B. K. Pramanik, Microplastic fragmentation into nanoplastics by water shear forces during wastewater treatment: Mechanical insights and theoretical analysis, Environ. Pollut., 2025, 364(P1), 125310, DOI:10.1016/j.envpol.2024.125310.
- M. Enfrin, J. Lee, Y. Gibert, F. Basheer, L. Kong and L. F. Dumée, Release of hazardous nanoplastic contaminants due to microplastics fragmentation under shear stress forces, J. Hazard. Mater., 2020, 384, 121393, DOI:10.1016/j.jhazmat.2019.121393.
- S. Ghosh, A. Sane, S. Gohil, V. Vashishtha, S. K. Kumar and G. Kumaraswamy, Mechanism of microplastic and nanoplastic emission from tire wear, Soft Matter, 2025, 21, 2782–2786, 10.1039/D5SM00074B.
- J. F. Archard, Contact and Rubbing of Flat Surfaces, J. Appl. Phys., 1953, 24(8), 981–988 CrossRef.
- H. A. McKellop, P. Campbell, S. H. Park, T. P. Schmalzried, P. Grigoris and H. C. Amstutz, et al., The origin of submicron polyethylene wear debris in total hip arthroplasty, Clin. Orthop. Relat. Res., 1995, 311(31), 3–20 Search PubMed.
- P. Bracco, A. Bellare, A. Bistolfi and S. Affatato, Ultra-high molecular weight polyethylene: Influence of the chemical, physical and mechanical properties on the wear behavior. A review, Materials, 2017, 10(7), 791, DOI:10.3390/ma10070791.
- T. P. Schmalzried, E. F. Shepherd, F. J. Dorey, W. O. Jackson, M. Dela Rosa and F. Fa’vae, et al., Wear is a function of use, not time, Clin. Orthop. Relat. Res., 2000, 381(381), 36–46 CrossRef PubMed.
- H. McKellop, I. Clarke, K. Markolf and H. Amstutz, Friction and wear properties of polymer, metal, and ceramic prosthetic joint materials evaluated on a multichannel screening device, J. Biomed. Mater. Res., 1981, 15(5), 619–653 CrossRef CAS PubMed.
- K. J. Brown, J. R. Atkinson, D. Dowson and V. Wright, The wear of ultrahigh molecular weight polyethylene and a preliminary study of its relation to the in vivo behaviour of replacement hip joints, Wear, 1976, 40(2), 255–264 CrossRef CAS.
- B. N. J. Persson, Theory of powdery rubber wear, J. Phys.: Condens. Matter, 2009, 21(48), 485001, DOI:10.1088/0953-8984/21/48/485001.
- B. Fayolle, E. Richaud, X. Colin and J. Verdu, Review: Degradation-induced embrittlement in semi-crystalline polymers having their amorphous phase in rubbery state, J. Mater. Sci., 2008, 43(22), 6999–7012 CrossRef CAS.
- N. F. Mendez, V. Sharma, M. Valsecchi, V. Pai, J. K. Lee and L. S. Schadler, et al., Mechanism of quiescent nanoplastic formation from semicrystalline polymers, Nat. Commun., 2025, 16(1), 3051 CrossRef CAS PubMed.
- X. Zheng, Y. Guo, J. F. Douglas and W. Xia, Competing Effects of Cohesive Energy and Cross-Link Density on the Segmental Dynamics and Mechanical Properties of Cross-Linked Polymers, Macromolecules, 2022, 55(22), 9990–10004 CrossRef CAS.
- D. J. Bray, P. Dittanet, F. J. Guild, A. J. Kinloch, K. Masania and R. A. Pearson, et al., The modelling of the toughening of epoxy polymers via silica nanoparticles: The effects of volume fraction and particle size, Polymer, 2013, 54(26), 7022–7032, DOI:10.1016/j.polymer.2013.10.034.
- R. Merget, T. Bauer, H. Küpper, S. Philippou, H. Bauer and R. Breitstadt, et al., Health hazards due to the inhalation of amorphous silica, Arch. Toxicol., 2002, 75(11), 625–634 CrossRef CAS.
- B. Crist and J. M. Schultz, Polymer spherulites: a critical review, Prog. Polym. Sci., 2016, 56, 1–63, DOI:10.1016/j.progpolymsci.2015.11.006.
- A. J. Müller, R. M. Michell and A. T. Lorenzo, Isothermal crystallization kinetics of polymers, Polymer Morphology: Principles, Characterization, and Processing, 2016, pp. 181–203 Search PubMed.
- A. Sharma, S. Thakre and G. Kumaraswamy, Microstructural differences between Viscose and Lyocell revealed by in-situ studies of wet and dry fibers, Cellulose, 2020, 27(3), 1195–1206, DOI:10.1007/s10570-019-02863-6.
- S. K. Kumar, B. C. Benicewicz, R. A. Vaia and K. I. Winey, 50th Anniversary Perspective: Are Polymer Nanocomposites Practical for Applications?, Macromolecules, 2017, 50(3), 714–731 CrossRef CAS.
- R. J. Young and P. A. Lovell, Introduction to Polymers, Online, CRC Press, Taylor & Francis Group, 3rd edn, 2011 Search PubMed.
- Z. Wang, M. Schaller, A. Petzold, K. Saalwächter and T. Thurn-Albrecht, How entanglements determine the morphology of semicrystalline polymers, Proc. Natl. Acad. Sci. U. S. A., 2023, 120(27), 1–8 Search PubMed.
- R. Seguela, Critical review of the molecular topology of semicrystalline polymers: The origin and assessment of intercrystalline tie molecules and chain entanglements, J. Polym. Sci., Part B: Polym. Phys., 2005, 43(14), 1729–1748 CrossRef CAS.
- Y.-L. Huang and N. Brown, Dependence of slow crack growth in polyethylene on butyl branch density: Morphology and theory, J. Polym. Sci., Part B: Polym. Phys., 1991, 29(1), 129–137 CrossRef CAS.
- S. Ghosh, A. Sane, S. Gohil, V. Vashishtha, S. K. Kumar and G. Kumaraswamy, Mechanism of microplastic and nanoplastic emission from tire wear, Soft Matter, 2025, 2782–2786 RSC.
- O. Der, H. Khaksar and E. Gnecco, On the Formation and Characterization of Nanoplastics During Surface Wear Processes, Surfaces, 2025, 8(27), 1–16 Search PubMed.
- Y. Nakanishi, H. Yamaguchi, Y. Hirata, Y. Nakashima and Y. Fujiwara, Micro-abrasive glass surface for producing microplastics for biological tests, Wear, 2021, 477, 203816, DOI:10.1016/j.wear.2021.203816.
- M. D. Acunto and P. Giusti, Characterization of Biomedical Polymer Coatings, Tribotest, 2006, 257–265 Search PubMed.
- Y. Nakanishi, Y. Fujiwara and Y. Nakashima, Generation of Nano/Microplastics for Immunological Assessments, Biotribology, 2023, 33–34, 100235, DOI:10.1016/j.biotri.2023.100235.
- Y. Su, C. Yang, S. Wang, H. Li, Y. Wu and B. Xing, et al., Mechanochemical Formation of Poly(melamine-formaldehyde) Microplastic Fibers During Abrasion of Cleaning Sponges, Environ. Sci. Technol., 2024, 58(24), 10764–10775 CrossRef CAS PubMed.
- E. Rahman, S. BinAhmed, P. Keyes, C. Alberg, S. Godfreey-Igwe and G. Haugstad, et al., Nanoscale Abrasive Wear of Polyethylene: A Novel Approach To Probe Nanoplastic Release at the Single Asperity Level, Environ. Sci. Technol., 2024, 58(31), 13845–13855 CrossRef CAS.
- H. Cai, E. G. Xu, F. Du, R. Li, J. Liu and H. Shi, Analysis of environmental nanoplastics: Progress and challenges, Chem. Eng. J., 2021, 410, 128208, DOI:10.1016/j.cej.2020.128208.
- C. Fang, Y. Luo and R. Naidu, Microplastics and nanoplastics analysis: Options, imaging, advancements and challenges, TrAC, Trends Anal. Chem., 2023, 166, 117158, DOI:10.1016/j.trac.2023.117158.
- C. Vitali, R. J. B. Peters, H. G. Janssen, M. W. F. Nielen and F. S. Ruggeri, Microplastics and nanoplastics in food, water, and beverages, part II. Methods, TrAC, Trends Anal. Chem., 2022, 157, 116819, DOI:10.1016/j.trac.2022.116819.
- J. Caldwell, P. Taladriz-Blanco, R. Lehner, A. Lubskyy, R. D. Ortuso and B. Rothen-Rutishauser, et al., The micro-, submicron-, and nanoplastic hunt: A review of detection methods for plastic particles, Chemosphere, 2022, 293, 133514, DOI:10.1016/j.chemosphere.2022.133514.
- Z. Zeng and J. C. Tan, AFM Nanoindentation to Quantify Mechanical Properties of Nano- and Micron-Sized Crystals of a Metal-Organic Framework Material, ACS Appl. Mater. Interfaces, 2017, 9(45), 39839–39854 CrossRef CAS.
- B. Nguyen, D. Claveau-Mallet, L. M. Hernandez, E. G. Xu, J. M. Farner and N. Tufenkji, Separation and Analysis of Microplastics and Nanoplastics in Complex Environmental Samples, Acc. Chem. Res., 2019, 52(4), 858–866 CrossRef CAS PubMed.
- A. L. Lusher, N. A. Welden, P. Sobral and M. Cole, Sampling, isolating and identifying microplastics ingested by fish and invertebrates, Anal. Methods, 2017, 9(9), 1346–1360 RSC.
- F. Meng, M. Brandão and J. M. Cullen, Replacing Plastics with Alternatives Is Worse for Greenhouse Gas Emissions in Most Cases, Environ. Sci. Technol., 2024, 58(6), 2716–2727 CrossRef CAS PubMed.
|
This journal is © The Royal Society of Chemistry 2025 |
Click here to see how this site uses Cookies. View our privacy policy here.