DOI:
10.1039/D4SU00571F
(Critical Review)
RSC Sustainability, 2025, Advance Article
State-of-the-art of industrial PET mechanical recycling: technologies, impact of contamination and guidelines for decision-making
Received
14th September 2024
, Accepted 8th December 2024
First published on 11th December 2024
Abstract
Poly(ethylene terephthalate) (PET) waste streams hold high societal and commercial value, with complementary mechanical and chemical recycling technologies enabling a circular implementation for many generations and life cycles, provided the multi-scale characteristics of polyester synthesis and recycling are properly quantified. The present contribution highlights the challenges faced by the PET mechanical recycling industry, connecting (i) variations at the molecular scale (e.g. degradation reactions), co-defining the material and ultimately the application properties, with (ii) variables at the plant scale (e.g. pre-treatment efficiencies). It is explained why both a polymer reaction engineering (PRE) analysis for the key processing (e.g. extrusion and solid state modification) units and a life cycle assessment (LCA) analysis at the process level (e.g. energy calculations) from the field of environmental engineering science (EES), acknowledging changes in contamination (e.g. non-intentionally added substances (NIAS)) levels and PET supply, are necessary. For each unit in the production plant the main influencing factors are discussed, highlighting how the overall performance is affected by the performance of each unit, from collection to relaunch of the PET product on the market. It is also elaborated how model-based design and data analysis can support the overall process and energy optimization. General guidelines are formulated, facilitating the combined molecular and process scale driven assessment of the feasibility of mechanical recycling technology. This in turn allows the initialization of a more fundamentally based framework for decision-making regarding preferred recycling technologies, including both the PET mechanical and chemical recycling routes.
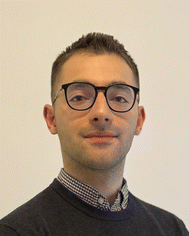 Erion Bezeraj | Erion Bezeraj is a PhD student at the Center for Polymer and Material Technologies (CPMT) at Ghent University under the supervision of Prof. Mariya Edeleva and Prof. Dagmar R. D'hooge. He obtained a National Science Foundation (FWO-Vlaanderen) scholarship on polyester recycling and is already a co-author of 2 full length research articles, as well as one submitted contribution. He is currently preparing two additional publications in the field of polymer circularity. |
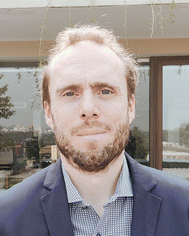 Dagmar R. D'hooge | Prof. Dagmar R. D'hooge is the elected Chair for the Department of “Materials, Textiles and Chemical Engineering” at Ghent University. His research emphasizes the multi-scale design of polymerization, polymer processing and polymer recycling. He uniquely performs research in chemical engineering, materials science, polymer science, and mechanics/rheology. He was a postdoctoral researcher at Carnegie Mellon University and the Karlsruhe Institute of Technology, Karlsruhe. He is a visiting scientist at Stanford University. He is a co-author of 200 peer-reviewed full length research articles, 6 book chapters, 2 books, and 3 patents. He is a co-founder of two spin-offs. |
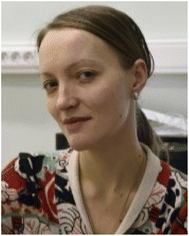 Mariya Edeleva | Prof. Mariya Edeleva is a tenure-track professor at the Center for Polymer and Material Technologies (CPMT) at Ghent University. Her research is focused on the development of polymeric materials and their recycling to promote polymer circularity. She applies chemical and material design for sustainable polymer manufacturing, including mechanical recycling and reactive modification. She was a postdoctoral researcher at Aix-Marseille University. She is a co-author of 65 peer-reviewed research articles, 4 book chapters, and several patents. |
Sustainability spotlight
PET mechanical recycling is an important technology to realize polymer circularity (UN SDG 12). Industrially the process can be challenging, due to the impact of contaminants (e.g. non-intentionally added substances; NIAS) as well as feedstock variations. The current review connects lower and higher technology readiness level (TRL) research and process design, combining polymer reaction engineering (PRE) and life cycle analysis (LCA) along the value chain. It is showcased that our current regulations on PET (waste) product quality can be further fine-tuned by mitigation at the process level (UN SDGs 9 and 13), once more science-driven analysis of each unit in the PET recycling plant is within reach by integrating experimental and software-based analysis.
|
1. Introduction
Polyester-rich waste streams are highly relevant in the global landscape of polymer recycling. The leading (thermoplastic) polyester is poly(ethylene terephthalate) (PET), with applications such as liquid containers, packaging and fibers.1,2 The most well-known commercial polyester item is the PET bottle, with an expected market value of over 40 billion dollars by 2033 according to a compound annual growth rate of ca. 4% from 2023 to 2032.3 Another important application is the PET tray, contributing to a market share of 25% in the packaging product segment in 2020 for the European Union (including e.g. the United Kingdom).4
PET recyclability is facilitated by its thermoplastic nature, allowing re-melting and solidification. Moreover, the reversibility of PET synthesis with its core polycondensation reactions, delivering small byproducts (e.g. water and methanol), makes PET-based products suitable for a wider range of recycling technologies, including chemical modification via either chain repair or full monomer/oligomer recovery. Consistently, the European Commission (EC) is demanding that certain PET-based packaging materials need to include already 30% of recycled plastics by 2030,5 exemptions being contact-sensitive applications such as medical, veterinary and food contact products requiring stricter safety and hygiene regulations.6,7 A challenge is that per recycling cycle the PET/polyester feed composition will change because of the mixing of different generations of (sorted) waste. This waste mixing likely involves different average chain length ranges and contamination levels, as well as geographically influenced variations in collection efficiencies.
As illustrated in Fig. 1, three main industrial technologies for PET recycling are mechanical or primary recycling, chemical or secondary recycling, and physical or tertiary recycling.8 In mechanical recycling, reshaping at the polymer level is aimed at minimizing (chemical) degradation reactions, whereas in chemical recycling the goal is to chemically transform polymer molecules into their original building blocks from the synthesis.9 Here one can distinguish depolymerization, reversing the synthesis, and pyrolysis.
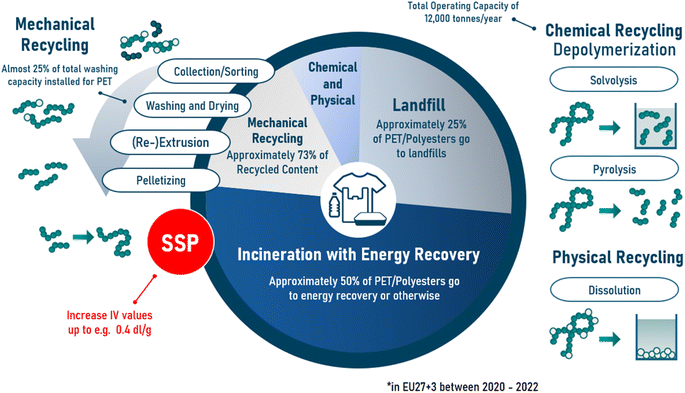 |
| Fig. 1 General principles for PET mechanical recycling via re-processing and PET chemical recycling, complemented with other techniques such as physical recycling via dissolution/precipitation.8 IV: intrinsic viscosity; SSP: solid-state polymerization. | |
For PET, chemical depolymerization can be realized via solvolysis, benefiting from the reversible nature of polycondensation reactions, ensuring (direct) repolymerization.9,10 For PET chemical recycling, one does not need to rely by default on pyrolysis delivering solid/melt-gas phase transitions, as for instance the case for chemically converting polyolefin waste into low carbon products.11 Physical recycling employs in turn dissolution and precipitation techniques to extract the desired/purified polymer from the waste stream.12 Both solvolysis and dissolution recycling use (chemical) solvents, so sometimes both are for simplicity categorized as chemical recycling techniques. However, from a more fundamental point of view, physical recycling should be distinguished from chemical recycling, as only chemical recycling aims at (dedicated) chemical modification of the polymer.
In the present contribution, the main emphasis is on the industrial principles and challenges for PET mechanical recycling technology, seeing as the main alternative for this technology is solvent-based depolymerization, and thus, chemical recycling technology through solvolysis. Mechanical recycling and solvolysis are complementary but it is currently unclear when which technology is preferred under which circumstances. We for instance still need to formulate a detailed answer to the following questions: (i) what is the impact of the quality of incoming waste on the recycling efficiency and economics of a given technology; (ii) how easily can recycled product streams be launched into the polymer and plastic market still dominated by virgin products and materials; and (iii) how decisive is the overall energy cost in the choice of a preferred recycling technology as well as the coupled plant design?
It goes without saying that many (process) variables come into play – along the whole polymer value chain – to verify if a certain recycling technology is economically viable in our societal striving for a circular world for plastic materials and products. In this context, a dedicated and systematic multi-scale approach, synergistically strengthening and bridging several scientific fields, is required for research innovation and process design activities, connecting the academic and industrial community. To enable a long-term circular implementation for PET products, a much better fundamental understanding of recycling technologies should be targeted, accounting for variations in feedstock (collection) as well as local and world-wide regulations and future intentions.
For a more fundamental understanding of PET recycling technologies, one needs to link investigations and data analysis at a lower and a higher technology readiness level (TRL). It should be stressed that even for the virgin PET and in general the virgin polymer market such linkages are rather rare. This is because we first need a detailed research approach at both TRL types before one can attempt their connection, which is historically less embedded in our overall product design approach; in academia in many cases most research studies deal with the very low TRL end (although sometimes with more realistic feedstock validation for at least a single unit), and in industry the focus is mainly on high TRL activities connecting several process units, considering rather fast decision making for the prior lower TRL input. However, only by better connecting both TRL types can one achieve a better interconnected adaptation to deliver genuine multi-scale design of the whole value chain for a long time period, correcting for sudden changes in product quality, societal expectations and governmental regulations.
To achieve a better connection of lower and higher TRL activities for PET mechanical recycling in the next decade, the current contribution aims at setting out general guidelines. This is done starting from our recent lower TRL contribution,13 dealing with PET degradation under ideal lab scale conditions, with at most a limited disturbance of contamination for the ongoing degradation reactions. The lower TRL contribution highlighted that depending on process variables such as temperature, mechanical forces (e.g. screw design), oxygen and water concentration, as well as exposure to sunlight, different (degradation) reaction pathways are more or less likely. The relevance of these pathways is additionally influenced by the type of comonomer unit present in the polyester backbones, and thus, influenced by the polyester feedstock composition.13 It has been further demonstrated by Fiorillo et al.13 that the PET rheological, thermal and mechanical material property variations upon consecutive ideal recycling can at least be partially correlated to the dominant molecular degradation reactions. Hence, at a lower TRL, it is critical to realize a clear understanding of the interactions and modifications of the (polyester) molecules present. One needs to sufficiently account for the chemistry variations, keeping in mind that the (melt) viscosity influences the (macro)molecular mobility and thus the observed (or apparent) mechanical recycling kinetics.14,15 This implies profound knowledge from the polymer reaction engineering (PRE) field for PET mechanical recycling optimization and market validation, recognizing the molecular scale.
As demonstrated in the current contribution, contaminants, specifically Non-Intentionally Added Substances (NIAS) such as benzene and bisphenol A, as present in higher TRL applications, complicate the appreciation of the mechanical recycling process at this molecular scale. There is thus a large difference between (low TRL) ideal lab scale and (high TRL) industrial scale PET mechanical recycling. Industrially, the waste needs to be collected, sorted and pre-treated, and this can increase the number of undesired (macro)molecules upon passing the processing train. For instance, the engineering actions in the washing unit of the recycling plant can affect the re-processing (repairing) potential later on in the plant, as certain (macro)molecules do not contain the correct functional end-groups. It can also be expected that a different PET waste entry is best treated with another overall plant scheme, i.e. the specific connection of certain pre-treatment and re-processing units either in the melt or solid state could be different for an optimal recycling performance.
In other words, for an industrial assessment of the PET mechanical recycling potential, one needs to evaluate the recycling technique efficiency from a life cycle assessment (LCA) point of view alongside a PRE one. Only then will it become clear how many generations of PET waste can be effectively managed using the mechanical recycling technology for a given geographical and legislative framework. It should be stressed that almost no contributions in the open literature exist that connect LCA with PRE insights, so that an unbiased interpretation of the compatibility of different PET recycling technologies in the overall polyester market is at this stage of a more subjective nature. At most one acknowledges some average PRE properties at the application level to define quality. LCA input on for instance energy use is merely a rough estimate that is yield and not chain length/functionality driven.
In what follows, it is first explained how PRE and LCA principles can be utilized to deliver science driven guidelines and boundaries for the selection of a certain mechanical recycling technology, acknowledging low and high TRL influencing factors. The most essential reactions at the molecular scale as well as the most important units at the process scale are discussed, and it is specifically highlighted which type of contaminant can alter the preferred connection of both scales. The impact of contaminants is also embedded in a concise overview of the current (European) standards and regulations, complemented by an overview of recycled PET (rPET) applications also addressing routes not involving mechanical recycling (e.g. physical recycling). This is done to identify challenges for the overall PET recycling community, bridging lower and higher TRL tasks and to open the pathway for an international roadmap, on introducing long-term circularity for PET and in general the polyester market.
2. Guidelines on selecting PET mechanical recycling: the need to connect the molecular and process scales
At the process level, from an energy point of view, mechanical or secondary recycling of PET (streams) is very likely the preferred technique over chemical or tertiary recycling as well as energy valorization/recovery or quaternary recycling.16 However, the downsides of mechanical recycling are the deterioration of the material properties upon consecutive recycling,16,17 and the need to retrieve a rather defined starting material before the actual re-processing. At one moment or under certain practical conditions, it can thus be anticipated that PET chemical recycling is the way forward with only in the worst case scenarios the option of energy recovery being the best, avoiding in any case landfill. Note that energy recovery emerges as the preferred recycling strategy upon dealing with very complex or heavily contaminated waste streams that are unsuitable for recycling through other methods. These too complex streams present severe challenges that prevent effective or economically viable recycling, positioning energy recovery as the only feasible option. The fuels produced through this process are energy-dense, making them valuable for generating heat or electricity.18
The relevance of PET chemical recycling is more evident for treating reasonably complex waste situations by the added possibility/flexibility to apply solvolysis, exploiting the reversible nature of polycondensation chemistry as opposed to chain growth polymerization chemistry (e.g. polyolefin market). Depolymerization through solvolysis allows advanced chemical degradation by contact of polymer molecules with an excess of solvent molecules that were seen as byproduct molecules in the original synthesis to re-generate the monomer and/or the first oligomers as formed during that original synthesis. A direct integration at the polymerization plant level is thus possible for PET solvolysis, in contrast to for instance pyrolysis of polyolefin molecules in which chemical recycling delivers a rather broad spectrum of oligomeric products. For such pyrolysis, the recycled liquid and gas molecular products can have easily a maximal carbon number of 30 so that ethylene or propylene, being examples of the original monomers with very low carbon numbers, are not dominantly formed.
Industrially, it is therefore paramount to define both energy-based and chemistry-driven guidelines that enable a fair assessment of the most suited recycling technology for a given polyester, in general, polymer waste streams. In other words, to enable a translation from the lab to the plant scale for a recycling technology, one needs to distinguish between influencing factors at the molecular scale as well as the process scale. For the molecular scale, one needs to determine whether the degradation reactions under mechanical recycling conditions are repairable or not. Only if no suited (macro)molecular repairs can be made, one, accounting for contaminations established at the process scale, needs to aim at dedicated degradation toward monomers or oligomer recovery. Physical recycling could be an alternative at one point; however, for PET waste streams, solvolysis is likely preferred once mechanical recycling is no longer a valid option.
It should be stressed that molecular variations always take place during mechanical recycling but only a certain degree or type of chemical modification is allowed to ensure a final application with acceptable material performance. Hence, a PRE oriented analysis connecting molecular characteristics to material properties is a key task for defining chemistry-driven recycling guidelines. These molecular variations and their potential repair should be seen in the overall plant design, as for instance a dominant contamination or a supply limitation can alter the recycling roadmap and market potential. This means that alongside the aforementioned PRE-based analysis on individual process units in the plant, e.g. an extrusion or solid-state unit, a LCA analysis is required along the whole value chain, putting forward the relevance of environmental engineering science (EES). A more fundamental decision making for recycling technology design will thus emerge by bridging PRE with EES, together defining the overarching field of sustainable polymer reaction engineering (sPRE), as highlighted in the present contribution.
In this section, attention is paid to the most important PRE and EES features for PET mechanical recycling, starting from the main conclusions and insights from our previous lower TRL contribution.13 That contribution dealt with the chemistry and material variations for ideal mechanical recycling in the absence of or at most limited presence of contaminants, and thus, lab scale degradation reactions under well-defined conditions of temperature and initial composition.
2.1. Polymer reaction engineering analysis: molecular variations during recycling
At the core of any polymer modification, either desired or undesired, lies a more fundamental understanding of the (macro)molecular chemistry variations at hand. This is because the material and thus application properties largely depend on molecular characteristics such as the chain length and branching distribution, or at least their averages.19,20 For example, the melt flow index (MFI)21,22 or intrinsic viscosity (IV) is known to correlate with the (mass) average molar mass (Mm),23,24 and the brittleness is affected by the degree of crosslinking or gel content.25
For PET chemical recycling purposes, these molecular scale variations are very clear, as one deliberately aims at a chemical alternation from the polymer to the oligomer level, and thus, one goes from very high to very low chain lengths in the limit a chain lenght of 1 (monomer level). For PET mechanical recycling purposes, in which the goal is to maintain very high chain lengths, molecular scale variations can however have a huge impact as well. For example, the formation of volatiles is associated with the specific release of small chemical moieties from the backbone structure. Furthermore, the repair potential of degraded macromolecules defining mechanical recycling mitigation strategies depends on the presence of certain functional groups, which can be disturbed by specific degradation pathways yielding irreversible (functional) groups. Hence, also for mechanical recycling, it is paramount to be aware of the chemistry behind the reprocessing steps, with for instance a too long (re)processing at elevated temperature, specifically with wet PET flakes inducing additional hydrolytic reactions, being a point of attention often overlooked in the field.
Intriguingly, per PET recycling cycle, the balance of reversible and irreversible molecular changes due to chemical (degradation) reactions is altering. This means that a large number of input variables and output design features need to be mapped to enable proper decision making regarding a preferred recycling technology implementation and optimization for a given time period. Consistent with evolutions in the chemical industry and the PRE field a pure experimental way of working is too restricted, and instead the use of computer tools is recommended, including experimental validation at least for a training set of operational conditions. Hence, a model-based assessment of the recycling potential, making a clear distinction between generations or types of waste, is preferred to decide which recycling technique is the most suited, taking into account an acceptable range of application target properties, geographical features, and economic constraints.
In what follows, emphasis is first on the most important (elementary) degradation reactions during mechanical recycling, focusing on a given subunit (e.g. section of an extruder). It is then highlighted that the industrial settings and equipment design have an impact on how these reactions affect the mechanical recycling efficiency, with a superposition of various molecular distributions being the result. It is also put forward which types of PRE modeling strategies enable the best support for the mapping and design of these (macro)molecular variations.
2.1.1. Elementary degradation reactions at a given subunit in the overall process.
As explained in detail in Fiorillo et al.,13 for polyester (mechanical) recycling, one can distinguish between a wide spectrum of (elementary) chemical reactions, either based on (i) thermal trigger defining thermal degradation reactions, (ii) a mechanical trigger typically at elevated temperature defining thermomechanical degradation reactions, (iii) the presence of an oxygen-rich environment delivering thermo-oxidative degradation reactions, and (iv) the contact with water or moisture putting forward hydrolytic reactions. Contact with ultraviolet (UV) light during polymer usage and application additionally induces photo-oxidative reactions.
Main examples of each type of degradation reaction are given in Fig. 2, selecting for illustration purposes virgin PET as the substrate and only a limited number of chain lengths. It should be noted that these reactions can occur for various chain lengths, defining molecular distribution, as well as along the whole value chain as long as the processing/environmental conditions allow the reaction time scales to be relevant. Most likely this is the case for a processing subunit operating at elevated temperature, e.g. a subunit of an extruder with a certain barrel temperature, or a processing subunit with an increased solvent content, e.g. a washing subunit in the pretreatment part of the plant.
 |
| Fig. 2 Examples of PET (lumped) degradation reactions as likely encountered during mechanical recycling and end-of-life; (1) mid-chain driven ester rearrangement or net results of fission and βH-abstraction, defining radical-based ester rearrangement, e.g. thermal or thermomechanical; (2) alternative end-driven ester rearrangement with intermediate cyclization; (3) hydrolysis; (4) carboxylation with CO2 formation; (5) volatile (aldehyde) formation; (6) hydrogen abstraction; (7) oxygen propagation as part of thermo-oxidative degradation; (8) chain transfer; (9) photo-oxidative scission. | |
Notably, depending on the molecular build-up of the polyester backbone, certain reaction pathways are faster or slower, with for instance the diethylene glycol (co)monomer unit more prone to a chemical attack compared to the traditional PET ethylene glycol unit from the rate coefficient point of view.26–28 Moreover, due to the presence of certain contaminants either formed during the first life cycle or during further PET recycling, the reaction mechanism becomes more complex.13,29–31 This means that if one compares lab and plant scale recycling data and design, the number of acceptable mechanical recycling passes could be lower at the plant scale, or a more dedicated process control is needed for the plant scale to guarantee a given number of such passes.
In Section 5 of the present contribution, a detailed overview is given of the role of these contaminants, making a link to the overall chemistry in the present subsection dealing with the main polymer-based reactions (cf. the discussion of Fig. 2).
2.1.2. Superposition of molecular distributions at the processing unit level.
It should be stressed that molecular characteristics (e.g. chain length and comonomer content) are more distributed at the industrial level, as non-idealities influenced by strong equipment and processing settings are unavoidable. However, even under well-defined lab scale conditions, a polymer is already characterized by rather strong chain length dependencies with the presence of both shorter and longer macromolecules. Furthermore, during lab scale modifications molecules can already be present or formed that display different topologies such as linear, branched and crosslinked.32
The diversity of molecular variations along an industrial processing unit is highlighted by the boxes in Fig. 3. If one in a first step only focuses on the (micro-scale) green box early in the processing unit, the lab scale situation can be understood, as for this small subunit or region a given temperature and pressure likely hold. The molecules in the green box are different in chemical build-up because of unavoidable stochastic variations during the prior synthesis, e.g. caused by the interplay of chemistry and chain length dependent diffusivity.19 In addition, chemical modifications are established during the actual processing in which molecules still stay in this green box, implying only a small residence time step.
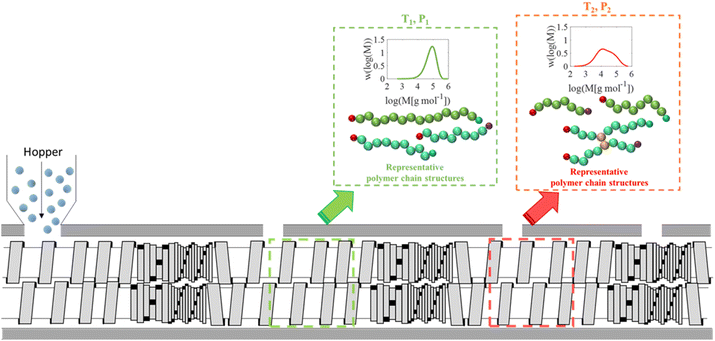 |
| Fig. 3 The distributed nature of polymer chemical modification as for instance occurring during mechanical recycling (the case of twin screws). In a given micro-scale region of a processing unit (e.g. green box), as defined by e.g. a given temperature and pressure, different molecules undergo different molecular scale variations; the small box can thus be seen as the lab scale analogue. Upon inspecting another region (e.g. orange box), likely influenced by macro-scale variations (as defined at the level of the process/plant scale), these molecular variations can be different as the temperature and pressure can be different and the mixing history can disturb the degree of chemical modification. | |
Upon inspecting in a second step a region more downwards the processing unit, e.g. the orange box in Fig. 3, other molecular variations are likely more relevant than those in the green box. On the one hand, this is because the molecules further away in the process train experienced a more extensive chemical modification history, as the residence times for the individual molecules are by default higher. On the other hand, larger set-ups, defining inherently a higher number of micro-scale regions, are more prone to macro-scale mixing and temperature gradients so that the bulk concentrations and temperature change per such region or subunit. For example, the green and orange boxes in Fig. 3 are likely characterized by a different screw design and temperature of the external heating element, which can result in a different alternation of the molecular build-up of the macromolecules for a given time period.
Hence, the polymer product after a (re-)processing step is likely characterized by a complex superposition of several (molecular) distributions as established at both the micro- and the macro-scale, highlighting the multi-scale nature of the (s)PRE field. There is thus a strong desire for data analysis approaches, recognizing (i) the distributed nature of molecular variations for a given micro-scale temperature and pressure and (ii) the impact of the scale of the processing equipment itself, leading to macro-scale variations.
Next to these micro- and macro-scale variations, meso-scale variations can be relevant as well. It is very likely that a multiphase system is being recycled even after proper sorting.33 Polymer blends are likely non-homogeneous already if the amount of blending contributors is limited, as one always has the presence of certain fillers, compatibilizers and/or polymer contaminant(s) compared to the major polymer component. Specifically, cooling can induce meso-scale mixing and thermal gradients as well as influence certain morphological (e.g. crystallinity) variations.
It should be made clear that PRE characterization of a processing unit as detailed in Fig. 3 can only be manifested, if one applies more advanced modeling tools. Most detailed is the so-called coupled matrix-based Monte Carlo (CMMC) approach,34–36 in which individual molecules are tracked at any position and time in a sufficiently large subunit (e.g. box in Fig. 3) during processing. In contrast to computational fluid dynamic (CFD) techniques, in CMMC, a rougher mesh is defined at the process scale, but very detailed interactions of chemical and molecular diffusion phenomena are accounted for. One also has the option to follow molecular distribution variations in CMMC, as one does not need to directly rely on averages as is e.g. the situation for the deterministic method of moments (MoM).37,38 This relevance of the distributed level with averages calculated a posteriori is for instance evident in the failure of pure average-based modeling to unbiasedly assign multi-peak systems,38 such peaks being highly relevant for mechanical recycling and recycling in general.
2.2. Environmental engineering science: life cycle assessment analysis integrating variations for processing units
As shown in Fig. 4, LCA is an analysis method to assess the environmental impact of a final product (e.g. PET bottle) throughout its life cycle, i.e. from natural resource extraction to manufacturing and subsequent usage, to ultimately waste management, including disposal and recycling.40 LCA has been initially developed as a comparison tool to evaluate the environmental impacts of a product, to develop the most suited production and recycling routes, and to enable a comparison of available alternatives.41 Nowadays, LCA is interconnected with marketing implementation, product design, product development, strategic planning, consumer education, ecolabeling and government policy making. However, LCA should be performed in a correct way avoiding subjective opinions, and purely economic and political driven incentives, highlighting the need to connect LCA with techno-economic assessment (TEA).41,42
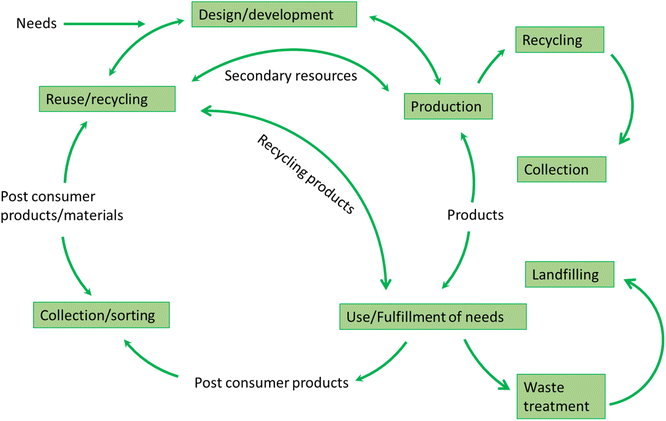 |
| Fig. 4 Example of the life cycle for a commercial item (based on ref. 39) in a typical life cycle assessment (LCA). | |
The most widely employed LCA approach is based on the well-established ISO 14040 standard.43 This approach is organized around several specific functions: (i) identifying opportunities to improve the environmental aspects of products throughout their life cycle, with goals such as management tasks, environmental mapping, social mapping, or footprint analysis; (ii) supporting decision-making in industry and government, including strategic planning, priority setting, product or process design or redesign, which can be mapped through inventory types such as flow chart implementation; (iii) selecting relevant indicators of environmental performance, such as toxicity or climate change impact, and applying appropriate measurement techniques; and (iv) driving marketing efforts through environmental claims, ecolabels, or product declaration, while also assessing improvements towards more sustainable products. Most recommended is to derive sufficiently detailed mass and energy balances,44e.g. also benefiting from more recent developments of multilevel statistical entropy analysis (SEA;45).
Notably, for plastic/PET mechanical and chemical recycling, several LCA studies have already been reported,46–50 but overall more data at the molecular scale are needed per (sub)unit in the overall production and value chain to better assess the product quality, differentiating between lab and plant scale operations. Such molecular scale driven embedding will facilitate the application of LCA at both lower and higher TRLs, which is currently still a huge challenge in the overall LCA field.
In what follows, it is explained how LCA has been applied for the polymer and specifically PET recycling industry and which studies already make a link to PRE or molecular variations. This is done first from a more general perspective mainly comparing mechanical and chemical recycling technologies and then includes a deeper analysis within each general recycling category, paying attention in a final part to the consideration of alternative feedstocks.
2.2.1. Comparing mechanical and chemical recycling technology.
Most plastic waste LCA studies mention an overall CO2 equivalent value (eq. per treated kg of waste), based on rather general process schemes so that only basic descriptions of the (processing) units involved are included. For example, for the PET market, Ncube and Borodin51 assessed the environmental impact for the bottle-to-bottle (BtB) mechanical recycling technique as 3.33 kg CO2 eq. compared to the waste to landfill option with a value of 47 kg CO2 eq.
Supported by the first PET LCA studies, as conducted in the middle of the previous century, it became quickly clear that plastic bottles are preferable over their glass counterparts.52,53 Specifically, PET-based beverage packaging provides many benefits, including rapid production and light-weight. The conventional implementation of returnable PET bottles involves major investments for the bottlers, as the empty bottles must be examined for contamination. In this context, BtB mechanical recycling has been developed as a sustainable alternative, which as depicted in Fig. 5(a) includes collection, cleaning, re-melting and reshaping as the process steps to be optimized.
 |
| Fig. 5 (a) PET bottle product life; (b)–(d) compared LCA results for PET vs. glass bottles for (b) process water consumption, (c) vehicle mileage and (d) landfill area; subfigures redrawn based on the data from Schmidt et al.54 | |
Assuming for instance that 50% of the recycled PET is employed for the fabrication of new bottles, Schmidt et al.54 showed that the PET recycling process delivers at least 20% benefits for process water consumption, vehicle mileage and landfill area compared to the glass bottle system (Fig. 5(b)–(d)). Arena et al.55 additionally evaluated the efficiency of PET mechanical recycling compared to landfill and incineration and stated the preference of the former technique because of the presence of at least at that time a stable market for recycled PET, a good collection system, and extensive cleaning procedures. Komly et al.56 in turn highlighted that PET mechanical or chemical recycling by solvolysis is always preferable over thermal recycling, and thus, pyrolysis. Moreover, these authors stated that within closed-loop recycling, the mechanical recycling pathway is preferred over glycolysis followed by repolymerization, the latter combination of chemical recycling and synthesis by repolymerization being feasible thanks to the technical developments in the last decades.
If this PET closed-loop recycling is compared to the energy recovery option, as done in the work of Chilton et al.,57 the first is seen as the better environmental option. However, other factors such as the PET market stability and the cost of collecting and processing the material should also be taken into account upon selecting recycling technologies. These authors pointed out that transportation costs and emission level disturbances are crucial for the correct LCA of PET closed-loop recycling. Many other earlier studies e.g. that of Tukker58 ignored this type of refinement, highlighting the challenge of extensive LCA developments for the PET virgin and recycling industry.
Another PET LCA challenge is the better implementation of the impact of contamination. As the impact of contaminants on the PET mechanical recycling potential is still rather vague, chemical recycling, e.g. solvolysis or pyrolysis, might be an interesting and logical alternative, as it should provide after polymerization again a pure polymer that can enter the market. The early LCA analysis of Song and Hyun59 mentioned that PET chemical recycling requires significantly more energy and depletes the fossil resources more compared to mechanical recycling. These authors stated that mechanical recycling must be seen as the preferred environmentally friendly technique over chemical recycling, as further elaborated on by Perugini et al.49
For completeness, it is mentioned here that for PET dissolution, the reported LCA data are not abundant. Chaudhari et al.60 for instance compared different dissolution–precipitation based techniques for PET. They reported that the anti-solvent treatment is less profitable compared to evaporation or cooling precipitation methods, with 60% more greenhouse gas (GHG) emissions compared to fossil-based virgin PET production. In a related contribution,61 chemical recycling and dissolution–precipitation have been compared, with the dissolution–precipitation being favorable in terms of GHG emissions.
Interestingly, more recent LCA studies have put forward that better defined boundary conditions are needed to make clear whether mechanical or chemical recycling makes sense. Nakatani et al.62 highlighted for instance that chemical recycling can be a beneficial option if transboundary transportation is involved. In more detail, the influence of domestic and transboundary transportation on the mechanical and chemical recycling of PET has been addressed. These authors showed that domestic recycling can be beneficial in the scope of GHG emissions, if the industrial processes are comparable. However, the differences in background parameters between the selected countries, Japan and China, influenced the GHG emissions in such a way that transboundary options had a lower environmental impact. Furthermore, Marathe et al.63 suggested that chemical recycling can be beneficial if the collection step is significantly optimized.
Meys et al.64 mentioned that compared to energy recovery PET chemical recycling could potentially reduce global warming impacts by up to 4.3 kg CO2 eq. (per kg treated PET). In addition, the LCA study of Allen and James65 states that PET chemical recycling is likely not as favorable as traditional mechanical recycling but is preferred over virgin PET production. The chemical recycling process could thus be likely applied to a rather broader range of lower-value wastes to increase the overall PET recycling rate. Complementarily, the study of Ragab and Ramzy66 compares the LCA of BtB mechanical recycling to virgin PET synthesis to conclude that recycling offers significant environmental benefits to virgin pellet production, further supported by the findings of Tamoor et al.67
Another more recent trend for (polyester) LCA is to include both attributional and consequential LCA,68 with the former identifying how environmental aspects (e.g. pollutants) are flowing in a given temporal window and the latter dealing with how flows are changing in response to decisions. For example, for PLA, Ricardo Rebolledo-Leiva et al.69 highlighted that indirect land use alters emissions from a consequential point of view and that lactic acid is a key point of attention related to pre-treatment and downstream operations.
2.2.2. Variations in methods per general recycling technology.
Another PET challenge at the LCA level is the identification of the most suited recycling method within a given general recycling technology category, as defined in Fig. 1. For example, for PET chemical recycling, Lang et al.70 compared methanolysis, glycolysis and hydrolysis via the LCA approach. They showed that glycolysis is the most suitable process due to its significant initial economic potential. However, process flexibility also matters with e.g. methanolysis delivering dimethyl terephthalate (DMT) to be repolymerized, which makes sense if direct equipment is available, and e.g. a costly purification to form terephthalic acid (TPA) for repolymerization. Peng et al.71 in turn put forward that acetolysis can eventually offer a low-carbon pathway to contribute to the circular integration of PET waste.
Similarly, it is interesting to identify the best PET mechanical recycling method so that PET mechanical and chemical recycling technology can be better compared on a general basis, based on the type of waste at hand and considering the connection with the virgin market variations. Due to thermo-mechanical degradation, it has been for instance claimed that the PET BtB route requires the addition of virgin material.72,73 In this scope, several studies74,75 focused on bottle-to-fabric recycling, as for the fabrics the required IV of the feedstock material is lower than for bottle production. For example, Shen et al.75 compared open- and closed-loop PET recycling, considering mechanical recycling, back-to-oligomer recycling, and back-to-monomer recycling. These authors concluded that bottle-to-fiber recycling reduces impacts for most of the environmental categories studied.
Moreover, Shen et al.75 assessed the benefits of multiple recycling loops for bottle-to-fiber recycling, as consecutive market relaunches should at first sight reduce the environmental impacts. However, they put forward that the savings become negligible after the third cycle. Notably, if the BtB market is preferred, high-impact reductions are likely achieved, and if no extra virgin PET is required, the quantities of recycled PET are maximized as well as the savings. The study of Shen et al.75 further highlighted that the quality of recycled PET (rPET), specifically its purity, molecular properties and e.g. IV, is crucial for the full exploitation of the BtB recycling technique.
Based on the discussion above, it thus follows that future LCA studies should address in more detail the relevance of all the influencing factors regarding production and waste management as well as specific features of the recycling technology, transportation and market availability. In this context, Valentino76 for instance performed a more detailed type of LCA for BtB PET recycling, focusing on the country Denmark and the Lombardy region. Attention has been paid to which kind of PET recycling route is environmentally better and to which extent performing multi-recycling loops is reasonable and environmentally sustainable. These authors concluded that BtB mechanical recycling presents lower impacts for the climate change impact category but delivers higher impacts for the water stress index and mineral and resource depletion value. Hence, upon choosing the environmentally most suited recycling scenario, it is necessary to take into consideration which impacts the decision-maker focuses on.
Furthermore, the effectiveness of multiple-recycling is related to (i) the collection efficiencies and (ii) the repair potential and design at the molecular scale in a given processing (sub)unit (cf. the discussion of Fig. 3). Again, it is thus clear that PRE and LCA analysis need to be connected in view of PET recycling decision-making.
2.2.3. Exploring alternative virgin feedstocks.
An extra challenge for the polyester market and LCA developments is the introduction of more sustainable (fresh/virgin) feedstocks. As indicated above, LCA has identified polymer synthesis as one of the most impactful operations in the complete PET bottle product life. In this scope, switching to more sustainable PET feedstocks might provide some advantages, at least from a LCA point of view.
Chen et al.77 for instance compared the environmental LCA for 100% bio-based PET bottles versus the one for 100% fossil-based bottles as well as the one for partially bio-based PET bottles, using a novel manufacturing process with lignocellulosic biomass from forest residues. They reported that woody-biomass-based PET bottles have 21% less global warming potential and require 22% less fossil fuel than their fossil-based counterparts. However, the bottles perform worse in other categories such as ecotoxicity and ozone depletion impacts. The authors highlighted that the results are likely very sensitive to the assumptions, again highlighting the need to better connect the molecular and process scale in future work.
Semba et al.78 performed a similar study on bio-based PET synthesis, considering the formation of para-xylene from ethanol. They found that GHG emissions decreased by 24% compared to petroleum-derived PET when forest residue was assumed as bio-feedstock. In addition, the GHG emissions of 100% bio-derived PET using bio-based ethanol from sugar cane were reported as 1.88 kg CO2 eq., denoting a reduction of 60% versus petroleum derived PET.78 The findings of Gursel et al.79 are similar, showing that when using either wheat straw, maize, wheat or sugar beet as feedstock, the environmental impact of PET bottle production decreases as well. García-Velásquez et al.80 in turn addressed the use of local biomass sources for the production of bio-based PET. Upon addressing the transportation and import costs, they found that the design of local biomass supply chains can reduce the need for imported materials.
For completeness, it is mentioned here that the extreme case of feedstock change is the application of polymers other than PET(-like) polymers for the beverage bottle production.81 For example, Shen82 examined the use of PLA, revealing that PLA needs to be fully diverted from landfills, which is not a realistic option nowadays. Gironi and Piemonte83 in turn showed that the advantage of PLA bottles arises from the use of renewable resources, but this benefit is somewhat lost in environmental terms due to the higher impact on human health and ecosystem quality. This is because of the use of pesticides, the consumption of land, and the consumption of water for the production of the raw materials.
Overall, it can be postulated that the shift to biomass feedstock can afford some environmental advantages for PET production, only if the supply chain is carefully designed from the raw material level onwards. This again highlights the need to (i) connect the molecular and process scales and (ii) generate data for several waste generations at both the PRE and EES levels.
3. PET mechanical recycling plant configuration: units and processes
In recent decades, the mechanical recycling of post-consumer plastic materials such as PET has evolved significantly, contributing to the conservation of natural resources and the mitigation of the accumulation of landfill waste. As explained in this section, this progress has been realized by focusing on design and optimization for the complete value chain, and thus, beyond the core re-extrusion step.
As shown in Fig. 6, the mechanical recycling process is implemented at the plant level through several key steps or unit operations, aiming at transforming (post-consumer) plastic waste into reusable (polymeric) materials. One generally recognizes four main steps: (i) collection and sorting; (ii) shredding; (iii) washing; and (iv) reprocessing.84,85 However, to ensure the production of high-quality recycled materials and efficient processes, alongside quality control (QC), additional steps are often integrated alongside the main four, taking into account the implications of these additional steps in promoting process economy and environmental conservation.
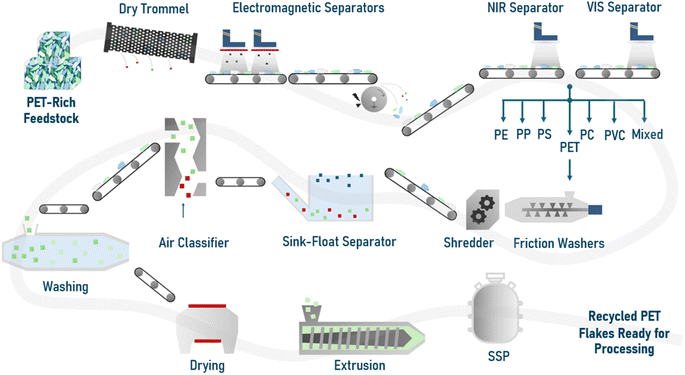 |
| Fig. 6 Key steps of PET mechanical recycling. Steps can sometimes be omitted or altered; e.g. extrusion and solid-state modification can be in a different configuration (or order). | |
In what follows, a detailed overview is given on the key steps for the industrial mechanical recycling process of plastic waste, with an emphasis on PET. It is also discussed how the process configurations align with the latest technological advancements in the field. An overview of actual commercial implementations and technologies is included in Section 5.
3.1. Collection and sorting
The recycling process of post-consumer PET begins with the collection of plastic waste from various sources, such as household goods consumption, business activities, and public areas, by waste management companies, which in turn transport them to drop-off centers and special collection and sorting facilities.86 Practically, this waste includes plastic packaging from food and beverages, personal care products, and household cleaning items, as well as plastic waste generated by for instance restaurants, retailers, and offices.
Once collected and transported to the sorting plants, the plastic waste undergoes a thorough sorting process. The plastic waste stream comprises various types of polymers along with impurities like labels and small metal pieces. Furthermore, the immiscible nature of polymers in the waste, coupled with color variations and separability issues, poses significant challenges to the sorting process. Consequently, a series of sorting techniques, crucial to ensure a high purity and quality of the input recycling stream for actual reprocessing, are employed to separate the different fractions of plastic waste, such as PET-based materials from mixed plastic waste streams.
Commonly used sorting techniques during the post-consumer PET recycling process include manual sorting (sorting type 1) as well as automatic plastic waste sorting (sorting type 2). The automatic sorting techniques can be grouped into two categories. The first one is direct sorting (sorting type 2a), which is based on variations in material properties such as density and electrical conductivity,86–88 and the second one is indirect sorting (sorting type 2b), which utilizes sensors and analysis techniques to detect feature information on the samples.87,88 Direct sorting includes methods such as mechanical sorting, air sorting, and electrostatic separation. These methods offer advantages such as low cost and high efficiency but are often limited by constraints on particle size, shape, and surface conditions. Indirect plastic sorting techniques include methods such as X-ray fluorescence (XRF), near-infrared spectroscopy (NIR) and optical sorting. These methods can separate two types of materials simultaneously with high reliability and limited pollutant emissions.89
Perhaps somewhat surprisingly, manual sorting still plays an essential role in the plastic recycling process, particularly for initial screening and the removal of large contaminants. This type 1 sorting technique involves trained workers, who visually check and separate different types of plastics that are transported along conveyor belts for inspection and segregation, based on criteria such as shape, color, and trademarks.90,91 However, this sorting technique also faces several challenges limiting the scope of its application. Manual sorting is usually a labor-intensive activity, requiring a significant workforce to handle large volumes of plastic waste effectively. This technique relies on human judgment and perception, which can introduce inconsistencies and errors in the sorting process, as workers may interpret visual cues differently, leading to variations in the sorting outcomes. Furthermore, this sorting technique can also impose significant delays in the recycling process, as workers need to inspect plastic items individually, thus affecting overall throughput and efficiency. Moreover, safety concerns are associated with manual sorting, especially upon handling sharp or hazardous materials mixed with plastic waste.82,90
The type 2a direct sorting technique relies on special automated machinery to separate plastic fractions in the waste stream based on their physical properties such as size, shape, and density. This technique can employ various mechanical (engineering) driven methods, including centrifugal force sorting, specific gravity sorting, and particle shape sorting. For instance, bowl-type centrifuges are employed during centrifugal force sorting to separate plastics according to their specific gravity, where lighter plastics move towards the outer edge while heavier plastics remain closer to the center, facilitating their separation.92,93 Specific gravity sorting is based on differences in material density, with plastics of higher specific gravity sinking while those of lower specific gravity float. This method is often used in sink–float separation units, where plastics are immersed in a fluid like water for separation based on specific gravity.87,90 As PET is relatively denser than many other plastics such as polyethylene (PE) and polypropylene (PP), it tends to sink in water while lighter plastics float, allowing for effective separation.85 Particle shape sorting in turn involves the use of equipment like screens or sieves to separate plastics based on their size and shape.
However, direct mechanical sorting also presents limitations. One major limitation is the difficulty in accurately differentiating between plastics with similar physical characteristics, which can result in contamination of recycled materials with unwanted plastics. Additionally, mechanical sorting processes may require regular maintenance and calibration to ensure optimal performance, leading to increased operational costs for recycling facilities.85,90,91
Another direct sorting technique closely linked to mechanical sorting is air sorting, also referred to as air classification or pneumatic sorting. It utilizes air streams to separate materials based on their density, size, and aerodynamic properties. In this process, lighter particles such as paper labels and debris are carried away by airflow, while heavier plastic waste falls into a separate collection bin.90 Furthermore, electrostatic separation is a direct sorting method commonly used to retrieve PET from plastic waste streams. This method exploits the differences in electrical conductivity among plastics. PET, being a relatively poor conductor of electricity, can be selectively separated from plastics like poly(vinyl chloride) (PVC), acrylonitrile butadiene styrene polymer (ABS), and polystyrene (PS). By applying an electrostatic charge to the plastic mixture, PET particles tend to be attracted to one electrode while other plastics are attracted to another, allowing for the effective separation of PET from the plastic waste stream. This sorting process contributes to environmental protection by recovering valuable raw materials from plastic mixtures traditionally difficult to separate. It is particularly useful for sorting tasks like separating PET and PVC in PET beverage bottle recycling.94
Focusing on indirect, and hence, type 2b sorting methods in the plastic waste recycling process, we find a variety of techniques, with the dominant one being XRF sorting operating on the principle of irradiating a material with X-rays to emit characteristic fluorescence pathways, enabling analysis of the elemental composition.95 In PET recycling, XRF allows plastics to be identified and classified based on their elemental composition, helping to separate PET from other types of plastics and contaminants. This technique is particularly valuable for identifying plastics containing heavy metals or elements with distinct XRF signatures.96
Another indirect sorting method widely used in post-consumer PET recycling is NIR spectroscopy. This method relies on the principle that when plastics are illuminated, they mostly reflect light in the near infrared wavelength spectrum, and different plastics reflect light differently.85 NIR spectroscopy utilizes sensors to detect and sort plastics based on their chemical composition, providing a non-intrusive approach to separate PET from other plastics. This technique enhances the sorting process by recognizing PET-based materials, thereby contributing to the overall purity and quality of the rPET stream. However, NIR spectroscopy is less suitable for dark-colored plastics, as they absorb nearly all light.
In addition, optical sorting relies on the use of optical sensors and cameras to identify and separate materials based on their visual characteristics such as color, shape, and texture. This type of sorting analysis is for instance applied to separate PET bottles from other plastics in recycling facilities by detecting the characteristic properties of these bottles, such as their transparent or translucent appearance and specific shapes. Optical sorting offers several advantages including high speed, accuracy, and automation, making it suitable for large-scale recycling operations. However, it may have limitations when dealing with plastics that have similar visual characteristics or if the plastics are heavily contaminated.
3.2. Shredding
Plastic shredding is a critical step of the recycling process for post-consumer plastic waste, including PET recycling. It serves to homogenize the material following collection and sorting. Even after sorting, PET materials vary in shapes and sizes, posing challenges for efficient handling and processing. Shredding addresses this by breaking down the materials into smaller, uniform particles that are easier to manage during subsequent processing steps.85 It offers two advantages. Firstly, it increases the surface area available for subsequent pre-treatment, such as washing, drying, or chemical treatment, which can remove contaminants and improve the quality of the recycled material.86 Secondly, shredding ensures more consistent material properties, facilitating more efficient melting during the extrusion steps of the mechanical recycling process.86
A shredder unit typically consists of a hopper, a cutting chamber with rotating blades driven by an electric motor, some sort of grid for size grading, and a collection bin.85 During operation, material is fed into the hopper and enters the cutting chamber, where rotating blades shred the material into smaller particles. These particles then pass through grids or screens, determining the final size of the shredded material or PET flakes. As a general rule, the (average) diameter of the PET flakes obtained from this processing step ranges between 0.4 and 8 mm,97 although variations are possible depending on the specific recycling technology employed.
3.3. Washing and decontamination
Following the shredding step in which PET materials are shredded into small pellets/flakes, we run into the washing and decontamination units in view of their subsequent reprocessing. During this step, the PET material undergoes thorough washing to remove impurities, residues, labels, adhesives, dirt, and other contaminants.84,85,92
The washing process may involve hot water or chemical washes to achieve a high purity. While most post-consumer waste undergoes washing, not all input material used for recycling follows this procedure. Some regrinds or agglomerates may be processed instantly without washing. The washing process typically involves the use of cold or hot water, with temperatures reaching up to 60 °C.85 Cold water usage may lead to an increased need for chemicals such as sodium hydroxide (NaOH) and mechanical energy.85 The waste water generated during washing is often treated internally for potential reuse within the facility.
Specifically focusing on the recycling of PET bottles, various methods are employed to purify the PET flakes. Washing of PET flakes commonly takes place in friction washers, which are effective and cost-efficient units that utilize heat, kinetic energy, and pressure to remove surface contaminants such as labels, adhesives, and general dirt from PET flakes. In some processes, chemical washing can also be performed, especially when heavier contamination of the PET flakes is expected. In these cases, extra washing usually is conducted in rotary washer units, with a heated caustic solution to further cleanse the PET bottles of oils and food residues. In a final step, PET flakes are rinsed thoroughly to remove any remaining detergent or chemical residues.92,98,99
Note that additional separation processes aiming at the elimination of unsuitable non-plastic materials such as paper or metals can be incorporated in the washing step. These processes involve mechanical separation methods such as sieving to filter out larger contaminants, magnetic separation to extract metallic components, and extra manual sorting to visually identify and remove remaining impurities.
3.4. Drying
After washing, the PET raw material undergoes a drying process to reduce the moisture content.100 This drying step is from a molecular point of view essential to prevent moisture-related defects during subsequent reprocessing (e.g. extrusion) steps and to ensure the quality of rPET material.13,100,101 Note that some industrial operations directly process highly wet PET material, aiming at (sufficient) chain repair later on.
The common industrial drying system for polymers, including PET, is a mechanical dewatering system using centrifugal dryers.102 Specifically, a multistage centrifuge system is recommended for the best dehumidification of polymers and the highest drying efficiency. However, centrifugal drying alone may not achieve the low moisture content required for stable extrusion. This is especially the case for flexible plastic films like PET, which tend to retain more moisture due to their thinness and different physical properties compared to rigid flakes.101
Hence, the drying process of PET may involve other methods, such as hot air drying, vacuum drying, or desiccant drying, to further decrease the residual moisture content in PET flakes from the mechanical drying step. The addition of these methods depends on the equipment available and the specific requirements of the recycling facility. If additional drying is necessary, particularly in the case of post-consumer PET, many recyclers opt for desiccant drying. In this drying technique, desiccants are used to absorb moisture from the PET flakes, usually operating at 170 °C for 6 hours before feeding the flakes to the extruder.97
3.5. Re-processing
After the sorting, shredding, washing and drying (or at least a certain number of these steps), the actual reprocessing needs to be executed. Screw-based systems are employed by default with a leading role for melt extrusion,84,86 which is a process widely used for producing pellets from purified PET flakes. In extrusion, PET flakes/grains are fed into the extruder utilizing a hopper. The PET solid material then comes into contact with a rotating screw that pushes the material forward into a heated barrel at the desired melt temperature, typically ranging from 240 °C to 280 °C. The pressure and screw design allows the plastic beads to mix and melt gradually as they move through the barrel. For finishing purposes, the molten plastic is pushed through a sieve to remove impurities, cooled, and pelletized.85,97,103
From a general engineering perspective, one needs to know the variation of the temperature and pressure to operate and design an extrusion unit (cf. boxes in Fig. 3). Preferably, one also has information about the processability, specifically the viscosity variations along the screw, in a first instance. It is critical to acknowledge that such variations are in many cases due to molecular changes because of either thermal, thermomechanical, thermo-oxidative or hydrolytic reactions. As outlined in Fiorillo et al.,13 a wide range of such reactions can be identified depending on the PET type and processing conditions, with examples of essential reaction types included in Fig. 2.
In addition, the blended nature of the extruder content can lead to less or more material heterogeneity depending on the processing history and number of recycling passes.103 A perfect macro-scale mixing is very unlikely in polymer-based systems, specifically if several compounds are present, as is inherent in PET re-extrusion, even after sorting and pre-treatment steps. In any case, the level of purity needs to be high for PET flakes, as contaminants in the extruder can potentially lead to more degradation or other degradation reactions at the high melt processing temperatures, thereby causing a too severe change in the molecular configuration in view of chain repair and application potential.104,105
As explained in Edeleva et al.,106 this complexity at both the molecular and the material level requires a multi-scale approach bridging experimental and modeling tools. As explained above, one of the most advanced modeling approaches is CMMC, in which the molecular variations of individual molecules are followed.34–36 This tracking of species is ideally done for every subunit of the processing unit, recognizing the formation of smaller molecules (e.g. volatiles), the chemical modification of (macro)molecules and the phase formation or alternation because of the presence of certain molecular features. On top of that, in CMMC, it is considered that molecules residing longer in the processing equipment will have a different molecular modification history than molecules exiting earlier.106 Hence, the coupling of molar mass and residence time distributions is considered, acknowledging variation in macro-scale mixing and temperature gradients.
As depicted in the first panel of Fig. 7 (left; a–f), taking for illustration purposes the model polyester compound poly(lactic acid) (PLA), it follows that CMMC allows the evaluation of the faith of individual molecules during consecutive extrusions, specifically two extrusions with intermediate shredding. The associated downward change of the average molar mass (number basis: Mn; and mass basis: Mm) can be compensated for upon the addition of chemicals. Furthermore, at any modification stage during the processing, the molar mass distribution (MMD) can be translated into a material property. For instance, as shown in Fig. 7 (right; g), the variation of the (apparent) viscosity as a function of the shear rate (frequency; ω), as determined experimentally via rheometers, can be predicted from the CMMC MMD input and output.
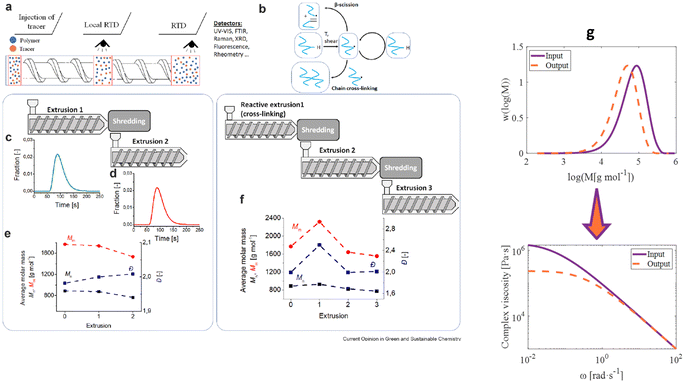 |
| Fig. 7 Potential of coupled matrix Monte Carlo (CMMC) to support the efficiency of a processing step in PET mechanical recycling, with on the left (subplots (a)–(f) as taken from Edeleva et al.,106 reproduced with the permission of Elsevier) the variation for the (c) residence time distribution (RTD) and (d) molar mass distribution (MMD; Mn/m: number and mass average molar mass; (e) and (f)) during two extrusion steps (using a tracer (a) and a typical degradation scheme (b) with poly(lactic acid (PLA) as model polyester) and on the right (subplot (g)) the translation of a CMMC simulated MMD before and after extrusion in a viscosity shear rate curve according to a Maxwell-like calculation;107 focus on the first extrusion in the first panel in the left subplot). Reproduced with permission of Elsevier© 2023. | |
It should be noted that MMDs are experimentally ideally determined by gel permeation chromatography (GPC) or size exclusion chromatography (SEC), and derived molecular properties are for instance average molar masses or chain lengths. Industrially, one typically relies on correlating MMD and/or averages to IV or MFI values.20,21 With software packages, one can close the gap by connecting chemical and material properties by direct calculations, depending on the preference of the user.
3.6. Quality control
After extrusion, the rPET pellets undergo rigorous QC checks to ensure that they meet industry targets before being used in subsequent manufacturing processes. These QC checks can be conducted at the molecular or material level, explaining e.g. the offline measurement of the average molar mass of rPET pellets as well as the measurement of the color, purity, and other relevant physical properties.
The measurement (or assessment) of molar mass properties for the (r)PET pellets involves techniques such as IV determination, viscometry and gel permeation chromatography (GPC). Furthermore, visual inspection and colorimetry or spectrophotometry are employed to maintain consistency and adherence to specified color standards. rPET is also analyzed to detect and quantify any possible remnant contaminants or impurities from the recycling process, usually achieved by means of rapid and non-destructive analytic techniques such as Fourier-transform infrared spectroscopy (FTIR) or NIR spectroscopy. Physical properties such as tensile strength, elongation at break, flexural modulus, and impact resistance can be additionally evaluated through (ISO) standard mechanical testing methods to ensure that rPET pellets meet mechanical requirements.92,108,109
Specifically, so-called functional performance tests can be included to assess how well rPET performs in certain applications. These tests evaluate the bottle strength, barrier properties, heat resistance, chemical resistance, dimensional stability, and compatibility with other materials.72,73,110 The QC measures ensure that rPET pellets meet the specific requirements and performance criteria for their intended applications, ensuring the overall quality and suitability of rPET materials in various industries.
3.7. Additional processing steps
Next to the aforementioned more standard PET mechanical processing steps (Section 3.1–Section 3.6), additional steps can significantly improve the quality of recycled materials to ensure optimal performance for various industrial applications while meeting industry targets. This subsection discusses the potential of several steps aimed at enhancing the quality of rPET, including (i) devolatilization to remove volatile contaminants or substances from the molten polymer and (ii) liquid/solid-state polymerization or polymer modification (reactive processing)111 to increase the average molar mass and to improve properties such as strength, durability, and thermal stability of the rPET material.
3.7.1. Devolatilization.
The primary focus of devolatilization is the removal of volatile contaminants, mainly volatile organic compounds (VOCs) or substances, including residual moisture from the molten polymer to enhance the quality of the recycled materials. This devolatilization is typically integrated into the overall recycling process stream and can occur at different stages, depending on the technologies used.
Practically, devolatilization takes place mostly during the extrusion of rPET through a vacuum-assisted devolatilization process.112,113 This technology employs vacuum systems to remove VOC contaminants from the molten polymer during extrusion. Specific venting zones are incorporated into the equipment to aid in VOC removal. Additionally, devolatilization during vacuum-assisted extrusion can be further enhanced by using various stripping agents to remove additional undesired contaminants.
The main function of these stripping agents is to generate bubbles inside the polymer bulk, and thus, to increase the free volume in the molten polymer and, consequently, to facilitate diffusion of the VOCs dissolved in the polymer matrix to the vapor phase.112 Selecting the right processing conditions, including pressure control and stripping agent design based on for instance the boiling point and polarity, is crucial for effectively removing volatiles. Stripping agents therefore vary from low-boiling-point solvents to steam or supercritical gases such as carbon dioxide (CO2).114,115
Other technological options aiding in devolatilization, alongside vacuum-assisted devolatilization, include the use of reactive extrusion (REX).96,116 In REX, chemical reactions are integrated into the extrusion process to convert VOCs into less harmful and easier-to-remove compounds, at least if a proper injection pattern is applied.117 Additionally, solid-state polycondensation118 as discussed in the next subsection assists in devolatilization by driving off volatile contaminants during the process.
Some recycling technologies may also incorporate devolatilization as part of the washing and drying stages before extrusion, effectively addressing some of the volatile contaminants early in the production process. By removing volatile contaminants and moisture before the material enters the extrusion process, the molten PET should be cleaner and of higher quality, potentially requiring less stringent purification during the extrusion phase. The inclusion of devolatilization before extrusion has thus the potential to streamline the mechanical recycling process by reducing the need for additional purification and reconditioning steps for rPET.
3.7.2. Solid-state modification.
Solid-state reactor units can be integrated into the mechanical recycling production process as an additional step after the initial recycling process. These units aim to enhance the properties of rPET material by increasing its average molar mass through solid-state polymerization. Specifically, the PET material is subjected to heat and vacuum conditions in a solid-state reactor at a temperature above the glass transition temperature of the polymer. This process promotes the extension of the molecular chains to improve mechanical properties (e.g. stiffness, strength, and impact resistance) as well as thermal properties.119,120
Solid-state polycondensation (SSP) temperatures typically range from 170 °C to 220 °C,118,121 with the material entering the SSP process ideally having a certain level of crystallinity, e.g. around 40%.121 This level of crystallinity is typically achieved through pre-crystallization steps using nitrogen fluxing at lower temperatures, around 140 °C. Once crystallization is achieved, the temperature is raised to facilitate esterification and transesterification reactions, leading to an increase in the average polymer molar mass. The initial PET material should also meet suitable IV values to ensure a successful SSP process, likely in the range of 0.68 dL g−1 to 0.8 dL g−1.121,122
Typical residence times for SSP can vary widely but are normally several hours, with specific durations depending on factors such as temperature, the desired increase in average molar mass, the extent of crystallization required, and, generally speaking, technological specifications or limitations.118,121,122 The pressure during SSP can vary, with some processes conducted under vacuum conditions to remove subproducts and minimize degradation, while other recyclers may involve the use of inert gases like nitrogen as a carrier gas. The use of vacuum during certain stages of SSP helps to enhance the efficiency of the reaction and remove volatile components.118,123
In case the SSP residence time is too high or the cost of the actual unit is excessive, one could opt for REX but keep the melt temperature not too high, e.g. between 260 °C and 280 °C.124,125 A chain extender such as pyromellitic dianhydride (PMDA) can be used, aimed at a uniform distribution within the PET matrix.126 Also, here residence time control is still needed as a longer reaction time could imply more side effects, seeing the higher temperature of the melt, overruling a stronger consumption of the chain extender. Compared to SSP, REX offers a faster and more economical alternative, utilizing existing extrusion infrastructure, but it typically does not achieve the same IV increase as SSP and is thus likely more suited for applications for which moderate improvements in molar mass increase are sufficient.127,128 In principle, REX could also be combined with SSP.
3.7.3. Liquid state polycondensation.
Liquid state polycondensation (LSP) represents an innovative technology within the mechanical recycling of PET, designed to convert post-consumer PET into a high-quality recycled material, complementary to SSP. This method takes advantage of the inherent propensity of PET to participate in condensation reactions under specific conditions, particularly if exposed to a vacuum in the melt or in general a liquid phase.
During the LSP process, PET flakes are subjected to elevated temperatures and vacuum conditions in the presence of a catalyst, typically an antimony compound,114,115 which promotes polymerization. As a result, the PET flakes melt and react to form longer polymer chains, thereby increasing the average molar mass of the material. This increase in average molar mass significantly enhances the mechanical properties of rPET, including its strength and durability.
The LSP process typically takes place within a reactor vessel, in which the PET flakes undergo heating under vacuum to eliminate volatile contaminants or by-products. Rigorous monitoring of the reaction parameters, such as temperature, pressure, and reaction time, is essential to ensure that the desired average molar mass and properties of rPET are achieved.
4. Commercial mechanical recycling technologies
As explained in Section 3 and summarized in Fig. 6, PET mechanical recycling plants are based on connecting four main steps, i.e. collection and sorting, shredding, (hot) washing, and reprocessing, complemented by additional steps such as devolatilization and solid-state modification.129 All these steps can be further grouped into three main categories, namely (i) pre-processing, including collection, sorting, shredding, and (hot) washing; (ii) processing, which is primarily extrusion-based and involves melting and pressurization combined with vacuum degassing and melt filtration; and (iii) post-processing, which includes additional steps such as solid-state modification and dealdehydation.129
In the present section, examples are given of relevant commercial technologies according to these three categories and the detailed principles outlined in Section 3. Complementarily, Table 1 presents a market oriented overview of more processing-like technologies with the main emphasis on their advantages, challenges, and claimed conversion rates. Specific energy consumption values for every recycling technology are given, which indicate the amount of energy required for the production of 1 kg of material.
Table 1 Overview of commercial recycling technologies and claimed efficiencies for PET mechanical recycling as e.g. reported by the European Food Safety Authority (EFSA); table continued on the next page(s)
Recycling technology |
Significances of technology |
Specific energy consumption [kW h kg−1] |
Claimed decontamination efficiency |
Applications |
Implemented amongst for instance |
References |
Includes the manufacturing of water bottles as specifically reported by the European Food Safety Authority (EFSA).
|
EREMA MPR B2B |
The vacuum reactor removes moisture, decontaminates, and dries flakes for extrusion, while also compacting and buffering the material to produce flakes with an output of up to 2000 kg h−1. No significant increase in IV values |
0.1 |
94.6–99.1% |
Up to 100% rPET for food packaging articles with or without hot-fill |
Alimpet (IT) |
130–132
|
VACUREMA basic technology |
Decontaminated flakes (max. 1.5% moisture content), with high purity, are directly fed into a single-screw extruder, eliminating the need for degassing, resulting in improved color values and minimal AA levels. IV increase up to e.g. 4% with output capacities reaching 4000 kg h−1 |
0.25–0,28 |
92.4–98.4% |
Less than 100% rPET for mostly thermoforming trays |
Buergofol (DE), ONDUPET (ES), RE-PET (DE) |
133–137
|
96.3–99.8% |
Up to 100% rPET for food packaging articles with or without hot-fill |
STF recycling (DE), NAN YA PLASTICS (TW), Utsumi (JP) |
133 and 138–144 |
VACUREMA advanced technology |
The vacuum crystallization dryer pre-dries and decontaminates the input material before feeding it into VACUREMA basic technology, ensuring a short residence time in the extruder due to its high decontamination efficiency. IV increase up to e.g. 6% |
0.28–0,31 |
94.6–99.1 |
Up to 100% rPET for food packaging articles with or without hot-fill |
Texplast (DE) |
133 and 145 |
Vacurema prime technology |
Two parallel vacuum crystallization dryers enhance output before processing with VACUREMA basic technology. IV increase up to 10% with adjustable dwell times to control decontamination efficiencies. Throughputs up to 4700 kg h−1 possible |
0.30–0.34 |
98.3–99.9 |
Up to 100% rPET for food packaging articles with or without hot-fill |
Jasz Plastik Kft (HU), Coca-Cola HBC Polska (PL), Fa. Enkador S.A. (EC) |
133 and 146–154 |
RecoSTAR FG(+) |
Multiple drying units decontaminate PET flakes, with an extruder featuring a degassing unit and a melt filter for increased efficiency, while water cooling controls crystallinity. RecoSTAR FG+ offers more IV increase compared to RecoSTAR FG due to the SSP process |
0.40–0.53 |
90.9–more than 99.9% |
Up to 100% rPET for food packaging articles with or without hot-fill |
Poly recycling AG (CH), Texplast (DE), Esterpet (Gb), Hiroyuki Industries (Jp) |
155–160
|
RecoSTAR PET iV (+) |
Utilizes an SSP reactor at the end of the RecoSTAR FG(+) setup to enhance the IV values of PET pellets. RecoSTAR iV+ claims to reduce AA and VOC levels to a minimum compared to RecoSTAR iV |
0.25–0.35 |
95.9–98.7% |
Up to 100% rPET for food packaging articles with or without hot-fill |
Poly recycling AG (CH), ester industries (IN) |
155–184
|
|
|
|
|
Up to 100% rPET for food packaging articles with or without hot-filla |
Alef recycling (NG), Duy tan plastic recycling (VN) |
169, 175, 182 and 185–194 |
Starlinger deCON(iV+) technology |
Preheated PET flakes are fed into a SSP continuous reactor at high temperature using a combination of vacuum and inert gas flow. Depending on the configuration, output can reach 2000 kg h−1. This technology offers promising decontamination efficiencies of 96.4% for benzophenone |
0.10–0.15 |
96.4–99.5% |
Up to 100% rPET for food packaging articles with or without hot-fill |
Veripack Embalajes (ES), Ferrarelle (IT), Pinaform (ES)… |
195–225
|
Starlinger PET direct iV+ technology |
Washed and dried flakes undergo extrusion, filtration, and crystallization in a water bath, followed by additional decontamination and improvement of the IV value in subsequent vacuum and SSP reactors. No pre-heating step before extrusion is needed |
0.20–0.35 |
98.8–more than 99% |
Up to 100% rPET for food packaging articles with or without hot-fill |
Dentis recycling Italy (IT), DY Polymer (KR), EcoBlue (TH) |
226–231
|
Polymetrix pellet technology (stand-alone) |
Washed and ground PET flakes undergo extrusion, followed by crystallization and polymerization in a crystallization reactor and SSP reactor, respectively, with the entire process utilizing an inert gas for enhanced decontamination, yielding pellets as output (up to 1100 t d−1) which can be used for B2B, yarn production or other PET recycling purposes |
Not specified |
95.9–more than 99% |
Up to 100% rPET for food packaging articles with or without hot-fill |
MOPET (DE), NOVAPET (ES) |
232–234
|
100% rPET for food packaging articles with or without hot-fill |
PT Veolia Indonesia (ID), Plastrec (CA) |
235 and 236 |
Vacunite technology |
Combines both the EREMA basic technology (first) and the Polymetrix pellet technology (second). AA levels remain under 1 ppm after processing |
0.35 |
97.1–99.8% |
Up to 100% rPET for food packaging articles with or without hot-fill |
SGR (FR), RCS plastics (DE), Renovatpet (ES) |
237–244
|
100% rPET for food packaging articles with or without hot-filla |
Veolia Huafei polymer technology (CN), Plastibak Iberia (ES) |
245–252
|
Bandera twin PET technology (HVTSE) |
Decontamination is efficiently achieved in a degassing twin-screw extruder, saving energy by eliminating the need for pre-treatment and operating at low pressures. Production up to 5 t h−1 with a low IV drop due to the use of a twin-screw system |
0.21 |
97.4–99.98% |
Up to 100% rPET for food packaging articles with or without hot-fill |
AMB (IT) |
253 and 254 |
Bandera PURe technology |
PET flakes are pre-conditioned with microwave devices, air treatment, vacuum pumps and protection filters to improve decontamination efficiency, often followed by HVTSE technology |
Not specified |
95.6–99.7% |
Up to 100% rPET for food packaging articles with or without hot-fill |
Aristea (IT), Roboplast (IT), Arcoplastica (IT) |
255–257
|
SML technology |
Virgin and post-industrial CW are combined with washed PET flakes, dried using IR-dryers and air dryers, and subsequently decontaminated and degassed in a single-screw extruder before further processing |
Not specified |
90.9–more than 99.9% |
Up to 50% rPET for water bottles |
SML Maschinengesellschaft (AT) |
258
|
Up to 80% rPET for general articles |
Up to 100% for food trays |
NGR technology |
MeltState polymerization transforms the polymer into strands, enhancing the surface-to-volume ratio and allowing for significant increases in IV values. Decreases processing times and operating costs significantly with output up to 3 t h−1 |
0.12–0.40 |
96.5–more than 99.9% |
Up to 100% rPET for food packaging articles with or without hot-fill |
Indorama Ventures recycling Verdun IVRV (FR), Wellman Neufchateau Recyclage WNR (FR) |
259–265
|
Kreyenborg IR CLEAN+ technology |
Sorted, washed, and ground flakes are infrared-heated with controlled air flow, desiccant-dried for further decontamination, without extrusion, yielding flakes as output |
Not specified |
95–more than 99.9% |
Up to 100% rPET for food packaging articles with or without hot-filla |
AR packaging flexibles (SE), Paccor Polska (PL), Amhil Europa (PL), Petainer Lidkoping (SE) |
266–269
|
Reifenhäuser technology |
Washed and dried flakes are fed continuously into an extruder which decontaminates the material by atmospheric degassing and vacuum pump degassing |
Not specified |
68.7–more than 99.9% |
Up to 100% rPET for articles which have to be stored at relatively low T |
Silver plastics (DE) |
270
|
Up to 75% rPET for confectionery packaging |
Up to 55% rPET for fruit and vegetable packaging |
Up to 15% rPET for cake, donut and chocolate packaging |
For completeness it is mentioned here that the current section does not aim for a complete listing of available (commercial) technologies but wants to illustrate for the general reader that several approaches exist with a limited link to the actual molecular changes taking place. Such changes are mostly only studied to a limited extent at a higher TRL.
4.1. Pre-processing commercial technology
Pre-processing (commercial) technology is mainly devoted to the development of (i) cleaning processes and (ii) sorting processes. Cleaning processes typically involve the removal of foreign impurities (e.g. wood, dirt, dust, labels, glass, and metal) from the recyclable streams, ensuring the quality of the infeed material in the actual recycling process. This cleaning step often employs techniques such as (caustic) washing in a NaOH water solution.129
Commercial cleaning technologies such as the MetaPure W-PET by Krones AG271,272 combine a pre-cleaning step with caustic washing and float–sink separation for optimal results. It is claimed that this washing technology ensures cleaner flakes with a high usability for high quality final shaping such as fibre production, film blowing and injection moulding. The process water can also be reused by the consideration of an integrated water cascade.
Furthermore, the Amut Group makes use of continuous wet grinding and (hot) friction washing in a way that the flakes are subjected to intense non-destructive friction actions at high temperature to elevate the quality of the flakes.273 Reg-Mac offers in turn washing solutions for all kinds of materials with their MINI/MIDI/MAXI technologies, accompanied by friction washers, float–sink separators and washing/drying centrifuges.274 Sikoplast claims to have developed a recycling unit, which consists of a washing stage based on caustic washing, friction washing, and sink–float separation, which ensures PET BtB recycling with a low energy consumption (<0.4 kW kg−1) and a closed-loop water recycling.275–277 NEUE HERBOLD GmbH is another example of a manufacturer that offers, among others, washing (e.g. IW/FW Series or TB Series) and granulation (e.g. LM Series, SX Series) technologies for contaminated bottles/containers, packaging materials and agricultural films.278,279
Sorting processes are equally important compared to cleaning processes, as they categorize materials based on their type, color and quality to further enhance the recycling effectiveness. Industrially, this step often employs sorting techniques such as magnetic separation, air classification and sensor-based sorting, e.g. FT-NIR spectroscopy or ultraviolet spectroscopy (VIS).
At the commercial level, TRENNSO-TECHNIK®279 is for instance specialized in the development and implementation of dry sorting technologies such as wind sifter technology (e.g. 3 ZZS Wind Sifter Technology or QSS Cross-Flow Sifter) and screening technology (e.g. SIK/SIS Series and TSM/RSM Series) to sort out the incoming waste stream based on their weight and shape. Complementary, the SPALECK GROUP offers a range of screening solutions to sort out co-mingled recyclables.280,281 Other dry separation solutions are found in the WESTERIA catalogue, which features advanced wind-sifter technologies (e.g. AirStar® and AirLift®) reaching throughputs up to 400 m3 h−1 with belt speeds up to 3 m s−1 and belt widths up to 3000 mm, as claimed by the manufacturer.282
Furthermore, optical solutions for mechanical recycling such as SORTEX®A, SORTEX® and SORTEX®N PolyVision technologies developed by the Bühler Group can offer optical sorting solutions to detect same-in-colour contaminants such as PVC, PP, PE, and PS as well as rubbers and silicon.283–285 Other manufacturers such as the Amut Group rely on metal detection, VIS/NIR detection techniques and dedusting to ensure a claimed concentration of less than 150 ppm of foreign particles, e.g. PVC, polyolefins, paper, glue or metals.273
TOMRA in turn developed flexible sorting technologies286 based on color sorting (e.g. AUTOSORT™ FLAKE or INNOSORT™ FLAKE), considering mass and density variations (e.g. AUTOSORT™ SPEEDAIR), depending on the nature of the material (e.g. X-TRACT™ for wood or COMBISENSE™ for grey metal sorting). MSORT and GSORT Technologies developed by MOGENSEN in turn deal with electro-optical sorting technologies, using X-ray and NIR, to sort out plastics from rough waste streams, which contain glass, salts and rocks.287,288 The manufacturer claims a sorting accuracy of up to 99.9% with low operation costs and detections of up to 25
000 particles per second. In addition, Wagner Magnete offers a wide range of (electro)magnetic solutions for (non-)ferro separation. Their Eddy Current Separator lines (e.g. Series 0438) consist of a neodymium magnet with working widths up to 3000 mm, belt speeds up to 2.8 m s−1 and rotor speeds up to 3000 1/min, as claimed by the manufacturer. Their overbelt separators (e.g. Series 0452) should be able to remove iron particles up to 250 mm from all kinds of waste streams, which are claimed to be robust and reliable.289
4.2. Commercial processing technology
As explained above, the workhorse of the mechanical recycling plant is the extrusion unit, in which the polymer is molten and brought to a recycled pellet or granulate in view of further shaping into an actual application, e.g. a film or injection mould part. Innovation lies in (i) the connectivity of the extrusion step to the pre-processing, finishing and performance actions as well as (ii) the model-based design of the overall energy consumption and molecular modification during each remelting step. In what follows some commercial examples are given in which the first type of innovation has been applied, highlighting the current overall process design in which the overall processing unit part is embedded in a suited benchmark framework.
At the commercial level, particularly for PET BtB mechanical recycling, BoreTech e.g. offers a complete bottle to bottle recycling plant approach for the conversion of post-consumer PET bottle bales into food grade rPET pellets.290 This manufacturer offers a washing line for decontamination and sorting, a pelletizing line for pelletization combined with a continuous SSP line. SIPA's XTREME Renew on the other hand offers preform moulding technologies with claimed lower injection pressures, melt stresses and IV drops throughout the moulding process.291 Sophisticated cameras and optical pyrometers allow inspection for visual defects such as bubbles, scratches and black specks, facilitating the output quality, which can contain up to 100% rPET. Its fully electric automated system enables a completely oil-free environment both for the end product and the operators. Additional systems such as XTREME SINCROCUBE or XTREME RENEW SINCROCUBE can further automate the moulding process.292 SOREMA Plastic Recycling Systems claim to offer complete PET BtB systems, which transform post-consumer PET bottles (curbside selective or deposit) into high quality recycled flakes (rPET) to be used in (food-grade) bottles, sheets, fibers and strappings.293
Additionally, SACMI developed Injection Preform Systems (e.g. IPS300 and IPS400 Series), which allow for reprocessing of rPET pellets or flakes up to 100% and 50%, respectively, with a throughput of up to 1220 kg h−1 with up to 144-cavity moulds. Add-ons (e.g. FLOW+ or COOL+) improve the thermal efficiency, shorten cycle times, decrease melt stress, and contribute to acetaldehyde (AA) reduction.294–296
Sikoplast Recycling Technologies in turn commercialized the so-called in-line SIKOREX extrusion system, which is developed for the nonwoven industry, in which edge strips, from a previous manufacturing process, are drawn in line and are converted into a melt during extrusion.276 Since no preliminary shredding is required, the load on the material is lowered and no milling dust is generated. Furthermore, INTAREMA® FibrePro offers fibre-to-fibre recycling with fibers containing up to 100% rPET.297 The developers claim that this technology can produce fibers characterized by a dtex number of 2 and an increased IV value of up to 0.25 dL g−1, while cleaning the fibres from spinning, texturizing and additive oils.
4.3. Additional commercial processing technology
Commercial technology has also been developed in view of additional processing steps, aiming at chain repair and molar mass alternation or in general chemical modification. For instance, commercial LSP systems such as P:REACT®116 developed by Next Generation Recyclingmaschinen GmbH (NGR) aim to control IV values and output quality. It has been claimed116,118,298 that one of the main advantages of the LSP process lies in its versatility to accommodate a wide range of input materials and mixture ratios, thereby conferring flexibility and adaptability to the recycling process. Moreover, LSP facilitates decontamination of the PET material, rendering it more suitable for food contact applications.
Another example of an interesting commercial LSP technology is LSPLINE®,121 aimed at bolstering the efficiency and efficacy of PET recycling processes. The reactor design and control and focus on energy efficiency should contribute to the overall challenge of a higher throughput, IV enhancement, and an increased purity of rPET materials.
Overall, it thus follows that PRE-LCA connections are not really standard in commercial technology comparisons. As explained in Section 2 by improving the connection of lower and higher TRL activities, a better appreciation of a given technology or a combination of technologies is within reach. Particularly, a model- or data-based comparison recognizing molecular and process scale variations will facilitate the interpretation of industrial data compared to the lab scale developments and enable systematic analyses based on more well-defined waste streams.
5. Contamination during PET mechanical recycling
The presence of contaminants in PET materials and their processing poses a significant challenge for the industrial realization of optimal mechanical recycling procedures and decision making. If the contamination level is significantly increased, one likely encounters issues regarding the attainable degrees of purity and product quality, with potentially adverse effects for the physical integrity and suitability for applications.122,123 Additionally, the presence of contaminants imposes potential risks to the health of consumers, specifically if these materials are used in items manufactured as food storage devices.299–301
The PET contaminants can originate from various sources throughout the production and lifecycle of the PET material. They may include chemical residues from PET production and processing, and contamination products during contact with food or other substances, and even during recycling stages. Specifically, the inadequate sorting and classification of materials as well as the inefficient handling and removal of the chemicals involved in the (mechanical) recycling process can contribute to an increase in contamination levels.
The majority of contaminants are usually referred to as Non-Intentionally Added Substances (NIAS),13,302 as they are not part of the intended PET formulation, although they are found in the final (commercial) PET products. Compounds such as AA, acetone, butanone, bisphenol A, limonene, furan, benzene, styrene, and 2-methyl-1,3-dioxolane are commonly classified as NIAS in rPET, as they are not added by the industrial operator during PET manufacturing or recycling processes.302 In contrast, water (or moisture) is not considered an NIAS, although its presence can facilitate the formation of certain NIAS.13
Notably, mechanical PET recyclers must comply with standards but the legislation on PET recycling for food packaging varies and is rather limited, despite PET being one the most widely used commodity products. Table 2 gives an overview of international agencies reporting relevant standards, providing guidelines for acceptable recycling of PET for food packaging relevant for the originating countries. Many international standards adopt (parts of) well-established guidelines, such as those provided by the EFSA and the FDA.
Table 2 Overview of international agencies reporting relevant standards providing guidelines for acceptable mechanical recycling of PET for food packaging as applicable to the originating countries
Country |
Regulatory authority |
Advisory scientific body |
Relevant Standards/Guidelines for Food Contact Materials |
References |
Australia and New Zealand |
Food Standards Australia New Zealand (FSANZ); New Zealand Ministry for Primary Industries (MPI) |
FSANZ Board; FSANZ Fellows |
Standard 1.1.1; Standard 1.4.1; Standard 2.6.2; Standard 3.2.2 (Australia); Standard 4.2.1 (Australia) |
303–306
|
Brazil |
Ministry of Health (Ministério da Saude) |
Agência Nacional de Vigilância Sanitária – ANVISA |
RDC 326/19; RDC No. 91/01; RDC No. 105/99; RDC No. 51/10; RDC No. 20/08; RDC No. 105/99 |
303, 304 and 307–312 |
Canada |
Health Canada (HC) |
Health Canada (HC) |
Section B.23.001 of the Canadian Food and Drugs Act and Regulations |
313
|
China |
Ministry of Health (MOH) |
Ministry of Health (MOH) |
GB 16487; GB 31604; GB 9685-2008 |
314–316
|
European Union |
European Commission (EC); Directorate General for Health Consumers |
European Food Safety Authority – EFSA |
94/62/EC; EC (No.) 10/2011; EC (No.) 1935/2004; (EU) 2022/16; EC (No.) 1012/2006; EC (No.) 1907/2006; EC (No.) 2023/2006 |
317–322
|
Eurasian Economic Union (EAEU) |
Eurasian Economic Commission (EEC) |
Eurasian Economic Commission (EEC) |
TR CU 005/2011 |
323
|
Japan |
The Japanese Ministry of Health Labour and Welfare (MHWL) |
Food Safety Commission |
Food Sanitation Act; Voluntary Design Guidelines for Designated PET Bottles (Appendix A and B) |
303, 304, 324 and 325 |
Southern Common Market – Mercosur |
Mercosur Standardization Committee (SGT No. 3) |
Health institutes of the participating Mercosur members |
GMC Resolution No. 03/92; GMC Resolution No. 32/99; GMC Resolution No. 02/12; GMC Resolution No. 32/07; GMC Resolution No. 19/21 |
326–328
|
United Kingdom |
Food Standards Agency – FSA |
Food Standards Agency – FSA |
Packaging (Essential Requirements) Regulation 2015; Waste Regulation 2011 – England and Wales; Producer Responsibility Obligation (Packaging and Packaging Waste) Regulations 2024; the Plastic Materials and Articles in Contact with Food (Amendment) Regulations 2012 – England, Wales and Northern Ireland |
329–332
|
United States |
U.S. Food and Drug Administration – FDA |
UFSDA Science Board; USFDA Food Advisory Committee |
FDA CFR 170.39; 21 CFR 174-178; Use of Recycled Plastics in Food Packaging (Chemistry Considerations): Guidance for Industry |
303, 304 and 333–335 |
More specifically in Europe one focuses for instance on Regulation (EU) 2022/1616,275 which mandates that over 95% of the input materials must be suitable for food contact. NIAS in recycled rPET could potentially impact food safety if they migrate into food or beverages stored in containers made from this material.336 According to Annex I of the Commission Regulation (EU) No. 10/2011 substances must not migrate above Specific Migration Limits (SMLs) for food safety.318 NIAS that are not listed in regulatory frameworks must undergo risk assessment to demonstrate that they do not pose a health hazard. Compounds such as bisphenol A, benzene, and styrene are e.g. recognized as substances of concern under the Global Harmonized System (GHS) for the classification and labeling of chemicals.336–338 Benzene is classified as a carcinogen (category 1A) and a mutagen (category 1B). Bisphenol A is classified as a reproductive toxin (category 1B), and styrene is classified as a reproductive toxin (category 2).302,339–341 These classifications raise significant concerns about the presence of these substances in materials used for food contact.
The concerns surrounding the presence of NIAS in PET products are amplified by the possibility that these substances might not be regulated or monitored as rigorously as intentionally added substances, posing further challenges in defining specific limits for NIAS in food contact PET containers.302,342 Hence, it is essential to identify the key steps in the mechanical recycling process and the PET life cycle where NIAS and other contaminants are generated.
Mechanical recycling steps such as shredding, melting, and extrusion can all result in the generation of contaminants in post-consumer PET,299,300,302 highlighting the need for systematic evaluations supported by PRE and LCA connections. In each of these steps, the thermal history, moisture contact, oxygen exposure, and mechanical stress variation can induce degradation within the polymer matrix, leading to the alteration of the molecular structure of the PET chains.13,342,343
As explained in Fiorillo et al.,13 molecular variations are likely first taking place for the ester bonds during re-processing, with the formation of smaller molecules (e.g. NIAS) in follow-up reactions.300,344 Residual foreign polymeric materials such as polyolefin material can undergo decomposition during PET reprocessing as well, further contributing to the accumulation of NIAS in the recycled material. In addition, PET can be mixed with polyesters not being PET, e.g. so-called copolyesters, defining other degradation pathways and rates, as also explained in Fiorillo et al.13 In more detail, the degradation of PET chains during recycling processes leads to an increase in the concentration of functional end groups such as carboxylic, carbonyl, and hydroxyl groups, as well as (conjugated) double bonds and aromatic compounds within the PET matrix. These newly generated chemical moieties act as chromophores, affecting the interaction of the polymer matrix with light inducing color changes or discoloration for rPET. These alterations in color can further impact the suitability of rPET for the desired applications, as in practice one requests certain esthetical features regardless of the application, particularly the mechanical properties.
Hence, the unavoidable presence and generation of NIAS at the industrial level emphasize the complexity of the recycling process starting from the molecular level and highlight the industrial demand for dedicated research on NIAS in view of the PET recycling potential and design. Consequently, understanding the nature and impact of contaminants, coupled with stringent control and assessment throughout recycling, is crucial to ensure the effectiveness and structural integrity of rPET for various applications, particularly regarding safety for materials intended for food contact. A too large contribution of contaminants can have a too strong impact on the process efficiency. It can e.g. lead to a too pronounced reduction of the process yield, can result in equipment damage, and can lower the product quality; for instance, the mechanical properties, visual characteristics and aesthetic appearance become less.
This section aims at a comprehensive overview of the various types of contaminants (including NIAS) encountered during PET recycling, their possible sources and the maximum acceptable contents of these contaminants in rPET, taking into account current regulation measures and standards. Additionally, it explores potential strategies to mitigate their prevalence and adverse effects.
5.1. Contaminant types, their impact and mitigation strategies
Contaminant classification of PET materials can be done in different ways, depending on the complexity and diversity of these materials and the perspectives on the performance, disposal and reuse. These classifications serve specific purposes aligned with the main points of interest of the relevant parties, including scientists, engineers, recycling facility managers, regulatory bodies, and public health authorities overseeing the production, recycling and use of these materials.
These classifications provide different views on the chemical composition, the sources, the impact on product quality and the ease of removal of contaminants during recycling processes. For instance, if the focus is on the origin or composition of the contaminants, they can be classified as organic and inorganic contaminants.345 Alternative categorizations deal with evaluating the effects of contaminants on the physicochemical properties of the material and their complicated interactions within the processing units, especially during the recycling process. This leads to their classification as physical or chemical contaminants.346,347 Additionally, contaminants can be classified in four ways from a more process level point of view, considering both intentionally and unintentionally added substances. The first category consists of here intentionally added contaminants or physically attached items to PET bottles.348 They include closures (e.g. high density polyethylene (HDPE), PP, and metals), label substrates (e.g. paper, PS, PVC, and hybrids), inks, glues, dyes, and pigments added to color PET, as well as additives for extra property control (e.g. AA/oxygen scavengers and UV blockers).348–351 The second category consists of food and beverage residues, being residues from the original contents of PET bottles, including non-food products such as shampoo.348,349,352 The third category consists of intentionally added contaminants during the flake washing process, being for instance metals and minerals from tap water, sodium/potassium hydroxide, soaps, and surfactants.129,353 The fourth category consists of high-density contaminants that cannot be removed by flotation at recycling facilities. Examples are (Si-based) dust, metals (e.g. tin-plated steel and aluminum), PVC, styrenics, polycarbonates, silicones, and other polyesters than PET.16,349,354
It is thus not surprising that the description of (process) contaminants and NIAS for PET recycling is not that well-defined with even classifications overlapping each other.348,349 Consequently, in this subsection, we aim to create a more uniform contaminant classification reference. Our goal is to emphasize the interactions of PET contaminants with the processing and handling (e.g. pre-treatment and finishing) units throughout the recycling process, while exploring the potential impact of these contaminants on material properties and performance. We differentiate between the contaminating contributions of moisture, labels/adhesives, particulate contaminants, polymers (e.g. in bottle caps), pigments/dyes, ortho-phthalates, heavy metals, bisphenol A, and VOCs. Note that most categories considered can be seen as NIAS but not all.350,355
5.1.1. Moisture.
One of the main challenges encountered during PET recycling is related to its hygroscopic nature and its potential to absorb moisture, due to the ester and hydroxyl groups embedded in its chemical structure.356 In case PET is subjected for a significantly long time to an elevated temperature during recycling for melting, the absorbed moisture can cause chain shortening through hydrolysis reactions.357 A larger extent of such reactions reduces the average molar mass, drastically altering the PET physical, chemical and mechanical properties.
Interestingly, due to the hydrolysis of PET, the formation of NIAS such as AA, formaldehyde, acetic acid, and ethylene glycol can be facilitated, as highlighted by Fiorillo et al.13,358,359 These substances are not part of the intended PET formulation and can be seen as by-products of hydrolysis. Water can thus become a double contaminant in PET recycling, as it not only degrades the polymer chains but also leads to the creation of these unwanted by-products.13,358
Likely during the recycling of PET, most of the moisture absorption occurs during the washing process.360 Hence, a mitigation strategy for downstream operations is highly recommendable. A common industrial mitigation approach to minimizing hydrolysis involves drying PET before melting and combining it with virgin PET material, antioxidants, and stabilizers.29,361,362 However, the drying process for PET has limitations, due to the strong attraction of water molecules and the polymer chains via intermolecular hydrogen bonds. Consequently, even after dedicated drying, some moisture tends to persist within the PET material. Nevertheless, if one wants to limit the number of re-processing units, the moisture content needs to be reduced to below e.g. 0.02 m% so that the material can be considered acceptable for sustainable melting and subsequent reprocessing.97 It should be reminded that one can also avoid the drying step and allow for hydrolysis to then aim at chain repair through SSP at sufficiently long time.119
5.1.2. Labels and adhesives.
On PET containers, it is common to find labels or sleeves made of materials such as low density polyethylene (LDPE), PVC, PS, and polyethylene terephthalate glycol (PETG).97 These labels and sleeves provide information about the product, its manufacturers, and the proper disposal. They are typically attached to PET containers using various adhesives, which are different in type and composition.363,364
The presence of labels and adhesives on PET containers presents significant challenges during the recycling process, leading to contamination of the recycling stream. To address this issue, removal methods involve multiple steps such as washing, shredding, and exposure to chemical solutions to facilitate their separation from PET containers.97,365
However, challenges exist for the treatment of labels and sleeves. For example, they can persist on PET bottles during sorting, resulting in a decreased rPET yield. Additionally, depending on their type, thickness, and size, they may disrupt the sorting accuracy, leading to misidentification of PET bottles as undesirables. PVC labels, in particular, pose a significant problem as they decompose during extrusion, clog extruder fillers, and cause quality issues, thereby increasing waste generation in the recycling process.97,365
The presence of labels and adhesives has a negative impact on the properties of rPET, as it affects both its mechanical characteristics and its processability. For example, some reports indicate that rPET samples, containing traces of these contaminants, show substantially decreased toughness and stiffness, as well as poor moldability and processability.364,365 Consistently, the extensive removal of these contaminants from the recycling stream has demonstrated marked improvements in the mechanical integrity of rPET. Note that three types of widely employed labels are (i) wrap-around, (i) full-wrap shrink sleeves, and (iii) plastic film pressure-sensitive labels. Each type could potentially influence the recycling process in a different manner but more research is needed to substantiate this variability.
Overall, it can be stated that alkali- or water-soluble adhesives are the preferred choice to attach labels to PET bottles.366 These adhesives aid in easier cleaning of the bottles before recycling, especially compared to non-water-soluble thermoplastic polymers commonly found in hot melts.367
5.1.3. Particulate contaminants.
During the PET recycling process external contaminants such as dust, sand or in general small particles may be present, affecting the purity of the recycling waste stream and the quality of rPET materials.129 These contaminants can come into contact with PET materials at any time in their life cycle, from the first moment that PET containers enter the market to their interaction with the target user group for a certain product. However, these contaminants also have the potential to infiltrate the recycling process during different phases of the process, including the collection phase, due to exposure to the outside environment, and during sorting and transportation. This is especially the situation if the sorting facilities or the transport units are not subject to adequate maintenance.
Like other types of contaminants, these particles negatively impact the physicochemical properties of rPET, compromising its suitability for various applications.86,129 In addition, these particles can have an abrasive effect on recycling machinery, causing wear and tear, further increasing maintenance costs and causing possible failures during the execution of the process.
It is thus necessary to maintain stringent contamination control measures and implement mitigation strategies for the removal of particulate matter contamination throughout the recycling process flow. These efforts are essential to safeguard the integrity of processing equipment, preserve the quality of rPET materials, and optimize the recycling process. Some of the control measures include technologies such as air classification, washing and rinsing, centrifugal separation, float–sink separation, electrostatic separation, surface treatment, and magnetic separation, specific to the characteristics of the particulate matter present in the PET flakes. These principles behind such mitigation measures have been described in Subsection 3.1 to Subsection 3.3 of the current contribution.
5.1.4. Pigments and dyes.
Clear PET stands as the benchmark material in applications such as bottle-to-bottle recycling, due to its transparency and capacity to produce high-quality recycled materials ideal for food packaging. Its ease of sorting and treatment during recycling, alongside its high demand in various markets and recycling streams, make PET BtB mechanical recycling economically advantageous.73 However, colored PET has also gained popularity within packaging materials, primarily for its role in enhancing brand recognition and aesthetics across diverse industries.
The incorporation of color into PET materials includes the use of color additives such as pigments or dyes during the manufacturing process.368 Moreover, color additives can come into contact with PET materials through printed ink labels added to PET containers,97 potentially leading to the migration of these additives into the recycling process. These color additives add complexity to the recycling process of post-consumer PET materials, requiring extra sorting stages and the implementation of technologies like color-sensitive sensors and spectroscopy to promote an effective separation of the different PET fractions based on their colors. Such a sorting strategy aims at mitigating the impact of these color additives on the quality of rPET and its potential applications.
The color additives used in PET, namely pigments and dyes, differ significantly in their interaction with the PET material. Pigments consist of solid, insoluble particles, either organic or inorganic, that are incorporated into the PET resin during production. These solid particles remain suspended in the PET matrix, producing opaque or semi-opaque colors.369,370 Conversely, dyes are soluble substances that have the ability to permeate the PET material, providing it with transparent or translucent color effects. However, dyes may have limitations in their solubility within PET and tend to be less durable than pigments, often fading over time.370 As a result, pigments are more commonly preferred as color additives in PET manufacturing for their superior durability and final product visual effects.
Titanium dioxide (TiO2) can be seen as one of the most frequently employed pigments in the production of PET, primarily utilized to provide a white or opaque color to the material. However, a significant concentration of TiO2 in PET (e.g. above 1.5 m% (ref. 226)) has been noted to affect the material visual attributes, while also compromising its mechanical behavior. The significant presence of TiO2 in PET seems to specifically influence the fracture behavior, potentially affecting both crack initiation and propagation, especially under conditions of physical aging such as those encountered during the daily use of PET containers.371,372
One example of a widely used dye in PET materials is anthraquinone blue.373 This dye provides bright colors and resists fading through interactions with the PET matrix, achieving consistent and uniform coloration. This offers significant advantages in visual appeal and product differentiation. However, anthraquinone blue, like other anthraquinone dyes, can pose environmental risks due to its persistence and potential to leach into soil and water bodies. This can adversely affect aquatic ecosystems and contribute to long-term environmental pollution.374
Moreover, this type of dye can degrade during recycling and form potentially hazardous substances such as benzene and formaldehyde, known carcinogens classified as Category 1A and Category 1B by the European Chemicals Agency (ECHA), respectively.339,375 Other byproducts may include quinones or hydroquinones, which have toxic and potentially carcinogenic properties. Additionally, anthracene and polycyclic aromatic hydrocarbons (PAHs) can be formed from the thermal degradation of anthraquinone dyes. These byproducts pose significant health risks and necessitate stringent monitoring and control measures during PET recycling to mitigate their occurrence.376
5.1.5.
Ortho-Phthalates.
Ortho-Phthalates are esters of phthalic acid commonly added to polymers as plasticizers to improve their mechanical properties, making them suitable for various applications including beverage containers, packaging materials and other plastic products.377 Different types of ortho-phthalates have been found in PET materials/bottles such as diethylhexyl phthalate (DEHP), dibutyl phthalate (DBP), benzyl butyl phthalate (BBP), diisobutyl phthalate (DIBP), and diisononyl phthalate (DIP).378–383
Notably, ortho-phthalates are not covalently bonded to the PET matrix, which makes them prone to migrating out of the PET materials, especially when these are exposed to high temperatures or are in contact with liquids, such as acidic beverages, during prolonged use.379,382 This propensity for migration from PET materials has raised significant concerns, due to the potential health risks associated with their ingestion such as endocrine disruption, kidney and liver problems as well as developmental problems and adverse effects on reproductive health, specifically in vulnerable populations such as infants and pregnant individuals.379,380,383
For PET bottles, additional complications associated with their continued reuse have been reported, as structural changes may occur from an amorphous to a more crystalline matrix. This contributes to the release of microscale PET flakes or particles from the bottle, potentially increasing the ingestion of ortho-phthalates along with the beverage contained in the bottles.377
5.1.6. Heavy metals.
Another category of contaminants often found in PET products comprises heavy metals such as nickel, chromium, cadmium, antimony, and lead. While in most cases these metals are not deliberately added to PET (in high concentrations), they can infiltrate the material during the manufacturing and recycling processes. Their presence in PET products raises significant concerns, due to their recognized toxicity and potential adverse effects on human health.384,385
In general, there are various sources responsible for the contamination of PET with heavy metals such as synthesis additives, labels, adhesives, inks, and debris introduced during transportation and sorting processes. Moreover, heavy metals can initiate chemical reactions within the polymer matrix, leading to a decrease in the PET average molar mass, compromising the mechanical properties. This contamination not only raises health concerns but also diminishes the efficiency of the recycling process of PET, thereby impacting the sustainability and viability of reusing PET materials.384
One of the main concerns about the presence of heavy metals in PET products, either from virgin or recycled sources, is related to the antimony (Sb) content, as it is a residual element from the catalyst used during the polymerization of PET. The migration of Sb from PET bottles into contained liquids such as water or drinks depends on the residual amount remaining in the polymer, the type of food (e.g. aqueous, acidic, high alcohol or high fat), and the IV of the polymer.386,387 An increased temperature and extended storage period can also promote leaching of Sb from PET bottles into contained liquids, exacerbating health concerns.385,387
It should be stressed that the use of Sb is approved and contemplated in Regulation (EU) No. 10/2011 for use in manufacturing plastic materials that come into contact with food, provided that its SML does not exceed 0.04 mg kg−1.274 However, instances have been reported where Sb has been found in PET products at concentrations ranging from 200 to 300 mg kg−1.388 Sb poses potential health risks, including skin irritation, respiratory problems, and gastrointestinal issues, even at trace levels.389 Furthermore, according to the ECHA database, antimony trioxide (Sb2O3), the typical form of Sb found in PET, is classified as a Category 2 carcinogen and as a Category 2 substance for Specific Target Organ Toxicity-Repeated Exposure (STOT-RE), indicating that it can cause damage to the lungs through prolonged or repeated exposure.390,391
Beyond Sb, concerns persist regarding the leaching of other metals such as nickel, chromium, cadmium, and lead from PET products into consumables. For example, the presence of nickel or chromium in products of human consumption has been associated with health problems, including the inhibition of human growth, development, and the possible initialization of cancer.385,391 On the other hand, the consumption of cadmium has been associated with kidney and skeletal damage, while the consumption of lead has been linked to problems such as a reduced mental capacity in children and memory loss in adults.
The presence of heavy metals in PET therefore not only compromises human health but also undermines the effectiveness of PET recycling efforts. Mitigating these risks requires strict monitoring, compliance with regulatory limits and innovations in manufacturing and recycling processes to ensure safer and more sustainable production and use of PET.
5.1.7. Volatile organic compounds.
For PET production and recycling, there have been significant concerns related to the presence of organic contaminants, each characterized by distinct chemical compositions and origins within the PET lifecycle. Among these contaminants, we specifically encounter organic VOCs such as AA, styrene, and toluene, known for their volatility and potential health and environmental implications.299,344
For instance, VOCs such as nonanal and decanal are known for their low odor threshold values, meaning that even small amounts can cause noticeable odors.392 Furthermore, the VOC migration raises concerns about the sensory quality of water stored in PET bottles, as these compounds can contribute to off-flavors or odors in the water. Moreover, there are potential health implications associated with the VOC migration from packaging materials into consumable products, although the detected levels are generally low.
Organic VOCs are generated during PET production, processing, and recycling, due to degradation reactions induced by the high (melt) temperatures. Furthermore, the VOC presence in rPET samples could result from various factors, including the misuse of post-consumer PET material, the lack of control in material collection, recontamination in the recycling system, or external contamination.344,393
One of the most critical VOC types of contaminants found in PET products is AA. This molecule is a byproduct of the breakdown or degradation of the PET matrix, either during the manufacturing or recycling, particularly when PET is molten due to the exposure at high processing temperatures.394 Acetaldehyde can become trapped within the PET polymer matrix and may migrate out of the PET materials, particularly if conditions favor this migration e.g. the product is carbonated or acidic.394,395
More importantly, this contaminant raises serious concerns due to its potential carcinogenic effects in humans. Prolonged exposure to elevated levels of AA has been specifically associated with respiratory problems and irritation.396,397 Additionally, its presence can compromise the mechanical properties of PET products, leading to discoloration or yellowing and accelerating their degradation, thereby shortening the PET lifespan. Moreover, even at low concentrations, AA can affect the taste of food and beverages stored in PET containers, potentially imparting off-flavors. This poses a significant concern for the food and beverage industry, specifically when maintaining the original flavor profile is essential.396–398
Another significant VOC for PET products is formaldehyde. This molecule is also a byproduct of the breakdown or degradation of the PET matrix, occurring either during manufacturing or recycling, especially when PET is exposed to high processing temperatures.361 Formaldehyde can migrate out of PET materials, especially at elevated temperatures and for prolonged storage times, or in the presence of carbon dioxide (CO2), which exacerbates its migration. For example, research has indicated that at 40 °C formaldehyde concentrations in carbonated mineral water are nearly three times higher than in flat natural mineral water due to CO2-induced methanediol cluster formation during degassing.399
The presence of formaldehyde can negatively impact the mechanical properties of PET products and contribute to discoloration or yellowing. Additionally, the presence of formaldehyde complicates the recycling process of PET, necessitating the use of specialized techniques, such as advanced sorting and separation technologies, to effectively manage PET fractions containing formaldehyde.398 During the recycling process, formaldehyde can also contribute to the formation of potentially hazardous NIAS, including other aldehydes and VOCs.
Intriguingly, formaldehyde poses serious health concerns due to its cytotoxic, genotoxic, and endocrine-disrupting properties. Under Regulation (EC) No. 1272/2008, formaldehyde is classified as a category 1B carcinogen and a skin sensitizer (Category 1), due to its propensity to cause skin irritation.375,400,401 Exposure, even at low levels, can also result in respiratory irritation, coughing, severe lower respiratory effects such as bronchitis and pneumonia, gastrointestinal tract tumors, and severe allergic reactions.400,402 Furthermore, formaldehyde contamination can compromise the quality and safety of food and beverages stored in PET containers. Its presence, even in trace amounts, can affect the taste and odor of the contents, posing a significant concern for the food and beverage industry. Although the migration levels of formaldehyde in bottled water are generally within international safety standards, the compound potential health risks necessitate strict monitoring and regulation during the PET recycling process.399,402
Other VOC substances commonly reported as contaminants for rPET include ethylene glycol, 2-methyl-1,3-dioxolane, acetone, butanone, limonene, furan, benzene, styrene, toluene, benzophenone, 2-tetracosane, chloroform, chlorobenzene, and naphthalene.300,392,393 The origin of these compounds in rPET varies widely but in general requires the consideration of a detailed reaction and process scheme.300,342
Similar to AA and formaldehyde, ethylene glycol residues in PET can originate from the breakdown of the PET matrix during processing or due to exposure to high temperatures.361 Additionally, ethylene glycol can remain as a remnant from the PET production process for which it serves as a monomer.342 Furthermore, substances such as acetone and butanone can come from cleaning agents or similar compounds used during manufacturing or recycling processes. Limonene, which is associated with cleaning agents used during PET recycling, may also be present in PET due to residues from beverages or other food sources, potentially migrating to PET containers.302,342
Regarding furan, benzene, and styrene, one can state that their presence is commonly linked to breakdown reactions of foreign materials dispersed within the PET matrix during recycling, often due to insufficient sorting and cleaning processes. For instance, benzene likely results from reactions within the PET matrix, potentially due to chlorine-containing substances present in rPET. Styrene might originate from the thermal degradation of PS contaminants within the rPET matrix. A similar explanation is often put forward for the presence of compounds such as 2-methyl-1,3-dioxolane in rPET. It must be admitted that the specific pathways through which this compound arises are not well-documented, and sources might include impurities in raw materials, involve breakdown products resulting from the recycling process as well as contaminants from previous use or storage, and from reactions occurring during the manufacturing or recycling of PET.302
Mitigation strategies to address VOC contamination in rPET include implementing effective cleaning processes such as super clean cleaning to remove contaminants. However, stringent monitoring and QC measures are necessary to ensure the safety of rPET materials, particularly for applications like food packaging.300,393 Furthermore, stabilizers such as 4-aminobenzoic acid, diphenylamine and 4,5-dihydroxybenzoic acid can be added to PET in order to minimize the amount of the generated AA.97
5.1.8. Linear and cyclic oligomers.
The presence of PET linear and cyclic oligomers along with polymer byproducts adds complexity to the classification of organic contaminants. These compounds manifest during degradation processes or as residues from the manufacturing and recycling of chains, raising concerns regarding their potential impact on product safety and environmental sustainability.300 They enter the PET matrix through multiple sources, such as (i) incomplete polymerization during manufacturing and (ii) thermal or hydrolytic degradation during processing and recycling as well as upon extensive usage. Additionally, they can originate from other polymer (parts) defining the PET-based application.
There are three primary series of oligomers in PET. The first one is oriented around a balanced mix of terephthalic acid and ethylene glycol units, whereas the second one is based on substituting one monoethylene glycol unit with a diethylene glycol unit, and the third one deals with replacing two monoethylene glycol units with diethylene glycol units. Additionally, byproducts such as terephthalic acid, ethane-1,2-diol, and 2,2′-oxybisethanole can be present, potentially stemming from ring-opening and breakdown processes.403,404 Unwanted comonomers like diethylene glycol can lead to the development of cyclic and linear structures within the polymer matrix.405
Mitigation efforts to reduce oligomers in PET involve the development of more stringent manufacturing processes, more thorough cleaning methods, and ongoing improvements in production techniques. Despite these mitigations, limiting oligomer content remains challenging, due to the complexity of production cycles. While PET is known for low oligomer migration, certain oligomers such as cyclic trimers, pentamers, and linear derivatives have been detected migrating into food and beverages. This migration is more notable at higher temperatures, potentially elevating concentrations to worrisome levels. Concerns arise regarding human exposure to these oligomers, as their levels vary based on the food types and storage conditions. Moreover, these oligomers and other byproducts can alter the physical properties of the PET products, impacting mechanical strength, thermal stability, and possibly their barrier qualities.403–405
5.1.9. Polymer byproducts.
Specifically, for PET bottles, contamination at the polymer, rather than by default at the oligomeric level, is relevant as well. PET is a highly preferred material for producing plastic bottles, given its favorable properties such as lightweight, strength, and durability. Additionally, the recyclability of PET plays a crucial role in its selection for bottle production, contributing to its economic feasibility across the entire process chain. However, upon considering auxiliary components such as bottle caps (and labels), materials other than PET are commonly present as well. The introduction of these non-PET plastic materials makes the recycling process less trivial. The mixing of these materials in the recycling stream can have adverse effects on the inherent properties of PET, impacting its material performance for the production of new bottles. As a result, these polymeric foreign materials act as contaminants during the PET recycling process.
Bottle caps are frequently crafted from plastics such as PP or HDPE, showcasing properties significantly different from those of PET.406 These differences are manifested in macroscopic properties such as strength, transparency, flexibility, and other relevant features. Consequently, these materials are considered potential contaminants that must be addressed during the PET recycling process, as they have a substantial impact on the quality and integrity of the rPET material. The recycling process itself can also introduce polymeric contaminants from other materials such as PVC and nylon. It should be noted that PET flakes must meet minimal requirements; for instance, it has been stated that they should contain less than 50 ppm of poly(vinyl chloride) and less than 10 ppm of polyolefins.13
Introducing other non-PET macromolecular materials into the recycling streams creates additional challenges in the sorting, cleaning, and processing stages, due to the highly divergent processing conditions, including different melting points of these materials.86 This complexity accentuates the need for enhanced sorting technologies and processing methods to ensure the efficient and sustainable recycling of PET in the presence of these diverse plastic components. Recent technological design for instance allows upon proper use the attachment of HDPE-based caps to used PET bottles. Additionally, the aforementioned challenges may result in increased operational costs, potentially leading to a reduction in profit margins for recycling facilities.406,407
5.1.10. Bisphenol A.
Bisphenol A (BPA) is a chemical compound primarily used in the production of polycarbonate and epoxy resins that can be present in PET waste streams. It should be stressed that BPA is not intentionally added to PET during its production process.408,409 However, instances have been reported where BPA has been found in PET products, generating concerns about the contamination of PET materials with BPA.410–413 The contamination with BPA occurs due to potential cross-contamination or accidental mixing of PET with other plastics containing BPA during manufacturing or recycling processes.411 Further sources of BPA in PET bottles, especially water bottles, have been associated with bottle closures412 and contaminated water with BPA prior to bottling.413
BPA is in general integral to the manufacturing of various plastic components such as food and beverage containers, electronic products, thermal papers, and dental sealants.408 However, the presence of BPA in these materials raises significant concerns for public health as well as wildlife and associated ecosystems. This is because of its ability to leach out of plastics, especially upon exposure to heat or acidic conditions. BPA is widely recognized as an endocrine disruptor as well as a skin sensitizer and is toxic to reproduction.340,410,414,415 Exposure to BPA has been linked to various health issues, including reproductive problems and developmental disorders, due to its estrogen-mimicking properties.409,412,413 Due to these concerns, the EU Expert Committee already approved a proposal from the European Commission to ban BPA due to its potentially harmful effects on the immune system.409,416,417 An actual ban, expected to be enacted by the end of 2024 with a transition period, primarily targets BPA in packaging such as can coatings, reusable plastic bottles, and kitchenware.417 However, exceptions exist, including epoxy resins used in large tanks and polysulfone plastic for filtration devices.417
5.2. Regulations and standards
As highlighted in the previous subsection, a wide range of contaminants can disturb the PET production and recycling. A paramount challenge is therefore the development of regulations and standards toward permissible contaminants and their amounts. This requires dedicated research and testing in the first stage for isolated contaminants, followed by efforts in the second stage aiming for upgrades in an industrial environment with mixed contributions from various contaminant types and potential accelerating or inhibiting effects.
Important official documents regarding current regulations and standards are e.g. (i) the directive 94/62/EC on Packaging and Packaging Waste;317 (ii) the Commission Regulation (EU) No. 10/2011 on Plastic Materials and Articles intended to come into contact with food;318 (iii) the Commission Regulation (EU) 2022/1616 on Recycled Plastic Materials and Articles intended to come into contact with foods;319 (iv) the Regulation (EC) No. 1935/2004;277 (v) the Commission Regulation (EC) No. 2023/2006;278 (vi) the Regulation (EC) No. 1907/2006;279 and (vii) the Scientific Opinion on the criteria to be used for Safety Evaluation of a Machinal Recycling Process to Produce Recycled PET intended to be used for manufacture of materials and articles in contact with food.418
In what follows, the context behind these official documents is framed by a series of examples including scientific data recording studies. It is however important to note that regulatory limits are routinely updated to reflect the most current scientific literature on levels that pose health risks.
A first example is given in the work of da Silva Costa et al.,409 who detected BPA concentration levels in PET bottles up to 5.7 × 10−3 ppm. This value is considerably lower than the SML set by Commission Regulation (EU) No. 10/2011 at 0.05 mg kg−1 (0.05 ppm) of food simulant.318 Nonetheless, the presence of BPA still raises some concerns regarding the total daily intake from all food sources.
A second example of a data recording study is the identification of the suited concentration of different phthalates. For example, Dekant et al.381 compared their findings with the specified tolerable daily intakes (TDIs) established by the European Food Safety Authority (EFSA).379,380 Although the concentrations detected did not surpass the regulated limits, there are still ongoing concerns about potential health issues linked to prolonged exposure.419
A third example is presented in the work of Whitt et al.,385 who examined the maximum allowable dose level (MADL) for heavy metals in rPET applications, specifically focusing on materials intended for direct food contact with the results shown in Table 3. These authors state that an increase in heavy metal contamination can be mainly attributed to commingling with electronic waste. Out of 200 tested sample replicates, the authors found that approximately 30 of them were contaminated with heavy metals. Nickel was found in approximately 96% of the cases, lead in approximately 90% of the cases, and Sb in approximately 97% of the cases.385 The study concluded that certain metals are more likely to be found in higher concentrations in rigid containers rather than thin films, highlighting the need for better monitoring of heavy metals when food contact applications are targeted.
Table 3 Maximum allowable dose level (MADL) for heavy metals potentially present in PET, based on the work of Whitt et al.385
Heavy metal |
MADL per daya |
SMLe |
The maximum allowable dose level, the amount that can be ingested per day that is considered safe.
NSRL, being the no significant risk level, has been adopted under Proposition 65 for ingested elemental nickel.
Daily lead exposure limit beyond which male and female developmental problems may occur.
Daily lead exposure limit beyond which carcinogenic health effects may occur in adults.
Substance migration limit according to European legislation.
ND: non-detectable; a detection limit of 0.002 mg per kg food (simulant) applies.
|
Nickel |
NSRLb |
0.02 mg per kg food or food simulant |
Lead |
0.5 μg per dayc |
NDf |
Lead, oral |
15 μg per dayd |
— |
Cadmium |
4.1 μg per day |
0.02 mg per kg food or food simulant |
Chromium |
8.2 μg per day |
NDf mg per kg food or food simulant |
Antimony |
6 ppb per day |
0.04 mg per kg food or food simulant |
Consistently, the European Directive (94/62/EC) on Packaging and Packaging Waste has established a (total) upper limit of 100 ppm for the amount of heavy metals such as lead, cadmium, mercury, chromium and/or compounds in plastic packaging.317,420 However, the EC has specified in the Commission Regulation (EU) No. 10/2011 additional laws for plastic packaging materials, which will/can come in contact with food items. Maximum allowable concentrations for leaching into food e.g. nickel and Sb are respectively 0.02 and 0.04 mg per kg of food. Additionally, it has been stated that the total amount of non-volatile substances that can migrate from plastic materials into food must not exceed the overall migration limit (OML) of 10 mg per 1 dm2 of food contact surface or 60 mg per 1 kg of food.420
In addition, regulatory bodies such as the EC and the American Environmental Protection Agency (US EPA) have specified different maximum tolerable values for the contribution of Sb. For instance, the EC sets a maximum concentration of 5 μg L−1 for drinking water and allows up to 40 μg L−1 for food in plastic containers, while the EPA regulates drinking water with a maximum of 6 μg L−1. Different research sources389,421,422 confirm that the concentration of Sb found in food products kept in PET containers, such as in the case of water stored in PET bottles, remains within regulated limits. However, prolonged storage or higher temperatures can elevate the levels of Sb, breaching acceptable consumption thresholds.389
In parallel, the EFSA and the Commission Regulation (EU) No. 10/2011 (ref. 318) established guidelines and thresholds relating to materials intended to come into contact with food, known as Food Contact Materials (FCM). The total migration threshold of oligomers set in the regulation is 50 μg kg−1. This criterion serves as a standard to evaluate the migration of FCM oligomers to food products. While these regulations specify a total migration limit for oligomers, they may not explicitly delineate concentrations for individual oligomers, which poses challenges upon evaluating the safety of specific compounds.404,405,423
The current challenges in the regulatory frameworks associated with NIAS in PET products further complicate defining well-defined specific and safe limits for these substances in food contact PET containers. Nevertheless, legislations such as the Plastic Regulation No. 10/2011 (ref. 318) and the Food Contact Materials (FCM) No. 1935/2004277 already demand further risk assessment for the migration of NIAS to prevent public health issues. Applicants who submit new technologies for mechanical recycling of plastics intended for the manufacturing of materials used in food and/or beverage packaging have to also successfully prove that their technology is in accordance with the Article of the Regulation (EC) No. 2022/1616.319
The last-mentioned standard considers the possible migration of chemicals into food at levels posing a threat to human health. Depending on the application, different surrogate levels are tolerated, as illustrated in Table 4. Generally, a challenge test is conducted in which rPET (flakes) is submerged and exposed to a mix of surrogates, such as toluene, chlorobenzene, chloroform, methyl salicylate, phenylcyclohexane, benzophenone, and methyl stearate, for several days at a certain temperature. These conditions simulate possible misuse of the material, and its surrogate concentration, after washing and drying, is measured before and after the PET flakes have undergone the proposed recycling process. The EFSA panel considers a threshold value of 0.0025 μg per kg per body weight per day to be low enough to overrule concerns over toxicological effects.
Table 4 Examples of estimated concentrations of surrogates found in collected PET, as reported by the EFSA419,424,425
Type of compound |
Estimated concentration in collected PET [mg kg−1] |
Maximum allowed concentration after recycling |
Limonene |
2.9–20 |
A total allowed maximum that leads to a mitigation of no more than 0.0025 μg per kg of body weight per day |
Methyl salicylate |
15.3–204 |
Hexanal, benzaldehyde |
<3.4 |
Triclosan |
1.6 |
Misuse chemicals (household chemicals, fuels or similar) |
1.4–2.7 |
Technical compounds (e.g. adipates, phthalates, and erucamides) |
<0.2–0.5 |
In more detail, the residual concentration of each surrogate contaminant in rPET (Cres) is compared with a modelled concentration of surrogate contaminants in PET (Cmod), which overestimates the real migration of surrogates by a value of 5 to 100. The modelled concentration deals with the surrogate migration that does not exceed the human exposure threshold value for chemicals with structural alerts for genotoxicity. The threshold value for surrogate migration can vary depending on the final application and its recycled content, e.g. 0.1 μg per kg food for infants, 0.15 μg per kg food for toddlers, and 0.75 μg per kg food for adults. A recycling process is considered safe if Cres is smaller than Cmod, and if one does not encounter a surrogate migration that is higher than the threshold value of 0.0025 μg per kg of body weight per day.
Overall, it thus follows that several studies have been already conducted for specific contaminants; however, detailed studies accounting for time dependent disturbance factors are still lacking. A full appreciation of reasonable tolerances requires a more detailed molecularly driven approach identifying the key mechanisms behind the formation and disappearance of contaminants throughout the (mechanical) recycling process as well as the life cycle of PET.
6. Recycling applications
In recent years, the demand for recycled PET (rPET) in, amongst others, the food packaging industry has grown, supported by legal frameworks that allow its use, as described in the previous section. The so-called super clean processes during primary recycling employ advanced technologies for efficient decontamination, enabling post-consumer recyclates to be safely reused in direct food contact applications, with bottle-to-bottle (BtB) recycling serving as a prime example.73
Additionally, bottle-to-fiber (BtF) recycling has shown good potential for a wide range of applications (e.g. textile manufacturing and construction), while simultaneously reducing both costs and the overall carbon footprint.426 Furthermore, secondary recycling and tertiary recycling aim to promote open-loop recycling with ongoing research on potential applications in e.g. coatings, soft tissue engineering, drug delivery, and additive extraction.427–430
In general, closed-loop recycling is often considered the priority solution as it maintains the value of the material and keeps resources within a target market. It should be highlighted that open recycling loops are not necessarily negative; rather, we should aim to further explore the compatibilities of all recycling strategies.4,431 In what follows the main aspects of closed- and open-loop rPET applications are covered as well as alternative routes.
6.1. Closed-loop mechanical recycling rPET applications
The primary end-use markets for rPET include food packaging for which a significant portion is utilized in the production of bottles, followed by the use of rPET for the manufacturing of trays and sheets. Of the 1.9 million tonnes of recyclates produced in the EU27+3 region in 2022, 48% was designated for bottle manufacturing and 25% for sheet extrusion (trays).4
It should be noted that post-consumer PET exhibits distinct processing characteristics compared to virgin PET.344 For instance, for bottle-to-bottle recycling, bottle-grade rPET resins may contain residual amounts of various virgin grades, with water-grade resins typically exhibiting lower IV values and containing acetaldehyde scavengers.344,432 In contrast, carbonated soft drink (CSD) grades possess higher IV values and include co-monomers designed to enhance resistance to expansion.344 Consequently, the final rPET pellets can vary in their co-monomer composition and additive levels, leading to lot-to-lot variability that alters the characteristics of the input resin. This variability is particularly significant in stretch blow molding for which the presence of contaminants can impact the optical properties and affect the efficiency of infrared (IR) radiation absorption.344,433 Such variations in absorption efficiency ultimately influence the heating of the preform, which in turn affects the final thickness distribution of the bottle during stretching, potentially impacting its overall compressive strength and even leading to ruptures.344,434
Similarly, PET recyclers are also challenged with tray-to-tray recycling due to several factors. A primary issue is the high level of contamination. PET tray bales typically exhibit higher impurity levels than bottle bales, with common contaminants including water, organic residues, labels, lidding films, and aluminum.435,436 Often PET trays are found to be unmanageable due to their distinct composition, which includes multi-layer and multi-material compositions that may lead to further contamination. Their incompatibility with polyolefins makes PET trays difficult to process for mixed plastic recyclers as well.435
While current technologies are able to distinguish mono-layer from multi-layer trays, they are often deemed financially infeasible for most material recovery facilities. To match output from bottle-to-bottle recycling facilities, the tray recycling process needs to be technologically improved, ideally with dedicated lines added.4 The tray-to-tray recycling capacity is anticipated to exceed 300
000 tonnes per year by 2025, driven by initiatives such as Tray2Tray and TrayRevive.437,438 It should however be noted that in Europe there is no specific legislation dedicated to thermoforming packaging yet.436
6.2. Open-loop mechanical recycling rPET applications
In addition to bottles and trays, fiber and strapping production represented the second and third largest end-use markets in 2022, accounting for 15% and 6% of the total rPET usage, respectively. The remaining 6% was allocated to various other applications.4
The textile industry is a significant consumer of rPET, utilizing approximately 15% of its total output in applications such as carpet fibers, fabrics for clothing, sport shoes, and luggage.439,440 The primary standards governing textiles made from recycled materials are the Recycled Claim Standard (RCS) and the Global Recycled Standard (GRS), both of which have been in effect since 2013 and 2011, respectively.439,440 The RCS is an international, voluntary standard that establishes requirements for third-party certification of recycled inputs and ensures proper chain custody.440,441 In contrast, the GRS encompasses additional criteria related to social and environmental processing requirements, as well as chemical restrictions.442
In line with these efforts, the European Commission published the EU strategy for Sustainable and Circular Textiles in March 2022,443 which aims to further promote fiber-to-fiber recycling by looking at the entire lifecycle of textile products and proposing coordinated actions to transform both the production and consumption patterns within the textile industry.444 Notably, unlike food packaging applications, which are subject to (very) stringent regulations regarding safety and migration limits, legislation governing rPET used for fiber production is less rigorous. This disparity reflects the different safety concerns associated with textiles compared to materials intended for food contact. Although both the RCS and the GCS standards are not mandated by law, they can enhance credibility and marketability in sectors increasingly focused on environmental responsibility.
A key point to consider is that fiber-to-fiber recycling is less common than bottle-to-fiber or tray-to-fiber recycling. After being converted to fibers, virgin PET loses its ability to be re-spun during its first melt spinning cycle due to various degradation reactions.445,446 Therefore, it becomes hard to recycle PET based textile waste to new fibers without applying any chain extension or consecutive depolymerization and repolymerization steps.97,446 Instead, at the end of their lifecycle, PET fibers can be repurposed as e.g. reinforcement in concrete, which has been shown to enhance both flexural and compressive strength compared to unreinforced concrete.440,447 Similarly, recent research has shown that rPET can be enhanced with additives, such as flame retardants and foaming agents, to expand its use in various engineering applications, including electrical and structural applications.448
6.3. rPET applications not involving mechanical recycling
As was highlighted in Section 1, secondary recycling includes the decomposition of materials into their constituent monomers, which can then serve as a feedstock for the production of new plastics or petrochemicals. The potential applications of by-products obtained from chemical recycling processes are highly diverse and depend on the specific recycling method employed, such as glycolysis, hydrolysis, methanolysis, aminolysis, or ammonolysis.440
For instance, Sarkar et al. synthesized a novel polyester using bis-(hydroxyethyl terephthalate) (BHET) monomers derived from rPET waste,428 with excellent cytocompatibility in vitro for soft tissue engineering and bone tissue engineering applications.428,429 Other examples include the manufacturing of e.g. hardeners, plasticizers for PVC, and rigid polyurethane foams from compounds derived from aminolysis from waste PET.129,440
Additionally, tertiary recycling of PET involves dissolution–precipitation techniques, where a solvent dissolves the selected polymer, which is then filtered and recovered, followed by the addition of an antisolvent to precipitate the dissolved polymer. Recent studies have demonstrated that PET can be efficiently recycled through this method, with potential applications in the recycling of multilayer plastic films.449,450 For example, CreaSolv Technology has utilized their MultiCycle CreaSolv® Pilot Plant to recover PET from multilayer flexible packaging for use in the production of textile fibers.451 Current research is still focused on optimizing the process to make it more cost-effective and environmentally sustainable.440
Furthermore, the chemical energy stored in PET can be recovered in the form of thermal energy during quaternary recycling, which is the least preferred method of recycling. Waste-to-energy technologies produce heat by burning PET waste in the form of superheated steam that can be used to generate electricity, or the residual heat from the waste stream can also be used for heating residential and industrial buildings.452–455
7. Conclusions and challenges
To fully define the boundary conditions that make mechanical recycling technology preferred over other techniques to handle poly(ethylene terephthalate) (PET) waste streams, it is paramount to establish a science-driven framework connecting lower and higher technology readiness level (TRL) research and insights.
This TRL connection implies the proper bridging of the molecular and process scales along the whole value chain and the connection of several scientific disciplines, with a leading role for the field of environmental engineering science (EES), specifically life cycle assessment (LCA) and polymer reaction engineering (PRE). The proper alignment of EES and PRE can enable sustainable polymer reaction engineering (sPRE), in which the PET process and its integration in a circular context are optimized according to sufficiently tested and fundamentally supported guidelines. Such guidelines enable more robust decision making, considering features such as environmental impact, economic suitability, and application properties as well as market potential, recognizing the molecular scale, industrial implementation schemes and waste compositional deviations.
The current LCA studies, being mainly geared by the interpretation of overall process schemes and yields in different steps, have indicated that for closed-loop recycling, mechanical recycling is preferred over e.g. glycolysis followed by repolymerization, but this combination is favored over virgin production if this production process is properly designed. The addition of virgin material can be needed, as put forward for enhanced PET bottle-to-bottle recycling. This approach is recommended to lower the impact of (thermo-mechanical) degradation, again putting forward the relevance of the molecular scale in the overall evaluation.
PRE driven molecular changes mainly take place in the melt- and solid-based re-processing units, being the workhorse of a mechanical recycling plant, at least assuming efficient pretreatment steps and well-established finishing techniques consistent with the virgin market. It is specifically critical to verify which degradation reactions are dominant and to which extent functional groups are converted or volatiles are created that lead to a too low final recycled polymer quality, even upon the application of chemical repair mechanisms or in general chemical engineering mitigation strategies. If such a diminishing in quality would be the case for a certain generation of PET waste, one can then better anticipate the market potential for next generations and sufficiently early start the integration of the complementary chemical recycling route, preferentially through depolymerization delivering the original monomer and first oligomers. In other words, LCA could be not only based on yields and energy efficiencies calculated for the overall plant scheme; instead, it can be based on molecular variations in each unit of such a scheme, with a direct connection to the application potential also including other types of qualities as originally intended. Current LCA outputs can thus be made more molecularly dependent or new LCA output can be defined, e.g. a LCA output correcting for repair potential.
The aforementioned molecular variations, as caused by the stochastic nature of polymer modification mechanisms at the micro-scale, should also be connected to PRE morphological variations at the meso-scale (e.g. crystallinity variations) and PRE macro-scale gradients in temperature and mixing to enable a molecular scale driven LCA along the whole value chain, particularly addressing the role of contaminants in disturbing the degradation chemistry and application outreach. These contaminants, either formed before or during the recycling, can negatively affect the equipment performance, leading to a decrease in process yield. Moreover, if these contaminants persist in the recycled PET material, they can decrease the material properties and performance, thereby hindering its effectiveness for the intended applications.
A challenge is therefore a better mapping of the influence of the various types of contaminants, including non-intentionally added substances (NIAS), to better pinpoint mitigation strategies as well as support the formulation of future guidelines and regulations, taking into account technological adaptations to better measure NIAS contributions and to avoid the formation of (critical) contaminants at the plant level. The required research efforts need to be embedded both in academia and industry, and upon their successful realization, will enable the full exploitation of sPRE.
In this emerging sPRE field, model-based design and data analysis will be essential to grasp with a sufficiently high level of fundamental detail how units in the PET recycling industry need to be connected, accounting for movements in the virgin market and the presence of mingled streams of PET waste of several generations in parallel to the virgin streams. The generated insights will enable further optimization of currently applied PET mechanical recycling strategies and introduce new technology in harmony with chemical and physical recycling technological design. Specifically, it will enable introducing recycling or repair indicators to assess if PET mechanical or chemical recycling is worthwhile. Such indicators can be generalized to any recycling process and facilitate a link between PRE software and LCA modeling tools and methodologies, thus enabling science driven guidelines for optimal recycling for a given region or range of technologies available.
Abbreviations
AA | Acetaldehyde |
ABS | Acrylonitrile butadiene styrene polymer |
BBP | Benzyl butyl phthalate |
BPA | Bisphenol A |
BtB | Bottle-to-bottle |
CFD | Computational fluid dynamics |
CMMC | Coupled matrix-based Monte Carlo |
CO2 | Carbon dioxide |
DBP | Dibutyl phthalate |
DEHP | Diethylhexyl phthalate |
DIBP | Diisobutyl phthalate |
DIP | Diisononyl phthalate |
EES | Environmental engineering science |
EC | European Commission |
ECHA | European Chemicals Agency |
EFSA | European Food Safety Authority |
eq. | Equivalent |
FCM | Food contact materials |
FTIR | Fourier-transform infrared spectroscopy |
GHG | Greenhouse gas |
GHS | Global harmonized system |
HDPE | High density polyethylene |
LDPE | Low density polyethylene |
LSP | Liquid state polycondensation |
LCA | Life cycle assessment |
IV | Intrinsic viscosity |
PAH | Polycyclic aromatic hydrocarbon |
PE | Polyethylene |
PET | Poly(ethylene terephthalate) |
PETG | Polyethylene terephthalate glycol |
PMDA | Pyromellitic dianhydride |
PLA | Poly(lactic acid) |
PP | Polypropylene |
PRE | Polymer reaction engineering |
PVC | Poly(vinyl chloride) |
MADL | Maximum allowable dose level |
MMD | Molar mass distribution |
MoM | Method of moments |
NaOH | Sodium hydroxide |
NIAS | Non-intentionally added substances |
NIR | Near-infrared spectroscopy |
OML | Overall migration limit |
REX | Reactive extrusion |
rPET | Recycled PET |
Sb | Antimony |
Sb2O3 | Antimony trioxide |
SSP | Solid-state polymerization |
TDI | Tolerable daily intake |
STOT-RE | Specific target organ toxicity-repeated exposure |
TiO2 | Titanium dioxide |
TRL | Technology readiness level |
rPET | Recycled PET |
SEA | Statistical entropy analysis |
SML | Specific migration limit |
sPRE | Sustainable polymer reaction engineering |
TEA | Techno-economic assessment |
US-EPA | American Environmental Protection Agency |
UV | Ultraviolet |
VIS | Ultraviolet spectroscopy |
QC | Quality control |
XRF | X-ray fluorescence |
VOC | Volatile organic compound |
Data availability
No new data were generated as part of this review.
Conflicts of interest
There are no conflicts to declare.
Acknowledgements
D. R. D. acknowledges the Research Foundation – Flanders (FWO) via the project G027122N and the agency for Flanders Innovation & Entrepreneurship (VLAIO) via the Green AM project as well as the Moonshot Initiative (Core2 project). M. E. acknowledges the Special Research Fund (BOF) of Ghent University.
References
-
L. T. Sin and B. S. Tueen, Plastics and environmental sustainability issues, in Plastics and Sustainability, Elsevier, 2023, pp. 1–43 Search PubMed.
- N. Malik, P. Kumar, S. Shrivastava and S. B. Ghosh, An overview on PET waste recycling for application in packaging, Int. J. Plast. Technol., 2017, 21(1), 1–24 CAS.
-
S. Bidwai and A. Shivarkar, Recycled polyethylene terephthalate market size, report by 2033, Precedence Research, 2024, available from: https://www.precedenceresearch.com/recycled-polyethylene-terephthalate-market.
-
Plastics Recyclers Europe, PET market in Europe: State of play – 2022 data, 2024 Mar, available from: https://www.plasticsrecyclers.eu/wp-content/uploads/2024/03/PET-Market-in-Europe-State-of-Play_2022-data.pdf.
-
European Union, Directive (EU) 2019/904 of the European Parliament and of the Council of 5 June 2019 on the reduction of the impact of certain plastic products on the environment, Official Journal of the European Union, 2019, vol. L155, pp. 1–19 Search PubMed.
-
European Union, Directive 2001/83/EC of the European Parliament and of the Council of 6 November 2001 on the Community code relating to medicinal products for human use, consolidated version 1 January 2022, Official Journal of the European Union, 2022, vol. L311, pp. 67–128 Search PubMed.
- Plastics Engineering, New EU regulation: What you need to know about food contact, Plastics Engineering, 2024 Feb; available from: https://www.plasticsengineering.org/2024/02/new-eu-regulation-what-you-need-to-know-about-food-contact-003315/.
- T. Muringayil Joseph, S. Azat, Z. Ahmadi, O. Moini Jazani, A. Esmaeili and E. Kianfar,
et al., Polyethylene terephthalate (PET) recycling: A review, Case Stud. Chem. Environ. Eng., 2024, 9(100673), 100673 CrossRef CAS.
- T. Thiounn and R. C. Smith, Advances and approaches for chemical recycling of plastic waste, J. Polym. Sci., 2020, 58(10), 1347–1364 CrossRef CAS.
- M. G. Davidson, R. A. Furlong and M. C. McManus, Developments in the life cycle assessment of chemical recycling of plastic waste – A review, J. Cleaner Prod., 2021, 293, 126163 CrossRef CAS.
- O. Dogu, M. Pelucchi, R. Van de Vijver, P. H. M. Van Steenberge, D. R. D’hooge and A. Cuoci,
et al., The chemistry of chemical recycling of solid plastic waste via pyrolysis and gasification: State-of-the-art, challenges, and future directions, Prog. Energy Combust. Sci., 2021, 84, 100901 Search PubMed.
- J. G. Poulakis and C. D. Papaspyrides, Dissolution/reprecipitation: A model process for PET bottle recycling, J. Appl. Polym. Sci., 2001, 81(1), 91–95 CAS.
- C. Fiorillo, L. Trossaert, E. Bezeraj, S. Debrie, H. Ohnmacht and P. H. M. Van Steenberge,
et al., Molecular and material property variations during the ideal degradation and mechanical recycling of PET, RSC Sustainability, 2024, 2(12), 3596–3637 CAS.
- D. R. D’hooge, M.-F. Reyniers and G. B. Marin, The crucial role of diffusional limitations in controlled radical polymerization, Macromol. React. Eng., 2013, 7(8), 362–379 Search PubMed.
- K. De Smit, Y. W. Marien, P. H. M. Van Steenberge, D. R. D’hooge and M. Edeleva, Playing with process conditions to increase the industrial sustainability of poly(lactic acid)-based materials, React. Chem. Eng., 2023, 8(7), 1598–1612 CAS.
-
A. Merrington, Recycling of plastics, in Applied Plastics Engineering Handbook, Elsevier, 2024, pp. 191–217 Search PubMed.
- M. del M. C. López, A. I. Ares Pernas, M. J. Abad López, A. L. Latorre, J. M. López Vilariño and M. V. González Rodríguez, Assessing changes on poly(ethylene terephthalate) properties after recycling: Mechanical recycling in laboratory versus postconsumer recycled material, Mater. Chem. Phys., 2014, 147(3), 884–894 Search PubMed.
- I. A. Ignatyev, W. Thielemans and B. Vander Beke, Recycling of polymers: A review, ChemSusChem, 2014, 7(6), 1579–1593 CAS.
- D. R. D’hooge, P. H. M. Van Steenberge, M.-F. Reyniers and G. B. Marin, The strength of multi-scale modeling to unveil the complexity of radical polymerization, Prog. Polym.
Sci., 2016, 58, 59–89 Search PubMed.
- L. De Keer, K. I. Kilic, P. H. M. Van Steenberge, L. Daelemans, D. Kodura and H. Frisch,
et al., Computational prediction of the molecular configuration of three-dimensional network polymers, Nat. Mater., 2021, 20(10), 1422–1430 CAS.
- N. B. Sanches, M. L. Dias and E. B. A. V. Pacheco, Comparative techniques for molecular weight evaluation of poly (ethylene terephthalate) (PET), Polym. Test., 2005, 24(6), 688–693 CAS.
- F. Ronkay, B. Molnár, E. Szabó, G. Marosi and K. Bocz, Water boosts reactive toughening of PET, Polym. Degrad. Stab., 2022, 203, 110052 CAS.
-
W. Lu and J. Mays, Dilute solution viscometry of polymers, in Molecular Characterization of Polymers, Elsevier, 2021, pp. 261–80 Search PubMed.
- H. M. Quackenbos, Relation between intrinsic viscosity and molecular weight, J. Appl. Polym. Sci., 1980, 25(7), 1435–1442 CrossRef CAS.
- L. E. Nielsen, Cross-linking–effect on physical properties of polymers, J. Polym. Sci., Part C, 1969, 3(1), 69–103 CAS.
- K. J. Lee, D. Y. Moon, O. O. Park and Y. S. Kang, Diffusion of ethylene glycol accompanied by reactions in poly(ethylene terephthalate) melts, J. Polym. Sci., Part B:Polym. Phys., 1992, 30(7), 707–716 CrossRef CAS.
- L.-W. Chen and J.-W. Chen, Kinetics of diethylene glycol formation from bishydroxyethyl terephthalate with zinc catalyst in the preparation of poly(ethylene terephthalate), J. Appl. Polym. Sci., 2000, 75(10), 1229–1234 CrossRef CAS.
- H. A. Lecomte and J. J. Liggat, Degradation mechanism of diethylene glycol units in a terephthalate polymer, Polym. Degrad. Stab., 2006, 91(4), 681–689 CrossRef CAS.
- S. S. Hosseini, S. Taheri, A. Zadhoush and A. Mehrabani-Zeinabad, Hydrolytic degradation of poly(ethylene terephthalate), J. Appl. Polym. Sci., 2007, 103(4), 2304–2309 CrossRef CAS.
- W. Romão, M. F. Franco, Y. E. Corilo, M. N. Eberlin, M. A. S. Spinacé and M.-A. De Paoli, Poly (ethylene terephthalate) thermo-mechanical and thermo-oxidative degradation mechanisms, Polym. Degrad. Stab., 2009, 94(10), 1849–1859 Search PubMed.
-
A. Gok, C. L. Fagerholm, D. A. Gordon, L. S. Bruckman and R. H. French, Degradation of poly(ethylene-terephthalate) under accelerated weathering exposures, in 2015 IEEE 42nd Photovoltaic Specialist Conference (PVSC), IEEE, 2015, pp. 1–6 Search PubMed.
- S. V. Canevarolo, Chain scission distribution function for polypropylene degradation during multiple extrusions, Polym. Degrad. Stab., 2000, 70(1), 71–76 CrossRef CAS.
-
A. Feil and T. Pretz, Mechanical recycling of packaging waste, in Plastic Waste and Recycling, Elsevier, 2020, pp. 283–319 Search PubMed.
- F. L. Figueira, Y.-Y. Wu, Y.-N. Zhou, Z.-H. Luo, P. H. M. Van Steenberge and D. R. D’hooge, Coupled matrix kinetic Monte Carlo simulations applied for advanced understanding of polymer grafting kinetics, React. Chem. Eng., 2021, 6(4), 640–661 CAS.
- K. De Smit, M. Edeleva, A. D. Trigilio, Y. W. Marien, P. H. M. Van Steenberge and D. R. D’hooge, Kinetic Monte Carlo residence time distributions and kinetics in view of extrusion-based polymer modification and recycling, React. Chem. Eng., 2023, 8(3), 563–576 RSC.
- F. L. Figueira, P. Reyes, M. Edeleva, Y. W. Marien, Y.-Y. Wu and Y.-N. Zhou,
et al., Combining ternary phase diagrams and multiphase coupled matrix-based Monte Carlo to model phase dependent compositional and molar mass variations in high impact polystyrene synthesis, Chem. Eng. J., 2024, 481, 148349 CrossRef CAS.
- Y.-N. Zhou, J.-J. Li, Y.-Y. Wu and Z.-H. Luo, Role of external field in polymerization: Mechanism and kinetics, Chem. Rev., 2020, 120(5), 2950–3048 CrossRef CAS PubMed.
- T.-T. Wang, Z.-H. Luo and Y.-N. Zhou, On the precise determination of molar mass and dispersity in controlled chain-growth polymerization: A distribution function-based strategy, Macromolecules, 2023, 56(3), 1130–1140 CrossRef CAS.
-
B. Davis, Study on the environmental impacts of different masks used in COVID-19 pandemic, 2020, Available from: DOI:10.13140/RG.2.2.10863.97444.
- G. Rebitzer, T. Ekvall, R. Frischknecht, D. Hunkeler, G. Norris and T. Rydberg,
et al., Life cycle assessment, Environ. Int., 2004, 30(5), 701–720 CrossRef CAS PubMed.
-
O. Jolliet, M. Saade-Sbeih, S. Shaked, A. Jolliet and P. Crettaz, Environmental Life Cycle Assessment, CRC Press, 2015 Search PubMed.
- J. Ferdous, F. Bensebaa and N. Pelletier, Integration of LCA, TEA, Process Simulation and Optimization: A systematic review of current practices and scope to propose a framework for pulse processing pathways, J. Cleaner Prod., 2023, 402, 136804 Search PubMed.
- International Organization for Standardization (ISO), ISO 14040:2006 – Environmental management – Life cycle assessment – Principles and framework [Internet], Geneva: ISO; 2006 [cited 2024 Dec 9].
- T. M. Kousemaker, G. H. Jonker and A. I. Vakis, LCA practices of plastics and their recycling: A critical review, Appl. Sci., 2021, 11(8), 3305 CAS.
- P. Nimmegeers, A. Parchomenko, P. De Meulenaere, D. R. D’hooge, P. H. M. Van Steenberge, H. Rechberger and P. Billen, Extending multilevel statistical entropy analysis towards plastic recyclability prediction, Sustainability, 2021, 13(6), 3553 CAS.
- U. Arena, M. L. Mastellone and F. Perugini, Life cycle assessment of a plastic packaging recycling system, Int. J. Life Cycle Assess., 2003, 8(2), 92–98 Search PubMed.
- U. Arena, M. L. Mastellone and F. Perugini, The environmental performance of alternative solid waste management options: a life cycle assessment study, Chem. Eng. J., 2003, 96(1–3), 207–222 CAS.
- O. Romero-Hernández, S. Romero Hernández, D. Muñoz, E. Detta-Silveira, A. Palacios-Brun and A. Laguna, Environmental implications and market analysis of soft drink packaging systems in Mexico. A waste management approach, Int. J. Life Cycle Assess., 2009, 14(2), 107–113 Search PubMed.
- F. Perugini, M. L. Mastellone and U. Arena, A life cycle assessment of mechanical and feedstock recycling options for management of plastic packaging wastes, Environ. Prog., 2005, 24(2), 137–154 CAS.
-
C. Caelli, F. Arfelli, F. Caraceni, D. Cespi, M. Cordara, C. Brondi, et al., Implementation of LCA in the Circular Economy context: methodological issues for application in PET packaging, Procedia CIRP, 2024, vol. 122, pp. 719–24 Search PubMed.
-
A. Ncube and Y. Borodin, Life Cycle Assessment of polyethylene terephthalate bottle, in 2012 7th International Forum on Strategic Technology (IFOST), IEEE, 2012 Search PubMed.
- R. G. Hunt, W. E. Franklin and R. G. Hunt, LCA — How it came about: – Personal reflections on the origin and the development of LCA in the USA, Int. J. Life Cycle Assess., 1996, 1(1), 4–7 Search PubMed.
-
R. G. Hunt and R. O. Welch, (1974) Resource and Environmental Profile Analysis of Plastics and Non-Plastics Containers, Midwest Research Institute, MRI Project No. 3714-D.
-
M. Schmidt, A. Ostermayer and D. Bevers, Life cycle assessment of PET (polyethylene terephthalate) bottles and other packaging alternatives, Pforzheim: Institute of Applied Sciences Pforzheim, 2000, Available from: https://www.hs-pforzheim.de/fileadmin/user_upload/uploads_redakteur/Forschung/INEC/Dokumente/Team__Publikationen_/2000_LCA_PET_IAF_DP12.pdf Search PubMed.
- U. Arena, M. L. Mastellone and F. Perugini, Life Cycle assessment of a plastic packaging recycling system, Int. J. Life Cycle Assess., 2003, 8(2), 92–98 Search PubMed.
- C.-E. Komly, C. Azzaro-Pantel, A. Hubert, L. Pibouleau and V. Archambault, Multiobjective waste management optimization strategy coupling life cycle assessment and genetic algorithms: Application to PET bottles, Resour., Conserv. Recycl., 2012, 69, 66–81 CrossRef.
- T. Chilton, S. Burnley and S. Nesaratnam, A life cycle assessment of the closed-loop recycling and thermal recovery of post-consumer PET, Resour., Conserv. Recycl., 2010, 54(12), 1241–1249 CrossRef.
-
A. Tukker, Comparing Feedstock Recycling of Plastics Waste to Mechanical Recycling Methods, TNO, Holland, 2002 Search PubMed.
- H.-S. Song and J. C. Hyun, A study on the comparison of the various waste management scenarios for PET bottles using the life-cycle assessment (LCA) methodology, Resour., Conserv. Recycl., 1999, 27(3), 267–284 CrossRef.
- U. S. Chaudhari, D. G. Kulas, A. Peralta, T. Hossain, A. T. Johnson and D. Hartley,
et al., Solvent based dissolution-precipitation of waste polyethylene terephthalate: Economic and environmental performance metrics, RSC Sustainability, 2023, 1(7), 1849–1860 RSC.
-
U. S. Chaudhari, D. G. Kulas, A. Peralta, R. M. Handler, A. T. Johnson, B. K. Reck, et al., Environmental and economic analyses of chemical recycling via dissolution of waste polyethylene terephthalate, Technology Innovation for the Circular Economy, Wiley, 2024, pp. 255–67 Search PubMed.
- J. Nakatani, M. Fujii, Y. Moriguchi and M. Hirao, Life-cycle assessment of domestic and transboundary recycling of post-consumer PET bottles, Int. J. Life Cycle Assess., 2010, 15(6), 590–597 CrossRef CAS.
-
K. V. Marathe, K. R. Chavan and P. Nakhate, Life cycle assessment (LCA) of PET bottles, in Recycling of Polyethylene Terephthalate Bottles, Elsevier, 2019, pp. 149–68 Search PubMed.
- R. Meys, F. Frick, S. Westhues, A. Sternberg, J. Klankermayer and A. Bardow, Towards a circular economy for plastic packaging wastes – the environmental potential of chemical recycling, Resour., Conserv. Recycl., 2020, 162, 105010 CrossRef.
-
R. D. Allen and M. I. James, Chemical recycling of PET, in ACS Symposium Series, American Chemical Society, Washington, DC, 2021, pp. 61–80 Search PubMed.
-
A. Ragab and A. Ramzy, Cradle-to-gate life cycle assessment of bottle-to-bottle recycling plant: Case study, in Progress in IS, Springer International Publishing, Cham, 2023, pp. 3–15 Search PubMed.
- M. Tamoor, N. A. Samak, M. Yang and J. Xing, The cradle-to-cradle life cycle assessment of polyethylene terephthalate: Environmental perspective, Molecules, 2022, 27(5), 1599 CrossRef CAS PubMed.
- B. P. Weidema, M. Pizzol, J. Schmidt and G. Thoma, Attributional or consequential Life Cycle Assessment: A matter of social responsibility, J. Cleaner Prod., 2018, 174, 305–314 CrossRef.
- R. Rebolledo-Leiva, D. Ladakis, S.-M. Ioannidou, A. Koutinas, M. T. Moreira and S. González-García, Attributional and consequential life cycle perspectives of second-generation polylactic acid: The benefits of integrating a recycling strategy, J. Cleaner Prod., 2023, 420, 138354 CrossRef.
- W. T. Lang, S. A. Mehta, M. M. Thomas, D. Openshaw, E. Westgate and G. Bagnato, Chemical recycling of polyethylene terephthalate, an industrial and sustainable opportunity for Northwest of England, J. Environ. Chem. Eng., 2023, 11(5), 110585 CrossRef CAS.
- Y. Peng, J. Yang, C. Deng, J. Deng, L. Shen and Y. Fu, Acetolysis of waste polyethylene terephthalate for upcycling and life-cycle assessment study, Nat. Commun., 2023, 14(1), 3249 CrossRef CAS PubMed.
- A. Oromiehie and A. Mamizadeh, Recycling PET beverage bottles and improving properties, Polym. Int., 2004, 53(6), 728–732 CrossRef CAS.
- F. Welle, Twenty years of PET bottle to bottle recycling—An overview, Resour., Conserv. Recycl., 2011, 55(11), 865–875 CrossRef.
- A. Majumdar, S. Shukla, A. A. Singh and S. Arora, Circular fashion: Properties of fabrics made from mechanically recycled poly-ethylene terephthalate (PET) bottles, Resour., Conserv. Recycl., 2020, 161, 104915 Search PubMed.
- L. Shen, E. Worrell and M. K. Patel, Open-loop recycling: A LCA case study of PET bottle-to-fibre recycling, Resour., Conserv. Recycl., 2010, 55(1), 34–52 Search PubMed.
-
G. Valentino, Life Cycle Assessment of PET bottles: closed and open loop recycling in Denmark and Lombardy region, Milan: Politecnico di Milano, 2017, Available from: https://www.politesi.polimi.it/retrieve/a81cb05c-82be-616b-e053-1605fe0a889a/2017_10_Valentino.pdf.
- L. Chen, R. E. O. Pelton and T. M. Smith, Comparative life cycle assessment of fossil and bio-based polyethylene terephthalate (PET) bottles, J. Cleaner Prod., 2016, 137, 667–676 CAS.
- T. Semba, Y. Sakai, T. Sakanishi and A. Inaba, Greenhouse gas emissions of 100% bio-derived polyethylene terephthalate on its life cycle compared with petroleum-derived polyethylene terephthalate, J. Cleaner Prod., 2018, 195, 932–938 CrossRef CAS.
- I. Vural Gursel, C. Moretti, L. Hamelin, L. G. Jakobsen, M. M. Steingrimsdottir and M. Junginger,
et al., Comparative cradle-to-grave life cycle assessment of bio-based and petrochemical PET bottles, Sci. Total Environ., 2021, 793, 148642 CrossRef CAS PubMed.
- C. García-Velásquez and Y. van der Meer, Can we improve the environmental benefits of biobased PET production through local biomass value chains? – A life cycle assessment perspective, J. Cleaner Prod., 2022, 380, 135039 CrossRef.
-
S. Nessi, T. Sinkko, C. Bulgheroni, P. Garcia-Gutierrez, J. Giuntoli, A. Konti, et al.Life Cycle Assessment (LCA) of Alternative Feedstocks for Plastics Production. Part 2, Illustrative Case Studies, Publications Office of the European Union, Luxembourg, 2022, available from: DOI:10.2760/655230.
-
J.-J. Shen, Comparative Life Cycle Assessment of Polylactic Acid (PLA) and Polyethylene Terephthalate (PET), 2011 Search PubMed.
- F. Gironi and V. Piemonte, Life cycle assessment of polylactic acid and polyethylene terephthalate bottles for drinking water, Environ. Prog. Sustainable Energy, 2011, 30(3), 459–468 CrossRef CAS.
-
K. Khait, Recycling, plastics, Encyclopedia of Polymer Science and Technology, Wiley, 2003 Search PubMed.
-
L. Shen and E. Worrell, Plastic Recycling, in Handbook of Recycling, Elsevier, 2014, pp. 179–90 Search PubMed.
- K. Ragaert, L. Delva and K. Van Geem, Mechanical and chemical recycling of solid plastic waste, Waste Manage., 2017, 69, 24–58 CrossRef CAS PubMed.
- V. Lahtela and T. Kärki, Mechanical sorting processing of waste material before composite manufacturing – A review, J. Eng. Sci. Technol. Rev., 2018, 11(6), 35–46 CrossRef CAS.
-
S. Serranti and G. Bonifazi, Techniques for separation of plastic wastes, in Use of Recycled Plastics in Eco-Efficient Concrete, Elsevier, 2019, pp. 9–37 Search PubMed.
- Q. Duan and J. Li, Classification of common household plastic wastes combining multiple methods based on near-infrared spectroscopy, ACS ES&T Eng., 2021, 1(7), 1065–1073 Search PubMed.
- B. Ruj, V. Pandey, P. Jash and V. K. Srivastava, Sorting of plastic waste for effective recycling, Int. J. Appl. Sci. Eng. Res., 2015, 4(4), 564–571 CAS.
- K. Bernat, Post-consumer plastic waste management: From collection and sortation to mechanical recycling, Energies, 2023, 16(8), 3504 CAS.
- S. D. Mancini, J. A. S. Schwartzman, A. R. Nogueira, D. A. Kagohara and M. Zanin, Additional steps in mechanical recycling of PET, J. Cleaner Prod., 2010, 18(1), 92–100 Search PubMed.
- W.-Z. Choi, J.-M. Yoo and B.-G. Cho, Separation of individual plastics from mixed plastic waste by gravity separation processes, Geosyst. Eng., 2006, 9(3), 65–72 Search PubMed.
- A. V. M. Silveira, M. Cella, E. H. Tanabe and D. A. Bertuol, Application of tribo-electrostatic separation in the recycling of plastic wastes, Process Saf. Environ. Prot., 2018, 114, 219–228 CAS.
- F. Bezati, D. Froelich, V. Massardier and E. Maris, Addition
of X-ray fluorescent tracers into polymers, new technology for automatic sorting of plastics: Proposal for selecting some relevant tracers, Resour., Conserv. Recycl., 2011, 55(12), 1214–1221 Search PubMed.
-
B. L. Riise, M. B. Biddle and M. M. Fisher, X-Ray Fluorescence Spectroscopy In Plastics Recycling, 2000, Available from: https://www.semanticscholar.org/paper/X-RAY-FLUORESCENCE-SPECTROSCOPY-IN-PLASTICS-Riise-Biddle/721cb5efb312db855a89aaf9f9d0a99f059b2b55.
- F. Awaja and D. Pavel, Recycling of PET, Eur. Polym. J., 2005, 41(7), 1453–1477 CAS.
- British Plastics Federation, How is plastic recycled?, A step by step guide to recycling, British Plastics Federation, available from: https://www.bpf.co.uk/plastipedia/sustainability/how-is-plastic-recycled-a-step-by-step-guide-to-recycling.aspx.
- Cleaning and decontamination of plastic waste, Areyour. 2020, available from: https://www.areyour.org/en/2020/10/09/cleaning-and-decontamination-of-plastic-waste/.
-
P. P. Stoughton, Guidelines for Drying PET, 2014, vol. 60, pp. 50–55 Search PubMed.
- I. Berkane, I. Aracil and A. Fullana, Evaluation of thermal drying for the recycling of flexible plastics, Waste Manage., 2023, 168, 116–125 CAS.
- O. Horodytska, F. J. Valdés and A. Fullana, Centrifugal dewatering performance in plastic films recycling, Waste Manage., 2018, 80, 211–217 CAS.
- M. A. S. Spinac and M. A. De Paoli, Characterization of poly(ethylene terephtalate) after multiple processing cycles, J. Appl. Polym. Sci., 2001, 80(1), 20–25 Search PubMed.
- R. Assadi, X. Colin and J. Verdu, Irreversible structural changes during PET recycling by extrusion, Polymer, 2004, 45(13), 4403–4412 CAS.
- G. Botelho, A. Queirós, S. Liberal and P. Gijsman, Studies on thermal and thermo-oxidative degradation of poly(ethylene terephthalate) and poly(butylene terephthalate), Polym. Degrad. Stab., 2001, 74(1), 39–48 CAS.
- M. Edeleva, K. De Smit, S. Debrie, A. Verberckmoes, Y. W. Marien and D. R. D’hooge, Molecular scale-driven upgrading of extrusion technology for sustainable polymer processing and recycling, Curr. Opin. Green Sustainable Chem., 2023, 43, 100848 CAS.
-
X. Zhou, D. Yu and O. Barrera, Mechanics constitutive models for viscoelastic solid materials: Development and a critical review, in Advances in Applied Mechanics, Elsevier, 2023, pp. 189–321 Search PubMed.
- F. Masmoudi, F. Fenouillot, A. Mehri, M. Jaziri and E. Ammar, Characterization and quality assessment of recycled post-consumption poly(ethylene terephthalate) (PET), Environ. Sci. Pollut. Res. Int., 2018, 25(23), 23307–23314 CAS.
- H. Wu, S. Lv, Y. He and J.-P. Qu, The study of the thermomechanical degradation and mechanical properties of PET recycled by industrial-scale elongational processing, Polym. Test., 2019, 77, 105882 CAS.
- R. Franz, M. Huber, O.-G. Piringer, A. P. Damant, S. M. Jickells and L. Castle, Study of functional barrier properties of multilayer recycled poly(ethylene terephthalate) bottles for soft drinks, J. Agric. Food Chem., 1996, 44(3), 892–897 CAS.
-
S. Makkam and W. Harnnarongchai, Rheological and mechanical properties of recycled PET modified by reactive extrusion, Energy Procedia, 2014, vol. 56, pp. 547–53 Search PubMed.
- A. Cabanes, F. J. Valdés and A. Fullana, A review on VOCs from recycled plastics, Sustainable Mater. Technol., 2020, 25, e00179 CAS.
- SpecialChem, Quality needs demand enhanced plastics recycling processes, 2024, available from: https://omnexus.specialchem.com/tech-library/article/quality-needs-demand-enhanced-plastics-recycling-processes.
- J. Wang, S. Zhang, Y. Han, L. Zhang, Q. Wang and G. Wang,
et al., UiO-66(Zr/Ti) for catalytic PET polycondensation, Mol. Catal., 2022, 532, 112741 CrossRef CAS.
- B. Duh, Effect of antimony catalyst on solid-state polycondensation of poly(ethylene terephthalate), Polymer, 2002, 43(11), 3147–3154 CrossRef CAS.
- NGR – Next Generation Recyclingmaschinen, P:React – Polycondensation reactor for post-consumer and industrial PET recycling, 2018, available from: https://www.ngr-world.com/wp-content/uploads/2018/09/NGR_PREACT_191010_EN.pdf.
-
C. Hopmann, M. Adamy and A. Cohnen, Introduction to Reactive Extrusion, in Reactive Extrusion, Wiley-VCH Verlag GmbH & Co. KGaA, Weinheim, Germany, 2017, pp. 1–10 Search PubMed.
- Engineering News, PET processing using the LSP method (liquid state polycondensation) [Internet], 2013 Oct 10, available from: https://www.engineeringnews.co.za/article/company-annoucementspet-processing-using-the-lsp-method-liquid-state-polycondensation-2013-10-10.
- S. A. Cruz and M. Zanin, PET recycling: Evaluation of the solid state polymerization process, J. Appl. Polym. Sci., 2006, 99(5), 2117–2123 CrossRef CAS.
- J. P. Jog, Solid state processing of polymers: A review, Adv. Polym. Technol., 1993, 12(3), 281–289 CrossRef CAS.
- Phite Technology, Liquid state polymerization (LSP) line: PET IV increase solution [Internet], available from: https://www.phite.com/liquid-state-polymerization-lspline-pet-iv-increase-solution.
- M. Seier, V.-M. Archodoulaki, T. Koch, B. Duscher and M. Gahleitner, Polyethylene terephthalate based multilayer food packaging: Deterioration effects during mechanical recycling, Food Packag. Shelf Life, 2022, 33, 100890 CrossRef CAS.
- R. L. Smith, S. Takkellapati and R. C. Riegerix, Recycling of plastics in the United States: Plastic material flows and polyethylene terephthalate (PET) recycling processes, ACS Sustain. Chem. Eng., 2022, 10(6), 2084–2096 CrossRef CAS PubMed.
- W. Guo, X. Tang, G. Yin, Y. Gao and C. Wu, Low temperature solid-state extrusion of recycled poly(ethylene terephthalate) bottle scraps, J. Appl. Polym. Sci., 2006, 102(3), 2692–2699 CAS.
- M. V. Candal, M. Safari, M. Fernández, I. Otaegi, A. Múgica and M. Zubitur,
et al., Structure and properties of reactively extruded opaque post-consumer recycled PET, Polymers, 2021, 13(20), 3531 CAS.
- F. Awaja, F. Daver and E. Kosior, Recycled poly(ethylene terephthalate) chain extension by a reactive extrusion process, Polym. Eng. Sci., 2004, 44(8), 1579–1587 CAS.
- S. N. Vouyiouka, E. K. Karakatsani and C. D. Papaspyrides, Solid state polymerization, Prog. Polym. Sci., 2005, 30(1), 10–37 CAS.
- J. J. Benvenuta Tapia, M. Hernández Valdez, J. Cerna Cortez, V. M. Díaz García and H. Landeros Barrios, Improving the rheological and mechanical properties of recycled PET modified by macromolecular chain extenders synthesized by controlled radical polymerization, J. Polym. Environ., 2018, 26(11), 4221–4232 CAS.
-
L. Delva, K. Van Kets, M. Kuzmanović, R. Demets, S. Hubo, N. Mys, S. De Meester and K. Ragaert, An Introductory Review: Mechanical Recycling of Polymers for Dummies, 2019 Search PubMed.
- EFSA Panel on Food Contact Materials, Enzymes and Processing Aids (CEP), V. Silano, J. M. Barat Baviera, C. Bolognesi, B. J. Brüschweiler and A. Chesson,
et al., Safety assessment of the process Alimpet, based on EREMA MPR B2B technology, used to recycle post-consumer PET into food contact materials, EFSA J., 2019, 17(5), e05677 Search PubMed.
- VACUREMA® MPR, [Internet], EREMA Group, available from: https://www.erema.com/en/vacurema_mpr/.
- VACUREMA® Inline, [Internet], EREMA Group, available from: https://www.erema.com/assets/media_center/folder/vacurema_inline_2022_03_en.pdf.
- Vacurema, [Internet], DKSH Direct, available from: https://direct.dksh.com.au/files/product_docs/Vacurema.pdf.
- EFSA Panel on Food Contact Materials, Enzymes and Processing Aids (CEP), V. Silano, J. M. Barat Baviera, C. Bolognesi, A. Chesson and P. S. Cocconcelli,
et al., Safety assessment of the process Buergofol, based on EREMA Basic technology, used to recycle post-consumer PET into food contact materials, EFSA J., 2020, 18(3), e06051 Search PubMed.
- EFSA Panel on Food Contact Materials, Enzymes and Processing Aids (CEP), V. Silano, J. M. Barat Baviera, C. Bolognesi, A. Chesson and P. S. Cocconcelli,
et al., Safety assessment of the process ONDUPET, based on EREMA Basic technology, used to recycle post-consumer PET into food contact materials, EFSA J., 2020, 18(10), e06251 Search PubMed.
- EFSA Panel on Food Contact Materials, Enzymes and Processing Aids (CEP), V. Silano, J. M. Barat Baviera, C. Bolognesi, A. Chesson and P. S. Cocconcelli,
et al., Safety assessment of the process RE-PET, based on EREMA Basic technology, used to recycle post-consumer PET into food contact materials, EFSA J., 2020, 18(3), e06049 Search PubMed.
- EFSA Panel on Food Contact Materials, Enzymes and Processing Aids (CEP), V. Silano, J. M. Barat Baviera, C. Bolognesi, A. Chesson and P. S. Cocconcelli,
et al., Safety assessment of the process Quinn Packaging, based on Erema Basic technology, used to recycle post-consumer PET into food contact materials, EFSA J., 2019, 17(7), e05771 Search PubMed.
- EFSA Panel on Food Contact Materials, Enzymes and Processing Aids (CEP), V. Silano, J. M. Barat Baviera, C. Bolognesi, A. Chesson and P. S. Cocconcelli,
et al., Safety assessment of the process STF, based on EREMA Basic technology, used to recycle post-consumer PET into food contact materials, EFSA J., 2020, 18(3), e06050 Search PubMed.
- EFSA Panel on Food Contact Materials, Enzymes and Processing Aids (CEP), C. Lambré, J. M. Barat Baviera, C. Bolognesi, A. Chesson and P. S. Cocconcelli,
et al., Safety assessment of the process NAN YA PLASTICS, based on the EREMA Basic technology, used to recycle post-consumer PET into food contact materials, EFSA J., 2022, 20(5), e07234 Search PubMed.
- EFSA Panel on Food Contact Materials, Enzymes and Processing Aids (CEP), C. Lambré, J. M. Barat Baviera, C. Bolognesi, A. Chesson and P. S. Cocconcelli,
et al., Safety assessment of the process Utsumi, based on the EREMA Basic technology, used to recycle post-consumer PET into food contact materials, EFSA J., 2022, 20(5), e07278 Search PubMed.
- EFSA Panel on Food Contact Materials, Enzymes and Processing Aids (CEP), C. Lambré, J. M. Barat Baviera, C. Bolognesi, A. Chesson and P. S. Cocconcelli,
et al., Safety assessment of the process Zibo Containers, based on the EREMA Basic technology, used to recycle post-consumer PET into food contact materials, EFSA J., 2022, 20(5), e07233 Search PubMed.
- EFSA Panel on Food Contact Materials, Enzymes and Processing Aids (CEP), C. Lambré, J. M. B. Baviera, C. Bolognesi, A. Chesson and P. S. Cocconcelli,
et al., Safety assessment of the process Zhenjiang Ceville, based on the EREMA Basic technology, used to recycle post-consumer PET into food contact materials, EFSA J., 2023, 21(3), e07831 Search PubMed.
- EFSA Panel on Food Contact Materials, Enzymes and Processing Aids (CEP), C. Lambré, J. M. Barat Baviera, C. Bolognesi, A. Chesson and P. S. Cocconcelli,
et al., Safety assessment of the process Cirrec Netherlands BV, based on the EREMA Basic technology, used to recycle post-consumer PET into food contact materials, EFSA J., 2023, 21(7), e08086 Search PubMed.
- EFSA Panel on Food Contact Materials, Enzymes and Processing Aids (CEP), C. Lambré, J. M. Barat Baviera, C. Bolognesi, A. Chesson and P. S. Cocconcelli,
et al., Safety assessment of the process INTCO MALAYSIA, based on the EREMA Basic technology, used to recycle post-consumer PET into food contact materials, EFSA J., 2022, 20(5), e07232 Search PubMed.
- EFSA Panel on Food Contact Materials, Enzymes and Processing Aids (CEP), V. Silano, J. M. Barat Baviera, C. Bolognesi, B. J. Brüschweiler and A. Chesson,
et al., Safety assessment of the process Texplast, based on EREMA Advanced technology, used to recycle post-consumer PET into food contact materials, EFSA J., 2019, 17(5), e05678 Search PubMed.
- EFSA Panel on Food Contact Materials, Enzymes and Processing Aids (EFSA CEP Panel), V. Silano, J. M. Barat Baviera, C. Bolognesi, B. J. Brüschweiler and A. Chesson,
et al., Safety assessment of the process “Jász-Plasztik”, based on Vacurema Prime technology, used to recycle post-consumer PET into food contact materials, EFSA J., 2019, 17(3), e05627 Search PubMed.
- EFSA Panel on Food Contact Materials, Enzymes and Processing Aids (CEP), C. Lambré, J. M. Barat Baviera, C. Bolognesi, A. Chesson and P. S. Cocconcelli,
et al., Safety assessment of the process Coca-Cola HBC Polska, based on the Vacurema
Prime technology, used to recycle post-consumer PET into food contact materials, EFSA J., 2022, 20(3), e07189 Search PubMed.
- VACUNITE® & VACUREMA® B2B, [Internet], EREMA Group, available from: https://www.erema.com/assets/media_center/folder/vacunite_vacurema_b2b_2022_09_en.pdf.
- EFSA Panel on Food Contact Materials, Enzymes and Processing Aids (CEP), C. Lambré, J. M. Barat Baviera, C. Bolognesi, A. Chesson and P. S. Cocconcelli,
et al., Safety assessment of the process Ambiental de Plasticos Recyclapet, based on the Vacurema Prime technology, used to recycle post-consumer PET into food contact materials, EFSA J., 2023, 21(10), e08266 Search PubMed.
- EFSA Panel on Food Contact Materials, Enzymes and Processing Aids (CEP), C. Lambré, J. M. Barat Baviera, C. Bolognesi, A. Chesson and P. S. Cocconcelli,
et al., Safety assessment of the process Creative Recycling World Company, based on the Vacurema Prime technology, used to recycle post-consumer PET into food contact materials, EFSA J., 2023, 21(3), e07921 Search PubMed.
- EFSA Panel on Food Contact Materials, Enzymes and Processing Aids (CEP), C. Lambré, J. M. Barat Baviera, C. Bolognesi, A. Chesson and P. S. Cocconcelli,
et al., Safety assessment of the process Bangladesh Petrochemical Company, based on the Vacurema Prime technology, used to recycle post-consumer PET into food contact materials, EFSA J., 2022, 20(6), e07360 Search PubMed.
- EFSA Panel on Food Contact Materials, Enzymes and Processing Aids (CEP), C. Lambré, J. M. Barat Baviera, C. Bolognesi, A. Chesson and P. S. Cocconcelli,
et al., Safety assessment of the process Shangrao Bisource Technology, based on the Vacurema Prime technology, used to recycle post-consumer PET into food contact materials, EFSA J., 2023, 21(10), e08268 Search PubMed.
- EFSA Panel on Food Contact Materials, Enzymes and Processing Aids (CEP), C. Lambré, J. M. Barat Baviera, C. Bolognesi, A. Chesson and P. S. Cocconcelli,
et al., Safety assessment of the process Poly Recycling, based on the Vacurema Prime technology, used to recycle post-consumer PET into food contact materials, EFSA J., 2023, 21(10), e08269 Search PubMed.
- EFSA Panel on Food Contact Materials, Enzymes and Processing Aids (CEP), C. Lambré, J. M. Barat Baviera, C. Bolognesi, A. Chesson and P. S. Cocconcelli,
et al., Safety assessment of the process Acepolymer, based on the Vacurema Prime technology, used to recycle post-consumer PET into food contact materials, EFSA J., 2023, 21(10), e08267 Search PubMed.
- Starlinger, recoSTAR PET food [Internet], available from: https://www.starlinger.com/en/recycling/recostar-product-line/recostar-pet-food/.
- PET to PET significantly increases capacities for food-grade rPET with new Starlinger line, [Internet], Packaging Magazine, available from: https://www.packaging-mag.com/pet-to-pet-significantly-increases-capacities-for-food-grade-rpet-with-new-starlinger-line/.
- Starlinger, recoSTAR PET, [Internet], available from: https://www.starlinger.com/fileadmin/user_upload/03_recycling_technology/recoSTAR_PET/FB_en/index.html.
- RecoSTAR PET, [Internet], CovemaTex, available from: https://www.covematex.be/uploads/recoSTARPET.pdf.
- EFSA Panel on Food Contact Materials, Enzymes and Processing Aids (CEP), V. Silano, J. M. Barat Baviera, C. Bolognesi, A. Chesson and P. S. Cocconcelli,
et al., Safety assessment of the process Poly Recycling, based on recoSTAR PET FG technology, used to recycle post-consumer PET into food contact materials, EFSA J., 2019, 17(10), e05836 Search PubMed.
- EFSA Panel on Food Contact Materials, Enzymes and, Processing Aids (CEP), C. Lambré, J. M. Barat Baviera, C. Bolognesi, A. Chesson and P. S. Cocconcelli,
et al., Safety assessment of the process Ester Industries, based on the recoSTAR PET FG technology, used to recycle post-consumer PET into food contact materials, EFSA J., 2022, 20(12), e07653 Search PubMed.
- EFSA Panel on Food Contact Materials, Enzymes and Processing Aids (CEP), V. Silano, J. M. Barat Baviera, C. Bolognesi, A. Chesson and P. S. Cocconcelli,
et al., Safety assessment of the process Poly Recycling, based on Starlinger iV+ technology, used to recycle post-consumer PET into food contact materials, EFSA J., 2019, 17(7), e05772 Search PubMed.
- EFSA Panel on Food Contact Materials, Enzymes and Processing Aids (CEP), V. Silano, J. M. Barat Baviera, C. Bolognesi, A. Chesson and P. S. Cocconcelli,
et al., Safety assessment of the process Texplast, based on Starlinger iV+ technology, used to recycle post-consumer PET into food contact materials, EFSA J., 2019, 17(7), e05773 Search PubMed.
- EFSA Panel on Food Contact Materials, Enzymes and Processing Aids (CEP), C. Lambré, J. M. Barat Baviera, C. Bolognesi, A. Chesson and P. S. Cocconcelli,
et al., Safety assessment of the process ESTERPET, based on Starlinger iV+ technology, used to recycle post-consumer PET into food contact materials, EFSA J., 2021, 19(8), e06789 Search PubMed.
- EFSA Panel on Food Contact Materials, Enzymes and Processing Aids (CEP), C. Lambré, J. M. Barat Baviera, C. Bolognesi, A. Chesson and P. S. Cocconcelli,
et al., Safety assessment of the process HIROYUKI INDUSTRIES, based on Starlinger iV+ technology, used to recycle post-consumer PET into food contact materials, EFSA J., 2021, 19(8), e06793 Search PubMed.
- EFSA Panel on Food Contact Materials, Enzymes and Processing Aids (CEP), C. Lambré, J. M. Barat Baviera, C. Bolognesi, A. Chesson and P. S. Cocconcelli,
et al., Safety assessment of the process Nosoplas, based on Starlinger iV+ technology, used to recycle post-consumer PET into food contact materials, EFSA J., 2021, 19(8), e06798 Search PubMed.
- EFSA Panel on Food Contact Materials, Enzymes and Processing Aids (CEP), C. Lambré, J. M. Barat Baviera, C. Bolognesi, A. Chesson and P. S. Cocconcelli,
et al., Safety assessment of the process PET STAR RECYCLING, based on Starlinger iV+ technology, used to recycle post-consumer PET into food contact materials, EFSA J., 2021, 19(8), e06791 Search PubMed.
- EFSA Panel on Food Contact Materials, Enzymes and Processing Aids (CEP), C. Lambré, J. M. Barat Baviera, C. Bolognesi, A. Chesson and P. S. Cocconcelli,
et al., Safety assessment of the process RECICLADOS INDUSTRIALES DE PRAVIA (RECINPRA), based on Starlinger iV+ technology, used to recycle post-consumer PET into food contact materials, EFSA J., 2021, 19(8), e06792 Search PubMed.
- EFSA Panel on Food Contact Materials, Enzymes and Processing Aids (CEP), C. Lambré, J. M. Barat Baviera, C. Bolognesi, A. Chesson and P. S. Cocconcelli,
et al., Safety assessment of the process Viridor Waste Management, based on Starlinger iV+ technology, used to recycle post-consumer PET into food contact materials, EFSA J., 2021, 19(8), e06788 Search PubMed.
- EFSA Panel on Food Contact Materials, Enzymes and Processing Aids (CEP), C. Lambré, J. M. Barat Baviera, C. Bolognesi, A. Chesson and P. S. Cocconcelli,
et al., Safety assessment of the process Alef Recycling, based on the Starlinger iV+ technology, used to recycle post-consumer PET into food contact materials, EFSA J., 2022, 20(12), e07672 Search PubMed.
- EFSA Panel on Food Contact Materials, Enzymes and Processing Aids (CEP), C. Lambré, J. M. Barat Baviera, C. Bolognesi, A. Chesson and P. S. Cocconcelli,
et al., Safety assessment of the process Biffa Waste Services, based on the Starlinger iV+ technology, used to recycle post-consumer PET into food contact materials, EFSA J., 2022, 20(1), e07015 Search PubMed.
- EFSA Panel on Food Contact Materials, Enzymes and Processing Aids (CEP), C. Lambré, J. M. Barat Baviera, C. Bolognesi, A. Chesson and P. S. Cocconcelli,
et al., Safety assessment of the process Brunetti Packaging, based on the Starlinger iV+ technology, used to recycle post-consumer PET into food contact materials, EFSA J., 2022, 20(8), e07469 Search PubMed.
- EFSA Panel on Food Contact Materials, Enzymes and Processing Aids (CEP), C. Lambré, J. M. Barat Baviera, C. Bolognesi, A. Chesson and P. S. Cocconcelli,
et al., Safety assessment of the process Circular Plastics, based on the Starlinger iV+ technology, used to recycle post-consumer PET into food contact materials, EFSA J., 2022, 20(1), e07019 Search PubMed.
- EFSA Panel on Food Contact Materials, Enzymes and Processing Aids (CEP), C. Lambré, J. M. Barat Baviera, C. Bolognesi, A. Chesson and P. S. Cocconcelli,
et al., Safety assessment of the process Circularpet IV80, based on the Starlinger iV+ technology, used to recycle post-consumer PET into food contact materials, EFSA J., 2022, 20(7), e07385 Search PubMed.
- EFSA Panel on Food Contact Materials, Enzymes and Processing Aids (CEP), C. Lambré, J. M. Barat Baviera, C. Bolognesi, A. Chesson and P. S. Cocconcelli,
et al., Safety assessment of the process DENTIS RECYCLING Italy, based on the Starlinger iV+ technology, used to recycle post-consumer PET into food contact materials, EFSA J., 2022, 20(1), e07016 Search PubMed.
- EFSA Panel on Food Contact Materials, Enzymes and Processing Aids (CEP), C. Lambré, J. M. Barat Baviera, C. Bolognesi, A. Chesson and P. S. Cocconcelli,
et al., Safety assessment of the process Duy Tan Plastic Recycling, based on the Starlinger iV+ technology, used to recycle post-consumer PET into food contact materials, EFSA J., 2022, 20(12), e07671 Search PubMed.
- EFSA Panel on Food Contact Materials, Enzymes and Processing Aids (CEP), C. Lambré, J. M. Barat Baviera, C. Bolognesi, A. Chesson and P. S. Cocconcelli,
et al., Safety assessment of the process Extremadura TorrePet, based on the Starlinger iV+ technology, used to recycle post-consumer PET into food contact materials, EFSA J., 2022, 20(7), e07388 Search PubMed.
- EFSA Panel on Food Contact Materials, Enzymes and Processing Aids (CEP), C. Lambré, J. M. Barat Baviera, C. Bolognesi, A. Chesson and P. S. Cocconcelli,
et al., Safety assessment of the process Ferrarelle, based on the Starlinger iV+ technology, used to recycle post-consumer PET into food contact materials, EFSA J., 2022, 20(1), e07017 Search PubMed.
- EFSA Panel on Food Contact Materials, Enzymes and Processing Aids (CEP), C. Lambré, J. M. Barat Baviera, C. Bolognesi, A. Chesson and P. S. Cocconcelli,
et al., Safety assessment of the process Ganesha ecosphere, based on the Starlinger iV+ technology, used to recycle post-consumer PET into food contact materials, EFSA J., 2022, 20(7), e07386 Search PubMed.
- EFSA Panel on Food Contact Materials, Enzymes and Processing Aids (CEP), C. Lambré, J. M. Barat Baviera, C. Bolognesi, A. Chesson and P. S. Cocconcelli,
et al., Safety assessment of the process Greenpet, based on the Starlinger iV+ technology, used to recycle post-consumer PET into food contact materials, EFSA J., 2022, 20(7), e07387 Search PubMed.
- EFSA Panel on Food Contact Materials, Enzymes and Processing Aids (CEP), C. Lambré, J. M. Barat Baviera, C. Bolognesi, A. Chesson and P. S. Cocconcelli,
et al., Safety assessment of the process OMT Recycling Project, based on the Starlinger iV+ technology, used to recycle post-consumer PET into food contact materials, EFSA J., 2022, 20(1), e07018 Search PubMed.
- EFSA Panel on Food Contact Materials, Enzymes and Processing Aids (CEP), C. Lambré, J. M. Barat Baviera, C. Bolognesi, A. Chesson and P. S. Cocconcelli,
et al., Safety assessment of the process Resinas del Ecuador, based on the Starlinger iV+ technology, used to recycle post-consumer PET into food contact materials, EFSA J., 2022, 20(1), e07021 Search PubMed.
- EFSA Panel on Food Contact Materials, Enzymes and Processing Aids (CEP), C. Lambré, J. M. Barat Baviera, C. Bolognesi, A. Chesson and P. S. Cocconcelli,
et al., Safety assessment of the process rPET Aviv Shalam, based on the Starlinger iV+ technology, used to recycle post-consumer PET into food contact materials, EFSA J., 2022, 20(12), e07670 Search PubMed.
- EFSA Panel on Food Contact Materials, Enzymes and Processing Aids (CEP), C. Lambré, J. M. Barat Baviera, C. Bolognesi, A. Chesson and P. S. Cocconcelli,
et al., Safety assessment of the process Srichakra Polyplast, based on the Starlinger iV+ technology, used to recycle post-consumer PET into food contact materials, EFSA J., 2022, 20(1), e07020 Search PubMed.
- EFSA Panel on Food Contact Materials, Enzymes and Processing Aids (CEP), C. Lambré, J. M. Barat Baviera, C. Bolognesi, A. Chesson and P. S. Cocconcelli,
et al., Safety assessment of the process Veolia, based on the Starlinger iV+ technology, used to recycle post-consumer PET into food contact materials, EFSA J., 2022, 20(3), e07187 Search PubMed.
- EFSA Panel on Food Contact Materials, Enzymes and Processing Aids (CEP), C. Lambré, J. M. Barat Baviera, C. Bolognesi, A. Chesson and P. S. Cocconcelli,
et al., Safety assessment of the process Akmert İplik, based on the Starlinger iV+ technology, used to recycle post-consumer PET into food contact materials, EFSA J., 2023, 21(3), e07924 Search PubMed.
- EFSA Panel on Food Contact Materials, Enzymes and Processing Aids (CEP), C. Lambré, J. M. Barat Baviera, C. Bolognesi, A. Chesson and P. S. Cocconcelli,
et al., Safety assessment of the process Basatli Boru Profil, based on the Starlinger iV+ technology, used to recycle post-consumer PET into food contact materials, EFSA J., 2023, 21(3), e07923 Search PubMed.
- EFSA Panel on Food Contact Materials, Enzymes and Processing Aids (CEP), C. Lambré, J. M. Barat Baviera, C. Bolognesi, A. Chesson and P. S. Cocconcelli,
et al., Safety assessment of the process Commercial Plastics, based on the Starlinger iV+ technology,
used to recycle post-consumer PET into food contact materials, EFSA J., 2023, 21(3), e07925 Search PubMed.
- EFSA Panel on Food Contact Materials, Enzymes and Processing Aids (CEP), C. Lambré, J. M. Barat Baviera, C. Bolognesi, A. Chesson and P. S. Cocconcelli,
et al., Safety assessment of the process Dialog Diyou PCR, based on the Starlinger iV+ technology, used to recycle post-consumer PET into food contact materials, EFSA J., 2023, 21(8), e08132 Search PubMed.
- EFSA Panel on Food Contact Materials, Enzymes and Processing Aids (CEP), C. Lambré, J. M. Barat Baviera, C. Bolognesi, A. Chesson and P. S. Cocconcelli,
et al., Safety assessment of the process General Plastic, based on the Starlinger iV+ technology, used to recycle post-consumer PET into food contact materials, EFSA J., 2023, 21(3), e07926 Search PubMed.
- EFSA Panel on Food Contact Materials; Enzymes and Processing Aids (CEP), C. Lambré, J. M. Barat Baviera, C. Bolognesi, A. Chesson and P. S. Cocconcelli,
et al., Safety assessment of the process Green PET Recycling, based on the Starlinger iV+ technology, used to recycle post-consumer PET into food contact materials, EFSA J., 2023, 21(3), e07928 Search PubMed.
- EFSA Panel on Food Contact Materials, Enzymes and Processing Aids (CEP), C. Lambré, J. M. Barat Baviera, C. Bolognesi, A. Chesson and P. S. Cocconcelli,
et al., Safety assessment of the process Lerg-Pet, based on the Starlinger iV+ technology, used to recycle post-consumer PET into food contact materials, EFSA J., 2023, 21(8), e08133 Search PubMed.
- EFSA Panel on Food Contact Materials, Enzymes and Processing Aids (CEP), C. Lambré, J. M. Barat Baviera, C. Bolognesi, A. Chesson and P. S. Cocconcelli,
et al., Safety assessment of the process PCR Ambalaj, based on the Starlinger iV+ technology, used to recycle post-consumer PET into food contact materials, EFSA J., 2023, 21(8), e08130 Search PubMed.
- EFSA Panel on Food Contact Materials, Enzymes and Processing Aids (CEP), C. Lambré, J. M. Barat Baviera, C. Bolognesi, A. Chesson and P. S. Cocconcelli,
et al., Safety assessment of the process Royce Universal, based on the Starlinger iV+ technology, used to recycle post-consumer PET into food contact materials, EFSA J., 2023, 21(3), e07927 Search PubMed.
- EFSA Panel on Food Contact Materials, Enzymes and Processing Aids (CEP), C. Lambré, J. M. Barat Baviera, C. Bolognesi, A. Chesson and P. S. Cocconcelli,
et al., Safety assessment of the process Tanrikulu Plastik, based on the Starlinger iV+ technology, used to recycle post-consumer PET into food contact materials, EFSA J., 2023, 21(8), e08131 Search PubMed.
- Decontamination at the highest level [Internet], Kunststoffe International, available from: https://en.kunststoffe.de/a/news/decontamination-at-the-highest-level-3357425.
- EFSA Panel on Food Contact Materials, Enzymes and Processing Aids (CEP), V. Silano, J. M. Barat Baviera, C. Bolognesi, A. Chesson and P. S. Cocconcelli,
et al., Safety assessment of the process Veripack Embalajes, based on Starlinger Decon technology, used to recycle post-consumer PET into food contact materials, EFSA J., 2019, 17(10), e05835 Search PubMed.
- EFSA Panel on Food Contact Materials, Enzymes and Processing Aids (CEP), V. Silano, J. M. Barat Baviera, C. Bolognesi, A. Chesson and P. S. Cocconcelli,
et al., Safety assessment of the process Ferrarelle, based on Starlinger Decon technology, used to recycle post-consumer PET into food contact materials, EFSA J., 2019, 17(10), e05834 Search PubMed.
- EFSA Panel on Food Contact Materials, Enzymes and Processing Aids (CEP), V. Silano, J. M. Barat Baviera, C. Bolognesi, A. Chesson and P. S. Cocconcelli,
et al., Safety assessment of the process Pinaform, based on Starlinger Decon technology, used to recycle post-consumer PET into food contact materials, EFSA J., 2019, 17(10), e05833 Search PubMed.
- EFSA Panel on Food Contact Materials, Enzymes and Processing Aids (CEP), V. Silano, J. M. Barat Baviera, C. Bolognesi, A. Chesson and P. S. Cocconcelli,
et al., Safety assessment of the process V & T Trade, based on Starlinger Decon technology, used to recycle post-consumer PET into food contact materials, EFSA J., 2019, 17(10), e05831 Search PubMed.
- EFSA Panel on Food Contact Materials, Enzymes and Processing Aids (CEP), V. Silano, J. M. Barat Baviera, C. Bolognesi, A. Chesson and P. S. Cocconcelli,
et al., Safety assessment of the process Reco-Kavala, based on Starlinger Decon technology, used to recycle post-consumer PET into
food contact materials, EFSA J., 2019, 17(10), e05830 Search PubMed.
- EFSA Panel on Food Contact Materials, Enzymes and Processing Aids (CEP), V. Silano, J. M. Barat Baviera, C. Bolognesi, A. Chesson and P. S. Cocconcelli,
et al., Safety assessment of the process PETman, based on Starlinger Decon technology, used to recycle post-consumer PET into food contact materials, EFSA J., 2019, 17(10), e05829 Search PubMed.
- EFSA Panel on Food Contact Materials, Enzymes and Processing Aids (CEP), V. Silano, J. M. Barat Baviera, C. Bolognesi, A. Chesson and P. S. Cocconcelli,
et al., Safety assessment of the process Marcato, based on Starlinger Decon technology, used to recycle post-consumer PET into food contact materials, EFSA J., 2019, 17(10), e05828 Search PubMed.
- EFSA Panel on Food Contact Materials, Enzymes and Processing Aids (CEP), V. Silano, J. M. Barat Baviera, C. Bolognesi, A. Chesson and P. S. Cocconcelli,
et al., Safety assessment of the process Ltd PolyER, based on Starlinger deCON technology, used to recycle post-consumer PET into food contact materials, EFSA J., 2020, 18(3), e06045 Search PubMed.
- EFSA Panel on Food Contact Materials, Enzymes and Processing Aids (CEP), V. Silano, J. M. Barat Baviera, C. Bolognesi, A. Chesson and P. S. Cocconcelli,
et al., Safety assessment of the process Carton Pack, based on Starlinger deCON technology, used to recycle post-consumer PET into food contact materials, EFSA J., 2020, 18(7), e06188 Search PubMed.
- EFSA Panel on Food Contact Materials, Enzymes and Processing Aids (CEP), V. Silano, J. M. Barat Baviera, C. Bolognesi, A. Chesson and P. S. Cocconcelli,
et al., Safety assessment of the process WIP, based on Starlinger deCON technology, used to recycle post-consumer PET into food contact materials, EFSA J., 2020, 18(7), e06187 Search PubMed.
- EFSA Panel on Food Contact Materials, Enzymes and Processing Aids (CEP), V. Silano, J. M. Barat Baviera, C. Bolognesi, A. Chesson and P. S. Cocconcelli,
et al., Safety assessment of the process sicht-pack Hagner, based on Starlinger deCON technology, used to recycle post-consumer PET into food contact materials, EFSA J., 2020, 18(10), e06256 Search PubMed.
- EFSA Panel on Food Contact Materials, Enzymes and Processing Aids (CEP), V. Silano, J. M. Barat Baviera, C. Bolognesi, A. Chesson and P. S. Cocconcelli,
et al., Safety assessment of the process Erreplast, based on Starlinger deCON technology, used to recycle post-consumer PET into food contact materials, EFSA J., 2020, 18(10), e06255 Search PubMed.
- EFSA Panel on Food Contact Materials, Enzymes and Processing Aids (CEP), V. Silano, J. M. Barat Baviera, C. Bolognesi, A. Chesson and P. S. Cocconcelli,
et al., Safety assessment of the process PT Asiaplast, based on Starlinger deCON technology, used to recycle post-consumer PET into food contact materials, EFSA J., 2020, 18(10), e06254 Search PubMed.
- EFSA Panel on Food Contact Materials, Enzymes and Processing Aids (CEP), V. Silano, J. M. Barat Baviera, C. Bolognesi, A. Chesson and P. S. Cocconcelli,
et al., Safety assessment of the process Flight Plastics (UK), based on Starlinger deCON technology, used to recycle post-consumer PET into food contact materials, EFSA J., 2020, 18(10), e06253 Search PubMed.
- EFSA Panel on Food Contact Materials, Enzymes and Processing Aids (CEP), V. Silano, J. M. Barat Baviera, C. Bolognesi, A. Chesson and P. S. Cocconcelli,
et al., Safety assessment of the process Somoplast – Riachi & Co, based on Starlinger deCON technology, used to recycle post-consumer PET into food contact materials, EFSA J., 2020, 18(10), e06252 Search PubMed.
- EFSA Panel on Food Contact Materials, Enzymes and Processing Aids (CEP), V. Silano, J. M. Barat Baviera, C. Bolognesi, A. Chesson and P. S. Cocconcelli,
et al., Safety assessment of the process Severn Valley Polymers, based on Starlinger deCON technology, used to recycle post-consumer PET into food contact materials, EFSA J., 2020, 18(11), e06308 Search PubMed.
- EFSA Panel on Food Contact Materials, Enzymes and Processing Aids (CEP), C. Lambré, J. M. Barat Baviera, C. Bolognesi, A. Chesson and P. S. Cocconcelli,
et al., Safety assessment of the process ROL, based on Starlinger deCON technology, used to recycle post-consumer PET into food contact materials, EFSA J., 2021, 19(6), e06644 Search PubMed.
- EFSA Panel on Food Contact Materials, Enzymes and Processing Aids (CEP), C. Lambré, J. M. Barat Baviera, C. Bolognesi, A. Chesson and P. S. Cocconcelli,
et al., Safety assessment of the process ISAP Packaging, based on Starlinger deCON technology, used to recycle post-consumer PET into food contact materials, EFSA J., 2021, 19(6), e06643 Search PubMed.
- EFSA Panel on Food Contact Materials, Enzymes and Processing Aids (CEP), C. Lambré, J. M. Barat Baviera, C. Bolognesi, A. Chesson and P. S. Cocconcelli,
et al., Safety assessment of the process Drava International, based on Starlinger deCON technology, used to recycle post-consumer PET into food contact materials, EFSA J., 2021, 19(6), e06642 Search PubMed.
- EFSA Panel on Food Contact Materials, Enzymes and Processing Aids (CEP), C. Lambré, J. M. Barat Baviera, C. Bolognesi, A. Chesson and P. S. Cocconcelli,
et al., Safety assessment of the process Marmara PET Levha, based on Starlinger deCON technology, used to recycle post-consumer PET into food contact materials, EFSA J., 2021, 19(10), e06868 Search PubMed.
- EFSA Panel on Food Contact Materials, Enzymes and Processing Aids (CEP), C. Lambré, J. M. Barat Baviera, C. Bolognesi, A. Chesson and P. S. Cocconcelli,
et al., Safety assessment of the process Sulpet Plásticos, based on Starlinger deCON technology, used to recycle post-consumer PET into food contact materials, EFSA J., 2021, 19(10), e06867 Search PubMed.
- EFSA Panel on Food Contact Materials, Enzymes and Processing Aids (CEP), C. Lambré, J. M. Barat Baviera, C. Bolognesi, A. Chesson and P. S. Cocconcelli,
et al., Safety assessment of the process BPCL, based on Starlinger deCON technology, used to recycle post-consumer PET into food contact materials, EFSA J., 2021, 19(10), e06866 Search PubMed.
- EFSA Panel on Food Contact Materials, Enzymes and Processing Aids (CEP), C. Lambré, J. M. Barat Baviera, C. Bolognesi, A. Chesson and P. S. Cocconcelli,
et al., Safety assessment of the process UTSUMI RECYCLE SYSTEMS, based on Starlinger deCON technology, used to recycle post-consumer PET into food contact materials, EFSA J., 2021, 19(10), e06869 Search PubMed.
- EFSA Panel on Food Contact Materials, Enzymes and Processing Aids (CEP), C. Lambré, J. M. Barat Baviera, C. Bolognesi, A. Chesson and P. S. Cocconcelli,
et al., Safety assessment of the process Greiner Packaging, based on Starlinger deCON technology, used to recycle post-consumer PET into food contact materials, EFSA J., 2022, 20(6), e07389 Search PubMed.
- EFSA Panel on Food Contact Materials, Enzymes and Processing Aids (CEP), C. Lambré, J. M. Barat Baviera, C. Bolognesi, A. Chesson and P. S. Cocconcelli,
et al., Safety assessment of the process Kalex Films, based on Starlinger deCON technology, used to recycle post-consumer PET into food contact materials, EFSA J., 2022, 20(6), e07382 Search PubMed.
- EFSA Panel on Food Contact Materials, Enzymes and Processing Aids (CEP), C. Lambré, J. M. B. Baviera, C. Bolognesi, A. Chesson and P. S. Cocconcelli,
et al., Safety assessment of the process Polyfab Plastics, based on Starlinger deCON technology, used to recycle post-consumer PET into food contact materials, EFSA J., 2022, 20(11), e07579 Search PubMed.
- EFSA Panel on Food Contact Materials, Enzymes and Processing Aids (CEP), C. Lambré, J. M. Barat Baviera, C. Bolognesi, A. Chesson and P. S. Cocconcelli,
et al., Safety assessment of the process Petecoflex, based on the Starlinger deCON technology, used to recycle post-consumer PET into food contact materials, EFSA J., 2023, 21(1), e07760 Search PubMed.
- EFSA Panel on Food Contact Materials, Enzymes and Processing Aids (CEP), C. Lambré, J. M. B. Baviera, C. Bolognesi, A. Chesson and P. S. Cocconcelli,
et al., Safety assessment of the process Derchia D.C. Plastics, based on the Starlinger deCON technology, used to recycle post-consumer PET into food contact materials, EFSA J., 2023, 21(1), e07759 Search PubMed.
- EFSA Panel on Food Contact Materials, Enzymes and Processing Aids (CEP), C. Lambré, J. M. Barat Baviera, C. Bolognesi, A. Chesson and P. S. Cocconcelli,
et al., Safety assessment of the process CERSA, based on the Starlinger deCON technology, used to recycle post-consumer PET into food contact materials, EFSA J., 2023, 21(7), e08144 Search PubMed.
- EFSA Panel on Food Contact Materials, Enzymes and Processing Aids (CEP), C. Lambré, J. M. Barat Baviera, C. Bolognesi, A. Chesson and P. S. Cocconcelli,
et al., Safety assessment of the process Langgeng, based on the Starlinger deCON technology,
used to recycle post-consumer PET into food contact materials, EFSA J., 2023, 21(8), e08156 Search PubMed.
- EFSA Panel on Food Contact Materials, Enzymes and Processing Aids (CEP), V. Silano, J. M. Barat Baviera, C. Bolognesi, A. Chesson and P. S. Cocconcelli,
et al., Safety assessment of the process ‘POLY RECYCLING PET DIRECT IV+’, used to recycle post-consumer PET into food contact materials, EFSA J., 2019, 17(10), e05865 Search PubMed.
- EFSA Panel on Food Contact Materials, Enzymes and Processing Aids (CEP), C. Lambré, J. M. Barat Baviera, C. Bolognesi, A. Chesson and P. S. Cocconcelli,
et al., Safety assessment of the process DENTIS RECYCLING ITALY, based on PET direct iV+ technology, used to recycle post-consumer PET into food contact materials, EFSA J., 2021, 19(8), e06796 Search PubMed.
- EFSA Panel on Food Contact Materials, Enzymes and Processing Aids (CEP), C. Lambré, J. M. Barat Baviera, C. Bolognesi, A. Chesson and P. S. Cocconcelli,
et al., Safety assessment of the process DY Polymer, based on PET direct iV+ technology, used to recycle post-consumer PET into food contact materials, EFSA J., 2021, 19(8), e06797 Search PubMed.
- EFSA Panel on Food Contact Materials, Enzymes and Processing Aids (CEP), C. Lambré, J. M. Barat Baviera, C. Bolognesi, A. Chesson and P. S. Cocconcelli,
et al., Safety assessment of the process Omorika Recycling, based on PET direct iV+ technology, used to recycle post-consumer PET into food contact materials, EFSA J., 2021, 19(10), e06872 Search PubMed.
- EFSA Panel on Food Contact Materials, Enzymes and Processing Aids (CEP), C. Lambré, J. M. Barat Baviera, C. Bolognesi, A. Chesson and P. S. Cocconcelli,
et al., Safety assessment of the process Verdeco Recycling, based on PET direct iV+ technology, used to recycle post-consumer PET into food contact materials, EFSA J., 2022, 20(8), e07472 Search PubMed.
- EFSA Panel on Food Contact Materials, Enzymes and Processing Aids (CEP), C. Lambré, J. M. Barat Baviera, C. Bolognesi, A. Chesson and P. S. Cocconcelli,
et al., Safety assessment of the process EcoBlue, based on PET direct iV+ technology, used to recycle post-consumer PET into food contact materials, EFSA J., 2022, 20(12), e07654 Search PubMed.
- POLYMETRIX, PET SSP stand-alone process, available from: https://www.polymetrix.com/en/process-technology/solid-state-polycondensation-ssp/pet-ssp-stand-alone-process/.
- EFSA Panel on Food Contact Materials, Enzymes and Processing Aids (CEP), C. Lambré, J. M. Barat Baviera, C. Bolognesi, A. Chesson and P. S. Cocconcelli,
et al., Safety assessment of the process MOPET, based on the Polymetrix pellet technology, used to recycle post-consumer PET into food contact materials, EFSA J., 2022, 20(1), e07013 Search PubMed.
- EFSA Panel on Food Contact Materials, Enzymes and Processing Aids (CEP), C. Lambré, J. M. Barat Baviera, C. Bolognesi, A. Chesson and P. S. Cocconcelli,
et al., Safety assessment of the process NOVAPET, based on the Polymetrix pellet technology, used to recycle post-consumer PET into food contact materials, EFSA J., 2022, 20(1), e07011 Search PubMed.
- EFSA Panel on Food Contact Materials, Enzymes and Processing Aids (CEP), C. Lambré, J. M. Barat Baviera, C. Bolognesi, A. Chesson and P. S. Cocconcelli,
et al., Safety assessment of the process PT Veolia Indonesia, based on the Polymetrix technology, used to recycle post-consumer PET into food contact materials, EFSA J., 2023, 21(7), e08147 Search PubMed.
- EFSA Panel on Food Contact Materials, Enzymes and Processing Aids (CEP), C. Lambré, J. M. Barat Baviera, C. Bolognesi, A. Chesson and P. S. Cocconcelli,
et al., Safety assessment of the process Plastrec, based on the Polymetrix technology, used to recycle post-consumer PET into food contact materials, EFSA J., 2023, 21(8), e08149 Search PubMed.
- EFSA Panel on Food Contact Materials, Enzymes and Processing Aids (CEP), C. Lambré, J. M. Barat Baviera, C. Bolognesi, A. Chesson and P. S. Cocconcelli,
et al., Safety assessment of the process Société Générale de Recyclage (SGR), based on the VACUNITE (EREMA basic and Polymetrix SSP V-leaN) technology, used to recycle post-consumer PET into food contact materials, EFSA J., 2022, 20(5), e07270 Search PubMed.
- EFSA Panel on Food Contact Materials, Enzymes and Processing Aids (CEP), C. Lambré, J. M. Barat Baviera, C. Bolognesi, A. Chesson and P. S. Cocconcelli,
et al., Safety assessment of the process
RCS Plastics, based on the VACUNITE (EREMA basic and Polymetrix SSP V-leaN) technology, used to recycle post-consumer PET into food contact materials, EFSA J., 2022, 20(5), e07277 Search PubMed.
- EFSA Panel on Food Contact Materials, Enzymes and Processing Aids (CEP), C. Lambré, J. M. Barat Baviera, C. Bolognesi, A. Chesson and P. S. Cocconcelli,
et al., Safety assessment of the process Renovapet, based on the VACUNITE (EREMA basic and Polymetrix SSP V-leaN) technology, used to recycle post-consumer PET into food contact materials, EFSA J., 2023, 21(4), e07920 Search PubMed.
- EFSA Panel on Food Contact Materials, Enzymes and Processing Aids (CEP), C. Lambré, J. M. Barat Baviera, C. Bolognesi, A. Chesson and P. S. Cocconcelli,
et al., Safety assessment of the process World PET Plastic, based on the VACUNITE (EREMA basic and Polymetrix SSP V-leaN) technology, used to recycle post-consumer PET into food contact materials, EFSA J., 2022, 20(5), e07271 Search PubMed.
- EFSA Panel on Food Contact Materials, Enzymes, Processing Aids (CEP), C. Lambré, J. M. Barat Baviera, C. Bolognesi, A. Chesson and P. S. Cocconcelli,
et al., Safety assessment of the process Roxane Nord, based on VACUNITE (EREMA basic and Polymetrix SSP V-leaN) technology, used to recycle post-consumer PET into food contact materials, EFSA J., 2022, 20(5), e07276 Search PubMed.
- EFSA Panel on Food Contact Materials, Enzymes and Processing Aids (CEP), C. Lambré, J. M. Barat Baviera, C. Bolognesi, A. Chesson and P. S. Cocconcelli,
et al., Safety assessment of the process Rekis, based on the VACUNITE (EREMA basic and Polymetrix SSP V-leaN) technology, used to recycle post-consumer PET into food contact materials, EFSA J., 2023, 21(11), e08407 Search PubMed.
- EFSA Panel on Food Contact Materials, Enzymes and Processing Aids (CEP), C. Lambré, J. M. Barat Baviera, C. Bolognesi, A. Chesson and P. S. Cocconcelli,
et al., Safety assessment of the process ENVICCO, based on EREMA basic and Polymetrix SSP leaN technology, used to recycle post-consumer PET into food contact materials, EFSA J., 2023, 21(10), e08262 Search PubMed.
- EFSA Panel on Food Contact Materials, Enzymes and Processing Aids (CEP), C. Lambré, J. M. Barat Baviera, C. Bolognesi, A. Chesson and P. S. Cocconcelli,
et al., Safety assessment of the process PET Verpackungen Deutschland, based on the EREMA basic and Polymetrix SSP leaN technology, used to recycle post-consumer PET into food contact materials, EFSA J., 2022, 20(5), e07280 Search PubMed.
- EFSA Panel on Food Contact Materials, Enzymes and Processing Aids (CEP), C. Lambré, J. M. Barat Baviera, C. Bolognesi, A. Chesson and P. S. Cocconcelli,
et al., Safety assessment of the process Veolia Huafei Polymer Technology (Zhejiang), based on the Vacunite (EREMA Basic and Polymetrix SSP V-LeaN) technology, used to recycle post-consumer PET into food contact materials, EFSA J., 2023, 21(8), e08134 Search PubMed.
- EFSA Panel on Food Contact Materials, Enzymes and Processing Aids (CEP), C. Lambré, J. M. Barat Baviera, C. Bolognesi, A. Chesson and P. S. Cocconcelli,
et al., Safety assessment of the process Plastipak Iberia, based on the VACUNITE (EREMA basic and Polymetrix SSP V-leaN) technology, used to recycle post-consumer PET into food contact materials, EFSA J., 2023, 21(3), e07829 Search PubMed.
- New global innovation: VACUNITE® at PETnology, [Internet], Recovery Worldwide, available from: https://www.recovery-worldwide.com/en/artikel/new-global-innovation-vacunite-at-petnology-3323146.html.
- EFSA Panel on Food Contact Materials, Enzymes and Processing Aids (CEP), C. Lambré, J. M. Barat Baviera, C. Bolognesi, A. Chesson and P. S. Cocconcelli,
et al., Safety assessment of the process Loreco Plast Recyclage, based on the VACUNITE (EREMA basic and Polymetrix SSP V-leaN) technology, used to recycle post-consumer PET into food contact materials, EFSA J., 2023, 21(8), e08136 Search PubMed.
- EFSA Panel on Food Contact Materials, Enzymes and Processing Aids (CEP), C. Lambré, J. M. Barat Baviera, C. Bolognesi, A. Chesson and P. S. Cocconcelli,
et al., Safety assessment of the process Intco Malaysia, based on the VACUNITE (EREMA basic and Polymetrix SSP V-leaN) technology, used to recycle post-consumer PET into food contact materials, EFSA J., 2023, 21(11), e08404 Search PubMed.
- EFSA Panel on Food Contact Materials, Enzymes and Processing Aids (CEP Panel), C. Lambré, J. M. Barat Baviera, C. Bolognesi, A. Chesson and P. S. Cocconcelli,
et al., Safety assessment of the process CPE based on the VACUNITE (EREMA basic and Polymetrix SSP V-leaN) technology, used to recycle post-consumer PET into food contact materials, EFSA J., 2023, 21(8), e08135 Search PubMed.
- EFSA Panel on Food Contact Materials,
Enzymes and Processing Aids (CEP), C. Lambré, J. M. Barat Baviera, C. Bolognesi, A. Chesson and P. S. Cocconcelli,
et al., Safety assessment of the process Guangxi Wuzhou Guolong Recyclable, based on the Vacunite (EREMA basic and Polymetrix SSP V-LeaN) technology, used to recycle post-consumer PET into food contact materials, EFSA J., 2023, 21(11), e08405 Search PubMed.
- EFSA Panel on Food Contact Materials, Enzymes and Processing Aids (CEP), C. Lambré, J. M. Barat Baviera, C. Bolognesi, A. Chesson and P. S. Cocconcelli,
et al., Safety assessment of the process Steinbeis PolyVert, based on the Vacunite (EREMA Basic and Polymetrix SSP V-LeaN) technology, used to recycle post-consumer PET into food contact materials, EFSA J., 2023, 21(4), e07919 Search PubMed.
- BANDERA Extrusion Intelligence®, UP-CYCLING, [Internet], available from: https://www.luigibandera.com/products/recycling/.
- EFSA Panel on Food Contact Materials, Enzymes and Processing Aids (CEP), V. Silano, J. M. Barat Baviera, C. Bolognesi, A. Chesson and P. S. Cocconcelli,
et al., Safety assessment of the process AMB, based on Bandera technology, used to recycle post-consumer PET into food contact materials, EFSA J., 2019, 17(7), e05770 Search PubMed.
- EFSA Panel on Food Contact Materials, Enzymes and Processing Aids (CEP), C. Lambré, J. M. Barat Baviera, C. Bolognesi, A. Chesson and P. S. Cocconcelli,
et al., Safety assessment of the process Roboplast, based on the Bandera PURe 15 technology, used to recycle post-consumer PET into food contact materials, EFSA J., 2023, 21(4), e07929 Search PubMed.
- EFSA Panel on Food Contact Materials; Enzymes and Processing Aids (CEP), C. Lambré, J. M. Barat Baviera, C. Bolognesi, A. Chesson and P. S. Cocconcelli,
et al., Safety assessment of the process Arcoplastica, based on the Bandera PURe 15 technology, used to recycle post-consumer PET into food contact materials, EFSA J., 2023, 21(10), e08265 Search PubMed.
- EFSA Panel on Food Contact Materials, Enzymes and Processing Aids (CEP), C. Lambré, J. M. Barat Baviera, C. Bolognesi, A. Chesson and P. S. Cocconcelli,
et al., Safety assessment of the process Aristea, based on the Bandera PURe 15 technology, used to recycle post-consumer PET into food contact materials, EFSA J., 2023, 21(4), e07930 Search PubMed.
- EFSA Panel on Food Contact Materials, Enzymes and Processing Aids (CEP), C. Lambré, J. M. Barat Baviera, C. Bolognesi, A. Chesson and P. S. Cocconcelli,
et al., Safety assessment of the process SML Maschinengesellschaft, based on SML technology, used to recycle post-consumer PET into food contact materials, EFSA J., 2021, 19(8), e06795 Search PubMed.
- EFSA Panel on Food Contact Materials, Enzymes and Processing Aids (CEP), C. Lambré, J. M. Barat Baviera, C. Bolognesi, A. Chesson and P. S. Cocconcelli,
et al., Safety assessment of the process Indorama Ventures Recycling Verdun (IVRV), based on the NGR technology, used to recycle post-consumer PET into food contact materials, EFSA J., 2022, 20(5), e07275 Search PubMed.
- EFSA Panel on Food Contact Materials, Enzymes and Processing Aids (CEP), C. Lambré, J. M. Barat Baviera, C. Bolognesi, A. Chesson and P. S. Cocconcelli,
et al., Safety assessment of the process Wellman Neufchâteau Recyclage (WNR), based on the NGR technology, used to recycle post-consumer PET into food contact materials, EFSA J., 2022, 20(5), e07274 Search PubMed.
- EFSA Panel on Food Contact Materials, Enzymes and Processing Aids (CEP), C. Lambré, J. M. Barat Baviera, C. Bolognesi, A. Chesson and P. S. Cocconcelli,
et al., Safety assessment of the process rPET InWaste, based on the NGR technology, used to recycle post-consumer PET into food contact materials, EFSA J., 2022, 20(5), e07273 Search PubMed.
- EFSA Panel on Food Contact Materials, Enzymes and Processing Aids (CEP), C. Lambré, J. M. Barat Baviera, C. Bolognesi, A. Chesson and P. S. Cocconcelli,
et al., Safety assessment of the process 3R, based on NGR technology, used to recycle post-consumer PET into food contact materials, EFSA J., 2022, 20(5), e07272 Search PubMed.
- EFSA Panel on Food Contact Materials, Enzymes and Processing Aids (CEP), C. Lambré, J. M. Barat Baviera, C. Bolognesi, A. Chesson and P. S. Cocconcelli,
et al., Safety assessment of the process Coca-Cola HBC, based on the NGR technology, used to recycle post-consumer PET into food contact materials, EFSA J., 2023, 21(7), e08088 Search PubMed.
- EFSA Panel on Food Contact Materials, Enzymes and Processing Aids (CEP), C. Lambré, J. M. Barat Baviera, C. Bolognesi, A. Chesson and P. S. Cocconcelli,
et al., Safety assessment of the process Umincorp, based on the NGR technology, used to recycle post-consumer PET into food contact materials, EFSA J., 2023, 21(10), e08263 Search PubMed.
- EFSA Panel on Food Contact Materials, Enzymes and Processing Aids (CEP), C. Lambré, J. M. Barat Baviera, C. Bolognesi, A. Chesson and P. S. Cocconcelli,
et al., Safety assessment of the process CCH CIRCULARPET, based on the NGR technology, used to recycle post-consumer PET into food contact materials, EFSA J., 2023, 21(7), e08087 Search PubMed.
- EFSA Panel on Food Contact Materials, Enzymes and Processing Aids (CEP), C. Lambré, J. M. Barat Baviera, C. Bolognesi, A. Chesson and P. S. Cocconcelli,
et al., Safety assessment of the process AR Packaging Flexibles, based on the Kreyenborg IR Clean+ technology, used to recycle post-consumer PET into food contact materials, EFSA J., 2022, 20(8), e07474 Search PubMed.
- EFSA Panel on Food Contact Materials, Enzymes and Processing Aids (CEP), C. Lambré, J. M. Barat Baviera, C. Bolognesi, A. Chesson and P. S. Cocconcelli,
et al., Safety assessment of the process Paccor Polska, based on the Kreyenborg IR Clean+ technology, used to recycle post-consumer PET into food contact materials, EFSA J., 2022, 20(8), e07475 Search PubMed.
- EFSA Panel on Food Contact Materials, Enzymes and Processing Aids (CEP), C. Lambré, J. M. Barat Baviera, C. Bolognesi, A. Chesson and P. S. Cocconcelli,
et al., Safety assessment of the process Amhil Europa, based on the Kreyenborg IR Clean+ technology, used to recycle post-consumer PET into food contact materials, EFSA J., 2022, 20(8), e07473 Search PubMed.
- EFSA Panel on Food Contact Materials, Enzymes and Processing Aids (CEP), C. Lambré, J. M. Barat Baviera, C. Bolognesi, A. Chesson and P. S. Cocconcelli,
et al., Safety assessment of the process Petainer Lidköping, based on the Kreyenborg IR Clean+ technology, used to recycle post-consumer PET into food contact materials, EFSA J., 2022, 20(8), e07476 Search PubMed.
- EFSA Panel on Food Contact Materials, Enzymes and Processing Aids (CEP), C. Lambré, J. M. Barat Baviera, C. Bolognesi, A. Chesson and P. S. Cocconcelli,
et al., Safety assessment of the process Silver Plastics, based on the Reifenhäuser technology, used to recycle post-consumer PET into food contact materials, EFSA J., 2023, 21(8), e08165 Search PubMed.
- Krones, PET recycling systems: Efficient solutions for sustainable PET recycling [Internet], available from: https://www.krones.com/en/products/complete-solutions/pet-recycling-systems.php.
- Krones, Whitepaper: rPET – Sustainability through recycling [Internet], 2021 Jun 7, available from:https://www.krones.com/media/downloads/210607_Whitepaper_rPET_EN.pdf.
- AMUT Group, PET recycling solutions [Internet], available from: https://www.amutgroup.com/downloads/pages/PET_ita-eng.pdf.
- Regmac, Advanced recycling technologies [Internet], available from: http://www.regmac.net/.
- Sikoplast Recycling, Granulating systems for efficient plastic recycling [Internet], available from: https://sikoplast-recycling.com/fileadmin/user_upload/Sikoplast/Downloads/SIKOPLAST_Flyer_GRANULIERSYSTEME_ENG.pdf.
- Sikoplast Recycling, SIKOREX: Recycling systems for sustainable plastic processing [Internet], available from: https://sikoplast-recycling.com/fileadmin/user_upload/Sikoplast/Downloads/SIKOPLAST_Flyer_SIKOREX_EN.pdf.
- Sikoplast Recycling, Innovative solutions for plastic recycling [Internet], available from: https://sikoplast-recycling.com/fileadmin/user_upload/Sikoplast/Downloads/SIKOPLAST_Broschuere_EN.pdf.
- Neue Herbold, Recycling machinery and solutions for plastic processing [Internet], available from: https://neue-herbold.com/en/.
- DKSH, Environmental technology solutions for a sustainable future [Brochure].
- Spaleck, Screening machines for recycling and processing Our conveying and separation technology for recycling, https://www.spaleck.eu/screening-machines/.
- Spaleck, Spaleck Group: Innovative solutions for recycling and processing [Internet], available from: https://www.spaleck.eu/spaleck-group/.
- Westeria, Airstar: Air-based separation technology for recycling [Internet], available from: https://westeria.de/en/machine/airstar/.
- Bühler Group, SORTEX A GlowVision: Optical sorter for precision sorting [Internet], available from: https://www.buhlergroup.com/global/de/products/optical_sorter_sortexaglowvision.html.
- Bühler Group, SORTEX B: Optical sorter for efficient recycling [Internet], available from:https://www.buhlergroup.com/global/en/products/sortex_b_opticalsorter.html.
- Bühler Group, SORTEX N PolyVision: Optical sorter for plastic recycling [Internet], available from: https://www.buhlergroup.com/global/en/products/optical_sorter_sortexnpolyvision.html.
- TOMRA, Catalogue 2022: Recycling solutions for a sustainable future [Internet], 2022, available from: https://4847902.fs1.hubspotusercontent-na1.net/hubfs/4847902/Catalog2022/TOMRA_Catalouge_2022_EN.pdf.
- Mogensen – JÖST Group, MSORT: Optical sorting systems for efficient recycling [Internet], available from: https://www.mogensen-joestgroup.com/en/msort/.
- Mogensen – JÖST Group, GSORT: High-performance gravity sorting systems [Internet], available from: https://www.mogensen-joestgroup.com/en/gsort/.
- Wagner Magnete, Magnetic separation and recycling solutions [Internet], available from: https://www.wagner-magnete.com/en/.
- BoReTech, PET recycling systems and solutions [Internet], available from: https://www.bo-re-tech.com/en/index.html.
- SIPA Solutions, XTREME Renew: Innovative preform system for PET recycling [Internet], available from: https://www.sipasolutions.com/en/catalog/preform-systems/xtreme-renew.
- SIPA Solutions, XTREME: Revolutionary preform production technology [Internet], 2022, available from: https://www.sipasolutions.com/uploads/product_attachment/8-SIPA_Brochure_XTREME_UK_2022.pdf.
- SOREMA, Plastic recycling systems: Catalogue [Internet], available from: https://www.ipmtc.com.pl/pliki/sorema/sorema_catalogue.pdf.
- SACMI, IPS 300: Preform injection system for PET [Internet], available from: https://sacmi.com/en-US/closures-preforms-containers/PET-preforms/Preform-injection-system/IPS-300.
- SACMI, New IPS 400: Sacmi holds preview for specialised press and Italian partners [Internet], available from: https://sacmi.com/en-US/packaging/news/5631/New-IPS-400-Sacmi-holds-preview-for-specialised-press-and-Italian-partners.
- SACMI, IPS Gamma: Innovative solutions for PET preform production [Internet], 2022, available from: https://sacmi.com/sharedcontent/media/Documents/Closures_Preforms_Containers/2022/IPS_GAMMA_EN-ES_20211227.pdf.
- EREMA, INTAREMA® FibrePro IV: Innovative recycling solutions for PET fibres [Internet], available from: https://www.erema.com/en/intarema_fibrepro_iv/.
- NGR – Next Generation Recyclingmaschinen GmbH, PET processing using the LSP method (liquid state polycondensation) [Internet], 2013 Oct 10, available from: https://www.pressebox.com/inactive/ngr-next-generation-recyclingmaschinen-gmbh/PET-Processing-Using-the-LSP-Method-Liquid-State-Polycondensation/boxid/631740.
- E. Barthélémy, D. Spyropoulos, M.-R. Milana, K. Pfaff, N. Gontard and E. Lampi,
et al., Safety evaluation of mechanical recycling processes used to produce polyethylene terephthalate (PET) intended for food contact applications, Food Addit. Contam.,:Part A, 2014, 31(3), 490–497 CrossRef PubMed.
- E. D. Tsochatzis, J. A. Lopes and M. Corredig, Chemical testing of mechanically recycled polyethylene terephthalate for food packaging in the European Union, Resour., Conserv. Recycl., 2022, 179, 106096 CrossRef CAS.
- D. Salazar-Beltrán, L. Hinojosa-Reyes, C. Palomino-Cabello, G. Turnes-Palomino, A. Hernández-Ramírez and J. L. Guzmán-Mar, Determination of phthalate acid esters plasticizers in polyethylene terephthalate bottles and its correlation with some physicochemical properties, Polym. Test., 2018, 68, 87–94 CrossRef.
- A. Kassouf, J. Maalouly, H. Chebib, D. N. Rutledge and V. Ducruet, Chemometric tools to highlight non-intentionally added substances (NIAS) in polyethylene terephthalate (PET), Talanta, 2013, 115, 928–937 CAS.
- B. Magnuson, I. Munro, P. Abbot, N. Baldwin, R. Lopez-Garcia and K. Ly,
et al., Review of the regulation and safety assessment of food substances in various countries and jurisdictions, Food Addit. Contam.,:Part A, 2013, 30(7), 1147–1220 CAS.
-
K. G. Gopalakrishna and N. Reddy. Regulations on recycling PET bottles, in Recycling of Polyethylene Terephthalate Bottles, Elsevier, 2019, pp. 23–35 Search PubMed.
- Food Standards Australia New Zealand (FSANZ), International regulations for food contact materials [Internet], 2016, available from: https://www.foodstandards.gov.au/sites/default/files/food-standards-code/proposals/Documents/P1034-Packaging-CFS-SD2.pdf.
- Food Standards Australia New Zealand (FSANZ), Food Standards Code: Legislation, available from: https://www.foodstandards.gov.au/food-standards-code/legislation.
- Agência Nacional de Vigilância Sanitária (ANVISA), Resolução da Diretoria Colegiada (RDC) n° 326, de 3 de dezembro de 2019, 2019, available from: https://www.in.gov.br/web/dou/-/resolucao-da-diretoria-colegiada-rdc-n-326-de-3-de-dezembro-de-2019-231272617.
- Agência Nacional de Vigilância Sanitária (ANVISA), Resolução da Diretoria Colegiada (RDC) n° 91, de 11 de maio de 2001, 2001, available from: https://antigo.anvisa.gov.br/documents/10181/2718376/%284%29RDC_91_2001_COMP.pdf.
- Agência Nacional de Vigilância Sanitária (ANVISA), Resolução n° 105, de 19 de maio de 1999 [Internet], 1999, available from: https://bvsms.saude.gov.br/bvs/saudelegis/anvisa/1999/res0105_19_05_1999.html.
- Agência Nacional de Vigilância Sanitária (ANVISA), Resolução da Diretoria Colegiada (RDC) n° 51, de 26 de novembro de 2010 [Internet], 2010, available from: https://antigo.anvisa.gov.br/documents/10181/2718376/RDC_51_2010_COMP.pdf/1e3cd7f0-d50c-4693-9db4-0082132dfb6e.
- Agência Nacional de Vigilância Sanitária (ANVISA), Resolução da Diretoria Colegiada (RDC) n° 20, de 26 de março de 2008 [Internet], 2008, available from: https://bvsms.saude.gov.br/bvs/saudelegis/anvisa/2008/rdc0020_26_03_2008.html.
- Agência Nacional de Vigilância Sanitária (ANVISA), Resolução n° 105, de 19 de maio de 1999 [Internet], 1999, available from: https://bvsms.saude.gov.br/bvs/saudelegis/anvisa/1999/res0105_19_05_1999.html.
- Health Canada, Information requirements for food packaging submissions [Internet], available from: https://www.canada.ca/en/health-canada/services/food-nutrition/legislation-guidelines/guidance-documents/information-requirements-food-packaging-submissions.html.
- Ministry of Ecology and Environment of the People's Republic of China, Control standards for import of waste used as raw materials [Internet], available from: https://www.env.go.jp/en/recycle/asian_net/Country_Information/Law_N_Regulation/China/Control_Standards_for_Import_of_Waste_Used_as_Raw_Materials.pdf.
- Standardization Administration of China, GB 31604: National food safety standard for food contact materials and articles [Internet], available from: https://gbstandards.org/index/Standards_Search.asp?word=GB31604.
- CIRS Group, China GB 9685: Hygienic standard for use of additives in food containers and packaging materials [Internet], available from: https://www.cirs-reach.com/China_Chemical_Regulation/China_GB_9685_Hygienic_Standard_for_Use_of_Additives_in_Food_Containers_and_Packaging_Materials.html.
-
European Union, Directive 94/62/EC of the European Parliament and of the Council of 20 December 1994 on packaging and packaging waste, 1994, available from: https://eur-lex.europa.eu/legal-content/EN/TXT/PDF/?uri=CELEX:31994L0062.
-
European Union, Commission Regulation (EU) No 10/2011 of 14 January 2011 on plastic materials and articles intended to come into contact with food [Internet], 2011, available from: https://eur-lex.europa.eu/legal-content/EN/TXT/PDF/?uri=CELEX:32011R0010.
-
European Union, Commission Regulation (EU) 2022/1616 of 15 September 2022 on recycled plastic materials and articles intended to come into contact with foods and repealing Regulation (EC) No 282/2008 [Internet], 2022, available from: https://eur-lex.europa.eu/legal-content/EN/TXT/PDF/?uri=CELEX:32022R1616.
-
European Union, Regulation (EC) No 1935/2004 of the European Parliament and of the Council of 27 October 2004 on materials and articles intended to come into contact with food and repealing Directives 80/590/EEC and 89/109/EEC [Internet], Consolidated version, 2021 Mar 27, available from: https://eur-lex.europa.eu/legal-content/EN/TXT/?uri=CELEX%3A02004R1935-20210327.
-
European Union, Commission Regulation (EC) No. 2023/2006 of 22 December 2006 on good manufacturing practice for materials and articles intended to come into contact with food (GMP Regulation) [Internet], Consolidated version, 2008 Apr 17, available from: https://eur-lex.europa.eu/legal-content/EN/TXT/PDF/?uri=CELEX:02006R2023-20080417.
-
European Union, Regulation (EC) No 1907/2006 of the European Parliament and of the Council concerning the Registration, Evaluation, Authorisation and Restriction of Chemicals (REACH), Official Journal of the European Union, available from: https://eur-lex.europa.eu/LexUriServ/LexUriServ.do?uri=OJ:L:2007:136:0003:0280:en:PDF Search PubMed.
-
European Commission, EU-RU SPS requirements decision 769/16: Implementation of the Agreement on the Application of Sanitary and Phytosanitary Measures [Internet], available from: https://food.ec.europa.eu/document/download/8a0639e9-5d76-46c6-a3eb-6a8f406081e8_en?filename=ia_eu-ru_sps-req_decision-769_16082011_en.pdf.
- Government of Japan, Food Sanitation Act [Internet], available from: https://www.japaneselawtranslation.go.jp/en/laws/view/3687/en.
- Japan PET Bottle Recycling Promotion Association, Design guidelines for PET bottles [Internet], available from: https://www.petbottle-rec.gr.jp/english/design.html.
- SGS, Food contact material regulations in the MERCOSUR region [Internet], available from: https://www.sgs.com/en/services/food-contact-material-regulations-mercosur-region.
- Sun Chemical, Food packaging MERCOSUR legislation: Version 1.1 [Internet], 2022, available from: https://www.sunchemical.com/wp-content/uploads/2022/04/Food-Packaging-Mercosur-Legislation-Version-1.1.pdf.
- SGS, Safeguards 155/21: MERCOSUR revises food contact resolutions [Internet], 2021 Nov, available from: https://www.sgs.com/en/news/2021/11/safeguards-15521-mercosur-revises-food-contact-resolutions.
- UK Government, The Materials and Articles in Contact with Food (England) Regulations 2015 [Internet], 2015, available from: https://www.legislation.gov.uk/uksi/2015/1640/contents.
- UK Government, The Plastic Materials and Articles in Contact with Food (England) Regulations 2011 [Internet], 2011, available from: https://www.legislation.gov.uk/uksi/2011/988/contents.
- UK Government, The Materials and Articles in Contact with Food (Amendment) (England) Regulations 2024 [Internet], 2024, available from: https://www.legislation.gov.uk/ukdsi/2024/9780348264654.
- UK Government, The Materials and Articles in Contact with Food (Wales) Regulations 2012 [Internet], 2012, available from: https://www.legislation.gov.uk/uksi/2012/2619/contents.
- U.S. Food and Drug Administration (FDA), Code of Federal Regulations: Title 21, Part 170 – Food additives [Internet], available from: https://www.accessdata.fda.gov/scripts/cdrh/cfdocs/cfcfr/CFRSearch.cfm?CFRPart=170.
- U.S. Food and Drug Administration (FDA), Code of Federal Regulations: Title 21, Part 174 – Indirect food additives: General [Internet], available from: https://www.accessdata.fda.gov/scripts/cdrh/cfdocs/cfcfr/CFRSearch.cfm?CFRPart=174.
- U.S. Food and Drug Administration (FDA), Packaging & food contact substances: Industry guidance [Internet], 2021, available from: https://www.fda.gov/media/150792/download.
-
F. Welle, Evaluation of non-intentionally added substances (NIAS) in PET bottles, 2016, available from DOI:10.13140/RG.2.2.31479.83362.
- D. Ginter-Kramarczyk, J. Zembrzuska, I. Kruszelnicka, A. Zając-Woźnialis and M. Ciślak, Influence of temperature on the quantity of bisphenol A in bottled drinking water, Int. J. Environ. Res. Public Health, 2022, 19(9), 5710 CAS.
- E. U. Thoden van Velzen, M. T. Brouwer, C. Stärker and F. Welle, Effect of recycled content and rPET quality on the properties of PET bottles, part II: Migration, Packag. Technol. Sci., 2020, 33(9), 359–371 CAS.
- European Chemicals Agency (ECHA), Substance information: Benzene [Internet], available from: https://echa.europa.eu/nl/substance-information/-/substanceinfo/100.000.685.
- European Chemicals Agency (ECHA), Substance information: 4,4'-isopropylidenediphenol [Internet], available from: https://echa.europa.eu/nl/substance-information/-/substanceinfo/100.001.133.
- European Chemicals Agency (ECHA), Substance information: Styrene [Internet], available from: https://echa.europa.eu/nl/substance-information/-/substanceinfo/100.002.592.
- E. U. Thoden van Velzen, M. T. Brouwer, C. Stärker and F. Welle, Effect of recycled content and rPET quality on the properties of PET bottles, part II: Migration, Packag. Technol. Sci., 2020, 33(9), 359–371 CAS.
-
S. Venkatachalam, G. Sangu, V. Jayprakash, R. Prashant, K. Rao and K. Anil, Degradation and recyclability of poly (ethylene terephthalate), in Polyester, InTech, 2012 Search PubMed.
- P. Benyathiar, P. Kumar, G. Carpenter, J. Brace and D. K. Mishra, Polyethylene terephthalate (PET) bottle-to-bottle recycling for the beverage industry: A review, Polymers, 2022, 14(12), 2366 CAS.
- N. Davis, J. E. Danes and K. Vorst, Sensor array for the detection of organic and inorganic contaminants in post-consumer recycled plastics for food contact, Food Addit. Contam.,:Part A, 2017, 34(10), 1681–1689 CAS.
- M. K. Eriksen, K. Pivnenko, M. E. Olsson and T. F. Astrup, Contamination in plastic recycling: Influence of metals on the quality of reprocessed plastic, Waste Manage., 2018, 79, 595–606 CrossRef CAS PubMed.
- J. N. Hahladakis, C. A. Velis, R. Weber, E. Iacovidou and P. Purnell, An overview of chemical additives present in plastics: Migration, release, fate and environmental impact during their use, disposal and recycling, J. Hazard. Mater., 2018, 344, 179–199 CAS.
- S. Gerassimidou, P. Lanska, J. N. Hahladakis, E. Lovat, S. Vanzetto and B. Geueke,
et al., Unpacking the complexity of the PET drink bottles value chain: A chemicals perspective, J. Hazard. Mater., 2022, 430, 128410 CAS.
- F. Cincotta, A. Verzera, G. Tripodi and C. Condurso, Non-intentionally added substances in PET bottled mineral water during the shelf-life, Eur. Food Res. Technol., 2018, 244(3), 433–439 CrossRef CAS.
- R. Franz and F. Welle, Contamination levels in recollected PET bottles from non-food applications and their impact on the safety of recycled PET for food contact, Molecules, 2020, 25(21), 4998 CrossRef CAS PubMed.
- B. A. Mrozinski, Y.-W. Kim, E. A. Lofgren and S. A. Jabarin, Chemistry of the interactions of acetaldehyde scavengers for poly(ethylene terephthalate), J. Appl. Polym. Sci., 2013, 130(6), 4191–4200 CrossRef CAS.
-
E. Velásquez, M. Guerrero Correa, L. Garrido, A. Guarda, M. J. Galotto and C. López de Dicastillo. Food packaging plastics: Identification and recycling, in Composites Science and Technology, Springer, Singapore, Singapore, 2021, pp. 311–343 Search PubMed.
- M. Roosen, L. Harinck, S. Ügdüler, T. De Somer, A.-G. Hucks and T. G. A. Belé,
et al., Deodorization of post-consumer plastic waste fractions: A comparison of different washing media, Sci. Total Environ., 2022, 812, 152467 CrossRef CAS PubMed.
- O. Kökkılıç, S. Mohammadi-Jam, P. Chu, C. Marion, Y. Yang and K. E. Waters, Separation of plastic wastes using froth flotation – An overview, Adv. Colloid Interface Sci., 2022, 308, 102769 CrossRef PubMed.
-
R. Franz and F. Welle, Investigation of non-intentionally added substances (NIAS) in PET bottles and closures, International Symposium on Food Packaging, Prague Czech Republic, 2008, Nov 19–21, [Poster] Search PubMed.
-
S. F. Aminuddin, L. Y. Wei, H. Hamada and N. Adnan, Recycled poly(ethylene terephthalate)/recycled polypropylene blend: Effect of hygrothermal treatment, in 2012 IEEE Symposium on Humanities, Science and Engineering Research, IEEE, 2012 Search PubMed.
- C. Sammon and J. Yarwood, Everall N. An FT–IR study of the effect of hydrolytic degradation on the structure of thin PET films, Polym. Degrad. Stab., 2000, 67(1), 149–158 CrossRef CAS.
- M. Čolnik, D. Pečar, Ž. Knez, A. Goršek and M. Škerget, Kinetics study of hydrothermal degradation of PET waste into useful products, Processes, 2021, 10(1), 24 CrossRef.
- V. S. Mahesh, K. Tharpa, N. S. Gadigone, B. F. Al-Farhood, F. H. Al-Mutairi and A. Kumar, Mechanism of acetaldehyde formation in polyethylene terephthalate resin—A new insight, Polym. Eng. Sci., 2021, 61(2), 362–366 CrossRef CAS.
- Y. Celik, M. Shamsuyeva and H. J. Endres, Thermal and mechanical properties of the recycled and virgin PET-part I, Polymers, 2022, 14(7), 1326 CrossRef CAS PubMed.
- F. Villain, J. Coudane and M. Vert, Thermal degradation of polyethylene terephthalate: study of polymer stabilization, Polym. Degrad. Stab., 1995, 49(3), 393–397 CrossRef CAS.
-
G. P. Karayannidis, I. D. Sideridou and D. X. Zamboulis, Antioxidants for poly(ethylene terephthalate), in Plastics Additives, Springer, Dordrecht, Netherlands, 1998, pp. 95–107 Search PubMed.
- J. Standish, Willing & Label: The impact of labels and adhesives on PET container recycling is significant, Plast. Eng., 2015, 71(1), 22–26 CrossRef.
- F. D. Alsewailem and J. K. Alrefaie, Effect of contaminants and processing regime on the mechanical properties and moldability of postconsumer polyethylene terephthalate bottles, Waste Manage., 2018, 81, 88–93 CrossRef CAS PubMed.
- B. Küppers, X. Chen, I. Seidler, K. Friedrich, K. Raulf and T. Pretz,
et al., Influences and consequences of mechanical delabelling on pet recycling, Detritus, 2019, 1 Search PubMed.
-
M. Puentes Gruezo, Design Factors Affecting Post-consumer Plastic Packaging Recyclability: A Review, 2019 Search PubMed.
- H. Onusseit, The influence of adhesives on recycling, Resour., Conserv. Recycl., 2006, 46(2), 168–181 CrossRef.
-
S. Heitzman, Colorants, Encyclopedia of Polymer Science and Technology, Wiley, 2003, p. pst067 Search PubMed.
- D. Arends, M. Schlummer and A. Mäurer, Removal of inorganic colour pigments from acrylonitrile butadiene styrene by dissolution-based recycling, J. Mater. Cycles Waste Manage., 2012, 14(2), 85–93 CrossRef CAS.
-
A. Kumar, U. Dixit, K. Singh, S. Prakash Gupta and M. Jamal Beg, Structure and properties of dyes and pigments, in Dyes and Pigments – Novel Applications and Waste Treatment, IntechOpen, 2021 Search PubMed.
- D. Loaeza, J. Cailloux, O. Santana Pérez, M. Sánchez-Soto and M. Maspoch, Impact of titanium dioxide in the mechanical recycling of post-consumer polyethylene terephthalate bottle waste: Tensile and fracture behavior, Polymers, 2021, 13(2), 310 CrossRef CAS PubMed.
- S. H. Alrefaee, S. A. Al-Ghamdi, K. S. Alrashdi, A. Almahri, O. Alaysuy and N. M. Alatawi,
et al., Effect of titanium oxide (TiO2) nanoparticles on the opto-mechanical properties of polyethylene terephthalate (PET) fibers, Opt. Mater., 2024, 157, 116242 Search PubMed.
- Y. Ding, M. Szymczyk, N. Mehraban, J. Lim, L. Parrillo-Chapman and A. El-Shafei,
et al., Molecular and excited state properties of photostable anthraquinone red and violet dyes for hydrophobic fibers, J. Mol. Struct., 2022, 1248, 131349 CrossRef CAS.
- S. Key, P. G. Ryan, S. E. Gabbott, J. Allen and A. P. Abbott, Influence of colourants on environmental degradation of plastic litter, Environ. Pollut., 2024, 347, 123701 CrossRef CAS PubMed.
- European Chemicals Agency (ECHA), Substance information: Formaldehyde, available from: https://echa.europa.eu/nl/substance-information/-/substanceinfo/100.000.002.
- R. Penthala, R. S. Kumar, G. Heo, H. Kim, I. Y. Lee and E. H. Ko,
et al., Synthesis and efficient dyeing of anthraquinone derivatives on polyester fabric with supercritical carbon dioxide, Dyes Pigm., 2019, 166, 330–339 CrossRef CAS.
- M. Jayaweera, H. Perera, N. Bandara, G. Danushika, B. Gunawardana and C. Somaratne,
et al., Migration of phthalates from PET water bottle in events of repeated uses and associated risk assessment, Environ. Sci. Pollut. Res. Int., 2020, 27(31), 39149–39163 CrossRef CAS PubMed.
- California Department of Toxic Substances Control (DTSC), Revised food packaging containing ortho-phthalates: Decision document, 2021 May, available from: https://dtsc.ca.gov/wp-content/uploads/sites/31/2021/10/Revised-Food-Packaging-Containing-Ortho-phthalates-Decision-Document-May-2021.pdf.
- S. Keresztes, E. Tatár, Z. Czégény, G. Záray and V. G. Mihucz, Study on the leaching of phthalates from polyethylene terephthalate bottles into mineral water, Sci. Total Environ., 2013, 458–460, 451–458 CrossRef CAS PubMed.
- K. Habschied, B. Kartalović, D. Lazić, V. Krstanović and K. Mastanjević, Survey on phthalates in beer packaged in aluminum cans, PET and glass bottles, Fermentation, 2023, 9(2), 125 CrossRef CAS.
- W. Dekant, Grouping of phthalates for risk characterization of human exposures, Toxicol. Lett., 2020, 330, 1–6 CrossRef CAS PubMed.
- D. Salazar-Beltrán, L. Hinojosa-Reyes, E. Ruiz-Ruiz, A. Hernández-Ramírez and J. L. Guzmán-Mar, Phthalates in beverages and plastic bottles: Sample preparation and determination, Food Anal. Methods, 2018, 11(1), 48–61 CrossRef.
- K. Pivnenko, M. K. Eriksen, J. A. Martín-Fernández, E. Eriksson and T. F. Astrup, Recycling of plastic waste: Presence of phthalates in plastics from households and industry, Waste Manage., 2016, 54, 44–52 CrossRef CAS PubMed.
- B. Goodlaxson, G. Curtzwiler and K. Vorst, Evaluation of methods for determining heavy metal content in polyethylene terephthalate food packaging, J. Plast. Film Sheeting, 2018, 34(2), 119–139 CrossRef CAS.
- M. Whitt, K. Vorst, W. Brown, S. Baker and L. Gorman, Survey of heavy metal contamination in recycled polyethylene terephthalate used for food packaging, J. Plast. Film Sheeting, 2013, 29(2), 163–173 CrossRef.
- M. Haldimann, A. Alt, A. Blanc, K. Brunner, F. Sager and V. Dudler, Migration of antimony from PET trays into food simulant and food: determination of Arrhenius parameters and comparison of predicted and measured migration data, Food Addit. Contam.,:Part A, 2013, 30(3), 587–598 CrossRef CAS PubMed.
- C. A. Chapa-Martínez, L. Hinojosa-Reyes, A. Hernández-Ramírez, E. Ruiz-Ruiz, L. Maya-Treviño and J. L. Guzmán-Mar, An evaluation of the migration of antimony from polyethylene terephthalate (PET) plastic used for bottled drinking water, Sci. Total Environ., 2016, 565, 511–518 CrossRef PubMed.
- R. Nisticò, Polyethylene terephthalate (PET) in the packaging industry, Polym. Test., 2020, 90, 106707 CrossRef.
- M. Filella, Antimony and PET bottles: Checking facts, Chemosphere, 2020, 261, 127732 CrossRef CAS PubMed.
- European Chemicals Agency (ECHA), Substance information: Diantimony Trioxide [Internet], available from: https://echa.europa.eu/nl/substance-information/-/substanceinfo/100.013.796.
-
M. Mahurpawar, Effects of heavy metals on human health, 2015, available from: https://mbbcollege.in/db/notes/408.pdf.
- E. M. Jung, D. J. Kim and K. T. Lee, Identification of the volatile compounds in polyethylene terephthalate bottles and determination of their migration content into mineral water, Korean J. Food Sci. Technol., 2014, 46(1), 19–24 CrossRef.
- C. Dutra, D. Pezo, M. T. de A. Freire, C. Nerín and F. G. R. Reyes, Determination of volatile organic compounds in recycled polyethylene terephthalate and high-density polyethylene by headspace solid phase microextraction gas chromatography mass spectrometry to evaluate the efficiency of recycling processes, J. Chromatogr. A, 2011, 1218(10), 1319–1330 CrossRef CAS PubMed.
- B. Nijssen, T. Kamperman and J. Jetten, Acetaldehyde in mineral water stored in polyethylene terephthalate (PET) bottles: odour threshold and quantification, Packag. Technol. Sci., 1996, 9(4), 175–185 CrossRef CAS.
- J. Ewender, R. Franz, A. Mauer and F. Welle, Determination of the migration of acetaldehyde from PET bottles into non-carbonated and carbonated mineral water, Z. Lebensm.-Unters. Forsch., 2003, 99(6), 215–221 CAS.
- D. W. Lachenmeier, F. Kanteres and J. Rehm, Carcinogenicity of acetaldehyde in alcoholic beverages: risk assessment outside ethanol metabolism, Addiction, 2009, 104(4), 533–550 CrossRef PubMed.
- R. Guo and J. Ren, Alcohol and acetaldehyde in public health: from marvel to menace, Int. J. Environ. Res. Public Health, 2010, 7(4), 1285–1301 CrossRef CAS PubMed.
- A. Choodum, P. Thavarungkul and P. Kanatharana, Acetaldehyde residue in polyethylene terephthalate (PET) bottles, J. Environ. Sci. Health, Part B, 2007, 42(5), 577–583 CrossRef CAS PubMed.
- G. Mohammad, T. J. Denis, B. Mohamed and G. E. Khadir, Formaldehyde contamination in PET-bottled mineral water: impact of CO2, temperature, and storage time with analytical method validation, Euro-Mediterr. J. Environ. Integr., 2024, 9(3), 1659–1671 Search PubMed.
- K.-H. Kim, S. A. Jahan and J.-T. Lee, Exposure to formaldehyde and its potential human health hazards, J. Environ. Sci. Health, Part C:Environ. Carcinog. Ecotoxicol. Rev., 2011, 29(4), 277–299 CrossRef CAS PubMed.
-
European Union, Regulation (EC) No 1272/2008 of the European Parliament and of the Council of 16 December 2008 on classification, labelling and packaging of substances and mixtures (CLP Regulation) [Internet], 2008, available from: https://eur-lex.europa.eu/legal-content/EN/TXT/?uri=celex%3A32008R1272.
- M. Mutsuga, Y. Kawamura, Y. Sugita-Konishi, Y. Hara-Kudo, K. Takatori and K. Tanamoto, Migration of formaldehyde and acetaldehyde into mineral water in polyethylene terephthalate (PET) bottles, Food Addit. Contam., 2006, 23(2), 212–218 CrossRef CAS PubMed.
- S. Ubeda, M. Aznar and C. Nerín, Determination of oligomers in virgin and recycled polyethylene terephthalate (PET) samples by UPLC-MS-QTOF, Anal. Bioanal. Chem., 2018, 410(9), 2377–2384 CrossRef CAS PubMed.
- E. D. Tsochatzis, J. Alberto Lopes, O. Kappenstein, T. Tietz and E. J. Hoekstra, Quantification of PET cyclic and linear oligomers in teabags by a validated LC-MS method – In silico toxicity assessment and consumer's exposure, Food Chem., 2020, 317, 126427 CrossRef CAS PubMed.
- M. Hoppe, R. Fornari, P. de Voogt and R. Franz, Migration of oligomers from PET: determination of diffusion coefficients and comparison of experimental versus modelled migration, Food Addit. Contam.,:Part A, 2017, 34(7), 1251–1260 CrossRef CAS PubMed.
- M. Gall, A. Schweighuber, W. Buchberger and R. Lang, Plastic bottle cap recycling—characterization of recyclate composition and opportunities for design for circularity, Sustainability, 2020, 12(24), 10378 CrossRef.
- K. Ragaert, S. Huysveld, G. Vyncke, S. Hubo, L. Veelaert and J. Dewulf,
et al., Design from recycling: A complex mixed plastic waste case study, Resour., Conserv. Recycl., 2020, 155, 104646 CrossRef.
- S. M. Nissy, V. R. Myneni and M. Vangalapati, Wrenching of Bisphenol A from plastics: Response surface methodology, Mater. Today, 2022, 62, 3869–3877 CAS.
- R. da Silva Costa, T. Sainara Maia Fernandes, E. de Sousa Almeida, J. Tomé Oliveira, J. A. Carvalho Guedes and Z. G. Julião,
et al., Potential risk of BPA and phthalates in commercial water bottles: a minireview, J. Water Health, 2021, 19(3), 411–435 CrossRef PubMed.
- C. Kubwabo, I. Kosarac, B. Stewart, B. R. Gauthier, K. Lalonde and P. J. Lalonde, Migration of bisphenol A from plastic baby bottles, baby bottle liners and reusable polycarbonate drinking bottles, Food Addit. Contam.,:Part A, 2009, 26(6), 928–937 CrossRef CAS PubMed.
- N. Dreolin, M. Aznar, S. Moret and C. Nerin, Development and validation of a LC–MS/MS method for the analysis of bisphenol a in polyethylene terephthalate, Food Chem., 2019, 274, 246–253 CrossRef CAS PubMed.
- A. Guart, F. Bono-Blay, A. Borrell and S. Lacorte, Migration of plasticizersphthalates, bisphenol A and alkylphenols from plastic containers and evaluation of risk, Food Addit. Contam.,:Part A, 2011, 28(5), 676–685 CrossRef CAS PubMed.
- X. Li, G.-G. Ying, H.-C. Su, X.-B. Yang and L. Wang, Simultaneous determination and assessment of 4-nonylphenol, bisphenol A and triclosan in tap water, bottled water and baby bottles, Environ. Int., 2010, 36(6), 557–562 CrossRef CAS PubMed.
- V. Gómez-Serrano, M. Adame-Pereira, M. Alexandre-Franco and C. Fernández-González, Adsorption of bisphenol A by activated carbon developed from PET waste by KOH activation, Environ. Sci. Pollut. Res. Int., 2021, 28(19), 24342–24354 CrossRef PubMed.
- I. Rebai, J. O. Fernandes, M. Azzouz, K. Benmohammed, G. Bader and K. Benmbarek,
et al., Urinary bisphenol levels in plastic industry workers, Environ. Res., 2021, 202, 111666 CrossRef CAS PubMed.
- United Nations Economic Commission for Europe (UNECE), Globally Harmonized System of Classification and Labelling of Chemicals (GHS): Annex 2 – Classification and labelling summary tables [Internet], 2011, available from: https://unece.org/DAM/trans/danger/publi/ghs/ghs_rev04/English/06e_annex2.pdf.
-
European Commission, Food safety: Restrictions on bisphenol A (BPA) and other bisphenols in food contact materials [Internet], available from: https://ec.europa.eu/info/law/better-regulation/have-your-say/initiatives/13832-Food-safety-restrictions-on-bisphenol-A-BPA-and-other-bisphenols-in-food-contact-materials_en.
- EFSA Panel on food contact materials, enzymes, flavourings and processing aids (CEF), Scientific Opinion on the criteria to be used for safety evaluation of a mechanical recycling process to produce recycled PET intended to be used for manufacture of materials and articles in contact with food, EFSA J., 2011, 9(7), 2184 Search PubMed.
- G. Latini, Monitoring phthalate exposure in humans, Clin. Chim. Acta, 2005, 361(1–2), 20–29 CrossRef CAS PubMed.
- Netherlands Institute for Sustainable Packaging (KIDV), Heavy metals in packaging: Factsheet, available from: https://kidv.nl/media/factsheets/voedselveiligheid/20220309_05_zware_metalen_factsheet_eng_def.pdf?1.2.23.
- P. H. M. Kiyataka, S. T. Dantas, A. C. Albino and J. A. L. Pallone, Antimony assessment in PET bottles for soft drink, Food Anal. Methods, 2018, 11(1), 1–9 CrossRef.
- W. Shotyk, M. Krachler and B. Chen, Contamination of Canadian and European bottled waters with antimony from PET containers, J. Environ. Monit., 2006, 8(2), 288–292 RSC.
- J. Alberto Lopes, E. D. Tsochatzis, L. Karasek, E. J. Hoekstra and H. Emons, Analysis of PBT and PET cyclic oligomers in extracts of coffee capsules and food simulants by a HPLC-UV/FLD method, Food Chem., 2021, 345, 128739 CrossRef CAS PubMed.
- R. Franz, A. Mauer and F. Welle, European survey on post-consumer poly(ethylene terephthalate) (PET) materials to
determine contamination levels and maximum consumer exposure from food packages made from recycled PET, Food Addit. Contam., 2004, 21(3), 265–286 CrossRef CAS PubMed.
-
European Commission: Directorate-General for Research and Innovation, F. Bayer, F. Welle and R. Franz. Guidance and criteria for safe recycling of post consumer polyethylene terephthalate (PET) into new food packaging applications, Publications Office, 2004, available from: https://op.europa.eu/en/publication-detail/-/publication/1fd85096-c1f2-4851-a56b-f682b16d7101 Search PubMed.
- G. Albini, V. Brunella, B. Placenza, B. Martorana and V. Guido Lambertini, Comparative study of mechanical characteristics of recycled PET fibres for automobile seat cover application, J. Ind. Text., 2019, 48(6), 992–1008 CrossRef CAS.
- K. Ghosal and C. Nayak, Recent advances in chemical recycling of polyethylene terephthalate waste into value added products for sustainable coating solutions – hopevs. hype, Mater. Adv., 2022, 3(4), 1974–1992 RSC.
- K. Sarkar, S. R. Krishna Meka, A. Bagchi, N. S. Krishna, S. G. Ramachandra and G. Madras,
et al., Polyester derived from recycled poly(ethylene terephthalate) waste for regenerative medicine, RSC Adv., 2014, 4(102), 58805–58815 RSC.
- S. Singh, S. Sharma, A. Umar, S. K. Mehta, M. S. Bhatti and S. K. Kansal, Recycling of waste poly(ethylene terephthalate) bottles by alkaline hydrolysis and recovery of pure nanospindle-shaped terephthalic acid, J. Nanosci. Nanotechnol., 2018, 18(8), 5804–5809 CrossRef CAS PubMed.
- S. Ügdüler, K. M. Van Geem, M. Roosen, E. I. P. Delbeke and S. De Meester, Challenges and opportunities of solvent-based additive extraction methods for plastic recycling, Waste Manage., 2020, 104, 148–182 CrossRef PubMed.
- R. Geyer, B. Kuczenski, T. Zink and A. Henderson, Common misconceptions about recycling: Common misconceptions about recycling, J. Ind. Ecol., 2016, 20(5), 1010–1017 CrossRef.
-
F. Welle, The facts about PET [Internet], Unpublished, 2015, available from: DOI:10.13140/RG.2.1.3043.2726.
- A.-D. Le, R. Gilblas, V. Lucin, Y. L. Maoult and F. Schmidt, Infrared heating modeling of recycled PET preforms in injection stretch blow molding process, Int. J. Therm. Sci., 2022, 181, 107762 CrossRef CAS.
-
O. Brandau, Bottles, Preforms and Closures: A Design Guide for PET Packaging, William Andrew Publishing, Norwich, CT, 2nd edn, 2012 Search PubMed.
- PET trays' existential dilemma, [Internet], Plastics Recyclers Europe, available from: https://www.plasticsrecyclers.eu/news/pet-trays-existential-dilemma/.
- Huge potential for tray-to-tray recycling: PETCORE, [Internet], Argus Media, available from: https://www.argusmedia.com/en/news-and-insights/latest-market-news/2578742-huge-potential-for-tray-to-tray-recycling-petcore.
- Klöckner Pentaplast, Tray2Tray®: A circular solution for food packaging [Internet], available from: https://www.kpfilms.com/en/food-packaging/sustainability/#/tray2tray.
- AMB Packaging, AMB TrayRevive, [Internet], available from: https://www.ambpackaging.com/products/amb-trayrevive/.
- Textile Exchange, Preferred Fiber and Materials Market Report 2021 [Internet], available from: https://textileexchange.org/app/uploads/2021/08/Textile-Exchange_Preferred-Fiber-and-Materials-Market-Report_2021.pdf.
- N. A. S. Suhaimi, F. Muhamad, N. A. Abd Razak and E. Zeimaran, Recycling of polyethylene terephthalate wastes: A review of technologies, routes, and applications, Polym. Eng. Sci., 2022, 62(8), 2355–2375 CrossRef CAS.
- Textile Exchange, Recycled Claim Standard (RCS) v2.2: Implementation manual, [Internet], available from: https://textileexchange.org/app/uploads/2021/02/RCS-v2.2-Implementation-Manual.pdf.
- Textile Exchange, Global Recycled Standard (GRS) v4.2: Implementation manual, [Internet], available from: https://textileexchange.org/app/uploads/2021/02/GRS-v4.2-Implementation-Manual.pdf.
- European Commission, EU strategy for sustainable and circular textiles: Communication from the Commission to the European Parliament, the Council, the European Economic and Social Committee and the Committee of the Regions [Internet], available from: https://environment.ec.europa.eu/document/download/74126c90-5cbf-46d0-ab6b-60878644b395_en?filename=COM_2022_141_1_EN_ACT_part1_v8.pdf.
- European Commission, EU strategy for sustainable and circular textiles [Internet], available from: https://environment.ec.europa.eu/strategy/textiles-strategy_en.
- F. Samperi, C. Puglisi, R. Alicata and G. Montaudo, Thermal degradation of poly(ethylene terephthalate) at the processing temperature, Polym. Degrad. Stab., 2004, 83(1), 3–10 CrossRef CAS.
- S. Haslinger, M. Hummel, A. Anghelescu-Hakala, M. Määttänen and H. Sixta, Upcycling of cotton polyester blended textile waste to new man-made cellulose fibers, Waste Manage., 2019, 97, 88–96 CrossRef CAS PubMed.
- T. Ochi, S. Okubo and K. Fukui, Development of recycled PET fiber and its application as concrete-reinforcing fiber, Cem. Concr. Compos., 2007, 29(6), 448–455 CrossRef CAS.
- M. Santiago-Calvo, A. Himmelsbach, C. Alonso, M.-T. Fernández, E. Cañibano and C. Brütting,
et al., Enhanced flame-retardant performance of undervalued polyethylene terephthalate waste as a potential use in foamed materials, J. Polym. Environ., 2024, 32(10), 4483–4495 Search PubMed.
- K. Kaiser, M. Schmid and M. Schlummer, Recycling of polymer-based multilayer packaging: A review, Recycling, 2017, 3(1), 1 CrossRef.
- T. Li, G. Theodosopoulos, C. Lovell, A. Loukodimou, K. K. Maniam and S. Paul, Progress in solvent-based recycling of polymers from multilayer packaging, Polymers, 2024, 16(12), 1670 CrossRef CAS PubMed.
- MultiCycle, [Internet], CreaSolv®, available from: https://www.creasolv.de/en/plants-projects/multicycle.html.
- V. Sinha, M. R. Patel and J. V. Patel, Pet waste management by chemical recycling: A review, J. Polym. Environ., 2010, 18(1), 8–25 CrossRef CAS.
- Converting household waste into energy, Veolia, available from: https://www.veolia.com/en/resources/circular-economy/converting-household-waste-energy.
- Renewable energies and waste-to-energy – SUEZ Group., available from: https://www.suez.com/en/waste/waste-recycling/renewable-energies.
- EEW – Energy From Waste, EEW Energy From Waste, 2024, available from: https://www.eew-energyfromwaste.com/en/.
|
This journal is © The Royal Society of Chemistry 2025 |
Click here to see how this site uses Cookies. View our privacy policy here.