DOI:
10.1039/D5SU00142K
(Tutorial Review)
RSC Sustainability, 2025, Advance Article
Recent breakthroughs in the valorization of lignocellulosic biomass for advancements in the construction industry: a review
Received
27th February 2025
, Accepted 6th June 2025
First published on 7th June 2025
Abstract
Extensive use of non-ecofriendly construction materials has already caused much damage to the environment. A novel array of green and sustainable construction materials (GSCMs) is required to address this challenge. Alternatives like Lignocellulosic biomass (LCBs) and other bio-based products have drawn the scientific community's attention over time. LCBs are eco-friendly materials originating from natural resources. Owing to their insoluble nature, morphological properties, and higher dimensional aspects, LCBs can be used to fabricate a wide category of biocomposites that can be consumed by the construction industry. However, for ease of research, there is a need for a review article highlighting up-to-date research connecting LCBs with GSCMs. This review provides a comprehensive examination of the numerous components, including cellulose, silica, lignin, and hemicellulose, that are present in LCBs. Furthermore, the review monitored the following: environmental challenges, novel waste recycling methods, modern valorization techniques, innovative applications of LCBs, durability, and performance enhancement. The importance of LCBs in GSCMs, such as biocomposites, bio-based insulating materials, coatings, adhesives, and various other applications, has been thoroughly examined. Finally, this review encompasses a summary of computational methods and life-cycle assessments (LCA) for the development of next-generation construction materials.
 Nilanjan Dey | Nilanjan Dey is currently enrolled as a PhD student at the Department of Polymer and Process Engineering, Indian Institute of Technology Roorkee, India, under the supervision of Prof. Pradip K. Maji. He received his Bachelor of Science degree from the University of Calcutta and a Master of Science degree from the Indian Institute of Technology Kharagpur. He has a 2-month research internship experience from IISER Kolkata and 1 year of research experience from the Indian Institute of Technology Bombay. His research interest focuses on extracting plant-based materials and valorizing them to fabricate high-end products for the construction industry. |
 Shakshi Bhardwaj | Shakshi Bhardwaj earned her BSc in Chemistry from the University of Delhi in 2017, followed by an MSc in Organic Chemistry from Maharshi Dayanand University, Rohtak, in 2019. In 2022, she commenced her PhD in the Department of Polymer and Process Engineering at the Indian Institute of Technology Roorkee, under the supervision of Prof. Pradip Kumar Maji. Her research focuses on the development of hydrophobic cellulose nanofiber aerogels integrated with phase change materials for thermal energy storage applications. In recognition of her academic excellence and research potential, she was awarded the Prime Minister's Research Fellowship, one of India's most prestigious doctoral fellowships. She has also received multiple awards for presenting her research at national and international conferences. |
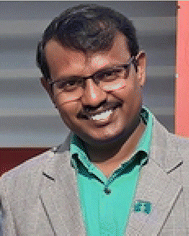 Pradip K. Maji | Dr Pradip Kumar Maji is an Institute Chair Professor in the Department of Polymer and Process Engineering at the Indian Institute of Technology Roorkee. He holds a PhD in Polymer Science and Technology from the Indian Institute of Technology Kharagpur. His research focuses on waste valorization, cellulose-based biopolymers, functional nanomaterials, and thermal insulation materials. He is a recipient of the JSPS Invitational Fellowship (2022), DAAD-Bilateral exchange fellowship (2024), the Outstanding Teachers Award from the Indian Institute of Technology Roorkee (2023), and the Young Scientist Award from the Asian Polymer Association (2023). He has been listed among Elsevier/Stanford's top 2% scientists globally for two consecutive years and has published over 150 peer-reviewed papers and patents. He also serves as an Associate Editor for Sustainable Chemistry and Pharmacy (Elsevier). |
Sustainability spotlight
This review emphasizes the innovative uses of lignocellulosic biomass in the construction sector, providing a sustainable substitute for traditional building materials. A thorough comparison is conducted between traditional and sustainable construction material sources bolstered by statistical data that demonstrate the environmental and socioeconomic effects of conventional materials. The study investigates advanced extraction processes and upscaling methodologies, connecting raw biomass to high-value goods and enhancing sustainability and resource efficiency in the building industry.
|
1. Introduction
Construction has been a fundamental aspect of human civilization since its inception. Having passed through the stone, bronze, and iron ages, we live in the polymer era.1 In our modern society, technologies are evolving swiftly, and many innovations have already been made in our daily lives. However, there is still a lot of scope for improvement in several sectors of modern society, the construction industry being one of them. In the ancient and medieval periods, people used to build their shelters primarily from wood and stone.2 In this modern era, those have been replaced by concrete, bricks, steel, and other masonry items. However, these traditional construction methods have several adverse environmental effects (shown in Fig. 1).
 |
| Fig. 1 A comparative illustration of the environmental effects of using conventional sources vs. sustainable sources. | |
Deforestation has emerged as a significant environmental concern in the rural areas of numerous impoverished and underdeveloped nations, as the predominant practice of using timber for constructing houses and household appliances has made the problem even worse.3 Apart from climate change issues, it is also responsible for the extinction of many Flora and Fauna species worldwide.4 According to a survey by the International Institute of Tropical Agriculture (IITA), Nigeria has been at the top of the table of countries with an alarming rate of deforestation. They have marked a worrisome rate of 3.5% deforestation, with approximately 400
000 hectares of forestland being deforested annually.5 A similar trend has also been observed in other parts of the world, the Amazon rainforest stands out as another appropriate example of it, where 20% of the mainland of the Brazilian Amazon has been deforested over the past three decades,6 as a result, there was an increase of surface temperature up to 3 °C,7 and by the year 2050, a decrease in rainfall has been estimated around 12–21% in the Amazon basin.8 Aside from deforestation, soil erosion is also trending upward in metro cities. In undisturbed regions, the rate of soil erosion is approximately 1.4 tons per year under natural conditions.9 Whereas, at construction sites, the rate might increase significantly from 700 times to as much as 40
000 times.10 In addition to land-related issues, air pollution has soared severely over the past few decades, due to a high level of CO2 emission, mainly attributed to many resources and non-renewable energy during unregulated construction activities.11,12 According to the Global Carbon Project statistics, in 2023, 37.55 billion metric tons of CO2 were released into the atmosphere,13 out of which a staggering 37% alone were contributed from the building sector.14 For apartment units, CO2 emission was recorded at 424.2–584.2 kg m−2 from steel and concrete, only.15 Apart from the aforementioned issues, several other concerns have arisen, the Urban Heat Island effect,16,17 Habitat Destruction,18 Resource Depletion,19,20 and Waste Generation21 being the prime ones. Research revealed that construction and demolition work generate trash at 63.74 kg m−2 and 1615 kg m−2 rate, respectively. It also highlights that the proper recycling of concrete and brick waste has the potential to be transformed into a $ 44.96 million economy.22
In light of the current crises related to resource depletion, waste generation, pollution, and sustainability challenges, our society requires some alternative resources that can serve as a greener solution in the construction sector. Here, our main focus would be the utilization of lignocellulosic biomass (LCBs) in the construction industry. Massive annual production of 8.2 billion tons of dry mass of different types of LCBs (shown in Table 1) demonstrates its potential to be utilized in construction and similar sectors where sustainability is a major issue.23 Nowadays, LCBs have been explored to be employed in many innovative ways. Biofuel production,24 bioplastic preparation,25 bioenergy generation,26 and polymeric materials27 are the extensive ones. Now, the question is, what are the basic features that made LCBs so significant for the construction industry? Well, LCBs possess many inherent properties that unveil their potential in the construction sector.
Table 1 Global annual production statistics of major agricultural crops
Crop |
Total dry biomass (million tons)30 |
Weight% of components present within |
References |
Cellulose |
Hemicellulose |
Lignin |
Asha |
Generally, Ash contains 80–95% silica.36 |
Rice |
905 |
37.0 |
16.5 |
13.6 |
19.8 |
31 |
Wheat |
62 |
40.2 |
38.8 |
17.0 |
2.3 |
32 |
Maize |
2724 |
42.7 |
23.2 |
17.5 |
6.8 |
31 |
Sugarcane |
1048 |
41.1 |
22.7 |
31.4 |
2.4 |
33 |
Barley |
23.46 |
37.5 |
37.1 |
15.8 |
4.2 |
34 |
Soybeans |
60.28 |
36.4 |
14.3 |
18.2 |
4.2 |
35 |
(a) Firstly, the abundance, renewability, and easy accessibility empowered it as a viable alternative to non-renewable resources.
(b) Secondly, its biodegradability, low ash content, and elemental composition make it chemically suitable and eco-friendly as well.
(c) Thirdly, from an engineering point of view, several factors like density, high aspect ratio, thermal properties, grindability, flowability, and high energy content put it ahead of other alternatives.28
(d) High content of inorganic materials, e.g., salts, silica, within these crops, can act as pozzolanic material, improving the durability and mechanical properties of concrete.29
(e) Lastly, the utilization of these materials lays a foundation for many small and medium-sized industries to grow economically following the waste-to-wealth approach.
Apart from the aforementioned points, a detailed discussion was also given below for every component of LCBs in an illustrative way (shown in Fig. 2).
 |
| Fig. 2 A detailed discussion of the structure, properties, and applications of cellulose, hemicellulose, lignin, and silica in an illustrative way. | |
To achieve desirable properties, all of these LCBs components have been used by researchers in some fixed proportion range. Neither all components are appropriate for every purpose nor any proportion of them. Cement and concrete composites generally require nano- or microfibers of cellulose in very small amounts of around 0.05–1 wt%, for reinforcement purposes. An excess proportion typically causes an adverse effect on concrete strength due to the agglomeration effect.37,38 A similar range of cellulose fiber wt% has also been followed in the case of fiber and plastic composites.39,40 Generally, in any type of composite material, cellulose fibers are used as an additional reinforcement, so the proportion is always kept low to fulfill the requirements. On the other hand, in aerogels, cellulose is used as a main structural component. For multipurpose applications like thermal insulation, acoustic insulation, fire-retardancy, etc., a 0.5–2 wt% suspension of cellulose pulp or fibers is considered, and into that other reactants are added in similar minor amounts to maintain the chemical homogeneity. In coatings and adhesives, lignin is generally utilized because of its hydrophobic nature. At maximum, 20–30 wt% lignin is incorporated into polyurethane-based coatings, because a greater amount can introduce brittleness and diminish the mechanical strength.41 In phenol-formaldehyde resins, around 20–40 wt% of lignin is generally used as a substitute for formaldehyde to maintain mechanical properties with enhanced reaction kinetics.42 For lignin-based epoxy coatings, optimum results were achieved at a 25 wt% proportion of lignin, whereas for polyester coatings low proportion of lignin (1–5 wt%) is usually maintained to avoid plasticizing and a more heterogeneous effect.43 In various bio-plastic materials, the application of lignin was also reported. It was observed that in lignin-starch-based foams, a replacement of 20 wt% of the starch by lignin so no adverse effect on the morphological features, besides improving the water-resistivity, elastic modulus, and thermal behaviours.44,45 The application of bio-based silica is also on trend in several sectors related to the construction industry. Rice husk ash generally contains 80–90 wt% of silica,46 which has been vaporized to fabricate low-weight but high-performance concrete materials. Apart from the structural components, silica aerogel is quite famous for its impressive thermal and acoustic insulation properties.47 Due to compositional dissimilarities, hemicellulose has some limited application in construction fields, although it is highly used in other fields like biomedical, energy applications, adsorbents, etc.48
The purpose of this study is to highlight the importance of sustainable alternatives in the construction sector. While numerous review journals are discussing the use of LCBs for bioenergy, biofuels, and biogas production, there is a lack of significant reviews on their utilization in the construction industry, despite the presence of many research articles on the topic.
This review aims to bridge that gap by providing a comprehensive overview. In chronological order, after the introduction part, the study begins by discussing the major environmental crises related to conventional construction techniques and emphasizes the importance of substituting traditional materials with sustainable alternatives. In this section, advanced functional materials derived from cellulose, hemicellulose, lignin, silica, and other bio-based resources like bamboo, cork, etc., have been discussed thoroughly. The third section outlines a thorough investigation of cut-edge technologies valorizing LCBs, that is, nothing but the combined process of extraction and subsequent purification methods to achieve the functional form of each constituent. A couple of following sections have been based on a detailed literature review of various construction industry-related products derived from the LCBs components. An additional section has been added based on the computational approach and Life Cycle Assessment (LCA). This section is completely based on theoretical assessments using various AI-ML tools. Eventually, the study ended with several insightful comments as concluding remarks aimed at challenging the status quo and guiding towards future directions.
2. Sustainable materials from lignocellulosic biomass and their impact on construction
Buildings made from sustainable, eco-friendly sources and that have minimal harmful effects on the environment as compared to traditional sources are termed “Green Buildings” (GB). From the production of materials to on-site construction, maintenance, or renovation, and finally, destruction, a GB has to be resource-efficient. Thus, careful selection of source materials, pre-estimation of environmental impacts, resource renewability issues, energy efficiency, and waste recyclability challenges must be a prerequisite in this case. Here, an assessment was done on specific points between conventional and sustainable sources.
2.1. Materials
As compared to traditional construction materials like steel, brick, concrete, etc. LCBs are abundant, renewable, and re-processable. However, the major challenge is utilizing the raw forms of LCBs and other biomaterials to produce the desired structural rigidity, which should cross the benchmark to be consumed by the construction industry. So, modifications are often needed in this case. Based on the requirements, this field offers a vast area for pursuing high-end research. A handful of quality journals have been published throughout the past few decades showcasing the ongoing research and the streak of development of advanced functional materials from cellulose, hemicellulose, lignin and silica, as well as the demand is showing an upward trend gradually (shown in Fig. 3). Before going into the detailed discussion, as an overview, the construction industry is a kind of sector where durability, longevity, strength and ductility (in some cases) are the key features that a product must have. A building material should have the ability to withstand the drastic changes in temperature and moisture content in the atmosphere. Thus, robust materials like bricks, concrete, cement, and steel have been used for a long time. But looking at the environmental crisis, it is high time to boost the research on such advanced materials, which is also one of the major objectives of this study. The research community has already explored several ways of the advancement of their materials, like doping, surface coating, tuning of nanostructure, composite fabrication, chemical functionalization, etc. Here, we have tried to sum up all of those valuable works concisely and enthusiastically.
 |
| Fig. 3 Number of publications published on LCBs functional material in the last 5 years. According to Scopus, searched on the 8th of August 2024. Search codes: “Cellulose Functional Material”, “Hemicellulose Functional Material”, “Lignin Functional Materials”, and “Silica Functional Materials”. | |
2.1.1. Cellulose advanced functional materials. Cellulose is the most abundant source of biomass on a global scale, having a production capacity of more than 100 billion tons annually.49 A demographic representation was introduced below to show the data on the worldwide production of cellulose in the year 2022 (ref. 50) (shown in Fig. 4). Due to the long chains of the β-d-glucopyranose rings, it provides a high aspect ratio to its micro and nanofibers, which proves its potential to be an initial substrate for manufacturing such robust materials. In the plant cell wall, cellulose forms the scaffold of the cell wall due to a thorough hydrogen-bonding network between the long strands of cellulose. This strong interaction is responsible for providing the tensile strength, which is required to endure the internal as well as external pressure to maintain the shape, integrity, and rigidity of the plant cell.51,52
 |
| Fig. 4 Global production statistics of cellulose (in 2022) with a demographic representation, data taken from ref. 53. | |
Due to the aforementioned properties, the usage of cellulose is conventional in many construction materials for providing additional mechanical strength, durability, and rigidity through reinforcement. Nowadays, in most functional materials, cellulose is usually incorporated in its nano- or micro-dimensional forms. Cellulose Nano Fibers (CNF),54 Cellulose Nano Crystals (CNC),55,56 and microfibrillated cellulose (MFC)57 are the most common forms. For example, Supit et al. have very recently developed an ultra-high-performing mortar; they have incorporated CNF and Wollastonite microfibers to improve the microstructure and mechanical properties. They have found that CNF in 0.005–0.030% along with 4.8% Wollastonite microfibers when mixed with 10% silica fume and 90% cement (by weight), compressive strength improved by 13% and flexural strength increased by over 30% than the control mortar. They have described the presence of Ca and Si in wollastonite as helping in the formation of C–S–H gel in a more effective way.58 Another good work was demonstrated recently by Raghunath et al., where they showed improvement in rheological properties, hydration kinetics, as well as mechanical features on the addition of CNCs as their key findings. In this study, they discovered that an amount of 0.02–4% (by weight) of fiber cement enhanced the shear-thinning property of the slurry. Additionally, at a higher % weight of CNC, around 2–4% hydration rate of the cement improved severalfold, also at 4% CNC, the flexural strength of the cement rose to 35.4% more than the unmodified fiber cement.59 Now, showcasing the efficacy of cellulose fibers of higher dimension, another commendable work has been published this year by Kadea et al., where they used MFC for the development of a laminate biocomposite. They found that a modification of polyvinyl alcohol (PVA) with 3-(trimethoxysilyl) propyl methacrylate (termed as “modified PVA”) showed an increase in flexural strength of the laminate biocomposite by 122% as compared to PVA. Further study revealed that the advancement of modified PVA with MFC (termed as modified PVA-MFC) causes an increase of impact strength of 148% as compared to modified PVA, besides mechanical properties, TGA data proved the enhancement of thermal stability as well. In light of all of these features, they claimed that the modified laminate biocomposite is suitable for applications like processing stage floors, furniture, and interior decorations.60 The discussed works render the utility of cellulose to be applied to the design of more advanced functional materials. More such research was discussed later in an application-oriented manner.
2.1.2. Hemicellulose advanced functional materials. Hemicellulose is the 2nd most abundant biomaterial of LCBs. They are highly branched heteropolymers consisting of various pentose (arabinose, xylose) and hexose (mannose, galactose) sugar units.61,62 They are responsible for binding cellulose with lignin to provide additional structural rigidity to the plant cell wall.59 It is also responsible for imparting flexibility and porosity to the cell wall. But this random branched structure makes hemicellulose amorphous; as a consequence, it does not show good mechanical strength and chemical resistance properties.63,64 That is the reason behind a comparatively lower number of available journals on hemicellulose advanced functional materials in comparison to cellulose advanced functional materials. Hemicellulose is more famous in the textile industry, packaging, biomedical applications like drug delivery, etc. Amongst very limited construction industry-related applications, Yang et al. successfully designed high-strength lignocellulosic fibers from agro-waste. Their fundamental idea was to bring the hemicellulose chains from the core to the surface, where, due to higher branching and the presence of the TEMPO-oxidized carboxyl group, bonding strength and mechanical properties have shown a noticeable change. They reported that the tensile index of the fibers improved from 18.72 N m g−1 to 33.28 N m g−1, the tearing index increased from 3.88 mN m2 g−1 to 4.63 mN m2 g−1, the bursting index enhanced from 1.71 kPa m2 g−1 to 3.04 kPa m2 g−1, while folding strength went from 3 to 58 times.65 That shows a perfect representation of processing high-value-added, low-cost products from simple agro waste, which can be further utilized in developing related materials.
2.1.3. Lignin advanced functional materials. Lignin is the third main component of LCBs. It is a polyphenolic complex organic compound found in plant cell walls. It mainly consists of three primary building blocks (also called phenylpropane units) named p-coumaryl alcohol, coniferyl alcohol, and sinapyl alcohol.66 It provides additional rigidity to the plant cell walls and water–repellent properties to the bark and leaves of plants. Highly branched structure, hydrophobic nature, and irregular crosslinking are the key features of this compound.67,68 Due to these inherent properties, lignin has always been a topic of interest to the scientific community for the synthesis of resins, foams, membranes, coatings, thermoplastics, etc.69 Lignin is highly used in the construction industry for hydrophobic coating and binding agents, or adhesive-related applications. People have also reported the application of lignin as a water-reducing agent in cement composites.70 Recently, one such application was demonstrated by Choowang et al., where they mixed glycerol and citric acid (as a crosslinking agent) with palm kernel shells (rich in lignin) to synthesize a binder for plywood production. They reported that, at an elevated temperature of 180–200 °C, the molten binder was able to penetrate the rubberwood efficiently, resulting in an enhancement of mechanical and water resistance properties. They also recommended using a 160–200 g m−2 amount of the adhesive for the best result.71 Another excellent piece of work was published by Long et al., where they introduced a lignin-derived hard carbon material having hybrid sp2-sp3 bonding. They incorporated microcrystalline units of graphene to generate sp2 fragments. This hard and hybrid carbon material could be used as an excellent precursor for making resins with tunable porosity.72 Numerous examples of such advanced materials are derived from components of LCBs that the construction industry can utilize highly.
2.1.4. Silica advanced functional materials. Silica is the major component in the ash of LCBs. It mainly remains in its silicate form in a mixture with other inorganic salts like carbonates, phosphates, etc.73,74 Silica can also be extracted via chemical treatment, without burning the LCBs.75 The long polymeric networks of silicates provide some additional stability to the plant tissues.76 Due to its catenation property and porous structure, there are plenty of novel applications feasible for silica/silicates, like the fabrication of semiconductors, insulators, cement composite, glass, tiles, etc.77–79 This year, one such review has been presented by Pobtocki et al., which summed up some decent works on upcycling the silica fume and fly ash (produced by industrial waste) to valorize geopolymer in a sustainable way that can be used as an eco-friendly building material.80 Talking about individual research, Mutlu et al. have recently published a commendable work. They utilized a high silica content clay to produce Galette tiles. Due to the high silica content, thermal and mechanical properties both improved in galette tiles. As a result, at elevated temperatures, flexural strength increased by up to 19%. Moreover, the unique thing of this work is that when reflectance measurement was done at the UV-Vis region, it revealed that besides improvement of thermal and mechanical properties, it also shows sterilizing properties under ambient conditions. This phenomenon happens as it is reflected in the UV-C region, and because of all of these, galette tiles produced here are ideal for industrial applications81
2.1.5. Miscellaneous. LCBs, in their extracted and modified form, are emerging as a sustainable alternative in the construction industry in modern society. However, from ancient times to the present rural area, different raw forms of plant biomass have traditionally been consumed by mankind. Bamboo, cork, hempcrete, straw bales, and natural latex are a few names under that category.82 Bamboo plays the same role as concrete pillars in traditional buildings or architecture; due to its low carbon emission rate and three times the growth rate of most other plants, it has a lot of potential as a sustainable alternative to replace concrete slabs, pillars, TMT bars, etc. Moreover, due to the highly elastic behavior of the vascular bundle present in bamboo, it shows a 6 times higher tensile strength than steel fiber, and the energy required for the production of the same mass of steel is 50 times higher than natural products.83 However, limitation emerges due to the poor compressive strength of bamboo than steel fibers. Some comparative data on the mechanical properties of different types of bamboo (found in various regions worldwide) with steel fiber reinforced concrete is given below (shown in Table 2). Now, coming to the flooring alternatives, people generally use cork, which is a sustainable, eco-friendly, and natural material found in the outer bark of Oak trees. Due to its lightweight, compact closed-cell structure, very low permeability for both solid and gas, low thermal conductivity, and chemical stability, it can be used as a green flooring option.84,85 A comparative study of the properties of the cork and ceramic tiles is provided below (shown in Table 3). Based upon such unique features, cork can be upscaled for many unique applications related to the construction industry like vibration damping,86 Volatile Organic Compounds (VOC) adsorbent,87 sandwich panels,88 plastic composite,89 insulation corkboards,90 cement composite91 etc.
Table 2 A comparison of the mechanical properties of different species of Bamboo with steel fiber reinforced concrete
Species |
Volume fraction of fiber (%) |
Native region |
Tensile strength (N mm−2) |
Compressive strength (N mm−2) |
Reference |
Bambusa bambus |
— |
India subcontinent |
239.00 |
51.33 |
83 |
Bambusa vulgaris |
— |
Southern China and Madagascar |
232.09 |
67.62 |
Olchlandra travancoria |
— |
Western Ghats (India) |
149.33 |
28.60 |
Dendrocalamus gigantis |
— |
Southeast Asia |
221.95 |
53.21 |
Steel fiber reinforced concrete |
0 |
— |
5.8 |
85 |
92 |
0.5 |
— |
6.9 |
91 |
1.0 |
— |
8.7 |
95 |
1.5 |
— |
10.8 |
98 |
2.0 |
— |
11.5 |
96 |
Table 3 Comparison between various physical properties of cork and ceramic tiles
Properties |
Cork |
Ceramic tiles |
References |
Density (kg m−3) |
160–240 |
2500–6000 |
96 and 97 |
Thermal conductivity (W m−1 K−1) |
0.045 |
0.6–1.7 |
97 and 98 |
Acoustic resistivity (kg m−2 s−1) |
1.2 × 105 |
— |
97 |
Specific heat (J kg−1 K−1) |
350 |
1000 |
97 and 99 |
Compressive strength (MPa) |
1 |
125–250 |
100 and 101 |
Tensile strength (MPa) |
0.85 |
25–50 |
100 and 101 |
Another frequently used natural material is hempcrete, prepared by mixing hemp fibers with water, cement, and lime.93 Again, just like cork, hempcrete also possesses some excellent properties that make it an ideal choice for building applications. High density (600–1000 kg m−3) for compact application, low thermal conductivity, acoustic insulation, vapour permeability, low energy demands, and CO2 adsorbing capacity advocates its potential to replace regular Portland cement.94,95
Similarly, Natural Rubber Latex (NRL) can also be applied to reinforcing cement mortars. NRL can be used as a promising agent in substituting commercial latex-like styrene-butadiene, polyvinyl acetate, etc. It is very cheap and easily accessible, mostly in South Asian countries. Thus, proper utilization can make it beneficial in several aspects of construction, like improving mechanical properties, filling microstructures, reducing shrinkages, replacing synthetic adhesives, etc. Recently, Mathew et al. demonstrated NRL's efficacy in upgrading mortar's mechanical properties. They highlighted an increase in NRL
:
cement ratio from 0.5% to 2%, flexural strength improved from 3.83% to 10.62%, and porosity diminished from 15.2% to 9.9%. Moreover, due to proper entrapment of the inner moisture, drying shrinkage and mass loss were reduced to 40.7% and 51.5%, respectively.102 On the other hand, a nice work on NH3-free NRL-based adhesive was presented by Román et al. They reported that the peeling strength of an NH3-free adhesive made from 35% dry natural latex rubber and 65% regular Cellulose-based office glue showed 4 times better adhesion properties than Elmer's glue. The peeling strength of said NH3-free NRL-based adhesive was 23.64 N cm−1, whereas Elmer's glue was just 6.29 N cm−1.103 From the above discussion, it is not very hard to understand that with proper operating procedures and required modifications, LCBs and natural and sustainable resources can completely replace the synthetic and commercial products from the construction sector.
2.2. Environmental impact and energy consumption
In the current scenario, 30% of greenhouse gas emissions and 40% of natural resources are being consumed by the building sector alone. In developed countries, 70% of electricity and 12% of water have been embezzled by this sector.104 The demand to make more commercial, residential, and industrial buildings kept rising over the years. Hence, the urge to produce more concrete, steel fibers, bricks, and cement is also moving upward. To cater to modern society's demands, 30 billion tons of concrete are produced every year. To make concrete, we also need to produce Portland cement (binding agent), which is responsible for 8–9% of anthropogenic CO2 emissions globally.105 Since the last 5 decades, energy consumption by the building sector has grown 1.8% per year and is projected to be over 4400 Mtoe (184.2 × 1018 J) by 2050.106 Some relevant data on the current topic is also represented below (shown in Fig. 5(a)–(e)). From this data, we can find some interesting trends. Firstly, countries having the most advanced technologies are mostly responsible for the major portion of Greenhouse gas emissions. Secondly, most residential, industrial, and transportation sectors are the major sectors that contribute to global energy consumption; thirdly, even in this modern era, human civilization is broadly dependent on fossil fuels, which is probably the most important outcome of the study. There is a huge gap in utilizing biomass and other renewable energies to address the sustainability issue in this field. Meanwhile, some other data (shown in Fig. 6(a) and (b)) describes how biomass in different forms on biomass in various continents, as well as globally, has been destroyed, which again turns out to be a major source of pollution. So, the way out is to the proper valorization of that biomass in different forms, to replace the non-renewable energies and non-eco-friendly products from the market.
 |
| Fig. 5 (a) Global CO2 emissions data by top 10 countries in the world (in 2022), data taken from ref. 107 (b) global energy consumption data resource-wise (in 2023), data taken from ref. 108, (c) sectoral share of global CO2 emissions, data taken from ref. 109 (d) share of global CO2 emissions by top 5 nations versus rest of the world, data taken from ref. 107 (e) sectoral share of global energy consumption data resource, data taken from ref. 110. | |
 |
| Fig. 6 (a) Continent-wise statistics of the extent of biomass destroyed by burning (in 2019), (b) global trend of total biomass burnt annually over the decades, reproduced from ref. 111 with permission from Elsevier, copyright 2024. | |
For example, Ardente et al. reviewed the role of materials in insulation boards for households by the Life Cycle Analysis (LCA) approach. They compared the Kenaf fibers with some other commercial materials used in making insulation boards, and they found the superiority of Kenaf fibers over other materials used for the same purpose.112 Apart from the environmental and energy data, they also considered the carcinogenic nature of some materials to draw their conclusions.
2.3. Durability and performance
Once we are done with the selection of the materials, the estimation of probable environmental and energy consumption parameters, the third and most important aspect is the ultimate performance of that product, and also how durable and sustainable it is! Hence, a thorough review of the product's above parameters is also necessary. In recent times, many good research journals have published on the valorization of LCBs to make value-added products, which can be a direct product or can be added with conventional sources in a composite to enhance their durability, quality, longevity, and performance (shown in Table 4).
Table 4 Enhancement of durability, performance, and quality of construction materials by valorization of LCBs
Amount of biomass (%) |
Material type |
Effect |
References |
100% |
Lignocellulosic flim |
High-performance biofilms were developed from LCBs, with an excellent tensile strength of 132.48 MPa, strain of 9.77%, and toughness of 9.77 MJ m−3 also at wet conditions tensile strength was found 70.38 MPa, strain of 7.70% and toughness of 3.76 MJ m−3, which accounts for an outstanding durability. It also has UV-resistance properties |
113 |
0.01–0.1% |
Cement mortar |
High flexural strength and a greater degree of hydration due to a more porous structure |
114 |
100% |
Bioplastic |
Honeycomb-like structure, better thermal and water stability, excellent biodegradable properties. It showed 35.67% of mass loss after 15 days |
115 |
0.5–2% |
Concrete |
The durability of the concrete increased when biochar was added to it, at 0.5–2% weight of the cement in the concrete. Compressive strength increased as high as 16%, decreased in water permeability by 40%, caused less thermal damage, 20% higher strength, and 22–25% water tightness |
116 |
10–20% |
Concrete |
Due to the mixing of rice husk ash, compressive strength was enhanced by 7.8% and tensile strength by 50% |
117 and 118 |
0–40% |
Adhesives |
A lignin-doped phenol-formaldehyde adhesive was made for the production of particleboard. Key findings are high viscosity, reduction in moisture uptake, and slight decrease in mechanical properties |
118 |
0–40% |
Ultra-high-performance concrete |
Sugarcane bagasse ash was used here to develop ultra-high-performance concrete, in which autogenous shrinkage was reduced by 30.25% while maintaining the same mechanical properties |
119 |
2.4. Waste and recyclability
To complete the lifecycle of a sustainable product, starting from the source materials to the production phase to the usage, the last criterion is to properly recycle the waste. That is where most of the commercial polymer materials failed. Polymeric materials can be well-designed to have the desired properties as per the application. But recyclability has always remained an issue, according to a survey of around 350 million metric tons of plastic waste generated every year which is estimated to increase to a staggering figure of 1 billion metric tons by 2060.120 Hence, pre-planned waste management and recycling protocols should be there for any such product, especially for the thermoset materials. Our future products should have the scope to be recycled into other value-added products after each life cycle, or they should be biodegradable so that they won't cause any soil or water pollution. This waste and recycling field is a challenging field nowadays. Lots of effort and money have been spent in this field to pursue quality research and find green solutions. As a consequence of it, we got some new fields of research, such as Vitrimerization.121 As research progresses, many such unique processes of recycling polymer waste are being reported every year. Some selected ones are discussed here also (shown in Table 5), just to give a flavour of the diversity of the available solutions.
Table 5 Different methods of recyclability of polymeric materials
Material |
Method of recyclability |
Description |
References |
Poly-trithiocarbamates |
Depolymerization |
Depolymerization of the polymer to its corresponding monomer is based on sulfur chemistry. The method includes solvolysis by alkali (KOH) at a moderate temperature of 40 °C |
122 |
Unsaturated polyester resin |
Self-healing |
Carbon fibers were incorporated into unsaturated polyester resins. A fast and good healable property was observed with 75% retention of the original flexural strength. Also, a max of 83% load value was reported compared to the reference sample |
123 |
Polymer composite |
Biodegradation |
The polymer matrices were made by copolymerization of cyclic esters and bis(1,3-dioxolan-4-one) cross-linker. Fibers were incorporated to generate strength and durability. However, they reported that they can reuse the fibers as the polymer matrices can be degraded to tartaric acid and its oligomers |
124 |
High-performance dynamic material |
Decrosslinking and depolymerization |
A covalent adaptable network was made to fabricate various functional materials. It showed both rubbery and plastic properties. The disulfide-based ring-opening polymerization technique was utilized here with boroxine chemistry and was also involved in the strategy of cross-linking. It shows self-healing properties at elevated temperatures and can be degraded by treating it with ethanol at 40 °C for 10 min. It can also be reprocessed as and when needed, just by evaporating the ethanol |
125 and 126 |
Epoxy vitrimers |
Reprocessing |
A fully biobased material was made from carboxy-terminated peach gum polysaccharide and epoxy-terminated itaconic acid. The β-hydroxy ester bond generated hereby exhibited excellent self-healing and reprocessing ability. Also, after getting healed, 92% of original strength recovery was noticed even after 3 processing cycles |
126 |
Geopolymer |
Biodegradation |
A natural fiber-based biodegradable composite was made for thermal insulation properties. Different natural fibers were tested, and results showed decent insulating properties of all the composites, lying in the range of 0.031–0.047 W m−1 K−1 |
127 |
3. Innovative valorization techniques for converting LCBs to biomaterials
The meaning of “Valorization” is to make something valuable or extremely useful from ordinary things. That is also our motivation behind writing this paper. We not only sum up the application of LCBs but also draw an overview of some modern valorization techniques concisely. These techniques act as a bridge to obtain valuable biomaterials from various sources in nature. It can be wood, straw, husk, bark, crop, root, leaves, or anything. Most of the time, these items are consumed as food, and the rest are burned as combustibles. This has been a major source of carbon emissions, greenhouse gases, and smoke, which is indirectly responsible for several lung diseases. So, it is utterly important to extract this biomass and valorize it to its corresponding components, which can be further shaped into different articles. Broadly, these techniques can be classified into 2 categories: (1) physical, (2) chemical methods. Different research can be classified under these two categories. Although a process cannot be fully physical or chemical, because every process needs some basic chemicals and some specific physical conditions. But based on the key step, this classification can be made.
3.1. Physical valorization methods
The physical extraction methods involve thermal and mechanical valorization approaches. These methods are extremely useful for reducing the particle size, increasing the porosity, and surface area while maintaining the chemical composition. Mechanical methods can be like grinding, milling, shredding, etc. In high-end techniques, steam explosion, ultrasonication, and microwave irradiation are quite famous for generating fine particles from LCBs. These processes are sophisticated but can be used numerous times with minimal usage of reagents. Some examples have been given below.
(a) Llorens et al. discovered an innovative way to valorize LCBs using supercritical-CO2 (Sc-CO2). They reported the convenience of this green method under conditions of 300 bars, 100 °C and 70% moisture content. A minimal effect was observed on the overall chemical composition and β-O-4 lignin structure. This pretreat also improved the solubilization of lignin for Organosolv extraction to 49% to 79%. In this technique, they took 70% aq. solution LSBs in a preheated chamber and maintain a constant flow of CO2 at a 50 g CO2 per min rate for 2 h. Throughout the experiment, pressure and temperature were maintained at 200–500 bar and 100–150 °C, respectively (shown in Fig. 7(a)). The whole set-up runs in a circular way, where extra-pure CO2 (≥99.7%) is pumped into the preheated chamber, which carries the extracted materials and then goes into a separation chamber, where materials get separated and gas is left out of the chamber in gaseous form, later condensed and compressed for reuse.128
 |
| Fig. 7 (a) Schematic diagram of the pretreatment process of wheat straw using Sc-CO2, reproduced from ref. 128 with permission from Elsevier, copyright 2024. (b) Schematic diagram of phosphotungstic acid-assisted delignification process of tobacco stalk, reproduced from ref. 132 with permission from Elsevier, copyright 2023. (c) Process of valorizing LCBs for the production of Eucommia ulmoides rubber via the DES method, reproduced from ref. 133 with permission from Elsevier, copyright 2023. (d) Ultrasonication-assisted DES method for the extraction of cellulose and other valuable polysaccharides from palm frond biomass, reproduced from ref. 135 with permission from Elsevier, copyright 2021. | |
(b) Freitas et al. represented an alternative technique to valorize Almond shells to cellulose other than doing Soxhlet extraction using organic solvents. Here, they employed a method called subcritical extraction. The fundamentals of this method are to heat the Almond shell feedstock at the subcritical temperature (150–320 °C) and pressure (20–150 bar). Under these conditions, several properties of water, like surface tension and dielectric constant, varied significantly, which makes it ideal for the extraction of substances that are even sparingly soluble in water. This condition is also ideal for breaking some specific bonds present in agro-waste. This treatment was further followed by a bleaching step of 8% H2O2 at 160 °C and 180 °C to remove lignin and hemicellulose. After the whole procedure, cellulose content recovered at 71% and 78%, with crystalline characters at 50% and 62% respectively, at 160 °C and 180 °C.129
(c) Aguilar et al. reported another unique process of the steam-explosion method. This process is beneficial, especially for those cases where surface modification is also needed. This process involves heating at high temperatures followed by sudden decompression, which generally affects surface properties and porosity. In detail, the process begins with alkali (NaOH) pre-treatment followed by steam explosion, and after that, oxidation by 30% H2O2 and 3.7 wt% of NaOCl. 70% of biomaterials have been recovered after the steam explosion.130
(d) Singh et al. recently described a technique for valorizing LCBs to silica and other biominerals. They talked about the thermal liquefication technique. With this method, they subjected the LCBs to an autoclave cycle equipped with a mechanical stirrer, pressure controller, thermocouple, and a heater. The parameters were set to 150 °C, 5 bar, and stirring was kept on. After the reaction, the instrument was cooled and depressurized. A liquid phase and some solid substances were recovered from it. Solid was dried at 105 °C for a day, and bio-oil was extracted from the liquid. The yield of bio-oil was found to be around 90%, and solid substances were found to be 98% pure, with mostly silica and some other minerals.131
3.2. Chemical valorization methods
Unlike physical methods, chemical methods are more specific; here, some selective reagents are used to break some targeted bonds. These techniques are very useful for the selective extraction of a particular component based on its substrate-reagent chemistry. Acid hydrolysis is widely used to selectively break the ester linkages between lignin and hemicellulose, for targeted removal of hemicellulose from biomass. Similarly, bleaching reactions using chlorite, alkali, and peroxides are known for lignin removal by destroying the chemical structure. In high-end techniques, deep eutectic solvents (DES) and ionic liquids are familiar for selectively dissolving LCBs components. Such methods are discussed below in detail.
(a) Liu et al. have highlighted a facile method of extraction of pure lignin from Tobacco stalks. They have utilized a very common hydrothermal method with the unique use of phosphotungstic acid, which helps in the selective removal of hemicellulose units. The hydrothermal process was carried out at 170 °C for 1 hour, and the pretreatment process with 1% (w/v) phosphotungstic acid was performed for the same time at a comparatively lower temperature of 130 °C. After all of these processes, an alkali treatment was done with 14% NaOH and 0.5% Anthraquinone to extract the lignin through “black liquor” (shown in Fig. 7(b)). This process was strategically selected for the fact that lignin, present in Tobacco stalks, has lots of structural similarity with hardwood lignin, which means they are very depolymerized. So, via this process, they claimed that they were able to recondense through the hydrothermal and pre-treatment process. A large number of phenol groups and high carbon content were detected in extracted lignin, which makes it ideal to be utilized in many bio-based composites.132
(b) Yao et al. utilized the DES method (shown in Fig. 7(c)) for valorizing LCBs for the production of Eucommia ulmoides rubber, a natural rubber comprised of trans-1,4-polyisoprene, which is extremely useful in making various composites. They reported some interesting results with the addition of cellulose and lignin nanoparticles as side products. In this process, they treated their LCBs feedstock with DES (consisting of lactic acid, Zinc Chloride) at 120 °C, 2 hours after the reaction, lignin was extracted from the mixture by a 1
:
1 (v/v) acetone-water mixture thrice. Lignin was precipitated by adding excess water and later recovered by freeze-drying. However, the solid substance obtained after extraction with a 1
:
1 (v/v) acetone-water mixture was subjected to alkali treatment (for neutralization purposes) and subsequent mechanical treatment for recovery of rubber. They highlighted that the process is utterly useful with a yield of 91% and a purity of rubber of more than 99% while maintaining the chemical structure. On the other hand, nano lignin recovered through this process was able to perform superior anti-oxidant properties than the commercial options.133
(c) Rastogi et al. developed another enzymatic-based technique for valorizing LCBs to lignin-free polysaccharides. They have used sugarcane bagasse and corn cob as their feedstock and subjected them to an alkali treatment (with 2% NaOH) for the delignification process, followed by xylanases enzyme treatment, which is extracted in-house using Aspergillus tubingensis strains. In this method, the substrate loading parameter was set to 2% (w/v), 100–500 U g−1 enzyme loading, and incubation conditions were set to 40 °C, 140 rpm, and 72 hours. The yield of saccharification reactions was found to be 81.4%. The result revealed greater saccharification of the hemicellulose fraction than cellulose. The quantity of reduced sugar was determined by the colourimetric method using DNA reagent.134
(d) Ong et al. combined ultrasonication with the DES process (shown in Fig. 7(d)), to valorize palm frond biomass into reducing sugar and its derivatives. The ultrasonication pre-treatment was carried out at 20 kHz, followed by DES with a choline chloride: urea mixture. It was established that with the addition of an ultrasonication method at 60% amplitude and 30-minute duration, delignification significantly improved from 30.92% to 47%. Also, upon enzymatic saccharification, glucose content was found to be 90.12%. Overall, the synergistic effects showed much better results.135
(e) Fawy et al. reported a dual valorization technique to convert LCBs into amorphous silica and activated carbon, which are highly consumed by the construction industry. They employed the pH reduction technique to precipitate silica. On the other hand, thermal treatment with N2 gas purging was used to generate activated carbon. At first, rice husk and straw were pre-treated with an alkaline solution of 50 g L−1 concentration, and then after cooling and filtering, the reaction mixture was neutralized with an acidic solution to make the pH of the solution around 7, resulting in the precipitation of sodium silicate from LCBs, that are further converted to amorphous silica. The pH of the rest of the filtrate was further brought down to near 1–2 range to precipitate components of the biomass; then they were washed, dried, and subjected to the carbonization process in a tube furnace for 8 hours with 800 °C, flow of N2/CO2 gas. For confirmation, both silica and activated carbon were characterized by several analytical tools like XRD, SEM, and FT-IR.136
4. Application of LCBs-based biomaterials in modern construction
In the previous section, we highlighted several modern-age technologies regarding the extraction of biomaterials like cellulose, hemicellulose, lignin, silica, and many other mineral or valuable inorganic compounds. These methods are also tailored to valorize those biomaterials into different shapes, sizes, forms, and textures according to the application field. Now, passing through the motive of our study, comparison of LCBs with conventional materials, and discussing some novel technologies for valorization, we have reached the advanced functional material stage. That means it's time to focus on our actual purpose, application! The way to utilize LCBs-based biomaterials to serve specific applications is to make commercial products. These products are vast in variety. Still, if we need to categorize the most frequently manufactured products from LCBs, two broad categories must be included in that list: (1) structural and (2) non-structural materials. Further, they can be classified into several sub-categories (shown in Fig. 8). The major ones are discussed below thoroughly.
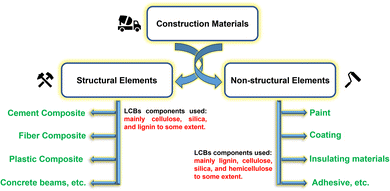 |
| Fig. 8 Classification of structural, non-structural construction material and components of LCBs consumed in the respective fields. | |
4.1. Structural materials
Structural components are the backbone of any construction project. These materials are designed to provide the structure for a building. They are responsible for structural support, carrying loads, maintaining the integrity, stability of the structure, etc. These materials are tested to withstand stresses like compression, tensile shear, etc. Cement composite, fiber composite, and plastic composites are the major ones from this category.
4.1.1. Cement composite. The idea of incorporating LCBs to improve the microstructure and mechanical properties originated a few decades ago. Research has been on this topic since the previous century. In the 80 s, the number of such journals started to grow slowly year by year. The scientific community revealed a basic yet novel idea that can be extrapolated to tackle the sustainability crises in the future. Just like, Mai et al. compared the mechanical properties of cellulose fibers reinforced cement composite, where in one case, bleached cellulose fibers were used in another case, unbleached. They found that bleaching causes an increase in mechanical properties except for the fracture toughness.137 In the next year, Mai et al. published another journal article where they focused on reducing cracks or fractures. They discovered that the rate of crack growth is much lower in wet cellulose fibers, evident from crack growth resistance vs. crack extension curves. These modified composites can show an improved value of both ductility and toughness.138 In the same decade, Thomas et al. highlighted the extraction of cellulose fibers from wastepaper and further valorization to the cement composite. They tried the combination of cellulose fibers with Kaolinitic clay and incorporated it into a cement matrix in some fixed proportion. They were able to achieve a compressive strength of 10.3 MPa and tensile strength of 2.8 MPa.139 As science progressed with time, researchers came up with some more advanced ideas to work on the fundamentals. Bentur et al. did thorough research on the aging the cement composites in natural conditions and with a mimicked accelerated condition in higher CO2 concentration. They found that in accelerated conditions, carbonation of the matrix leads to an increase in flexural strength and E-modulus. However, accelerated aging in normal environmental conditions deteriorates the material quickly, resulting in a decrease in toughness.140 In the 1990s, Bakula et al. investigated the effects of autoclaved cellulose fiber on cement composite, where they reported a 25% increase in bending strength and almost twice the increase in bending toughness.141 In this period, people started looking for improvement in microstructure also, from micro-level reinforcement to micro-crack filling, and the field became more enriched; Klemm et al. demonstrated some modification with cellulose to make methyl hydroxy ethyl cellulose (MHEC), they mixed it with polyvinyl alcohol (PVA) and applied to the cement composite. This strategy was again taken to cease the deterioration of concrete from moisture and low temperatures. The addition of MEHC helped in retaining the water present within the concrete, whereas PVA improved the adhesion property. All together enabled the concrete to withstand adverse weather conditions and enhanced its longevity.142As we moved from the 20th to the 21st century, other components of LCBs were introduced to this field. People started exploring lignin and, most importantly, advanced silica materials to serve their purpose. Bilba et al. utilized lignin extracted from sugarcane bagasse to reinforce the concrete. They mentioned that the incorporation of lignin delayed the setting time of the concrete, and side by side, it also enhanced the hydration temperature. They also stated that a heat treatment at 200 °C enables their cement composite to exhibit similar properties to those we observed in regular Portland cement. Moreover, DSC studies revealed that their cement composite has thermal stability up to 450 °C143 Similar results were also observed in a study conducted by Morton et al., where they used a 0–4 wt% lignin extracted from slash pine. Their key findings were an increase in flexural toughness from 1.69 kJ m−2 to 3.69 kJ m−2, which also shows a similar trend at aging when an accelerated aging test was performed. Apart from that, several other mechanical properties showed an improvement, such as fracture energy, modulus of rupture, lower water absorption capabilities, and excellent dimensional stab.144 In 2008, Wang et al. conveyed a nice study revealing the effects of using fly ash (majorly silica) on mechanical strength, durability, microscopic changes and to investigate its kinetics. Their result highlighted that up to a 25% incorporation of biomass fly ash provides exactly similar compressive strength as that of pure cement and a composite using coal fly ash for up to a year. Microscopic studies revealed a change of smooth surface to rough due to the formation of C–S–H gel when 1-year-old reacted concrete compared with the raw one. Kinetics was found to be indifferent with respect to the consumption rate of Ca for both coal and biomass fly ash. With all of these results, they concluded that biomass fly ash has exactly similar and better performance in some cases compared to coal fly ash, hence potentially being used to make cement composites.145 Similarly, in this time period, many other good journals have been published explaining the effects of fly ash on mechanical properties,146 pozzolanic activities,147,148 hydration kinetics,116 water permeability,118 microstructure,149 durability149,150 and performance151,152 etc.
In recent years, the number of journals discussing LCBs-based cement composites has increased exponentially. Thought processes have upgraded quite a lot, and new sources, methods, and approaches have been explored vigorously. For example, Huang et al. developed a novel Mineralized Cellulose Composite (ML-CCM) through vacuum filling and an in situ mineralization strategy (shown in Fig. 9(a)–(c)). This composite has shown excellent thermal insulation, fire retardancy, and a passive radiative cooling effect due to the presence of ZnO nanoparticles. Moreover, the multilevel scaffold, micropores, and micro-nano minerals present within the ML-CCM enable it to capture CO2 and Environment Tobacco Smoke (ETS) (shown in Fig. 9(d)–(g)).153 Taheri et al. prepared a composite using CNF and ordinary Portland cement (OPC) in various proportions. They highlighted the significance of homogeneity and the degree of entanglement between fibers in defining various mechanical, thermal, and chemical properties. They found that short CNF played a significant role in improving the mechanical properties, whereas long and entangled fibers reduced the density and thermal conductivity of the composite.154 Manjunath et al. published a very interesting study including electrical resistivity and ultrasonic pulse velocity through cement mortar structure. They first prepared Cashew Nutshell Ash (CNSA) through vigorous processing (shown in Fig. 10(a)) and mixed it with cement to prepare the composite. Results show that CNSA-based mortars have impressive compressive strength, water absorption, and porosity. It was also noticed that ultrasonic pulse velocity and electrical resistivity (ER) have increased with the percentage of CNSA in the mortar (shown in Fig. 10(b) and (c)).151 In recent times, some journals have also published on the effects of CNF doping on the 3D-printability of cement composites. Like, Fahim et al. described the application of alkali-activated CNC, based on their viscosity-enhancing property, a reduction of extrusion pressure by 35%, a maximum 20% increment in mechanical properties, and a 25% increase in the degree of hydration was observed in the composite. The internal curing potential of CNC was enhanced even more when they were heated thoroughly. They mentioned that due to this heating, the unreacted particles have been dissolved, generating a denser and more interconnected structure. Hence, fewer microcracks were observed in the case of heat-cured samples than in seal-cured ones. They concluded that due to the viscosity-modifying effect of CNC, overall improved the overall consistency and buildability of the cement mixture were improved without using any synthetic viscosity-modifier, which enables this composite for 3D-printing applications.155 Similar applications were also represented by Kilic et al. They found a 0.3 wt% of CNF can provide desirable rheological and mechanical properties. Various tests were conducted by them for elucidating compressive, tensile, flexural strength, dynamic yield stress, and viscoelastic characteristics using a model of Bingham plastic material (shown in Fig. 10(d)–(g)). Buildability and printability assessment was done using a 3D-concrete printer facilitated with a screw pump mechanism and nozzle of 10 mm diameter (shown in Fig. 10(h)).156
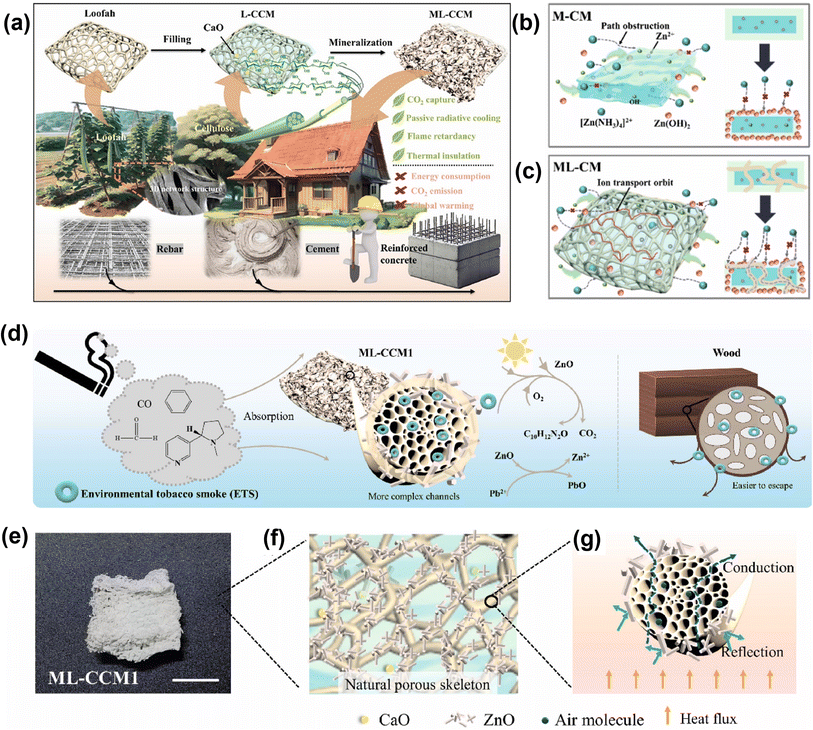 |
| Fig. 9 (a) Fabrication of ML-CCM composites. (b) Mechanism of structural formation of M-CM composite. (c) Mechanism of structural formation of ML-CM composite. (d) Mechanism of absorption and fixation of ETS ML-CCM1. (e) Appearance morphology (scale bar: 2 cm), (f) internal structure, and (g) heat transfer mechanism of ML-CCM1 composite, reproduced from ref. 153 with permission from Elsevier, copyright 2024. | |
 |
| Fig. 10 (a) Procedure for the generation of CNSA. (b) UPV values of blended cement mortar at different CNSA percentages. (c) Electrical resistivity of blended cement mortar at different CNSA percentages, reproduced from ref. 151 with permission from Elsevier, copyright 2023. (d) Flow curves, (e) Bingham model fits, (f) Dynamic yield stress, and (g) viscosity values of the mixes with increasing CNF concentration. (h) Buildability assessment of the mixes with 0.2%, 0.3%, 0.4%, and 0.5% CNF concentration, reproduced from ref. 156 with permission from Elsevier, copyright 2024. | |
4.1.2. Plastic composite. Considering the accumulation of plastic commodities on land as well as ocean surfaces, there is no need to explain the importance of bioplastic nowadays. Plastic materials are not biodegradable, require high energy for burning and are responsible for the greenhouse effect. It is worth mentioning that when 1 kg of plastic is burnt, it generates 2.8 kg of CO2.157 Thus, bio-based or bio-derived plastics are the high demand of our society. To reduce pollution, enhance sustainability and move towards greener alternatives, bioplastics are introduced in the previous century. In the 20th century, Wilde et al. published a journal discussing the key features and prerequisites for a bioplastic to be accepted for daily use applications.158 In the last decade, Brodin et al. published a review of various methods for the production of bioplastics, as well as a detailed discussion on the application of different types of bioplastics and their environmental concerns.159Now, talking about the applications, Orts et al. prepared polymeric gels and films using cellulose microfibrils (2–10%) as a reinforcing agent. Several properties, like Young's modulus, tensile strength, and load-bearing capacity, were estimated using different sources of cellulose fibers. At 10.3 wt% of cotton-derived cellulose fibers 5 times increase in Young's modulus was observed.160 Ganster et al. represented the utility of man-made cellulose filament with high tenacity to reinforce commonly used commercial polymers like polypropylene (PP), poly-(lactic acid) (PLA), polystyrene, etc., for injection molding applications. Compared to glass fiber reinforcement, these cellulose filaments were noticed to improve overall mechanical properties and impact strength due to their low density and anisotropic nature, which provides lower stiffness. Especially, in the case of PLA, a dramatic reduction in brittleness was observed, with excellent biodegradability and mechanical strength.161 Some research groups also reported state-of-the-art works on the fabrication of wood-based bioplastics. Chen et al. fabricated a wood-derived bioplastic where they extracted the latex from Hevea brasiliensis, modified it with some vulcanizing agent, and mixed it with delignified balsa. In situ vulcanization and densification led to the bioplastic (shown in Fig. 11(a)–(c)). It has shown good mechanical properties, biodegradability, water absorption capacity, and many more. Compared to delignified balsa, the fabricated bioplastic's water absorption capacity was almost 6 times lower (shown in Fig. 11(d)). The tensile strength of the bioplastic has also improved thrice after adding both the natural rubber latex (NR) and vulcanized natural rubber latex (VNR) (shown in Fig. 11(e)). Moreover, this bioplastic also offers an excellent in-built O2 barrier property, however, the delignified balsa does not have this O2 barrier property due to the porous structure between the cellulose fibers, but during the processing of the bioplastic, hot-pressing and addition of NR Latex produced a tight packing among the cellulose fibers leading to this O2 barrier property (shown in Fig. 11(f)–(g)), and talking about biodegradability, it has shown an incredible biodegradable behaviour by decomposing by the soil microorganism in just 5 weeks (shown in Fig. 11(h)).162 Similarly, Zhou et al. developed an entirely cellulose-based bioplastic from waste wood residues through a step-by-step process of matrix removal, blending, oxidation, and hot press (shown in Fig. 11(i)). The fabricated Oxidized all-cellulose Microfiber Film (OCMF) has superior wet strength, transparency, extensibility, thermal stability, biodegradability, and hydrophobicity as compared to unprocessed hydrophilic cellulose fiber-based films and plastics (shown in Fig. 11(j)–(k)). Even compared to other material-based bioplastics like chitin and chitosan, the OCMF has better dry and wet strength (shown in Fig. 11(l)), making this a robust one.163 Chen et al. modified ultra-fine fibers with cellulose acetate and polyethylene glycol (PEG/GA) composite via an electrospinning method for thermal storage applications and to improve water resistance. For further upgradation of thermal and mechanical properties, toluene-2,4-diisocyanate was embodied as a cross-linking agent. Due to this modification, a 10 °C increment in decomposition temperature was recorded in differential thermogravimetric data.164 Saralegi et al. inspected a study on shape-memory-based properties of the incorporation of CNC into segmented thermoplastic polyurethanes. In this study, castor oil and corn cob were used as the source of polyurethanes and CNC, respectively, which were covalently bound to each other. DSC and DMA revealed that the melting of soft and hard phases was responsible for shape fixity and shape recovery, respectively. The thermo-mechanical data confirmed nearly 100% shape recovery in the 2nd cycle. The effect of CNC is nothing but the increase of hard phase crystallinity, generating more network points.165 Farias et al. demonstrated a plasma therapy using either air or pure oxygen to remove the amorphous layer of lignin present on the surface of coir fibers to decrease the lignin-to-cellulose ratio, leading to improved mechanical strength. After the plasma treatment, they found a 3 times increase in tensile strength and an almost 20-fold increase in elastic modulus, which is attributed to better fiber-matrix adhesion. They mentioned 80 W and 7.2 minutes as the optimum parameters for oxygen plasma treatment.166
 |
| Fig. 11 (a) Schematic of Hevea brasiliensis and its radial cross-section showing the latex vessel in the bark. (b) Illustrative demonstration of the fabrication of the wood-derived bioplastic through delignification, redistribution, and vulcanization of natural rubber to make it more porous. (c) Schematic representation of the derivation of the wood-derived bioplastic using a rotary cutting method and demonstration of its unique properties, like biodegradability, water stability, and excellent oxygen barrier. (d) Comparison of water adsorption properties of delignified balsa and wood-derived bioplastics infiltrated with 26% NR and 26% VNR, respectively. (e) Tensile wet strength comparison of the soaked D-balsa and wood-derived bioplastic (26 wt% of VNR and 26 wt% of NR). (f) Schematic of the high oxygen permeability of natural balsa due to the porous structure. (g) Schematic of O2 barrier property due to the dense packing of cellulose nanofibers. (h) Images of the biodegradability test of the wood-derived bioplastic and PE under moist soil, reproduced from ref. 162 with permission from Elsevier, copyright 2022. (i) Diagram of the conversion process from waste wood particles into OCMF. (j) Schematic diagram of the formation mechanism and performance of OCMF. (k) Qualitative radar plot comparing UCMF, OCMF, and plastics. (l) Wet and dry tensile strength of OCMF compared with the reported works, such as cellulose-based, chitin-based, and chitosan-based films, reproduced from ref. 163 with permission from ACS, copyright 2024. | |
Similarly, Lei et al. represented a facile method for industry-level processing of dual-crosslinked Carboxymethyl Cellulose Fiber (CMF)-based films with a total preparation time of just 1 hour. They extracted the softwood kraft pulp, bleached it, and treated the slurry with polyamide epichlorohydrin resin and Al2(SO4)3 for cross-linking through electrostatic interactions. Later, the slurry was fabricated into bioplastic film through several steps like dehydration, drying, hot pressing, etc. (shown in Fig. 12(a)). Apart from excellent mechanical properties in both dry and wet states, transparency, flexibility, and printability, these bioplastic films are easily recyclable by disintegrating the cellulose fibers in water to reprocess the slurry (shown in Fig. 11(b)). These bioplastic films have many applications, like fabricating interior décor, packaging, commercial paper, etc. (shown in Fig. 12(c)–(e)).167 On the other hand, Yeo et al. utilized the same lignin with some modification using (3-aminopropyl) triethoxysilane to process a composite with polypropylene-graft-maleic anhydride via the melt-bending method. Due to the homogenous distribution of modified lignin particles, a 2-fold increase in tensile strength and tensile modulus was observed as compared to pristine lignin. This modification also contributed to greater interfacial adhesion forces. Just like cement composites, 3D-printing domains were also explored in the case of plastic composites.168 For example, Koo et al. focused their research on developing a bio-based thermoplastic elastomer for 3D-printing applications and the production of bio-integrated devices. Keeping an eye on sustainability, they fabricated the elastomer with CNC-doped bio-furans (like 2,5-furandicarboxylic acid). Uniformly distributed CNC acted as the nanofiller, providing a superior tensile strength of 67 MPa that is 7 times greater than synthetic thermoplastic urethanes, as reported. With a significant extensibility of 8.6 folds and almost negligible in vivo cytotoxicity, this surely becomes a superior alternative to petroleum-based thermoplastic elastomers.169
 |
| Fig. 12 (a) Schematic of the industrial production process of the CMF/Al2(SO4)3/PAE crosslinked bioplastic film through a roll-to-roll production line. (b) Schematic of the recycling process of the CMF/Al2(SO4)3/PAE bioplastic film. (c) & (d) Digital photos of the CMF/Al2(SO4)3/PAE bioplastic film showing the potential of this film in transparent packaging material. (e) Digital photo of commercial paper-related application of the CMF/Al2(SO4)3/PAE bioplastic film, reproduced from ref. 167 with permission from ACS, copyright 2022. (f) Scheme for the preparation of a UD-NCLF-VE composite using the VARTM process and compression molding, reproduced from ref. 170 with permission from ACS, copyright 2024. (g) Fabrication of CLF-reinforced VDE prepreg preparation using the hand lay-up method, reproduced from ref. 171 with permission from Elsevier, copyright 2024. | |
Apart from bioplastic films, some researches are also focused on the fabrication of semi-synthetic epoxy-composites using cellulose fibers. Like, Adil et al. prepared a Unidirectional-Nano-Cellulose-Long-Filament-Reinforced Vanillin Epoxy green Composites (UD-NCLF-VE) through Vacuum-Assisted Transfer Molding (VARTM) and compression molding method (shown in Fig. 12(f)). The prepared UD-NCLF-VE has shown excellent thermal, water-resistant, and biodegradable properties along with comparable flexural properties to pure VE composite, which makes this composite a more sustainable option to overcome plastic pollution and landfill issues.170 Adil et al. published another good work where they made a similar type of Vanillin Derived Epoxy (VDE) composite, which consists of fire–retardant properties along with the previous applications. Here, they extracted the wood-based CNF and lignin and compounded it with VDE to form the Cellulose Long Filaments (CLF)-reinforced VDE Prepreg using the hand lay-up technique (shown in Fig. 12(g)), which finally shaped into the CLF-reinforced VDE composite through compression molding and some post-cure treatment. The composite has shown a commendable enhancement of 100.9% flexural strength and flexural modulus compared to the neat VDE resin and also secured a V-o rating under the UL-94 test for flame-retardancy.171
Apart from those, there are so many journals published on the various applications of LCBs modifying plastic composites. Some selective research areas are lignin-cellulose containing PVA composites for generating biodegradable plastics,172 active food packaging applications,173 to generate tribological properties,174 epoxy vitrimers,175 transparent UV-protecting films,176 improving piezo-resistance,177 etc.
4.1.3. Fiber composite. Fiber composites, as the name suggests, are materials manufactured using two or more different types of fibers. The fiber components may vary as per the requirement, such as ultra-tough, ultra-light, chemical resistant, moisture resistant, UV-resistant, or with fine microstructural arrangements. As in this review, our main objective is to find out the available materials that can bear mechanical stress in applications related to the construction industry, as well as those that are sustainable and biodegradable. So, here we have mainly discussed those fibers which are purely natural or semi-synthetic. In this regard, Mohanty et al. published a comprehensive review comparing bio-based fibers with glass fibers. It was mentioned that several fibers, especially the hemp and flax fibers, have greater E-modulus and specific modulus than glass fibers. Moreover, the advantages of matrix modification and novel fabrication methods with low-energy requirements make the fibers suitable for numerous applications.178 Lacoste et al. investigated the effect of alginate-based adhesives on biofibers. They compared a bunch of aldehyde-based synthetic cross-linkers with alginate-based binders. They reported of development of semi-rigid fiber composites with flexural strength around 0.2–0.54 MPa and compressive strength around 0.4–1.41 MPa, along with a thermal conductivity value of 0.08 W m−1 K−1, which stands for the thermal insulation application in green buildings.179 Ramlee et al. developed another robust natural fiber composite using sugarcane bagasse (SCB) and oil palm empty fruit bunch (OPEFB) fibers. They tested several properties like tensile strength, void percentage, swelling behavior, and water resistance capacity. They found that the composite made of 70% OPEFB and 30% SCB showed better UTM results with 5.56 MPa of tensile strength and 661 MPa of tensile modulus. Whereas a composite made with 30% OPEFB and 70% SCB performed better in water adsorption and swelling experiments. Overall, these natural fibers are suitable for green insulation applications, as described in this article.180In search of some other applications of fiber composites, we found a recent journal of Charai et al. talking about upscaling hemp fibers for green plaster-based construction items. They manufactured plasterboards using Moroccan hemp fibers with a wt% ranging from 0–6%. On comparing the 6% sample with control plasters (without fibers), it was observed that the density has lowered by 24.5%, thermal insulation properties improved by 31.3%, whereas heat transfer reduced by 8.5%. It was also mentioned that the 2% sample stands out to be the best in terms of thermal heat capacity. In conclusion, these biofiber-based plasterboards can be very useful as a green building material, having low weight, low energy demand, and the least environmental impact.181 Yu et al. developed another robust and durable semi-synthetic composite using glass fibers and bamboo scrimbers with various thicknesses. They found an enhancement in every mechanical feature: compressive strength increased by 7%, shear strength improved by 25%, modulus of rupture enhanced by 18%, and modulus of elasticity increased by 22%. Moreover, aging test results prove excellent dimensional stability, and impressive fire–resistance properties were also recorded by the infrared thermal imaging method for these composites, especially the thicker ones. Fire limitation test results also support the IR imaging data, where the limitation duration was found to be increased by 650% and the mass loss rate reduced by 400%.182 Liu et al. prepared some biomass bricks using corn stalk (15%) and Ca(OH)2 (85%) with brown sugar (0.85%) doping. In comparison with the control specimen, these brown sugar bricks showed a 51.03% increase in compressive strength, 40.91% enhancement in tensile strength, and 64.24% improvement in flexural strength. The efficacy of brown sugar was attributed to its ability to disperse the CO2 within the bricks, ultimately resulting in a slow carbonation rate. Due to this, pore-clogging is delayed around the surface, leading to enhanced mechanical properties of the brick, which makes them the ideal candidate for adhesives and processing of building materials.183 Qureshi et al. reviewed a study on the application of Fiber Reinforced Polymer (FRP) (shown in Fig. 13(a)) in modern-day civil engineering. These FRPs are used to provide additional mechanical strength to the concrete slab, leading to an entire hybrid building structure (shown in Fig. 13(b)).184 On the other hand, Hasan et al. conducted a mini-review on bamboo fiber-reinforced polymer composites, where they represented a wide category of applications of bamboo-based FRPs in buildings and daily households (shown in Fig. 13(c)).185
 |
| Fig. 13 (a) Various kinds of FRP, (b) five-storey hybrid building made using FRP (Switzerland), reproduced from ref. 184 with permission from MDPI, copyright 2022. (c) Utilization of Bamboo fiber-reinforced composites in sustainable furniture, reproduced from ref. 186 with permission from Elsevier, copyright 2012. | |
4.2. Non-structural materials
Non-structural materials are not directly involved in load-bearing jobs. They are responsible for surface-finishing jobs like coating, insulation, moisture resistance, fire retardancy, etc. So far, we have discussed the modification of structural components by LCBs, which is the first step toward constructing a green building. However, these modifications are only limited to constructing a building; to make this building a home, workplace, or institute, several internal advancements are highly required. For example, a building material that is performing excellently in ambient conditions might not exhibit the same performance in some specific geographical areas with extremely cold, hot, or humid weather, so there we need proper thermal or moisture insulation. On the other hand, if we are constructing some building in an area where sound pollution is a major issue, like beside some airports, railway stations, auditoriums, stadiums, or even a construction site itself, so there we need some pretty good arrangements of acoustic insulation for living with sound health. Similarly, to protect building material from corrosion, deterioration, and other chemical factors, we need proper water-resistant coatings, also to ensure stable joining between the structural components, it requires strong adhesives. Hence, a growing market for insulation products is observed all around the globe. According to a survey conveyed in 2022, the global insulation market was estimated at around $67 billion, out of which a staggering $29.75 billion, which is projected to expand to a massive economy of $110.6 billion and $48.69 billion respectively, by 2032, with a growth rate of 5.2% between 2022-2032.187 Here, we have discussed some major categories of non-structural construction materials.
4.2.1. Thermal insulation. The concept of thermal insulation in residential buildings did not originate in recent times. From the ancient period, human civilization has used straws, big leaves, and even wood stems for this purpose. We can still see these types of huts and cottages in rural areas, especially in the continents of Asia and Africa. At present, besides different forms of forest materials, the extracted forms of LCBs are being used as thermal insulating substances.188,189 Particularly, for thermal insulation purposes, the use of cellulose and silica has been observed the most; apart from that, journals were also available on hemicellulose and lignin. Now, let's do some background study; the first question arises: how does heat conduction occur in different states of matter? Well, it is commonly known that in solids, the heat is conducted through the material due to the combined effect of lattice vibrations and energy transport via electrons. Whereas liquid and gas heat conduction occur due to collisions between different molecules and diffusion from one place to another.190 So, to manufacture some products with specific shapes and sizes, we have to think about the solid state of matter. Now, as lattice vibrations are mostly responsible for heat conduction in solids, we have to keep the density of our solid insulating material as low as possible and porosity as high as possible; these are the primary requirements for a material to use as thermal insulation in buildings. So, researchers have developed ultra-lightweight and highly porous materials like aerogels, foams, etc.191 Bhardwaj et al. described the inner mechanism of heat conditioning through the air medium present with a porous structure in aerogel. It was described that if we can reduce the pore size of the aerogels to less than the mean free path of air (70 nm), then we can reduce the heat conduction that occurs due to successive collisions. Hence, this way, we can decrease the thermal conductivity even less than that of air (∼25 mW m−1 K−1).192 To improve the quality of these insulating products, many research groups attempted different methods, for example, Biswas et al. tried with nano-PCM (Phase change material) incorporated wallboard for thermal insulation to reduce the energy consumption. In that paper, they fabricated an innovative PCM using graphite nanosheets. They not only show good conductivity but also distribute heat energy pretty well; due to the interconnected structure, they overall have excellent thermal storage capacity. They tested this modified wallboard with regular gypsum wallboard in extreme conditions throughout the year. Both heat gain and heat loss data reflected lower numerical values for PCM-modified wallboards, proving their capacity to provide better insulation.193 Similar use of PCM was also discussed in research done by Lee et al. They incorporated PCM into building walls, and the result proves a reduction in average heat flux daily is 25.4% for individual walls in four directions (e.g., north, south, east, west). A 20.1% reduction in the hourly average of heat flux was noticed in the sum of all walls.194 Another great piece of work has been published by Wicklein et al. They have prepared some anisotropic foam consisting of Graphene oxide (GO), CNF, and sepiolite nanorods, which performed way better than traditional polymeric insulating materials. It gave an outstanding insulation capacity with only 15 mW m−1 K−1 radial thermal conductivity. Brilliant mechanical properties with axial specific Young’ modulus of 77 kN m kg−1 and impressive fire retardancy with limiting oxygen index (LOI) of 34, which means a 60% higher concentration of oxygen than O2 present in the air (21%), will be required to burn the material. Concisely, the performance of these foams, made from sustainable sources, is much better than usual halogenated flame-retardant materials, and due to their anisotropic properties, like greater mechanical strength in the axial direction and lower thermal conductivity in the radial direction, enables them for versatile applications.195 As the amount of quality research published on this particular thermal insulation topic is huge, we have shortlisted some insulating materials and discussed their thermal conductivity and other relative properties (shown in Table 6).
Table 6 Comparison between different bio-based insulating materials based on their thermal conductivity and other related features
Type of material |
Components present |
Thermal conductivity (mW m−1 K−1) |
Valuable features |
References |
Aerogel |
Cellulose, Mg(OH)2 |
56–81 |
Flame retardant |
197 |
Aerogel |
Cellulose |
25.5 |
Low density, high strength |
198 |
High porosity wood |
Cellulose |
38 |
Lightweight, noise reduction |
199 |
Bamboo particle boards |
Lignin, glue |
101–201 |
Hygrothermal properties |
200 |
Aerogel |
Silica, lignin, ethylene glycol polymer |
40 |
Fire resistance, superhydrophobic performance |
196 |
Aerogel |
Silica |
19–23 |
Acoustic insulation |
201 |
Aerogel |
Konjac glucomannan, silica |
21 |
Ultralight, high mechanical strength, hydrophobic |
202 |
Aerogel |
Cellulose nanowhisker |
45 |
Flexible, flame retardant, high mechanical strength |
203 |
Aerogel |
Cellulose, PVA |
31–42 |
Ultralow density, high porosity, superhydrophobic |
204 |
Aerogel |
Cellulose, graphene confined-zirconium phosphate nanosheets |
18 |
High mechanical strength, fire retardancy |
205 |
Aerogel |
Bacterial cellulose |
13 |
Flexible |
206 |
Foam |
Wood fiber, phytic acid, polyethyleneimine |
33.6–40 |
Mechanically tough, fire-retardant, self-extinguishing property |
207 |
Apart from the above research discussed in Table 6, a few other recent works show some promising results with a commendable presentation. For example, Ou et al. presented a noteworthy work on lignin-silica-based aerogel with a bunch of desired properties like thermal insulation, fire-retardancy, robust structure, superhydrophobicity, durability, etc.
Here, they fabricated a silica-mineralized lignin nanocomposite aerogel (LigSi) having a flexible multilevel micro/nanostructure, and the fabrication method is based on an eye-catching water-induced self-assembly and in situ mineralization technique (shown in Fig. 14(a)). The composite aerogel has some extraordinary mechanical strength, which can comfortably take a load of a person weighing 65 kg (shown in Fig. 14(b) and (c)). The optimized LigSi has shown an ultrahigh stiffness (a specific modulus of ∼376.3 kN m kg−1), humidity–resistant properties, intrinsic superhydrophobic performance (158° WCA), etc. Prepared aerogel composite had some exceptional NIR reflectance properties originating from the multi-scaled morphological structure and hybrid composition of silica-lignin of the composite (shown in Fig. 14(d)), resulting in very low NIR absorption (∼9%), which upscaled the thermal insulation property. Now talking about thermal insulation property, the result revealed that the composite has a low thermal conductivity of ∼0.04 W m−1 K−1. To ensure comfortable living, they made a model building where they used their composite as an insulating material; the result was found very satisfactory as recorded in the thermal IR camera (shown in Fig. 14(e) and (f)). To correlate the lower NIR absorbance and thermal insulation property, a photochemical conversion test was also done and recorded through a thermal IR camera, which concludes the excellence of their scheme (shown in Fig. 14(g) and (h)).196 Boquera et al. developed a novel plaster using gypsum and lignin. They evaluated their thermal, acoustic, and mechanical properties. They mentioned that the plaster composite has similar thermal insulation properties as compared to the pure-lignin-based test. However, acoustic performance was reduced with an increase in lignin content, and mechanical properties were found to be better at 50–70% lignin content.208 Sun et al. prepared another lignocellulose-based aerogel with multiple exciting properties like thermal insulation, durability, mechanical stability, and fire retardancy. For their synthesis purpose, they have used a recyclable DES, along with incorporating tourmaline particles and ammonium sulfate to form a stable structure through H-bonding. The overall structure formed is highly porous, ultralight weight, impressive flame retardancy, excellent thermal insulation properties with thermal conductivity of 29.67 mW m−1 K−1 for the TLA-4 sample (the optimized one), and a dramatic enhancement in Negative oxygen ions (NOI) was found to be 74.1%, which signifies its ability to purify the air which is good for our health.209
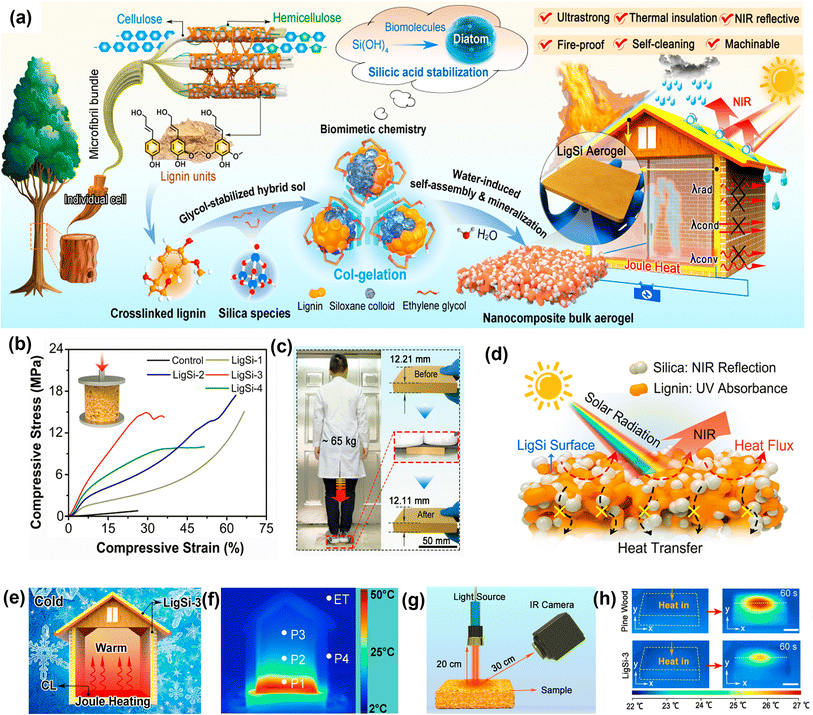 |
| Fig. 14 (a) Schematic illustration of the fabrication strategy of LigSi aerogel composite through the water-induced self-assembly and in situ mineralization technique. (b) Compressive stress–strain curves of typical LigSi materials. (c) An example showing the extraordinary mechanical property of LigSi aerogel, which can bear a 65 kg weight of a human, with minimal deformation. (d) Illustration representing the low photothermal conversion. (e) Illustrations of the energy-efficient model building, whose roof, floor, and external sidings are made of LigSi-3 material. (f) Thermal IR photographs of the model energy-efficient building when power is applied (10 V). (g) Schematic setup for testing the photothermal conversion of LigSi-3 samples as compared to pine wood (reference). (h) Thermal IR photographs of LigSi-3 and the pine wood, illuminated by a NIR light (1350–1600 nm), reproduced from ref. 196 with permission from ACS, copyright 2022. | |
Some research groups also represented the real-life implications of their material for thermal insulation purposes. For example, Baetens et al. have represented a collage of such real-life applications of thermal insulating materials in their review. They enlisted a number of photographs of buildings using translucent aerogel for thermal insulation (shown in Fig. 15(a) and (b)). They also emphasize the effectiveness of aerogel in insulating heat by comparing insulated and non-insulated buildings/floors (shown in Fig. 15(c)).210 Mendes et al. reviewed a more specific topic; they selected silica-based aerogel for thermal insulation. There, they represented different designs or protocols for building wall insulation, such as the External Thermal Insulation Composite System (ETICS) and the Internal Thermal Insulation multi-layer system (ITI) (shown in Fig. 15(d)). They also incorporated some journals talking about the characterization of the thermal performance of aerogel-based radiant barrier systems in residential attics (shown in Fig. 15(e) and (f)). Moreover, the journal also consists of aerogel used as the glazing system (shown in Fig. 15(g) and (h)).215 Abraham et al. have published work on a similar topic, where they developed a highly transparent Silanized-Cellulose Aerogel (SiCellA) for the glazing systems in buildings to boost energy efficiency. They show how a thin coating of their aerogel on the surface of Insulating Glass Units (IGUs) can resist the heat by several folds and provide comfort inside (Shown in Fig. 15(i) and (j)).214
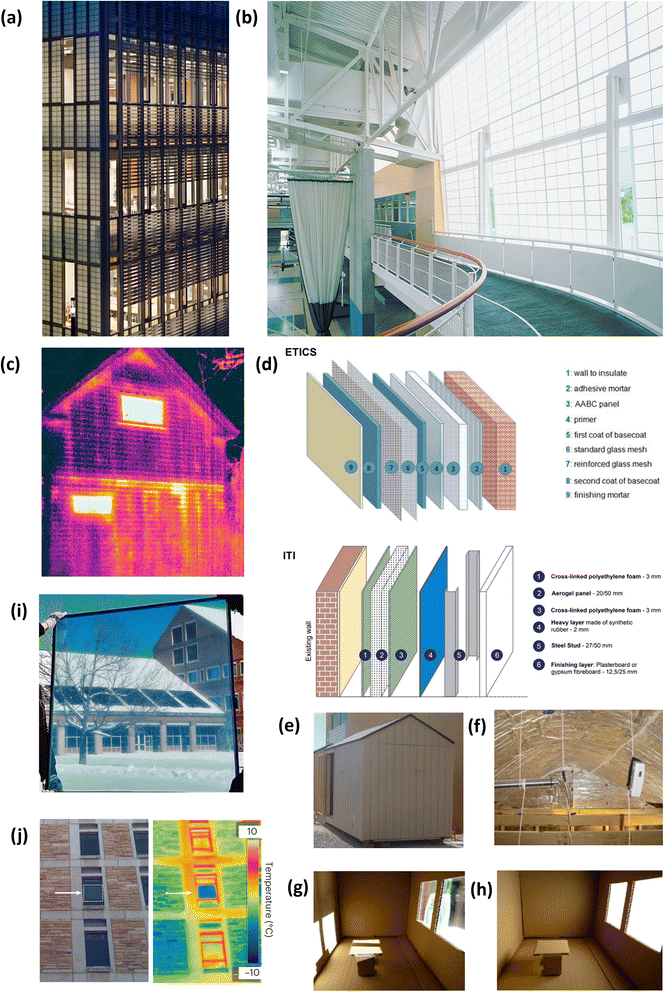 |
| Fig. 15 (a) Real-life application of translucent aerogel used to insulate the curtain wall at the sculpture building of Yale University (USA). (b) Example of thermal insulating performance by translucent aerogel in daylight. (c) A thermographic photograph of the timber wall of a house, where the aerogel insulation was used at the top floor, and the ground floor is kept uninsulated, reproduced from ref. 210 with permission from Elsevier, copyright 2011. (d) Schematic illustration of ETICS and ITI systems, reproduced from ref. 211 with permission from Elsevier, copyright 2019. (e) Test house, (f) attic deck area of that house where the aerogel-based radiant barrier was used, reproduced from ref. 212 with permission from Elsevier, copyright 2018. Representation of (g) double glazing unit and (h) aerogel glazing unit in test house reproduced from ref. 213 with permission from Elsevier, copyright 2016. (i) Real-life images of Double-pane IGU with LoĒ-366 coatings on one glass pane and 3 mm-thick SiCellA films on the surface of the other glass panes. (j) Evaluation of the thermal performance of a single-pane window retrofitted with a 72.1 cm × 71.4 cm SiCellA 1.5 mm-thick film (in a building on the University of Colorado campus), reproduced from ref. 214 with permission from Nature, copyright 2023. | |
4.2.2. Acoustic insulation. Acoustic insulation means protection from sound pollution, indeed, one of the most important topics of discussion. Temperature fluctuation can cause discomfort, but living in an area with noise pollution issues can cause severe mental illness and deafness. So, first, we have to understand how a material can act as an insulator of sound waves. Well, it was well known that in a solid medium, the sound spreads due to the collective vibration of solid atoms and then disperses in all directions. So, the best way to cut off that transmission is to create some structure where the constituent atoms are not heavily connected. Hence, the ideal material might be porous, lightweight, and elastic. The sound insulating properties might be understood from the sound transmission loss, which is nothing but the difference between decibels of incoming and propagating sound. The greater the numerical value, the better the sound-insulating properties will be.216 In the current scenario, we can find many such advanced building materials providing good acoustic insulation properties. For example, Faustino et al. developed a corn con particleboard; the result indicates that the value of impact sound insulation gain (ΔLW in dB) is 30, which is very much comparable with the traditional synthetic alternatives used for the same purpose as glass wool (31 dB) and expanded polystyrene (30 dB). So, we can see they can be potentially used to replace the commercial options.217Yeon et al. upscaled the paper waste to process cellulosic materials for superior sound absorption. They evaluated the acoustic insulation capacity by comparing the Noise reduction coefficient (NRC) of their material with synthetic materials, which is nothing but the ability to absorb sound. NRC = 0 means no absorption, while 1 means total absorption of sound, i.e., complete insulation. They found the NRC to be 0.75 for their insulating material with a thickness of 60 mm and density of 36 kg m−3, whereas that of glass wool and polyester are 0.85 and 60, respectively, which again proves the applicability of lignocellulosic material to replace the synthetic ones.221 Moving one step ahead, Zhu et al. exhibits a lot of modifications within their materials. Firstly, they modified CNC with methyltrimethoxysilane (MTMS) to synthesize Si–CNC and then mixed it up with red mud and a cross-linking agent, Hexamethylene diisocyanate (HDI), to fabricate novel organic-inorganic materials (shown in Fig. 16(a)–(e)) for various purposes, including acoustic absorption. They depicted that the sound absorption coefficient (SAC) (ratio of incident and propagated sound energy) decreased by around 50.2% on increasing the red mud content by 6 times the weight of Si–CNC compared to the sample having no red mud (shown in Fig. 16(f)). Authors highlighted the fact that ultra-low density, high porosity, and presence of inorganic particles in the form of red mud acted as a natural barrier to the thermal and acoustic waves, leading to superior insulating properties (shown in Fig. 15(g)).218 Bikumalla et al. incorporated surfactants to fabricate some biodegradable bagasse foams. Although they used various types of surfactants, they reported the ultimate performance for Sodium dodecyl sulfate, which enhanced the acoustic properties of the foam by 200%. The highest sound absorption coefficient reported by them is 0.85. The novelty of this study is the fabrication method, which did not include the use of any sort of synthetic epoxy or other resins.222 Yu et al. developed another outstanding sound-absorbing material from natural resources like bamboo pulp. They shaped this into a foam with the additional incorporation of halloysite nanotubes, which is an alumina-silicate-based mineral with a hollow structure. They also added chitosan and phytic acid for layer-by-layer arrangement to improve porosity and mechanical properties. This bio-based foam (especially the BPF-4BL variant) displayed excellent sound-absorbing properties with a SAC as high as 0.95 and an impressive self-extinguishing property in the torch-burning experiment.223 Such a high value of SAC was also found in a recent work of Li et al., where they developed a silica-based flexible aerogel via a sol–gel process. Along with many other properties like elasticity, mechanical, and thermal, this aerogel provides an impressive SAC of 0.91 at 2000 Hz and sound transmission loss of 13–21 dB between 500-1600 Hz.224 Wang et al. published a very interesting work on the synthesis of lignin aerogel, where they used cellulose as an adhesion agent. In this work, they have taken 1-butyl-3-methylimidazolium chloride (BMIMCl), a common ionic liquid, for simultaneous dissolution and preparation of lignin-cellulose-based gel, which was further solvent exchanged with water and freeze-dried to form a complete aerogel structure (shown in Fig. 15(h)). All the prepared aerogel samples have shown excellent SAC in the mid-higher frequency range of 500–4000 Hz; the highest SAC value was noted as 0.94, which is just wonderful (shown in Fig. 16(i)).219 Feng et al. also described a similar kind of work of making hybrid aerogels using silica–cellulose; in this paper, additional information was added in terms of a prototype of the SAC measurement set-up (shown in Fig. 16(j)).220 Last but not least, we would like to discuss another study conducted by Buratti et al. on the effect of the granule size of the insulating material on its thermal and acoustic insulation properties. The result showed that the smaller granules (0.01–1.2 mm) are much more effective in enhancing the sound absorption properties than the larger granules (1–4 mm), probably because of more surface area to absorb the sound waves, small interstitial spaces, and multiple scatterings. The values of SAC and transmission loss are 0.95 and 15 dB, respectively.201
 |
| Fig. 16 (a) Isolation of CNC from tunicate through acid hydrolysis. (b) Surface modification of CNC through silylation. (c) Ball-milling process of red mud, along with SEM images and schematics of aggregate formation of red mud particles. (d) Freeze-drying, (e) Cross-linking mechanism of the composite aerogels using HDI. (f) SAC of the series of composite aerogels, and (g) Schematic of the proposed mechanism of thermal and acoustic insulation effect of the composite aerogels containing various RM contents, reproduced from ref. 218 with permission from ACS, copyright 2018. (h) Schematic diagram of the lignin-cellulose gel formation process using BMIMCl. (i) The sound-absorbing performance testing of samples, reproduced from ref. 219 with permission from Nature, copyright 2016. (j) Set-up for quantifying the SAC, reproduced from ref. 220 with permission from Elsevier, copyright 2016. | |
4.2.3. Moisture insulation. This type of insulating material is comparatively less common than thermal and acoustic insulation. However, the requirement of proper insulation for moisture is not insignificant at all. In humid conditions, especially in tropical regions and also other parts of the globe where a proper rainy season exists, the building materials (both inner and outer), electrical appliances, paint, coatings, and their respective properties can be severely harmed by the high moisture content in the air. Again, laboratories where a specific range of moisture content should be maintained for experimental purposes also need innovative products that can control the moisture.So, talking about different methods to generate resistance or insulation against moisture, the first method that comes to mind is superhydrophobicity. Many research groups followed this technique to serve their purpose; let's say Long et al. have developed a superhydrophobic composite aerogel using polybenzoxazine (PBOZ) and CNF (shown in Fig. 17(a)). The material formed thereby was ultra-light and super hydrophobic with a negligible water absorption rate throughout the time. The result confirmed the superhydrophobic nature with the highest contact angle of 162.7° for the PC-24 sample. It was also observed that the Water Contact Angle (WCA) has increased in a very slow manner with the increase in the cellulose content in the composite aerogel from PC-0 to PC-30. Amount of silica present in the aerogel (shown in Fig. 17(b)). However, the presence of silica nanoparticles has a strong influence over the superhydrophobic behavior for the same sample prepared without silica, which has shown a continuous decrease in WCA (shown in Fig. 17(c)), for the same PC-24 sample, the WCA angle was found to be 121.6° for the variant which does not contain any silica (sown in Fig. 17(d)). Also, an almost unchanged water absorption rate was recorded throughout the water absorption test over a long period (shown in Fig. 17(e) and (f)). Similarly, the mass moisture absorption rate also remained invariant at the value of 0.25% over a long period (shown in Fig. 17(g)).225 A similar type of aerogel was also synthesized by the same group, but this time using fully green materials like silica, cellulose, and Aminopropyltriethoxysilane (APTES) as crosslinker (shown in Fig. 17(h)). This aerogel also performed excellently, with a contact angle of 150.8° and a constant moisture absorption rate of 0.44% with respect to saturated mass over a long period (shown in Fig. 17(i) and (j)); they mentioned that the superhydrophobic nature is mainly attributed to the use of superhydrophobic silica nanopowder.226 Sobhana et al. represented a different type of strategy for making a superhydrophobic composite material, where they grafted hydrophobic and eco-friendly stearic acid on cellulose fibers through some inorganic crosslinker like Mg–Al layered double hydroxide to generate a sandwich-like structure (between cellulose and stearic acid), via an in situ coprecipitation method. Their result showed a pretty interesting phenomenon of pH-dependent regulation of superhydrophobicity. At lower pH, the contact angle lies between 134–140°, whereas at high pH, it increases up to 144°. They discussed that at lower pH, the sandwich-like double-layered hydroxide structure faces corrosion. Hence, the grafting of stearic acid on cellulose fibers was reduced to some extent, leading to a decrease in hydrophobicity. On the other hand, at higher pH, an additional –OH group is supplied from the solution, which maintains the uniform coverage of stearic acid on the cellulose surface, leading to superhydrophobic behavior.227 Yoon et al. recently developed a moisture-resistant foam concrete consisting of silica-based nanogel using common silylating agents such as methyltrimethoxysilane (MTMS) and tetraethoxysilane (TEOS). The silica-modified nanogel showed a contact angle of 120.8°, and a 75% lower absorption of water, even after 24 hours, was observed as compared to the conventional sample (shown in Fig. 17(k) and (l)).228
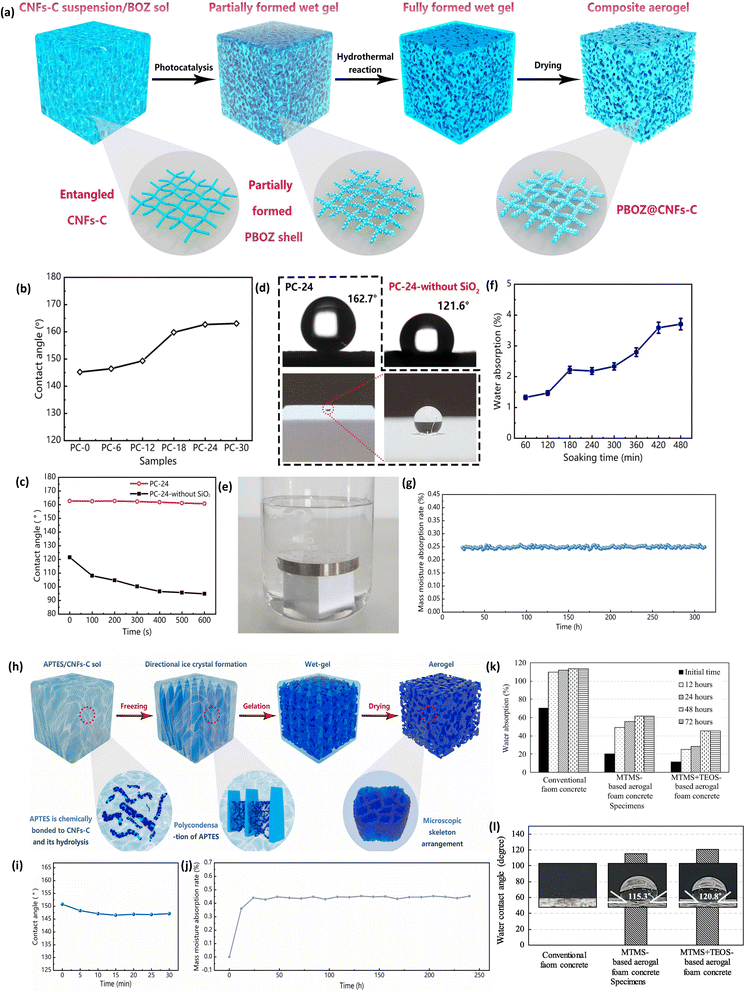 |
| Fig. 17 (a) Schematic illustration of the preparation of the PBOZ@CNFs-C composite aerogel. (b) A static change in WCA from the PC-0 to the PC-30. (c) Evolution of static WCA of the PC-24 sample with and without SiO2. (d) Difference in static WCA of the PC-24 sample with and without SiO2. (e) Water absorption test set-up for the PC-24 sample. (f) Change of the water absorption % against the soaking time of the PC-24 sample. (g) Change of mass moisture absorption rate of the PC-24 sample over time, reproduced from ref. 225 with permission from Elsevier, copyright 2023. (h) Schematic diagram of the preparation method of the Silica–Cellulose composite aerogel. (i) Evolution of WCA within 30 minutes. (j) Change in the mass moisture absorption rate over time, reproduced from ref. 226 with permission from Elsevier, copyright 2023. (k) Comparison of water absorption rate of silanized and non-silanized foam concrete specimens over time. (l) WCA comparison of silanized and non-silanized foam concrete specimens, reproduced from ref. 228 with permission from Elsevier, copyright 2020. | |
4.2.4. Fire and smoke retardants. These kinds of materials are only necessary for exceptional cases like fire hazards or gas leakage. However, that doesn't reduce their significance; these types of materials are very crucial for the safety of lives and other valuable materialistic things, and also very useful to reduce the impact of these types of disasters and to save the building material itself from burning. Now, we have to know the mechanisms by which flame retardants work. Well, talking about the main ones, it can be through some chemical reactions, just like the well-known halogen-based flame retardants,229,230 which generally emits some heavy gas during the combustion process, to cut off the contact between the material surface and air to extinguish the flame. Some chemical reactions might also be endothermic in nature, which reduces the heat and helps to diminish the impact of the fire.231 There are also some phosphorus or other inorganic salt-containing materials which, when ignited, react with oxygen to form non-volatile compounds and thus create a protecting layer on the surface of the material to stop the burning process; this is a good example of retardancy by physical barrier.232,233Now, talking about the advanced results obtained from some recent research, Liu et al. developed a Boron nitride nanosheet (BNNS)-based aerogel through an ice-templating method (shown in Fig. 18(a)). In this aerogel, they used L-glutamine grafted BN nanosheets combined with CNF. They tested the flame resistance nature of this aerogel using a butane flame (1400 °C) in the presence of air for 2 minutes, a result of that black layer of char formed mainly originated from BN and carbonized CNF that protects the rest of the material from combustion, they also highlight the different mechanism of axial and lateral burning (Fig. 18(b)–(e)). Less damage was observed with almost negligible change in weight and no emission of smoke (shown in Fig. 18(f) and (g)). This bio-based fire-retardant material is indeed a great alternative to halogenated materials, which produce toxic gases during combustion.234 Zuo et al. prepared another robust CNF aerogel doped with GO and sodium montmorillonite (MMT) clay to design a novel material that can be used for fire alarms. In this case, the mechanism also includes a physical barrier to the oxygen that GO and MMT produce. He mentioned that a fire alarm made from their material can be triggered within 1.9 seconds of fire contact with the aerogel, which can last up to 137 seconds.236 Missio et al. fabricated a nanocellulose-tannin-based lighter yet rigid foam that can be used as a flame retardant. These foams, due to their inner humidity content, can be able to reduce the up to 30 °C with just a 5 mm thickness.237 Wang et al. found a little different solution in the form of a silica fume-based geopolymer coating, targeted to be used on the plywood to make the fire resistant. They commented on the fire retardancy behavior of the coating based on the Fire Performance Index (FPI) and Fire Growth Index (FGI). In brief, FPI is the ratio of ignition time to heat release rate, so the higher the FPI value, the longer the time required for the sample to be ignited. On the other hand, FGI is the ratio of the peak heat release rate to the time required to reach that peak condition. So, here, higher FGI means a greater tendency towards fire hazards. Thus, it should be as low as possible. In their study, they found that at 350 cps kinematic viscosity of silica fume gave them the best possible result with a shift of FPI from 0.83 to 3.80 s m2 kW−1 and a decrease of FGI from 0.34 to 0.17 kW m−2 s−1, all of which indicate an improved fire retardancy.238
 |
| Fig. 18 (a) Schematic diagram of the preparation of CNFs/BNNSs-g aerogel. (b) Illustrative diagram of the lateral flame combustion. (c) Fire-resistant and thermal insulation mechanism of the aerogel in the lateral direction of combustion. (d) Illustrative diagram of the axial flame combustion. (e) Fire-resistant and thermal insulation mechanism of the aerogel in the axial direction of combustion. (f) Weight change and weight loss rate of the aerogel in the lateral direction. (g) Weight change and weight loss rate of the aerogel in the axial direction, reproduced from ref. 234 with permission from ACS, copyright 2021. (h) Schematic diagram of the synergistic gaseous phase-solid phase of fire-retardant mechanism, reproduced from ref. 235 with permission from Elsevier, copyright 2024. | |
Now, let us explore some smoke suppressors as well, for example, Wu et al. represented an innovative lignin-based material with surfactant modification to form a sandwich-like double-layered structure of hydroxide for smoke suppression and fire retardation. They incorporated this whole system into polypropylene via the melt bending method. They found a decrease in peak heat release rate, total smoke release rate, and total smoke release rate by 62.9%, 25.1%, and 43.3%, respectively, as compared to pure polypropylene samples. They described that during a fire hazard, the sandwich-like bilayer structure collapsed due to heat generated from the fire, which produces bimetallic oxide and amorphous carbon in large amounts. Later, they transform into char and stay on the surface without decomposing, resulting in the breaking of contact between oxygen and the material surface.239 Yu et al. worked on another great piece of work, where they modified the wood sample with carboxymethylated alkali lignin, and to enhance the fire resistance property, they doped phytic acid and melamine-urea-glyoxal resin as a source of phosphorus and nitrogen, respectively. These modified and viscous wood shows a synergistic gas phase and solid phase extinguishing mechanism (Shown in Fig. 18(h)), which stops the combustion very rapidly, resulting in a reduction of heat and smoke. Due to the presence of a dense layer of lignin, it generates a lot of char, which helped in diminishing the flame by a physical barrier; on the other hand, in the gas phase, a dilution effect was observed for oxygen due to the formation of CO2, several N and P containing gases evolved as well as, which inhibits the chain reaction of combustion. Based on all of these, an impressive reduction of 56.8% was observed in heat release, a remarkable decrease of 92.3% was obtained in smoke generation, while LOI also improved significantly from 23.6% (natural wood) to 41.5% (modified wood sample).235
4.2.5. Bio-coatings and adhesives. We have discussed structural components of the buildings like bricks, concrete, floorings, fibers, and different plastic composites. We have also pointed out some useful insulation materials and fire and smoke retardants required to protect the building and the lives residing within. Then what's next? Well, to finish the building and to make it ready to move, all we need to do is paint it and put in some coatings and adhesive as and when required. Hence, in this section, we have discussed some advancements in bio-coatings and adhesives; these types of materials are mostly hydrophobic; thus, unlike other products, here we can see extensive use of lignin rather than cellulose. For example, Wang et al. developed a semi-synthetic coating for the protection of cementitious material; in this coating, they incorporated lignin into the polyurethane matrix. In this research, their fundamental objective was to develop a self-healing coating because it was generally observed that the coating, which is used for the protection of building materials, itself got deformed due to various factors like harsh environmental conditions, UV radiation, drastic temperature differences, and chemical corrosion. So, to tackle that problem and to generate self-healing properties, they mixed aniline and ammonium persulfate with lignin, leading to the preparation of lignin-based coating with remarkable self-healing properties due to dynamic S–S bonds. This adhesive was mixed with polyurethane by the physical blending method until a homogenous solution was obtained and molded to a dumbbell-shaped structure to examine its self-healing properties. The result revealed that the self-healing efficiency of tensile strength was enhanced and crossed the maxima at 86.42% at 60 °C, while the same in the case of elongation first goes upward and then reduces after crossing the maxima at 93.77% at 40 °C Apart from that, the coating also offered an excellent abrasion resistance property and hydrophobicity. After 40 circles, the contact angle just decreased by 10.4%, from its initial value of 139.4° to 124.2° (at the end of the 40th cycle).240 Borisova et al. fabricated a purely biobased coating with a modification of regular kraft lignin (brittle) by spider-silk-inspired protein, which not only enhanced the mechanical property of kraft lignin but also improved its interfacial bonding property. Due to this overall physiochemical advancement.241 Henn et al. focused their research on the fabrication of a purely bio-based adhesive made of lignin. They utilized interfacial catalysis to modify unmodified kraft lignin to synthesise epoxy kraft lignin and later mixed it with biocolloids to obtain lignin nanoparticles, which showed exceptional mechanical as well as adhesive properties. The adhesive, when applied through a hot press at 130–160 °C for just 3–5 minutes, results in a shear strength of 13 MPa and also performs pretty well in wet conditions despite having formaldehyde in it. This adhesive also stood out in thermal stability and even displayed flame–resistant properties. The authors also projected a production cost of around 600 € per ton, thus, there is a high chance of scalability.242 Scarica et al. also utilized lignin with succinic anhydride (through ester bonding) to fabricate a novel thermosetting polyester coating. Due to this crosslinking, the thermal stability of the coating was enhanced remarkably. The hydrophobic character and hardness (around 0.6 GPa) are due to high-lignin content.243Another bio-based formaldehyde-free glue was produced by Siahkamari et al., where they used lignin-glyoxal chemistry (shown in Fig. 19(a)). This bio-based glue also has excellent dry adhesion properties with an adhesion strength of 3.9 MPa in dry conditions with optimized resin formulation. In a comparison of shear strength and wood failure on replacing glyoxal with formaldehyde, a downward trend was followed (shown in Fig. 19(b)). However, as compared to commercial lignin-formaldehyde glues. The present adhesive has lower shear strength and wood failure of around 2.6 MPa and 62%, respectively, which has improved up to 3.9 MPa and 90% on changing the formulation (shown in Fig. 19(c)). It was found that and also showed promising results in wet conditions in water immersion tests (shown in Fig. 19(d)). However, this glue was limited to the hot water boiling test (shown in Fig. 19(e)), but at room temperature, in wet conditions, the adhesion remained intact for more than a week. Overall, this non-toxic, purely bio-based glue can surely be used for interior purposes like furniture, wood joints, etc.244 Kanbargi et al. published a very interesting work; they worked on a renewable lignin-based thermoplastic adhesive that can be potentially used for steel joining (shown in Fig. 19(f)). About their key findings, they reported that the highest adhesive strength was obtained at around 13.1 MPa, at 60% lignin content. They also conducted a computational study to evaluate the adhesive leap shear strength of the dry adhesive through the Cohesive Zone Model (CZM). The results have shown a good resemblance to the theoretical and experimental values (shown in Fig. 19(g)).245 There are plenty of journals published, especially in the last few years, covering the same topic of bio-based adhesives and coatings for wood or similar materials. We might not be able to cover all the novel research, but we at least try to give a flavor to different products, methods, and modifications. Apart from these major applications, LCBs have many other applications related to the construction industry that might not fall under any category. So, here, we also include some of such novel applications under the miscellaneous category (shown in Table 7).
 |
| Fig. 19 (a) Schematic illustration of the synthesis of lignin-glyoxal base adhesive. (b) Change in shear strength and wood failure of lignin-based adhesives with the replacement of glyoxal content with formaldehyde. (c) Comparison of dry adhesion performance between phenol-formaldehyde (PF), optimized lignin-formaldehyde (LF), and lignin-glyoxal (LG) adhesives. (d) Wet strength test and (e) failure of wet strength in boiling water, reproduced from ref. 244 with permission from ACS, copyright 2022. (f) Illustrative diagram of the synthesis of lignin-derived adhesive. (g) Comparison of the leap shear strength test results obtained from experiment and computational analysis through CZM, reproduced from ref. 245 with permission from Elsevier, copyright 2023. | |
Table 7 Miscellaneous applications of LCBs related to green building
Bio-material used |
Application |
References |
Microcrystalline cellulose |
Thermochemical energy storage-based solar panels |
246 |
Lignin nanoparticles |
Electromagnetic shielding and superior fire safety |
247 |
TEMPO-oxidized bacterial cellulose |
Humidity sensor and triple-stimuli-driven actuator |
248 |
Ethyl cellulose-based phase change material |
Thermal energy storage |
249 |
Rice straw-based lignocellulosic fibers |
Insulation boards for the wood-based panel industry |
250 |
Cellulose acetate |
Fluorescence-based ultra-sensitive humidity sensor |
251 |
Bamboo-based cellulose |
Electromagnetic shielding for energy-efficient buildings |
252 |
Cellulose nanofibers |
Antifungal-resistant foams |
253 |
Bacterial cellulose |
Cooling material for building |
254 |
Cellulose |
Highly transparent phosphorescent materials for LED optics application in buildings |
255 |
Lignin, cellulose |
UV-blocking capacity, useful in light management, is the ability to scatter and absorb light |
256 |
Silica |
Anti-reflecting material for high-rise buildings |
257 |
Nanocellulose |
Ceiling tiles |
258 |
Silica micro/nanoparticles |
Weather resistance and daytime radiative cooling |
259 |
Silica microsphere |
Building integrated optoelectronic applications |
260 |
Cellulose nanofibers |
Furniture construction |
261 |
Cellulose |
Strain sensor and triboelectric nanogenerator |
262 |
5. Emerging trends in utilizing simulation and machine learning in the construction industry
Besides experimental works, a handful of computational works have been published yearly. To cross-verify the experimental results or to make assumptions about the probable outcomes, many research groups have come up with some interesting numerical methods, computational models, artificial intelligence, and even machine learning. Here, we have summarized some of such works contributing to the different aspects of the construction industry. Kaplan et al. recently embodied Carboxymethyl cellulose (CMC) and Microcrystalline cellulose (MCC) in their cement composite. Other than the experimental result, they have also represented some valuable theoretical data acquired by the response surface method, where firstly they plotted their experimental data by taking the reference of the theoretical curve (shown in Fig. 20(a)), which helped them to calculate the ratio of variance (R2). Later, they illustrated the surface plots in 2D and 3D space (shown in Fig. 20(b)) to highlight the correlation between increasing cellulose content and various properties like compressive strength, flexural strength, etc. They mentioned in this methodology that the value of R2 tends to 1, more will be the reliability of the data. There, they ended up with R2 values of 0.9031, 0.9299, and 0.9785 in the cases of compressive strength, flexural strength, and ultrasonication pulse velocity result respectively.263 Su et al.264 employed the Holmquist–Johnson–Cook (HJC) model to explain the uniaxial compression failure behaviour of their rice husk-glass powder-doped concrete on a mesoscopic scale. The strength parameters were evaluated using the normalized stress equation (shown in eqn (1)). |
σ* = [A(1 − D) + BP*N][1 + C ln(ε*)] ≤ Smax
| (1) |
where σ* is the normalized equivalent stress, A, B, C, and N are material constants, P* = P/fc, represents normalized pressure, D is the damage parameter, ε* is the dimensionless strain rate, and Smax is the normalized maximum strength.
 |
| Fig. 20 (a) Comparison between experimental and theoretical data for compressive strength of the concrete. (b) The combined effect of cellulose rate and cellulose derivative on the compressive strength of concrete is represented by 3D and 2D response surface plots, reproduced from ref. 263 with permission from Elsevier, copyright 2024. Comparison of damage model data with experimental results for (c) OC and (d) RGC2. Illustration of final failure mode for (e) OC and (f) RGC2, reproduced from ref. 264 with permission from Elsevier, copyright 2024. (g) Illustration of temperature distribution and heat flux of the 2D reconstructed structure, calculated using numerical analysis, reproduced from ref. 265 with permission from Elsevier, copyright 2018. (h) Demonstration of different parts of the SCP unit. (i) Comparison between simulation and experimental result of the application of SCP on a reinforced concrete beam, reproduced from ref. 266 with permission from Elsevier, copyright 2024. | |
They have also calculated the damage parameters using the damage model. Validation of the model was proved by an excellent correlation between the experimental and model values (shown in Fig. 20(c) and (d)). Combining all outputs from the HJC model, the proposed final failure mode of each sample. The OC sample, which does not contain any glass powder and rice husk, was found to show a brittle failure (shown in Fig. 20(e)) whereas, the RGC2 and RGC3 samples, which have both rice husk and glass powder were observed to show plastic deformation at initial stages which later transformed into ductile failure characteristics (shown in Fig. 20(f)).264 She et al. investigated the effect of pore sizes and shapes on the thermal behaviors of cellular concrete using a 2D Finite Element model (FEM). The model also offered the variation of Effective Thermal Conductivity (ETC) with pore orientations and distribution, which is generally very difficult to determine from some experimental methods. As evidence of their research, it was found that ETC was reduced when triangular ones replaced the circular pores; they highlighted the increasing tortuosity as the probable reason. However, other shapes, like square, hexagon, pentagon, etc., were found to have minimal effect on ETC. Results have shown that the shape change in pores has a more pronounced effect on ETC than the pore sizes. On the other hand, ETC was found to be higher along the principal axis direction for the aligned pores. The distribution of temperature and heat flux was also represented in this journal (shown in Fig. 20(g)).265 Computational research was also conducted on the recycling of concrete; recently, Ning et al. conducted a simulation study on the effect of Static Pressure Crushing (SPC) on reinforced concrete beams. They found this method to be a low-carbon technology for recycling concrete beams (shown in Fig. 20(h)). Before the real-life implementation of this method, they conducted this numerical analysis using FEM and traditional erosion algorithm. In this case, the experimental result also supports the simulation data to the fullest (shown in Fig. 20(i)).266
There are also a couple of excellent works published recently on the use of AI tools in predicting compressive strength of concrete. Anwar et al. show the utilization of a regression machine learning model in determining the compressive strength of CNF-modified sustainable concrete composite. They have used numerous machine learning models like Random Forest, Support Vector Regressor, Gradient Boosting Regressor, Bagging Regressor, Decision Tree, etc. All models are applied to an experimental data-based dataset having 695 data points, which are further divided into two categories – training data (70%) and testing data (30%). Seven independent variables and five metrics were employed to measure the ability of the models. As a result, 7 out of 10 models were predicted to assess the effectiveness of CNF addition in enhancing the compressive strength of concrete materials with an R2-value greater than 0.6. Sensitivity analysis data by the Random Forest model was specifically found to be quite impressive in determining that the water and cement proportion are the key factors to the compressive strength of reinforced concrete, while the addition of coarse aggregates affects the compressive strength negatively. As a conclusion, the Random Forest model, along with the Bagging Regressor and Decision Tree model, are found to be the superior ones in this research.267 On a similar topic, Sun et al. examined a study with an identical machine learning approach. In this study, they employed 3 models – K-nearest neighbour, linear regression, and artificial neural network, on 282 data points to evaluate the effect of various parameters on compressive strength of cementitious material. The conclusion was made on R2-value and statistical error analysis. Among all models, the artificial neural network model stood out to be the best one with an R2-value of 0.885. Similar to the previous study, this research also predicts water-to-cement ratio to be the most crucial factor in determining the compressive strength of concrete, followed by curing time, coarse and fine aggregate proportions.268 Similar to Anwar et al., Kashyap et al. also concluded that the random forest model is the best machine learning model to evaluate the compressive strength of concrete. They tested over 54 different concrete mixes and drew their conclusion based on several parameters, like R2-value, mean absolute error, and mean square error. For the random forest model, these values came to 0.95, 1.05 kN mm−2, and 5.25 kN mm−2, respectively. With a little extension to the previous models, they designed this model in such a way that the model can help in providing the highest possible mechanical properties with minimal use of resources to reduce water pollution and land degradation-related issues.269
A little different from the above studies, Bashir et al. developed a new hybrid machine learning model with explainable artificial intelligence methods to determine the optimal water-to-binder ratio to improve the durability, performance, and sustainability of concrete. They did a similar survey with multiple machine learning models, including a random forest model. They used a database having 192 datapoints, each representing different environmental conditions and mixed proportions of the concrete. They concluded that the addition of an AI algorithm to these hybrid machine learning models has a significant impact on optimizing properties over fresh as well as hardened concrete mix.270 Like this research, Liu et al. did an identical machine learning driven study to predict and regulate fluidity and rheological fresh cement-based materials. They investigated a 233-sample database, varied by proportion of cement, water, superplasticizers, silica fume, sand, and hydroxypropyl methylcellulose. They have included Shapley Additive Explanations (SHAP) and Partial Dependence Plot (PDP) analyses, which worked excellently in achieving rapid and accurate control over the workability of fresh cement-based materials.271 More such interesting works focused on different aspects of the construction industry are given below (shown in Table 8).
Table 8 Use of simulation and machine learning in the construction sector
Method used |
Objective |
Key findings |
References |
A new constitutive material model |
Evaluation of damage caused by various dynamic loads on steel fiber reinforced concrete (SFRC) |
In this study, shear deformation and volumetric deformation were taken separately for a more accurate description of strain hardening and softening behaviour. The radial rate enhancement method was implemented to elaborate on the effect of strain rate on the material characteristics of SFRC. |
272 |
Drying shrinkage model |
Evaluation of shrinkage-induced initial damage on the frost resistance of concrete in cold regions with low relative humidity |
It was found that, as compared to samples cured at standard conditions, the samples that had been cured at 40% relative humidity experienced more critical freeze-thaw damage, like higher apparent deterioration, greater mass loss rates, and a more pronounced decay in compressive strength |
273 |
A numerical simulation model based on the Mohr–Coulomb failure criterion and plastic failure height prediction |
A study on the 3D-printability of eco-friendly concrete reinforced by carbon fibers |
This model was found to be a desired tool to predict the feasibility of printing new mixtures, ensuring they meet structural requirements before printing. This study also explained the crucial role of adjusting water-to-binder ratios and superplasticizer dosages to enhance the workability and printability of carbon fiber-reinforced eco-friendly concrete |
274 |
A mathematical model of fresh concrete particle packing |
Simulation study to optimize the concrete mix proportion based on fluidity |
As a result of this study optimal sand-to-aggregate ratio can be determined. Moreover, from this model, we can also predict the quantitative design of a concrete mix proportion, including water consumption, based on the required criteria |
275 |
A three-phase model of concrete based on the boundary element method |
Simulation analysis of chloride-induced corrosion of steel-reinforced concrete |
The model was found to be more accurate than FEM. Results showed that chloride attack was more susceptible to the coarse aggregate content and less affected by the interfacial transition zone (ITZ) diffusion coefficient. It might be due to the higher volume of aggregates in concrete than ITZ. |
276 |
Machine learning model using Monte–Carlo simulation, capacity-spectrum method, and seismic Vulnerability assessment |
To develop a machine learning-based assessment model for the seismic vulnerability of reinforced concrete frame buildings |
The study has successfully developed a machine-learning-based approach to predict the seismic Vulnerability of reinforced concrete buildings for future earthquakes |
277 |
Riedel–Hiermaier–Thoma (RHT) constitutive model |
To design ultra-high-performance concrete |
The study suggests that an enhancement in the strength of longitudinal reinforcement could help to regulate the maximum deflection of the slab in the reinforcement design. Whereas, in the case of transverse reinforcement, low-grade reinforcement should be used, and the ratio of reinforcement should be reduced appropriately. |
278 |
A system combining deep learning and building information modeling |
To detect the underwater cracks of concrete structures |
The result offered the coordinate transformation relation between the real world and the sonar images. Moreover, the crack coordinates were mapped to the BIM model, based on Dynamo's secondary development for Revit. The model was found to be an appropriate one to detect underwater cracks and so the damage in the concrete structure |
279 |
6. A summary of LCA approaches towards sustainable infrastructure
After combining all aspects of the construction sector, this discussion perfectly concludes with an LCA comparison between the traditional buildings and GBs. There are a lot of journals present on this topic. Research groups like Wu et al. talked about the utilization of wood components in the modern construction industry as a sustainable solution to global warming. They surveyed a cradle-to-grave LCA approach for a qualitative as well as quantitative analysis of various environmental footprints in terms of global warming, natural resource depletion, pollution, and habitat destruction from production and disposal methods of transparent wood (shown in Fig. 21(a)). Their result showed that the usage of transparent wood in building structures has reduced the propensity toward global warming by 57%, 57%, and 13% as compared to the transparent polymethyl methacrylate, polycarbonate, and polyethylene terephthalate, respectively. So, the conclusion is that transparent wood can potentially replace petroleum-based items from the building sector, leading to sound planetary health.280 Andersen et al. also worked on the same topic; they conducted an LCA on the incorporation of forest resources in modern buildings to minimize the adverse environmental impact. They reported a highest 81% reduction in greenhouse gas emissions from buildings.281 The same group conducted another survey specifically on the wooden and bio-based buildings regarding their environmental effects. In this study, they considered the biogenic carbon footprints and temporal emissions, which are most of the time ignored in other LCA. So, they combined all the emissions into a single pulse emission according to their methodology. The estimation of time-dependent biogenic CO2 uptake of dry wood (shown in Fig. 21(b)) using the Chapman-Richards growth function. They used both static and dynamic LCA methods for their study of 45 cases of bio-based buildings. It was reported that the environmental impact of these buildings is very sensitive to the method applied, and dynamic LCA has been found to have less impact on the total emission result.282 Zhang et al. compared concrete buildings and Timber-concrete hybrid buildings in terms of seismic performance. For this study, at first, they virtually constructed two such kinds of buildings using ETABS software (shown in Fig. 21(c) and (d)). They also embodied lateral load-resisting systems for both systems to overcome the seismic shear (shown in Fig. 21(e)). As a result, they described that upon substituting the concrete structure with wooden materials, a 30% weight reduction was recorded. Moreover, a substantial decrease in base share was found to be 37% and 27% in the X and Y directions. The more interesting fact was noticed in terms of inter-story drift, which was reduced by up to 50% in hybrid buildings than in traditional concrete buildings. Talking about the environmental aspect, the result of this LCA study suggested a 65% lower emission of greenhouse gases, which has a much lower impact on global warming.283
 |
| Fig. 21 (a) System boundary for processing of transparent wood, reproduced from ref. 280 with permission from Elsevier, copyright 2024. (b) The conceptual illustrative plot of time-distributed biogenic carbon uptake of dry wood against time horizon (TH) using the Chapman-Richards function, reproduced from ref. 282 with permission from Elsevier, copyright 2024. 3D-ETABS model of (c) hybrid and (d) concrete building. (e) Schematic model of the lateral-load bearing system for both types of buildings, reproduced from ref. 283 with permission from MDPI, copyright 2023. | |
Apart from this topic, there are many LCA studies on some other topics related to the construction industry. For example, Katebi et al. studied a cradle-to-gate LCA on the reuse of temporary buildings. They found that reutilization of disassembled parts of the building can reduce the environmental damage and associated costs by 79% and 77%, respectively.284 Miao et al. conducted a more specific LCA study on lignin-based building blocks. These composites were found to have similar strength and structural properties to lightweight concrete. These building blocks are sustainable and have a much lower carbon footprint. The authors described that these materials could be potentially used as the inner applications of buildings, like inner walls, façades, and even roof tiles.285 Last but not least, recently, Gay et al. worked on developing a digital tool for LCA of construction projects. Their results have shown how a digital tool can influence the decisions taken during LCA. This tool can also efficiently measure the global warming impact for a particular construction project in the early stages and can effectively diminish product-based CO2 emissions by up to 40%. Moreover, calculations received from this digital tool were found to be more accurate and quicker than most of the manual methods already reported in the literature.286 Jiang et al. surveyed a very crucial LCA study concerning the current scenario. They evaluated the effect of low-carbon-based mortars on the performance and durability of cementitious material. Chloride-induced deterioration has been a long-term problem with concrete materials. They have used multiple low-carbon-based mortars like calcium sulphoaluminate cement (CSA), CO2-cured calcium sulphoaluminate cement (CSA-C), alkali-activated slag (AAS), and limestone calcined clay cement (LC3). Using these materials, they fabricated a series of concrete materials having identical compressive strength and subjected them to various corrosive tests like mercury intrusion porosimetry, chloride ion diffusion, hydration phase analysis, and water permeability tests. Results show that alkali-activated slag and limestone calcined clay cement have a more pronounced effect on reducing carbon emissions than ordinary portland cement (OPC). Production of both of them causes a much lower carbon emission than OPC. Moreover, AAS and LC3 mortars possess superior resistance to chloride penetration and water permeation, which is why they require less annual maintenance and lower repair time than OPC, which again stands for their superior nature as compared to OPC.287 A similar study was also conducted by Sbahieh et al. on different concrete mixes with partial and total replacement of OPC based on sustainability. The study was done by substituting OPC with different Supplementary Cementitious Materials (SCMs) like fly ash, silica fume, metakaolin, ground granulated blast furnace slag (GGBS), etc. They also applied geopolymer concrete for the same purpose. The result reveals that among SCMs, GGBS has the highest effect in CO2 reduction, which was found around 28.7%, which is higher than other SCMs like silica fume (28.3%), fly ash (17.25%), and metakaolin (15.1%). On the other hand, geopolymer concrete has a more pronounced effect than SCMs, fly ash, and GGBS-based geopolymer registered a 67% and 54% reduction in carbon emission. However, geopolymers have some negative impact on other environmental issues, like fossil depletion, human toxicity, and ozone depletion, due to the emission of sodium silicate and sodium hydroxide. So, in conclusion, SCMs are a better alternative as a substitute for OPC to reduce CO2 emissions; however, geopolymer could be a more sustainable option if the challenges mentioned earlier can be addressed.288
A bunch of similar research was also performed to improve the various properties of cement composites. Khan et al. performed a study to develop sustainable concrete from artificial lightweight aggregate originating from sand-plastic composite. In this paper, they replaced the natural coarse aggregate with artificial lightweight aggregate at different replacement levels. They found an overall 84.5% retention of compressive strength at 30% replacement level, while 100% replacement brought down the compressive strength to 52% of the original. At 100% replacement level, only a 34.7% and 20% reduction was found for tensile and flexural strength, respectively. As a result of the LCA study, they concluded that using these artificial aggregates, we can reduce the potential of global warming up to 54.83%, which is a step towards a sustainable future.289 Benzal et al. assessed the performance of commercial steel fibers, recycled steel fibers with treatment, and without treatment, to examine the mechanical, environmental (cradle-to-gate), and economic impacts. Their findings highlight that recycled fibers are a superior choice to commercial fibers for reinforcement purposes from any aspect. They have shown a 19.2% reduction in shrinkage along with a 37.7% increase in flexural strength. Moreover, from a circular economy and environmental perspective, it diminished CO2 emission and production cost by 23.4% and 14.5% respectively. Overall, it leads to a more eco-friendly and sustainable industry.290 Similar to recycled fiber waste, Scioti et al. published another identical work on the production of construction materials from stone waste. They have varied the amount of sludge, water, cement, and compaction pressure to observe the effect on compressive strength. According to their key findings, the production of artificial stones helps in recycling a huge amount of waste material. The artificial blocks well passed the threshold value of compressive strength required for a building construction, the compressive strength lies within the range of 29.9 to 13.12 N mm−2. The presence of these artificial mortars reduced the brittleness of the construction materials. Optical microscopic study reveals that the slurries made thereby are very cohesive with tiny voids inside. Overall, these materials stand out as an excellent and sustainable replacement for building blocks.291 Another study was performed by Nawaz et al. in utilizing the Municipal waste incinerator bottom ash (MIBA) in fabricating alkali-activated concrete materials; they reviewed their mechanical performance and conducted an LCA study on them. The main focus of this study examine the replaceability of MIBA with AAS or fly ash. To assess this, they used several parameters like compressive strength, SEM analysis, and dry density test, while LCA was evaluated on environmental impact and sustainability. Although mechanical properties did not appear as expected, to keep the compressive strength above a threshold value, only 15% replacement is allowed by MIBA; however, LCA study demonstrates that its contribution towards sustainability by decreasing Terrestrial Acidification Potential (TAP) and Marine Eutrophication Potential (MEP) by 16% at 5% replacement, 45% at 15% replacement, and 60% at 20% replacement level.292
7. Challenges and future pathways
For the shake of advancement, science also required some critical comments that open the doors for many future pathways, so some critical comments were also given below:
(1) In this review, we have scrutinized research covering various sources, methods, products, and applications. During this process, it was realized that the number of publications of fully biobased products is comparatively lower than that for biobased composites. Most of the research products were made in such a way that they still consist of one or more synthetic, harmful, non-eco-friendly components.
(2) Though in terms of insulating capacity, adhesive properties, or flame retardancy, fully bio-based products performed exceptionally well over commercial products due to a perfect overlap of the requirements of the products and characteristics of biomaterials. But in the case of structural products where mechanical strength and robustness are the prime criteria, their fully bio-based products limit themselves. In most cases, they have just been used as an additional reinforcement of synthetic materials with a minor wt% of 0.1–5 (commonly).
(3) In biocomposites, after a certain limit, LCB components have shown a decreasing order of values corresponding to various mechanical and durable properties.
Hence, as a future perseverance, we might explore the following bulletins:
(1) More emphasis on the valorization of agricultural waste rather than cutting living plants, which ultimately leads to several disasters related to deforestation.
(2) Production of fully bio-based products using some other bio-based source as reinforcement should be explored.
(3) Amongst the components of LCBs, mainly the utilization of cellulose and lignin was observed; we should focus more on the total use of biomass, including hemicellulose, bio-based silica, pectin, etc.
(4) Last but not least, we must also keep an eye on the maintenance of these bio-based products because, due to their fully organic nature and moisture present within, they might be decomposed by bacteria and fungi, which severely deteriorate the material, leading to decay in performance.
8. Concluding remarks
In this review, we have tried to portray a current scenario on global research trends on valorization and application of LCBs components in construction materials. While many review articles focus on biofuels, bioenergy, some particular component of LCBs, or some specific category of product materials from them, our study stands out by providing.
A comprehensive overview of modern valorization methods, contribution of LCBs-based products towards the construction of “Green Building”, computational approaches, and comparison of conventional and sustainable sources of construction.
To conclude, here are a few key takeaways:
(a) LCBs are sustainable and renewable, unlike fossil fuels and mined materials. Greater adoption of them in the modern construction industry will help in conserving non-renewable resources for the future.
(b) LCBs-based material requires significantly less energy for extraction, processing, and upscaling, indirectly cutting down fossil fuel consumption.
(c) LCBs are versatile; they can be easily modified to meet diverse structural and functional requirements.
(d) Most importantly, they're biodegradable, offering an eco-friendly alternative to conventional materials like plastics, which pollute ecosystems and harm wildlife.
Abbreviations
Green and sustainable construction materials | GSCMs |
Lignocellulosic biomass | LCBs |
Green building | GB |
Cellulose nano fibers | CNF |
Cellulose nano crystals | CNC |
Micro fibrillated cellulose | MFC |
Polyvinyl alcohol | PVA |
Volatile organic compounds | VOC |
Natural rubber latex | NRL |
Life cycle analysis | LCA |
Supercritical-CO2 | Sc-CO2 |
Deep eutectic solvent | DES |
Methyl hydroxy ethyl cellulose | MHEC |
Polyvinyl alcohol | PVA |
Carboxymethyl cellulose | CMC |
Microcrystalline cellulose | MCC |
Ordinary Portland cement | OPC |
Polypropylene | PP |
Poly-(lactic acid) | PLA |
Phase change material | PCM |
Graphene oxide | GO |
Limiting oxygen index | LOI |
Negative oxygen ions | NOI |
Noise reduction coefficient | NRC |
Methyltrimethoxysilane | MTMS |
Sound absorption coefficient | SAC |
Boron nitride nano sheet | BNNS |
Montmorillonite | MMT |
Fire performance index | FPI |
Fire growth index | FGI |
Holmquist–Johnson–Cook | HJC model |
Effective thermal conductivity | ETC |
Finite element model | FEM |
Static pressure crushing | SPC |
Steel fiber reinforced concrete | SFRC |
Interfacial transition zone | ITZ |
Riedel–Hiermaier–Thoma | RHT constitutive model |
Mineralized cellulose composite | ML-CCM |
Environment tobacco smoke | ETS |
Cashew nutshell ash | CNSA |
Life cycle assessment | LCA |
Oxidized all-cellulose microfiber Film | OCMF |
Carboxymethyl cellulose fiber | CMF |
Unidirectional-nano-cellulose-long-filament-reinforced vanillin epoxy green composites | UD-NCLF-VE |
Vacuum-assisted resin transfer molding | VARTM |
Cellulose long filaments | CLF |
Fiber reinforced polymer | FRP |
External thermal insulation composite system | ETICS |
Internal thermal insulation multi-layer system | ITI |
Silanized-cellulose aerogel | SiCellA |
Insulating glass units | IGUs |
Hexamethylene diisocyanate | HDI |
1-Butyl-3-methylimidazolium chloride | BMIMCl |
Polybenzoxazine | PBOZ |
Water contact angle | WCA |
Aminopropyltriethoxysilane | APTES |
Cohesive zone model | CZM |
Shapley additive explanations | SHAP |
Partial dependence plot | PDP |
Calcium sulphoaluminate cement | CSA |
CO2-cured calcium sulphoaluminate cement | CSA-C |
Alkali-activated slag | AAS |
Limestone calcined clay cement | LC3 |
Ordinary Portland cementOPCSupplementary cementitious materials | OPCSupplementary cementitious materialsSCMs |
Granulated blast furnace slag | GGBS |
Municipal waste incinerator bottom ash | MIBA |
Terrestrial acidification potential | TAP |
Marine eutrophication potential | MEP |
Data availability
The authors confirm that the data supporting the findings of this study are available within the article. It will also be shared on request.
Author contributions
Nilanjan Dey: writing – original draft, investigation, formal analysis, data curation. Shakshi Bhardwaj: writing – review & editing. Pradip K. Maji: writing – review & editing, validation, supervision, resources, project administration, funding acquisition, conceptualization.
Conflicts of interest
The authors declare that they have no known competing financial interests or personal relationships that could have appeared to influence the work reported in this paper.
Acknowledgements
The authors acknowledge the support from the Indian Institute of Technology, Roorkee. This work received funding from the National Buildings Construction Corporation (NBCC), Government of India, India (Grant No. NBC-2293-PPE).
References
- Eras in Human History | Overview, Timeline & Significance – Lesson. https://study.com/academy/lesson/ages-of-human-history.html, accessed 2024-11-30.
- History of Construction and Building Materials – We Build Value. https://www.webuildvalue.com/en/infrastructure-news/building-materials-history.html, accessed 2024-11-30.
- M. H. Ramage, H. Burridge, M. Busse-Wicher, G. Fereday, T. Reynolds, D. U. Shah, G. Wu, L. Yu, P. Fleming, D. Densley-Tingley, J. Allwood, P. Dupree, P. F. Linden and O. Scherman, The Wood from the Trees: The Use of Timber in Construction, Renewable Sustainable Energy Rev., 2017, 1, 333–359, DOI:10.1016/j.rser.2016.09.107.
- E. Oladipo, Global Impact Of Environmental Sustainability On Deforestation, Int. J. Sci. Eng. Res., 2015, 6(9), 103–115 Search PubMed.
- Premium Times - Nigeria leading newspaper for news, investigations. https://www.premiumtimesng.com/, accessed 2024-11-30.
- D. C. Zemp, C. F. Schleussner, H. M. J. Barbosa and A. Rammig, Deforestation Effects on Amazon Forest Resilience, Geophys. Res. Lett., 2017, 44(12), 6182–6190, DOI:10.1002/2017GL072955.
- D. Werth and R. Avissar, The Local and Global Effects of Amazon Deforestation, J. Geophys. Res.:Atmos., 2002, 107(D20), LBA 55, DOI:10.1029/2001jd000717.
- D. V. Spracklen, S. R. Arnold and C. M. Taylor, Observations of Increased Tropical Rainfall Preceded by Air Passage over Forests, Nature, 2012, 489(7415), 282–285, DOI:10.1038/nature11390.
- D. Wuepper, P. Borrelli and R. Finger, Countries and the Global Rate of Soil Erosion, Nat. Sustain., 2020, 3(1), 51–55, DOI:10.1038/s41893-019-0438-4.
- K. Russell, Potential Sediment Supply Fluxes Associated with Greenfield Residential Construction, Anthropocene, 2021, 35, 100300, DOI:10.1016/j.ancene.2021.100300.
- M. Lu and J. Lai, Review on Carbon Emissions of Commercial Buildings, Renewable Sustainable Energy Rev., 2020, 119, 109545, DOI:10.1016/j.rser.2019.109545.
- Y. Zhang, D. Yan, S. Hu and S. Guo, Modelling of Energy Consumption and Carbon Emission from the Building Construction Sector in China, a Process-Based LCA Approach, Energy Policy, 2019, 134, 110949, DOI:10.1016/j.enpol.2019.110949.
- Global CO2 emissions by year 1940-2024, Statista. https://www.statista.com/statistics/276629/global-co2-emissions/, accessed 2024-11-30 Search PubMed.
- Building Materials And The Climate: Constructing A New Future, UNEP - UN Environment Programme. https://www.unep.org/resources/report/building-materials-and-climate-constructing-new-future, accessed 2024-11-30 Search PubMed.
- Y. S. Jeong, S. E. Lee and J. H. Huh, Estimation of CO2 Emission of Apartment Buildings Due to Major Construction Materials in the Republic of Korea, Energy Build., 2012, 49, 437–442, DOI:10.1016/J.ENBUILD.2012.02.041.
- A. Mohajerani, J. Bakaric and T. Jeffrey-Bailey, The Urban Heat Island Effect, Its Causes, and Mitigation, with Reference to the Thermal Properties of Asphalt Concrete, J. Environ. Manage., 2017, 15, 522–538, DOI:10.1016/j.jenvman.2017.03.095.
- L. Yang, F. Qian, D. X. Song and K. J. Zheng, Research on Urban Heat-Island Effect, Procedia Eng., 2016, 169, 11–18, DOI:10.1016/j.proeng.2016.10.002.
- C. G. Scanes, Human Activity and Habitat Loss: Destruction, Fragmentation, and Degradation, Animals and Human Society, 2018, pp. 451–482, DOI:10.1016/B978-0-12-805247-1.00026-5.
- T. Huang, F. Shi, H. Tanikawa, J. Fei and J. Han, Materials Demand and Environmental Impact of Buildings Construction and Demolition in China Based on Dynamic Material Flow Analysis, Resour., Conserv. Recycl., 2013, 72, 91–101, DOI:10.1016/j.resconrec.2012.12.013.
- B. De Meester, J. Dewulf, S. Verbeke, A. Janssens and H. Van Langenhove, Exergetic Life-Cycle Assessment (ELCA) for Resource Consumption Evaluation in the Built Environment, Build. Environ., 2009, 44(1), 11–17, DOI:10.1016/j.buildenv.2008.01.004.
- P. V. Sáez, M. Del Río Merino, C. Porras-Amores and A. S. A. González, Assessing the Accumulation of Construction Waste Generation during Residential Building Construction Works, Resour., Conserv. Recycl., 2014, 93, 67–74, DOI:10.1016/j.resconrec.2014.10.004.
- R. Islam, T. H. Nazifa, A. Yuniarto, A. S. M. Shanawaz Uddin, S. Salmiati and S. Shahid, An Empirical Study of Construction and Demolition Waste Generation and Implication of Recycling, Waste Manage., 2019, 95, 10–21, DOI:10.1016/j.wasman.2019.05.049.
- N. Dahmen, I. Lewandowski, S. Zibek and A. Weidtmann, Integrated Lignocellulosic Value Chains in a Growing Bioeconomy: Status Quo and Perspectives, GCB Bioenergy, 2019, 11(1), 107–117, DOI:10.1111/gcbb.12586.
- A. Devi, S. Bajar, H. Kour, R. Kothari, D. Pant and A. Singh, Lignocellulosic Biomass Valorization for Bioethanol Production: A Circular Bioeconomy Approach, Bioenergy Res., 2022, 15, 1820–1841, DOI:10.1007/s12155-022-10401-9.
- L. Machineni and G. Rao Anupoju, Review on Valorization of Lignocellulosic Biomass for Green Plastics Production: Sustainable and Cleaner Approaches, Sustain. Energy Technol. Assessments, 2022, 53, 102698, DOI:10.1016/j.seta.2022.102698.
- K. Van Meerbeek, B. Muys and M. Hermy, Lignocellulosic Biomass for Bioenergy beyond Intensive Cropland and Forests, Renewable Sustainable Energy Rev., 2019, 102, 139–149, DOI:10.1016/j.rser.2018.12.009.
- S. Sugiarto, R. R. Pong, Y. C. Tan, Y. Leow, T. Sathasivam, Q. Zhu, X. J. Loh and D. Kai, Advances in Sustainable Polymeric Materials from Lignocellulosic Biomass, Mater. Today Chem., 2022, 26, 101022, DOI:10.1016/j.mtchem.2022.101022.
- J. Cai, Y. He, X. Yu, S. W. Banks, Y. Yang, X. Zhang, Y. Yu, R. Liu and A. V. Bridgwater, Review of Physicochemical Properties and Analytical Characterization of Lignocellulosic Biomass, Renewable Sustainable Energy Rev., 2017, 76, 309–322, DOI:10.1016/j.rser.2017.03.072.
- A. K. Akhnoukh and C. Buckhalter, Ultra-High-Performance Concrete: Constituents, Mechanical Properties, Applications and Current Challenges, Case Stud. Constr. Mater., 2021, 15, e00559, DOI:10.1016/j.cscm.2021.e00559.
- A. T. Hoang, S. Nizetic, H. C. Ong, C. T. Chong, A. E. Atabani and V. V. Pham, Acid-Based Lignocellulosic Biomass Biorefinery for Bioenergy Production: Advantages, Application Constraints, and Perspectives, J. Environ. Manage., 2021, 296, 113194, DOI:10.1016/j.jenvman.2021.113194.
- T. Qu, W. Guo, L. Shen, J. Xiao and K. Zhao, Experimental Study of Biomass Pyrolysis Based on Three Major Components: Hemicellulose, Cellulose, and Lignin, Ind. Eng. Chem. Res., 2011, 50(18), 10424–10433, DOI:10.1021/ie1025453.
- X. F. Sun, R. C. Sun, P. Fowler and M. S. Baird, Extraction and Characterization of Original Lignin and Hemicelluloses from Wheat Straw, J. Agric. Food Chem., 2005, 53(4), 860–870, DOI:10.1021/jf040456q.
- M. Kim and D. F. Day, Composition of Sugar Cane, Energy Cane, and Sweet Sorghum Suitable for Ethanol Production at Louisiana Sugar Mills, J. Ind. Microbiol. Biotechnol., 2011, 38(7), 803–807, DOI:10.1007/s10295-010-0812-8.
- X. F. Sun, Z. Jing, P. Fowler, Y. Wu and M. Rajaratnam, Structural Characterization and Isolation of Lignin and Hemicelluloses from Barley Straw, Ind. Crops Prod., 2011, 33(3), 588–598, DOI:10.1016/j.indcrop.2010.12.005.
- A. Ferrer, C. Salas and O. J. Rojas, Physical, Thermal, Chemical and Rheological Characterization of Cellulosic Microfibrils and Microparticles Produced from Soybean Hulls, Ind. Crops Prod., 2016, 84, 337–343, DOI:10.1016/J.INDCROP.2016.02.014.
- B. S. Todkar, O. A. Deorukhkar and S. M. Deshmukh, Extraction
of Silica from Rice Husk, Int. J. Eng. Res. Dev., 2016, 12(3), 69–74 Search PubMed.
- C. G. Hoyos, R. Zuluaga, P. Gañán, T. M. Pique and A. Vazquez, Cellulose Nanofibrils Extracted from Fique Fibers as Bio-Based Cement Additive, J. Clean. Prod., 2019, 235, 1540–1548, DOI:10.1016/j.jclepro.2019.06.292.
- L. Jiao, M. Su, L. Chen, Y. Wang, H. Zhu and H. Dai, Natural Cellulose Nanofibers as Sustainable Enhancers in Construction Cement, PLoS One, 2016, 11(12), e0168422, DOI:10.1371/journal.pone.0168422.
- S. Chung, S. A. Park, S. B. Park, H. Kwak, D. X. Oh, D. S. Hwang, H. Jeon, J. M. Koo and J. Park, Biobased Super Engineering Plastic Nanocomposite of Cellulose Nanofibers and Isosorbide, Polym. Degrad. Stab., 2023, 215, 110445, DOI:10.1016/j.polymdegradstab.2023.110445.
- K. Harada, P. Chu, K. Xu and A. Fujimori, Polypropylene-Based Nanocomposite with Improved Mechanical Properties: Effect of Cellulose Nanofiber and Polyrotaxane with Partial Miscibility, Polym. Compos., 2023, 44(5), 2977–2987, DOI:10.1002/pc.27295.
- N. Mahmood, Z. Yuan, J. Schmidt and C. Xu, Depolymerization of Lignins and Their Applications for the Preparation of Polyols and Rigid Polyurethane Foams: A Review, Renewable Sustainable Energy Rev., 2016, 60, 317–329, DOI:10.1016/j.rser.2016.01.037.
- Y. Park, W. O. S. Doherty and P. J. Halley, Developing Lignin-Based Resin Coatings and Composites, Ind. Crops Prod., 2008, 27(2), 163–167, DOI:10.1016/j.indcrop.2007.07.021.
- J. Ruwoldt, F. H. Blindheim and G. Chinga-Carrasco, Functional Surfaces, Films, and Coatings with Lignin - a Critical Review, RSC Adv., 2023, 13(18), 12529–12553, 10.1039/d2ra08179b.
- M. Mariana, T. Alfatah, H. P. S. Abdul Khalil, E. B. Yahya, N. G. Olaiya, A. Nuryawan, E. M. Mistar, C. K. Abdullah, S. N. Abdulmadjid and H. Ismail, A Current Advancement on the Role of Lignin as Sustainable Reinforcement Material in Biopolymeric Blends, J. Mater. Res. Technol., 2021, 15, 2287–2316, DOI:10.1016/j.jmrt.2021.08.139.
- A. Chatterjee, S. Sen, S. Singh, S. Bhardwaj and P. K. Maji, Corrosion Protection of Mild Steel via Cerium Nitrate Loaded Acrylic-Vinyl Polysilazane Based Hybrid Coatings, Prog. Org. Coat., 2024, 197, 108831, DOI:10.1016/j.porgcoat.2024.108831.
- D. S. Gunarathne, I. A. Udugama, S. Jayawardena, K. V. Gernaey, S. S. Mansouri and M. Narayana, Resource Recovery from Bio-Based Production Processes in Developing Asia, Sustain. Prod. Consum., 2019, 17, 196–214, DOI:10.1016/j.spc.2018.11.008.
- P. Verma, S. Shukla and P. Pal, Potential Application of Nano-Silica in Concrete Pavement: A Bibliographic Analysis and Comprehensive Review, Mater. Today Sustain., 2025, 29, 101079, DOI:10.1016/j.mtsust.2025.101079.
- G. Liao, E. Sun, E. B. G. Kana, H. Huang, I. A. Sanusi, P. Qu, H. Jin, J. Liu and L. Shuai, Renewable Hemicellulose-Based Materials for Value-Added Applications, Carbohydr. Polym., 2024, 341, 122351, DOI:10.1016/j.carbpol.2024.122351.
- F. Foroughi, E. R. Ghomi, F. M. Dehaghi, R. Borayek and S. Ramakrishna, A Review on the Life Cycle Assessment of Cellulose: From Properties to the Potential of Making It a Low Carbon Material, Materials, 2021, 14(4), 1–23, DOI:10.3390/ma14040714.
- Leading pulp for paper producing countries 2022 | Statista, https://www.statista.com/statistics/1333386/pulp-for-paper-production-by-country/, accessed 2024-11-30.
- S. Mazumder and N. Zhang, Cellulose–Hemicellulose–Lignin Interaction in the Secondary Cell Wall of Coconut Endocarp, Biomimetics, 2023, 8(2), 188, DOI:10.3390/biomimetics8020188.
- S. Kumar, D. Kumar, C. Upadhyay, M. Bansal, B. Rathi and P. Singh, Functionalization of Cellulose Nanocrystals with a Potent Antimalarial Compound: Synthesis, Characterization, and Biological Studies, Int. J. Biol. Macromol., 2024, 282, 136660, DOI:10.1016/j.ijbiomac.2024.136660.
- Leading pulp for paper producing countries 2022 | Statista, https://www.statista.com/statistics/1333386/pulp-for-paper-production-by-country/, accessed 2024-11-30.
- P. Gupta, A. Pandey, K. K. Gaikwad, S. Roy and P. K. Maji, The Role of Rheological Premonitory of Hydrogels Based on Cellulose Nanofibers and Polymethylsilsesquioxane on the Physical Properties of Corresponding Aerogels, Polym. Eng. Sci., 2021, 61(4), 1220–1231, DOI:10.1002/pen.25671.
- M. Sathwane, M. Chhajed, C. Verma, K. K. Gaikwad and P. K. Maji, Synergistic Effect of Hybrid Hydroxylated Boron Nitride and Cellulose Nanocrystals for Enhancing the Thermal, Mechanical, and Hydrophobic Properties of Composite Film, Polym. Compos., 2023, 44(1), 492–504, DOI:10.1002/pc.27112.
- S. Singh, S. Bhardwaj, N. Choudhary, R. Patgiri, Y. Teramoto and P. K. Maji, Stimuli-Responsive Chiral Cellulose Nanocrystals Based Self-Assemblies for Security Measures to Prevent Counterfeiting: A Review, ACS Appl. Mater. Interfaces, 2024, 14, 41743–41765, DOI:10.1021/acsami.4c08290.
- N. Lavoine, I. Desloges, A. Dufresne and J. Bras, Microfibrillated Cellulose – Its Barrier Properties and Applications in Cellulosic Materials: A Review, Carbohydr. Polym., 2012, 90(2), 735–764, DOI:10.1016/J.CARBPOL.2012.05.026.
- S. W. M. Supit, T. Nishiwaki, F. U. A. Shaikh, K. Boonserm and S. A. Rahman, Influences of Hybrid Fiber-Reinforcement Using Wollastonite and Cellulose Nanofibers on Strength and Microstructure Characterization of Ultra-High-Performance Mortar, Constr. Build. Mater., 2024, 423, 135802, DOI:10.1016/j.conbuildmat.2024.135802.
- S. Raghunath, M. Hoque and E. J. Foster, On the Roles of Cellulose Nanocrystals in Fiber Cement: Implications for Rheology, Hydration Kinetics, and Mechanical Properties, ACS Sustainable Chem. Eng., 2023, 11(29), 10727–10736, DOI:10.1021/acssuschemeng.3c01392.
- S. Kadea, T. Kittikorn and R. Hedthong, Sustainable Laminate Biocomposite of Wood Pulp/PLA with Modified PVA-MFC Compatibilizer: Weathering Resistance and Biodegradation in Soil, Ind. Crops Prod., 2024, 218, 118913, DOI:10.1016/j.indcrop.2024.118913.
- P. Li, T. Shu, T. Liu, T. Yu, H. Wang, C. Fu and L. Yu, Visually Revealing the Ramie Bast Structure and Its Obstructive Effects on Bio-Degumming, Ind. Crops Prod., 2024, 221, 119301, DOI:10.1016/j.indcrop.2024.119301.
- H. V. Scheller and P. Ulvskov, Hemicelluloses, Annu. Rev. Plant Biol., 2010, 61, 263–289, DOI:10.1146/ANNUREV-ARPLANT-042809-112315/CITE/REFWORKS.
- G. Brunner, Processing of Biomass with Hydrothermal and Supercritical Water, Supercritical Fluid Science and Technology, 2014, vol. 5, pp. 395–509, DOI:10.1016/B978-0-444-59413-6.00008-X.
- L. Li, J. S. Rowbotham, H. Christopher Greenwell and P. W. Dyer, An Introduction to Pyrolysis and Catalytic Pyrolysis: Versatile Techniques for Biomass Conversion, in New and Future Developments in Catalysis: Catalytic Biomass Conversion, Elsevier B.V., 2013, pp 173–208, DOI:10.1016/B978-0-444-53878-9.00009-6.
- W. Yang, X. Zhang, K. Lin, Y. Chen, B. Cheng, P. Pan, S. Niu, L. Huang, J. Li and L. Chen, High-Strength Lignocellulosic Material from Agro-Waste, Ind. Crops Prod., 2024, 220, 119204, DOI:10.1016/j.indcrop.2024.119204.
- S. Alejandro, Y. Lee, T. Tohge, D. Sudre, S. Osorio, J. Park, L. Bovet, Y. Lee, N. Geldner, A. R. Fernie and E. Martinoia, AtABCG29 Is a Monolignol Transporter Involved in Lignin Biosynthesis, Curr. Biol., 2012, 22(13), 1207–1212, DOI:10.1016/j.cub.2012.04.064.
- S. W. A. Shah, Q. Xu, M. W. Ullah, Zahoor, S. Sethupathy, G. M. Morales, J. Sun and D. Zhu, Lignin-Based Additive Materials: A Review of Current Status, Challenges, and Future Perspectives, Addit. Manuf., 2023, 74, 103711, DOI:10.1016/j.addma.2023.103711.
- S. Wang, W. Liu, D. Yang and X. Qiu, Highly Resilient Lignin-Containing Polyurethane Foam, Ind. Eng. Chem. Res., 2019, 58(1), 496–504, DOI:10.1021/acs.iecr.8b05072.
- A. J. Ragauskas, G. T. Beckham, M. J. Biddy, R. Chandra, F. Chen, M. F. Davis, B. H. Davison, R. A. Dixon, P. Gilna, M. Keller, P. Langan, A. K. Naskar, J. N. Saddler, T. J. Tschaplinski, G. A. Tuskan and C. E. Wyman, Lignin Valorization: Improving Lignin Processing in the Biorefinery, Science, 2014, 344(6185), 1246843, DOI:10.1126/science.1246843.
- N. Nair, M. I. Haque, S. Siddique, R. I. Khan, W. Ashraf, K. Gourlay and S. Shah, Role of Delignified and Lignin-Containing Cellulose Nanofibers in Enhancing Durability Performances of Portland Cement Composites, Cem. Concr. Compos., 2024, 145, 105316, DOI:10.1016/j.cemconcomp.2023.105316.
- R. Choowang, M. Luengchavanon and J. Raknarong, Employing a Mixture of Fine-Particle PKS, Glycerol, and Citric Acid as an Eco-Friendly Binder for Plywood Production from Rubberwood (Hevea Brasiliensis) Veneer, J. Wood Sci., 2024, 70(31), 1–11, DOI:10.1186/s10086-024-02145-1.
- S. Y. Long, Y. Qin, J. L. Liu, X. Q. Xian, L. Q. Zhou, W. Da Lv, P. D. Tang, Q. Y. Wang and Q. S. Du, Study on the Lignin-Derived Sp2–Sp3 Hybrid Hard Carbon Materials and the Feasibility for Industrial Production, Sci. Rep., 2024, 14(1), 5091, DOI:10.1038/s41598-024-54190-x.
- S. Nanda, P. Mohanty, K. K. Pant, S. Naik, J. A. Kozinski and A. K. Dalai, Characterization of North American Lignocellulosic Biomass and Biochars in Terms of Their Candidacy for Alternate Renewable Fuels, Bioenergy Res., 2013, 6(2), 663–677, DOI:10.1007/s12155-012-9281-4.
- S. V. Vassilev, D. Baxter, L. K. Andersen, C. G. Vassileva and T. J. Morgan, An Overview of the Organic and Inorganic Phase Composition of Biomass, Fuel, 2012, 1–33, DOI:10.1016/j.fuel.2011.09.030.
- D. Barana, A. Salanti, M. Orlandi, D. S. Ali and L. Zoia, Biorefinery Process for the Simultaneous Recovery of Lignin, Hemicelluloses, Cellulose Nanocrystals and Silica from Rice Husk and Arundo Donax, Ind. Crops Prod., 2016, 86, 31–39, DOI:10.1016/j.indcrop.2016.03.029.
- A. Pettersson, M. Zevenhoven, B. M. Steenari and L. E. Åmand, Application of Chemical Fractionation Methods for Characterisation of Biofuels, Waste Derived Fuels and CFB Co-Combustion Fly Ashes, Fuel, 2008, 87(15–16), 3183–3193, DOI:10.1016/j.fuel.2008.05.030.
- C. Raynaud, Electrical Characterization Review Silica films on Silicon Carbide: A Review of Electrical Properties and Device Applications, J. Non-Cryst. Solids, 2001, 280, 1–31, DOI:10.1016/S0022-3093(00)00350-1.
- D. S. Vijayan, P. Devarajan and A. Sivasuriyan, A Review on Eminent Application and Performance of Nano Based Silica and Silica Fume in the Cement Concrete, Sustain. Energy Technol. Assessments, 2023, 56, 103105, DOI:10.1016/j.seta.2023.103105.
- R. Casasola, J. M. Rincón and M. Romero, Glass-Ceramic Glazes for Ceramic Tiles: A Review, J. Mater. Sci., 2012, 47, 553–582, DOI:10.1007/s10853-011-5981-y.
- K. Pobłocki, M. Pawlak, J. Drzeżdżon, B. Gawdzik and D. Jacewicz, Clean Production of Geopolymers as an Opportunity for Sustainable Development of the Construction Industry, Sci. Total Environ., 2024, 928, 172579, DOI:10.1016/j.scitotenv.2024.172579.
- H. Kuru Mutlu, High-Strength Tile Production from Yellow Clay with High Silicon Dioxide Content and Its Reflection in Ultraviolet and Visible Regions, Case Stud. Constr. Mater., 2024, 21, e03534, DOI:10.1016/j.cscm.2024.e03534.
- M. Yadav and M. Agarwal, Biobased Building Materials for Sustainable Future: An Overview, Mater. Today: Proc., 2021, 43, 2895–2902, DOI:10.1016/j.matpr.2021.01.165.
- N. Mohan, S. P. Dash, N. Mary Boby and D. Shetty, Study of Bamboo as a Building Material – Construction & Preservation Techniques and Its Sustainability, Mater. Today Proc.c, 2022, 60, 100–114, DOI:10.1016/j.matpr.2021.12.263.
- S. Knapic, V. Oliveira, J. S. Machado and H. Pereira, Cork as a Building Material: A Review, Eur. J. Wood Wood Prod., 2016, 74(6), 775–791, DOI:10.1007/s00107-016-1076-4.
- L. Gil, New Cork-Based Materials and Applications, Materials, 2015, 8(2), 625–637, DOI:10.3390/ma8020625.
- H. Lopes, S. P. Silva, J. P. Carvalho and J. Machado, The Influence of Cork and Manufacturing Parameters on the Properties of Cork–Rubber Composites for Vibration Isolation Applications, Sustainability, 2021, 13(20), 11240, DOI:10.3390/su132011240.
- A. M. A. Pintor, C. I. A. Ferreira, J. C. Pereira, P. Correia, S. P. Silva, V. J. P. Vilar, C. M. S. Botelho and R. A. R. Boaventura, Use of Cork Powder and Granules for the Adsorption of Pollutants: A Review, Water Res., 2012, 46(10), 3152–3166, DOI:10.1016/j.watres.2012.03.048.
- P. R. Oliveira, M. May, T. H. Panzera and S. Hiermaier, Bio-Based/Green Sandwich Structures: A Review, Thin-Walled Struct., 2022, 177, 109426, DOI:10.1016/j.tws.2022.109426.
- L. C. Gil, Sustainability and New Applications, Front. Mater., 2015, 1(38), 1–3, DOI:10.3389/fmats.2014.00038.
- T. Dickson and S. Pavía, Energy Performance, Environmental Impact and Cost of a Range of Insulation Materials, Renewable Sustainable Energy Rev., 2021, 140, 110752, DOI:10.1016/j.rser.2021.110752.
- D. K. Panesar and B. Shindman, The Mechanical, Transport and Thermal Properties of Mortar and Concrete Containing Waste Cork, Cem. Concr. Compos., 2012, 34(9), 982–992, DOI:10.1016/j.cemconcomp.2012.06.003.
- P. S. Song and S. Hwang, Mechanical Properties of High-Strength Steel Fiber-Reinforced Concrete, Constr. Build. Mater., 2004, 18(9), 669–673, DOI:10.1016/j.conbuildmat.2004.04.027.
- M. Yadav and A. Saini, Opportunities & Challenges of Hempcrete as a Building Material for Construction: An Overview, Mater. Today: Proc., 2022, 65, 2021–2028, DOI:10.1016/j.matpr.2022.05.576.
- S. D. Kore and J. S. Sudarsan, Hemp Concrete: A Sustainable Green Material for Conventional Concrete, J. Build. Mater. Sci., 2021, 3(2), 1–7, DOI:10.30564/jbms.v3i2.3189.
- T. Jami, S. R. Karade and L. P. Singh, A Review of the Properties of Hemp Concrete for Green Building Applications, J. Clean. Prod., 2019, 239, 117852, DOI:10.1016/j.jclepro.2019.117852.
- Density | SICT, https://ceramique-technique.com/en/properties/density, accessed 2024-12-01.
- A. P. Duarte and J. C. Bordado, Cork – a Renewable Raw Material: Forecast of Industrial Potential and Development Priorities, Front. Mater., 2015, 2(2), 1–8, DOI:10.3389/fmats.2015.00002.
- E. García, A. De Pablos, M. A. Bengoechea, L. Guaita, M. I. Osendi and P. Miranzo, Thermal Conductivity Studies on Ceramic Floor Tiles, Ceram. Int., 2011, 37(1), 369–375, DOI:10.1016/j.ceramint.2010.09.023.
- C. Effting, S. Güths and O. E. Alarcon, Evaluation of the Thermal Comfort of Ceramic Floor Tiles, Mater. Res., 2007, 10(3), 301–307, DOI:10.1590/S1516-14392007000300016.
- Cork, https://www.makeitfrom.com/material-properties/Cork, accessed 2024-12-01.
- C. Fragassa, Limits in Application of International Standards to Innovative Ceramic
Solutions, Int. J. Qual. Res., 2015, 9(2), 279–298 Search PubMed.
- L. A. Mathew and G. Joseph, Natural Rubber Latex for the Development of High Performance Cement Mortar, Innov. Infrastruct. Solut., 2024, 9(4), 97, DOI:10.1007/s41062-024-01398-5.
- A. J. Román, O. Dibisa, G. Pardo, J. C. Rodríguez and T. A. Osswald, Evaluation of an Ammonia-Free Natural Rubber Latex Adhesive, SPE Polymers, 2024, 5(1), 11–19, DOI:10.1002/pls2.10103.
- V. Warang, Y. Patil and B. A. Lavanya, Sustainable Building and Its Comparative Analysis with Conventional Building, Int. J. Res. Appl. Sci. Eng. Technol., 2023, 11(6), 4815–4821, DOI:10.22214/ijraset.2023.54510.
- D. Zhang, CO2 Utilization for Concrete Production: Commercial Deployment and Pathways to Net-Zero Emissions, Sci. Total Environ., 2024, 931, 172753, DOI:10.1016/j.scitotenv.2024.172753.
- P. Nejat, F. Jomehzadeh, M. M. Taheri, M. Gohari and M. Z. Muhd, A Global Review of Energy Consumption, CO2 Emissions and Policy in the Residential Sector (with an Overview of the Top Ten CO2 Emitting Countries), Renewable Sustainable Energy Rev., 2015, 43, 843–862, DOI:10.1016/j.rser.2014.11.066.
- CO2 Emissions by Country - Worldometer. https://www.worldometers.info/co2-emissions/co2-emissions-by-country/, accessed 2024-12-01.
- H. Ritchie, P. Rosado and M. Roser, Energy Mix. Our World in Data, 2024 Search PubMed.
- OECD; Agency, I. Energy, CO2 Emissions from Fuel Combustion 2013, OECD Publishing, 2013 Search PubMed.
- M. J. Laustsen, Energy Efficiency Requirements In Building Codes, Energy Efficiency Policies For New Buildings IEA InformAtIon PApEr In Support of the G8 Plan of Action, 2008, http://www.iea.org/Textbase/about/copyright.asp.
- K. Jiang, R. Xing, Z. Luo, W. Huang, F. Yi, Y. Men, N. Zhao, Z. Chang, J. Zhao, B. Pan and G. Shen, Pollutant Emissions from Biomass Burning: A Review on Emission Characteristics, Environmental Impacts, and Research Perspectives, Particuology, 2024, 85, 296–309, DOI:10.1016/j.partic.2023.07.012.
- F. Ardente, M. Beccali, M. Cellura and M. Mistretta, Building Energy Performance: A LCA Case Study of Kenaf-Fibres Insulation Board, Energy Build., 2008, 40(1), 1–10, DOI:10.1016/j.enbuild.2006.12.009.
- R. Shen, D. Wang, L. Sun, M. Diao, Q. Zheng, X. Gong, L. Liu and J. Yao, Strong and Flexible Lignocellulosic Film Fabricated via a Feasible Molecular Remodeling Strategy, Int. J. Biol. Macromol., 2023, 253, 126521, DOI:10.1016/j.ijbiomac.2023.126521.
- A. Guo, Z. Sun, N. Sathitsuksanoh and H. Shang, Dispersion of Sonicated Sulfated Cellulose Nanocrystals and Their Effect on the Mechanical Properties of Cement Mortars, J. Mater. Civ. Eng., 2023, 35(6), 04023149, DOI:10.1061/jmcee7.mteng-15117.
- D. K. Chandra, A. Kumar and C. Mahapatra, Fabricating Chitosan Reinforced Biodegradable Bioplastics from Plant Extract with Nature Inspired Topology, Waste Biomass Valorization, 2024, 15(4), 2499–2512, DOI:10.1007/s12649-023-02293-3.
- S. Gupta, H. W. Kua and S. D. Pang, Effect of Biochar on Mechanical and Permeability Properties of Concrete Exposed to Elevated Temperature, Constr. Build. Mater., 2020, 234, 117338, DOI:10.1016/j.conbuildmat.2019.117338.
- J. Alex, J. Dhanalakshmi and B. Ambedkar, Experimental Investigation on Rice Husk Ash as Cement Replacement on Concrete Production, Constr. Build. Mater., 2016, 127, 353–362, DOI:10.1016/j.conbuildmat.2016.09.150.
- M. Němec, L. Prokůpek, V. Obst, T. Pipíška, P. Král and Š. Hýsek, Novel Kraft-Lignin-Based Adhesives for the Production of Particleboards, Compos. Struct., 2024, 344, 118344, DOI:10.1016/j.compstruct.2024.118344.
- N. Wu, T. Ji, P. Huang, T. Fu, X. Zheng and Q. Xu, Use of Sugar Cane Bagasse Ash in Ultra-High Performance Concrete (UHPC) as Cement Replacement, Constr. Build. Mater., 2022, 317, 125881, DOI:10.1016/j.conbuildmat.2021.125881.
- Global plastic waste generation by application 2019-2060, Statista, https://www.statista.com/statistics/1339200/global-plastic-waste-generation-outlook-by-application/, accessed 2024-12-01 Search PubMed.
- L. Yue, H. Guo, A. Kennedy, A. Patel, X. Gong, T. Ju, T. Gray and I. Manas-Zloczower, Vitrimerization: Converting Thermoset Polymers into Vitrimers, ACS Macro Lett., 2020, 9(6), 836–842, DOI:10.1021/acsmacrolett.0c00299.
- J. Z. Zhao, T. J. Yue, B. H. Ren, X. B. Lu and W. M. Ren, Closed-Loop Recycling of Sulfur-Rich Polymers with Tunable Properties Spanning Thermoplastics, Elastomers, and Vitrimers, Nat. Commun., 2024, 15(1), 3002, DOI:10.1038/s41467-024-47382-6.
- G. Rizzo, V. Prasad, M. Yasar, G. Cicala, A. Ivankovic, N. Murphy and A. Latteri, Investigation of Mechanical Properties and Self-Healing Efficiency of Carbon Fibers Composites Infused with Unsaturated Polyester Vitrimer, Polym. Compos., 2024, 45(11), 10404–10417, DOI:10.1002/pc.28483.
- E. K. Billington, T. Şucu and M. P. Shaver, Mechanical Properties and Recyclability of Fiber Reinforced Polyester Composites, ACS Sustain. Chem. Eng., 2024, 12(26), 10011–10019, DOI:10.1021/acssuschemeng.4c03341.
- M. Shi, C. Y. Shi, Q. Zhang and D. H. Qu, Orthogonal Dynamic Covalent Boroxine-Crosslinked Poly(Disulfide) Networks for Chemically Recyclable Encryption Materials, Chem. Eng. J., 2024, 484, 149564, DOI:10.1016/j.cej.2024.149564.
- X. Pan, Z. Luo, F. Liu, Q. Yi and Y. Zeng, Construction of Robust and Fully Bio-Based Epoxy Vitrimers with Facile Malleability, Self-Healing Ability, and Recyclability from Peach Gum Polysaccharide and Itaconic Acid, Ind. Crops Prod., 2024, 208, 117779, DOI:10.1016/j.indcrop.2023.117779.
- A. Bąk, J. Mikuła, I. Oliinyk and M. Łach, Basic Research on Layered Geopolymer Composites with Insulating Materials of Natural Origin, Sci. Rep., 2024, 14(1), 12576, DOI:10.1038/s41598-024-63442-9.
- S. Bertran-Llorens, F. Perondi, A. L. Slama de Freitas, J. Chen, G. van Erven and P. J. Deuss, Supercritical CO2 as Effective Wheat Straw Pretreatment for Subsequent Mild Fractionation Strategies, Chem. Eng. J., 2024, 497, 154491, DOI:10.1016/j.cej.2024.154491.
- I. Gil-Guillén, P. A. V. Freitas, C. González-Martínez and A. Chiralt, Obtaining Cellulose Fibers from Almond Shell by Combining Subcritical Water Extraction and Bleaching with Hydrogen Peroxide, Molecules, 2024, 29(14), 3284, DOI:10.3390/molecules29143284.
- V. M. Serrano-Martínez, H. Pérez-Aguilar, M. P. Carbonell-Blasco, F. Arán-Ais and E. Orgilés-Calpena, Steam Explosion-Based Method for the Extraction of Cellulose and Lignin from Rice Straw Waste, Appl. Sci., 2024, 14(5), 2059, DOI:10.3390/app14052059.
- M. Singh, A. Chauhan and S. Kumar, Rice Husk Valorization: Production of Bio-Oil and Silica-Rich Solid Phase Using Direct Thermal Liquefaction, Biomass Convers. Biorefin., 2024 DOI:10.1007/s13399-024-05988-2.
- Z. Liu, X. Peng, Y. Xu, T. Tang, S. Wei, B. Liu, D. Wang, H. M. Wang and J. Jiang, Macromolecular Structural Characteristics and Functional Potential of Tobacco Stalk Lignin from the Phosphotungstic Acid-Assisted Delignification Process, Biomass Bioenergy, 2023, 170, 106706, DOI:10.1016/j.biombioe.2023.106706.
- X. Yao, Y. Pan, X. Ma, S. Yin and M. Zhu, Efficient Separation and Production of High-Quality Rubber, Lignin Nanoparticles and Fermentable Sugars from Eucommia Ulmoides Pericarp via Deep Eutectic Solvent Pretreatment, Int. J. Biol. Macromol., 2023, 253, 127221, DOI:10.1016/j.ijbiomac.2023.127221.
- M. Rastogi and S. Shrivastava, Assessment of Indigenous Fungal Biocatalysts towards Valorization of Delignified Physico-Chemically
Pretreated Corn Cobs and Sugarcane Bagasse, Biofuels, Bioprod. Biorefin., 2023, 17(1), 153–166, DOI:10.1002/bbb.2435.
- V. Z. Ong, T. Y. Wu, K. K. L. Chu, W. Y. Sun and K. P. Y. Shak, A Combined Pretreatment with Ultrasound-Assisted Alkaline Solution and Aqueous Deep Eutectic Solvent for Enhancing Delignification and Enzymatic Hydrolysis from Oil Palm Fronds, Ind. Crops Prod., 2021, 160, 112974, DOI:10.1016/j.indcrop.2020.112974.
- H. S. M. Abd-Rabboh, K. F. Fawy, M. S. Hamdy, S. I. Elbehairi, A. A. Shati, M. Y. Alfaifi, H. A. Ibrahium, S. Alamri and N. S. Awwad, Valorization of Rice Husk and Straw Agriculture Wastes of Eastern Saudi Arabia: Production of Bio-Based Silica, Lignocellulose, and Activated Carbon, Materials, 2022, 15(11), 3746, DOI:10.3390/ma15113746.
- Y. W. Mai, M. I. Hakeem and B. Cotterell, Effects of Water and Bleaching on the Mechanical Properties of Cellulose Fibre Cements, J. Mater. Sci., 1983, 18, 2156–2162, DOI:10.1007/BF00555010.
- Y. W. Mai and M. I. Hakeem, Slow Crack Growth in Cellulose Fibre Cements, J. Mater. Sci., 1984, 19, 501–508, DOI:10.1007/BF02403237.
- C. O. Thomas, R. C. Thomas, M. Asce and K. C. Hover, Wastepaper Fibers in Cementitious Composites, J. Environ. Eng., 1987, 113, 16–31 CrossRef CAS.
- A. Bentur and S. A. S. Akerst, The Microstructure and Ageing of Cellulose Fibre Reinforced Cement Composites Cured in a Normal Environment, Int. J. Cem. Compos. Lightweight Concr., 1989, 11(2), 99–109, DOI:10.1016/0262-5075(89)90120-6.
- F. Bakula and V. Kaucie, The Study of Autoclaved Cellulose Fiber-Reinforced Cement Composites, Cem. Concr. Res., 1995, 25(1), 71–78 CrossRef CAS.
- A. J. Klemm and P. Klemmt, The Effects of the Alternate Freezing and Thawing Cycles on the Pore Structure of Cementitious Composites Modified by MHEC and PVA, Build. Environ., 1997, 32(6), 509–512, DOI:10.1016/S0360-1323(97)00025-5.
- K. Bilba, M.-A. Arsene and A. Ouensanga, Sugar Cane Bagasse Fibre Reinforced Cement Composites. Part I. Influence of the Botanical Components of Bagasse on the Setting of Bagasse/Cement Composite, Cem. Concr. Compos., 2003, 25(1), 91–96, DOI:10.1016/S0958-9465(02)00003-3.
- J. H. Morton, T. Cooke and S. A. S. Akers, Performance of Slash Pine Fibers in Fiber Cement Products, Constr. Build. Mater., 2010, 24(2), 165–170, DOI:10.1016/j.conbuildmat.2007.08.015.
- S. Wang and L. Baxter, Comprehensive Study of Biomass Fly Ash in Concrete: Strength, Microscopy, Kinetics and Durability, Fuel Process. Technol., 2007, 88(11–12), 1165–1170, DOI:10.1016/j.fuproc.2007.06.016.
- S. Zhou, X. Zhang and X. Chen, Pozzolanic Activity of Feedlot Biomass (Cattle Manure) Ash, Constr. Build. Mater., 2012, 28(1), 493–498, DOI:10.1016/j.conbuildmat.2011.09.003.
- S. Demis, J. G. Tapali and V. G. Papadakis, An Investigation of the Effectiveness of the Utilization of Biomass Ashes as Pozzolanic Materials, Constr. Build. Mater., 2014, 68, 291–300, DOI:10.1016/j.conbuildmat.2014.06.071.
- R. Kaminskas, V. Cesnauskas and R. Kubiliute, Influence of Different Artificial Additives on Portland Cement Hydration and Hardening, Constr. Build. Mater., 2015, 95, 537–544, DOI:10.1016/j.conbuildmat.2015.07.113.
- J. Li, Q. Jin, W. Zhang, C. Li and P. J. M. Monteiro, Microstructure and Durability Performance of Sustainable Cementitious Composites Containing High-Volume Regenerative Biosilica, Resour., Conserv. Recycl., 2022, 178, 106038, DOI:10.1016/j.resconrec.2021.106038.
- J. Fořt, J. Šál, M. Keppert, M. Mildner, P. Hotěk, A. Ślosarczyk, Ł. Klapiszewski and R. Černý, Durability Analysis of Sustainable Mortars with Biomass Fly Ash as High-Volume Replacement of Portland Cement, J. Build. Eng., 2024, 91, 109565, DOI:10.1016/j.jobe.2024.109565.
- B. Manjunath, C. M. Ouellet-Plamondon, B. B. Das and C. Bhojaraju, Potential
Utilization of Regional Cashew Nutshell Ash Wastes as a Cementitious Replacement on the Performance and Environmental Impact of Eco-Friendly Mortar, J. Build. Eng., 2023, 66, 105941, DOI:10.1016/j.jobe.2023.105941.
- L. Yang, W. Xu, Y. Huang, B. Deng, Y. Wu and J. Sun, Research on the Effect of Recombustion Treatment on the Performance of Straw Biomass Fly Ash, Biomass Convers. Biorefin., 2024, 9735, DOI:10.1007/s13399-024-05831-8.
- C. Huang, H. Y. Yu, G. Chen and Y. Liao, “Reinforced Concrete” Design of Robust Mineralized Cellulose Composite with Multilayered Structure for Efficient CO2 Capture and Passive Radiative Cooling Ability, Compos. Sci. Technol., 2024, 258, 110886, DOI:10.1016/j.compscitech.2024.110886.
- H. Taheri, N. A. Heidari, A. Perrot, G. Siqueira, G. Nyström and S. Kawashima, Selection of Suitable Cellulose Nanofibers Derived from Eco-Friendly Sources for the Production of Lightweight Cementitious Composites with Tuned Rheological, Mechanical, and Microstructure Properties, Cem. Concr. Compos., 2024, 151, 105586, DOI:10.1016/j.cemconcomp.2024.105586.
- A. A. Fahim, N. Admassu, G. Dailey and M. Khanzadeh Moradllo, Application of Cellulose Nanocrystals in 3D Printed Alkali-Activated Cementitious Composites, J. Build. Eng., 2024, 82, 108380, DOI:10.1016/j.jobe.2023.108380.
- U. Kilic, N. Soliman, A. Omran and O. E. Ozbulut, Effects of Cellulose Nanofibrils on Rheological and Mechanical Properties of 3D Printable Cement Composites, Cem. Concr. Compos., 2024, 152, 105617, DOI:10.1016/j.cemconcomp.2024.105617.
- N. Burgos, A. Valdés and A. Jiménez, Valorization of Agricultural Wastes for the Production of Protein-Based Biopolymers, J. Renewable Mater., 2016, 4(3), 165–177, DOI:10.7569/JRM.2016.634108.
- B. De Wilde and J. Boelens, Prerequisites for Biodegradable Plastic Materials for Acceptance in Real-Life Cornposting Plants and Technical Aspects, Polym. Degrad. Stab., 1998, 59(1–3), 7–12, DOI:10.1016/S0141-3910(97)00159-6.
- M. Brodin, M. Vallejos, M. T. Opedal, M. C. Area and G. Chinga-Carrasco, Lignocellulosics as Sustainable Resources for Production of Bioplastics – A Review, J. Clean. Prod., 2017, 646–664, DOI:10.1016/j.jclepro.2017.05.209.
- W. J. Orts, J. Shey, S. H. Imam, G. M. Glenn, M. E. Guttman and J. F. Revol, Application of Cellulose Microfibrils in Polymer Nanocomposites, J. Polym. Environ., 2005, 13(4), 301–306, DOI:10.1007/s10924-005-5514-3.
- J. Ganster, H. P. Fink and M. Pinnow, High-Tenacity Man-Made Cellulose Fibre Reinforced Thermoplastics - Injection Moulding Compounds with Polypropylene and Alternative Matrices, Composites, Part A, 2006, 37(10), 1796–1804, DOI:10.1016/j.compositesa.2005.09.005.
- G. Chen, Z. Wu, Z. Shen, H. Y. Li, J. Li, B. Lü, G. Song, X. Gong, M. Qin, C. L. Yao and F. S. Peng, Strong and Water-Stable Wood-Derived Bioplastic, Chem. Eng. J., 2022, 439, 135680, DOI:10.1016/j.cej.2022.135680.
- J. Zhou, M. You, J. Xu, Y. Jin, D. Li, Z. Xu and C. Chen, All-Cellulose Bioplastics from Waste Wood Particles, ACS Sustain. Chem. Eng., 2024, 12(25), 9550–9557, DOI:10.1021/acssuschemeng.4c03425.
- C. Chen, L. Wang and Y. Huang, Crosslinking of the Electrospun Polyethylene Glycol/Cellulose Acetate Composite Fibers as Shape-Stabilized Phase Change Materials, Mater. Lett., 2009, 63(5), 569–571, DOI:10.1016/j.matlet.2008.11.033.
- A. Saralegi, M. L. Gonzalez, A. Valea, A. Eceiza and M. A. Corcuera, The Role of Cellulose Nanocrystals in the Improvement of the Shape-Memory Properties of Castor Oil-Based Segmented Thermoplastic Polyurethanes, Compos. Sci. Technol., 2014, 92, 27–33, DOI:10.1016/j.compscitech.2013.12.001.
- J. G. G. de Farias, R. C. Cavalcante, B. R. Canabarro, H. M. Viana, S. Scholz and R. A. Simão, Surface Lignin Removal on Coir Fibers by Plasma Treatment for Improved Adhesion in Thermoplastic Starch Composites, Carbohydr. Polym., 2017, 165, 429–436, DOI:10.1016/j.carbpol.2017.02.042.
- C. Lei, Y. Wei, Y. Qian, Q. Wang, P. Zhu, G. Qiu and G. Chen, Large-Scale Manufacture of Recyclable Bioplastics from Renewable Cellulosic Biomass Derived from Softwood Kraft Pulp, ACS Appl. Polym. Mater., 2022, 4(2), 1334–1343, DOI:10.1021/acsapm.1c01729.
- J. S. Yeo, D. W. Seong and S. H. Hwang, Chemical Surface Modification of Lignin Particle and Its Application as Filler in the Polypropylene Composites, J. Ind. Eng. Chem., 2015, 31, 80–85, DOI:10.1016/j.jiec.2015.06.010.
- J. M. Koo, J. Kang, S. H. Shin, J. Jegal, H. G. Cha, S. Choy, M. Hakkarainen, J. Park, D. X. Oh and S. Y. Hwang, Biobased Thermoplastic Elastomer with Seamless 3D-Printability and Superior Mechanical Properties Empowered by in-Situ Polymerization in the Presence of Nanocellulose, Compos. Sci. Technol., 2020, 185, 107885, DOI:10.1016/j.compscitech.2019.107885.
- S. Adil, B. Kumar and J. Kim, Degradable, Lightweight, and High-Performance Unidirectional Nanocellulose-Long-Filament-Reinforced Vanillin Epoxy Composites for Structural Applications, ACS Appl. Polym. Mater., 2024, 6(14), 7932–7937, DOI:10.1021/acsapm.4c01634.
- S. Adil, B. Kumar, D. H. Pham and J. Kim, Biobased, Cellulose Long Filament-Reinforced Vanillin-Derived Epoxy Composite for High-Performance and Flame-Retardant Applications, Int. J. Biol. Macromol., 2024, 256, 128411, DOI:10.1016/j.ijbiomac.2023.128411.
- M. Yang, X. Zhang, S. Guan, Y. Dou and X. Gao, Preparation of Lignin Containing Cellulose Nanofibers and Its Application in PVA Nanocomposite Films, Int. J. Biol. Macromol., 2020, 158, 1259–1267, DOI:10.1016/j.ijbiomac.2020.05.044.
- J. Jo, H. Kim, S. Y. Jeong, C. Park, H. S. Hwang and B. Koo, Changes in Mechanical Properties of Polyhydroxyalkanoate with Double Silanized Cellulose Nanocrystals Using Different Organosiloxanes, Nanomaterials, 2021, 11(6), 1542, DOI:10.3390/nano11061542.
- D. Nedelcu, S. N. Mazurchevici, R. I. Popa, N. M. Lohan, D. Maldonado-Cortés and C. Carausu, Tribological and Dynamical Mechanical Behavior of Prototyped PLA-Based Polymers, Materials, 2020, 13(16), 3615, DOI:10.3390/MA13163615.
- H. Memon, Y. Wei, L. Zhang, Q. Jiang and W. Liu, An Imine-Containing Epoxy Vitrimer with Versatile Recyclability and Its Application in Fully Recyclable Carbon Fiber Reinforced Composites, Compos. Sci. Technol., 2020, 199, 108314, DOI:10.1016/j.compscitech.2020.108314.
- B. Hararak, W. Wanmolee, P. Wijaranakul, N. Prakymoramas, C. Winotapun, W. Kraithong and K. Nakason, Physicochemical Properties of Lignin Nanoparticles from Softwood and Their Potential Application in Sustainable Pre-Harvest Bagging as Transparent UV-Shielding Films, Int. J. Biol. Macromol., 2023, 229, 575–588, DOI:10.1016/j.ijbiomac.2022.12.270.
- Y. Fei, F. Chen, W. Fang, A. Hejna, L. Xu, T. Liu, M. Zhong, J. Yang and T. Kuang, Conductive Thermoplastic Polyurethane Nanocomposite Foams Derived from a Cellulose/MWCNTs Aerogel Framework: Simultaneous Enhancement of Piezoresistance, Strength, and Endurance, J. Mater. Chem. C, 2021, 9(38), 13103–13114, 10.1039/d1tc02874j.
- A. K. Mohanty, M. Misra and L. T. Drzal, Sustainable Bio-Composites from Renewable Resources: Opportunities and Challenges in the Green Materials World, J. Environ. Polym. Degrad., 2002, 10, 19–26, DOI:10.1023/A:1021013921916.
- C. Lacoste, R. El Hage, A. Bergeret, S. Corn and P. Lacroix, Sodium Alginate Adhesives as Binders in Wood Fibers/Textile Waste Fibers Biocomposites for Building Insulation, Carbohydr. Polym., 2018, 184, 1–8, DOI:10.1016/j.carbpol.2017.12.019.
- N. A. Ramlee, M. Jawaid, E. S. Zainudin and S. A. K. Yamani, Tensile, Physical and Morphological Properties of Oil Palm Empty Fruit Bunch/Sugarcane Bagasse Fibre Reinforced Phenolic Hybrid Composites, J. Mater. Res. Technol., 2019, 8(4), 3466–3474, DOI:10.1016/j.jmrt.2019.06.016.
- M. Charai, H. Sghiouri, A. Mezrhab and M. Karkri, Thermal Insulation Potential of Non-Industrial Hemp (Moroccan Cannabis Sativa L.) Fibers for Green Plaster-Based Building Materials, J. Clean. Prod., 2021, 292, 126064, DOI:10.1016/j.jclepro.2021.126064.
- J. Yu, D. Yang, Q. He, B. Du, S. Zhang and M. Hu, Strong, Durable and Fire-Resistant Glass Fiber-Reinforced Bamboo Scrimber, Ind. Crops Prod., 2022, 181, 114783, DOI:10.1016/j.indcrop.2022.114783.
- X. Liu, M. Wang and Z. Lu, Brown Sugar Enhancing Strength of Corn Stalk Biomass Bricks, Ind. Crops Prod., 2023, 195, 116417, DOI:10.1016/j.indcrop.2023.116417.
- J. Qureshi, A Review of Fibre Reinforced Polymer Structures, Fibers, 2022, 10(3), 27, DOI:10.3390/fib10030027.
- K. M. F. Hasan, K. N. A. Hasan, T. Ahmed, S. T. György, M. N. Pervez, L. Bejó, B. Sándor and T. Alpár, Sustainable Bamboo Fiber Reinforced Polymeric Composites for Structural Applications: A Mini Review of Recent Advances and Future Prospects, Case Stud. Chem. Environ. Eng., 2023, 8, 100362, DOI:10.1016/j.cscee.2023.100362.
- H. P. S. Abdul Khalil, I. U. H. Bhat, M. Jawaid, A. Zaidon, D. Hermawan and Y. S. Hadi, Bamboo Fibre Reinforced Biocomposites: A Review, Mater. Des., 2012, 42, 353–368, DOI:10.1016/j.matdes.2012.06.015.
- Insulation Market Size to Surpass USD 110.58 Bn by 2032, https://www.globenewswire.com/news-release/2024/01/04/2804134/0/en/Insulation-Market-Size-to-Surpass-USD-110-58-Bn-by-2032.html, accessed 2024-12-01.
- P. Gupta, M. Sathwane, M. Chhajed, C. Verma, Y. Grohens, B. Seantier, A. K. Agrawal and P. K. Maji, Surfactant Assisted In Situ Synthesis of Nanofibrillated Cellulose/Polymethylsilsesquioxane Aerogel for Tuning Its Thermal Performance, Macromol. Rapid Commun., 2023, 44(2), 2200628, DOI:10.1002/marc.202200628.
- S. Bhardwaj, S. Singh, P. Gupta, N. Choudhary and P. K. Maji, Role of Morphological Arrangements in Cellulose Nanofiber-Based Aerogels for Thermal Insulation: A Systematic Review, Int. J. Green Energy, 2023, 22(8), 1491–1512, DOI:10.1080/15435075.2023.2253873.
- M. Ghassemi and A. Shahidian, Biosystems Heat and Mass Transfer, Nano and Bio Heat Transfer and Fluid Flow, 2017, pp. 31–56, DOI:10.1016/B978-0-12-803779-9.00003-0.
- S. Bhardwaj, S. Singh, N. Choudhary and P. K. Maji, One-Pot Fabrication of Structurally Stable Cellulose Nanofibers/Biochar-Based Phase Change Composites with Enhanced Thermal Energy Conversion and Storage Capacity, ACS Appl. Polym. Mater., 2025, 7(7), 4619, DOI:10.1021/acsapm.5c00397.
- S. Bhardwaj, S. Singh, K. Dev, M. Chhajed and P. K. Maji, Harnessing the Flexibility of Lightweight Cellulose Nanofiber Composite Aerogels for Superior Thermal Insulation and Fire Protection, ACS Appl. Mater. Interfaces, 2024, 16(14), 18075–18089, DOI:10.1021/acsami.4c01803.
- K. Biswas, J. Lu, P. Soroushian and S. Shrestha, Combined Experimental and Numerical Evaluation of a Prototype Nano-PCM Enhanced Wallboard, Appl. Energy, 2014, 131, 517–529, DOI:10.1016/j.apenergy.2014.02.047.
- K. O. Lee, M. A. Medina, X. Sun and X. Jin, Thermal Performance of Phase Change Materials (PCM)-Enhanced Cellulose Insulation in Passive Solar Residential Building Walls, Sol. Energy, 2018, 163, 113–121, DOI:10.1016/j.solener.2018.01.086.
- B. Wicklein, A. Kocjan, G. Salazar-Alvarez, F. Carosio, G. Camino, M. Antonietti and L. Bergström, Thermally Insulating and Fire-Retardant Lightweight Anisotropic Foams Based on Nanocellulose and Graphene Oxide, Nat. Nanotechnol., 2015, 10(3), 277–283, DOI:10.1038/nnano.2014.248.
- Q. Fan, R. Ou, X. Hao, Q. Deng, Z. Liu, L. Sun, C. Zhang, C. Guo, X. Bai and Q. Wang, Water-Induced Self-Assembly and In Situ Mineralization within Plant Phenolic Glycol-Gel toward Ultrastrong and Multifunctional Thermal Insulating Aerogels, ACS Nano, 2022, 16(6), 9062–9076, DOI:10.1021/acsnano.2c00755.
- Y. Han, X. Zhang, X. Wu and C. Lu, Flame Retardant, Heat Insulating Cellulose Aerogels from Waste Cotton Fabrics by in Situ Formation of Magnesium Hydroxide Nanoparticles in Cellulose Gel Nanostructures, ACS Sustain. Chem. Eng., 2015, 3(8), 1853–1859, DOI:10.1021/acssuschemeng.5b00438.
- P. Gupta, B. Singh, A. K. Agrawal and P. K. Maji, Low Density and High Strength Nanofibrillated Cellulose Aerogel for Thermal Insulation Application, Mater. Des., 2018, 158, 224–236, DOI:10.1016/j.matdes.2018.08.031.
- X. Zhao, Y. Liu, L. Zhao, A. Yazdkhasti, Y. Mao, A. P. Siciliano, J. Dai, S. Jing, H. Xie, Z. Li, S. He, B. C. Clifford, J. Li, G. S. Chen, E. Q. Wang, A. Desjarlais, D. Saloni, M. Yu, J. Kośny, J. Y. Zhu, A. Gong and L. A. Hu, Scalable High-Porosity Wood for Sound Absorption and Thermal Insulation, Nat. Sustain., 2023, 6(3), 306–315, DOI:10.1038/s41893-022-01035-y.
- D. M. Nguyen, A. C. Grillet, Q. B. Bui, T. M. H. Diep and M. Woloszyn, Building Bio-Insulation Materials Based on Bamboo Powder and Bio-Binders, Constr. Build. Mater., 2018, 186, 686–698, DOI:10.1016/j.conbuildmat.2018.07.153.
- C. Buratti, F. Merli and E. Moretti, Aerogel-Based Materials for Building Applications: Influence of Granule Size on Thermal and Acoustic Performance, Energy Build., 2017, 152, 472–482, DOI:10.1016/j.enbuild.2017.07.071.
- J. Zhu, J. Hu, C. Jiang, S. Liu and Y. Li, Ultralight, Hydrophobic, Monolithic Konjac Glucomannan-Silica Composite Aerogel with Thermal Insulation and Mechanical Properties, Carbohydr. Polym., 2019, 207, 246–255, DOI:10.1016/j.carbpol.2018.11.073.
- W. Liang, R. Wang, C. Wang, J. Jia, H. Sun, J. Zhang, Y. Yang, Z. Zhu and A. Li, Facile Preparation of Attapulgite-Based Aerogels with Excellent Flame Retardancy and Better Thermal Insulation Properties, J. Appl. Polym. Sci., 2019, 136(32), 47849, DOI:10.1002/app.47849.
- Q. B. Thai, S. T. Nguyen, D. K. Ho, T. Du Tran, D. M. Huynh, N. H. N. Do, T. P. Luu, P. K. Le, D. K. Le, N. Phan-Thien and H. M. Duong, Cellulose-Based Aerogels from Sugarcane Bagasse for Oil Spill-Cleaning and Heat Insulation Applications, Carbohydr. Polym., 2020, 228, 115365, DOI:10.1016/j.carbpol.2019.115365.
- D. Wang, H. Peng, B. Yu, K. Zhou, H. Pan, L. Zhang, M. Li, M. Liu, A. Tian and S. Fu, Biomimetic Structural Cellulose Nanofiber Aerogels with Exceptional Mechanical, Flame-Retardant and Thermal-Insulating Properties, Chem. Eng. J., 2020, 389, 124449, DOI:10.1016/j.cej.2020.124449.
- B. Fleury, E. Abraham, J. A. De La Cruz, V. S. Chandrasekar, B. Senyuk, Q. Liu, V. Cherpak, S. Park, J. B. Ten Hove and I. I. Smalyukh, Aerogel from Sustainably Grown Bacterial Cellulose Pellicles as a Thermally Insulative Film for Building Envelopes, ACS Appl. Mater. Interfaces, 2020, 12(30), 34115–34121, DOI:10.1021/acsami.0c08879.
- Y. Zhu, I. Therrien, Z. Wan, Z. Yu, J. Zhu, D. Zheng, H. Sun, O. J. Rojas and F. Jiang, One-Pot Complexation of Phytic Acid and Polyethyleneimine on Cellulosic Microfibers towards Insulative and Flame-Resistant Foam, Int. J. Biol. Macromol., 2024, 275, 133521, DOI:10.1016/j.ijbiomac.2024.133521.
- L. Boquera, E. Olacia, C. Fabiani, A. L. Pisello, A. D'Alessandro, F. Ubertini and L. F. Cabeza, Thermo-Acoustic and Mechanical Characterization of Novel Bio-Based Plasters: The Valorisation of Lignin as by-Product from Biomass Extraction for Green Building Applications, Constr. Build. Mater., 2021, 278, 122373, DOI:10.1016/j.conbuildmat.2021.122373.
- X. Sun, Q. Yu, F. Wang, S. Hu, J. Zhou, Y. Liu, Z. Jiang, X. Wang, Y. Yu, H. Yang and C. Wang, Sustainable Lignocellulose Aerogel for Air Purifier with Thermal Insulation, Flame Retardancy, Mechanical Strength, and Its Life Cycle Assessment, Int. J. Biol. Macromol., 2024, 257, 128599, DOI:10.1016/j.ijbiomac.2023.128599.
- R. Baetens, B. P. Jelle and A. Gustavsen, Aerogel Insulation for Building Applications: A State-of-the-Art Review, Energy Build., 2011, 43(4), 761–769, DOI:10.1016/j.enbuild.2010.12.012.
- M. Ibrahim, K. Nocentini, M. Stipetic, S. Dantz, F. G. Caiazzo, H. Sayegh and L. Bianco, Multi-Field and Multi-Scale Characterization of Novel Super Insulating Panels/Systems Based on Silica Aerogels: Thermal, Hydric, Mechanical, Acoustic, and Fire Performance, Build. Environ., 2019, 151, 30–42, DOI:10.1016/j.buildenv.2019.01.019.
- J. Kosny, A. D. Fontanini, N. Shukla, A. Fallahi, A. Watts, R. Trifu and B. Ganapathysubramanian, Thermal Performance Analysis of Residential Attics Containing High Performance Aerogel-Based Radiant Barriers, Energy Build., 2018, 158, 1036–1048, DOI:10.1016/j.enbuild.2017.10.081.
- T. Gao, T. Ihara, S. Grynning, B. P. Jelle and A. G. Lien, Perspective of Aerogel Glazings in Energy Efficient Buildings, Build. Environ., 2016, 95, 405–413, DOI:10.1016/j.buildenv.2015.10.001.
- E. Abraham, V. Cherpak, B. Senyuk, J. B. ten Hove, T. Lee, Q. Liu and I. I. Smalyukh, Highly Transparent Silanized Cellulose Aerogels for Boosting Energy Efficiency of Glazing in Buildings, Nat. Energy, 2023, 8(4), 381–396, DOI:10.1038/s41560-023-01226-7.
- A. Lamy-Mendes, A. D. R. Pontinha, P. Alves, P. Santos and L. Durães, Progress in Silica Aerogel-Containing Materials for Buildings' Thermal Insulation, Constr. Build. Mater., 2021, 286, 122815, DOI:10.1016/j.conbuildmat.2021.122815.
- Finishing Materials, in Building Materials in Civil Engineering, Elsevier, 2011, pp 316–423, DOI:10.1533/9781845699567.316.
- J. Faustino, L. Pereira, S. Soares, D. Cruz, A. Paiva, H. Varum, J. Ferreira and J. Pinto, Impact Sound Insulation Technique Using Corn Cob Particleboard, Constr. Build. Mater., 2012, 37, 153–159, DOI:10.1016/j.conbuildmat.2012.07.064.
- G. Zhu, H. Xu, A. Dufresne and N. Lin, High-Adsorption, Self-Extinguishing, Thermal, and Acoustic-Resistance Aerogels Based on Organic and Inorganic Waste Valorization from Cellulose Nanocrystals and Red Mud, ACS Sustain. Chem. Eng., 2018, 6(5), 7168–7180, DOI:10.1021/acssuschemeng.8b01244.
- C. Wang, Y. Xiong, B. Fan, Q. Yao, H. Wang, C. Jin and Q. Sun, Cellulose as an Adhesion Agent for the Synthesis of Lignin Aerogel with Strong Mechanical Performance, Sound-Absorption and Thermal Insulation, Sci. Rep., 2016, 6, 32383, DOI:10.1038/srep32383.
- J. Feng, D. Le, S. T. Nguyen, V. Tan Chin Nien, D. Jewell and H. M. Duong, Silica–Cellulose
Hybrid Aerogels for Thermal and Acoustic Insulation Applications, Colloids Surf. A Physicochem. Eng. Asp., 2016, 506, 298–305, DOI:10.1016/j.colsurfa.2016.06.052.
- J. O. Yeon, K. W. Kim, K. S. Yang, J. M. Kim and M. J. Kim, Physical Properties of Cellulose Sound Absorbers Produced Using Recycled Paper, Constr. Build. Mater., 2014, 70, 494–500, DOI:10.1016/j.conbuildmat.2014.07.088.
- K. Bikumalla, T. Bhuvana, A. Tiwari and C. Chandraprakash, Binder-Free, Non-Carcinogenic Surfactant-Based Cellulose-Rich Bagasse Foams as Acoustic Panels, J. Appl. Polym. Sci., 2024, 141(11), e55096, DOI:10.1002/app.55096.
- X. Yu, X. Jin, Y. He, Z. Yu, R. Zhang and D. Qin, Eco-Friendly Bamboo Pulp Foam Enabled by Chitosan and Phytanic Acid Interfacial Assembly of Halloysite Nanotubes: Toward Flame Retardancy, Thermal Insulation, and Sound Absorption, Int. J. Biol. Macromol., 2024, 260, 129393, DOI:10.1016/j.ijbiomac.2024.129393.
- X. Li, Z. Yang, K. Li, S. Zhao, Z. Fei and Z. Zhang, A Flexible Silica Aerogel with Good Thermal and Acoustic Insulation Prepared via Water Solvent System, J. Sol-Gel Sci. Technol., 2019, 92(3), 652–661, DOI:10.1007/s10971-019-05107-y.
- X. Long, P. Huang, X. Wei, J. Yu, S. Wang and J. Liao, Ultra-High Strength, Highly Deformable and Superhydrophobic Polybenzoxazine@cellulose Nanofiber Composite Aerogel for Thermal Insulation, Composites, Part A, 2023, 175, 107771, DOI:10.1016/j.compositesa.2023.107771.
- X. Long, X. Wei, M. Hu, J. Yu, S. Wang, L. Zhou and J. Liao, Anisotropic and High-Strength SiO2/Cellulose Nanofiber Composite Aerogel with Thermal Superinsulation and Superhydrophobicity, Ceram. Int., 2023, 49(17), 28621–28628, DOI:10.1016/j.ceramint.2023.06.116.
- S. S. L. Sobhana, X. Zhang, L. Kesavan, P. Liias and P. Fardim, Layered Double Hydroxide Interfaced Stearic Acid – Cellulose Fibres: A New Class of Super-Hydrophobic Hybrid Materials, Colloids Surf. A Physicochem. Eng. Asp., 2017, 522, 416–424, DOI:10.1016/j.colsurfa.2017.03.025.
- H. S. Yoon, T. K. Lim, S. M. Jeong and K. H. Yang, Thermal Transfer and Moisture Resistances of Nano-Aerogel-Embedded Foam Concrete, Constr. Build. Mater., 2020, 236, 117575, DOI:10.1016/j.conbuildmat.2019.117575.
- M. Venier, A. Salamova and R. A. Hites, Halogenated Flame Retardants in the Great Lakes Environment, Acc. Chem. Res., 2015, 48(7), 1853–1861, DOI:10.1021/acs.accounts.5b00180.
- L. Chen and Y. Z. Wang, A Review on Flame Retardant Technology in China. Part I: Development of Flame Retardants, Polym. Adv. Technol., 2010, 21(1), 1–26, DOI:10.1002/pat.1550.
- J. Shen, J. Liang, X. Lin, H. Lin, J. Yu and S. Wang, The Flame-Retardant Mechanisms and Preparation of Polymer Composites and Their Potential Application in Construction Engineering, Polymers, 2022, 14(1), 82, DOI:10.3390/polym14010082.
- W. Liu, D. Q. Chen, Y. Z. Wang, D. Y. Wang and M. H. Qu, Char-Forming Mechanism of a Novel Polymeric Flame Retardant with Char Agent, Polym. Degrad. Stab., 2007, 92(6), 1046–1052, DOI:10.1016/j.polymdegradstab.2007.02.009.
- F. Hu, B. Cheng, K. Cong, D. Li, W. Zhang, Z. Qin and R. Yang, Enhancing Char Formation and Flame Retardancy of Ethylene-Vinyl Acetate Copolymer (EVA)/Aluminum Hydroxide (ATH) Composites by Grafting Ladder Phenyl/Vinyl Polysilsesquioxane (PhVPOSS), Polymers, 2023, 15(15), 3312, DOI:10.3390/polym15153312.
- C. Liu, L. Wan, Q. Li, X. Sun, A. Natan, D. Cao, P. Luan and H. Zhu, Ice-Templated Anisotropic Flame-Resistant Boron Nitride Aerogels Enhanced through Surface Modification and Cellulose Nanofibrils, ACS Appl. Polym. Mater., 2021, 3(3), 1358–1367, DOI:10.1021/acsapm.0c01219.
- F. Yu, Z. Ba, Z. Gao, Y. Wang, Y. Xie, H. Wang, Z. Qiu and Z. Xiao, Modification with Lignin-Based N-P Flame Retardant to Improve the Flame Retardancy and Smoke Suppression of Wood, Chem. Eng. J., 2024, 493, 152827, DOI:10.1016/j.cej.2024.152827.
- B. Zuo and B. Yuan, Flame-Retardant Cellulose Nanofiber Aerogel Modified with Graphene Oxide and Sodium Montmorillonite and Its Fire-Alarm Application, Polym. Adv. Technol., 2021, 32(4), 1877–1887, DOI:10.1002/pat.5231.
- A. L. Missio, C. G. Otoni, B. Zhao, M. Beaumont, A. Khakalo, T. Kämäräinen, S. H. F. Silva, B. D. Mattos and O. J. Rojas, Nanocellulose Removes the Need for Chemical Crosslinking in Tannin-Based Rigid Foams and Enhances Their Strength and Fire Retardancy, ACS Sustain. Chem. Eng., 2022, 10(31), 10303–10310, DOI:10.1021/acssuschemeng.2c02678.
- Y. C. Wang, J. P. Zhao and J. Chen, Effect of Polydimethylsiloxane Viscosity on Silica Fume-Based Geopolymer Hybrid Coating for Flame-Retarding Plywood, Constr. Build. Mater., 2020, 239, 117814, DOI:10.1016/j.conbuildmat.2019.117814.
- K. Wu, S. Xu, X. Y. Tian, H. Y. Zeng, J. Hu, Y. H. Guo and J. Jian, Renewable Lignin-Based Surfactant Modified Layered Double Hydroxide and Its Application in Polypropylene as Flame Retardant and Smoke Suppression, Int. J. Biol. Macromol., 2021, 178, 580–590, DOI:10.1016/j.ijbiomac.2021.02.148.
- L. Wang, Y. Wang, J. Zhang, F. Wang, Z. Liu and J. Jiang, Investigation on Self-Healing Polyurethane Coating Doped with Lignin Composites for Protecting Cementitious Materials, Constr. Build. Mater., 2024, 411, 134368, DOI:10.1016/j.conbuildmat.2023.134368.
- A. S. Borisova, T. Virkkala, R. Pylkkänen, M. Kellock and P. Mohammadi, Toughening Brittle Kraft Lignin Coating on Mismatched Substrate with Spider Silk-Inspired Protein as an Interfacial Modulator, J. Colloid Interface Sci., 2024, 655, 789–799, DOI:10.1016/j.jcis.2023.11.057.
- K. A. Henn, S. Forssell, A. Pietiläinen, N. Forsman, I. Smal, P. Nousiainen, R. P. Bangalore Ashok, P. Oinas and M. Österberg, Interfacial Catalysis and Lignin Nanoparticles for Strong Fire- and Water-Resistant Composite Adhesives, Green Chem., 2022, 24(17), 6487–6500, 10.1039/d2gc01637k.
- C. Scarica, R. Suriano, M. Levi, S. Turri and G. Griffini, Lignin Functionalized with Succinic Anhydride as Building Block for Biobased Thermosetting Polyester Coatings, ACS Sustain. Chem. Eng., 2018, 6(3), 3392–3401, DOI:10.1021/acssuschemeng.7b03583.
- M. Siahkamari, S. Emmanuel, D. B. Hodge and M. Nejad, Lignin-Glyoxal: A Fully Biobased Formaldehyde-Free Wood Adhesive for Interior Engineered Wood Products, ACS Sustain. Chem. Eng., 2022, 10(11), 3430–3441, DOI:10.1021/acssuschemeng.1c06843.
- N. Kanbargi, D. Hoskins, S. Gupta, Z. Yu, Y. Shin, Y. Qiao, D. R. Merkel, C. C. Bowland, N. Labbé, K. L. Simmons and A. K. Naskar, A Renewable Lignin-Based Thermoplastic Adhesive for Steel Joining, Eur. Polym. J., 2023, 189, 111981, DOI:10.1016/j.eurpolymj.2023.111981.
- N. Rong, Z. Mu, J. Shao, L. Han, K. Liu, L. Ge, S. Wang, X. Shi and G. Wang, Enhanced Thermochemical Energy Storage Properties of SiC-Doped Calcium-Based Material with Steam Addition during Heat Charging Process, J. Energy Storage, 2024, 95, 112609, DOI:10.1016/j.est.2024.112609.
- Y. Liu, X. Zhao, Z. Liu, B. Sun, X. Liu, R. Zhao, B. Liu, Z. Sun, Y. Men, W. Hu and Z. B. Shao, Functionalized Lignin Nanoparticles Assembled
with MXene Reinforced Polypropylene with Favorable UV-Aging Resistance, Electromagnetic Shielding Effects and Superior Fire-Safety, Int. J. Biol. Macromol., 2024, 265, 130957, DOI:10.1016/j.ijbiomac.2024.130957.
- J. Liu, S. He, Z. Liu, X. Wu, Z. Cui, J. Liu and W. Shao, Construction of Black Phosphorus Incorporated Film by a Brick-on-Cement Strategy for Highly Sensitive Humidity Sensor and Triple-Stimuli-Driven Actuator, Sens. Actuators, B, 2024, 413, 135899, DOI:10.1016/j.snb.2024.135899.
- A. Ismail, M. Bahmani, X. Chen and J. Wang, An Organic-Inorganic Hybrid Microcapsule of Phase Change Materials for Thermal Energy Storage in Cementitious Composites, Constr. Build. Mater., 2024, 416, 135289, DOI:10.1016/j.conbuildmat.2024.135289.
- H. S. Yang, D. J. Kim, Y. K. Lee, H. J. Kim, J. Y. Jeon and C. W. Kang, Possibility of Using Waste Tire Composites Reinforced with Rice Straw as Construction Materials, Bioresour. Technol., 2004, 95(1), 61–65, DOI:10.1016/j.biortech.2004.02.002.
- M. Li, Q. Lyu, L. Sun, B. Peng, L. Zhang and J. Zhu, Fluorescent Metallosupramolecular Elastomers for Fast and Ultrasensitive Humidity Sensing, ACS Appl. Mater. Interfaces, 2020, 12(35), 39665–39673, DOI:10.1021/acsami.0c11278.
- J. Wang, X. Wu, Y. Wang, W. Zhao, Y. Zhao, M. Zhou, Y. Wu and G. Ji, Green, Sustainable Architectural Bamboo with High Light Transmission and Excellent Electromagnetic Shielding as a Candidate for Energy-Saving Buildings, Nano-Micro Lett., 2023, 15(1), 11, DOI:10.1007/s40820-022-00982-7.
- M. El Hajam, W. Sun, R. Hossain, I. Hafez, C. Howell and M. Tajvidi, Surfactant-Assisted Foam-Forming of High Performance Ultra-Low Density Structures Made from Lignocellulosic Materials and Cellulose Nanofibrils (CNFs), Ind. Crops Prod., 2024, 221, 119357, DOI:10.1016/j.indcrop.2024.119357.
- Y. Zhang, D. Wu, J. Li, Y. Yu, H. Lv, A. Xu, Q. Wang, W. Li, P. Lv and Q. Wei, Biomass Confined Gradient Porous Janus Bacterial Cellulose Film Integrating Enhanced Radiative Cooling with Perspiration-Wicking for Efficient Thermal Management, Carbohydr. Polym., 2024, 343, 122482, DOI:10.1016/j.carbpol.2024.122482.
- X. Wang, X. Meng, T. Cui, Q. Hu, B. Jin, Y. He, X. Zhu and C. Ye, Highly Transparent Cellulose-Based Phosphorescent Materials with Tunable Afterglow Colors and White Emission, Carbohydr. Polym., 2024, 341, 122309, DOI:10.1016/j.carbpol.2024.122309.
- X. Li, J. Li, X. Shen, M. Cao, Y. Wang, W. Zhang, Y. Xu, Z. Ling, S. Chen and F. Xu, Transparent Cellulose/Lignin Composite Films with Adjustable Haze and UV-Blocking Performance for Light Management, ACS Sustain. Chem. Eng., 2024, 12(14), 5427–5435, DOI:10.1021/acssuschemeng.3c07076.
- T. Cui, Y. Zheng, M. Hu, B. Lin, J. Wang, W. Cai, B. Fei, J. Zhu and Y. Hu, Biomimetic Multifunctional Graphene-Based Coating for Thermal Management, Solar De-Icing, and Fire Safety: Inspired from the Antireflection Nanostructure of Compound Eyes, Small, 2024, 20(35), 2312083, DOI:10.1002/smll.202312083.
- N. Yildirim, Design of Adhesive-free Bio-based Suspended Ceiling Tiles Using Nanocellulose, BioResources, 2018, 13(4), 7360–7370, DOI:10.15376/biores.13.4.7360-7370.
- X. J. Kang, H. Zhang, C. Y. He, B. H. Liu, Y. Z. Zhang and X. H. Gao, Harnessing the Synergy of ZrO2 and SiO2 Dielectric Micro-/Nanoparticles in Polymer-Based Photonic Films for Robust Passive Daytime Radiative Cooling, Mater. Today Energy, 2024, 43, 101579, DOI:10.1016/j.mtener.2024.101579.
- H. T. Nguyen, T. T. Nguyen, T. T. Tran, J. Bang, M. Kumar, J. Kim and J. H. Yun, Colour-Passive Radiative Cooling in Optoelectronics with Silver/Quantum Dot Decorated Silica Multifunctional Hybrid Structures, Chem. Eng. J., 2024, 488, 150840, DOI:10.1016/j.cej.2024.150840.
- J. Song, C. Chen, S. Zhu, M. Zhu, J. Dai, U. Ray, Y. Li, Y. Kuang, Y. Li, N. Quispe, Y. Yao, A. Gong, U. H. Leiste, H. A. Bruck, J. Y. Zhu, A. Vellore, H. Li, M. L. Minus, Z. Jia, A. Martini, T. Li and L. Hu, Processing Bulk Natural Wood into a High-Performance Structural Material, Nature, 2018, 554(7691), 224–228, DOI:10.1038/nature25476.
- C. Feng, B. Xu, L. Chen, Z. Qiu and J. Guo, Cellulose Hydrogels with High Response Sensitivity and Mechanical Adaptability for Flexible Strain Sensor and Triboelectric Nanogenerator, Eur. Polym. J., 2024, 214, 113173, DOI:10.1016/j.eurpolymj.2024.113173.
- A. N. Kaplan, M. Z. Tufan and C. Özel, Investigation of Some Cellulose Derivatives Effects on Concrete Properties Using Response Surface Methodology, Constr. Build. Mater., 2024, 416, 135115, DOI:10.1016/j.conbuildmat.2024.135115.
- Q. Su and J. Xu, Mechanical Properties of Rice Husk Ash and Glass Powder Concrete: Experimental and Mesoscopic Studies, J. Build. Eng., 2024, 95, 110278, DOI:10.1016/j.jobe.2024.110278.
- W. She, G. Zhao, D. Cai, J. Jiang and X. Cao, Numerical Study on the Effect of Pore Shapes on the Thermal Behaviors of Cellular Concrete, Constr. Build. Mater., 2018, 163, 113–121, DOI:10.1016/j.conbuildmat.2017.12.108.
- J. Ning, J. Xiao, Q. Liu, L. Li and Z. Zhao, Simulation Study on Static Pressure Crushing Performance of Demolished Reinforced Concrete Beams for Recycling, Eng. Struct., 2024, 321, 118902, DOI:10.1016/j.engstruct.2024.118902.
- A. Anwar, Y. Wenyi, L. Jing, W. Yanwei, B. Sun, M. Ameen, I. Shah, L. Chunsheng, Z. U. Mustafa and Y. Muhammad, Predicting the Compressive Strength of Cellulose Nanofibers Reinforced Concrete Using Regression Machine Learning Models, Cogent Eng., 2023, 10(1), 2225278, DOI:10.1080/23311916.2023.2225278.
- H. Sun, M. N. Amin, M. T. Qadir, S. U. Arifeen, B. Iftikhar and F. Althoey, Investigating the Effectiveness of Carbon Nanotubes for the Compressive Strength of Concrete Using AI-Aided Tools, Case Stud. Constr. Mater., 2024, 20, e03083, DOI:10.1016/j.cscm.2024.e03083.
- R. Kashyap, M. Saxena, A. Gautam, A. Kushwaha, K. Priyanka, A. Patel and R. K. Maurya, Exploring Sustainable Construction through Experimental Analysis and AI Predictive Modelling of Ceramic Waste Powder Concrete, "Asian J. Civ. Eng., 2024, 25(6), 4789–4801, DOI:10.1007/s42107-024-01080-2.
- A. Bashir, M. M. Jibril, U. M. Jibrin, S. I. Abba and S. I. Malami, A New Strategy Using Intelligent Hybrid Learning for Prediction of Water Binder Ratio of Concrete with Rice Husk Ash as a Supplementary Cementitious Material, J. Build. Pathol. Rehabil., 2025, 10(1), 36, DOI:10.1007/s41024-024-00541-0.
- Y. Liu, Z. M. A. Mohammed, J. Ma, R. Xia, D. Fan, J. Tang and Q. Yuan, Machine Learning Driven Fluidity and Rheological Properties Prediction of Fresh Cement-Based Materials, Materials, 2024, 17(22), 5400, DOI:10.3390/ma17225400.
- L. Yang, X. Lin, H. Li and R. J. Gravina, A New Constitutive Model for Steel Fibre Reinforced Concrete Subjected to Dynamic Loads, Compos. Struct., 2019, 221, 110849, DOI:10.1016/j.compstruct.2019.04.021.
- Y. Miao, W. Yu, L. Jin, L. Wang, J. Lin, Y. Li, Z. Lu and J. Jiang, Effect of Shrinkage-Induced Initial Damage on the Frost Resistance of Concrete in Cold Regions, Eng. Fract. Mech., 2024, 312, 110652, DOI:10.1016/j.engfracmech.2024.110652.
- W. Xu, D. Jiang, Q. Zhao and L. Wang, Study on Printability of 3D Printing Carbon Fiber Reinforced Eco-Friendly Concrete: Characterized by Fluidity and Consistency, Case Stud. Constr. Mater., 2024, 21, e03589, DOI:10.1016/j.cscm.2024.e03589.
- Y. Wang, X. Wang, F. Li and G. Lou, Numerical Simulations Study of Concrete Mix Proportion Based on Fluidity, Constr. Build. Mater., 2024, 455, 139236, DOI:10.1016/j.conbuildmat.2024.139236.
- W. Liang, Z. Chen and J. Yu, A Three-Phase Model Based on Boundary Element Method for Simulation of Chloride Diffusion in Concrete, Case Stud. Constr. Mater., 2024, 21, e03454, DOI:10.1016/j.cscm.2024.e03454.
- K. M. Gondaliya, S. A. Vasanwala, A. K. Desai, J. A. Amin and V. Bhaiya, Machine Learning-Based Approach for Assessing the Seismic Vulnerability of Reinforced Concrete Frame Buildings, J. Build. Eng., 2024, 97, 110785, DOI:10.1016/j.jobe.2024.110785.
- S. Song, X. Xu, W. Ren, S. Liu and J. Jiang, Determination and Application of the RHT Constitutive Model Parameters for Ultra-High-Performance Concrete, Structures, 2024, 69, 107488, DOI:10.1016/j.istruc.2024.107488.
- W. Cao, J. Li, X. Zhang, F. Kang and X. Wu, Sonar Combines Deep Learning and Building Information Modeling for Underwater Crack Detection of Concrete Structures, Structures, 2024, 70, 107834, DOI:10.1016/j.istruc.2024.107834.
- J. Wu, H. Ye, S. Li, Z. Que, Y. Peng, L. Cai and C. Xia, Life Cycle Assessment of Transparent Wood in Building Industry: A Sustainable Solution for Global Warming Mitigation, Constr. Build. Mater., 2024, 438, 137303, DOI:10.1016/j.conbuildmat.2024.137303.
- C. E. Andersen, I. Stupak, E. Hoxha, K. Raulund-Rasmussen and H. Birgisdóttir, Forest Dynamics in LCA: Integrating Carbon Fluxes from Forest Management Systems into the Life Cycle Assessment of a Building, Resour., Conserv. Recycl., 2024, 209, 107805, DOI:10.1016/j.resconrec.2024.107805.
- C. E. Andersen, E. Hoxha, F. N. Rasmussen, C. G. Sorensen and H. Birgisdottir, Temporal Considerations in Life Cycle Assessments of Wooden Buildings: Implications for Design Incentives, J. Clean. Prod., 2024, 445, 141260, DOI:10.1016/j.jclepro.2024.141260.
- X. Zhang, W. Huang, M. Khajehpour, M. Asgari and T. Tannert, Seismic Performance and LCA Comparison between Concrete and Timber–Concrete Hybrid Buildings, Buildings, 2023, 13(7), 1714, DOI:10.3390/buildings13071714.
- A. Katebi, H. H. Eghdam and G. Asadollahfardi, LCA and Economic Cradle-to-Gate Analysis on the Reuse of a Temporary Building, Environ. Sci. Pollut. Res., 2024, 31, 59087–59102, DOI:10.1007/s11356-024-35132-6.
- B. H. Miao, R. J. Headrick, Z. Li, L. Spanu, D. J. Loftus and M. D. Lepech, Life Cycle Assessment and Design of LignoBlock: A Lignin Bound Block on the Path towards a Green Transition of the Construction Industry, J. Clean. Prod., 2024, 474, 143610, DOI:10.1016/j.jclepro.2024.143610.
- I. Campo Gay, L. Hvam, A. Haug, G. Q. Huang and R. Larsson, A Digital Tool for Life Cycle Assessment in Construction Projects, Dev. Built Environ., 2024, 20, 100535, DOI:10.1016/j.dibe.2024.100535.
- Z. Jiang, K. Lu, M. Limdevit, C. Fu, Y. Ling and B. Dong, Influence of Durability Properties on Life-Cycle Carbon Reduction of Low-Carbon Mortar with Similar Compressive Strength, Case Stud. Constr. Mater., 2025, 22, e04558, DOI:10.1016/j.cscm.2025.e04558.
- S. Sbahieh, G. McKay, A. Nurdiawati and S. G. Al-Ghamdi, The Sustainability of Partial and Total Replacement of Ordinary Portland Cement: A Deep Dive into Different Concrete Mixtures through Life Cycle Assessment, J. Build. Eng., 2025, 108, 112830, DOI:10.1016/j.jobe.2025.112830.
- H. Khan, J. Ahmad, Z. B. Zahid, S. Irfan and M. Umer, Development of Extrusion Based Artificial Lightweight Aggregates from Sand-Plastic Waste Composite for Sustainable Concrete Production: Performance Evaluation and Life Cycle Assessment, Case Stud. Constr. Mater., 2025, 22, e04663, DOI:10.1016/j.cscm.2025.e04663.
- A. Zaragoza-Benzal, D. Ferrández, M. I. Prieto and A. L. Matilla, Impact Assessment of Different Steel Fibres on Mechanical, Environmental and Economic Performance in Cement Mortars, Results Eng., 2025, 26, 105021, DOI:10.1016/j.rineng.2025.105021.
- A. Scioti, F. Fabbrocino and F. Fatiguso, Sustainable Production of Building Blocks by Reusing Stone Waste Sludge, Appl. Sci., 2025, 15(9), 5031, DOI:10.3390/app15095031.
- M. M. Nawaz, H. A. Khan, J. Ahmad and M. Noman, Mechanical Performance and Life Cycle Assessment of Alkali-Activated Concrete with Municipal-Waste Incinerated Bottom Ash as Partial Precursor, Multiscale Multidiscip. Model. Exp. Des., 2025, 8(6), 279, DOI:10.1007/s41939-025-00865-5.
|
This journal is © The Royal Society of Chemistry 2025 |
Click here to see how this site uses Cookies. View our privacy policy here.