DOI:
10.1039/D2PY00069E
(Paper)
Polym. Chem., 2022,
13, 2459-2468
Design rules for performing water-sensitive ring-opening polymerizations in an aqueous dispersion†
Received
17th January 2022
, Accepted 4th March 2022
First published on 16th March 2022
Abstract
The water sensitivity of ring-opening polymerizations (ROP) prevents any polymerization technique using water as a solvent which ultimately sets a limit on the polymeric material accessible. We implement a droplet microfluidic encapsulation strategy to create polyester and polyether particles dispersed in water. In this work, we systematically investigated the process and formulation parameters that govern the stability of the micro-droplets during generation, flow, and collection. More specifically, we tune droplet viscosity, surface tension, and hydrophobicity through the addition of amphiphilic block copolymers (ABC) and hydrophobes to further shield the ROP catalyst in the aqueous dispersion. The increased catalyst stability ultimately results in higher monomer conversion and higher molecular weight polymer. We subsequently show that by changing the ABC composition, we can further tune the ROP reaction time. Finally, we applied the encapsulation technique and formulation optimization to perform another water-sensitive ROP in an aqueous dispersion. Utilizing our design rules to tune the viscosity and surface tension of the droplets, we successfully synthesized polyether particles dispersed in water. Overall, we demonstrate the power and versatility of the encapsulation methodology and establish the fundamental guiding principles to encapsulate water-sensitive polymerization catalysts to yield spherical polymer particles dispersed in water.
Introduction
The process used to produce a polymer is known to impact the final properties of the material. For example, polystyrenes synthesized via solution polymerization versus suspension polymerization have different material properties and thus are used for different applications (e.g., expanded polystyrene and high impact polystyrene).1–3 Suspension polymerization is a process that uses mechanical agitation to generate monomer droplets suspended in a nonsolvent. The polymerization occurs within the monomer droplets, and the liquid phase outside of the droplets provides temperature and viscosity control allowing the polymerization to reach high molecular weight. Water is a very common continuous phase for suspension polymerizations as it is economical, environmentally friendly, and has extremely low solubility in most synthetic polymers.4,5 Aqueous suspension polymerization, however, is incompatible with water-sensitive chemistries like the ring-opening polymerization (ROP) of cyclic monomers (e.g., ester and ether), at the exception of ring-opening metathesis polymerization (ROMP).6–10 In previous work, we encapsulated water-sensitive ROP catalysts via droplet-based microfluidics, which temporarily shielded the catalyst and allowed polymerization to proceed in an aqueous dispersion.11
The microfluidic encapsulation strategy separately supplies a catalyst solution and a monomer solution in a hydrophobic solvent, which are fed into a narrow tube where the polymerization starts before meeting the immiscible continuous aqueous phase at a co-flowing junction to form micrometer-sized droplets, Fig. 1a. By supplying the catalyst solution between two monomer streams, we ensure that the hydrophobic solvent and monomer surround the catalyst to protect the catalyst during droplet formation. The device can operate in both a droplet generating orientation and a ‘fast quench’ orientation, Fig. S1.† The fast quench configuration allows us to precisely determine the reaction extent at the end of the hypodermic tubing outlet tip responsible for droplet generation for each flowrate before droplet formation. This technique allows us to access particles that could not be directly synthesized using any other polymerization technique, specifically we will show production of spherical crosslinked polyester11 and polyether particles in flow.
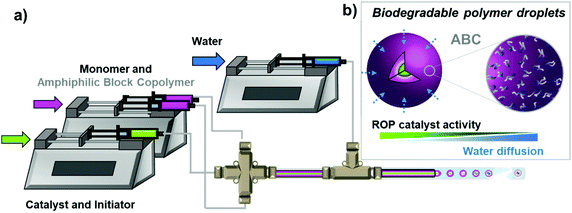 |
| Fig. 1 (a) Schematic of the droplet-based microfluidic device, where the monomer and catalyst streams are separately supplied until they reach the cross-tee. The ROP is initiated within the reactor volume until coming in contact with the immiscible water phase and shearing off into droplets. (b) After droplet generation, water begins to diffuse into the droplet microreactor, consequently quenching the ROP catalyst. As more water diffuses into the droplet, catalyst activity decreases. The amphiphilicity of the ABC added in the monomer phase allows its migration to the droplet interface, stabilizing the droplet. | |
To further expand this methodology to other water-sensitive ROP chemistries, we sought to understand the parameters enabling control of the rate of water diffusion. A slower rate of water diffusion would equate directly with a longer polymerization time and thus higher monomer conversion and polymer molecular weight. From our previous studies, we revealed that the addition of a nonionic surfactant to the aqueous phase led to both increased consistency in the droplet formation and minimized coalescence of the droplets during collection. Both observations appeared vital to the success of the methodology as any perturbation of the droplets during generation or collection would decrease the amount of time the catalyst has to polymerize before water diffusion into the droplet resulting in catalyst deactivation. Herein, we focus on probing and altering the two most important droplet generating parameters (i.e., the viscous and interfacial forces). By changing the viscous and interfacial forces through the formulation of the organic phase, we hypothesized that we would slow the diffusion of water into the droplet and, therefore, extend the catalyst's lifetime in the aqueous dispersion. The encapsulation methodology lets us easily tune droplet viscosity, surface tension, and hydrophobicity by adding amphiphilic block copolymers (ABC) and hydrophobes within the polymerization solution, Fig. 1b. We will explore the organocatalyzed ROP of δ-valerolactone with urea anion catalyst to form microparticles. The design rules we develop show how changing the ABC loading and composition can change the water-sensitive ROP catalysts’ polymerization activity in an aqueous phase. Finally, we expand the encapsulation methodology to include another water-sensitive ROP system to demonstrate the versatility of this methodology. We will show the ROP of propylene oxide catalyzed by a frustrated Lewis pair (phosphazene + organoboranes) with and without crosslinker to form polyether microparticles.
Results and discussion
Formulation and fluid dynamics
The droplet-based microfluidic device we implement is a co-flow geometry reactor constructed with all commercially available components and generates an oil-in-water (O/W) emulsion of 300 μm sized droplets.11 Fig. S2† provides a detailed description of the device. The choice of microfluidics as the encapsulation method allows great control over encapsulation efficiency and homogeneity in droplet size. The droplet formation is influenced by four forces, including viscous, interfacial tension, inertia, and buoyancy. Because flow velocities are relatively low (μL min−1–mL min−1) and the surface to volume ratio is high for micron-sized droplets, gravity and inertia forces become insignificant.12 Thus, we are left with viscous and interfacial tension as the two main forces that influence droplet dynamics.13 The viscous stresses at the tip of the needle act to elongate the interface before droplet formation, whereas the surface tension attempts to minimize the surface area. These two forces are best expressed by the Capillary number
(viscous/interfacial), where μ is viscosity, U is flow velocity, and γ is interfacial tension.14
To control droplet generation, breakup, coalescence, and mixing, we can tune each of the parameters in the Capillary number individually to see its effect on polymerization progress in the aqueous phase. Firstly, we looked at velocity (U), which is the most straightforward parameter to control via the flow rates (Q). For consistent catalyst encapsulation within microdroplets, we must operate in a dripping regime, where the droplet pinches off near the organic phase outlet tip before the droplet fills the cross-section of the outer capillary channel. The organic phase intrudes into the outer capillary, where the aqueous phase is continuously flowing. The droplet begins to form under the competition of interfacial tension, drag force, and momentum force. As the droplet size increases, the flow of the aqueous phase is obstructed and the drag force induced by the outer phase increases, which elongates the droplet and eventually leads to droplet break-off. The point at which the droplet breaks off is dependent on the flow rate ratio (i.e., Q = Qdispersed/Qcontinuous). The use of syringe pumps allows precise control over the flow rates, which is paramount because if the flow rate of the continuous phase is too high (Q ≪ 1) droplet forms in the jetting regime. Droplets formed in the jetting regime are less desirable as they are less uniform because droplet breakup is erratic, and the jetting stream exposes more surface area to the aqueous phase before droplet formation,15 leading to faster quenching of the polymerization, Fig. S3a.† On the other hand, when the continuous phase flow rate is too low (Q > 1), the flow regime shifts to the slug regime, where the droplet fills the width of the outer capillary channel. The interaction between the capillary tube wall and droplet perturbs the interface. This perturbation induces mixing and, therefore, would increase the diffusion of water into the droplet, Fig. S3b.†
16–18 For this geometry to operate in the dripping regime, we keep the flow rate ratio between 0.3 and 0.5.
Next, we look at optimizing the interfacial tension (γ). In the dripping regime, the shear force acts against the interfacial force. The addition of a surfactant, which contains hydrophobic and hydrophilic portions, lowers the surface tension at the interface between the two immiscible phases.19,20 Thus, during passive droplet formation, surfactants are transported to the interface, where they stabilize the droplets against coalescence.21 Previously, we found that a 1 wt% Tergitol loading to the aqueous phase was sufficient to improve droplet formation and prevent coalescence during flow and collection. However, we found that when an insufficient amount of surfactant was added to the system, we only produced droplets in a small area of flow rates, and most process conditions were producing droplets in the jetting regime. Alternatively, when an excess of surfactant was added, the droplets would break apart into smaller droplets during flow and coalesce during collection. Thus, relying solely on the addition of surfactant to the aqueous phase is insufficient to improve droplet formation without detrimental changes to the flow regime.
Lastly, we looked at the role of viscosity. We hypothesized that if we increased the viscosity of the droplet, we could increase the stability of the droplet during collection. The viscosity of the organic phase has a positive correlation to the extent of the ROP. As the residence time within the reactor volume increases, the polymerization conversion and the resulting continuous phase viscosity increase concurrently. As the mass concentration of polymer in the droplet increases, there is an increase in the fluid viscosity and shear resistance. If we change the viscosity of the solution through the change of formulation, we will also change the droplet generation dynamics.22 Therefore, the force required for droplet break-off increases. With this in mind, we looked towards changing the formulation of the organic phase through both the interfacial tension and viscosity. Ultimately, we opted to add an amphiphilic block copolymer to the dispersed phase, which would both increase the viscosity of the organic phase and alter the surface tension between the two phases leading to clean and consistent droplet formation, Fig. 2.
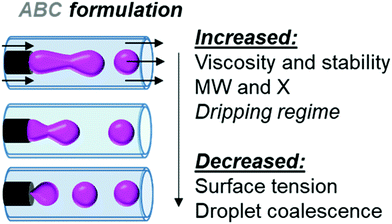 |
| Fig. 2 Through formulation and fluid mechanic optimization, droplet formation shifts from the undesirable jetting regime to the desirable dripping regime. | |
Urea anion ROP chemistry and amphiphilic block copolymers
We focus the encapsulation methodology on urea anion catalysts which perform the ring-opening polymerization (ROP) of cyclic esters to yield biodegradable polymers, Scheme 1a.6,8,23 The extreme water sensitivity of this polymerization allows us to easily see how the changes in the parameters affect the stability of the catalyst within the micro-droplets. Additionally, this catalytic system has been shown to exhibit fast kinetics (full conversion X > 90% in t < 10 s) for several cyclic esters.24–26 The success of the methodology relies on the high rate of polymerization to compete with the rate of water diffusion into the droplets. The faster the polymerization is, the better the chance of seeing polymerization progress before complete catalyst quenching via water diffusion. The choice of δ-valerolactone as the monomer is deliberate as it is a liquid monomer, which affords operation at high monomer concentrations with less solvent.
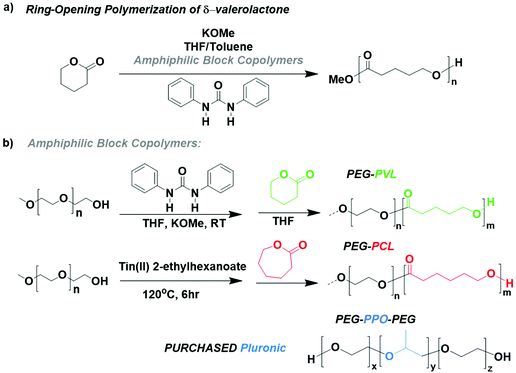 |
| Scheme 1 (a) The urea anion catalyst ring-opening polymerization of δ-valerolactone with the addition of amphiphilic block copolymers. (b) Synthetic scheme for organocatalytic ROP of block copolymers poly(ethylene glycol)-poly(valerolactone) (PEG-PVL) and poly(ethylene glycol)-poly (caprolactone) (PEG-PCL). Structure of purchased Pluronic poly(ethylene glycol)-poly(propylene glycol)-poly(ethylene glycol) (PEG-PPO-PEG). | |
We synthesized two ABCs with different polyester blocks, including poly(ethylene glycol)-poly(caprolactone) (PEG-PCL)27 and poly(ethylene glycol)-poly(valerolactone) (PEG-PVL),28 and purchased a Pluronic (PEG-PPO-PEG), Scheme 1b. A table listing the ABC molecular weights and block lengths can be found in the ESI, Table S1.† Before transferring the chemistry to the microfluidic device, we first tested the compatibility and impact of the ABCs on the urea anion catalyzed polymerization of δ-valerolactone. We found that even at an excess loading of 2 wt%, there was little to no effect on the polymerization kinetics in batch for PEG-PVL, PEG-PCL, and the Pluronic Fig. S6.†
Amphiphilic block polymer loading impact on catalytic activity
We chose the Pluronic (14 kg mol−1) to build the ABC loading ladder and identify the optimal ABC loading to the monomer solution. The optimal loading of Pluronic would produce a large range of residence times in the droplet regime without clogging the device. If the viscosity increases too much due to the progress of the ROP and the addition of the Pluronic within the solution, it can lead to significant pressure build-up within the smallest internal diameter in the device and result in clogging or stalling of the pumps. By placing the Pluronic in the monomer phase, the amphiphilic molecule is added at the outer shell of the organic droplet and thus closer to the interface organic/water interphase, where it decreases the droplet's surface tension. At a loading below 0.25 wt% of Pluronic in the dispersed phase, we could not produce droplets in the dripping regime. At loadings higher than 1 wt%, the device would experience clogging at the longer residence times. Therefore, we focused the loadings in between those bounds. To measure the success of the ROP protection from the aqueous phase, we compared the monomer conversion (using gas chromatography, GC) and the polymer molecular weight (using gel permeation chromatography, GPC) obtained from both the fast quench and droplet samples.29 Using a GC to determine the conversion of the monomer in the biphasic mixture was not trivial as we had to ensure that the biphasic aliquots were homogeneously dissolved in the GC solvent. We use THF as the main solvent and decane as the internal standard. A detailed description of the polymer product analysis can be found in the ESI.†
First, we confirmed that the addition of the Pluronic has no adverse effect on the ROP in flow. To do this, we operated the device in the ‘fast quench’ configuration and compared the different loadings to a control with no Pluronic in the solution, Fig. 3a and c. Both the polymer's molecular weight (GPC) and monomer's conversion (GC) data agreed that the addition of the Pluronic did not slow down the polymerization, as similar molecular weight polymers and conversion were obtained within the device at each residence time for all the loadings.
 |
| Fig. 3 Figure showing the effects of Pluronic loading (0.25 wt%–1 wt%). (A) GPC data for Pluronic loadings during fast quench into acetic acid. (B) GPC data for Pluronic loadings during droplet formation, using water as the continuous phase. (C) GC data for Pluronic loadings during the fast quench, using decane as an internal standard. (D) GC data for Pluronic loadings during droplet formation, using decane as an internal standard. | |
Next, we operated the device in the droplet generating configuration at each of the Pluronic loadings. We observed a positive correlation between the molecular weight and conversion attainable at each residence time with the increase in Pluronic loading from 0.25 wt% to 1 wt%, Fig. 3b and d. For example, at the longest residence time ∼12.5 s, the conversion attainable with an ABC loading of 0 compared to 1 wt% leads to an increase from 22% to 42%, respectively. The maximum molecular weight attainable was tripled with the addition of the 1 wt% loading compared to the 0 wt% control (14.6 kg mol−1 to 45.3 kg mol−1). These results confirmed that we temporarily shielded the water-sensitive ROP catalyst from the aqueous phase by tuning the Pluronic loading to the organic phase allowing the ROP to proceed while in the aqueous dispersion.
Amphiphilic block copolymer composition impact on catalytic activity
After demonstrating that the loading of the Pluronic in the organic phase played a role in catalyst protection, we investigated whether the ABC chemical composition also affects the final molecular weight and conversion attainable in the droplet. First, we confirmed that neither the PEG-PVL nor PEG-PCL adversely affected the ROP kinetics in the ‘fast quench’ configuration at the optimal 1 wt% loading found previously, Fig. 4a and c. Similarly, as residence time increases, there is a steady increase in molecular weight (GPC) and conversion (GC) for all the ABC implemented in the flow device. Therefore, we concluded that the composition of these three ABCs did not negatively affect the ROP kinetics while in the device.
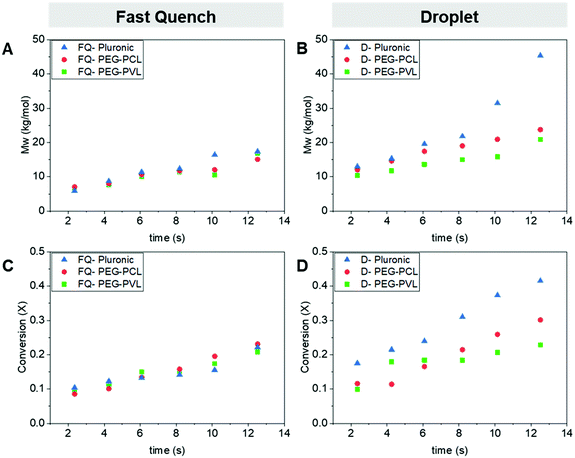 |
| Fig. 4 Figure showing the effects of ABC composition, comparing PEG-PVL, PEG-PCL, and Pluronic at 1 wt% loading. (A) GPC data for the different ABC compositions during fast quench into acetic acid. (B) GPC data for the different ABC compositions during droplet formation, using water as the continuous phase. (C) GC data for the different ABC compositions during the fast quench, using decane as an internal standard. (D) GC data for the different ABC compositions during droplet formation, using decane as an internal standard. | |
Next, we compared the impact of the three different ABC compositions on the ROP within the droplets. We observed a difference in the conversion and the ultimate polyester molecular weight between the three ABCs, Fig. 4b and d. The Pluronic outperforms the two di-blocks, while PEG-PCL seems to perform slightly better than PEG-PVL at higher residence times. We tentatively attributed this difference in performance to the difference in the hydrophilic–lipophilic balance values (HLB) between the ABCs used, Table 1.
Table 1 Composition comparison between amphiphilic block copolymers
Composition |
M
w a |
Hydrophobic/hydrophilic repeating unit |
HLB |
M
w determined by GPC in THF at 40 °C versus polystyrene standards.
Pluronic purchased from Sigma Aldrich. PEG-PCL and PEG-PVL synthesized.
|
Pluronicb |
14 600 |
0.16 |
16.5 |
PEG-PCL |
13 300 |
0.71 |
7.08 |
PEG-PVL |
6500 |
0.74 |
6.12 |
We conjecture that the larger amount of hydrophilic repeating units of the Pluronic increases the amount of hydrophilic units that migrate to the aqueous/droplet interface. The amphiphilicity of the ABC can lower the surface tension of the droplets during droplet generation and flow, which would lead to higher droplet stability and increased catalyst protection. The HLB for non-ionic surfactants takes into account the molecular weight of the hydrophilic portion of the molecule (Mh) and the molecular weight of the whole molecule (M),
. As you increase the HLB of the ABC from 0 to 18 you shift from a hydrophobic/oil-soluble molecule (HLB ∼ 0–6) to a water-dispersible molecule (HLB ∼ 6–9) and finally to a hydrophilic/water-soluble molecule (HLB ∼ 8–18).30–32 The PEG-PVL, PEG-PCL, and Pluronic, therefore, fall into the oil-soluble, water-dispersible, and water-soluble categories, respectively. The Pluronic, which performs the best, has an HLB consistent with surfactants utilized as oil/water emulsifying agents. Since we are generating an oil/water dispersion, it is consistent that the micro-droplets and subsequent dispersion are most stable with the Pluronic as the ABC versus the other two compositions. As mentioned previously, the stability of the droplet during generation, flow, and collection is paramount to the success of the process. Any perturbation of the droplet throughout its formation could increase the rate of transport of water into the droplet and lead to faster catalyst quenching. Overall, these experiments revealed that the composition of the ABC impacts the catalyst protection efficiency, which affects the catalyst activity within the droplet before quenching.
Addition of hydrophobes to micro-droplet formulation
After seeing the dramatic increase in ROP stability that the Pluronic ABC gave to the ROP chemistry, we wanted to investigate whether adding a superhydrophobe to the dispersed phase formulation increased the conversion in the micro-droplets. The rationale behind adding a superhydrophobic agent to the reaction mixture was that it would further prohibit the diffusion of water into the micro-droplet and extend the reaction time before catalyst quenching. We probed a series of superhydrophobic solvents (hexane, silicon oil, and hexadecane) that were miscible with the starting reaction solution to determine which did not negatively affect the ROP kinetics. Ultimately, we chose hexadecane as our superhydrophobic agent because we found that the organic solution was transparent and homogenous, and the ROP reached high molecular weight and conversion in under 30 seconds in batch. The addition of hexadecane in batch was shown to not affect the ROP kinetics at 0.4 M, Fig. S7.†
However, once we added the hexadecane into the flow reactor with the same reactant concentrations as previous experiments, we observed a deviation from the stable increase in molecular weight and conversion in the fast quench with the addition of 1 wt% Pluronic, Fig. 5a and c. The significant decrease in rate in the fast quench set-up was further observed in the droplet configuration with and without the addition of Pluronic to the trials containing the hydrophobe, Fig. 5b and d. During droplet formation, we noticed that there were precipitants already forming inside of the droplet as the solution was exiting the outlet tip. We postulate that both the Pluronic and polymer resulting from the ROP have poor solubility within the hexadecane and therefore are crashing out of the solution.
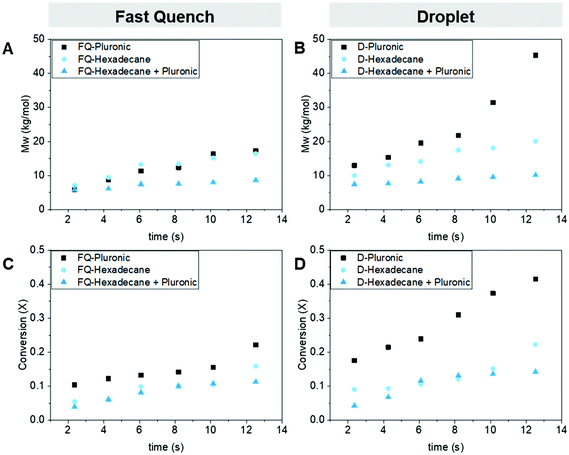 |
| Fig. 5 Figure showing the effects of superhydrophobic hexadecane addition at 0.4 M with and without 1 wt% loading of Pluronic. (A) GPC data for the addition of hexadecane with and without Pluronic during fast quench into acetic acid. (B) GPC data for the addition of hexadecane with and without Pluronic during droplet formation, using water as the continuous phase. (C) GC data for the addition of hexadecane with and without Pluronic during fast quench, using decane as an internal standard. (D) GC data for the addition of hexadecane with and without Pluronic during droplet formation, using decane as an internal standard. | |
Even though decreasing the polarity of the organic phase through the addition of the hydrophobe proved to be unsuccessful in this case, it highlighted an important constraint for this methodology. Specifically, we learned that we must ensure that the reactants, ABC, and the polymer product are soluble within the hydrophobe chosen. Further investigation into other superhydrophobes in the system is needed to assess whether or not they have the potential to decrease water diffusion into the micro-droplets for enhanced catalyst protection efficiency from the aqueous phase.
Encapsulation of ROP epoxide catalysts
To demonstrate the robustness of the design rules, we aimed to expand polymerization techniques in a different water-sensitive catalyst system.33 Specifically, we applied the micro-droplet encapsulation methodology to the ROP of epoxide catalyzed by a frustrated Lewis pair (phosphazene + organoboranes).34–37 We performed the ROP of propylene oxide (PO) with octanol as the initiator, phosphazene base (P2-t-Bu) and triethyl borane (Et3B) as co-catalysts, Scheme 2. We opted for this polymerization chemistry as we hypothesized that it could yield high molecular weight polymers within seconds.
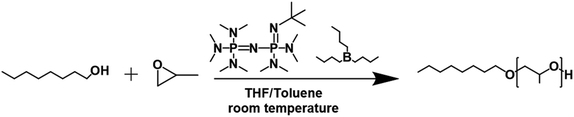 |
| Scheme 2 Ring-opening polymerization of propylene oxide catalyzed by a phosphazene base and triethyl borane. | |
We first attempted to identify the loading of the catalysts and concentration of the PO to achieve fast kinetics in batch. However, the high rate of polymerization targeted also equated with a highly exothermic reaction due to the high heat of polymerization of epoxides.38 Therefore, we utilized the microfluidic flow system to safely assess different catalyst loadings and monomer concentrations as the long microfluidic reactor could absorb the heat released by the polymerization. Additionally, we immediately quenched the solution as it exits the outlet tip in the fast quench configuration and through the water diffusion into the micro-droplets. To further enhance the safety of the experiment, we slightly modified the microfluidic flow system to prevent any possible backflow of the catalyst solution into the monomer reservoir, Fig. S8.† More information on the modifications can be found in the ESI.† This set-up led us to safely identify a formulation that delivers the fast kinetics necessary to compete with water diffusion during droplet formation. The final formulation utilized a monomer loading of 4 M and a initiator
:
base
:
borane
:
monomer ratio of 1
:
3
:
16
:
100.
We then verified that the there are no negative effects to the reaction kinetics with the addition of the pluronics to the formulation Fig. 6a. Next, we performed the polymerization in the droplet configuration, and we saw a similar increase in extent of reaction for each of the residence times compared to the fast quench results, for example at rt = 9.5 s the conversion in fast quench compared to droplet was 17.1% to 23.5%, respectively. This slight increase in conversion was indicative that the droplets were providing some catalyst protection; however, we aimed to further increase the extent of reaction happening within the dispersion to validate that polymerization does continue in the aqueous phase. Based on the design principles we developed, we postulated that an increase in viscosity or an increase in ABC loading would enhance the stability of the droplet, which would lead to a greater extent of reaction in the dispersion. The first formulation modification intended to increase the viscosity of the polymer attained after droplet formation by adding a crosslinker, 1,4-butanediol diglycidyl ether. With the addition of 1 wt% crosslinker, we saw a rapid increase in viscosity after the 10 s residence timepoint, which resulted in clogging within the device. Therefore, we operated between 2–10 s to avoid clogging when adding the crosslinker. With the addition of the crosslinker, we saw an increase in conversion at rt = 9.5 s from 26% in the fast quench to 41% during droplet generation, Fig. S9.† By introducing the crosslinking molecule, we increased the maximum conversion and molecular weight attainable in the dispersion.
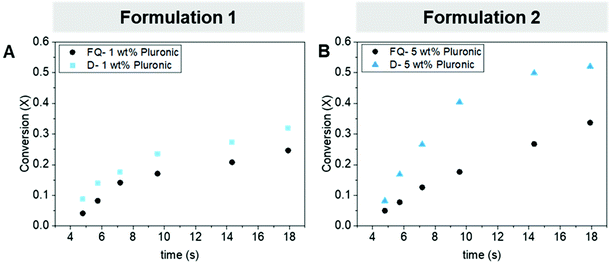 |
| Fig. 6 (A) Fast quench (FQ) versus droplet (D) conversion for the ROP of PO with 1 wt% Pluronic, resulting in a small increase in conversion for droplet over fast quench (B) Fast quench (FQ) versus droplet (D) for the ROP of PO with 5 wt% Pluronic, resulting in an increase in conversion for droplet over fast quench. | |
The second formulation modification intended to increase both the viscosity and decrease surface tension by increasing the ABC loading from 1 to 5 wt%. This formulation showed the largest catalyst stability enhancement in the dispersion illustrated by an increase in conversion from 17.6% to 40.3% at rt = 9.5 s, Fig. 6b. Both these experiments further demonstrated the validity and robustness of the developed design rules. Through simple formulation optimization we altered the viscosity and surface tension of the organic phase, which directly lead to an increase in catalyst stability and subsequently increased reaction extent. From our deep understanding of the role that viscosity and surface tension play on the stability of the droplet during generation, flow, and collection, we were able to temporarily shield a new water-sensitive catalyst and promote, for the first time, the ROP of PO in an aqueous dispersion. Additionally, we confirmed that the micro-droplet encapsulation methodology can be applied to other water-sensitive catalytic systems, which can increase catalytic activity within an aqueous dispersion.
Conclusions
In conclusion, we have implemented a droplet encapsulation strategy on two water-sensitive ring-opening polymerizations to successfully polymerize 300 μm size polyester and polyether particles in an aqueous dispersion. The encapsulation resulted in increased catalytic activity over our previous results owing to a systematic study probing the two most important droplet parameters, the viscous and interfacial forces. We assessed the addition of three amphiphilic block copolymers (PEG-PVL, PEG-PCL, and Pluronic) and a hydrophobe (hexadecane) and their effectiveness in improving particle formation and control leading to enhanced catalyst protection from the aqueous phase. We established that an increase in the loading of a Pluronic ABC resulted in an increase in catalytic activity. The 1 wt% Pluronic loading led to the highest molecular weight (45.3 kg mol−1) and conversion (X = 42%) compared to the 0 wt% loading (Mw = 14.6 kg mol−1X = 22%). Next, we showed that the composition of the ABC affect the catalyst protection efficiency. As the hydrophobic to hydrophilic repeat unit ratio increases, there is fewer hydrophilic units capable of assembling at the droplet interface, which would prevent the decrease in surface tension and therefore decrease droplet stability. Similarly, as the hydrophilic–lipophilic balance value increased we saw an increase in consistent droplet formation and stability during collection. The Pluronic which had the most hydrophilic repeating units and the largest hydrophilic–lipophilic balance, was shown to best stabilize the oil/water micro-droplets in the aqueous dispersion leading to the highest monomer conversion. Next, we investigated whether adding a superhydrophobe, hexadecane, would decrease or slow water diffusion into the micro-droplets. However, we found that the ABC and resulting polymer from the ROP would precipitate out of the solvent at the detriment to the catalytic activity.
Finally, we highlighted the versatility of the micro-droplet encapsulation methodology by expanding to another water-sensitive polymerization. Specifically, we performed the ROP of propylene oxide via an organic Lewis-Pair catalyst system. Through our deep understanding of the role that viscosity and surface tension play on droplet dynamics, we optimized the formulation to achieve a monomer conversion 20% higher within the microdroplets than in the fast quench. These results highlight that the off-the-shelf droplet-based microfluidic device and encapsulation methodology has the potential to be compatible with any fast water-sensitive polymerization.
Abbreviations
ROP | Ring-opening polymerization |
rt | Residence time |
VL | δ-Valerolactone |
CL | ε-Caprolactone |
BCP | Bis(ε-caprolactone-4-yl)propane |
Ca | Capillary number |
ABC | Amphiphilic block copolymers |
PO | propylene oxide |
GPC | gas permeation chromatography |
GC | gas chromatograph |
PEG | poly(ethylene glycol) |
Author contributions
Device design, device fabrication, amphiphilic block copolymer synthesis, and experiments were performed by D. D. H. The manuscript was written through the contributions of all authors. All authors have given approval to the final version of the manuscript.
Conflicts of interest
There is no conflicts to declare.
Acknowledgements
This material is based upon work supported by the National Science Foundation Graduate Research Fellowship under Grant No. DGE-1746047 and the National Science Foundation through Grant CBET 17-06911.
References
-
J. Maul, B. G. Frushour, J. R. Kontoff, H. Eichenauer, K.-H. Ott and C. Schade, Polystyrene and Styrene Copolymers, in Ullmann's Encycl. Ind. Chem, 2007 Search PubMed.
- E. Vivaldo-Lima, P. E. Wood, A. E. Hamielec and A. Penlidis, An Updated Review on Suspension Polymerization, Ind. Eng. Chem. Res., 1997, 36(4), 939–965 CrossRef CAS.
- B. Brooks, Suspension Polymerization Processes, Chem. Eng. Technol., 2010, 33(11), 1737–1744 CrossRef CAS.
- K. Häckl and W. Kunz, Some Aspects of Green Solvents, C. R. Chim., 2018, 21(6), 572–580 CrossRef.
- M. F. Cunningham, Controlled/Living Radical Polymerization in Aqueous Dispersed Systems, Prog. Polym. Sci., 2008, 33(4), 365–398 CrossRef CAS.
- D. J. Walsh, M. G. Hyatt, S. A. Miller and D. Guironnet, Recent Trends in Catalytic Polymerizations, ACS Catal., 2019, 9(12), 11153–11188 CrossRef CAS.
- J. Herzberger, K. Niederer, H. Pohlit, J. Seiwert, M. Worm, F. R. Wurm and H. Frey, Polymerization of Ethylene Oxide, Propylene Oxide, and Other Alkylene Oxides: Synthesis, Novel Polymer Architectures, and Bioconjugation, Chem. Rev., 2015, 116(4), 2170–2243 CrossRef PubMed.
- N. E. Kamber, W. Jeong, R. M. Waymouth, R. C. Pratt, B. G. G. Lohmeijer and J. L. Hedrick, Organocatalytic Ring-Opening Polymerization, Chem. Rev., 2007, 107(12), 5813–5840 CrossRef CAS PubMed.
-
A. Duda, ROP of Cyclic Esters: Mechanisms of Ionic and Coordination Processes, Elsevier B.V., 2012, vol. 4 Search PubMed.
-
W.-F. Su, Ring-Opening Polymerization, Springer, Berlin, Heidelberg, 2013, pp. 267–299 Search PubMed.
- D. D. Harrier, P. J. A. Kenis and D. Guironnet, Ring-Opening Polymerization of Cyclic Esters in an Aqueous Dispersion, Macromolecules, 2020, 53(18), 7767–7773 CrossRef CAS.
-
T. Glawdel, C. Elbuken and C. L. Ren, Droplet Generation in Microfluidics, in Encyclopedia of Microfluidics and Nanofluidics, Springer US, 2013, pp. 1–12 Search PubMed.
- T. Dinh and T. Cubaud, Role of Interfacial Tension on Viscous Multiphase Flows in Coaxial Microfluidic Channels, Langmuir, 2021, 37(24), 7420–7429 CrossRef CAS PubMed.
- P. Zhu and L. Wang, Passive and Active Droplet Generation with Microfluidics: A Review, Lab Chip, 2017, 17(1), 34–75 RSC.
- X. Liu, L. Wu, Y. Zhao and Y. Chen, Study of Compound Drop Formation in Axisymmetric Microfluidic Devices with Different Geometries, Colloids Surf., A, 2017, 533, 87–98 CrossRef CAS.
- L. Lei, Y. Zhao, W. Chen, H. Li, X. Wang and J. Zhang, Experimental Studies of Droplet Formation Process and Length for Liquid–Liquid Two-Phase Flows in a Microchannel, Energies, 2021, 14(5), 1–17 CrossRef.
- J. D. Tice, H. Song, A. D. Lyon and R. F. Ismagilov, Formation of Droplets and Mixing in Multiphase Microfluidics at Low Values of the Reynolds and the Capillary Numbers, Langmuir, 2003, 19(22), 9127–9133 CrossRef CAS.
- J. Wang, J. Wang, L. Feng and T. Lin, Fluid Mixing in Droplet-Based Microfluidics with a Serpentine Microchannel, RSC Adv., 2015, 5(126), 104138–104144 RSC.
-
J.-C. Baret, Surfactants in Droplet-Based Microfluidics, in Lab on a Chip, Royal Society of Chemistry, 2012, pp. 422–433 Search PubMed.
- A. R. Harikrishnan, P. Dhar, P. K. Agnihotri, S. Gedupudi and S. K. Das, Effects of Interplay of Nanoparticles, Surfactants and Base Fluid on the Surface Tension of Nanocolloids, Eur. Phys. J. E, 2017, 40(5), 1–14 CrossRef CAS PubMed.
- B. Riechers, F. Maes, E. Akoury, B. Semin, P. Gruner and J. C. Baret, Surfactant Adsorption Kinetics in Microfluidics, Proc. Natl. Acad. Sci. U. S. A., 2016, 113(41), 11465–11470 CrossRef CAS PubMed.
- D. Pan, Y. Zhang, T. Zhang and B. Li, Flow Regimes of Polymeric Fluid Droplet Formation in a Co-Flowing Microfluidic Device, Colloids Interface Sci. Commun., 2021, 42, 100392 CrossRef CAS.
- M. K. Kiesewetter, E. J. Shin, J. L. Hedrick and R. M. Waymouth, Organocatalysis: Opportunities and Challenges for Polymer Synthesis, Macromolecules, 2010, 2093–2107 CrossRef CAS.
- A. P. Dove, R. C. Pratt, B. G. G. G. Lohmeijer, R. M. Waymouth and J. L. Hedrick, Thiourea-Based, Bifunctional Organocatalysis : Supramolecular Recognition for Living Polymerization, J. Am. Chem. Soc., 2005, 127(40), 13798–13799 CrossRef CAS PubMed.
- B. Lin and R. M. Waymouth, Organic Ring-Opening Polymerization Catalysts: Reactivity Control by Balancing Acidity, Macromolecules, 2018, 51(8), 2932–2938 CrossRef CAS.
- B. Lin and R. M. Waymouth, Urea Anions: Simple, Fast, and Selective Catalysts for Ring-Opening Polymerizations, J. Am. Chem. Soc., 2017, 139(4), 1645–1652 CrossRef CAS PubMed.
- L. Azouz, F. Dahmoune, F. Rezgui and C. G'Sell, Full Factorial Design Optimization of Anti-Inflammatory Drug Release by PCL-PEG-PCL Microspheres, Mater. Sci. Eng., C, 2016, 58, 412–419 CrossRef CAS PubMed.
- C. L. Maikawa, A. Sevit, B. Lin, R. J. Wallstrom, J. L. Mann, A. C. Yu, R. M. Waymouth and E. A. Appel, Block Copolymer Composition Drives Function of Self-Assembled Nanoparticles for Delivery of Small-Molecule Cargo, J. Polym. Sci., Part A: Polym. Chem., 2019, 57(12), 1322–1332 CrossRef CAS PubMed.
- D. J. Walsh, M. A. Wade, S. A. Rogers and D. Guironnet, Challenges of Size-Exclusion Chromatography for the Analysis of Bottlebrush Polymers, Macromolecules, 2020, 53(19), 8610–8620 CrossRef CAS.
- R. C. Pasquali, M. P. Taurozzi and C. Bregni, Some Considerations about the Hydrophilic-Lipophilic Balance System, Int. J. Pharm., 2008, 356(1–2), 44–51 CrossRef CAS PubMed.
- N. Ohba, Hydrophile-Lipophile Balance Values for O/W Emulsions Stabilized by Nonionic Surfactants. I. Hydrophile-Lipophile Balance Values of Nonionic Surfactants Determined by Emulsification, Bull. Chem. Soc. Jpn., 1962, 35(6), 1016–1020 CrossRef CAS.
- M. Muranaka, K. Hirota and T. Ono, PEG–PLA Nanoparticles Prepared by Emulsion Solvent Diffusion Using Oil-Soluble and Water-Soluble PEG–PLA, Mater. Lett., 2010, 64(8), 969–971 CrossRef CAS.
- C. Maitre, F. Ganachaud, O. Ferreira, J. F. Lutz, Y. Paintoux and P. Hémery, Anionic Polymerization of Phenyl Glycidyl Ether in Miniemulsion, Macromolecules, 2000, 33(21), 7730–7736 CrossRef CAS.
- Y. Chen, J. Shen, S. Liu, J. Zhao, Y. Wang and G. Zhang, High Efficiency Organic Lewis Pair Catalyst for Ring-Opening Polymerization of Epoxides with Chemoselectivity, Macromolecules, 2018, 51(20), 8286–8297 CrossRef CAS.
- J. Zhao, N. Hadjichristidis and Y. Gnanou, Phosphazene-Promoted Anionic Polymerization, Polimery, 2014, 59(01), 49–59 CrossRef CAS.
- J.-L. Yang, H.-L. Wu, Y. Li, X.-H. Zhang and D. J. Darensbourg, Perfectly Alternating and Regioselective Copolymerization of Carbonyl Sulfide and Epoxides by Metal-Free Lewis Pairs, Angew. Chem., 2017, 129(21), 5868–5873 CrossRef.
- S. Boileau and N. Illy, Activation in Anionic Polymerization: Why Phosphazene Bases Are Very Exciting Promoters, Prog. Polym. Sci., 2011, 36(9), 1132–1151 CrossRef CAS.
- J. Herzberger, K. Niederer, H. Pohlit, J. Seiwert, M. Worm, F. R. Wurm and H. Frey, Polymerization of Ethylene Oxide, Propylene Oxide, and Other Alkylene Oxides: Synthesis, Novel Polymer Architectures, and Bioconjugation, Chem. Rev., 2016, 116(4), 2170–2243 CrossRef CAS PubMed.
Footnote |
† Electronic supplementary information (ESI) available. See DOI: 10.1039/d2py00069e |
|
This journal is © The Royal Society of Chemistry 2022 |
Click here to see how this site uses Cookies. View our privacy policy here.