DOI:
10.1039/D0AN00621A
(Paper)
Analyst, 2020,
145, 4352-4357
An enhanced gas sensor based on SiO2@mesoporous MCM-41 core–shell nanocomposites for SO2 visual detection†
Received
30th March 2020
, Accepted 14th May 2020
First published on 20th May 2020
Abstract
A colorimetric sulfur dioxide (SO2) gas sensor based on a core–shell composite was developed. The composite was fabricated with a silicon dioxide core and a mesoporous MCM-41 shell (SiO2@MCM-41), and further loaded with a mixture of zinc chloride (ZnCl2), sodium nitroprusside (SNP) and hexamine as an SO2 indicator. The sensing properties of SiO2@MCM-41 toward SO2 were measured in solid powder, discs and a gas detection tube (GDT), respectively. Each of these sensing configurations showed a distinct color change from pale yellow to red, which indicates good potential for naked-eye detection of SO2. The limit of detection (LOD) is 2 ppm for SiO2@MCM-41 discs, which indicates high sensitivity to SO2. The performance of GDT suggested a linear relationship between the SO2 concentration and the response length of the red portions in a range of 100–1000 ppm. This work shows promising potential of SiO2@MCM-41 as an easy, effective and rapid response sensing material for the in situ detection of SO2.
Introduction
SO2 has drawn worldwide attention as one of the major pollutants in the atmosphere, and is mainly produced from the burning of fossil fuels. After dissolving in water vapor, SO2 can interact with other particles in air and form an acid.1–4 The emission of SO2 has contributed to a series of problems that threaten the environment and human health, such as acid rain, eye irritation, and respiratory illnesses. The acid rain has caused great losses in forestry, agriculture, aquaculture, animal husbandry, and construction.5–7 Moreover, the acid rain areas of China are the world's third largest acid rain areas next to Europe and North America, which have reached 30% of the total land area.8 Without effective monitoring, air pollution and environmental acidification caused by the acid rain will increase. Therefore, it is significant to develop an SO2 sensor with quick and accurate detection. Various approaches, including optics, semiconductor and electrolyte technologies, have been used to detect SO2.9–12 However, the abovementioned methods for SO2 detection usually suffer from the requirement of expensive instruments and complicated operation and are inconvenient for on-site monitoring.13,14
In the early 1990s, scientists in Mobil prepared M41S silicate mesoporous molecular sieves with highly uniform and ordered pore structures, which extend the pore size from micropores to mesopores.15 Mesoporous materials have been vastly studied as adsorbents, sensors, catalysts, and drug carriers because of their high specific surface areas, tunable pore sizes, high mechanical strength and capability of chemical functionalization.16–20 Various mesoporous materials have been reported for sensing. For example, mesoporous semiconductor metal oxides are widely used for gas sensing. Zhao et al. synthesised ordered mesoporous Fe doped In2O3 for NO2 gas sensing, and the as-prepared sensor exhibited an excellent response to NO2 gas.21 Izu et al. fabricated a V2O5/WO3/TiO2 resistive sensor for SO2 detection, and the response range is from 20 to 5000 ppm.22
Although mesoporous materials have great potential in different areas, it is gradually becoming difficult for single-component mesoporous materials to meet the requirements of various applications. Recently, multifunctional mesoporous composites with a controlled microstructure, which can overcome the deficiencies of single-component mesoporous materials, have attracted increasing attention. Core–shell composites are nanostructures that have a core that is coated by another material, and they have been extensively explored for their unique structures and properties.23 The hybrid structures of core–shell nanoparticles enhance the chemical and thermal stability. Also, the combined functionalities of cores and shells can allow them to achieve synergistic functions and have good potential for applications in various research fields.24–27 In particular, considering the high surface to volume ratio, core–shell mesoporous materials can enhance the gas sensing performance. Wu et al.28 fabricated hematite hollow spheres with a mesoporous shell, and the obtained α-Fe2O3 exhibited high gas sensitivity toward formaldehyde and ethanol at room temperature. Li et al.29 proposed an NH3 sensor based on a Au-loaded mesoporous In2O3 nanosphere@polyaniline core–shell nanohybrid, and the sensor showed excellent sensitivity, selectivity and reproducibility to NH3 at room temperature.
Gas sensing involves the adsorption and desorption processes on the surfaces of materials, and core–shell mesoporous materials with high surface specific areas are favorable for gas diffusion. Herein, we report core–shell silica nanoparticles with a silica core and ordered mesoporous silica shell for SO2 sensing. The SiO2 core was synthesized based on the Stöber method,30 and the mesoporous MCM-41 shell was obtained by using cetyltrimethyl ammonium bromide (CTAB) as a template. ZnCl2, SNP and hexamine were mixed as an SO2 indicator, which was loaded on the surface of MCM-41. The sensing performance of SO2 gas was measured by the as-prepared SiO2@MCM-41 in 3 different forms, and each form of SiO2@MCM-41 involved a distinct color change. Additionally, the SiO2@MCM-41 sensor exhibited remarkable repeatability, high sensitivity and perfect response concentration linearity to SO2 at room temperature, which suggests its promising applications for SO2 gas sensing.
Experimental
Chemicals & apparatus
Glycerin, SNP, ZnCl2, hydrochloric acid and hexamine were purchased from Beijing Chemical Plant. Sodium hydroxide (NaOH) and anhydrous sodium sulfate were obtained from Beijing Tongguang Fine Chemicals Co. Ltd. Tetraethyl orthosilicate (TEOS), CTAB, ethanol, isopropanol, and ammonium hydroxide (NH3·H2O) were purchased from J&K Scientific Ltd.
The heating process was carried out in a DNP-9022 electro-thermal incubator (Jinghong). The calcination of SiO2@MCM-41 was carried out in a muffle furnace (Yiheng, SX2-8-10NP). The microstructure was characterized using a scanning electron microscope (SEM) (Hitachi, S-4800) and a transmission electron microscope (TEM) (JEM-2100, JEOL). The porous properties of SiO2@MCM-41 were investigated by nitrogen adsorption and desorption at 77.3 K using an ASAP 2020, Micromeritics Instrument Corp, USA. The pore-size-distribution curves were obtained from the adsorption branches using non-local density functional theory (NLDFT).
Synthesis of SiO2@MCM-41 composites
Preparation of SiO2@MCM-41 core–shell nanoparticles.
SiO2 nanoparticles were prepared according to a previously published method.31 Briefly, 2 mL TEOS was added to 2 mL NH3·H2O, 20 mL deionized H2O and 200 mL isopropanol at 35 °C under magnetic stirring. After stirring for 2 h, the resultant mixture was collected by centrifugation, followed by washing with ethanol and water 3 times. The above obtained SiO2 nanospheres were dispersed in the mixed solution of 100 mL ethanol and 200 mL deionized H2O. 2 mL of 1 mol L−1 NaOH was added into the above solution under 500 rpm magnetic stirring for 30 min. Then, 2 g CTAB was added to the mixture. After 30-minute-stirring, 0.45 mL TEOS was added to the mixture. The product was collected by centrifugation after reaction for 8 h and then washed repeatedly with ethanol and water to remove the template CTAB. Finally, the as-prepared products were heated in a muffle furnace to 550 °C for 6 h and SiO2@MCM-41 nanoparticles were produced.
Preparation and loading of the SiO2@MCM-41 indicator.
The SiO2@MCM-41 indicator was prepared by dissolving 1 g ZnCl2 in 10 mL ultrapure water with 0.5 mL hydrochloric acid, 1 g SNP in 10 mL ultrapure water with 0.5 mL glycerol, and 2 g hexamine in 10 mL ultrapure water. Afterward, we added 0.1, 0.2 and 0.1 mL as-prepared ZnCl2, SNP and hexamine solution to 30 mg SiO2@MCM-41 solid powder, respectively. After mixing the solution with SiO2@MCM-41 uniformly, the powder was dried in an oven for 30 min at 80 °C. The mechanism of ZnCl2, SNP and hexamine as an SO2 indicator was referred to a previous report.32 Before SiO2@MCM-41 was loaded with the SO2 indicator, we weighed the SiO2@MCM-41 solid powder with an electric balance, and the weight was found to be 563 mg. Then we treated SiO2@MCM-41 with the SO2 gas indicator and dried it in an oven. After the powder was completely dried, we weighed it again, and the weight was 576 mg. The weight of the SiO2@MCM-41 solid powder increased after being loaded with the SO2 indicator; so we suggested that the indicator was loaded successfully.
Gas sensing measurement
SiO2@MCM-41 solid gas sensing test.
The gas sensing test was carried out on an as-fabricated gas sensing system, which is shown in S1.† SiO2@MCM-41 solid samples were placed inside an airbag (1L) and then different ratios of SO2 and air were injected. After the balance between SO2 adsorption and desorption, the color change of the SiO2@MCM-41 solid samples was recorded.
Gas adsorption test.
The concentration of sulfate ions in solution can be obtained by ion chromatography.33 1.479 g anhydrous sodium sulfate was dissolved in ultrapure water and transferred to a 1 L volumetric flask as a sulfate ion stock liquid. We added 0.5, 1, 2.5, 5 and 7.5 mL of the sulfate ion stock liquid to 10 mL volumetric flasks, respectively. Sequentially, 50, 100, 250, 500 and 750 mg L−1 sulfate ion standard solutions were obtained. Then, 30 μL of each concentration sulfate ion standard solution was injected into the ion chromatography system, and a standard working curve was prepared based on the chromatographic peak area (S2).†
For the measurement of the gas adsorption rate of the SiO2@MCM-41 solid samples, first, 100 mL of 0.2 mol mL−1 NaOH solution and hydrogen peroxide solution were mixed as the SO2 adsorption solution. Afterward, we placed 30 mg of the SiO2@MCM-41 solid samples inside an airbag and injected 50 ml of SO2 at 15 °C. While waiting for the balance of gas adsorption, the remaining gas in the airbag was delivered into a sealed container with the as-prepared SO2 adsorption solution. After adsorption at 5 °C for 6 h, sulfate ions were detected by ion chromatography. Then the concentration of sulfate ions in the as-prepared SO2 adsorption solution can be obtained from the standard working curve. According to the amount of sulfate ions, the adsorption rate of SO2 was calculated.
3SO2 gas detection tube (GDT) test.
A homemade sensing system of SO2 GDT is presented in S3.† We injected different concentrations of SO2 gas prepared in airbags through a tube using a 100 mL syringe. After the gas passed through the SO2 GDT, it was collected by another 100 mL syringe, which was connected to the end of the tube. For each concentration, the experiment was repeated 10 times, and the color change and response length of the SO2 GDT were recorded. Scheme 1 shows a schematic illustration of the fabrication and sensing processes of SiO2@MCM-41.
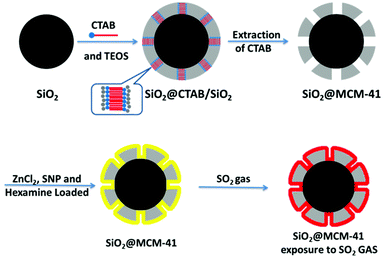 |
| Scheme 1 Schematic illustration of the fabrication and detection processes of SiO2@MCM-41. | |
Results and discussion
Characterization of SiO2@MCM-41
From the SEM image (Fig. 1a), the mean diameter of SiO2 particles is found to be 206 ± 5 nm, and the sizes of these particles are uniform. SiO2 nanoparticles showed good monodispersity and sphericity. After the combination of SiO2 with MCM-41, the SEM image showed that the mean diameter of SiO2@MCM-41 increased to 235 ± 5 nm, and the TEM image revealed a distinct core–shell structure of SiO2@MCM-41 composite nanoparticles, and both implied that the MCM-41shell integrated with the SiO2 core successfully (Fig. 1b and c). The adsorption curves of SiO2@MCM-41 exhibited the type-IV isotherm (Fig. S4†), which is characteristic of mesoporous materials. A Brunauer–Emmett–Teller (BET) surface area of 656 m2 g−1 was estimated for SiO2@MCM-41. The NLDFT gave rise to a narrow pore size distribution with an average pore width of 10.6 nm (Fig. S4†).
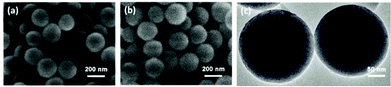 |
| Fig. 1 SEM images of (a) SiO2 nanoparticles and (b) SiO2@MCM-41 composite nanoparticles. (c) TEM image of SiO2@MCM-41 composite nanoparticles. | |
The visual detection of SO2
The response of the SiO2@MCM-41 nanocomposite toward SO2 was investigated over a range of 100–8000 ppm, and the results are presented in Fig. 2. After exposure to SO2, the color of the SiO2@MCM-41 nanocomposite changed from pale yellow to red visually. In the presence of SO2 with different concentrations, the powder showed a different color. In this enclosed environment of SO2, the observed response time is typically around 20 s. Based on the above experiment studies and literature findings, we proposed a mechanism for the sensing of SiO2@MCM-41. After the gas adsorption, SO32− is generated. When SNP and SO32− are mixed, a deep red coloration develops. The coloration results from what is commonly called the Boedeker reaction.34 SNP and sulfite interact to give the red, highly dissociated sulphitonitroprusside ions as follows:
Fe(CN)5 NO2− + SO2−3 ⇌ Fe(CN)5 NOSO34− |
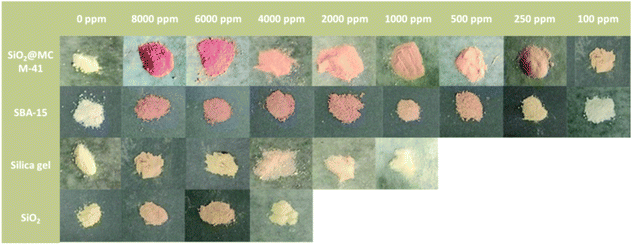 |
| Fig. 2 The visual color changes of SiO2@MCM-41, SBA-15, silica gel and SiO2 in response to different concentrations of SO2 gas. | |
According to the previous research,35 the addition of zinc ions results in the formation of sparingly soluble zinc sulphitonitroprusside and markedly increases the sensitivity of the Boedeker reaction. The alkaline medium can form ion-pairs of the type Fe(CN)5 NOSO3M3−, where M is an alkaline medium. So we added ZnCl2 and hexamine to help increase the sensitivity of the Boedeker reaction. Also, the larger the volume of SO2 that SiO2@MCM-41 adsorbed, the larger the volume of sulphitonitroprusside ions it reacted with, so that the color change of the response becomes more significant.
The SO2 sensing properties for other porous solids were also measured (Fig. 2). The SiO2@MCM-41 nanocomposite exhibits a higher response than SBA-15, silica gel and SiO2, which is in agreement with their adsorption properties. Compared to SiO2@MCM-41, the color changes of these materials are less obvious. The LOD value of SiO2@MCM-41 is lower than 100 ppm while the LOD values of SBA-15, silica gel and SiO2 are 250 ppm, 2000 ppm and 6000 ppm, respectively. These results are due to the difference in the specific surface areas of these solids. SiO2@MCM-41 has a higher specific surface area than others, which can provide more binding sites and lead to more rapid adsorption of SO2 on the surface.
The adsorption properties of the SiO2@MCM-41 solid
The reproducibility of the SiO2@MCM-41 sensing system was evaluated as the weight changes of SiO2@MCM-41 for 10 cycles (Fig. 3a). The SiO2@MCM-41 nanoparticles were alternately placed under air and SO2 atmosphere at 15 °C. The initial weight of the solids was 540 mg in air, and changed to ∼691 mg after exposure to SO2 gas. With the adsorption and desorption of SO2 from the pore structure of SiO2@MCM-41, the weight changed and the adsorption rate was maintained after 10 cycles. Moreover, after SO2 gas bound with the indicator that loaded on SiO2@MCM-41, the nanoparticles changed from white to red accordingly. The color change of SiO2@MCM-41 upon exposure to SO2 and air is reversible, which implies the remarkable stability and repeatability of this sensor.
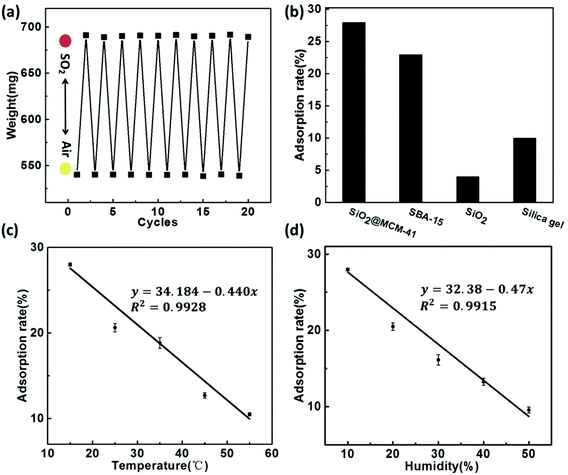 |
| Fig. 3 (a) Reversible changes of the weight of SiO2@MCM-41 when alternately exposed to air and SO2 gas, and the corresponding color changes. (b) The adsorption rates of SiO2@MCM-41, SBA-15, silica gel and SiO2 toward SO2 gas. (c) The relationship between the adsorption rate and the temperature of SO2 gas. (d) The relationship between the adsorption rate and the humidity of SO2 gas. | |
Fig. 3b illustrates the adsorption capacity of a series of nanoparticles including SiO2@MCM-41, SBA-15, silica gel and SiO2. Owing to the porous structure and high specific surface area of SiO2@MCM-41, which allow them to adsorb more gas, the adsorption capacity of SiO2@MCM-41 is higher than that of other porous materials. The adsorption rate for SO2 is 28% for SiO2@MCM-41 while the rates are 23%, 10% and 4% for SBA-15, silica gel and SiO2. Hence, we believe that SiO2@MCM-41 is an ideal material for SO2 gas sensing.
For practical applications, temperature and humidity are critical influencing factors for gas sensors. Fig. 3c and d show how the adsorption rate toward SO2 varies with its temperature and humidity, respectively. With the increasing temperature, the absorption capacity decreased, suggesting an exothermic process (Fig. 3c). This indicated that low temperature is in favor of SO2 absorption. In a high-moisture environment, water vapor can block the adsorption sites on the surface of SiO2@MCM-41 and compete with SO2 gas for these sites. As a result, the adsorption rate for SO2 decreased (Fig. 3d). These adsorption behaviours under different temperatures and humidity are consistent with the references.36–38
SO2 sensing properties
The SiO2@MCM-41 solid was pressed into discs with a manual hydraulic press at 20 MPa to detect the gases of low-concentration SO2 (Fig. 4). When the SO2 gases with different concentrations were injected into the airbag, these discs exhibited different color changes in 10 s. With the increase of the SO2 concentration, more red reaction products were obtained and the color change became more obvious. Moreover, the LOD of SiO2@MCM-41 was also investigated. When the concentration of SO2 is lower than 2 ppm, the amount of gas SiO2@MCM-41 absorbed is too small to obtain sufficient red reaction products that the human eyes can observe. Thus, we suggest that the LOD of SiO2@MCM-41 is 2 ppm, which exhibits high sensitivity for SO2 naked-eye detection.
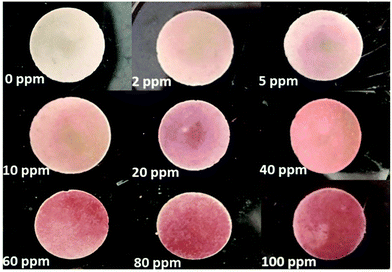 |
| Fig. 4 The visual color changes of SiO2@MCM-41 discs in response to low concentrations of SO2 gases. | |
By observing the color change of the SiO2@MCM-41 solid, we can estimate the approximate concentration of SO2 gas. However, for a practical, visual and rapid SO2 gas sensor, it should be able to detect SO2 quantitatively. Therefore, we proposed an SO2 GDT. The apparatus consists of a transparent glass tube with iron meshes at both ends, and the SiO2@MCM-41 solid samples were fixed between the iron meshes. After the injection of different concentrations of SO2 gases through a 100 mL syringe, the color of the SO2 GDT turned to red at different lengths (Fig. 5a). The response lengths of the red portions toward 100, 200, 400, 800 and 1000 ppm are about 1.6, 3.2, 6.5, 12.5 and 17.4 mm, respectively. By measuring the length of the product, we can infer the concentration of SO2 gas quantitatively. Fig. 5b shows the relationship between the SO2 concentration and the color change length of the SO2 GDT. According to the calibration curve, a very good linear correlation with R2 = 0.9971 is achieved, which reveals a good potential application for in situ SO2 gas monitoring. Besides, the red reaction product of the GDT cannot remain stable in air for a long time. So after exposure to air for 2 days, the red reaction product vanished, and the SO2 GDT could be reused again.
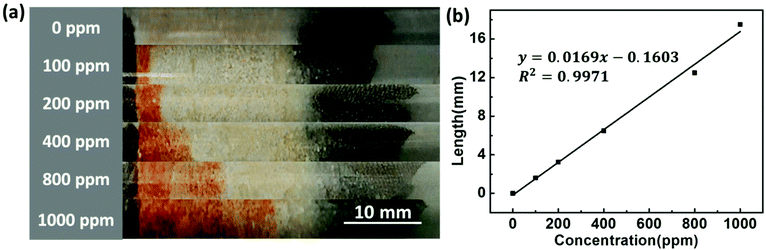 |
| Fig. 5 (a) The visual color change length and (b) corresponding fitting curve of the SO2 GDT in response to various concentrations of SO2 gases. | |
Conclusions
This paper reports a core–shell SiO2@MCM-41 sensor synthesized by an easily operated method and loaded with ZnCl2, SNP and hexamine as indicators. The SiO2@MCM-41 sensor was made into solid powder, discs and a GDT. The as-prepared three SiO2@MCM-41 sensors were measured by exposure to different concentrations of SO2 gas, and the sensing properties were systematically investigated. As a result, the SiO2@MCM-41 sensor displayed different color changes with various concentrations and a quick response. The LOD of SiO2@MCM-41 is 2 ppm, which indicated that the sensor is highly sensitive. Moreover, the SO2 GDT performed colorimetric quantitative detection, and hence we suggest the potential application of practical SO2 sensing. In summary, this SiO2@MCM-41 sensor is easy to fabricate and operate. The research results in this paper show high sensitivity, outstanding stability and perfect response concentration linearity to SO2. Besides, the distinct color change of SiO2@MCM-41 after exposure to SO2 makes naked-eye detection possible. Thus, we believe it is a qualified candidate for SO2in situ monitoring.
Conflicts of interest
There are no conflicts to declare.
Acknowledgements
The financial support was obtained from the National Natural Science Foundation of China (U1530141, 21874009 and 21804009).
References
- D. Zhang, J. Wu, P. Li and Y. Cao, J. Mater. Chem. A, 2017, 5, 20666–20677 RSC.
- K. G. Anne, S. Krenn and H. Puxbaum, Fresenius' J. Anal. Chem., 1999, 363, 73–76 CrossRef.
- M. R. Tchalala, P. M. Bhatt, K. N. Chappanda, S. R. Tavares, K. Adil, Y. Belmabkhout, A. Shkurenko, A. Cadiau, N. Heymans, G. D. Weireld, G. Maurin, K. N. Salama and M. Eddaoudi, Nat. Commun., 2019, 10, 1328–1337 CrossRef CAS PubMed.
- A. V. Leontiev and D. M. Rudkevich, J. Am. Chem. Soc., 2015, 127, 14126–14127 CrossRef PubMed.
- J. Nisar, Z. Topalian, A. De Sarkar, L. Osterlund and R. Ahuja, ACS Appl. Mater. Interfaces, 2013, 5, 8516–8522 CrossRef CAS PubMed.
- J. N. Yun, C. Zhu, Q. Wang, Q. L. Hu and G. Yang, Catal. Commun., 2018, 114, 79–83 CrossRef CAS.
- C. Ma, X. D. Hao, X. Yang, X. H. Liang, F. M. Liu, T. Liu, C. H. Yang, H. Q. Zhu and G. Y. Lu, Phys. Chem. Chem. Phys., 2014, 16, 19327–19332 RSC.
- L. Ping, X. Fei, P. Jiayong, C. Yiping, P. Huaming and C. Shaohua, Environ. Sci. Manage., 2011, 36, 30–35 Search PubMed.
- Y. Uneme, S. Tamura and N. Imanaka, Sens. Actuators, B, 2013, 177, 529–534 CrossRef CAS.
- J. Zhang, Z. Qin, D. Zeng and C. Xie, Phys. Chem. Chem. Phys., 2017, 19, 6313–6329 RSC.
- J. L. Martínez-Hurtado, C. Davidson, J. Blyth and C. R. Lowe, Langmuir, 2010, 26, 15694–15699 CrossRef PubMed.
- T. Dinh, I. Choi, Y. Son and J. Kim, Sens. Actuators, B, 2016, 213, 529–538 CrossRef.
- U. Tumuluri, J. D. Howe, W. P. Mounfield III, M. J. Li and A. C. S. Sustain, Chem. Eng., 2017, 5, 9295–9306 CAS.
- T. Wang, D. Huang, Z. Yang, S. Xu, G. He, X. Li, N. Hu, G. Yin, D. He and L. Zhang, Nano-Micro Lett., 2016, 8, 95–119 CrossRef PubMed.
- C. T. Kresge, M. E. Leonowicz, W. J. Roth, J. C. Vartuli and J. S. Beck, Nature, 1992, 359, 710–712 CrossRef CAS.
- L. Li, M. Krissanasaeranee, S. W. Pattinson, M. Stefik, U. Wiesner, U. Steiner and E. Dominik, Chem. Commun., 2010, 46, 7620–7622 RSC.
- Y. K. Lu and X. P. Yan, Anal. Chem., 2004, 76, 453–457 CrossRef CAS PubMed.
- Y. Li, W. Luo, N. Qin, J. Dong, J. Wei, W. Li, S. Feng, J. Chen, J. Xu, A. A. Elzatahry, M. H. Es-Saheb, Y. Deng and D. Zhao, Angew. Chem., Int. Ed., 2014, 53, 9035–9040 CrossRef CAS PubMed.
- S. Shao, M. Dimitrov, N. Guan and R. Köhn, J. Mater. Chem., 2009, 19, 8411–8410 RSC.
- Z. Hou, C. Li, P. Ma, Y. Dai, D. Yang, Z. Cheng and J. Lin, Adv. Funct. Mater., 2012, 22, 2713–2722 CrossRef CAS.
- J. Zhao, T. Yang, Y. Liu, Z. Wang, X. Li, Y. Sun, Y. Du, Y. Li and G. Lu, Sens. Actuators, B, 2014, 191, 806–812 CrossRef CAS.
- N. Izu, G. Hagen, D. Schönauer, U. Röder-Roith and R. Moos, Sensors, 2011, 11, 2982–2991 CrossRef CAS PubMed.
- R. Chaudhuri and S. Paria, Chem. Rev., 2012, 112, 2373–2433 CrossRef PubMed.
- W. Schartl, Nanoscale, 2010, 2, 829–843 RSC.
- Y. Deng, D. Qi, C. Deng, X. Zhang and D. Zhao, J. Am. Chem. Soc., 2008, 130, 28–29 CrossRef CAS PubMed.
- J. D. Qiu, H. P. Peng, R. P. Liang and X. H. Xia, Biosens. Bioelectron., 2010, 25, 1447–1453 CrossRef CAS PubMed.
- Y. Chen, B. Zhu, M. Yao, S. Wang and S. Zhang, Catal. Commun., 2010, 11, 1003–1007 CrossRef CAS.
- Z. Wu, K. Yu, S. Zhang and Y. Xie, J. Phys. Chem. C, 2008, 112, 11307–11313 CrossRef CAS.
- S. Q. Li, Y. J. Diao, Z. J. Yang, J. M. He, J. Wang, C. C. Liu, F. M. Liu, H. Y. Lu, X. Yan, P. Sun and G. Y. Lu, Sens. Actuators, B, 2018, 276, 526–533 CrossRef CAS.
- W. StoBer, A. Fink and E. Bohn, J. Colloid Interface Sci., 1968, 26, 62–69 CrossRef.
- J. Huang, M. Antonietti and J. Liu, J. Mater. Chem. A, 2014, 2, 7686 RSC.
-
Compiling group, Huaxue Qiye Kongqizhong Youhai Wuzhi Ceding Fangfa, Chemical Industry Press, Beijing, 1983 Search PubMed.
- Y. Zhao, C. Ge and Y. Liang, Huaxue Fenxi Jiliang, 2016, 25, 77–79 Search PubMed.
- W. Moser, R. A. Chalmers and A. G. Fogg, J. Inorg. Nucl. Chem., 1965, 27, 1–40 CrossRef.
- A. G. Fogg, W. Moser and R. A. Chalmers, Anal. Chim. Acta, 1966, 36, 248–251 CrossRef CAS.
- R. W. Stevens, R. V. Siriwardane and J. Logan, Energy Fuels, 2008, 22, 3070–3079 CrossRef CAS.
- S. Sjostrom and H. Krutka, Fuel, 2010, 89, 1298–1306 CrossRef CAS.
- H. G. Stenger, K. Hu and D. R. Simpson, Gas Sep. Purif., 1993, 7, 19–25 CrossRef CAS.
Footnote |
† Electronic supplementary information (ESI) available. See DOI: 10.1039/d0an00621a |
|
This journal is © The Royal Society of Chemistry 2020 |
Click here to see how this site uses Cookies. View our privacy policy here.