DOI:
10.1039/D3GC04697D
(Paper)
Green Chem., 2024,
26, 2592-2598
Preparation of reusable copper-based biomass-carbon aerogel catalysts and their application in highly selective reduction of maleimides to succinimides with hydrosilane as a hydrogen source†
Received
30th November 2023
, Accepted 29th December 2023
First published on 10th January 2024
Abstract
Selective reduction is one of the most essential and frequently used transformations in organic synthesis. In this work, we developed a novel copper-based biomass-carbon aerogel catalyst (Cu(OTf)2@CAC) as a highly efficient and selective catalyst for maleimide reduction with hydrosilane as a hydrogen source for the first time. A strategy integrating chitin dissolution, nanofibrous regeneration, aerogel construction, and customizable carbonization was designed for the reduction of copper trifluoromethane sulfonate (Cu(OTf)2) to Cu(0) and Cu(I) on the CAC. The Cu(OTf)2@CAC exhibited excellent catalytic activity, chemo-selectivity, and recyclability for selective maleimide reduction to succinimides under mild conditions. Moreover, the Cu(OTf)2@CAC can be reused six times without noticeably losing activity. This work provides a representative and referential approach to achieve efficient catalytic conversion based on the reprocessing and customizable treatment of waste biomass resources.
Introduction
Developing efficient synthetic strategies for highly selective reduction reactions is essential due to their widespread occurrence in molecular synthesis.1 Succinimides2 are important structural units existing in natural products, pharmaceuticals, and advanced materials, such as methsuximide,3moiramide B and andrimide,4 XCF-37B,5etc. (Fig. 1). Compared to the classical synthetic methodologies, selective reduction of maleimide is a straightforward method to synthesize functional succinimides owing to atom- and step-economy. With mild conditions and good chemoselectivities, hydrosilane has emerged as a suitable hydrogen donor for selective reduction6 compared to the classical hydrogen7 and metal hydride reagents (such as LiAlH4 or NaBH4).8 However, most selective hydrosilylations to access target compounds using homogeneous transition metal catalysts require high catalyst loadings and ligands and cannot be reused. Maleimide comprising two –NCO– bonds and one C
C bond has attracted attention as a useful intermediate in organic transformations.9 At least three reduction products would be produced via homogeneous transition metal-catalyzed reduction, including pyrrolidine, pyrrole, and succinimide.10 The highly selective reduction to access succinimides is still a challenging issue that has to be solved.
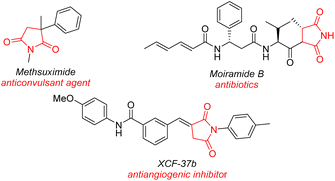 |
| Fig. 1 Representative bioactive compounds bearing a succinimide fragment. | |
Considering the above challenges, the development of recyclable catalysts would be the key to achieving the synthetic purpose. In recent years, owing to their high stability, easy recyclability, and different pathways, heterogeneous metal nanocatalysts have obtained more and more attention in organic transformations,11 such as CO2 transformations,12 Alder–ene reaction of allenynamides,13 alcohol oxidation,14 reductive amination,15 nitrile reduction,16 N-heterocycle synthesis,17etc.
Following our previous contributions on heterogeneous catalysis,18 we wish to report herein the preparation of copper-based biomass-carbon aerogel catalysts (Cu(OTf)2@CAC) and demonstrate their first application in the highly selective catalytic reduction of maleimides to achieve succinimides with hydrosilane as a hydrogen source under mild conditions. For the conversion of copper trifluoromethane sulfonate (Cu(OTf)2) to Cu(0) and Cu(I) on the CAC, a method incorporating waste chitin (shrimp and crab shells) dissolution, nanofibrous regeneration, aerogel fabrication, and adaptable carbonization was developed. Under benign conditions, the Cu(OTf)2@CAC showed outstanding chemo-selectivity, catalytic activity, and recyclability for selective maleimide reduction to succinimides. The Cu(OTf)2@CAC can also be used up to 6 times without significantly losing effectiveness. Based on the reprocessing and adaptable treatment of waste biomass resources, this study offers a representative and reference strategy for effective catalytic conversion.
Results and discussion
Formation of a copper-based biomass-carbon aerogel catalyst (Cu(OTf)2@CAC)
In this work, we designed a bottom-up approach by integrating chitin dissolution, regeneration, aerogel structuring, and pyrolysis to prepare a nanostructured copper-based biomass carbon aerogel catalyst (Cu(OTf)2@CAC) (Fig. 2a). First, crab shells (Fig. S1, ESI†), which were purified as in our previous work,18a were dissolved using potassium hydroxide/urea solution to obtain a yellow, transparent and viscous chitin solution (Fig. S2†). Then, the chitin solution was subsequently poured into a customized mold, immersed in anhydrous ethanol to trigger the sol–gel phase transition and washed to obtain nanofibrous chitin hydrogels (Fig. S3†). Subsequently, ethanol and acetone were used alternately to remove the solvent in the gel, and the as-prepared organogel was immersed in Cu(OTf)2-containing acetone solution to promote the stable complexation of Cu2+ with hydroxyl groups and amides on the molecular chain of chitin (Fig. S4†). Next, chitin-Cu2+ aerogels with three-dimensional porous structures were prepared by freeze-drying the above organogels. Finally, the CAC aerogel comprised Cu(0) and Cu(I), and the biomass carbon was prepared by pyrolyzing the composite aerogel under a nitrogen atmosphere (Fig. 2b). The SEM image shows a rich three-dimensional nano-network structure inside the copper-based biomass catalyst (Fig. 2c). Furthermore, the TEM images show that the chitin nanofibers present an amorphous nano-morphology after carbonization and realize the reduction of Cu2+ during the thermal decomposition process (Fig. 2d). The HRTEM images of Fig. S5† exhibited lattice fringes displaying interplanar spacings of 0.24 nm and 0.18 nm, being in agreement with Cu3N(100) and Cu(100), respectively (Fig. S5†).19 In addition, elements such as C, N, and Cu are shown using the EDS test. After carbonization, they are still retained and uniformly dispersed inside the Cu(OTf)2@CAC specimen (Fig. S6†). The porous nanostructure and uniform element distribution of the Cu(OTf)2@CAC specimen prove the feasibility of the strategy of using a chitin nanofibrous aerogel to support Cu, and at the same time provide abundant active sites for the improvement of catalytic activity.
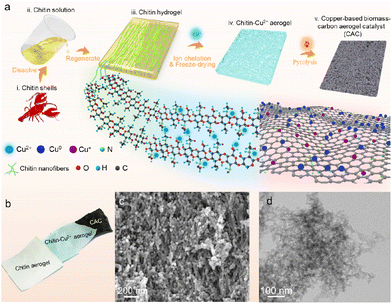 |
| Fig. 2 (a) Schematic diagram of the preparation of the copper-based biomass carbon aerogel catalyst (Cu(OTf)2@CAC). (b) Photographs of chitin aerogels, chitin/Cu2+ composite aerogels, and aerogel catalysts. (c) SEM image of Cu(OTf)2@CAC. (d) High magnification TEM image of Cu(OTf)2@CAC. | |
We further explored the structural regulation process of the Cu(OTf)2@CAC aerogel to reveal the effect of carbonization time on the microscopic morphology and determine the preparation conditions (Fig. 3). Raman imaging technology is a non-destructive and efficient method for characterizing material structures. We first tested the standard Raman spectra of the aerogel in different states (Fig. 3a). Obviously, the chitin/Cu(II) aerogel sample not only retains the C
O stretching vibration peak (1655.8 cm−1) and the C–N out-of-plane bending vibration peak (953.0 cm−1) of chitin, but also reserves the characteristics of metal salt peaks (750 and 1150 cm−1).20 Subsequently, the characteristic peaks of 1362.5 cm−1 and 1575.5 cm−1 in the Raman spectrum of the carbonized composite carbon aerogel represent the D and G peaks of amorphous carbon,21 respectively. In contrast, the characteristic peaks of chitin completely disappear (Fig. 3b and Fig. S7†). Fig. 3c shows a representative line diagram of the Raman characteristic spectrum of the Cu(OTf)2@CAC aerogel section treated with different carbonization times. The results show a strong time dependence of the D and G peak intensities from the surface to the interior of the carbon aerogel. When the pyrolysis time is less than 4 h, although the carbonization reaction occurs inside the Cu(OTf)2@CAC, the intensity of the D and G peaks is much lower than that on the surface; in contrast, when the pyrolysis time reaches 4 h, there is a uniform intensity distribution inside and outside the Cu(OTf)2@CAC (Fig. 3c).
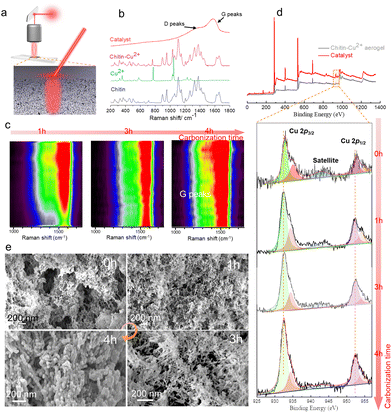 |
| Fig. 3 Preparation parameters and structure of the CAC aerogel. (a) Schematic illustration of structural characterization by the Raman imaging technique. (b) Raman spectra of the CAC aerogel, chitin/Cu2+ aerogel, and pristine chitin aerogel. (c) Representative 2D Raman imaging from the outside to the inside of the composite aerogel treated with different pyrolysis times (0–4 h). (d) XPS spectra of composite carbon aerogels, chitin/Cu aerogels, and Cu 2p spectra after 0 h, 1 h, 3 h, and 4 h of carbonization. (e) SEM images of aerogels with different carbonization treatment times. | |
Furthermore, we used X-ray photoelectron spectroscopy (XPS) to detect the valence state changes of copper in the CAC prepared at different pyrolysis times to clarify the relationship between the chemical properties of the CAC and the carbonization time (Fig. 3d). As shown, there are representative peaks of Cu 2p3/2 (934.99 eV) and Cu 2p1/2 (954.85 eV), and a satellite peak of 941.01 eV in the chitin/Cu(II) aerogel, confirming the presence of solid chelation between chitin and Cu(II) for the retention of Cu(II).22 After pyrolysis treatment, the characteristic peaks of Cu 2p3/2 and Cu 2p1/2 shifted to the direction of lower binding energies to 932.48 eV and 952.48 eV, respectively, indicating that Cu(II) was transformed into Cu(0) at a high-temperature pyrolysis process. In addition, the representative peaks of Cu–N at 934.38 eV and 954.08 eV also demonstrate the presence of Cu(I),23–25 which is consistent with the interplanar spacing results. In addition, by prolonging the pyrolysis time from 1 h to 4 h, the Cu 2p3/2 and Cu 2p1/2 peak intensities continued to increase, proving the necessity of prolonging the pyrolysis time to increase the content of Cu(0) in the CAC. Besides, the peak intensity of N 1s also becomes lower than the pristine state, which testifies to the combination of Cu–N (Fig. S2†). Therefore, we set the pyrolysis time as 4 h. Subsequently, we characterized the microstructure of the composite aerogel with different pyrolysis times. The results showed that after pyrolysis treatment for 1 h, the microstructure of the aerogel still showed a uniform three-dimensional nanofiber network structure similar to the pristine aerogel, with a specific surface area and an average pore diameter of 135.2 m2 g−1 and 32 nm, respectively; when the pyrolysis time was prolonged, the decomposition of chitin in the Cu(OTf)2@CAC is more thorough, forming a denser nano-network structure (average pore size 12–22 nm) (Fig. 3e), and a maximum specific surface area of 152.5 m2 g−1 (Fig. S9†). The above results illustrate that the timely pyrolysis process can achieve complete carbonization of the chitin nanofiber network and realize the reduction preparation of Cu(0) and Cu3N. This carbon aerogel with a rich nanoporous structure is expected to achieve highly efficient catalytic effects.
Catalytic reduction of maleimides with hydrosilane
To test our hypothesis, we initially investigated the reaction of N-phenylmaleimide 1a by using H3SiPh as the hydrogen donor and 5 mol% of different ruthenium complexes, including RuHCl(CO)(PPh3)3, Ru3(CO)12, RuH2(CO)(PPh3)3, [RuCl2(p-cymene)]2, [RuCl2(COD)]n, and RuCl3 in toluene at 120 °C for 12 h. A mixture of different ratios of products succinimide 3a, pyrrolidine 4a, and pyrrole 5a was always obtained (Table 1, entries 1–7). Notably, no reaction of N-phenyl maleimide 1a was detected without the additional catalyst (Table 1, entry 8). When a nanostructured RuCl3-based biomass carbon aerogel catalyst (RuCl3@CAC) was used instead of ruthenium complexes, only 14% yield but with highly selective product succinimide 3a was obtained (Table 1, entry 9). However, a 97% yield of succinimide 3a was produced by using Cu(OTf)2@CAC as the catalyst (Table 1, entry 10). Different hydrosilanes (HSi(Me)2Ph, H2SiPh2, and HSiPh3) and solvents (1,4-dioxane, CH3CN, DMC, and THF) were then evaluated, (Table 1, entries 11–18) and H3SiPh as the hydrogen donor and THF as the solvent in the presence of the Cu(OTf)2@CAC at 60 °C for 12 h were the optimized reaction conditions (Table 1, entry 18). The same catalyst loading using Cu(OTf)2 just led to a 22% yield of succinimide 3a under the above conditions (Table 1, entry 19).
Table 1 Optimization of the reaction conditions for the selective reduction of N-phenyl maleimidea
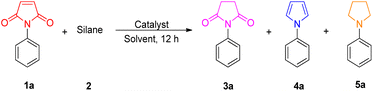
|
Entry |
Catalyst |
Silane |
Solvent |
Temp. (°C) |
Yield (%) |
3a/4a/5a |
Reaction conditions: 1-phenyl-1H-pyrrole-2,5-dione 1a (0.25 mmol), silane 2 (0.5 mmol), catalyst (20 mg, 1.2 mol%), solvent (1.0 mL) at 120 °C, 12 h, detected by GC.
5 mol%.
1.2 mol%.
|
1b |
RuHCl(CO)(PPh3)3 |
H3SiPh |
Toluene |
120 |
4/55/40 |
2b |
Ru3(CO)12 |
H3SiPh |
Toluene |
120 |
0/40/60 |
3b |
RuH2(CO)(PPh3)3 |
H3SiPh |
Toluene |
120 |
9/21/64 |
4b |
[RuCl2(p-cymene)]2 |
H3SiPh |
Toluene |
120 |
20/16/57 |
5b |
RuCl2(PPh3)3 |
H3SiPh |
Toluene |
120 |
6/33/60 |
6b |
[RuCl2(COD)]n |
H3SiPh |
Toluene |
120 |
31/15/47 |
7b |
RuCl3 |
H3SiPh |
Toluene |
120 |
44/15/40 |
8 |
— |
H3SiPh |
Toluene |
120 |
0/0/0 |
9 |
RuCl3@CAC |
H3SiPh |
Toluene |
120 |
14/0/0 |
10 |
Cu(OTf)2@CAC |
H3SiPh |
Toluene |
120 |
97/0/0 |
11 |
Cu(OTf)2@CAC |
— |
Toluene |
120 |
0/0/0 |
12 |
Cu(OTf)2@CAC |
HSi(Me)2Ph |
Toluene |
120 |
10/0/0 |
13 |
Cu(OTf)2@CAC |
H2SiPh2 |
Toluene |
120 |
24/0/0 |
14 |
Cu(OTf)2@CAC |
HSiEt3 |
Toluene |
120 |
4/0/0 |
15 |
Cu(OTf)2@CAC |
H3SiPh |
1,4-Dioxane |
100 |
98/0/0 |
16 |
Cu(OTf)2@CAC |
H3SiPh |
CH3CN |
80 |
16/0/0 |
17 |
Cu(OTf)2@CAC |
H3SiPh |
DMC |
90 |
62/0/0 |
18 |
Cu(OTf)2@CAC |
H3SiPh |
THF |
60 |
99/0/0 |
19c |
Cu(OTf)2 |
H3SiPh |
THF |
60 |
22/0/0 |
With the results in Table 1, we explored the substrate scopes of this first Cu(OTf)2@CAC-catalyzed selective reductions (Scheme 1). Firstly, a 1-aryl ring of maleimide-bearing substituents including –OMe, –Me, –tBu, –iPr, –OPh, –OH, –F, –Cl, –Br, –I, –CF3, etc. The ortho, meta, or para positions (3b–3q) smoothly transferred to the corresponding succinimide compounds in 40–92% yields. The electronic effect and steric effects did not hinder this selective catalytic reduction. Interestingly, 1-arylmaleimides 1r–3t with ketone and ester groups were tolerated and isolated in good yields without reducing the C
O bond in this catalytic reduction system. Moreover, succinimide with N-functional rings, such as benzyl, naphthalene, fluorene, pyrene, and aminoglutethimide (3u–3aa), produced good yields. Moreover, phenyl and methyl-substituted maleimide 1ab and 1ac would also be applied in this transformation, which could give a quaternary carbon center of the corresponding product.
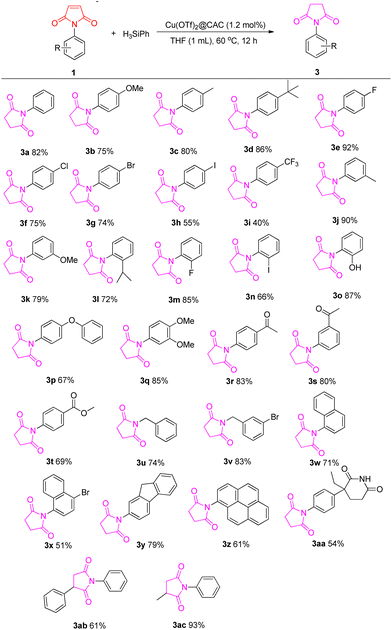 |
| Scheme 1 Cu(OTf)2@CAC catalyzed selective reduction of maleimides. Maleimide 1a (0.5 mmol), Cu(OTf)2@CAC (1.2 mol%, 20 mg), PhSiH3 (1.0 mmol), THF (1 mL), at 60 °C, for 12 h. | |
To gain insight into the mechanism of this reaction, some controlled experiments were conducted (Scheme 2). No C
O bond was reduced from amide under standard conditions, whereas 4-methoxystyrene could be easily converted to 4-ethylanisole. Moreover, when 0.2 mL of D2O was added to the reaction, deuterated compound 3ab-D was obtained from the transformation of substrate 1ab. These results indicated that the C
C bond is easier to reduce than the –CONR– bond. When the reaction was conducted under N2, only 20% yield of compound 3a was detected, but when the reaction mixture was kept under air for 5 h the yield of compound 3a increased to 99%. Moreover, an important observation is the formation of 1,3-diphenyldisiloxane during the reaction. These results rule out the possibility that the O atom of 1,3-diphenyldisiloxane comes from the air. As Cu(0) and Cu(I) species were detected on the CAC, Cu(0)@CAC and Cu(I)(OTf)@CAC were prepared and tested in the model reaction and full yield of succinimide 3a was found with Cu(I)(OTf)@CAC, which means Cu(I) on the CAC plays an important role in this catalytic reaction.
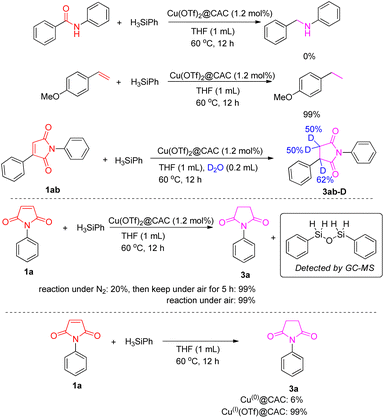 |
| Scheme 2 Controlled experiments. | |
In addition, the catalytic performance with different temperatures has been evaluated. As shown in Fig. 4, only 21% yield of succinimide 3a was obtained and 79% yield of N-phenyl maleimide 1a was still observed. The yield of succinimide 3a is slowly increasing below 40 °C, whereas N-phenyl maleimide 1a reacts smoothly above 40 °C and leads to full conversion at 60 °C.
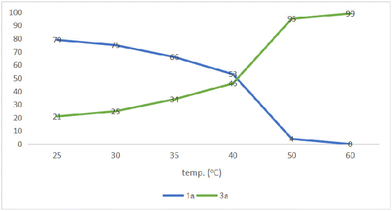 |
| Fig. 4 The catalytic performance at different temperatures. | |
Furthermore, the stability and reusability of our newly developed Cu(OTf)2@CAC were examined by the model reaction of N-phenyl maleimide 1a with PhSiH3 (Fig. 5). The Cu(OTf)2@CAC could be easily reused for the next catalytic cycle through a simple filtration. As illustrated in Fig. 5, the Cu(OTf)2@CAC could be reused at least 6 times, and the yield of product 3a did not show a significant decline, which demonstrates excellent catalytic activity and reusability of the developed Cu(OTf)2@CAC.
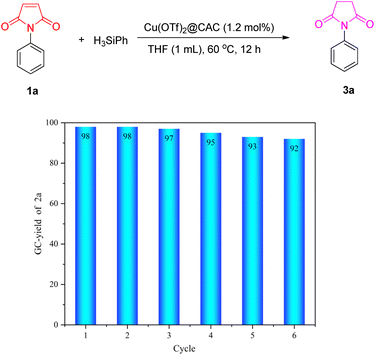 |
| Fig. 5 Reuse of the Cu(OTf)2@CAC. | |
Based on the above controlled experiments and previous literature on copper catalyzed hydrosilylation,26 a possible mechanism for the reaction is proposed in Scheme 3. Firstly, the “Cu–H” species would be easily generated by the reaction of phenylsilane to the Cu center of the CAC. Then, the “Cu–H” species would react with maleimide 1via the alkene insertion process, leading to intermediate A. Next, intermediate A underwent a σ-bond metathesis process with hydrosilane to generate intermediate B.26 Finally, the desired product succinimide 3a would be produced by the reaction of hydrosilane and oxygen from air with the release of the by-product silyl ether, and the regenerated “Cu–H” species would be used for the next cycle.
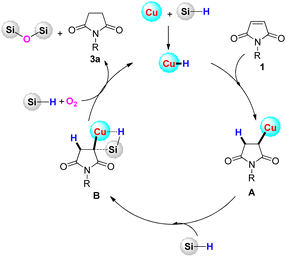 |
| Scheme 3 Proposed mechanism for the Cu(OTf)2@CAC-catalyzed selective reduction of maleimides. | |
Conclusions
In summary, a novel nanostructural biomass carbon aerogel catalyst (Cu(OTf)2@CAC) was designed and synthesized via a facile method and characterized by SEM, TEM, BET, Raman mapping, and XPS results. Cu(OTf)2@CAC was applied as an efficient and highly selective heterogeneous catalyst for the selective reduction of maleimides to succinimides with hydrosilane as a hydrogen source, which is superior to other homogeneous metal catalysts. Cu(OTf)2@CAC displayed excellent recyclability such that it could be reused at least six times without significant loss of activity. Further studies on this reaction mechanism and the application of the heterogeneous Cu(OTf)2@CAC for other selective reduction processes are underway.
Experimental section
Materials
Chitin, potassium hydroxide, urea, tert-butanol, and copper trifluoromethane sulfonate (Cu(OTf)2) were purchased from Aladdin Biochemical Technology Co., Ltd (Shanghai, China). Acetone and absolute ethanol were purchased from Guangzhou Chemical Reagent Co., Ltd. (Guangzhou, China).
Chitin powder purification
First, 400 g of crab shells were crushed, dispersed in 4 L of 4 wt% NaOH solution, and stirred for 8 h to remove proteins. Then, the substance was successively dispersed in 4 L of 0.3 wt% Na2ClO (8 h, stirring, 80 °C) and the pH level of the mixture was constantly maintained by adding 7 wt% HCl to remove pigments and minerals. After repeating the above steps twice, chitin powders were obtained by drying at 50 °C.
Chitin hydrogel and chitin aerogel preparation
First, 5.26 g of chitin powders were added slowly to 100 g of 20 wt% KOH/4 wt% urea solution while stirring in the trap at −40 °C for 2 h. The turbid mixture turned into a yellow viscous chitin solution after centrifugation at 10
000 rpm and 0 °C. Then, the chitin solution was poured and cast into the homemade mold. The chitin gel was formed by immersing the mold in 1 L of absolute alcohol at −25 °C for 24 h. Finally, the transparent chitin hydrogel was cut into 2 × 2 cm chitin gel pieces.
Copper-based biomass-carbon aerogel catalyst (Cu(OTf)2@CAC) preparation
First, 16 pieces of the chitin gel were dispersed in 50 mL of acetone to obtain chitin organogels, which are immersed in 50 mL of 5 wt% Cu(OTf)2 acetone solution and stirred for 5 h (Fig. S4†). Subsequently, the chitin/Cu gels were washed and replaced with 50 mL of acetone and 50 mL of tert-butanol for 24 h, respectively. Then the chitin/Cu gels were immersed in a box filled with liquid nitrogen and the chitin/Cu aerogels were obtained by freeze-drying (Christ Alpha 2-4 LDplus, −80 °C, 0.045 atm). Finally, 120 mg of the chitin/Cu aerogels were carbonized under a nitrogen atmosphere at 250 °C (heating rate is 5 °C min−1 and cooling rate is 10 °C min−1) for 1 h to obtain Cu(OTf)2@CAC-1 h. What's more, 120 mg of the chitin/Cu aerogels were carbonized under a nitrogen atmosphere at 250 °C (heating rate is 5 °C min−1 and cooling rate is 10 °C min−1) for 3 h to obtain Cu(OTf)2@CAC-3 h, and 120 mg of the chitin/Cu aerogels were carbonized for 4 h using the same procedure to obtain Cu(OTf)2@CAC-4 h. All Cu(OTf)2@CAC-1 h, Cu(OTf)2@CAC-3 h and Cu(OTf)2@CAC-4 h samples were washed with 10 mL of acetone for 12 h and dried at 50 °C to remove impurities.
Data availability
All experimental data and detailed procedures are available in the ESI.†
Author contributions
Shaohuan Lv and Zhanhong Yuan contributed equally to this work. S. Lv performed the experiments and the data analysis. Z. Yuan and Z. Liu prepared the Cu@CAC catalysts and characterization. D. Ye designed the Cu@CAC catalysts and wrote the catalyst part in the manuscript. B. Li convinced the idea, wrote and revised the manuscript, and directed the project. J. Zheng, J. Ye, J. Li, and S. Xu provided some experimental assistance and discussed the project. F. Xie revised the manuscript.
Conflicts of interest
There are no conflicts to declare.
Acknowledgements
We are thankful for the support from the Foundation of the Department of Education of Guangdong Province (no: 2021ZDZX2045), the Foundation of Wuyi University (no: 2021WGALH06), and the Wuyi University Innovation and Entrepreneurship Project.
References
-
(a) E. Vitaku, D. T. Smith and J. T. Njardarson, J. Med. Chem., 2014, 57, 10257–10274 CrossRef CAS PubMed;
(b) V. Froidevaux, C. Negrell, S. Caillol, J. P. Pascault and B. Boutevin, Chem. Rev., 2016, 116, 14181–14224 CrossRef CAS PubMed;
(c) J. Mayol-Llinàs, A. Nelson, W. Farnaby and A. Ayscough, Drug Discovery Today, 2017, 22, 965–969 CrossRef PubMed;
(d) R. V. Jagadeesh, K. Murugesan, A. S. Alshammari, H. Neumann, J. Pohl, M.-M. Radnik and M. Beller, Science, 2017, 358, 326–332 CrossRef CAS PubMed;
(e) O. I. Afanasyev, E. Kuchuk, D. L. Usanov and D. Chusov, Chem. Rev., 2019, 119, 11857–11911 CrossRef CAS PubMed.
-
(a) M.-X. Zhao, Q. Liu, K.-M. Yu, X.-L. Zhao and M. Shi, Org. Chem. Front., 2019, 6, 3879–3884 RSC;
(b) M. Aslam, S. Mohandoss and Y. R. Lee, Org. Lett., 2021, 23, 6206–6211 CrossRef CAS PubMed.
- E. C. Chen, N. Khuri, X. Liang, A. Stecula, H.-C. Chien, S. W. Yee, Y. Huang, A. Sali and K. M. Giacomini, J. Med. Chem., 2017, 60, 2685–2696 CrossRef CAS PubMed.
- C. Freiberg, H. P. Fischer and N. A. Brunner, Antimicrob. Agents Chemother., 2005, 49, 749–759 CrossRef CAS PubMed.
- K. Luo, Y. Bao, F. Liu, C. Xiao, K. Li, C. Zhang, R. Huang, J. Lin, J. Zhang and Y. Jin, Eur. J. Med. Chem., 2019, 179, 805–827 CrossRef CAS PubMed.
-
(a) D. Wei and C. Darcel, Chem. Rev., 2019, 119, 2550–2610 CrossRef CAS PubMed;
(b) J. Wu, S. Tongdee, Y. Ammaiyappan and C. Darcel, Adv. Synth. Catal., 2021, 363, 3859–3865 CrossRef CAS;
(c) J. Ke, W. Liu, X. Zhu, X. Tan and C. He, Angew. Chem., Int. Ed., 2021, 60, 8744–8749 CrossRef CAS PubMed;
(d) D. Mu, W. Yuan, S. Chen, N. Wang, B. Yang, L. You, B. Zu, P. Yu and C. He, J. Am. Chem. Soc., 2020, 142, 13459–13468 CrossRef CAS PubMed;
(e) J. Y. Corey, Chem. Rev., 2016, 116, 11291–11435 CrossRef CAS PubMed.
-
(a)
H.-U. Blaser and F. Spindler, in Handbook of homogeneous hydrogenation, Ed. J. G. de Vries and C. J. Elsevier, Wiley-VCH, Weinheim, 2007, vol. 3, p. 1193 Search PubMed;
(b) W. Tang and X. Zhang, Chem. Rev., 2003, 103, 3029–3070 CrossRef CAS PubMed;
(c) J.-H. Xie, S.-F. Zhu and Q.-L. Zhou, Chem. Rev., 2011, 111, 1713–1760 CrossRef CAS PubMed;
(d)
M. Beller and C. Bolm, Transition metals for organic synthesis, Wiley-VCH, Weinheim, 2004 CrossRef;
(e) V. G. Chandrashekhar, W. Baumann, M. Beller and R. V. Jagadeesh, Science, 2022, 376, 1433–1441 CrossRef CAS PubMed;
(f) J. Hou, X. Han, Y. Zhang, J. Huang, J. Wang and K. Yuan, Org. Lett., 2023, 25, 5709–5713 CrossRef CAS PubMed.
-
(a)
R. O. Hutchins and M. K. Hutchins, in Comprehensive
Organic Synthesis, ed. B. M. Trost and I. Fleming, Pergamon Press, Oxford, U. K., 1991, vol. 8, pp. 25–78 Search PubMed;
(b)
J. Seyden-Penne, Reductions by the Alumino and Borohydrides in Organic Synthesis, Wiley-VCH, New York, 2nd edn, 1997, pp. 122–129 Search PubMed.
-
(a) Y. Sheng, Y. Gao, B. Duan, M. Lv, Y. Chen, M. Yang, J. Zhou, G. Liang and Z. Song, Adv. Synth. Catal., 2022, 364, 307–313 CrossRef CAS;
(b) I. Dokli, R. Pohl, B. Klepetářová and U. Jahn, Chem. Commun., 2019, 55, 3931–3934 RSC.
-
(a) M. Ito, S. Ayaka, C. Kobayashi and T. Ikariya, J. Am. Chem. Soc., 2007, 129, 290–291 CrossRef CAS PubMed;
(b) L. Longwitz and T. Werner, Angew. Chem., Int. Ed., 2020, 59, 2760–2763 CrossRef CAS PubMed.
-
(a) J. Li, A. Mao, W. Yao, H. Zhu and D. Wang, Green Chem., 2022, 24, 2602–2612 RSC;
(b) J. Li, M. Yu, Z.-C. Duan, H. Zhu, W. Yao and D. Wang, Mater. Chem. Front., 2021, 5, 7861–7872 RSC;
(c) R. Tao, Y. Yang, H. Zhu, X. Hu and D. Wang, Green Chem., 2020, 22, 8452–8461 RSC;
(d) W.-Y. Huang, G.-Q. Wang, W.-H. Li, T.-T. Li, G.-J. Ji, S.-C. Ren, M. Jiang, L. Yan, H.-T. Tang, Y.-M. Pan and Y.-J. Ding, Chem, 2020, 6, 2300–2313 CrossRef CAS;
(e) W.-H. Li, C.-Y. Li, H.-Y. Xiong, Y. Liu, W.-Y. Huang, G.-J. Ji, Z. Jiang, H.-T. Tang, Y.-M. Pan and Y.-J. Ding, Angew. Chem., Int. Ed., 2019, 58, 2448–2453 CrossRef CAS PubMed;
(f) G. Gao, J.-Q. Di, H.-Y. Zhang, L.-P. Mo and Z.-H. Zhang, J. Catal., 2020, 387, 39–46 CrossRef CAS;
(g) Y.-M. Wang, J.-B. Wang, J. Huang, Z.-S. Cui, M. Zhang and Z.-H. Zhang, J. Catal., 2023, 427, 115100 CrossRef CAS.
-
(a) Y. Guo, S. Mei, K. Yuan, D.-J. Wang, H.-C. Liu, C.-H. Yan and Y.-W. Zhang, ACS Catal., 2018, 8, 6203–6215 CrossRef CAS;
(b) S. Navarro-Jaen, J. C. Navarro, L. F. Bobadilla, M. A. Centeno, O. H. Laguna and J. A. Odriozola, Appl. Surf. Sci., 2019, 483, 750–761 CrossRef CAS;
(c) A. Bordet, L.-M. Lacroix, P.-F. Fazzini, J. Carrey, K. Soulantica and B. Chaudret, Angew. Chem., Int. Ed., 2016, 55, 15894–15898 CrossRef CAS PubMed;
(d) M. I. Qadir, F. Bernardi, J. D. Scholten, D. L. Baptista and J. Dupont, Appl. Catal., B, 2019, 252, 10–17 CrossRef CAS.
- Z. Zheng, L. Deiana, D. Posevins, A. A. Rafi, K. Zhang, M. J. Johansson, C.-W. Tai, A. Cordova and J.-E. Backvall, ACS Catal., 2022, 12, 1791–1796 CrossRef CAS PubMed.
-
(a) H. Su, K.-X. Zhang, B. Zhang, H.-H. Wang, Q.-Y. Yu, X.-H. Li, M. Antonietti and J.-S. Chen, J. Am. Chem. Soc., 2017, 139, 811–818 CrossRef CAS PubMed;
(b) Y. X. Zhou, Y. Z. Chen, L. Cao, J. Lu and H. L. Jiang, Chem. Commun., 2015, 51, 8292–8295 RSC;
(c) W. Zhong, H. Liu, C. Bai, S. Liao and Y. Li, ACS Catal., 2015, 5, 1850–1856 CrossRef CAS;
(d) R. V. Jagadeesh, H. Junge, M. M. Pohl, J. Radnik, A. Bruckner and M. Beller, J. Am. Chem. Soc., 2013, 135, 10776–10782 CrossRef CAS PubMed;
(e) C. Zhu, Z. Tan, H. Jiang and M. Zhang, Green Chem., 2018, 20, 1992–1997 RSC.
-
(a) G. Liang, A. Wang, L. Li, G. Xu, N. Yan and T. Zhang, Angew. Chem., Int. Ed., 2017, 56, 3050–3054 CrossRef CAS PubMed;
(b) G. Liang, Y. Zhou, J. Zhao, A. Y. Khodakov and V. V. Ordomsky, ACS Catal., 2018, 8, 11226–11234 CrossRef CAS;
(c) T. Komanoya, T. Kinemura, Y. Kita, K. Kamata and M. Hara, J. Am. Chem. Soc., 2017, 139, 11493–11499 CrossRef CAS PubMed.
-
(a) M. R. Axet, S. Conejero and I. C. Gerber, ACS Appl. Nano Mater., 2018, 1, 5885–5894 CrossRef CAS;
(b) F. Leng, I. C. Gerber, P. Lecante, S. Moldovan, M. Girleanu, M. R. Axet and P. Serp, ACS Catal., 2016, 6, 6018–6024 CrossRef CAS;
(c) H. Ye, Q. Wang, M. Catalano, N. Lu, J. Vermeylen, M. J. Kim, Y. Liu, Y. Sun and X. Xia, Nano Lett., 2016, 16, 2812–2817 CrossRef CAS PubMed;
(d) M. Zhao, L. Xu, M. Vara, A. O. Elnabawy, K. D. Gilroy, Z. D. Hood, S. Zhou, L. Figueroa-Cosme, M. Chi, M. Mavrikakis and Y. Xia, ACS Catal., 2018, 8, 6948–6960 CrossRef CAS;
(e) C. Wang, R. Ciganda, L. Salmon, D. Gregurec, J. Irigoyen, S. Moya, J. Ruiz and D. Astruc, Angew. Chem., Int. Ed., 2016, 55, 3091–3095 CrossRef CAS PubMed;
(f) J.-L. Sun, H. Jiang, P. H. Dixneuf and M. Zhang, J. Am. Chem. Soc., 2023, 145(31), 17329–17336 CrossRef CAS PubMed.
-
(a) K. Sun, H. Shan, G.-P. Lu, C. Cai and M. Beller, Angew. Chem., Int. Ed., 2021, 60, 25188–25202 CrossRef CAS PubMed;
(b) J. Sun, C. Ci, H. Jiang, P. H. Dixneuf and M. Zhang, Angew. Chem., Int. Ed., 2023, e202303007 CAS;
(c) Q. Liu, C. Ci, H. Zhao, R. Xie, H. Jiang and M. Zhang, Green Chem., 2023, 25, 678–683 RSC;
(d) H. Jia, R. Xie, G. Lu, H. Jiang and M. Zhang, ACS Catal., 2022, 12, 10294–10303 CrossRef CAS;
(e) R. Xie, W. Mao, H. Jia, J. Sun, G. Lu, H. Jiang and M. Zhang, Chem. Sci., 2021, 12, 13802–13808 RSC.
-
(a) Z. Lin, J. Zou, S. Li, C. Zhang, F. Xie, B. Li and D. Ye, ACS Sustainable Chem. Eng., 2021, 9, 1568–1575 CrossRef CAS;
(b) B. Li, S. Liu, Q. Lin, Y. Shao, S. Peng and Y. Li, Chem. Commun., 2018, 54, 9214–9217 RSC;
(c) X. Zhang, H. Liu, X. Sheng, X. Mai, S. Hou, B. Li, X. Chen, Y. Li and F. Xie, J. Catal., 2022, 408, 227–235 CrossRef CAS;
(d) F. Xie, X. Chen, X. Zhang, C. Luo, S. Lin, X. Chen, B. Li, Y. Li and M. Zhang, J. Catal., 2021, 398, 192–197 CrossRef CAS.
- P. Xi, Z. Xu, D. Gao, F. Chen, D. Xue, C.-L. Tao and Z.-N. Chen, RSC Adv., 2014, 4, 14206–14209 RSC.
- M. Kaya, M. Mujtaba, H. Ehrlich, A. M. Salaberria, T. Baran, C. T. Amemiya, R. Galli, L. Akyuz, I. Sargin and J. Labidi, Carbohydr. Polym., 2017, 176, 177–186 CrossRef CAS PubMed.
- X. Li, L. Zhu, T. Kasuga, M. Nogi and H. Koga, Chem. Eng. J., 2022, 450, 137943 CrossRef CAS.
- H. F. Heiba, A. A. Taha, A. R. Mostafa, L. A. Mohamed and M. A. Fahmy, Int. J. Biol. Macromol., 2020, 152, 554–566 CrossRef CAS PubMed.
- T. Wang, R. Yang, N. Shi, J. Yang, H. Yan, J. Wang, Z. Ding, W. Huang, Q. Luo, Y. Lin, J. Gao and M. Han, Small, 2019, 15, 1902410 CrossRef CAS PubMed.
- J. Wang, C. Liu, J. Feng, D. Cheng, C. Zhang, Y. Yao, Z. Gu, W. Hu, J. Wan and C. Yu, J. Hazard. Mater., 2020, 394, 122567 CrossRef CAS PubMed.
- Y. Xue, Y. Li, G. Luo, K. Shi, E. Liu and J. Zhou, Adv. Energy Mater., 2020, 10, 2002644 CrossRef CAS.
-
(a) Y. Wang, Z.-L. Wang, W.-W. Ma and Y.-H. Xu, Org. Lett., 2022, 24, 4081–4086 CrossRef CAS PubMed;
(b) M. Zhang, Y. Ji, Z. Zhang and C. Zhang, Org. Lett., 2022, 24, 2756–2761 CrossRef CAS PubMed;
(c) M. W. Gribble Jr., M. T. Pirnot, J. S. Bandar, R. Y. Liu and S. L. Buchwald, J. Am. Chem. Soc., 2017, 139, 2192–2195 CrossRef PubMed.
|
This journal is © The Royal Society of Chemistry 2024 |
Click here to see how this site uses Cookies. View our privacy policy here.