DOI:
10.1039/D4MH00793J
(Review Article)
Mater. Horiz., 2024,
11, 5874-5894
Multifunctional microwave absorption materials: construction strategies and functional applications
Received
21st June 2024
, Accepted 20th August 2024
First published on 22nd August 2024
Abstract
The widespread adoption of wireless communication technology, especially with the introduction of artificial intelligence and the Internet of Things, has greatly improved our quality of life. However, this progress has led to increased electromagnetic (EM) interference and pollution issues. The development of advanced microwave absorbing materials (MAMs) is one of the most feasible solutions to solve these problems, and has therefore received widespread attention. However, MAMs still face many limitations in practical applications and are not yet widely used. This paper presents a comprehensive review of the current status and future prospects of MAMs, and identifies the various challenges from practical application scenarios. Furthermore, strategies and principles for the construction of multifunctional MAMs are discussed in order to address the possible problems that are faced. This article also presents the potential applications of MAMs in other fields including environmental science, energy conversion, and medicine. Finally, an analysis of the potential outcomes and future challenges of multifunctional MAMs are presented.
Wider impact
Numerous microwave absorbing materials (MAMs) have been developed to reach satisfactory EM wave absorbing performances in the past decade, but the practical applications of MAMs remain limited and have not been widely adopted. This discrepancy can be attributed to the fact that MAMs in the civilian domain must fulfil basic EM absorption requirements (stronger absorption efficiency, wider absorption band, lower density, and thinner match thickness) while also possessing multifunctional characteristics for various modern technological applications and specific application scenarios. Given the multitude of difficulties associated with the practical application of MAMs, it is evident that a comprehensive understanding of the limitations of conventional MAMs and an overview of recent advancements in multifunctional MAMs are essential. Based on recently reported studies, we discuss what are the major mechanism and theoretical support of various functions, and how to design a multifunctional MAM. And we provide a number of examples to demonstrate the feasibility of multifunctional MAMs. Furthermore, we also present new and diverse applications of MAMs in fields like environmental science, energy conversion, and medicine. This expansion presents exciting opportunities for interdisciplinary collaboration and progress, underscoring the versatility and impact of MAMs across various domains. We believe that this review can provide guidance for the design and applications of multifunctional MAMs.
|
1. Introduction
The rapid advancement of radar technology during World War II prompted a search for methods to reduce the ability of aircraft and submarines to be detected by electromagnetic (EM) waves. Additionally, the development of wireless communication technology has led to the gradual application of this technology in civilian areas, such as the internet and the Internet of Things, which has played a profound impact on people's daily lifestyles.1–3 However, as shown in Fig. 1, the application of these technologies has also resulted in a considerable increase in the number of EM pollutants in the human living environment. The impact of EM pollution on human well-being can be broadly categorized into two areas: (1) interference with the operation of precision electronics, such as on-board radar in self-driving or assisted-driving cars, potentially leading to vehicular collisions;4–6 (2) adverse effects on physical health, including sleep patterns, cell growth, and transcription factor expression and function.7–9 In parallel with the proliferation of wireless electronic devices, solving the resulting considerable EM pollution problems has become a matter of urgency. Microwave absorbing materials (MAMs), which can effectively convert EM waves into heat and other energy, have been demonstrated to be efficacious in the radar stealth and EM pollution mitigation.10–12 Despite the significant advances of MAMs made in laboratory settings over the past few decades, the practical applications of MAMs remain limited and have not been widely adopted.13,14 This discrepancy can be attributed to the fact that MAMs in the civilian domain must fulfil basic EM absorption requirements (stronger absorption efficiency, wider absorption band, lower density, and thinner match thickness) while also possessing multifunctional characteristics for various modern technological applications and specific application scenarios.
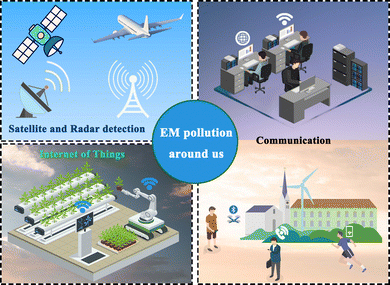 |
| Fig. 1 The advent of wireless communication technology has profoundly altered the manner in which human beings interact with one another and the world around them. However, this technological revolution has also introduced a multitude of complex EM environments. | |
With the gradual deployment of 5G technology across the globe, applications such as self-driving cars, telemedicine, virtual reality (VR), and augmented reality (AR) are progressively being realized. Nevertheless, the challenge of managing and controlling EM radiation generated by these technologies has also emerged as a significant issue in the research and engineering applications of MAMs. It is very challenging for traditional MAM coatings to fulfill the current diversified requirements for EM wave management due to the extensive application of emerging technologies and the increasing complexity of the EM environment. For example, in addition to the excellent EM wave absorbing performance, MAMs utilized in the building materials often require good sound absorption and thermal management capabilities to create an environment that meets the needs of human habitation.15,16 To ensure the durability and long service life in humid, salt spray and extreme environments, MAMs must also exhibit robust hydrophobic properties, chemical resistance, and antimicrobial capacity.17–19 To meet the requirements for miniaturization and highly integrated components of miniature smart wearable devices, MAMs should have the lowest possible density while integrating sensing functions, flexibility, and EM wave absorbing performance.20,21 Besides, it is vital to develop self-adaptive and intelligent MAMs for dynamic EM wave management and control, which possess greater flexibility and adaptability in different application scenarios.22,23 In conclusion, research on MAMs should consider not only their EM wave absorbing performance but also the needs of environmental adaptability, intelligence and multifunctional integration with the development of an intelligent era (Fig. 2).
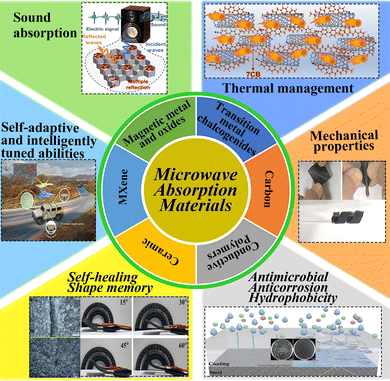 |
| Fig. 2 Classification and multifunctional scalability of advanced microwave absorbing materials. Image for “Sound absorption”: reproduced with permission.24 Copyright 2024, Springer Nature. Image for “Thermal management”: reproduced with permission.25 Copyright 2023, John Wiley and Sons. Image for “Mechanical properties”: top part: reproduced with permission.26 Copyright 2019, John Wiley and Sons. Bottom part: Reproduced with permission.27 Copyright 2023, Springer Nature. Image for “Antimicrobial, Anticorrosion, Hydrophobicity”: reproduced with permission.28 Copyright 2023, Springer Nature. Image for “Self-healing, Shape memory”: reproduced with permission.29 Copyright 2022, John Wiley and Sons. Image for “self-adoptive and intelligently tuned abilities”: reproduced with permission.30 Copyright 2024, John Wiley and Sons. | |
Since 2000, a notable increase in publications on the field of MAMs suggests that EM pollution has attracted significant attention globally. Consequently, researchers have explored various methodologies to enhance the EM wave absorbing performance of MAMs, including micro–nanostructures, interface engineering, and component systems.31–35 However, these discussions have not adequately addressed the challenges MAMs encounter in complex real-world environments, as these issues are not the primary focus of the papers. Given the multitude of difficulties associated with the practical application of MAMs, it is evident that a comprehensive understanding of the limitations of conventional MAMs and an overview of recent advancements in multifunctional MAMs are essential. This article, therefore, examines the limitations of conventional MAMs and outlines their multifunction scalability as a strategy to resolve the possible challenges in future applications. By reviewing recent advancements, this paper highlights the transition from traditional MAMs to multifunctional materials capable of adapting to complex applications. This review is structured as follows: Section 2 discusses conventional MAMs, detailing their inherent limitations. Section 3 explores multifunctional MAMs, emphasizing their additional functions beyond EM wave absorbing performance. Finally, Section 4 examines interdisciplinary applications of MAMs, highlighting their potential in various fields.
2. Conventional MAMs: from single to multi-component systems
The Maxwell's equations establish a relationship between the transmission properties of EM waves (such as reflection, absorption, and transmission) and the intrinsic EM parameters of materials.36,37 However, it is often difficult for single-component materials to simultaneously achieve the high absorption efficiency and broader absorbing bandwidth due to the interplay between impedance matching characteristics and attenuation mechanisms.38,39 To overcome this challenge, component engineering plays a key role in balancing impedance matching with attenuation capabilities.40–42 Therefore, conventional MAMs have evolved from single-component to more complex multi-component systems, thereby improving EM wave absorbing performances. This section provides a comprehensive review of the development and inherent limitations of conventional MAMs.
2.1 Magnetic metals and magnetic metal oxides
The study of metals has been a constant throughout human history, from the earliest civilizations to the present day. Metals, particularly magnetic metals, have been extensively studied due to their exceptional magnetic response characteristics and cost-effective preparation.43,44 In the field of magnetic metal-based MAMs, Che and his group have made significant contributions in enhancing magnetic properties through various strategies.45–49 For instance, using a magnetic field induced strategy, they designed one-dimension core–shell structured bimetallic magnetic chains. The obtained results indicated that magnetic coupling is significantly facilitated due to the oriented magnetic chain structure. And the off-axis electron holographs further confirmed the stronger magnetic coupling interaction in magnetic chains (Fig. 3a).50 Besides, doping engineering is also an effective way to modulate the magnetic properties.51–53 For example, Lv et al. measured the EM parameters of 11 kinds of FeCoNi alloy with different proportions of Fe, Co, and Ni elements. The obtained results implied that the addition of Ni to FeCo alloy could improve the ferromagnetic resonance and natural loss, which has a significant effect on the loss of EM waves. Micromagnetic simulation further revealed that the magnetic moments at the edge regions vibrated more violently during a single period as the Ni content increased, indicating more intensive energy dissipation.54
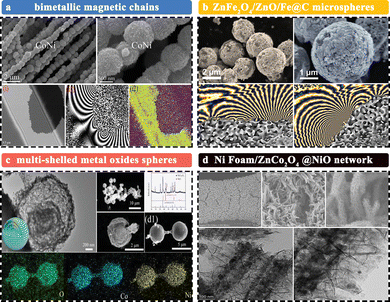 |
| Fig. 3 (a) and (b) SEM and off-axis electron holographic analysis of CoNi magnetic chains and ZnFe2O4/ZnO/Fe@C microspheres; reproduced with permission.50,55 Copyright 2020 and 2023, John Wiley and Sons. (c) Morphology and EDS mapping of multi-shelled NiCo2O4/NiO hollow spheres; reproduced with permission.56 Copyright 2021, John Wiley and Sons. (d) Morphology and structure of the Ni foam/ZnCo2O4@NiO network; reproduced with permission.57 Copyright 2022, Elsevier. | |
However, it should be noted that magnetic metals have a notable tendency to self-corrode, thereby limiting their long-term use in high oxygen and humidity environments. Consequently, magnetic metal oxides are regarded as promising alternatives, due to higher stability and adjustable magnetic properties and electronic structure.58–60 For example, Che et al. fabricated core–shell ZnFe2O4/ZnO/Fe@C microspheres with a rich heterogeneous interface via confined growth. By adjusting the molar ratio of Fe/Zn, the heterogeneous interface and conductivity of the as-prepared sample could be effectively regulated, thus improving the dielectric loss capability. Moreover, the stray magnetic field distribution revealed an enhanced magnetic coupling network constructed by the magnetic components (ZnFe2O4 and Fe) both inside and outside the material, further attenuating incident EM waves (Fig. 3b).55 Despite the aforementioned advancements, the high density of metals and metal oxides places a significant limitation on their use in aerospace and other mass-sensitive fields. To tackle this problem, researchers have attempted to achieve lighter weight in terms of the design of morphology and micro–nanostructures of a material.61,62 As shown in Fig. 3c, Wu et al. developed a series of multi-shelled metal oxide hollow spheres, which exhibit a lower density about 41.1 mg cm−3. And different M2+ of multi-shelled Co-based MCo2O4 hollow spheres also effectively facilitated defect induced polarization loss.56 Similarly, Qi et al. constructed novel mixed-dimensional heterostructures comprised of Ni Foam, NiO nanosheets and ZnCo2O4 nanowires (Fig. 3d). This mixed-dimensional structure provided numerous interfaces under the reduced density, effectively enhancing the dielectric loss capability.57 In conclusion, the density of materials can be effectively reduced via the application of morphology design (e.g., quantum dots, nanosheets, nanowires) and structure engineering (e.g., hollow, yolk shells, foams).5,63
Although the progress made in the design of magnetic MAMs has expanded their range of applications, there are still inherent obstacles that have not been completely circumvented. Two of these challenges are the corrosion and Curie temperatures. The durability and dependability of MAMs under extreme conditions remain significant constraints. Further research is needed to develop magnetic MAMs that can withstand corrosive and high temperature environments without compromising their magnetic properties.
2.2 Transition metal chalcogenides
Compared to the O element, the larger atomic radii and multiple coordination modes of chalcogen group elements (such as S, Se, and Te) render the electronic states of transition metal chalcedonics (TMCs) more susceptible to modulation. This regulation of the energy band structure enables TMCs to exhibit the transition from superconductors to insulators.64–66 Therefore, TMCs with an easily modifiable energy band structure and conductivity are particularly well-suited for utilization in the field of MAMs.67–69 For example, Wu and his group constructed a spiny globose-like NiCo2X4 (X = O, S, Se, Te) and the energy band and conductivity of the as-prepared samples can be manipulated by regulating the chalcogen group elements. Additionally, due to the improved conductive loss and impedance matching characteristics, the effective absorption bandwidths (EAB) of NiCo2Se4 and NiCo2Te4 could reach 5.28 and 4.88 GHz, respectively (Fig. 4a).70 Similarly, Qi et al. employed an anion regulating strategy to design hollow carbon shell@MoSxSe2−x (x = 0.2, 0.6 and 1.0) nanocomposites (Fig. 4b). The incorporation of the S element allowed for the modulation of the energy bandgap and an increase in the concentration of S vacancies, thereby simultaneously improving both conductive and polarization loss capacities.71 In summary, the chalcogenide group elements enable TMCs to exhibit highly adjustable EM behavior, impedance matching characteristics, and EM wave absorbing performance.
 |
| Fig. 4 (a) The schematic synthesis process, SEM images, complex permittivity, and 3D reflection loss curves of NiCo2X4; reproduced with permission.70 Copyright 2021, Elsevier. (b) Morphology, XRD, XPS and complex permittivity of hollow carbon shell@MoSxSe2−x (x = 0.2, 0.6 and 1.0) composites; reproduced with permission.71 Copyright 2023, Springer Nature. | |
Transition metal dichalcogenides (TMDs, e.g., MoS2, MoSe2, WS2, WSe2), as a special class of TMCs, have a distinctive two-dimensional graphene-like morphology. This morphology provides TMDs with a larger specific surface area, longer electron transport paths, and faster electron mobility.72,73 For instance, Cao and co-workers developed a range of nanocomposites based on 2D TMDs, including MoS2/Fe3O4, WS2/rGO, WSe2/Co3O4/CNTs, NbS2/rGO, VSe2/CNTs, and VS2/NiO.74–79 In addition, Table 1 presents an overview of a significant number of recently reported TMD-based MAMs.74–93 In summary, the multilayer nanosheet structure of TMDs allows for repeated reflection and absorption of EM waves between the nanosheets, while the large specific surface area of TMDs enhances the interfacial effects.71,94 Therefore, to make effective use of the large specific surface area of TMDs, Qi et al. constructed a 3D hierarchical network heterostructure of rGO foam/MoS2 nanosheet composites by chemical vapor deposition and hydrothermal routes. This composite showed rich interfaces, thereby contributing to enhanced interfacial effects and interfacial polarization loss.95 However, it is worth noting that 2D/2D structures are able to maximize interfacial effects more than other structures like 0D/2D, 1D/2D, and 3D/2D.96–98 Therefore, based on previous work, Qi et al. further designed rGO/MoX2 (X = S, Se) van der Waals heterojunctions, which allow for effective modulation of the interfacial effect by adjusting the ratio of rGO and MoX2. Experimental and theoretical calculation results together demonstrated that the 2D/2D structure optimizes impedance matching and enhances interfacial polarization loss, leading to the rGO/MoSe2 heterojunction exhibiting an EAB of 4.40 GHz at an ultrathin thickness of 1.35 mm.99
Table 1 Summary of the recently reported TMD-based MAMs
Material |
RLmin (dB) |
EAB (GHz) |
Thickness (mm) |
Ref. |
MoS2/Fe3O4 |
−87.24 |
5.52 |
7.83 |
74
|
WS2/rGO |
−41.50 |
3.50 |
1.70 |
75
|
WSe2/Co3O4/CNTs |
−56.90 |
6.56 |
1.41 |
76
|
NbS2/rGO |
−51.88 |
4.40 |
2.00 |
77
|
VSe2/CNTs |
−57.53 |
3.32 |
6.00 |
78
|
VS2/NiO |
−58.98 |
3.50 |
1.20 |
79
|
MoS2/carbon foam |
−45.88 |
5.68 |
2.20 |
80
|
Mo2TiC2/MoS2/Sn2S3 |
−70.60 |
3.92 |
1.88 |
81
|
CuFe2O4/MoS2 |
−40.33 |
8.16 |
2.3 |
82
|
MoSe2/MoC/C |
− 59.09 |
6.96 |
1.90 |
83
|
MoSe2@graphene |
−52.30 |
6.40 |
2.10 |
84
|
1T/2H NbS2 |
−43.85 |
6.48 |
2.07 |
85
|
WSe2/CoCu/C |
−53.43 |
6.00 |
1.80 |
86
|
SiC@WS2 |
−72.76 |
7.70 |
2.84 |
87
|
Ti3C2Tx/WS2 |
−61.06 |
6.50 |
2.50 |
88
|
MoS2/C |
−75.94 |
4.12 |
1.68 |
89
|
C/C foam@MoSe2 |
−47.98 |
8.10 |
2.70 |
90
|
Co/C@MoSe2 |
−42.00 |
5.10 |
2.50 |
91
|
2H/1T MoS2 |
−45.50 |
3.89 |
2.00 |
92
|
CoS2@MoS2 |
−58.00 |
6.24 |
2.40 |
93
|
Two-dimensional TMDs exhibit a number of advantages in terms of technical applications. Nevertheless, significant challenges remain in achieving precise control over material thickness, crystal structure, and defects. This challenge becomes particularly acute when attempting to prepare large-area TMDs, which hinders their industrial-scale application.
2.3 Carbon materials
Carbon materials, known for their diverse structures and properties, exhibit a wide range of applications in various fields.100,101 Based on dimensions, carbon materials can be classified as zero-dimensional (e.g., carbon dots, carbon spheres), one-dimensional (e.g., fibers, nanotubes), two-dimensional (e.g., graphene, carbon nanosheets), and three-dimensional (e.g., foams, aerogels).102 The strong chemical inertness and high electrical conductivity of carbon materials have made them valuable for use in MAMs.103,104 For instance, Huang et al. fabricated a graphene foam that is ultralight and compressible through solvothermal/freeze-drying/annealing treatment. The high porosity structure of graphene foam allowed significant optimization of impedance matching characteristics, which in turn facilitated the incidence of EM waves. The 3D conductive network of the graphene foam enhanced conduction loss, and compressing the graphene foam further increased the density of the conductive network, which led to rapid attenuation of EM waves. Based on the above results, the graphene foam achieved an impressive ultra-bandwidth of 60.5 GHz at 90% compressive strain (Fig. 5a).105 Additionally, Huang and his group also developed a large number of ultra-bandwidth materials based on graphene, including MWCNT/graphene foam, graphene oxide/VO2 aerogels, graphene/carbon fiber aerogels, CoTe2/RGO foam and graphene/polyaramid foam.106–110 Besides, as shown in Fig. 5b, Peng and co-workers constructed the aligned CNT film via chemical vapor deposition. By controlling the intersectional angles between the stacked CNT films, the EM parameters and attenuation capacity can be effectively modulated. The four-layered aligned CNT films with an intersectional angle of 90° exhibited a maximum reflection loss (RLmin) and EAB value of −47.66 dB and 4.4 GHz, respectively.111
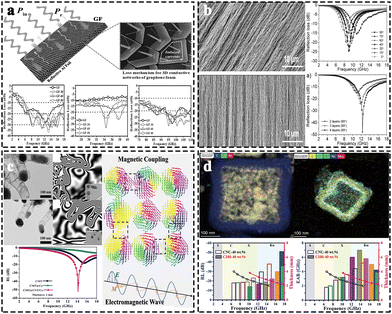 |
| Fig. 5 (a) Schematic of the conductive network in graphene foam and RL curves; reproduced with permission.105 Copyright 2015, John Wiley and Sons. (b) SEM images of stack-aligned CNTs with intersectional angles and the dependence of EAB and RL values on intersectional angles; reproduced with permission.111 Copyright 2014, John Wiley and Sons. (c) TEM images, off-axis electron holograms, RL curve and the simulated magnetic moments of hierarchically tubular C/Co nanoparticle composite; reproduced with permission.112 Copyright 2019, John Wiley and Sons. (d) EDS mapping, RL and EAB values of CoNi@void@C and CoNi@void@C@MoS2 nanocomposites; reproduced with permission.113 Copyright 2022, Springer Nature. | |
While carbon materials are advantageous in a variety of aspects, their excessive conductivity when used as MAMs may lead to impedance mismatching and a single attenuation mechanism.114,115 To overcome this problem, Che et al. proposed a magnetoelectric synergy strategy to optimize impedance matching and enhance magnetic loss. They produced a hierarchically tubular C/Co nanoparticle composite through two-step hydrothermal and carbonization treatment. The off-axis electron holography technique demonstrated that stray flux lines from Co nanoparticles can penetrate through the carbon shell, resulting in strong intrinsic magnetism and a pronounced magnetic coupling network (Fig. 5c). Thanks to the large-scale magnetic coupling and conductive network, the impedance matching, magnetic and dielectric loss capacities are enhanced, resulting in a RLmin of −52.3 dB and a broad EAB of 5.1 GHz.112 A comparable outcome can be observed with the CoNi@void@C@MoS2 composites developed by Qi et al. in Fig. 5d. The introduction of CoNi alloy and MoS2 nanosheets resulted in improvement of impedance matching and increasement of heterogeneous interfaces due to the magnetoelectric synergic effect, thus effectively enhancing the EM wave absorbing performance.113
Carbon materials still have certain limitations that need to be addressed. Firstly, carbon materials are susceptible to flammability and oxidation at elevated temperatures, which hinders their safe utilization in certain environments. Secondly, the chemical inertness of carbon materials presents a difficulty in surface functionalization and compositing with other materials. This limitation impacts their potential use in various applications such as composites, coatings, and other functional materials.
2.4 Conductive polymers
The discovery of polyacetylene in the 1970s sparked significant interest in the field of polymers, particularly in the realm of conductive polymers.116,117 Moreover, the conductivity of conductive polymers can be widely varied between insulators, semiconductors and metal conductors, thus enabling the triple conversion among EM wave transmission, absorption and shielding.118–120 Therefore, the adjustable dielectric properties of conducting polymers have positioned them as promising materials in the realm of MAMs. For instance, Wang et al. prepared CoSe2@polythiophene nanocomposites with a yolk–shell structure, as shown in Fig. 6a. The introduction of polythiophene resulted in enhanced EM parameters and improved impedance matching characteristics (Fig. 6b).121 In a similar vein, Xie et al. successfully coated polypyrrole (PPy) onto hierarchical MnO2@C nanorods. As illustrated in Fig. 6c, it can be observed that the conductivity of the prepared samples increased with the introduced PPy. The optimized sample exhibited RLmin and EAB values of −64 dB and 6.74 GHz, respectively.122
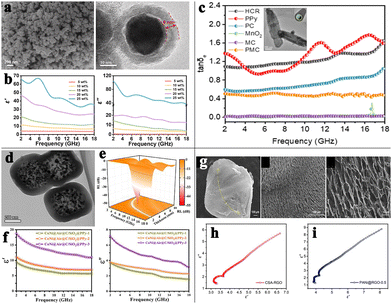 |
| Fig. 6 (a) SEM image and TEM image and (b) complex permittivity of CoSe2@polythiophene. Reproduced with permission.121 Copyright 2023, Elsevier. (c) TEM image and dielectric loss tangent of MnO2@C@PPy (PMC); reproduced with permission.122 Copyright 2023, Elsevier. (d) TEM image, (e) 3D RL curve and (f) complex permittivity of CoNi@Air@C/SiO2@PPy nanocubes; reproduced with permission.123 Copyright 2023, Elsevier. (g) SEM images and (h) and (i) Cole–Cole curves of polyaniline@rGO microspheres; reproduced with permission.124 Copyright 2023, Elsevier. | |
However, as MAMs with purely conductive loss, conductive polymers with a single attenuation mechanism have limited further improvement in EM wave absorbing performance.125,126 Therefore, Qi and his group proposed a meticulous fabrication method for CoNi@Air@C/SiO2@PPy nanocubes, involving a continuous co-precipitation/Stöber method/thermal treatment/polymerization route. The resulting nanocubes exhibited excellent magnetic–dielectric synergistic and scattering effects, thus leading to a RLmin value of −52.75 dB and EAB of 4.80 GHz (Fig. 6d–f).123 Similarly, Meng et al. developed polyaniline@rGO microspheres via the wet spinning technique (Fig. 6g). The EAB of polyaniline@rGO microspheres (7.60 GHz with a thickness of 2.80 mm) was significantly enhanced compared to rGO microspheres without polyaniline. This enhancement can be attributed to the non-homogeneous interface between graphene and polyaniline, resulting in charge accumulation and improved interfacial polarization (Fig. 6h and i).124 Generally, the regulation and optimization of the EM wave absorbing performance of a conductive polymer can be achieved by modulating the micro–nano structures and components to meet the regulation of EM properties.
Conductive polymers show great potential for application in the field of MAMs due to their unique conductivity tuning ability and excellent stability. Looking ahead, however, research will continue to explore innovative synthesis methods and design strategies to develop conductive polymer composites with superior performance and more versatile functions for a wider range of applications.
2.5 Ceramic materials
While many MAMs exhibit excellent EM wave absorbing performances at room temperature, their properties tend to deteriorate in high-temperature environments. This is particularly problematic in applications such as high-power microwave equipment, stealth fighter coatings and engines, where the physical properties of MAMs are significantly affected by elevated temperatures. Consequently, ceramic materials with exemplary mechanical properties, oxidation resistance, and high-temperature resistance are well suited for high-temperature MAMs.127,128 In the field of high-temperature MAMs, based on polymer-derived ceramics strategy, Kong and his group have recently reported a significant number of ceramic-based high-temperature MAMs, including SiBNC ceramics, SiBCNHf ceramics, SiBNCx ceramics, TiC/SiBCN, Fe–SiBCN ceramics and graphene@Fe3O4/SiBCN nanocomposites.129–134 For example, Kong et al. designed polysiloxane-derived ceramic metamaterials via a 3D printing technique as illustrated in Fig. 7a and b. By modifying the dimensions of the unit structure, the EM parameters and attenuation characteristics of Si–O–C ceramic metamaterials can be effectively tuned to achieve EAB coverage of the X band and K–Ku band, respectively. Furthermore, the passivation layer formed by SiO2 in the ceramics ensures that the obtained samples maintain stable microwave absorption properties at high temperatures (Fig. 7c and d).135 In summary, this innovative polymer-derived ceramic strategy is very favorable for the preparation of ceramic-based MAMs, which gives them great potential for applications in harsh environments.
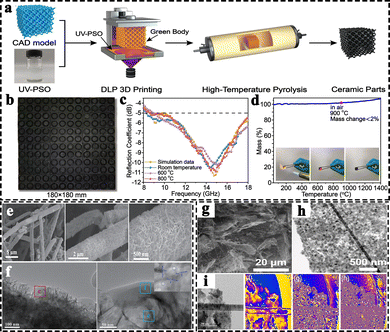 |
| Fig. 7 (a) Fabrication route, (b) photograph, (c) high temperature stability and (d) oxidation resistance of Si–O–C ceramic metamaterials; reproduced with permission.135 Copyright 2022, Springer Nature. (e) SEM and (f) TEM images of SiC@MnO2@PPy nanowires; reproduced with permission.136 Copyright 2022, Springer Nature; (g) SEM, (h) TEM and (i) charge density images of SiC aerogels; reproduced with permission.137 Copyright 2023, Elsevier. | |
In addition to applications in high-temperature environments, ceramic materials also offer a wide range of possibilities in room-temperature settings.138–140 For example, to effectively utilize structural engineering, Li et al. prepared SiC@MnO2@PPy nanowires through chemical vapor deposition and two-step electrodeposition processes. The rich heterogeneous interfaces and conductive networks promoted interfacial polarization and conductive loss (Fig. 7e and f), leading to a RLmin value of −50.59 Db and an EAB of 6.64 GHz under a thickness of 2.46 mm.136 Similarly, Fan and colleagues developed SiC aerogels using a freeze casting, carbonation and calcination process (Fig. 7g and h). This foam exhibited an EAB of 9.82 GHz at a thickness of 1.7 mm, providing coverage from 6.65 GHz to 16.47 GHz. Additionally, in Fig. 7i, the charge density images further demonstrate the accumulation of abundant charge and high-strength interfacial polarization.137
Nevertheless, it is important to acknowledge that ceramic-based MAMs come with certain disadvantages. These include their relatively high density, the need for high-temperature synthesis processes, and their inherent brittleness. These factors contribute to increased costs associated with manufacturing, maintenance and repair.
2.6 MXene
MXene is a two-dimensional material that is gaining attention due to its graphene-like layered structure, which provides it with properties such as light weight, large specific surface area, and high electrical conductivity.141–143 These characteristics make MXene a promising material for MAMs. MXene's exceptional electron transport properties and the introduced functional groups in the preparation process contribute to its impressive dielectric loss capability.144–146 For instance, Zhao et al. conducted a study where they prepared MXene nanosheets with controllability in surface functional groups and layer spacing by alkali treatment, as shown in Fig. 8a. The results of experimental and DFT calculations indicated that an increase in the layer spacing of MXene nanosheets is associated with a reduction in electrical conductivity. Besides, increasing the presence of –OH functional groups on the MXene nanosheets enhanced the conductivity in comparison to others enriched with
O and –F functional groups (Fig. 8b and d). By simultaneously adjusting the MXene surface functional groups and interlayer spacing, the impedance matching characteristics and attenuation capability can be balanced, resulting in an excellent EM wave absorbing performance.147
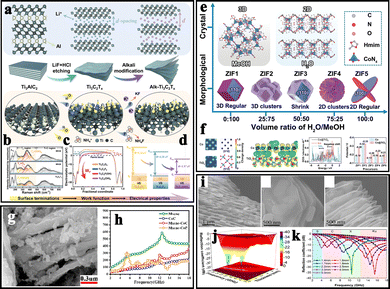 |
| Fig. 8 (a) Schematic illustration of the regulation of layer spacing and termination of MXene. (b) Raman spectra, (c) work function and (d) electrical property of MXene with different functional groups; reproduced with permission.147 Copyright 2023, John Wiley and Sons. (e) Design concepts for ZIFs with different morphologies and crystal structures and (f) effect of the built-in electric field on electronic structures; reproduced with permission.148 Copyright 2024, John Wiley and Sons. (g) SEM image and (h) attenuation constant of MXene/Co nanocomposite; reproduced with permission.149 Copyright 2021, Elsevier. (i) SEM images, (j) 3D RL and (k) RL-f curves of laminated carbon/TiO2 composites; reproduced with permission.150 Copyright 2017, American Chemical Society. | |
Due to the high conductivity of MXene, it is difficult to use it alone as a MAM. Consequently, a strategy to achieve impedance matching is to combine MXene with other materials.33,151 For example, Koo and co-workers reported a zeolitic imidazolate framework/MXene nanocomposite via an electrostatic self-assembly process. This nanocomposite exhibited a built-in electric field effect, attributed to the presence of Mott–Schottky heterointerfaces between the zeolitic imidazolate framework and MXene (Fig. 8e and f). By manipulating the built-in electric field, electron migration can be effectively modulated to promote dielectric loss capacity, thus enabling an optimized sample with an EAB up to 6.32 GHz.148 In addition, by combining MXene with Co nanochains (Fig. 8g and h), Lu et al. prepared MXene/Co nanocomposite with optimized impedance matching and magnetic loss capabilities. This enabled the sample to exhibit a RLmin value of −46.48 dB under an ultra-thin matching thickness of 1.02 mm.149
It is noteworthy that defects, edges, and vacancies of MXene are susceptible to oxidation.152,153 However, this oxidation can have both advantages and disadvantages in terms of its EM wave absorbing performance. For example, in Fig. 8i, Gogotsi et al. converted MXene into laminated carbon/TiO2 composites with a sandwich structure by annealing treatment. As the annealing temperature increased, the impedance matching and dipole polarization induced by intrinsic carbon defects were optimized and enhanced, resulting in composites with an EAB covering the entire Ku band at a thickness of 1.7 mm (Fig. 8j and k).150 Overall, despite the significant progress in MXene synthesis in recent years, the complex and costly nature of its preparation poses challenges and limits its potential for large-scale applications.
In summary, the task of achieving optimal EM wave absorbing performance using a single-component material is challenging. As a result, there has been a growing trend towards the use of multi-component MAMs through component engineering. This approach combines the advantages of different materials to enhance the overall performance of MAMs. Although conventional MAMs have made significant advancements, the need for multifunctionality in practical applications has driven the development of advanced MAMs. The following section will delve into these multifunctional MAMs and their integrated capabilities, which are designed to meet specific application requirements.
3. Multifunctional MAMs: from EM wave absorbing performance to functional diversification
In recent decades, a variety of MAMs has been devised, showcasing remarkable EM wave absorbing performances. Notable examples include graphene/NiFe2O4 composites, amorphous/crystalline γ-Fe2O3 nanosheets, and rGO/CNT/cellulose nanofibrils.154–156 However, focusing solely on EM wave absorbing performance without considering practical applications is insufficient for resolving the fundamental issues of EM pollution. For instance, while magnetic metals demonstrate exceptional low-frequency microwave absorption performances, their utility in moist settings is constrained due to a self-corrosion trend. Therefore, diverging from traditional MAMs designed for peak performance, multifunctional MAMs are rooted in practical realities, aiming to tackle more practical challenges. The primary goal of multifunctional MAMs is to maintain EM wave absorbing performance while broadening material properties to align with the demands of intricate EM landscapes and application contexts. Thus, a comprehensive understanding of a materials' inherent physical traits and an interdisciplinary perspective are crucial for advancing multifunctional MAMs. The following sections provide an in-depth analysis and categorization of multifunctional MAMs, elucidating their underlying principles and demonstrating how these materials achieve their functionalities.
3.1 Sound-absorbing property
The rapid expansion of transportation and industrial activities is concurrently intensifying the prevailing issue of environmental noise, emerging as a substantial public health concern.157,158 Consequently, both a material's sound absorption and EM wave absorbing performance have significant market potential for enhancing living environments, finding applications in diverse sectors such as building materials, recording studios, and scientific research facilities. Sound-absorbing materials can be categorized into two main types based on their structural attributes: resonance sound-absorbing materials and porous sound-absorbing materials.159,160 For resonance sound-absorbing materials, the material structure resonates when the frequency of the sound wave coincides with its intrinsic frequency, thereby resulting in significant vibration within the system. This result leads to a dramatic dissipation of sound energy. However, due to the specific resonance frequency required, the design of resonance absorbers is intricate, and the absorption band is relatively narrow.161 Porous sound-absorbing materials, characterized by interconnected pores throughout their structure, are more commonly employed for sound absorption. As sound waves traverse through these interconnected gaps and small apertures, air movement generates viscous friction and temperature elevation, thereby converting sound energy into thermal energy.162,163
To achieve excellent sound-absorbing MAMs, the following strategies can be employed: (1) composite the MAMs with other materials that have abundant pore structures; (2) construct appropriate porous structures within the MAMs. For example, as shown in Fig. 9a, Wu et al. utilized phenolic aldehyde amine as a binder to produce a flexible graphite/melamine foam with tunable impedance matching and dielectric loss properties. The resulting sample displayed an EAB of 9.8 GHz at a thickness of 2.60 mm. Besides, the results of the acoustic simulation demonstrated that the noise absorption coefficient of graphite/melamine foam can be up to 0.85 when the thickness and incident sound wave are in the ranges of 0.02–0.06 m and 2000–10
000 Hz (Fig. 9b), respectively. The effective acoustic performance is mainly attributed to the three-dimensional network and numerous pores in the foam structure, which extend the transmission path of sound waves and enhance the air vibration. This effectively converts the sound waves into mechanical and thermal energy.164 Similarly, Jiang et al. designed a hollow sphere composed of Fe/C nanosheets based on structural engineering (Fig. 9c–e). The remarkable magnetoelectric synergistic effect enabled the Fe/C nanospheres to exhibit an exceptional EM wave absorbing performance. Additionally, the high porosity and hollow structure of the Fe/C nanosphere facilitated the incidence of sound waves and increased the effective contact surfaces between the sound waves and sample, resulting in improved attenuation of the sound energy (Fig. 9f).165
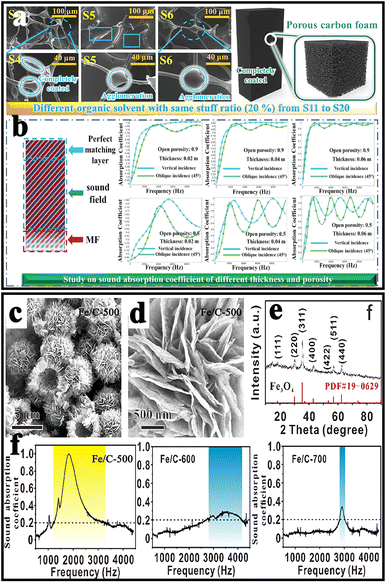 |
| Fig. 9 (a) SEM images and (b) the simulated sound absorption performance of graphite/melamine foam; reproduced with permission.164 Copyright 2023, John Wiley and Sons; (c) and (d) SEM images, (e) XRD pattern and (f) sound absorption performance of Fe/C nanospheres; reproduced with permission.165 Copyright 2023, American Chemical Society. | |
In conclusion, the design of a porous structure allows MAMs to achieve excellent absorption of sound waves.20,164 It is anticipated that a considerable portion of future building materials will integrate both sound-absorbing and EM wave absorption properties, which can provide humans with a more livable and healthy living environment. Nevertheless, the search for low-cost and durable sound-absorbing materials is still in its infancy.
3.2 Thermal management
Rapid progress in science and technology has resulted in the emergence of thermal management materials, which are indispensable for regulating heat transfer in a multitude of sectors, including electronics, automotive, aerospace, and construction. These materials play a vital role in improving equipment performance, extending device lifespan, and reducing energy consumption and emissions. Thermal management materials can be broadly categorized into two groups: thermal conductive materials and thermal insulation materials. Thermal conductive MAMs can be utilized to solve issues such as EM interference and heat accumulation in electronic products due to their high integration and miniaturization potential.20,166 On the other hand, thermal insulating MAMs can be used for both thermal and insulation requirements as well as infrared and radar stealth in military applications.167,168
It is known that heat conduction in solids primarily occurs via the thermal motion of electrons and lattice vibrations. And the thermal property mainly depends on the sum of electronic thermal conductivity and phonon thermal conductivity. Consequently, the thermal conductivity of thermal conductive MAMs can be effectively enhanced by promoting its electrical conductivity and reducing phonon scattering.169,170 Based on previous research on thermally conductive and EM functional materials,171–173 Gu and his group developed a chained CoNi/PDMS nanocomposite via a solvothermal method and polymerization (Fig. 10a and b). As illustrated in Fig. 10c and d, this as-prepared sample exhibited higher thermal conductivity compared to pure PDMS, due to the higher electrical conductivity of CoNi chains and increased thermal conduction pathways. Furthermore, the magnetic coupling effect induced by the chain structure of CoNi alloy also enhanced the magnetic loss capability and impedance matching characteristics in low-frequency.174 Additionally, considering that the graphene-like structure of BCN nanosheets helps to increase the propagation speed of phonons, Wang et al. prepared a biomass-derived BCN nanosheet utilizing coconut shells as a carbon source, as shown in Fig. 10e. Benefiting from the graphene-like structure and the interconnected nanosheets, the as-prepared sample exhibited a thermal conductivity of 0.338 W m−1 K−1 (Fig. 10f and g). And due to the synergistic effect of favorable impedance matching, dipole polarization, and multiple reflections/scattering, the EAB of optimal BCN nanosheets can reach 4.16 GHz with an exceedingly thin thickness of 1.4 mm.175 However, it is essential to note that excessive conductivity can lead to the reflection of EM waves, which complicates the simultaneous achievement of high thermal conductivity and EM wave absorbing performance in a single material.
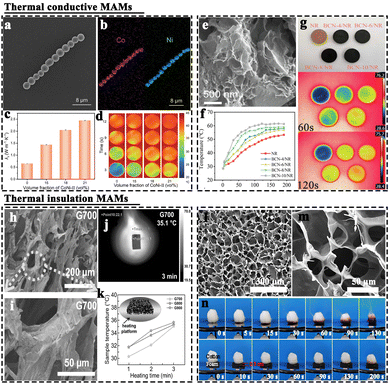 |
| Fig. 10 (a) SEM image and (b) EDS mapping of CoNi chains. (c) Thermal conductivity and (d) infrared thermal images of CoNi/PDMS; reproduced with permission.174 Copyright 2024, John Wiley and Sons. (e) SEM image, (f) surface temperature-heating time curves and (g) infrared thermal images of BCN nanosheets; reproduced with permission.175 Copyright 2022, Elsevier. (h) and (i) SEM images, (j) thermal infrared image and (k) heating time versus temperature curve of carbon aerogel; reproduced with permission.176 Copyright 2021, Springer Nature. (l) and (m) SEM images and (n) thermal isolation property of carbon foam; reproduced with permission.177 Copyright 2023, Springer Nature. | |
Conversely, the thermal insulation properties of MAMs are achieved by reducing electrical conductivity and enhancing phonon scattering. However, a reduction in electrical conductivity can diminish the dielectric loss ability, which is not beneficial to EM wave absorbing performance. Researchers have found that heterogeneous interfaces and porous structure design can enhance phonon scattering and utilize the low thermal conductive air (0.026 W m−1 K−1) in porous structures to improve the thermal insulation property.178,179 For instance, using a freeze-drying method and calcination process, Ji and his group developed a carbon aerogel with a porous structure from shaddock peel as shown in Fig. 10h and i. By varying the annealing temperature, the EM parameters and impedance matching characteristics of the prepared samples can be effectively altered to achieve an EAB of 5.8 GHz. Furthermore, the low thermal conductivity of air in the porous structure resulted in a slow warming of the samples at 70 °C (Fig. 10j and k).176 Similarly, Qi et al. prepared carbon foam with varying porous structures via freeze-drying and carbonization processes (Fig. 10l and m). The regulation of the porous structure of carbon foam can effectively modulate the EM parameters and EM wave absorbing performance, thus resulting in an EAB of 6.40 GHz at 2.56 mm. The air with low thermal conductivity in the pore structure effectively reduced the thermal conductivity of carbon foam. As a result, the cotton placed on the sample can be maintained for 2 min under the heating of an alcohol lamp without any significant change (Fig. 10n).177 Overall, constructing pore structures can confer excellent thermal insulation properties to MAMs while simultaneously maintaining their EM wave absorbing performance.18,180
3.3 Mechanical properties
Conventional MAMs are often employed as coatings or patches however, their bending or deformation may be result in flaking and peeling. Consequently, they are not well-suited for use on deformable or irregular objects. In more intricate scenarios, such as wearable electronics, MAMs must possess both flexibility and mechanical strength to adapt to irregular surface shapes and endure daily physical stresses.181,182 These materials are often engineered in the form of fibers, films, or elastomers to balance EM wave absorption, material durability, and adaptability. For instance, Fan et al. prepared SiC@SiO2 nanofiber aerogels by simple chemical vapor deposition and heat treatment routes. As shown in Fig. 11a–d, they exhibited a typical hysteresis loop due to the loss of energy during the aerogels periodic deformation. Under the 1000 cycles at 60% strain after different temperature treatments (25 °C, −196 °C and 700 °C), the small alteration in the area of the hysteresis loop demonstrated that the aerogels display remarkable toughness and resistance to fatigue. The unloading curves almost return to zero, implying complete shape recovery without plastic deformations. Besides, the synergistic effect of multiple reflections, dielectric loss and polarization loss capabilities enabled the SiC@SiO2 nanofiber aerogels to achieve a maximum EAB of 8.6 GHz.183
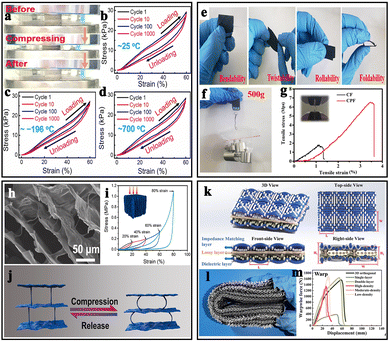 |
| Fig. 11 (a) Compression test and (b)–(d) cyclic compression stress–strain curves of SiC@SiO2 nanofiber aerogels at different temperatures; reproduced with permission.183 Copyright 2022, Springer Nature. (e) and (f) Mechanical properties and (g) stress–strain curves of cellulose nanofiber and cellulose/polyaniline nanofiber; reproduced with permission.184 Copyright 2022, Elsevier. (h) SEM image, (i) compressive stress–strain curve and (j) compression-release mechanism of MXene/aramid nanofiber/polyimide aerogels; reproduced with permission.185 Copyright 2022, Elsevier. (k) Schematic diagram of the designed polyamide@carbon/Fe3O4 textiles, (i) optical image and (m) tensile properties; reproduced with permission.186 Copyright 2023, Elsevier. | |
Here, three design strategies for the constructed flexible MAMs are summarized. Firstly, the utilization of a flexible conductive polymer can enhance the flexibility of MAMs. For example, Ji and his research group developed a cellulose/polyaniline nanofiber through the processes of electrostatic spinning and in situ polymerization. As shown in Fig. 11e–g, the sample could be freely bent and folded. The tensile stress and elongation of the as-prepared samples were determined following the coating of polyaniline compared to cellulose nanofibers. Besides, the excellent electrical conductivity of polyaniline and the constructed conductive network also resulted in the as-prepared sample exhibiting an excellent EM wave absorbing performance including a RLmin of −49.24 dB and EAB of 6.90 GHz.184 Secondly, the selection of a flexible filler or substrate material is crucial. Using polyimide as a flexible substrate, Yao et al. prepared flexible MXene/aramid nanofiber/polyimide aerogels by in situ polymerization and freeze-drying (Fig. 11h). Based on the stress–strain curves of samples under various compressive strains in Fig. 11i, three characteristic regions can be found: a linear-elastic region (<40%), implying the reversible bending of the cell walls; a plateau region (40–60%), indicating the elastic buckling of the cell walls; and a steep slope region (>60%), corresponding to the impingement of the cell walls. Benefiting from the layered structure of MXene and flexibility of polyimide, the obtained aerogels exhibited an exceptional mechanical performance (Fig. 11j).185 Finally, multi-scale structural engineering can also be an effective approach to realizing mechanical properties. For instance, as depicted in Fig. 11k and l, Fu et al. constructed polyamide@carbon/Fe3O4 textiles through the application of micro-morphological design and macro-weaving techniques. In Fig. 11m, the warpwise breaking force was enhanced when the textile was modulated from single layer to double layer, while the breaking elongation remained similar. Following the blending of the textile with PET yarns as the warp, a reduction in the breaking elongations of all samples was observed. The low-density textile exhibited the highest warpwise breaking strength, which can be attributed to the dominance of the PET yarns with good breaking strength. In contrast, the high-density textile exhibited higher warpwise breaking strength than the moderate-density textile, due to the higher warp density which resulted in greater interweaving resistance. Furthermore, by modifying the number of layers and pattern density of the textile, it is possible to enhance the mechanical properties and flexibility, while also effectively facilitating the EM wave absorption of different frequency bands.186
3.4 Hydrophobicity, antimicrobial property, and corrosion resistance
Hydrophobicity is essential for materials intended for outdoor applications, providing self-cleaning, water-repellent, and ice-resistant properties, which enhance their adaptability to various environmental conditions.187,188 Imparting hydrophobic characteristics to MAMs can prevent water infiltration, improve corrosion resistance and stabilize EM absorbing performance, thereby extending the material's service life. According to previous research studies,189,190 the construction of hydrophobic properties in MAMs can be summarized as follows: (1) reducing the surface free energy of the material through physical or chemical methods to achieve hydrophobicity, and (2) creating micro–nano structures to modify surface roughness. For instance, Yu and co-workers designed a polyacrylonitrile/polybenzoxazine/CNTs/Fe3O4 hybrid aerogel employing the low surface free energy of polybenzoxazine. The contact angles of the samples remained largely unchanged after the increased addition of CNTs, indicating that the strong hydrophobicity of the samples was primarily due to the polybenzoxazine component (Fig. 12a and b). Thanks to the synergistic effect between the organic (polyacrylonitrile and polybenzoxazine) and inorganic components (CNTs and Fe3O4), the as-prepared sample demonstrated the multifunctional potential of MAMs.191 Furthermore, by freeze-drying and atomic layer deposition, Liu et al. prepared a MoS2/MXene aerogel EM wave absorber with tunable surface roughness (Fig. 12c–e). With the increase in atomic layer deposition cycles, there was a significant increase in the number of MoS2 nanosheets, which led to the enhanced surface roughness of the MoS2/MXene aerogel. The contact angle test further demonstrated that the progressively rougher surface remarkably improved the hydrophobicity (Fig. 12f and g). And the rough surface is conducive to the expansion of specific surface area, facilitating the multiple reflections and scattering of EM waves.192
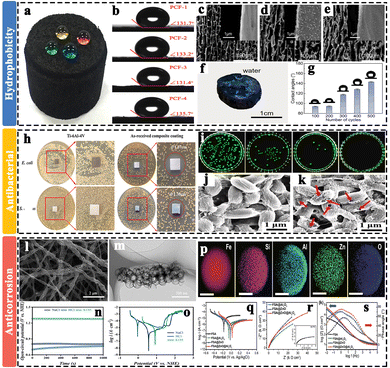 |
| Fig. 12 (a) Hydrophobicity and (b) water contact angle of hybrid aerogels with different CNT additions; reproduced with permission.191 Copyright 2018, John Wiley and Sons. (c)–(e) SEM images, (f) hydrophobicity and (g) water contact angle of MoS2/MXene aerogels with different surface roughness; reproduced with permission.192 Copyright 2022, John Wiley and Sons. (h) Antibacterial performance of the precursor and Co(Ni, Ag)/Fe(Al, Cr)2O4 coatings, reproduced with permission.193 Copyright 2022, American Chemical Society. (i) Antibacterial performance and SEM images before (j) and after (k) treatment of Cu2O@NiCo2O4/RGO; reproduced with permission.194 Copyright 2022, Elsevier. (l) SEM, (m) TEM images, (n) open-circuit potential curves and (o) Tafel curves of carbon/polyacrylonitrile nanofibers; reproduced with permission.195 Copyright 2024, John Wiley and Sons. (p) EDS mapping and (q)–(s) electrochemical testing of FeSiAl@ZnO@Al2O3 nanocomposites; reproduced with permission.196 Copyright 2021, Springer Nature. | |
It is inevitable that EM wave absorbing fabrics and wearable electronic devices will make contact with the human body during use process, and sweat secreted by the human body will lead to the growth of bacteria on the fabrics and devices. Furthermore, the bacteria on the material surface will also lead to localized corrosion of the material.197,198 Therefore, MAMs with an antibacterial effect also have better adaptability to complex application scenarios. In order to enhance the antibacterial properties of MAMs, numerous researchers have explored the introduction of nanomaterials (e.g., Ag and Cu nanoparticles) into MAMs, which have the ability to significantly inhibit bacterial growth.199,200 For example, Xu et al. prepared Co(Ni, Ag)/Fe(Al, Cr)2O4 coatings with excellent EM wave absorbing properties by sputter deposition. As illustrated in Fig. 12h, disk diffusion tests displayed that the Co(Ni, Ag)/Fe(Al, Cr)2O4 coatings exhibited a pronounced inhibitory effect in comparison to the untreated coating.193 Similarly, Chen et al. synthesized core–shell structured Cu2O@NiCo2O4/RGO nanocomposites via a simple hydrothermal method. The samples exhibited an EAB of 6.64 GHz, which was attributed to the large specific surface area and excellent dielectric loss capability. Moreover, the prepared samples presented excellent long-term antimicrobial activity due to the synergistic effect of the continuous release of Cu ions and the reactive oxygen molecules generated by photocatalysis (Fig. 12i–k).194
In environments prone to corrosion, such as humid atmospheres, seawater, and acidic or alkaline soils, MAMs including metal-based materials, are susceptible to degradation and failure. Therefore, designing corrosion-resistant MAMs is essential to ensure long-term performance. One effective approach is selecting MAMs with high chemical stability to combat corrosion. For instance, Qi and co-workers developed a necklace-like carbon/polyacrylonitrile nanofiber via an electrostatic spinning-carbonization-etching strategy. The strong chemical inertness of carbon and polyacrylonitrile enabled the carbon/polyacrylonitrile nanofiber to maintain a high impedance modulus after a week of immersion in a strong alkaline solution (Fig. 12l–o). More importantly, the necklace-like carbon/polyacrylonitrile nanofiber showed an excellent EM wave absorbing performance with a RLmin value of −44.73 dB and a EAB of 6.60 GHz.195 Additionally, constructing suitable micro–nano structures can effectively prevent the penetration of corrosive mediums, thus preventing the corrosion of materials.201,202 For example, Deng et al. prepared a core–shell structured FeSiAl@ZnO@Al2O3 nanocomposite via atomic layer deposition, which exhibits an EAB covering the L and S bands at low frequencies. Electrochemical tests indicated that all FeSiAl-based nanocomposites exhibit enhanced corrosion resistance compared to pure FeSiAl alloy. Particularly, as shown in Fig. 12p–s, the FeSiAl@ZnO@Al2O3 sample with two oxide layers showed the most significant enhancement, indicating that the atomic-level oxide layers effectively blocked the penetration of corrosive media.196 Moreover, integrating hydrophobicity and antimicrobial properties into MAM designs represents a promising approach to further enhance corrosion resistance.203,204
3.5 Self-healing and shape memory function
As electronic products continue to evolve towards miniaturization, integration, intelligence, and wearability, the MAMs used in flexible electronic devices face the mechanical damage caused by repeated bending, stretching, and twisting. Introducing self-healing capabilities to MAMs enables autonomous restoration post-damage, offering another pathway to enhance stability and extend operational longevity. The self-healing of materials is achieved via the presence of reversible bonds, including dynamic covalent bonds such as acyl, imide, and disulfide bonds, as well as physical interactions such as hydrogen bonds and electrostatic interactions.205–207 Given that the majority of self-healing materials are organic polymers with limited electrical conductivity and dielectric loss capabilities, researchers frequently select the strategy of uniformly incorporating MAMs into the self-healing material (utilizing the self-healing material as a filler) in order to achieve both EM wave absorbing performance and self-healing function. For example, employing the self-healing capacity of poly(vinylidene fluoride-hexafluoropropylene)/dibutyl phthalate (PHB), Yao et al. constructed multifunctional carbon@(medium entropy alloy/oxide)/PHB composites with an integrated EM wave absorbing performance and self-healing property. The resulting samples can achieve 90% self-healing within 3 hours post-fracture, maintaining EM parameters similar to the original sample (Fig. 13a–c).208 Similarly, Zhang et al. developed self-healing MAMs by dispersing S-doped NiSe/rGO into self-healing polyurethane. As illustrated in Fig. 13d, the optimized sample exhibited a self-healing property after 24 hours at room temperature. It is well established that a precipitous decline in the stress–strain curves is indicative of a fracture in the samples. In Fig. 13e, as the healing time increases, the stress–strain curves of the fracture samples gradually approached the initial curve, suggesting that the material is capable of fully recovering both the elastic properties and the plastic deformation of the original sample after fracture. Furthermore, appropriate heat treatment can facilitate the self-healing rate of a fractured sample.209 However, incorporating self-healing polymers as fillers for MAMs can lead to reduced self-healing efficacy or failure when the filler ratio is too high. Thus, the challenge lies in striking an optimal balance between self-healing properties and EM wave absorption performance in self-healing MAMs.
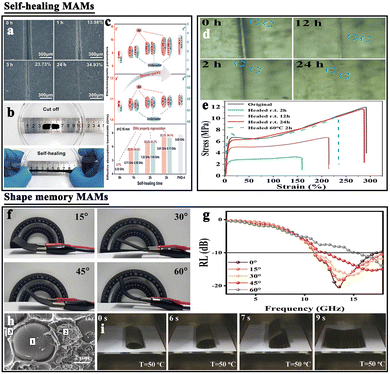 |
| Fig. 13 (a) Microscope pictures and (b) digital photos of underwater self-healing. (c) EM parameters and EAB before and after self-healing; reproduced with permission.208 Copyright 2023, John Wiley and Sons. (d) Microscopy images of the healed S-doped NiSe/rGO/polyurethane film and (e) stress–strain curves of the self-healed S-doped NiSe/rGO/polyurethane film with different healing times; reproduced with permission.209 Copyright 2024, American Chemical Society. (f) Electricity-driven deformation process of Co/N-doped carbon/graphene/PCL/TPU and (g) RL curve with different EM wave incident angles; reproduced with permission.29 Copyright 2022, John Wiley and Sons. (h) SEM image and (i) heat-driven deformation processes of cell-structured epoxy/Ba-ferrite/CNTs/polyvinyl butyral composites; reproduced with permission.210 Copyright 2023, Elsevier. | |
In the majority of published works, the evaluation of EM wave absorbing performance is typically conducted with EM waves incident perpendicular to the surface of the material.80,153 However, EM waves in the living environment often propagate from different angles. A significant number of research studies have demonstrated that the incidence of EM waves from different angles has a pronounced impact on the EM wave absorbing performance.211,212 Shape memory function in MAMs allows for shape changes in response to stimuli like heat, light, electricity, and magnetic fields, enabling EM wave absorption in specific orientations. For instance, utilizing the shape memory effect of PCL/TPU, Zhou et al. designed Co/N-doped carbon/graphene/PCL/TPU nanocomposites. By leveraging the temperature-based shape memory effect of PCL, they could modulate the bending angle of the film by varying the duration of applied voltage. And as shown in Fig. 13f and g, the alteration of the angle maximizes the absorption of EM waves in a specific direction.29 Besides, Zhou et al. designed a cell-structured epoxy/Ba-ferrite/CNTs/polyvinyl butyral composite where CNT/polyvinyl butyral acted as a cell wall around the epoxy core, with Ba-ferrite filling the interstitial spaces (Fig. 13h). This special structure leads to elasticity during thermal movement of the epoxy spheres and polyvinyl butyral/CNTs, allowing the film to return to its original shape (Fig. 13i). And thanks to the attenuation capability and impedance matching of the prepared samples, the EAB can be reach 11.5 GHz with a thickness of only 0.3 mm.210 In summary, research on MAMs in terms of shape memory is still in its early stages, and further exploration is necessary due to the relatively limited ways in which these materials currently respond to shape memory stimuli. Both self-healing and shape memory MAMs show promise for diverse applications, but their complex mechanisms pose challenges for maximizing their functions alongside EM wave absorption performance.
3.6 Self-adaptive and intelligently tuned abilities
Conventional MAMs are typically static, meaning that their physical and chemical properties are fixed after they are prepared. And they exhibit optimal performance only under specific conditions, such as temperature, thickness, and frequency. The transition from static MAMs to self-adaptive and intelligently tuned MAMs marks a significant advancement in material design. These new materials can dynamically adjust their performance in response to environmental changes through internal mechanisms or external stimuli, achieving broadband coverage, selecting specific absorbing frequency bands, and switching absorption/transmission performance.213 This adaptability enhances their flexibility and responsiveness to varying conditions, making them ideal for applications in stealth technology, electronic warfare facilities, protective shelters, and civil communication technology.
Despite the numerous advantages of self-adaptive and intelligently tuned MAMs, realizing their functionality is extremely challenging due to the interdisciplinary nature of their design, requiring expertise in materials science, physics, chemistry, and computer science. The design of adaptive intelligently tuned MAMs can originate from internal mechanisms (physics and chemistry), incorporating special structures or phase change materials. By leveraging the response of external stimuli like stress, temperature, light, or electric fields, variations in EM parameters can be achieved, enabling dynamic control of the EM wave absorbing performance. For instance, as shown in Fig. 14a and b, Wang et al. developed compressible carbon nanocoils/carbon foam composites through a continuous atomic layer deposition, chemical vapor deposition and carbonization route. By applying a different compressive strain to the prepared samples, they exhibited a dynamic EAB covering almost from 2 to 18 GHz (Fig. 14c and d). The modulation of EAB and RL under compressive strain primarily stems from a conductivity enhancement of increased conductive networks and variations in matching thickness based on the 1/4 wavelength theory (Fig. 14e and f).214 By utilizing phase engineering, Che and co-workers constructed a temperature-dependent V2C–VO2 EM absorber. When the temperature is increased, the change from EM wave-transparent to EM wave-absorbing behavior was triggered due to the temperature-induced insulator–metal transition of VO2. Furthermore, the EM wave absorbing performance of the absorbers remains stable even under cyclic heating–cooling conditions, demonstrating their excellent stability (Fig. 14g–i).215 Additionally, Wu and his group have fabricated an EM absorber device comprising an insulating substrate (pxylene-C)/absorber layer (Sn/SnS/SnO2@C)/charge transport layer (MWCNTs). The intrinsic dielectric properties of the device can be changed by applying voltage. Under appropriate voltage conditions, the optimized sample exhibited an EAB covering 90% of the C band, indicating an exceptional low-frequency EM wave absorbing performance (Fig. 14j–m).26
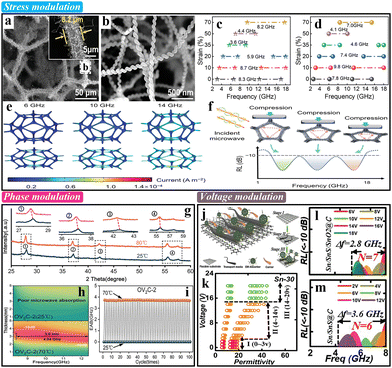 |
| Fig. 14 (a) and (b) SEM images, (c) and (d) EAB with different compression strains, (e) simulation of current density before and after compression and (f) mechanism of dynamic frequency regulation of carbon nanocoil/carbon foam composites; reproduced with permission.214 Copyright 2022, John Wiley and Sons. (g) In situ XRD spectra, (h) EM wave absorbing performance at different temperatures and (i) cyclic stability of EM wave absorbing performance switching of V2C–VO2; reproduced with permission.215 Copyright 2023, John Wiley and Sons. (j) Schematic diagram of the voltage-driven device, the dependence of voltage on (k) permittivity and (l) and (m) EAB; reproduced with permission.26 Copyright 2019, John Wiley and Sons. | |
The development of MAMs with adaptive and intelligent regulation capabilities has been a challenging task. While adaptive MAMs have been researched for some time, they often rely on external inputs such as changing stress, electric voltage, or temperature to exhibit their adaptive behavior.216,217 This reliance on external stimuli poses a significant obstacle for real-time applications of MAMs. Creating MAMs that can autonomously regulate their properties without the need for external inputs is highly desirable but remains extremely difficult to achieve. Therefore, based on an artificial neural network, Chen et al. proposed an intelligent EM invisible system, which is comprised four key components: tunable reconfigurable metasurface inclusion (self-adaptive MAMs), a detector, pre-trained artificial neural network, and a power supply. In this system, deep learning is employed to analyze the EM wave responses detected by the detector and simultaneously adjust the tunable reconfigurable metasurface inclusion to achieve a stealth effect. Through extensive data training, the pre-trained artificial neural network can autonomously adapt and regulate the stealth system based on the detected EM waves. The training results demonstrate an impressive 85% reduction in the Radar Cross Section (RCS) of the model within milliseconds (Fig. 15a–c).218 Importantly, this system is scalable, allowing for substitution of the tunable reconfigurable metasurface inclusion with other adaptive MAMs to construct an effective stealth system.
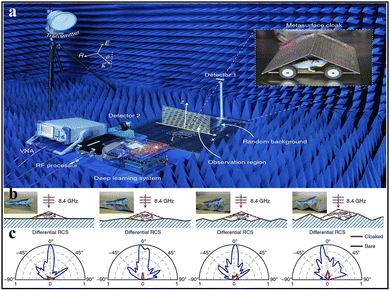 |
| Fig. 15 (a) Experimental set-up, (b) the four backgrounds and (c) the corresponding far-field differential RCS of the cloaked and bare objects; reproduced with permission.218 Copyright 2020, Springer Nature. | |
In conclusion, the field of multifunctional MAMs has witnessed remarkable advancements in recent decades. While initial research primarily focused on the EM wave absorbing performance, contemporary developments have expanded the functional scope of MAMs to address a wider array of practical applications. By integrating diverse properties such as sound absorption, thermal management, mechanical properties, hydrophobicity, antimicrobial resistance, self-healing, shape memory, and adaptive responses, multifunctional MAMs are increasingly tailored to meet the complex demands of modern technological landscapes. These innovations enhance the performance and versatility of MAMs. Overall, multifunctional MAMs have tremendous potential for future technological advancements, promising to become integral components in a wide array of applications, thereby significantly enhancing human life.
4. Interdisciplinary applications of MAMs
Initially, MAMs were predominantly used in military and industrial contexts, such as in radar stealth and EM interference protection. These materials are capable of effectively absorbing EM waves in specific frequency bands and converting them into heat or other forms of energy via magnetic and dielectric loss mechanisms, thereby reducing the reflection of EM waves. However, the potential of MAMs extends beyond their conventional applications. As scientific and technological advancements continue, researchers are discovering new and diverse applications of MAMs in fields like environmental science, energy conversion, medicine, and more. This expansion presents exciting opportunities for interdisciplinary collaboration and progress, underscoring the versatility and impact of MAMs across various domains.
4.1 Microwave responsive catalyst
Environmental pollution caused by plastics and organic waste poses a significant global challenge. One promising approach to address this issue involves utilizing catalysts to convert these materials into valuable chemicals. Heating plays a crucial role in catalytic reactions by providing the necessary energy to overcome barriers and facilitate reactant conversion. Conventional thermal catalysis relies on heat conduction and convection, often leading to uniform heating of the material and catalyst. This results in low product selectivity and energy inefficiency. In contrast, microwave radiation offers distinct advantages, such as deep penetration and concentrated energy, enabling rapid and uniform heating of a catalyst with specific EM properties. This characteristic accelerates reaction rates, improves selectivity in product formation, and generates a “hot spot” effect on the absorber's surface under microwave irradiation. The “hot spot” effect involves elevated temperatures at heterogeneous interfaces and metal sites compared to the absorber, providing additional energy for surrounding chemical reactions through heat conduction.219,220
To fully leverage the benefits of microwave catalysis, microwave-responsive catalysts need to simultaneously exhibit an exceptional EM wave absorbing performance and catalytic activity to effectively drive reactions. For instance, Edwards and co-workers utilized FeAlOx particles as a microwave catalyst to selectively convert plastic waste into hydrogen and carbon in 20 s. Their purity reached 90 vol% and 92 wt% (Fig. 16a and b). The simulation results revealed distinct interfacial polarization at the boundary between the catalyst and plastic, with the electric field strength and heating rate at this interface being three times greater than in pure plastic (Fig. 16c). This phenomenon significantly enhances the catalytic activity and selectivity of microwave catalysts.221 Moreover, microwave-responsive catalysts have found extensive applications in wastewater treatment and biomass conversion, highlighting their versatility and potential in addressing environmental challenges and promoting sustainable practices.222–224
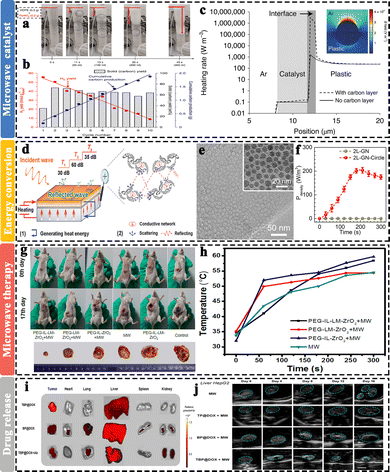 |
| Fig. 16 (a) Collection device of H2 when the microwave is turned on, (b) the yield of H2 and carbon and (c) modelling of microwave responsive catalyst; reproduced with permission.221 Copyright 2020, Springer Nature. (d) Modelling for energy conversion and the self-circulated system; reproduced with permission.225 Copyright 2018, John Wiley and Sons. (e) TEM images and (f) power density of staggered circular nanoporous graphene; reproduced with permission.226 Copyright 2023, Springer Nature. (g) Volume changes and (h) surficial temperature curves of a tumor with a microwave responder and differences in EM wave therapy; reproduced with permission.227 Copyright 2019, American Chemical Society. (i) Fluorescence images of tumors and major organs with different medicine carriers and (j) ultrasound monitoring of liver cancer with different drug carriers at different treatment times; reproduced with permission.228 Copyright 2019, American Chemical Society. | |
4.2 Energy conversion
Typically, EM waves incident on the inside of MAMs are converted into heat or other energy, which are then dissipated without beneficial use. Converting thermal energy into electrical energy represents a significant advancement in reducing EM pollution and recycling wasted energy, particularly suited for self-powered devices requiring EM protection. Given that the recovery of thermal energy is required, thermoelectric materials (TEMs) are typically combined with MAMs. It is, however, important to note that excellent thermoelectric properties require materials with lower thermal conductivity (electronic thermal conductivity and lattice thermal conductivity), higher electrical conductivity, and a higher Seebeck coefficient.229–231 Nevertheless, there is a clear positive correlation between electrical conductivity and electronic thermal conductivity and the Seebeck coefficient, which presents a challenge in the design of excellent thermoelectric materials. Furthermore, the heat generated by microwave losses is uniformly distributed, and there is not a sufficient temperature gradient for temperature difference power generation, which is also an aspect that needs to be addressed.
To overcome this challenge, Cao et al. conducted experimental and theoretical exploration of EM energy harvesters utilizing the Seebeck effect. The obtained research results demonstrated the competing and synergistic effects of EM energy harvesters in the process of EM energy conversion. Regrettably, although EM energy harvesters remain theoretical models with high feasibility, they have not yet been fully realized in practice (Fig. 16d).225 Following the model proposed by Cao, Wu and co-workers developed an EM energy harvester based on graphene with a nanopore structure in Fig. 16e. By regulating the nanopore shape and size, and number of graphene layers, a balance was achieved between the thermoelectric characteristics and the EM conversion efficiency, which was mainly attributed to the fact that the nanopores and the interleaved porous structure altered the electronic and phononic structure of graphene (Fig. 16f). Based on a high EM attenuation constant and thermoelectric conversion efficiency, the overall EM energy conversion efficiency of the EM energy harvester can reach 5.6%.226 Despite current limitations in EM energy conversion efficiency and challenges in transitioning from theoretical and experimental stages to practical applications, the potential applications of this research are highly promising. The ongoing exploration of EM energy harvesting and thermoelectric materials has significant potential for advancing sustainable energy solutions and promoting efficient utilization of EM energy in various technology.
4.3 Microwave hyperthermia therapy
Microwave hyperthermia therapy (MHT) is a non-invasive medical technology employed in tumor treatment, pain alleviation, and inflammation suppression.232–234 MHT uses microwave energy at specific frequencies to produce thermal effects in human tissues, achieving therapeutic purposes such as increasing local temperature, improving blood circulation, and promoting cell metabolism. It is important to acknowledge that during cancer treatment, while normal cells exhibit greater resistance to elevated temperatures compared to cancer cells, a significant number of normal cells in human tissues still experience cell death.232 However, advancements in nanomedicine have enabled researchers to integrate MAMs into tumor-targeting formulations. This integration ensures the efficient concentration and conduction of microwave energy, enhancing the safety and effectiveness of the treatment. For example, Meng and co-workers synthesized dual-functional nanoparticles by loading GaIn alloys (LM) and ionic liquids (IL) onto mesoporous ZrO2 nanoparticles (PEG-IL-LM-ZrO2). This combination of components presented an excellent synergistic effect, resulting in high EM energy conversion efficiency and reactive oxygen species generating capacity in tumors. As a result, the as-prepared samples were able to effectively reduce the tumor volume under microwave conditions, indicating a significant therapeutic effect on the tumor, as shown in Fig. 16g and h.227
To prevent microwave interference with radio communications, broadcasting, and radar systems, existing microwave thermotherapy typically operates within a limited frequency range of around 2.5 GHz. This limitation also restricts the utilization of high frequency MAMs. Considering the use of MAMs in the human body, biocompatibility, thermal stability, and thermal conductivity are all issues that need to be considered in addition to efficient EM heat conversion efficiency. The integration of MAMs into microwave hyperthermia therapy showcases their promising potential for enhancing treatment efficacy, minimizing side effects, and improving patient outcomes. By addressing challenges related to frequency limitations, biocompatibility, and thermal properties, researchers can further optimize the application of MAMs in medical treatments, paving the way for more effective and targeted therapeutic interventions.
4.4 Microwave-controlled drug release
With developments in medicine, a large number of new drugs are introduced every year. However, the efficacy of some drugs is often limited due to their rapid clearance in the body, poor water solubility and low cellular uptake.235 Microwave-controlled drug release has gained attention due to its non-invasive nature, deep penetration capability, and rapid heating properties. In general, microwave-controlled drug release systems consist of three components: a microwave generator, a drug carrier, and a control system. The drug is encapsulated in microwave-responsive carriers, which are capable of responding to microwaves at specific frequencies.236 When microwave irradiation is applied to the drug carrier, the absorption of microwave energy produces thermal effects, triggering changes in the carrier's structure and controlling drug release. For instance, Liang et al. conducted a study in which they utilized the microwave sensitivity of 1-butyl-3-methylimidazolium-l-lactate (BML) to create a drug carrier that responds to microwaves. This drug carrier (TBP@DOX) was prepared by encapsulating BML and the doxorubicin (drug) in liposomal nanoparticles. As illustrated in Fig. 16i and j, the researchers successfully achieved the accumulation and release of doxorubicin in hepatocellular carcinoma via exposure to microwaves. The inhibitory effect on the growth of hepatocellular carcinoma was found to be 1.95 and 1.6 times higher than that of non-targeted and non-stimuli responsive doxorubicin. Furthermore, the carrier did not cause any adverse metabolic events when compared to traditional doxorubicin chemotherapy.228 The application of microwave-controlled drug release systems offers a novel strategy to enhance drug delivery, targeting, and therapeutic outcomes. By harnessing the power of microwaves for precise and controlled drug release, researchers are paving the way for more effective and targeted drug therapies with reduced side effects and improved patient outcomes.
5. Conclusion and prospects
The evolution of MAMs from conventional single-component materials to complex multifunctional composites represents a significant advancement in addressing the challenges posed by EM pollution. This review summarizes key advancements in material composition, structure, and multifunctional integration that have significantly improved the application range of MAMs. Further analysis outlines the functional scalability and design principles of multifunctional MAMs, providing promising solutions for various application scenarios. Future research should continue to focus on optimizing the balance between multifunctional properties and highly-effective EM wave absorbing performance. Additionally, MAMs are expected to contribute significantly to other fields (environmental science, energy conversion, medicine and so on) by fostering interdisciplinary collaboration and innovation.
In the future, prospects for MAMs involve leveraging emerging technologies such as machine learning and material genome engineering. These tools can facilitate the development of a comprehensive database of multifunctional MAMs, enabling the prediction and optimization of material combinations and structures for specific applications. This approach will accelerate the discovery of novel MAMs with enhanced performance, broader application range, and integrated functionality. To illustrate, prospective military applications of smart clothing with infrared and adaptive EM stealth technology to circumvent multi-band radar detection, and its lightweight, flexible, self-healing, anti-bacterial, hydrophobic, and thermal insulation properties can also effectively safeguard the user in a multitude of austere environments. Furthermore, in addition to their highly efficient EM wave and acoustic absorption properties, the MAMs of the future will also be capable of converting the EM waves present in the surrounding environment into thermal energy, which can then be utilized for heating and power generation. This will not only result in the creation of a healthy and liveable environment, but will also lead to a reduction in energy consumption for low-carbon purposes. Overall, the continuous innovation and interdisciplinary collaboration in the field of MAMs has the potential to revolutionize various industries and improve the quality of life, making MAMs an indispensable component of modern technology and society.
Author contributions
Junxiong Xiao: conceptualization, information collection, and writing original draft. Mukun He, Beibei Zhan, Hua Guo, Jing-liang Yang, and Yali Zhang: information collection and writing original draft. Xiaosi Qi and Junwei Gu: conceptualization, writing (editing), supervision, and project administration.
Data availability
No primary research results or code have been included and no new data were generated or analysed as part of this review.
Conflicts of interest
There are no conflicts to declare.
Acknowledgements
The authors are grateful for the support from the National Natural Science Foundation of China (U21A2093 and 11964006), the Guizhou Provincial Science and Technology Projects for Platform and Talent Team Plan (GCC[2023]007), the Shaanxi Province Key Research and Development Plan Project (2023-YBGY-461), the Innovation Group of Guizhou University ([2024]08), the Fok Ying Tung Education Foundation (171095), and the Innovation Foundation for Doctor Dissertation of Northwestern Polytechnical University (CX2024094).
Notes and references
- X. X. Wang, W. Q. Cao, M. S. Cao and J. Yuan, Adv. Mater., 2020, 32, 2002112 CrossRef CAS PubMed.
- A. Al-Fuqaha, M. Guizani, M. Mohammadi, M. Aledhari and M. Ayyash, IEEE Commun. Surv. Tutorials, 2015, 17, 2347–2376 Search PubMed.
- H. Lv, Z. Yang, H. Pan and R. Wu, Prog. Mater. Sci., 2022, 127, 100946 CrossRef CAS.
- H. Lee, S. H. Ryu, S. J. Kwon, J. R. Choi, S. Lee and B. Park., Nano-Micro Lett., 2023, 15, 76 CrossRef CAS PubMed.
- A. Iqbal, F. Shahzad, K. Hantanasirisakul, M. K. Kim, J. Kwon, J. Hong, H. Kim, D. Kim, Y. Gogotsi and C. M. Koo, Science, 2020, 369, 446–450 CrossRef CAS.
- Y. Zhang, K. Ruan, K. Zhou and J. Gu, Adv. Mater., 2023, 35, 2211642 CrossRef CAS.
- L. Liu, H. Deng, X. Tang, Y. Lu, J. Zhou, X. Wang, Y. Zhao, B. Huang and Y. Shi, Proc. Natl. Acad. Sci. U. S. A., 2021, 118, e2105838118 CrossRef CAS.
- Y. Lu and Y. Shi, Bioelectrochemistry, 2023, 154, 108554 CrossRef CAS PubMed.
- B. Huang, W. Zhao, X. Cai, Y. Zhu, Y. Lu, J. Zhao, N. Xiang, X. Wang, H. Deng, X. Tang, L. Liu, Y. Zhao and Y. Shi, Int. J. Mol. Sci., 2023, 24, 11131 CrossRef CAS PubMed.
- Y. Wu, S. Tan, Y. Zhao, L. Liang, M. Zhou and G. Ji, Prog. Mater. Sci., 2023, 135, 101088 CrossRef.
- Y. Guo, K. Ruan, G. Wang and J. Gu, Sci. Bull., 2023, 68, 1195–1212 CrossRef CAS PubMed.
- X. J. Zeng, C. Zhao, X. Jiang, R. H. Yu and R. C. Che, Small, 2023, 19, 2303393 CrossRef CAS PubMed.
- X. Zhang, X. Tian, N. Wu, S. Zhao, Y. Qin, F. Pan, S. Yue, X. Ma, J. Qiao, W. Xu, W. Liu, J. Liu, M. Zhao, K. Ostrikov and Z. H. Zeng, Sci. Adv., 2024, 10, eadl6498 CrossRef CAS PubMed.
- R. Zhao, T. Gao, Y. Li, Z. Sun, Z. Zhang, L. Ji, C. Hu, X. Liu, Z. Zhang, X. Zhang and G. Qin, Nat. Commun., 2024, 15, 1497 CrossRef CAS PubMed.
- T. T. Liu, M. Q. Cao, Y. S. Fang, Y. H. Zhu and M. S. Cao, J. Mater. Sci. Technol., 2022, 112, 329–344 CrossRef CAS.
- R. Yao, S. Liao, X. Chen, G. Tang, G. Wang and F. Zheng, Ceram. Int., 2016, 42, 8179–8189 CrossRef CAS.
- G. Wang, S. J. H. Ong, Y. Zhao, Z. J. Xu and G. Ji, J. Mater. Chem. A, 2020, 8, 24368–24387 RSC.
- Y. Wang, X. Di, J. Chen, L. She, H. Pan, B. Zhao and R. Che, Carbon, 2022, 191, 625–635 CrossRef CAS.
- L. Gai, H. Zhao, F. Wang, P. Wang, Y. Liu, X. Han and Y. Du, Nano Res., 2022, 15, 9410–9439 CrossRef.
- B. X. Wang, C. Xu, G. Duan, W. Xu and F. Pi, Adv. Funct. Mater., 2023, 33, 2213818 CrossRef CAS.
- B. Li, H. Tian, L. Li, W. Liu, J. Liu, Z. Zeng and N. Wu, Adv. Funct. Mater., 2024, 34, 2314653 CrossRef CAS.
- O. Balci, E. O. Polat, N. Kakenov and C. Kocabas, Nat. Commun., 2015, 6, 6628 CrossRef CAS PubMed.
- L. Wu, S. Shi, J. Liu, X. Liu, P. Mou, J. Zhao, L. Li, L. Yu, J. Wen and G. Wang, Nano Energy, 2023, 118, 108938 CrossRef CAS.
- H. Sun, B. Yang and M. Zhang, Adv. Fiber Mater., 2024, 6, 1122–1137 CrossRef CAS.
- K. Ruan, X. Shi, Y. Zhang, Y. Guo, X. Zhong and J. Gu, Angew. Chem., Int. Ed., 2023, 62, e202309010 CrossRef CAS.
- H. Lv, Z. Yang, H. Xu, L. Wang and R. Wu, Adv. Funct. Mater., 2020, 30, 1907251 CrossRef CAS.
- S. Zhang, X. Liu, C. Jia, Z. Sun, H. Jiang, Z. Jia and G. Wu, Nano-Micro Lett., 2023, 15, 204 CrossRef CAS PubMed.
- T. Chen, Y. Tian, Z. Guo, Y. Chen, Q. Qi and F. Meng, Nano Res., 2024, 17, 913–926 CrossRef CAS.
- Y. Liu, X. Wei, X. He, J. Yao, R. Tan, P. Chen, B. Yao, J. Zhou and Z. Yao, Adv. Funct. Mater., 2023, 33, 2211352 CrossRef CAS.
- Z. Wang, C. Qian, P. Lin, B. Zheng, G. Kim, J. Noh, E. Li, J. Rho and H. Chen, Adv. Mater., 2024, 2400797 CrossRef CAS PubMed.
- M. S. Cao, X. X. Wang, M. Zhang, J. C. Shu, W. Q. Cao, H. J. Yang, X. Y. Fang and J. Yuan, Adv. Funct. Mater., 2019, 29, 1807398 CrossRef.
- S. Gupta and N. H. Tai, Carbon, 2019, 152, 159–187 CrossRef CAS.
- S. H. Kim, S. Y. Lee, Y. Zhang, S. J. Park and J. Gu, Adv. Sci., 2023, 10, 2303104 CrossRef CAS.
- M. Panahi-Sarmad, S. Samsami, A. Ghaffarkhah, S. A. Hashemi, S. Ghasemi, M. Amini, S. Wuttke, O. Rojas, K. C. Tam, F. Jiang, M. Arjmand, F. Ahmadijokani and M. Kamkar, Adv. Funct. Mater., 2023, 2304473 CrossRef.
- C. Wei, L. Shi, M. Li, M. He, M. Li, X. Jing, P. Liu and J. Gu, J. Mater. Sci. Technol., 2024, 175, 194–203 CrossRef CAS.
- Y. D. Chong and A. D. Stone, Phys. Rev.
Lett., 2011, 107, 163901 CrossRef CAS PubMed.
- N. I. Landy, S. Sajuyigbe, J. J. Mock, D. R. Smith and W. J. Padilla, Phys. Rev. Lett., 2008, 100, 207402 CrossRef CAS PubMed.
- Q. Liu, Q. Cao, H. Bi, C. Liang, K. Yuan, W. She, Y. Yang and R. Che, Adv. Mater., 2016, 28, 486–490 CrossRef CAS PubMed.
- X. Gao, X. Wang, J. Cai, Y. Zhang, J. Zhang, S. Bi and Z. L. Hou, Carbon, 2023, 211, 118083 CrossRef CAS.
- X. Liu, W. Ma, Z. Qiu, T. Yang, J. Wang, X. Ji and Y. Huang, ACS Nano, 2023, 17, 8420–8432 CrossRef CAS.
- T. Jia, X. Qi, L. Wang, J. L. Yang, X. Gong, Y. Chen, Y. Qu, Q. Peng and W. Zhong, Carbon, 2023, 206, 364–374 CrossRef CAS.
- Y. Wu, S. Tan, T. Zhang, M. Zhou, G. Fang and G. Ji, Nano Res., 2023, 16, 8522–8532 CrossRef CAS.
- Y. Han, M. He, J. Hu, P. Liu, Z. Liu, Z. Ma, W. Ju and J. Gu, Nano Res., 2023, 16, 1773–1778 CrossRef CAS.
- F. Chen, S. Zhang, B. Ma, Y. Xiong, H. Luo, Y. Cheng, X. Li, X. Wang and R. Gong, Chem. Eng. J., 2022, 431, 134007 CrossRef CAS.
- J. Liu, R. Che, H. Chen, F. Zhang, F. Xia, Q. Wu and M. Wang, Small, 2012, 8, 1214–1221 CrossRef CAS PubMed.
- L. Wang, X. Yu, X. Li, J. Zhang, M. Wang and R. Che, Chem. Eng. J., 2020, 383, 123099 CrossRef CAS.
- J. Cheng, H. Zhang, H. Wang, Z. Huang, H. Raza, C. Hou, G. Zheng, D. Zhang, Q. Zheng and R. Che, Adv. Funct. Mater., 2022, 32, 2201129 CrossRef CAS.
- P. Liu, S. Gao, G. Zhang, Y. Huang, W. You and R. Che, Adv. Funct. Mater., 2021, 31, 2102812 CrossRef CAS.
- G. Chen, R. Zhang, M. Yuan, S. Xue, Y. Liu, B. Li, K. Luo, Y. Lai, J. Zhang, H. Lv and R. Che, Adv. Mater., 2024, 36, 2313411 CrossRef CAS PubMed.
- B. Zhao, Y. Li, Q. Zeng, L. Wang, J. Ding, R. Zhang and R. Che, Small, 2020, 16, 2003502 CrossRef CAS PubMed.
- Z. Zhang, J. Yuan, G. Lian, S. Ren, Y. Du, R. Chen, W. You and R. Che, J. Alloys Compd., 2024, 988, 174175 CrossRef CAS.
- S. Lv, H. Luo, Z. Wang, J. Yu, Y. Cheng, F. Chen and X. Li, Carbon, 2024, 218, 118668 CrossRef CAS.
- Z. Zhang, W. Wang, J. Zhang, J. Chen, X. Sun, G. Sun, Y. Liang and W. Zhang, Ceram. Int., 2023, 49, 28660–28673 CrossRef CAS.
- B. Yang, J. Fang, C. Xu, H. Cao, R. Zhang, B. Zhao, M. Huang, X. Wang, H. Lv and R. Che, Nano-Micro Lett., 2022, 14, 170 CrossRef CAS PubMed.
- M. Huang, L. Wang, K. Pei, B. Li, W. You, L. Yang, G. Zhou, J. Zhang, C. Liang and R. Che, Adv. Funct. Mater., 2024, 34, 2308898 CrossRef CAS.
- M. Qin, L. Zhang, X. Zhao and H. Wu, Adv. Sci., 2021, 8, 2004640 CrossRef CAS PubMed.
- Y. Rao, X. Qi, Q. Peng, Y. Chen, X. Gong, R. Xie and W. Zhong, J. Alloys Compd., 2022, 910, 164974 CrossRef CAS.
- Y. Liu, C. Tian, F. Wang, B. Hu, P. Xu, X. Han and Y. Du, Chem. Eng. J., 2023, 461, 141867 CrossRef CAS.
- J. Qiao, Q. Song, X. Zhang, S. Zhao, J. Liu, G. Nyström and Z. Zeng, Adv. Sci., 2024, 11, 2400403 CrossRef CAS PubMed.
- F. Wang, W. Gu, J. Chen, Y. Wu, M. Zhou, S. Tang, X. Cao, P. Zhang and G. Ji, Nano Res., 2022, 15, 3720–3728 CrossRef CAS.
- C. Xu, P. Liu, Z. Wu, H. Zhang, R. Zhang, C. Zhang, L. Wang, L. Wang, B. Yang, Z. Yang, W. You and R. Che, Adv. Sci., 2022, 9, 2200804 CrossRef CAS PubMed.
- M. Tang, J. Y. Zhang, S. Bi, Z. L. Hou, X. H. Shao, K. T. Zhan and M. S. Cao, ACS Appl. Mater. Interfaces, 2019, 11, 33285–33291 CrossRef CAS PubMed.
- X. Xie, B. Wang, Y. Wang, C. Ni, X. Sun and W. Du, Chem. Eng. J., 2022, 428, 131160 CrossRef CAS.
- Y. Tokumoto, K. Hamano, S. Nakagawa, Y. Kamimura, S. Suzuki, R. Tamura and K. Edagawa, Nat. Commun., 2024, 15, 1529 CrossRef CAS PubMed.
- Y. Kim, W. J. Woo, D. Kim, S. Lee, S. M. Chung, J. Park and H. Kim, Adv. Mater., 2021, 33, 2005907 CrossRef CAS PubMed.
- P. Miró, M. Audiffred and T. Heine, Chem. Soc. Rev., 2014, 43, 6537–6554 RSC.
- H. Zhang, J. Cheng, H. Wang, Z. Huang, Q. Zheng, G. Zheng, D. Zhang, R. Che and M. Cao, Adv. Funct. Mater., 2022, 32, 2108194 CrossRef CAS.
- M. Ning, P. Jiang, W. Ding, X. Zhu, G. Tan, Q. Man, J. Li and R. W. Li, Adv. Funct. Mater., 2021, 31, 2011229 CrossRef CAS.
- Y. Yan, K. Zhang, G. Qin, B. Gao, T. Zhang, X. Huang and Y. Zhou, Adv. Funct. Mater., 2024, 2316338 CrossRef CAS.
- X. Zhou, Z. Jia, X. Zhang, B. Wang, X. Liu, B. Xu, L. Bi and G. Wu, Chem. Eng. J., 2021, 420, 129907 CrossRef CAS.
- J. Xiao, X. Qi, L. Wang, T. Jing, J. L. Yang, X. Gong, Y. Chen, Y. Qu, Q. Peng and W. Zhong, Nano Res., 2023, 16, 5756–5766 CrossRef CAS.
- Y. Wang, J. C. Kim, R. J. Wu, J. Martinez, X. Song, J. Yang, F. Zhao, A. Mkhoyan, H. Y. Jeong and M. Chhowalla, Nature, 2019, 568, 70–74 CrossRef CAS PubMed.
- H. K. Ng, D. Xiang, A. Suwardi, G. Hu, K. Yang, Y. Zhao, T. Liu, Z. Cao, H. Liu, S. Li, J. Cao, Q. Zhu, Z. Dong, C. K. I. Tan, D. Chi, C. W. Qiu, K. Hippalgaonkar, G. Eda, M. Yang and J. Wu, Nat. Electron., 2022, 5, 489–496 CrossRef CAS.
- M. Ma, Q. Zheng, Y. Zhu, L. Li and M. Cao, J. Materiomics, 2022, 8, 577–585 CrossRef.
- D. Zhang, T. Liu, J. Cheng, Q. Cao, G. Zheng, S. Liang, H. Wang and M. S. Cao, Nano-Micro Lett., 2019, 11, 38 CrossRef CAS PubMed.
- Q. Wang, B. Niu, Y. Han, Q. Zheng, L. Li and M. Cao, Chem. Eng. J., 2023, 452, 139042 CrossRef CAS.
- Y. Li, Y. Jin, J. Cheng, Y. Fu, J. Wang, L. Fan, D. Zhang, P. Zhang, G. Zheng and M. Cao, Carbon, 2023, 213, 118245 CrossRef CAS.
- M. Ma, Q. Zheng, X. Zhang, L. Li and M. Cao, Carbon, 2023, 212, 118159 CrossRef CAS.
- Z. Zhou, X. Yang, D. Zhang, H. Zhang, J. Cheng, Y. Xiong, Z. Huang, H. Wang, P. Zhang, G. Zheng and M. Cao, Adv. Compos. Hybrid Mater., 2022, 5, 2317–2327 CrossRef CAS.
- L. Lyu, F. Wang, B. Li, X. Zhang, J. Qiao, Y. Yang and J. Liu, J. Colloid Interface Sci., 2021, 586, 613–620 CrossRef CAS PubMed.
- X. Zeng, X. Jiang, Y. Ning, Y. Gao and R. Che, Nano-Micro Lett., 2024, 16, 213 CrossRef CAS PubMed.
- J. Liu, Z. Jia, W. Zhou, X. Liu, C. Zhang, B. Xu and G. Wu, Chem. Eng. J., 2022, 429, 132253 CrossRef CAS.
- T. Zhao, Z. Jia, J. Liu, Y. Zhang, G. Wu and P. Yin, Nano-Micro Lett., 2024, 16, 6 CrossRef CAS PubMed.
- Y. Zhang, L. Zhang, B. Zhou, H. Cheng, Q. Zhang and B. Zhang, Carbon, 2023, 205, 562–572 CrossRef CAS.
- H. Zhang, J. Cheng, H. Wang, Z. Huang, Q. Zheng, G. Zheng, D. Zhang, R. Che and M. Cao, Adv. Funct. Mater., 2022, 32, 2108194 CrossRef CAS.
- T. Zhao, T. Zheng, D. Lan, Y. Zhang, Z. Sun, C. Wang, Z. Jia and G. L. Wu, Nano Res., 2024, 17, 1625–1635 CrossRef CAS.
- Z. Zhao, Z. Du, X. Huang and C. Jiang, Ceram. Int., 2023, 49, 9916–9923 CrossRef CAS.
- H. Ren, S. Wang, X. Zhang, Y. Liu, L. Kong, C. Li, X. Lu and Y. Chen, J. Am. Ceram. Soc., 2021, 104, 5537–5546 CrossRef CAS.
- J. Cheng, L. Cai, Y. Shi, F. Pan, Y. Dong, X. Zhu, H. Jiang, X. Zhang, Z. Xiang and W. Lu, Chem. Eng. J., 2022, 431, 134284 CrossRef CAS.
- X. Zhao, Y. Huang, H. Jiang, X. Liu, M. Yu and M. Zong, Carbon, 2024, 224, 119063 CrossRef CAS.
- J. Su, Z. Nie, Y. Feng, X. Hu, H. Li, Z. Zhao, S. Zan and S. Qi, Composites, Part A, 2022, 162, 107140 CrossRef CAS.
- M. Q. Ning, P. H. Jiang, W. Ding, X. B. Zhu, G. G. Tan, Q. K. Man, J. B. Li and R. W. Li, Adv. Funct. Mater., 2021, 31, 2011229 CrossRef CAS.
- T. Zhu, W. Shen, X. Wang, Y. Song and W. Wang, Chem. Eng. J., 2019, 378, 122159 CrossRef CAS.
- T. Zhao, Z. Jia, J. Liu, Y. Zhang, G. Wu and P. Yin, Nano-Micro Lett., 2023, 16, 6 CrossRef PubMed.
- C. Li, Z. Li, X. Qi, X. Gong, Y. Chen, Q. Peng, C. Deng, T. Jing and W. Zhong, J. Colloid Interface Sci., 2022, 605, 13–22 CrossRef CAS PubMed.
- J. Luo, M. Feng, Z. Dai, C. Jiang, W. Yao and N. Zhai, Nano Res., 2022, 15, 5781–5789 CrossRef CAS.
- W. Xue, G. Yang, S. Bi, J. Y. Zhang and Z. L. Hou, Carbon, 2021, 173, 521–527 CrossRef CAS.
- D. Pan, G. Yang, H. M. Abo-Dief, J. Dong, F. Su, C. Liu, Y. Li, B. Bin Xu, V. Murugadoss, N. Naik, S. M. El-Bahy, Z. M. El-Bahy, M. Huang and Z. Guo, Nano-Micro Lett., 2022, 14, 118 CrossRef CAS PubMed.
- L. Xiang, A. K. Darboe, Z. Luo, X. Qi, J. J. Shao, X. J. Ye, C. S. Liu, K. Sun, Y. Qu, J. Xu and W. Zhong, Adv. Compos. Hybrid Mater., 2023, 6, 215 CrossRef CAS.
- Y. Fang, Y. Liu, L. Qi, Y. Xue and Y. Li, Chem. Soc. Rev., 2022, 51, 2681–2709 RSC.
- Z. Li, L. Deng, I. A. Kinloch and R. J. Young, Prog. Mater. Sci., 2023, 135, 101089 CrossRef CAS.
- Y. Sun, X. L. Shi, Y. L. Yang, G. Suo, L. Zhang, S. Lu and Z. G. Chen, Adv. Funct. Mater., 2022, 32, 2201584 CrossRef CAS.
- Y. Zhang, Y. Huang, H. Chen, Z. Huang, Y. Yang, P. Xiao, Y. Zhou and Y. Chen, Carbon, 2016, 105, 438–447 CrossRef CAS.
- C. Wu, J. Wang, X. Zhang, L. Kang, X. Cao, Y. Zhang, Y. Niu, Y. Yu, H. Fu, Z. Shen, K. Wu, Z. Yong, J. Zou, B. Wang, Z. Chen, Z. Yang and Q. Li, Nano-Micro Lett., 2022, 15, 7 CrossRef PubMed.
- Y. Zhang, Y. Huang, T. Zhang, H. Chang, P. Xiao, H. Chen, Z. Huang and Y. Chen, Adv. Mater., 2015, 27, 2049–2053 CrossRef CAS PubMed.
- H. Chen, Z. Huang, Y. Huang, Y. Zhang, Z. Ge, B. Qin, Z. Liu, Q. Shi, P. Xiao, Y. Yang, T. Zhang and Y. Chen, Carbon, 2017, 124, 506–514 CrossRef CAS.
- Z. Cheng, R. Wang, Y. Cao, Z. Cai, Z. Zhang and Y. Huang, Adv. Funct. Mater., 2022, 32, 2205160 CrossRef CAS.
- Y. Cao, Z. Cheng, R. Wang, X. Liu, T. Zhang, F. Fan and Y. Huang, Carbon, 2022, 199, 333–346 CrossRef CAS.
- Z. Zhang, Z. Cai, L. Xia, D. Zhao, F. Fan and Y. Huang, ACS Appl. Mater. Interfaces, 2021, 13, 30967–30979 CrossRef CAS PubMed.
- Z. Cheng, R. Wang, Y. Cao, Z. Zhang, W. Ma, T. Zhang, F. Fan and Y. Huang, ACS Appl. Mater. Interfaces, 2022, 14, 3218–3232 CrossRef CAS PubMed.
- H. Sun, R. Che, X. You, Y. Jiang, Z. Yang, J. Deng, L. Qiu and H. Peng, Adv. Mater., 2014, 26, 8120–8125 CrossRef CAS PubMed.
- Z. Wu, K. Pei, L. Xing, X. Yu, W. You and R. Che, Adv. Funct. Mater., 2019, 29, 1901448 CrossRef.
- C. Li, X. Qi, X. Gong, Q. Peng, Y. Chen, R. Xie and W. Zhong, Nano Res., 2022, 15, 6761–6771 CrossRef CAS.
- Q. Li, Z. Zhang, L. Qi, Q. Liao, Z. Kang and Y. Zhang, Adv. Sci., 2019, 6, 1801057 CrossRef PubMed.
- H. Guan, Q. Wang, X. Wu, J. Pang, Z. Jiang, G. Chen, C. Dong, L. Wang and C. Gong, Composites, Part B, 2021, 207, 108562 CrossRef CAS.
- N. Hall, Chem. Commun., 2003, 1–4 Search PubMed.
- Z. Zhao, K. Xia, Y. Hou, Q. Zhang, Z. Ye and J. Lu, Chem. Soc. Rev., 2021, 50, 12702–12743 RSC.
- M. Wang, X. H. Tang, J. H. Cai, H. Wu, J. B. Shen and S. Y. Guo, Carbon, 2021, 177, 377–402 CrossRef CAS.
- Y. Xie, Y. Guo, T. Cheng, L. Zhao, T. Wang, A. Meng, M. Zhang and Z. Li, Chem. Eng. J., 2023, 457, 141205 CrossRef CAS.
- T. Hou, Z. Jia, A. Feng, Z. Zhou, X. Liu, H. Lv and G. Wu, J. Mater. Sci. Technol., 2021, 68, 61–69 CrossRef CAS.
- C. Dong, D. Li, H. Wang, B. Cai, Y. Xin, H. Peng, Y. Zhao, N. Wang, Z. Cui and G. Wang, Carbon, 2023, 215, 118459 CrossRef CAS.
- L. Wu, H. Gao, R. Guo, W. Li, F. Wu, S. Tao, X. Zhu and A. Xie, Chem. Eng. J., 2023, 460, 141749 CrossRef CAS.
- Q. Liang, L. Wang, X. Qi, Q. Peng, X. Gong, Y. Chen, R. Xie and W. Zhong, J. Mater. Sci. Technol., 2023, 147, 37–46 CrossRef CAS.
- Y. Tian, D. Zhi, T. Li, J. Li, J. Li, Z. Xu, W. Kang and F. Meng, Chem. Eng. J., 2023, 464, 142644 CrossRef CAS.
- H. Pang, Y. Duan, L. Huang, L. Song, J. Liu, T. Zhang, X. Yang, J. Liu, X. Ma, J. Di and X. Liu, Composites, Part B, 2021, 224, 109173 CrossRef CAS.
- S. Liu, S. Qin, Y. Jiang, P. Song and H. Wang, Composites, Part A, 2021, 145, 106376 CrossRef CAS.
- Q. Xia, Z. Han, Z. Zhang, Z. Huang, X. Wang, J. Chang, Q. Chen and M. Chen, J. Mater. Chem. C, 2023, 11, 4552–4569 RSC.
- Z. Wang, Y. Hou, H. Hao, Y. Shuai and Z. Wang, Carbon, 2023, 211, 118092 CrossRef CAS.
- C. Luo, Y. Tang, T. Jiao and J. Kong, ACS Appl. Mater. Interfaces, 2018, 10, 28051–28061 CrossRef CAS PubMed.
- Y. Song, Z. Liu, X. Zhang, R. Zhu, Y. Zhang, P. Liu, L. He and J. Kong, J. Mater. Sci. Technol., 2022, 126, 215–227 CrossRef CAS.
- Y. Song, P. Liu, R. Zhou, R. Zhu and J. Kong, Carbon, 2022, 188, 12–24 CrossRef CAS.
- J. Ding, F. Chen, J. Chen, J. Liang and J. Kong, J. Am. Ceram. Soc., 2021, 104, 1772–1784 CrossRef CAS.
- Y. Song, S. Jin, K. Hu, Y. Du, J. Liang and J. Kong, J. Am. Ceram. Soc., 2021, 104, 5244–5256 CrossRef CAS.
- C. Luo, T. Jiao, J. Gu, Y. Tang and J. Kong, ACS Appl. Mater. Interfaces, 2018, 10, 39307–39318 CrossRef CAS PubMed.
- R. Zhou, Y. Wang, Z. Liu, Y. Pang, J. Chen and J. Kong, Nano-Micro Lett., 2022, 14, 122 CrossRef CAS PubMed.
- M. Zhang, L. Zhao, W. Zhao, T. Wang, L. Yuan, Y. Guo, Y. Xie, T. Cheng, A. Meng and Z. Li, Nano Res., 2023, 16, 3558–3569 CAS.
- L. Song, C. Wu, Q. Zhi, F. Zhang, B. Song, L. Guan, Y. Chen, H. Wang, R. Zhang and B. Fan, Chem. Eng. J., 2023, 467, 143518 CrossRef CAS.
- B. Zhao, Y. Du, Z. Yan, L. Rao, G. Chen, M. Yuan, L. Yang, J. Zhang and R. Che, Adv. Funct. Mater., 2023, 33, 2209924 CrossRef CAS.
- H. Zhang, H. Liu, H. Wu, M. Yuan, J. Chen, X. Yang, X. Liu and Z. Huang, J. Eur. Ceram. Soc., 2022, 42, 1249–1257 CrossRef CAS.
- J. Jiang, L. Yan, Y. Xue, J. Li, C. Zhang, X. Hu, A. Guo, H. Du and J. Liu, Chem. Eng. J., 2024, 482, 148878 CrossRef CAS.
- A. VahidMohammadi, J. Rosen and Y. Gogotsi, Science, 2021, 372, eabf1581 CrossRef CAS PubMed.
- Y. Zhao, J. Zhang, X. Guo, X. Cao, S. Wang, H. Liu and G. Wang, Chem. Soc. Rev., 2023, 52, 3215–3264 RSC.
- J. M. Cao, I. V. Zatovsky, Z. Y. Gu, J. L. Yang, X. X. Zhao, J. Z. Guo, H. Xu and X. L. Wu, Prog. Mater. Sci., 2023, 135, 101105 CrossRef CAS.
- F. Hu, X. Wang, S. Bao, L. Song, S. Zhang, H. Niu, B. Fan, R. Zhang and H. Li, Chem. Eng. J., 2022, 440, 135855 CrossRef CAS.
- H. Cheng, Y. Pan, X. Wang, C. Liu, C. Shen, D. W. Schubert, Z. Guo and X. Liu, Nano-Micro Lett., 2022, 14, 63 CrossRef CAS PubMed.
- F. Wu, Z. Liu, J. Wang, T. Shah, P. Liu, Q. Zhang and B. Zhang, Chem. Eng. J., 2021, 422, 130591 CrossRef CAS.
- Y. Du, Z. Yan, W. You, Q. Men, G. Chen, X. Lv, Y. Wu, K. Luo, B. Zhao, J. Zhang and R. Che, Adv. Funct. Mater., 2023, 33, 2301449 CrossRef CAS.
- Z. Gao, A. Iqbal, T. Hassan, S. Hui, H. Wu and C. M. Koo, Adv. Mater., 2024, 36, 2311411 CrossRef CAS PubMed.
- F. Pan, L. Yu, Z. Xiang, Z. Liu, B. Deng, E. Cui, Z. Shi, X. Li and W. Lu, Carbon, 2021, 172, 506–515 CrossRef CAS.
- M. Han, X. Yin, X. Li, B. Anasori, L. Zhang, L. Cheng and Y. Gogotsi, ACS Appl. Mater. Interfaces, 2017, 9, 20038–20045 CrossRef CAS PubMed.
- M. S. Cao, Y. Z. Cai, P. He, J. C. Shu, W. Q. Cao and J. Yuan, Chem. Eng. J., 2019, 359, 1265–1302 CrossRef CAS.
- J. Tang, T. S. Mathis, N. Kurra, A. Sarycheva, X. Xiao, M. N. Hedhili, Q. Jiang, H. N. Alshareef, B. Xu, F. Pan and Y. Gogotsi, Angew. Chem., Int. Ed., 2019, 58, 17849–17855 CrossRef CAS PubMed.
- N. Liu, Q. Li, H. Wan, L. Chang, H. Wang, J. Fang, T. Ding, Q. Wen, L. Zhou and X. Xiao, Nat. Commun., 2022, 13, 5551 CrossRef CAS PubMed.
- Y. Wang, L. Yao, Q. Zheng and M. S. Cao, Nano Res., 2022, 15, 6751–6760 CrossRef CAS.
- P. Wu, X. Kong, Y. Feng, W. Ding, Z. Sheng, Q. Liu and G. Ji, Adv. Funct. Mater., 2024, 34, 2311983 CrossRef CAS.
- W. Ma, X. Liu, T. Yang, J. Wang, Z. Qiu, Z. Cai, P. Bai, X. Ji and Y. Huang, Adv. Funct. Mater., 2024, 2314046 CrossRef.
- T. Münzel, S. Kröller-Schön, M. Oelze, T. Gori, F. P. Schmidt, S. Steven, O. Hahad, M. Röösli, J. M. Wunderli, A. Daiber and M. Sørensen, Annu. Rev. Public Health, 2020, 41, 309–328 CrossRef PubMed.
- R. Guski, D. Schreckenberg and R. Schuemer, Int. J. Environ. Res. Public Health, 2017, 14, 1539 CrossRef PubMed.
- M. Yang, S. Chen, C. Fu and P. Sheng, Mater. Horiz., 2017, 4, 673–680 RSC.
- X. Cai, Q. Guo, G. Hu and J. Yang, Appl. Phys. Lett., 2014, 105, 121901 CrossRef.
- J. Feng, Q. Liang, Y. Dou, J. He, J. He and T. Chen, Phys. Rev. Appl., 2022, 18, 034054 CrossRef CAS.
- M. Yang and P. Sheng, Annu. Rev. Mater. Res., 2017, 47, 83–114 CrossRef CAS.
- U. Berardi and G. Iannace, Build. Environ., 2015, 94, 840–852 CrossRef.
- Z. Li, L. Zhang and H. Wu, Small, 2024, 20, 2305120 CrossRef CAS.
- S. Bao, M. Zhang, X. Bu, W. Zhang, Z. Jiang and Z. Xie, ACS Appl. Mater. Interfaces, 2023, 15, 13565–13575 CrossRef CAS PubMed.
- X. Zhong, M. He, C. Zhang, Y. Guo, J. Hu and J. Gu, Adv. Funct. Mater., 2024, 34, 2313544 CrossRef CAS.
- Y. Gao, Z. Lei, L. Pan, Q. Wu, X. Zhuang, G. Tan, M. Ning and Q. Man, Chem. Eng. J., 2023, 457, 141325 CrossRef CAS.
- W. Gu, J. Tan, J. Chen, Z. Zhang, Y. Zhao, J. Yu and G. Ji, ACS Appl. Mater. Interfaces, 2020, 12, 28727–28737 CrossRef CAS PubMed.
- R. Hu, Y. Liu, S. Shin, S. Huang, X. Ren, W. Shu, J. Cheng, G. Tao, W. Xu, R. Chen and X. Luo, Adv. Energy Mater., 2020, 10, 1903921 CrossRef CAS.
- S. Wu, T. Li, Z. Tong, J. Chao, T. Zhai, J. Xu, T. Yan, M. Wu, Z. Xu, H. Bao, T. Deng and R. Wang, Adv. Mater., 2019, 31, 1905099 CrossRef CAS.
- J. Yang, H. Wang, Y. Zhang, H. Zhang and J. Gu, Nano-Micro Lett., 2024, 16, 31 CrossRef CAS.
- J. Gu and D. Wang, Chin. J. Polym. Sci., 2024, 42, 895–896 CrossRef CAS.
- C. Liang, H. Qiu, P. Song, X. Shi, J. Kong and J. Gu, Sci. Bull., 2020, 65, 616–622 CrossRef CAS PubMed.
- M. He, J. Hu, H. Yan, X. Zhong, Y. Zhang, P. Liu, J. Kong and J. Gu, Adv. Funct. Mater., 2024, 2316691 CrossRef.
- P. Mou, J. Zhao, G. Wang, S. Shi, G. Wan, M. Zhou, Z. Deng, S. Teng and G. Wang, Chem. Eng. J., 2022, 437, 135285 CrossRef CAS.
- W. Gu, J. Sheng, Q. Huang, G. Wang, J. Chen and G. Ji, Nano-Micro Lett., 2021, 13, 102 CrossRef CAS PubMed.
- B. Zhan, Y. Hao, X. Qi, Y. Qu, J. Ding, J. L. Yang, X. Gong, Y. Chen, Q. Peng and W. Zhong, Nano Res., 2024, 17, 927–938 CrossRef CAS.
- C. Chen, Y. Kuang, S. Zhu, I. Burgert, T. Keplinger, A. Gong, T. Li, L. Berglund, S. J. Eichhorn and L. Hu, Nat. Rev. Mater., 2020, 5, 642–666 CrossRef CAS.
- Y. Cui, H. Gong, Y. Wang, D. Li and H. Bai, Adv. Mater., 2018, 30, 1706807 CrossRef.
- J. Xu, X. Zhang, Z. Zhao, H. Hu, B. Li, C. Zhu, X. Zhang and Y. Chen, Small, 2021, 17, 2102032 CrossRef CAS PubMed.
- Z. Lu, Y. Wang, X. Di, N. Wang, R. Cheng and L. Yang, Carbon, 2022, 197, 466–475 CrossRef CAS.
- S. Zheng, W. Xu, J. Liu, F. Pan, S. Zhao, Y. Wang, Z. Zeng and N. Wu, Adv. Funct. Mater., 2024, 2402889 CrossRef.
- L. Song, F. Zhang, Y. Chen, L. Guan, Y. Zhu, M. Chen, H. Wang, B. R. Putra, R. Zhang and B. Fan, Nano-Micro Lett., 2022, 14, 152 CrossRef CAS PubMed.
- Z. Zhang, G. Wang, W. Gu, Y. Zhao, S. Tang and G. Ji, J. Colloid Interface Sci., 2022, 605, 193–203 CrossRef CAS PubMed.
- F. Yang, J. Yao, L. Jin, W. Huyan, J. Zhou, Z. Yao, P. Liu and X. Tao, Composites, Part B, 2022, 243, 110161 CrossRef CAS.
- X. Deng, S. Gao, X. Qi, H. Dai, S. Fu, Q. Ni and Y. Fu, Chem. Eng. J., 2023, 473, 145040 CrossRef CAS.
- D. Wakerley, S. Lamaison, F. Ozanam, N. Menguy, D. Mercier, P. Marcus, M. Fontecave and V. Mougel, Nat. Mater., 2019, 18, 1222–1227 CrossRef CAS PubMed.
- X. Li, G. Dong, Z. Liu and X. Zhang, ACS Nano, 2021, 15, 4759–4768 CrossRef CAS PubMed.
- Q. Zeng, H. Zhou, J. Huang and Z. Guo, Nanoscale, 2021, 13, 11734–11764 RSC.
- S. Goharshenas Moghadam, H. Parsimehr and A. Ehsani, Adv. Colloid Interface Sci., 2021, 290, 102397 CrossRef CAS.
- Y. Li, X. Liu, X. Nie, W. Yang, Y. Wang, R. Yu and J. Shui, Adv. Funct. Mater., 2019, 29, 1807624 CrossRef.
- J. Yang, J. Wang, H. Li, Z. Wu, Y. Xing, Y. Chen and L. Liu, Adv. Sci., 2022, 9, 2101988 CrossRef CAS PubMed.
- J. Xu, Y. Zhao, Y. Chen, Y. Chen, Z. H. Xie and P. R. Munroe, ACS Appl. Mater. Interfaces, 2022, 14, 42468–42482 CrossRef CAS PubMed.
- C. Ma, W. Wang, D. Kong, S. Wei, W. Li and S. Chen, J. Cleaner Prod., 2022, 378, 134419 CrossRef CAS.
- J. Xiao, B. Zhan, M. He, X. Qi, X. Gong, J. L. Yang, Y. Qu, J. Ding, W. Zhong and J. Gu, Adv. Funct. Mater., 2024, 2316722 CrossRef.
- W. Tian, J. Li, Y. Liu, R. Ali, Y. Guo, L. Deng, N. Mahmood and X. Jian, Nano-Micro Lett., 2021, 13, 161 CrossRef CAS.
- H. T. Dinh, J. Kuever, M. Mußmann, A. W. Hassel, M. Stratmann and F. Widdel, Nature, 2004, 427, 829–832 CrossRef CAS PubMed.
- D. Xu, T. Gu and D. R. Lovley, Nat. Rev. Microbiol., 2023, 21, 705–718 CrossRef CAS.
- M. Godoy-Gallardo, U. Eckhard, L. M. Delgado, Y. J. D. de Roo Puente, M. Hoyos-Nogués, F. J. Gil and R. A. Perez, Bioact. Mater., 2021, 6, 4470–4490 CAS.
- Q. Liu, A. Zhang, R. Wang, Q. Zhang and D. Cui, Nano-Micro Lett., 2021, 13, 154 CrossRef CAS PubMed.
- J. Cai, V. Murugadoss, J. Jiang, X. Gao, Z. Lin, M. Huang, J. Guo, S. A. Alsareii, H. Algadi and M. Kathiresan, Adv. Compos. Hybrid Mater., 2022, 5, 641–650 CrossRef CAS.
- Y. Cao, D. Zheng, F. Zhang, J. Pan and C. Lin, J. Mater. Sci. Technol., 2022, 102, 232–263 CrossRef CAS.
- B. Li, S. Xue, P. Mu and J. Li, ACS Appl. Mater. Interfaces, 2022, 14, 30192–30204 CrossRef CAS PubMed.
- H. Chen, F. Wang, H. Fan, R. Hong and W. Li, Chem. Eng. J., 2021, 408, 127343 CrossRef CAS.
- C. C. M. Sproncken, P. Liu, J. Monney, W. S. Fall, C. Pierucci, P. B. V. Scholten, B. Van Bueren, M. Penedo, G. E. Fantner, H. H. Wensink, U. Steiner, C. Weder, N. Bruns, M. Mayer and A. Ianiro, Nature, 2024, 630, 866–871 CrossRef CAS PubMed.
- C. R. Ratwani, A. R. Kamali and A. M. Abdelkader, Prog. Mater. Sci., 2023, 131, 101001 CrossRef CAS.
- K. Cerdan, M. Thys, A. Costa Cornellà, F. Demir, S. Norvez, R. Vendamme, N. Van den Brande, P. Van Puyvelde and J. Brancart, Prog. Polym. Sci., 2024, 152, 101816 CrossRef.
- J. Tao, J. Zhou, Z. Yao, J. Wang, L. Xu, X. Tao and H. Wu, Adv. Funct. Mater., 2024, 34, 2310640 CrossRef CAS.
- Y. Zhang, L. Zhang, L. Tang, R. Du and B. Zhang, ACS Nano, 2024, 18, 8411–8422 CrossRef CAS PubMed.
- H. L. Yang, Y. Chen, C. Q. Li, G. Wu and J. N. Wang, Carbon, 2023, 210, 118079 CrossRef CAS.
- W. L. Song, L. Z. Fan, Z. L. Hou, K. L. Zhang, Y. Ma and M. S. Cao, J. Mater. Chem. C, 2017, 5, 2432–2441 RSC.
- M. Li, W. Zhu, X. Li, H. Xu, X. Fan, H. Wu, F. Ye, J. Xue, X. Li, L. Cheng and L. Zhang, Adv. Sci., 2022, 9, 2201118 CrossRef CAS PubMed.
- L. Liang, C. Li, X. Yang, Z. Chen, B. Zhang, Y. Yang and G. Ji, Nano Lett., 2024, 24, 2652–2660 CrossRef CAS PubMed.
- L. Wu, S. Shi, G. Wang, P. Mou, X. Liu, J. Liu, L. Li and C. Du, Adv. Funct. Mater., 2022, 32, 2209898 CrossRef CAS.
- F. Pan, K. Pei, G. Chen, H. Guo, H. Jiang, R. Che and W. Lu, Adv. Funct. Mater., 2023, 33, 2306599 CrossRef CAS.
- B. Edwards, A. Alù, M. G. Silveirinha and N. Engheta, Phys. Rev. Lett., 2009, 103, 153901 CrossRef PubMed.
- L. Zigoneanu, B. I. Popa and S. A. Cummer, Nat. Mater., 2014, 13, 352–355 CrossRef CAS PubMed.
- C. Qian, B. Zheng, Y. Shen, L. Jing, E. Li, L. Shen and H. Chen, Nat. Photonics, 2020, 14, 383–390 CrossRef CAS.
- X. Li, Z. Le, X. Chen, Z. Li, W. Wang, X. Liu, A. Wu, P. Xu and D. Zhang, Appl. Catal., B, 2018, 236, 501–508 CrossRef CAS.
- Y. Feng, Y. Tao, Q. Meng, J. Qu, S. Ma, S. Han and Y. Zhang, Chem. Eng. J., 2022, 441, 135924 CrossRef CAS.
- X. Jie, W. Li, D. Slocombe, Y. Gao, I. Banerjee, S. Gonzalez-Cortes, B. Yao, H. AlMegren, S. Alshihri, J. Dilworth, J. Thomas, T. Xiao and P. Edwards, Nat. Catal., 2020, 3, 902–912 CrossRef CAS.
- A. Ramirez, J. L. Hueso, M. Abian, M. U. Alzueta, R. Mallada and J. Santamaria, Sci. Adv., 2019, 5, eaau9000 CrossRef CAS PubMed.
- C. Zhou, Q. M. Sun, Q. Cao, J.-H. He and J.-M. Lu, Small, 2023, 19, 2205341 CrossRef CAS PubMed.
- W. Wang, J. Huang, Y. Fu, W. Jiang, Y. Chen, Y. Ma and S. Han, Appl. Catal., B, 2023, 333, 122787 CrossRef CAS.
- M. Cao, X. Wang, W. Cao, X. Fang, B. Wen and J. Yuan, Small, 2018, 14, 1800987 CrossRef PubMed.
- H. Lv, Y. Yao, S. Li, G. Wu, B. Zhao, X. Zhou, R. L. Dupont, U. I. Kara, Y. Zhou, S. Xi, B. Liu, R. Che, J. Zhang, H. Xu, S. Adera, R. Wu and X. Wang, Nat. Commun., 2023, 14, 1982 CrossRef CAS PubMed.
- Q. Wu, N. Xia, D. Long, L. Tan, W. Rao, J. Yu, C. Fu, X. Ren, H. Li, L. Gou, P. Liang, J. Ren, L. Li and X. Meng, Nano Lett., 2019, 19, 5277–5286 CrossRef CAS PubMed.
- J. Xu, X. Cheng, L. Tan, C. Fu, M. Ahmed, J. Tian, J. Dou, Q. Zhou, X. Ren, Q. Wu, S. Tang, H. Zhou, X. Meng, J. Yu and P. Liang, Nano Lett., 2019, 19, 2914–2927 CrossRef CAS.
- H. Hu, Y. Ju, J. Yu, Z. Wang, J. Pei, H. C. Thong, J. W. Li, B. Cai, F. Liu, Z. Han, B. Su, H. L. Zhuang, Y. Jiang, H. Li, Q. Li, H. Zhao, B.-P. Zhang, J. Zhu and J. F. Li, Nat. Mater., 2024, 23, 527–534 CrossRef CAS PubMed.
- M. Massetti, F. Jiao, A. J. Ferguson, D. Zhao, K. Wijeratne, A. Würger, J. L. Blackburn, X. Crispin and S. Fabiano, Chem. Rev., 2021, 121, 12465–12547 CrossRef CAS.
- C. Liu, Z. Zhang, Y. Peng, F. Li, L. Miao, E. Nishibori, R. Chetty, X. Bai, R. Si, J. Gao, X. Wang, Y. Zhu, N. Wang, H. Wei and T. Mori, Sci. Adv., 2023, 9, eadh0713 CrossRef CAS PubMed.
- Y. Zhu, Q. Li, C. Wang, Y. Hao, N. Yang, M. Chen, J. Ji, L. Feng and Z. Liu, Chem. Rev., 2023, 123, 7326–7378 CrossRef CAS PubMed.
- S. Son, J. Kim, J. Kim, B. Kim, J. Lee, Y. Kim, M. Li, H. Kang and J. S. Kim, Chem. Soc. Rev., 2022, 51, 8201–8215 RSC.
- Z. Yang, D. Gao, J. Zhao, G. Yang, M. Guo, Y. Wang, X. Ren, J. S. Kim, L. Jin, Z. Tian and X. Zhang, Nat. Rev. Clin. Oncol., 2023, 20, 116–134 CrossRef PubMed.
- A. Zhang, K. Jung, A. Li, J. Liu and C. Boyer, Prog. Polym. Sci., 2019, 99, 101164 CrossRef CAS.
- H. Xiang and Y. Chen, Small, 2019, 15, 1805339 CrossRef PubMed.
|
This journal is © The Royal Society of Chemistry 2024 |
Click here to see how this site uses Cookies. View our privacy policy here.